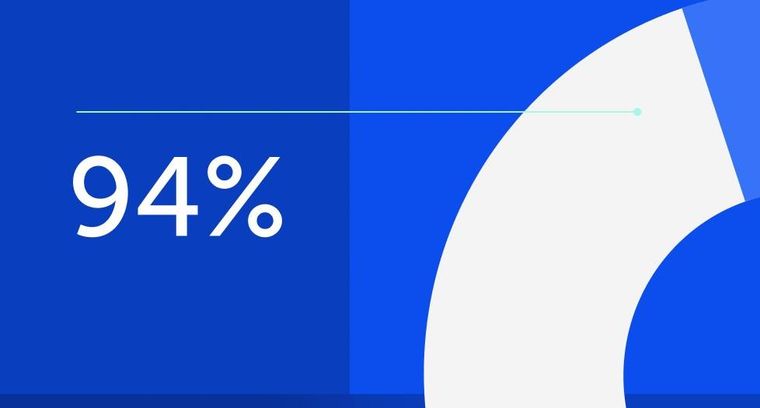
94% of researchers rate our articles as excellent or good
Learn more about the work of our research integrity team to safeguard the quality of each article we publish.
Find out more
REVIEW article
Front. Therm. Eng., 14 April 2023
Sec. Thermal Science and Energy Systems
Volume 3 - 2023 | https://doi.org/10.3389/fther.2023.1143987
This article is part of the Research TopicRole of Mathematical Modeling in Advanced Power Generation SystemsView all 10 articles
The present review focuses on the current progress on harnessing the potential of hydrogen production by Methane Steam Reforming (MSR). First, based on the prominent literature in last few years, the overall research efforts of hydrogen production using different feed stocks like ethanol, ammonia, glycerol, methanol and methane is presented. The presented data is based on reactor type, reactor operating conditions, catalyst used and yield of hydrogen to provide a general overview. Then, the most widely used process [steam methane reforming (SMR)/methane steam reforming (MSR)] are discussed. Major advanced reactors, the membrane reactors, Sorption Enhanced methane steam reforming reactors and micro-reactors are evaluated. The evaluation has been done based on parameters like residence time, surface area, scale-up, coke formation, conversion, space velocity and yield of hydrogen. The kinetic models available in recently published literature for each of these reactors have been presented with the rate constants and other parameters. The mechanism of coke formation and the rate expressions for the same have also been presented. While membrane reactors and sorption enhanced reactors have lot of advantages in terms of process intensification scale-up to industrial scale is still a challenge due to factors like membrane stability and fouling (in membrane reactors), decrease in yield with increasing WHSV (in case of Sorption Enhanced Reactors). Micro-reactors pose a higher potential in terms of higher yield and very low residence time in seconds though the volumes might be substantially lower than present industrial scale conventional reactors.
Hydrogen as a chemical is highly useful for various purposes. A few examples are: It acts as the robust backbone for the ammonia-based fertilizer industry and is highly useful for hydro-treating and hydro-cracking in petroleum industries. Moreover, over the last few years, hydrogen has developed as a fuel due to two major reasons (for example, in fuel cells) 1) zero emissions creating no environmental hazards and 2) as a byproduct gives cleaning drinking water. The demand for pure hydrogen has increased over a decade. Hydrogen can be classified into four major types based on their production source and methodology. Figure 1 shows the classification of hydrogen on the basis of their production methodology and source. Green hydrogen is based on the production of hydrogen from electrolysis of water. Grey Hydrogen and Blue Hydrogen are produced from same raw material as natural gas which majorly consists of methane and from same process of steam reforming. The only difference between them is that the latter has the carbon capturing technologies while the former does not. Black hydrogen is obtained from coal gasification. The present article deals with the production of hydrogen from methane, i.e., Grey Hydrogen and Blue Hydrogen.
Hydrogen can be produced from various routes using chemicals like methane, ethanol, ammonia, methanol, and glycerol. Current trends on the production of hydrogen include processes involving decomposition of ammonia, and steam reforming of ethanol and glycerol (Lytkina et al., 2019a; Saidi and Moradi, 2020; Itoh et al., 2021). In recent years, methanol steam reforming using innovative reactor configurations has also become an emerging field of research (Shtyka et al., 2018; Lytkina et al., 2019a; Lytkina et al., 2019b; Cai et al., 2019; Cao et al., 2019; Fasanya et al., 2019; Kamyar et al., 2019; Khani et al., 2019; Kim et al., 2019; Lian et al., 2019; Mohtashami and Taghizadeh, 2019; Sarafraz et al., 2019; Zeng et al., 2019).
Traditionally, methane had remained an effective source of hydrogen production. Various strategies for hydrogen production using methane include Partial Oxidation of Methane (POM) and Methane Steam Reforming (MSR). The most efficient and pure hydrogen production of all the methods have been developed using steam reforming of methane. Challenges in current technologies and increasing demands for lower capital and operating expenses in chemical production have fueled interest in developing novel approaches such as process intensification (Benson and Ponton, 1993; Moulijn and Stankiewicz, 2004). MSR produces nearly 48% of hydrogen globally (Gaudernack, 1998) using natural gas, with a maximum efficiency of 75% (Veziroglu and Barbir, 1998). To understand the feasibility of other raw materials than methane, three different tables are presented below. Table 1 summarizes the prominent works of hydrogen production using various feeds other than methane while Table 2 summarizes the recent advancements in hydrogen production using methanol and Table 3 for hydrogen production using methane. Most importantly, it can be observed that different types of reactors and catalysts are used by different authors to achieve high yields of hydrogen from different feed stocks other than methane. However, while the works of some authors are interesting the catalysts used by them are made of elements which are expensive and might be difficult for commercialization at industrial scale. Similarly, Table 2 focuses only on methanol where the recent studies have reported a varied range of conversion and selectivities from as low as 10% to as high as 100% providing very high yields. The different reactors in which these studies have been carried out, different operating conditions and catalyst types are also listed. Similarly, a listing of the most recent studies for methane as a feed stock in Table 3 shows that the advent of newer reactor types and different catalyst types (dominated predominantly by Nickel, Palladium and Platinum) have reduced reactor operating temperatures from conventional range of 800°C–1,000°C to 350°C–500°C maintaining yields above 90% which is a major advantage for MSR technology and process intensification. One of the major limitations of MSR as the most widely used process for hydrogen production is its high energy consumption. Due to this a major thrust has been pursued on process intensification. Hence, process intensification is of primary importance to further reduce the cost. Various strategies of process intensification can be acquired either by integrating unit processes involving chemical reactions and unit operations such as separation and heat exchanger or, more recently, by the miniaturization of the characteristic flow paths into unambiguous, structured geometries (Simsek et al., 2011; Önsan and Avci, 2011). One of the strategies of process intensification is coupling of innovative methods in catalyst design and reactor design. Process intensification (PI) is a technique for increasing energy efficiency using the strategies like 1 overcoming thermodynamic limitations 2 reduction in mass transfer resistances (De Deken et al., 1982; Soliman et al., 1988), 3 reduction in heat transfer resistance. PI can be very effective in conventional MSR, due to a) mass transfer limitations (Elnashaie, 1994), b) limitations due to thermodynamics and c) coke formation leading to the deactivation of the catalyst (Trimm, 1997). Adsorptive or membrane catalytic reactors may help overcome thermodynamic limitations (Adris et al., 1991; Hufton et al., 1999), while mass transfer limitations can be reduced through multifunctional catalysts (catalyst particles capable of doing multiple tasks, e.g., a catalyst particle having dual functionality, i.e., acting as a catalyst and also having membrane properties) (Dietrich et al., 2005). Innovative catalyst design, on the other hand, can aid in achieving desired kinetics. Thus, intensification of MSR can be achieved either by replacing conventional catalysts with multifunctional catalysts (Rusu and Cormier, 2003) or by intensifying processes like adsorptive or membrane catalytic reactors. Micro-reactors provide an integration of exothermic combustion channel and endothermic reforming channel. In addition, the metal walls that are responsible for the indirect heat exchange are made of advanced materials with higher heat transfer coefficients. This aids in improving the thermal efficiency of the process. On the other hand, advances in novel catalysts (e.g., Ni based catalysts) aids in a) decrease in residence times b) decrease in reactor volumes and c) increase in throughput (Tonkovich et al., 2004; Tonkovich et al., 2007).
Following are the objectives of the present study: a) to present a comparison of the most recent studies on hydrogen production using different feed stocks based on reactor types, operating conditions, catalysts and yield of hydrogen, b) classify and select major types of process intensification based advanced reactors most suited for industrial production c) perform a critical analysis of the key strengths in those reactors, their challenges and current status with respect to industrial implementation d) perform a detailed analysis of the kinetic models (essentially their rate expressions, kinetic rate constants and other parameters) and mechanism of coke formation (along with their rate expressions) for the chosen reactors and f) comparison of the MSR’s based on their advantages and limitations.
The Figures 2A–D show the schematics of the different types of reactors and their functioning. Figure 3 shows the various advantages and limitations of each of the reactors chosen for comparison and the applications for which they are used other than MSR.
Figure 2. Various Types of Reactor Configurations (A) Membrane Reactor. Reproduced under CC-BY 4.0 from Hafeez et al. (2020). (B) Micro-channel Reactor. Reproduced from Chen et al. (2019), with permission from ACS Publications. (C) Tubular Packed Bed Reactor. Reproduced from Iulianelli et al. (2016), with permission from Taylor and Francis. (D) Sorption Enhanced Methane steam Reformer. Reproduced from Huang W.-J. et al. (2021), with permission from Elsevier.
MR consists of a reactor volume filled with catalyst with one of its sides consisting of membrane (as shown in Figures 2A, C) that selectively removed hydrogen during MSR process due to pressure difference. The schematic of the MR in Figure 2A, shows that reactant (methane + steam) enters the catalyst section which is separated from the central section using the membrane. Hydrogen produced by MSR permeates into the central section and collected at the end with sweep steam while the unpermeated gas is collected at outlet of catalytic section. Depending on the geometric and operating parameters like reactor length, pressure, and temperature, the methane conversion upto 100% can be achieved, and pure hydrogen can be produced. These results in optimization in terms of number of equipments required in process material cost and temperature control is possible aiding the economics and design of the process.
Further, such reactors consist of three major steps, namely, reforming, water-gas shift and purification all taking place in the same reactor. Membrane reactors combine the capabilities of fixed or fluidized beds with perm-selective membranes embedded in the reactors. The membranes are especially useful in shifting conventional thermodynamic equilibrium and in-situ separation while also reducing the undesired by-products. To summarize, as the membrane reactor combines the reactor and separator units into one, it helps in reducing overall capital cost whilst increasing the yield and selectivity of hydrogen production.
Membrane reactors face problems like membrane fouling. Another important parameter is the strength of the membrane is important since the pressure at which the hydrogen is obtained is higher than atmospheric pressure. Other criteria like the purity of hydrogen obtained as the product and the mass transfer from the membrane is vital to decide good membrane performance. Hence, the type of membrane used is a crucial parameter in performance of MR’s. Palladium based membranes are mostly used but they are expensive. Hence, palladium with combination of cesium oxide (Tong et al., 2005), or dense ceramic membranes or modified pervoskite membranes (Bouwmeester, 2003; Thursfield and Metcalfe, 2004) or mixed ceramic metal membranes (Dong et al., 2001) have been used. Recent studies have shown that Carbon Molecular Sieve Membranes (CMSM) have been found useful for the production of hydrogen at low temperatures and are also resistant to CO and Sulphur poisoning (Bernardo et al., 2020). Palladium-based membranes provide a combination of both as a catalyst for hydrogen production whilst helping in the purification of hydrogen with excellent hydrogen selectivity (Bernardo et al., 2020). Electrochemical Hydrogen Pumping Membranes (EHPM) have high hydrogen permeation and selectivity at low energy consumption (Bernardo et al., 2020). In addition to this, the quality of feed and operating conditions harms membrane stability.
Membrane reactors are being tested on a small scale. For example, a small MR built and tested for production of hydrogen (capacity of 15 Nm3/hr) by Tokyo gas company (Seki et al., 2000). Other projects like hydrogen production initiatives by European Commission-funded project using Ag/Pd membranes faced challenges in commercialization due to several design issues (Dams et al., 2000). Research and development on hydrogen separation catalysts are ongoing in several companies (John Matthey catalysts, Aspen systems). Several government and private organizations like (Northwest power systems, Natural resources Canada, Institute of Gas Technology, and Dais-Analytic) (Huang et al., 2003) have granted patents for this technology. Micro-Membrane reactors have been extensively used for the hydrogen production due to enhanced heat and mass transfer characteristics, removal of mass transfer limitations and intense process intensification due to integration of different process units into single unit (Hafeez et al., 2020).
Figure 2D shows a typical SEMSR in a tubular fixed bed reactor. The length of the tube (Lr) is divided into three parts where Lc is the catalyst bed while some distance is kept before and after the bed to maintain fully developed flow/hydrodynamics (denoted by Lu and Ld). SEMSR involves addition of sorbents to have a twofold advantage a) increases in reaction rate b) in situ carbon-dioxide separation. The temperatures to achieve these reaction rates are in the range of 450°C–650°C. It also has advantages like high ability to adsorb and lower operating temperatures for calcination and carbonation. Pressure Swing Adsorption (PSA) is generally used for adsorption.
A multifunctional catalyst involves the characterization of the catalyst particle for different adsorbent fractions in the particle and diffusivities inside the particle (Zanfir and Gavriilidis, 2003; Yuan et al., 2007). These are also called combined sorbent catalyst particles (CSCM) (Di Giuliano et al., 2020) in which the solid particles consist of both the catalyst for MSR and the sorbent for CO2 capture. It possesses unique advantages like negligible inter and intra particle resistances, thermal integration between endothermic and exothermic reactions and reduced solid hold up in the case of heterogeneous reactors. Recently, the multifunctional catalyst configurations have been in the form of Nickel for MSR and CaO as the sorbent for CO2 capture. These enable the MSR process to be carried out at atmospheric pressures and 650°C than the high pressures and temperatures required in the conventional industrial processes.
Air Products and Chemical Inc. have shown the implementation of SEMSR via a pilot plant that essentially saves capital expenditure compared to conventional SMR’s (McLeod et al., 1997). The feasibility to use multifunctional catalysts like CaO15Ni(N)10 for industrial scale have been successfully demonstrated by researchers for 200 cycles (Di Giuliano et al., 2020). However, it has also been found that Ni sintering causes deactivation of the catalyst which would need further investigation in terms of Ni stability. Other characteristics like wet impregnation, wet mixing and attrition resistance were found to be good in these types of catalysts when tested on industrial scale.
Implementation of SEMSR’s are however challenging also due to the non-uniform temperature distribution due to the endothermic reaction of MSR and the exothermic reaction of CO2 sorption. Due to this it has been observed that the hydrogen production decreases with increase in weight hourly space velocity (WHSV) for the same geometric conditions (Huang W.-J. et al., 2021). This suggests more amount of research to be performed on industrial scale conditions for higher tube diameters for coming up with strategies to obtain higher hydrogen yields.
Micro-reactors used for hydrogen production are of different types in terms of whether the reactor has catalyst particles packed in the reactor or they are wall coated. This will in explained in the forthcoming subsections.
TPBM contains a concentric tubular system in which the inner tube is a membrane containing a catalyst. The feed enters inside the annular space between the concentric tube or the smaller concentric tube. The reaction happens on the surface of the catalyst. If the feed enters into the annular space between the concentric tube, then the reactants will permeate through the membrane and the product will be received through the outlet of the membrane itself. But if the feed enters into the smaller catalyst membraned concentric tube, the product permeates out of the membrane and received from the annular space. For Tubular membrane reactors (TMR’s), a two-step methane reforming process will be more efficient than the single-step conventional methane reforming. The authors also discussed that the optimum conditions for MSR by the two-step strategy are 720°C, Steam carbon ratio of 4, and pressure ranging between 3 and 10 bar. The two-step process also gives an energy efficiency of 35%–40%. Abanades et al. (2014) studied MSR in a solar-powered tubular packed bed reactor. The reactor directly used the solar indirect-irradiation concept to gain higher temperatures and also for complete driving of the endothermic MSR reaction. Carbon black was used as a catalyst for the reactor. The product received was 100% pure hydrogen without any by-products. The product contained no CO2. The authors discussed that the residence time and the temperature of the gas flowing through the catalyst bed act as important parameters influencing the chemical conversion and hydrogen yield.
Micro-channel process technology consists of reactors with channels in the range of 50–5,000 µm working in a laminar flow regime. A typical micro-channel reactor is shown in Figure 2B. It consists of alternating channels of catalytic combustion and reforming with inlets of methane-air mixture and methane-water mixture respectively. The walls on the reforming side are coated with Ruthenium catalyst while those on combustion side are coated with platinum catalyst. The heat transfer takes place through the walls as shown in the figure. Two types of catalytic systems: Palladium MMRs and Zeolite MMRs are used for hydrogen production (Kiani et al., 2021). Typical characteristics of micro-reactors include a high surface-to-volume ratio (for SMR also) improved heat and mass transfer rates (typically the rates are inversely proportional to channel diameters), low-pressure drops, and ease in thermal integration (Tonkovich et al., 2004; Delsman et al., 2005; Lou et al., 2008; Zhai et al., 2011). Further, micro-channel reactors can be scaled up by numbering up of several micro-channels in parallel that helps in production due to increase in throughput. Micro-reactors are characterized by micro-channels (which may have different shapes) in the range ∼10−5 and 10−3 m. Flow in these cases is essentially laminar. The construction material consists of plates (substrates) in which the channels are constructed. The surface areas are in the 1 × 104–5 × 104 m2m−3, which are ca. 50–100 times higher than those of their conventional packed bed counterparts (Simsek et al., 2011). The presence of the higher surface areas, smaller dimensions of sub-millimeters in combination with the use of metal-based catalysts help in uniform temperature distribution. The catalyst can either be packed into the channels or coated as a layer on the internal channel walls. MSR is favored at higher steam to carbon ratios of the feed at high temperatures. MSR being an endothermic reaction, a packed bed reactor would encounter axial and radial temperature gradients which in turn require cautious heat input and removal. On the other hand, coating catalysts on the walls, causes are helpful in minimization of transport resistances and provides a uniform temperature distribution over the catalyst layer. It is evident however that the above advantages of the micro-reactors can be harnessed depending on catalyst characteristics, stability, coating ability and activity.
In SMR process, two parameters that play a vital role are temperature and flow arrangement, the former being the most important. In micro-channels, the length scale for complete combustion is very small. At temperatures in the range 930°C–1,000°C overall conversion of 96% is achieved. Cross flow arrangement is mostly used while wall coated Fe-Cr-Al-Y catalysts are used in micro-reactors for MSR as per published literature (Stutz et al., 2006). Investigations have suggested that the complete combustion of methane takes place at a very short reactor distance at channel entry. One of the many advantages of micro-reactors is the ability to house multiple operations in a single unit (Tonkovich et al., 2007). This includes multiple inlets (like inlets for feed components like methane and steam and for preheating materials like fuel and air which make the process energy efficient).
Micro-channel reactors have been found to perform well at high space velocities higher than 105 h−1. In a study by (Zhai et al., 2011), the authors found conversions up to 100% for high space velocities upto 1.2 × 105 h−1. A three time increase in space velocity caused 50% decrease in conversion while an increase of five times decreased conversion by 30%.
Micro-reactors provide a reduction in plant complexity by incorporating multiple unit operations in a single modular reactor (Tonkovich et al., 2007). This can essentially help in small scale processing (Tonkovich et al., 2007) including specialty chemicals, fuel processing, and combinatorial or analytical applications.
Further, micro-reactors have the potential to reduce the cost of energy-consuming pieces of equipment like blowers and compressors. For example, as per study of the literature, a pilot scale micro-reactor in 40 h of continuous operation can give 90% MSR methane conversion at around 150 kPa pressure, and 850°C with about 25% of excess air and reaction times as low as 6 ms (Tonkovich et al., 2007). Further, the heat flux required to maintain the reaction temperature due to the reaction being endothermic does not destroy the mechanical integrity (Tonkovich et al., 2007). As per the published literature, around 55% of the total energy produced by combustion (fuel + air) was consumed to overcome endothermicity higher than conventional reactors. Further, of the 700 W produced by combustion in the micro-reactor, 311 W were consumed by the endothermic MSR reaction (6 ms contact time) and about 314 W (45%) were associated with thermal losses. The losses may be very low for pilot-scale systems due to the large surface-area to volume ratio. However, in a commercial-scale system, the thermal losses are calculated to drop below 5% while combustion contact times were 4 ms.
Micro-reactors have successfully been scaled up to produce 10 m3/s of hydrogen (Tonkovich et al., 2004). Numbering of reactors plays a major role in increasing the plant capacity during scaleup (Tonkovich et al., 2004). Conventional large-scale reformers suffer from the inefficient use of heat recovered from combustion gases in the form of steam and reduced thermal efficiencies of radiant reformer.
In a micro-structured steam–methane reformer, the heat transfer area required for recovering heat does not depend on the reactor volume which provides ample opportunity for process intensification and high energy savings as compared to conventional tubular reformers (Endou et al., 2004). In some cases, the energy required for reforming process is obtained from energy recovered from hot exhaust streams. In others, the catalytic fixed beds are embedded with heat exchangers providing high thermal efficiency (due to additional heat transfer area requirement), no extra steam generation (avoiding the necessity of steam utilization) least requirement of process control and high scalability.
In terms of dispersion, sintering and coking characteristics, the authors observed that good supports ensured lower tendency of sintering and coking. The lesser carbon formation in Ni catalyst was attributed to high saturation concentration of carbon in the smaller nickel crystals. The authors also observed distinct possibilities of catalysts being coated on the walls of the micro-channel to achieve high performance in terms of low sintering and coking and shorter residence times. Further, the authors also found that catalysts prepared by mixing Nickel, Magnesium and Alumina (e.g., Ni0.5Mg2.5AlO9) were cost effective, stable, and active for long residence times comparable or better than Rhodium catalysts. The authors have also found that existence of NiAl2O4 helped to restrain sintering and keep small crystal size.
Development of kinetic models for couple processes has always posed a challenge to the research fraternity. Kinetic models depend heavily on the basic data like the rate constants and order of reaction obtained from experimental data. However, depending only on experimental data is not advisable and advanced techniques like molecular modeling needs to be used to determine the above parameters. This is also possible due to the increase in computational power over more than a decade now. A few researchers have been able to predict kinetic parameters with different reaction mechanisms (Yang et al., 2000; Chen et al., 2004). However, the information, obtained from molecular dynamic simulations cannot be used directly during the scale-up of reactors. Scale-up methodology involves model development for different length and time scales, due to which the rate-limiting parameters need to be identified at the molecular level. Further, a correlation of these parameters (at micro-scale) with parameters at the macro level needs to be established and controlled by manipulating the micro-scale parameters. This approach has been referred to as multi-scale modeling approach by various authors (Bhat and Sadhukhan, 2009). The major advantage of such multi-scale modeling is in catalyst design only. Other aspects like predictions in conversion, yield, etc. can be achieved even by tuning the existing empirical models if coupled with changes in online experimental and multi-scale modeling does not provide any specific advantage.
With reference to the above discussion, an effort has been made to find the current status of the kinetic models in the published literature (Chen et al., 2020; Katheria et al., 2020; Niu et al., 2020; Parvasi et al., 2020; Huang W.-J. et al., 2021). The kinetic models [of the most recent and prominent research works (Parvasi et al., 2020; Huang W.-J. et al., 2021)] along with their rate constant expressions developed for the membrane and sorption enhanced reactors have been presented in Table 4. Below are the reactions occurring in a reactor during MSR:
The reaction kinetics and the rate constants for the reaction systems depends on several parameters. The major parameters affecting the reaction system are temperature, pressure, and activation energy. The activation energy for the reaction system depends upon the reactor system and the catalyst used for the reactor. Table 4 summarizes the reactions kinetics for the same.
Coke Formation results as an undesirable side reaction during MSR. Coke formation causes the formation of a layer of carbon over the layer of the catalyst. Because of the collection of coke over the catalyst, the active sites of the catalyst which should be used by reactants for product formation, gets consumed. This leads to catalyst deactivation and efforts are needed to minimize them. Figure 4 shows coke formation on a metal catalyst with support.
Figure 4. Coking mechanism on catalyst [Reproduced under CC-BY 4.0 from Stenina and Yaroslavtsev (2022)], Pink-Catalyst Support; Blue-Metal Catalyst; Black-Carbon.
Though it is clear that there is coke formation during the MSR reactions, the complete mechanism of the coke formation should be understood to avoid it. Sheintuch and German (2021) studied the reaction mechanism of coke formation during MSR in a Pd membrane. They also modelled the coke formation using a micro-kinetic model. According to the authors, the following reaction steps occur during MSR when coke formation takes place:
The reaction kinetics are given as follows:
The authors observed that the at high temperatures of 873 K and low hydrogen pressure of less than 1 millibar, there is formation of CH and O intermediates in very large amounts. This leads to coke formation. At the same time, at high hydrogen pressure and low temperature of 773 K, there is negligible amount of coke formation.
Studies have been done to diminish the coke formation effects (Ali et al., 2023).
Table 5 summarizes the performance, advantages and limitations of the usage of several reactors. The salient features of each of the reactors have been described below:
Membrane Reactors have wide advantages like continuous production, and low energy and space requirements while giving enhanced yields and selectivity with reduced capital costs. Because of these reasons, the use of MR has increased for hydrogen production using MSR. MR has been found effective for H2 production in a working temperature range of 400°C–500°C. Moreover, a higher conversion of 84% can be achieved using MSR. The recovery of the produced H2 is also appreciable (≈98.7%). However, the use of MR has also certain limitations. The major limitation of an MR is the ineffectiveness of MR in scale-up. The performance of an MR decreases rapidly because of membrane fouling. Moreover, there is a requirement for high working capital investment because of the limited life of a membrane and the excessive costs of a membrane. However, integration of membranes with conventional fluidized and packed beds have shown positive results by some researchers and breakthroughs can be expected in the near future.
Tubular Packed Bed Micro Reactors are an easy-to-build reactor system with low capital investment. Moreover, on using TPBMR, there is a high conversion rate per weight of catalyst used. TPBMR also provides a high contact area. TPBMR has higher efficiencies at higher temperatures and pressures. TPBMRs are operative in a temperature range of 600°C–1,000°C. It also provides a conversion of 92%. MSR can also achieve a stream of high H2 (mole fraction = 0.5) with very low side reactions. While it provides a high conversion, temperature control and heat transfer within the reactor are difficult. The catalyst is also difficult to separate.
Wall coated Micro Reactors (MIR) are an excellent reactor choice when the reaction requires higher mixing characteristics. MIR also has better reaction control and fewer hold-up volume requirements. The reactor has increased safety parameters with the best reagent usage. The scale-up of the reactor system is also achievable. A temperature range of 500°C–600°C is optimum for use of MIR. MIR can achieve a high conversion rate of 90% with an appreciable H2 recovery of 95%. The stream can also possess a high amount of mole fraction of 0.4, limiting the side reactions. However, the fabrication cost of a reactor is high. The performance of an MIR is also highly affected by clogging and precipitating products. Also, the reaction time is low and hence the reaction should be falling within that particular range.
Plate Reformers have a compact design with a faster start-up. There is also higher heat transfer within the reactor simultaneously with low capital investment. PR has been effectively tested within a temperature range of 527°C–727°C. PR can achieve a high conversion of 85%. However, the side reactions can lead to a stream with low H2 content (mole fraction = 0.1–0.2). PR is also highly sensitive to carbon deposition. Catalytic Wall Reactors have a small area requirement as the reactor system is smaller in size. CWR is the best reactor system for gaseous reactions because of the low-pressure drops. Thermal energy management is also excellent in a CWR. CWR can achieve a high conversion of up to 90% of methane.
Sorption Enhanced Methane steam Reformers have unique process intensification capabilities with an ability to produce hydrogen and capture carbon simultaneously due to the catalyst and sorbent particles present in the same catalyst bed. They also have a good operating temperature range and potential for high hydrogen recovery. The inherent difficulties of non-uniform temperature distribution due to simultaneous exothermic and endothermic reactions in the catalyst bed promote decrease in hydrogen production at higher WHSV’s. This is primarily one of the major hurdles for scale-up of these reactors.
Hydrogen production using both methane and methanol have been carried out for four major novel reactor systems. The following conclusions can be drawn based on their characteristics:
• Membrane Reactors gives higher conversions at lower temperatures with a combination of separation unit in themselves. They can also be integrated with conventional fixed or fluidized bed reactors. Hence, Membrane Reactors have the potential to be the most suitable reactors for hydrogen production using MSR except for the high capital and maintenance expenditure.
• Sorption Enhanced Methane Steam Reformers poses a very good process intensification method since the carbon separation happens in the catalyst bed which consists of catalyst and sorbent particles thus enhancing the reaction rate.
• Micro Reactors are found to be having optimized hydrogen production with an efficient hydrogen recovery. These have the advantages of low residence time, better thermal efficiencies, reaction control, high yields, and higher conversions.
• Nickel catalysts having different compositions of magnesium and alumina are found to have the potential for uniform dispersion on certain supports which can result in higher stability and lower sintering and coking. This has been seen as a cost-effective alternative to Rh catalysts. This is also preferred due to its ability to be coated on walls of micro-channels.
• Energy utilization in micro-reactors has been seen to be much better than conventional reactors due to non-necessity of steam export, less heat transfer, area requirement due to a decoupled requirement of reaction volume and heat transfer area.
• Micro-reactors (packed bed or wall coated) have an edge over other reactors due to their high yields and short residence times and have a high potential to be commercialized for lower volumes of hydrogen production
• Kinetic models for membrane reactors and Sorption enhanced type of reactors reported in literature are mostly chemisorption with surface reaction based LHHW kinetics. These largely depend on the catalyst used. The kinetics of MSR’s in micro-reactors are not that widely available and have not been presented
• Coke formation mechanisms and their models available in the literature are able to explain the coke formation. Further, ways and means to suppress the formation is also available and reported
• Membrane reactors are difficult to scale-up due to the high cost and maintenance charges of membranes due to membrane fouling while Sorption enhanced reactors suffer from the non-uniform temperature distribution in the catalyst beds as the WHSV increases posing difficulties in scale-up. Micro-reactors have shown good potential for scale-up in cases of hydrogen production
A comprehensive review of hydrogen production with the variants like green hydrogen and gray hydrogen along with blue and black hydrogen would be taken up in future work. This would include details of research work carried on with different technologies like electrolysis of water.
Conceptualization, AG and VB; methodology, AG; formal analysis, VB; investigation, AG and VB; resources, AG; writing—original draft preparation, AG and VB; writing—review and editing, AG and VB; supervision, AG; project administration, AG; funding acquisition, AG. Both authors contributed to the article and approved the submitted version.
The authors declare that the research was conducted in the absence of any commercial or financial relationships that could be construed as a potential conflict of interest.
All claims expressed in this article are solely those of the authors and do not necessarily represent those of their affiliated organizations, or those of the publisher, the editors and the reviewers. Any product that may be evaluated in this article, or claim that may be made by its manufacturer, is not guaranteed or endorsed by the publisher.
Abanades, S., Kimura, H., and Otsuka, H. (2014). Hydrogen production from thermo-catalytic decomposition of methane using carbon black catalysts in an indirectly-irradiated tubular packed-bed solar reactor. Int. J. hydrogen energy 39, 18770–18783. doi:10.1016/j.ijhydene.2014.09.058
Adris, A., Elnashaie, S., and Hughes, R. (1991). A fluidized bed membrane reactor for the steam reforming of methane. Can. J. Chem. Eng. 69, 1061–1070. doi:10.1002/cjce.5450690504
Ali, S., Gamal, A., and Khader, M. M. (2023). Development of highly active and coke-resilient Ni-based catalysts for low-temperature steam reformation of methane. Catal. Commun., 106605.
Antzaras, A. N., Heracleous, E., and Lemonidou, A. A. (2020). Sorption enhanced–chemical looping steam methane reforming: Optimizing the thermal coupling of regeneration in a fixed bed reactor. Fuel Process. Technol. 208, 106513. doi:10.1016/j.fuproc.2020.106513
Anzelmo, B., Wilcox, J., and Liguori, S. (2017). Natural gas steam reforming reaction at low temperature and pressure conditions for hydrogen production via Pd/PSS membrane reactor. J. Membr. Sci. 522, 343–350. doi:10.1016/j.memsci.2016.09.029
Ashraf, M. A., Tacchino, S., Peela, N. R., Ercolino, G., Gill, K. K., Vlachos, D. G., et al. (2020). Experimental insights into the coupling of methane combustion and steam reforming in a catalytic plate reactor in transient mode. Industrial Eng. Chem. Res. 60, 196–209. doi:10.1021/acs.iecr.0c04837
Benson, R., and Ponton, J. (1993). Process miniaturisation: A route to total environmental acceptability? Chem. Eng. Res. Des. 71, 160–168.
Bernardo, G., Araújo, T., Da Silva Lopes, T., Sousa, J., and Mendes, A. (2020). Recent advances in membrane technologies for hydrogen purification. Int. J. Hydrogen Energy 45, 7313–7338. doi:10.1016/j.ijhydene.2019.06.162
Bernardo, P., Barbieri, G., and Drioli, E. (2010). Evaluation of membrane reactor with hydrogen-selective membrane in methane steam reforming. Chem. Eng. Sci. 65, 1159–1166. doi:10.1016/j.ces.2009.09.071
Bhat, S. A., and Sadhukhan, J. (2009). Process intensification aspects for steam methane reforming: An overview. AIChE J. 55, 408–422. doi:10.1002/aic.11687
Bouwmeester, H. J. (2003). Dense ceramic membranes for methane conversion. Catal. today 82, 141–150. doi:10.1016/s0920-5861(03)00222-0
Cai, F., Lu, P., Ibrahim, J. J., Fu, Y., Zhang, J., and Sun, Y. (2019). Investigation of the role of Nb on Pd− Zr− Zn catalyst in methanol steam reforming for hydrogen production. Int. J. Hydrogen Energy 44, 11717–11733. doi:10.1016/j.ijhydene.2019.03.125
Cao, L., Lu, M., Li, G., and Zhang, S. (2019). Hydrogen production from methanol steam reforming catalyzed by Fe modified Cu supported on attapulgite clay. React. Kinet. Mech. Catal. 126, 137–152. doi:10.1007/s11144-018-1493-y
Charisiou, N. D., Siakavelas, G., Tzounis, L., Dou, B., Sebastian, V., Hinder, S. J., et al. (2020). Ni/Y2O3–ZrO2 catalyst for hydrogen production through the glycerol steam reforming reaction. Int. J. Hydrogen Energy 45, 10442–10460. doi:10.1016/j.ijhydene.2019.04.237
Charisiou, N., Papageridis, K., Siakavelas, G., Sebastian, V., Hinder, S., Baker, M., et al. (2019). The influence of SiO2 doping on the Ni/ZrO2 supported catalyst for hydrogen production through the glycerol steam reforming reaction. Catal. Today 319, 206–219. doi:10.1016/j.cattod.2018.04.052
Chen, D., Bjørgum, E., Lødeng, R., Christensen, K. O., and Holmen, A. (2004). “Microkinetic model assisted catalyst design for steam methane reforming,” in Studies in surface science and catalysis (Elsevier), 139–144.
Chen, J., Song, W., and Xu, D. (2019). Compact steam-methane reforming for the production of hydrogen in continuous flow microreactor systems. ACS omega 4, 15600–15614. doi:10.1021/acsomega.9b02063
Chen, K., Zhao, Y., Zhang, W., Feng, D., and Sun, S. (2020). The intrinsic kinetics of methane steam reforming over a nickel-based catalyst in a micro fluidized bed reaction system. Int. J. Hydrogen Energy 45, 1615–1628. doi:10.1016/j.ijhydene.2019.11.080
Chen, M., Liang, D., Wang, Y., Wang, C., Tang, Z., Li, C., et al. (2021). Hydrogen production by ethanol steam reforming over M-Ni/sepiolite (M= La, Mg or Ca) catalysts. Int. J. Hydrogen Energy 46, 21796–21811. doi:10.1016/j.ijhydene.2021.04.012
Chompupun, T., Limtrakul, S., Vatanatham, T., Kanhari, C., and Ramachandran, P. A. (2018). Experiments, modeling and scaling-up of membrane reactors for hydrogen production via steam methane reforming. Chem. Eng. Processing-Process Intensif. 134, 124–140. doi:10.1016/j.cep.2018.10.007
Dams, R., Moore, S., and Hayter, P. (2000). “Compact, fast response methanol fuel processing systems for PEMFC electric vehicles,” in Fuel cell seminar), 526–529.
De Deken, J., Devos, E., and Froment, G. (1982). “Steam reforming of natural gas: intrinsic kinetics, diffusional influences, and reactor design,” in Chemical Reaction Engineering–Boston (Boston: ACS Publications).
Delsman, E., Laarhoven, B., De Croon, M., Kramer, G., and Schouten, J. (2005). Comparison between conventional fixed-bed and microreactor technology for a portable hydrogen production case. Chem. Eng. Res. Des. 83, 1063–1075. doi:10.1205/cherd.04260
Di Giuliano, A., Gallucci, K., Di Carlo, A., Stendardo, S., Courson, C., and Foscolo, P. U. (2020). Sorption enhanced steam methane reforming by Ni/CaO/mayenite combined systems: Overview of experimental results from E uropean research project ASCENT. Can. J. Chem. Eng. 98, 1907–1923. doi:10.1002/cjce.23779
Dietrich, W., Lawrence, P. S., Grünewald, M., and Agar, D. W. (2005). Theoretical studies on multifunctional catalysts with integrated adsorption sites. Chem. Eng. J. 107, 103–111. doi:10.1016/j.cej.2004.12.016
Dong, H., Shao, Z., Xiong, G., Tong, J., Sheng, S., and Yang, W. (2001). Investigation on POM reaction in a new perovskite membrane reactor. Catal. Today 67, 3–13. doi:10.1016/s0920-5861(01)00277-2
Elnashaie, S. S. (1994). Modelling, Simulation and Optimization of Industrial Fixed Bed Catalytic Reactors. London: CRC Press.
Endou, A., Jung, C., Kusagaya, T., Kubo, M., Selvam, P., and Miyamoto, A. (2004). Combinatorial computational chemistry approach to the design of metal catalysts for deNOx. Appl. Surf. Sci. 223, 159–167. doi:10.1016/s0169-4332(03)00913-9
Fasanya, O. O., Al-Hajri, R., Ahmed, O. U., Myint, M. T., Atta, A. Y., Jibril, B. Y., et al. (2019). Copper zinc oxide nanocatalysts grown on cordierite substrate for hydrogen production using methanol steam reforming. Int. J. Hydrogen Energy 44, 22936–22946. doi:10.1016/j.ijhydene.2019.06.185
Fukuda, T., Harada, M. R., Ookawara, S., Hamzah, A. B., Yoshikawa, S., and Matsumoto, H. (2021). Double-layered catalytic wall-plate microreactor for process intensification of dry reforming of methane: Reaction activity improvement and coking suppression. Chem. Eng. Processing-Process Intensif. 164, 108406. doi:10.1016/j.cep.2021.108406
Gaudernack, B. (1998). Hydrogen production from fossil fuels. Hydrogen power Theor. Eng. solutions, 75–89. doi:10.1007/978-94-015-9054-9_10
Greluk, M., Rotko, M., and Turczyniak-Surdacka, S. (2020). Enhanced catalytic performance of La2O3 promoted Co/CeO2 and Ni/CeO2 catalysts for effective hydrogen production by ethanol steam reforming. Renew. Energy 155, 378–395. doi:10.1016/j.renene.2020.03.117
Hafeez, S., Al-Salem, S., Manos, G., and Constantinou, A. (2020). Fuel production using membrane reactors: A review. Environ. Chem. Lett. 18, 1477–1490. doi:10.1007/s10311-020-01024-7
Huang, C., Yu, Y., Tang, X., Liu, Z., Zhang, J., Ye, C., et al. (2020). Hydrogen generation by ammonia decomposition over Co/CeO2 catalyst: Influence of support morphologies. Appl. Surf. Sci. 532, 147335. doi:10.1016/j.apsusc.2020.147335
Huang, C., Yu, Y., Yang, J., Yan, Y., Wang, D., Hu, F., et al. (2019). Ru/La2O3 catalyst for ammonia decomposition to hydrogen. Appl. Surf. Sci. 476, 928–936. doi:10.1016/j.apsusc.2019.01.112
Huang, K., Zhan, X.-L., Chen, F.-Q., and Lü, D.-W. (2003). Catalyst design for methane oxidative coupling by using artificial neural network and hybrid genetic algorithm. Chem. Eng. Sci. 58, 81–87. doi:10.1016/s0009-2509(02)00432-3
Huang, W.-J., Yu, C.-T., Sheu, W.-J., and Chen, Y.-C. (2021a). The effect of non-uniform temperature on the sorption-enhanced steam methane reforming in a tubular fixed-bed reactor. Int. J. Hydrogen Energy 46, 16522–16533. doi:10.1016/j.ijhydene.2020.07.182
Huang, Y., Zhang, Z., Wei, W., Long, Y., and Li, G. (2021b). Experimental study on characteristics of hydrogen production from exhaust gas-fuel reforming in a catalytic fixed-bed reactor. Fuel 290, 120068. doi:10.1016/j.fuel.2020.120068
Hufton, J., Mayorga, S., and Sircar, S. (1999). Sorption-enhanced reaction process for hydrogen production. AIChE J. 45, 248–256. doi:10.1002/aic.690450205
Irankhah, A., Rahimi, M., and Rezaei, M. (2014). Performance research on a methane compact reformer integrated with catalytic combustion. Chem. Eng. Technol. 37, 1220–1226. doi:10.1002/ceat.201300469
Itoh, N., Kikuchi, Y., Furusawa, T., and Sato, T. (2021). Tube-wall catalytic membrane reactor for hydrogen production by low-temperature ammonia decomposition. Int. J. Hydrogen Energy 46, 20257–20265. doi:10.1016/j.ijhydene.2020.03.162
Iulianelli, A., Liguori, S., Wilcox, J., and Basile, A. (2016). Advances on methane steam reforming to produce hydrogen through membrane reactors technology: A review. Catal. Rev. 58, 1–35. doi:10.1080/01614940.2015.1099882
Kamyar, N., Khani, Y., Amini, M. M., Bahadoran, F., and Safari, N. (2019). Embedding Pt-SnO nanoparticles into MIL-101 (Cr) pores: Hydrogen production with low carbon Monoxide content from a new methanol steam reforming catalyst. ChemistrySelect 4, 6113–6122. doi:10.1002/slct.201901071
Katheria, S., Kunzru, D., and Deo, G. (2020). Kinetics of steam reforming of methane on Rh–Ni/MgAl2O4 catalyst. React. Kinet. Mech. Catal. 130, 91–101. doi:10.1007/s11144-020-01767-y
Khani, Y., Bahadoran, F., Safari, N., Soltanali, S., and Taheri, S. A. (2019). Hydrogen production from steam reforming of methanol over Cu-based catalysts: The behavior of ZnxLaxAl1-xO4 and ZnO/La2O3/Al2O3 lined on cordierite monolith reactors. Int. J. hydrogen energy 44, 11824–11837. doi:10.1016/j.ijhydene.2019.03.031
Kiani, M. R., Meshksar, M., Makarem, M. A., and Rahimpour, E. (2021). Catalytic membrane micro-reactors for fuel and biofuel processing: A mini review. Top. Catal., 1–20. doi:10.1007/s11244-021-01505-1
Kim, C.-H., Han, J.-Y., Lim, H., Lee, K.-Y., and Ryi, S.-K. (2018). Methane steam reforming using a membrane reactor equipped with a Pd-based composite membrane for effective hydrogen production. Int. J. Hydrogen Energy 43, 5863–5872. doi:10.1016/j.ijhydene.2017.10.054
Kim, J. H., Jang, Y. S., Kim, J. C., and Kim, D. H. (2019). Anodic aluminum oxide supported Cu-Zn catalyst for oxidative steam reforming of methanol. Korean J. Chem. Eng. 36, 368–376. doi:10.1007/s11814-018-0211-9
Lian, H.-Y., Liu, J.-L., Li, X.-S., Zhu, X., Weber, A. Z., and Zhu, A.-M. (2019). Plasma chain catalytic reforming of methanol for on-board hydrogen production. Chem. Eng. J. 369, 245–252. doi:10.1016/j.cej.2019.03.069
Lou, Y., Smith, R., and Sadhukhan, J. (2008). "Decarbonisation in process sites", in: 2008 AIChE spring national meeting, conference proceedings).
Lytkina, A., Mironova, E. Y., Orekhova, N., Ermilova, M., and Yaroslavtsev, A. (2019a). Ru-containing catalysts for methanol and ethanol steam reforming in conventional and membrane reactors. Inorg. Mater. 55, 547–555. doi:10.1134/s0020168519060104
Lytkina, A., Orekhova, N., Ermilova, M., Petriev, I., Baryshev, M., and Yaroslavtsev, A. (2019b). RuRh based catalysts for hydrogen production via methanol steam reforming in conventional and membrane reactors. Int. J. hydrogen energy 44, 13310–13322. doi:10.1016/j.ijhydene.2019.03.205
Mcleod, A., Johnston, M., and Gladden, L. (1997). Development of a genetic algorithm for molecular scale catalyst design. J. Catal. 167, 279–285. doi:10.1006/jcat.1997.1565
Mohtashami, Y., and Taghizadeh, M. (2019). Performance of the ZrO2 promoted CuZnO catalyst supported on acetic acid-treated MCM-41 in methanol steam reforming. Int. J. Hydrogen Energy 44, 5725–5738. doi:10.1016/j.ijhydene.2019.01.029
Niu, J., Wang, Y., Qi, Y., Dam, A. H., Wang, H., Zhu, Y.-A., et al. (2020). New mechanism insights into methane steam reforming on Pt/Ni from DFT and experimental kinetic study. Fuel 266, 117143. doi:10.1016/j.fuel.2020.117143
Önsan, Z. I., and Avci, A. K. (2011). “Reactor design for fuel processing,” in Fuel cells: Technologies for fuel processing (Elsevier), 451–516.
Parvasi, P., Jokar, S., Shamseddini, A., Babapoor, A., Mirzaie, F., Abbasfard, H., et al. (2020). A novel recovery loop for reducing greenhouse gas emission: Simultaneous production of syngas and pure hydrogen in a membrane reformer. Renew. Energy 153, 130–142. doi:10.1016/j.renene.2020.01.147
Pashchenko, D., Mustafin, R., and Mustafina, A. (2021). Steam methane reforming in a microchannel reformer: Experiment, CFD-modelling and numerical study. Energy 237, 121624. doi:10.1016/j.energy.2021.121624
Qingli, X., Zhengdong, Z., Kai, H., Shanzhi, X., Chuang, M., Chenge, C., et al. (2021). Ni supported on MgO modified attapulgite as catalysts for hydrogen production from glycerol steam reforming. Int. J. Hydrogen Energy 46, 27380–27393. doi:10.1016/j.ijhydene.2021.06.028
Rusu, I., and Cormier, J.-M. (2003). On a possible mechanism of the methane steam reforming in a gliding arc reactor. Chem. Eng. J. 91, 23–31. doi:10.1016/s1385-8947(02)00043-8
Saidi, M., and Moradi, P. (2020). Conversion of biodiesel synthesis waste to hydrogen in membrane reactor: Theoretical study of glycerol steam reforming. Int. J. Hydrogen Energy 45, 8715–8726. doi:10.1016/j.ijhydene.2020.01.064
Sarafraz, M., Safaei, M. R., Goodarzi, M., and Arjomandi, M. (2019). Reforming of methanol with steam in a micro-reactor with Cu–SiO2 porous catalyst. Int. J. Hydrogen Energy 44, 19628–19639. doi:10.1016/j.ijhydene.2019.05.215
Seki, T., Komiya, J., Fujiki, H., Shirasaki, Y., Inoue, K., Miura, T., et al. (2000). “(Year) development of fuel processing systems for PEFC residential stationary application,” in Fuel cell seminar abstract), 376–379.
Sheintuch, M., and German, E. D. (2021). Permeance inhibition due to reaction, coking and leakage of Pd membranes during methane steam reforming estimated from a micro-kinetic model. Chem. Eng. J. 411, 128272. doi:10.1016/j.cej.2020.128272
Shtyka, O., Higashino, Y., Kedziora, A., Dubkov, S., Gromov, D., and Maniecki, T. (2018). Monometallic Ru, Au, and Pt catalysts deposited on carbon nanotubes for oxidative steam reforming of methanol. Fibre Chem. 50, 301–305. doi:10.1007/s10692-019-09980-9
Simsek, E., Avci, A. K., and Önsan, Z. I. (2011). Investigation of catalyst performance and microstructured reactor configuration for syngas production by methane steam reforming. Catal. today 178, 157–163. doi:10.1016/j.cattod.2011.08.021
Soliman, M., El-Nashaie, S., Al-Ubaid, A., and Adris, A. (1988). “Simulation of steam reformers for methane,” in Tenth international symposium on chemical reaction engineering (Elsevier), 1801–1806.
Stankiewicz, A. I., and Moulijn, J. A. (2004). Re-engineering the Chemical Processing Plant: Process Intensification. Boca Raton: M. Dekker.
Stenina, I., and Yaroslavtsev, A. (2022). Modern technologies of hydrogen production. Processes 11, 56.
Stutz, M. J., Hotz, N., and Poulikakos, D. (2006). Optimization of methane reforming in a microreactor—Effects of catalyst loading and geometry. Chem. Eng. Sci. 61, 4027–4040. doi:10.1016/j.ces.2006.01.035
Thursfield, A., and Metcalfe, I. S. (2004). The use of dense mixed ionic and electronic conducting membranes for chemical production. J. Mater. Chem. 14, 2475–2485. doi:10.1039/b405676k
Tong, J., Matsumura, Y., Suda, H., and Haraya, K. (2005). Thin and dense Pd/CeO2/MPSS composite membrane for hydrogen separation and steam reforming of methane. Sep. Purif. Technol. 46, 1–10. doi:10.1016/j.seppur.2005.03.011
Tonkovich, A. L. Y., Yang, B., Perry, S. T., Fitzgerald, S. P., and Wang, Y. (2007). From seconds to milliseconds to microseconds through tailored microchannel reactor design of a steam methane reformer. Catal. Today 120, 21–29. doi:10.1016/j.cattod.2006.07.022
Tonkovich, A., Perry, S., Wang, Y., Qiu, D., Laplante, T., and Rogers, W. A. (2004). Microchannel process technology for compact methane steam reforming. Chem. Eng. Sci. 59, 4819–4824. doi:10.1016/j.ces.2004.07.098
Trimm, D. L. (1997). Coke formation and minimisation during steam reforming reactions. Catal. Today 37, 233–238. doi:10.1016/s0920-5861(97)00014-x
Veziroglu, T., and Barbir, F. (1998). “Emerging technology series, hydrogen energy technologies,” in Tech. rep. (Vienna): United Nations Industrial Development Organization).
Wang, F., Zhang, L., Deng, J., Zhang, J., Han, B., Wang, Y., et al. (2019). Embedded Ni catalysts in Ni-O-Ce solid solution for stable hydrogen production from ethanol steam reforming reaction. Fuel Process. Technol. 193, 94–101. doi:10.1016/j.fuproc.2019.05.004
Yang, W.-S., Xiang, H.-W., Li, Y.-W., and Sun, Y.-H. (2000). Micro-kinetic analysis and Monte Carlo simulation in methane partial oxidation into synthesis gas. Catal. today 61, 237–242. doi:10.1016/s0920-5861(00)00368-0
Yuan, J., Ren, F., and Sundén, B. (2007). Analysis of chemical-reaction-coupled mass and heat transport phenomena in a methane reformer duct for PEMFCs. Int. J. Heat Mass Transf. 50, 687–701. doi:10.1016/j.ijheatmasstransfer.2006.07.005
Yuan, Q., Gu, R., Ding, J., and Lu, J. (2017). Heat transfer and energy storage performance of steam methane reforming in a tubular reactor. Appl. Therm. Eng. 125, 633–643. doi:10.1016/j.applthermaleng.2017.06.044
Zanfir, M., and Gavriilidis, A. (2003). Catalytic combustion assisted methane steam reforming in a catalytic plate reactor. Chem. Eng. Sci. 58, 3947–3960. doi:10.1016/s0009-2509(03)00279-3
Zeng, Z., Liu, G., Geng, J., Jing, D., Hong, X., and Guo, L. (2019). A high-performance PdZn alloy catalyst obtained from metal-organic framework for methanol steam reforming hydrogen production. Int. J. Hydrogen Energy 44, 24387–24397. doi:10.1016/j.ijhydene.2019.07.195
Zhai, X., Ding, S., Liu, Z., Jin, Y., and Cheng, Y. (2011). Catalytic performance of Ni catalysts for steam reforming of methane at high space velocity. Int. J. hydrogen energy 36, 482–489. doi:10.1016/j.ijhydene.2010.10.053
* Permeate Conditions
Keywords: steam methane reforming, process intensification, residence time, space velocity, microreactors, microreactor, membrane reactor, sorption enhanced reactor
Citation: Ganguli A and Bhatt V (2023) Hydrogen production using advanced reactors by steam methane reforming: A review. Front. Therm. Eng. 3:1143987. doi: 10.3389/fther.2023.1143987
Received: 13 January 2023; Accepted: 28 March 2023;
Published: 14 April 2023.
Edited by:
Gaweł Żyła, Rzeszów University of Technology, PolandReviewed by:
Po-Chih Kuo, Delft University of Technology, NetherlandsCopyright © 2023 Ganguli and Bhatt. This is an open-access article distributed under the terms of the Creative Commons Attribution License (CC BY). The use, distribution or reproduction in other forums is permitted, provided the original author(s) and the copyright owner(s) are credited and that the original publication in this journal is cited, in accordance with accepted academic practice. No use, distribution or reproduction is permitted which does not comply with these terms.
*Correspondence: Arijit Ganguli, Z2FuZ3VsaWFyaWppdEBnbWFpbC5jb20=
Disclaimer: All claims expressed in this article are solely those of the authors and do not necessarily represent those of their affiliated organizations, or those of the publisher, the editors and the reviewers. Any product that may be evaluated in this article or claim that may be made by its manufacturer is not guaranteed or endorsed by the publisher.
Research integrity at Frontiers
Learn more about the work of our research integrity team to safeguard the quality of each article we publish.