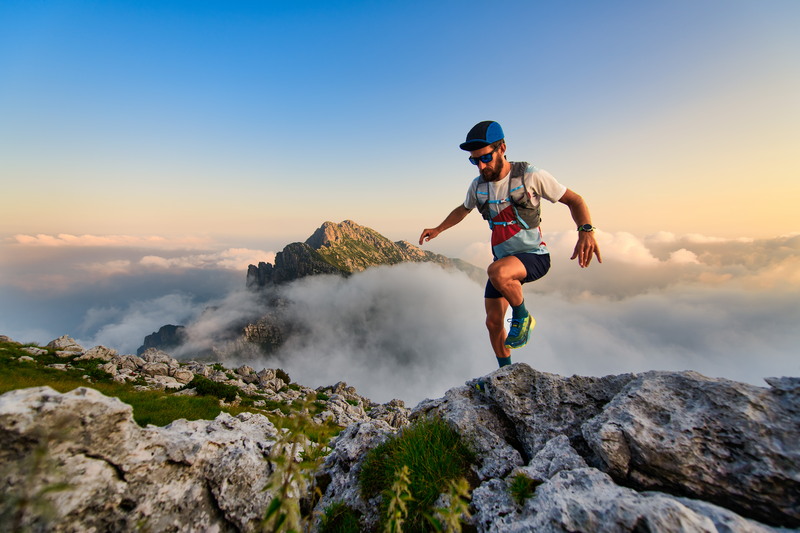
95% of researchers rate our articles as excellent or good
Learn more about the work of our research integrity team to safeguard the quality of each article we publish.
Find out more
REVIEW article
Front. Sustain. Resour. Manag. , 17 April 2023
Sec. Sustainable Materials
Volume 2 - 2023 | https://doi.org/10.3389/fsrma.2023.1127001
As the global consumption of lithium-ion batteries (LIBs) continues to accelerate, the need to advance LIB recycling technologies and create a more robust recycling infrastructure has become an important consideration to improve LIB sustainability and recover critical materials to reuse in new LIB production. Battery collection, sorting, diagnostics, and second-life usage all contribute to the LIB logistics network, and developments in each of these areas can improve the ultimate recycling and recovery rate. Recent progress in LIB recycling technology seeks to increase the amount of valuable metal compounds, electrode materials, and other LIB components that are recoverable and that can be redeployed in new LIB production or other markets. This review establishes an overview of these developments and discusses the strengths and weaknesses of each major recycling technology. Of particular note are the differences in recycling technology and infrastructure requirements created by various LIB markets, as well as the techno-economic considerations for different recycling methods based on the evolving LIB formats and component compositions.
The global drive toward electrification of vehicles, coupled with both existing consumer electronic (CE) usage and the anticipation of expanded grid storage, has rapidly accelerated the demand for lithium-ion batteries (LIBs). The World Economic Forum estimates that the value of the overall LIB market will grow to $300B by 2030 (Alliance, 2019). In the electric vehicle (EV) and battery electric storage system (BESS) sectors, the consumption of LIBs is expected to grow respectively from 269 GWh and 56 GWh in 2021 to 2,600 GWh and 1,194 GWh in 2030 (BloombergNEF, 2021, 2022). To meet this growth, demand for LIB cathode raw materials will likewise increase, which will continue to put a strain on existing supply sources. Demand for cobalt, for example, is estimated to be around 270,000 tons in 2030 (Pillot, 2020), which is 80% over the estimated 2020 cobalt supply from mining. Mining of minerals also presents an ethics challenge. For example, the Democratic Republic of the Congo, which currently represents the world's largest source of cobalt, has been heavily criticized for dangerous mining practices that can result in accidents, overexertion, exposure to toxic chemicals, and violence (Murray, 2022). The demand gap and ethical issues can in part be alleviated by low-cobalt cathode technologies, such as low-cobalt lithium nickel cobalt manganese oxide (NCM) or lithium iron phosphate (LFP). However, even with a reduced demand for cobalt, the continued supply of other critical materials, such as lithium, remains a pressing issue. Furthermore, the improper disposal of an increasing number of end-of-life (EOL) LIBs leads to environmental concerns (Winslow et al., 2018), especially given the possibility of hazardous compounds derived from electrolyte, cobalt, copper, and nickel leaching out and contaminating water supplies and ecosystems.
The efficient recycling of LIBs therefore can provide a source of relief for both disposal and critical materials supply issues. The extraction and collection of the components inside LIBs mitigate the amount of waste that ultimately ends up in a landfill and provides a source of materials for reuse (Peters et al., 2017; Granholm, 2021). In addition, efficient recycling of LIBs can also reduce the amount of waste generated in the production process for LIBs (Dai et al., 2022). Manufacturing scrap and defective batteries can likewise be transformed into materials for reuse in LIBs or other applications.
This review focuses on novel technologies, as well as design and infrastructure considerations, that can improve the efficiency and sustainability of the LIB recycling supply chain. The current U.S. recycling rate of LIBs is low and is often estimated to be around 5% (O'Connor, 2021). The low recycling rate can be attributed to a number of issues, including both available technology and surrounding infrastructure, and is primarily centered on the recycling of EOL CE LIBs, given the larger current availability (Bai et al., 2020). The journey for EOL LIBs from consumer to recycler is multi-step, having to pass from collectors and sorters to processors, before finally being recycled back into usable materials (Figure 1). It is of critical importance that these steps that convey batteries to be reclaimed utilize best-in-class automation, logistics, and diagnostic methods to improve the economics, reliability, and safety of EOL LIB handling. Recently, the Department of Energy invested $5.5MM in the Lithium-Ion Battery Recycling Prize to stir innovation in addressing these types of infrastructure issues (HeroX, 2022).
Current recycling methods primarily degrade the battery into elemental compounds and then harvest those compounds for reuse. Battery components, such as cathode and anode, must then be resynthesized in order to be reused in new batteries. Direct recycling is championed as an alternative method that can reclaim certain components of the battery, such as cathode and anode, non-destructively, thus shortening the pathway for materials from EOL to reintegration into new LIBs. The value of the output of direct recycling can be 30–40% more than hydrometallurgical and pyrometallurgical recycling for NCM and LFP (Dunn J. et al., 2022). Additionally, lithium cobalt oxide (LCO), NCM, and LFP produced through direct recycling are estimated to be 43, 16–27, and 15% lower in cost than their virgin counterparts, respectively (Wang et al., 2018).
Recycling considerations for LIBs start with their design and usage, which can affect how LIBs are collected, transported, and processed. LIBs can be separated into three primary market segments: CE, EV, and BESS (Ding et al., 2019). The CE market includes LIBs for phones, laptops, power tools, gadgets and toys, and drones. The EV market includes LIBs in cars, trucks, boats, planes, and other vehicles. BESS LIBs are used to store electricity generated from intermittent renewable sources such as wind, solar power, and tidal power (Ding et al., 2019). Different fields of use have different requirements for properties; typical example specifications for each market are summarized in Figure 2 (Wang and Huang, 2011). These differences have implications on how LIBs are ultimately reclaimed during the recycling process.
Figure 2. Relative performance requirements for the three primary LIB markets: consumer electronics (CE), electric vehicle (EV), and battery electric stationary storage (BESS).
Typical CE LIB lifespan is around 2–6 years (Winslow et al., 2018; Washington Post, 2022), so the requirements for cycling life are typically lower (e.g., 500~1,000 cycles). CE LIBs come in smaller single cells (Recycling Inside, 2022) or packs containing two to eight small cells (Admin, 2022; ZDNET, 2022). The uniformity among the LIBs is low, as there is little standardization between different devices and appliances, even for those of the same kind. CE LIBs focus more on the volumetric energy density because of the limited space in the CE. Therefore, high energy density and high value cathode materials such as LCO or NCM with higher cobalt compositions are typically used (Wang and Huang, 2011; Stan et al., 2014). Furthermore, these batteries are commonly embedded in devices (Salinas et al., 2019), which can create difficulties for battery removal at end of life.
The life of an EV LIB is around 9 years (Winslow et al., 2018) so, EV LIBs require better cycling life than CE LIBs. EV LIBs typically come with a large pack with multiple cells, and uniformity (Khateeb et al., 2004; Liu C. et al., 2019; Chen et al., 2021) among the LIBs is important. Because of the large quantity requirement of LIBs, the cost needs to be lower on average than CE LIBs (Ding et al., 2019). The EV LIBs focus more on the specific energy density (Khateeb et al., 2004; Ding et al., 2019) but also have a larger emphasis on safety given the application and battery size. Therefore, medium energy density cathode materials with acceptable safety metrics [such as medium-to-low cobalt NCM, lithium nickel cobalt aluminum oxide (NCA)] or even lower energy density materials with higher safety [such as lithium manganese oxide (LMO) or LFP], or a blend of materials, are used.
Lastly, BESS LIBs require the largest overall quantity of LIB capacity per battery system. Lifespan (>10 years) (Pagliaro and Meneguzzo, 2019) and cost (Kim et al., 2022) are the most important factors. Since there is no limitation on space and mass given their stationary use, energy density is not the critical criterion for BESS LIBs. BESS LIBs will typically have larger cells and many cells forming substantial packs and systems. LFP has been the cathode chemistry of choice due to its low cost and long lifespan.
Among all the components of LIB, cathode materials play arguably the most critical role in the LIB's electrochemical performance and safety properties, and typically stand as the highest individual component cost (Gaines et al., 2018) (e.g., ~36% of the overall LIB cell). Table 1 shows the properties of various common cathode materials.
Table 1. LIB material properties, operating characteristics, and markets for common cathode chemistries: lithium cobalt oxide (LCO), lithium manganese oxide (LMO), lithium iron phosphate (LFP), lithium nickel cobalt manganese oxide (NCM), and lithium nickel cobalt aluminum oxide (NCA) (Wang and Huang, 2011; Mulder et al., 2013; Stan et al., 2014; Harper et al., 2019; Warner, 2019; Le Varlet et al., 2020; Choi et al., 2021).
The advantage of LCO includes a stable structure, higher capacity, also a high volumetric energy density due to high tap density and operating voltage (Markets, 2022). The disadvantage of the LCO includes poor safety, high cost, and fair cycling life (Markets, 2022). Considering the requirements of CE LIBs which have critical requirements of volumetric energy density, LCO has dominated the CE market. Recently, some of the NCM LIBs have also started appearing in the CE market because of their lower cost and higher safety, especially in larger format devices that have less stringent volumetric energy density requirements. NCM, LMO, and LFP occupy the majority of the EV market (Mulder et al., 2013). NCM has a higher capacity and a high energy density, especially for high nickel NCM, which has both high capacity and strong cycling life. The advantages of LFP LIBs include high safety, long cycling life, and low cost, which are the reasons why it has become more prevalent in the EV market and also dominated the market for BESS (Choi et al., 2021; Gutsch and Leker, 2022; Kim et al., 2022).
The markets for LIBs and the designs that are catered to those markets have a profound effect on the various strategies and approaches used to reclaim LIB materials at end of life. The consequences of choices in component materials, form factor, packaging, usage, and collection channels all play a role in shaping the recycling ecosystem. The recycling pathway, the various considerations due to these design choices, and the technologies being developed to address the growing recycling needs will be discussed in the following sections.
Collecting EOL LIBs is the first step toward bridging LIB consumption and the reclamation process. Currently, collection is a major challenge, and only a small amount of LIB is able to be recovered for recycling. The U.S. Department of Energy has estimated that the current collection rate can be as low as 5% (Simmons, 2021), while also recommending a long-term objective to achieve a recycling rate of 90% across all LIBs by 2030 (Granholm, 2021). Efforts toward a high LIB recycling rate can be compared to efforts to recycle lead acid batteries, which has been a nationwide success in the U.S., achieving recycling rates of over 99% (National Recycling Rate Study, 2022). However, currently the U.S., there is no federal regulation that promotes the recycling of LIBs. Some states have implemented battery recycling laws. Most notably California has passed the Responsible Battery Recycling Act of 2022 (LegiScan, 2023) to create battery producer-funded stewardship programs for collecting and recycling batteries. In the EU, a directive has been established to promote the collection and recycling of LIBs in member states (European Parliament of the Council, 2006) with a goal to reach 45% LIB recycling by 2016. The results have been mixed, as not all member states have been able to achieve the targets of the directive. Neumann et al. and Winslow et al. provide a more detailed summary of these recent global policy initiatives (Winslow et al., 2018; Neumann et al., 2022).
The CE market has traditionally dominated LIB usage, which is the leading cause for low collection rates. Collecting CE LIB is a challenging process compared to the EV and BESS LIBs because, in addition to mixed legislative policy success for implementing collection programs, no strong infrastructure exists for systematic collection. In the U.S., companies such as Call2Recycle have developed nationwide collection programs that partner with various retailers to provide collection sites for batteries. Despite being arguably the largest battery collector in North America, Call2Recycle reported about 1,000 tons of LIBs collected in 2021 (Annual Report, 2019), which is just a small fraction of the estimated LIBs available (48,500 tons; Gaines et al., 2021) to be collected and recycled. Therefore, it is critical that a number of technological, policy, and infrastructural initiatives are developed to address the gap in collection.
With the rapid growth of both EV and BESS sectors, a shift in the relative contributions of these market segments to EOL LIBs is forthcoming. The total volume of collectible domestic EOL EV and BESS is expected to exceed the volume of collectible EOL CE batteries in 2027 and exceed 1MM tons by 2030 (LaMotte and Clare, 2022). These markets have an easier collection process. For one, the average battery size is larger, leading to the handling of fewer batteries for an equivalent weight processed. For EVs, collection can occur at centralized locations, such as dealerships (AXIOS, 2022) or repair and maintenance shops (Li, 2022), where the responsibility of proper battery disposal is transferred to the service provider or contractor, instead of to the consumer. For BESS, the majority of LIBs will be handled by larger corporations or licensed contractors (Salim et al., 2019). These would also provide an opportunity to establish better disposal and collection processes over the CE market sector.
Battery sorting is a critical component of the battery recovery process, allowing for better aggregation of similar batteries, more efficient transportation, and the development of more effective processes for battery recycling. Collectors, especially for CE LIBs, will send collected mixed battery waste streams to sorters for further processing. LIBs sorting can be separated into three steps: isolating LIBs from other batteries or waste (Bebat, 2022a; How to Identify Different Types of Battery Chemistries, 2022); diagnosing the LIBs based on state-of-health (SOH) factors, such as remaining useful life (RUL) and state-of-charge (SOC), to decide if the LIBs can be repurposed for secondary use or recycling (Pagliaro and Meneguzzo, 2019; Martins et al., 2021; The Equation, 2022); and sorting the battery based on different major properties, such a cathode chemistry (Fricke, 1999; Larouche et al., 2020; Call2Recycle, 2022). An example breakdown of these processes is shown in Figure 3. Currently, sorting by type is widely used as the primary form of sorting with more development being done on SOH and chemistry-based sorting for LIBs.
Considering the difference in the recovery processes among various types of batteries, sending the appropriate battery types to their corresponding recyclers is the first and arguably most important step. Sorting by battery type also benefits further storage and transportation since lithium-containing batteries having special transportation (Huo et al., 2017) and storage (CTS, 2022) requirements that tend to be more costly than other batteries. For LIB and non-LIB separation, manual sorting processes dominate the market. Trained personnel visually identify and physically sort batteries that are placed in front of them via a conveyor or sorting table (Eco Batt, 2021; Bebat, 2022a,b; Sorting Batteries, 2022). Such a process relies heavily on the training and capability of personnel (in addition to overall availability of labor) to identify and sort batteries accurately and efficiently. More recent developments in battery sorting automation rely on vision-based technologies and artificial intelligence to separate batteries based on their optical characteristics, such as label or shape (Eco Batt, 2021; Snapshot, 2022). This process is claimed to have higher sorting efficiency and higher accuracy. Although the vision technology helps with collecting data on batteries and feeding them into a machine learning algorithm, which further optimizes the efficiency and accuracy of sorting, the technology has some limitations. Refind Technologies has designed a line to identify all cylindrical batteries up to D size and sort all 9 V batteries into four classes: alkaline, NiMH, NiCd, and lithium (Eco Batt, 2021; Recycling Product News, 2022), while Opti-Sort can only sort cylindrical batteries (Harper et al., 2019). Also, a large amount of manual pre-sorting (Bebat, 2022a) can be required before entering the vision sorting machine to remove non-conforming batteries, which further reduces the efficiency of the overall process. Li Industries recently developed a Smart Battery Sorting System that leverages vision, chemical measurements, machine learning, and industrial internet of things (IIoT) technology to automatically sort a much wider range of battery types, shapes, and chemistries (Call2Recycle, 2022; Submission, 2022). However, vision technologies alone are limited in their ability to identify batteries, especially when the batteries are not packaged uniformly or are damaged. These issues could be alleviated by more standardized disposal and collection policies (Call2Recycle, 2017; Team, 2019). Overall, continued development is needed to fully deploy an automated solution into the sorting industry to reduce pain points related to labor cost, accuracy, and efficiency.
Not all discarded LIBs are truly at end of life. Although they may no longer be optimal for continued use in their original application, many LIBs qualify for second life use based on their SOH, since different applications have varied criteria for performance. For example, the LIBs retired from the EV can be reused for BESS (Lyu et al., 2019; Battery, 2021). However, due to the inconsistency of degradation among cells in the pack, the SOH of each cell may be different. Thus, the diagnosis or prediction of SOH and remaining useful life (RUL) can be applied to determine if LIBs need to be recycled or whether they can be reused. The prediction approaches, according to the mechanisms they used, can be classified as model-based methods and data-driven methods (Berecibar et al., 2016; Li et al., 2019). Model-based SOH and RUL simulate the behavior (e.g., electrochemical behaviors and thermal behaviors) of batteries with numerical models, and thus predict the SOH and RUL. Electrochemical models that solve the mass and charge kinetics with partial differential equations are typically employed (Ramadesigan et al., 2012). Electrical models are also widely used with electrical-circuit analogs (Nejad et al., 2016). Data-driven methods for SOH and RUL prediction require large sets of degradation-related data rather than an accurate degradation model, thus relying heavily on the experimental data that captures the historical observations of the batteries (Hu et al., 2015; Xiong et al., 2018).
For both model-based and data-driven predictions, the most commonly used diagnostic method is physically making an electrical connection to the LIB and applying various electrochemical assessments. This group of diagnostic methods can be separated into the static and dynamic methods, while the static method is a one-time measurement and not related to the working status, dynamic diagnosis focuses on the change of the parameters during the charging and discharging process (Xiaoyu et al., 2014). Table 2 shows different examples of parameters and methods used in determining SOH of LIBs and their advantages and disadvantages. Static diagnosis takes measurements when batteries are in open circuit. The diagnosis can finish within seconds, but the prediction error can be as high as 10% (Berecibar et al., 2016). Dynamic diagnosis measures the parameters while batteries are in operation. Such diagnosis needs to take measurements over a portion of or a whole operation cycle (which can take up to hours), but the prediction error tends to be lower (< 5%) within well-modeled working conditions (Waag et al., 2014; Berecibar et al., 2016; Lipu et al., 2018; Sarmah et al., 2019). The drawback of the physical contact measurement is that single-parameter sorting methods are not accurate while multiple-parameter sorting methods increase the complexity and time (Chen W. et al., 2019). Non-contact diagnosis using X-ray (Chen and Shen, 2017) or ultrasound technology has also been proposed and developed. Titan Advanced Energy Solutions has developed a new sorting technology that uses ultrasound to detect the LIBs SOH, which is claimed to be fast and accurate (Titanaes, 2022). Furthermore, analysis methods utilizing fuzzy logic, machine learning, or other computational techniques have been used to increase the accuracy of assessments (Xiong et al., 2018; Lyu et al., 2019).
Table 2. Examples of different state-of-health (SOH) sorting methods with their advantages and disadvantages (Chen and Shen, 2017; Chen W. et al., 2019; Lyu et al., 2019; Li R. et al., 2020; Battery, 2021; Titanaes, 2022).
A third step of sorting that can prove useful to downstream processing is cathode material sorting, which separates the LIBs into different categories by their cathode chemistry. Cathode sorting helps hydrometallurgical and pyrometallurgical recycling reduce the complexity of the process and increase the purity level of recycled materials (Larouche et al., 2018). The value of generated material from these processes is improved if, for example, sorting provides LIB waste streams with high Co or Ni content (e.g., LCO, NCM, NCA), when compare to LIB waste streams with higher Fe or Mn content (e.g., LFP, LMO), due to the relative value of these different metals (Larouche et al., 2020; Lander et al., 2021). Sorting is also necessary for more sustainable and cost-effective recycling technologies such as direct recycling, which requires relatively pure single cathode waste streams. Cathode materials can be retrieved from battery information databases if those chemistries are known for particular battery models, which can be more common in the EV and BESS LIB market due to the lower number of battery models available. For CE LIBs, the identification of different models and correlation to a database of chemistries may prove to be more challenging. Overall, visual identification methods could be improved with the better standardization of labeling or if other identification technologies such as RFID and QR code or barcode tags are used (Preradovic and Karmakar, 2010; Gaines, 2018; Zheng et al., 2021). Other available technologies for identifying cathode chemistries include both invasive and non-invasive spectroscopic techniques (OnTo-Technologies, 2014; Submission, 2022), which have been recently developed in automated sorting systems.
Recycling of LIBs can be organized in the following stages: (Alliance, 2019) pretreatment (including deactivation and disassembly), (BloombergNEF, 2021) separation/extraction/ purification, and (BloombergNEF, 2022) redeployment (Chen W. et al., 2019; Martins et al., 2021). All recycling methods generally subject LIBs to these three stages of processing, but their end products differ. Pyrometallurgical and hydrometallurgical recycling operations use high temperature and/or strong alkaline/acid solution to destructively smelt LIBs or leach LIBs, followed by purification and precipitation processes (Chagnes and Pospiech, 2013; Chen M. et al., 2019; Makuza et al., 2021). The end product consists of elemental compounds that can be used for new battery materials synthesis or applications in other industries. Direct recycling, on the other hand, focuses on non-destructive separation, retaining viable electrode material that is isolated from the rest of the battery (Wu et al., 2022). These electrode materials can be purified and regenerated to form new electrode material for direct reuse in new batteries (thus bypassing a re-synthesis process). Other battery components are typically recycled in a more similar manner. For example, Cu and Al obtained from the current collectors of LIBs are typically isolated and processed as scrap metal (Sommerville et al., 2020; Wu et al., 2022). Plastics from packaging and the separator, as well as other organic materials, may be harvested for recycling or burned to recover energy (Makuza et al., 2021; Dang et al., 2022). Figure 1 summarizes the main processes of these different recycling methods and how they interact with the rest of the LIB lifecycle. Direct recycling is able to bypass materials re-synthesis for recycled electrode materials, thus shortening the pathway for EOL LIB incorporation into new batteries. Figure 4 similarly shows the differences between process and output for electrode material components undergoing pyrometallurgical, hydrometallurgical, and direct recycling. Pyrometallurgical and hydrometallurgical recycling downcycles these materials into elemental compounds, while direct recycling maintains electrode material integrity and function (Harper et al., 2019; Wu et al., 2022).
Pretreatment is essential to all types of the recycling process. The pretreatment includes disassembly, discharging, and shredding, comminution, or exposing of the LIB core materials. Pretreatment helps to reduce the safety issues by removing any residual energy stored in the LIB and improve consistency among starting materials that are entering downstream processes (Zhang et al., 2013). Different types of LIBs may require different levels of pretreatment to render the battery sufficiently safe or prepared for further processing.
For all types of recycling methods, the disassembly process is essential for certain types of LIB formats. The majority of EV and BESS LIBs, and some CE LIBs, are assembled into a pack containing multiple single LIB modules and/or cells. For ease of recycling, the packs can first be disassembled into modules, and modules are disassembled into single LIBs (Harper et al., 2019; Wu et al., 2022). The LIB packs can be large and heavy and include extra accessories (Arora et al., 2016; Xia et al., 2018; ZDNET, 2022), such as electronics, cooling systems, and various types of packaging (Harper et al., 2019). The large size and varying formats make packs hard to be directly processed by semi-automated or fully automated machinery. The constituent materials of the extra accessories can also introduce impurities during the recycling process, so separation and removal of these extra accessories is ideal (Zhang et al., 2013).
Disassembly can be manual (Blankemeyer et al., 2021; Martins et al., 2021), semi-automatic (Fan et al., 2022), or automatic (Zorn et al., 2022). Manual disassembly is common but not as efficient or safe (Waldmann et al., 2016). However, when there are a variety of pack and battery form factors and other design features, manual disassembly may be required. The semi-automatic disassembly process comprises both manual steps and some automated machine-assisted steps (Herrmann et al., 2014). Machines replace the worker to work on tedious and redundant tasks such as removing screws and moving modules out of the packs (Kay et al., 2022). Semi-automatic processes are popular in industry, especially for larger and more standardized battery systems (Fan et al., 2022). Fully automatic disassembly, on the other hand, is an ideal standard as it reduces labor costs and improves efficiency. However, this mode of disassembly is challenging because of the lack of conformity among different LIB pack designs (Zorn et al., 2022). An automatic disassembly line can be expensive and may need to be adapted for each different pack design, thus reducing practicability for most applications except for those that have a low pack design variance (Zorn et al., 2022). Harper et al. (2019) provides further review on the recycling of LIBs with a focus on the EV sector, with discussion on the different design considerations and types of disassembly (Harper et al., 2019). The authors highlight the variation among battery shapes and the lack of standardization for battery cells, packs, or systems, emphasizing the challenges in all types of efficient disassembly, especially in attempts to automate disassembly processes.
The LIBs before or after disassembly need to be discharged before they can be safely processed further (Gratz et al., 2014; Chen W. et al., 2019; Sommerville et al., 2020). If undischarged LIBs are shorted during the recycling process, the LIBs can cause serious damage due to thermal events. This issue has been of particular concern in proper LIB waste management with LIB-related fires in waste management facilities becoming more common in the last decade (O'Connor, 2021). Discharging, or an equivalent process, seeks to reduce or eliminate this use by removing most of the residual, stored energy in LIBs. Common discharging methods includes resistive discharging through a solid electrical connection (Dewan et al., 2010; Huria et al., 2021), thermal discharging (Feng et al., 2018), and salt solution discharging (Lv et al., 2018). The LIBs can be discharged by connecting the anode and cathode with high-power resistors (Sommerville et al., 2020). Such discharging systems have become commercially available and are designed to accommodate various types of LIBs (such as different EV LIBs) (Dewan et al., 2010). This method can be limited by varying LIB designs and so can be hard to accommodate all incoming LIBs. Thermal discharging heats the battery at 100–500°C for a specific time (Sommerville et al., 2020). The degradation of LIBs components makes the LIBs self-discharging (Mo Seong et al., 2018). The method is compatible with pyrometallurgical recycling because it can be combined with the steps in the pyrometallurgical. In fact, in many cases, pyrometallurgical recycling may not require a separate discharge process at all (Wu et al., 2022). Salt solution discharging involves an ionic process that electrolyzes water to discharge LIBs (Nembhard, 2020). This method has been widely used for all types of LIB recycling. Some other processes seek to bypass a separate discharge process entirely. Shredding the LIBs under liquid nitrogen or inert atmosphere prevents rapid oxidation of the LIB when the electrode are exposed to air (Fan et al., 2020). Shredding with the application of a water spray can discharge the battery while shredding the battery. The water also provides a method of controlling the thermal discharge from the battery during this process, since the overall process is less controlled than other discharge methods but is preferred in many recycling operations due to lower processing costs (Harper et al., 2019).
Physical separation is essential to hydrometallurgical recycling and direct recycling and can be used in pyrometallurgical recycling as well. The separation processes rely primarily to mechanical methods to isolate various materials such as the current collector (Cu, Al), packaging materials (Fe, plastics), separator, and electrolyte from cathode and anode materials. The removal of these materials can improve the effectiveness of downstream processes, as well as reduce the amount of low value materials present in the processing stream. The powder generated from the physical separating line is called “black mass”, which contains the cathode and anode active material, binder [e.g., polyvinylidene fluoride (PVDF)], carbon, and some Al, Fe, Cu, and organic impurities (Punt et al., 2022).
Depending on the cell format of the LIBs, which can vary depending on application, the physical separation process is also different. Figure 5 shows several examples of the black mass generation process for common cell formats, such as polymer case pouch cells, Al case prismatic pouch cells, and steel case cylindrical cells (Full et al., 2020). The first step is crushing the discharged individual cells or small packs with high-power crushers, which downsizes the LIBs into smaller flakes (Shin et al., 2020). Prismatic cells which have heavier casing materials (Full et al., 2020) can first be separated by weight using a process like wind sifting. This sifting process to remove larger, heavier materials (such as larger Al casing) reduces issues downstream with shredding. A shredding process can mill the small flakes into a coarse powder (Ku et al., 2016; Wang X. et al., 2016; Ebin et al., 2018). For cylindrical LIBs with steel casing, the steel casing can be left in the coarse powder or removed by magnetic separators (Harper et al., 2019; Sommerville et al., 2020). The separators in LIBs can be removed by a second wind sifter (Vaško, 2015; Zheng et al., 2017), which applies relatively weaker air flow when compared to the first wind sifting. Then, the coarse powders are processed by sieving to remove larger-sized particles. The blocked materials can be further shredded into smaller particle sizes to obtain finer powder (Ku et al., 2016; Wang X. et al., 2016; Ebin et al., 2018). After the second shaking sieve, the majority of the black mass is separated from the rest of the materials, including Al and Cu current collector, as well as packaging materials. The black mass can be treated by furnaces around 300–500°C to remove the binder and electrolyte. The mixtures of Al, Cu, and packaging materials can be further isolated from each other from the black mass by a gravity separation (Vaško, 2015; Sommerville et al., 2020). The lighter Al and packaging materials are brought to one side by the application of airflow, thus separating from heavier Cu powders. The steel, Al case, separator, Al powder, Al polymer case, Cu powder, and black mass are collected and packaged individually. The black mass generated from physical separation is widely recycled by the hydrometallurgical or pyrometallurgical methods. The black mass with low impurity can also be recycled by direct recycling with the addition of cathode/anode separation steps, such as froth flotation (Kim et al., 2021; Verdugo et al., 2022).
After separation, hydrometallurgical methods use one or more aqueous solutions to leach the metals in LIBs, which is then followed by different stages of purification and precipitation to recover the transition metals and lithium. A variety of aqueous solutions have been tested and applied to leach the LIBs. Alkaline leaching includes ammonia-based systems, sodium hydroxide, while acid leaching typically utilizes inorganic strong acids, such as HCl, H2SO4, and HNO3, or organic acids, such as citric acid, ascorbic acid, oxalic acid, and formic acid (Li et al., 2012; Ku et al., 2016; Gao et al., 2017; Huang et al., 2018; Du et al., 2022). After leaching, purification procedures are used to remove impurity ions. The purification methods include solvent extraction, chemical precipitation, and other separation methods like electrodeposition, electrolysis, adsorption, flotation, and ion exchange (Larouche et al., 2020). The solvent extraction method uses the difference in solubility of metal or metal compounds in aqueous or organic solutions. The chemical precipitation methods rely on the differences in the dissolution of metal compounds under various pH conditions (Du et al., 2022). After purification, the metals are precipitated using methods such as co-precipitation and sol-gel. Both methods adjust the proportion of metal ions in the leaching solution and use some precipitate agent to form elemental compounds. The co-precipitation method is limited to the inorganic acid leaching system while the sol-gel method can be applied to organic acid (Wu et al., 2022). Figure 6 shows several hydrometallurgical methods for different cathode materials. LCO generates materials such as Co(OH)2 and Li2CO3 (Wang et al., 2011); NCM decomposes to Ni1/3Co1/3Mn1/33(OH)2 (or alternatively isolated Ni, Co, and Mn compounds) and Li2CO3 (Sidiq et al., 2022; Singapore Battery Consortium, 2022), and LFP can be broken down into FePO4 and Li3PO4 or Li2CO3 (Li H. et al., 2017; Larouche et al., 2020). Those products generated by hydrometallurgical processes are Co, Ni, Mn, Fe compounds, and Li salt, which can be precursor materials but are typically not able to be directly used in the production of new LIBs. To make LIB precursor, sometimes additional processes are required. For example, the common products NiSO4, CoSO4 and MnSO4 from hydrometallurgical methods need an additional precipitation or crystallization procedure to be ready for use in NCM synthesis (Ma et al., 2020).
Although pyrometallurgical recycling can also benefit from physical separation processes (e.g., by increasing the amount of higher value material entering downstream processes; Ruismäki et al., 2020) LIBs with less pretreatment and separation are also able to be directly processed. High temperature treatments smelt the LIBs to form a metal alloy. The organic components, such as binder, electrolytes, and separator, are burned off during the smelting process (Wu et al., 2022). Pyrometallurgical recycling can be categorized into three groups: direct roasting (Li et al., 2014), In situ reduction roasting (Zhou et al., 2021), and salt roasting (Makuza et al., 2021; Du et al., 2022; Wu et al., 2022). The direct roast reduces the metal oxide at >1,000°C with reducing agents. In situ roasting involves pyrolysis under a vacuum or inert atmosphere without additives, which uses a relatively lower temperature than direct roasting, between 800 and 1,000°C (Li et al., 2016; Xiao et al., 2017; Zhou et al., 2021). Salt roasting can be operated at even lower temperature <600°C, and reports have shown higher materials recovery rates (Wang D. et al., 2016; Dang et al., 2018; Fan et al., 2019). Because the products generated from pyrometallurgy are alloys and slag, further processing is needed to improve the value of the generated materials. Hydrometallurgical processing, using leaching and purification steps to isolate elemental compounds, is typically employed downstream of pyrometallurgical recycling (Mayyas et al., 2019; Dang et al., 2020).
Despite high energy use and higher emission rates, the pyrometallurgical process is popular in industry because of its simple procedures, high productivity, and its ability to leverage off existing mining procedures and equipment (Liu W. et al., 2019; Makuza et al., 2021). However, recently, the large energy cost and toxic emissions are making this process less attractive. Furthermore, pyrometallurgical recycling can efficiently extract those heavy elements like Co, Ni, Fe, and Cu, but the anode and organic components are not able to be recovered. To recover Li, extra steps need to be added which can result in higher costs and longer processing times (Dunn J. B. et al., 2022).
Unlike pyrometallurgical and hydrometallurgical recycling methods, which destroy the structure of cathode materials, direct recycling technology collects and purifies electrode material without destroying the structure (Figure 7). Various forms of physical separation can be used with direct recycling, although due to higher purity requirements for separation, some processes specific to direct recycling have been developed to better isolate the electrode materials from the rest of the LIB. After disassembly, deactivation, and some other processing to open cells, such as shredding, direct recycling methods focus on separating the electrode materials from the current collector by removing the binder (Ross, 2020; Zhan et al., 2020). The most common binder is the nonaqueous organic material PVDF. Aqueous binders, such as styrene-butadiene rubber (SBR) and carboxymethyl cellulose (CMC), gained popularity recently as well (Courtel et al., 2011; Zhang et al., 2021). Most binders can be removed by heat treatment or solvent dissolution. For example, PVDF decomposes to C/CO2 and HF at temperatures of 400–550°C (Zhan et al., 2020; Fujita et al., 2021; Wang et al., 2021)and can also be dissolved by organic solvents, such as N-methyl-2-pyrrolindone (NMP), dimethylformamide, or the greener solvent Cyrene (Marshall et al., 2021). Aqueous binders can similarly be decomposed at elevated temperatures (Zhang J. et al., 2018) or washed in an aqueous solution (Courtel et al., 2011; Li J. et al., 2020).
After binder removal, electrode powder can be separated from the current collector by mechanical means (e.g., water sonication, mechanical washing, sieving, and air separation; Li X. et al., 2017; Sloop and Sloop, 2023). Those electrode powders contain cathode active materials, anode materials (normally graphite), and small amount of Al and Cu impurities from current collectors generated during the separation process. Studies have reported removal of these impurities using various methods, such as low-concentration alkaline solutions (Ku et al., 2016; Chen M. et al., 2019) or weak acid solutions (Fink et al., 2022) or mechanical, particle size, or density-based separation (Tsang et al., 2017). After purification, the anode and cathode material need to be separated; flotation and density separation are common techniques for this purpose (Shin et al., 2020; Folayan et al., 2021; Zhan et al., 2021). The flotation separates the cathode and anode based on hydrophobicity differences, since the carbon-based anode material is hydrophobic, and most cathode material is hydrophilic (Folayan et al., 2021). Density separation relies on separating the lower density graphite anode from the cathode materials (Wolf et al., 2021).
Upon completion of purification, high purity EOL cathode and anode materials are generated. However, these recovered cathode materials are typically lithium deficient and may have structural damage (Chikkannanavar et al., 2014; Yang et al., 2020). Likewise, the anode may have some residual lithium or other chemical or morphological changes (Sabisch et al., 2018). Regeneration processes are used to restore the performance of these electrode materials so that they can be redeployed in new LIBs. These regeneration processes are discussed in more detail below.
Some additional steps are required to bridge the output of the recycling processes with usable inputs in manufacturing processes. The products generated from pyrometallurgy are metal alloys and slags, like Co-Ni-Cu-Fe alloy, and Mn-rich slag. The products can be used in fields such as construction (Rämä et al., 2018). However, for the production of new cathode material, further processing is required. As mentioned above, typically hydrometallurgical processes are added to isolate elemental compounds, thus aligning the outputs of pyrometallurgical and hydrometallurgical to a similar set of materials. Following some additional processing, these products generated from hydrometallurgy can be considered as precursors of new LIB cathode synthesis.
Effectively, at this point in the process for hydrometallurgical and pyrometallurgical recycling, the downstream steps are identical to new cathode synthesis. For example, the metal precursors for NCM are mixed (e.g., sol-gel or co-precipitation) and subject to some preprocessing, further mixed with a lithium source, and then typically undergo a two-step synthesis to generate new cathode material. For standard synthesis procedures, the first step is around 400–550°C for 4–6 h, and the second step is around 800–1,000°C for 12 h (Xia et al., 2009; Hua et al., 2014; Duan et al., 2021). Table 3 outlines some example re-synthesis methods. Some recent hydrometallurgical methods also have proposed direct co-precipitation of the various cathode elemental compounds after dissolution and purification to produce mixed precursor that is ready to be mixed with a Li source to undergo re-synthesis (Duan et al., 2021; Ascend Elements, 2022). These processes are able to bypass the additional steps of precipitating precursor and then undergoing an additional mixing process. Upon completion of the synthesis steps, the new cathode material is ready to be used in new LIBs.
Table 3. Methods for NMC/LCO re-synthesis from precursors for pyrometallurgical/hydrometallurgical recycling and regeneration for direct recycling.
After the separation and purification procedure in direct recycling, purified but lithium-deficient cathode materials are generated. To recover the performance of the cathode, a regeneration process is required to relithiate and reverse any structural damage from previous electrochemical cycling. Relithiation methods includes hydrothermal (Shi et al., 2018; Xu et al., 2021), which requires elevated pressure and temperature; solid phase sintering (Nie et al., 2015; Li J. et al., 2020) which requires high temperature; ionothermal methods (Wang M. et al., 2020); and electrochemical methods (Yang et al., 2020). Although both hydrometallurgical/pyrometallurgical recycling and direct recycling require heat treatment procedures to generate functional cathode, the complexity and energy inputs are different, with direct recycling requiring a shorter heat treatment step on average (Table 3). The simpler procedures, shorter time, and lower temperatures make direct recycling potentially more environmentally sustainable and economically efficient.
The direct recycling of LFP can have additional advantages not observed in other cathode materials. Commercial LFP materials all come with conductive coating to increase the electronic conductivity and rate performance (Doeff et al., 2006; Oh et al., 2010). Also, nano-sized LFP materials have become popular recently and demonstrate superior performance compared to micron-sized LFP (Ding et al., 2010; Borkiewicz et al., 2015). During the pyrometallurgy/hydrometallurgy, the original carbon coatings are destroyed, and the generated precursors do not retain the original particle size (Chagnes and Pospiech, 2013; Zhang G. et al., 2019; Larouche et al., 2020). To produce commercial LFP from these recycled precursor components, the entire synthesis process must be redone from scratch. Shown in the Figure 8, ball milling (Gao et al., 2007) or nano-bead milling (Islam et al., 2015) is the most commonly used process to downsize precursors, during which 0.3-0.4 mm milling balls are added to the precursor mixture. The rotor run under high rotation speed to stir the precursor mixture with milling balls for 1–3 h. After milling to the nanoscale, the mixture needs to be dried by spray dryers, which preserves the original chemical and morphological properties (Gao et al., 2007; Rigamonti et al., 2020). During the synthesis process, the carbon coatings are generated from the incomplete burning of organic compounds under N2, H2/Ar, or other inert atmosphere (Belharouak et al., 2005; Mi et al., 2005; Konarova and Taniguchi, 2010). On the other hand, direct recycling has a non-destructive treatment of the cathode during the separation and purification process, which retains the cathode's original structure, morphology, and coatings or other modifications.
Figure 8. Process examples to produce LFP from hydrometallurgical/pyrometallurgical recycling (top) and direct recycling (bottom).
The downside for direct recycling in this case is revealed when considering the evolution of morphology from older EOL LIBs. These older LIBs may not have the same cathode morphology and thus modification to the morphology during regeneration may be required (Xu et al., 2019). Likewise, for other types of cathode materials, such as NCM, changes in preference for composition, dopants/coatings, and other modifications may create a gap between the materials produced from recycling and materials desired for new batteries. Various methods of upcycling have been proposed as a way to bridge that gap to either change the composition or modify the recycled cathode material to meet performance or manufacturing processing demands (Schiavi et al., 2021; Lin et al., 2022; Parikh et al., 2022; Zhang et al., 2022).
Although graphite anode material is not considered as valuable compared to cathode material, recovered graphite from EOL LIBs can have multiple applications if properly recycled. There have been recent developments on anode recovery methods as a way of improving the overall sustainability and economics of recycling (Zhang J. et al., 2019). Figure 9 shows several recycling pathways for graphite. In some cases, methods have been proposed to recycle EOL LIBs with an initial separation of anode and cathode (Li et al., 2012; Yang and Xi, 2015), while in other cases the entire LIB is processed and separation occurs later (Punt et al., 2022). When anode sheets are able to be separated from the rest of the components, the graphite direct recycled using washing procedures to free the graphite from aqueous-based binders (Courtel et al., 2011; Li J. et al., 2020). The separated graphite can contain impurities, including Cu (Punt et al., 2022) and Li salts (e.g., Li2CO3, Li2O, LiF, ROCO2Li, CH3OLi, and Li2O) (An et al., 2016).
Pyrometallurgical methods are typically unable to recover the graphite because of the initial high temperature processing that burns off organic material. The graphite that is derived from hydrometallurgical methods can be of high purity if the other LIB components are dissolved and isolated (Ma et al., 2019). As described above, direct recycling of anode when the cathode and anode are not initially separated requires a separation/purification process such as flotation or density separation (Folayan et al., 2021; Zhan et al., 2021) to isolate the anode from the cathode. The resulting recovered graphite can have a small amount of impurities including Cu, Al, Li salt, and some cathode materials (Chen et al., 2022). To further purify the graphite, the lithium and other metal components can be extracted by acid leaching (Chen et al., 2022; Wang et al., 2022).
Purified recycled graphite powder can be reused in LIBs through a regeneration process (Sabisch et al., 2018). The graphite can also be repurposed for other applications using upcycling methods (Liu et al., 2020). For example, recovered graphite has been shown to be able to generate graphene (Zhang Y. et al., 2018; Yang et al., 2019) and carbon sorbent (Du et al., 2022).
The choice of recycling technology is highly dependent on the economics of recycling costs and outputs. These economics, in turn, are related directly to the choice of cathode chemistry in the manufacturing of the LIB. Although Ciez and Whitacre found that NCM cathode is about 20% of the cost of input materials into a NCM cylindrical cell (Ciez and Whitacre, 2019; Schneider et al., 2019) and 8% of the total manufacturing cost, the recovered cathode material or its elemental constituents can be most of the revenue generated from recycling (Mayyas et al., 2019; Lander et al., 2021). Therefore, the profitability, and viability of the recycling operation, is tied to the cathode that is being processed. Lander et al. performed an analysis on this profitability (Figure 10) for hydrometallurgical, pyrometallurgical, and direct recycling operations in the U.S. and found a wide range of results based on the cathode material of the input LIB. Pyrometallurgical operations tended to be unprofitable regardless of the input material, while hydrometallurgical operations could be profitable with cathode compositions containing more cobalt and nickel. Direct recycling was profitable in all cases (Lander et al., 2021). Yang et al. (2021) compare the different recycling methods cost among different countries and present the overall revenue generated per kg cell recycled (Yang et al., 2021). The authors found that in general pyrometallurgical operations were not profitable, while direct recycling operations were. Similar results are also shown by economic comparison work from Yu et al. (2021).
As LFP becomes a more dominant cathode in the market (Lunde, 2022), recyclability of these LFP LIBs are increasingly becoming a concern. The issue with LFP as a cathode material is that it requires the same recycling effort for a lower overall value, since the material lacks high value Co or Ni (Table 4). The majority of the material value of LFP is in the production process and less so in the raw materials, due to the relatively low economic value of the main constituents (Li, Fe, P) (Wang T. et al., 2020). Both pyrometallurgical and hydrometallurgical processes have intrinsic challenges with processing. Pyrometallurgy is not feasible due to the lack of usable product, while hydrometallurgy can extract primarily Li as a somewhat valuable product (Beaudet et al., 2020). Therefore, only direct recycling is a truly economically viable technology for recycling LFP LIBs, barring any subsidies or other policy-related assistance.
Development of strategies to combat the increasing number of LIBs to be reclaimed has seen an uptick in activity in recent years, as LIBs have come to forefront as a vital aspect of transportation electrification, grid modernization, and high energy and power portable electronics. However, a temporal and scale-up gap remains between many of these new developments and the realized application in industry. Collection and sorting remain primarily less-than-ideal in terms of optimization and prevalence, and more work is needed to be done to modernize the infrastructure surrounding these activities to improve recycling rates. On the recycling side, many of the newer ideas in recycling have yet to see incorporation into industrial practices. In particular, direct recycling is still on the cusp of being commercially accepted as an alternative to pyrometallurgical and hydrometallurgical recycling, despite the clear need for a new solution for lower-value LIBs, such as those containing LFP or LMO. The recycling space is large enough that all of three primary recycling methods can co-exist with one another. It is important, therefore, to understand the relative strengths and weaknesses of the various technologies available, such that the overall efficiency of the entire recycling ecosystem can be improved.
Looking forward into how a modernized LIB recycling supply chain could reveal itself, the authors see a split between how the different LIB markets will be largely handled. CE LIBs, having such a wide variety (PCH, 2022) of form factors and a lack of unified or centralized reclamation process, will require greater policy intervention and investment in infrastructure to handle the collection and sorting of these batteries (Electrek, 2022). This market segment is where the most development is needed for automated solutions and improved logistics prior to arriving at the recycler. Furthermore, second use applications are less likely given the difficulty of measuring SOH for each battery. On the recycling side, because high cobalt chemistries will continue to dominate the CE market, developments specific to pyrometallurgical and hydrometallurgical processes can be effective and, given the existing industrial presence of these methods, will have a shorter time to market. These considerations may change in the future as novel energy storage technologies are developed and commercialized, such as flow-batteries, solid state batteries, and sodium-ion batteries.
On the other hand, EV and BESS LIBs have fewer collection and sorting concerns, although the introduction of certain technologies in these areas will be beneficial. The development of SOH monitoring will help reduce the number of LIBs that actually need to enter the recycling process, and second-use strategies will continue to be developed to make best use of these batteries (Lyu et al., 2019; Battery, 2021). Challenges in recycling are centered around the efficient dismantling of large systems, as well as the profitable recycling of these LIBs as lower-value cathode chemistries take a more dominant position in the market (Lander et al., 2021; Lunde, 2022). Direct recycling is favorable under these circumstances, but to integrate direct recycling, cathode sorting will be required. The integration of several steps, such as sorting and recycling or recycling and cathode production, some of which is already underway in industry, can lower transportation costs and improve overall recycling economics.
Overall, recycling has become a dynamic research and development space that has gained significant traction, government interest, and private investment over the past few years. The need for these technologies in terms of environmental benefit, critical materials reclamation, and reduced LIB lifecycle cost is clear. It is important then for researchers, policymakers, and industry leaders to understand the careful application of the available technologies (as well as consideration toward infrastructure and policy) to their respective areas of strength, taking into account both the design considerations for LIBs, their respective markets, and the resulting techno-economics of recovery.
PZ: constructs the manuscript structure, drafts the manuscript, contributes to the majority of technology content with figures and tables, and edits the manuscript. DY: drafts the manuscript, contributes to the economic content and part of technology content, edits, and reviews the whole manuscript. YX, TY, and ZL: reviews and edits manuscript. All authors contributed to the article and approved the submitted version.
PZ, TY, and DY are employees of Li Industries, Inc. ZL is employee of Virginia Tech and has ownership in Li Industries, Inc.
The remaining author declares that the research was conducted in the absence of any commercial or financial relationships that could be construed as a potential conflict of interest.
All claims expressed in this article are solely those of the authors and do not necessarily represent those of their affiliated organizations, or those of the publisher, the editors and the reviewers. Any product that may be evaluated in this article, or claim that may be made by its manufacturer, is not guaranteed or endorsed by the publisher.
Admin (2022). The Construction of the Li-ion Battery Pack. Available online at: https://news.inventuspower.com/blog/construction-of-the-li-ion-battery-pack (accessed November 6, 2022).
Alliance, G. B. (2019). Vision for a Sustainable Battery Value Chain in 2030: Unlocking the Full Potential to Power Sustainable Development and Climate Change Mitigation. Geneva, Switzerland: World Economic Forum
An, S. J., Li, J., Daniel, C., Mohanty, D., Nagpure, S., Wood, D. L., et al. (2016). The state of understanding of the lithium-ion-battery graphite solid electrolyte interphase (SEI) and its relationship to formation cycling. Carbon. 105, 52–76. doi: 10.1016/j.carbon.2016.04.008
Annual Report (2019). Call2Recycle and United States. Available online at: https://www.call2recycle.org/annualreport/ (accessed November 6, 2022).
Arora, S., Shen, W., and Kapoor, A. (2016). Review of mechanical design and strategic placement technique of a robust battery pack for electric vehicles. Renew. Sust. Energ. Rev. 60, 1319–1331. doi: 10.1016/j.rser.2016.03.013
Ascend Elements (2022). Ascend Elements News and Insights on Advanced EV Battery Materials and Recycling. Available online at: https://ascendelements.com/news-insights/ (accessed November 14, 2022).
AXIOS (2022). The Charge to Keep EV Batteries Out of the Trash. Available online at: https://www.axios.com/2022/02/18/ev-batteries-recycling-trash (accessed November 6, 2022).
Bai, Y., Muralidharan, N., Sun, Y. K., Passerini, S., Stanley Whittingham, M., Belharouak, I., et al. (2020). Energy and environmental aspects in recycling lithium-ion batteries: concept of battery identity global passport. Mat. Today. 41, 304–15. doi: 10.1016/j.mattod.2020.09.001
Battery, B. (2021). What's is Lithium Battery conSistency and How to Sort. Available online at: https://www.bonnenbatteries.com/how-to-sort-the-lithium-battery/ (accessed November 14, 2022)
Beaudet, A., Larouche, F., Amouzegar, K., Bouchard, P., and Zaghib, K. (2020). Key challenges and opportunities for recycling electric vehicle battery materials. Sustainability. 12, 5837. doi: 10.3390/su12145837
Bebat (2022a). Available online at: https://www.bebat.be/en/sorting (accessed November 7, 2022).
Bebat (2022b). Sorting Batteries? This is How We Do it. Available online at: https://www.bebat.be/en/blog/how-sorting-batteries (accessed November 6, 2022).
Belharouak, I., Johnson, C., Amine, K. (2005). Synthesis and electrochemical analysis of vapor-deposited carbon-coated LiFePO4. Electrochem. Commun. 7, 983–988. doi: 10.1016/j.elecom.2005.06.019
Berecibar, M., Gandiaga, I., Villarreal, I., Omar, N., Van Mierlo, J., Van den Bossche, P., et al. (2016). Critical review of state of health estimation methods of Li-ion batteries for real applications. Renew. Sust. Energ. Rev. 56, 572–587. doi: 10.1016/j.rser.2015.11.042
Blankemeyer, S., Wiens, D., Wiese, T., Raatz, A., and Kara, S. (2021). Investigation of the potential for an automated disassembly process of BEV batteries. Procedia CIRP. 98, 559–564. doi: 10.1016/j.procir.2021.01.151
BloombergNEF (2021). Electric Vehicle Sales Set to Rise Faster Than Ever, but More Policy Action Needed to Get on Track for Net Zero. BloombergNEF. Available online at: https://about.bnef.com/blog/electric-vehicle-sales-set-to-rise-faster-than-ever-but-more-policy-action-needed-to-get-on-track-for-net-zero/ (accessed December 15, 2021).
BloombergNEF (2022). Global Energy Storage Market to Grow 15-Fold by 2030. BloombergNEF. Available online at: https://about.bnef.com/blog/global-energy-storage-market-to-grow-15-fold-by-2030/ (accessed December 15, 2021).
Borkiewicz, O. J., Wiaderek, K. M., Chupas, P. J., and Chapman, K. W. (2015). Best practices for operando battery experiments: influences of X-ray experiment design on observed electrochemical reactivity. J Phys Chem Lett. 6, 2081–2085. doi: 10.1021/acs.jpclett.5b00891
Call2Recycle (2017). Damaged, Defective, and Recalled Batteries, Call2Recycle| United States. Available online at: https://www.call2recycle.org/safety/damaged-defective-and-recalled-batteries/ (accessed November 7, 2022).
Call2Recycle (2022). Call2Recycle Partners with Li Industries to Innovate Battery Sorting and Recycling | Call2Recycle| United States. Available online at: https://www.call2recycle.org/call2recycle-partners-with-li-industries-to-innovate-battery-sorting-and-recycling/ (accessed November 6, 2022).
Chagnes, A., Pospiech, B. (2013). A brief review on hydrometallurgical technologies for recycling spent lithium-ion batteries. J. Chem. Technol. Biotechnol. 88, 1191–1199. doi: 10.1002/jctb.4053
Chen, H., and Shen, J. (2017). A degradation-based sorting method for lithium-ion battery reuse. PLoS ONE 12, e0185922. doi: 10.1371/journal.pone.0185922
Chen, M., Ma, X., Chen, B., Arsenault, R., Karlson, P., Simon, N., et al. (2019). Recycling end-of-life electric vehicle lithium-ion batteries. Joule. 3, 2622–2646. doi: 10.1016/j.joule.2019.09.014
Chen, Q., Huang, L., Liu, J., Luo, Y., and Chen, Y. A. (2022). new approach to regenerate high-performance graphite from spent lithium-ion batteries. Carbon. 189, 293–304. doi: 10.1016/j.carbon.2021.12.072
Chen, S., Garg, A., Gao, L., and Wei, X. (2021). An experimental investigation for a hybrid phase change material-liquid cooling strategy to achieve high-temperature uniformity of Li-ion battery module under fast charging. Int. J. Energ. Res. 45, 6198–212. doi: 10.1002/er.6241
Chen, W., Liang, J., Yang, Z., and Review, L. (2019). GA of lithium-ion battery for electric vehicle applications and beyond. Energy Procedia. 158, 4363–4368. doi: 10.1016/j.egypro.2019.01.783
Chikkannanavar, S. B., Bernardi, D. M., and Liu, L. (2014). A review of blended cathode materials for use in Li-ion batteries. J. Power Sources. 248, 91–100. doi: 10.1016/j.jpowsour.2013.09.052
Choi, D., Shamim, N., Crawford, A., Huang, Q., Vartanian, C. K., Viswanathan, V. V., et al. (2021). Li-ion battery technology for grid application. J. Power Sourc. 511, 230419. doi: 10.1016/j.jpowsour.2021.230419
Ciez, R. E., and Whitacre, J. F. (2019). Examining different recycling processes for lithium-ion batteries. Nat. Sustain. 2, 148–156. doi: 10.1038/s41893-019-0222-5
Courtel, F. M., Niketic, S., Duguay, D., Abu-Lebdeh, Y., and Davidson, I. J. (2011). Water-soluble binders for MCMB carbon anodes for lithium-ion batteries. J. Power Sources. 196, 2128–2134. doi: 10.1016/j.jpowsour.2010.10.025
CTS (2022). Lithium Ion Battery Storage and Maintenance Char Ging. Available online at: https://www.Crtes.Com/Cts_Images/Whitepapers/CTS-WP001_whitepaper.pdf (accessed November 7, 2022).
Dai, Q., Spangenberger, J., Ahmed, S., Gaines, L., Kelly, J. C., Wang, M., et al. (2022). EverBatt: A Closed-loop Battery Recycling Cost and Environmental Impacts Model. Available online at: http://www.osti.gov/servlets/purl/1530874/ (accessed November 5, 2022).
Dang, H., Chang, Z., Zhou, H., Ma, S., Li, M., Xiang, J., et al. (2022). Extraction of lithium from the simulated pyrometallurgical slag of spent lithium-ion batteries by binary eutectic molten carbonates. Int. J. Miner Metall Mater. 29, 1715–1721. doi: 10.1007/s12613-021-2366-3
Dang, H., Li, N., Chang, Z., Wang, B., Zhan, Y., Wu, X., et al. (2020). Lithium leaching via calcium chloride roasting from simulated pyrometallurgical slag of spent lithium ion battery. Sep. Purif. Technol. 233, 116025. doi: 10.1016/j.seppur.2019.116025
Dang, H., Wang, B., Chang, Z., Wu, X., Feng, J., Zhou, H., et al. (2018). Recycled lithium from simulated pyrometallurgical slag by chlorination roasting. ACS Sust. Chem. Eng. 6, 13160–13167. doi: 10.1021/acssuschemeng.8b02713
Dewan, A., Donovan, C., Heo, D., and Beyenal, H. (2010). Evaluating the performance of microbial fuel cells powering electronic devices. J. Power Sources. 195, 90–96. doi: 10.1016/j.jpowsour.2009.07.001
Ding, Y., Cano, Z. P., Yu, A., Lu, J., and Chen, Z. (2019). Automotive Li-Ion Batteries: Current Status and Future Perspectives. Electrochem Energ Rev. 2, 1–28. doi: 10.1007/s41918-018-0022-z
Ding, Y., Jiang, Y., Xu, F., Yin, J., Ren, H., Zhuo, Q., et al. (2010). Preparation of nano-structured LiFePO4/graphene composites by co-precipitation method. Electrochem. Commun. 12, 10–13. doi: 10.1016/j.elecom.2009.10.023
Doeff, M. M., Wilcox, J. D., Kostecki, R., and Lau, G. (2006). Optimization of carbon coatings on LiFePO4. J. Power Sources. 163, 180–184. doi: 10.1016/j.jpowsour.2005.11.075
Du, K., Ang, E. H., Wu, X., and Liu, Y. (2022). Progresses in sustainable recycling technology of spent lithium-ion batteries. Energ. Environ. Mat. 5, 1012–1036. doi: 10.1002/eem2.12271
Duan, L., Cui, Y., Li, Q., Wang, J., Man, C., Wang, X., et al. (2021). Recycling and direct-regeneration of cathode materials from spent ternary lithium-ion batteries by hydrometallurgy: status quo and recent developments : economic recovery methods for lithium nickel cobalt manganese oxide cathode materials. Johnson Matthey Technol. Rev. 65, 431–452. doi: 10.1595/205651320X15899814766688
Dunn, J., Kendall, A., and Slattery, M. (2022). Electric vehicle lithium-ion battery recycled content standards for the US – targets, costs, and environmental impacts. Res. Conserv. Recycl. 185, 106488. doi: 10.1016/j.resconrec.2022.106488
Dunn, J. B., Gaines, L., Barnes, M., Sullivan, J. L., Wang, M. (2022). Material and Energy Flows in the Materials Production, Assembly, and End-of-Life Stages of the Automotive Lithium-Ion Battery Life Cycle. Argonne National Lab. (ANL), Argonne, IL (United States). Available online at: https://www.osti.gov/biblio/1177517/ (accessed November 14, 2022).
Ebin, B., Petranikova, M., and Ekberg, C. (2018). Physical separation, mechanical enrichment and recycling-oriented characterization of spent NiMH batteries. J. Mater Cycles Waste Manag. 20, 2018–2027. doi: 10.1007/s10163-018-0751-4
Eco Batt (2021). Admin Battery Sorting. Available online at: https://www.ecobatt.net/battery-sorting/ (accessed November 7, 2022).
Electrek (2022). Here's What the Future of Battery Recycling is Going to Look Like for EV Owners. Available online at: https://electrek.co/2022/03/21/heres-what-the-future-of-battery-recycling-is-going-to-look-like-for-ev-owners/ (accessed December 16, 2022).
European Parliament and of the Council (2006). Directive 2006/66/EC of the European Parliament of the Council of 6 September 2006 on Batteries and Accumulators and Waste Batteries and Accumulators and Repealing Directive 91/157/EEC (Text with EEA relevance). Available online at: http://data.europa.eu/eli/dir/2006/66/oj/eng (accessed September 6, 2006).
Fan, E., Li, L., Lin, J., Wu, J., Yang, J., Wu, F., et al. (2019). Low-temperature molten-salt-assisted recovery of valuable metals from spent lithium-ion batteries. ACS Sust. Chem. Eng. 7, 16144–16150. doi: 10.1021/acssuschemeng.9b03054
Fan, E., Li, L., Wang, Z., Lin, J., Huang, Y., Yao, Y., et al. (2020). Sustainable recycling technology for li-ion batteries and beyond: challenges and future prospects. Chem. Rev. 120, 7020–7063. doi: 10.1021/acs.chemrev.9b00535
Fan, J., Zheng, P., Li, S., Wang, L. (2022). An integrated hand-object dense pose estimation approach with explicit occlusion awareness for human-robot collaborative disassembly. IEEE Trans. Autom. Sci. Eng. 2022, 1–10. doi: 10.1109/TASE.2022.3215584
Feng, X., Ouyang, M., Liu, X., Lu, L., Xia, Y., He, X., et al. (2018). Thermal runaway mechanism of lithium ion battery for electric vehicles: a review. Energy Storage Mat. 10, 246–267. doi: 10.1016/j.ensm.2017.05.013
Fink, K., Gasper, P., Major, J., Brow, R., Colclasure, A., Keyser, M., et al. (2022). Optimized Purification Methods for Metallic Contaminant Removal from Directly Recycled Li-Ion Battery Cathodes. Available online at: https://www.ssrn.com/abstract=4238572 (accessed November 14, 2022). doi: 10.2139/ssrn.4238572
Folayan, T. O., Lipson, A. L., Durham, J. L., Pinegar, H., Liu, D., Pan, L., et al. (2021). Direct recycling of blended cathode materials by froth flotation. Energ. Technol. 9, 2100468. doi: 10.1002/ente.202100468
Fricke, J. (1999). “Collection and recycling of spent portable batteries-the actual situation in Europe,” in 21st International Telecommunications Energy Conference INTELEC '99 (Cat No99CH37007), 254.
Fujita, T., Chen, H., and Wang, K. (2021). Reduction, reuse and recycle of spent Li-ion batteries for automobiles: a review. Int. J. Miner Metall. Mater. 28, 179–92. doi: 10.1007/s12613-020-2127-8
Full, J., Wanner, J., Kiemel, S., Miehe, R., Weeber, M., Sauer, A., et al. (2020). “Comparing Technical Criteria of Various Lithium-Ion Battery Cell Formats for Deriving Respective Market Potentials,” in 2020 IEEE Electric Power and Energy Conference (EPEC), 1–6.
Gaines, L. (2018). The future of automotive lithium-ion battery recycling: Charting a sustainable course. Sust. Mat. Technol. 2, 2–7. doi: 10.1016/j.susmat.2014.10.001
Gaines, L., Dai, Q., Vaughey, J. T., and Gillard, S. (2021). Direct recycling R&D at the recell center. Recycling. 6, 31. doi: 10.3390/recycling6020031
Gaines, L., Richa, K., and Spangenberger, J. (2018). Key issues for Li-ion battery recycling. MRS Energy Sust. 5, E14. doi: 10.1557/mre.2018.13
Gao, F., Tang, Z., and Xue, J. (2007). Preparation and characterization of nano-particle LiFePO4 and LiFePO4/C by spray-drying and post-annealing method. Electrochimica Acta. 53, 1939–1944. doi: 10.1016/j.electacta.2007.08.048
Gao, W., Zhang, X., Zheng, X., Lin, X., Cao, H., Zhang, Y., et al. (2017). Lithium carbonate recovery from cathode scrap of spent lithium-ion battery: a closed-loop process. Environ. Sci. Technol. 51, 1662–1669. doi: 10.1021/acs.est.6b03320
Granholm, J. M. (2021). National Blueprint for Lithium Batteries 2021–2030. Available online at: https://www.energy.gov/sites/default/files/2021-06/FCAB%20National%20Blueprint%20Lithium%20Batteries%200621_0.pdf (accessed October 17, 2022).
Gratz, E., Sa, Q., Apelian, D., and and Wang, Y. (2014). A closed loop process for recycling spent lithium ion batteries. J. Power Sources. 262, 255–262. doi: 10.1016/j.jpowsour.2014.03.126
Gutsch, M., and Leker, J. (2022). Global warming potential of lithium-ion battery energy storage systems: a review. J. Energ. Storage. 52, 105030. doi: 10.1016/j.est.2022.105030
Harper, G., Sommerville, R., Kendrick, E., Driscoll, L., Slater, P., Stolkin, R., et al. (2019). Recycling lithium-ion batteries from electric vehicles. Nature. 575, 75–86. doi: 10.1038/s41586-019-1682-5
HeroX (2022). Lithium-ion Battery Recycling Challenge. Available online at: https://www.herox.com/BatteryRecyclingPrize (accessed November 5, 2022).
Herrmann, C., Raatz, A., Andrew, S., and Schmitt, J. (2014). Scenario-based development of disassembly systems for automotive lithium ion battery systems. AMR. 907, 391–401. doi: 10.4028/www.scientific.net/AMR.907.391
How to Identify Different Types of Battery Chemistries (2022). Available online at: https://ezontheearth.com/2019/05/20/how-to-identify-different-types-of-battery-chemistries/ (accessed November 6, 2022).
Hu, X., Jiang, J., Cao, D., and Egardt, B. (2015). Battery health prognosis for electric vehicles using sample entropy and sparse Bayesian predictive modeling. IEEE Trans. Ind. Electr. 63, 2645–2656. doi: 10.1109/TIE.2015.2461523
Hua, W., Zhang, J., Zheng, Z., Liu, W., Peng, X., Guo, X. D., et al. (2014). Na-doped Ni-rich LiNi 0.5 Co 0.2 Mn 0.3 O 2 cathode material with both high rate capability and high tap density for lithium ion batteries. Dalton Tran. 43, 14824–14832. doi: 10.1039/C4DT01611D
Huang, B., Pan, Z., Su, X., and An, L. (2018). Recycling of lithium-ion batteries: recent advances and perspectives. J. Power Sources. 399, 274–286. doi: 10.1016/j.jpowsour.2018.07.116
Huo, H., Xing, Y., Pecht, M., Züger, B. J., Khare, N., Vezzini, A., et al. (2017). Safety requirements for transportation of lithium batteries. Energies. 10, 793. doi: 10.3390/en10060793
Huria, T., Ceraolo, M., Gazzarri, J., and Jackey, R. (2021). “High fidelity electrical model with thermal dependence for characterization and simulation of high power lithium battery cells,” in 2012 IEEE International Electric Vehicle Conference, IEEE, 1–8. doi: 10.1109/IEVC.2012.6183271
Islam, M., Yoon, M. S., and Ur, S. C. (2015). Synthesis of a LiFePO4/C cathode material by using a high-energy nano mill. J. Korean Phys. Soc. 67, 384–388. doi: 10.3938/jkps.67.384
Kay, I., Farhad, S., Mahajan, A., Esmaeeli, R., and Hashemi, S. R. (2022). Robotic disassembly of electric vehicles' battery modules for recycling. Energies. 15, 4856. doi: 10.3390/en15134856
Khateeb, S. A., Farid, M. M., Selman, J. R., and Al-Hallaj, S. (2004). Design and simulation of a lithium-ion battery with a phase change material thermal management system for an electric scooter. J. Power Sourc. 128, 292–307. doi: 10.1016/j.jpowsour.2003.09.070
Kim, N., Shamim, N., Crawford, A., Viswanathan, V. V., Sivakumar, B. M., Huang, Q., et al. (2022). Comparison of Li-ion battery chemistries under grid duty cycles. J. Power Sourc. 546, 231949. doi: 10.1016/j.jpowsour.2022.231949
Kim, S., Bang, J., Yoo, J., Shin, Y., Bae, J., Jeong, J., et al. (2021). A comprehensive review on the pretreatment process in lithium-ion battery recycling. J. Clean. Prod. 294, 126329. doi: 10.1016/j.jclepro.2021.126329
Konarova, M., and Taniguchi, I. (2010). Synthesis of carbon-coated LiFePO4 nanoparticles with high rate performance in lithium secondary batteries. J. Power Sources. 195, 3661–3667. doi: 10.1016/j.jpowsour.2009.11.147
Ku, H., Jung, Y., Jo, M., Park, S., Kim, S., Yang, D., et al. (2016). Recycling of spent lithium-ion battery cathode materials by ammoniacal leaching. J. Hazardous Mat. 313, 138–146. doi: 10.1016/j.jhazmat.2016.03.062
LaMotte, R., and Clare, J. (2022). California Passes Two New Laws to Overhaul State's Battery Extended Producer Responsibility Program and Broadly Expand State's E-Waste Program. Beveridge and Diamond PC. Available online at: https://www.bdlaw.com/publications/california-passes-two-new-laws-to-overhaul-states-battery-extended-producer-responsibility-program-and-broadly-expand-states-e-waste-program/ (accessed November 6, 2022).
Lander, L., Cleaver, T., Rajaeifar, M. A., Nguyen-Tien, V., Elliott, R. J. R., Heidrich, O., et al. (2021). Financial viability of electric vehicle lithium-ion battery recycling. iScience. 24, 102787. doi: 10.1016/j.isci.2021.102787
Larouche, F., Demopoulos, G. P., Amouzegar, K., Bouchard, P., and Zaghib, K. (2018). Recycling of Li-Ion and Li-Solid State Batteries: The Role of Hydrometallurgy. Cham: Springer International Publishing.
Larouche, F., Tedjar, F., Amouzegar, K., Houlachi, G., Bouchard, P., Demopoulos, G. P., et al. (2020). Progress and status of hydrometallurgical and direct recycling of li-ion batteries and beyond. Materials. 13, 801. doi: 10.3390/ma13030801
Le Varlet, T., Schmidt, O., Gambhir, A., Few, S., and Staffell, I. (2020). Comparative life cycle assessment of lithium-ion battery chemistries for residential storage. J. Energ. Storage. 28, 101230. doi: 10.1016/j.est.2020.101230
LegiScan (2023). California AB2440 | 2021-2022 | Regular Session. LegiScan. Available online at: https://legiscan.com/CA/text/AB2440/id/2606965 (accessed February 6, 2023).
Li, D., Wang, C., Qiu, D., Yin, F., Chen, Y., Yang, B., et al. (2014). Method for Directly Roasting and Processing Spent Lithium Ion Batteries and Recycling Valuable Metals. Available online at: https://patents.google.com/patent/CN101519726A/en (accessed November 11, 2022).
Li, H., Xing, S., Liu, Y., Li, F., Guo, H., Kuang, G., et al. (2017). Recovery of lithium, iron, and phosphorus from spent LiFePO4 batteries using stoichiometric sulfuric acid leaching system. ACS Sust. Chem. Eng. 5, 8017–8024. doi: 10.1021/acssuschemeng.7b01594
Li, J., Lu, Y., Yang, T., Ge, D., Wood, D. L., and Water-Based Electrode, L. Z., et al. (2020). Manufacturing and direct recycling of lithium-ion battery electrodes—a green and sustainable manufacturing system. iScience. 23, 101081. doi: 10.1016/j.isci.2020.101081
Li, J., Wang, G., and Xu, Z. (2016). Environmentally-friendly oxygen-free roasting/wet magnetic separation technology for In situ recycling cobalt, lithium carbonate and graphite from spent LiCoO2/graphite lithium batteries. J. Hazardous Mat. 302, 97–104. doi: 10.1016/j.jhazmat.2015.09.050
Li, L., Lu, J., Ren, Y., Zhang, X. X., Chen, R. J., Wu, F., et al. (2012). Ascorbic-acid-assisted recovery of cobalt and lithium from spent Li-ion batteries. J. Power Sources. 218, 21–27. doi: 10.1016/j.jpowsour.2012.06.068
Li, R., Zhang, H., Li, W., Zhao, X., and Zhou, Y. (2020). Toward group applications: a critical review of the classification strategies of lithium-ion batteries. World Elect. Vehicle J. 11, 58. doi: 10.3390/wevj11030058
Li, X. (2022). Collection mode choice of spent electric vehicle batteries: considering collection competition and third-party economies of scale. Sci. Rep. 12, 6691. doi: 10.1038/s41598-022-10433-3
Li, X., Zhang, J., Song, D., Song, J., and Zhang, L. (2017). Direct regeneration of recycled cathode material mixture from scrapped LiFePO4 batteries. J. Power Sources. 345, 78–84. doi: 10.1016/j.jpowsour.2017.01.118
Li, Y., Liu, K., Foley, A. M., Zülke, A., Berecibar, M., Nanini-Maury, E., et al. (2019). Data-driven health estimation and lifetime prediction of lithium-ion batteries: a review. Renew. Sust. Energ. Rev. 113, 109254. doi: 10.1016/j.rser.2019.109254
Lin, J., Fan, E., Zhang, X., Li, Z., Dai, Y., Chen, R., et al. (2022). Sustainable upcycling of spent lithium-ion batteries cathode materials: stabilization by In situ Li/Mn disorder. Adv. Energy Mat. 12, 2201174. doi: 10.1002/aenm.202201174
Lipu, M. S. H., Hannan, M. A., Hussain, A., Hoque, M. M., Ker, P. J., Saad, M. H. M., et al. (2018). A review of state of health and remaining useful life estimation methods for lithium-ion battery in electric vehicles: challenges and recommendations. J. Cleaner Prod. 205, 115–133. doi: 10.1016/j.jclepro.2018.09.065
Liu, C., Lin, J., Cao, H., Zhang, Y., and Sun, Z. (2019). Recycling of spent lithium-ion batteries in view of lithium recovery: a critical review. J. Clean. Prod. 228, 801–813. doi: 10.1016/j.jclepro.2019.04.304
Liu, K., Yang, S., Luo, L., Pan, Q., Zhang, P., Huang, Y., et al. (2020). From spent graphite to recycle graphite anode for high-performance lithium ion batteries and sodium ion batteries. Electrochimica Acta. 356, 136856. doi: 10.1016/j.electacta.2020.136856
Liu, W., Jia, Z., Luo, Y., Xie, W., and Deng, T. (2019). Experimental investigation on thermal management of cylindrical Li-ion battery pack based on vapor chamber combined with fin structure. Appl. Therm. Eng. 162, 114272. doi: 10.1016/j.applthermaleng.2019.114272
Lunde, A. E. (2022). Investigating How the LFP Battery Demand is Shaping the Future of Phosphorus and the Role of Secondary Resources [Master thesis]. Available online at: https://ntnuopen.ntnu.no/ntnu-xmlui/handle/11250/3023802 (accessed November 14, 2022).
Lv, W., Wang, Z., Cao, H., Sun, Y., Zhang, Y., Sun, Z. A., et al. (2018). Critical review and analysis on the recycling of spent lithium-ion batteries. ACS Sust. Chem. Eng. 6, 1504–1521. doi: 10.1021/acssuschemeng.7b03811
Lyu, C., Song, Y., Wang, L., Li, J., Zhang, B., Liu, E. A., et al. (2019). new method for lithium-ion battery uniformity sorting based on internal criteria. J. Energy Storage. 25, 100885. doi: 10.1016/j.est.2019.100885
Ma, X., Chen, M., Chen, B., Meng, Z., and Wang, Y. (2019). High-performance graphite recovered from spent lithium-ion batteries. ACS Sust. Chem. Eng. 7, 19732–19738. doi: 10.1021/acssuschemeng.9b05003
Ma, Y., Svärd, M., Xiao, X., Gardner, J. M., Olsson, R. T., Forsberg, K., et al. (2020). Precipitation and crystallization used in the production of metal salts for Li-ion battery materials: a review. Metals. 10, 1609. doi: 10.3390/met10121609
Makuza, B., Tian, Q., Guo, X., Chattopadhyay, K., and Yu, D. (2021). Pyrometallurgical options for recycling spent lithium-ion batteries: a comprehensive review. J. Power Sources. 491, 229622. doi: 10.1016/j.jpowsour.2021.229622
Markets, R. (2022). Global Lithium-ion Battery Markets Report 2022-2030: Increasing Government Funding In Grid Installations and Growing Consumption Of Rechargeable Batteries In Consumer Electronics Driving Growth. GlobeNewswire News Room. Available online at: https://www.globenewswire.com/en/news-release/2022/06/06/2456617/28124/en/Global-Lithium-ion-Battery-Markets-Report-2022-2030-Increasing-Government-Funding-In-Grid-Installations-Growing-Consumption-Of-Rechargeable-Batteries-In-Consumer-Electronics-Drivin.html (accessed November 6, 2022).
Marshall, J. E., Zhenova, A., Roberts, S., Petchey, T., Zhu, P., Dancer, C. E. J., et al. (2021). On the solubility and stability of polyvinylidene fluoride. Polymers. 13, 1354. doi: 10.3390/polym13091354
Martins, L. S., Guimarães, L. F., Botelho Junior, A. B., Tenório, J. A. S., and Espinosa, D. C. R. (2021). Electric car battery: an overview on global demand, recycling and future approaches towards sustainability. J. Environ. Manage. 295, 113091. doi: 10.1016/j.jenvman.2021.113091
Mayyas, A., Steward, D., and Mann, M. (2019). The case for recycling: Overview and challenges in the material supply chain for automotive li-ion batteries. Sust. Mat. Technol. 19, e00087. doi: 10.1016/j.susmat.2018.e00087
Mi, C. H., Zhao, X. B., Cao, G. S., and Tu, J. P. (2005). In situ synthesis and properties of carbon-coated LiFePO[sub 4] as Li-ion battery cathodes. J. Electrochem. Soc. 152, A483. doi: 10.1149/1.1852438
Mo Seong, W., Park, K. Y., Hwan Lee, M., Moon, S., Oh, K., Park, H., et al. (2018). Abnormal self-discharge in lithium-ion batteries. Energ. Environ. Sci. 11, 970–978. doi: 10.1039/C8EE00186C
Mulder, G., Omar, N., Pauwels, S., Meeus, M., Leemans, F., Verbrugge, B., et al. (2013). Comparison of commercial battery cells in relation to material properties. Electrochimica Acta. 87, 473–88. doi: 10.1016/j.electacta.2012.09.042
Murray, A. (2022). Cobalt Mining: The Dark Side of the Renewable Energy Transition. Earth.Org. Available online at: https://earth.org/cobalt-mining/ (accessed February 17, 2021).
National Recycling Rate Study (2022). Available online at: http://essentialenergyeveryday.com/wp-content/uploads/2019/11/BCI_433784-19_RecyclingRateStudy_19Update_FINAL.pdf (accessed November 6, 2022).
Nejad, S., Gladwin, D. T., and Stone, D. A. A. (2016). systematic review of lumped-parameter equivalent circuit models for real-time estimation of lithium-ion battery states. J. Power Sources. 316, 183–196. doi: 10.1016/j.jpowsour.2016.03.042
Nembhard, N. (2020). Safe, sustainable discharge of electric vehicle batteries as a pre-treatment step to crushing in the recycling process (Master's thesis), Barcelona: Universitat Politècnica de Catalunya.
Neumann, J., Petranikova, M., Meeus, M., Gamarra, J. D., Younesi, R., Winter, M., et al. (2022). Recycling of lithium-ion batteries—current state of the art, circular economy, and next generation recycling. Adv. Energ. Mat. 12, 2102917. doi: 10.1002/aenm.202102917
Nie, H., Xu, L., Song, D., Song, J., Shi, X., Wang, X., et al. (2015). LiCoO2: recycling from spent batteries and regeneration with solid state synthesis. Green Chem. 17, 1276–80. doi: 10.1039/C4GC01951B
O'Connor, P. (2021). An Analysis of Lithium-ion Battery Fires in Waste Management and Recycling. Available online at: https://www.epa.gov/system/files/documents/2021-08/lithium-ion-battery-report-update-7.01_508.pdf (accessed November 7, 2022).
Oh, S. W., Myung, S. T., Oh, S. M., Oh, K. H., Amine, K., Scrosati, B., et al. (2010). Double carbon coating of LiFePO4 as high rate electrode for rechargeable lithium batteries. Adv. Mat. 22, 4842–4845. doi: 10.1002/adma.200904027
OnTo-Technologies (2014). OnTo Technology. Available online at: https://www.onto-technology.com/cathode-healing (accessed November 14, 2022).
Pagliaro, M., and Meneguzzo, F. (2019). Lithium battery reusing and recycling: a circular economy insight. Heliyon. 5, e01866. doi: 10.1016/j.heliyon.2019.e01866
Parikh, V. P., Ahmadi, A., Parekh, M. H., Sadeghi, F., and Pol, V. G. (2022). Upcycling of Spent Lithium Cobalt Oxide Cathodes from Discarded Lithium-Ion Batteries as Solid Lubricant Additive. Environ. Sci. Technol. 53, 3757–63. doi: 10.1021/acs.est.8b07016
PCH (2022). Enhancing the Reliability and Safety of Lithium Ion Batteries. Available online at: https://www.pchintl.com/wp-content/uploads/2021/04/PCH-Li-ion-Batteries.pdf (accessed December 16, 2022).
Peters, J. F., Baumann, M., Zimmermann, B., Braun, J., Weil, M. (2017). The environmental impact of Li-Ion batteries and the role of key parameters – A review. Renew. Sust. Energ. Rev. 67, 491–506. doi: 10.1016/j.rser.2016.08.039
Pillot, C. (2020). The Rechargeable Battery Market and Main Trends 2011–2018. Available online at: https://rechargebatteries.org/wp-content/uploads/2019/02/Keynote_2_AVICENNE_Christophe-Pillot.pdf (accessed November 6, 2022).
Preradovic, S., and Karmakar, N. (2010). Chipless RFID: Bar Code of the Future. IEEE Microwave. 11, 87–97. doi: 10.1109/MMM.2010.938571
Punt, T., Bradshaw, S. M., van Wyk, P., Akdogan, G. (2022). The efficiency of black mass preparation by discharge and alkaline leaching for LIB recycling. Minerals. 12, 753. doi: 10.3390/min12060753
Rämä, M., Nurmi, S., Jokilaakso, A., Klemettinen, L., Taskinen, P., Salminen, J., et al. (2018). Thermal processing of jarosite leach residue for a safe disposable slag and valuable metals recovery. Metals. 8, 744. doi: 10.3390/met8100744
Ramadesigan, V., Northrop, P. W. C., De, S., Santhanagopalan, S., Braatz, R. D., Subramanian, V. R., et al. (2012). Modeling and simulation of lithium-ion batteries from a systems engineering perspective. J Electrochem Soc. 159, R31–45. doi: 10.1149/2.018203jes
Recycling Inside (2022). Separation and Sorting in Li-Ion Battery Recycling. Available online at: https://recyclinginside.com/recycling-technology/separation-and-sorting-technology/separation-and-sorting-in-li-ion-battery-recycling/ (accessed November 6, 2022).
Recycling Product News (2022). Refind Technologies Brings Optical Battery Sorting Technology to Ontario. Available online at: https://www.recyclingproductnews.com/article/27038/refind-technologies-brings-optical-battery-sorting-technology-to-ontario (accessed November 7, 2022).
Rigamonti, M. G., Chavalle, M., Li, H., Antitomaso, P., Hadidi, L., Stucchi, M., et al. (2020). LiFePO4 spray drying scale-up and carbon-cage for improved cyclability. J. Power Sources. 462, 228103. doi: 10.1016/j.jpowsour.2020.228103
Ross, B. J. (2020). LeResche M, Liu D, Durham JL, Dahl EU, Lipson AL. Mitigating the impact of thermal binder removal for direct li-ion battery recycling. ACS Sust. Chem. Eng. 8, 12511–12515. doi: 10.1021/acssuschemeng.0c03424
Ruismäki, R., Rinne, T., and Dańczak, A., Taskinen, P., Serna-Guerrero, R., Jokilaakso, A., et al. (2020). Integrating flotation and pyrometallurgy for recovering graphite and valuable metals from battery scrap. Metals. 10, 680. doi: 10.3390/met10050680
Sabisch, J. E. C., Anapolsky, A., Liu, G., and Minor, A. M. (2018). Evaluation of using pre-lithiated graphite from recycled Li-ion batteries for new LiB anodes. Res. Conserv. Recycl. 129, 129–134. doi: 10.1016/j.resconrec.2017.10.029
Salim, H. K., Stewart, R. A., Sahin, O., and Dudley, M. (2019). Drivers, barriers and enablers to end-of-life management of solar photovoltaic and battery energy storage systems: a systematic literature review. J. Cleaner Prod. 211, 537–54. doi: 10.1016/j.jclepro.2018.11.229
Salinas, F., Krüger, L., Neupert, S., and Kowal, J. A. (2019). second life for li-ion cells rescued from notebook batteries. J. Energ. Storag. 24, 100747. doi: 10.1016/j.est.2019.04.021
Sarmah, S. B., Kalita, P., Garg, A., and Niu, X. (2019). dong, Zhang XW, Peng X, et al. A review of state of health estimation of energy storage systems: challenges and possible solutions for futuristic applications of li-ion battery packs in electric vehicles. J. Electrochem. Energ. Conv. Storage. 10, 16. doi: 10.1115/1.4042987
Schiavi, P. G., Zanoni, R., Branchi, M., Marcucci, C., Zamparelli, C., Altimari, P., et al. (2021). Upcycling real waste mixed lithium-ion batteries by simultaneous production of rgo and lithium-manganese-rich cathode material. ACS Sust. Chem. Eng. 9, 13303–13311. doi: 10.1021/acssuschemeng.1c04690
Schneider, S. F., Bauer, C., Novák, P., and Berg, E. J. (2019). A modeling framework to assess specific energy, costs and environmental impacts of Li-ion and Na-ion batteries. Sust. Energ. Fuels. 3, 3061–3070. doi: 10.1039/C9SE00427K
Shi, Y., Chen, G., and Chen, Z. (2018). Effective regeneration of LiCoO2 from spent lithium-ion batteries: a direct approach towards high-performance active particles. Green Chem. 20, 851–862. doi: 10.1039/C7GC02831H
Shin, H., Zhan, R., Dhindsa, K. S., Pan, L., and Han, T. (2020). Electrochemical performance of recycled cathode active materials using froth flotation-based separation process. J Electrochem. Soc. 167, 020504. doi: 10.1149/1945-7111/ab6280
Sidiq, A. L., Floweri, O., Karunawan, J., Abdillah, O. B., Santosa, S. P., Iskandar, F. N. C. M., et al. (2022). Cathode active materials reproduced from end-of-life Li-ion batteries using a simple and green hydrometallurgical recycling process. Mat. Res. Bulletin. 153, 111901. doi: 10.1016/j.materresbull.2022.111901
Simmons, D. R. (2021). Assistant Secretary for Energy Efficiency and Renewable Energy US Department of Energy. Available online at: https://www.energy.gov/sites/prod/files/2019/07/f64/112306-battery-recycling-brochure-June-2019%202-web150.pdf (accessed December 16, 2022).
Singapore Battery and Consortium (2022). Process for Rejuvenation of Spent Lithium-ion Battery Cathodes. Available online at: https://www.batteryconsortium.sg/tech-bundles/process-for-rejuvenation-of-spent-lithium-ion-battery-cathodes.html-01-03-2021 (accessed November 11, 2022).
Sloop, S. E., and Sloop, S. E. (2023). Recycled Battery Materials. Available online at: https://patentimages.storage.googleapis.com/af/5a/2b/ff5fc2abb28ab7/US9287552.pdf (accessed November 14, 2022).
Snapshot (2022). Available online at: https://www.bebat.be/en/blog/how-sorting-batteries (accessed November 6, 2022).
Sommerville, R., Shaw-Stewart, J., Goodship, V., Rowson, N., and Kendrick, E. (2020). A review of physical processes used in the safe recycling of lithium ion batteries. Sust. Ma. Technol. 25, e00197. doi: 10.1016/j.susmat.2020.e00197
Sorting Batteries (2022). Available online at: http://www.g-pbatt.co.uk/sort.html (accessed November 7, 2022).
Stan, A. I., Swierczyński, M., Stroe, D. I., Teodorescu, R., and Andreasen, S. J. (2014). “Lithium ion battery chemistries from renewable energy storage to automotive and back-up power applications — An overview,” in: 2014 International Conference on Optimization of Electrical and Electronic Equipment (OPTIM). Columbia, MD: OPTIM, 713–20. doi: 10.1109/OPTIM.2014.6850936
Submission (2022). Available online at: https://www.herox.com/BatteryRecyclingPrize/round/460/entry/23267 (accessed November 7, 2022).
Team, L. (2019). Lithium Ion Battery Labeling: How to Ship Lithium Ion Batteries Without Getting Into Trouble With The IATA, 2019 Version. LabelValue.com. Available online at: https://www.labelvalue.com/blog/warning-look-at-2019s-lithium-ion-battery-transport-regulations-or-else/ (accessed November 7, 2022).
The Equation (2022). Quick Guide to Battery Reuse and Recycling. Available online at: https://blog.ucsusa.org/hanjiro-ambrose/a-quick-guide-to-battery-reuse-and-recycling/ (accessed November 6, 2022).
Titanaes (2022). Battery Diagnostics. Available online at: https://www.titanaes.com/battery-diagnostics (accessed November 14, 2022).
Tsang, F., Hailey, P., and Energy, F. (2017). Applicant: Farasis Energy. Available online at: https://patentimages.storage.googleapis.com/66/7c/49/f68ca34d2ffe64/US10103413.pdf (accessed November 14, 2022).
Vaško, T. (2015). Postupci razvrstavanja otpada kod postupka recikliranja proizvoda. Tehnički Glasnik. 9, 345–351.
Verdugo, L., Zhang, L., Saito, K., Bruckard, W., Menacho, J., Hoadley, A., et al. (2022). Flotation behavior of the most common electrode materials in lithium ion batteries. Sep. Purif. Technol. 301, 121885. doi: 10.1016/j.seppur.2022.121885
Waag, W., Fleischer, C., and Sauer, D. U. (2014). Critical review of the methods for monitoring of lithium-ion batteries in electric and hybrid vehicles. J. Power Sources. 258, 321–339. doi: 10.1016/j.jpowsour.2014.02.064
Waldmann, T., Iturrondobeitia, A., Kasper, M., Ghanbari, N., Aguesse, F., Bekaert, E., et al. (2016). Review—post-mortem analysis of aged lithium-ion batteries: disassembly methodology and physico-chemical analysis techniques. J Electrochem Soc. 163, A2149. doi: 10.1149/2.1211609jes
Wang, D., Wen, H., Chen, H., Yang, Y., and Liang, H. (2016). Chemical evolution of LiCoO2 and NaHSO4·H2O mixtures with different mixing ratios during roasting process. Chem. Res. Chin. Univ. 32, 674–677. doi: 10.1007/s40242-016-5490-2
Wang, H., Ren, H., Yan, T., Li, Y., and Zhao, W. A. (2021). latent highly activity energetic fuel: thermal stability and interfacial reaction kinetics of selected fluoropolymer encapsulated sub-micron sized Al particles. Sci. Rep. 11, 738. doi: 10.1038/s41598-020-80865-2
Wang, H., Vest, M., and Friedrich, B. (2011). “Hydrometallurgical processing of Li-Ion battery scrap from electric vehicles,” in 6th European Metallurgical Conference (EMC) Aachen, Germany.
Wang, J., Ma, J., Jia, K., Liang, Z., Ji, G., Zhao, Y., et al. (2022). Efficient extraction of lithium from anode for direct regeneration of cathode materials of spent li-ion batteries. ACS Energ. Lett. 7, 2816–2824. doi: 10.1021/acsenergylett.2c01539
Wang, M., Spangenberger, J., Ahmed, S., Dai, Q., Gaines, L., and Kelly, J. (2018). Battery Recycling Modeling Project Battery ID# bat 342. Argonne National Laboratory. Available online at: https://www.energy.gov/sites/default/files/2018/06/f52/bat342_spangenberger_2018_o_v2.pdf (accessed December 15, 2021).
Wang, M., Tian, Y., Liu, W., Zhang, R., Chen, L., Luo, Y., et al. (2020). A moving urban mine: the spent batteries of electric passenger vehicles. J. Cleaner Prod. 265, 121769. doi: 10.1016/j.jclepro.2020.121769
Wang, T., Luo, H., Bai, Y., Li, J., Belharouak, I., and Dai, S. (2020). Direct recycling of spent NCM cathodes through ionothermal lithiation. Adv. Energ. Mat. 10, 2001204 doi: 10.1002/aenm.202001204
Wang, X., Gaustad, G., and Babbitt, C. W. (2016). Targeting high value metals in lithium-ion battery recycling via shredding and size-based separation. Waste Manage. 51, 204–213. doi: 10.1016/j.wasman.2015.10.026
Wang, Y., and Huang, H. Y. S. (2011). Comparison of Lithium-Ion Battery Cathode Materials and the Internal Stress Development. Energy Systems Analysis, Thermodynamics and Sustainability; Combustion Science and Engineering; Nanoengineering for Energy, Parts A and B. Denver, CO: ASMEDC; Available online at: https://asmedigitalcollection.asme.org/IMECE/proceedings/IMECE2011/54907/1685/356045 (accessed November 6, 2022).
Washington Post (2022). Review Gadget Graveyard: We Found the Hidden Death Dates on Popular Devices. Available online at: https://www.washingtonpost.com/technology/2022/08/02/electronics-death-date/ (accessed November 6, 2022).
Winslow, K. M., Laux, S. J., and Townsend, T. G. A. (2018). review on the growing concern and potential management strategies of waste lithium-ion batteries. Res. Conserv. Recycl. 129, 263–77. doi: 10.1016/j.resconrec.2017.11.001
Wolf, A., Flegler, A., Prieschl, J., Stuebinger, T., Witt, W., Seiser, F., et al. (2021). Centrifugation based separation of lithium iron phosphate (LFP) and carbon black for lithium-ion battery recycling. Chem. Eng. Proc. Process Int. 160, 108310. doi: 10.1016/j.cep.2021.108310
Wu, X., Ma, J., Wang, J., Zhang, X., Zhou, G., Liang, Z., et al. (2022). Progress, key issues, and future prospects for li-ion battery recycling. Global Challenges. 8, 2200067. doi: 10.1002/gch2.202200067
Xia, H., Wang, H., Xiao, W., Lu, L., and Lai, M. O. (2009). Properties of LiNi1/3Co1/3Mn1/3O2 cathode material synthesized by a modified Pechini method for high-power lithium-ion batteries. J. Alloys Comp. 480, 696–701. doi: 10.1016/j.jallcom.2009.02.023
Xia, Q., Wang, Z., Ren, Y., Sun, B., Yang, D., Feng, Q. A., et al. (2018). Reliability design method for a lithium-ion battery pack considering the thermal disequilibrium in electric vehicles. J. Power Sources. 386, 10–20. doi: 10.1016/j.jpowsour.2018.03.036
Xiao, J., Li, J., and Xu, Z. (2017). Recycling metals from lithium ion battery by mechanical separation and vacuum metallurgy. J. Hazard. Mat. 338, 124–131. doi: 10.1016/j.jhazmat.2017.05.024
Xiaoyu, L., Tiansi, W., Lei, P, Chunbo, Z., Bingliang, X. (2014). A Comparative Study of Sorting Methods for Lithium-ion Batteries. In: 2014 IEEE Conference and Expo Transportation Electrification Asia-Pacific (ITEC Asia-Pacific). Beijing: IEEE. doi: 10.1109/ITEC-AP.2014.6940724
Xiong, R., Li, L., and Tian, J. (2018). Towards a smarter battery management system: a critical review on battery state of health monitoring methods. J. Power Sources. 405, 18–29. doi: 10.1016/j.jpowsour.2018.10.019
Xu, B., Dong, P., Duan, J., Wang, D., Huang, X., Zhang, Y., et al. (2019). Regenerating the used LiFePO4 to high performance cathode via mechanochemical activation assisted V5+ doping. Ceramics Int. 45, 11792–11801. doi: 10.1016/j.ceramint.2019.03.057
Xu, P., Yang, Z., Yu, X., Holoubek, J., Gao, H., Li, M., et al. (2021). Design and optimization of the direct recycling of spent li-ion battery cathode materials. ACS Sust. Chem. Eng. 9, 4543–4553. doi: 10.1021/acssuschemeng.0c09017
Yang, L., and Xi, G. (2015). Recovery of Co, Mn, Ni, and Li from spent lithium ion batteries for the preparation of LiNixCoyMnzO2 cathode materials. Ceramics Int. 41, 11498–11503. doi: 10.1016/j.ceramint.2015.05.115
Yang, L., Yang, L., Xu, G., Feng, Q., Li, Y., Zhao, E., et al. (2019). Separation and recovery of carbon powder in anodes from spent lithium-ion batteries to synthesize graphene. Sci Rep. 9, 9823. doi: 10.1038/s41598-019-46393-4
Yang, T., Lu, Y., Li, L., Ge, D., Yang, H., Leng, W., et al. (2020). An Effective relithiation process for recycling lithium-ion battery cathode materials. Adv. Sust. Syst. 4, 1900088. doi: 10.1002/adsu.201900088
Yang, Y., Okonkwo, E. G., Huang, G., Xu, S., Sun, W., He, Y., et al. (2021). On the sustainability of lithium ion battery industry – A review and perspective. Energ. Storage Materials. 36, 186–212. doi: 10.1016/j.ensm.2020.12.019
Yu, M., Bai, B., Xiong, S., and Liao, X. (2021). Evaluating environmental impacts and economic performance of remanufacturing electric vehicle lithium-ion batteries. J. Cleaner Prod. 321, 128935. doi: 10.1016/j.jclepro.2021.128935
ZDNET (2022). Inside a Notebook Battery Pack. Available online at: https://www.zdnet.com/article/inside-a-notebook-battery-pack/ (accessed November 6, 2022).
Zhan, R., Payne, T., Leftwich, T., Perrine, K., and Pan, L. (2020). De-agglomeration of cathode composites for direct recycling of Li-ion batteries. Waste Manage. 105, 39–48. doi: 10.1016/j.wasman.2020.01.035
Zhan, R., Yang, Z., Bloom, I., and Pan, L. (2021). Significance of a solid electrolyte interphase on separation of anode and cathode materials from spent li-ion batteries by froth flotation. ACS Sust. Chem. Eng. 9, 531–540. doi: 10.1021/acssuschemeng.0c07965
Zhang, G., Du, Z., He, Y., Wang, H., Xie, W., Zhang, T. A., et al. (2019). Sustainable process for the recovery of anode and cathode materials derived from spent lithium-ion batteries. Sustainability. 11, 2363. doi: 10.3390/su11082363
Zhang, J., Hu, J., Liu, Y., Jing, Q., Yang, C., Chen, Y., et al. (2019). Sustainable and facile method for the selective recovery of lithium from cathode scrap of spent LiFePO4 batteries. ACS Sust. Chem. Eng. 7, 5626–5631. doi: 10.1021/acssuschemeng.9b00404
Zhang, J., Li, X., Song, D., Miao, Y., Song, J., Zhang, L., et al. (2018). Effective regeneration of anode material recycled from scrapped Li-ion batteries. J. Power Sources. 390, 38–44. doi: 10.1016/j.jpowsour.2018.04.039
Zhang, N., Deng, W., Xu, Z., and Wang, X. (2022). Upcycling of Spent LiCoO2 Cathodes via Nickel- and Manganese-Doping. Carbon Energy. Available online at: https://onlinelibrary.wiley.com/doi/abs/10.1002/cey2.231 (accessed November 14, 2022).
Zhang, S., Xie, J., Zhang, P., and Zhao, X. (2021). Low-cost and scalable preparation of nano-Si from photovoltaic waste silicon for high-performance Li-ion battery anode. Funct. Mater Lett. 14, 2151033. doi: 10.1142/S1793604721510334
Zhang, X., Xie, Y., Lin, X., Li, H., and Cao, H. (2013). An overview on the processes and technologies for recycling cathodic active materials from spent lithium-ion batteries. J. Mater Cycles Waste Manag. 15, 420–430. doi: 10.1007/s10163-013-0140-y
Zhang, Y., Song, N., He, J., Chen, R., and Li, X. (2018). Lithiation-aided conversion of end-of-life lithium-ion battery anodes to high-quality graphene and graphene oxide. Nano Letters. 19, 512–519. doi: 10.1021/acs.nanolett.8b04410
Zheng, M., Salim, H., and Liu, T. (2021). A intelligence-assisted predesign for the sustainable recycling of lithium-ion batteries and beyond. Energ. Environ. Sci. 14, 5801–5815. doi: 10.1039/D1EE01812D
Zheng, R., Wang, W., Dai, Y., Ma, Q., Liu, Y., Mu, D., et al. (2017). A closed-loop process for recycling LiNixCoyMn(1–x–y)O2 from mixed cathode materials of lithium-ion batteries. Green Energ. Environ. 2, 42–50. doi: 10.1016/j.gee.2016.11.010
Zhou, Z., Lai, Y., and Peng, Q. (2021). Assessment of merging recycling methods for spent lithium ion batteries. Energies. 14, 6263. doi: 10.3390/en14196263
Keywords: lithium-ion battery, cathode recycling, anode recycling, battery sorting and collection, circular economy
Citation: Zheng P, Young D, Yang T, Xiao Y and Li Z (2023) Powering battery sustainability: a review of the recent progress and evolving challenges in recycling lithium-ion batteries. Front. Sustain. Resour. Manag. 2:1127001. doi: 10.3389/fsrma.2023.1127001
Received: 19 December 2022; Accepted: 30 March 2023;
Published: 17 April 2023.
Edited by:
Gavin Harper, University of Birmingham, United KingdomReviewed by:
Quanyin Tan, Tsinghua University, ChinaCopyright © 2023 Zheng, Young, Yang, Xiao and Li. This is an open-access article distributed under the terms of the Creative Commons Attribution License (CC BY). The use, distribution or reproduction in other forums is permitted, provided the original author(s) and the copyright owner(s) are credited and that the original publication in this journal is cited, in accordance with accepted academic practice. No use, distribution or reproduction is permitted which does not comply with these terms.
*Correspondence: Zheng Li, emhlbmdsaUB2dC5lZHU=
†These authors have contributed equally to this work and share third authorship
Disclaimer: All claims expressed in this article are solely those of the authors and do not necessarily represent those of their affiliated organizations, or those of the publisher, the editors and the reviewers. Any product that may be evaluated in this article or claim that may be made by its manufacturer is not guaranteed or endorsed by the publisher.
Research integrity at Frontiers
Learn more about the work of our research integrity team to safeguard the quality of each article we publish.