- School of Mechanical and Materials Engineering, Indian Institute of Technology Mandi, Mandi, India
The increasing energy demands, especially in transportation sector, and the challenges of excess pollution and environmental degradation caused due to the conventional fuels, as well as their limited availability has highlighted the need to look for alternative fuels to sustain future needs. Methane is capable of catering to these demands due to its wide availability, both in renewable and non-renewable energy sources. The present work explores the effect of methane supplementation on the performance and emission characteristics as well as the vibrations in internal combustion engines. A four-stroke compression ignition engine is modified to run as a methane-diesel dual fuel engine where methane is inducted through intake manifold and diesel is directly injected into cylinder. Tests are performed by varying engine load and methane energy levels up to 75%. Our study shows that the participation of methane at lower load conditions is weak due to its higher auto ignition temperature and higher calorific value. The emissions, particularly CO and NO, are observably higher at 75% load conditions due to the efficient combustion and higher temperature at higher load conditions. The vibration studies on the dual fuel combustion indicates that the introduction of methane also suppresses the frequency spectrum of combustion noise and reduces the ringing intensity level of vibration for complete spectrum of engine loads, with the effect being prominent at higher loads. Overall, our results suggests that combustion of methane in dual fuel diesel engine shows distinct characteristics at contrasting load conditions.
1 Introduction
The global energy demand is increasing continuously and the polluting characteristics of the traditional fuels, along with limited availability, geopolitical conflicts and price fluctuations have motivated industries and researchers to search for sustainable and clean energy sources (Chu and Majumdar, 2012). The transportation sector has also been suffering from stringent emission norms and disruptive supply chains, result being the highest transportation costs the world has ever seen. This has created an unprecedented need to look out for alternative fuels which do not compromise on the efficiency of present-day systems and can be applied to the present automotive vehicles with minimal retrofitting to support transition for the future transportation needs.
In the last few years, various fuels have been explored at for transportation needs at research scale (Salvi et al., 2013; Tripathi et al., 2019). Biofuels, methanol, electricity, methane, and hydrogen have attracted lots of interest from researchers and policymakers due to their potential to reduce harmful emissions. However, among these, methane has the ability to address future energy needs due to its availability, strong infrastructure and the ease of its utilization in different forms such as compressed natural gas (CNG), pure methane, pipe natural gas (PNG), etc. (Sahoo et al., 2022; Tripathi and Dhar, 2022) Methane is main element of biogas and its extraction processes require acceleration to meet increasing demand (Chynoweth et al., 2001; Channappagoudra et al., 2020; Deheri et al., 2020; Petrollese and Cocco, 2020). Additionally, the utilization of methane in existing engine requires comparatively less modifications to operate in the dual fuel mode (Singh et al., 2021; Saxena et al., 2022; Tripathi and Dhar, 2022; Tripathi et al., 2022).
The other advantage of using methane with diesel in the existing systems is its clean combustion characteristics in comparison to diesel (Tripathi et al., 2020a), as well its comparable performance characteristics to diesel (Tripathi et al., 2020b). Methane is suitable alternate for CI engines as it has high auto-ignition temperature, anti-knock characteristics, high compression ratio, and comparable heating value than diesel fuel (Porpatham et al., 2008; Xiao et al., 2008). The physiochemical characteristics of diesel and methane fuel are compared in Table 1 (Di Iorio et al., 2016).
Modifying a CI engine into a dual fuel engine by accommodating the injection of methane in the intake manifold is a straightforward way to utilize methane for the CI engine operation (Barata, 1995; Mansor et al., 2017; Tripathi et al., 2018). Various studies in the past investigates the methane-diesel dual fuel engine’s performance characteristics. Dual fuel operation results into lower emission of soot, NOx, and CO2, than traditional CI engines (Carlucci et al., 2011; Maghbouli et al., 2013). Yun and Lee found that the existing methods for prediction of knocking in diesel engine through degree of modulation are imperfect because these methods are based on hearing edges, broadband sound and harmonic noise (Yun and Lee, 2017). The existing literature revealed that vibration amplitude in the CI engine is dependent on the exciting force in the vibratory system; which are mainly driven by engine combustion and other mechanical operations (Webster et al., 1969). Earlier studies have explored that piston-slap, intake and exhaust motion and cooling water circulation have played an important role in engine noise and vibration (Alfredson and Davies, 1970). Although there have been number of studies on the vibrations of diesel engine, very few researchers worked on the noise and vibrational analysis of the methane-diesel dual fuel CI engine (Jenkins, 1975). Selim et al. executed the test with methane diesel dual fuel engine by modifying diesel engine into dual fuel mode and explored that methane has higher knock resistance than LPG-diesel dual fuel engine (Selim, 2004). They also revealed that increase in level of methane energy share causes higher pressure and noise level. Celebi et al. has performed the experiment to determine the noise and vibration characteristics of CNG and biodiesel supplemented diesel engine (Çelebi et al., 2017). They found that the port fuel injection technique of CNG is very helpful in reducing the level of noise and vibration. A recent study has been performed the frequency analysis of a LPG-diesel dual fuel engine and explored that the frequency range of vibration distributions has been contracted with LPG supplementation (Omar et al., 2017). Nag et al. supplemented the hydrogen gas in diesel dual fuelled engine and reported that the vibration and noise levels were reduced with gaseous fuel supplementation (Nag et al., 2019; Nag et al., 2022). Patro et al. has studied the noise and vibration related issues for CNG-diesel dual fuel engine and reported that CNG supplementation resulted in quieter operation (Patro and Larue, 1999). Polk et al. studied the methane-diesel dual fuel engine and explored that higher methane supplementation resulted in knocking tendency as it releases the heat sharply (Polk et al., 2013). This points towards a literature gap and inconclusive knowledge of methane supplementation on the noise and vibration characteristics of methane diesel dual fuel engine.
Thus, the present investigation addresses the vibrational characteristics of methane supplemented diesel engine along with critical analysis of performance and emission characteristics. Additionally, the existing challenges of misfire at part load condition and knocking at higher load condition were also discussed with methane substitution in CI engine. It was observed that methane substitution reduces the ringing intensity and suppresses the frequency spectrum of combustion. The lower methane supplementation at lower load condition has depreciated the engine performance. The presented net mean effective pressure and emission data is great addition for researchers to redesign the engine for dual fuel mode.
2 Experimental setup and methods
The experiments were performed on a four-stroke single cylinder water-cooled direct-injection diesel engine, which was in-house modified to operate in dual fuel mode. The specifications of the test engine is given in Table 2.
The test engine was mounted on a universal test bed connected to a 3-Phase servo motor (Figure 1). The motor was connected to a load cell (Flintec; ULB 100) which provides response to the dynamometer’s programmable logic control (PLC) unit. The in-cylinder pressure sensor (Kistler, 6045B) was fitted in the cylinder head and the diesel fuel pressure sensor (Kistler, 4067E) was mounted on the supply-line. Engine crank-gear was attached to optical-encoder that measures shaft rotation with a resolution of 0.144° CAD. An accelerometer was mounted at the engine head to record engine and combustion vibrations. Data acquisition and electronic control were executed with an engine control system (ECS) (NI-cRIO, 9082), which registers the pressure and speed signals, and allows the control of injection timings of gaseous fuel. Methane was injected to the air intake manifold using a port fuel injector. The methane supply line was fitted with two flame arrestors (Messers, DG91N) and a flame-trap to ensure safety during operation. The flow rate of methane was measured using a Coriolis mass-flow meter (Bronkhorst mini, CORI-FLOW M14) and diesel fuel amount was measured using a shear-beam type load cell (Sensortronics, 65089). An air-box of capacity 0.2 m3 was used for damping the oscillations of intake air. The supplied air was quantified with the help of an orifice plate and U-tube manometer.
The experiments were performed at total 12 different situations of engine load and methane energy shares as shown in Table 3, where the entire load spectrum (25%–75%) and the methane supplementation (0%–100%) was covered to gain insights on real world implementation. Engine speed (1500 RPM) and compression ratio (17.5:1) were kept constant throughout the investigation. The methane injection started at 14.5° ATDC, rather than at 4° ATDC when the exhaust valve closes, which allows ∼10° crank angle safety margin, as there was 9° crank angle valve overlap period after intake valve open till exhaust valve close at 4° ATDC. The methane injection ended at 75.5° bTDC. The duration of methane injection was kept fixed (90° crank angle) throughout the investigation. The injection timings and the valve timings are shown in Figure 2.
The pressure of gas supply line was fixed at 3 bars and its injection amount was varied through a needle valve. The amount of methane energy supplementation is calculated through following Eq. 1.
Where,
3 Results and discussion
The investigation of engine characteristics due to the co-combustion of liquid-gas fuel pair (here, methane and diesel) is interesting as both fuels have their own combustion properties. Additionally, the fumigation of methane also affects the mixing process of air and fuel which may translate into unexpected engine characteristics.
3.1 Effect of methane supplementation on the engine performance parameters
Mean effective pressure (MEP) is an important performance characteristic and is the measure of engine’s capability to perform work. Moreover, it is a crucial parameter for engine design and optimization. Figure 3 describes the variation of gross mean effective pressure (GMEP) at different methane supplementation levels and different engine loads. GMEP is based on combustion pressure during compression and expansion stroke. Our investigation found that at lower load condition, increase in MES reduces the GMEP in comparison to neat diesel operation. At 25% load, as MES level increases from 0% to 75%, the GMEP decreases by 5.9%. This is because of lower combustion temperature at lower load results in inappropriate participation of methane in combustion. On the other hand, at medium and higher load, methane supplementation increases the GMEP. At 50% and 75% engine load, as MES increases from 0% to 75%, the GMEP increases by 5% and 7%, respectively. This is because of higher combustion temperature at higher load results in an appropriate participation of supplemented methane quantity in combustion. Similarly, Figure 4 describes the variation of net mean effective pressure (NMEP) at different engine load and varying quantity of methane energy shares. The NMEP is similar to GMEP, however it calculated for whole engine cycle of 720°. It was found that at lower load methane supplementation reduces the NMEP and at medium and higher load methane supplementation increases the NMEP. As MES increases from 0% to 75%, the NMEP reduces by 6.7% at 25% load and it increases by 5.8% and 6.9% at 50% and 75% load, respectively. This variation of NMEP can be explained on the basis of lower temperature, similar to that for GMEP. The NMEP is also helpful in theoretical calculation of indicated power through following Eq. 2.
where, IP is indicated power, Pm is NMEP, L is length of stroke, A is area of bore, K is number of cylinders and n is number of revolutions per power stroke. The variation of indicated power (IP) at different engine load and MES levels has been shown in Figure 3.
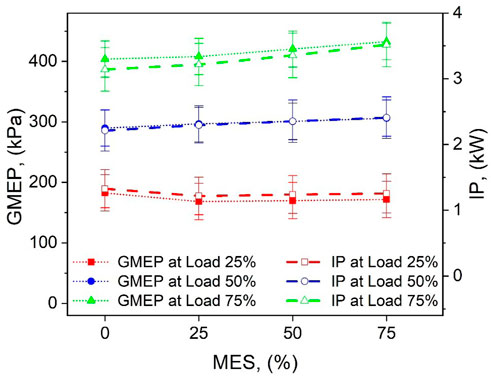
Figure 3. Variation of gross mean effective pressure and indicated power with respect to diesel fuel with MES level at different loads.
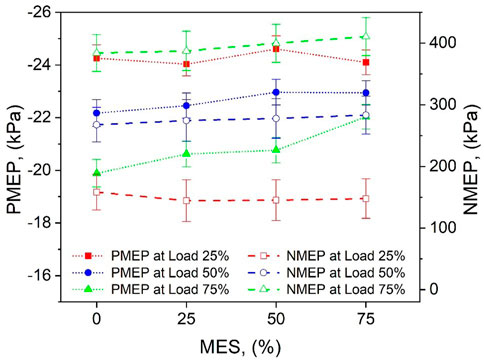
Figure 4. Variation of pumping mean effective pressure and net mean effective pressure with respect to diesel fuel with MES level at different loads.
The difference in GMEP and NMEP is known as pumping mean effective pressure (PMEP). The PMEP is the MEP related with work of air movement during suction and exhaust of air through intake and exhaust valve. Figure 4 shows the variation of PMEP with MES level for different load conditions. It was found that increase in MES level decreases the PMEP at lower load and increases the PMEP at medium and higher load conditions. This is because methane participates in combustion depending on combustion temperature. As load increases the combustion temperature increase and air fuel ratio tends to achieve the stoichiometric air fuel ratio. That causes more active participation of methane in combustion.
The effect of MES is observed on brake thermal efficiency (BTE) is similar to that of GMEP. Figure 5 shows percentage change in BTE w. r.t conventional diesel fuel at different MES and load conditions. It was observed that as MES level increases, percentage increase in BTE also increases at each load condition. Maximum percentage reduction in BTE is 8, 14% and 16% at 25, 50% and 75% MES level in comparison to conventional diesel fuel.
3.2 Effect of methane augmentation on engine emission
Percentage change in different emissions w.r.t conventional diesel fuel at different MES and load level is presented in Figures 6–8. Since methane does not combust completely in engine cylinder that is why it reduces the combustion temperature which directly reduces the formation of NO as shown in Figure 6. It was observed from Figure 6 that the maximum 57% NO reduces in comparison to diesel fuel at 75% MES. Increase in percentage of MES put adverse effect on HC and CO formation. It was observed from Figures 7, 8 that maximum increase in HC and CO emission is 1,146% and 481%, respectively, at 75% MES level in comparison to pure diesel operation. These carbon-containing emissions increased because of inefficient combustion of supplemented CH4. As methane supplementation ratio increased it replaces the air in intake manifold. Ultimately that result in scarcity of oxygen content in engine cylinder. That causes incomplete oxidation of carbon mono-oxide and hydrocarbons. That is why CO and HC emissions were higher for 75% MES as shown in Figures 7, 8. Whereas, it was clear from Figure 6 that NO emission percentage reduction in comparison to diesel fuel is higher for higher methane addition. This is also because of scarcity of oxygen in engine cylinder. As lack of oxygen restrict the chances of complete oxidation. Most of chemical reaction does not take place because of undesired thermodynamic state of charge. Since most of exothermic chemical reaction does not take place, it ultimately results in lower combustion temperature and nitrogen available in air and fuel does not activate itself to form NO. Since methane replaces air in intake manifold. The reduction in air quantity also reduces the available nitrogen quantity in engine cylinder to form NO emission (Tripathi et al., 2020b).
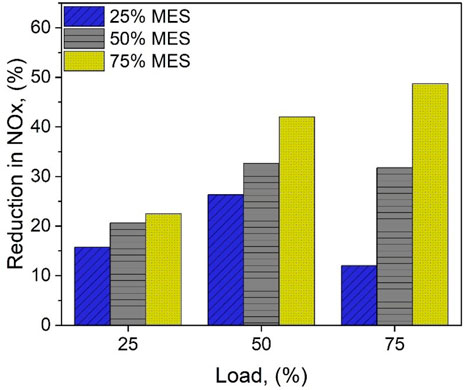
Figure 6. Percentage change in NO emissions with respect to diesel fuel with varying MES level at different loads.
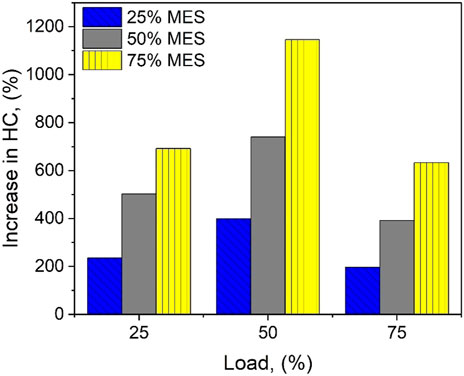
Figure 7. Percentage change in HC emissions with respect to diesel fuel with varying MES level at different loads.
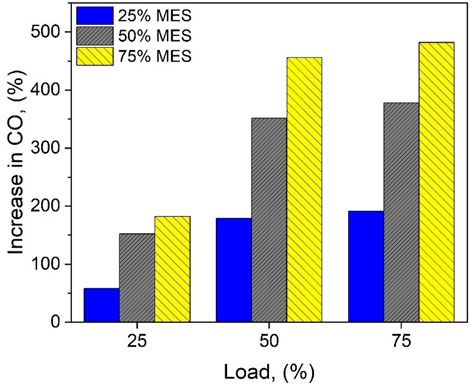
Figure 8. Percentage change in CO emissions with respect to diesel fuel with varying MES level at different loads.
3.3 Frequency pulsations
The frequency variation with load and methane share is described below for vibrations analysis of engine which is captured by using the accelerometer mounted on the cylinder head (Figure 9). The signature captured also depicts the events of air valve opening and closing during the engine operation, which for the tested engine were at −356°, −144°, 144°, and 356°. On comparing the signature for the 0% MES and 75% MES for all the studied, a distinct operation was observed. For the 0% MES, broad combustion spectra has peaks at two different frequencies. However, for the 75% MES, a single spectrum with lower combustion frequency was observed. For each MES, the combustion spectrum shows shrunken frequency range. Methane has a high heat specific capacity and slow-burning rate, which clearly explains the rationale. Moreover, the result opens a scope for the use of accelerometers as a non-intrusive technique for combustion studies.
3.4 Ringing intensity
Ringing Intensity (RI) is an acoustic parameter, which gives us the measure of knock. Basically, RI (flux of acoustic-energy) is formed with pressure-oscillations (Maria et al., 2013; Dernotte et al., 2015). RI is calculated with the help Eq. 3.
Where,
Figure 10 shows the variation of RI with methane energy share and load. The x-axis represents the engine operating condition at different methane energy share and load. For example, L25M0 represents, the engine operating condition corresponding to 25% load that is L and 0% methane energy share that is M. The y-axis represents the normalised ringing intensity that is equal to RI divided by RImax. Here, normalised ringing intensity is termed as knocking index. If its value is greater than one then it causes knocking in operation. Such as, in Figure 10 the condition L75M25 has knocking index nearly equal to 1. Thus, L75M25 condition would corresponds to knocking. The reason behind the knocking at L75M25 is the sudden burning of charge. This sudden combustion of charge occurred because of 1) availability of premixed mixture as methane enhances the premix 2) higher combustion temperature at higher load. In our recent study, the same knocking like behaviour was observed in the in-cylinder pressure plot for similar corresponding conditions at L75M25 (Tripathi et al., 2020a). Figure 11 shows the combustion noise for various engine load and MES. The combustion noise was calculated by converting the cylinder pressure angle domain data to the time domain data followed by the Fast Fourier transformation to convert it to frequency domain. The frequency domain data was then converted to the 3rd octave spectra and A-weighted filter was applied to emphasize frequencies where human hearing is sensitive (Nag et al., 2022). The combustion noise data also presents a spike at L75M25, which confirms the knocking as depicted by the ringing index values.
It was observed that knocking does not occur at L75M50 and L75M75. This is because of replacement of oxygen by methane share is higher at those conditions which result in relatively lower temperature and chances of knocking was reduced. A previous study has reported faster decrease in peak in-cylinder pressure as the MES increases from 25% to 50% (Tripathi et al., 2020a). Moreover, a much lower combustion noise is observed at these operating conditions, as shown in Figure 11. If knocking index value is lower than 0.5 then there are chances of misfire. Such as, in Figure 10 the condition L25M75 has knocking index less than 0.5. Thus, L25M75 condition would corresponds to misfire. The reason behind the misfire at L25M75 is the exceeding the flammability limit of methane. The upper flammability limit of methane has been crossed because of localised methane rich fuel availability. This is because of 1) presence of higher methane quantity at M75 condition and 2) lower combustion temperature at lower load (L25) which does not allow methane to expand and result in localised rich methane fuel, whereas it was observed that misfire does not occur at M25 and M50 at L25. It was due to the lower amount of methane at those conditions and do not exceed the upper flammability limit of methane.
4 Conclusion
Performance, vibration and emissions characteristics of methane-diesel dual fuel CI engine were studied experimentally in this article. The study was performed at twelve test conditions by varying the methane energy shares (0, 25, 50, and 75%) and engine load (25, 50, and 75%). The major findings of this study are:
• The engine load affects the participation of methane in combustion process. The mean effective pressure, which is an important engine performance parameter, exhibits trend reversal at low and high load conditions on addition of methane. At lower load, methane supplementation reduces the mean effective pressure, and the opposite is observed at higher load. This is due to the higher temperatures at high load conditions.
• Oxides of nitrogen emissions are reduced with methane supplementation, however, increase in CO and HC emissions were observed.
• For methane energy share enhancement, the combustion noise spectrum shows narrower frequency range. The application of methane in diesel engine also reduces the ringing intensity level of vibration.
Overall, this study highlighted the distinct engine performance characteristics at contrasting load conditions. The engine vibrations however reduced with addition of methane at all load conditions. Therefore, methane supplementation at higher loading is beneficial, both in respect to performance and vibrations, however, the drop in performance at lower loads needs to be addressed.
Data availability statement
The raw data supporting the conclusions of this article will be made available by the authors, without undue reservation.
Author contributions
All authors contributed to manuscript writing, revision, read, and approved the submitted version.
Funding
Authors thankfully recognize the funding support by (DST- SERB); Delhi, India vide Project Number. ECR/2015/000135, “Study of Synergistic Use of Hydrogen and other Alternative Fuels in a Dual Fuel Engine for Emissions Reduction” at Indian Institute of Technology (IIT) Mandi, Himachal Pradesh (H.P.), India.
Conflict of interest
The authors declare that the research was conducted in the absence of any commercial or financial relationships that could be construed as a potential conflict of interest.
Publisher’s note
All claims expressed in this article are solely those of the authors and do not necessarily represent those of their affiliated organizations, or those of the publisher, the editors and the reviewers. Any product that may be evaluated in this article, or claim that may be made by its manufacturer, is not guaranteed or endorsed by the publisher.
References
Alfredson, R. J., and Davies, P. O. A. L. (1970). The radiation of sound from an engine exhaust. J. Sound. Vib. 13, 389–408. doi:10.1016/s0022-460x(70)80044-x
Barata, J. M. M. (1995). Performance and emissions of a dual fueled DI diesel engine. SAE Tech. Pap., 952364. doi:10.4271/952364
Carlucci, A. P., Laforgia, D., Saracino, R., and Toto, G. (2011). Combustion and emissions control in diesel–methane dual fuel engines: The effects of methane supply method combined with variable in-cylinder charge bulk motion. Energy Convers. Manag. 52, 3004–3017. doi:10.1016/j.enconman.2011.04.012
Çelebi, K., Uludamar, E., Tosun, E., Yıldızhan, Ş., Aydın, K., and Özcanlı, M. (2017). Experimental and artificial neural network approach of noise and vibration characteristic of an unmodified diesel engine fuelled with conventional diesel, and biodiesel blends with natural gas addition. Fuel 197, 159–173. doi:10.1016/j.fuel.2017.01.113
Channappagoudra, M., Ramesh, K., and Manavendra, G. (2020). Effect of injection timing on modified direct injection diesel engine performance operated with dairy scum biodiesel and Bio-CNG. Renew. Energy 147, 1019–1032. doi:10.1016/j.renene.2019.09.070
Chu, S., and Majumdar, A. (2012). Opportunities and challenges for a sustainable energy future. Nat 488, 294–303. doi:10.1038/nature11475
Chynoweth, D. P., Owens, J. M., and Legrand, R. (2001). Renewable methane from anaerobic digestion of biomass. Renew. Energy 22, 1–8. doi:10.1016/s0960-1481(00)00019-7
Deheri, C., Acharya, S. K., Thatoi, D. N., and Mohanty, A. P. (2020). A review on performance of biogas and hydrogen on diesel engine in dual fuel mode. Fuel 260, 116337. doi:10.1016/j.fuel.2019.116337
Dernotte, J., Dec, J. E., and Ji, C. (2015). Energy distribution analysis in boosted HCCI-like/LTGC engines - understanding the trade-offs to maximize the thermal efficiency. SAE Int. J. Engines 8, 956–980. doi:10.4271/2015-01-0824
Di Iorio, S., Magno, A., Mancaruso, E., and Vaglieco, B. M. (2016). Characterization of particle number and mass size distributions from a small compression ignition engine operating in diesel/methane dual fuel mode. Fuel 180, 613–623. doi:10.1016/j.fuel.2016.04.108
Jenkins, S. H. (1975). Analysis and treatment of diesel-engine noise. J. Sound. Vib. 43, 293–304. doi:10.1016/0022-460x(75)90329-6
Maghbouli, A., Saray, R. K., Shafee, S., and Ghafouri, J. (2013). Numerical study of combustion and emission characteristics of dual-fuel engines using 3D-CFD models coupled with chemical kinetics. Fuel 106, 98–105. doi:10.1016/j.fuel.2012.10.055
Mansor, M. R. A., Abbood, M. M., and Mohamad, T. I. (2017). The influence of varying hydrogen-methane-diesel mixture ratio on the combustion characteristics and emissions of a direct injection diesel engine. Fuel 190, 281–291. doi:10.1016/j.fuel.2016.11.010
Maria, A., Cheng, W. K., Kar, K., and Cannella, W. (2013). Understanding knock metric for controlled auto-ignition engines. SAE Int. J. Engines 6, 533–540. doi:10.4271/2013-01-1658
Nag, S., Dhar, A., and Gupta, A. (2022). Hydrogen-diesel co-combustion characteristics, vibro-acoustics and unregulated emissions in EGR assisted dual fuel engine. Fuel 307, 121925. doi:10.1016/j.fuel.2021.121925
Nag, S., Sharma, P., Gupta, A., and Dhar, A. (2019). Combustion, vibration and noise analysis of hydrogen-diesel dual fuelled engine. Fuel 241, 488–494. doi:10.1016/j.fuel.2018.12.055
Omar, F. K., Selim, M. Y. E., and Emam, S. A. (2017). Time and frequency analyses of dual-fuel engine block vibration. Fuel 203, 884–893. doi:10.1016/j.fuel.2017.05.034
Patro, T. N., and Larue, D. A. (1999). Alternate fueled powertrain - an insight into its combustion related NVH issues. SAE Tech. Pap. doi:10.4271/1999-01-1758
Petrollese, M., and Cocco, D. (2020). Techno-economic assessment of hybrid CSP-biogas power plants. Renew. Energy 155, 420–431. doi:10.1016/j.renene.2020.03.106
Polk, A. C., Gibson, C. M., Shoemaker, N. T., Srinivasan, K. K., and Krishnan, S. R. (2013). Detailed characterization of diesel-ignited propane and methane dual-fuel combustion in a turbocharged direct-injection diesel engine. Proc. Institution Mech. Eng. Part D J. Automob. Eng. 227, 1255–1272. doi:10.1177/0954407013487292
Porpatham, E., Ramesh, A., and Nagalingam, B. (2008). Investigation on the effect of concentration of methane in biogas when used as a fuel for a spark ignition engine. Fuel 87, 1651–1659. doi:10.1016/j.fuel.2007.08.014
Sahoo, S., Kumar, V. N. S. P., and Srivastava, D. K. (2022). Quantitative analysis of engine parameters of a variable compression ratio CNG engine using machine learning. Fuel 311, 122587. doi:10.1016/j.fuel.2021.122587
Salvi, B. L., Subramanian, K. A., and Panwar, N. L. (2013). Alternative fuels for transportation vehicles: A technical review. Renew. Sustain. Energy Rev. 25, 404–419. doi:10.1016/j.rser.2013.04.017
Saxena, M. R., Rana, S., and Maurya, R. K., and (2022). Analysis of low- and high-temperature heat release in dual-fuel RCCI engine and its relationship with particle emissions. Energy Resour. Technol. 144. doi:10.1115/1.4053517
Selim, M. Y. E. (2004). Sensitivity of dual fuel engine combustion and knocking limits to gaseous fuel composition. Energy Convers. Manag. 45, 411–425. doi:10.1016/s0196-8904(03)00150-x
Singh, P., Kumar, R., Sharma, S., and Kumar, S. (2021). Effect of engine parameters on the performance of dual-fuel CI engines with producer gas—a review. Energy Fuels 35, 16377–16402. doi:10.1021/acs.energyfuels.1c02279
Tripathi, G., and Dhar, A. (2022). Performance, emissions, and combustion characteristics of methane-diesel dual-fuel engines: A review. Front. Therm. Eng. 0, 13. doi:10.3389/fther.2022.870077
Tripathi, G., Sharma, P., and Dhar, A. (2022). Computational study of diesel injection strategies for methane-diesel dual fuel engine. Clean. Eng. Technol. 6, 100393. doi:10.1016/j.clet.2021.100393
Tripathi, G., Sharma, P., and Dhar, A. (2020). Effect of methane augmentation on combustion stability and unregulated emissions in compression ignition engine. Fuel 263, 116672. doi:10.1016/j.fuel.2019.116672
Tripathi, G., Sharma, P., and Dhar, A. (2020). Effect of methane augmentations on engine performance and emissions. Alex. Eng. J. 59, 429–439. doi:10.1016/j.aej.2020.01.012
Tripathi, G., Sharma, P., Dhar, A., and Sadiki, A. (2019). Computational investigation of diesel injection strategies in hydrogen-diesel dual fuel engine. Sustain. Energy Technol. Assessments 36, 100543. doi:10.1016/j.seta.2019.100543
Webster, J. C., Woodhead, M. M., and Carpenter, A. (1969). Identifying diesel engine sounds. J. Sound. Vib. 9, 241–246. doi:10.1016/0022-460x(69)90030-3
Xiao, F., Sohrabi, A., and Karim, G. A. (2008). Effects of small amounts of fugitive methane in the air on diesel engine performance and its combustion characteristics. Int. J. Green Energy 5, 334–345. doi:10.1080/15435070802229100
Keywords: diesel engine, alternative fuel, dual fuel, methane, emission, vibration
Citation: Tripathi G, Nag S, Sharma P and Dhar A (2023) Effect of methane supplementation on the performance, vibration and emissions characteristics of methane-diesel dual fuel engine. Front. Therm. Eng. 3:1101333. doi: 10.3389/fther.2023.1101333
Received: 17 November 2022; Accepted: 09 January 2023;
Published: 17 January 2023.
Edited by:
Haifeng Liu, Tianjin University, ChinaCopyright © 2023 Tripathi, Nag, Sharma and Dhar. This is an open-access article distributed under the terms of the Creative Commons Attribution License (CC BY). The use, distribution or reproduction in other forums is permitted, provided the original author(s) and the copyright owner(s) are credited and that the original publication in this journal is cited, in accordance with accepted academic practice. No use, distribution or reproduction is permitted which does not comply with these terms.
*Correspondence: Atul Dhar, YWRkQGlpdG1hbmRpLmFjLmlu