- 1Discipline of Civil Engineering, Monash University Malaysia, Subang Jaya, Malaysia
- 2Department of Civil Engineering, International University of Business Agriculture and Technology, Dhaka, Bangladesh
- 3Department of Civil Engineering, Stellenbosch University, Stellenbosch, South Africa
- 4Department of Civil Engineering, University of Asia Pacific, Dhaka, Bangladesh
- 5Microlab, Faculty of Civil Engineering and Geosciences, Delft University of Technology, Delft, Netherlands
Studies have shown that the incorporation of waste tire rubber aggregates reduces the strength, increases permeability and decrease thermal conductivity of concrete. However, only a few studies have investigated the effect of surface-modified rubber aggregates on the properties of concrete. This study investigates the effect of the surface treatment of waste tire rubber as coarse aggregates with different oxidizing solutions and different treatment durations on the mechanical, durability and thermal properties of concrete. The properties of concrete incorporated with 8% rubber coarse aggregates (by volume of natural aggregates) which were treated with three different solutions: water (H2O), 20% sodium hydroxide (NaOH) and 5% calcium hypochlorite [Ca(ClO)2] (both as% weight of water) for durations of 2, 24, and 72 h, respectively. The effect of these treatments on the compressive strength, splitting tensile strength, water permeability, thermal conductivity and diffusivity of concrete was investigated. Results show that Ca(ClO)2 has a more positive effect on the strength and permeability compared to NaOH solution and water. Experimental results were statistically analyzed using ANOVA and Post Hoc tests. The analyses showed that the improvement of concrete strength is only significant when the treatment with NaOH and Ca(ClO)2 is prolonged to 72 h. Furthermore, the microstructural analysis of concrete showed that the improvement in the strength is due to the improved bonding between cement paste and rubber aggregates as a result of surface treatment. This microstructural improvement also resulted in lower water permeability of concrete. However, the thermal conductivity and diffusivity increased when the surface treatment duration increases as there are less air voids in the samples. This study shows that, with appropriate pretreatment, a certain percentage of natural aggregates can be safely replaced with waste tire rubber aggregates while maintaining sufficient quality of the resulting concrete.
Introduction
Over the past few decades, the amount of waste tires generated globally has been increasing due to increasing population, leading to a rapid growth in automotive industry and use of vehicles. In general, rubber tires originate from motorcycles, automobiles, and trucks. Although to a certain extent these tires are suitable for recycling, most of them still end up in landfills. Huge amounts of waste tires are a cause of concern, as they are not bio-degradable, leading to their accumulation at landfills. Such landfills are a health and environmental hazard to surrounding communities. One of the possible solutions for disposal of waste tires is their use as (partial) replacement of natural aggregates in concrete production.
The processing of tire aggregates involves several steps such as mechanical system (making small pieces), cryogenic system (methods of cutting rubber in to tiny pieces), steel fiber removal stage, screening and milling stage and cleaning stage. In the cleaning stage, rubber particles are cleaned thoroughly with water and other cleaning agents such as ammonia solution, citric acid, etc. Depending on the application, three categories of rubber is used in concrete: are shredded or chipped tires (size 12–50 mm), ground rubber (0.425–2 mm) and granulated rubber (0.425–12 mm). In terms of chemical compositions, tire rubber granules contain more than 90% of styrene-butadiene rubber (SBR) and carbon black, together with small amount of Oxidize zinc and Sulfur (Jusli et al., 2014). The weight loss of rubber granule at different temperature was also investigated by Jusli et al. (2014) and it was found that at temperatures of 40–125°C, 325–435°C and 470–525°C, the weight loss was about 2, 35, and 55.3%, respectively. The specific weight and elongation of rubber can be up to 0.9–1.16 g/cm3 and 420%, respectively (Oikonomou and Mavridou, 2009; Bekhiti et al., 2014). The stiffness modulus of tire shred varies between 0.47 and 2.7 MPa and is dependent on the loading direction (Edeskär, 2006). The percentages of rubber aggregates used in cementitious materials also vary from as low as 5% to maximum 100% (Bideci et al., 2017; Haryanto et al., 2017).
Studies have shown that the incorporation of rubber tire aggregates into Portland cement concrete reduces the exploitation of natural aggregates and the negative impact caused by waste rubber tire disposed at the landfill. The benefits of rubber concrete include lower cost due to lower density, improvement in toughness and impact resistance (Reda Taha et al., 2008). Rubber tires are used in concrete in three forms: rubber aggregates as replacement of coarse aggregates, rubber crumbs as replacement of fine aggregates, and ground rubber as replacement of very fine aggregates (Shu and Huang, 2014).
Incorporation of rubber aggregates in concrete alters its properties. In general, concrete density decreases with increasing amount of rubber aggregates due to their low specific gravity compared to natural aggregates. For example, concrete with a density of 2000 kg/m3 can be achieved by replacing 45% of coarse aggregate with rubber aggregates (Topcu, 1995). The addition of rubber aggregates is also seen to decrease slump due to their irregular shape and jagged edges (Lv et al., 2015; Aslani et al., 2018). However, improved workability can be achieved if rubber aggregates are soaked in water for 24 h (Mohammadi et al., 2014).
Compressive and tensile strength of concrete also reduce as the amount of rubber aggregate increases due to their weak interfacial bond with the cement paste (Eldin and Senouci, 1994). In addition, the deformability of the rubber aggregates themselves compared to the surrounding cementitious matrix causes cracks to initiate in concrete under loading (Khatib and Bayomy, 1999). A study by Abdelmonem et al. (2019) showed a reduction of strength from 65 MPa to 35 MPa when 30% of rubber aggregates were used in high strength concrete. The study of Raffoul et al. (2016) showed that the strength further reduces as the particle size of recycled tire aggregates increases. Atahan and Yücel (2012) found that the static and dynamic modulus of elasticity reduce as the content of rubber aggregates increases. This reduction also depends on the size of the rubber aggregates. A 58% lower modulus of elasticity of concrete was measured when maximum 20 mm size of rubber aggregates was used. In the same concrete, this reduction was about 46% with 10 mm aggregates size (Haryanto et al., 2017). Nevertheless, a study by Vadivel et al. (2012) reported that the concrete specimens with 6% replacement of waste tire rubber aggregates can have similar compressive, tensile and flexural strength and follow the curvature of the conventional specimen in all the tests in M20 and M25 grades of concrete. It depicts that, based on concrete grade, an optimum amount of rubber aggregate can be used without sacrificing the concrete properties. It is worth mentioning that the mechanical properties of concrete can also vary under static and impact loading. Incorporation of waste tire aggregates in concrete can absorb significant energy and undergo relatively large deformations without full disintegration. This property can be utilized in various structural elements in which the deformation at peak load is a primary design concern (Vadivel et al., 2014).
Partial replacement of natural with waste tire aggregates is also seen to affect the transport properties of concrete. This is also explained by weak bond and a porous interfacial transition zone (Ganjian et al., 2009). Thermal conductivity of concrete was reduced by nearly 20% to 50% when the percentage replacement of coarse aggregates with rubber tire increased from 10 to 30%. Sukontasukkul (2009) reported that the conductivity to be in the range of 0.241 to 0.443 W/mK. A previous study of Aliabdo et al. (2015) showed that 100% replacement of fine aggregates by rubber reduced the thermal conductivity and sound insulation by 59 and 69%, respectively. Nevertheless, it is feasible to use higher volume of rubber aggregates in concrete for improved sound insulation. Replacement of rubber aggregates by 50 and 75% of natural aggregates in concrete enhanced the noise reduction effect by 58 and 68% compared with the reference concrete without rubber (Zhang and Poon, 2018).
As the strength reduction is commonly associate with the weak interfacial transition zone (ITZ), various treatments of rubber aggregates have been investigated: (1) washing and soaking with water; (2) treatment with sodium hydroxide (NaOH); (3) treatment with silane coupling agent (SCA); and (4) treatments with solvents such as acetone and ethanol. It was found that water washing provided a small improvement of less than 5% on the compressive strength of rubber concrete (Najim and Hall, 2013). Another study showed a significant increase of strength after soaking of rubber aggregates in water for 24 h (Mohammadi and Khabbaz, 2015). Other studies showed that treatment using NaOH increases the compressive strength (Su et al., 2015; Youssf et al., 2016). A treatment with SCA has shown to result in a more drastic increase in compressive strength of more than 6.5% (Su et al., 2015). In terms of solvents, acetone was found to be more effective than ethanol (Rivas-Vázquez et al., 2015). Other treatments investigated include UV and gamma radiation and heat treatment (Roychand et al., 2020). It must be emphasized that the improvement of compressive strength in is influenced also by factors other than the pretreatment, such as e.g., concrete mix design and the size of rubber aggregate particles.
Only a few studies have focused on the influence of surface treatment on the tensile strength, permeability, and thermal conductivity of concrete. The current study aims to investigate the influence of rubber surface treatment on the mechanical, transport, and thermal properties of concrete. In the concrete, 8% of natural aggregates by volume have been replaced with rubber aggregates pretreated with water (H2O), calcium hypochloride [Ca(ClO)2] and sodium hydroxide (NaOH) for different durations (2, 24, and 72 h). Calcium hypochloride has previously been successfully used to treat plastic waste aggregates (Lee et al., 2019), which was the reason for using it also in this study. Based on the hypothesis that the improvement of the mechanical properties is related to the improvement of the ITZ, this study focused on the influence of treatments and their durations on the resulting properties. Post Hoc Tukey-Kramer procedure was adopted after the analysis of variance (ANOVA) was performed at 1% significance level to check any significant difference between the means of the different concrete mix groups statistically. Finally, Scanning Electron Microscope (SEM) and microscopic images were also collected for rubberized concrete treated with H2O, NaOH and Ca(ClO)2 for 72 h to investigate the interfaces between the rubber and cement paste.
Experiments
Materials
The materials used in this study comprised of tap water, cement, sand, crushed rocks, and waste tire rubber aggregates. All mixtures used ordinary Portland cement (OPC) type I. Crushed rock as natural coarse aggregate had a maximum size of 12 mm and a specific gravity of 2.58, whereas, the sand had a fineness modulus of 2.98. The moisture content of crushed rocks, sand and rubber aggregates was 0.074, 1.38, and 0.78%, respectively, which was considered during the mix design process to adjust the water content. Waste truck tires provided by Yong Fong Rubber Industries SdnBhd, Malaysia, were used to make rubber aggregates with a maximum size of 15 mm (Figure 1). In general, rubber tires had relatively smooth surfaces, apart from the cutting surface which was rough. The flakiness index of rubber granules was found to be 64.3%. Grain size distribution of the aggregates was determined using sieve analysis in accordance with ASTM C136 (ASTM, 2006; Figure 2).
Concrete mix design was determined following the British method. In all mixes, the water to cement ratio (w/c) was 0.628 and no superplasticizer was added. If the water to cement ratio is corrected to take into account the water absorption capacity of the aggregates, the w/c ratio is 0.6. The mix design of the control sample was aimed to achieve a compressive strength of 40 MPa at 28 days with a slump value in a range between 80 and 120 mm. For the rubberized concrete, the target strength was more than 30 MPa. In this regard, initially, five concrete mix designs were prepared, and these were conventional concrete without rubber (REF) and concrete made with rubber aggregates replacing natural coarse aggregates at 8, 10, 20, and 30% as named R8, R10, R20, and R30, respectively (Table 1). Therefore, only the concrete made with 8% rubber aggregate was considered for the effect of different treatment methods. Therefore, 14 concrete mixes were prepared for the investigation of treatment methods due to variation in treatment durations and agents. The notation RX-(N or C or W) Y is used, where X is the rubber content in percent; N, C and W stands for sodium hydroxide, calcium hypochlorite and water, respectively; Y is the treatment duration in hours. For example, 8% rubber content treated in NaOH for 2 h is represented by R8-N2h.
Sample Preparation and Testing Methods
Solutions for the pretreatments −20% NaOH by weight of water (wt/w) and 5% wt/w of Ca(ClO)2 – were prepared. Before concrete mixing, the rubber tire aggregates were soaked in those solutions for 2, 24 or 72 h. The rubber aggregates were then rinsed with tap water and kept under the ambient conditions for 24 h until the saturated surface dry (SSD) condition was achieved.
Cubic specimens with a size of 100 mm × 100 mm × 100 mm were prepared for compressive strength, splitting tensile strength and thermal conductivity tests. For water permeability tests, cubes of 150 mm × 150 mm × 150 mm were prepared. After mixing, slump was measured per BS EN 12350-2:2009 (BSI, 2009). Cast specimens were covered with plastic sheets for 24 h to prevent evaporation and minimize early age shrinkage. After 24 h, specimens were demolded and kept in a curing tank until testing at 7 and 28 days.
For hardened concrete, compressive and splitting tensile strength were tested in accordance with (BSI, 2000) and (SABS, 2006), respectively. The loading rate of the compression machine was set at 2500N/s. Concrete permeability was determined using water permeability testing in accordance with BS EN 12390-8 (BSI, 2000), Figure 3A. For this purpose, 150 mm3 concrete cube was used. The test was performed on the cube samples after 28 days of curing. As shown in Figure 3A, around 500 kPa water pressure is applied to the surface of the sample for about 72 h. The samples were split into 2 parts (by means of splitting test) immediately after the testing to determine the depth of water penetration. Thermal conductivity and diffusivity of concrete samples were also tested using C-Therm TCkit by sandwiching the transient plane source sensor between two concrete cube samples. The thermal conductivity test is illustrated in Figure 3B. The magnitude of thermal conductivity and diffusivity was automatically generated by the software when the apparatus applies an electric current to the sensor and the rise in temperature is analyzed by the software.
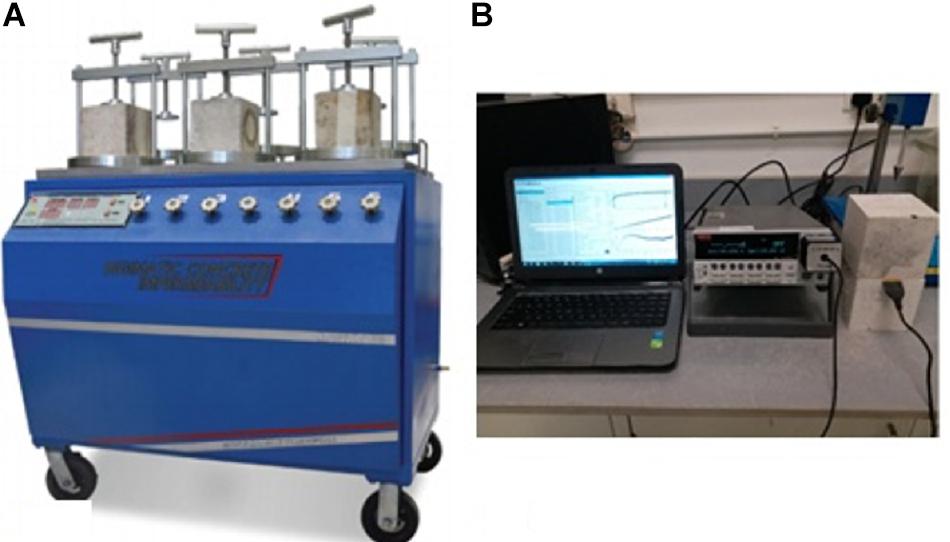
Figure 3. (A) Digimatic concrete water permeability apparatus and (B) thermal conductivity test using C-THERM TCkit.
The microstructure of rubberized concrete specimens was evaluated using scanning electron microscopy (SEM) and digital microscopy. Three samples were tested to compare the gap between the treated rubber aggregates (using H2O, NaOH, and Ca(ClO)2 for 72 h) and the cementitious matrix. For SEM images, backscattered electron mode, an accelerating voltage of 15 kV with a magnification of 20.000 was set for all three samples. The brand of digital microscope was “Dino-Lite,” and the magnification was set to 1000x with a unit of μm. For both SEM and microscope images, samples were prepared by cutting the cube concrete samples.
Results and Discussion
Optimum Percentage of Rubber Replacement
Before studying the effect of aggregate treatment, the optimal percentage of replacement of coarse aggregates by rubber aggregates was first determined. Compressive strength values after 7 and 28 days are shown in Figure 4. These results are in accordance with a previous study of Abdelmonem et al. (2019), which showed a decreasing compressive strength with an increasing rubber aggregate content. As shown in Figure 4, the 28-day compressive strength of concrete reduces by 25% when 10% of coarse aggregate is replaced with rubber aggregate. For 20 and 30% replacements, the reduction of compressive strength was 56 and 62%, respectively. Therefore, it was decided that the optimal replacement percentage of coarse aggregates with rubber aggregates was around 8%, which resulted in 17% lower compressive strength compared to the reference mix. As mentioned before, this drastic drop of compressive strength is commonly attributed to the poor adhesion of cement paste on the rubber aggregate surface due to the hydrophobic nature of tire rubber (Eldin and Senouci, 1994). In addition, larger size of rubber aggregates compared to natural aggregates (maximum size is 15 mm for rubber and 12 mm for natural aggregates, Figure 2) could lead to more voids in the concrete mix, resulting in lower compressive strength. The increased air content in concrete as a result of increased percentages of rubber aggregates has already been reported (Skripkiūnas et al., 2010; Zimmermann et al., 2016). The presence of higher air content in rubber concrete used in this study can also be seen from the water penetration test result in section “Water Permeability”.
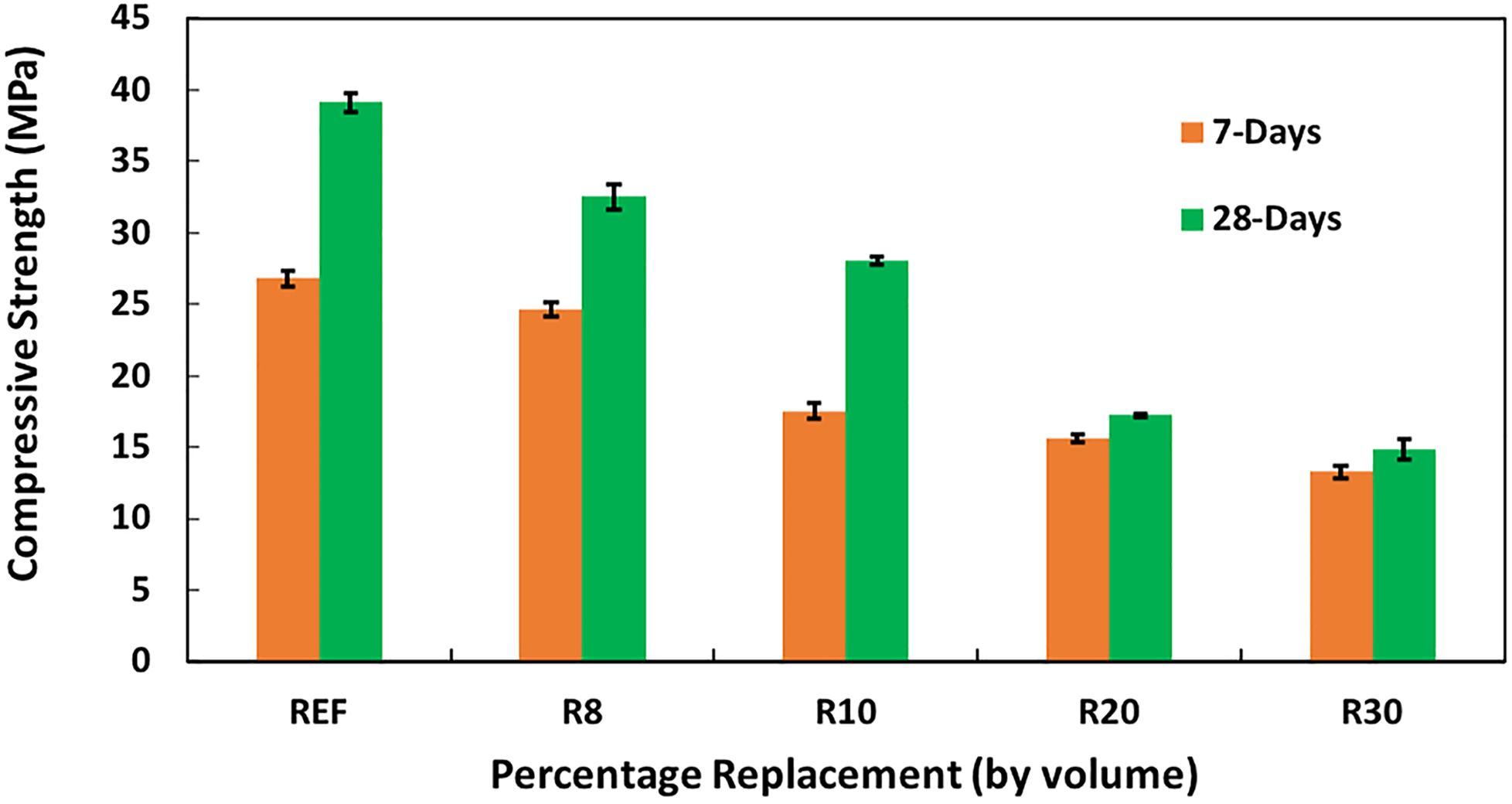
Figure 4. 7- and 28-days compressive strength of trial concrete mix with made different rubber content.
Dry density of all mixtures was also determined using the water displacement method. It was shown that concrete density reduced gradually with the increasing replacement of coarse aggregates with rubber aggregates. The average density of natural coarse aggregates and rubber aggregates concretes were found to be 2581 kg/m3 for reference concrete and 2140 kg/m3 for 30% rubber concrete.
Concrete Workability
Figure 5 shows slump values of the reference mixture and all mixtures with 8% rubber aggregates with different treatments and durations. Slump of the reference mixture was measured to be 98 mm, which was set as the desired slump in the beginning of the study. Incorporation of 8% of untreated rubber aggregates caused a decrease of slump to 87 mm, a decrease of around 11%. In addition, pretreatment with water does not cause any noticeable change in the slump. On the contrary, slump reduced when rubber aggregates were treated with chemicals, i.e., NaOH and Ca(ClO)2.
The decrease of slump when natural coarse aggregates are partially replaced with rubber aggregates can be attributed to the shape of rubber aggregate particles. These particles are flaky or flat-surfaced, as shown in Figure 1. Angular rubber aggregates have a higher surface area compared to crushed rock aggregated, thereby increasing friction and reducing interparticle movement. The slump further decreased when the rubber was treated with NaOH and Ca(ClO)2 because when rubber is treated, the cement paste can adhere stronger to the surface of rubber aggregates and the cohesiveness is enhanced, thus absorbing water from the cement mortar and reduce the overall workability. Another reason for slump reduction can be the fact that the NaOH and Ca(ClO)2 impact cement hydration and affect the yield strength and plastic viscosity of the cement paste itself.
Compressive Strength
Compressive strength at 7 and 28 days is shown in Figure 6. At 7 days (Figure 6A), untreated rubber aggregate concrete (R8) showed around 8% lower compressive strength compared to the reference concrete (REF). However, when rubber aggregates were pretreated, the compressive strength of concrete for R8-W2h, R8-W24h and R8-W72h were 5.15, 5.86, and 5.11% lower than that of REF concrete, respectively. For the rubber aggregates treated with NaOH, the compressive strength of concrete for R8-N2h, R8-N24h and R8-N72h were 4.74, 5.37, and 5.07% lower compared to the REF concrete, respectively. Similarly, when the rubber aggregates were treated with Ca(ClO)2, the compressive strength of concrete for R8-C2h, R8-C24h, and R8-C72h were 5% lower, 1.87% lower and 2.91% higher, respectively, than that of REF concrete.
Compressive strength results at 28 days are shown in Figure 6B. At 28 days, compressive strength for R8 was 16.82% lower than that of REF concrete. When the rubber aggregates were treated with water, the compressive strength of concrete was 14.34, 15.37, and 14.6% lower for R8-W2h, R8-W24h, and R8-W72h, respectively, than that of REF concrete. On the other hand, when rubber aggregates were treated with NaOH, the compressive strength was 15.11, 12.43, and 9.74% lower for R8-N2h, R8-N24h, and R8-N72h, respectively, compared to the REF concrete. Finally, when rubber aggregates were treated with Ca(ClO)2, the compressive strength was 14.78, 11.02, and 3.4% lower for R8-C2h, R8-C24h, and R8-C72h, respectively, compared to the REF concrete.
The observed improvement of compressive strength as a result of the surface treatment of rubber aggregates is in accordance with previously reported findings (Albano et al., 2005). However, the improvement of compressive strength was relatively minor, as also reported previously (Su et al., 2015).
Compressive strength of concrete is, to a large extent, governed by the bonding between the aggregates and the cement paste (Van Mier, 2017). While the hydrated cement paste phase is reported to have quite high compressive strength (Zhang et al., 2019), the interfacial transition zone is, in general, the weakest link in the cementitious composite (Scrivener et al., 2004; Zhang et al., 2019). As stated previously, the low compressive strength of concrete with waste tire rubber aggregates is partially attributed to their weak bond with the cement paste, caused by their hydrophobic nature. Treatment of rubber particles with NaOH improves this bond because this chemical treatment forms a hydrophilic group and an oxygen-containing hydroxyl OH group on the surface of rubber particles. This may increase the Van der Waals interaction energy or Hamaker constant, thereby reducing the hydrophobic characteristic of rubber aggregates (Chou et al., 2007). Similarly, Ca(ClO)2 treatment produces R-OH and R-COOH to the species to the polymeric chain of rubber aggregates, which is much more reactive than polymeric hydrocarbon of existing rubber aggregates (Naik et al., 1996). It has also been reported that strength improves when rubber aggregates are pretreated because of the formation of a hard shell around the rubber particles as a result of cement hydration, which increases the compatibility in terms of stiffness between the rubber and the cement paste (Huang et al., 2013).
Experimental results were also analyzed using statistical tools. Two methods – ANOVA and Post Hoc testing – were used to analyze the average results of compressive strength measurements of concretes with 8% aggregates at 7 and 28 days. Statistical methods were used to determine which treatment has the highest effectiveness in modifying the rubber particles so that the compressive strength is improved. In general, ANOVA F-test analysis only shows if one or more of the means are significantly different from each other, but it does not show the significant difference which lies within each group. Therefore, Post Hoc Tukey-Kramer procedure was adopted after performing ANOVA to identify which of the means are significantly different. The significance level set for the analysis was 1%. The 1% significance level indicates that there is a 99% probability (null hypothesis) that the means within the group do not have any significant difference. Therefore, when the null hypothesis is rejected under 1% significant analysis, indicating an obvious significant difference in means of the groups.
For 7 and 28-day compressive strength results, the Fcritical values were determined to be 3.46 for both cases. However, based on the ANOVA analysis at a 99% confidence level, Fcalculated were determined to be 5.08 and 5.941 for 7- and 28-days compressive strength results, respectively, which fall beyond the Fcritical point of 3.46. Thus, the null hypothesis can be rejected since it is inside the rejection zone. Therefore, it was proven that there is a significant difference between the means of the group.
Post Hoc Tukey-Kramer was then performed, and the results are given in Table 2. The critical range for the Tukey-Kramer procedure was determined to be 2.06 and 3.91 for 7- and 28-days results, respectively. If the absolute difference exceeds the critical value, it indicates that there is a significant difference between means of the group. Results showed that for both 7- and 28-days compressive strength of concrete, only R8-N24h, R8-N72h, R8-C24h and R8-C72h showed a significant increment in compressive strength. Rubber aggregates treated with Ca(ClO)2 for 72 h showed the optimum result as indicated by the highest absolute difference and the compressive strength, as shown in Figure 6B. Post Hoc test also showed that only 72 h of treatment produces a significant difference between means of the group for Ca(ClO)2. Treatment with NaOH does not give significant results even for 72 h of treatment duration. Even in compressive strength result comparison with REF, it was found that 72 h of treatment with NaOH showed about 10% lower strength, where this was only 3% for Ca(ClO)2. Therefore, the most effective treatment agent determined from this study is Ca(ClO)2 and the optimum treatment duration is found to be 72 h.
In terms of chemistry, when sulfur from rubber particles reacts with NaOH, it produces sodium sulfate, sodium sulfide, and water. The addition of sodium sulfate to high-alkali-cements may accelerate cement hydration and contributes to the higher strength of concrete (Kim et al., 2000; Sancak and Özkan, 2015). Ca(ClO)2 contains a higher amount of chlorine. In the past, chlorine (in the form of e.g., CaCl2) has been added to concrete as an accelerating agent. In addition, a new hydration product of calcium aluminate chloride hydrate, also known as Friedel’s salt (3CaO⋅Al2O3⋅CaCl2⋅10H2O), could form in the concrete made with rubber tire aggregates treated with Ca(ClO)2. Friedel’s salt has a plate-like crystal morphology, and its solid-phase volume expands by 75.5% during formation of the hydrate (Cheng et al., 2017). This volumetric expansion of Friedel’s salt could fill up the pores in the microstructure, densifying it and increasing the strength of the concrete. A similar mechanism is at play during carbonation of Portland cement paste (Šavija and Luković, 2016). However, chloride ions can be the cause of steel corrosion in reinforced concrete, which is highly detrimental (Bertolini et al., 2013). Therefore, more research is needed related to this mechanism before concrete with treated rubber aggregates is used in reinforced concrete structures.
Splitting Tensile Strength
Splitting tensile strength of various concrete mixtures, tested at 28 days, is shown in Figure 7. Reference concrete (REF) had an average splitting tensile strength of around 3.32 MPa. When 8% of untreated rubber aggregates were incorporated, the splitting tensile strength was reduced by 32.14%. When rubber aggregates were treated with water, the splitting tensile strengths of R8-W2h, R8-W24h, R8-W72h were 31.14, 29.97, and 29.67% lower than the REF concrete, respectively. When NaOH treatment is applied, the splitting tensile strength of R8-N2h, R8-N24h, R8-N72h were 26.14, 24.61, and 18.98% lower than that of REF concrete, respectively. When Ca(ClO)2 treatment is performed, the splitting tensile strength of R8-C2h, R8-C24h, R8-C72h were 25.66, 21.02, and 13.58% lower than that of REF concrete, respectively. From these results it can be postulated that the most effective treatment is Ca(ClO)2 in terms of improvement of splitting tensile strength of concrete.
Water Permeability
The water penetration test was performed to investigate the permeability of concrete mixtures in this study. Maximum penetration depth and the water penetration rate into the concrete specimens are given in Table 3. It can be observed that, when 8% of untreated rubber aggregates are incorporated in concrete, the water penetration depth is 32.3% higher than the reference (i.e., REF) concrete. This is in accordance with existing literature (Ganjian et al., 2009). Treatment of rubber aggregates with water does not improve the transport properties of the concrete, as the penetration depths are comparable to those of concrete containing untreated aggregates. NaOH treatment does improve resistance to water ingress, as the water penetration depths of R8-N2h, R8-N24h and R8-N72h were 12.2, 19.5, and 26.8% lower than that of R8 concrete, respectively. Similarly, Ca(ClO)2 treatment results in lower water penetration depth: the values were 17.1, 26.8, and 41.5% lower compared to R8 concrete for R8-C2h, R8-C24h, and R8-C72h, respectively. It is worth noting that the permeability of R8-C72h was even lower than the REF concrete, by 22.6%. Similar results were reported previously by Su et al. (2015). All mixtures in this study can be classified as having medium-range permeability according to DIN 1048, except mixture R8-C72h, which has a low-range permeability.
Results show that treating rubber aggregates with Ca(ClO)2 is the most efficient way to reduce the permeability of concrete mixtures. Furthermore, the longest treatment duration (72 h) showed the best results. While treating the aggregates with NaOH also resulted in reduced permeability, the improvement was significantly lower than treating with Ca(ClO)2. This reduction can also be attributed to improved rubber aggregate/paste bonding, which results in a lower porosity of the ITZ. Since ITZ is known to have a profound effect on transport properties of concrete (Delagrave et al., 1997; Šavija et al., 2014), this improvement resulted in lower water permeability.
Thermal Conductivity and Diffusivity
Thermal conductivity and diffusivity of all mixtures is reported in Table 4. It can be seen that, when 8% of untreated rubber aggregates are incorporated in concrete, the thermal conductivity reduces by 7.34% compared to the reference (REF) mixture. Similar results have already been reported: (Aliabdo et al., 2015) found that replacing 20% of sand with rubber particles causes thermal conductivity to decrease by 34%. When rubber aggregates were treated with water, the thermal conductivity decreased by a maximum of 8% compared to reference (REF) concrete. Chemical treatment of rubber aggregates caused an increase in thermal conductivity of resulting concretes. This increase was most significant for the longest treatments (i.e., 72 h). For R8-C72h, the thermal conductivity of rubberized concrete increased by 9.58% compared to R8 concrete. A similar trend was observed for thermal diffusivity of concrete. Therefore, it can be stated that surface treatment of rubber aggregates with NaOH and Ca(ClO)2 can increase the thermal conductivity of concrete.
On the other hand, a drop of thermal conductivity when untreated rubber aggregates are incorporated could be caused by additional entrapped air and larger voids which are present due to larger particle size of rubber aggregates compared to the natural aggregates they replace (maximum size: 15 mm for rubber and 12 mm for natural aggregates, see Figure 2). However, in treated conditions, interfacial transition zone is improved, resulting in lower overall air void content and increased thermal conductivity.
Microstructural Analysis
For microstructural analyses, SEM and digital microscopic images were obtained for concretes containing rubber aggregates treated for 72 h with water, NaOH and Ca(ClO)2 (Figure 8). Images of interfacial areas were taken. Distinct grooves were observed at the ITZ with a gap width of approximately 7 μm when rubber aggregates were treated with water. The width of this gap reduced to 2.4–3 μm when rubber aggregate particles were treated with NaOH for 72 h. When Ca(ClO)2 treatment is applied for 72 h, no gaps were observed at the interface. This can be attributed to better aggregate/matrix bonding induced by the rough tire surface and lower porosity caused by possible formation of Friedel’s salt. This is in accordance with strength results, which showed that the drop in strength observed for untreated rubber particles has been almost completely negated when aggregates were treated with Ca(ClO)2 for 72 h.
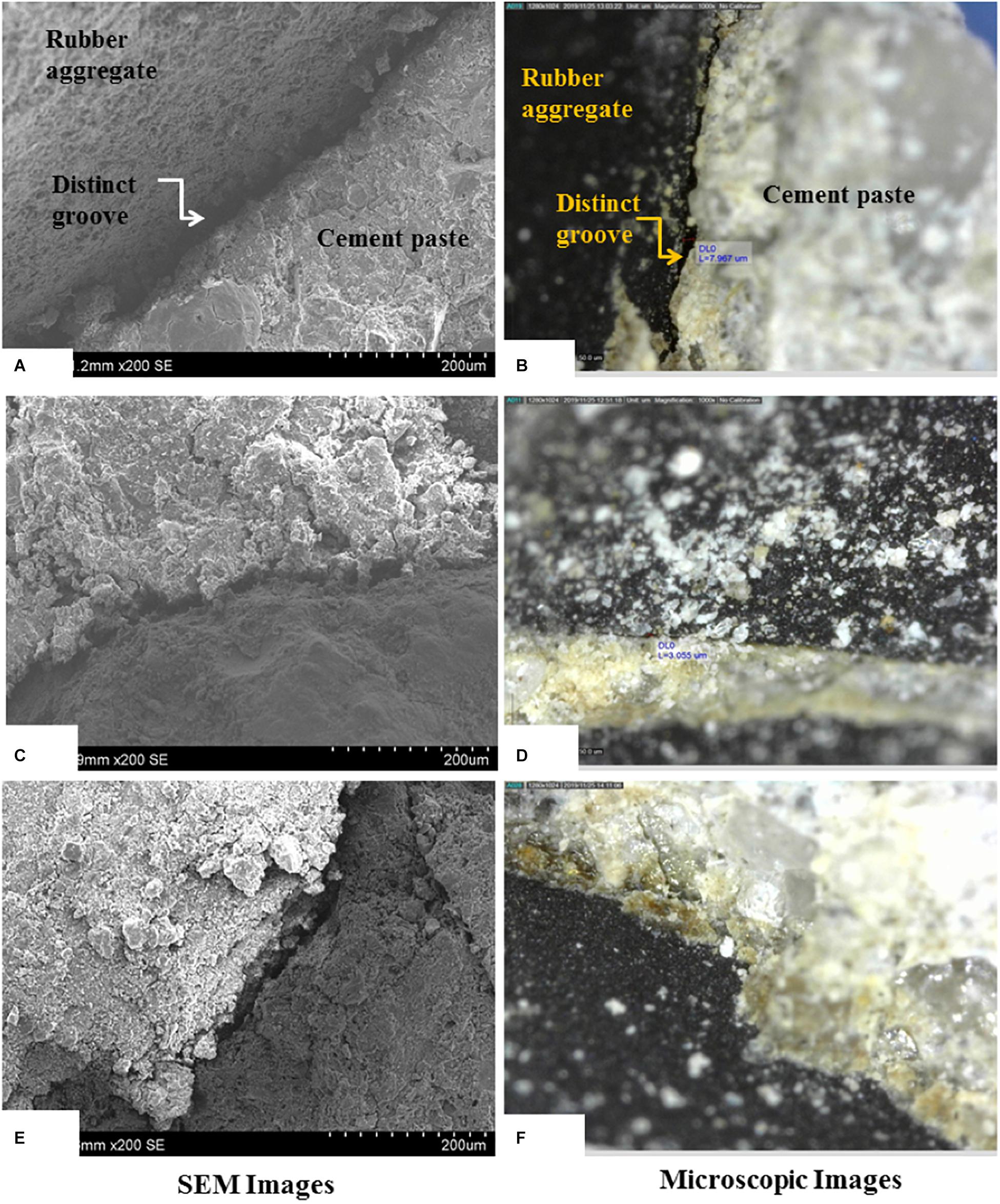
Figure 8. SEM and microscopic images of concrete made with rubber aggregates treated for 72 h in (A,B) water, (C,D) NaOH, and (E,F) Ca(ClO)2.
Conclusion
In this work, the influence of chemical treatment of rubber aggregates using sodium hydroxide solution (NaOH) and calcium hypochlorite solution [Ca(ClO)2] on fresh, mechanical, and transport properties of concrete have been studied. A constant amount of rubber aggregates – 8% replacement – was used in all mixtures. Based on the presented results, the following conclusions can be drawn:
• In terms of fresh properties, it has been found that replacing 8% of natural aggregate with rubber particles reduces the slump due to higher friction between rubber aggregates. Treatments with NaOH and Ca(ClO)2 did not cause any noticeable difference in terms of slump.
• Replacing 8% of natural aggregates with tire rubber resulted in 18% lower compressive strength at 28 days compared to the reference mixture. On the other hand, when tire rubber aggregates were treated with NaOH and Ca(ClO)2 resulted in lower reduction of compressive strength: compared to the reference, concrete containing rubber aggregates treated by Ca(ClO)2 for 72 h resulted in strength similar to the reference concrete. Similar trend was observed for splitting tensile strength.
• Water penetration depth has been significantly reduced if the rubber aggregates have been treated compared to untreated rubber aggregates. Furthermore, some of the treatments resulted in lower water penetration depth compared to the reference concrete.
• Treatment of aggregates with NaCl and Ca(ClO)2 solutions resulted in an increase in thermal conductivity by 1.66 and 9%, respectively, compared to concrete with untreated aggregates. This may be caused by better bonding of treated aggregates with cement paste, which caused a reduction of air voids in the concrete and therefore higher thermal conductivity.
• In general, it was found that pretreatment with Ca(ClO)2 solution is more effective compared to NaOH and water. Statistical analyses also showed that the treatment must be prolonged for 72 h if significant improvements are sought after.
While the results reported herein are certainly promising, it is clear that more research is needed. First, only a single replacement percentage (8%) was studied. If more rubber aggregates are to be used, it is possible that an even more prolonged treatment duration would be needed. Furthermore, although Ca(ClO)2 treatment has shown to be promising, the actual mechanism behind it is still not completely understood. Fundamental understanding of the process is important if pretreatment procedures are to be upscaled and used industrially in concrete production.
Data Availability Statement
The datasets generated for this study are available on request to the corresponding author.
Author Contributions
YK: methodology, investigation, writing original draft, and visualization. SP and SK: supervision, methodology, and writing original draft. AB, VA, MM, and BŠ: writing, review, and editing.
Conflict of Interest
The authors declare that the research was conducted in the absence of any commercial or financial relationships that could be construed as a potential conflict of interest.
Acknowledgments
The authors are thankful to the Monash University Malaysia and Dr. Mavinakere Eshwaraiah. The APC fee has been paid by the TU Delft Open Access fund.
References
Abdelmonem, A., El-Feky, M., Nasr, E.-S. A., and Kohail, M. (2019). Performance of high strength concrete containing recycled rubber. Constr. Build. Mater. 227:116660. doi: 10.1016/j.conbuildmat.2019.08.041
Albano, C., Camacho, N., Reyes, J., Feliu, J., and Hernández, M. (2005). Influence of scrap rubber addition to Portland I concrete composites: destructive and non-destructive testing. Compos. Struct. 71, 439–446. doi: 10.1016/j.compstruct.2005.09.037
Aliabdo, A. A., Elmoaty, A. E. M. A., and AbdElbaset, M. M. (2015). Utilization of waste rubber in non-structural applications. Constr. Build. Mater. 91, 195–207. doi: 10.1016/j.conbuildmat.2015.05.080
Aslani, F., Ma, G., Wan, D. L. Y., and Le, V. X. T. (2018). Experimental investigation into rubber granules and their effects on the fresh and hardened properties of self-compacting concrete. J. Clean. Prod. 172, 1835–1847. doi: 10.1016/j.jclepro.2017.12.003
ASTM (2006). Standard Test Method for Sieve Analysis of Fine and Coarse Aggregates. West Conshohocken, PA: ASTM International.
Atahan, A. O., and Yücel, A. Ö (2012). Crumb rubber in concrete: static and dynamic evaluation. Constr. Build. Mater. 36, 617–622. doi: 10.1016/j.conbuildmat.2012.04.068
Bekhiti, M., Trouzine, H., and Asroun, A. (2014). Properties of waste tire rubber powder. Eng. Technol. Appl. Sci. Res. 4, 669–672.
Bertolini, L., Elsener, B., Pedeferri, P., Redaelli, E., and Polder, R. (2013). Corrosion of Steel in Concrete. Hoboken, NJ: Wiley Online Library.
Bideci, ÖS., Saka, R. C., and Bideci, A. (2017). Physical characteristics of rubberized concrete including granulated waste tire aggregate. Politeknik Dergisi 20, 777–786. doi: 10.2339/politeknik.368985
Cheng, Y., Li, Z.-g, Huang, X., and Bai, X.-h (2017). Effect of Friedel’s salt on strength enhancement of stabilized chloride saline soil. J. Cent. S. Univ. 24, 937–946. doi: 10.1007/s11771-017-3496-7
Chou, L. H., Lu, C.-K., Chang, J.-R., and Lee, M. T. (2007). Use of waste rubber as concrete additive. Waste Manag. Res. 25, 68–76. doi: 10.1177/0734242x07067448
Delagrave, A., Bigas, J., Ollivier, J., Marchand, J., and Pigeon, M. (1997). Influence of the interfacial zone on the chloride diffusivity of mortars. Adv. Cem. Based Mater. 5, 86–92. doi: 10.1016/s1065-7355(96)00008-9
Edeskär, T. (2006). Use of Tyre Shreds in Civil Engineering Applications: Technical and Environmental Properties. Luleå: Luleå tekniska universitet.
Eldin, N. N., and Senouci, A. B. (1994). Measurement and prediction of the strength of rubberized concrete. Cem. Concr. Compos. 16, 287–298. doi: 10.1016/0958-9465(94)90041-8
Ganjian, E., Khorami, M., and Maghsoudi, A. A. (2009). Scrap-tyre-rubber replacement for aggregate and filler in concrete. Constr. Build. Mater. 23, 1828–1836. doi: 10.1016/j.conbuildmat.2008.09.020
Haryanto, Y., Hermanto, N., Pamudji, G., and Wardana, K. (2017). “Compressive strength and modulus of elasticity of concrete with cubed waste tire rubbers as coarse aggregates,” in Proceedings of the IOP Conference Series: Materials Science and Engineering (Surabaya: IOP Publishing).
Huang, B., Shu, X., and Cao, J. (2013). A two-staged surface treatment to improve properties of rubber modified cement composites. Constr. Build. Mater. 40, 270–274. doi: 10.1016/j.conbuildmat.2012.11.014
Jusli, E., Nor, H. M., Jaya, R. P., and Zaiton, H. (2014). Chemical properties of waste tyre rubber granules. Adv. Mater. Res. 91, 77–81. doi: 10.4028/www.scientific.net/amr.911.77
Khatib, Z. K., and Bayomy, F. M. (1999). Rubberized portland cement concrete. J. Mater. Civil Eng. 11, 206–213.
Kim, B.-G., Jiang, S., and Aiitcin, P.-C. (2000). Effect of sodium sulfate addition on properties of cement pastes containing different molecular weight PNS superplasticizers. Spec. Publ. 195, 485–504.
Lee, Z. H., Paul, S. C., Kong, S. Y., Susilawati, S., and Yang, X. (2019). Modification of waste aggregate PET for improving the concrete properties. Adv. Civil Eng. 2019:6942052.
Lv, J., Zhou, T., Du, Q., and Wu, H. (2015). Effects of rubber particles on mechanical properties of lightweight aggregate concrete. Constr. Build. Mater. 91, 145–149. doi: 10.1016/j.conbuildmat.2015.05.038
Mohammadi, I., and Khabbaz, H. (2015). Shrinkage performance of crumb rubber concrete (CRC) prepared by water-soaking treatment method for rigid pavements. Cem. Concr. Compos. 62, 106–116. doi: 10.1016/j.cemconcomp.2015.02.010
Mohammadi, I., Khabbaz, H., and Vessalas, K. (2014). In-depth assessment of crumb rubber concrete (CRC) prepared by water-soaking treatment method for rigid pavements. Constr. Build. Mater. 71, 456–471. doi: 10.1016/j.conbuildmat.2014.08.085
Naik, T. R., Singh, S. S., Huber, C. O., and Brodersen, B. S. (1996). Use of post-consumer waste plastics in cement-based composites. Cem. Concr. Res. 26, 1489–1492. doi: 10.1016/0008-8846(96)00135-4
Najim, K. B., and Hall, M. R. (2013). Crumb rubber aggregate coatings/pre-treatments and their effects on interfacial bonding, air entrapment and fracture toughness in self-compacting rubberised concrete (SCRC). Mater. Struct. 46, 2029–2043. doi: 10.1617/s11527-013-0034-4
Oikonomou, N., and Mavridou, S. (2009). “The use of waste tyre rubber in civil engineering works,” in Sustainability of Construction Materials, ed. J. Khatib (Cambridge: Wood Head Publishing Limited), 213–238. doi: 10.1533/9781845695842.213
Raffoul, S., Garcia, R., Pilakoutas, K., Guadagnini, M., and Medina, N. F. (2016). Optimisation of rubberised concrete with high rubber content: an experimental investigation. Constr. Build. Mater. 124, 391–404. doi: 10.1016/j.conbuildmat.2016.07.054
Reda Taha, M. M., El-Dieb, A. S., Abd El-Wahab, M., and Abdel-Hameed, M. (2008). Mechanical, fracture, and microstructural investigations of rubber concrete. J. Mater. Civil Eng. 20, 640–649. doi: 10.1061/(asce)0899-1561(2008)20:10(640)
Rivas-Vázquez, L., Suárez-Orduña, R., Hernández-Torres, J., and Aquino-Bolaños, E. (2015). Effect of the surface treatment of recycled rubber on the mechanical strength of composite concrete/rubber. Mater. Struct. 48, 2809–2814. doi: 10.1617/s11527-014-0355-y
Roychand, R., Gravina, R. J., Zhuge, Y., Ma, X., Youssf, O., and Mills, J. E. (2020). A comprehensive review on the mechanical properties of waste tire rubber concrete. Constr. Build. Mater. 237:117651. doi: 10.1016/j.conbuildmat.2019.117651
SABS (2006). Concrete Tests — Tensile Splitting strEngth of Concrete SANS 6253:2006. Pretoria: South African National Standard.
Sancak, E., and Özkan, Ş (2015). Sodium sulphate effect on cement produced with building stone waste. J. Mater. 2015:813515.
Šavija, B., and Luković, M. (2016). Carbonation of cement paste: understanding, challenges, and opportunities. Constr. Build. Mater. 117, 285–301. doi: 10.1016/j.conbuildmat.2016.04.138
Šavija, B., Luković, M., and Schlangen, E. (2014). Lattice modeling of rapid chloride migration in concrete. Cem. Concr. Res. 61, 49–63. doi: 10.1016/j.cemconres.2014.04.004
Scrivener, K. L., Crumbie, A. K., and Laugesen, P. (2004). The interfacial transition zone (ITZ) between cement paste and aggregate in concrete. Interf. Sci. 12, 411–421. doi: 10.1023/b:ints.0000042339.92990.4c
Shu, X., and Huang, B. (2014). Recycling of waste tire rubber in asphalt and portland cement concrete: an overview. Constr. Build. Mater. 67, 217–224. doi: 10.1016/j.conbuildmat.2013.11.027
Skripkiūnas, G., Grinys, A., and Janavičius, E. (2010). “Porosity and durability of rubberized concrete,” in Proceedings of the 2nd International Conference on Sustainable Construction Materials and Technologies, Ancona, 28–30.
Su, H., Yang, J., Ghataora, G. S., and Dirar, S. (2015). Surface modified used rubber tyre aggregates: effect on recycled concrete performance. Mag. Concr. Res. 67, 680–691. doi: 10.1680/macr.14.00255
Sukontasukkul, P. (2009). Use of crumb rubber to improve thermal and sound properties of pre-cast concrete panel. Constr. Build. Mater. 23, 1084–1092. doi: 10.1016/j.conbuildmat.2008.05.021
Topcu, I. B. (1995). The properties of rubberized concretes. Cem. Concr. Res. 25, 304–310. doi: 10.1016/j.wasman.2008.01.015
Vadivel, T. S., Thenmozhi, R., and Doddurani, M. (2012). Experimental study on waste tyre rubber reinforced concrete. J. Struct. Eng. 39, 291–299.
Vadivel, T. S., Thenmozhi, R., and Doddurani, M. (2014). Experimental behaviour of waste tyre rubber aggregate concrete under impact loading. Iran. J. Sci. Technol. Trans. Civil Eng. 38, 251–259.
Youssf, O., Mills, J. E., and Hassanli, R. (2016). Assessment of the mechanical performance of crumb rubber concrete. Constr. Build. Mater. 125, 175–183. doi: 10.1016/j.conbuildmat.2016.08.040
Zhang, B., and Poon, C. S. (2018). Sound insulation properties of rubberized lightweight aggregate concrete. J. Clean. Prod. 172, 3176–3185. doi: 10.1016/j.jclepro.2017.11.044
Zhang, H., Gan, Y., Xu, Y., Zhang, S., Schlangen, E., and Šavija, B. (2019). Experimentally informed fracture modelling of interfacial transition zone at micro-scale. Cem. Concr. Compos. 104:103383. doi: 10.1016/j.cemconcomp.2019.103383
Zhang, H., Xu, Y., Gan, Y., Chang, Z., Schlangen, E., and Šavija, B. (2019). Combined experimental and numerical study of uniaxial compression failure of hardened cement paste at micrometre length scale. Cem. Concr. Res. 126:105925. doi: 10.1016/j.cemconres.2019.105925
Keywords: waste rubber, mechanical strength, water permeability, thermal conductivity, ANOVA
Citation: Khern YC, Paul SC, Kong SY, Babafemi AJ, Anggraini V, Miah MJ and šavija B (2020) Impact of Chemically Treated Waste Rubber Tire Aggregates on Mechanical, Durability and Thermal Properties of Concrete. Front. Mater. 7:90. doi: 10.3389/fmats.2020.00090
Received: 04 January 2020; Accepted: 25 March 2020;
Published: 15 April 2020.
Edited by:
Guangming Chen, South China University of Technology, ChinaReviewed by:
Farshad Rajabipour, Pennsylvania State University (PSU), United StatesMuhan Wang, Qingdao University of Technology, China
Copyright © 2020 Khern, Paul, Kong, Babafemi, Anggraini, Miah and Šavija. This is an open-access article distributed under the terms of the Creative Commons Attribution License (CC BY). The use, distribution or reproduction in other forums is permitted, provided the original author(s) and the copyright owner(s) are credited and that the original publication in this journal is cited, in accordance with accepted academic practice. No use, distribution or reproduction is permitted which does not comply with these terms.
*Correspondence: Branko Šavija, Yi5zYXZpamFAdHVkZWxmdC5ubA==