- 1Community and Urban Science Research Group, National Renewable Energy Laboratory, Golden, CO, United States
- 2Computational Science Center, National Renewable Energy Laboratory, Golden, CO, United States
- 3Pre Framing Corp., Berkeley, CA, United States
- 4SimFactory Automation SA, Stabio, Switzerland
The National Renewable Energy Laboratory is actively developing and testing Immersive Industrialized Construction Environments (IICE) for construction automation and worker-machine interaction to investigate possible solutions and increase workforce productivity. At full scope and matured functionality, IICE allows us to accelerate the development of and better explore industrialized construction approaches such as prefabrication. IICE also enables wider adoption of energy-efficient products and Industry 4.0 construction automation through worker-machine interaction pilots. Industry 4.0 and industrialized construction approaches can encourage workforce specialization in energy efficiency construction, address the lack of multi-skilled workers, and increase workforce productivity with construction automation. However, recent attempts to integrate these concepts with the industry have only been moderately successful. To address this, focusing the pedagogy on using a digital twin, its digital models, and virtual reality could make the experience of continuing education on construction automation more affordable, accessible, scalable, immersive, and safer, and could greatly improve the efficiency and robustness of the building and construction industry. IICE accurately represents the realities of construction uncertainties without having to create full scale physical prototypes of machines. In this paper, we address the following research question: How can a digital twin and its models in virtual reality enhance the learning experience and productivity of energy efficiency construction workers to gain the skills in operating Industry 4.0 components such as construction automation and handling energy-efficient products in industrialized construction factories and on-site? We introduce original research on developing IICE and present preliminary findings from time and motion pilot studies.
Introduction
Energy efficiency businesses lead the U.S. energy economy in creating jobs—accounting for about half of the sector’s entire job growth in 2018. According to the seminal 2020 report, Energy Efficiency Jobs in America, 56% of energy efficiency businesses are in the construction industry (Energy, 2019). A recent American Council for an Energy-Efficient Economy (ACEEE) paper led by the National Renewable Energy Laboratory (NREL), “Building the Efficiency Workforce,” highlights that the lack of technical skills and lack of industry-specific knowledge were two of the top three reasons energy-efficient employers cited for their hiring difficulty (Truitt et al., 2020). That paper also calls for increasing energy efficiency construction workforce training by using digital tools to manage performance as part of existing continuing education modules.
Over the last few years, the U.S. construction industry has begun adopting industrialized construction (IC) approaches to reduce construction timelines and improve workforce productivity. IC is the process of producing prefabricated systems, building components, or building structures in a protected factory environment and transporting them to the construction site for installation or assembly (Razkenari et al., 2019). Following are two key benefits of IC:
1. IC is expected to substantially improve the production efficiency by using innovative products such as computer-aided construction and automation (Fenner et al., 2017). Major Industry 4.0 components such as construction automation, robotics, and Internet of Things are now getting attention to enable a digitized construction environment (Oesterreich and Teuteberg, 2016). IC approaches such as off-site construction and prefabrication lend themselves to Industry 4.0 components. However, practical applications of Industry 4.0 components are still in their infancy because widely adopting Industry 4.0 components entails a particular set of workforce training and experience that is currently missing.
2. IC approaches such as modular construction have proven to reduce construction time and landfill waste, improve indoor air quality, lead to high-performance building envelopes, and improve energy performance (Ganiron and Almarwae, 2014). NREL’s ongoing research in IC innovation aims to accelerate the integration of energy-efficient products during IC to help deliver net-zero energy modular buildings at scale (Podder et al., 2020). Therefore, IC approaches should be part of energy efficiency construction workforce training.
Despite the proven and promised advantages from IC, the construction workforce is experiencing significant challenges arising from its increasing use. There is a need to accelerate the development of and better explore IC approaches such as prefabrication. There is also a need to enable wider adoption of energy-efficient products and Industry 4.0 construction automation by investigating worker-machine interactions. IC approaches generally need multi-skilled workers with comprehensive knowledge of traditional construction and manufacturing crafts in both on-site and off-site locations (Goulding et al., 2012). Although the construction industry is actively embracing IC approaches to increase its dwindling workforce productivity (Barbosa et al., 2017), the average worker must follow a steep learning curve in a demanding work environment to familiarize and develop expertise with a wide range of Industry 4.0 components. For construction of high-performance buildings and installation of energy-efficient products, the skill requirement further increases. Unlike new and emerging construction products such as steel, wood, concrete, certain new and emerging energy-efficient products such as pre-insulated wood studs and bio-based materials are not widely used in the industry. Furthermore, energy-efficient products are a complex productization of multiple building components such as Insulated truss studs (ITSs) that are a combination of structural wood and insulation into one product. It is heavier that standard studs and needs advanced skills. In addition, energy-efficient products need better quality control and less error. To achieve this, a machine-mediated approach is necessary. ITSs need to be cut accurately in order for them to lead to walls that are better quality, less leaky, and very air-tight. The TRAMCON program—Training for Manufactured Construction—is an example of a recent attempt to increase Industry 4.0 and IC approaches in the construction industry, address the lack of multi-skilled workers, and encourage specialization in energy efficiency construction (Razkenari et al., 2018). The TRAMCON program’s training module includes “Sustainable Manufacturing,” through which supervisor trainees learn about sustainable construction, green building concepts, and green building rating systems. The program attempts to bridge the skill gap in both the larger construction industry and the niche energy efficiency construction industry, but we consistently see a major limitation in TRAMCON and other similar programs that they do not focus the pedagogy on using digital twins, digital models, and virtual reality to make the experience of continuing education on construction automation more affordable, accessible, scalable, immersive, and safer.
In this brief research report article, we aim to address the following question: “How can a digital twin and its models in virtual reality enhance the learning experience and productivity of energy efficiency construction workers to gain the skills in operating Industry 4.0 construction automation and handling energy-efficient products in IC factories and on-site?” We introduce our original research following a two-stage integrated methodology to develop a novel application of immersive environments. Then, we provide preliminary data and findings from piloting a case study. Our case study involves the following three key entities:
1) An Industry 4.0 component: The Pre Framer machine™ (PF) is a purpose-built automated cut-saw machine that serves as a novel Industry 4.0 component for the construction industry.
2) An energy-efficient product: ITSs are thermally broken, insulated wooden studs for use in exterior and interior walls. ITSs serve as energy-efficient standard lumber replacements.
3) An energy efficiency construction workforce trainee: In the case study, an energy efficiency construction workforce trainee enrolls to learn how to operate the PF, increase workforce productivity, and handle the ITSs as the material feedstock for the machine.
Methods
We define Immersive Industrialized Construction Environments (IICE) as digitally mediated learning environments in virtual reality (VR) that are more affordable, accessible, scalable, and safer than real-world construction environments in factory and on-site. Lui (2014) defines immersive environments as “digitally mediated learning environments designed to engage users in an artificially created make-believe world.” A wide variety of immersive technologies exist from head-mounted displays to large-scale surround-screen projection-based environments such as Cave Automatic Virtual Environments (CAVE ®) (Cruz-Neira et al., 1993). The technology is activity being used to support scientific and engineering analysis (Gruchalla and Brunhart-Lupo, 2019), industrial product design (Berg and Vance, 2017), and virtual training (Vaughan et al., 2016), among other uses.
IICE is currently being developed and tested for energy efficiency construction workforce training in NREL’s large-scale projection-based immersive environment in Golden, Colorado. The environment is two-sided (a 5 m × 2.5 m wall and a 5 m × 1.75 m floor) illuminated by six active-stereo projectors for a total resolution of 3540 × 2808 pixels (Gruchalla and Brunhart-Lupo, 2019). The projection volume and the room it sits in are optically tracked by a Vicon™ camera system. In its full scope and matured functionality, IICE would enable the energy efficiency construction workforce to engage in artificially created worlds and interact with digital twins and digital models of a wide range of physical assets associated with IC approaches such as prefabrication, Industry 4.0 such as the PF, and energy-efficient products such as ITSs. As a virtual reality module, IICE accurately represents the realities of construction uncertainties without having to create full scale physical prototypes of machines. We follow a two-stage integrated methodology to develop IICE (Figure 1) The scope of this Brief Research Report article covers original research, preliminary input/output data, and preliminary findings from Stage I. Stage II is future research work, since this is an ongoing capability development effort at NREL. As shown in Figure 1, Stage I involves physical prototypes of the machine and ITSs along with fiducial markers (illustrated as solid white shapes), digital twin v1 and the twin’s digital model versions as v2 ... , vn (illustrated as solid grey shapes), and input/output data as d1, d2 ... , dn (illustrated as black arrows). A brief overview of the methodology is as follows:
• In Stage I, we leverage data from past real-world projects to inform immersive time-and-motion studies. At the end of this stage, we reached an early development stage of IICE with PF digital model v2 in NREL’s immersive environment. The experimental setup aims to validate a trainee participant’s behavior in IICE against a typical worker’s behavior when operating the full-scale physical prototype of the Pre Framer™ machine. The important criteria to consider is the improvement in workforce productivity when operating the machine prototype in real world. Therefore, the key performance indicator is workforce productivity, with the machine to complete a set of discrete sub-tasks and introduction of slight changes during the activities.
• In Stage II, we plan to leverage output data from Stage I to create two what-if learning scenarios in NREL’s immersive environment where the trainee interacts with multiple digital model versions of the PF.
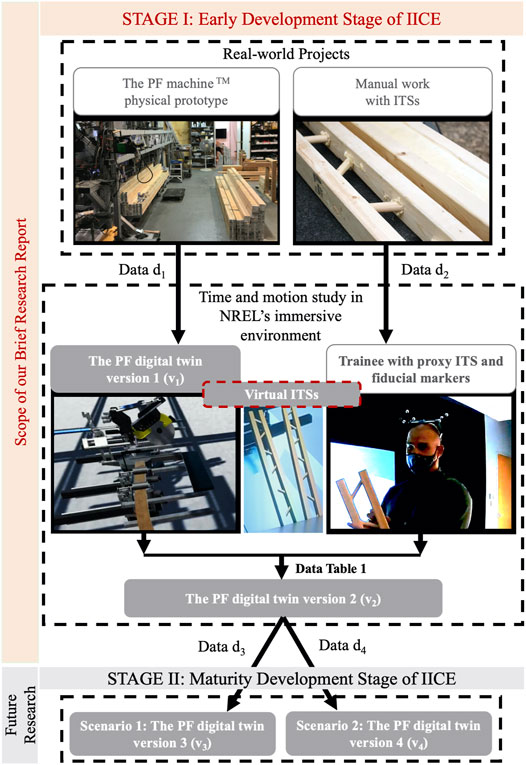
FIGURE 1. A two-stage integrated methodology to develop IICE (note that DT stands for digital twin). Photos from Pre Framing Corp and NREL.
The following detailed description of each stage explains the physical prototypes, the digital twin, the twin’s digital model versions, and input/output data:
• Stage I: Early Development Stage of IICE
∘ Real-world projects: Both the PF and ITSs are being used to deliver various projects across the United States. Standard wooden studs are used as material feedstocks for the PF. To our best knowledge, there has not been any real-world project where ITSs are used as material feedstock for the PF. IICE development was initiated using data from existing literature and documentation of projects related to the following physical assets:
⁃ The PF physical prototype: Pre Framing Corp owns and operates the Pre Framer machine (referred to as the PF in this paper). A working prototype of this purpose-built automated cut-saw machine is utilized at full capacity in Pre Framing Corp’s warehouse to cut, pre-frame, and pre-package standard wooden studs into walls. The intended machine operator is a construction worker with knowledge and experience of wall framing, with motivation to learn IC approaches such as prefabrication, and with skills to operate such an Industry 4.0 machine. The output data (d1) is the geometric data extracted from 3D computer-aided design (CAD) drawings and documentation on operating conditions of the PF physical prototype.
⁃ Manual work with ITSs: ITSs have emerged in the residential buildings construction industry as a commoditized energy-efficient product that can replace the standard wood studs and the continuous insulation in building envelopes. ITSs are being used by energy efficiency construction workforce to frame walls with improved thermal performance, and in many cases without the need for additional continuous insulation. The output data (d2) is the geometric data extracted from 3D CAD drawings and documentation on material characteristics, structural performance, and thermal performance of ITSs.
∘ Time-and-motion study in NREL’s immersive environment: Time and motion study of the construction workforce can contribute to productivity improvement and ergonomic analysis (Guo et al., 2016). Human actions and postures involved in performing manual tasks are determined by working environments (Golabchi et al., 2015). Thus, spatial data of workplaces extracted from plan layouts and geometric data of physical assets extracted from 3D CAD drawings are the key to conducting time and motion study of manual tasks like operating the PF, feeding ITSs into the machine from one end, and collecting cut parts of ITSs as they come out from the other end of the machine. Instead of performing our time-and-motion study in the real world as part of a demanding construction work environment, we leveraged NREL’s immersive environment as a risk-free, controlled environment that encourages learning (Figure 2). Past studies on learning in construction industry has shown the effect of “forgetting” on productivity. It has been noted that due to lack to repetitiveness, there is ‘forgetting’ which leads to lower productivity. Redoing the same activity with the introduction of specific changes with each iteration allows strengthening of the training activity. Furthermore, there is not a lot of room to learn a task and identify potential changes in activities on site, especially with new products that the typical workforce has not utilized in the past. NREL’s immersive environment provides a learning space where the same task can be redone with opportunities to make impactful changes with every iteration. In our time-and-motion study, we found that introducing a seemingly small change with stud storage and distance/orientation of feeding activity can have a significant impact on productivity. The following data recording plan was followed for the study in NREL’s immersive environment:
⁃ Tracking: The trainee’s head position was tracked with optical fiducial markers placed on the active-stereo glasses. Proxy ITSs built from foam-core board were also tracked with fiducial markers, serving as input devices to manipulate the virtual ITS. A trainee wearing the tracked glasses collects and manipulates the physical prototype of proxy ITS with the virtual PF. All fiducial markers are reference points or measuring units for positional tracking of input devices. Thus, for motion data, the primary data recorded is the local X, Y, Z coordinates (initial and final) of each fiducial marker at specific time intervals. For time data, a global clock is used, and the data recorded is a timestamp. The frequency of the local X, Y, Z coordinates collected is set at one data point per minimum 83 milliseconds (ms).
⁃ Experimental setup in NREL’s immersive environment: We uploaded the PF digital twin version 1 (v1) to the environment in 1:1 scale. In the experimental design setup, the trainee interacts with the PF digital twin v1 in NREL’s immersive environment. The experimental setup is a time and motion data collection strategy that integrates real-world actions with VR reactions. In the experimental setup, 11 data sets were recorded that included 11 motion data and time data for 8 discrete sub-tasks. In Figure 3, fiducial markers on the trainee and on the proxy ITS are illustrated by yellow circles. 11 data sets include motion and time data from 3 locations and 8 sub-tasks as described in the following list (as shown in Figure 3):
A) Initial storing data set: Proxy ITS in storage for material feedstock (real-world immersive environment). Data recorded: Local X, Y, Z coordinates of the fiducial marker representing the initial position of the proxy ITS.
B) Pre-feeding collecting sub-task: Trainee performs the sub-task of feeding the proxy ITS into PF digital twin v1.
C) Feeding activity sub-task: The position and motion (i.e., change in position) of the proxy ITS is accurately mimicked in VR as a virtual ITS. First, the local X, Y, Z coordinates of the fiducial marker on the proxy ITS is represented in VR.
D) release and move sub-task: The position of the trainee at release of the proxy ITS marks the end of feeding activity i.e., the virtual ITS has been fed into the PF digital twin v1.
E) Pre-cut supervision data set: The primary data recorded are the local X, Y, Z coordinates of the fiducial marker representing the resting position of the trainee while supervising the cut-saw as the virtual ITS moves across the PF digital twin v1. In VR, the cut-saw is in the idle state marked as 0.
F) Safety check data set: The distance between (e) and (g) is recorded to ensure that a safe distance is maintained between the trainee and the cut-saw (along the Y-axis). Data recorded is local X, Y, Z coordinates of the fiducial marker.
G) Automated cutting sub-task: In VR, the cut-saw switches from the idle state marked as 0 to the cutting state marked as 1.
H) Cutting supervision and move sub-task: The position of the trainee at the end of the automated cutting activity is recorded.
I) Post-cut supply sub-task: The position and motion (i.e., change in position) of the virtual ITS cut pieces in VR is recorded.
J) Post-cut collecting sub-task: The primary data recorded is the local X, Y, Z coordinates of the fiducial marker representing the collecting position of the trainee.
K) Final storing sub-task: Proxy ITS cut pieces are stored in the real-world immersive environment. Data recorded: Local X, Y, Z coordinates of the marker representing the final position of the proxy ITS cut pieces.
• Stage I data and key output: Under Pilot 3, one trainee performed the full task that consists of the sequential 8 sub-tasks. The same trainee performed a total number of two runs of this same pre-defined set of activities or sub-tasks. We introduce a slight change in initial position and orientation at the end of task run 1. Individual time for each sub-task, average time for each sub-task, and total time for full task in each test run were recorded for two test runs of the same set of 8 sub-tasks. We plan to perform Moving Average Smoothing (MAS) of the time-series data from multiple pilots. MAS is critical for our time series analysis and forecasting because it will smooth out short-term fluctuations and highlight longer-term cycles that are more impactful in productivity improvements. Since calculating a moving average involves creating a new series where the values are comprised of the average of raw observations in the original time series, we have demonstrated the first step of averaging the data from the two test runs. The average eliminates some of the randomness in the data. Data is presented in Table 1 under “Results.” The reduction of total time to perform the 8 sub-tasks leads to an increase in workforce productivity (the key performance indicator).
• Stage II Maturity Development Stage of IICE: The current physical machinery is a prototype. We will complete a fully functional ready to use on site version of the machinery by mid 2022. This will allow us to accurately document the state of on site productivity with the physical machinery followed by the comparison with off-site (as shown in Figure 1).
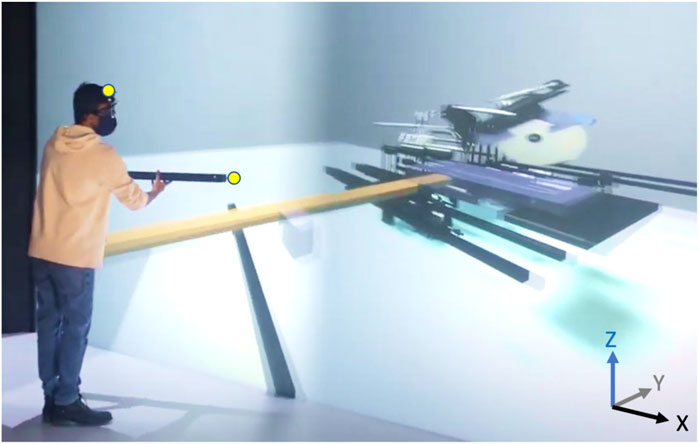
FIGURE 2. Time and motion study using fiducial markers (illustrated as yellow circles) on active-stereo glasses and input devices for outside-in tracking while the trainee performs the act of feeding the proxy ITS into the PF digital twin v1 (1:1 scale) in NREL’s immersive environment. Local X, Y, Z coordinates of fiducial markers are the primary data recorded at a minimum of 83 milliseconds. Photo by NREL.
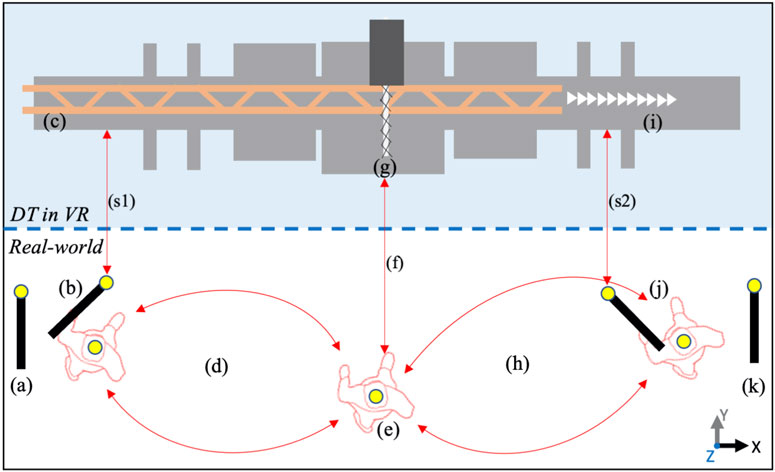
FIGURE 3. Plan layout of the experimental design setup in NREL’s immersive environment, illustrating VR and real-world on either side of the blue dashed line. 11 data sets are marked as: (A) initial storing, (B) pre-feeding collecting, (C) feeding, (D) release and move, (E) pre-cut supervision, (F) safety check, (G) automated cutting, (H) cutting supervision and move, (I) post-cut supply, (J) post-cut collecting, and (K) final storing.
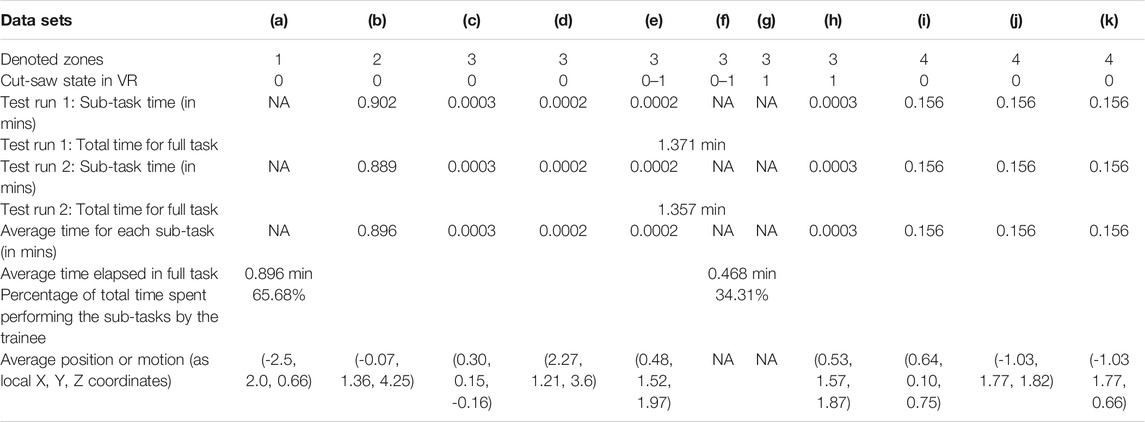
TABLE 1. Tabulated workbook with two test runs focused on preliminary calibration of the experimental setup, introduction of a slight change in position and orientation, and continuous improvements implemented, recorded position or motion data for each discrete training sub-task from two test runs by one trainee in Pilot 3.
Results
Table 1 presents the preliminary findings from two test runs in Stage I. Table 1 has been created from the original time and motion study data sets by carefully extracting, reorganizing, and tabulating into a workbook that can be used for future research that would include more pilots and further development of IICE. For the two runs of 8 sub-tasks by one trainee in Pilot 3, the time between each data point recorded was kept at a minimum of 83 ms. Total time for full task in test run 1 is 1.371 min and for full task in test run 2 is 1.357 min. The average time elapsed (from test run 1 and test run 2) to perform the full task is 1.364 min. We had one trainee participant, so we did a comparison between time data from different runs of like scenarios to understand the significance of the data and quantify workforce productivity. Productivity can be calculated by measuring the total output produced (in units) relative to the total time taken to complete the full task for the given output (in minutes). The full task is considered completed with a single cut of one ITS into two ITS cut pieces that makes the output as 2 units. Thus, for the same output in like scenarios, productivity in test run 1 is 1.459 and test run 2 is 1.473. The average productivity of the trainee from this study is 1.466. Clearly, lower the time taken to perform the full task, higher the workforce productivity. The relative distance of the digital model of the machine from the location of proxy ITS was also fixed. We present these results in light of previous knowledge on improving workforce productivity by focusing on the preparation stage which includes all the activities which are required to be done in order for the actual work to be performed in the best possible way (Hajikazemi et al., 2017). Past studies on workforce productivity pilots demonstrate that the preparation time can be higher than downtime and that such activities include preparation of the work area, machines, or tool (Loera et al., 2013). Performed changes concerning the two test runs led to better preparation at sub-task (b) pre-feeding collecting and as a result, an increase in productivity. The performed changes concerning the two test runs are:
• In test run 1, the trainee was unfamiliar with the storage location and orientation of the proxy ITS for material feedstock. In test run 2, the position of the proxy ITS was fixed to -2.5, 2.0, 0.66 (local X, Y, Z coordinates of the fiducial marker representing the initial position) as storage.
• Due to change in initial position of the proxy ITS, sub-task (b) takes less time which indicates learning. We found that 65.68% of the total time to perform the full task is taken up by sub-task (b) making it the focus for continuous improvement strategies.
Discussion
We address the research question by demonstrating that the experimental setup with a digital twin and its digital models in virtual reality enhanced the learning experience in the preparation stage and increased the productivity of one trainee participant. The experimental setup validates that continuous improvement strategies through two test runs of the same set of sub-tasks with the introduction of a slight change each time significantly influences the trainee’s behavior in IICE. At the end of two test runs, the trainee participant’s perceptions of the use of IICE for training includes the recognition that virtual reality environment in experimental setups allows focus on potential improvements with non-critical sub-tasks such as preparation stage. While we have successfully demonstrated an early version of IICE that can be leveraged to train the energy efficiency construction workforce to learn operating novel automation tools with energy-efficient products and increase productivity, our research was limited in scope, findings, and impact. For our study, we were limited to one trainee due to technical and non-technical constraints. NREL’s visualization room is not currently fitted with data acquisition system that can be utilized without manual supervision. This technical constraint called for two VR experts to be in the room along with one trainee. The two VR experts did not serve as trainees too since they had to be dedicated to ensuring that the data acquisition system was working properly during VR pilots and test runs. Furthermore, our experimental setup was iterative which means one VR expert ensured slight spatial changes to the setup with change in orientation and position of the dummy ITS and another focused on the ensuring robust functioning of the data acquisition system. Non-technical constraints included covid-induced challenges where we received permission for one trainee to perform the two test runs while maintaining safe indoor environment due to covid protocols from the two VR experts. With follow on funding, we are planning for additional test runs with different trainees and considering completion of these task runs in a real-world environment once the machinery is ready in mid-2022. We plan to perform MAS of the time-series data from multiple pilots. Further research needs to be done to make IICE replicable across different VR platforms and directly accessible from outside NREL’s immersive environment. This will allow workers to gain the skills needed to operate Industry 4.0 components such as construction automation and handling energy-efficient products from familiar environments of their IC factories or from the site using head-mounted displays and other portable, user-friendly VR devices.
Data Availability Statement
The raw data supporting the conclusions of this article will be made available by the authors, without undue reservation.
Ethics Statement
The studies involving human participants were reviewed and approved by William C. Bailey, MRIGlobal IRB. The patients/participants provided their written informed consent to participate in this study.
Author Contributions
The sequence of authors has been determined by the relative overall contributions to the manuscript. AP has first authorship. AP was the co-PI of this research project and contributed most to the writing of this manuscript. KG has second authorship. KG contributed to the Methods section of this manuscript. KG led the development of the experimental setup and was instrumental in the success of the IICE pilots with proxy ITS and fiducials. NB-L has third authorship. NB-L led the digital model development and was also instrumental in the success of the IICE pilots. NB-L contributed to the Results section of this manuscript. SP has senior authorship. SP played a significant role setting the direction of this research and driving the team towards achieving results. SP was the co-PI of this research project and provided valuable feedback to improve this manuscript. MS and PL share last authorship. MS and PL were the industry partners on this project and their contribution to the manuscript includes data from real-world pilots with the machine and data from early digital twin of the machine. All authors agree to be accountable for the content of the work.
Funding
This work was authored in part by the National Renewable Energy Laboratory, operated by Alliance for Sustainable Energy, LLC, for the U.S. Department of Energy (DOE). Majority of the funding to perform this preliminary research and develop early IICE capability at NREL was provided by the Wells Fargo Foundation’s Innovation Incubator (IN2). This research was performed using computational resources sponsored by the U.S. DOE’s Office of Energy Efficiency and Renewable Energy and located at NREL. The funded project was a collaboration between NREL, Pre Framing Corp, and SimFactory Automation SA. The views expressed in the article do not necessarily represent the views of the DOE or the U.S. Government. The U.S. Government retains and the publisher, by accepting the article for publication, acknowledges that the U.S. Government retains a nonexclusive, paid-up, irrevocable, worldwide license to publish or reproduce the published form of this work, or allow others to do so, for U.S. Government purposes.
Conflict of Interest
Author MS was employed by Pre Framing Corp. Author PL was employed by SimFactory Automation SA.
The remaining authors declare that the research was conducted in the absence of any commercial or financial relationships that could be construed as a potential conflict of interest.
Publisher’s Note
All claims expressed in this article are solely those of the authors and do not necessarily represent those of their affiliated organizations, or those of the publisher, the editors and the reviewers. Any product that may be evaluated in this article, or claim that may be made by its manufacturer, is not guaranteed or endorsed by the publisher.
References
Barbosa, F., Woetzel, J., Mischke, J., Ribeirinho, M. J., Sridhar, M., Parsons, M., et al. (2017). Reinventing Construction through a Productivity Revolution. Houston, TX: McKinsey. https://www.mckinsey.com/business-functions/operations/our-insights/reinventing-construction-through-a-productivity-revolution.
Berg, L. P., and Vance, J. M. (2017). Industry Use of Virtual Reality in Product Design and Manufacturing: a Survey. Virtual Reality 21, 1–17. doi:10.1007/s10055-016-0293-9
Cruz-Neira, C., Sandin, D. J., and DeFanti, T. A. (1993). “Surround-screen Projection-Based Virtual Reality: The Design and Implementation of the CAVE,” in Proceedings of the 20th Annual Conference on Computer Graphics and Interactive Techniques (SIGGRAPH ’93) (New York, NY, USA: ACM), 135–142.
Energy (2019). Energy Efficiency Jobs in America. Available at: https://e4thefuture.org/wp-content/uploads/2019/09/Energy-Efficiency-Jobs-in-America-2019.pdf. Accessed on January 10, 2021.
Fenner, A. E., Razkenari, M., Hakim, H., and Kibert, C. J. (2017). “A Review of Prefabrication Benefits for Sustainable and Resilient Coastal Areas,” in Proceedings of the 6th International Network of Tropical Architecture Conference, Tropical Storms as a Setting for Adaptive Development and Architecture (Gainesville, FL, USA: iNTA2017) 1–3.
Ganiron, T. U., and Almarwae, M. (2014). Prefabricated Technology in a Modular House. Int. J. Adv. Sci. Techn. 73, 51–74. doi:10.14257/ijast.2014.73.04
Golabchi, A., Han, S., Seo, J., Han, S., Lee, S., and Al-Hussein, M. (2015). An Automated Biomechanical Simulation Approach to Ergonomic Job Analysis for Workplace Design. J. Constr. Eng. Manage. 141 (8), 04015020. doi:10.1061/(asce)co.1943-7862.0000998
Goulding, J., Nadim, W., Petridis, P., and Alshawi, M. (2012). Construction Industry Offsite Production: A Virtual Reality Interactive Training Environment Prototype. Adv. Eng. Inform. 26 (1), 116. doi:10.1016/j.aei.2011.09.004
Gruchalla, K., and Brunhart-Lupo, N. (2019). “The Utility of Virtual Reality for Science and Engineering,” in VR Developer Gems. Editor W. R. Sherman (Boulder, CO: Taylor & Francis), 383–402. Chapter 21. doi:10.1201/b21598-21
Guo, X., Golabchi, A., Han, S., and Kanerva, J. (2016). “3D Modeling of Workplaces for Time and Motion Study of Construction Labor,” in Proceedings of the 16th International Conference on Computing in Civil and Building Engineering (ICCCBE) (Osaka, Japan: ICCCBE), 6–8.
Hajikazemi, S., Andersen, B., and Langlo, J. A. (2017). Analyzing Electrical Installation Labor Productivity through Work Sampling. Int. J. productivity Perform. Manag. 66, 1–21. doi:10.1108/ijppm-06-2016-0122
Loera, I., Espinosa, G., Enríquez, C., and Rodriguez, J. (2013). Productivity in Construction and Industrial Maintenance. Proced. Eng. 63, 947–955. doi:10.1016/j.proeng.2013.08.274
Lui, M. (2014). “Immersive Environments,” in Encyclopedia of Science Education. Editor R. Gunstone (Dordrecht: Springer), 1–2. doi:10.1007/978-94-007-6165-0_39-1
Oesterreich, T. D., and Teuteberg, F. (2016). Understanding the Implications of Digitisation and Automation in the Context of Industry 4.0: A Triangulation Approach and Elements of a Research Agenda for the Construction Industry. Comput. Industry 83, 121–139. doi:10.1016/j.compind.2016.09.006
Podder, A., Pless, S., Rothgeb, S., Klammer, N., Blazek, C., Louis, J., et al. (2020). Integrating Energy Efficiency Strategies with Industrialized Construction for Our Clean Energy Future. Natl. Renew. Energ. Lab. [Preprint]. NREL/CP-5500-77259. https://www.nrel.gov/docs/fy20osti/77259.pdf, 1–16.
Razkenari, M. A., Fenner, A. E., Hakim, H., and Kibert, C. J. (2018). Training for Manufactured Construction (TRAMCON)—Benefits and Challenges for Workforce Development at Manufactured Housing Industry. Hollywood, FL: Modular and Offsite Construction (MOC) Summit.
Razkenari, M., Bing, Q., Fenner, A., Hakim, H., Costin, A., and Kibert, C. J. (2019). “Industrialized Construction: Emerging Methods and Technologies,” in Computing in Civil Engineering 2019: Data, Sensing, and Analytics (Reston, VA: American Society of Civil Engineers), 352–359. doi:10.1061/9780784482438.045
Truitt, S., Williams, J., and Salzman, M. (2020). Building the Efficiency Workforce. Golden, CO: National Renewable Energy Laboratory. NREL/CP-5500-75497. https://www.nrel.gov/docs/fy20osti/75497.pdf, 1–16.
Keywords: industrialized construction, industry 4.0, construction automation, productivity, workforce, energy efficiency, digital twins, immersive environments
Citation: Podder A, Gruchalla K, Brunhart-Lupo N, Pless S, Sica M and Lacchin P (2022) Immersive Industrialized Construction Environments for Energy Efficiency Construction Workforce. Front. Virtual Real. 3:781170. doi: 10.3389/frvir.2022.781170
Received: 22 September 2021; Accepted: 23 February 2022;
Published: 10 March 2022.
Edited by:
Franca Giannini, National Research Council, ItalyReviewed by:
Mark Dennison, United States Army Research Laboratory, United StatesFrederic Merienne, ParisTech École Nationale Supérieure d'Arts et Métiers, France
Copyright © 2022 Podder, Gruchalla, Brunhart-Lupo, Pless, Sica and Lacchin. This is an open-access article distributed under the terms of the Creative Commons Attribution License (CC BY). The use, distribution or reproduction in other forums is permitted, provided the original author(s) and the copyright owner(s) are credited and that the original publication in this journal is cited, in accordance with accepted academic practice. No use, distribution or reproduction is permitted which does not comply with these terms.
*Correspondence: Ankur Podder, QW5rdXIuUG9kZGVyQG5yZWwuZ292