- Chair of Stability and Failure of Functionally Optimized Structures, Institute of Mechanics, Faculty V Mechanical Engineering and Transport Systems, Technische Universität Berlin, Berlin, Germany
Additive Manufacturing (AM), often referred to as 3D printing, is expected to have a high impact on the manufacturing industry as well as on society. The inherent characteristics of AM make it possible to help solve global challenges, which can be explored in reference to the 17 Sustainable Development Goals (SDGs) of the United Nations. This is the first paper that examines the connection of AM and the 17 SDGs through a literature review. In this work, it is outlined which SDGs have a high, moderate or low potential to be fostered by AM. The SDGs are introduced and corresponding studies relevant to the respective SDG are presented. It is found that six out of 17 SDGs have high potential to be promoted by AM. These are SDG 1 (No poverty), SDG 3 (Good Health and Wellbeing), SDG 4 (Quality Education), SDG 9 (Industry, Innovation, and Infrastructure), SDG 12 (Responsible Consumption and Production), and SDG 14 (Life below Water). Furthermore, two SDGs have been identified that have moderate potential to be cultivated by AM. These are SDG 7 (Affordable and Clean Energy) and SDG 10 (Reduced Inequalities).
1. Introduction
1.1. Additive Manufacturing
Additive Manufacturing (AM), often referred to as 3D printing, is a production technology that creates objects layer by layer and is applicable to a variety of materials such as polymers (Zhou et al., 2020; Arefin et al., 2021), ceramic (Chen et al., 2019), metal (Murr, 2018; Buchanan and Gardner, 2019), concrete (Nehme and Abeidi, 2022), soil (Fratello and Rael, 2020), and tissue (Richards et al., 2013).
AM is a collective term comprising several different 3D printing techniques. All these techniques make use of a digital file, which represents an object, which is printed layer by layer. According to ISO/ASTM 52900:2021 there are in total seven different AM process categories (ISO/ASTM International, 2021). The four AM process categories which play a major role in this work are outlined below by their definition according to ISO/ASTM 52900:2021.
• Binder jetting technology (BJT): liquid bonding agent is selectively deposited to join powder materials.
• Directed energy deposition (DED): thermal energy is used to fuse materials by melting as they are being deposited.
• Material extrusion (MEX): material is selectively dispensed through a nozzle or orifice.
• Powder bed fusion (PBF): thermal energy selectively fuses regions of a powder bed.
MEX comprises several AM techniques such as fused filament fabrication (FFF), where the material is delivered in the form of a filament which is molten or slightly fluidized. FFF is a very common and often low-cost AM technique, especially when referring to so-called “desktop” 3D printers.
PBF also comprises several AM techniques such as Selective Laser Melting (SLM) and Selective Laser Sintering (SLS). Many other names are used to refer to techniques that ultimately are a form of PBF. To keep things simple, as few abbreviations as possible are used.
This paper does not focus on any particular production technique. Rather, AM as a totality of all these techniques is examined. This is the reason why some sections of this work do not elaborate on the specific AM technique that is used in a respective case study.
AM shows many advantages in contrast to conventional manufacturing. The key advantages are:
• On-site manufacturing. Apart from a 3D printer, power supply, and raw material, no further tools or facilities are needed. That makes it possible to produce nearly everywhere and anytime, thus on demand and decentralized (King et al., 2014; Ford and Despeisse, 2016).
• Higher efficiency, e.g., through less waste material (also referred to as a low buy-to-fly ratio) (Gebler et al., 2014).
• Shorter supply chains (Gebler et al., 2014).
• More design freedom. AM allows easy production of complex and entirely new geometries (Olsson et al., 2017; Li et al., 2020) and thus a high degree of customization (Attaran, 2017; Srinivasan et al., 2018).
• Possibility to easily print spare parts (Ford and Despeisse, 2016).
• Lower production costs per piece, especially for small quantities (Hopkinson et al., 2006).
• New materials with new or enhanced properties (Zhang et al., 2023; Zou et al., 2023), e.g., enhanced material combinations (Zheng et al., 2021), functionally graded materials (Zhang et al., 2022) as well as 4D printed parts (Sheikh et al., 2023; Wang et al., 2023).
• Potential for open source appropriate technology (Pearce et al., 2010).
For these and other reasons, AM is expected to have a high impact on the manufacturing industry as well as on society (Jiang et al., 2017). Zarrabeitia-Bilbao et al. (2019) summarize the benefits of AM as follows: “AM technologies have been identified as revolutionary because of their power to change, among other things, productive systems, skills and wellbeing; and they will have major implications for society.”
The inherent characteristics of AM make it possible to solve not only specific problems but fundamental global challenges as well. One prominent summary of the most important global challenges are the 17 Sustainable Development Goals (SDGs) of the United Nations.
1.2. The Sustainable Development Goals
The 17 Sustainable Development Goals (SDGs) have been adopted by the United Nations in 2015 as part of the 2030 Agenda for Sustainable Development. The 17 SDGs are to be achieved by the year 2030 and formulated as follows (cited from United Nations, 2015):
• SDG 1: No poverty
• SDG 2: Zero hunger
• SDG 3: Good health and wellbeing
• SDG 4: Quality education
• SDG 5: Gender equality
• SDG 6: Clean water and sanitation
• SDG 7: Affordable and clean energy
• SDG 8: Decent work and economic growth
• SDG 9: Industry, innovation, and infrastrucure
• SDG 10: Reduced inequalities
• SDG 11: Sustainable cities and communities
• SDG 12: Responsible consumption and production
• SDG 13: Climate action
• SDG 14: Life below water
• SDG 15: Life on land
• SDG 16: Peace, justice, and strong institutions
• SDG 17: Partnerships for the goals
Each SDG has so-called targets which specify the objective of the respective SDG. These targets will be used to examine if AM can foster a certain SDG.
For achieving the SDGs and their targets, several aspects of modern reality can make a contribution, also a technology like AM. Many different studies have investigated specific effects of AM on particular sustainability aspects, but only one paper has yet been published about AM and its importance for sustainable development in general: Pearce et al. (2010) determined that AM has “enourmous potential” in stimulating sustainable development and many other articles support this statement. However, no paper has yet been published that investigates the connection of AM and each of the 17 SDGs. This paper is the first one to do so. It reviews and assesses the impact of AM on the abovementioned SDGs and their targets and therefore presents a summary of publications and findings. Furthermore, this paper may also serve as a guide to researchers across all disciplines who are interested in meaningful work related to 3D printing.
2. Method
This work subsumes the findings of a detailed literature research about AM in connection with the SDGs. All results have been obtained by means of the search engines Web of Science and Semanticscholar using the keywords “3D Printing” or “Additive Manufacturing” in connection with the keywords mentioned or indicated by the SDGs or their respective targets. In each section of this article, one SDG will be introduced and the main aspects of AM and their contribution to the achievement of the SDG will be outlined, evidenced by studies. At the end of each section, the potential of AM to contribute to the achievement of the SDG will be evaluated, using the qualitative grades “high”, “moderate”, and “low”. These grades have been defined as follows:
• High potential: AM could foster at least one target of the respective SDG, if deployed accordingly.
• Moderate potential: AM could foster one target of the respective SDG, if deployed accordingly. However, the connection between AM and the target is rather indirect and/or the evidence is not as strong.
• Low potential: No or not enough evidence could be found indicating that AM can foster any target of the respective SDG.
It is hereby underlined that this work assesses the potential of certain SDGs to be stimulated by AM. In many cases, this potential is not realized. If certain benefits of AM are not (yet) applied widely because of high costs, lack of infrastructure, or other external reasons, this is not interpreted as a lower potential.
This literature review does not focus on any particular AM technique. Furthermore, the differences of the various AM techniques are not considered in this work. Every study is taken into account which is suitable to establish a connection between any aspect, technique, or application of AM and a target of an SDG.
Because this work mentions efficiency improvements and related environmental gains, it is hereby underlined that the rebound effect has to be kept in mind when evaluating the resulting environmental gains. However, a detailed calculation on all mentioned AM-driven efficiency improvements and their rebound-adjusted amounts is not performed in this work.
3. Qualitative results
3.1. SDG 1: no poverty
The aim of SDG 1 is stated as follows: “End poverty in all its forms everywhere” (United Nations, 2015). Regarding SDG 1, it was found that AM benefits two independent areas: Disaster relief and economic poverty reduction.
Disaster relief is addressed by Target 1.5 of SDG 1, which aims to “build the resilience of the poor [...] and reduce their exposure and vulnerability to [...] disasters”. AM can directly stimulate this target because many benefits of AM in a commercial setting apply in disaster relief and humanitarian aid as well (Tatham et al., 2015; Raeymaekers et al., 2021).
The benefits of AM for disaster relief and humanitarian aid are
• On-site production (James and Gilman, 2015; Tatham et al., 2015; Saripalle et al., 2016; Corsini et al., 2020; Raeymaekers et al., 2021),
• Simpler, faster or more robust supply chain (James and Gilman, 2015; Tatham et al., 2015; Corsini et al., 2020; Rodríguez-Espíndola et al., 2020; Raeymaekers et al., 2021),
• On demand production, obviating the need for warehousing (James and Gilman, 2015; Tatham et al., 2015; Saripalle et al., 2016),
• High mass:volume ratio of the filament, leading to efficient shipping (James and Gilman, 2015; Tatham et al., 2015),
• Higher ability to meet unanticipated demands for certain goods or operations (Tatham et al., 2015; Kieslinger et al., 2021; Raeymaekers et al., 2021),
• High ability to print spare parts and other customized parts (James and Gilman, 2015; Tatham et al., 2015; Corsini et al., 2020), and
• Possibility to print post-disaster homes/shelters (Gregory et al., 2016; Venturi et al., 2019).
The benefits lead to an enhanced logistic efficiency. This directly implies high financial savings because “60 to 80 percent of humanitarian aid is spent on logistics and shipping” (Saripalle et al., 2016). The sources mentioned in this context refer to FFF printers in most but not all of the cases.
Many further (case) studies have proven that AM already is a very useful and feasible way to improve disaster relief and humanitarian aid (James and Gilman, 2015; James and James, 2016; Saripalle et al., 2016; Rodríguez-Espíndola et al., 2020; Tönissen and Schlicher, 2021) and that vulnerable communities in particular can be helped by AM-supported disaster relief (Yu and Khan, 2015; Mohammed et al., 2018b). Examples of additive manufactured goods in humanitarian aid are spare parts for hospital equipment (Saripalle et al., 2016) and pipe fittings for water supply (Mohammed et al., 2018b).
One further application example of AM in humanitarian aid has been given by Savonen et al. (2018) who successfully developed an open hardware, self-replicating FFF 3D printer specially designed for humanitarian aid. The printer is robust, portable, easy to repair and applicable with a variety of materials and geometries (see Figure 1).
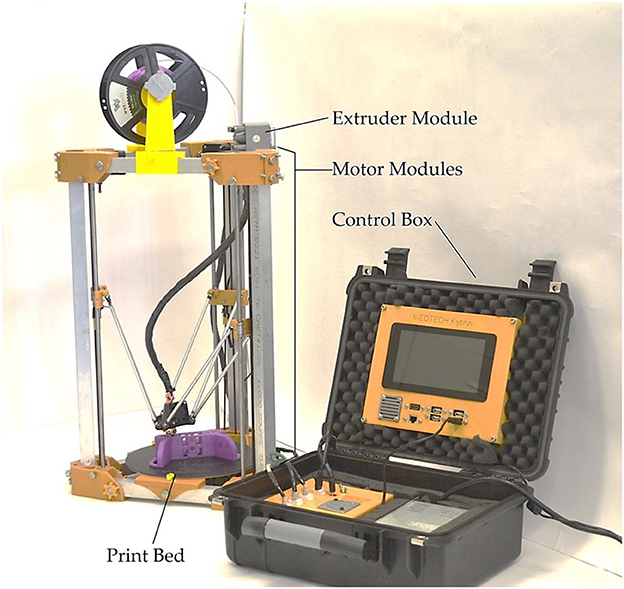
Figure 1. The printer developed by Savonen et al. (2018). Image source: Savonen et al. (2018), Creative Commons Attribution (CC BY) license (http://creativecommons.org/licenses/by/4.0/).
Moreover, two studies indicate that AM could help in addressing the need of post-disaster housing by 3D-printing shelters of soil or concrete (Venturi et al., 2019; Akeila et al., 2021), which could be understood as a way to reduce the “exposure and vulnerability to [...] disaster” as mentioned in Target 1.5.
A second way in which AM could benefit SDG 1 is economic poverty reduction. Target 1.1 aims to “eradicate extreme poverty for all people everywhere, currently measured as people living on <$ 1.25 a day.” Gwamuri et al. (2016) state: “[FFF] 3D printers powered by affordable mobile PV solar systems have a great potential to reduce poverty through employment creation, as well as ensuring a constant supply of scarce products for isolated communities.” In another study, King et al. (2014) conclude that “The ability to easily fabricate custom and complex parts or products at exceptionally low-cost offers people anywhere in the world the ability to print themselves out of poverty as they can print items to meet their own needs, those of their community, and export items to sell”. Two studies also examined the effects of so-called “plastic banks,” where waste plastic can be exchanged for money. The waste plastic is subsequently turned into flakes, pellets or 3D printing filament which is mostly used in FFF printers. Both studies conclude that the plastic banks can help in reducing poverty (Feeley et al., 2014; Katz, 2019) by giving waste pickers a financial perspective. However, AM is not the only application possibility for the produced raw material so it cannot be deduced that all socio-economic advantages of the plastic banks can be connected to AM.
Interim Conclusion: AM has many advantages that pay off very well in humanitarian aid. A variety of studies and case studies observe that AM is a useful and feasible way to improve disaster relief and humanitarian aid. Even post-disaster shelters could be made by AM. Two studies also indicate that vulnerable communities in particular can be helped by AM-supported disaster relief. For this reason, we conclude that AM can stimulate target 1.5, which aims to “build the resilience of the poor [...] and reduce their exposure and vulnerability to [...] disasters”. Additionally, AM could also have some bearing on economic poverty reduction and thus could contribute at least in a small way to target 1.1, which aims to “eradicate extreme poverty for all people everywhere”. All in all, there is a robust body of evidence to support the thesis that AM could cultivate at least one target of SDG 1 (target 1.5), if deployed accordingly. According to our definitions, this leads to the conclusion that SDG 1 has high potential to be encouraged by AM.
3.2. SDG 2: zero hunger
SDG 2 is formulated as to “[e]nd hunger, achieve food security and improved nutrition and promote sustainable agriculture” (United Nations, 2015). As AM can in some cases give support to farmers, two targets of SDG 2 are relevant in the context of farming: Firstly, target 2.4 aims to “ensure sustainable food production systems and implement resilient [and sustainable] agricultural practices” (United Nations, 2015). Secondly, target 2.a mentions “technology development [...] to enhance agricultural productive capacity” (United Nations, 2015).
For food production in general and sustainable agriculture in particular, small-scale farms are of particular importance (Willer et al., 2019; United Nations, 2020). AM can support resource-poor landholders by enabling production of cheap, durable and customizable farming tools (Gebremedhin et al., 2015; Pearce, 2015; Koslow, 2016; NUI Galway, 2017) and by supporting prototyping and fabrication of spare parts for agricultural machinery (Gummert et al., 2019).
Another topic that links AM and SDG 2 is the ability 3D print food products which, if texture or shape-modified, may enhance nutrition and quality of living of people with swallowing disabilities (Chen et al., 2022). This aspect touches upon target 2.1 which aims among other things to “[...] ensure access by people in vulnerable situations [...] to safe, nutritious and sufficient food” (United Nations, 2015).
Interim conclusion: It seems that AM could give some support for farmers in special cases, but there is no clear evidence that AM can help implementing “sustainable food production systems” or “practices” as mentioned in target 2.4 or that the technological support by AM can “enhance agricultural productive capacity” as mentioned in target 2.a. The most reliable link between AM and any target of SDG 2 seems to be given by 3D printed food products. These may contribute to the quality of live of people with swallowing disabilities and thus touch upon target 2.1. However, it cannot be evaluated whether AM can enhance the access to sufficient and suitable food. For this reason, SDG 2 is concluded to have only low potential to be stimulated by AM.
3.3. SDG 3: good health and wellbeing
SDG 3 is formulated as to “[e]nsure healthy lives and promote wellbeing for all at all ages” (United Nations, 2015). In terms of AM, target 3.8 is of special interest. It is verbalized as to “[a]chieve universal health coverage, including financial risk protection, access to quality essential health-care services and access to safe, effective, quality and affordable essential medicines and vaccines for all” (United Nations, 2015). The medical and healthcare sector is experiencing a number of advances enabled by AM (Trenfield et al., 2019). Because there is such a large number of publications dealing with AM in the medical sector, this work focuses on some prominent examples: medical devices and instruments, prosthetics and orthotics, surgical simulators and personalized medicine.
In the field of medical devices, AM is already about to establish itself (Culmone et al., 2019; 3D LifePrints UK Ltd, 2020). During the first two years of the COVID-19-pandemic, a vast amount of papers report or investigate AM of personal-protective equipment such as face shields, face masks and respiratory filters (Bharti and Singh, 2020; Celik et al., 2020; Fillat-Goma et al., 2020; Gomes et al., 2020; Rendeki et al., 2020; Sinha et al., 2020; Wierzbicki et al., 2020; Zhang et al., 2020; Aydin et al., 2021; Li S. et al., 2021; Longhitano et al., 2021; Mathew et al., 2021; Sherborne and Claeyssens, 2021; Singh et al., 2021; Spake et al., 2021; Sterman et al., 2021; Wang Y. et al., 2021). One main advantage in the medical field is that AM can strongly help overcome shortage (Bishop and Leigh, 2020; Tarfaoui et al., 2020), amongst other things by supporting or changing the supply chain (Guttridge et al., 2021; Guvener et al., 2021; Ibrahim et al., 2021; Singh et al., 2021). Another advantage pays off best in remote regions, where cheap and on-site production (e.g., of prostheses) can facilitate access to healthcare (Ishengoma and Mtaho, 2014; Culmone et al., 2019). Additionally, AM allows production of medical instruments and devices with previously unachievable shapes, sizes and degrees of customization (Culmone et al., 2019; Haleem and Javaid, 2020), e.g., surgical guides (Zadpoor and Malda, 2016), which in turn can increase surgical accuracy and hence bring forth the state of the art in medicine generally. Another medical field benefiting from AM is the domain of prosthetics and orthotics with a variety of application examples (South et al., 2010; Zadpoor and Malda, 2016; Zuniga et al., 2016; Enabling the Future, 2019; Team UnLimbited, 2019; Projeto de Extensão Mao3D, 2020; Ribeiro et al., 2021).
With AM, not only solid objects can be printed, but soft objects as well. This simplifies the production of mockups of the human body, so-called surgical simulators (see Figure 2). So far, a variety of realistic 3D printed simulators have been developed, e.g., for
• Ear surgery (Barber et al., 2016),
• Brain surgery (Ryan et al., 2016; Weinstock et al., 2017; Ding et al., 2019; Chen et al., 2020; Licci et al., 2020; Hong et al., 2021; Thiong'o et al., 2021),
• Ear, nose and throat surgery (Shcheglov et al., 2020),
• And other specific kinds of surgery (Barber et al., 2018; Murr et al., 2021).
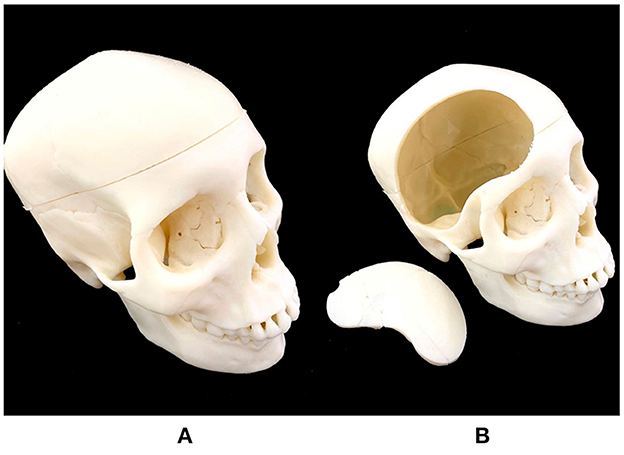
Figure 2. A 3D printed skull, which is part of a surgical simulator for brain surgery (A). A piece of the skull can be removed as in an operation (B). Image source: Chen et al. (2020), Creative Commons Attribution (CC BY) license (http://creativecommons.org/licenses/by/4.0/).
Some of the studies mentioned above suggest positive learning outcomes of prospective or active surgeons through training with these simulators, some studies also mention the possibility of manufacturing patient-customized simulators. The studies in their entirety suggest that AM will enhance the state of the art in medicine by enabling riskless and realistic surgical training.
The ability of AM to produce highly customizable items in small quantities is also of special interest to the domain of medicine. 3D printed wound dressings with patient-specific drug dosage and drug release are being explored and found feasible (Teoh et al., 2021, 2022), however, AM of oral drugs is studied more widely. The main benefits of oral drugs produced via AM are as follows:
• Many different materials and AM techniques can be used for this purpose (Jamróz et al., 2018; Azad et al., 2020; Li et al., 2020; Vaz and Kumar, 2021).
• A variety of dosage forms is possible (Afsana et al., 2018).
• Customized dosing and drug release profile can be realized, tailored to the genetic profile, physiology and other individual requirements of each patient (Afsana et al., 2018; Aquino et al., 2018; Mathew et al., 2020; Vaz and Kumar, 2021). This is mainly because many complicated, elaborate structures can be achieved by AM that are hard or only cost-intensive to achieve in conventional ways (Li et al., 2020).
• Through AM, several different drugs can be combined in one tablet (Afsana et al., 2018; Vaz and Kumar, 2021). Besides, it is assumed that AM could possibly help make patient-specific medication smarter and more sustainable (Aquino et al., 2018).
Furthermore, it is expected that 3D printed food could improve the “physical and emotional health of older people with swallowing disability” (Chen et al., 2022).
Interim conclusion: There is profound evidence that AM changes and will continue to change the state of the art in healthcare systems worldwide. Besides, AM is considered to be a “great opportunity to provide easy access to healthcare in [countries of the global south]” (Culmone et al., 2019), which directly addresses target 3.8 of SDG 3. This allows the conclusion that AM can foster at least one target of SDG 3, if deployed accordingly, which means that SDG 3 has high potential to be cultivated by AM (according to our definition).
3.4. SDG 4: quality education
SDG 4 aims at “[e]nsur[ing] inclusive and equitable quality education and promote lifelong learning opportunities for all” (United Nations, 2015). One group that has to be considered especially in this context are physically impaired students as they are particularly at risk of being excluded from education (UNESCO, 2020). SDG 4 has two targets that address inclusion of disabled students: Firstly, target 4.5 is dedicated to—amongst other things—“equal access to all levels of education [...] for the vulnerable, including persons with disabilities”. Secondly, target 4.a aims at “inclusive and effective learning environments for all”.
In general, the targets of SDG 4 address education in schools as well as higher education. For this reason also studies dealing with AM in higher education will be taken into account. Two main aspects have been identified in which AM can enhance education: As an assistive technology in education in general and as a supportive technology for blind or low-vision students.
AM has been proven as an assistive technology in schools many times. There is profound evidence that AM can improve learning processes in a variety of school subjects (Ford and Despeisse, 2016; Pinger et al., 2020; Asempapa and Love, 2021; Lin et al., 2021; Monkovic et al., 2021; Novak et al., 2021; Pearson and Dube, 2022). Furthermore, results indicate that AM can
• Promote creativity and analytical thinking (Kostakis et al., 2015; Ford and Minshall, 2019; Novak and Wisdom, 2020; Levin and Verner, 2021),
• Increase student motivation/engagement (Kostakis et al., 2015; Ford and Minshall, 2019; Jones and Mendez, 2021; Monkovic et al., 2021),
• Raise students' confidence (Ford and Minshall, 2019) and
• Support interdisciplinary teaching by connecting STEM subjects with non-STEM subjects (Novak and Wisdom, 2020).
In chemistry class, AM enables the fabrication of customized devices for laboratory which are difficult or very costly to fabricate with conventional manufacturing technologies (Pinger et al., 2020). Also integrating AM into the curriculum of engineering undergraduate seems to hold positive potential in various ways, e.g., by enabling fast testing of designs and thus enhancing iterative design processes (Ford and Minshall, 2019).
Children with disabilities are one of the main groups to be included in the school context and beyond (UNESCO, 2020). As teaching material in schools is often accessible only in a visual way, the inclusion of students needs new learning environments and materials to be made available. AM provides some solutions, as is has been found to be very supporting for blind or low-vision students in different subjects such as maths (Willemsen, 2015), chemistry (Singhal and Balaji, 2020), programming (Kane and Bigham, 2014) or for learning Braille language (Samonte et al., 2019). In most of these cases, AM is supportive by enabling cheap and fast production of tactile objects (See and Advincula, 2021).
Interim conclusion: There is evidence that AM has the potential to enhance classroom learning in many ways. However, the advantages of AM can pay off more in the context of inclusive education as mentioned in target 4.5 and 4.a. There is profound evidence that AM could highly enhance education for blind or low-vision pupils because it enables cheap, fast and highly individual production of tactile objects in many different kinds of school subjects, hence providing a cheap way to increase accessability of learning materials. This way, AM could contribute to “inclusive and effective learning environments for all”. This suggests that AM could support at least target 4.a, if deployed accordingly. For this reason, it is concluded that SDG 4 has high potential to be fostered by AM.
3.5. SDG 5: gender equality
SDG 5 reads: “Achieve gender equality and empower all women and girls” (United Nations, 2015). Most targets of SDG 5 aim at closing the gender gap by means of policies and laws. One characteristic manifestation of the gender gap is a significantly low share of female and non-binary persons in decision-making positions, certain degree courses, or occupational fields. Currently, women are underrepresented in the engineering occupation (World Economic Forum, 2022) and also in AM-related occupation (Women in 3D Printing, 2020b; Sculpteo, 2021). However, AM is considered to help narrowing the gender gap in certain engineering fields because “With every new technology, social power relations and thus gender relations are negotiated” (Carstensen et al., 2014). Two initiatives could be identified that are related to AM and the empowerment of women as well. These will be introduced and evaluated in the following.
Women in 3D Printing is a global organization with the goal to promote women in the AM sector. The community of this initiative aims to increase the visibility of women who work or do research in the AM sector and to encourage women to make use of AM (Women in 3D Printing, 2020a). These intentions are implemented by networking events, chapters, and annual conferences (Women in 3D Printing, 2020a). Women in 3D Printing describes itself as “one of the largest Additive Manufacturing community worldwide” (Tipe 3D Printing, 2021). With initiatives like these, AM is part of a movement that already is successfully starting to alleviate gender inequality. Nevertheless, it is hard to verify a direct link between AM and an increase in gender equality on a bigger scale.
FabLabs are maker spaces and a community that provides open access to certain technology and knowledge (FabFoundationUK, 2016). As outlined by De Filippi and Troxler (2016), AM “plays a central role” in FabLabs. The diversity aspect in FabLabs has been examined by Voigt et al. (2017). Amongst other things, it was found that FabLabs have “a huge potential for technological action—without implying technology determinism—where communities of any gender, race or age can be empowered” (Voigt et al., 2017). One example for an inclusive working atmosphere was given by “‘WeMake' FabLab in Milan, which is managed by a female maker [and has] gender ratios of 40% female makers vs. 60% male makers” according to personal communication (Voigt et al., 2017). Nevertheless, the majority of all FabLabs is male-dominated (Voigt et al., 2017). Even though AM plays an important role in FabLabs and FabLabs in turn are considered being empowering to people of every gender, it is hard to deduce a direct link between AM and an increase in gender equality.
Another promising consideration is the number of female authorships in AM-related studies, research papers and technical reports. Studies about the number of female authorships in AM-related research are lacking. For this reason, no conclusions can be drawn regarding this aspect.
Interim conclusion: There are AM-related initiatives that may stimulate gender equality, and they give hope but no robust evidence yet. The connection between AM and gender equality via these initiatives is too indirect and too unexplored to be considered as evidence for medium or high potential. According to our definitions, a lack of evidence for medium or high potential is considered as low potential. For this reason, it is concluded that SDG 5 has low potential to be promoted by AM. More research in this field is needed.
3.6. SDG 6: clean water and sanitation
SDG 6 reads as follows: “Ensure availability and sustainable management of water and sanitation for all” (United Nations, 2015). There are different methods to prepare drinking water by using solar radiation, a few of which are highly suitable for remote regions. AM can push forward the efficiency of the following methods:
• Solar disinfection of drinking water (Vyatskikh et al., 2018)
• Passive solar still (Li et al., 2017)
• Water processing through membranes and filters (Beloshenko et al., 2019; Dommati et al., 2019; Issac and Kandasubramanian, 2020; Kim et al., 2020; König et al., 2020; Luukkonen et al., 2020; Tijing et al., 2020; Wang Z. et al., 2021).
Because most of these methods are highly suitable for remote areas with the need for better access to drinking water, it seems that there could be a link between AM and “universal and equitable access to safe and affordable drinking water for all” as mentioned in target 6.1. However, even if AM could increase the efficiency of drinking water preparation, there is no reliable evidence that this could increase access to or lower the price of drinking water. For this reason it is concluded that SDG 6 has low potential to be cultivated by AM.
3.7. SDG 7: affordable and clean energy
SDG 7 is formulated as to “[e]nsure access to affordable, reliable, sustainable and modern energy for all” (United Nations, 2015). The only target of SDG 7 that can be connected to AM in any way is target 7.2 which aims to “increase substantially the share of renewable energy in the global energy mix”.
The connection between AM and target 7.2 can be drawn via energy storage systems which are crucial for the integration of (a higher share of) renewable energy. Energy storage can be classified into two types:
• Electrical energy storage to provide buffers for the highly varying electrical energy produced by some of the renewable sources.
• Thermal energy storage, e.g., for utilizing industrial waste heat (Miró et al., 2016) or better integrate wind power (Heidar Esfehani, 2020).
Electrical energy storage uses batteries or similar kinds of electrochemical energy storage devices. A variety of research groups used AM to fabricate battery parts or entire batteries. Many of them achieved better battery performance due to the use of AM and, most notably, stated that AM will strongly push forward the efficiency or overall performance of batteries (Rocha et al., 2017; Tian et al., 2017; Down et al., 2019; Singh et al., 2019; Pang et al., 2020).
Thermal energy storage systems represent another type of energy storage which can be enhanced by AM (Dada et al., 2020). Especially in the field of phase change materials AM enables some major advancements, e.g., in the heat transfer performance (Dada et al., 2020; Ge et al., 2020; Moon et al., 2020).
Apart from energy storage, clean energy supply is another major topic regarding SDG 7. One of the most promising examples as well for stationary and for mobile energy supply is the fuel cell (Tai et al., 2019). In the last years of research, a variety of AM technologies have been utilized on different types of fuel cells. Most of all, the so-called microbial fuel cell has been made by AM in parts or entirely, achieving different types of improvements (Calignano et al., 2015; Bermúdez-Agudelo et al., 2020; You et al., 2020). One microbial fuel cell completely made by AM can be seen in Figure 3. The potential of AM for the field of fuel cells has been underlined by all research groups mentioned above. Various studies state that AM is important for further fuel cell development and that AM enables to improve the performance of fuel cells and their commercialization (Calignano et al., 2015; Tai et al., 2019; Bermúdez-Agudelo et al., 2020; You et al., 2020; Jang and Kelsall, 2022; Jia et al., 2022; Sapkota et al., 2022; Tarancon et al., 2022).
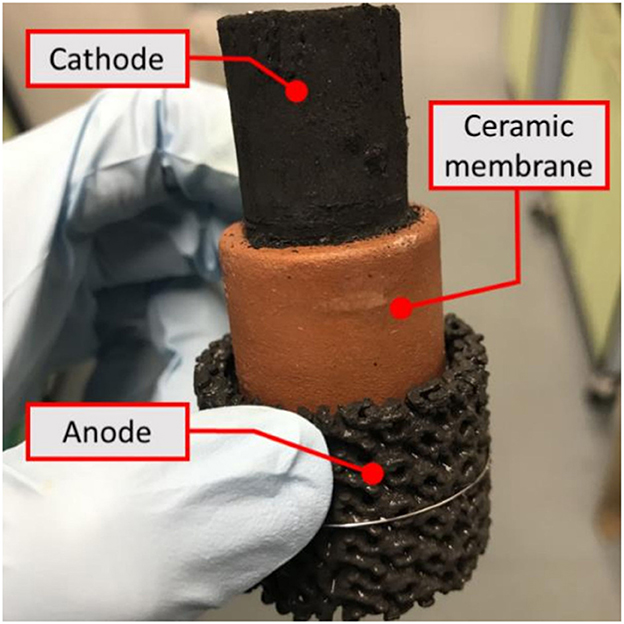
Figure 3. A microbial fuel cell completely made by AM. Image source: You et al. (2020), Creative Commons Attribution (CC BY) license (http://creativecommons.org/licenses/by/4.0/).
Interim conclusion: Due to the facts that AM is expected to enhance the efficiency of batteries and it could push forward the efficiency of thermal energy storage, it is concluded that AM is involved and can be involved more in the improvement of energy storage, which in turn is crucial for a higher share of renewables in the global energy mix. This means that AM could encourage some domains related to target 7.2, but only indirectly. According to our definitions, it is deduced that SDG 7 has a moderate potential to be fostered by AM.
3.8. SDG 8: decent work and economic growth
SDG 8 is formulated as to “[p]romote sustained, inclusive and sustainable economic growth, full and productive employment and decent work for all”. The targets of SDG 8 mainly deal with economic growth, a high employment rate, and labor rights/conditions. Even though there are studies examining the impact of AM and AM-related production systems on the labor market (Kianian et al., 2015; Pérez-Pérez et al., 2018; Ben-Ner et al., 2019; Freeman and McMahon, 2020), none of them could draw a conclusion about whether AM will have a rather positive or rather negative effect on either the job market or labor conditions. No further studies could be found that yield further information related to AM in connection to SDG 8. For this reason, it is concluded that SDG 8 has no or low potential to be promoted by AM.
3.9. SDG 9: industry, innovation, and infrastructure
SDG 9 aims to “[b]uild resilient infrastructure, promote inclusive and sustainable industrialization and foster innovation” (United Nations, 2015). The topic of resilient infrastructure is considered too remote from AM. However, two bigger topics remain that have a close connection to AM: Distributed Manufacturing and Innovation. Target 9.2 aims to, inter alia, “[p]romote inclusive and sustainable industrialization” (United Nations, 2015). This keyword leads to the topic of Distributed Manufacturing, which is a new approach to organize manufacturing. It works through a broad geographic dispersion (decentralization) of smaller, regional, inter-connected manufacturing sites (Johansson et al., 2005) and exhibits a variety of benefits like shorter lead time, more flexible supply chains, positive sustainability aspects and job creation (Ford and Despeisse, 2016; Huang et al., 2017; Nagarajan et al., 2018; Freeman and McMahon, 2020). Distributed AM is a specific type of Distributed Manufacturing. Its key benefits are:
• Financial savings for the producer and/or for the customers (Huang et al., 2017; Turner et al., 2019), in special cases more than 94% (Gallup et al., 2018),
• 12–60% less lead time (Huang et al., 2017),
• Suitability for spare parts production (Durão et al., 2016), and
• Reduced primary energy use and green house gas emissions (Baechler et al., 2013; Kreiger and Pearce, 2013; Huang et al., 2017)
Most of these benefits can be seen as a hint toward AM supporting inclusive and sustainable industrialization.
One objective of target 9.5 and 9.b is to support innovation in general (United Nations, 2015). AM itself can be described as an innovation (Gebhardt et al., 2018), but it also enables innovations. Almost every section of this work deals with innovations enabled by AM and there are many more AM-enabled innovations that are not being mentioned in this work. In general, AM provides many benefits that inherently enable new or significantly improved characteristics of produced parts. A few of these benefits are:
• More design freedom. AM allows easy production of complex and entirely new geometries (Olsson et al., 2017) and a high degree of customization (Attaran, 2017).
• On-site manufacturing. Apart from a 3D printer, power supply, and raw material, no further tools or facilities are needed. That makes it possible to produce nearly everywhere and anytime, thus on demand and decentralized (Ford and Despeisse, 2016). In theory, this also gives everyone with a 3D printer the possibility to innovate at home, which is pointing toward the topic of “user innovators” (Backstrom and Bengtsson, 2020)
• Higher efficiency, e.g., through less waste material and shorter supply chains (Gebler et al., 2014; Sun et al., 2021).
• Possibility to easily print spare parts (Ford and Despeisse, 2016).
• Lower production costs per piece, especially for small quantities (Hopkinson et al., 2006).
• Potential for open source appropriate technology (Pearce et al., 2010).
Woodson et al. (2019) examined if AM enables innovations in an inclusive way. It was found that AM is inclusive in some aspects (higher accessibility due to its open source nature) while being exclusive in other aspects (design requires preknowledge).
Interim conclusion: Apart from Distributed AM possibly fostering “inclusive and sustainable industrialization” as mentioned in target 9.2, the main benefit of AM with regard to SDG 9 is its deep connection to innovations. AM enables the production of new, previously hard to achieve designs (Olsson et al., 2017) and it changes the way innovations can assume shape, namely at home. This way, AM can deeply encourage innovations as indicated in targets 9.5 and 9.b. For this reason, it is concluded that AM has a high potential to support the achievement of SDG 9.
3.10. SDG 10: reduced inequalities
The aim of SDG 10 is to “[r]educe inequality within and among countries” (United Nations, 2015). Most of the targets of SDG 10 are thematically quite remote from AM and mostly concern economics, policies or management. This section will highlight only those two targets of SDG 10 where a connection to AM can be drawn. Target 10.1 is stated as follows: “By 2030, progressively achieve and sustain income growth of the bottom 40% of the population at a rate higher than the national average” (United Nations, 2015). In low-income countries, AM could help reducing poverty (Feeley et al., 2014; King et al., 2014; Gwamuri et al., 2016) (see section about SDG 1). This suggests the assumption that AM could possibly contribute to the achievement of target 10.1.
Target 10.2 reads: “By 2030, empower and promote the social, economic and political inclusion of all [...]” (United Nations, 2015). A link between political or economic inclusion and AM could not be found. However, two connections between social inclusion and AM could be found:
• For assistive devices for people with certain physical impairments, AM strongly supports development / design (see Figure 4) as well as enabling people to produce the assistive devices themselves on very low costs (Gallup et al., 2018; Gherardini et al., 2020). The assistive devices can in turn help impaired people to manage their daily life and enable more autonomy. This way, social inclusion might possibly be enhanced as well.
• AM can enhance the accessibility of cultural heritage: It enables an easier production of enhanced and scaled replicas (e.g., of sculptures) that can be touched and examined at close range. This way, certain groups can encounter art and cultural heritage in a much better way than before, e.g., visually impaired people or children (Neumüller et al., 2014). It can be deduced that this aspect possibly enhances social inclusion.
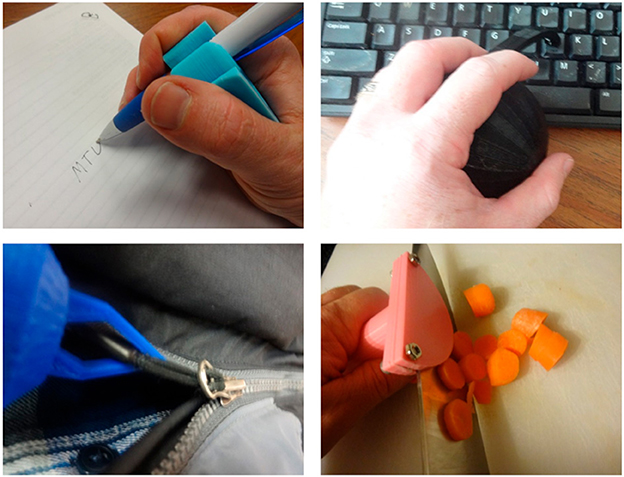
Figure 4. Selection of adaptive aids for arthritic patients. Clockwise: pen holder aid, typing aid, knife guide aid, zipper pull aid. Image source: Gallup et al. (2018), Creative Commons Attribution (CC BY) license (http://creativecommons.org/licenses/by/4.0/).
Interim conclusion: AM as a technology cannot replace or compensate for the measures needed in policy to eradicate inequality. However, AM can possibly support social inclusion in an indirect way (see above) and thus foster target 10.2. Due to the fact that AM can promote this target only in an indirect way, it is assessed that SDG 10 has only moderate potential to be cultivated by AM.
3.11. SDG 11: sustainable cities and communities
SDG 11 aims to “[m]ake cities and human settlements inclusive, safe, resilient and sustainable” (United Nations, 2015). The following sections mention a few aspects of SDG 11 that can be addressed a little bit by AM.
Noise is one of the main problems in cities. In terms of sound absorption, especially low-frequency noise cannot yet be controlled effectively. For this case of application, so-called “acoustic metamaterials” are a relatively new and promising technique both for the improvement of acoustics in and around buildings/road noise mitigation (Kumar and Lee, 2019). Several studies have shown that AM can enable new acoustic metamaterials with higher absorption rates and/or otherwise better sound absorption properties (Haberman and Guild, 2016; Gao and Hou, 2018; Guild et al., 2018; Yang et al., 2020). However, sound absorption is only the alleviation of symptoms and not the elimination of causes, which would be more effective.
AM gives the opportunity to build large-scale objects as well, such as buildings. It has been found that buildings or building components made of AM are likely to exhibit a higher energy efficiency than conventionally manufactured buildings (Mrazović et al., 2018). AM of concrete buildings is also a topic of research (Kaszynska et al., 2020). Furthermore, AM was used by architect Deena El-Mahdy for building houses of local material in the Western Desert of Egypt. This directly relates to target 11.c which addresses “buildings utilizing local materials” (United Nations, 2015).
Interim conclusion: The aspects connected to AM and sustainable cities are rather vague hints than robust evidence. Furthermore, no single target of SDG 11 could be found for which a convincing connection with AM could be established. Hence, it is assessed that SDG 11 has no or low potential to be promoted by AM.
3.12. SDG 12: responsible consumption and production
SDG 12 aims to “[e]nsure sustainable consumption and production patterns” (United Nations, 2015). AM can support this goal in many ways, e.g., through fostering Circular Economy, Distributed Recycling and spare parts production.
Target 12.5 aims to “substantially reduce waste generation through prevention, reduction, recycling and reuse” (United Nations, 2015), as does the concept of Circular Economy (CE). The CE concept is based on a closed-loop of resources, repairable and durable products, waste reduction, and renewable energy (Kristensen and Mosgaard, 2020). CE practices have been found to be potentially directly beneficial for the achievement of several SDGs, such as SDG 6, 7, 8, 12, and 15 (Schroeder et al., 2019).
AM exhibits some aspects that potentially could benefit CE, for example
• Possibility to enhance product lifetime by printing spare parts (Durão et al., 2016; Ford and Despeisse, 2016) or by specific repair of critical sections via DED (Saboori et al., 2019; Li L. et al., 2021; Jamieson et al., 2022; Arai et al., 2023),
• Recycling of waste through waste-to-filament processes (Feeley et al., 2014; Ponis et al., 2021; Romani et al., 2021), and
• More efficient use of resources through complex structures that need less material (Gebler et al., 2014; Sauerwein et al., 2019; Sun et al., 2021).
For these and other reasons, many studies come to the conclusion that AM and CE are compatible with each other (Despeisse et al., 2017; Sauerwein et al., 2019; Sanchez et al., 2020; Wilts and Long, 2020; de Mattos Nascimento et al., 2022; Kromoser et al., 2022).
A key concept of CE is recycling. One specific kind of recycling that involves AM is called distributed recycling for additive manufacturing (DRAM). The DRAM concept is often understood as a system where consumers collect their household or AM waste plastic, and subsequently, the waste plastic is recycled by the consumers themselves or in a nearby small-scale recycling site (Pavlo et al., 2018; Little et al., 2020).
The key advantages of DRAM are as follows:
• DRAM requires less energy than centralized recycling as it can significantly lower transportation emissions or in some cases can be solar powered (Baechler et al., 2013; Mohammed et al., 2018a; Monnet et al., 2018).
• Economic savings or income for consumers: Waste can be understood as raw material. When consumers have the means available to process this raw material, DRAM opens up a way for them to produce goods on their own and save or earn money (King et al., 2014; Dertinger et al., 2020).
DRAM has been proven to be feasible by various studies (Dertinger et al., 2020; Ong et al., 2020; Tanney et al., 2020), also regarding the mechanical strength of recycled material (Mägi et al., 2016; Anderson, 2017; Mohammed et al., 2017; Sanchez et al., 2017; Woern et al., 2018; Little et al., 2020; Ong et al., 2020; Vidakis et al., 2021).
In addition to that, AM supports resource efficiency in general, mainly through the following aspects:
• AM facilitates shorter delivery channels and shorter supply chains (Gebler et al., 2014; Ford and Despeisse, 2016; Freeman and McMahon, 2020). This increases logistic sustainability of parts or products made by AM (Pilz et al., 2020) as almost every kind of transport is accompanied by CO2 emissions.
• In contrast to conventional manufacturing techniques like milling or casting only as much raw material as needed is used and less material waste is produced (Gebler et al., 2014; Ford and Despeisse, 2016; Sauerwein et al., 2019).
• AM enables an extended product life, e.g., through easy production of replacement parts (Ford and Despeisse, 2016; Sauerwein et al., 2019). On various different websites websites such as yeggi.com, thingiverse.com, pinshape.com, myminifactory.com, or cults3d.com, an immense number of files of replacement parts for household goods, machinery, and electronic devices can be downloaded and printed at home. Apart from this DIY approach, AM is also promising for industrial-made replacement parts: Jiang et al. (2017) evaluate that it is likely that in 2030, all commercial spare parts will be 3D printed.
Hence, AM can significantly increase resource efficiency and thus sustainable practices. These sustainable practices are addressed in target 12.6 which is formulated as to “[e]ncourage companies, especially large and transnational companies, to adopt sustainable practices and to integrate sustainability information into their reporting cycle” (United Nations, 2015).
Interim conclusion: If AM would be deployed accordingly, it could stimulate sustainable consumption and production patterns in various ways. In particular, target 12.5 and 12.6 could be promoted by AM under favorable conditions. Hence, it is concluded that SDG 12 has high potential to be cultivated by AM.
3.13. SDG 13: climate action
SDG 13 directly addresses climate change, aiming to “[t]ake urgent action to combat climate change and its impacts” (United Nations, 2015), but the means for achieving this target are not specified very detailed. For this reason, this section will be oriented toward the targets of SDG 13.
Target 13.1 approaches resilience to climate-related hazards and disasters, target 13.2 covers climate change measures, target 13.a aims to ensure climate change-related financial aid to developing countries, and target 13.b mainly addresses inclusive climate change-related management in the least developed countries and small island developing countries (United Nations, 2015).
Even though AM might lead to a more resource-efficient production and consumption, no way could be found how AM can effectively help to “combat climate change and its impacts” as framed in SDG 13 (United Nations, 2015). No evidence could be found indicating that AM-related efficiency enhancements are extensive enough to considerably combat climate change via emission reduction or in another way. Hence, it is concluded that the potential of SDG 13 to be stimulated by AM is low.
3.14. SDG 14: life below water
SDG 14 is formulated as follows: “Conserve and sustainably use the oceans, seas and marine resources for sustainable development” (United Nations, 2015).
Target 14.2 intends to “sustainably manage and protect marine and coastal ecosystems to avoid significant adverse impacts, including by strengthening their resilience, and take action for their restoration in order to achieve healthy and productive oceans” (United Nations, 2015). For the restoration of coral reefs, 3D printed fake reefs have been successfully produced via ceramic MEX and installed under the sea. The geometrical shape and surface structure provide sufficient habitat conditions for coral polyps and fish (Albalawi et al., 2021; Oren et al., 2023). Over the first years of testing, these measures appear to be a successful approach to restore coral reefs (Berman et al., 2023), thereby directly facilitating target 14.2. According to our definition, it is concluded that SDG 14 has high potential to be fostered by AM.
3.15. SDGs 15, 16, 17
For the following SDGs no or only low potential has been identified:
• SDG 15 (Life on Land) is dedicated to “protect, restore and promote sustainable use of terrestrial ecosystems, sustainably manage forests, combat desertification, and halt and reverse land degradation and halt biodiversity loss” (United Nations, 2015). For this SDG and its targets, no noteworthy AM-related publication could be found.
• SDG 16 (Peace, Justice, and strong Institutions) aims to “promote peaceful and inclusive societies for sustainable development, provide access to justice for all and build effective, accountable and inclusive institutions at all levels” (United Nations, 2015). This SDG cannot be fostered by any manufacturing technology.
• SDG 17 (Partnerships for the Goals) is formulated as to “strengthen the means of implementation and revitalize the Global Partnership for Sustainable Development”. This goal clearly cannot be supported by any manufacturing technology, either.
Due to the absence of meaningful publications establishing a connection between AM and any of these SDGs, the potential of all these SDGs has been assessed as low.
4. Concluding discussion
This paper is the first to examine the relationship between Additive Manufacturing and all 17 SDGs. Based on a literature review, sources were sought for each SDG that prove whether AM can contribute to the achievement of this SDG. In the course of the research, it became apparent that some SDGs seem to be very predestined to be promoted by AM, others little or not at all. Our classification of all SDGs into the categories “high,” “moderate,” and “low” showed that six out of 17 SDGs have great potential to be promoted by AM: These are:
• SDG 1 (No poverty),
• SDG 3 (Good health and wellbeing),
• SDG 4 (Quality education),
• SDG 9 (Industry, innovation, and infrastructure),
• SDG 12 (Responsible consumption, and production), and
• SDG 14 (Life below water).
Furthermore, two SDGs have been identified that have moderate potential to be fostered by AM. These are:
• SDG 7 (Affordable and clean energy), and
• SDG 10 (Reduced inequalities).
The potential of SDG 5 was hard to estimate because studies about the number of female authorships in AM-related research are lacking. Furthermore, studies about the general connection between AM and an increase in gender equality are missing. This research gap is waiting to be dealt with.
It has been shown that in some areas AM has great potential to benefit the SDGs. However, several of the papers mentioned above point to the fact that this potential is far from being fully realized. The results of our research suggest the assumption that each high potential SDG could be promoted much more strongly by AM if this would be wanted and planned. Future research is needed about how exactly these SDGs could be fostered by AM.
5. Remark: about the citations in this work
Engineering-related articles tend to underrepresent women scientists in the citation. After writing this work, the female quota of all persons mentioned in the bibliography was evaluated by a python script—see Huber (2022) for further information. The female scientist quota of all cited persons in this work is roughly 23%. The aim of this paragraph is to raise awareness to this topic and to increase the number of female authors in science.
Author contributions
CV had the idea of the topic. JM has collected and organized all the sources, wrote a first draft of the manuscript, and refined the methodology. JM and AK wrote the final manuscript. AK and CV supervised the project and gave critical feedback. All authors contributed to the article and approved the submitted version.
Funding
We acknowledge support by the German Research Foundation and the Open Access Publication Fund of TU Berlin.
Conflict of interest
The authors declare that the research was conducted in the absence of any commercial or financial relationships that could be construed as a potential conflict of interest.
Publisher's note
All claims expressed in this article are solely those of the authors and do not necessarily represent those of their affiliated organizations, or those of the publisher, the editors and the reviewers. Any product that may be evaluated in this article, or claim that may be made by its manufacturer, is not guaranteed or endorsed by the publisher.
References
3D LifePrints UK Ltd (2020). Medical 3D Printing at the Point of Care - Improving Patient Outcomes With 3D Technologies. 3D LifePrints UK Website. Available online at: https://www.3dlifeprints.com/ (accessed January 30, 2021).
Afsana, J. V., Haider, N., and Jain, K. (2018). 3D printing in personalized drug delivery. Curr. Pharm. Des. 24, 5062–5071. doi: 10.2174/1381612825666190215122208
Akeila, M., Preece, C., and Kuok, K. K. K. (2021). Evaluating the environmental performance of 3D printed shelters in Jordan. J. Construct. Dev. Ctries. 26, 117–134. doi: 10.21315/jcdc2021.26.2.6
Albalawi, I. H., Khan, Z. N., Valle-Perez, A. U., Kahin, K. M., Hountondji, M., Alwazani, H., et al. (2021). Sustainable and eco-friendly coral restoration through 3D printing and fabrication. ACS Sustain. Chem. Eng. 9, 12634–12645. doi: 10.1021/acssuschemeng.1c04148
Anderson, I. (2017). Mechanical properties of specimens 3D printed with virgin and recycled polylactic acid. 3D Print. Addit. Manufact. 4, 110–115. doi: 10.1089/3dp.2016.0054
Aquino, R. P., Barile, S., Grasso, A., and Saviano, M. (2018). Envisioning smart and sustainable healthcare: 3D printing technologies for personalized medication. Futures 103, 35–50. doi: 10.1016/j.futures.2018.03.002
Arai, M., Muramatsu, T., Ito, K., Izumi, T., and Yokota, H. (2023). Three-dimensional numerical simulation of repairing process by laser direct energy deposition. J. Therm. Spray Technol. 32, 111–123. doi: 10.1007/s11666-022-01499-6
Arefin, A. M. E., Khatri, N. R., Kulkarni, N., and Egan, P. F. (2021). Polymer 3D printing review: materials, process, and design strategies for medical applications. Polymers 13. doi: 10.3390/polym13091499
Asempapa, R. S., and Love, T. S. (2021). Teaching math modeling through 3D-printing: Examining the influence of an integrative professional development. Sch. Sci. Math. 121, 85–95. doi: 10.1111/ssm.12448
Attaran, M. (2017). The rise of 3-D printing: the advantages of additive manufacturing over traditional manufacturing. Bus. Horiz. 60, 677–688. doi: 10.1016/j.bushor.2017.05.011
Aydin, A., Demirtas, Z., Ok, M., Erkus, H., Cebi, G., Uysal, E., et al. (2021). 3D printing in the battle against COVID-19. Emerg. Mater. 4, 363–386. doi: 10.1007/s42247-021-00164-y
Azad, M. A., Olawuni, D., Kimbell, G., Badruddoza, A. Z. M., Hossain, M. S., and Sultana, T. (2020). Polymers for extrusion-based 3D printing of pharmaceuticals: a holistic materials–process perspective. Pharmaceutics 12. doi: 10.3390/pharmaceutics12020124
Backstrom, I., and Bengtsson, L. (2020). Play, print, and share: 3D printing enthusiasts as user innovators and entrepreneurs. Int. J. Entrepr. Vent. 12, 648–664. doi: 10.1504/IJEV.2020.112237
Baechler, C., DeVuono, M., and Pearce, J. (2013). Distributed recycling of waste polymer into reprap feedstock. Rapid Prototyp. J. 19, 118–125. doi: 10.1108/13552541311302978
Barber, S. R., Kozin, E. D., Dedmon, M., Lin, B. M., Lee, K., Sinha, S., et al. (2016). 3D-printed pediatric endoscopic ear surgery simulator for surgical training. Int. J. Pediatr. Otorhinolaryngol. 90, 113–118. doi: 10.1016/j.ijporl.2016.08.027
Barber, S. R., Kozin, E. D., Naunheim, M. R., Sethi, R., Remenschneider, A. K., and Deschler, D. G. (2018). 3D-printed tracheoesophageal puncture and prosthesis placement simulator. Am. J. Otolaryngol. 39, 37–40. doi: 10.1016/j.amjoto.2017.08.001
Beloshenko, V., Plavan, V., Rezanova, N., Savchenko, B., and Vozniak, I. (2019). Production of high-performance multi-layer fine-fibrous filter material by application of material extrusion-based additive manufacturing. Int. J. Adv. Manuf. Technol. 101, 2681–2688. doi: 10.1007/s00170-018-3152-x
Ben-Ner, A., Urtasun, A., and Taska, B. (2019). “Tasks and skill in additive versus traditional manufacturing: a first look at evidence from job vacancies,” in SIOE 2021, 1–40.
Berman, O., Weizman, M., Oren, A., Neri, R., Parnas, H., Shashar, N., et al. (2023). Design and application of a novel 3D printing method for bio-inspired artificial reefs. Ecol. Eng. 188. doi: 10.1016/j.ecoleng.2023.106892
Bermúdez-Agudelo, M. C., Hampe, M., Reiber, T., and Abele, E. (2020). Investigation of porous metal-based 3D-printed anode gdls for tubular high temperature proton exchange membrane fuel cells. Materials 13, 2096. doi: 10.3390/ma13092096
Bharti, N. and Singh, S. (2020). COVID-19: The use of 3D printing to address PPE shortage during a pandemic-a safety perspective. ACS Chem. Health Saf. 27, 335–340. doi: 10.1021/acs.chas.0c00089
Bishop, E. G. and Leigh, S. J. (2020). Using large-scale additive manufacturing (LSAM) as a bridge manufacturing process in response to shortages in PPE during the COVID-19 outbreak. Int. Bioprint. 6, 281. doi: 10.18063/ijb.v6i4.281
Buchanan, C. and Gardner, L. (2019). Metal 3D printing in construction: a review of methods, research, applications, opportunities and challenges. Eng. Struct. 180, 332–348. doi: 10.1016/j.engstruct.2018.11.045
Calignano, F., Tommasi, T., Manfredi, D., and Chiolerio, A. (2015). Additive manufacturing of a microbial fuel cell – a detailed study. Sci. Rep. 5, 17373–17373. doi: 10.1038/srep17373
Carstensen, T., Walter-Herrmann, J., and Büching, C. (2014). “Gendered fab labs,” in Fab Lab: of Machines, Makers and Inventors, eds J. Walter-Herrmann and C. Büching, Transcript Verlag, 53–64.
Celik, H. K., Kose, O., Ulmeanu, M.-E., Rennie, A. E. W., Abram, T. N., and Akinci, I. (2020). Design and additive manufacturing of medical face shield for healthcare workers battling coronavirus (COVID-19 ). Int. J. Bioprint. 6, 30–50. doi: 10.18063/ijb.v6i4.286
Chen, L., Debono, D., and Hemsley, B. (2022). A bite closer: using 3D food printing to achieve sustainable development goals 2, 3, 9 and 17. Int. J. Speech Lang. Pathol. 25, 58–61. doi: 10.1080/17549507.2022.2132290
Chen, P.-C., Lin, J.-C., Chiang, C.-H., Chen, Y.-C., Chen, J.-E., and Liu, W.-H. (2020). Engineering additive manufacturing and molding techniques to create lifelike willis' circle simulators with aneurysms for training neurosurgeons. Polymers 12. doi: 10.3390/polym12122901
Chen, Z., Li, Z., Li, J., Liu, C., Lao, C., Fu, Y., et al. (2019). 3D printing of ceramics: a review. J. Eur. Ceram. Soc. 39, 661–687. doi: 10.1016/j.jeurceramsoc.2018.11.013
Corsini, L., Aranda-Jan, C. B., and Moultrie, J. (2020). The impact of 3D printing on the humanitarian supply chain. Prod. Plann. Control 0, 1–13. doi: 10.1080/09537287.2020.1834130
Culmone, C., Smit, G., and Breedveld, P. (2019). Additive manufacturing of medical instruments: a state-of-the-art review. Addit. Manuf. 27, 461–473. doi: 10.1016/j.addma.2019.03.015
Dada, M., Popoola, P., and Mathe, N. (2020). Laser Additive Manufacturing of Nanomaterials for Solar Thermal Energy Storage Applications, Chapter 62. Cham: Springer International Publishing, 1–16.
De Filippi, P. and Troxler, P. (2016). From Material Scarcity to Artificial Abundance: The Case of FabLabs and 3D Printing Technologies, Chapter 1. The Hague: T.M.C. Asser Press, 65–83.
de Mattos Nascimento, D. L., Nepomuceno, R. M., Gusmao Caiado, R. G., Manuel Maqueira, J., Moyano-Fuentes, J., and Garza-Reyes, J. A. (2022). A sustainable circular 3D printing model for recycling metal scrap in the automotive industry. J. Manuf. Technol. Manag. 33, 876–892. doi: 10.1108/JMTM-10-2021-0391
Dertinger, S., Gallup, N., Tanikella, N. G., Grasso, M., Vahid, S., Foot, P. J., et al. (2020). Technical pathways for distributed recycling of polymer composites for distributed manufacturing: windshield wiper blades. Resour. Conserv. Recycl. 157, 104810. doi: 10.1016/j.resconrec.2020.104810
Despeisse, M., Baumers, M., Brown, P., Charnley, F., Ford, S., Garmulewicz, A., et al. (2017). Unlocking value for a circular economy through 3D printing: a research agenda. Technol. Forecast. Soc. Change 115, 75–84. doi: 10.1016/j.techfore.2016.09.021
Ding, C.-Y., Yi, X.-H., Jiang, C.-Z., Xu, H., Yan, X.-R., Zhang, Y.-L., et al. (2019). Development and validation of a multi-color model using 3-dimensional printing technology for endoscopic endonasal surgical training. Am. J. Transl. Res. 11, 1040–1048.
Dommati, H., Ray, S., chang Wang, J., and Chen, S. (2019). A comprehensive review of recent developments in 3D printing technique for ceramic membrane fabrication for water purification. RSC Adv. 9, 16869–16883. doi: 10.1039/C9RA00872A
Down, M., Martínez-Periñán, E., Foster, C. W., Lorenzo, E., Smith, G., and Banks, C. (2019). Next-generation additive manufacturing of complete standalone sodium-ion energy storage architectures. Adv. Energy Mater. 9, 1803019. doi: 10.1002/aenm.201803019
Durão, L. F. C. S., Christ, A., Anderl, R., Schützer, K., and Zancul, E. (2016). Distributed manufacturing of spare parts based on additive manufacturing: use cases and technical aspects. Proc. CIRP 57, 704–709. doi: 10.1016/j.procir.2016.11.122
Enabling the Future (2019). About Us. Enabling the Future Website. Available online at: http://enablingthefuture.org/about/ (accessed January 12, 2021).
FabFoundationUK (2016). What is a Fablab? FabFoundation UK Website. Available online at: http://www.fabfoundationuk.org/what-is-a-fablab/ (accessed January 12, 2021).
Feeley, S., Wijnen, B., and Pearce, J. (2014). Evaluation of potential fair trade standards for an ethical 3-D printing filament. J. Sustain. Dev. 7, 1. doi: 10.5539/jsd.v7n5p1
Fillat-Goma, F., Coderch-Navarro, S., Martinez-Carreres, L., Monill-Raya, N., Nadal-Mir, T., Lalmolda, C., et al. (2020). Integrated 3D printing solution to mitigate shortages of airway consumables and personal protective equipment during the COVID-19 pandemic. BMC Health Serv. Res. 20. doi: 10.1186/s12913-020-05891-2
Ford, S. and Despeisse, M. (2016). Additive manufacturing and sustainability: an exploratory study of the advantages and challenges. J. Clean. Prod. 137, 1573–1587. doi: 10.1016/j.jclepro.2016.04.150
Ford, S. and Minshall, T. (2019). Invited review article: where and how 3D printing is used in teaching and education. Addit. Manuf. 25, 131–150. doi: 10.1016/j.addma.2018.10.028
Fratello, V. S. and Rael, R. (2020). Innovating materials for large scale additive manufacturing: salt, soil, cement and chardonnay. Cement Conc. Res. 134, 106097. doi: 10.1016/j.cemconres.2020.106097
Freeman R. and McMahon, C. (2020). “The potential role of re-distributed manufacturing in improving industrial sustainability,” in Encyclopedia of Renewable and Sustainable Materials, eds S. Hashmi, and I. A. Choudhury (Oxford: Elsevier), 451–457.
Gallup, N., Bow, J. K., and Pearce, J. (2018). Economic potential for distributed manufacturing of adaptive aids for arthritis patients in the U.S. Geriatrics 3. doi: 10.3390/geriatrics3040089
Gao, N. and Hou, H. (2018). Sound absorption characteristic of micro-helix metamaterial by 3D printing. Theoret. Appl. Mech. Lett. 8, 63–67. doi: 10.1016/j.taml.2018.02.001
Ge, R., Humbert, G., Martínez, R., Attallah, M., and Sciacovelli, A. (2020). Additive manufacturing of a topology-optimised multi-tube energy storage device: experimental tests and numerical analysis. Appl. Therm. Eng. 180, 115878. doi: 10.1016/j.applthermaleng.2020.115878
Gebhardt, A., Kessler, J. C., and Thurn, L. (2018). Basics of 3D printing technology. 3D Print. doi: 10.3139/9781569907030.001
Gebler, M., Schoot Uiterkamp, A. J., and Visser, C. (2014). A global sustainability perspective on 3D printing technologies. Energy Policy 74, 158–167. doi: 10.1016/j.enpol.2014.08.033
Gebremedhin, Z., Spillane, C., and Murray, U. (2015). Labour Saving Technology to Empower Women Smallholder Farmers. CCAFS Website. Available online at: https://ccafs.cgiar.org/news/labour-saving-technology-empower-women-smallholder-farmers (accessed January 3, 2021).
Gherardini, F., Petruccioli, A., Dalpadulo, E., Bettelli, V., Mascia, M. T., and Leali, F. (2020). “A methodological approach for the design of inclusive assistive devices by integrating co-design and additive manufacturing technologies,” in Intelligent Human Systems Integration 2020, eds T. Ahram, W. Karwowski, A. Vergnano, F. Leali and R. Taiar, Vol. 1131 (Cham: Springer), 816–822.
Gomes, B. D. A., Queiroz, F. L. C., Pereira, P. L. D. O., Barbosa, T. V., Tramontana, M. B., Afonso, F. A. C., et al. (2020). In-house three-dimensional printing workflow for face shield during COVID-19 pandemic. J. Craniofac. Surg. 31, E652–E653. doi: 10.1097/SCS.0000000000006723
Gregory, M., Hameedaldeen, S. A., Intumu, L. M., Spakousky, J. J., Toms, J. B., and Steenhuis, H. J. (2016). “3D printing and disaster shelter costs,” in 2016 Portland International Conference on Management of Engineering and Technology (PICMET) (Honolulu), 712–720.
Guild, M., Rothko, M., Sieck, C. F., Rohde, C., and Orris, G. J. (2018). 3D printed sound absorbers using functionally-graded sonic crystals. J. Acoust. Soc. Am. 143, 1714–1714. doi: 10.1121/1.5035582
Gummert, M., Mueller, J., Munder, S., and Meissner, K. (2019). Project Report for Small Scale 3-D Printing. Innovative Technology to Improve Farmer Livelihoods With 3-D Printing: The Future of Agricultural Machinery Servicing. Hohenheim: Technical Report, University of Hohenheim.
Guttridge, C., O'Sullivan, A., O'Sullivan, K. J., and O'Sullivan, L. W. (2021). Three-dimensional printed devices for health care in response to the coronavirus disease 2019: lessons learned to date. 3D Print. Addit. Manuf. 8, 340–342. doi: 10.1089/3dp.2020.0266
Guvener, O., Eyidogan, A., Oto, C., and Huri, P. Y. (2021). Novel additive manufacturing applications for communicable disease prevention and control: focus on recent COVID-19 pandemic. Emerg. Mater. 4, 351–361. doi: 10.1007/s42247-021-00172-y
Gwamuri, J., Franco, D., Khan, K., Gauchia, L., and Pearce, J. (2016). High-efficiency solar-powered 3-D printers for sustainable development. Machines 4. doi: 10.3390/machines4010003
Haberman, M. and Guild, M. (2016). Acoustic metamaterials. Phys. Today 69, 42–48. doi: 10.1063/PT.3.3198
Haleem, A. and Javaid, M. (2020). 3D printed medical parts with different materials using additive manufacturing. Clin. Epidemiol. Global Health 8, 215–223. doi: 10.1016/j.cegh.2019.08.002
Heidar Esfehani, H. (2020). Simulation-Based Study and Analysis of the Wind Power Integration Using Heat Pump and Thermal Energy Storage (PhD thesis). TU Berlin, Berlin. Available online at: https://depositonce.tu-berlin.de/bitstream/11303/10622/4/heidar_esfehani_hamidreza.pdf (accessed January 12, 2023).
Hong, W., Liu, Y., He, B., Huang, S., Chen, Z., Liao, Z., et al. (2021). Assessment of a 3D printed simulator of a lateral ventricular puncture in interns' surgical training. Br. J. Neurosurg. 35, 597–602. doi: 10.1080/02688697.2021.1922608
Hopkinson, N., Hague, R., and Dickens, P. (2006). Rapid Manufacturing: An Industrial Revolution for the Digital Age. John Wiley & Sons.
Huang, R., Riddle, M. E., Graziano, D. J., Das, S., Nimbalkar, S. U., Cresko, J., et al. (2017). Environmental and economic implications of distributed additive manufacturing: the case of injection mold tooling. Wiley Blackwell. 21, S130–S143. doi: 10.1111/jiec.12641
Huber, T. (2022). Gender Equity in Scientific Authorships - Designing a Tool for Counting Female Authors Cited in Bibliographies. Technical Report, Technical University Berlin. Available online at: https://www.appropedia.org/Gender_Equity_in_Scientific_Authorships_-_Designing_a_Tool_for_Counting_Female_Authors_Cited_in_Bibliographies (accessed February 17, 2023).
Ibrahim, N., Jovic, T., Jessop, Z. M., and Whitaker, I. S. (2021). Innovation in a time of crisis: a systematic review of three-dimensional printing in the COVID-19 pandemic. 3D Print. Addit. Manuf. 8, 201–215. doi: 10.1089/3dp.2020.0258
Ishengoma, F. R. and Mtaho, A. B. (2014). 3D printing: developing countries perspectives. arxiv. 104, 30–34. doi: 10.5120/18249-9329
Issac, M. N. and Kandasubramanian, B. (2020). Review of manufacturing three-dimensional-printed membranes for water treatment. Environ. Sci. Pollut. Res. 27, 36091–36108. doi: 10.1007/s11356-020-09452-2
James, E. and Gilman, D. (2015). Shrinking the Supply Chain: Hyperlocal Manufacturing and 3D Printing in Humanitarian Response. Occasional Policy Paper 14, United Nations Office for the Coordination of Humanitarian Affairs (OCHA). Available online at: https://www.unocha.org/publication/policy-briefs-studies/shrinking-supply-chain-hyperlocal-manufacturing-and-3d-printing (accessed January 12,2023).
James, E. and James, L. (2016). 3D printing humanitarian supplies in the field. Human. Exch. 66, 43–45. Available online at: https://odihpn.org/publication/3d-printing-humanitarian-supplies-in-the-field/ (accessed January 9, 2023).
Jamieson, C. D., Brennan, M. C., Spurgeon, T. J., Brown, S. W., Keist, J. S., and Reutzel, E. W. (2022). Tailoring alloy 718 laser directed energy deposition process strategies for repair applications. J. Laser Appl. 34. doi: 10.2351/7.0000534
Jamróz, W., Szafraniec, J., Kurek, M., and Jachowicz, R. (2018). 3D printing in pharmaceutical and medical applications—recent achievements and challenges. Pharm. Res. 35. doi: 10.1007/s11095-018-2454-x
Jang, I. and Kelsall, G. H. (2022). Fabrication of 3D nio-ysz structures for enhanced performance of solid oxide fuel cells and electrolysers. Electrochem. Commun. 137, 107260 doi: 10.1016/j.elecom.2022.107260
Jia, K., Zheng, L., Liu, W., Zhang, J., Yu, F., Meng, X., et al. (2022). A new and simple way to prepare monolithic solid oxide fuel cell stack by stereolithography 3D printing technology using 8 mol% yttria stabilized zirconia photocurable slurry. J. Eur. Ceram. Soc. 42, 4275–4285. doi: 10.1016/j.jeurceramsoc.2022.03.060
Jiang, R., Kleer, R., and Piller, F. T. (2017). Predicting the future of additive manufacturing: a delphi study on economic and societal implications of 3D printing for 2030. Technol. Forecast. Soc. Change 117, 84–97. doi: 10.1016/j.techfore.2017.01.006
Johansson, A., Kisch, P., and Mirata, M. (2005). Distributed economies—a new engine for innovation. J. Clean. Prod. 13, 971–979. doi: 10.1016/j.jclepro.2004.12.015
Jones, K. and Mendez, J. D. (2021). Enhancing learning with 3D print technology: a case study of problem based learning. J. Educ. Bus. 96, 187–194. doi: 10.1080/08832323.2020.1774735
Kane, S. and Bigham, J. (2014). “Tracking @stemxcomet: teaching programming to blind students via 3D printing, crisis management, and twitter,” in Proceedings of the 45th ACM Technical Symposium on Computer Science Education, SIGCSE '14 (Atlanta: ACM), 247–252.
Kaszynska, M., Skibicki, S., and Hoffmann, M. (2020). 3D concrete printing for sustainable construction. Energies 13. doi: 10.3390/en13236351
Katz, D. E. (2019). Plastic bank: launching social plastic®revolution. Field Act. Sci. Rep. 19, 96–99. Available online at: http://journals.openedition.org/factsreports/5478 (accessed 12 January 2023).
Kianian, B., Tavassoli, S., and Larsson, T. (2015). The role of additive manufacturing technology in job creation: an exploratory case study of suppliers of additive manufacturing in sweden. Proc. CIRP 26, 93–98. doi: 10.1016/j.procir.2014.07.109
Kieslinger, B., Schaefer, T., Fabian, C. M., Biasin, E., Bassi, E., Freire, R. R., et al. (2021). Covid-19 response from global makers: the careables cases of global design and local production. Front. Sociol. 6, 45. doi: 10.3389/fsoc.2021.629587
Kim, K., Ratri, M. C., Choe, G., Nam, M., Cho, D., and Shin, K. (2020). Three-dimensional, printed water-filtration system for economical, on-site arsenic removal. PLoS ONE 15, e0231475. doi: 10.1371/journal.pone.0231475
King, D., Babasola, A., Rozario, J., and Pearce, J. (2014). Mobile open-source solar-powered 3-D printers for distributed manufacturing in off-grid communities. Challeng. Sustain. 2, 18–27. doi: 10.12924/cis2014.02010018
König, R., Spaggiari, M., Santoliquido, O., Principi, P., and an Alberto Ortona, G. B. (2020). Micropollutant adsorption from water with engineered porous ceramic architectures produced by additive manufacturing and coated with natural zeolite. J. Clean. Prod. 258, 120500. doi: 10.1016/j.jclepro.2020.120500
Koslow, T. (2016). Myanmar farmers utilize makerbot 3D printers to create their own tools. 3DPrint.com Website. Available online at: https://3dprint.com/149881/myanmar-makerbot-farming/ (accessed 13 Aug 2022).
Kostakis, V., Niaros, V., and Giotitsas, C. (2015). Open source 3D printing as a means of learning: an educational experiment in two high schools in greece. Telemat. Inf. 32, 118–128. doi: 10.1016/j.tele.2014.05.001
Kreiger, M. A., and Pearce, J. (2013). Environmental impacts of distributed manufacturing from 3-D printing of polymer components and products. MRS Proc. 1492, 85–90. doi: 10.1557/opl.2013.319
Kristensen, H. and Mosgaard, M. (2020). A review of micro level indicators for a circular economy—moving away from the three dimensions of sustainability? J. Clean. Prod. 243, 118531. doi: 10.1016/j.jclepro.2019.118531
Kromoser, B., Reichenbach, S., Hellmayr, R., Myna, R., and Wimmer, R. (2022). Circular economy in wood construction - additive manufacturing of fully recyclable walls made from renewables: proof of concept and preliminary data. Construct. Build. Mater. 344. doi: 10.1016/j.conbuildmat.2022.128219
Kumar S. and Lee, H. P. (2019). The present and future role of acoustic metamaterials for architectural and urban noise mitigations. Acoustics 1, 590–607. doi: 10.3390/acoustics1030035
Levin L. and Verner, I. (2021). Student practice in 3D design and printing for promoting analytical and applied mathematical thinking skills. Int. J. Eng. Pedag. 11, 39–53. doi: 10.3991/ijep.v11i3.19893
Li, C., Pisignano, D., Zhao, Y., and Xue, J. (2020). Advances in medical applications of additive manufacturing. Engineering 6, 1222–1231. doi: 10.1016/j.eng.2020.02.018
Li, L., Zhang, X., and Liou, F. (2021). Experimental and numerical investigation in directed energy deposition for component repair. Materials 14. doi: 10.3390/ma14061409
Li, S., Tan, Y., Willis, S., Bahshwan, M., Folkes, J., Kalossaka, L., et al. (2021). Toward mass customization through additive manufacturing: an automated design pipeline for respiratory protective equipment validated against 205 faces. Int. J. Bioprint. 7, 123–134. doi: 10.18063/ijb.v7i4.417
Li, Y., Gao, T., Yang, Z., Chen, C., Luo, W., Song, J., et al. (2017). 3D-printed, all-in-one evaporator for high-efficiency solar steam generation under 1 sun illumination. Adv. Mater. 29, 26. doi: 10.1002/adma.201700981
Licci, M., Thieringer, F. M., Guzman, R., and Soleman, J. (2020). Development and validation of a synthetic 3D-printed simulator for training in neuroendoscopic ventricular lesion removal. Neurosurg. Focus 48. doi: 10.3171/2019.12.FOCUS19841
Lin, K.-Y., Lu, S.-C., Hsiao, H.-H., Kao, C.-P., and Williams, P. J. (2021). Developing student imagination and career interest through a stem project using 3D printing with repetitive modeling. Interact. Learn. Environ. 1–15. doi: 10.1080/10494820.2021.1913607
Little, H. A., Tanikella, N. G., Reich, M. J., Fiedler, M., Snabes, S. L., and Pearce, J. (2020). Towards distributed recycling with additive manufacturing of pet flake feedstocks. Materials 13. doi: 10.3390/ma13194273
Longhitano, G. A., Nunes, G. B., Candido, G., and da Silva, J. V. L. (2021). The role of 3D printing during COVID-19 pandemic: a review. Progr Addit. Manuf. 6, 19–37. doi: 10.1007/s40964-020-00159-x
Luukkonen, T., Yliniemi, J., Sreenivasan, H., Ohenoja, K., Finnila, M., Franchin, G., et al. (2020). Ag- or Cu-modified geopolymer filters for water treatment manufactured by 3D printing, direct foaming, or granulation. Sci. Rep. 10. doi: 10.1038/s41598-020-64228-5
Mägi, P., Krumme, A., and Pohlak, M. (2016). Recycling of pa-12 in additive manufacturing and the improvement of its mechanical properties. Key Eng. Mater. 674, 14–19. doi: 10.4028/www.scientific.net/KEM.674.9
Mathew, E., Gilmore, B. F., Larraneta, E., and Lamprou, D. A. (2021). Antimicrobial 3D printed objects in the fight against pandemics. 3D Print. Addit. Manuf. 8, 79–86. doi: 10.1089/3dp.2020.0267
Mathew, E., Pitzanti, G., Larrañeta, E., and Lamprou, D. (2020). 3D printing of pharmaceuticals and drug delivery devices. Pharmaceutics 12. doi: 10.3390/pharmaceutics12030266
Miró, L., Gasia, J., and Cabeza, L. F. (2016). Thermal energy storage (tes) for industrial waste heat (iwh) recovery: a review. Appl. Energy 179, 284–301. doi: 10.1016/j.apenergy.2016.06.147
Mohammed, M. I., Das, A., Gomez-Kervin, E., Wilson, D., and Gibson, I. (2017). “Ecoprinting: investigating the use of 100% recycled acrylonitrile butadiene styrene (abs) for additive manufacturing,” in Proceedings of the 28th Annual International Solid Freeform Fabrication Symposium—An Additive Manufacturing Conference, Solid Freeform Fabrication 2017 (Austin), 532–542.
Mohammed, M. I., Wilson, D., Gomez-Kervin, E., Rosson, L., and Long, J. (2018a). “Ecoprinting: investigation of solar powered plastic recycling and additive manufacturing for enhanced waste management and sustainable manufacturing,” in 2018 IEEE Conference on Technologies for Sustainability (SusTech) (Piscataway, NJ), 1–6.
Mohammed, M. I., Wilson, D., Gomez-Kervin, E., Vidler, C., Rosson, L., and Long, J. (2018b). The recycling of e-waste abs plastics by melt extrusion and 3D printing using solar powered devices as a transformative tool for humanitarian aid. Solid Freeform Fabr. 80–92. Available online at: https://repository.lboro.ac.uk/articles/conference_contribution/Ecoprinting_investigating_the_use_of_100_recycled_acrylonitrile_butadiene_styrene_ABS_for_additive_manufacturing/12627581 (accessed January 9, 2023).
Monkovic, J. M., Jones, S. M., Nicolas, M., Katyal, P., Punia, K., Noland, D., et al. (2021). From concept to reality: the use and impact of 3D prints as academic tools for high school biology education. J. Biol. Educ. 56, 528–539. doi: 10.1080/00219266.2020.1858927
Monnet, W., Carroll, J. R., and Embery, P. D. (2018). Using solar thermal collectors for plastic recycling in additive manufacturing. UKH J. Sci. Eng. 2, 43–47. doi: 10.25079/ukhjse.v2n1y2018.pp43-47
Moon, H., Miljković, N., and King, W. (2020). High power density thermal energy storage using additively manufactured heat exchangers and phase change material. Int. J. Heat Mass Transf. 153, 119591. doi: 10.1016/j.ijheatmasstransfer.2020.119591
Mrazović, N., Baumers, M., Hague, R., and Fischer, M. (2018). Guiding building professionals in selecting additive manufacturing technologies to produce building components. Mater. Today Commun. 15, 199–202. doi: 10.1016/j.mtcomm.2018.02.012
Murr, A. T., Lumley, C. J., Feins, R. H., and Hackman, T. G. (2021). Evaluation of a 3D-printed transoral robotic surgery simulator utilizing artificial tissue. Laryngoscope. 132, 1588–1593. doi: 10.1002/lary.29981
Murr, L. E. (2018). A metallographic review of 3D printing/additive manufacturing of metal and alloy products and components. Metallogr. Microstruct. Anal. 7, 103–132. doi: 10.1007/s13632-018-0433-6
Nagarajan, H., Raman, A., and Haapala, K. R. (2018). A sustainability assessment framework for dynamic cloud-based distributed manufacturing. Proc. CIRP 69, 136–141. doi: 10.1016/j.procir.2017.11.120
Nehme, S. and Abeidi, A. (2022). 3D concrete printing: review. Epitoanyag 74, 183–187. doi: 10.14382/epitoanyag-jsbcm.2022.27
Neumüller, M., Reichinger, A., Rist, F., and Kern, C. (2014). “3D printing for cultural heritage: preservation, accessibility, research and education,” in 3D Research Challenges in Cultural Heritage, eds I. Marinos and Q. Ewald (Berlin: Springer-Verlag), 119–134.
Novak, E., Brannon, M., Librea-Carden, M. R., and Haas, A. L. (2021). A systematic review of empirical research on learning with 3D printing technology. J. Comp. Assist. Learn. 37, 1455–1478. doi: 10.1111/jcal.12585
Novak E. and Wisdom, S. (2020). Using 3D Printing in Science for Elementary Teachers, Chapter 45. Cham: Springer International Publishing, 729–739.
NUI Galway (2017). About 3d4agdev. 3D4AgDev. Available online at: http://3d4agdev.org/about (accessed January 3, 2021).
Olsson, A., Hellsing, M. S., and Rennie, A. (2017). New possibilities using additive manufacturing with materials that are difficult to process and with complex structures. Phys. Scrip. 92, 053002. doi: 10.1088/1402-4896/aa694e
Ong, T. K., Choo, H. L., Choo, W. J., Koay, S. C., and Pang, M. M. (2020). “Recycling of polylactic acid (pla) wastes from 3D printing laboratory,” in Advances in Manufacturing Engineering, Lecture Notes in Mechanical Engineering, eds F. Chaari, F. Gherardini V. Ivanov and M, Haddar (Singapore: Springer), 725–732.
Oren, A., Berman, O., Neri, R., Tarazi, E., Parnas, H., Lotan, O., et al. (2023). Three-dimensional-printed coral-like structures as a habitat for reef fish. J. Mar. Sci. Eng. 11. doi: 10.3390/jmse11040882
Pang, Y., Cao, Y., Chu, Y., Liu, M., Snyder, K., MacKenzie, D., et al. (2020). Additive manufacturing of batteries. Adv. Funct. Mater. 30, 1906244. doi: 10.1002/adfm.201906244
Pavlo, S., Fabio, C., Hakim, B., and Mauricio, C. (2018). “3D-printing based distributed plastic recycling: a conceptual model for closed-loop supply chain design,” in 2018 IEEE International Conference on Engineering, Technology and Innovation (ICE/ITMC), 1–8.
Pearce, J. (2015). Applications of open source 3-D printing on small farms. Org. Farm. 1, 19–35. doi: 10.12924/of2015.01010019
Pearce, J., Blair, C. M., Laciak, K. J., Andrews, R., Nosrat, A. H., and Zelenika-Zovko, I. (2010). 3-D printing of open source appropriate technologies for self-directed sustainable development. J. Sustain. Dev. 3, 17. doi: 10.5539/jsd.v3n4p17
Pearson, H. A. and Dube, A. K. (2022). 3D printing as an educational technology: theoretical perspectives, learning outcomes, and recommendations for practice. Educ. Inf. Technol. 27, 3037–3064. doi: 10.1007/s10639-021-10733-7
Pérez-Pérez, M., Gómez, E., and Sebastián, M. A. (2018). Delphi prospection on additive manufacturing in 2030: implications for education and employment in spain. Materials 11. doi: 10.3390/ma11091500
Pilz, T. L., Nunes, B., Maceno, M. M. C., Cleto, M. G., and Seleme, R. (2020). Systematic analysis of comparative studies between additive and conventional manufacturing focusing on the environmental performance of logistics operations. Gestão Produção 27. doi: 10.1590/0104-530x5289-20
Pinger, C., Geiger, M., and Spence, D. (2020). Applications of 3D-printing for improving chemistry education. J. Chem. Educ. 97, 112–117. doi: 10.1021/acs.jchemed.9b00588
Ponis, S., Aretoulaki, E., Maroutas, T. N., Plakas, G., and Dimogiorgi, K. (2021). A systematic literature review on additive manufacturing in the context of circular economy. Sustainability 13. doi: 10.3390/su13116007
Projeto de Extensão Mao3D (2020). Historia. Mao 3D Website. Available online at: https://www.mao3d.com.br/historiamao3d (accessed January 30, 2023).
Raeymaekers, B., Leang, K. K., Porfiri, M., and Xu, S. (2021). Manufacturing for the masses: a novel concept for consumer 3D printer networks in the context of crisis relief. Adv. Intell. Syst. 3, 12. doi: 10.1002/aisy.202100121
Rendeki, S., Nagy, B., Bene, M., Pentek, A., Toth, L., Szanto, Z., et al. (2020). An overview on personal protective equipment (PPE) fabricated with additive manufacturing technologies in the era of COVID-19 pandemic. Polymers 12. doi: 10.3390/polym12112703
Ribeiro, D., Cimino, S. R., Mayo, A. L., Ratto, M., and Hitzig, S. L. (2021). 3D printing and amputation: a scoping review. Disabil. Rehabil. Assist. Technol. 16, 221–240. doi: 10.1080/17483107.2019.1646825
Richards, D. J., Tan, Y., Jia, J., Yao, H., and Mei, Y. (2013). 3D printing for tissue engineering. Israel J. Chem. 53, 805–814. doi: 10.1002/ijch.201300086
Rocha, V. G., García-Tuñón, E., Botas, C., Markoulidis, F., Feilden, E., D'Elia, E., et al. (2017). Multimaterial 3D printing of graphene-based electrodes for electrochemical energy storage using thermoresponsive inks. ACS Appl. Mater. Interf. 9, 37136–37145. doi: 10.1021/acsami.7b10285
Rodríguez-Espíndola, O., Chowdhury, S., Beltagui, A., and Albores, P. (2020). The potential of emergent disruptive technologies for humanitarian supply chains: the integration of blockchain, artificial intelligence and 3D printing. Int. J. Prod. Res. 58, 4610–4630. doi: 10.1080/00207543.2020.1761565
Romani, A., Rognoli, V., and Levi, M. (2021). Design, materials, and extrusion-based additive manufacturing in circular economy contexts: from waste to new products. Sustainability 13. doi: 10.3390/su13137269
Ryan, J. R., Almefty, K. K., Nakaji, P., and Frakes, D. H. (2016). Cerebral aneurysm clipping surgery simulation using patient-specific 3D printing and silicone casting. World Neurosurg. 88, 175–181. doi: 10.1016/j.wneu.2015.12.102
Saboori, A., Aversa, A., Marchese, G., Biamino, S., Lombardi, M., and Fino, P. (2019). Application of directed energy deposition-based additive manufacturing in repair. Appl. Sci. 9. doi: 10.3390/app9163316
Samonte, M. J., Laurente, E. D., Magno, K. M., and Perez, C. (2019). Braille3d: using haptic and voice feedback for braille recognition and 3D printing for the blind. IOP Conf. Ser. 482, 012027. doi: 10.1088/1757-899X/482/1/012027
Sanchez, F. A. C., Boudaoud, H., Camargo, M., and Pearce, J. M. (2020). Plastic recycling in additive manufacturing: a systematic literature review and opportunities for the circular economy. J. Clean. Prod. 264. doi: 10.1016/j.jclepro.2020.121602
Sanchez, F. A. C., Boudaoud, H., Hoppe, S., and Camargo, M. (2017). Polymer recycling in an open-source additive manufacturing context: mechanical issues. Addit. Manuf. 17, 87–105. doi: 10.1016/j.addma.2017.05.013
Sapkota, P., Brockbank, P., and Aguey-Zinsou, K.-F. (2022). 3D printing to enable self-breathing fuel cells. 3D Print. Addit. Manufact. doi: 10.1089/3dp.2021.0303
Saripalle, S., Bush, A., and Lundman, N. (2016).“3D printing for disaster preparedness: making life-saving supplies on-site, on-demand, on-time,” in 2016 IEEE Global Humanitarian Technology Conference (GHTC), 205–208.
Sauerwein, M., Doubrovski, E., Balkenende, R., and Bakker, C. (2019). Exploring the potential of additive manufacturing for product design in a circular economy. J. Clean. Prod. 226, 1138–1149. doi: 10.1016/j.jclepro.2019.04.108
Savonen, B. L., Mahan, T., Curtis, M. W., Schreier, J. W., Gershenson, J. K., and Pearce, J. (2018). Development of a resilient 3-D printer for humanitarian crisis response. Technologies 6. doi: 10.3390/technologies6010030
Schroeder, P., Anggraeni, K., and Weber, U. (2019). The relevance of circular economy practices to the sustainable development goals. J. Ind. Ecol. 23, 77–95. doi: 10.1111/jiec.12732
Sculpteo (2021). The State of 3D Printing, 2021 Edn. Available online at: https://www.sculpteo.com/de/ebooks/state-of-3d-printing-report-2021/ (accessed January 16, 2022).
See A. R. and Advincula, W. D. (2021). Creating tactile educational materials for the visually impaired and blind students using ai cloud computing. Appl. Sci. 11. doi: 10.3390/app11167552
Shcheglov, B. O., Galkina, V. I, Lembikov, A. O., Shchelkanov, E. M., Baranchugov, I. A., et al. (2020). Rhinolaryngological simulators based on 3D printing open up new opportunities for professional training. Yakut Med. J. 60–63. doi: 10.25789/YMJ.2020.71.16
Sheikh, A., Abourehab, M. A. S., and Kesharwani, P. (2023). The clinical significance of 4d printing. Drug Discov. Today 28, 103391. doi: 10.1016/j.drudis.2022.103391
Sherborne C. and Claeyssens, F. (2021). Considerations using additive manufacture of emulsion inks to produce respiratory protective filters against viral respiratory tract infections such as the COVID-19 virus. Int. J. Bioprint. 7, 47–65. doi: 10.18063/ijb.v7i1.316
Singh, R., Singh, H., Farina, I., Colangelo, F., and Fraternali, F. (2019). On the additive manufacturing of an energy storage device from recycled material. Comp. Part B Eng. 156, 259–265. doi: 10.1016/j.compositesb.2018.08.080
Singh, S. N., Venkatesh, V. S. S., and Deoghare, A. B. (2021). A review on the role of 3D printing in the fight against COVID-19: safety and challenges. Rapid Prototyp. J. 27, 407–420. doi: 10.1108/RPJ-08-2020-0198
Singhal I. and Balaji, B. S. (2020). Creating atom representations using open-source, stackable 3D printed interlocking pieces with tactile features to support chemical equation writing for sighted and visually impaired students. J. Chem. Educ. 97, 118–124. doi: 10.1021/acs.jchemed.9b00255
Sinha, M. S., Bourgeois, F. T., and Sorger, P. K. (2020). Personal protective equipment for COVID-19: distributed fabrication and additive manufacturing. Am. J. Public Health 110, 1162–1164. doi: 10.2105/AJPH.2020.305753
South, B. J., Fey, N. P., Bosker, G., and Neptune, R. R. (2010). Manufacture of energy storage and return prosthetic feet using selective laser sintering. J. Biomech. Eng. Transact. Asme 132. doi: 10.1115/1.4000166
Spake, C. S. L., Carruthers, T. N., Crozier, J. W., Kalliainen, L. K., Bhatt, R. A., Schmidt, S. T., et al. (2021). 3D printed N-95 masks during the COVID-19 pandemic: lessons learned. Ann. Biomed. Eng. 49, 3666–3675. doi: 10.1007/s10439-021-02859-z
Srinivasan, R., Giannikas, V., McFarlane, D., and Thorne, A. (2018). Customising with 3D printing: the role of intelligent control. Comp. Ind. 103, 38–46. doi: 10.1016/j.compind.2018.09.003
Sterman, Y., Tarazi, E., Berman, O., Gur, Y., Parnas, H., Tareef, R., et al. (2021). Safety on demand: a case study for the design and manufacturing-on-demand of personal protective equipment for healthcare workers during the COVID-19 pandemic. Saf. Sci. 136. doi: 10.1016/j.ssci.2021.105162
Sun, C., Wang, Y., McMurtrey, M. D., Jerred, N. D., Liou, F., and Li, J. (2021). Additive manufacturing for energy: a review. Appl. Energy 282. doi: 10.1016/j.apenergy.2020.116041
Tai, X. Y., Zhakeyev, A., Wang, H., Jiao, K., Zhang, H., and Xuan, J. (2019). Accelerating fuel cell development with additive manufacturing technologies: state of the art, opportunities and challenges. Fuel Cells 19, 636–650. doi: 10.1002/fuce.201900164
Tanney, D., Meisel, N., and Moore, J. (2020). “Investigating material degradation through the recycling of pla in additively manufactured parts,” in Proceedings of the 28th Annual International Solid Freeform Fabrication Symposium—An Additive Manufacturing Conference, Solid Freeform Fabrication 2017, 519–531.
Tarancon, A., Esposito, V., Torrell, M., Di Vece, M., Son, J. S., Norby, P., et al. (2022). 2022 roadmap on 3D printing for energy. J. Phys. Energy 4. doi: 10.1088/2515-7655/ac483d
Tarfaoui, M., Nachtane, M., Goda, I., Qureshi, Y., and Benyahia, H. (2020). 3D printing to support the shortage in personal protective equipment caused by COVID-19 pandemic. Materials 13. doi: 10.3390/ma13153339
Tatham, P., Loy, J., and Peretti, U. (2015). Three dimensional printing—a key tool for the humanitarian logistician? J. Human. Logist. Supply Chain Manag. 5, 188–208. doi: 10.1108/JHLSCM-01-2014-0006
Team UnLimbited (2019). Our Story. Team UnLimbited Website. Available online at: https://www.teamunlimbited.org/about (accessed January 30, 2021).
Teoh, J. H., Mozhi, A., Sunil, V., Tay, S. M., Fuh, J., and Wang, C.-H. (2021). 3D printing personalized, photocrosslinkable hydrogel wound dressings for the treatment of thermal burns. Adv. Funct. Mater. 31. doi: 10.1002/adfm.202105932
Teoh, J. H., Tay, S. M., Fuh, J., and Wang, C.-H. (2022). Fabricating scalable, personalized wound dressings with customizable drug loadings via 3D printing. J. Controll. Release 341, 80–94. doi: 10.1016/j.jconrel.2021.11.017
Thiong'o, G. M., Bernstein, M., and Drake, J. M. (2021). 3D printing in neurosurgery education: a review. 3D Print. Med. 7. doi: 10.1186/s41205-021-00099-4
Tian, X., Jin, J., Yuan, S., Chua, C. K., Tor, S. B., and Zhou, K. (2017). Emerging 3D-printed electrochemical energy storage devices: a critical review. Adv. Energy Mater. 7, 1700127. doi: 10.1002/aenm.201700127
Tijing, L. D., Dizon, J. R. C., Ibrahim, I., Nisay, A. R. N., Shon, H. K., and Advincula, R. C. (2020). 3D printing for membrane separation, desalination and water treatment. Appl. Mater. Today 18, 100486. doi: 10.1016/j.apmt.2019.100486
Tipe 3D Printing (2021). A Word From the Founder. Available online at: https://www.tipe3dprinting.com/ (accessed January 30, 2021).
Tönissen D. D. and Schlicher, L. (2021). Using 3D-printing in disaster response: the two-stage stochastic 3D-printing knapsack problem. Comp. Operat. Res. 133, 105356. doi: 10.1016/j.cor.2021.105356
Trenfield, S. J., Awad, A., Madla, C. M., Hatton, G. B., Firth, J., Goyanes, A., et al. (2019). Shaping the future: recent advances of 3D printing in drug delivery and healthcare. Exp. Opin. Drug Deliv. 16, 1081–1094. doi: 10.1080/17425247.2019.1660318
Turner, C., Moreno, M., Mondini, L., Salonitis, K., Charnley, F., Tiwari, A., et al. (2019). Sustainable production in a circular economy: a business model for re-distributed manufacturing. Sustainability 11, 4291. doi: 10.3390/su11164291
UNESCO (2020). Global Education Monitoring Report 2020: Inclusion and education: All Means All. Paris: UNESCO.
United Nations (2015). Transforming Our Wold: The 2030 Agenda for Sustainable Development. A/RES/70/1. Available online at: https://sdgs.un.org/publications/transforming-our-world-2030-agenda-sustainable-development-17981 (accessed January 12, 2023).
United Nations (2020). The Sustainable Development Goals Report 2020. New York, NY:United Nations Department of Economic & Social Affairs.
Vaz, V. M. and Kumar, L. (2021). 3D printing as a promising tool in personalized medicine. AAPS PharmSciTech 22. doi: 10.1208/s12249-020-01905-8
Venturi, T., Turrin, M., Setaki, F., Veer, F., Pronk, A., Teuffel, P., et al. (2019). Terra–ink additive earth manufacturing for emergency architecture. J. Architect. Built Enviro. 6, 41–46. doi: 10.7480/spool.2019.2.4373
Vidakis, N., Petousis, M., Tzounis, L., Grammatikos, S., Porfyrakis, E., Maniadi, A., et al. (2021). Sustainable additive manufacturing: mechanical response of polyethylene terephthalate glycol over multiple recycling processes. Materials 14. doi: 10.3390/ma14051162
Voigt, C., Unterfrauner, E., and Stelzer, R. (2017). Diversity in fablabs: culture, role models and the gendering of making. Int. Conf. Int. Sci. 52–68. doi: 10.1007/978-3-319-70284-1_5
Vyatskikh, A., Kudo, A., Delalande, S., and Greer, J. (2018). Additive manufacturing of polymer-derived titania for one-step solar water purification. Mater. Today Commun. 15, 288–293. doi: 10.1016/j.mtcomm.2018.02.010
Wang, F., Liu, C., Yang, H., Wang, H., Zhang, H., Zeng, X., et al. (2023). 4D printing of ceramic structures. Addit. Manuf . 63. doi: 10.1016/j.addma.2023.103411
Wang, Y., Ahmed, A., Azam, A., Bing, D., Shan, Z., Zhang, Z., et al. (2021). Applications of additive manufacturing (AM) in sustainable energy generation and battle against COVID-19 pandemic: the knowledge evolution of 3D printing. J. Manuf. Syst. 60, 709–733. doi: 10.1016/j.jmsy.2021.07.023
Wang, Z., Liao, X., Wang, X., Bai, Y., Huang, H., Shen, K., et al. (2021). Converting complex sewage containing oil, silt, and bacteria into clean water by a 3D printed multiscale and multifunctional filter. ACS Appl. Bio Mater. 4, 8509–8521. doi: 10.1021/acsabm.1c01004
Weinstock, P., Rehder, R., Prabhu, S. P., Forbes, P. W., Roussin, C. J., and Cohen, A. R. (2017). Creation of a novel simulator for minimally invasive neurosurgery: fusion of 3D printing and special effects. J. Neurosurg. Pediatr. 20, 1–9. doi: 10.3171/2017.1.PEDS16568
Wierzbicki, J., Nowacki, M., Chrzanowska, M., Matkowski, R., Zietek, M., Nowacka, K., et al. (2020). Additive manufacturing technologies enabling rapid and interventional production of protective face shields and masks during the COVID-19 pandemic. Adv. Clin. Exp. Med. 29, 1021–1028. doi: 10.17219/acem/126296
Willemsen, D. (2015). Designing Haptic Graphics for Mathematics: Towards Accessible Math Education for Blind Students (Master thesis). TU Delft, Delft.
Willer, H., Lernoud, J., and Kemper, L. (2019). “The world of organic agriculture 2019: summary,” in The World of Organic Agriculture: Statistics and Emerging Trends 2019, eds C. H. Frick, and D. Bonn [Research Institute of Organic Agriculture (FiBL) and IFOAM—Organics International], 25–34.
Wilts, E. and Long, T. (2020). Sustainable additive manufacturing: predicting binder jettability of water-soluble, biodegradable, and recyclable polymers. Polym. Int. 70, 958–963. doi: 10.1002/pi.6108
Woern, A. L., Byard, D. J., Oakley, R. B., Fiedler, M. J., Snabes, S. L., and Pearce, J. (2018). Fused particle fabrication 3-d printing: recycled materials' optimization and mechanical properties. Materials 11, 1413. doi: 10.3390/ma11081413
Women in 3D Printing (2020a). About Us. Women in 3D Printing Website. Available online at: https://womenin3dprinting.com/about-us/ (accessed January 30, 2021).
Women in 3D Printing (2020b). Frequently Asked Questions. Women in 3D Printing Website. Available online at: https://womenin3dprinting.com/faq/ (accessed May 30, 2023).
Woodson, T., Alcantara, J. T., and do Nascimento, M. S. (2019). Is 3D printing an inclusive innovation? An examination of 3D printing in brazil. Technovation 80–81, 54–62. doi: 10.1016/j.technovation.2018.12.001
Yang, W., Bai, X., Zhu, W., Kiran, R., An, J., Chua, C., et al. (2020). 3D printing of polymeric multi-layer micro-perforated panels for tunable wideband sound absorption. Polymers 12. doi: 10.3390/polym12020360
You, J., Fan, H., Winfield, J., and Ieropoulos, I. A. (2020). Complete microbial fuel cell fabrication using additive layer manufacturing. Molecules 25, 3051. doi: 10.3390/molecules25133051
Yu, A. W. and Khan, M. (2015). On-demand three-dimensional printing of surgical supplies in conflict zones. J. Trauma Acute Care Surg. 78, 201–203. doi: 10.1097/TA.0000000000000481
Zadpoor, A. A. and Malda, J. (2016). Additive manufacturing of biomaterials, tissues, and organs. Ann. Biomed. Eng. 45, 1–11. doi: 10.1007/s10439-016-1719-y
Zarrabeitia-Bilbao, E., Meaza, I. Á., Río-Belver, R. M., and Anacabe, G. G. (2019). Additive manufacturing technologies for biomedical engineering applications: research trends and scientific impact. Prof. Inf. 28, 9. doi: 10.3145/epi.2019.mar.20
Zhang, P. C., Ahmed, Y., Hussein, I. M., Afenu, E., Feasson, M., and Daud, A. (2020). Optimization of community-led 3D printing for the production of protective face shields. 3D Print. Med. 6. doi: 10.1186/s41205-020-00089-y
Zhang, R., Jiang, F., Xue, L., and Yu, J. (2022). Review of additive manufacturing techniques for large-scale metal functionally graded materials. Crystals 12. doi: 10.3390/cryst12060858
Zhang, Y., Qin, B., Chan, K., Lupoi, R., Yin, S., Xie, Y., et al. (2023). Enhancement on mechanical properties of cocrni medium entropy alloy via cold spray additive manufacturing associated with sintering. J. Manuf. Process. 94, 413–423. doi: 10.1016/j.jmapro.2023.03.017
Zheng, X., Williams, C., Spadaccini, C. M., and Shea, K. (2021). Perspectives on multi-material additive manufacturing. J. Mater. Res. 36, 3549–3557. doi: 10.1557/s43578-021-00388-y
Zhou, L.-Y., Fu, J., and He, Y. (2020). A review of 3D printing technologies for soft polymer materials. Adv. Funct. Mater. 30. doi: 10.1002/adfm.202000187
Zou, B., Wang, L., Zhang, Y., Liu, Y., Ouyang, Q., Jin, S., et al. (2023). Enhanced strength and ductility of metal composites with intragranularly dispersed reinforcements by additive manufacturing. Mater. Res. Lett. 11, 360–366. doi: 10.1080/21663831.2022.2153630
Keywords: Additive Manufacturing, 3D printing (3DP), sustainability, Sustainable Development Goals (SDGs), sustainable development
Citation: Muth J, Klunker A and Völlmecke C (2023) Putting 3D printing to good use—Additive Manufacturing and the Sustainable Development Goals. Front. Sustain. 4:1196228. doi: 10.3389/frsus.2023.1196228
Received: 18 April 2023; Accepted: 22 June 2023;
Published: 07 July 2023.
Edited by:
Rodrigo Lozano, University of Gävle, SwedenReviewed by:
Antti Salminen, University of Turku, FinlandAshish Ganvir, University of Turku, Finland
Copyright © 2023 Muth, Klunker and Völlmecke. This is an open-access article distributed under the terms of the Creative Commons Attribution License (CC BY). The use, distribution or reproduction in other forums is permitted, provided the original author(s) and the copyright owner(s) are credited and that the original publication in this journal is cited, in accordance with accepted academic practice. No use, distribution or reproduction is permitted which does not comply with these terms.
*Correspondence: Christina Völlmecke, Y2hyaXN0aW5hLnZvZWxsbWVja2VAdHUtYmVybGluLmRl