- 1Division of Energy Technology, Chalmers University of Technology, Göteborg, Sweden
- 2SINTEF Energy Research, Trondheim, Norway
The pulp and paper industry has an important role in the industrial transition towards net zero or negative emissions, given its renewable biomass-based feedstock and energy supply. In particular, pulp and paper mills have large existing sources of biogenic CO2, with a high potential to contribute to carbon dioxide removal through carbon capture and storage (CCS). To effectively navigate anticipated changes in feedstock and energy markets, there is a need for a better understanding of how different technology pathways for the pulp and paper industry interact with one another, for instance, how enhanced valorization of biomass side streams may affect the potential for carbon capture. This paper aims to investigate the effect of combining carbon capture with lignin extraction in a chemical pulp mill. Pinch analysis is used to study how the targets for heat recovery, fuel usage and electricity generation, are affected by different mill and capture configurations. Based on these results, the effect on carbon flows is evaluated. The results show that when carbon capture technology is implemented and fuel use is minimized at the case-study mill, there is still enough heat available from the recovery boilers to supply the process needs without requiring usage of a utility boiler. However, when carbon capture is combined with lignin extraction, the heat production of the recovery boilers is no longer sufficient to cover the process demands, and additional heat from a utility boiler is required. However, this case implies that some of the carbon leaves the mill embedded in the extracted lignin product, which can be expected to have a higher value than captured carbon dioxide. When back-pressure electricity production was maximized for the different mill configurations, a very high fuel-to-electricity efficiency could be achieved, but since the CO2 emissions from the utility boiler were not assumed to be captured, this would lead to more carbon being emitted compared to the capture scenarios with minimized fuel use.
1 Introduction
Carbon dioxide removal (CDR) technologies will have an important role in reaching climate targets, by compensating for residual emissions from hard-to-abate sectors and allowing for net negative emissions. Bio-Energy Carbon Capture and Storage (BECCS) is one of few CDR technologies that can be implemented on a large scale and deliver secure long-term storage of the CO2 in a relatively cost-efficient way (Fajardy et al., 2021). A major limitation for BECCS, however, is the access to sustainable sources of biomass and biogenic carbon that can be captured. A number of studies have raised concerns that large-scale implementation of purpose-grown biomass for BECCS could have many negative effects including, but not limited to, loss of biodiversity, increased competition for agricultural land, and increased emissions due to land use change (Smith et al., 2016; Hanssen et al., 2022).
Kraft pulp mills have been shown to be promising candidates for BECCS, since they have large existing point sources of biogenic CO2 emissions, originating from biomass that is used primarily for production of useful materials. More specifically, pulp mills use biomass as feedstock to produce pulp and by-products, such as turpentine and tall oil. The kraft-pulping process is energy-intensive and has large emissions of biogenic CO2 mainly due to the combustion of black liquor. Black liquor is a slurry of spent processing chemicals and biogenic compounds, and the combustion of the liquor is an important part of the regeneration of the processing chemicals that also supply energy to the process.
Kuparinen et al. (2019) estimated the global technical potential for capture of (mainly biogenic) CO2 from kraft pulp mills to 135 Mt/yr. Recently, Rosa et al. (2021) estimated the technical potential for biogenic CDR from existing point sources in 30 European countries, and found the potential for CDR from pulp and paper plants to be 62 (+/-5) Mt/yr. This is similar to previously reported potentials for BECCS in the pulp and paper industry, with estimates of 60 Mt/yr in Europe (Jönsson and Berntsson, 2012). A large share of this BECCS potential is found in Sweden (Hansson et al., 2017; Rootzén et al., 2018) and in Finland (Kuparinen et al., 2019), each with annual emissions from chemical pulp mills of around 20 Mt/yr.
With increasing demands for renewable carbon resources from other sectors, the pulp and paper industry is under pressure to strive towards better utilization of the biomass resource, and to convert a larger share of the biomass feedstock into valuable products. This can be enabled by integration of new technologies and processes for extraction and valorization of side streams from the pulp by-products. For example, there are opportunities for extracting renewable and valuable chemicals from the kraft black liquor (Akbari et al., 2018; Pola et al., 2022). One such possibility is the extraction of lignin (Hubbe et al., 2019), which can be further processed into biochemicals, biomaterials or biofuels (Téguia et al., 2017). By extracting the lignin from the black liquor, the amount of biomass that is combusted is reduced, but another valuable by-product is produced. Another advantage of lignin extraction is that the heat transfer area of recovery boilers is often the main bottleneck for mill throughput, and by removing some of the lignin from the black liquor, this bottleneck can be removed, and production increased (Vakkilainen and Välimäki, 2009).
Other opportunities for biomass valorization in pulp mills, which have attracted attention in recent literature include the integration of various biorefinery processes with the mill. Results by Granacher et al. (2022) show that pulp-mill integrated biorefineries is an economically viable way to achieve better resource utilization [see also Granacher et al. (2023) for a general overview of pulp mill biorefinery options]. More specifically, Geleynse et al. (2020) investigated the integration of lignocellulosic ethanol fermentation for alcohol-to-jet fuel production in a pulp mill. Ong et al. (2020) proposed a kraft mill-integrated design for a hydrothermal liquefaction process. Mongkhonsiri et al. (2020) designed a biomass gasification process for integration in a pulp mill, aiming to produce of succinic acid and DME. Ribeiro Domingos et al. (2021) compared different black liquor gasification routes for production of methanol and dimethyl ether (DME).
Alternatively, or additionally, to recover the biogenic carbon by extracting side streams from the pulping process, the biogenic carbon could be recovered through “end-of-pipe” capture from mill flue gas streams. The captured CO2 could then be utilized for production of bio-based chemicals in Carbon Capture and Utilization (CCU) concepts. For example, the CO2 could be reacted with hydrogen produced via electrolysis to form methanol (Marlin et al., 2018). On-site opportunities for CO2 utilization in Kraft pulp mills include, e.g., tall oil manufacturing, lignin extraction and production of precipitated calcium carbonate (Kuparinen et al., 2019).
New process concepts are also being developed, which could replace core process units in the mills with new technologies that could reduce the use of fuel and combustion-related emissions and/or provide opportunities for more efficient capture of CO2. Some of these opportunities involve replacing the lime kiln, which is the conventional calcination process, either by an oxyfuel combustion or an electrified plasma calcination process (Lefvert and Grönkvist, 2023). Amongst other potential benefits, the CO2 from the calcination reaction would then be obtained as a pure stream that could be captured directly without the need for separation from a flue gas (Svensson et al., 2021). Another novel concept, that was recently evaluated, could be to replace the conventional power boiler (fluidized bed) with a chemical looping combustion system with oxygen uncoupling (Saari et al., 2023). However, while small-scale capture from the calcination process can be very efficient, larger-scale capture is typically required to reach acceptable economies of scale for BECCS applications. And with regards to the scale of capture from the power boiler, this will only be significant in larger integrated pulp and paper mills, while the power boiler is used to a much lesser extent in efficient pulp-only mills.
To manage the energy balances of the mill when a larger share of the biomass is valorized as by-products and no longer is available for combustion on-site, or when new heat demands are introduced, such process changes must typically also be combined with energy efficiency improvements and/or electrification of heat production (Lipiäinen et al., 2023). When investigating a potential future integration of carbon capture in a pulp or paper mill, it is thus also necessary to consider the expected strategic development in the mill and investigate how new process concepts may affect the potential for carbon capture and the site-wide energy balances.
Several studies have investigated the integration of post-combustion amine-based carbon capture in the chemical pulping industry. More recent examples include the work by Onarheim et al. (2017a), Onarheim et al. (2017b), Kuparinen et al. (2023) and Nwaoha and Tontiwachwithikul (2019). These studies have investigated heat integration opportunities, effects on mill energy balances, as well as capture and emission avoidance costs for different capture configurations applied to different flue gas sources (recovery boiler, lime kiln and power boilers) of a chosen, conventional, case study mill, without consideration of simultaneous implementation of other strategic mill development projects.
Only a few studies have considered the potential combination of carbon capture and other emerging process developments. For example, Möllersten et al. (2003) included the option of replacing the conventional recovery boiler with a black liquor gasification plant with pre-combustion CO2 capture in their study on potential for CO2 reductions in Swedish pulp and paper industry. Möllersten et al. (2006) also investigated CCS in combination with biomass gasification as a replacement for the conventional power boiler systems. More recently, Santos et al. (2021) proposed a new process concept based on calcium looping, which would replace a large part of the conventional chemical recovery cycle while also allowing for efficient capture of CO2. Solid looping is an emerging concept, which seems to have promising techno-economic potential for carbon capture in several industrial sectors, including pulp and paper (Santos and Hanak, 2022). In a recent paper by Mendoza-Martinez et al. (2022), hydrothermal carbonation (HTC) of bio-sludge generated from wastewater treatment was investigated in a mill that was also assumed to have integrated post-combustion carbon capture on the recovery boiler and lime kiln. The biochar produced from the HTC process offers further potential for carbon removal.
Skagestad et al. (2018) investigated the total capture cost for different capture integration cases representing full or partial CO2 capture in a model mill. For this mill, which represents a modern, energy-efficient mill using best available technologies, a significant amount of excess steam is available from the recovery boiler. When sizing a partial capture plant to use only this excess energy and no additional fuel, partial capture could be achieved at considerably lower specific capture cost than full capture. In the same paper, Skagestad et al. (2018) also evaluated a CCU case, in which a part flow of the captured CO2 is assumed to be utilized for lignin extraction. For this scenario, they also analyzed the effect of lignin extraction on the capture potential and emissions from the mill. However, for this case, only the partial capture scenario was considered, where the CO2 capture rate was limited to the amount of CO2 that could be captured using excess steam from the recovery boiler.
This paper aims to investigate the effect of integrating full-scale (90%) carbon capture on the recovery boiler and lime kiln in a pulp mill, which is also assumed to implement a large-scale lignin extraction plant. To our knowledge, this is the first published case study of a real pulp mill for which the combined integration of lignin extraction and carbon capture is analyzed. Compared to the ideal model mills previously studied in literature the mill can be assumed to have a less favorable energy balance, thus being more representative for integration of new technology in mills in the near term. The study illustrates the need to consider the interaction between different technology pathways for the industrial energy and climate transition, where in this case, the pulp mill can contribute to decarbonization by making either biogenic CO2 or biomass resources available for carbon dioxide removals or for replacing fossil carbon sources in other sites or sectors. The paper offers a different perspective on renewable energy integration focusing on a sector where the majority of the thermal energy supply already comes from renewable energy (in the form of biomass). On the other hand, the thermal energy systems of these sites may be strongly affected by the integration of new technology, thereby changing the conditions for the efficient use of these renewable resources.
2 Materials and methods
Hubbe (2021) reviewed the literature for state of the art approaches to improve the energy efficiency of pulp and paper mills. The extensive review discusses methods based on thermodynamic principles such as exergy analysis and pinch analysis, as well as energy management practices and energy audits.
In this study, pinch analysis was used to estimate how the heat balances of a case study mill may be affected by the integration of a carbon capture process, and how this may differ if the mill is also assumed to implement a lignin extraction process. The impact of changes in heat balances on the overall fuel demand and electricity generation potential in the mill was analyzed for two different scenarios: one in which additional (biomass) fuel use is minimized, and one in which the back-pressure steam turbine power generation is maximized. Furthermore, the utilization of the biogenic carbon in the feedstock was analyzed with regards to the amount of carbon that is converted into useful products.
The case study mill is described in Section 2.1. Then, in Sections 2.2 and 2.3, the modelling of the carbon capture and liquefaction process and the lignin extraction process are described. In Section 2.4, the pinch-based energy targeting approach is explained, and the different integration cases and optimization scenarios defined.
2.1 Case study mill
For this study, a kraft pulp mill in Sweden producing about 0.5 million tonnes of pulp per year from birch and conifer feedstock was used as a case study. The mill is a stand-alone market pulp mill, which means it does not have integrated paper production.
A simplified flow chart of the kraft pulp process is shown in Figure 1. In the cooking plant, lignin is dissolved and separated from cellulose fibers using white liquor, which is a water-based solution with sodium hydroxide and sodium sulfide. The separated cellulose fibers are further processed into the finished pulp product, while the liquor with the dissolved lignin and the spent cooking chemicals, referred to as black liquor, is processed in the recovery cycle to regenerate the cooking chemicals and recover the energy content of the organic components (mainly lignin and hemicelluloses) of the liquor.
For efficient combustion of the black liquor, the water content must be reduced significantly. This is done in the evaporation section where the dry solids content is increased from about 20% to 70%–72%. The evaporation section consists of a series of integrated evaporator effects where the first one uses low pressure steam as heat source, and the following effects use vapor from the previous effect to drive the evaporation.
The concentrated black liquor from the evaporation section is sprayed into the recovery boilers, where the organic components are combusted and some of the chemical reactions necessary to recover the cooking chemicals take place. The combustion generates large amounts of biogenic carbon dioxide in the flue gas. However, some of the carbon that enters with the black liquor is also converted to carbonates, which leave the recovery boiler together with the other inorganic chemicals as a smelt, which is dissolved in water to form so-called green liquor.
In the causticization section, green liquor is mixed with burnt lime (calcium oxide) to form white liquor. This is achieved in a series of reactions, where the burnt lime first reacts with the water of the green liquor, forming calcium hydroxide (slaked lime), which in turn reacts with the sodium carbonate of the green liquor to form sodium hydroxide and calcium carbonate. The calcium carbonate is separated from the liquor and sent to the lime kiln to be regenerated into burnt lime, and the liquor is now regenerated into white liquor, that can be reused in the cooking. The regeneration of burnt lime from calcium carbonate in the lime kilns requires energy at high temperatures. At the studied mill, this energy is supplied using tall oil pitch as fuel. Tall oil pitch is a biofuel, which is a residue from the processing of crude tall oil into tall oil. When the calcium carbonate is oxidized to calcium oxide, carbon dioxide is formed, which will exit the lime kiln with the flue gas. Through the series of reactions explained above, this carbon originates from the organic components in the black liquor and is thus considered to be biogenic carbon dioxide. Since the lime kiln flue gas contains carbon dioxide both from the oxidization of the lime and from the combustion of (bio-) fuel, the carbon dioxide concentration of the flue gas is usually high.
Pulp mills are energy-intensive industrial plants that consume large amounts of heat and electricity. However, like most modern, energy-efficient market kraft pulp mills, the case study mill is essentially self-sufficient in heat supply from internally generated fuel by-products. In fact, the mill currently operates completely free from fossil fuels. Most of the steam demand (including steam for turbines, which cover a large share of the mill’s electric power demand) is covered by steam generated through black liquor combustion in the mill’s recovery boilers. To a smaller extent, the mill’s steam demand is currently also supplemented by combustion of bark and other internally generated wood fuels in the power boiler.
The steam generated in the boilers is fed to a high-pressure steam header. This steam is expanded through a back-pressure, extraction steam turbine, or, if necessary, through direct expansion valves to medium-pressure and low-pressure steam headers. Pressure and temperature specifications for the steam headers are presented in Table 1. In the mill, medium-pressure and low-pressure steam is used in various parts of the process, mainly to supply heat through heat exchangers but also by mixing the steam with process streams directly.
Process cooling in the mill is achieved via the secondary heat recovery system. Process streams are cooled with water, which is heated to warm or hot water temperatures and sent to the water tanks of the secondary heating system. The water is then used for heating and as process or cleaning water in various parts of the mill. Additional cooling at the mill is done using cooling towers to cool dirty water before wastewater treatment.
As a basis for the heat integration analysis (see Section 2.4), all process heating and cooling demands in the mill were mapped according to their heat flows and temperature levels (see Section 12).
Table 2 reports flue gas data for all CO2 emission sources in the mill. The two recovery boilers have separate stacks, with different flue gas treatment systems installed. Flue gases from the larger recovery boiler go through a convective section with a superheater and economizer before being passed through an electrostatic filter and then sent to the stack. In the smaller recovery boiler, the flue gases also go through a superheater first, but then pass through an electrostatic filter before going to the economizer. These flue gases also pass through a scrubber, where they are further cleaned and cooled before being sent to the stack. The hot flue gas from the lime kilns goes through an electrostatic filter before being sent to the stack.
While the recovery boilers and lime kilns are operated based on demand for recovering chemicals from the black liquor, the power boiler is operated to balance total steam production with the process steam demands. Consequently, the load of the power boiler varies quite significantly, and will also differ between the integration scenarios. The numbers in the table are only meant to provide an indication of typical current emission levels from the boiler, which are not considered for capture. In order to estimate the change in carbon flows related to the power boiler, the CO2 emission factor of the solid wood fuel used in the power boiler was assumed to be 96 g/MJ (Naturvårdsverket, 2005) and the fuel to heat efficiency of the boiler was assumed to be 85%.
2.2 Modeling of the carbon capture and liquefaction plant
The carbon capture process assumed in this paper is a post combustion amine absorption process, since this is one of the most mature options for carbon capture from flue gases, which is also well-suited for retrofit of existing industrial plants such as pulp and paper mills. The capture process was assumed to use the AMP (2-amino-2-methyl-propanol) -PZ (piperazine) solvent that has been suggested as the new benchmark solvent for post-combustion carbon capture (Feron et al., 2020).
It is further assumed that 90% of the CO2 from the flue gases of the two recovery boilers and the lime kilns is captured, with a common absorber treating the mixed flue gases from all three stacks. The CO2 from the power boiler is not considered for capture, partly because the power boiler can have large operational variations as described above, and partly because the load of the power boiler, and consequently its CO2 emissions, is highly dependent on the energy balances of the integrated processes at the mill site, and therefore would differ considerably between the different integration scenarios.
A simplified flowsheet of the carbon capture process using AMP-PZ solvent is shown in Figure 2. The CO2-rich flue gas feed is cooled to around 40°C before being sent to an absorber for CO2 absorption. A water wash section is placed at the top of the absorber to recover solvents from the CO2-lean flue gases. The rich solvent is extracted from the absorber bottom and sent to the stripper for regeneration. The CO2 captured is extracted from the stripper top and sent to the subsequent conditioning unit. The solvent is thereafter regenerated, i.e., lean solvent is extracted from the stripper bottom and sent back to the absorber for reuse. A lean-rich heat exchanger is used for heat recovery from the lean solvent. The carbon capture process was simulated using rate-based models in Aspen Plus V10. The eNRTL property method was used. The reactions involved, the equilibrium and kinetics parameters and interaction parameters were taken from Aspen Plus default library models for AMP and PZ solvents and literature (Li et al., 2014; Zhang et al., 2017). The process was simulated with flue gas data representing normal mill operation as specified in Table 2. High-temperature flue gases were assumed to be cooled to 125°C before entering the direct contact cooler, in order to enable recovery of as much heat as possible without risking condensation of acids in the heat exchangers.
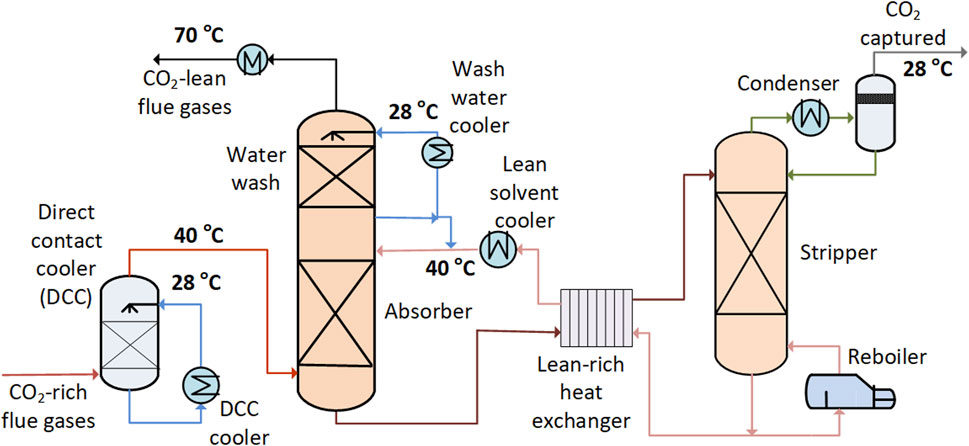
FIGURE 2. Flowsheet of the carbon capture process assumed for the integration study. Adapted from Voldsund et al. (2019), licensed CC-BY-4.0.
The CO2 leaving the stripper was further assumed to be conditioned in a liquefaction plant to the conditions required for ship transport, before being sent to a buffer storage. In the liquefaction plant, the CO2-rich stream from the capture process is compressed in a multi-stage compressor train with intercoolers, and liquefied using an ammonia refrigeration cycle. In the compression train, condensed water is removed from the feed gas through phase separators. Deep water removal is achieved with a dehydration unit. Other impurities, mainly O2, are removed as a purge gas after the liquefaction, resulting in a minor loss of the CO2. The process also includes a recirculation of flash gas that is generated during a throttling step for further purification of the liquified CO2. The liquified CO2 has a pressure of 16 bar(a), a temperature of −26°C, and is purified to 99.999 mol% CO2 and 0.001 mol% N2 to fulfil the Northern Lights specifications (Equinor, 2019). The modeling of the liquefaction plant is described in detail in (Deng et al., 2019).
The carbon capture and the liquefaction processes require both heating and cooling in different parts of the processes and these thermal energy requirements are summarized in Table 3.
2.3 Lignin extraction
The predominant way of extracting lignin from black liquor is by precipitation (Pola et al., 2022). A simplified process flowsheet is shown in Figure 3. The lignin is extracted by removing a part of the black liquor flow from the evaporation plant and acidifying it with CO2 to lower the solubility of lignin in the liquor. The precipitated lignin is then separated from the remaining liquor through press filters. The crude lignin from the first press filters is then further purified by further lowering the pH value, washing and dewatering it in a second press filter.
A major advantage for lignin extraction of having a CO2 capture unit in the mill is that the need for CO2 for the lignin precipitation can be fulfilled by captured CO2, thereby avoiding the need to purchase CO2.
In this study, it was assumed that 0.12 tonnes of lignin is extracted from the black liquor per air-dried tonne of pulp. This is well within the range of feasible extraction rates reported in literature (Välimäki et al., 2010), and similar to plants in commercial operation (Haaker, 2015).
The major effect of lignin extraction on the mass and heat flows of the mill is connected to the operation of the recovery boilers. When lignin is extracted from the black liquor, it will no longer be combusted in the recovery boiler, thereby reducing the steam production in the boiler as well as the amount of CO2 (available for capture) in the flue gases. The lost heat production must either be met by reductions in steam use in the mill processes or steam turbines, or by increased steam production (with corresponding CO2 emissions) in utility boilers. Moreover, the lignin-lean black liquor and wash water streams returned from the lignin extraction plant means more water must be evaporated in the evaporation section, which consequently requires a higher heat demand.
The CO2 that is added to the precipitation vessel is assumed to react with the cooking chemicals of the liquor and form carbonates. The carbonates will remain with the liquor until the causticization unit, and the carbon finally is released as CO2 with the flue gas of the lime kiln. Since the CO2 in the lime kiln is captured, this will result in a small recirculation of CO2.
Overall, since the flue gases are assumed to be mixed before being sent to the capture plant, the increased release of CO2 from the lime kilns and the changed reaction conditions in the recovery boiler are assumed to have only a minor effect on the concentration of CO2 in the mixed flue gases. In this work, it is assumed that this effect is small enough to not affect the heating and cooling requirements of the carbon capture and liquefaction process per tonne of captured CO2.
A summary of the effects of lignin extraction on mill heat and carbon balances is presented in Table 4.
2.4 Heat integration assessment
To investigate how the integration of carbon capture would affect the heat balances and power co-generation potential at the pulp mill, an approach based on Pinch Analysis (see e.g., Klemeš, 2023) was used. Specifically, pinch-based tools were applied to establish targets for heat recovery through optimized heat cascades as well as corresponding minimum utility requirements for different mill configurations. Next, the theoretical targets for minimum hot and cold utility, as well as targets for minimum fuel use and maximized co-generation were compared between the different mill configurations. The approach closely follows the method proposed by Svensson et al. (2019) for estimation of excess heat and co-generation targets.
One of the strengths of applying an energy targeting approach is that the graphical representation of the optimized heat cascade, the GCC, can be conveniently used for visualizing the potential for heat integration between a process (e.g., the mill) and its utility system or another process (e.g., a capture process). This is commonly referred to as splitting the GCC (see e.g., Kemp and Shiun Lim, 2020). Basing the analysis of integration potential on energy targets also avoids the need to collect information regarding existing process heat recovery solutions in the mill, as well as the need to know how the heat recovery system for the new processes will be designed. However, it should be noted that the GCC represents heat flows in a process with maximum internal heat recovery and does not consider any constraints of the process layout and design besides the minimum temperature difference for heat exchange. Such ideal heat integration is unlikely to occur in an actual process plant, and especially not in an existing plant that has been revamped regularly over a long period of time. On the other hand, the assumption about ideal heat recovery allows for a consistent and fair comparison between different configurations, avoiding the risk of comparing one optimized configuration with a non-optimized one. Furthermore, the heat integrated process may be a better representation of a future scenario in which further steps have been taken to improve heat recovery in the mill.
In our analysis, two different cases were assumed for the mill processes, where the first corresponds to the current mill configuration and normal operation, and the second assumes that lignin extraction has been implemented in the mill. In both cases, high temperature heat from combustion of black liquor in the recovery boiler is considered to be a process-inherent heat source (i.e., the steam from the recovery boiler is not seen as utility steam), since the processing of black liquor in the recovery boiler is a necessary step in the recovery of chemicals. Note, however, that the amount of heat available from the recovery boiler will be lower when lignin is assumed to be extracted from the black liquor. The mill configuration without lignin extraction is also used as a base case for the energy targeting study, and serves as a reference when comparing the energy targets for the mill with the integrated carbon capture process to the mill without capture.
The optimal heat cascades were established assuming a minimum temperature difference for heat exchange (ΔTmin) of 10 K. The process streams representing the heat sources and sinks of the mill (see Section 12) form the so-called background process. The process streams related to the carbon capture and liquefaction process form the foreground process. In our analysis, the potential matching of the heat cascades for the foreground and background processes was evaluated numerically. This provides an indication of how well the carbon capture plant can be heat integrated with the mill. The GCCs representing the respective heat cascades can also be plotted in the same figure in order to visualize the potential integration between the two processes. For the base case mill configuration without lignin extraction, the split GCCs for the mill and the capture processes are shown in Figure 4.
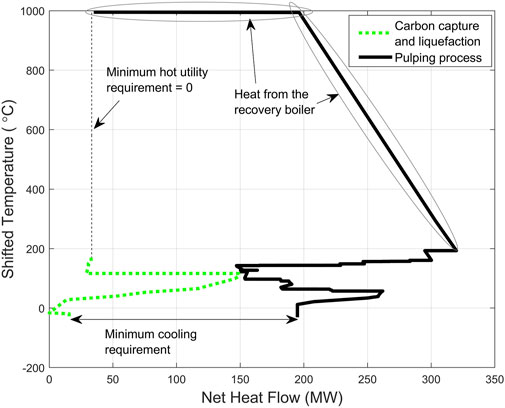
FIGURE 4. Split GCCs illustrating the potential heat integration between the carbon capture and liquefaction process (foreground) and the kraft pulping process, including the high-temperature heat from the recovery boiler (background).
Next, it was estimated how the integration of the carbon capture and liquefaction process would affect the potential for steam turbine power generation in the mill. Again, the matching of the heat cascades for the pulp mill and carbon capture process (the background) and the steam cycles (the foreground), can be evaluated numerically, but in this case, the size of the steam turbine cycle is not fixed and can be optimized. To find the potential for power co-generation, the steam flows through different turbine stages were therefore optimized to identify the integrated heat cascades that correspond to ideal integration of steam turbine cycles. In order to keep the programming model linear, a simplified steam cycle was assumed with turbine extractions limited to the existing steam levels of the mill, and an assumed fixed value for the isentropic efficiency of the turbine. For each mill and capture integration configuration, the heat cascades of the processes and the steam cycle are optimized to minimize primary hot utility (i.e., fuel use) and maximize power generation according to an objective function where these two objectives are combined.
For formulation of the objective function, two different optimization scenarios were considered: “Minimized fuel use” and “Maximized power co-generation.” In the first scenario, minimized fuel is the main objective, and always prioritized over power generation. In this scenario, power generation would only be achieved if there is sufficient heat from the recovery boiler to generate all steam necessary for process heating as well as steam for turbine operation. To include the power generation potential from available high-temperature excess heat, power generation is, however, also included in the objective function, but with a lower weight than fuel use. In the second scenario, maximized power generation is the main objective and prioritized over minimized fuel use. However, only co-generation of power in back-pressure steam turbines are considered. To avoid solutions where fuel is used for power-only generation, fuel use is considered in the objective function also in this scenario, but now with a lower weight than power generation. The weights of hot utility and power generation in the objective function can be chosen rather arbitrarily as long the relative weights ensure that one of the objectives is prioritized over the other according to the chosen optimization scenario. The energy targeting computations were performed using the in-house Matlab-based tool Mat4PI (Morandin, 2017).
The integration with the steam turbine cycle can also be visualized using split GCCs, e.g., as shown in Figure 5. In this case, the stream data for the integrated carbon capture and pulping process (base case mill configuration without lignin extraction) was used to construct the GCC for the background process, while the steam turbine cycle is represented as the foreground GCC. For further information about energy targeting for integration of steam turbine CHP (see Harvey et al., 2023).
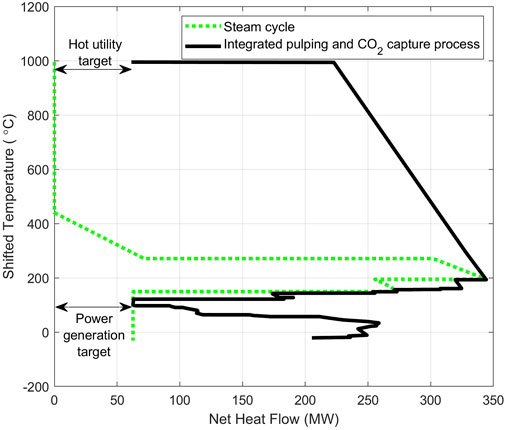
FIGURE 5. Illustration of the integration between the processes and the steam turbine cycle, represented as split GCCs. The background process GCC represents ideal heat integration between heat sources and sinks in the mill and in the capture process, and includes unavoidable high-temperature heat from the recovery boiler.
All in all, three different mill configurations and two scenarios for the optimization trade-off between fuel use and electricity generation were investigated. These mill configurations and scenarios are briefly summarized in Table 5.
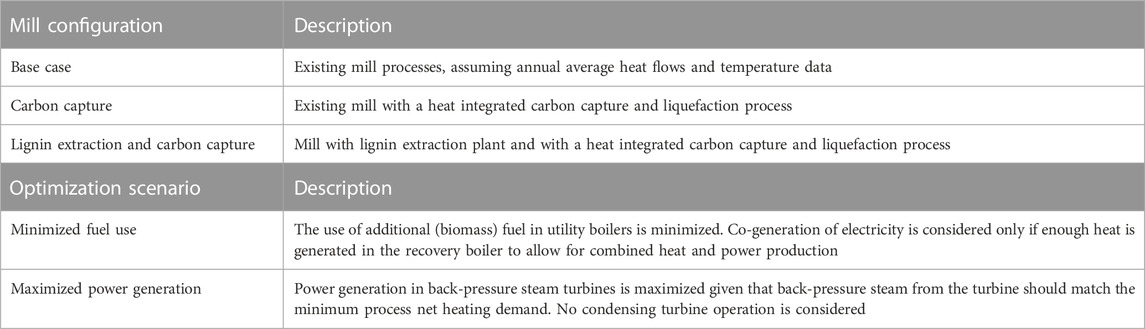
Table 5. Overview of investigated mill configurations and optimization scenarios for the heat integration analysis.
3 Results
3.1 Minimum heating and cooling requirements
Figure 4 shows the integration between the mill (without lignin extraction) and the capture and liquefaction process. The GCC of the carbon capture and liquefaction process is shown as the foreground curve and the GCC of the pulp process is shown as the background curve. The shifted pinch temperature of the carbon capture and liquefaction process is 122°C, and since most of the excess heat from the pulping process is available below 100°C, the opportunity for heat integration between the two processes is very limited.
Figure 4 shows that the high-temperature heat generated by combustion of black liquor in the recovery boiler of the mill has the potential to cover the combined heat demand of the carbon capture process and the mill. This will, however, require that almost all the high temperature excess heat is used for process heating. Currently this heat is used to generate high-pressure steam, which is run through a back-pressure steam turbine to co-generate electricity while also providing steam for heating the mill’s processes. If the heat demand of the carbon capture process should also be covered by the recovery boiler heat, this would require that the steam turbines are by-passed. Consequently, this would come at the cost of greatly reducing the electricity production. An alternative would be to use a utility boiler to generate enough additional steam to allow for co-generation of electricity in steam turbines, while providing the necessary amount of steam to the process. This would increase the fuel use at the mill, but the marginal electrical efficiency of additional fuel use would be close to 100%.
While the results of the integration assessment are illustrated graphically for the mill configuration with carbon capture but no lignin extraction in Figure 4, the minimum heating and cooling requirements were determined numerically for all mill configurations. The results are presented in Table 6, which also shows the heat generation from the recovery boiler in each case.
Table 6 shows that if the pulping process is modified to extract lignin from the black liquor, the recovery boiler would not generate enough heat to meet the minimum heat requirements of a carbon capture process integrated with the mill. For this mill configuration, there would be a deficit of heat from the recovery boiler, even if no co-generation of electricity is assumed. This is mainly due to the reduced heat production in the recovery boiler when the extracted lignin is no longer being combusted, thus reducing the heating value of the black liquor fuel sent to the recovery boiler. To balance the deficit of heat additional hot utility must be provided, e.g., by a power boiler.
3.2 Effects on fuel demand and power generation potential
For further investigation of utility boiler requirements and potential steam turbine power generation for the different mill configurations, the integration of a steam turbine cycle was also estimated using foreground/background analysis (see Section 2.4). Two cases representing different trade-offs between fuel use and electricity generation were investigated for each mill configuration scenario. In the first case, minimized fuel use is prioritized, and in the second case, maximized back-pressure steam turbine electricity generation is prioritized. For the mill configuration without lignin extraction where carbon capture is integrated, the maximized co-generation scenario is illustrated graphically in Figure 5. For this and the other mill configurations and optimization scenarios, the results were derived numerically, and are presented in Table 7.
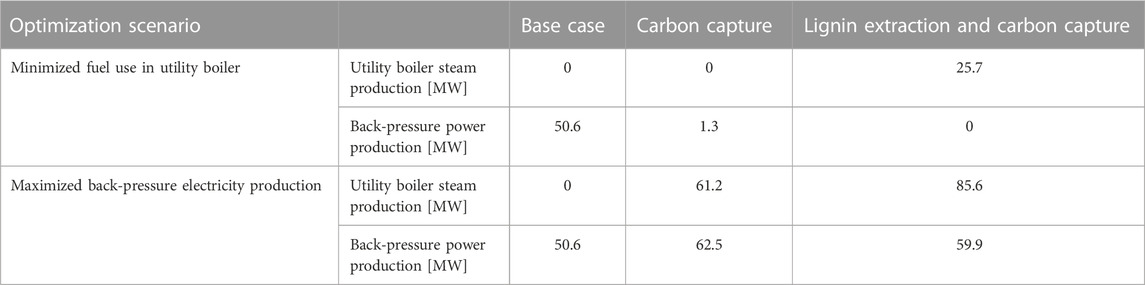
Table 7. Estimated minimum utility boiler heat production and maximum potential power generation from the back-pressure steam turbine under different assumptions about the trade-off between fuel use and electricity generation.
In Table 7 it is shown that, if minimizing fuel use, it is only necessary to use a utility boiler when both lignin extraction and carbon capture are implemented in the mill, which is in line with the results from Table 6. However, when back-pressure electricity production is maximized, both the case with only carbon capture and the case with both lignin extraction and carbon capture require significant use of a utility boiler. The required new steam production can be compared to the current steam production in the recovery boiler (286 MW) which would be reduced to 248 MW if lignin is extracted. Note that for the base case, i.e., for the pulp mill without carbon capture and lignin extraction, additional utility boiler use would not be required (based on the theoretical energy targets) even when back-pressure electricity production is maximized since the heat available from the recovery boiler is sufficient to cover the demands of the integrated mill and steam cycle.
The potential power generation varies somewhat between the process configurations when the back-pressure electricity production is maximized, depending on how large the heat requirements are for the integrated processes. The two process configurations with carbon capture (with or without lignin extraction) show a very similar increase in electricity production potential when comparing maximized power generation with minimized fuel use. Consequently, the corresponding increase in utility boiler use is also very similar.
The results should also be put in relation to existing boiler and turbine capacities in the mill. Because of the significant effect on utility boiler requirements if aiming for maximized co-generation, the integration of a carbon capture process is likely to require new boiler capacity in these scenarios, and since the power co-generation potential increases compared to the base case, potentially also new turbine capacity. Available capacity in existing boilers and turbines will, therefore, be important input for deciding to what extent minimized fuel use or maximized power generation should be prioritized. The optimal solution is likely to be a trade-off, where, power co-generation is maximized within the capacity constraints of existing boilers and turbines, and additional hot utility requirements are met with minimized fuel use as the main priority.
In the case study mill, existing boiler and turbine capacity is currently fully utilized, at least during certain periods of the year (see further Section 4 for a discussion regarding seasonal variations). Consequently, any increase in targeted fuel use or power generation would require investment in new boiler or turbine capacity, respectively. While the capacity of the existing power boiler (95 MW) does not represent the varying (spare) capacity available to cover new heat demands, the estimated utility boiler steam requirements can be compared to this value to get a rough idea about the need for new boiler investments.
Overall, the results show that the integration of a carbon capture plant strongly affects the energy balances of the mill, and if lignin extraction is implemented in the mill where carbon capture is integrated, the energy balances become even more constrained. In the case where lignin extraction is implemented in the mill, the theoretical energy targets show that additional fuel use in a utility boiler would be required independently of the trade-off between fuel use and power co-generation.
3.3 Carbon flows for the different mill configurations
Figure 6 shows differences in estimated biogenic carbon flows for the three different mill configurations, both in the scenario when fuel use is minimized (Figure 6A) and in the scenario when back-pressure steam turbine power generation is maximized (Figure 6B). Note that the figure only shows carbon flows of product and exhaust streams, which are affected by the integration of the carbon capture and/or the lignin extraction plant.
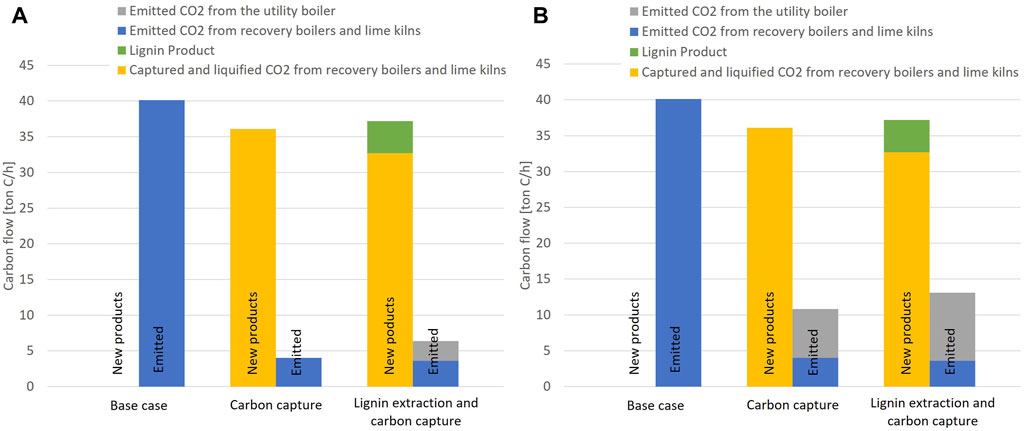
FIGURE 6. Carbon flows from the mill that are affected by the integration of a carbon capture process or lignin extraction process. Results for different mill configurations and two scenarios: (A) minimizing fuel use, and (B) maximizing back-pressure steam turbine power generation. Note that the carbon flow associated with the core pulp product (ca 25 ton C/h) is not included since it is the same for all configurations and scenarios.
Figure 6 shows that if carbon capture is integrated in a mill with lignin extraction more biogenic carbon would be converted to products (compared to integrating carbon capture in a mill without lignin extraction). However, due to the unfavorable energy balances of this mill configuration, it would also result in more carbon being emitted. If only considering the carbon efficiency of the process, this mill configuration would perform worse than the carbon capture configuration without lignin extraction, since the increase in emitted carbon is higher than the increase in recovered carbon in products.
A simple carbon efficiency would, however, not capture the usefulness of the recovered carbon and the value of the different product streams. Obviously, the potential for high-value applications is expected to be much higher for lignin than for both CO2 and the solid biomass fuels used in the utility boiler.
The analysis of direct impacts on carbon flows in the mill would also not capture the indirect effects on CO2 emissions resulting from the changes in mill’s (net) electricity balance. Comparing the results for scenarios A and B in Figure 6 shows how the maximization of electric power generation clearly increases the amount of emitted (biogenic) carbon (from the mill site) compared to the scenario where fuel use is minimized, due to increased emissions from the utility boiler. However, in a wider systems perspective, the effects on CO2 emissions would be strongly dependent also on the emissions intensity of grid electricity generation, which would be replaced by the electricity from the mill.
Note that the results for carbon flows (similarly to the results for energy balances) are affected by the assumption of 90% capture of CO2 from the flue gases. With a lower capture rate, it would be possible to avoid increased wood fuel use and associated emissions from the utility boiler. On the other hand, less carbon would be captured and the emitted carbon from the recovery boiler would be higher.
4 Discussion
For the pinch analysis presented in this paper, a minimum temperature difference for heat exchange of 10 K was assumed for all streams. When designing an actual heat exchanger network, a more careful selection of temperature difference contributions for individual process and utility streams is likely necessary to ensure that the design can come close to the estimated energy targets while ensuring operability and an economically sound distribution of heat transfer area within the heat recovery system. However, for this study, varying the (global) minimum temperature difference for heat exchange had no significant effect on the overall energy targets for minimum heating and cooling requirements, which are the main results of the pinch analysis. In short, the potential improvements in heat recovery that could be achieved by allowing for a smaller temperature difference would be minor compared to the total energy requirements.
The case study mill, as any pulp mill, is subject to varying conditions that affect the operation and heat flows in the mill. This includes, for example, seasonal variations in feedstock temperature and defrosting requirements, make-up water temperature, district heating demands, etc., which all increase the heat demand during winter. Since this study evaluates the mill during typical normal operation represented by annual mean operating data, it does not capture seasonal variations and their effect on the required utility boiler capacity. Furthermore, there are also short-term variations in the steam balances of the mill due to, e.g., variations in feedstock properties, various process disturbances, and cleaning and maintenance schedules, which typically are managed by a utility boiler. Altogether, the effect of the different sources of variations in the mill is large enough that the existing power boiler, at times, during winter, is fully utilized, while it can be completely shut down during the summer. Consequently, the existing power boiler has a rather large spare capacity available during summer, which can be used to cover additional steam demands for carbon capture integration, but almost no spare capacity during winter.
Limited and varying availability of additional capacity in the existing power boiler can be managed in different ways. One option would be to invest in additional utility boiler capacity, which would allow to run the carbon capture processes at full capacity all the time (also when lignin is extracted) but would require investments and additional fuel use. This can also be combined with investments in additional back-pressure turbine capacity to enable maximized co-generation of power. Other options would be to reduce electricity production (if not already at zero) by by-passing the turbines, or to run the capture plant at part load, thus reducing the steam demand for solvent regeneration, during periods when utility boiler capacity is limiting. The mill with both carbon capture and lignin extraction would have yet another flexibility option, through the opportunity to vary the amount of lignin extracted from the black liquor. By running the lignin extraction plant at part load, the heat produced by the recovery boilers can be increased during periods when there is a deficit of steam from the power boiler. Temporarily reducing the carbon capture or lignin extraction rate could also be interesting options to make more steam available for the steam turbines when electricity prices are sufficiently high to make the value of electricity production higher than the value of CO2 capture or lignin extraction, respectively.
While any flexibility option may be promising in a context of varying demands or prices, it is important to consider that varying operation would always involve part-load operation during certain periods. Whether this is handled by steam boiler and turbine system, the lignin extraction plant, or the capture plant, this would imply that any capacity invested in will not be fully utilized. With regards to varying operation of the capture plant, its consequences for utilization of the invested capacity in downstream liquefaction, intermediate storage, and transport and logistics chain should also be considered.
In this study, CO2 capture was considered only for the flue gases from the recovery boiler and lime kiln, and the capture rate was assumed to be 90%. However, the capture plant could be sized for other combinations of flue gases sources and/or other capture rates, which would be associated with different benefits and drawbacks. One potentially interesting option is to capture CO2 also from the utility boiler to maximize the recovery of biogenic carbon in products instead of releasing it to the atmosphere. This can make a significant difference in carbon recovery efficiency, especially in the cases with lignin extraction, where the load of the utility boiler is the highest. However, as discussed in Section 2.2, it would be more difficult to establish the optimal design and operation of a carbon capture process applied to the flue gases from the utility boiler due to the variations in the utility boiler load. Carbon capture applied on the utility boiler flue gases would also further increase the demand for utility boiler capacity and fuel use, due to the increased heat demand. Another interesting option for the mill with lignin extraction could be to design the capture plant for partial capture, by sizing the plant to capture only the amount of CO2 that can be captured using steam from the recovery boiler. This would result in a steam balance similar to that of a plant with carbon capture but without lignin extraction, but with an important difference in product distribution, due to the extracted lignin.
In the end, the deciding factor between these different options for configuration and design of the capture plant will be the expected technoeconomic performance, which in turn depends on the future value of the captured biogenic CO2, the lignin product, as well as electricity and fuel prices. As thoroughly discussed and investigated by Kuparinen et al. (2021) and Kuparinen et al. (2023), the value of the captured biogenic CO2 depends on future markets for green products that can be synthesized from the CO2 (e.g., methanol), or the value of carbon removal credits. In the case of using CO2 for carbon removals (negative emissions), it has also been shown that even though costs for capture and liquefaction dominate the costs for CCS, transport logistics and infrastructure are also deciding factors in the techno-economic evaluation of CCS (Karlsson et al., 2023). Other strategic considerations are also expected to influence the decision, for example, related to sustainability criteria for biomass, development of standards and certifications for negative emissions accounting, as well as the value of flexibility towards increasingly volatile electricity markets.
5 Conclusion
In this study, pinch analysis was used to determine the theoretical minimum heat requirements of a kraft pulp mill with or without lignin extraction, in which a carbon capture process is integrated. The carbon capture process is assumed to capture 90% of the carbon dioxide from the recovery boilers and lime kilns in the mill.
The results show that when carbon capture technology is implemented and fuel use is minimized at the case study mill, the heat available from the recovery boilers (286 MW) is sufficient to cover the heat demands of the integrated mill and capture processes. However, the amount of high-temperature excess heat available for back-pressure electricity production is greatly reduced, from around 50 MW to almost zero. When carbon capture instead is integrated to a mill where lignin is extracted from the black liquor, the heat produced by the recovery boilers is not sufficient to cover the process demands, and approximately 26 MW of additional heat from the utility boiler is required. The increased utility boiler load results in more carbon dioxide being released from the mill since the carbon dioxide emissions from the utility boiler are assumed to not be captured. On the other hand, when extracting lignin, more of the carbon from the biomass feedstock is recovered in useful products, since some of this biogenic carbon ends up in the extracted lignin, and this should have a higher value than captured carbon dioxide.
When production of back-pressure electricity is prioritized instead of minimizing the fuel use, additional heat must be supplied by the utility boiler, but an opportunity for generating back-pressure electricity with very high efficiency can be realized. The resulting difference between the electricity-maximization and the fuel-minimization scenario is very similar for a mill with and without lignin extraction. For both mill configurations, prioritization of back-pressure electricity generation leads to a similar increase in electricity production (ca 60 MW), at the cost of a corresponding increase in fuel use and carbon dioxide emissions from the utility boiler. However, in the mill with lignin extraction the boiler capacity is more likely to become a limiting factor, possibly requiring new investments.
Overall, the combined integration of lignin extraction and carbon capture has a strong negative effect on the steam balances of a kraft pulp mill, with the capture process significantly increasing the minimum steam requirement at the same time as extraction of lignin reduces the steam production in the recovery boiler. However, both technologies have a large potential for recovery of carbon from the wood by-products, which are currently only used for heat and power production. Their combined integration in a pulp mill would allow for better utilization of the biomass feedstock, for carbon dioxide removals and production of valuable bio-based products.
The results show that the consequences on energy and carbon balances of integrating carbon capture in pulp mills is strongly dependent on other strategic developments in the mill. Since the energy and carbon flows are determining factors for the economic and environmental performance of the carbon capture process, future studies of pulp mill carbon capture should consider the interaction with other potential technologies that may be integrated in the mill.
Data availability statement
The datasets presented in this study can be found in online repositories. The names of the repository/repositories and accession number(s) can be found below: https://doi.org/10.5281/zenodo.8276314.
Author contributions
HS: Conceptualization, Data curation, Formal Analysis, Investigation, Methodology, Visualization, Writing–original draft. CF: Methodology, Writing–original draft. SH: Funding acquisition, Project administration, Supervision, Writing–review and editing. ES: Conceptualization, Methodology, Supervision, Validation, Visualization, Writing–original draft, Writing–review and editing.
Funding
The authors declare financial support was received for the research, authorship, and/or publication of this article. The work presented in this paper received funding from the European Union’s Horizon 2020 research and innovation programme under grant agreement No. 101022487 (ACCSESS).
Acknowledgments
The authors would like to acknowledge support from Stora Enso, and especially from Karin Lindgren and Conny Johansson, for their collaboration and useful input to this work.
Conflict of interest
The authors declare that the research was conducted in the absence of any commercial or financial relationships that could be construed as a potential conflict of interest.
Publisher’s note
All claims expressed in this article are solely those of the authors and do not necessarily represent those of their affiliated organizations, or those of the publisher, the editors and the reviewers. Any product that may be evaluated in this article, or claim that may be made by its manufacturer, is not guaranteed or endorsed by the publisher.
References
Akbari, M., Oyedun, A. O., Jain, S., and Kumar, A. (2018). Options for the conversion of pulp and paper mill by-products in Western Canada. Sustain. Energy Technol. Assessments 26, 83–92. doi:10.1016/J.SETA.2017.10.003
Deng, H., Roussanaly, S., and Skaugen, G. (2019). Techno-economic analyses of CO2 liquefaction: impact of product pressure and impurities. Int. J. Refrig. 103, 301–315. doi:10.1016/j.ijrefrig.2019.04.011
Equinor (2019). Northern Lights project concept report (RE-PM673-00001). Northern Lights, Available at: https://norlights.com/wp-content/uploads/2021/03/Northern-Lights-Project-Concept-report.pdf.
Fajardy, M., Morris, J., Gurgel, A., Herzog, H., Mac Dowell, N., and Paltsev, S. (2021). The economics of bioenergy with carbon capture and storage (BECCS) deployment in a 1.5 °C or 2 °C world. Glob. Environ. Change 68, 102262. doi:10.1016/j.gloenvcha.2021.102262
Feron, P. H. M., Cousins, A., Jiang, K., Zhai, R., and Garcia, M. (2020). An update of the benchmark post-combustion CO2-capture technology. Fuel 273, 117776. doi:10.1016/j.fuel.2020.117776
Geleynse, S., Jiang, Z., Brandt, K., Garcia-Perez, M., Wolcott, M., and Zhang, X. (2020). Pulp mill integration with alcohol-to-jet conversion technology. Fuel Process. Technol. 201, 106338. doi:10.1016/j.fuproc.2020.106338
Granacher, J., Castro-Amoedo, R., Schnidrig, J., and Maréchal, F. (2023). Closing the balance – on the role of integrating biorefineries in the future energy system. Sustain. Energy & Fuels 7 (19), 4839–4854. doi:10.1039/D3SE00473B
Granacher, J., Nguyen, T.-V., Castro-Amoedo, R., McDonald, E. C., and Maréchal, F. (2022). Enhancing biomass utilization by combined pulp and fuel production. Front. Energy Res. 10. doi:10.3389/fenrg.2022.979502
Haaker, A. (2015). LignoBoost-anläggning från valmet överlämnad till Stora Enso. Bioenergitidningen 5. Available at: https://bioenergitidningen.se/lignoboost-anlaggning-fran-valmet-overlamnad-till-stora-enso/.
Hanssen, S. V., Steinmann, Z. J. N., Daioglou, V., Čengić, M., Van Vuuren, D. P., and Huijbregts, M. A. J. (2022). Global implications of crop-based bioenergy with carbon capture and storage for terrestrial vertebrate biodiversity. GCB Bioenergy 14 (3), 307–321. doi:10.1111/gcbb.12911
Hansson, J., Hackl, R., Taljegard, M., Brynolf, S., and Grahn, M. (2017). The potential for electrofuels production in Sweden utilizing fossil and biogenic CO2 point sources. Front. Energy Res. 5 (MAR), 4. doi:10.3389/fenrg.2017.00004
Harvey, S., Morandin, M., Berntsson, T., Papadokonstantakis, S., and Svensson, E. (2023). “Analysis and synthesis of utility systems, including heat pumping and combined heat and power,” in Handbook of process integration (PI). Editor J. J. Klemeš (Woodhead Publishing), 187–215.
Hubbe, M. A. (2021). Energy efficiency challenges in pulp and paper manufacturing: a tutorial review. Bioresrources 16 (4), 8567–8639. doi:10.15376/biores.16.4.8567-8639
Hubbe, M. A., Alén, R., Paleologou, M., Kannangara, M., and Kihlman, J. (2019). Lignin recovery from spent alkaline pulping liquors using acidification, membrane separation, and related processing steps: a review. BioResources 14 (1), 2300–2351. doi:10.15376/biores.14.1.2300-2351
Jönsson, J., and Berntsson, T. (2012). Analysing the potential for implementation of CCS within the European pulp and paper industry. Energy 44 (1), 641–648. doi:10.1016/j.energy.2012.05.028
Karlsson, S., Normann, F., Odenberger, M., and Johnsson, F. (2023). Modeling the development of a carbon capture and transportation infrastructure for Swedish industry. Int. J. Greenh. Gas Control 124, 103840. doi:10.1016/j.ijggc.2023.103840
Kemp, I. C., and Shiun Lim, J. (2020). “Process change and evolution,” in Pinch analysis for energy and carbon footprint reduction—user guide to process integration for the efficient use of energy. Third Edition (Butterworth-Heinemann).
J. J. Klemeš (Editor) (2023). Handbook of process integration (PI): minimisation of energy and water use, waste and emissions. Second edition (Woodhead Publishing). http://www.sciencedirect.com:5070/book/9780128238509/handbook-of-process-integration-pi.
Kuparinen, K., Lipiäinen, S., and Vakkilainen, E. (2021). Can carbon capture be a new revenue opportunity for the pulp and paper sector? TAPPI J. 20 (8), 527–540. doi:10.32964/TJ20.8.527
Kuparinen, K., Lipiäinen, S., Vakkilainen, E., and Laukkanen, T. (2023). Effect of biomass-based carbon capture on the sustainability and economics of pulp and paper production in the Nordic mills. Environ. Dev. Sustain. 25 (1), 648–668. doi:10.1007/s10668-021-02074-9
Kuparinen, K., Vakkilainen, E., and Tynjälä, T. (2019). Biomass-based carbon capture and utilization in kraft pulpmills. Mitig. Adapt. Strategies Glob. Change 24 (7), 1213–1230. doi:10.1007/s11027-018-9833-9
Lefvert, A., and Grönkvist, S. (2023). Smarter ways to capture carbon dioxide – exploring alternatives for small to medium-scale carbon capture in Kraft pulp mills. Int. J. Greenh. Gas Control 127, 103934. doi:10.1016/j.ijggc.2023.103934
Li, H., Frailie, P. T., Rochelle, G. T., and Chen, J. (2014). Thermodynamic modeling of piperazine/2-aminomethylpropanol/CO2/water. Chem. Eng. Sci. 117, 331–341. doi:10.1016/j.ces.2014.06.026
Lipiäinen, S., Apajalahti, E.-L., and Vakkilainen, E. (2023). Decarbonization prospects for the European pulp and paper industry: different development pathways and needed actions. Energies 16 (2), 746. doi:10.3390/en16020746
Marlin, D. S., Sarron, E., and Sigurbjörnsson, Ó. (2018). Process advantages of direct CO2 to methanol synthesis. Front. Chem. 6, 446. doi:10.3389/fchem.2018.00446
Mendoza-Martinez, C., Kuparinen, K., Martins, M., Cardoso, M., Vakkilainen, E., and Saari, J. (2022). Negative carbon-dioxide emissions from Eucalyptus pulp mill including biosludge HTC treatment. O Papel. 83 (6), 83–89.
Möllersten, K., Gao, L., and Yan, J. (2006). CO2 capture in pulp and paper mills: CO2 balances and preliminary cost assessment. Mitig. Adapt. Strategies Glob. Change 11 (5–6), 1129–1150. doi:10.1007/s11027-006-9026-9
Möllersten, K., Yan, J., and Westermark, M. (2003). Potential and cost-effectiveness of CO2 reductions through energy measures in Swedish pulp and paper mills. Energy 28 (7), 691–710. doi:10.1016/S0360-5442(03)00002-1
Mongkhonsiri, G., Charoensuppanimit, P., Anantpinijwatna, A., Gani, R., and Assabumrungrat, S. (2020). Process development of sustainable biorefinery system integrated into the existing pulping process. J. Clean. Prod. 255, 120278. doi:10.1016/j.jclepro.2020.120278
Morandin, M. (2017). MAT4PI: a Matlab based framework for process integration studies—user guide. Chalmers Univ. Technol. Div. Energy Technol. 2017. [Computer software].
Naturvårdsverket (2005). Förbränningsanläggningar för energiproduktion inklusive rökgaskondensering [Combustion plants for energy production including flue gas condensation] (Industry Fact Sheet). Naturvårdsverket. Available at: https://www.naturvardsverket.se/globalassets/media/publikationer-pdf/8100/91-620-8196-9.pdf.
Nwaoha, C., and Tontiwachwuthikul, P. (2019). Carbon dioxide capture from pulp mill using 2-amino-2-methyl-1-propanol and monoethanolamine blend: techno-economic assessment of advanced process configuration. Appl. Energy 250, 1202–1216. doi:10.1016/j.apenergy.2019.05.097
Onarheim, K., Santos, S., Kangas, P., and Hankalin, V. (2017a). Performance and cost of CCS in the pulp and paper industry part 2: economic feasibility of amine-based post-combustion CO2 capture. Int. J. Greenh. Gas Control 66, 60–75. doi:10.1016/J.IJGGC.2017.09.010
Onarheim, K., Santos, S., Kangas, P., and Hankalin, V. (2017b). Performance and costs of CCS in the pulp and paper industry part 1: performance of amine-based post-combustion CO2 capture. Int. J. Greenh. Gas Control 59, 58–73. doi:10.1016/j.ijggc.2017.02.008
Ong, B. H. Y., Walmsley, T. G., Atkins, M. J., and Walmsley, M. R. W. (2020). A kraft mill-integrated hydrothermal liquefaction process for liquid fuel Co-production. Processes 8 (10), 1216. doi:10.3390/pr8101216
Pola, L., Collado, S., Oulego, P., and Díaz, M. (2022). Kraft black liquor as a renewable source of value-added chemicals. Chem. Eng. J. 448, 137728. doi:10.1016/J.CEJ.2022.137728
Ribeiro Domingos, M. E. G., Flórez-Orrego, D., Santos, M. T. d., and Junior, S. de O. (2021). “Comparative assessment of black liquor upgraded gasification in integrated kraft pulp, methanol and dimethyl ether production plants,” in Computer aided chemical engineering. Editors M. Türkay, and R. Gani (Elsevier), 50, 25–30. doi:10.1016/B978-0-323-88506-5.50005-X
Rootzén, J., Kjärstad, J., Johnsson, F., and Karlsson, H. (2018). “Deployment of BECCS in basic industry—a Swedish case study,” in International Conference on Negative CO2 Emissions, Göteborg, Sweden, May 22-24, 2018. https://research.chalmers.se/en/publication/506150.
Rosa, L., Sanchez, D. L., and Mazzotti, M. (2021). Assessment of carbon dioxide removal potential via BECCS in a carbon-neutral Europe. Energy & Environ. Sci. 14 (5), 3086–3097. doi:10.1039/D1EE00642H
Saari, J., Peltola, P., Kuparinen, K., Kaikko, J., Sermyagina, E., and Vakkilainen, E. (2023). Novel BECCS implementation integrating chemical looping combustion with oxygen uncoupling and a kraft pulp mill cogeneration plant. Mitig. Adapt. Strategies Glob. Change 28 (4), 21. doi:10.1007/s11027-023-10057-6
Santos, M. P. S., and Hanak, D. P. (2022). Carbon capture for decarbonisation of energy-intensive industries: a comparative review of techno-economic feasibility of solid looping cycles. Front. Chem. Sci. Eng. 16 (9), 1291–1317. doi:10.1007/s11705-022-2151-5
Santos, M. P. S., Manovic, V., and Hanak, D. P. (2021). Unlocking the potential of pulp and paper industry to achieve carbon-negative emissions via calcium looping retrofit. J. Clean. Prod. 280, 124431. doi:10.1016/j.jclepro.2020.124431
Skagestad, R., Garðarsdóttir, S. Ó., Normann, F., Anheden, M., and Wolf, J. (2018). “A case study of partial capture of CO2 from a pulp mill – the CO2 capture cost,” in 14th Greenhouse Gas Control Technologies Conference (GHGT-14), Melbourne, Australia, 21-26 October 2018. doi:10.2139/ssrn.3366243
Smith, P., Davis, S. J., Creutzig, F., Fuss, S., Minx, J., Gabrielle, B., et al. (2016). Biophysical and economic limits to negative CO2 emissions. Nat. Clim. Change 6 (1), 42–50. doi:10.1038/nclimate2870
Svensson, E., Morandin, M., and Harvey, S. (2019). Characterization and visualization of industrial excess heat for different levels of on-site process heat recovery. Int. J. Energy Res. 43 (14), 7988–8003. doi:10.1002/er.4787
Svensson, E., Wiertzema, H., and Harvey, S. (2021). Potential for negative emissions by carbon capture and storage from a novel electric plasma calcination process for pulp and paper mills. Front. Clim. 3. doi:10.3389/fclim.2021.705032
Téguia, C. D., Albers, R., and Stuart, P. R. (2017). Analysis of economically viable lignin-based biorefinery strategies implemented within a kraft pulp mill. Tappi J. 16 (3), 157–169. doi:10.32964/tj16.3.157
Vakkilainen, E., and Välimäki, E. (2009). “Effect of lignin separation to black liquor and recovery boiler operation,” in TAPPI’s 2009 Engineering, Pulping, and Environmental Conference, Memphis TN, USA. doi:10.13140/2.1.2039.6485
Välimäki, E., Niemi, P., and Haaga, K. (2010). “A case study on the effects of lignin recovery on recovery boiler operation,” in International Chemical Recovery Conference, Williamsburg, VA, USA. doi:10.13140/2.1.1777.5046
Voldsund, M., Gardarsdottir, S. O., De Lena, E., Pérez-Calvo, J.-F., Jamali, A., Berstad, D., et al. (2019). Comparison of technologies for CO2 capture from cement production—Part 1: technical evaluation. Energies 12 (3), 559. doi:10.3390/en12030559
Keywords: carbon capture, pulp and paper, heat integration, lignin extraction, carbon dioxide removal
Citation: Skoglund H, Fu C, Harvey S and Svensson E (2023) Integration of carbon capture in a pulp mill—effect of strategic development towards better biomass resource utilization. Front. Therm. Eng. 3:1282028. doi: 10.3389/fther.2023.1282028
Received: 23 August 2023; Accepted: 17 October 2023;
Published: 01 November 2023.
Edited by:
Stanislav Boldyryev, University of Zagreb, CroatiaReviewed by:
Mamdouh Gadalla, Port Said University, EgyptNidret Ibric, University of Tuzla, Bosnia and Herzegovina
Copyright © 2023 Skoglund, Fu, Harvey and Svensson. This is an open-access article distributed under the terms of the Creative Commons Attribution License (CC BY). The use, distribution or reproduction in other forums is permitted, provided the original author(s) and the copyright owner(s) are credited and that the original publication in this journal is cited, in accordance with accepted academic practice. No use, distribution or reproduction is permitted which does not comply with these terms.
*Correspondence: Elin Svensson, ZWxpbi5zdmVuc3NvbkBjaGFsbWVycy5zZQ==