- 1Textile Architecture Network, Department of Architecture, Built Environment and Construction Engineering, Polytechnic of Milan, Milan, Italy
- 2TextilesHUB–The Interdepartmental Research Laboratory on Textiles and Polymers, Polytechnic of Milan, Milan, Italy
A building information modeling (BIM)-integrated workflow for quantifying and assessing the environmental and economic impacts during the life cycle of buildings is presented and deepened in this essay. With the support of digital methods and informative building models, these impacts can be scored through the analysis of variants and their weighted comparison. Through an optimized computational code, the semiautomatic calculation can directly link the results with the visualization tools (dashboards and colored 3D models), thus accelerating—and making it more accessible—the optioneering of multiple design alternatives during the project development.
Introduction
The study describes a life cycle assessment (LCA)—life cycle costing (LCC) method for the architectural and construction industry, which addresses the impacts of building products along the entire life cycle (construction, maintenance, replacement, and demolition) and stimulates the growing global awareness on environmental and economic issues. In particular, the article deals with a dynamic method to finalize an environmental and cost assessment that can be applied during the diverse design stages (schematic design, detailed design, and construction design) of BIM architectural works.
The recent development of associative possibilities between information and digital models has opened up numerous scenarios in the use of BIM in the construction sector. The interoperability between the modeling software and the LCA analysis tools (One-Click LCA, 2022; Tally LCA, 2022) allows implementing the environmental evaluation in the various phases of the design, thus resulting in a valuable decision-making tool.
The integration of LCA analysis in BIM environment was underlined by previous studies in this field (Llatas et al., 2020). Hollberg et al. (2020), for example, proposed the link between LCA and BIM as a multiplication between the quantities of each material with the LCA factors (embodied impacts) from the database of the Swiss Association of construction and real estate bodies of the public builders—KBOB et al. (2016). Soust-Verdaguer et al. (2020) proposed it to improve the bill of quantities, automatically extracted from the BIM model, with Supplementary Data (such as auxiliary materials and transports). Shin and Cho (2015) based the LCA and LCC application in BIM on various design documents and equations to develop the calculations, which required time to avoid errors in result. Then, the more detailed structure and information are needed in the LCA application, the more difficult to conduct free-error in LCA techniques in BIM, due to a large amount of data or the difficulty in automizing the workflow. Moreover, the analysis of literature reveals the following major issues of the integration process:
1. Creating asynchronized LCA methodology that enables a clear identification of the inputs needed;
2. Developing information databases that ontologically and semantically conform to the BIM environment and that also correspond to the desired design phase of the project;
3. Creating a flawless and automated exchange of information between BIM and LCA tools that is adapted to the specific software constraints (tags, families of elements, properties, etc.), whose benefits are demonstrated by Potrč Obrecht et al. (2020);
4. Collecting data on the organizational aspects along the entire life cycle—from the production chain of products to the operational energy of the building and the final disposal of materials—as evidenced by Petti et al. (2016).
Because of these concerns, a more reliable integration of BIM and LCA would foster the optimization of the environmental performance of buildings during the design process and thereby improve the future building stock quality. An optimized integration of BIM and LCA, where the users have control, and an overview of the entire range of processes and material flows during the entire life cycle of the building, will likely lead to an improved design process, as well as generating replicable and trustworthy LCA results.
In order to describe the interoperable workflow, a case study—a digital mock-up of an office building—explains the method starting from a level of detail of the digital model equal to a level of development—LOD C (detailed design) according to Ente Nazionale Italiano di Unificazione—UNI 11337:2017 (2017). The method is resumed as follows:
1. Identification of geometric and information design framework through the writing of asset information requirements (AIRs)—according to the European (EN) and International (ISO) Standardization EN ISO 19650-1:2018—that define the project info to collect during the design stages (EN ISO 19650-1:2018, 2018).
2. Life cycle assessment (LCA) and life cycle costing (LCC) of the BIM models as valuable decision tools to be used during the different design stages.
For the LCA–LCC analysis, diverse technological and material variations are evaluated through a dynamic dashboard and a colored visualization in Autodesk Revit (2022). The methodology complies with both the LCA—(EN ISO 14040:2006, 2006; EN ISO 14044:2006, 2006; UNI EN 15978:2011, 2011; ISO 21930:2017, 2017; ISO 21931:2019, 2019; EN 15804:2022-03, 2022)—and LCC international standards—(ISO 15686-5:2017, 2017). The assessments consider the entire life cycle of the analyzed building (“cradle-to-grave”), including production, maintenance, replacement of the material, and any end of life. The input–output population from/to the BIM model has been automatized through the development of codes in Autodesk Dynamo (Dynamo BIM, 2022).
The structure of the dashboard permits also weighing differently the key performance indicators (global warming potential, radioactivity, product and transportation cost, maintenance and replacement cost, end-of-life cost) according to the project requirements. This peculiarity simplifies the assessment of multiple design variations, for both the environmental (incorporated energy and indoor pollution) and economic (construction costs and operational and maintenance costs) points of views.
Method: Experimental test on a digital mock-up
Although the BIM objects can be used as data storage of any type of technical information about the corresponding construction element, the bill of materials' quantities is still considered one of the most relevant means for quickly coupling BIM- and LCA-based techniques (Soust-Verdaguer et al., 2017); in fact, together with the finding of a proper building material LCA database, the data extraction represents a time-consuming process, especially in the case of complex buildings (Hollberg et al., 2020). In order to obtain a wider overview of the building elements than a simple quantity take-off, the improvement in an asset information requirement (AIR) allows us to list the design properties to be populated into the BIM model. In the AIR, the geometric and informative properties are ordered by disciplines (architectural, structural, mechanical) and type of work (civil and infrastructural works) and explained through Property-set (P-set) to compile during the model authoring of each of the design stages: schematic design, detailed design, and construction design (Figure 1). Specifically, the list of selected parameters follows the guidelines of the Standard UNI 11337-3-4 (UNI 11337:2015, 2015; UNI 11337:2017, 2017) regarding the technical specifications (levels of geometry and information) that the digital representation of building products has to achieve within the BIM model at the different scales of the design process (from LOD A to G).
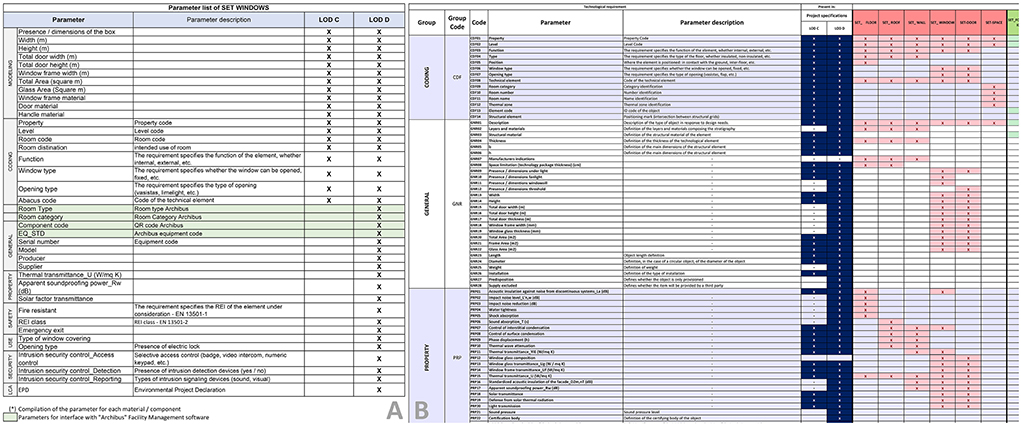
Figure 1. Asset information requirements (AIRs) used to define an input dataset for LCA–LCC analysis: Parameter list of the set “Windows and Curtain Walls” (A); extract from the matrix that identifies the parameters per Revit families and permits the direct link with the .dyn code (B).
Once identified the information requirements that are necessary to create a larger overview of the analyzing design, the work focuses on the development of a dashboard template in .xls format that categorizes the analysis histograms per multiple indexes, in order to simplify any return of information to the designers and BIM coordinators of the project. The dashboard also makes it possible to compare different design options (e.g., between different materials and/or technological solutions).
Both sheets—AIR and dashboard—are then linked to the Autodesk Dynamo canvas. This allows the development of a .dyn code that simultaneously calculates the environmental and economic indicators for each technological unit of the digital mock-up. The organizational scheme of the Dynamo script is divided into the following five main bodies (Figure 2):
A. The first is focusing on the integration of the necessary parameters in specific Property-set (P-set) into the Revit model, which would then assist in the calculation and data extraction parts that are taking place in the next bodies.
B. The second solves the data population of the info obtained from the AIR, which can be compiled by designers and suppliers directly in .xls format, to the Revit model.
C. The third deals with the LCA calculation, through a code that facilitates the data filtering from the P-sets of the Revit families and makes it faster the data transfer from/to the cloud platform of One-Click LCA through its Revit Add-on.
D. The following one calculates the cost estimation through the direct link with the cost estimation sheet of the project; this part of the code also includes the formula to calculate the radioactivity of materials according to the European directives.
E. The last .dyn block is focused on the population of the final LCA–LCC values into the Revit model (using the P-set created initially) and on the parallel data extraction into a .xls dashboard.
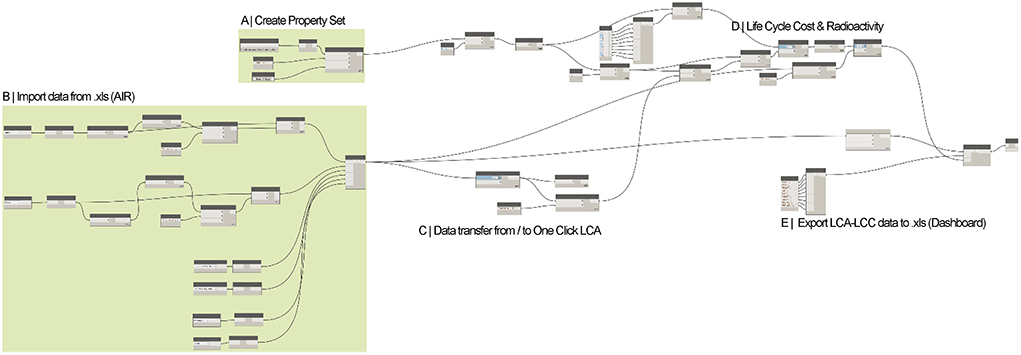
Figure 2. Screenshot of the main blocks of the code created with the visual programming tool Dynamo.
The values obtained from the LCA–LCC calculation can be used to set different design variations by simply modifying the parameters of Revit families. The experimentation makes it possible to systematize evaluations of an environmental nature (LCA analysis and indoor pollution) and economic (LCC analysis), which can be weighed differently in a final summary graph. The methodology is experimentally applied to a significant portion of the digital model of a new office building located in Rome. The mock-up consists in an open-space office with a facing bioclimatic greenhouse for a net area of around 600 m2. The BIM models of the architectural (ARC) and structural (STR) disciplines—both representative of a level of geometric and informative development equal to a LOD C—allow extracting quantities and combining them with a set of technical specifications for the building elements and materials that were collected in advance in a test sample of precompiled AIR (Figure 3).
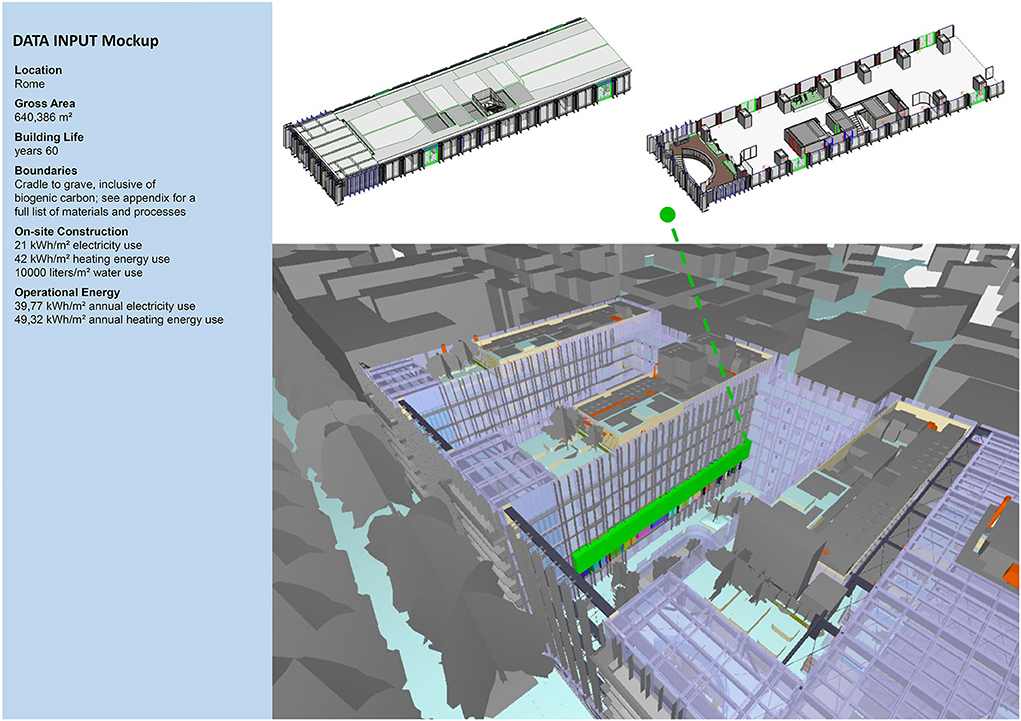
Figure 3. Overview of the digital mock-up (LOD C) of an office space that has been analyzed within this experimental work.
The coding implementation in Dynamo assigns a new P-set to all the Revit families involved in the analysis (windows, doors, stairs, facade elements, and struts as well as ceilings from the ARC model; structural elements such as columns and girders from the STR file). First, all component-specific materials and different Revit properties, such as component name, area, volume, and quantity, are summarized, and then, they are queried and transferred into the new P-set. These pieces of info are then merged with the data coming from the AIR, such as the final material assignment, product overviews, environmental product declaration (EPD) data, and the predicted service life and energy requirement. The collection of the known boundary conditions, as well as the pre-defined information on the observation period, relevant life cycle phases, and transport definitions, can be adapted or modified simply overwriting the info after a rapid compatibility checking set directly in Dynamo.
Life cycle assessment
The term “life cycle” describes the whole existence of products, from resource extraction through manufacturing, use, and disposal (Nieuwlaar, 2013). Consequently, the LCA methodology refers to a technique for assessing how materials affect the environment over the course of their entire life cycle (EN ISO 14044:2006, 2006; Monticelli, 2006). The methodology is structured in four steps: In the first step, the goal and scope, the functional unit for the comparison, and the procedure for incorporating environmental data into decision making are described (Nieuwlaar, 2013). Then, data will be collected in the life cycle inventory (LCI) step. This dataset contains not only a list of all inflows and outflows involving various individual supply chain unit procedures but also environmental impacts and energy consumption during the production of products from raw materials (Pagnon et al., 2020). Moreover, LCI contains numerical data based on reference units (Nieuwlaar, 2013). The goal and scope determine how much life cycle data and phases can be included in LCI (Nieuwlaar, 2013). According to the numerical data coming from LCI, the potential environmental impacts originating from the elementary flows will be assessed in the life cycle impact assessment (LCIA) step (Nieuwlaar, 2013). The life cycle interpretation will be a conclusion of the obtained data in different steps of LCA, which can provide some recommendations (Monticelli, 2006, 2007; Nieuwlaar, 2013) for the architects.
Following the above-described method, in this study, the authors use the info collected in the AIR as a way for covering and comparing more technical data—not only the quantity take-off—and guaranteeing a correct LCI allocation to the Revit objects. For example, this can be the minimum compressive strength class for concrete, the tree species or material type for wood, or the type and processing of metals. The sensible data—transferred to the new Revit P-set created for each object—are exported through .xls to the cloud platform of One-Click LCA (2022), in which every individual Revit element can be referenced to the ÖKOBAUDAT Platform (2002); then, the obtained LCI can be adapted or supplemented with the values of density and transport, the combination of composite materials, the eventual assignment of data from an EPD, the service life, and operational energy. Through the .dyn code that operates a geometrical and technical checking in order to examine that the right materials have been mapped in Revit material library, the One-Click LCA platform is ready to be automatically compiled and run.
Radioactivity rate of materials
The study also intends to analyze the amounts—small but not negligible—of natural radioactivity present in building materials, due to the radioisotopes uranium (U-238), thorium (Th-232), and potassium (K-40) in variable quantity concentrations depending on the type and origin. By way of example, some sorts of granite and tuffs can sometimes record sensitive concentrations of radioisotopes, while in marbles radioactivity is rarely present in significant quantities. Radioactivity can be present in other materials, such as various types of sand used for porcelain stoneware or some particular cements. These (possible) contributions therefore contribute to the dose of radioactivity of natural origin materials (Kang et al., 2020).
At the European level, the Directive 2013/59/EURATOM was published in 2013 to harmonize the various regulations in force in the Member States (Council Directive 2013/59/EURATOM, 2013). The directive states that any radiation emissions from building materials must not constitute a risk to the health of the occupants of the building and/or that of the neighbors, but this (generic) principle has not had, up to now, a clear application due to the failure to set limit values for these emissions at European level. The European Committee for Standardization (CEN), to which the European Commission has given the mandate for the drafting of future regulations on radioactivity in construction materials, intends to proceed according to the criteria and principles set out in the guidelines issued by European Commission (1999).
The European Directive 2013/59/EURATOM defines the basic safety standards for the health of workers and the public in general against the danger deriving from ionizing radiation. The asset concentration index should only be used as a screening tool to identify materials that may be of concern. The purpose of the controls is to limit the highest individual doses. The directive establishes the different limit values of index I, which correspond to increases in effective gamma dose to individuals of 0.3 and 1 mSv/y, depending on the dose limit to be respected (for the population and for workers, respectively) and the type of use that is made of the building material, i.e., as a structural or cladding material. If, for example, building materials are used as cladding materials, when the index I is lower than 2, they can be considered exempt from any type of restriction, while if it is higher than 6, they should not be used except in exceptional cases and locally. If the index is between these values, the material may be subject to restrictions regarding its use, however, based on specific dose assessments (European Commission, 1999).
The Directive 2013/59/EURATOM also provides indications regarding the internal exposure of the population, due to the inhalation of radon, proposing to include in the design phase specific and control measures that guarantee a maximum threshold of radon concentration in new buildings equal to 200 Bq/m3 (=10 mSv), while for those existing at European level it is recommended an intervention threshold of 400 Bq/m3 (=20 mSv). Ra, Th, and K are the activity concentrations of uranium, thorium, and potassium (Bq kg−1), respectively, in the building material. The activity concentration index must not exceed the value of 0.5 according to the dose criterion (0.3 mSv ∧ a−1) allowing for surface materials with limited use, for example, tiles and panels (Council Directive 2013/59/EURATOM, 2013). The activity concentration index is expressed by the following formula (I = activity concentration index; Ra-226 = concentration of uranium activity; Th-232 = concentration of thorium activity; K-40 = concentration of potassium activity).
Life cycle costing
The Standard ISO 15686-5:201 defines the life cycle costing as “cost of an asset, or its parts throughout its life cycle, while fulfilling the performance requirements” (ISO 15686-5:2017, 2017). Generally, it is a technique to calculate the overall cost of a project from construction, use, and deconstruction (Manewa et al., 2021). According to Korpi and Ala-Risku (2008), LCC can deliver 70%−90% cost confidence for operational expenditure (OPex) in the design phase, allowing for the comparison of different design options (Manewa et al., 2021), reducing potential risks, and predicting project success (Boussabaine and Kirkham, 2004). Despite the method's many benefits, its application is restricted due to a lack of data uniformity, client awareness, and methodology (Manewa et al., 2021).
This phase of the research analyzes the overall cost of the entire life cycle of the mock-up of the building. The need to know more about the costs of construction and technological management derives from the need to satisfy an ever-increasing desire of the customer to evaluate the economic consequences of using a building or making an investment in the real estate sector.
The developed methodology makes it possible to compare the costs of supply and processing of materials and technological components associated with the portion of the building analyzed (as detailed in the estimated metric calculation) to the costs that can be projected for the entire useful life of the building (estimated in 60 years). In order to prepare a fairly reliable calculation tool, during the life cycle of the building the expenses of scheduled maintenance are considered replacements whenever a material or component has a nominal life span lower than the estimated life of the building and inflation equal to 1% per year (in line with the Italian annual average). The study refers to the following basic equation (Land of Buildings, 2005):
where C is the year 0 construction cost (hard and soft costs); PVRECURRING is the present value of all recurring costs (utilities, maintenance, replacements, service, etc.), also considering the annual escalation rate of the various types of goods and services; and PVRESIDUALVALUE represents the residual value at the end of the study life (set to 0 in that study).
According to studies (Land of Buildings, 2005; Santos et al., 2019), the basic equation has been expressed to directly link with the data input coming from the AIR. The formula considers the construction, maintenance, and decommissioning costs of products included in the analyzed mock-up (LCC = life cycle cost; Ci = procurement and construction cost; Co = operation cost; Cm = maintenance and/or replacement cost; d = discount rate; N = no. of years of the study period; and r = annual inflation).
The adaptation makes it possible to directly use the data coming from the official project documents shared by the designers: The procurement and construction costs are based on price lists including the costs of the entire production phase, including the transport and the final assembly. The data are directly linked from the AIR to the Revit objects that are present in the ARC and STR models of the mock-up. The analysis also counts the transport from the manufacturer to the construction site during the construction phase, according to the distances defined for the LCA analysis, and the energy costs for the construction phases, calculated on the basis of the consumption estimated in the environmental assessment phase.
The maintenance and replacement costs of construction products are calculated in accordance with their expected life span, as automatically assigned by One-Click LCA, or alternatively as declared by the manufacturer. This includes the transportation of replacement products to the site. With reference to operational costs, the calculation is based on the expected maintenance activities that are periodically scheduled during the life of an office building.
Once the service life is ended, the economic analysis includes the costs related to the end-of-life treatment of existing products: material recycling costs, incineration costs, and landfill disposal costs. The analysis is based on material-type unitary price list, such as plastic waste, biodegradable or compostable waste, and inert material. The unitary prices also consider the potential economic returns due to energy and material recycle or reuse, which can be finalized at the end of the product's life. For example, the incineration of materials includes a lump sum credit for energy recovery, as well as the recycling of raw materials.
Results and discussion
The results are directly shown as data lists in the Revit Add-on for the whole mock-up by means of the .dyn code. The script also organizes the data—obtained from the software cloud in .xls format—into the dashboard template and groups them per Revit categories, materials and life cycle stages: production (A1–A3), transport (A4), construction (A5), maintenance and replacement (B2–B5), operational energy (B6), and end-of-life (C2–C4). The calculation considers the potential for reuse that exceeds the limit of the system (D), such as energy recovery and recycled materials (i.e., for the wooden elements).
Focusing on the results of the interior partitions and finishes, the histograms show that, of the five lifecycle stages, the production stage has the greatest negative impact on the environment of each material. Metals and fluoropolymer coating have the most harmful impact on the environment with a global warming potential (GWP) performance equal to 40% of the total impact (Figure 4). Following the design requirements of the de-constructability of the technological systems, the recyclable materials are modeled using an avoided load approach where the primary material production burden is assigned to the next life cycle based on the amount of secondary materials recovered (module D).
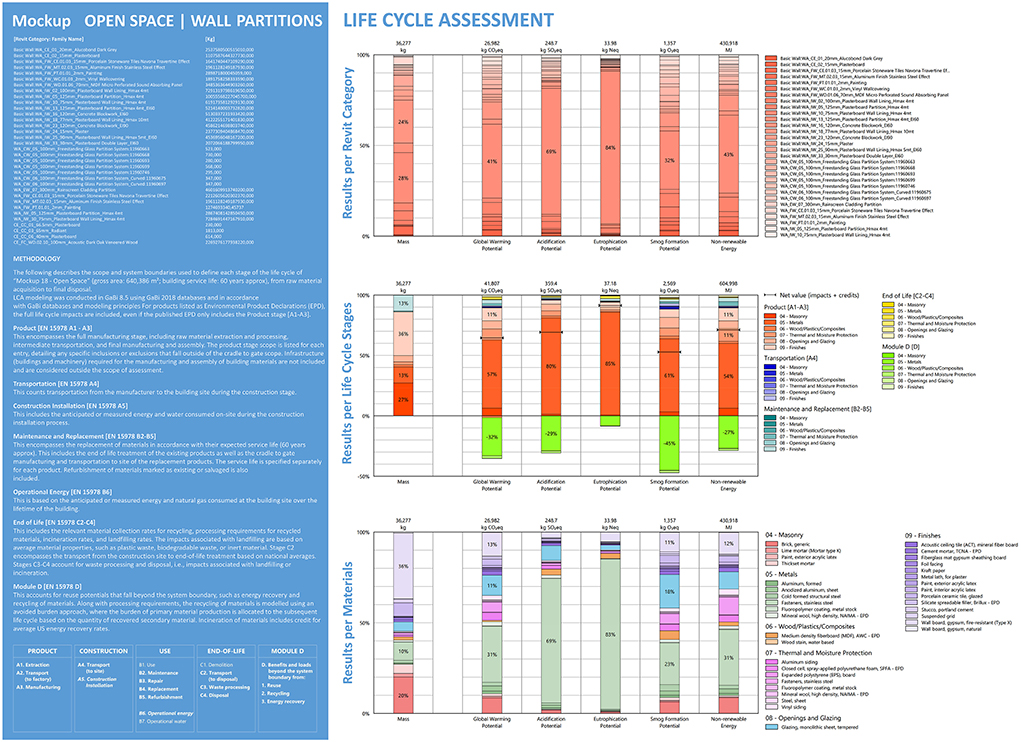
Figure 4. LCA analysis of the interior wall partitions and finishes, categorized by Revit categories, life cycle stages, and materials.
Another data visualization method aims to thematize the Revit model through a color scale, according to the LCA results. The color scale starts from the green color for the lowest values contained in the P-set and therefore for the least impacting elements and passes from yellow–orange and reaches the red color for the highest values and therefore for the elements that have a greater environmental impact. In the legislation, there is no reference to a color scale with the respective ranges of values; the choice has been arbitrary and was made for having a graphical representation of the extent of the impact of the individual elements of the model, in the 3D view, allowing the final reader to quickly identify the elements that have worse values (and therefore should be modified or exchanged in future). Furthermore, by using the same color scale on two different design options, it is possible to see immediately the solutions that are better (Figure 5). Referring to the radioactivity analysis, the study adopted the typical activity concentrations in common building materials that are published within the Radiation Protection 112 (Council Directive 2013/59/EURATOM, 2013). The calculation shows how some building material, if largely used in an indoor space, can produce concentrations of natural radionuclides at levels that can exceed the annual dose criterion of 0.3 mSv ∧ a−1 (I>0.5), such as in the case of porcelain stoneware coatings to be used in the portion of the analyzed mock-up (Figure 6).
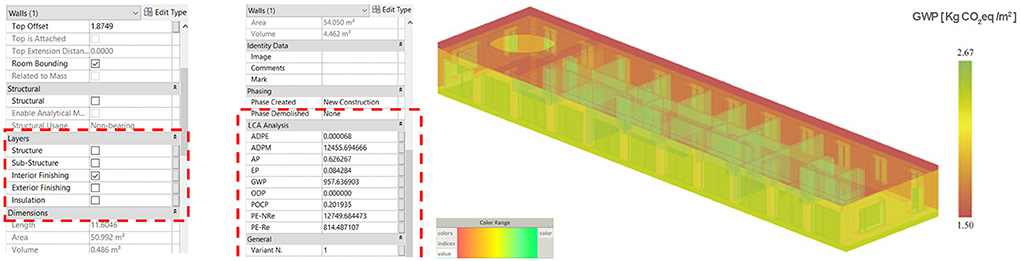
Figure 5. Visualization of GWP impacts of the interior wall partitions and finishes through a .dyn color coding of the technical elements in Revit.
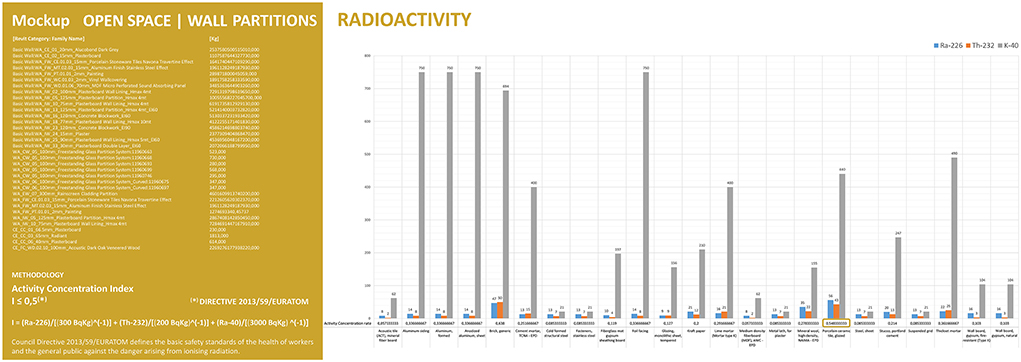
Figure 6. Radioactivity analysis of the interior wall partitions and finishes, categorized by activity concentrations of uranium, thorium, and potassium (Bq kg−1), and calculation of the activity concentration index in each material.
Finally, the cost analysis underlines that wooden materials are more expensive than vinyl products (Figure 7); their service life is shorter than that of a typical lifetime of an office building (60 years for the analyzed mock-up), so materials would need to be replaced at least once. Also, wood siding requires continuous painting or staining that can reduce the amount of recyclable material at the end of life. A constraint to consider when performing LCA is that values associated with ÖKOBAUDAT database are representative of the year of the model and can vary due to changes in efficiency, pollution regulations, or production levels (Environmental Stewardship Committee, 2002; Carnegie Mellon University, 2016). With the objective to finalize a comparison that directly evaluates the environmental declaration of manufacturers, a sheet of the dashboard has been structured to permit the embedding, for each component of the project, of the GWP value declared in the EPDs of three different commercial products, in order to define the procurement for the next construction stage. This further upgrade of the proposed BIM–LCA/LCC framework provides sufficient flexibility to methodology that can be adapted both to ongoing design stage and to the background knowledge of the users; in fact, they can conduct a quick analysis (just considering the databases of common materials) or a comprehensive analysis (considering the environmental declarations of products) within a BIM-based environment.
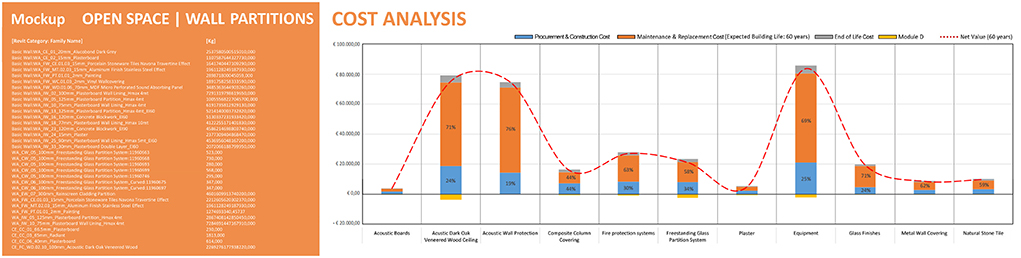
Figure 7. Cost analysis of the interior wall partitions and finishes, categorized by building life stages: Procurement and construction, maintenance and replacement, and end of life.
The data output, obtained from a selection of three EPDs for each material, is then used as a valuable indicator for the optioneering, together with other four key performance indicators (KPIs) coming from the analysis described in Pars. 3.2 and 3.3: radioactivity, product and transportation cost, maintenance and replacement cost, and end-of-life cost.
The graphs in Figure 8 resume the production of environmental impact data, radiation exposure, and cost comparison of three different products for the digital objects that are present in the mock-up. The design score calculations can vary depending on the weight for each KPI given by the stakeholders; each of the three analyzed products is evaluated using a normalizing scale of values between 1 (worst rate) and 10 (best rate). The maximum value −10—is associated with the best performing product for each analyzed indicator.
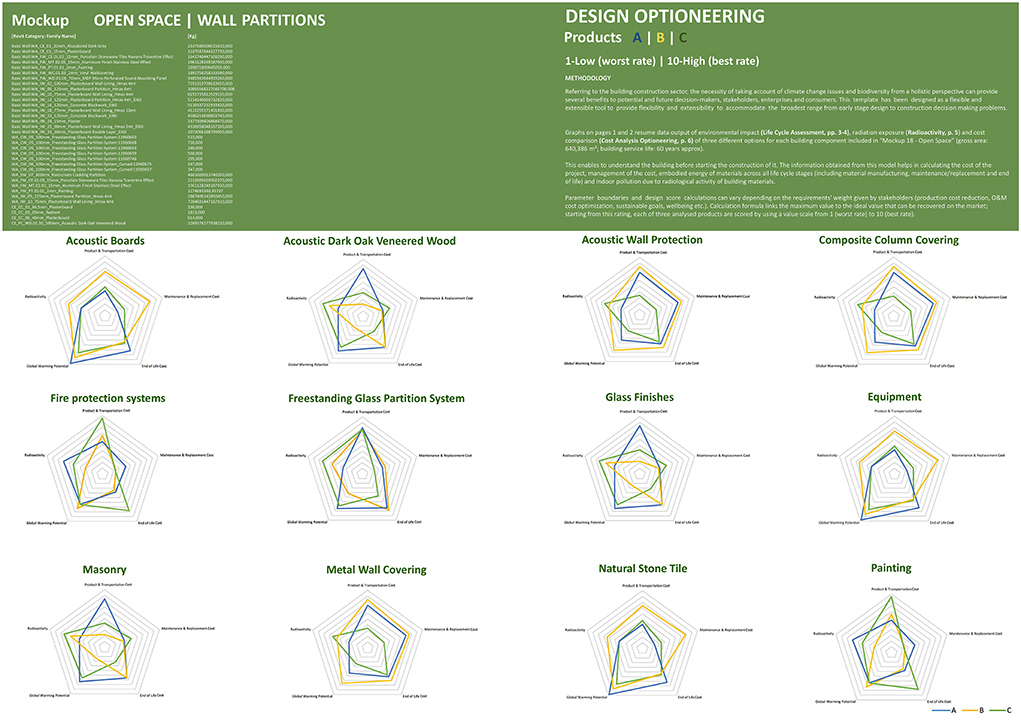
Figure 8. Comparison between different product alternatives (A, B, C) for the elements used in the mock-up.
This practical investigation demonstrates that this direct and reactive workflow—with which the calculation can be automated and dynamically updated inside Revit by the use of the visual programming tool Dynamo—can solve the issues that still involve the largely used LCA-LCC optioneering for the construction industry and permit to make it replicable for different projects and design stages. In fact, it is observed that, although the most recent BIM standard [such as the Industry Foundation Classes (IFC)] already considers some of the required information (EN ISO 16739-1:2020, 2020), a considerable number of properties are still required to conduct a comprehensive LCA and LCC analysis (Bueno and Fabricio, 2018).
Conclusion
Referring to the construction sector, the need for considering the issues of climate change and biodiversity from a holistic perspective can offer numerous benefits to potential and future decision makers, stakeholders, businesses, and consumers. The interoperability—developed in Dynamo, with the aim to directly link the modeling software (Revit) and the LCA analysis tool (One-Click LCA)—can implement the evaluation in the various phases of the design, thus making it both a valuable decision-making tool during the design phases and a holistic method for evaluating the overall sustainability of the work, in complementarity with the international certification protocols (LEED, BREEAM, WELL, etc.).
Another focus of the work is to supplement life cycle assessments with the cost analysis to take the economic dimension into account. The adopted evaluation methodology predicts the full life cycle cost of a project, including the acquisition, design, construction, operation, maintenance, and disposal phase costs.
The evaluation dashboard has been designed as a flexible and extensible tool to provide flexibility and extensibility to accommodate the widest range from early-stage design to construction decision problems. The information included in the panels can vary depending on the objectives of the analysis: the embodied energy of materials and the other environmental impacts, the project costs, the cost management during the service life of the building (including material production, maintenance/replacement, and end of life), and the indoor pollution due to the radiological activity of building materials. Consequently, the work presented can contribute to the existing background knowledge necessary for future implementations of current BIM-based LCA–LCC operative procedures and software.
Data availability statement
The data analyzed in this study is subject to the following licenses/restrictions: copyrighted data. Requests to access these datasets should be directed to SV, c2FsdmF0b3JlLnZpc2N1c29AcG9saW1pLml0.
Author contributions
SV and CM contributed to figure out the methodological plan of the study and wrote the first draft of the manuscript. AA organized the database and implemented the digital models. SV performed the dynamo coding and finalized the analysis. SV and AA wrote the sections of the manuscript. AZ contributed to manuscript revision, read, and approved the submitted version. All authors contributed to the article and approved the submitted version.
Conflict of interest
The authors declare that the research was conducted in the absence of any commercial or financial relationships that could be construed as a potential conflict of interest.
Publisher's note
All claims expressed in this article are solely those of the authors and do not necessarily represent those of their affiliated organizations, or those of the publisher, the editors and the reviewers. Any product that may be evaluated in this article, or claim that may be made by its manufacturer, is not guaranteed or endorsed by the publisher.
Supplementary material
The Supplementary Material for this article can be found online at: https://www.frontiersin.org/articles/10.3389/frsus.2022.1002257/full#supplementary-material
References
Autodesk Revit. (2022). Available online at: www.autodesk.eu (accessed May 25, 2022).
Boussabaine, A., and Kirkham, R. (2004). Whole Life Cycle Costing: Risk and Risk Responses. Oxford; Malden, MA: Blackwell Publishing.
Bueno, C., and Fabricio, M. M. (2018). Comparative analysis between a complete LCA study and results from a BIM-LCA plug-in. Autom. Constr. 90, 188–200. doi: 10.1016/j.autcon.2018.02.028
Carnegie Mellon University. (2016). Economic Input-Output Life-Cycle Assessment. Assumptions, Uncertanity, and other Considerations with the EIO-LCA Method. Available online at: http://www.eiolca.net/Method/assumptions-and-uncertainty.html (accessed May 25, 2022).
Council Directive 2013/59/EURATOM. (2013). Laying down basic safety standards for protection against the dangers arising from exposure to ionising radiation, and repealing Directives 89/618/Euratom, 90/641/Euratom, 96/29/Euratom, 97/43/Euratom and 2003/122/Euratom.
Dynamo BIM. (2022). Available online at: https://dynamobim.org/ (accessed May 25, 2022).
EN 15804:2022-03. (2022). Sustainability of Construction Works - Environmental Product Declarations - Core Rules for the Product Category of Construction Products; German Version EN 15804:2012+A2:2019 + AC:2021. International Organization for Standardization (ISO).
EN ISO 14040:2006. (2006). Environmental Management - Life Cycle Assessment - Principles and Framework. International Organization for Standardization (ISO).
EN ISO 14044:2006. (2006). Environmental Management - Life Cycle Assessment - Requirements and Guidelines. International Organization for Standardization (ISO).
EN ISO 16739-1:2020. (2020). Industry Foundation Classes (IFC) for Data Sharing in the Construction and Facility Management Industries - Part 1: Data Schema. International Organization for Standardization (ISO).
EN ISO 19650-1:2018. (2018). Organization and Digitization of Information About Buildings and Civil Engineering Works, Including Building Information Modeling (BIM) - Information Management Using Building Information Modelling - Part1: Concepts and Principles. International Organization for Standardization (ISO).
Environmental Stewardship Committee Stanford University.. (2002). Guidelines for Sustainable Buildings. Available online at: http://cpm.stanford.edu/pdp.html (accessed May 25, 2022).
European Commission. (1999). Radiation protection 112: radiological protection principles concerning the natural radioactivity of building materials. Directorate-General Environment, Nuclear Safety and Civil Protection. Available online at: https://ec.europa.eu/energy/sites/ener/files/documents/112.pdf (accessed May 25, 2022).
Hollberg, A., Genova, G., and Habert, G. (2020). Evaluation of BIM-based LCA results for building design. Autom. Constr. 109, 102972. doi: 10.1016/j.autcon.2019.102972
ISO 15686-5:2017. (2017). Buildings and Constructed Assets - Service Life Planning - Part 5: Life-Cycle Costing. International Organization for Standardization (ISO).
ISO 21930:2017. (2017). Sustainability in Buildings and Civil Engineering Works - Core Rules for Environmental Product Declarations of Construction Products and Services. International Organization for Standardization (ISO).
ISO 21931:2019. (2019). Sustainability in Buildings and Civil Engineering Works - Framework for Methods of Assessment of the Environmental, Social and Economic Performance of Construction Works as a Basis for Sustainability Assessment. International Organization for Standardization (ISO).
Kang, C. M., Liu, M., Garshick, E., and Koutrakis, P. (2020). Indoor particle alpha radioactivity origins in occupied homes. Aerosol Air Qual Res. 2020, 20. doi: 10.4209/aaqr.2020.01.0037
KBOB eco-bau and IPB 2016 KBOB Ökobilanzdatenbestand DQRv2.. (2016). Grundlage für die KBOB-Empfehlung 2009/1:2016: Ökobilanzdaten im Baubereich, Stand 2016 (Koordinationskonferenz der Bau- und Liegenschaftsorgane der öffentlichen Bauherren c/o BBL Bundesamt für Bauten und Logistik).
Korpi, E., and Ala-Risku, T. (2008). Life cycle costing: a review of published case studies. Manag. Audit. J. 23, 240–261 doi: 10.1108/02686900810857703
Land of Buildings Stanford University.. (2005). Guidelines for Life Cost Analysis. Available online at: https://sustainable.stanford.edu/sites/default/files/Guidelines_for_Life_Cycle_Cost_Analysis.pdf (accessed May 25, 2022)
Llatas, C., Soust-Verdaguer, B., and Passer, A. (2020). Implementing life cycle sustainability assessment during design stages in building information modelling: From systematic literature review to a methodological approach. Build. Environ. 182, 107164. doi: 10.1016/j.buildenv.2020.107164
Manewa, A., Siriwardena, M., and Wijekoon, C. (2021). Life Cycle Costing in Construction: Current Trends and Emerging Directions. doi: 10.31705/WCS.2021.35
Monticelli, C. (2006). Environmental profile and Building Process. “Life cycle assessment application to experimental dry external wall construction system,” in Clever Design, Affordable Comfort a Challenge for Low Energy Architecture and Urban Planning PLEA 2006, 23th International Conference on Passive and Low Energy Architecture. Ginevra, Svizzera, Imprimerie St.Paul, Fribourg, 1023–1028.
Monticelli, C. (2007). “Environmental damage and energy consumption: the life cycle analysis in the building process,” in International Conference Sustainable Conference South Europe Proceedings (Celid), 285–292.
Nieuwlaar, E. (2013). Life cycle assessment and energy systems. Reference Module Earth Syst. Environ. Sci. doi: 10.1016/b978-0-12-409548-9.01334-8
Pagnon, F., Mathern, A., and Ek, K. (2020). A review of online sources of open-access life cycle assessment data for the construction sector. IOP Conf. Ser. Earth Environ. Sci. 588, 042051. doi: 10.1088/1755-1315/588/4/042051
Petti, L., Serreli, M., and Di Cesare, S. (2016). Systematic literature review in social life cycle assessment. Int. J. Life Cycle Assess. 23, 422–431. doi: 10.1007/s11367-016-1135-4
Potrč Obrecht, T., Röck, M., Hoxha, E., and Passer, A. (2020). BIM and LCA integration: A systematic literature review. Sustainability. 12, 5534. doi: 10.3390/su12145534
Santos, R., Aguiar Costa, A., Silvestre, J., and Pyl, L. (2019). Integration of LCA and LCC analysis within a BIM-based environment. Autom. Constr. 103, 127–149. doi: 10.1016/j.autcon.2019.02.011
Shin, Y., and Cho, K. (2015). BIM application to select appropriate design alternative with consideration of LCA and LCCA. Math. Prob. Engg. 2015, 1–14. doi: 10.1155/2015/281640
Soust-Verdaguer, B., Llatas, C., and García-Martínez, A. (2017). Critical review of BIM-based LCA method to buildings. Energy Build. 136, 110–120. doi: 10.1016/j.enbuild.2016.12.009
Soust-Verdaguer, B., Llatas, C., and Moya, L. (2020). Comparative BIM-based life cycle assessment of uruguayan timber and concrete-masonry single-family houses in design stage. J. Clean. Prod. 277, 121958. doi: 10.1016/j.jclepro.2020.121958
Tally LCA. (2022). Available online at: https://choosetally.com/ (accessed May 25, 2022).
UNI 11337:2015. (2015). Building and Civil Engineering Works - Codification Criteria for Construction Products and Works, Activities and Resources - Part 3: Models of Collecting, Organizing and Recording the Technical Information for Construction Products. Ente Nazionale Italiano di Unificazione (UNI).
UNI 11337:2017. (2017). Edilizia e opere di ingegneria civile - Gestione digitale dei processi informativi delle costruzioni - Parte 4: Evoluzione e sviluppo informativo di modelli, elaborati e oggetti. Ente Nazionale Italiano di Unificazione (UNI).
Keywords: life cycle assessment, life cycle costing, building information modeling, interoperability, design optioneering
Citation: Viscuso S, Monticelli C, Ahmadnia A and Zanelli A (2022) Integration of life cycle assessment and life cycle costing within a BIM-based environment. Front. Sustain. 3:1002257. doi: 10.3389/frsus.2022.1002257
Received: 24 July 2022; Accepted: 20 September 2022;
Published: 21 October 2022.
Edited by:
Roberto Rosa, University of Modena and Reggio Emilia, ItalyReviewed by:
Alcinia Sampaio, Technical University of Lisbon, PortugalFlávio José Simioni, Santa Catarina State University, Brazil
Copyright © 2022 Viscuso, Monticelli, Ahmadnia and Zanelli. This is an open-access article distributed under the terms of the Creative Commons Attribution License (CC BY). The use, distribution or reproduction in other forums is permitted, provided the original author(s) and the copyright owner(s) are credited and that the original publication in this journal is cited, in accordance with accepted academic practice. No use, distribution or reproduction is permitted which does not comply with these terms.
*Correspondence: Salvatore Viscuso, c2FsdmF0b3JlLnZpc2N1c29AcG9saW1pLml0