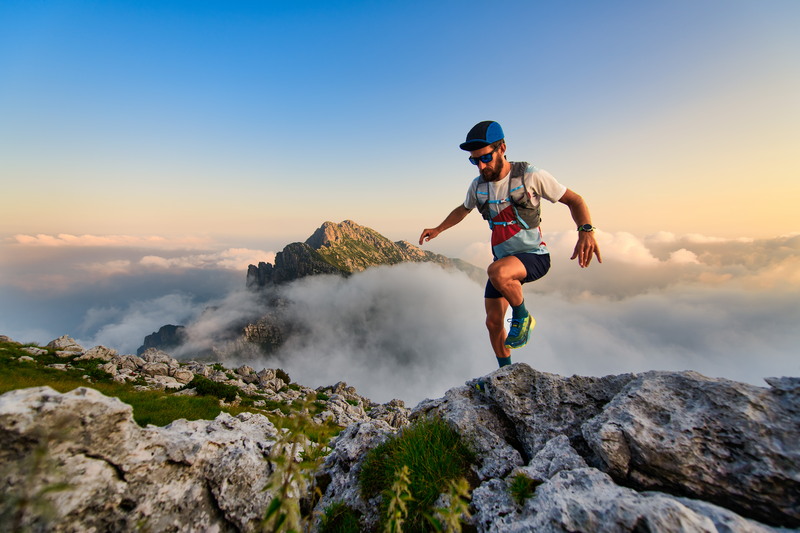
95% of researchers rate our articles as excellent or good
Learn more about the work of our research integrity team to safeguard the quality of each article we publish.
Find out more
ORIGINAL RESEARCH article
Front. Therm. Eng. , 02 April 2025
Sec. Heat Engines
Volume 5 - 2025 | https://doi.org/10.3389/fther.2025.1548806
This article is part of the Research Topic Hybrid Renewable Energy Systems for Power, Heating, and Cooling View all articles
The present study examines the performance and emission attributes of an indirect injection diesel engine powered by blends of waste plastic pyrolysis oil (WPPO) and ethanol, evaluating their viability as substitutes for traditional diesel fuel. Experimental results reveal that blend BL2 (25 vol.% WPPO and 10 vol.% ethanol) exhibits superior brake thermal efficiency (BTHE), surpassing diesel by 1.3% at full load, while other prepared blends demonstrate comparable performance. Brake-specific fuel consumption decreases with increasing load, with BL2 outperforming diesel by 3.7% at full load. Unburned hydrocarbon emissions are lower for BL1 (15% WPPO and 5% ethanol) and BL2, with reductions of 6.7% and 10.4%, respectively, compared to diesel at full load. In contrast, blends with higher ethanol content show decreased nitric oxide emissions, with BL1 and BL2 reducing 20.1% and 21.7. Carbon monoxide emissions are consistently reduced across all blends, with 25% reductions attributed to improved oxygen availability for combustion. The findings demonstrate that WPPO-ethanol blends, particularly BL1 and BL2, offer a promising pathway for reducing environmental pollutants while maintaining or enhancing engine performance, highlighting their potential as supplementary fuels for internal combustion engines.
The evolution of plastics has been remarkable since their first public introduction by Alexander Parkes at the Great International Exhibition in London in 1862. The term “plastic” originates from the Greek words “plastikos,” meaning “capable of being shaped or molded,” and “plastos,” meaning “molded” (Plastikos and Scott, 2011; Etymonline, 2011). Presently, plastics are moulded for millions of different uses. Plastics are non-biodegradable polymers primarily composed of carbon and hydrogen, along with other elements like chlorine and nitrogen. The use of plastics in the industrial field is increasing continuously due to their relatively low cost, lightweight, versatility, durability, energy efficiency, imperviousness to water, and faster production rate and design flexibility. Globally, approximately 129 million tonnes of plastics are produced annually, with 77 million tonnes derived from petroleum (Vu et al., 2001). In India, the annual demand for plastics is around 8 million tonnes, with over 10,000 metric tons produced daily and an equivalent amount imported. The per capita plastic consumption in India stands at about 3 kg, significantly lower than the 30–40 kg observed in developed nations. A substantial portion of this consumption is attributed to the packaging and food industries (Mani et al., 2009). A nationwide survey conducted in 2003 revealed that India generates over 10,000 metric tons of plastic waste daily, of which only 40% is recycled. If plastics are not recycled, it become waste, sometimes filling up the landfills and releasing toxic fumes if trying to burn them. Plastic waste poses a major challenge to municipal waste management due to its non-biodegradable nature.
On the other hand, “pyrolysis” comes from the Greek word where “pyro” means “fire” and “lysis” means “decomposition” (AnupT and Vilas, 2014). That means pyrolysis is the thermal decomposition process of organic substances without oxygen. Plastic oil produced through pyrolysis has certain drawbacks, including high viscosity, low volatility, a tendency to form gum, and carbon residue. Viscosity can be reduced by transesterification process, micro-emulsion and dilution by blending with diesel, distillation process, preheating and using additives. The primary challenges of using pure plastic oil in diesel engines include elevated smoke emissions and lower thermal efficiency, which result from its high viscosity and carbon residue compared to diesel fuel.
Diesel fuel engines are more suitable for heavy vehicles in the transportation and industrial sectors due to their higher thermal efficiency. Although it offers certain benefits, it produces high levels of NOx and smoke, posing risks to human health. To mitigate these pollutants, stringent emission regulations have been implemented (Williams and Williams, 1990). Fossil fuels are rapidly depleted due to increased fuel consumption. Consequently, the enforcement of strict emission standards and the diminishing reserves of fossil fuels have driven the pursuit of alternative fuels for diesel engines.
On the other hand, waste disposal is a key problem in most countries. Research predominantly focuses on blending waste plastic oil with heavy oil for marine applications, showing that such combinations significantly reduce viscosity and enhance engine performance (Soloiu et al., 2000). However, limited studies have explored their application in high-speed diesel engines. In India, a pilot-scale recycling process produces approximately 25,000 L of waste plastic oil daily (Vu et al., 2001). Common plastic materials used include Polyethylene, Polypropylene, Teflon, Nylon, and Dacron. For marine applications, waste plastic oil is employed in marine diesel engines (Arvanitoyannis and Tserkezou, 2008), where mixing it with heavy marine fuel oil substantially lowers viscosity. Additionally, discarded plastic items such as bags, bottles, ropes, and nets pose severe threats to marine life, choking and endangering thousands of animals and seabirds annually (Moriya et al., 2000). Extracting oil from such waste not only addresses disposal challenges but also generates valuable energy.
The collection of plastic waste is a critical starting point for effective recycling. Innovative methods for waste collection are essential, as are establishing cooperative forums within value chains and offering consultancy to private enterprises to improve collection practices. Cost-effective collection constitutes the first two steps of the recycling value chain. Once collected, the plastic waste is sorted into specific types to separate and upgrade valuable raw materials for pyrolysis plastic oil production. After sorting, the cleaning process begins with washing to remove impurities like paper labels, adhesives, and other contaminants. Labels on containers, bottles, and bins must be removed to ensure high-quality recycled plastic. The cleaned plastic is then shredded or crushed into chips (30–50 mm) using rotating metal teeth. Magnetic separation and metal detection remove foreign materials, such as nails, staples, and aluminum foil. The chips are further reduced to smaller sizes before being fed into a reactor.
In the reactor, suitable plastic chips decompose at temperatures of 450°C–550°C, depending on pyrolysis conditions and the type of plastic. Both kiln-type and screw-type reactors are used, and electric induction heating is a viable alternative to burners. Over time, carbon deposits accumulate on the reactor’s inner surfaces, requiring regular removal to maintain heat conduction efficiency. The decomposed plastics produce evaporated oil, which undergoes further cracking with a catalyst in a cracker to control the boiling point of the oil. Hydrocarbons with high boiling points, such as diesel, kerosene, and gasoline, are condensed in a condenser cooled by water. Meanwhile, gaseous hydrocarbons like methane and ethane, which cannot be condensed, are incinerated in a flare stack to manage exhaust gas volumes. The condensed evaporated oil yields pyrolysis oil, which undergoes distillation to separate undesirable components through selective evaporation and condensation. Distillation enhances the concentration of desired components by exploiting differences in the volatility of the mixture’s substances. Finally, in the transesterification process, alcohol (commonly methanol or ethanol) reacts with a triglyceride, facilitated by a base catalyst such as sodium hydroxide, potassium hydroxide, or sodium methoxide. This process accelerates the reaction, producing high-value byproducts without consuming the catalyst. Overall, these steps contribute to the efficient conversion of plastic waste into valuable raw materials and products (Figure 1).
The utilisation of vegetable oils as alternative fuels dates back to the early 20th century when Rudolf Diesel demonstrated using peanut oil to power a compression ignition (CI) engine. Eight decades later, rising awareness about environmental concerns and performance improvements led to a quest for cleaner alternative fuels that could reduce pollution without compromising engine performance. Due to their drawbacks, significant developments in internal combustion (IC) engines have shifted the focus away from vegetable oils. Simultaneously, the increase in waste materials has prompted researchers to explore their potential as alternative fuels. Waste materials, after undergoing decontamination processes, are now being used in engines with performance comparable to diesel fuel.
Blends of waste plastic pyrolysis oil (WPPO), diesel, and additives have shown promising results. The literature review focuses on studies that investigate the performance, combustion, and emission characteristics of WPPO-diesel-additive blends in IC engines. Sudhir Kumar (2013) conducted experiments on a single-cylinder, air-cooled, 256-cc, 3-BHP, four-stroke spark ignition (SI) engine at 3,000 rpm, fueled with plastic petrol (derived from waste plastic), gasoline, and their 50:50 blend. Performance parameters, including brake thermal efficiency (BTHE) and specific fuel consumption (SFC), are comparable to those of gasoline. Emission parameters like CO, O2, and HC decreased with increasing load, although unburnt HC and CO2 are slightly higher for plastic petrol. Plastic petrol’s flash point and volatility are higher than gasoline, contributing to better combustion and increased efficiency. Devaraj et al. (2015) tested a vertical, single cylinder, water-cooled, direct injection (DI) diesel engine using WPPO, WPPO blended with 5% diethyl ether (DEE) (WD05), and WPPO blended with 10% DEE (WD10) at various loads. Results indicated that WD10 exhibited higher BTHE due to reduced viscosity and improved atomisation of the air-fuel mixture. Brake-specific fuel consumption (bsfc) for WD blends approached diesel values at higher engine speeds. DEE blends reduced CO and NOx emissions, whereas increased HC emissions. AnupT and Vilas (2014) explored WPPO as an alternative for SI and CI engines. Results showed that engines could run on 100% WPPO, achieving higher thermal efficiency up to 50% and 75% of rated power for petrol and diesel engines, respectively. NOx emissions varied between 55 and 91 ppm for petrol-grade WPPO and 192–1,268 ppm for diesel-grade WPPO. Exhaust gas temperatures are higher for WPPO, and CO emissions increased by 5% compared to diesel. In a pilot-scale study, Miskolczi et al. (2009) investigated the pyrolysis of high-density polyethylene and polypropylene at 520°C using a ZSM-5 catalyst. The catalyst enhanced the yield of gasoline (20%–48%) and light oil (17%–36%), demonstrating its effectiveness in converting plastic waste into useful fuels. Lee (2009) studied pyrolytic oil’s thermal and catalytic degradation using a fluid catalytic cracking (FCC) catalyst. The addition of FCC catalyst improved liquid and gas yields and increased the fraction of heavy hydrocarbons in the oil. Catalytic degradation resulted in higher middle-hydrocarbon yields and calorific value than thermal degradation. Kumar et al. (2013) examined CI engines fueled with diesel, WPPO from high-density polyethylene, and their blends under various loads. Results showed lower BTHE and higher bsfc for WPPO blends compared to diesel. NOx and CO emissions increased with higher WPPO content, while HC emissions decreased with increasing load. Mani et al. (2009) performed multiple investigations on single-cylinder diesel engines using WPPO. Results showed that engines could run on 100% WPPO with BTHE, comparable to diesel, and up to 75% of rated power. NOx emissions are 25% higher, while CO emissions increased by 5%. Longer ignition delays and higher peak pressures are observed. Retarding injection timing reduced NOx emissions and improved combustion efficiency. Hunicz et al. (2024) investigated the use of waste plastic pyrolysis oils as diesel fuel blending components, showing that up to 60% PPO can be efficiently combusted in modern compression ignition engines. The study found that with heavy EGR and advanced injection timing, PPO achieved NOX emissions as low as 1.37 g/kWh and PM emissions of 0.04 g/kWh, reducing cumulative emissions by 50% compared to diesel fuel. Also, a 20% PSO blend resulted in an 81% reduction in cumulative emissions, highlighting the potential of waste-derived fuels in sustainable engine applications. Pratoomyod and Laohalidanond (2024) evaluated a six-cylinder DI diesel engine fueled with WPPO-diesel blends. WPPO blends exhibited higher bsfc and emissions (CO, CO2, NOx, HC) compared to diesel, while torque and power values are slightly lower due to the lower heating value of WPPO.
Thus, in view of the above studies made by various researchers, it is clear that For WPPO operation on SI engine, BTHE and bsfc were found to be similar with gasoline up to 50% of the rated power and unburned HC emission is less for different load whereas CO2 emission increases. For WPPO operation without blends and additives on the CI engine, it is found that the BTHE of WPO is closer to diesel, up to 75% of rated power; beyond that, it starts decreasing. Unburned HC emission is less, whereas NOx and CO emission are increased. For WPPO blends operation on CI engine, it found that Lower BTHE (ignition delay of WPO-DF blends is longer than DF) that of diesel, bsfc increases, NOx and CO emission increase with the higher percentage of WPO. Whereas at retarded injection timing (about 23 deg bTDC) increases BTHE and decreases NOx, CO, Unburned HC emission whereas smoke increased. For WPPO blends with additives operation on CI engine, with the addition of additives increases in BTHE and reduces CO, CO2, HC, NOx emission.
Additives are introduced in varying amounts to perform specific functions, such as reducing harmful emissions, enhancing fluid stability, improving the viscosity index by minimizing viscosity changes with temperature, and promoting better ignition by shortening delay times, among others (Fuel Additives, 2024). Ethanol, or ethyl alcohol, the same type found in alcoholic beverages, is commonly used as a motor fuel, primarily as a biofuel additive for gasoline (Hansdah et al., 2012). As a low-cost oxygenate, ethanol contains 34% more oxygen by weight compared to gasoline (Cardona and Sánchez, 2007). Ethanol can be produced biologically through fermentation from a range of biomass sources, including sugarcane, corn, sugar beet, molasses, and cassava root (Masum et al., 2013). The integration of ethanol in diesel engines can significantly boost the rural economy (Mofijur et al., 2015).
The outcome of such pyrolysis oil-ethanol-based dual fuel operation has undoubtedly established ample opportunity to undergo an optimisation study wherein the various input parameters can be suitably tuned to obtain the maximum gain of dual fuel operation by substituting base diesel. The motivations for exploring such alternative fuel assets are energy security, an increase in global warming and climate change difficulties that have collectively represented the necessary sustainability of the present energy scenario. Furthermore, the literature review has ventured into the numerous employability of diesel-pyrolysis oil-additive substances and their blends to acknowledge the IC engine performance and emission paradox (Vedaraman et al., 2011; Kumar, 2013). In the present scenario, the offline computational-based investigation technique is endowed with a pertinent juncture to conduct profundity sensitivity analysis and institute a cost-effective investigative podium. IC Engine optimisation studies (Deb et al., 2015a; Deb et al., 2015b; Deb et al., 2015c; Deb et al., 2014; Bose et al., 2013) have often unravelled the feasibility of multi-objective trade-off studies, which would lead to optimising one objective without compromising the other desired objectives. The present experimental investigation outcome has acknowledged the significance of precise regulation of the input parameters to acquire optimal performance and emission trade-off venture, i.e., BTHE, NO & UHC. Furthermore, pyrolysis oil-fuelled IC engine plans are deficient. On the other hand, it is ensured that in our day-to-day life, the contribution of fossil fuels has caused ecological imbalances like global warming and several health problems, which can be minimised by using alternative fuel sources as a substitute for conventional diesel fuel. The main objective of this study is to find an alternative energy source that improves engine performance parameters and reduces engine emission characteristics by utilising waste plastic materials. To achieve the objective, an unmodified IDI diesel engine would be used to carry out the experiments.
In the present experimental investigation, performance and exhaust emission analysis are performed with base diesel, 99.5% pure ethyl alcohol and the waste plastic pyrolysis oil. The diesel and ethyl alcohol are collected from the nearest diesel fueling station and a therapeutic shop. The plastic oil is obtained from waste plastic by the pyrolysis method. The WPPO is blended with commercial diesel and ethanol, which act as additives. The ethanol tends to miscible up to 10% by volume of diesel fuel; in winter, temperatures do not fall too low. A two-phase heterogeneous mixture is produced to increase the percentage of ethanol in diesel. On the basis of solubility, the diesel-WPPO-ethanol blends are prepared, and it is found that 5% of ethanol suitably mixes up to 15% of WPPO and 80% of diesel and 10% of ethanol that suitably mixes up to 25% of WPPO and 65% of diesel fuel. And beyond 10% by volume of ethanol, all blends showed instant phase separation, as shown in Figures 2, 3. Phase separation is temperature-dependent, and the phase separation observations were performed at room temperature (25°C). Based on this study, four blends are prepared under stable conditions these are D100 and BL1, BL2, BL3, and BL4. WPPO100%–100% waste plastic pyrolysis oil. BL1:P15E5- 15% waste plastic pyrolysis oil and 5% ethanol. BL2:P25E10%–25% waste plastic pyrolysis oil and 10% ethanol. BL3:P20%–20% waste plastic pyrolysis oil. BL4:P40%–40% waste plastic pyrolysis oil. The various properties of all the employed fuels in the existing experimental study are highlighted and estimated based on base liquid fuels by Equations 1–3 (Paul et al., 2015a; Paul et al., 2015b), and it is mentioned in Table 1.
Where,
Figure 2. Miscibility study of diesel-waste plastic pyrolysis oil-ethanol blends (WPPO100, P15E5 & P20E5).
The experimental investigation is carried out in an existing single-cylinder, 4-stroke, air-cooled IDI diesel engine, as shown in Figures 4, 5. The engine is mounted on a sturdy base frame (1,300 × 1,450 mm), while the dimension of the panel is 1,550 × 580 mm. The base frame is fabricated with a mild steel “C” channel. The engine is set up directly and coupled to an eddy current dynamometer with a control system using a flexible coupling and a stub shaft assembly. The technical engine specification is as per the Indian Standards IS: 11,170–1985 as shown in Table 2.
The engine dynamometer output is connected to a strain gauge load cell of an electronic data acquisition system to measure the load applied to the engine. The engine is equipped with provisions to apply various loads ranging from 0 to 6 kg. Six temperature sensors are placed at different points of the setup, with a key sensor positioned at the exhaust manifold before cooling in the calorimeter. The instrumentation is linked to a computer via a centralized NI LabVIEW®-based data acquisition (DAQ) platform, synchronized with a crank angle encoder and integrated with user interface-based Engine Soft post-processing software. The DAQ is programmed to collect in-cylinder and fuel injection pressure data at one-degree crank intervals, presenting the data smoothed over one hundred consecutive cycles to account for cyclic variations at a specific engine operating condition.
In contrast, common performance parameters are reported as estimated values for the same period of sampling. The specific fuel consumption is measured by a fuel burette for all tests, are fuel consumption for a time interval of 60 seconds is recorded in a fuel burette of 12.4 mm diameter. The mass flow rate of inducted air is estimated in kg/hr. From the sensed manometric depression in the integrated air box. The setup includes a single load panel box that contains the fuel tank, air box, manometer, fuel measuring unit, process indicator, and engine indicator. As the calorimeter is water-cooled, rotameters are used to measure the water flow, which is maintained at a rate above 80 mL/sec. All instruments are connected to a computer through a centralized data acquisition system (DAQ) platform, synchronized with a crank angle encoder. The typical computer configuration required is a CPU Pentium 3.0 GHz, RAM minimum of 512 MB, CD-ROM drives, USB Port, OS: Windows 7. Initially, the engine is made to run to obtain the steady state condition, and accordingly, experiments are performed using pure diesel to provide the baseline data.
The injection timing is optimised and set at 23°bTDC (static), as shown in Figure 6. The engine speed is kept at 1,500 rpm static with varying loads (0%, 25%, 50%, 75% and 100%). The AVL Digas 444 exhaust gas analyzer is attached to the engine’s exhaust pipe to measure exhaust emission parameters. Emission data is recorded in real-time, coinciding with the engine’s performance to obtain precise exhaust values corresponding to the performance at that moment. For authenticity in data analysis, three readings are taken at identical loads and then averaged to get the precise values. All procedures, including experimental testing preparation, performance check, and recording of test results, are confirmed to the Indian Standards specifications as 10,000 (Vu et al., 2001; Mani et al., 2009; AnupT and Vilas, 2014). The cooling water temperature, average ambient temperature and relative humidity throughout experimentation are recorded at 19°C, 28°C and 54%, respectively.
The exhaust gas analyser AVL Digas 444 is used for the exhaust gas analyser. The emissions, including Carbon Monoxide (CO), Carbon Dioxide (CO2), and Oxygen (O2), are measured by volume percentage (%), while Unburnt Hydrocarbons (UHC) and Nitrogen Oxide (NO) are measured in parts per million (ppm) as n-hexane equivalents. These parameters collectively represent the emission characteristics of the combustion process. The analyzer’s measuring pipe is directly connected to the engine’s exhaust manifold, positioned after the calorimeter.
Table 3 represents the measurement range of the AVL Digas 444 (Figure 7) exhaust gas analyser. The emissions parameters such as carbon monoxide, oxygen and carbon dioxide are represented in % Vol; the other parameters, such as hydrocarbon and nitrogen oxide, are represented as n-Heptane equivalent parts per million (ppm).
Ensure that all fasteners, including those for the engine, dynamometer, coupling, and base frame, are securely tightened to the specified torque values. Verify that the engine sump contains an adequate amount of lubrication oil, which can be accurately assessed by checking the oil level against the marked indicator on the dipstick. Connect the data cables from the engine test bed to the panel. Switch ON the mains. Ensure sufficient fuel in the fuel tank. Remove air in the fuel line, if any. Switch ON the Panel. Ensure the pressure sensor and crank angle encoder are connected to the engine combustion analysis kit. Switch ON the computer. Allow sufficient water flow for the calorimeter, i.e., 80 mL/s. Ensure the dynamometer load control knob is in the zero position.
Start the water pump and ensure the water flows out of the calorimeter’s drainpipe. The injection timing is optimized and set to 23° before the Top Dead Center (TDC) (static). This precise timing is maintained across various operating modes. Prior to conducting the experiment, the engine is allowed to run for 10 min to achieve a steady state. Baseline data is first collected by performing experiments using diesel fuel, with the engine running for the same 10-minute duration to ensure steady-state conditions are reached before starting the tests.
The engine speed is held constant at 1,500 rpm across all load conditions. Slowly increase the load to 25% of the full load and note down readings as per the tabular column. The engine is loaded by 25%, 50%, 75%, and 100% of rated load (6 kg). Data are procured for each load step, ensuring the speed remains stable at 1,500 rpm. The percentage variation in engine speed at each load condition is less than 1%. Once the experiment is finished, reduce the engine speed gradually. Switch OFF the Mains. Close the water line. The uncertainties of the measured parameters are provided in the Supplementary Material.
Investigations are carried out using waste plastic pyrolysis oil, ethanol, and pure diesel fuel at a constant speed of 1,500 rpm at 25%, 50%, 75%, and 100% full load conditions. At each load condition, various performance and emissions analyses are performed. The data were procured from the DAQ system as the average of 15-minute intervals, and the experiments were conducted three times to ensure reliability. The average values from these trials have been presented in the results section to ensure accuracy and consistency.
BTHE reflects the combustion system’s capability to utilize the experimental fuel and serves as a reliable metric for evaluating the efficiency with which the energy in the fuel is converted into mechanical output (Zhu et al., 2011). The variation of BTHE at different load conditions when the engine was operated with diesel, diesel-WPPO and diesel-WPPO with ethanol is shown in Figure 8. BTHE is the true indicator of efficiency with which the chemical energy input in the form of fuel of converted into useful work. It is observed that the BTHE increases with load for all fuel.
BTHE is slightly higher for fuel blends compared to diesel at higher loads, while at lower loads, it remains comparable to that of diesel. This can be attributed to the rapid premixed combustion part possessed by WPPO blends because of improved mixing during ignition delay oxygen enrichment, leading to higher energy release, higher pressure development and better combustion (Putrasari et al., 2013). The enhancement of the diffusive combustion phase can be attributed to oxygen enrichment. The heat release process is nearly complete at the same crank angle, which further supports the faster diffusive burning phases observed in various blends. As a result, the energy consumption rate of the blends decreased, while BTHE increased, as reported in the literature.
As shown in Figure 8, the thermal efficiency is 28.34% at full load when using diesel. However, when the engine is fueled with WPO-diesel blends, such as 20% WPPO and 40% WPPO, the thermal efficiency at full load is 27.55% and 27.87%, respectively. For WPPO-ethanol-diesel blends, such as 15% WPPO, 5% ethanol, and 80% diesel, and 25% WPPO, 10% ethanol, and 65% diesel, the thermal efficiencies at full load are 28.65% and 28.99%, respectively. It is evident that the BTHE of the WPPO-diesel blend is slightly lower than that of pure diesel, likely due to the lower calorific value of the WPPO-diesel blend compared to diesel, as WPPO has a lower calorific value. However, the exhaust gas temperature is marginally lower for the blend than for diesel. At full load, the blends in BL2 show a 1.23% improvement over diesel, while BL1 exhibits an increasing trend, though it remains 0.31% lower than diesel. The higher BTHE observed for BL1 and BL2 at different load conditions may be due to their improved combustion characteristics at the tested load conditions, despite their slightly lower calorific value compared to diesel.
This can be attributed to the presence of ethanol, which acts as a viscosity improver, as well as the higher oxygen content, which enhances combustion efficiency by facilitating higher temperatures during combustion (Roy MurariMohon et al., 2014).
bsfc is the ratio between mass fuel consumption and brake power. Figure 9 shows the comparison of bsfc of various blends at varying loads. As evident from Figure 9 bsfc shows a persistent trend of reduction with load for all fuel, which may be due to the higher percentage increase in brake power with load compared to the increase in fuel consumption. For the blend, BL1 bsfc is comparable and slightly more comparable to diesel, respectively. This could be attributed to the dissolved oxygen in the ethanol blend, which promotes complete combustion, preventing the negative effects associated with increased viscosity. However, as the WPPO concentration in the blend increases further, the bsfc rises at all loads, with a higher percentage increase observed at lower loads and a nearly constant increase at higher loads. This can be shown for the bsfc of blends BL2, are 3.66% lower than diesel, while BL1, BL3 and BL4 are 3.21%, 9.28% and 7.03% higher than diesel at full load condition.
bsfc is approximately lower than the standard diesel (BL2 for full load and BL1, BL2 at 75% of rated load). This might be due to higher oxygen content and better combustion process (Graboski et al., 2003). While with increase in the WPPO content in the blend, the bsfc tends to increase with respect to diesel. In addition to the high viscosity of the blends may also inhibit the proper atomisation of the fuel, which in turn affects the combustion process. The bsfc also depends on the relationship between the fuel injection system, fuel properties, fuel oxygenation nature, and higher viscosity and lower calorific value. These effects significantly impact combustion. Due to the greater density of the experimental fuel, a higher mass of fuel is injected into the combustion chamber for the same volume compared to the amount of diesel injected.
UHC emissions arise from incomplete combustion. As the load increases, more complete combustion occurs, resulting in a reduction in UHC emissions, as illustrated in Figure 10. The UHC emissions increase as the load increases and are maximum at full load condition; this might be due to the enrichment of air-fuel mixture, and the lesser air is available at higher load condition. Unburnt hydrocarbon emissions are primarily caused by incomplete combustion, deposition on the walls of the combustion chamber, and other factors (Salvi and Jindal, 2013). For ethanol-blended WPPO–diesel blends, a reduction in unburnt hydrocarbon emissions is observed at low concentrations, while at higher concentrations, the emissions tend to increase.
UHC emissions are obtained from the engine exhaust due to incomplete combustion of the experimental fuel in the combustion chamber (Özener et al., 2014). As the load increases, complete combustion is attained, resulting in a reduction of UHC emissions. The WPPO-ethanol-diesel-based blends is successively reduced UHC emissions, where BL2 showed 10.35% lower than diesel and BL1 by 6.66% lower, whereas BL3 and BL4 showed 8.57% and 1.54% higher as compared to that of base diesel at full load condition which may be due to the enrichment of air-fuel mixture admission with insufficient supply of air (Rashedul et al., 2014).
NO is formed through the reaction of nitrogen and oxygen at elevated temperatures and is a significant component of NOx emissions (Hulwan and Joshi, 2011). The formation of NO for diesel, BL1, BL2, BL3 and BL4 are shown in Figure 11. The NO values for diesel vary from 123.7 ppm at 25% load and 427 ppm at full load. For BL1, it varies from 115 ppm at 25% load and 355.7 ppm at full load. For BL2, BL3 and BL4, it varies from 119 to 351 ppm, 140 ppm–440 ppm and 160 to 496 at 25% load to full load condition. BL1 and BL2 have shown 20.1% and 21.7% lower NO emissions than diesel emissions. The NO formed increases as the load increases. The NO emissions from the blends decrease as the percentage of ethanol in the WPPO blend increases. Ethanol, with its high oxygen content and high heat of evaporation (Fuel Additives, 2024), facilitates easier ignition of the fuel-air mixture and results in a shorter combustion duration. The addition of ethanol reduces heat release during the diffusion-controlled combustion phase, leading to lower NO emissions. Ethanol’s latent heat of vaporization (900 kJ/kg) is higher than that of conventional diesel (600 kJ/kg). Furthermore, experimental studies with various fuel blends containing oxygen have shown that NO emissions decrease due to the reduced high-temperature duration experienced by the combustion gases.
Figure 12 illustrates the variations in CO emissions as a function of blend ratios and engine loads. As expected, CO emissions decrease with increasing load, as more complete combustion occurs at higher loads. CO, an intermediate combustion product, is primarily formed due to insufficient oxygen and incomplete fuel combustion. Compared to baseline diesel, WPPO-blended fuels result in lower CO emissions, as WPPO has a higher cetane number and greater heat of vaporization requirements than diesel (Hulwan and Joshi, 2011). However, ethanol-WPPO blended fuels exhibit a lower cetane number and longer ignition delay, leading to incomplete combustion in the cylinder and higher CO emissions in the exhaust compared to pure WPPO fuels. If combustion is complete, CO is converted into CO2; otherwise, the lack of sufficient air leads to the formation of CO.
Thus, carbon monoxide is an indication of the combustion characteristics of fuels. The CO emission of all blends is less than that of the base diesel. The CO emissions of blends BL1, BL2, BL3, and BL4 are 0.2%, 0.2%, 25%, and 25%, respectively, less than the diesel in full load condition.
The main objective of the present investigations is to utilise the potential of waste plastic pyrolysis oil and study the performance and emissions characteristic of an IDI diesel engine fuelled with different blends. This study investigated the effect of using different blends on the performance and emission characteristics of an unmodified IDI diesel engine. From the tests conducted with diesel and waste plastic pyrolysis oil blend, the following conclusions can be drawn:
• The brake thermal efficiency of blend BL2 is slightly greater than that of conventional diesel at all biodiesel loading conditions. At full load conditions, the blends BL2 are 1.3% greater than diesels. Blend BL1, BL3, and BL4 are comparable at full load conditions.
• As evident from results obtained for brake-specific fuel consumption, the value of bsfc for all fuels decreases with an increase in load. Blends BL1 and BL2 at lower loads perform nearly the same as those with diesel. While at increased load, all the blends perform almost the same, whereas overall blend BL2 outperforms diesel, with approximately blend BL2 being 3.7% lower while blend BL1, BL3 and BL4 are 3.2%, 9.282% and 7.6% higher as compared with diesel at full load respectively.
• The unburned hydrocarbon (UHC) emissions are where WPPO-ethanol blends are expected to perform better than diesel. For WPPO, the UHC emissions at full loading conditions BL2 and BL4 are consistently lower than diesel. Meanwhile, in half-loading conditions, the UHC emissions of all blends are higher than those of diesel except BL2 and BL1. BL1 and BL2 are 6.7% and 10.4% lower, while BL3 and BL4 are 8.6% and 1.5% higher than diesel at full load, respectively.
• NO emission is the area where the use of WPPO suffers a setback. Because of the presence of more oxygen and higher temperature, NO emissions are higher in the case of WPPO. As shown in the results and discussion, all blends’ NO emission is higher than diesel at all loads. In comparison, the blend contains more ethanol percentage that has a tendency of minimise nitric oxide emission. NO emission for blends BL1, BL2 and BL3 BL4 is 20.1%, 21.7% lower and 2.9% and 13.9% higher than diesel at full load, respectively.
• The CO emission of all blends is lower than that of D100. This may be possible due to the higher oxygen content in blends of WPPO, which results in complete combustion, which converts CO into CO2. The CO emissions of blends BL1, BL2, BL3, and BL4 are 0.2%, 0.2%, 25% and 25%, respectively, less than the diesel in full load condition.
From experimental results, it is clear that WPPO is a viable alternative fuel for internal combustion (IC) engines. The blends BL1 and BL2 have shown promising performance and emission characteristics, suggesting that they could potentially serve as supplementary fuels to diesel in IC engines.
The raw data supporting the conclusions of this article will be made available by the authors, without undue reservation.
MB: Conceptualization, Data curation, Formal Analysis, Funding acquisition, Investigation, Methodology, Project administration, Resources, Software, Supervision, Validation, Visualization, Writing–original draft. MD: Methodology, Supervision, Validation, Writing–review and editing. GS: Conceptualization, Formal Analysis, Funding acquisition, Project administration, Resources, Supervision, Writing–review and editing.
The author(s) declare that no financial support was received for the research, and/or publication of this article.
The authors declare that the research was conducted in the absence of any commercial or financial relationships that could be construed as a potential conflict of interest.
The author(s) declare that no Generative AI was used in the creation of this manuscript.
All claims expressed in this article are solely those of the authors and do not necessarily represent those of their affiliated organizations, or those of the publisher, the editors and the reviewers. Any product that may be evaluated in this article, or claim that may be made by its manufacturer, is not guaranteed or endorsed by the publisher.
The Supplementary Material for this article can be found online at: https://www.frontiersin.org/articles/10.3389/fther.2025.1548806/full#supplementary-material
Arvanitoyannis, I. S., and Tserkezou, P. (2008). Cereal waste management: treatment methods and potential uses of treated waste. Waste Manag. Food Industries, 629–702. doi:10.1016/b978-012373654-3.50013-4
Bose, P. K., Deb, M., Banerjee, R., and Majumder, A. (2013). Multi objective optimization of performance parameters of a single cylinder diesel engine running with hydrogen using a Taguchi-fuzzy based approach. Energy 63, 375–386. doi:10.1016/j.energy.2013.10.045
Cardona, C. A., and Sánchez, Ó. J. (2007). Fuel ethanol production: process design trends and integration opportunities. Bioresour. Technol. 98, 2415–2457. doi:10.1016/j.biortech.2007.01.002
Deb, M., Banerjee, R., Majumder, A., and Sastry, G. R. K. (2014). Multi objective optimization of performance parameters of a single cylinder diesel engine with hydrogen as a dual fuel using pareto-based genetic algorithm. Int. J. Hydrogen Energy 39 (Issue 15), 8063–8077. ISSN 0360-3199. doi:10.1016/j.ijhydene.2014.03.045
Deb, M., et al. (2015c). Effect of hydrogen-diesel dual fuel combustion on the performance and emission characteristics of a four stroke-single cylinder diesel engine. World Acad. Sci. Eng. Technol. Int. J. Mech. Aerosp. Industrial, Mechatron. Manuf. Eng. 9 (6), 885–891.
Deb, M., Paul, A., Debroy, D., Sastry, G., Panua, R. S., and Bose, P. (2015a). An experimental investigation of performance-emission trade off characteristics of a CI engine using hydrogen as dual fuel. Energy 85, 569–585. doi:10.1016/j.energy.2015.03.108
Deb, M., Sastry, G., Bose, P., and Banerjee, R. (2015b). An experimental study on combustion, performance and emission analysis of a single cylinder, 4-stroke DI-diesel engine using hydrogen in dual fuel mode of operation. Int. J. Hydrogen Energy 40 (27), 8586–8598. doi:10.1016/j.ijhydene.2015.04.125
Devaraj, J., Robinson, Y., and Ganapathi, P. (2015). Experimental investigation of performance, emission and combustion characteristics of waste plastic pyrolysis oil blended with diethyl ether used as fuel for diesel engine. Energy 85, 304–309. doi:10.1016/j.energy.2015.03.075
Etymonline (2011). Plastic, online etymology dictionary. Available online at: Etymonline.com (Accessed July 01, 2011).
Fuel Additives (2024). Use and benefits: technical committee of petroleum additive manufacturers in europe, september 2013/atc document 113. Available online at: https://www.atc-europe.org/showdoc.asp?doc_id=1461.
Graboski, M. S., McCormick, R. L., Alleman, T. L., and Herring, A. M. (2003). The effect of biodiesel composition on engine emissions from a DDC series 60 diesel engine. National Renewable Energy Laboratory: Golden, Colorado. (Report No: NREL/SR-510-31461).
Hansdah, D., Murugan, S., and Das, L. (2012). Experimental studies on a DI diesel engine fueled with bioethanol-diesel emulsions. Alexandria Eng. J. 52, 267–276. doi:10.1016/j.aej.2013.06.001
Hulwan, D. B., and Joshi, S. V. (2011). Performance, emission and combustion characteristic of a multicylinder DI diesel engine running on diesel–ethanol–biodiesel blends of high ethanol content. Appl. Energy 88 (12), 5042–5055. doi:10.1016/j.apenergy.2011.07.008
Hunicz, J., Rybak, A., Szpica, D., Gęca, M. S., Woś, P., Yang, L., et al. (2024). Waste plastic pyrolysis oils as diesel fuel blending components: detailed analysis of combustion and emissions sensitivity to engine control parameters. Energy 313, 134093. doi:10.1016/j.energy.2024.134093
Kumar, S., Prakash, R., Murugan, S., and Singh, R. K. (2013). Performance and emission analysis of blends of waste plastic oil obtained by catalytic pyrolysis of waste HDPE with diesel in a CI engine. Energy Convers. Manag. 74, 323–331. doi:10.1016/j.enconman.2013.05.028
Kumar, S. K. (2013). Performance and emission analysis of diesel engine using fish oil and biodiesel blends with isobutanol as an additive. Am. J. Eng. Res. (AJER) 2, 322–329.
Lee, K.-H. (2009). Thermal and catalytic degradation of pyrolytic oil from pyrolysis of municipal plastic wastes. J. Anal. Appl. Pyrolysis 85 (Issues 1–2), 372–379. doi:10.1016/j.jaap.2008.11.032
Mani, M., Subash, C., and Nagarajan, G. (2009). Performance, emission and combustion characteristics of a DI diesel engine using waste plastic oil. Appl. Therm. Eng. 29 (13), 2738–2744. doi:10.1016/j.applthermaleng.2009.01.007
Masum, B. M., Masjuki, H. H., Kalam, M. A., Rizwanul Fattah, I. M., Palash, S. M., and Abedin, M. J. (2013). Effect of ethanol–gasoline blend on NOx emission in SI engine. Renew. Sustain Energy Rev. 24, 209–222. doi:10.1016/j.rser.2013.03.046
Miskolczi, N., Angyal, A., Bartha, L., and Valkai, I. (2009). Fuels by pyrolysis of waste plastics from agricultural and packaging sectors in a pilot scale reactor. Fuel Process. Technol. 90 (Issues 7–8), 1032–1040. doi:10.1016/j.fuproc.2009.04.019
Mofijur, M., Rasul, M. G., and Hyde, J. (2015). Recent developments on internal combustion engine performance and emissions fuelled with biodiesel-diesel-ethanol blends. Procedia Eng. 105, 658–664. doi:10.1016/j.proeng.2015.05.045
Moriya, S., Watanabe, H., Yaginuma, R., Matsumoto, T., Nakajima, M., Tsukada, M., et al. (2000). Studied of recycled fuel oil for diesel engine extracted from waste plastics disposals. Energy Convers. Eng. Conf. Exhib. 1, 510–515. (IECEC), 35th Intersociety. doi:10.1109/iecec.2000.870749
Özener, O., Yüksek, L., Ergenç, A. T., and Özkan, M. (2014). Effects of soybean biodiesel on a DI diesel engine performance, emission and combustion characteristics. Fuel 115, 875–883. doi:10.1016/j.fuel.2012.10.081
Paul, A., Bose, P. K., Panua, R., and Debroy, D. (2015a). Study of performance and emission characteristics of a single cylinder CI engine using diethyl ether and ethanol blends. J. Energy Inst. 88 (1), 1–10. doi:10.1016/j.joei.2014.07.001
Paul, A., Panua, R. S., Debroy, D., and Bose, P. K. (2015b). An experimental study of the performance, combustion and emission characteristics of a CI engine under dual fuel mode using CNG and oxygenated pilot fuel blends. Energy 86, 560–573. doi:10.1016/j.energy.2015.04.050
Plastikos, H. G. L., and Scott, R. (2011). A Greek-English lexicon, at perseus. Available online at: Perseus.tufts.edu (Accessed July 01, 2011).
Pratoomyod, J., and Laohalidanond, K. (2024). Performance and emission evaluation of blends of diesel fuel with waste plastic oil in a diesel engine. Carbon 79, 75–99.
Putrasari, Y., Nur, A., and Muharam, A. (2013). Performance and emission characteristic on a two cylinder DI diesel engine fuelled with ethanol-diesel blends. Energy Procedia 32, 21–30. doi:10.1016/j.egypro.2013.05.004
Rashedul, H. K., Masjuki, H., Kalam, M., Ashraful, A., Ashrafur Rahman, S., and Shahir, S. (2014). The effect of additives on properties, performance and emission of biodiesel fuelled compression ignition engine. Energy Convers. Manag. 88, 348–364. doi:10.1016/j.enconman.2014.08.034
Roy, M. M., Wang, W., and Alawi, M. (2014a). Performance and emissions of a diesel engine fueled by biodiesel–diesel, biodiesel–diesel-additive and kerosene–biodiesel blends. Energy Convers. Manag. 84 (2014), 164–173. doi:10.1016/j.enconman.2014.04.033
Salvi, B. L., and Jindal, S. (2013). A comparative study of engine performance and exhaust emissions characteristics of linseed oil biodiesel blends with diesel fuel in a direct injection diesel engine. J. Inst. Eng. India Ser.C 94 (1), 1–8. doi:10.1007/s40032-013-0057-1
Soloiu, A., Yoshinobu, Y., Masakatsu, H., Kazuie, N., Yasuhito, M., and Yasufumi, N. (2000). The investigation of a new diesel produced from waste plastics. ISME.
Sudhir Kumar, J. (2013). Performance and emission characteristics of spark ignition engine fuelled with plastic petrol derived from waste plastic. Int. J. Multidiscip. Curr. Res.
Vedaraman, N., Puhan, S., Nagarajan, G., and Velappan, K. (2011). Preparation of palm oil biodiesel and effect of various additives on NOx emission reduction in B20: an experimental study. Int. J. Green Energy 8, 383–397. doi:10.1080/15435075.2011.557847
Vu, P. H., Nishida, O., Fujita, H., Harano, W., Toyoshima, N., and Iteya, M. (2001). Reduction of NOx and PM from diesel engines by WPD emulsified fuel. SAE Technical Paper. doi:10.4271/2001-01-0152
AnupT, J., and Vilas, W. (2014). Waste plastic pyrolysis oil as alternative for SI and CI engines. International Journal of Innovative Research in Science, Engineering and Technology 3 (7).
Williams, P. T., and Williams, E. A. (1990). Interaction of plastics in mixed plastics pyrolysis. J. Energy Fuels 13, 188–196. doi:10.1021/ef980163x
Keywords: waste plastic pyrolysis oil (WPPO), diesel engine performance, emission characteristics, alternative fuels, brake thermal efficiency
Citation: Bhowmik M, Deb M and Sastry GRK (2025) Performance and emission assessment of an indirect ignition diesel engine fuelled with waste plastic pyrolysis oil and ethanol blends. Front. Therm. Eng. 5:1548806. doi: 10.3389/fther.2025.1548806
Received: 06 January 2025; Accepted: 27 February 2025;
Published: 02 April 2025.
Edited by:
Pradip Mondal, SR University, IndiaReviewed by:
Ambarish Datta, Memari Government Polytechnic, IndiaCopyright © 2025 Bhowmik, Deb and Sastry. This is an open-access article distributed under the terms of the Creative Commons Attribution License (CC BY). The use, distribution or reproduction in other forums is permitted, provided the original author(s) and the copyright owner(s) are credited and that the original publication in this journal is cited, in accordance with accepted academic practice. No use, distribution or reproduction is permitted which does not comply with these terms.
*Correspondence: Mrinal Bhowmik, bXJpbmFsYmhvd21pa0BuaXRtYW5pcHVyLmFjLmlu, bXJpbmFsYmhvd21pazAyQGdtYWlsLmNvbQ==
†Present addresses: Mrinal Bhowmik, Department of Engineering, Durham University, Durham, United Kingdom
G. R. K. Sastry, Department of Mechanical Engineering, National Institute of Technology Andhra Pradesh, Andhra Pradesh, India
Disclaimer: All claims expressed in this article are solely those of the authors and do not necessarily represent those of their affiliated organizations, or those of the publisher, the editors and the reviewers. Any product that may be evaluated in this article or claim that may be made by its manufacturer is not guaranteed or endorsed by the publisher.
Research integrity at Frontiers
Learn more about the work of our research integrity team to safeguard the quality of each article we publish.