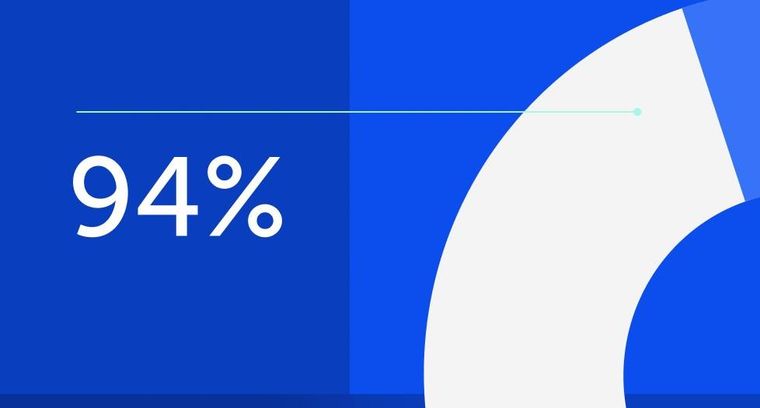
94% of researchers rate our articles as excellent or good
Learn more about the work of our research integrity team to safeguard the quality of each article we publish.
Find out more
ORIGINAL RESEARCH article
Front. Sustain., 26 February 2025
Sec. Modeling and Optimization for Decision Support
Volume 6 - 2025 | https://doi.org/10.3389/frsus.2025.1528514
This article is part of the Research TopicTransdisciplinary Engineering for Sustainability DecisionsView all articles
The current business environment is characterized by heightened competition, rising customer expectations, and increasing demands for cost efficiency and sustainability. Within this context, management's mandate for a seamless flow of products to customers, especially those with high priority, is underscored by imperatives to lower costs, adhere to policies and regulations, and sustain personnel wellbeing and motivation. This research advances the Vehicle Routing Problem (VRP) by integrating a transdisciplinary approach to customer prioritization that extends beyond revenue-based metrics. By incorporating customer preferences and sustainability considerations alongside traditional economic and logistical factors into the decision-making process, the model ensures a more efficient allocation of resources and improved customer service, ultimately enhancing long-term profitability. A real-world numerical illustration is provided, demonstrating that order acceptance is crucial and highlighting that not all customers should be served when considering the Triple Bottom Line (TBL) objectives. The study further explores how prioritization strategies, when managed across different business functions, can lead to better alignment with TBL, balancing economic, social, and environmental goals. The model's application offers significant practical implications for businesses operating under resource constraints, helping them optimize routes, reduce operational costs, and achieve sustainable growth while maintaining high customer satisfaction. Finally, the paper presents avenues for future research, including expanding the model's scope to incorporate reverse logistics and further refining customer prioritization strategies.
Heightened competition, escalating customer expectations, and increasing demands for cost efficiency and sustainability characterize the current business environment. In this context, the transportation of goods plays a critical role in meeting these challenges and driving economic growth and employment, making it a key factor in the overall success of modern distribution systems (Fink et al., 2019). This underscores the critical importance of optimizing them for effectively addressing the multiple stakeholders' needs (e.g., customers, logistics, sales, human resources), each with their particular objectives and performance indicators (Lopez-Arboleda et al., 2019; Pilati and Tronconi, 2024). Despite advancements in technology and methodology, transportation continues to pose significant challenges in ensuring the seamless flow of products to customers while navigating labor considerations, cost pressures, new regulatory frameworks, and more complex sustainability issues (Islam et al., 2021). Although engineering solutions provide valuable insights, they alone are not enough to tackle the complexities of modern transportation logistics. A transdisciplinary approach, which incorporates input from all stakeholders and integrates knowledge from diverse disciplines (Ertas, 2010) is essential for addressing the multifaceted and interconnected challenges faced in today's transportation systems.
Since its inception, the Vehicle Routing Problem (VRP) (Dantzig and Ramser, 1959) has been instrumental in transportation logistics. Over the years, increasingly complex real-world scenarios have given rise to various VRP variants. For instance, the capacitated VRP (CVRP) is a variation that includes an additional constraint: each vehicle has a fixed carrying capacity (Laporte et al., 2010) or the multi-compartment VRP (MCVRP), which is a variation where vehicles have multiple compartments to transport different product types without contamination (Lahyani et al., 2015). Another variant is the VRP with prioritized pairwise customer precedence (Nucamendi-Guillén et al., 2020), which has gained renewed significance in today's business landscape and is the focus of the present study. This variant enhances model realism and makes solution approaches more applicable in practice (Braekers et al., 2016), avoiding the widespread assumption that all customer orders must be accepted and served. However, this approach overlooks the operational realities faced by many organizations, including resource limitations, fluctuating service times, and differences in customer contributions to profitability. This has led to models that prioritize route efficiency without accounting for the strategic trade-offs between serving all customers versus selectively choosing high-value orders. Furthermore, these models typically overlook the potential for order acceptance to act as a lever to balance economic, environmental, and social goals within the Triple Bottom Line (TBL) framework (Elkington, 1997).
Relying exclusively on VRP solutions is insufficient to achieve the optimal outcomes of a transdisciplinary process, as it fails to actively involve all relevant stakeholders (Lattanzio et al., 2021). To achieve a truly comprehensive solution, it is crucial to move beyond traditional optimization techniques and allow for a collaborative approach that considers the intersection of various functional areas, including logistics, sales, customer service, and human resources (Jensen and Dahl, 2009). By doing so, organizations can effectively address the complexities of modern transportation logistics (Scholz and Steiner, 2015). Thus, the real value of the proposed model lies in enhancing the firm's decision-making capabilities by integrating technical and human elements into management objectives (Lenstra and Kan, 1981). By introducing a model that incorporates order acceptance alongside customer prioritization, our study addresses these limitations. It enables firms to make strategic decisions about which orders to accept based on resource availability and TBL impact, thus offering a more adaptable and realistic framework for solving VRPs in practical contexts.
The implementation of the proposed model in a real-work illustration integrates key elements from the economic, social, and environmental dimensions of the TBL. It first considers the prioritized customers, ensuring that the most valuable customers receive timely and efficient service. The model then optimizes delivery routes to reduce environmental impact by minimizing fuel consumption and emissions while also considering truck drivers' working shifts, ensuring their wellbeing is factored into the scheduling. By balancing these factors, the model promotes profitability and fosters long-term sustainability and collaboration among all stakeholders. Applying the framework creates the groundwork for a collaborative decision-making process that allows for the integration of diverse perspectives and enhances the quality of decisions made by leveraging each participant's unique insights and expertise.
The contribution of this article is significant in two key areas: First, it introduces a novel variation of the VRP with customer prioritization that allows for selective order fulfillment, prioritizing customers based on economic, social, and environmental objectives outlined in the TBL framework. Second, by adopting a transdisciplinary approach, this research incorporates diverse stakeholder perspectives to develop routing and scheduling solutions that are not only efficient and profitable but also socially responsible and sustainable. This dual focus on order acceptance and stakeholder collaboration sets a new benchmark for addressing real-world operational challenges in distribution systems, offering actionable insights for academia and industry.
The remainder of the paper is organized as follows: The following section presents a literature review on VRP, customer prioritization, and the integration of the TBL principles into the VRP. This review explores existing research on optimizing delivery routes while considering economic, social, and environmental factors and the role of customer prioritization and order acceptance in enhancing business performance and sustainability. Section 3 addresses the problem definition and underlying assumptions, elaborates on the mathematical model, and presents the proposed transdisciplinary framework. Section 4 demonstrates the application of the framework using a large-scale, real-world VRP problem. Lastly, Section 5 presents the discussion, summarizes the study's conclusions, presents some of the study limitations and offers avenues for future research.
Since developed by Dantzig and Ramser (1959), the VRP has been one of the most extensively researched subjects in operations research due to its complex nature and widespread practical implications (Konstantakopoulos et al., 2022). Despite advances in technology and methodology, transportation continues to pose significant business challenges. For example, heightened market pressure to accelerate the fulfillment process of consumer products results in substantial costs, causing environmental harm and sometimes leading to adverse working conditions (Barbee et al., 2021). In this complex ecosystem, management faces multifaceted challenges in ensuring the seamless flow of products to customers while navigating labor and cost considerations, regulatory frameworks, and sustainability issues (Islam et al., 2021; Mojtahedi et al., 2021).
Given the complexity of the VRP, efforts have been made toward the development of efficient heuristic algorithms capable of delivering satisfactory solutions in reasonable time frames, allowed by the exponential growth in the processing speed and memory capacity of modern computers (Konstantakopoulos et al., 2022). Current challenges are primarily related to the substantial volume of data to be managed and the increasing demands and expectations of customers (Nagata and Bräysy, 2009). This progress has spurred research advancements and led to the development of specialized commercial software. For example, companies in the food and beverage sector, such as Coca-Cola, Heineken, and numerous others, rely heavily on this software to design efficient routing solutions for their daily deliveries to thousands of sales points (Rincon-Garcia et al., 2018).
As time passes, the complexities inherent to contemporary business problems have impacted the classical VRP problem, leading to variations that account for vehicle capacities, time constraints, customer-set time windows, multiple depots engaged in distribution, and customer prioritization. For instance, the VRP is an NP-hard problem encompassing a combinatorial optimization challenge that aims to determine the optimal set of routes for vehicles to follow to deliver products to prioritized customers in the least amount of time (Tarhini et al., 2022).
Given limited resources to meet changing customer demands, firms must prioritize their customers and direct their efforts toward those deemed most important, though the definition of “importance” may vary. Typically, prioritization is conducted by the sales departments, considering customer profitability, lifetime value, purchase frequency, and strategic alignment with the firm's goals. Other factors may involve the customer's growth potential, their influence or reputation in the market, and the strength of the existing relationship. Prioritizing based on these criteria allows firms to allocate resources more effectively, enhancing service quality for key accounts while managing operational constraints. This targeted approach ultimately supports sustained profitability and meeting high-value customer expectations. Previous research has indicated that prioritizing customers leads to higher average customer profitability and increased return on sales by positively impacting relationships with top-tier customers while maintaining positive interactions with bottom-tier customers, ultimately reducing marketing and sales costs (Homburg et al., 2008). Additionally, studies have shown that a special focus on key customers positively affects customer satisfaction, leading to higher retention rates and sales growth within those customers (Hong-kit Yim et al., 2004). Another advantage of customer prioritization is the more efficient allocation of marketing resources, which results in a higher return on marketing investment than the traditional, non-prioritized allocation methods (Venkatesan and Kumar, 2004).
Other research has uncovered certain boundary conditions to customer prioritization, suggesting that while prioritizing valuable customers often brings benefits, it may also have unintended consequences. Findings indicate that prioritization can hinder account profitability growth as priority customers may develop heightened expectations, potentially becoming excessively demanding due to the elevated status they perceive they have achieved (Wetzel et al., 2014). Under this context, customer prioritization becomes crucial, but this process is not solely about focusing on the immediate value of customers, but rather a long-term strategy aimed at maximizing Customer Lifetime Value (CLV). CLV represents the total value a customer brings to a company over their entire relationship (Firmansyah et al., 2024).
When prioritizing customers, firms must consider the strategic decisions of order acceptance. This process involves evaluating whether to accept an order based on the firm's capacity, resource availability, and the order's alignment with broader business goals (Slotnick, 2011; Trigos and López, 2016). Not every order contributes equally to profitability or customer relationships; therefore, assessing the potential impact of accepting or declining an order is essential (Moodie, 1999). By establishing clear criteria for order acceptance, firms can better manage demand, prioritize high-value customers, and avoid misuse of limited resources. Strategies for order acceptance include negotiating or renegotiating time windows, service time and pricing, considering capacity rationing, revenue management, and due-date setting (Calosso et al., 2003). Most VRP studies assume that all customer orders are accepted, focusing solely on optimizing delivery routes to minimize costs and environmental impact. However, this assumption overlooks the strategic decision of order acceptance—a crucial element for businesses operating under resource constraints. Therefore, firms must focus on three key actions: prioritizing customers, deciding which orders to accept, and establishing their schedules.
Businesses today are encouraged to go beyond financial gains and consider their impact on society and the environment, as outlined by the TBL framework (Elkington, 1997). This approach highlights the importance of balancing economic, social and environmental objectives (Goel, 2010), emphasizing that a sustainable and well-rounded business model requires companies to seamlessly integrate these dimensions into their operations (Venkatraman and Nayak, 2015).
The economic dimension emphasizes a business's financial health and profitability while linking its growth to the broader economy, demonstrating how it contributes to and strengthens the surrounding system. Customers' engagement and loyalty directly drive the organization's capacity to create economic value, sustain growth, and contribute to long-term economic stability (Homburg et al., 2008; Wetzel et al., 2014). Customers are the foundation of any business and serve as its primary source of revenue. A strong and loyal customer base is crucial to building sustainable businesses and fulfilling the economic aspect of the TBL.
In transportation and distribution, customer satisfaction hinges on accepting orders and delivering them promptly and efficiently. A key benefit of priority status is the ability to offer specific delivery time windows, with narrower windows assigned to higher-priority customers (Ghannadpour et al., 2014). By tailoring delivery time windows based on customer priority, businesses can enhance long-term loyalty, drive repeat business, and maximize overall customer lifetime value (CLV), fostering sustainable growth and profitability (Rust and Verhoef, 2005; Venkatesan and Kumar, 2004). Therefore, it is crucial to strike a balance between accepting and delivering orders and meeting the broader objectives of the TBL. This is why effective planning and control are necessary to enhance a firm's order acceptance strategy (Slotnick, 2011; Tarhini et al., 2022; van Benthem et al., 2020).
The social dimension focuses on a company's responsibility toward the wellbeing of internal and external stakeholders impacted by its operations. This includes employees, suppliers, customers, and the broader community (Freeman, 2010; Freeman et al., 2020). By addressing the needs and expectations of these stakeholders, businesses contribute to positive social outcomes, which are critical for long-term sustainable growth (Dytianquin et al., 2024). Under this context, the social dimension can be addressed by cultivating a collaborative environment that extends beyond mathematical efficiency (Date and Chandrasekharan, 2018).
While the efficiencies generated by the VRPC cater to various functional areas such as sales, customer service, logistics, and environmental compliance, the concerns of fleet drivers have frequently been neglected. Truck drivers represent a highly vulnerable and underserved workforce, often lacking the personal and environmental resources essential for their health and wellbeing (Apostolopoulos et al., 2011). Although there has been a growing focus on improving the health and wellbeing of these workers, driven by new regulations aimed at enhancing working conditions and safety in transportation, significant challenges remain. For example, the European Union has established a comprehensive set of regulations in relation to the work conditions of truck drivers, including maximum daily shift durations, mandatory breaks, overtime limits, minimum rest periods between shifts, and requirements for weekly rest days (Mendes and Iori, 2020). However, this is not the case in all geographies where there is still much to be done. Often, these workers are uncertain about the duration of their routes to complete all scheduled deliveries. Drivers sometimes involuntarily accept excessively long work shifts, which, while offering additional income, are neither healthy, safe, nor sustainable when they occur regularly (Ng et al., 2015). Ultimately, the effectiveness of the distribution process hinges directly on the commitment and performance of these individuals, who benefit from predictable working schedules (Ng et al., 2015; Macassa et al., 2021). Addressing their wellbeing is ethically imperative and crucial for achieving sustainable and effective transportation systems.
The environmental dimension encompasses the organization's efforts to mitigate its ecological footprint by reducing its environmental impact. Organizations can achieve this by adopting practices such as utilizing renewable energy sources, implementing waste reduction and recycling programs, and optimizing operational processes to enhance resource efficiency. By prioritizing these efforts, companies contribute to environmental preservation to improve their reputation among consumers and stakeholders who increasingly value sustainability (Goel, 2010).
Research indicates that the environmental dimension of the TBL is paramount. This emphasis on environmental sustainability likely explains why scholars have devoted more attention to this dimension than to social and economic aspects (James et al., 2015). Prioritizing the environmental dimension is essential not only for the health of our planet but also for the long-term viability of economic and social systems, highlighting the interconnectedness of these three pillars of sustainability. In response to environmental challenges and the compliance requirements that firms face, a variant of VRP known as the Green VRP has emerged (Lin et al., 2014). This adaptation focuses on minimizing the environmental impact of transportation logistics by optimizing routes to reduce fuel consumption and emissions. By incorporating sustainability into routing strategies, companies can enhance operational efficiency while contributing to broader environmental goals. Typically, the objective is to minimize either the total distance traveled or the total travel time. Achieving this leads to reduced fuel consumption and decreases carbon emissions from the fleet (Braekers et al., 2016).
Viewing the VRP through a TBL lens aligns resource allocation with economic, social, and environmental objectives, providing a balanced approach that meets high-priority customer needs while supporting sustainable business practices. One of the most significant limitations we observed was the widespread assumption that all customer orders must be accepted and served. This approach disregards the operational realities facing many organizations, such as limited resources, fluctuating service times, and varying customer contributions to profitability. Existing VRP models typically overlook the integration of order acceptance and customer prioritization, which are essential in balancing business profitability with environmental and social responsibilities. By addressing this gap, our study introduces a novel approach that incorporates these factors, thereby contributing to the theoretical advancement of VRP models and offering a more holistic view of routing strategies.
The methodology section begins with the presentation of the mathematical model, which forms the foundation of this study by addressing key variables such as customer marginal contribution, customer prioritization, order acceptance, and delivery schedule. Then, the transdisciplinary framework is introduced, highlighting how the model integrates economic, social, and environmental considerations to provide a comprehensive and sustainable approach to vehicle routing and distribution operations from a transdisciplinary approach. It is important to note that the terms vehicle and route will be used interchangeably.
The problem parameters and decision variables are defined and summarized in Table 1 to establish clarity and consistency in the mathematical model.
Bard et al. (2002) proposed an efficient two-index model to minimize the number of routes required to serve a full set of customers. This work is utilized as the foundation for the model presented herein, with significant extensions. Notable differences include the incorporation of business value in the objective function and customer prioritization, which is addressed through the introduction of a priority customer (customers that must be served) set (Ip) and a non-priority customer (customers that could be either neglected or served on a future work shift) set (In). The proposed Customer Prioritization Vehicle Routing Problem with Time Windows (CP VRP TW) is defined as follows:
where w ∈ ℝn+1, and x ∈ 𝔹(n+1) × (n+1).
The function in Equation 1 represents the model objective function to maximize. It is called marginal work shift income (MWI). Specifically, this is achieved by considering the marginal contribution of each customer (e.g., the revenue of the order minus direct variable costs) and the work shift costs (including capital and operational expenditures named CAPEX and COPEX) of the vehicles used in the solution. The objective function aims to maximize the company's value by building vehicle routes to serve all priority customers plus the most value-creating non-priority customers. Thus, route efficiency, measured by the system time utilization (STU, the percentage of the work shift time that vehicles are either servicing customers or in motion), plays a crucial role in this endeavor. Efficient routes translate into more sustainable (economic, environmental, and societal) operations.
The constraint in Equation 2 implies that no more than K routes (vehicles) depart the depot (O) at the beginning of the work shift. Thus, the number of routes departing from the depot must be less or equal to the number of vehicles available.
The constraint in Equation 3 ensures that every priority customer is visited precisely once. This is, the number of vehicles departing priority customers must be equal to exactly one.
The constraint in Equation 4 models the customer selection process of non-priority. This means that non-priority customers are visited at most once.
The constraint in Equation 5 represents the equation of balance per customer. This means that the number of vehicles that arrive at each customer location is the same as the number of vehicles that leave that location. Thus, if the customer is selected to be served, one vehicle arrives at the customer's location, and the same one departs from it. However, if the customer is not selected to be served, then zero vehicles arrive at the customer location, and zero vehicles leave that exact location.
The constraint in Equation 6 does the timekeeping per pair of nodes, where wi represents the time each selected customer starts its service. In addition, wO represents the start of the work shift for the depot. In this form, if customer j is served immediately after i, the time at which customer i is served (wi) plus its service time (sti) plus the travel time from customer i to customer j (ti, j) is when the vehicle arrives at the customer j. Since this time might be early for the customer j time window (tmini), the time to start the customer j service (wj) can not be earlier than the vehicle arrival time. If customer j is not immediately served after i, then xi, j = 0, and the constraint becomes inactive by the large value of the parameter M.
Notice that the constraint (Equation 2) makes sure that at most K vehicles leave the depot O, and constraints (Equation 3) though Equation 4 makes sure that at most all (n) customer nodes are visited. Thus, at most n + K constraints in Equation 6 are active. This constraint ensures that the arrival time for each customer on the route does not decrease as one passes through the customers on the same route, and then a path is warranted. Hence, no closed loops could be found in the routes, making unnecessary sub-tour elimination routines.
The constraint (Equation 7) models the start of each customer service (wi) to be within its time windows.
It is important to note that during the model solution process if a new route is added to the solution, a new arc (O, i), where i ∈ {1, ..., n} is added to start its route. Hence, the optimal solution of the CP VRP TW in Equation 1 through Equation 7 involves the minimum number of routes to maximize the direct marginal contribution as shown in MWI (Equation 1), as long as tc > 0.
Table 2 shows the transdisciplinary framework proposed in this research. The objective is to find a balanced solution for all stakeholders to the CP VRP TW. The framework consists of three key sections. The first focuses on identifying the stakeholders involved in the process. The second establishes the structural data foundation necessary for decision-making. Finally, in the third, the transdisciplinary team works the mathematical model on several scenarios to determine the solution that balances the interests and objectives of all stakeholders and better suits the environment.
This section aims to illustrate the application of the transdisciplinary framework described in Section 3.2 using the actual case of a last-mile delivery company. This section is composed of three subsections; in the first one, the general description of the company is stated; in the second one, the implementation of the transdisciplinary framework is presented; and in the last one, some of the challenges faced are pointed out.
The company operates in a major Latin American city, utilizing a fleet of 30 vehicles (K = 30) to manage its operations. Its customer catalog encompasses approximately 3,000 clients, with each work shift requiring service for a distinct subset of customers. In each work shift, the company categorizes its customers into two groups based on a custom-defined policy: priority customers, who must be served within the designated work shift, and non-priority customers, whose orders can be deferred to a subsequent shift if required. Each selected customer must be served within its specific time window.
Currently, the company often fails to meet the customer time windows. Consequently, vehicle crews frequently work longer than regular shifts, incurring significant overtime costs. This situation highlights operational inefficiencies that affect both customer satisfaction and employee wellbeing. Historically, the company has built its delivery routes empirically but now seeks to adopt modern optimization techniques using a transdisciplinary approach to enhance business sustainability. They realize that improving routing implies better economic conditions, customer and crew satisfaction (related to the social dimension) and fewer gas emissions (related to the environmental dimension). As a result, the executive committee approved conducting a preliminary analysis using data from Monday's first shift, which is among the busiest work shifts.
This section is based on a real Monday's first work shift. The particular customers and priorities of Monday's first work shift are known at the end of Sunday's first work shift; this means that the parameters are known fourteen hours in advance, leaving fourteen hours to build a vehicle routing schedule. This particular work shift includes 280 customers to be served, from which 136 are priority customers and 144 are non-priority.
The transdisciplinary framework detailed in Table 2 will be applied to address this challenge.
Phase I. Stakeholders
Step 1. The stakeholders identified are customers, vehicle crews and their families representing society, company stockholders representing economic interests, and last but not least, environmental interest due to the use of internal combustion engine vehicles owned by the company to run the service; thus, the more efficient the routes are, the less pollution is poured into the environment.
Step 2. The company assembled a transdisciplinary team led by the chief executive officer (CEO) and composed of representatives from the following departments: operations, logistics, finance, accounting, sales, human resources, and customer service. The objective of this committee is to enhance customer service by maximizing the fulfillment of customer orders in their desired time windows while simultaneously achieving the TBL objectives.
Phase II. Structural data building
Step 3. The company operates a fleet of (K = 30) vehicles, each with an hourly cost of $50/hr. This cost encompasses labor and vehicle-related costs, including capital expenditures (CAPEX) and operational expenditures (OPEX). Thus, tc = 50 × 8 hours/shift = $400/shift.
Step 4. The company has compiled a comprehensive database for the 280 customers and the company depot (addresses and GPS location).
Step 5. Based on this GPS information, the company has developed a 281 × 281 travel time matrix of average travel time (in minutes) between all locations (depot and customers) using a commercial software application.
Phase III. Work shift solution
Step 6. Since this is a preliminary analysis, the customers to be served in the work shift are the same as those identified in Step 4. The work shift data used in this section are openly available in a MsExcel file.1 This file contains a worksheet called “Travel time (min),” featuring matrix T. The second worksheet, “Customer info,” includes the customer's marginal contribution (r, referring to the customer's revenue minus the variable cost of the products delivered). This worksheet also includes the customer classification, where 1 refers to a priority customer and 0 to a non-priority customer, service times (st) of each customer, and their delivery time window (tmin and tmax).
Step 7. The numerical experiments were run on GAMS 48.6 using IBM ILOG CPLEX 48.6.0 f19e462d Jan 9, 2025 DAC arm 64bit/macOS. The option of 8 threads was set on a MacBook Air with 16 GB RAM, an Apple M1 processor with one socket, eight cores, and eight threads available, running under macOS Sequoia 15.1.
The size (number of constraints and variables) of the CP VRP TW model (as reported by the solver) for each scenario is significant. Table 3 shows the size of the four scenarios proposed in the transdisciplinary framework. The first column shows the scenario name, and the number of constraints is included in the second column. The number of binary and continuous decision variables are shown in columns three and four, and the last column shows the sum of decision variables.
The number of binary variables sets the number of possible solutions for each scenario. For instance, a scenario where the number of binary variables is 18, 632 makes 218, 632 possible solutions in the search space. This number is beyond any possible complete search. This is why the VRP is considered one of the most challenging problems in mathematical programming. Since an exhaustive search is not possible, a mathematical-directed search was placed in order. In our case, the software aims for an optimal solution but is restricted by the computer time allowed, which we set at four hours for every scenario i. The sizes of scenarios b, c, and d are almost identical but significantly larger than scenario a.
Table 4 summarizes the numerical results for the four scenarios; its first column shows the name of each scenario. The second column represents the value of the marginal Work shift income (MWI), i.e. the value of the CP VRP TW in function (Equation 1). The third column specifies the number of routes required in the scenario (R). Column four includes the number of customers served in the solution (C). Columns five to eight show the sum of the selected customer's service time (SU), travel time (TT), total work time (TWT), and system time utilization percentage (STU) of each scenario. As previously mentioned, four computational hours were allocated to solve each problem, amounting to 16 hours. This timeframe aligns with the company's operational schedule, as the problem data is available 16 hours in advance.
The numerical results presented in Table 4 demonstrate that the company can achieve a maximum MWI of $12,580.84 while successfully meeting the time windows of 277 customers without the need to deploy additional vehicles. This outcome is evident as the solutions for scenarios b and c are identical, despite the exclusion of three non-priority customers (refer to Table 5). If the company is willing to serve all 280 customers, this decision will cost $138.49 (the difference MWI of scenario c minus d 12,580.84-12,442.35); this value includes the cost of getting an additional vehicle.
Table 5 shows the information related to the three non-priority customers that were not included in the solution of scenario c. The first column of the table shows the customer, and the marginal contribution and percentiles (computed from the 280 customer set) are shown in columns two and three. Columns four and five show the service time and percentiles (computed from the customer set of 280) involved. The last two columns include the customer's lower and upper time window limits. From this, we observe that these customers requested deliveries during the latter half of the 480-min (8-h) work shift and fall within the high percentiles for service time (the time required to serve each customer). Additionally, these customers do not rank in the high percentiles for marginal contribution. This raises a key consideration for further analysis–specifically, the need to review the products included in these customers' orders and evaluate the associated service times.
It is evident that the CP VRP TW model considers customers' acceptance based on economic impact, service time, the requested service time window, and location (customer or depot distance to the rest of the locations). Hence, from an economic standpoint, serving all customers may not always be the optimal choice. However, making a final decision requires a comprehensive evaluation that considers a broader set of criteria beyond purely economic factors.
The set of solutions in Table 4 is presented to the transdisciplinary committee, whose main task now is to determine if it is worth (by non-economic reasons) to get an additional vehicle to implement the solution in scenario e (servicing all customers), knowing that servicing customer c711, c599 and c252 will incur in a net MWI reduction of $138.49, this is 1.1% of the MWI in scenario c.
The CP VRP TW modeled in Equation 1 through Equation 7, by maximizing the variable economic contribution of the system (MWI), not only selects the minimum number of routes by minimizing total work time, but discards customers that do not add economic value from a systemic view. It is important to highlight that the optimization of delivery routes leads to several positive outcomes. First, optimal route travel times minimize pollution poured into the environment by the internal combustion engines of the vehicles. Second, businesses benefit economically by maximizing variable income (MWI), as more efficient routes reduce operational costs and increase profitability. Lastly, the social dimension is addressed by incorporating factors such as the wellbeing of vehicle crews into the route planning process. This is achieved by ensuring that routes do not require excessive driving time or result in overtime, promoting healthier and more sustainable working conditions for the truck drivers and staff at the depot. By doing this, the CP VRP TW mathematical model in this illustration fosters a sustainable approach to business operations, balancing environmental, economic, and social considerations.
While the numerical illustration provided in the previous section represents a pilot effort that models a single work shift. The ultimate goal of the transdisciplinary committee is to implement this technology as a standardized operational procedure for all work shifts. However, achieving this objective presents several challenges that must be carefully addressed. While these challenges are substantial, they are not insurmountable. Therefore, the company's management committee should thoroughly assess whether investing in their resolution is a worthwhile and strategic decision. The evidence presented in the numerical illustration strongly suggests that the benefits of tackling these challenges could outweigh the associated costs and efforts:
1. Building the travel time matrix T. Given that the customer catalog includes 3,000 customers, the complete travel time matrix would have a size of 3,001 × 3,001 (including the depot). Constructing this matrix involves a substantial effort in terms of time and financial resources, particularly when using tools like Google Maps to compute real travel times for each pair of locations. An alternative approach is to estimate travel times using mathematical norms. For instance, Norm 1 distances (sum of horizontal and vertical distances) or Norm 2 distances (straight-line distances) can be calculated from the GPS coordinates of each location. These distances can then be adjusted using average vehicle speeds to approximate travel times. This approach offers a feasible alternative to the direct computation of all 3,001 × 3,001 travel times and warrants further exploration to assess its practicality and accuracy.
2. Keeping service time per customer (st) constantly updated. This time might be correlated to the number and type of products delivered.
3. Keeping the marginal contribution per customer, constantly updated for every product (sell price minus cost, including cost changes using LIFO of FIFO accounting systems).
4. Computing the vehicle cost per work shift (tc) using engineering economics, financial and accounting standards.
5. Strategising the company's policy for customer prioritization. Establishing a clear company-wide definition for categorizing customers as priority or non-priority is essential. This definition should account for various factors, such as contractual obligations, customer preferences, or past purchase behavior. Additionally, it is important to recognize that a customer's priority status may change over time due to evolving circumstances, such as changes in order frequency, value, or service requirements. By implementing a dynamic classification system, the company can ensure that its priority-setting process remains adaptable and aligned with its operational goals and customer needs.
6. Developing a systemic information system to routinely automate every work shift's routing operation to aid decision-making. Implementing and operating an automated routing system for periodical work shift decision-making requires significant investment in both cost and expertise. The system must integrate various data sources, such as customer locations, product requirements and time windows, company financial and accounting information, and vehicle availability, and process this information in real-time. This requires specialized software development, robust hardware infrastructure, and continuous maintenance. Furthermore, the company must invest in training personnel to effectively use the system and ensure it aligns with business operations. The expertise required spans areas such as data analytics, optimization algorithms, and transportation logistics, making it a complex yet valuable long-term investment for improving operational efficiency.
This study contributes to the literature by advancing the VRP framework with a novel variation of the VRP with prioritized customers. Unlike traditional models that treat customer orders as uniform or prioritize them solely based on revenue, the proposed model assumes that not all orders must be served, allowing businesses to make strategic decisions about order acceptance. In addition, the model integrates customer-specific requirements and prioritization criteria beyond revenue, incorporating the principles of the TBL framework to balance economic, social, and environmental objectives. This holistic approach ensures that customer preferences and needs are addressed while promoting sustainability and operational efficiency (Braekers et al., 2016; Mojtahedi et al., 2021). This study also emphasizes the wellbeing of both customers and truck drivers, ensuring that the social dimension receives its fair share of attention. Unlike existing literature, which often overlooks the social aspects of distribution systems, the proposed model prioritizes customer satisfaction and employee welfare as integral components of the optimization process (Macassa et al., 2021).
Customer prioritization allows businesses to allocate resources efficiently and create tailored strategies that enhance long-term profitability. However, as demonstrated in this research, prioritization strategies that rely solely on customer revenue or economic metrics and are managed exclusively by the sales team may not be sufficient. A more holistic approach, which includes considering order acceptance under operational constraints and the sustainability of logistics processes, is essential. Effective prioritization requires a transdisciplinary approach, where a committee comprising experts from sales, finance, accounting, logistics, operations, and customer service collaboratively determines which customers receive priority service. Considering additional factors, such as customer location, service time, and logistical efficiency, ensures that prioritization decisions are economically viable and operationally practical, aligning with broader company objectives. As shown in the numerical illustration, the solutions obtained do not represent final solutions but are meant to serve as a starting conversation in stakeholder negotiations. By applying a transdisciplinary lens guided by the TBL framework, this research enhances routing practices and encourages open communication between stakeholders, paving the way for efficient, cost-effective, socially responsible, and sustainable solutions.
The proposed model is particularly well-suited for implementation in industries such as logistics and last-mile delivery services, where order acceptance, customer prioritization, and sustainability goals play a critical role. One promising application of the model is in the beverage or consumer goods industry, specifically in delivery to points of sale such as small retailers, mom-and-pop stores, or restaurants. These businesses often operate with diverse order volumes, varying service-time requirements, and specific delivery constraints, making them ideal candidates for testing the model. However, in practice, a successful application may encounter several significant operational hurdles. Firstly, there is the risk of disruption to regular operations (Bhalaji et al., 2022). Implementing the model requires careful coordination to minimize service interruptions and ensure a seamless transition. Secondly, the accuracy and consistency of service times pose a critical challenge. Real-world service times often deviate from those recorded in the system due to unforeseen circumstances such as traffic delays, weather conditions, or variations in customer readiness. These discrepancies can compromise the model's ability to deliver optimized solutions unless systems are continuously updated with accurate, real-time data or a predictive model can be generated with historical data for further accuracy. Third, price variations across regions or market conditions can affect the financial parameters of the model, requiring frequent re-calibration to reflect the dynamic nature of costs and revenues. To address these challenges, advanced technology is needed to enable real-time data integration and discipline in updating model variables, such as service times, customer priorities, and operational costs, which are critical to maintaining the relevance and effectiveness of the model.
Although this analysis provides valuable insights and demonstrates the potential for generalization to various companies, certain limitations should be noted. First, the findings are based on a per-shift analysis, which may not fully capture complexities arising in continuous, multi-shift operations that span entire days and weeks. Consequently, the model may require adjustments to optimize runtime and maintain efficiency across multiple shifts within 24 hours or over several days. Furthermore, variations in demand, resource allocation, and operational constraints unique to different companies or industries may require further customization. Future research should explore adaptations to ensure the robustness and efficiency of the model in diverse multi-shift and multi-day scheduling scenarios. Building on the current model, another promising area for future research involves encompassing capacitated VRPs to enhance the model's applicability by incorporating capacity constraints, which are critical for many real-world logistics scenarios. Exploring classic optimization problems like location allocation and transhipment, among others, may further advance decision-making processes.
Another valuable direction for future research involves the development of improved methods for classifying customers from a transdisciplinary perspective. By incorporating insights from fields like operations management, marketing, and sustainability studies, future models could provide customers' priority status more accurately, allowing businesses to allocate resources and deliver services that align with customer needs and the TBL objectives.
Lastly, a promising avenue for future research lies in the integration of customer prioritization within reverse logistics. Reverse logistics, which involves the process of returning goods from customers to the manufacturer or retailer, has gained significant importance, particularly in the aftermath of the COVID-19 pandemic (Sar and Ghadimi, 2023). Research that incorporates customer prioritization into this process could offer valuable insights, as not all returns have the same level of urgency or profitability. By analysing customer needs and the value of returns, companies could better allocate resources, prioritize high-value returns, and minimize operational inefficiencies.
The original contributions presented in the study are included in the article/supplementary material, further inquiries can be directed to the corresponding author.
FT: Conceptualization, Data curation, Formal analysis, Investigation, Methodology, Project administration, Resources, Software, Supervision, Validation, Visualization, Writing – original draft, Writing – review & editing. MO: Conceptualization, Investigation, Methodology, Writing – original draft, Writing – review & editing.
The author(s) declare that no financial support was received for the research, authorship, and/or publication of this article.
The authors declare that the research was conducted in the absence of any commercial or financial relationships that could be construed as a potential conflict of interest.
The author(s) declare that no Gen AI was used in the creation of this manuscript.
All claims expressed in this article are solely those of the authors and do not necessarily represent those of their affiliated organizations, or those of the publisher, the editors and the reviewers. Any product that may be evaluated in this article, or claim that may be made by its manufacturer, is not guaranteed or endorsed by the publisher.
1. ^https://www.dropbox.com/scl/fi/4x6xtuy0dfxmy57hfud0f/Paper-Fontiers-Data.xlsm?rlkey=1a0u6zjr676e3ytodlnd3kqf1&st=i6hfae1d&dl=0
Apostolopoulos, Y., Sönmez, S., Shattell, M., Haldeman, L., Strack, R., and Jones, V. (2011). Barriers to truck drivers' healthy eating: environmental influences and health promotion strategies. J. Workplace Behav. Health 26, 122–143. doi: 10.1080/15555240.2011.573754
Barbee, J., Jayakumar, J., Touse, S., and Venkataraman, K. (2021). Retail's need for speed: Unlocking value in omnichannel delivery. McKinsey & Company.
Bard, J., Kontoravdis, G., and Yu, G. (2002). A branch-and-cut procedure for the vehicle routing problem with time windows. Transp. Sci. 36, 250–269. doi: 10.1287/trsc.36.2.250.565
Bhalaji, R., Sankaranarayanan, B., Alam, S. T., Ibne Hossain, N. U., Ali, S. M., and Karuppiah, K. (2022). A decision support model for evaluating risks in a collaborative supply chain of the medical equipment manufacturing industry. Supply Chain Forum. 23, 227–251. doi: 10.1080/16258312.2021.1989268
Braekers, K., Ramaekers, K., and Van Nieuwenhuyse, I. (2016). The vehicle routing problem: State of the art classification and review. Comp. Indust. Eng. 99, 300–313. doi: 10.1016/j.cie.2015.12.007
Calosso, T., Cantamessa, M., Vu, D., and Villa, A. (2003). Production planning and order acceptance in business to business electronic commerce. Int. J. Prod. Econ. 85, 233–249. doi: 10.1016/S0925-5273(03)00112-9
Dantzig, G. B., and Ramser, J. H. (1959). The truck dispatching problem. Manage. Sci. 6, 80–91. doi: 10.1287/mnsc.6.1.80
Date, G., and Chandrasekharan, S. (2018). Beyond efficiency: engineering for sustainability requires solving for pattern. Eng. Stud. 10, 12–37. doi: 10.1080/19378629.2017.1410160
Dytianquin, N., Paindavoine, S., and Kalogeras, N. (2024). Going circular with what we wear and how we build: Parallelisms between the dutch and french catwalks of fashion and construction. Front. Sustainab. 5:1456302. doi: 10.3389/frsus.2024.1456302
Ertas, A. (2010). Understanding of transdiscipline and transdisciplinary process. Transdiscipl. J. Eng. Sci. 1:7. doi: 10.22545/2010/0007
Fink, M., Desaulniers, G., Frey, M., Kiermaier, F., Kolisch, R., and Soumis, F. (2019). Column generation for vehicle routing problems with multiple synchronization constraints. Eur. J. Oper. Res. 272, 699–711. doi: 10.1016/j.ejor.2018.06.046
Firmansyah, E. B., Machado, M. R., and Moreira, J. L. R. (2024). How can artificial intelligence (AI) be used to manage customer lifetime value (CLV)—a systematic literature review. Int. J. Inform. Managem. Data Insights 4:100279. doi: 10.1016/j.jjimei.2024.100279
Freeman, R. E. (2010). Strategic Management: A Stakeholder Approach. Cambridge: Cambridge University Press.
Freeman, R. E., Phillips, R., and Sisodia, R. (2020). Tensions in stakeholder theory. Busin. Soc. 59, 213–231. doi: 10.1177/0007650318773750
Ghannadpour, S. F., Noori, S., and Tavakkoli-Moghaddam, R. (2014). A multi-objective vehicle routing and scheduling problem with uncertainty in customers' request and priority. J. Comb. Optim. 28, 414–446. doi: 10.1007/s10878-012-9564-x
Goel, P. (2010). Triple bottom line reporting: an analytical approach for corporate sustainability. J. Finance, Account. Managem. 1:1.
Homburg, C., Droll, M., and Totzek, D. (2008). Customer prioritization: does it pay off, and how should it be implemented? J. Mark. 72, 110–130. doi: 10.1509/jmkg.72.5.110
Hong-kit Yim, F., Anderson, R. E., and Swaminathan, S. (2004). Customer relationship management: Its dimensions and effect on customer outcomes. J. Personal Sell. Sales Managem. 24, 263–278. doi: 10.1080/08853134.2004.10749037
Islam, M. S., Moeinzadeh, S., Tseng, M.-L., and Tan, K. (2021). A literature review on environmental concerns in logistics: trends and future challenges. Int. J. Logist. Res. Appl. 24, 126–151. doi: 10.1080/13675567.2020.1732313
James, B., Katie, G., Jitendra, M., and Bharat, M. (2015). ‘The big idea' the sustainable economy and the TBL (triple bottom line). Adv. Managem. 8:1.
Jensen, A., and Dahl, S. (2009). Truck drivers hours-of-service regulations and occupational health. Work 33, 363–368. doi: 10.3233/WOR-2009-0884
Konstantakopoulos, G. D., Gayialis, S. P., and Kechagias, E. P. (2022). Vehicle routing problem and related algorithms for logistics distribution: a literature review and classification. Operat. Res. 22, 2033–2062. doi: 10.1007/s12351-020-00600-7
Lahyani, R., Coelho, L. C., Khemakhem, M., Laporte, G., and Semet, F. (2015). A multi-compartment vehicle routing problem arising in the collection of olive oil in tunisia. Omega 51:1–10. doi: 10.1016/j.omega.2014.08.007
Laporte, G., Musmanno, R., and Vocaturo, F. (2010). An adaptive large neighbourhood search heuristic for the capacitated arc-routing problem with stochastic demands. Transp. Sci. 44,125–135. doi: 10.1287/trsc.1090.0290
Lattanzio, S., Nassehi, A., Parry, G., and Newnes, L. (2021). Concepts of transdisciplinary engineering: a transdisciplinary landscape. Int. J. Agile Syst. Managem. 14, 292–312. doi: 10.1504/IJASM.2021.118072
Lenstra, J. K., and Kan, A. R. (1981). Complexity of vehicle routing and scheduling problems. Networks 11, 221–227. doi: 10.1002/net.3230110211
Lin, C., Choy, K. L., Ho, G. T., Chung, S. H., and Lam, H. (2014). Survey of green vehicle routing problem: past and future trends. Expert Syst. Appl. 41, 1118–1138. doi: 10.1016/j.eswa.2013.07.107
Lopez-Arboleda, E., Sarmiento, A. T., and Cardenas, L. M. (2019). Systematic review of integrated sustainable transportation models for electric passenger vehicle diffusion. Sustainability 11:2513. doi: 10.3390/su11092513
Macassa, G., McGrath, C., Tomaselli, G., and Buttigieg, S. C. (2021). Corporate social responsibility and internal stakeholders' health and wellbeing in europe: a systematic descriptive review. Health Promot. Int. 36, 866–883. doi: 10.1093/heapro/daaa071
Mendes, N., and Iori, M. (2020). “A decision support system for a multi-trip vehicle routing problem with trucks and drivers scheduling,” in Proceedings of the 22nd International Conference on Enterprise Information Systems (ICEIS 2020), Vol. 1, 339–349. doi: 10.5220/0009364403390349
Mojtahedi, M., Fathollahi-Fard, A. M., Tavakkoli-Moghaddam, R., and Newton, S. (2021). Sustainable vehicle routing problem for coordinated solid waste management. J. Indust. Inform. Integrat. 23:100220. doi: 10.1016/j.jii.2021.100220
Moodie, D. (1999). Due date demand management: negotiating the trade-off between price and delivery. Int. J. Prod. Res. 37, 997–1021. doi: 10.1080/002075499191373
Nagata, Y., and Bräysy, O. (2009). A powerful route minimization heuristic for the vehicle routing problem with time windows. Operat. Res. Lett. 37, 333–338. doi: 10.1016/j.orl.2009.04.006
Ng, M. K., Yousuf, B., Bigelow, P. L., and Van Eerd, D. (2015). Effectiveness of health promotion programmes for truck drivers: a systematic review. Health Educ. J. 74, 270–286. doi: 10.1177/0017896914533953
Nucamendi-Guillén, S., Flores-Díaz, D., Olivares-Benitez, E., and Mendoza, A. (2020). A memetic algorithm for the cumulative capacitated vehicle routing problem including priority indexes. Appl. Sci. 10:3943. doi: 10.3390/app10113943
Pilati, F., and Tronconi, R. (2024). Tri-objective vehicle routing problem to optimize the distribution process of sustainable local e-commerce platforms. Sustainability 16:1810. doi: 10.3390/su16051810
Rincon-Garcia, N., Waterson, B. J., and Cherrett, T. J. (2018). Requirements from vehicle routing software: Perspectives from literature, developers and the freight industry. Transp. Rev. 38, 117–138. doi: 10.1080/01441647.2017.1297869
Rust, R. T., and Verhoef, P. C. (2005). Optimizing the marketing interventions mix in intermediate-term crm. Market. Sci. 24, 477–489. doi: 10.1287/mksc.1040.0107
Sar, K., and Ghadimi, P. (2023). A systematic literature review of the vehicle routing problem in reverse logistics operations. Comp. Indust. Eng. 177:109011. doi: 10.1016/j.cie.2023.109011
Scholz, R. W., and Steiner, G. (2015). The real type and ideal type of transdisciplinary processes: part I-theoretical foundations. Sustainab. Sci. 10, 527–544. doi: 10.1007/s11625-015-0326-4
Slotnick, S. A. (2011). Order acceptance and scheduling: a taxonomy and review. Eur. J. Oper. Res. 212, 1–11. doi: 10.1016/j.ejor.2010.09.042
Tarhini, A., Danach, K., and Harfouche, A. (2022). Swarm intelligence-based hyper-heuristic for the vehicle routing problem with prioritized customers. Ann. Operat. Res. 2022, 1–22. doi: 10.1007/s10479-020-03625-5
Trigos, F., and López, E. M. (2016). Maximising profit for multiple-product, single-period, single-machine manufacturing under sequential set-up constraints that depend on lot size. Int. J. Prod. Res. 54, 1134–1151. doi: 10.1080/00207543.2015.1055348
van Benthem, T., Bergman, M., and Mes, M. (2020). “Solving a bi-objective rich vehicle routing problem with customer prioritization,” in Computational Logistics: 11th International Conference, ICCL 2020 (Enschede: Springer), 183–199.
Venkatesan, R., and Kumar, V. (2004). A customer lifetime value framework for customer selection and resource allocation strategy. J. Mark. 68, 106–125. doi: 10.1509/jmkg.68.4.106.42728
Venkatraman, S., and Nayak, R. R. (2015). Corporate sustainability: An is approach for integrating triple bottom line elements. Soc. Responsib. J. 11, 482–501. doi: 10.1108/SRJ-11-2013-0136
Keywords: customer prioritization, distribution, negotiation, transdisciplinary engineering, value creation, Vehicle Routing Problem
Citation: Trigos F and Osorio ML (2025) Integrating the Triple Bottom Line into the Vehicle Routing Problem: a transdisciplinary approach to customer prioritization. Front. Sustain. 6:1528514. doi: 10.3389/frsus.2025.1528514
Received: 14 November 2024; Accepted: 10 February 2025;
Published: 26 February 2025.
Edited by:
Adam C. G. Cooper, University College London, United KingdomReviewed by:
Karuppiah Koppiahraj, Saveetha University, IndiaCopyright © 2025 Trigos and Osorio. This is an open-access article distributed under the terms of the Creative Commons Attribution License (CC BY). The use, distribution or reproduction in other forums is permitted, provided the original author(s) and the copyright owner(s) are credited and that the original publication in this journal is cited, in accordance with accepted academic practice. No use, distribution or reproduction is permitted which does not comply with these terms.
*Correspondence: María Lucila Osorio, bHVjaWxhb3NvcmlvQHRlYy5teA==
Disclaimer: All claims expressed in this article are solely those of the authors and do not necessarily represent those of their affiliated organizations, or those of the publisher, the editors and the reviewers. Any product that may be evaluated in this article or claim that may be made by its manufacturer is not guaranteed or endorsed by the publisher.
Research integrity at Frontiers
Learn more about the work of our research integrity team to safeguard the quality of each article we publish.