- Biomolecular Engineering Program, Physics, and Chemistry Department, Milwaukee School of Engineering, Milwaukee, WI, United States
Succinic acid is an industrially important commodity chemical that acts as a precursor to numerous other chemicals. This article explores an alternative biochemical route (as opposed to the traditional route from petroleum), by modeling a succinic acid production plant using Actinobacillus succinogenes, to convert the renewable sugars of corn stover feedstock. The model developed with SuperPro Designer v9.0 was used to evaluate the feasibility of this approach. This design is on par with the throughput of currentlarge scale manufacturers, by achieving an annual production rate of 11.5 US kilotons of succinic acid. The plant's economic standing is very attractive with a payback time of just under 5 years and return on investment of 20.4%. This article shows a facility design that maximizes profitability for a feasible and sustainable solution for bio-based succinic acid production.
Introduction
Succinic acid, C4H6O4, is an industrially important commodity chemical with applications in the pharmaceutical, food additive, polymer and adhesive industries. The Department of Energy expects the current global market demand of 30–50 kilotons to grow 90% annually for the next 5 years (Clark, 2014). The traditional method of producing succinic acid through hydrogenation of the petrochemical maleic acid anhydride, is nonrenewable and environmentally damaging for it can produce as much as 8.82 kg of carbon dioxide per 1 kg of succinic acid (Cok et al., 2013). This ratio is very high, so lowering it is the main goal of most bio-based production methods. The succinic acid market is also significantly affected by petroleum price fluctuations. Fortunately, succinic acid is also naturally produced in various cellular metabolism pathways and can be generated by microbial fermentation of sugars. The main drivers behind bio-based chemical production are market need supply and demand, consumer demand, environmental impact, and superior properties that allow for lower costs (Dickinson et al., 2017; Simchick et al., 2021). All of these drivers are pushing bio-based succinic acid production, but the heaviest influence is the chemical's superior properties. Succinic acid is a platform chemical and viewed as a potential replacement for 1,4-butanediol. Use of succinic acid in important applications such as paints and coatings, adhesives, sealants, food additives, biodegradable plastics, cosmetics and pharmaceuticals, supports the chance of extreme market expansion and offtake agreements amongst producers and buyers, in the coming years (Biddy, 2016).
This article explores an alternative biochemical route by modeling a succinic acid production plant using Actinobacillus succinogenes, a natural succinic acid producing rumen bacteria, to convert the renewable sugars of corn stover feedstock (McKinlay et al., 2005). Actinobacillus succinogenes is chemoorganotrophic and a facultative anaerobe that sequesters CO2 to produce succinic acid and byproducts. Under the right growth conditions, it can yield high concentrations of succinic acid (Guettler et al., 1999). There have been several studies done investigating the succinic acid production from pulp logs using biorefinery approach (Ghayur et al., 2019), and life cycle analysis of succinic acid production from bread waste (Gadkari et al., 2021) and sorghum grains (Moussa et al., 2016). Several bio-based renewable chemical companies around the globe including GC Innovation America (Myriant Technologies, LLC.) (Myriant Technologies, 2013), BioAmber Inc., and Reverdia, are taking advantage of succinic acid's properties to produce at least 10 US kilotons of succinic acid annually via fermentation with genetically modified microbes. They have been using first-generation feedstocks such as corn or sugarcane, for efficiency and elimination of extra production steps and costs. A drawback of these methods is first-generation feedstocks compete with the food industry. This study addresses that issue by evaluating the feasibility of using corn stover, a second-generation feedstock, for succinic acid production. It also assesses the feasibility of using a naturally producing microbe, Actinobacillus succinogenes, over a genetically modified species of yeast or E. coli. A unique downstream process combination of direct crystallization for recovering and purifying the final product, and power generation for operation cost savings and material recycling, encourage the claim of this unique design being feasible and sustainable for succinic acid production. This paper addresses a novel solution for sustainable bio-succinic acid production on an industrial scale.
Methodology
To evaluate this novel solution of succinic acid production from Actinobacillus succinogenes fermentation of the sugars composing corn stover feedstock, and recovery and purification using direct crystallization ideology, the entire process was modeled in SuperPro Designer v9.0. This all-in-one modeling software provided mass and energy balances for the system, along with cost and sustainability estimates.
Process description
Succinic acid production from second-generation feedstock is a complex process and requires an upstream and downstream process which are further broken down into smaller subsystems. The upstream process consists of feedstock pretreatment and fermentation, while the downstream process consists of direct crystallization and an optional power generation loop. Each of these subsystems are important to the overall process and need to work cohesively and efficiently for the production plant to meet the purity and annual production goals. Because succinic acid is commonly used in food and feed additives, our product must be considered “Generally Recognized as Safe” by the FDA (US Food Drug Administration, 2014). To be competitive in the current bio-based market, it's essential to produce at least 10 US kilotons/year of 99.5% pure product. The process flow is depicted below in Figure 1.
Feedstock pretreatment
The purpose of this subsystem is to physically disrupt and chemically degrade the large polysaccharide complexes of corn stover, so the smaller sugars of glucose and xylose are more accessible for the bacteria in the fermentation step. The corn stover enters the production plant and is first sent through a washer (P-1/WSH-101) to remove dirt particulates and pesticides from the farm fields and transportation. A succeeding clarification unit (P-1/CL-101) collects, cleans and recycles the wash water. The clean corn stover then goes through a grinder (P-2/GR-101) for size reduction, before entering the dilute acid reactor vessel (P-3/R-101). 2.8% mass composition sulfuric acid is mixed with the correct amount of corn stover for a 2% dilute acid composition in the vessel. This reaction takes place for 30 mins at 140°C, and the outlet stream goes through a microfiltration unit (P-4/MF-101) to obtain a stream solely consisting of cellulose and hemicellulose oligomers, and water (Zheng et al., 2010).
For this subsystem, it was very important to properly define corn stover composition to achieve accurate oligomer concentrations in the outlet stream. Table 1 below shows the corn stover feedstock composition utilized in the modeling. These values were taken from the study done by Shekiro et al. (2014).
It was also important to accurately model the cellulose and hemicellulose oligomers. These were defined by using the molecular weights of the repeating units and degrees of polymerization. Cellulose's repeating unit is glucose and has a degree of polymerization of 2,800 when treated with dilute acid. Hemicellulose's repeating unit is xylose and has a degree of polymerization of 20 when treated with dilute acid (Hallac and Ragauskas, 2011). These values were used to define the outlet stream of the pretreatment reactor vessel.
Fermentation
The purpose of this subsystem is to actually produce the succinic acid product via microbial fermentation of sugars. Since the cellulose and hemicellulose oligomers from the feedstock pretreatment stream are too big for the bacteria to utilize for metabolic purposes, simultaneous saccharification and fermentation (SSF) was chosen to be modeled. As cellulase enzyme breaks down the complex polysaccharides to glucose and xylose, Actinobacillus succinogenes is simultaneously metabolically converting glucose and xylose to succinic acid, acetic acid and formic acid. SSF helps with maintaining low glucose concentrations in the fermentation broth, for high concentrations of glucose can be detrimental and act as an inhibitor for the bacteria (Zhao and Xia, 2009; Li et al., 2010a,b).
Fermentation should take place for 48 h at 37°C, with the saccharification reactions occurring parallel with the fermentation reactions (Bradfield et al., 2015). Equations 1–5 below show these reactions, with (1) and (2) showing saccharification of cellulose and hemicellulose, and (3), (4) and (5) showing fermentation of glucose and xylose (succinic acid product is underlined).
Magnesium carbonate was added to the fermentor vessel as an additional reagent to maintain the required pH. It also metabolically enhances Actinobacillus succinogenes' pathways of succinic acid production for higher yields (Samuelov et al., 1991). All bacterial cells that are used for the process are grown at the production facility to help with reducing costs. Bacterial cell scale-up process was modeled, beginning with shake flasks (P-7/SFR-101), moving to 6 L fermentors (P-9/FR-101) and ending with the large 90,000 L industrial fermentor (P-8/FR-102). At the beginning of modeling, this fermentation step was a bottleneck in the process for it took the most time to complete, so equipment utilization was a key factor in efficiently designing this subsystem. In the end, “Stagger Mode” was applied to the large industrial fermentor to allow for more continuous batch processing. Our data projected 10 industrial fermenters as the optimum production scale, and this can be reviewed in the “Economic Analysis” section. Additionally, the maximum fermentation stream outlet concentration of succinic acid was set to 100 g/L which was found to be the maximum achievable product concentration with A. succinogenes (Li et al., 2010a,b; Zheng et al., 2010).
Direct crystallization
The purpose of this subsystem to recover and purify the succinic acid product to a state at which is appropriate for selling on the market. The succinic acid is a component of the fermentation broth and enters this subsystem at 99.8 g/L, along with high concentrations of unwanted components, including cell debris. To rid this, the broth passes through a bowl centrifuge (P-10/BC-102), and the remaining supernatant of water, acetic, formic, and succinic acid, and small amounts of unmetabolized glucose and xylose, is collected. This supernatant enters a crystallizer (P-15/CR-101) to recover the succinic acid. At 4°C, the crystallizer's operating temperature, succinic acid's solubility in water is dramatically decreased, while the other organic acids retain their solubility. The solubility of each compound at 25°C is shown below in Table 2 (“Acetic Acid.”, 2004; “Formic Acid.”, 2004; “Succinic Acid.”, 2004). At this reference temperature, succinic acid's solubility is 92% lower than acetic acid and formic acid. The solubility will drop even more when the temperature is lowered to 4°C, for there is less kinetic energy to break the intermolecular forces apart, that are holding the organic compounds together.
The first operation used for purifying is an activated carbon blending tank (P-11/V-102). This will remove all organic impurities from the product, like the unmetabolized glucose and xylose, through chemical adsorption. The second operation used for purifying is an ion exchange column (P-13/INX-101). Inside the column is a charged surface that ions in the process stream adhere to as it passes through, to be removed from the product. For our process, ions that should be removed during this step are those formed from the dissociation of hydrochloric acid, magnesium carbonate and sulfuric acid. SuperPro Designer v9.0 has limitations in being able to show chemical dissociation in the ionic form, so the outlet stream of this operation contains the non-dissociated chemical for modeling purposes. After this, acetic acid, formic acid, succinic acid, and water are the only components in the product stream. Again, due to its differing solubility compared to acetic and formic acid, the purified succinic acid crystals can be isolated by passing the stream through another crystallizer (P-14/CR-102) at 4°C. The crystals are then sent to a tray drier (P-16/TDR-101) to prepare them for packaging and selling (Lin et al., 2010; Cheng et al., 2012).
The mass composition value for the succinic acid crystals in the outlet stream of the tray drier was calculated as 99.7%, confirming our desired level of purity.
Power generation
This is an optional subsystem to the design, for it has no direct impact on the production, recovery, or purification of our succinic acid product. The purpose of this subsystem is to provide the facility with power and steam so it can be partially self-sustaining. This also drastically reduces the facility's environmental impact with lowering the exiting waste amounts. The large amounts of biomass and organic waste produced from the centrifuge and microfiltration unit of the upstream process, are available fuel for the steam generation operation. The needed water for this operation comes from two other process waste streams: ion exchange column and second crystallizer. Pairing the steam generator (P-20/SG-101) with a steam expansion unit (P-21/T-101) allows for the additional generation of electricity. Both the steam and the power are recycled back to the facility to accommodate a portion of the utility needs. Specifically, 21% of the annual power demand and 95% of the annual steam demand can be generated from this subsystem.
There are several benefits to the system described in the economic analysis section below, such as cost savings, waste minimization and smaller environmental impact, which persuaded the inclusion of this subsystem in the final facility design.
Economic analysis
The effects of several economic variables were assessed to evaluate the overall profitability, feasibility, and sustainability of our succinic acid production facility.
Production, profitability, and sustainability
Prior to beginning the design of our production plant, extensive research was done to understand the succinic acid market and competitors our facility would be up against if it were to be implemented. An annual production trend of 10–30 US kilotons of succinic acid was observed amongst GC Innovation America (Myriant Technologies, LLC.), BioAmber Inc., and Reverdia, influencing our annual production goal of at least 10 US kilotons. This was evaluated through SuperPro Designer v9.0's programmed calculations. Figure 2 shows a chart of the economic breakdown of the plant.
The selling price of succinic acid was set to $9.00/kg (Vasmani, 2010). Generated electricity was credited back to the facility at $0.10/kW-hr. Water and aqueous waste streams that were recycled back through the facility were credited at $11.00/1000 kg.
A sensitivity analysis was done as one component of the sustainability analysis. This predicts how specific output variables would be influenced by fluctuations in specific input variables. The input variables for this facility were price sensitivity of succinic acid, corn stover and growth media, and was graphed against the output variable of facility profits. Input variable percentage cost change was evaluated in ±0.1 increments. The effects on the facility profits were plotted and compared in Figure 3.
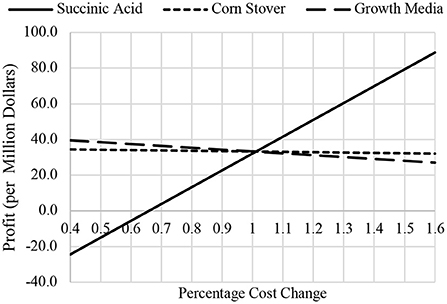
Figure 3. Sensitivity analysis for succinic acid, corn stover, and growth media price verse facility profits.
Equipment optimization
In order to ensure the best economic and production results, each component of the production process was carefully investigated. Debottlenecking the process at the fermentation stage was crucial to ensure annual succinic acid production amounts of at least 10 kilotons, with a purity of 99.5%. The optimum number of staggered industrial fermentors was determined by evaluating the production and economic data for each option. The results were graphed in Figure 4, and the respective maximum and minimums were found.
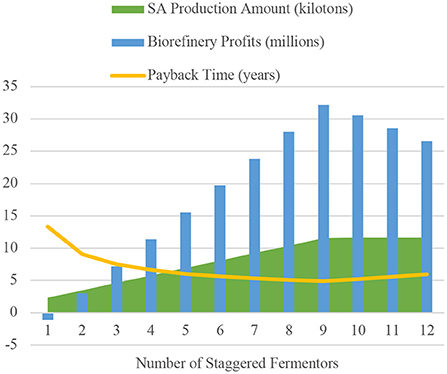
Figure 4. Analysis of “Stagger Mode” fermentor values to determine that nine vessels was the optimal choice.
Results and discussion
Intermediate and final products
The main revenue stream and desired product from the process was bio-based succinic acid, C4H6O4. The mass composition data for the product stream exiting the tray drier operation is 99.7% succinic acid crystals and 0.3% water. The flowrate of succinic acid crystals was 6,714.3 kg/batch. Based on scheduling, SuperPro Designer v9.0 calculates 1,556 batches can be processed in a year, resulting in an annual production rate of 11.5 US kilotons of succinic acid. With a CO2 sequester rate of 1,430 kg/batch from the stoichiometric ratios for production of each organic compound, this annual production rate sequesters 2,225,080 kg of CO2 per year. Both our purity and production goals for succinic acid, were exceeded with this model. The detailed composition of the main streams in this simulation is provided in Table 3.
The optional power generation subsystem allowed for the plant to partially self-sustain its utilities needs by burning 21,514.95 kg of available fuel (~50% water and ~50% organic impurities/matter such as acetic acid, formic acid, lignin, biomass, etc.), per batch, to produce 21% of the needed standard power and 95% of the steam demand. Now, 9,858,272 kW-hr/year of the total amount of electricity needed (46,332,997 kW-hr/year) and 106,000 MT steam/year of the total amount of steam needed (111,000 MT steam/year), are available to the facility, revealing the importance of this subsystem.
As stated previously, fermentation by-products of acetic acid and formic acid are also available in the fermentation broth for recovery, purification and selling. This option was explored but not included in the model due to the insufficient profitability of the processes. The costs for the equipment to perform these operations, exceeded the revenue of selling the available amount of these chemicals. A future direction of this model would be to try and find a profitable method of recovering and purifying these by-products to encourage the facility growth toward a biorefinery, but for now, the available fuel in these organic acids is put to use in the power generation subsystem.
Production, profitability, and sustainability
By using the annual succinic acid production as 11.5 US kilotons and the selling price of $9.00/kg, the overall annual revenues for the facility were calculated as $94,311,000. Annual operating costs were $66,639,000, but the savings and credits from the power generation and material recycling should be considered in this value as well. $3,517,050 was credited back to the plant and $985,827 was saved on an annual basis from the power generation. These yield a net annual operating cost value of $62,136,295. With annual revenues exceeding the net operating costs by $32,174,705 (Gross profit = Total revenues—Net annual operating cost), this facility is profitable. From the profits, SuperPro Designer v9.0 calculates the payback time (Payback time {in years} = {Total investment}/ {Net profit}) of the initial $167,395,000 total capital investment to be 4.90 years which makes this process favorable for investors. The return on investment (ROI) is 20.40% (ROI = {Net profit}/{Total investment}*100).
Figure 2 is a graphical representation of these results. The net profit provided in the plot was defined as
Net profit= Gross Profit-Taxes(40%)+ Depreciation
and calculated by SuperPro Designer.
Analysis of the sustainability of the facility was promising as well. The sensitivity analysis showed below in Figure 3, exhibits that facility profits fluctuate very little if the price of corn stover or growth were to ever drastically fluctuate. The succinic acid line has the largest slope value and since that chemical is the only revenue producing product for the facility, this does show concern for potential economic downtown. For the facility to be unprofitable, the price of succinic acid would have to drop all the way down to about $6.00/kg. We are confident this most likely will not happen for the succinic acid market forecasts of an annual 90% growth rate for the next 5 years.
Equipment optimization
“Stagger mode” in SuperPro Designer v9.0 gives the opportunity to model the process with pieces of equipment on stand-by. This mode was utilized in our process to debottleneck the fermentation step because it is the longest operation at 48 hours. The values of 1–12 staggered fermentors were tested to find the value in which annual succinic acid production and facility profits were maximized, and payback time was minimized. Figure 4 below indicates that nine staggered fermentors, for a total of 10 vessels, was the optimal design choice.
“Stagger mode” was helpful for optimizing the number of fermentors in the upstream portion of the process, whereas the equipment type, arrangement, and size, were used to optimize the downstream process. The well-chosen order of operations that the process stream goes through in the downstream portion of the process, allows for gradual volume reduction as some form of waste is collected as a by-product after each operation. gradual volume reduction in the various equipment operations This strategy saves in capital investment and operating costs. A good example of this is the tray drier (P-16/TDR-101). With less process passing through this operation due to gradual volume reduction, the piece of equipment can be much smaller and utilizes much less electricity since it doesn't need to heat up and dry as large of a material volume.
Comparison to current and competing solutions
This article presents a unique solution for producing bio-based succinic acid because of the key differences it has with the current and competing market solutions. As stated previously, there are global companies already producing bio-based succinic acid in large quantities. This solution is different from GC Innovation America (Myriant Technologies LLC's), BioAmber's and Reverdia's processes with the use of the second-generation feedstock instead of a first-generation feedstock, and a naturally producing microbe verse a modified organism. Their solution is working and has been successful in industry, but comes at a much higher cost due to those main differences.
There are other research studies currently going on to develop models of succinic acid production from various types of biomass. Bakery wastes has been proven successful as a carbon source for Actinobacillus succinogenes fermentation, to produce succinic acid (Lam et al., 2014). The developed model shows one ton of bakery waste being processed through a small pretreatment operation, 44-hour fermentation step and a resin distillation and crystallization downstream process to obtain the succinic acid product. A more extensive pretreatment operation is needed in our design since the sugars of corn stover are more difficult to access than the sugars in bakery waste. The use of simultaneous saccharification and fermentation in our unique solution, compared to just normal fermentation, allows for higher microbe conversion efficiency with lower possibilities of glucose inhibition. Our proposed design is also scaled for more than 10 kilotons of annual production, where the proposed pilot-scale bakery waste conversion facility produces about 0.03 kilotons/year, which is much less than the demand of our target market.
We believe that further research on succinic acid production would bring out more solutions to the existing problems and encourage the companies to invest more on this promising chemical production.
Additional production methods investigated
Aqueous Two-Phase System Extraction (ATPS) was also explored at the beginning, as an alternative downstream process method to Direct Crystallization, in attempts to compare the performance of two different designs. ATPS is an extensive process with several steps and pieces of equipment. It begins with mixing the fermentation broth with sulfuric acid to reduce the pH to the desirable state in which succinic acid is in its dissociative form. Acetone and ammonium sulfate are added to the acid-broth mixture, and ultimately two phases are formed. These were found to be the best organic solvent/salt combination because their chemical properties allow for the fermentation impurities to settle in the heavy ammonium sulfate lower phase, and the succinic acid product to settle in the light acetone upper phase (Gu et al., 2014). Four more unit operations are needed to act upon the light phase to recover the succinic acid at 99.5% purity, including distillation, activated carbon decolorization, crystallization and tray drying. The economic analysis of ATPS was very comparable to Direct Crystallization, for the annual production amounts and revenues were very similar. The largest drawback of using ATPS was evident in the model though; larger amounts of waste were produced because expensive equipment would be needed to recycle and reuse reagents. This supported the idea that Direct Crystallization would be a more sustainable solution for the facility.
Shifting the scope of this facility to be a biorefinery, instead of just a production plant, was also explored by examining the possibility of recovering and purifying the acetic acid and formic acid byproducts. However, it was determined that this was not a sustainable and profitable idea for the facility, for the equipment costs needed to perform these actions were higher than the revenues these chemicals would provide the facility. Table 4 below shows the small quantities of acetic acid and formic acid produced, and the selling price of these organic acids, ultimately exhibiting the very low revenues, the plant would receive from selling these compounds. The profits however would be negative for costs to sell these, are higher than the revenues.
Still in attempts of creating a biorefinery even after recovery of acetic acid and formic acid was determined as not profitable, the potential of ethanol recovery was explored. Actinobacillus succinogenes has two metabolic pathways; C4 pathway produces succinic acid and the C3 pathway produces the other by-products including ethanol. Because the two products come from two different pathways, certain environmental conditions would have to be used to encourage the bacteria to use both pathways instead having one dominate the other. Research showed that lowering the carbon dioxide levels available to the bacteria all the way down to a 6.5 stoichiometric ratio, would lower the C4 pathway enzyme activity enough to encourage the C3 pathway and ethanol production (Samuelov et al., 1991). Using this stoichiometric ratio in the SuperPro Designer v9.0 modeling equations, ethanol was being produced as a byproduct but in very small quantities. This supported the claim not to include this in our final design since it lowered the amount of succinic acid being produced by 65%, and the ethanol production portion wouldn't be profitable to the facility.
Conclusions
The goal of this design was to present a novel solution for producing bio-based succinic acid at the industrial scale. Current petroleum processes are environmentally damaging not only from the carbon dioxide emissions, but also harm from mining the feedstock. This proposed bio-based design has a lower environmental impact from sequestering carbon dioxide and not mining for fossil fuels. Current bio-based succinic acid facilities use first-generation feedstocks and genetically-modified microbes, but this design takes advantage of the energy potential of a second-generation feedstock (corn stover) and uses a naturally-occurring microorganism for fermentation.
Our proposed design has the capability of producing 11.5 US kilotons of 99.7% pure bio-based succinic acid annually. The feedstock pretreatment subsystem physically and chemically degrades the corn stover feedstock using a dilute acid method, to more readily expose the sugars for the bacteria during fermentation. Operating the fermentation mode with SSF, cellulose and hemicellulose oligomers are broken down while Actinobacillus succinogenes metabolizes the glucose and xylose products to succinic acid. SSF maintains the glucose levels so they don't become inhibitory to the system. The fermentation broth is directly acted on in the direct crystallization downstream process. A unique sequence of operations removes all waste, organic impurities and ions from the product stream, to isolate, recover and purify the succinic acid to 99.7%. The power generation subsystem takes advantage of the energy potential in the process waste to generate 21% of the facility's electricity needs and 95% of the facility's steam demands. The estimated annual operating costs are $62.13 million and estimated revenues are $94.31 million. With those healthy profits and a $167.4 million total initial capital investment, the payback time for investors is 4.90 years, making this an attractive solution for the bio-based succinic acid market, for its novelty, profitability and economic feasibility.
Data availability statement
The original contributions presented in the study are included in the article/supplementary material, further inquiries can be directed to the corresponding author.
Author contributions
All authors listed have made a substantial, direct, and intellectual contribution to the work and approved it for publication.
Funding
Milwaukee School of Engineering provided funds for the open access publication fees.
Conflict of interest
The authors declare that the research was conducted in the absence of any commercial or financial relationships that could be construed as a potential conflict of interest.
Publisher's note
All claims expressed in this article are solely those of the authors and do not necessarily represent those of their affiliated organizations, or those of the publisher, the editors and the reviewers. Any product that may be evaluated in this article, or claim that may be made by its manufacturer, is not guaranteed or endorsed by the publisher.
References
“Acetic Acid.” (2004). Data from: National Center for Biotechnology Information and PubChem Compound Database US National Library of Medicine. Available online at: https://pubchem.ncbi.nlm.nih.gov/compound/acetic_acid#section=Top (accessed July 01, 2022).
“Formic Acid.” (2004). National Center for Biotechnology Information. PubChem Compound Database, U.S. National Library of Medicine. Available online at: https://pubchem.ncbi.nlm.nih.gov/compound/formic_acid#section=Top (accessed July 01, 2022).
“Succinic Acid.” (2004). National Center for Biotechnology Information. PubChem Compound Database, U.S. National Library of Medicine. Available online at: https://pubchem.ncbi.nlm.nih.gov/compound/succinic_acid#section=Top
Biddy, M. J. (2016). “Chemicals from biomass: a market assessment of bioproducts with near-term potential,” in National Renewable Energy Laboratory. Available online at: www.nrel.gov/publications (accessed July 1, 2022).
Bradfield, M., Mohagheghi, A., Salvachua, D., Smith, H., Black, B., Dowe, N., et al. (2015). Continuous succinic acid production by Actinobacillus succinogenes on xylose-enriched hydrolysate. Biotechnol. Biofuels. 8, 181–197. doi: 10.1186/s13068-015-0363-3
Cheng, K., Zhao, X., Zeng, J., Wu, R., Xu, Y., Liu, D., et al. (2012). Downstream processing of biotechnological produced succinic acid. Appl. Microbiol. Biotechnol. 95, 841–850. doi: 10.1007/s00253-012-4214-x
Clark, S. (2014). Bio Succinic Acid Market by Application—Global Opportunity Analysis and Industry Forecast, 2013–2020. Pune: Allied Market Research.
Cok, B., Tsiropoulos, I., Roes, A., and Patel, M. (2013). Succinic acid production derived from carbohydrates: an energy and greenhouse gas assessment of a platform chemical toward a bio-based economy. Biofuels Bioproduc. Biorefin. 8, 16–29. doi: 10.1002/bbb.1427
Dickinson, S., Mientus, M., Frey, D., et al. (2017). A review of biodiesel production from microalgae. Clean Techn. Environ. Policy. 19, 637–668. doi: 10.1007/s10098-016-1309-6
Gadkari, S., Kumar, D., Qin, Z. H., Ki Lin, C. S., and Kumar, V. (2021). Life cycle analysis of fermentative production of succinic acid from bread waste. Waste Manage. 126, 861–871. doi: 10.1016/j.wasman.2021.04.013
Ghayur, A., Verheyen, T., and Meuleman, E. (2019). Techno-economic analysis of a succinic acid biorefinery coproducing acetic acid and dimethyl ether. J. Clean. Product. 230, 1165–1175. doi: 10.1016/j.jclepro.2019.05.180
Gu, B., Zheng, P., Yan, Q., and Liu, W. (2014). Aqueous two-phase system: an alternative process for recovery of succinic acid from fermentation broth. Separat. Purificat. Technol. 138, 47–54. doi: 10.1016/j.seppur.2014.09.034
Guettler, M. V., Rumler, D., and Jain, M. K. (1999). Actinobacillus succinogenes sp. nov., a novel succinic-acid-producing strain from the bovine rumen. Int. J. Systemat. Bacteriol. 49, 207–216. doi: 10.1099/00207713-49-1-207
Hallac, B. B., and Ragauskas, A. J. (2011). Analyzing cellulose degree of polymerization and its relevancy to cellulosic ethanol. Biofuels Bioproduct. Biorefin. 5, 215–225. doi: 10.1002/bbb.269
Lam, K. F., Leung, C. C. J., Lei, H. M., and Lin, C. S. K. (2014). Economic feasibility of a pilot-scale fermentative succinic acid production from bakery wastes. Food Bioproduct. Process. 92, 282–290. doi: 10.1016/j.fbp.2013.09.001
Li, J., Zheng, X. Y., Fang, X. J., Liu, S. W., Chen, K. Q., Jiang, M., et al. (2010a). A complete industrial system for economical succinic acid production by Actinobacillus succinogenes. Bioresour. Technol. 102, 6147–6152. doi: 10.1016/j.biortech.2011.02.093
Li, Q., Wang, D., Wu, Y., Li, W., Zhang, Y., Xing, J., et al. (2010b). One step recovery of succinic acid from fermentation broths by crystallization. Separat. Purificat. Technol. 72, 294–300. doi: 10.1016/j.seppur.2010.02.021
Lin, S., Du, C., Blaga, A., Camarut, M., Webb, C., Stevens, C., et al. (2010). Novel resin-based vacuum distillation-crystallization method for recovery of succinic acid crystals from fermentation broth. Green Chemistr. 12, 666–671. doi: 10.1039/b913021g
McKinlay, J. B., Zeikus, J. G., and Vieille, C. (2005). Insights into actinobacillus succinogenes fermentative metabolism in a chemically defined growth medium. Appl. Environ. Microbiol.71, 6651–6656. doi: 10.1128/AEM.71.11.6651-6656.2005
Moussa, H., Elkamel, A., and Young, S. (2016). Assessing energy performance of bio-based succinic acid production using LCA. J. Clean. Product. 139, 761–769. doi: 10.1016/j.jclepro.2016.08.104
Myriant Technologies, L. L. C. (2013). Succinic Acid and Derivatives SBU. Available online at: http://www.myriant.com/pdf/myriant-succinic-acid-customer-presentation-english.pdf (accessed July 1, 2022).
Samuelov, N. S., Lamed, R., Lowe, S., and Zeikus, J. G. (1991). Influence of CO2-HCO3 Levels and pH on Growth, Succinate Production, and Enzyme Activities of Anaerobiospirllum succiniciproducens. Appl. Environ. Microbiol. 57, 3013–3019. doi: 10.1128/aem.57.10.3013-3019.1991
Shekiro, I. I. I., Isralmj, J., Kuhn, E. M., Nagle, N. J., Tucker, M. P., Elander, R. T., et al. (2014). Characterization of pilot-scale dilute acid pretreatment performance using deacetylated corn stover. Biotechnol. Biofuels 7, 23–32. doi: 10.1186/1754-6834-7-23
Simchick, C., Zidek, B., Moder, D., Madson, D., Payne, M., Kelsey, J., et al. (2021). Techno economic analysis of the modified mixalco process. Processes 9, 958–975. doi: 10.3390/pr9060958
US Food Drug Administration (2014). Food Additive Status List. Available online at: https://www.fda.gov/food/food-additives-petitions/food-additive-status-list (accessed July 1, 2022).
Vasmani, S. (2010). Process Economics Program Review 2010-2014: Biobased Succinic Acid. SRI Consulting. Available online at: https://ihsmarkit.com/pdf/RW2010-14_220240110917062932.pdf (accessed July 1, 2022).
Zhao, J., and Xia, L. (2009). Simultaneous saccharification and fermentation of alkaline-pretreated corn stover to ethanol using recombinant yeast strain. Fuel Process. Technol. 90, 1193–1197. doi: 10.1016/j.fuproc.2009.05.018
Keywords: techno-economical assessment, facility design, SuperPro Designer, corn stover, succinic acid, bio-based chemical, renewable feedstock
Citation: Tomczyk S, Ozturk S, Wawrzyniak T, Tessman M, Ehrlich C and Shaikh F (2022) The design and techno economic analysis of a succinic acid production facility. Front. Sustain. 3:953942. doi: 10.3389/frsus.2022.953942
Received: 26 May 2022; Accepted: 13 July 2022;
Published: 16 August 2022.
Edited by:
Urmila Diwekar, Vishwamitra Research Institute, United StatesReviewed by:
Dong Xiang, Anhui University, ChinaMunawar Abdul Shaik, United Arab Emirates University, United Arab Emirates
Copyright © 2022 Tomczyk, Ozturk, Wawrzyniak, Tessman, Ehrlich and Shaikh. This is an open-access article distributed under the terms of the Creative Commons Attribution License (CC BY). The use, distribution or reproduction in other forums is permitted, provided the original author(s) and the copyright owner(s) are credited and that the original publication in this journal is cited, in accordance with accepted academic practice. No use, distribution or reproduction is permitted which does not comply with these terms.
*Correspondence: Faisal Shaikh, c2hhaWtoQG1zb2UuZWR1