- 1Group Production Engineering/Automation of Production Processes, Department SciTec, Ernst-Abbe University of Applied Sciences Jena, Jena, Germany
- 2Group for Inorganic Non-Metallic Materials, Department Mechanical Engineering, Technische Universität Ilmenau, Ilmenau, Germany
The creation of holes in hard-brittle materials is highly relevant for various applications. The often-necessary high aspect ratios of the drill holes pose a particular challenge, with drill diameters of a few millimeters and drill lengths of up to several hundred millimeters. This requires the application of suitable tools with a high aspect ratio and sufficient stability. In particular the drilling process itself must be thoroughly understood and optimized in order to produce deep holes without component and tool defects while maintaining the required dimensional and positional accuracy. This paper presents investigations on the influence of an ultrasonic tool oscillation for drilling high aspect ratio holes. Two kinematic approaches, deep drilling and helical drilling, are examined with focus on the achievable dimensional accuracy of the holes and the roughness of the inner walls of the bore. It is found, that adding a longitudinal high frequency tool oscillation enables a considerable reduction in dimensional deviations of 91% for helical drilling.
1 Introduction
Numerous applications for components made from inorganic non-metallic materials like silicate glasses require internal contours with high requirements, such as a very high aspect ratio (length to diameter). Such components can be required in fiber preform production, in order to be able to draw fiber types with special properties. In order to draw an optical fiber, such a preform, which is a multiple of the later end product in terms of dimensions but already has identical geometric proportions, must first be manufactured. In the case of complex, multi-core fibers, this preform may already have a very elaborate design and require, for example, the drilling of a high-purity quartz glass rod with several different holes which can be filled with cylinders of other materials (Bliedtner, 2022; Schartner et al., 2017). Besides other preform fabrication methods the drilling of a bulk material enables a wide geometrical range and is applicable to a variety of optical materials. There is a high motivation to improve the manufacturing technologies of optical preforms, since this should lead to the evolution of new optical fiber properties and applications of them (Monro and Ebendorff-Heidepriem, 2006). Aspect ratio requirements of preforms are, for example, to insert a drill hole diameter of 3 mm into a 300 mm long preform. The particular challenge here, in addition to the high aspect ratio, is the quality of the borehole wall, which in some applications must correspond to an almost final polished surface (Rq < 2 nm) (Bliedtner, 2022; Pflanz and Ketelaer, 2023). Another important field of application for complex component geometries is the production of laser gyroscopes, which are used to detect changes in direction or position control. Optical ring laser gyroscopes work based on the Sagnac effect to enable sensing of an angular rotation and have the highest market share of gyroscopes. A common design of this device is a triangular glass block containing three air channels and three mirrors at the end of the channels creating an optical resonator (Passaro et al., 2017). These devices are mostly applied for navigation or orientation purposes in the aerospace industry (Dell’Olio et al., 2014). The larger the ring laser gyroscope the higher is its sensitivity which justifies the interest in being able to manufacture large components and thus also deep bores (Passaro et al., 2017). Here too, both the outer and inner contours of a component must be manufactured with the utmost precision in order to ensure functionality and high accuracy. In addition to the surface quality requirements, high dimensional accuracy and low conicity of the internal contours produced (usually bores) also play a decisive role. In order to guarantee this, the grinding process for diamond drilling tools is highly relevant. Various strategies can be used, whereby in most cases a distinction is made between deep drilling and helical drilling with diamond hollow drills (Bliedtner, 2022).
Here it is possible to support the process with ultrasonic assistance, whereby the rotation of the tool is superimposed with a high-frequency ultrasonic oscillation than can result into certain processing benefits. This movement is usually generated by piezoceramic actuators. The oscillation occurs with amplitudes typically in the single-digit µm range (sometimes also in the low two-digit range) and high frequencies in the ultrasonic region (over 20 kHz) (Bertsche et al., 2013; Park et al., 2014). Due to the superimposition of the active movements, the individual abrasive grains of the tool travel sinusoidal paths in the workpiece, which is why the effective cutting depth constantly fluctuates during the process (Bliedtner, 2022; Jianhua et al., 2014). This makes it possible to achieve a better coolant supply and chip removal from the machining zone (Bleicher and Bernreiter, 2009; Bleicher and Bernreiter, 2015). As a result, the temperatures on the tool are also reduced and the lower thermal load, in conjunction with lower process forces, increases the tool life (Bleicher and Bernreiter, 2009; Choi et al., 2013). Reduced tool wear is therefore a significant advantage of ultrasonic-assisted grinding (Bleicher and Bernreiter, 2015; Lauwers et al., 2010; Tawakoli and Azarhoushang, 2008). More detailed investigations of tool wear, in which the changes in individual diamond grains were determined microscopically as machining progressed, show that ultrasonic machining primarily results in constant, small micro-chipping of the individual grains. The result is a self-sharpening effect of the tool (Ding et al., 2014; Geng et al., 2015).
The investigation of drilling applications in particular has already been proven in many cases that drilling with ultrasonic support can reduce the grinding forces during the process and positively influence the formation of edge chipping at the entry and exit points of the tool (Wang et al., 2016; Wang et al., 2018). Anwar et al. also found a reduction in force when the ultrasonic power was increased, although the ultrasonic oscillation also tended to have a negative effect. For example, increasing the power resulted in an increase in the conicity of the 3-mm-deep drill holes, which had a negative effect on dimensional accuracy (Anwar et al., 2018). Jadoun et al. investigated the manufacturing accuracy of drill holes in aluminum oxide-based ceramics. Using silicon carbide tools, they attempted to improve the accuracy of the holes using various process parameters. They found that the hole oversize and conicity increase with higher grain size and concentration. In their experiments, the roundness of the drill holes was most strongly influenced by the grain size. They found that the deviation of the holes was about twice as large as the average diameter of the abrasive used. Furthermore, they were also able to show that the deviation from the nominal diameter and the conicity also rise slightly with increasing ultrasonic power (Jadoun et al., 2009). Alkahalefah also investigated the effect on the dimensional accuracy of drilled holes on aluminum oxide during rotary ultrasonic drilling using different process variables. It was observed that the cylindricity is significantly influenced by the rotational speed and the feed rate. The best cylindricity of a drilled hole was achieved with a spindle speed of 4,000 rpm, a feed rate of 1.5 mm/min, a vibration amplitude of 20 µm and an ultrasonic frequency of 23 kHz (Alkhalefah, 2020). In contrast, Dong and Zhang carried out tests on fluorophlogopite ceramics for helical drilling of deep, small holes and compared the grinding force, roundness deviation and surface roughness using conventional and rotational ultrasonic grinding. They were able to establish that the use of rotational ultrasonic grinding leads to a significant improvement in the test parameters mentioned, with increasing spindle speed and ultrasonic power having the greatest influence. Increasing the feed rate, on the other hand, led to a deterioration in shape accuracy, which is why they recommend a combination of the aforementioned results for efficient machining (Dong and Zhang, 2019). Abdelkawy and El-Hofy also carried out investigations on soda glass on the dimensional accuracy of drilled holes by varying the feed rate and spindle speed. They also used different grain concentrations and analyzed their influence on the surface quality. The authors were able to establish that low feed rates and high spindle speeds have a positive influence on the dimensional accuracy and surface quality of holes in ultrasonic drilling. The use of higher grain concentrations also showed a significant improvement in the analyzed parameters in their experiments (Abdelkawy and El-Hofy, 2021).
Furthermore, the ultrasonic, rotational speed and feed rate parameters can also have an essential influence on the achievable edge quality of the drilled holes. Kumar and Singh investigated the interaction of the three parameters and attempted to optimize their combination in such a way that the edge chipping was as low as possible. A speed of 5,000 rpm, a feed rate of 0.3 mm/min and an ultrasonic power of 70% (700 W) were identified as the optimum combination (Kumar and Singh, 2019a). In their studies on float glass, Sharma et al. also cite the feed rate as an important factor for optimized hole creation. They recommend selecting the feed rate as low as possible to ensure a ductile and more gentle process and thus achieve a lower level of edge chipping. In combination with a high ultrasonic amplitude and a small tool diameter, the best results could be achieved (Sharma et al., 2018). Singh and Singhal were also able to detect similar results in parameter analyses on Macor® ceramics. They also recommend a low feed rate of 1.14 mm/min in combination with a higher spindle speed of 4,100 1/min and ultrasonic assistance for low edge chipping (Singh and Singhal, 2018). In addition to selecting the ideal parameters, edge chipping can also be significantly influenced by the grain size of the tool. Nath et al. found that the hole integrity (quality of the hole entry and roughness of the hole wall) is dependent on the grain size used and found that the size and length of the resulting edge chipping is about two to four times as large as the grain radius of the abrasive used (Nath et al., 2012). In the area of surface quality and material removal rate, the three parameters feed rate, spindle speed and ultrasonic power are also those that significantly influence process efficiency. Singh and Kumar found that the removal rate during drilling is largely influenced by the feed rate and only to a small extent by the rotational speed. With regard to surface roughness, the feed rate also had the greatest influence (Singh and Kumar, 2019). The same authors also came to similar conclusions in their parameter analyses of the machining performance of rotary ultrasonic drilling of N-BK7 glass. They also listed the feed rate, followed by the spindle speed and the ultrasonic power, as the greatest influencing factor for the achievable surface quality and material removal rate. Furthermore, it was also shown that low feed rates lead to ductile material removal, which is why they consider a medium feed rate with high spindle speed and ultrasonic power to be suitable for efficient performance (Kumar and Singh, 2019b).
In the following, it will be analyzed how a defined ultrasonic oscillation affects factors such as dimensional accuracy and surface quality when drilling fused silica. The aim is to find out to what extent the previous findings in the literature on several brittle-hard materials can be confirmed in the application for fused silica glass or if other behaviors become apparent. Another focus is set on the comparison between two kinematic approaches, deep drilling and helical drilling.
2 Materials and methods
During drilling, the feed movement of the tool generally only takes place in one spatial direction (usually Z). This is called deep-hole drilling, in which the tool diameter is identical to the drill diameter to be produced in the component. The adjustable grinding parameters are limited to the rotational speed or cutting speed vc and the feed rate vf at which the tool moves along an axis into the component. In contrast, helical drilling is a kinematically more complex, yet geometrically easily definable variant. This involves a spiral feed of the tool into the component, for which X, Y, and Z movements take place simultaneously. The resulting drilling diameter is therefore dependent on the tool and the diameter of the spiral. In addition to the grinding parameters cutting speed and the feed rate of the path movement, the helical infeed depth ap Helix, i.e., the depth of infeed during a 360° helix revolution, is an additional setting parameter. Figure 1 illustrates the kinematics of the two drilling variants.
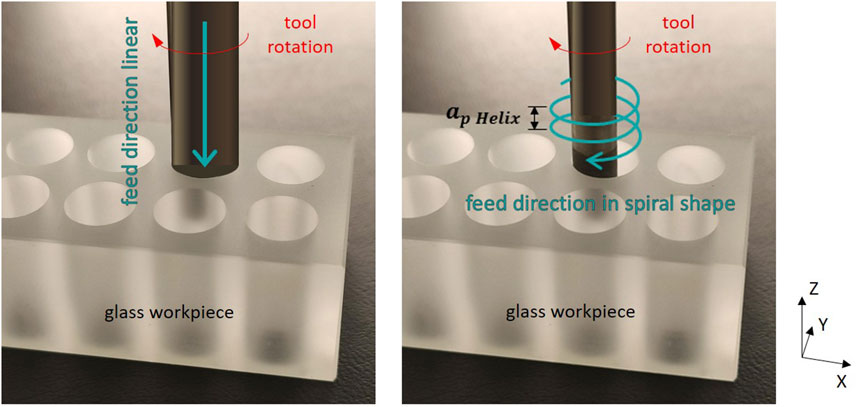
Figure 1. Schematic representation of the kinematic approaches for drilling operations: deep drilling (left) and helical drilling (right).
The presented investigations are carried out on a 5-axes CNC grinding machine “Ultrasonic 20 linear” from DMG Mori. It offers a working area of 200 × 200 × 200 mm³ (X/Y/Z) and the possibility of an inner tool cooling which is a necessity for drilling of deep bores. Another special feature of this machine is the possibility to apply a high frequency oscillation in Z direction to the grinding tool in addition to the tool rotation. The ultrasonic frequency can be adjusted between 20 and 30.5 kHz leading to a tool and frequency dependent amplitude in the micrometer range between around 1–16 µm.
A hollow drill grinding tool with an outer diameter of 5 mm and a tool length of 70 mm from Schott Diamantwerkzeuge is used that incorporates a diamond grain size D64 and C200 concentration in a galvanic metal bond (Figure 2). This tool is applied for either deep drilling of ø 5 mm bores or helical drilling of ø 7.5 mm holes into cuboid fused silica workpieces (“HPFS7980” from Corning) with dimensions of 50 × 50 × 50 mm³. 50 mm deep through-holes are therefore produced with either activated or deactivated ultrasonic assistance and otherwise constant grinding parameters.
The grinding parameters were evaluated beforehand in preliminary investigations. These have shown that a high spindle speed of over 20,000 rpm can lead to the tool beginning to vibrate laterally due to its length. This results in significant edge chipping on the top of the bore and loud grinding noises. Adjusting the grinding parameters and the associated significant reduction in speed to 2,000 rpm (cutting speed vc approx. 0.5 mm) can reduce the vibration and enable successful deep holes to be drilled. To guide and precisely position the long and therefore more unstable hollow drill, a pilot hole is implemented in the process using a shorter (<10 mm) cylindrical grinding tool, which further improves process quality and stability. The grinding parameter settings defined for the main tests are listed in Table 1.
As already mentioned, the effective ultrasonic amplitude of the tool depends on its geometry and its excitation frequency. For this reason, the vibration behavior of the tool used was first determined by vibrometry measurements. Therefore, a single point laser Doppler vibrometer “OFV-534” from Polytec GmbH is applied to achieve a contactless and therefore non-intrusive vibration measurement of the tool. The measurement signal is taken from the end face of the tool by guiding the laser beam from the measurement head to the tool from below via a mirror (Figure 3).
The ultrasonic amplitude was then measured while the excitation frequency was continuously tuned within the available range from 20,000 to 30,500 Hz. This results in a tool geometry specific ultrasonic diagram as can be seen in Figure 4. In a certain frequency range around the tool’s resonance frequency (26,500 Hz) high applicable tool amplitudes can be found. The resonance frequency itself must be avoided for the used machine, since longer application of this frequency can lead to ultrasonic generator overheating. Instead, a working frequency must be found by which the generator power is below a value of about 14% while still offering a high amplitude. Between 26,400 and 27,000 Hz the generator power increases up to over 25% which is according to the machine manufacturer DMG Mori too high for applications longer than a few seconds for the given machine generation and could cause defects of the ultrasonic generator or tool holder. Therefore, in the given case a working frequency of 27,100 Hz is chosen which produces the highest possible tool oscillation amplitude outside of this critical frequency window of approx. 5 μm. In case of the main experiments this ultrasonic assistance is activated and deactivated in half of the drilling tests enabling a direct comparison of the ultrasonic influence onto the process.
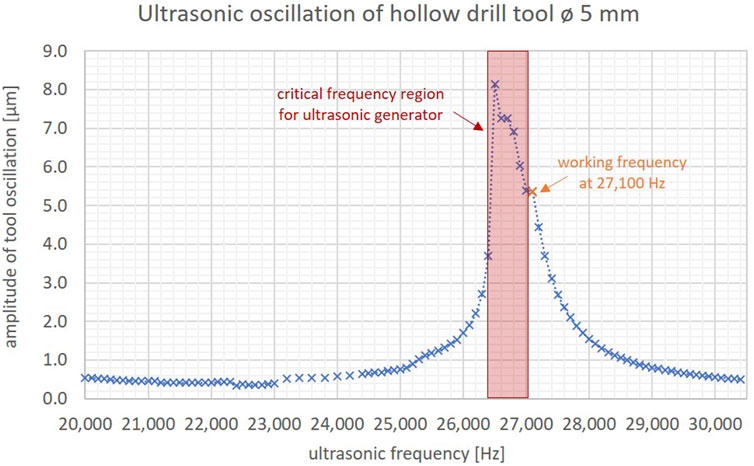
Figure 4. Measured tool oscillation amplitude of the used hollow drill grinding tool depending on the set ultrasonic frequency.
After each drilling experiment, the surface quality of the holes is measured along the hole wall. The tactile stylus method is used to determine the roughness, whereby a special small stylus tip (total height 1.2 mm) is applied to ensure accessibility even in small holes. The stylus measuring device is a “Talysurf 50” from Taylor Hobson. For each measured point the mean value and standard deviation of six roughness measurements (three identically drilled holes each measured twice) is generated over a measurement length of 4 mm. The dimensional accuracy of the holes is determined using the measuring probe integrated in the grinding machine. By application of the “Power Probe 400” optical tactile measuring probe (Renishaw), the diameter produced is measured in different depth positions along the whole bore length. This is done in the clamped state within the grinding machine. The tactile measuring system contains a ruby ball with a diameter of 2 mm for probing surfaces. The repeat accuracy of this measurement system is specified as 0.25 µm. Regarding the experimental error, diameter measurement variation for each depth position is below ±3 µm.
3 Results
The results of the drill holes produced in the experiments are presented below. Here, a subdivision is made into roughness results and achieved dimensional accuracy of the bores.
3.1 Roughness investigations
The rms roughness value Rq is determined at three positions at the inner wall of the bore over a measuring distance of 4 mm. These positions include the tool entry (measured at a drilling depth of approx. 10 mm), the center of the hole (measured at a drilling depth of approx. 25 mm) and the tool exit (measured at a drilling depth of approx. 40 mm). Figure 5 shows the roughness results obtained.
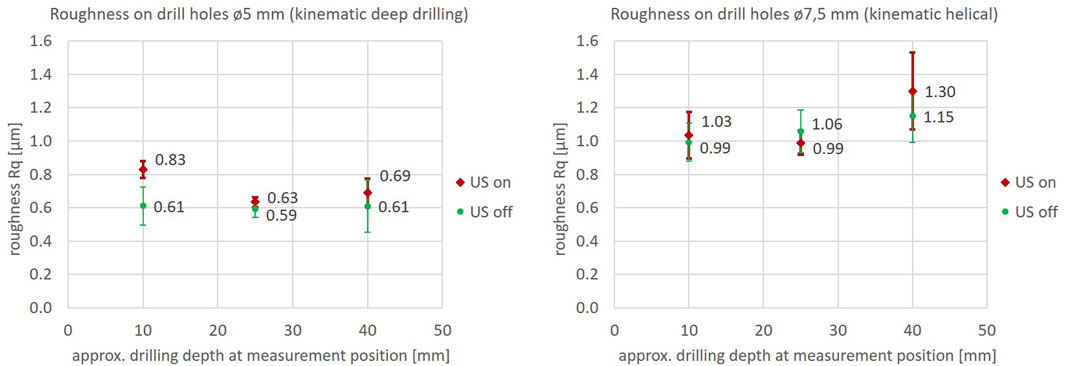
Figure 5. Roughness of the borehole inner walls along the drilling path as a function of the ultrasonic assistance and the kinematics: deep drilling (left) and helical drilling (right).
It is apparent that the kinematics have a significant influence on the resulting surface qualities within the holes. Regardless of the hole section, the roughness values of the helically produced holes are significantly (around 40%) higher than those of the deep drilled holes. This can be explained by the greater stability of the deep drilling process (tool load acts continuous and only in one direction) compared to helical drilling (lateral tool load that constantly changes direction). In both cases, the added ultrasonic assistance has a different effect on the machining results. When observing the roughness results for direct deep-hole drilling, it can be seen that these are on average around 17% better when grinding without ultrasonic. Previous investigations for different grinding applications like planar face and lateral grinding have also shown the tendency of increase of the high frequency surface deviation by high frequency tool oscillation (Schulze et al., 2021; Binder et al., 2024). This effect should be investigated in detail in future investigations. In contrast, ultrasonic oscillation has no significant influence on helical drilling.
3.2 Dimensional accuracy
The grinded bore diameters are measured in 21 different depth positions from 1 mm to 39 mm depth along the bore length. Figure 6 shows the progression of the actual diameter of the deep-hole drillings plotted against the drilling depth. The mean and the absolute deviations from the values of three equally ground holes are visualized, on the one hand with and on the other hand without ultrasonic support. It is apparent that the actual diameter is higher than the target diameter of 5 mm both with and without ultrasonic. The deviation is between approx. 20 and 45 µm. This is primarily due to the protrusion of the abrasive grains, which have an average size of 64 µm. If smaller dimensional deviations are required, the diameter of the hollow drilling tool used may need to be corrected slightly. In the case of processing without ultrasonic assistance, a slight increase in the drill diameter can be seen within the first 15 mm drilling depth, after which the drill diameter remains stable. Interesting is the curve with activated ultrasonic oscillation, which shows a local minimum of the generated drilling diameter at a depth of approx. 4 mm and at this point is congruent with the drilling diameter without ultrasonic. This could be attributed to the special oscillation shape of the ultrasonic-excited tool, which oscillates primarily in the Z direction, i.e., along the bore axis, but according to the manufacturer’s specifications has lateral oscillation nodes and oscillation bellies. There is a characteristic waveform with ultrasonic support, especially within the first 15 mm drilling depth. This behavior and the effect of the ultrasonic oscillation on the shape of the bore inner wall could be shown here for the first time and represent a potential field for further in-depth ultrasonic focused observations with other tools and ultrasonic settings.
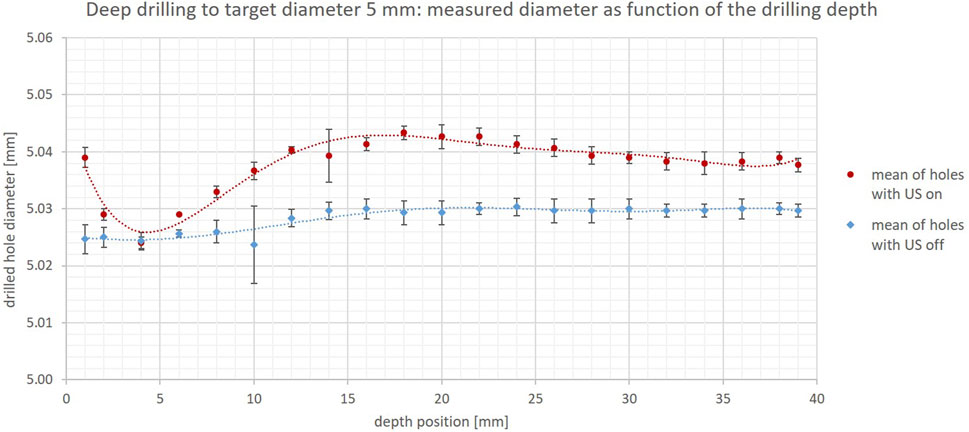
Figure 6. Dimensional accuracy of the diameter of the deep drilled holes (target diameter 5 mm) as a function of the drilling depth.
However, the ultrasonic application is particularly relevant from a manufacturing point of view in the case of helical kinematics. Preliminary investigations on helical drilled holes for 16 mm depth already show strong differences of the drilled diameter depending on the depth position. Here, the dimensional deviation in diameter between the highest measured depth position of 2 mm and deepest position of 14 mm were compared (mean value and standard deviation for 12 drilled holes with either ultrasonic on or off) in Figure 7. Apparently, the deviations in the ultrasonic assisted process are significantly lower with a mean deviation along the drilling depth of only 4 µm compared to 68 µm (with also much higher standard deviation) with ultrasonic oscillation.
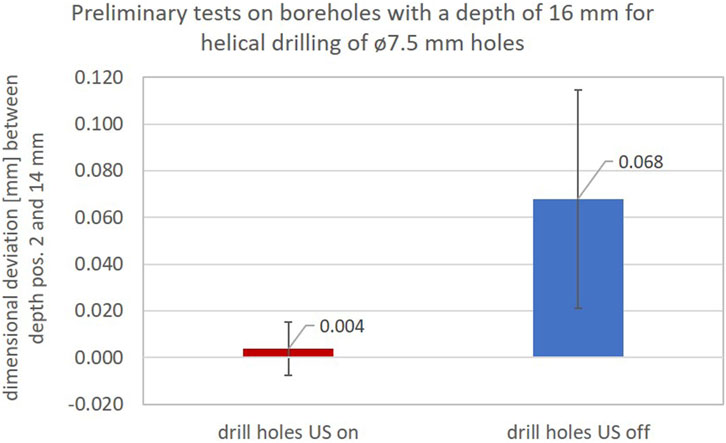
Figure 7. Dimensional deviation in preliminary helical drilling tests for 16 mm deep drill holes, showing already way lower deviations with activated ultrasonic oscillation.
Figure 8 shows the resulting progression of the actual diameter of the helical drilling plotted against the drilling depth in the main experiments for 50 mm total bore depth. As the drilling depth increases, there is always an increasing deviation from the target diameter of 7.5 mm (actual diameter decreases continuously), which is due to the increasing tool loads at depth when using helical kinematics. In this case, however, the high-frequency oscillating tool shows the ability to keep the bore dimensions almost constant over the entire course of the bore. Without the use of the ultrasonic, enormous deviations from the nominal diameter of over 2.2 mm occur close to the bore exit with otherwise identical grinding parameters. In addition, the reproducibility of the diameters with identical parameters is also highly error-prone, as shown by the large absolute deviations of the averaged curve with the ultrasonic (US) switched off in Figure 8 (max. deviation of equally produced bores of over 1 mm).
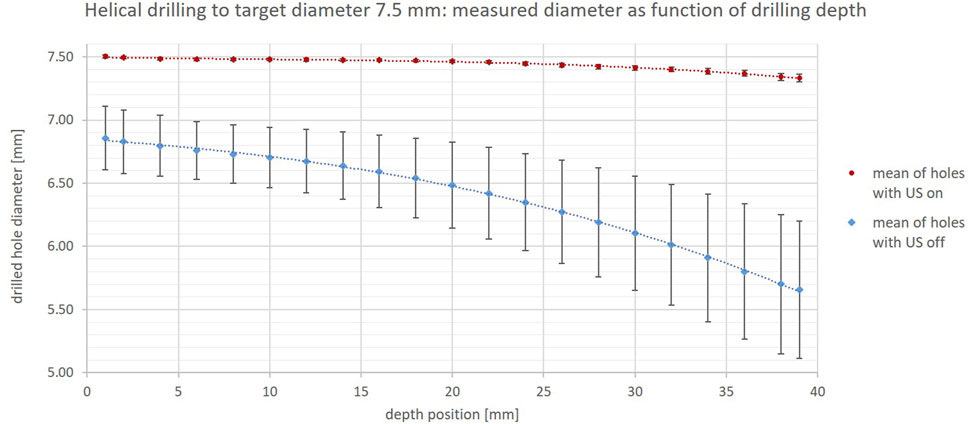
Figure 8. Dimensional accuracy of the diameter of the helical drilled holes (target diameter 7.5 mm) as a function of the drilling depth.
This contrasts with maximum deviations with activated ultrasonic of max. 0.19 mm in relation to the target diameter. This is a reduction of over 91% compared to without ultrasonic. The reproducibility of the drill holes is also enormously optimized by the US. Here, the maximum deviation between the three bores ground with ultrasonic is only 0.055 mm (reduction of over 94% compared to without ultrasonic), which results in a correspondingly low standard deviation of the average curve shown. Apparently, the ultrasonic application enables a stable helical drilling process which is under the given circumstances not possible without the tool oscillation. These results are completely novel and mean that helical drilling with long grinding tools can be utilized as an efficient, flexible way of producing deep holes in various application areas by using the process with ultrasonic support.
Finally, Figure 9 shows an overview of the maximum dimensional deviations from the target diameter. The columns represent both the minimum and the maximum deviation from the nominal value that is determined for the individual holes. It can be seen that the dimensional deviations are higher with the helical drilling kinematics than with the deep drilling kinematics. With ultrasonic assistance, the dimensional deviation is approx. 3.5 times higher with helical drilling than with deep drilling. Without ultrasonic, the enormously high dimensional deviation in helical drilling kinematics already explained is evident, which once again emphasizes the usefulness of ultrasonic vibration in helical drilling with hollow grinding tools.
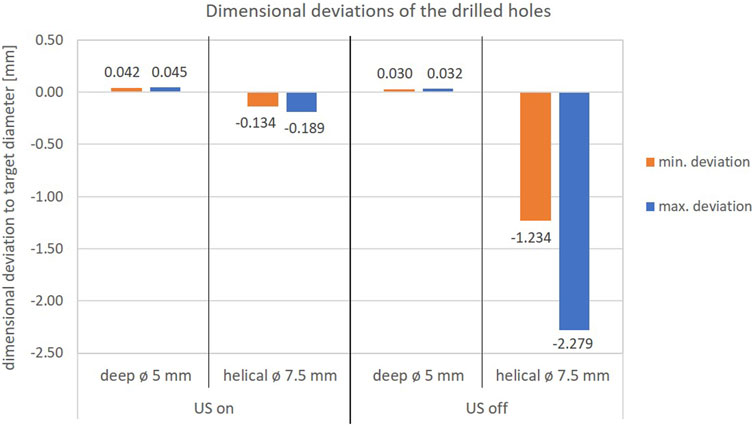
Figure 9. Dimensional deviations of the deep drilled and helical drilled holes in relation to the target diameter.
4 Discussion
The presented investigations have shown a strong influence from the drilling strategy on resulting roughness and dimensional deviations. As previously shown and as also visually recognizable in diameter differences in the resulting drilled workpiece in Figure 10, ultrasonic assistance enables a far lower diameter deviation compared to the target diameter.
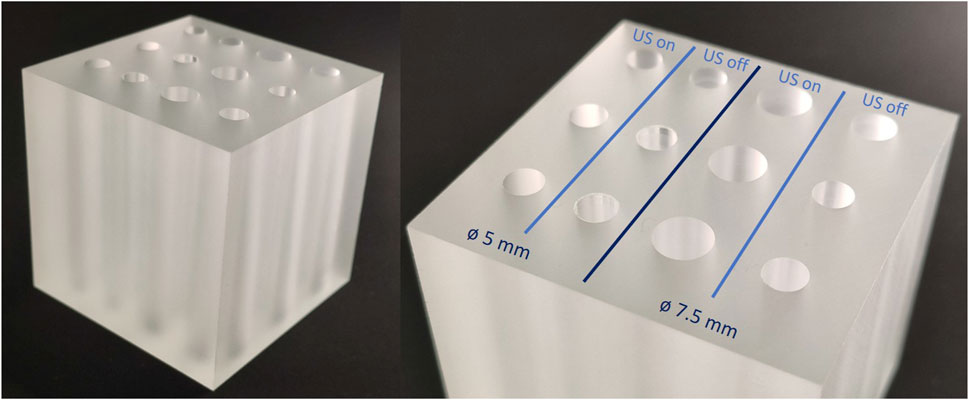
Figure 10. Processed fused silica sample cube (50x50x50 mm³) with through-holes of 5 mm and 7.5 mm target diameter either with ultrasonic assistance on or off.
It can be assumed that the additional oscillation in the Z direction can achieve a reduction in force and lateral stabilization of the drill along the helical machining path, thus enabling constant removal down to the bore depth. This is of great importance in terms of production technology, as it means that helically produced bores can be realized by using ultrasonic support with economical grinding parameters, which is not possible in a comparable way without the application of ultrasonic. The applicability of the helical kinematic for producing deep drill holes enables several advantages regarding fabrication of optical components like fiber preforms or laser gyroscopes. In helical drilling, it is not the diameter accuracy of the tool as the main factor that determines the resulting drilling diameter, but the kinematic machining parameters. The process is therefore much more flexible than deep drilling, there are more correction options and fewer tools are required to produce different drilling diameters. An existing tool can therefore also be dressed several times in diameter, the resulting reduction in diameter can be compensated for by slightly adjusting the helical path. It is therefore potentially possible to produce holes of various diameters with increased aspect ratio efficiently and with sufficient accuracy using the ultrasonic-assisted helical drilling process, which is very beneficial for the described applications of fiber preforms, optical gyroscopes, or other monolithic optical elements. Figure 11 shows an example preform design of a 300 mm long element with ø32 mm that has several drill holes with different diameters. The application of deep drilling and ultrasonic assisted helical drilling would be able to produce these bore holes efficiently after further process optimizations using only one tool geometry of ø5 mm.
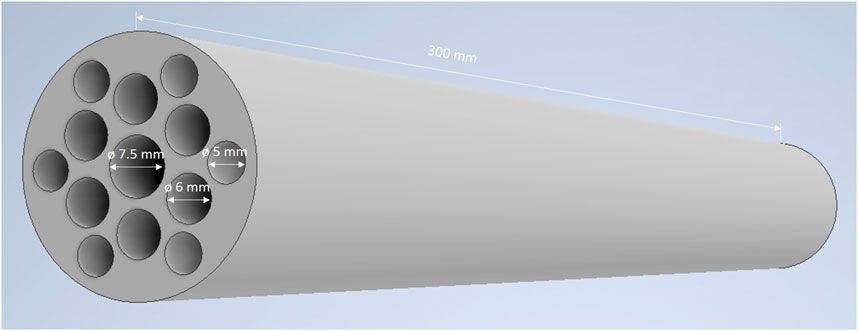
Figure 11. Possible preform design example with a diameter of 32 mm and 300 mm length including 13 different sized bore holes that could be manufactured with the same drill tool (ø 5 mm) using deep drilling and ultrasonic assisted helical drilling.
More in depth investigations on the interactions between the geometry of the tool, its high-frequency excitation and interactions with the workpiece material are in preparation. Future research is planned to investigate the influence of ultrasonic oscillation on the drilling process for other tool specifications and, where appropriate, variations in the ultrasonic frequency and thus also the ultrasonic amplitude for the dimensional accuracy and quality of bore holes. The goal is the achievement of holes with an even higher aspect ratio and depths up to above 300 mm. Possible limitations may occur due to tool wear over extended use. However, since previous work has shown the possibility to reduce tool wear by ultrasonic application by more than 50% (Schwager et al., 2017), the high frequency oscillation might be beneficial in this case as well. In addition, based on the research findings of other ultrasonic-assisted grinding processes of other inorganic non-metallic materials, a material dependency of ultrasonic assisted drilling is to be expected, particularly with regard to the roughness that can be produced. Possible relevant materials for future investigations include N-BK7 optical glass, or Zerodur glass ceramic.
5 Conclusion
Investigations on two different kinematic approaches for grinding of deep bore holes with a high aspect ratio were carried out focussing on surface quality of the inner bore walls and dimensional accuracy. The helical kinematic approach is more versatile since different bore diameters can be produced with one tool diameter in contrast to deep drilling, where the tool diameter determines the resulting hole diameter. However, deep drilling enables lower roughness and better dimensional accuracy with the used parameters. For helical and deep drilling, an added ultrasonic tool oscillation has a different effect on the resulting roughness. For direct deep-hole drilling, rms roughness values Rq are on average around 17% better when grinding without ultrasonic, for helical drilling ultrasonic assistance does not show a significant trend on Rq. Regarding the dimensional accuracy in helical drilling ultrasonic tool oscillation has a strong effect. Here, the application of ultrasonic leads to a highly significant improvement for the helical drilling approach. Maximum diameter deviations can be reduced by over 91% compared to an identical grinding process without ultrasonic tool vibration. This result was not apparent in the literature so far. Also, the reproducibility of the drill diameters was strongly optimized by ultrasonic application in the presented experiments. The maximum deviations between identically grinded bores were reduced by over 94% with active ultrasonic. The addition of a high frequency grinding tool oscillation greatly enhances stability and reproducibility in the helical drilling process.
Data availability statement
The raw data supporting the conclusions of this article will be made available by the authors, without undue reservation.
Author contributions
SH: Investigation, Methodology, Writing–original draft, Writing–review and editing. MB: Investigation, Methodology, Writing–original draft. MK: Writing–original draft. JB: Project administration, Writing–review and editing. ER: Writing–review and editing.
Funding
The author(s) declare that financial support was received for the research, authorship, and/or publication of this article. The authors gratefully acknowledge financial support by the German Federal Ministry for Economic Affairs and Climate Action in the funding program ZIM (funding reference: ZF4039613TV8).
Conflict of interest
The authors declare that the research was conducted in the absence of any commercial or financial relationships that could be construed as a potential conflict of interest.
Generative AI statement
The author(s) declare that no Generative AI was used in the creation of this manuscript.
Publisher’s note
All claims expressed in this article are solely those of the authors and do not necessarily represent those of their affiliated organizations, or those of the publisher, the editors and the reviewers. Any product that may be evaluated in this article, or claim that may be made by its manufacturer, is not guaranteed or endorsed by the publisher.
References
Abdelkawy, A., and El-Hofy, H. (2021). Experimental and statistical study for measurements of surface roughness and hole geometry of ultrasonic-assisted drilling of soda glass. J. Braz. Soc. Mech. Sci. Eng. 43 (10), 449. doi:10.1007/s40430-021-03172-5
Alkhalefah, H. (2020). Precise drilling of holes in alumina ceramic (Al2O3) by rotary ultrasonic drilling and its parameter optimization using MOGA-II. Materials 13 (5), 1059. doi:10.3390/ma13051059
Anwar, S., Nasr, M. M., Pervaiz, S., Al-Ahmari, A., Alkahtani, M., and El-Tamimi, A. (2018). A study on the effect of main process parameters of rotary ultrasonic machining for drilling BK7 glass. Adv. Mech. Eng. 10 (1). doi:10.1177/1687814017752212
Bertsche, E., Ehmann, K., and Malukhin, K. (2013). An analytical model of rotary ultrasonic milling. Int. J. Adv. Manuf. Technol. 65, 1705–1720. doi:10.1007/s00170-012-4292-z
Binder, M., Henkel, S., Bliedtner, J., Fritzsche, M., Biegler, E., Tan, Ö., et al. (2024). Optimization of the surface quality of brittle-hard materials in CNC grinding processes based on vibration and topography analyses and the use of machine learning. Eleventh Eur. Seminar Precis. Opt. Manuf. 13221, 7. doi:10.1117/12.3031802
Bleicher, F., and Bernreiter, J. (2009). Mechatronic system for the hybrid-machining of brittle-hard materials. Ann. DAAAM 2009 & Proc. 20th Int. DAAAM Symposium 20 (1).
Bleicher, F., and Bernreiter, J. (2015). Hybridbearbeitung von SiC - Optimierung der spanenden Bearbeitung durch Ultraschall-Anregung. Vienna: Technische Universität Wien. Available at: https://publik.tuwien.ac.at/files/PubDat_188552.pdf.
Bliedtner, J. (2022). Optiktechnologie - Grundlagen – Verfahren – Anwendungen – Beispiele. München: Carl Hanser Verlag.
Choi, Y.-J., Park, K.-H., Hong, Y.-H., Kim, K.-T., Lee, S.-W., and Choi, H.-Z. (2013). Effect of ultrasonic vibration in grinding; horn design and experiment. Int. J. Precis. Eng. Manuf. 14 (11), 1873–1879. doi:10.1007/s12541-013-0253-1
Dell’Olio, F., Tatoli, T., Ciminelli, C., and Armenise, M. N. (2014). Recent advances in miniaturized optical gyroscopes. J. Eur. Opt. Society-Rapid Publ. 9, 14013i. doi:10.2971/jeos.2014.14013
Ding, K., Fu, Y., Su, H., Gong, X., and Wu, K. (2014). Wear of diamond grinding wheel in ultrasonic vibration-assisted grinding of silicon carbide. Int. J. Adv. Manuf. Technol. 71, 1929–1938. doi:10.1007/s00170-014-5625-x
Dong, G., and Zhang, L. (2019). Investigation on grinding force and machining quality during rotary ultrasonic grinding deep-small hole of fluorophlogopite ceramics. Int. J. Adv. Manuf. Technol. 104 (5-8), 2815–2825. doi:10.1007/s00170-019-04138-7
Geng, D., Zhang, D., Xu, Y., He, F., Liu, D., and Duan, Z. (2015). Rotary ultrasonic elliptical machining for side milling of CFRP: tool Performance and surface integrity. Ultrasonics 59, 128–137. doi:10.1016/j.ultras.2015.02.006
Jadoun, R. S., Kumar, P., and Mishra, B. K. (2009). Taguchi’s optimization of process parameters for production accuracy in ultrasonic drilling of engineering ceramics. Prod. Eng. 3 (3), 243–253. doi:10.1007/s11740-009-0164-2
Jianhua, Z., Yan, Z., Shuo, Z., Fuqiang, T., Lanshen, G., and Ruizhen, D. (2014). Study on effect of ultrasonic vibration on grinding force and surface quality in ultrasonic assisted micro end grinding of silica glass. Shock Vib. 2014, 1–10. doi:10.1155/2014/418059
Kumar, V., and Singh, H. (2019a). Investigation of hole quality in rotary ultrasonic drilling of borosilicate glass using RSM. J. Braz. Soc. Mech. Sci. Eng. 41, 36. doi:10.1007/s40430-018-1524-7
Kumar, V., and Singh, H. (2019b). Optimization of rotary ultrasonic drilling of optical glass using Taguchi method and utility approach. Eng. Sci. Technol. Int. J. 22 (3), 956–965. doi:10.1016/j.jestch.2019.02.004
Lauwers, B., Bleicher, F., Ten Haaf, P., Vanparys, M., Bernreiter, J., Jacobs, T., et al. (2010). “Investigation of the process-material interaction in ultrasonic assisted grinding of ZrO2 based ceramic materials,” in Proceedings of 4th international conference on high performance cutting.
Monro, T. M., and Ebendorff-Heidepriem, H. (2006). Progress in microstructured optical fibers. Annu. Rev. Mater. Res. 36 (1), 467–495. doi:10.1146/annurev.matsci.36.111904.135316
Nath, C., Lim, G. C., and Zheng, H. Y. (2012). Influence of the material removal mechanisms on hole integrity in ultrasonic machining of structural ceramics. Ultrasonics 52 (5), 605–613. doi:10.1016/j.ultras.2011.12.007
Park, K.-H., Hong, Y.-H., Kim, K.-T., Lee, S.-W., Choi, H.-Z., and Choi, Y.-J. (2014). Understanding of ultrasonic assisted machining with diamond grinding tool. Mod. Mech. Eng. 04, 1–7. doi:10.4236/mme.2014.41001
Passaro, V. M. N., Cuccovillo, A., Vaiani, L., De Carlo, M., and Campanella, C. E. (2017). Gyroscope technology and applications: a review in the industrial perspective. Sensors 17 (10), 2284. doi:10.3390/s17102284
Pflanz, C., and Ketelaer, J. (2023). Ultrasonic-assisted drilling of preforms for fibre optics. Tenth Eur. Seminar Precis. Opt. Manuf., 5. doi:10.1117/12.2676016
Schartner, E. P., Dowler, A., and Ebendorff-Heidepriem, H. (2017). Fabrication of low-loss, small-core exposed core microstructured optical fibers. Opt. Mater. Express 7 (5), 1496–1502. doi:10.1364/OME.7.001496
Schulze, C., Henkel, S., and Bliedtner, J. (2021). Experimental results from face and lateral fine grinding of fused silica and BK7 using metal and resin bonded tools. EPJ Web Conf. 255, 03002. doi:10.1051/epjconf/202125503002
Schwager, A. M., Bliedtner, J., Götze, K., Rädlein, E., Schulze, C., Gerhardt, M., et al. (2017). New surface smoothing technologies for manufacturing of complex shaped glass components. Optifab 2017 10448, 7. doi:10.1117/12.2277189
Sharma, A., Jain, V., and Gupta, D. (2018). Characterization of chipping and tool wear during drilling of float glass using rotary ultrasonic machining. Measurement 128, 254–263. doi:10.1016/j.measurement.2018.06.040
Singh, H., and Kumar, V. (2019). Parametric optimization in rotary ultrasonic drilling of BK7 through RSM based PSO. IOP Conf. Ser. Mater. Sci. Eng. 627 (1), 012005. doi:10.1088/1757-899X/627/1/012005
Singh, R. P., and Singhal, S. (2018). An experimental study on rotary ultrasonic machining of Macor ceramic. Proc. Institution Mech. Eng. Part B J. Eng. Manuf. 232 (7), 1221–1234. doi:10.1177/0954405416666897
Tawakoli, T., and Azarhoushang, B. (2008). Influence of ultrasonic vibrations on dry grinding of soft steel. Int. J. Mach. Tools Manuf. 48 (14), 1585–1591. doi:10.1016/j.ijmachtools.2008.05.010
Wang, J., Feng, P., Zhang, J., Zhang, C., and Pei, Z. (2016). Modeling the dependency of edge chipping size on the material properties and cutting force for rotary ultrasonic drilling of brittle materials. Int. J. Mach. Tools Manuf. 101, 18–27. doi:10.1016/j.ijmachtools.2015.10.005
Keywords: ultrasonic assisted grinding, drilling, glass, fused silica, diamond tools
Citation: Henkel S, Binder M, Knauf M, Bliedtner J and Rädlein E (2024) Influence of ultrasonic tool oscillation during drilling of fused silica. Adv. Opt. Technol. 13:1513056. doi: 10.3389/aot.2024.1513056
Received: 17 October 2024; Accepted: 02 December 2024;
Published: 17 December 2024.
Edited by:
Allen Yi, The Ohio State University, United StatesReviewed by:
David Piétroy, Université Jean Monnet, FranceGanesh Regmi, National Polytechnic Institute of Mexico (CINVESTAV), Mexico
Copyright © 2024 Henkel, Binder, Knauf, Bliedtner and Rädlein. This is an open-access article distributed under the terms of the Creative Commons Attribution License (CC BY). The use, distribution or reproduction in other forums is permitted, provided the original author(s) and the copyright owner(s) are credited and that the original publication in this journal is cited, in accordance with accepted academic practice. No use, distribution or reproduction is permitted which does not comply with these terms.
*Correspondence: Sebastian Henkel, c2ViYXN0aWFuLmhlbmtlbEBlYWgtamVuYS5kZQ==
†ORCID: Edda Rädlein, orcid.org/0000-0001-9205-9488