- 1Department of Chemical Engineering, Texas A&M University, College Station, TX, United States
- 2Gas and Fuels Research Center, Texas A&M Engineering Experiment Station, College Station, TX, United States
- 3Energy Institute, Texas A&M University, College Station, TX, United States
- 4Department of Chemical Engineering, Qatar University, Doha, Qatar
Extreme events cause significant damage and disruption to the manufacturing sector, associated supply chains, and adjacent communities. These disastrous shocks may include natural disasters (e.g., hurricanes, floods, earthquakes), pandemics, catastrophic economic collapses (e.g., price crash of oil and gas), and terrorist and cyberattacks. Although much research has addressed the resilience of infrastructure, very little work has targeted the resilience of the manufacturing processes. Even less work has addressed the topic of process design approaches to create disaster-resilient industrial processes. The objective of this paper is to provide perspectives on the use of process integration for developing disaster-resilient designs of industrial plants with a focus on the process industries (e.g., chemical, petrochemical, oil, gas, specialty chemicals, pharmaceuticals, biorefining). Focus is given to three categories of extreme events: natural disasters, pandemics, and economic collapses. Although several principles have been proposed for resilience engineering of infrastructure, industrial processes have unique features that warrant a tailored discussion. To streamline the discussion, we have identified 12 principal strategies for creating disaster-resilient designs: (1) Fail-safe by design, (2) Redundancy, (3) Reconfigurability, (4) Modularity/Mobility/Distributability, (5) Repurposability, (6) Flexibility, (7) Controllability, (8) Reliability, (9) Recoverability/restorability, (10) Rapidity, (11) Robustness, and (12) Resourcefulness. These strategies are generally applicable to the process industries because they transcend the specific type of the manufacturing facility. Examples of industrial applications are given to explain the resilience strategies and discuss the research challenges and potential use of process integration in the systematic development of design concepts and tools for resilient design. The paper concludes with a list of future directions and promising research opportunities.
Introduction
Traditionally, the design, operation, and optimization of manufacturing facilities have been largely driven by economic factors with little consideration of risk, resilience, interactions with surrounding communities, and integration with supply chains. In addressing the potential impact of disasters, most facilities rely on emergency response plans. The result has been ineffectiveness in responsive policies, stagnation in technological breakthroughs, and tremendous losses in the wake of disasters such as hurricanes, tropical storms, storm surges, and floods. For instance, the US Gulf Coast Region (which represents the backbone of the US continuous manufacturing sector) has endured more than $550 B (Figure 1). These economic losses do not reflect the devastating impacts on lives and livelihoods; dislocation of workforce and communities; public health problems due to leaking hazardous materials from energy production and manufacturing sites; and disruptions of goods and services.
Generally speaking, resilience engineering is aimed at decreasing the negative impact of shocks on the system performance and enhancing the adaptive capacity of the system to respond quickly and favorably to expected and unexpected disruptions. Ayyub (2014) defines resilience as “the ability to prepare for and adapt to changing conditions and withstand and recover rapidly from disruptions.” As such, there are three main capacities of a resilient system: absorptive, adaptive, and restorative. Righi et al. (2015) provided a review of resilience engineering, covered six possible definitions, and presented the alignment with the safety management paradigm. A review of definitions and metrics of resilience is given by Ayyub (2014). Different studies have highlighted the key characteristics of a resilient system such as robustness, resourcefulness, rapidity, and redundancy (Bruneau and Reinhorn, 2007; Yu et al., 2020) or the key resilience functions to resist, restabilize, rebuild, and reconfigure (Gasser et al., 2019). Woods (2015) classified the use of resilience around four concepts: rebounding from trauma, a synonym to robustness, graceful extensibility (opposite of brittleness), and sustainability of a network of architectures that can adapt to future events. Although much research has been addressed the resilience of infrastructure, very little work has targeted the resilience of the manufacturing processes (not the infrastructure of these plants). Even less work has addressed the topic of process design approaches to create disaster-resilient industrial processes. Dinh et al. (2012) described six principles for resilience engineering of industrial processes: flexibility, controllability, early detection, minimization of failure, limitation of effects, and administrative controls/procedures. Reniers et al. (2018) proposed an initiative to enhance the resilience of the chemical industrial parks by emphasizing education, learning, training, proactive risk minimization, and safety innovation. Pasman et al. (2020) discussed how the resilience of processing facilities can enhance safety and sustainability. Jain et al. (2017, 2018) introduced process analysis framework to assess resilience and highlighted the importance of three characteristics of resilience: avoidance, survival, and recovery. Moreno-Sader et al. (2019) introduced an economic framework for coupling conventional profitability analysis with resilience projects using process-integration targeting techniques. Jain et al. (2020) introduced a process resilience analysis framework and used it to illustrate the relationship between strengthening process resilience and enhancing sustainability and business continuity. Caputo et al. (2020) proposed an approach for estimating the capacity loss of a plant under seismic disruption. Gong and You (2018) presented an approach to the resilient design and operation of chemical processes by using resilience and economic objectives in a two-stage mixed-integer fractional programming model that includes five strategies: selection from alternative designs, increasing absorptive capacity of units, using parallel processing, installing redundant units, and developing scheduling strategies for recovery. Orosz et al. (2020) proposed a methodology for the analysis of structural and operational aspects of process using the P-graph framework. Jafarinejad (2020) proposed a framework for designing resilient, energy-efficient, and sustainable wastewater treatment plants. Salehi and Veitch (2020) studies the factors contributing to the adaptive capacity of processing facilities based on data obtained from plant managers at different levels. Vairo et al. (2020) evaluated the resilience of hazardous-materials storage plants using Bayesian network analysis. Benjamin et al. (2020) used input-output modeling to evaluate risk and resilience for integrated biorefineries. Son et al. (2020) provided a review of emergency response strategies for processing facilities. Sengupta and Yelvington (2020) described the role of modular and intensified processes in enhancing the resilience of manufacturing facilities and supply chains. Abimbola and Khan (2019) and Taleb-Berrouane and Khan (2019) modeled resilience through a dynamic object-oriented Bayesian network and stochastic approaches. Resilience using control systems was discussed by Lenhoff and Morari (1982) to optimize the dynamic behavior of a process under disturbance. There have also been research activities in the areas of flexibility and reliability which are related to resilience. Thomaidis and Pistikopoulos (1994) proposed the inclusion of flexibility, reliability, and maintenance in design while addressing uncertainty in process parameters. Yarveisy et al. (2020) introduced resilience metrics based on reliability, maintainability, and system modeling approach. Ade et al. (2018) investigated the role of inherent safety on the reliability of industrial processes. Al-Douri et al. (2020) introduced an economic framework for mitigating operational failure by considering reliability, availability, and maintainability. Park et al. (2020) and Roy et al. (2016) provided recent literature surveys on the use of safety in process design.
Before describing the role of process design in enhancing resilience of the manufacturing facilities, it is instructive to highlight the main negative consequences of hurricanes, floods, and pandemics on the manufacturing sector and associated communities. Table 1 highlights these impacts and shows common consequences for hurricanes/floods and pandemics. Resilience strategies should have the characteristics of mitigating these negative impacts.
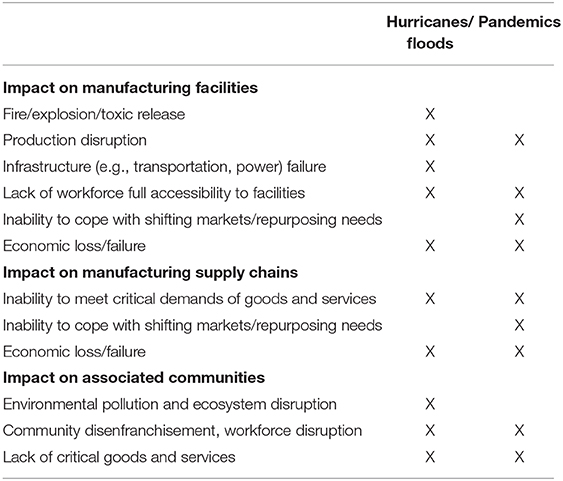
Table 1. Main impacts of hurricanes, floods, and pandemics on the manufacturing sector and communities.
Although operational and responsive strategies help lessen the consequences of a disaster on a manufacturing facility and impact communities, design modifications can play a dominant role in mitigating, withstanding, and recovering from the impact of disasters. Process integration is a particularly powerful framework for the design of manufacturing facilities. Process integration is defined as a “holistic approach to process design and operation which emphasizes the unity of the process” (El-Halwagi, 1997, 2017b). There are three primary categories of process integration: mass integration, energy integration, and property integration. There is already a compelling track record for the success of process integration in increasing profitability, conserving natural resources, preventing pollution, and enhancing sustainability. For overviews of the principles, tools, and industrial applications of process integration, the reader is referred to literature (e.g., El-Halwagi and Spriggs, 1998; Dunn and El-Halwagi, 2003; Kemp, 2009; Majozi, 2010; Noureldin, 2011; Foo, 2012; El-Halwagi, 2017b). Because of its strong track record in the fields of design and sustainability and its holistic and multi-scale nature, process integration is uniquely poised to yield a powerful framework for systematically creating resilient designs that are highly effective, robust, and novel.
The objective of this paper is to provide perspectives on the use of process integration for developing disaster-resilient designs of industrial plants with focus on the process industries (e.g., chemical, petrochemical, oil, gas, specialty chemicals, pharmaceuticals, biorefining). The paper is structured around 12 principal strategies for creating disaster-resilient designs. An explanation is given to each strategy. Several industrial examples and research challenged are discussed to demonstrate the research challenges and potential use of process integration in the systematic development of design concepts and tools for resilient design.
The 12 Principal Strategies for Disaster-Resilient Design of Industrial Processes
In this paper, the resilience of a manufacturing facility is defined as the ability to anticipate, prepare for, mitigate, withstand, adapt to, and recover from the impact of disastrous shocks. In general disastrous shocks may include natural disasters (e.g., hurricanes, floods, earthquakes), pandemics, catastrophic economic collapses (e.g., price crash of oil and gas), wars, terrorist and cyberattacks, and the disruption of critically associated supply chains. In this paper, focus will be given to the first three categories of extreme events: natural disasters, pandemics, and economic collapses. Although several principles have been proposed for resilience engineering of infrastructure, industrial processes have unique features that warrant a tailored discussion. Therefore, we propose the following 12 principal strategies for disaster-resilient designs of manufacturing facilities:
1. Fail-safe by design: When the process is not robust enough to withstand an extreme event, it should be allowed to fail but in a safe(r) manner which mitigates risks and poses little or no harm to the surroundings, people, or communities. It is also worth noting that a fail-safe design must be coupled with safe-fail approaches which are aimed at the inclusion of adaptive capacity to minimize the negative consequences once new risks are identified and revealed (Park et al., 2011). To illustrate this concept, let us first recall an incident that resulted from Hurricane Harvey which dropped more than 50 inches of rain in Texas and caused a disruption in electric power and partial submergence of manufacturing facilities. In one of the chemical facilities, power disruption and facility submergence led to failed refrigeration systems and resulted in the rise of the temperature of stored organic peroxides which violently decomposed leading to explosions [(CSB (Chemical Safety Hazard Identification Board), 2018)]. Next, let us consider an example of an exothermic catalytic reaction system which requires cooling to avoid temperature rise and a runaway reaction (Figure 2A). If an extreme event causes a power supply disruption, the coolant pump will fail. The increasing temperature of the reaction mixture will trigger runaway reactions, ultimately leading to fire, explosion, and toxic chemical release. Figure 2B shows the sequence of steps that start with a loss of power that leads to failure of the cooling system to maintain the reaction temperature and subsequently leads to a runaway reaction that results in fire, explosion, and release of toxic materials.
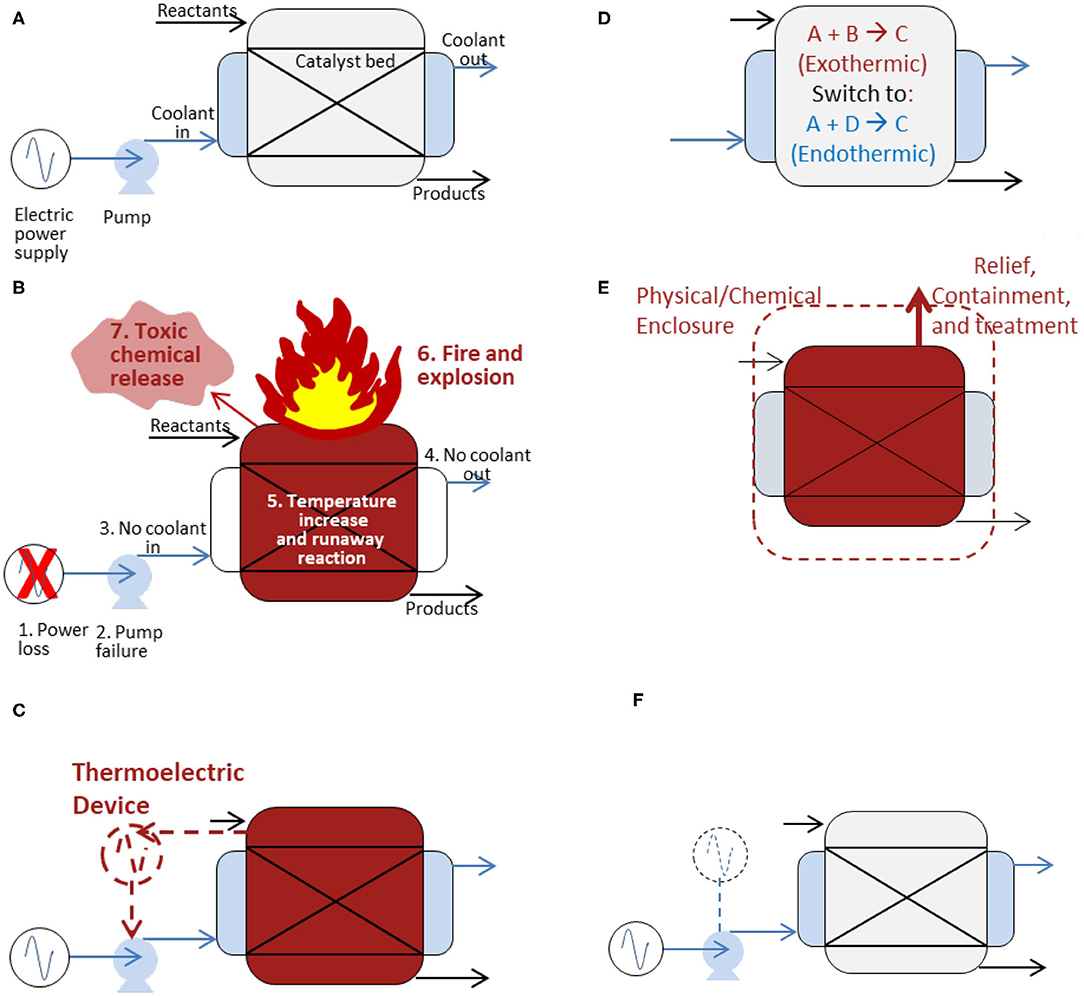
Figure 2. (A) An exothermic reaction system during normal operation. (B) Non-resilient operation following power loss. (C) Fail-safe via substitution to resilient emergency power. (D) Fail-safe via reactant substitution. (E) Fail-safe via containment, relief, and treatment. (F) Redundancy via an energy storage and dispatch system.
One option for a fail-safe design is to utilize excessive heat release to generate power and lower the reactor temperature (e.g., using thermoelectric devices) and to power the coolant pump (Figure 2C). Another option is the use of alternate reactants can transform exothermic reactions into endothermic reactions with an inherently safer shutdown upon power loss (Figure 2D). Another fail-safe approach is to enclose the unit with a resilient containment equipped with proper relief systems that can contain the explosion and treat or prevent the release of toxic chemicals (Figure 2E). An example of containment is the case of producing phosgene (a highly hazardous chemical) for which that reactor may be enclosed in a containment building (often operated under slight vacuum) and/or surrounded with scrubbing systems to protect from leaks (Gowland, 1996; Thiel et al., 2020). The systematic development of such fail-safe designs will require the evolution of conventional process integration approaches such as reaction pathway synthesis (Rotstein et al., 1982; Crabtree and El-Halwagi, 1994; Pham and El-Halwagi, 2012; Ponce-Ortega et al., 2012), combined heat and power; (Mohan and El-Halwagi, 2007; El-Halwagi et al., 2009; Kemp, 2009), and integrated molecular and process design (Eljack et al., 2007).
2. Redundancy: A simple form of redundancy is duplication (e.g., Rubio-Castro et al., 2013). Here, we adopt a more general definition that refers to the use of components of the process to replace or supplement failing parts of the system to maintain the original operation/functionality or move the operation to a satisfactory goal for resilience. In the previous example of the reaction system, the simple form of redundancy will be to install two coolant pumps. But if there is power outage, both will fail. On the other hand, if an alternate form of supplying power (e.g., an energy storage and dispatch unit) is added and activated upon failure of the main power supply, then it can run the coolant pump and avoid runaway reactions (Figure 2F). Another example is shown by Figure 3 where a dedicated power generation system is installed to partially replace the external power from the grid upon failure or to use it to supplement the external power as part of a cogeneration system. In case of loss or partial failure of the external power supply, the process-generated power is allocated to the most critical parts of the process. This paradigm is analogous to the use of plant-owned standby turbines dedicated to peak shaving to address the case of a sudden increase in power consumption of the plant (e.g., Smith, 2000). During non-disaster times, the internally-generated power can be used to “shave off the peaks” in consumption that can trip the external power system or incur substantial penalties.
3. Reconfigurability: This corresponds to the ability to alter the process flowsheet using the same pieces of equipment but in different arrangements and/or for multiple purposes. In the field of process integration, this concept has been largely limited to batch processes and, to a much lesser extent, to small-scale specialty-chemical or pharmaceutical processes (e.g., Adamo et al., 2016). Large-scale processing facilities are notorious for their fixed configuration. An effective way of reconfiguring the process without moving the fixed and bulky equipment is to use different configurations of the connecting pipelines. A particularly useful tool that has been used in process synthesis is the superstructure approach. It is a network representation which embeds all configurations of interest that can then be translated into an optimization formulation to be solved for the selection of the optimal configuration. A recent review of the superstructures is provided by Mencarelli et al. (2020). To illustrate this concept, consider Figure 4A that shows a superstructure based on the state-space representation (Bagajewicz and Manousiouthakis, 1992). It encapsulates numerous alternatives that can be generated by selecting and deselecting (assigning a zero flowrate to) the streams. For instance, Figures 4B,C show the reduced superstructures that represent the associated flowsheets. There is a research gap and an opportunity to evolve conventional superstructure approaches to address reconfigurability and resilience because the goal is not to select an optimal flowsheet from among the various alternatives. Instead, the goal is to identify various reconfigurable configurations that can be created by altering connectivities to address disaster-based scenarios as well as normal operations. Since the unit capacities will also need to be determined, issues of capital productivity, resilience objectives, operability, and scenario probability must also be included. For instance, consider an example of three units that operate normally in the following sequence: A followed by B then C. Under normal conditions, this sequence is the cost-optimal configuration. Unit A is a separation device that removes and neutralizes a certain pollutant (p1). Suppose that as a result of a disruption that the feed composition changed in a way that introduced an additional component into the system and that upon reaction in unit C, a hazardous chemical (p2) is produced. Separation unit A has the ability to remove and neutralize both p1 and p2. Therefore, to continue operation following the disruption, unit A must be moved after unit C. In a large-scale facility, units cannot be readily moved around. Nonetheless, if the plant is equipped with the superstructure of the piping network shown by Figure 4A, the flow in the piping network can be easily moved from the configuration shown by Figure 4B to the one shown by Figure 4C (by simply closing and opening the appropriate valves) with the effective reconfiguration of the units to have the new sequence B followed by C then A. All of this can be done with proper pre-planning and without having to move a single unit. Although the new configuration is not cost optimal but it provides the plant of a way to continue operation during disruption times.
4. Modularity/Mobility/Distributability: Conventional process plants with large throughputs tend to include large units. Modular units, on the other hand, tend to be small and are typically mounted on a skid. These skids can tackle small throughputs and can also be interconnected to handle large throughput. These units can also contribute to the establishment of distributed manufacturing networks. Tian et al. (2019) described a modular approach to process integration and intensification. Allen et al. (2019) introduced a design and scheduling framework for capacity planning of modular and transportable infrastructure for shale gas production and processing. Al-Fadhli et al. (2019) provided a network-based approach for the use of modular units in hydrocarbon processing. Oke et al. (2020) developed an optimization framework for using modular units in treating flowback wastewater in oil and gas fields. Roy (2017) discussed the main advantages of modular units including worksite safety (since most of the modular units may be manufactured offsite), scheduling efficiency, and flexibility of adding more units easily. The primary disadvantage of modular units is the loss of the benefits of “economy of scale” for larger plants. Another disadvantage is the increased level of complexity in interconnecting and operating a large number of modular units. Sengupta and Yelvington (2020) discussed the use of modular units to promote resilient manufacturing—especially the speed at which these units may be manufactured and the ability to deploy these units to disaster-impacted sites. Furthermore, the placement of these modular units over a network of sites supports the notion of distributed manufacturing that enhances the overall resilience of the network especially when certain sites are spared the impact of extreme events. The following are two examples of the use of modular units to addresses extreme events:
◦ The first example is inspired by the Waha hub in West Texas in March and April of 2018 when two compression stations in New Mexico failed and caused a severe limit on the amount of natural gas that could flow in the distribution network. Without a local manufacturing infrastructure to process the gas, the price of natural gas plummeted to minus $4.28/MM Btu (DiSavino, 2020). Another example is the historic crash in the price of crude oil which plummeted to minus $38/bbl (Coy, 2020) with the problem exacerbated by the lack of additional storage or refining capacities. These are examples of a disaster in the form of an economic collapse and, additionally in the case of the Waha hub, environmental pollution (even when the gases are flared, they have a negative environmental impact). For the Waha hub case, if there were an available fleet of modular gas processing units (e.g., gas-to-liquid GTL), they could have been deployed as a disaster-relief set of resilient “plants on wheels” (or other forms of transportation) to convert the gas to liquid transportation fuels or chemicals that can be easily transported to consumers especially communities that were deprived of natural gas following the distribution failure. Figures 5A,B illustrate the base case and the resilient solution through modularity and mobility.
◦ The second case deals with a common situation that follows flood-impacted industrial facilities when wastewater treatment facilities fail and pollutants contaminate adjacent communities (Olyaei et al., 2018). In such cases, a modular wastewater treatment unit can be deployed to treat wastewater and offer clean water for the impacted community as shown by Figures 6A,B.
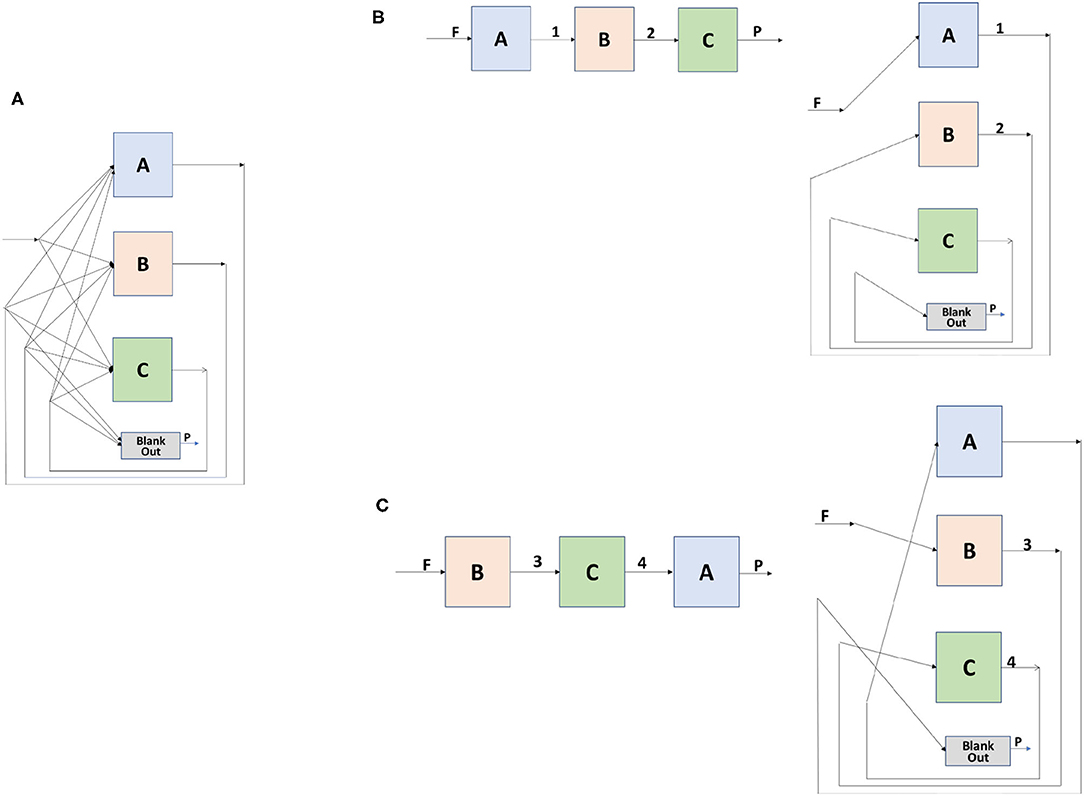
Figure 4. (A) A superstructure representation. (B) A reduced superstructure for representing the first process configuration. (C) A reduced superstructure for representing the second process configuration.
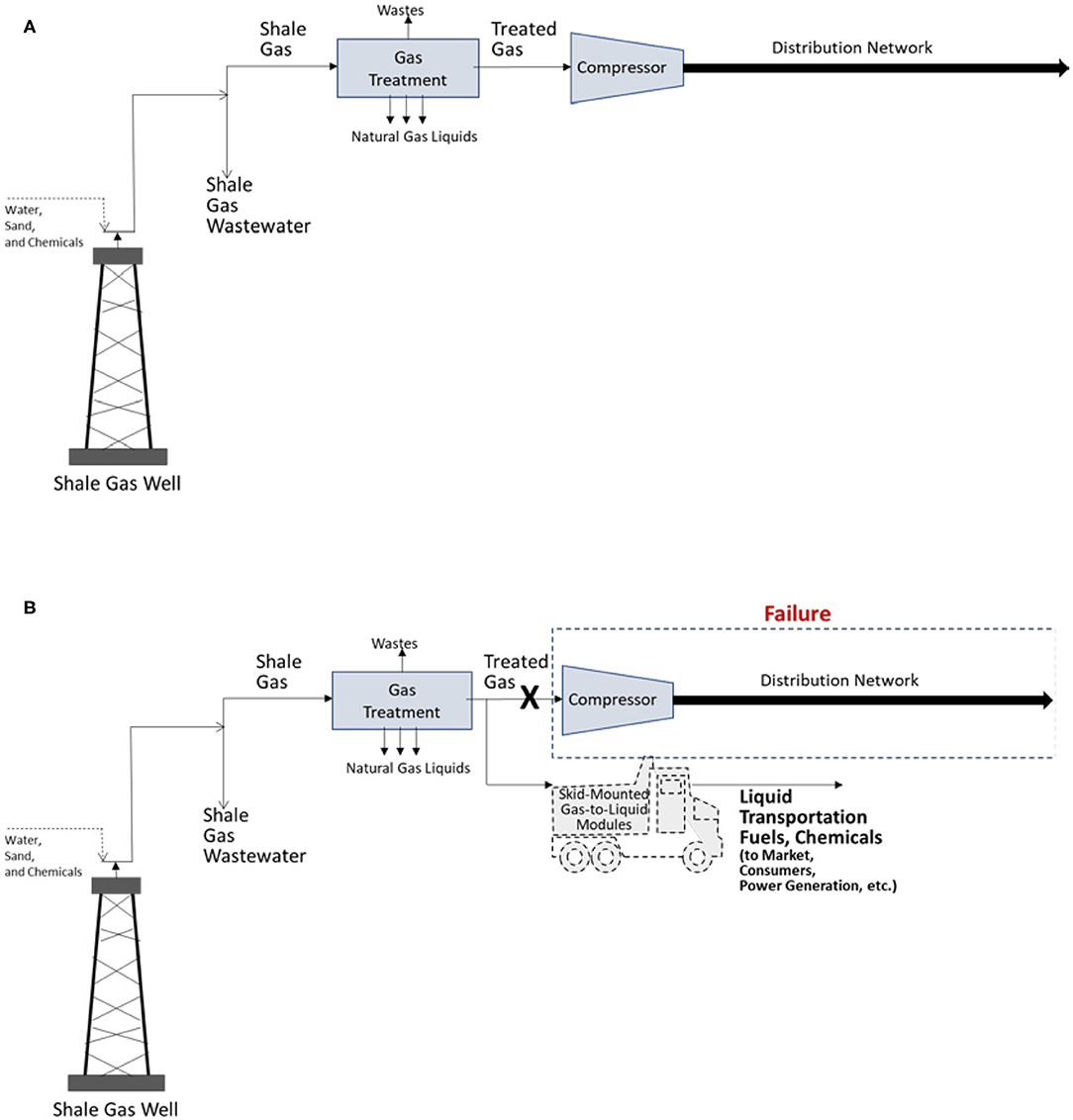
Figure 5. (A) Shale gas distribution. (B) Deployment of modular GTL units for resilient shale gas monetization.
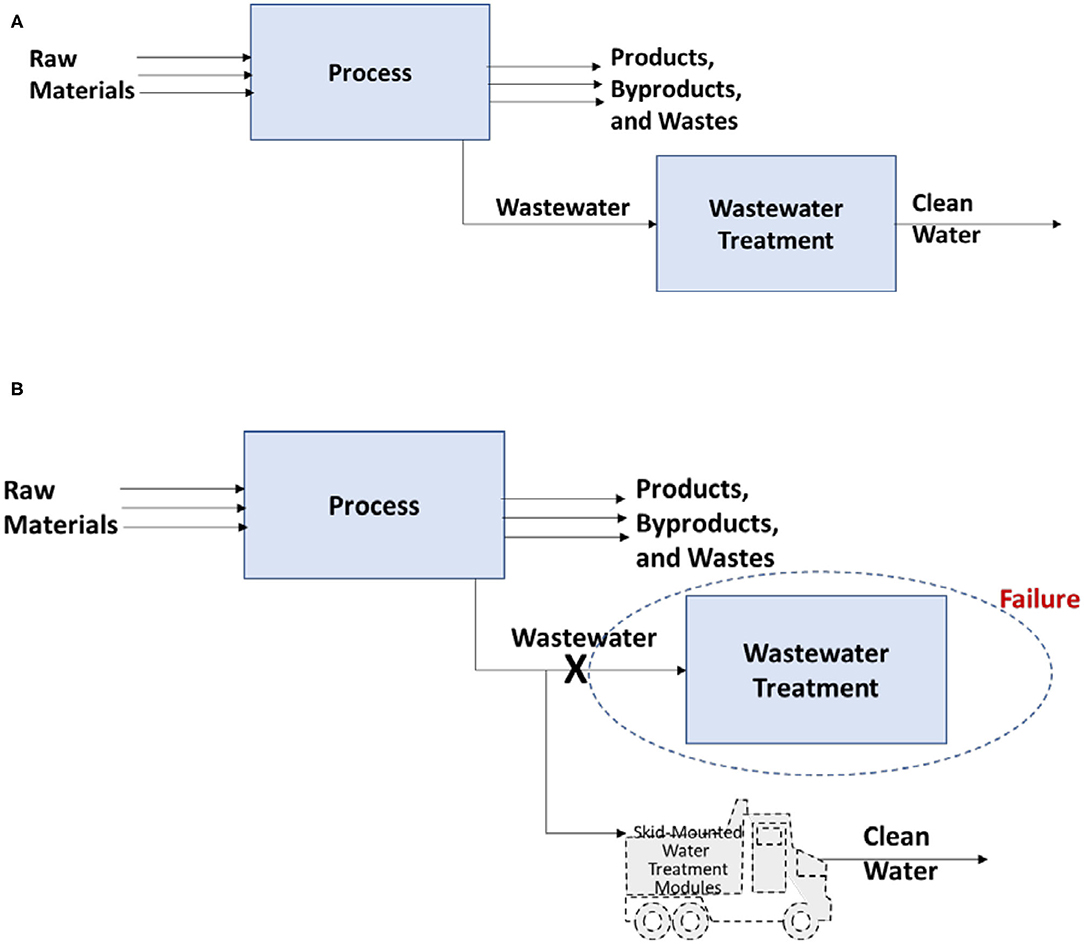
Figure 6. (A) A manufacturing site with wastewater treatment. (B) Deployment of modular units for resilient wastewater treatment.
New process integration tools are needed to determine the optimal selection of type, size, and the number of deployable modules and the scheduling schemes. The tools must take into consideration the various disaster scenarios and the probabilistic, spatial, and temporal aspects of these scenarios.
5. Repurposability: which refers to the capability of a process to be used for purposes or products that are different from the original ones. During disaster times, there is insufficient time to resort to conventional retrofitting or revamping activities. Nonetheless, if the process has a pre-disaster design which is re-purposeful, alteration from one mode of operation to the other becomes almost instantaneously possible. For instance, consider a process that converts natural gas to methanol. Figure 7A is a simplified block flow diagram (based on the detailed design provided by Ehlinger et al., 2014; Alsuhaibani et al., 2019). During pandemics, it is anticipated that there will be increased demands for hand sanitizers because of the additional use and panic buying. An important ingredient in the production of hand sanitizers is ethanol. Methanol cannot be used in hand sanitizers because it leads to severe health problems. Can a methanol plant be repurposed to produce ethanol? The answer is yes but the repurposing requires pre-planning during the greenfield design or retrofitting phases. Process simulation and synthesis techniques may be used to ensure the ability to repurpose and to identify necessary changes in vessel design, operating conditions, and catalyst. Figure 7B shows the simplified process after repurposing during pandemic times to produce ethanol. The process configuration is virtually the same with changes in sizing, operating conditions, and catalyst (Rh-based instead of Cu-based) (de Carvalho Miranda et al., 2020). This process is not the common plant for producing ethanol (which is commercially produced via biomass fermentation) but it has the major advantage of being re-purposeful during disaster times then switched again to the original process afterward.
6. Flexibility: In the field of process design, flexibility has been used to represent the “ability of the system to feasible operation over a range of uncertain conditions” (Dimitriadis and Pistikopoulos, 1995). These uncertain conditions may result from unplanned disturbances such as disastrous disruptions or from pre-planned activities such as the aforementioned repurposing operations. If the output of the system stays within acceptable performance bounds, then the process design is flexible. On the other hand, if subsets of the output of the system violate the acceptable performance bounds, then the system is inflexible. Figure 8 is a schematic representation of the flexibility concept. Important research contributions have been made in the assessment of and design for flexibility and design under uncertainty (e.g., Grossmann and Morari, 1983; Swaney and Grossmann, 1985; Pistikopoulos and Grossmann, 1989; Zhu and El-Halwagi, 1995; El-Halwagi et al., 2013; Kazantzi et al., 2013; Kazi et al., 2015, 2018; Tovar-Facio et al., 2017; Mukherjee and El-Halwagi, 2018; Ortiz-Espinoza et al., 2019; Mukherjee et al., 2020). These contributions can constitute a strong basis for the flexibility approaches needed for resilient design to systematically include the objectives of enhancing the absorptive capacity and adaptability of the process in response to extreme events such as disasters and surges in demands following pandemics while reconciling these aspects with the technical, economic, environmental, and safety objective of the process.
7. Controllability: This may be defined as the ability “to steer dynamical system from an arbitrary initial state to an arbitrary final state using the set of admissible controls.” (Klamka, 1991). Therefore, controllability addresses the dynamic issues and trajectories for the system behavior which are not considered in the aforementioned flexibility analysis. It is worth noting that toward resilience, the final state may vary depending on the disaster scenario and a desirable objective. Although controllability belongs to the field of process control, process design has a strong impact on controllability. Recent research efforts have endeavored to include controllability during the design phase and to develop a unified approach for process design and control (e.g., Burnak et al., 2019a,b; Onel et al., 2019).
8. Reliability: which refers to the ability of the process or its components to function without failure. The conventional definition of reliability entails identifying the probability of failure and the mean time to failure (e.g., Ade et al., 2018; Al-Douri et al., 2020). Nonetheless, under extreme events the definition must be expanded to reflect the impact of the external shocks and their consequences.
9. Recoverability/restorability: which refer to the process inherent and adaptive capacities to undergo corrective actions to restore stability and normal operation either to the original (pre-disruption) state or to a new desirable state (e.g., repurposed state or fail-safe state). A research challenge for process integration is to develop systematic targeting techniques to establish benchmarks for recoverability and restorability. Once these targets are established, conventional design approaches can be used to generate processes that feature rapid and robust recoverability while balancing this objective with the technical, economic, environmental, and safety objectives of the process.
10. Rapidity: Bruneau and Reinhorn (2007) define rapidity as: “the capacity to meet priorities and achieve goals in a timely manner in order to contain losses, recover functionality, and avoid future disruption.” In order to further understand rapidity, it is instructive to first discuss the typical stages of a resilient system following disruption. Taleb-Berrouane and Khan (2019) describe a five-stage lifecycle model of resilience: stability, disruption effect, system reaction to disruption, rehabilitation from the disruption, and return to stability. Figure 9 shows the “bathtub curve” associated with these five stages, but with two additional options for returning to stability: a new stable based on a re-purposed objective or a fail-safe objective. It is worth noting that the re-purposed objective is only temporary. For instance, if there is a surge demand for certain products that are not currently produced by the process, and the process has to be repurposed to produce these new products, the repurposing will be carried out for the duration of the surge demand, after which the process will be restored to its normal operation. In this case, rapidity deals with the speed at which such repurposing takes place. The deterioration performance and duration are associated with the system's robustness and absorptive capacity. The system's response to duration depends on its adaptive capacity. Finally, restoration and rehabilitation reflect the system's restorative capacity based on preventive or responsive actions. Rapidity is captured by the period between disruption start and end. A shorter time between disruption start and end represents a more rapid recovery and leads to a more resilient system. A research challenge for process integration is to develop systematic design approaches that lead to inherent and adaptive features that minimize disruption time for potential scenarios while balancing this objective with the technical, economic, and environmental objectives of the process.
11. Robustness: A common definition of robustness is given by Bruneau and Reinhorn (2007) as: “the strength, or the ability to withstand a given level of stress or demand without suffering degradation or loss of function.” As such, robustness is closely tied to the system's absorptive capacity. Woods (2015) highlighted the alignment between the concepts of resilience and robustness and discussed the relevance to the field of robust control which offers stability and/or robust performance over given bounds on uncertainties and disturbances (e.g., Pistikopoulos et al., 2009). For manufacturing facilities, robustness covers the integrity of process equipment as well as satisfactory continuity of operation. As such, robustness can be achieved through a combination of design and operation procedures and protocols.
12. Resourcefulness: the ability of the process to deploy and utilize various resources (e.g., materials, energy, technologies, human) to maintain proper operation or avoid detrimental consequences when faced with disruptions especially in the supply of raw materials and energy. Consider the following example for the production of isopropyl alcohol (IPA) or isopropanol which is a common ingredient in hand sanitizers. A typical route for IPA production is to start with propane as the primary feedstock which is converted to propylene via dehydrogenation (Agrawal et al., 2018) then hydration is used to yield IPA (Panjapakkul and El-Halwagi, 2018). Suppose that the supply of propane gets disrupted because of a natural disaster or becomes insufficient because of a sudden surge in the demand for IPA (as was the case in the US following the spread of the COVID-19 pandemic). Reaction pathway synthesis and process integration techniques can be used to identify alternate routes that do not require propane. For instance, as shown by Figure 10, methanol (produced from natural gas or biomass) or glycerol may be used to yield propylene. If the process is designed to be capable of processing methanol or glycerol instead of or in addition to propane, then such resourcefulness can maintain production despite disruption/deficiency in raw materials/supply chains.
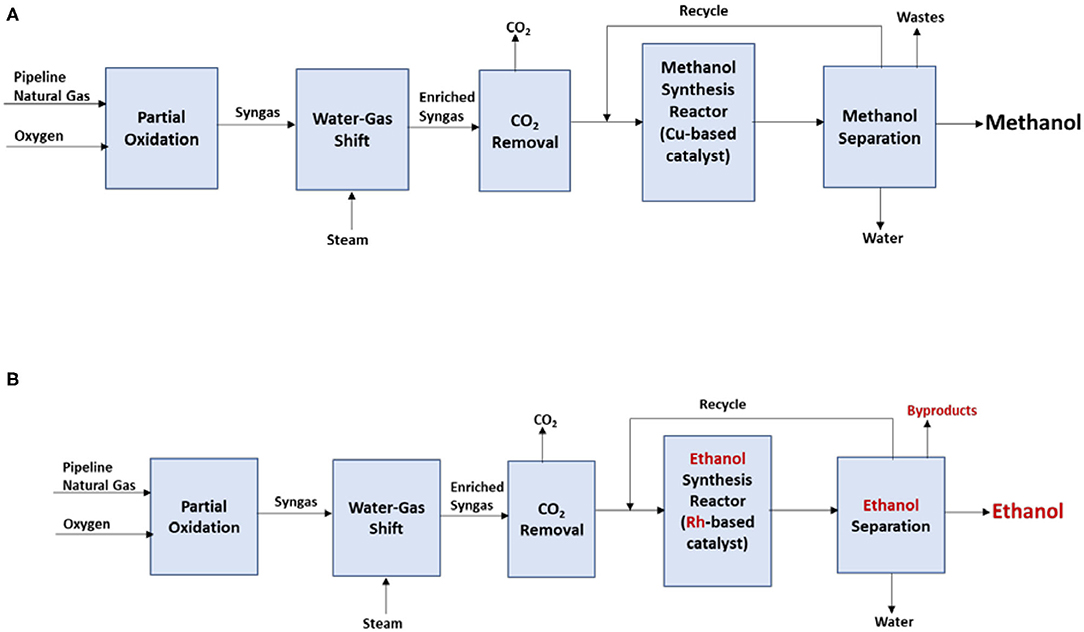
Figure 7. (A) A methanol production process. (B) A repurposed process for the production of ethanol.
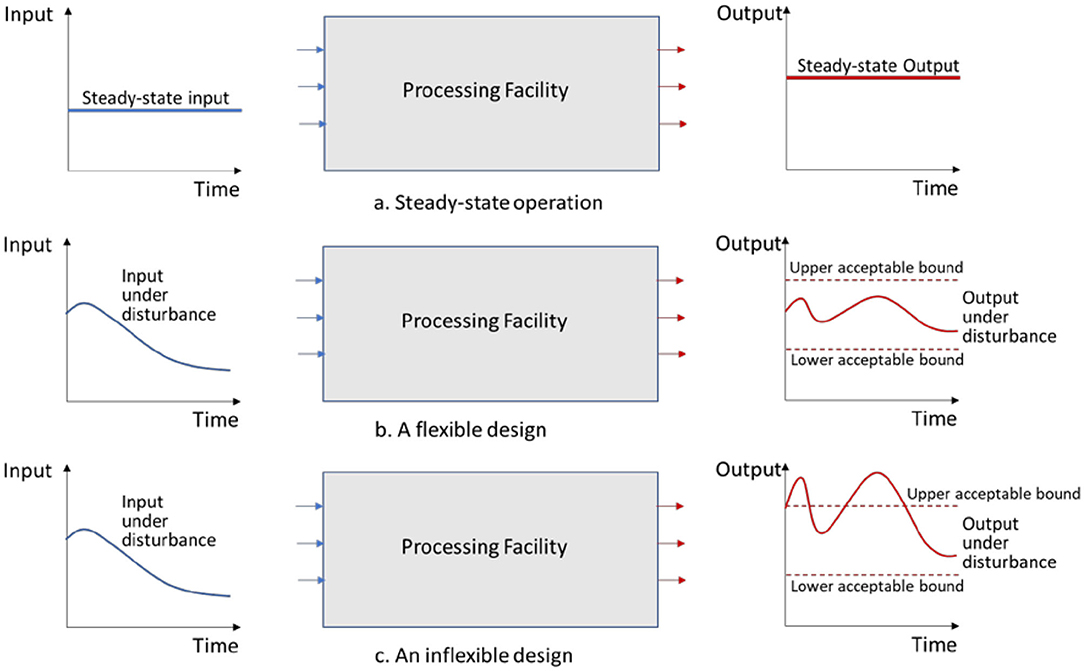
Figure 8. Flexibility assessment: (A) Under steady-state conditions, (B) A flexible design, and (C) an Inflexible design.
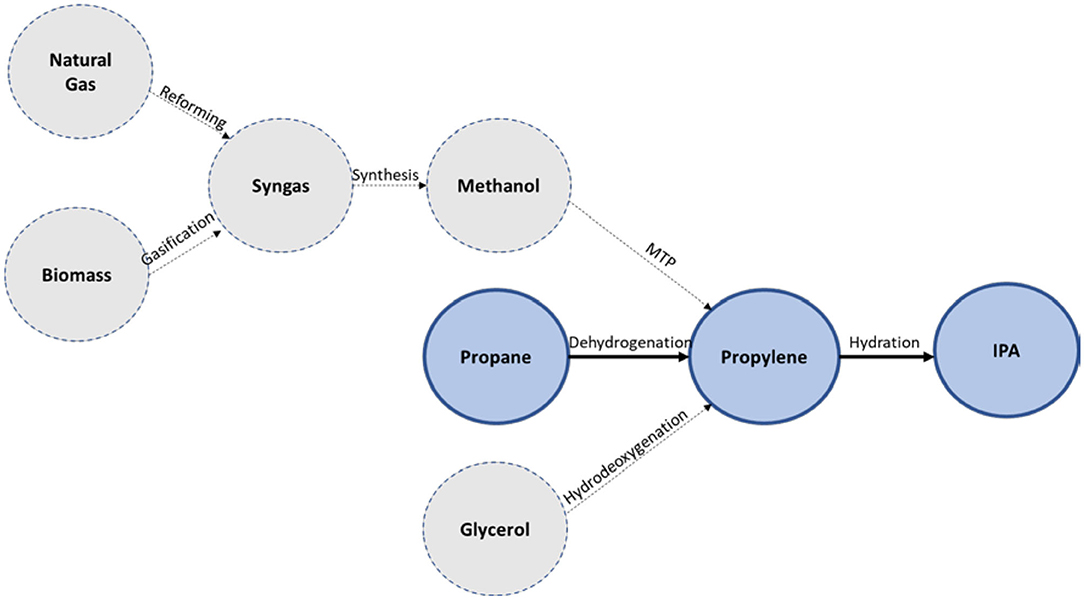
Figure 10. Alternate pathways for mitigating disruption or insufficiency in propane feedstock to produce isopropyl alcohol (adapted from Panjapakkul and El-Halwagi, 2018).
Conclusions and Future Directions
This work has focused on the intersectionality of disasters, resilience, and design of industrial processes. Twelve principal strategies have been identified for creating disaster-resilient designs of industrial processes: Fail-safe by design, (2) redundancy, (3) reconfigurability, (4) modularity/mobility/distributability, (5) repurposability, (6) flexibility, (7) controllability, (8) reliability, (9) recoverability/restorability, (10) rapidity, (11) robustness, and (12) resourcefulness. Process integration has been presented as a powerful framework for current use and future research. Examples of industrial applications have been given to explain the resilience strategies and discuss the research challenges and potential use of process integration in the systematic development of design concepts and tools for resilient design. Since most process design approaches have been driven by techno-economic factors, a major research challenge is to assess resilience and to develop systematic tools to incorporate resilience in greenfield and retrofitting designs. The following are critical research needs and promising directions:
• Integration of design, operation, and control for resilience: The full extent of robustness can be achieved when the design strategies are integrated with operation, control, and scheduling. Recent research efforts in incorporating operability into design especially for intensification objectives (e.g., Tian et al., 2018a,b; Burnak et al., 2019a,b; Demirel et al., 2019 can be used as a platform for addressing resilience.
• Multi-scale approaches to resilience: This paper has focused on the process level. The resilience of a processing facility is strongly tied to the resilience of the external systems and supply chains. Multi-scale approaches to the optimization of designing individual processes, eco-industrial parks, and associated supply chains can provide a valuable framework for creating resilient processes and supply chains (e.g., Juárez-García et al., 2018; Mukherjee and El-Halwagi, 2018; Zhao and You, 2019; Avraamidou et al., 2020).
• Smart Manufacturing, Data Analytics, and Digitalization: Innovations of the 4th industrial revolution can have significant potential to enhance disaster resilience practices in the process industries. Big data analytics, digitization and automation, cloud computing, cyber-physical systems, smart human machine interaction, machine-to-machine communication, decentralization of the data flow, internet-of-things (IoT) inclusion, automatic data exchange, and communication may provide extra layers of protection for handling emergencies. For example, autonomous production and smart manufacturing can show some extra resilience during a pandemic situation like COVID-19, when limited human interaction becomes the norm. Industry 4.0 and smart manufacturing can provide the agility in switching product manufacturing fast for retaining business and fulfilling new demands during the pandemic. It can provide resilience by production-line monitoring, predictive maintenance, smart decision-making, and by providing real-time visibility into raw materials, workforce, and products. Artificial intelligence (AI), Machine Learning (ML), and Augmented Reality (AR) can be the crucial elements to accelerate monitoring and training on resilience and productive manufacturing while keeping pace with the rapid changes. Industry 4.0 and smart manufacturing also come with challenges such as security, protecting intellectual properties/information, and above all operational challenges. Recent contributions in the field (Ogumerem and Pistikopoulos, 2000; Ivanov, 2018; Lee et al., 2019; Bag and Pretorius, 2020; Ma et al., 2020) can be extended to include resilience strategies and integration with smart manufacturing and digitalization.
• Benchmarking designs for resilience: One of the most powerful techniques of process integration is “targeting” which refers to the ability to determine standards of excellence (benchmarks) for a process ahead of detailed design and without commitment to a specific process configuration. There have been numerous contributions in systematically benchmarking various objectives such as minimizing external heating and cooling utilities (e.g., Linnhoff and Hindmarsh, 1983; Papoulias and Grossmann, 1983; Kemp, 2009), minimizing fresh-resource usage and waste discharge (e.g., El-Halwagi et al., 2003; Kazantzi and El-Halwagi, 2005; Foo, 2012), minimizing fresh-water usage and wastewater discharge (e.g., Wang and Smith, 1994), minimizing the use of external mass separating agents and maximizing the use of process mass separating agents (e.g., El-Halwagi and Manousiouthakis, 1989), and maximizing power cogeneration using internal resources (e.g., Klemeš et al., 1997; Mavromatis and Kokossis, 1998; El-Halwagi et al., 2009). There is a critical need to make similar contributions toward benchmarking resilience.
• Resilience metrics for the process industries: Although there have been attempts to develop resilience metrics for general systems and infrastructures, there is a critical need to develop resilience metrics for the process industries especially concerning the characteristics and idiosyncrasies associated with the 12 resilience strategies identified in this work. Toward this goal, recent research efforts have endeavored to use the concept of sustainability-weighted return on investment (El-Halwagi, 2017a) to extend it to include safety and resilience (Guillen-Cuevas et al., 2018; Moreno-Sader et al., 2019). These approaches use the power of process-integration targeting to set resilience within a financial framework.
• Resilience as a pathway to sustainability: Although the fields of sustainable design and resilient design have evolved as separate domains with sustainability focusing on economic, environmental, and societal matters, we are convinced that resilience and safety should be essential components of sustainability. A unified framework should be developed.
Based on the aforementioned discussion, there are still grand challenges in the design of resilient processes. The good news is that fundamental concepts and enabling tools in the field of process integration combined with the advancement in analytics and digitalization can provide an effective framework to aid in the development of resilient designs on industrial processes. Specifically, the systematic approaches of process integration can be used by capitalizing on the following activities which have shown a proven track record in other domains such as sustainability, safety, and profitability (El-Halwagi, 2006, 2017b):
1. Task Identification: The goals of resilience and other process objectives must first transformed into actionable tasks (along the lines of the 12 resilience principles described in this paper).
2. Targeting: Prior to detailed design, it is important to set clear benchmarks to target the process performance with respect to the desired key performance indicators.
3. Generation of Alternatives (Synthesis): Process synthesis provides a powerful framework for creating process alternatives for a given set of inputs to satisfy a certain set of outputs. This approach works well for greenfield (new) designs as well as retrofitting existing designs to meet the new objectives. Upon the generation of the alternatives or the embodiment of the alternatives, multi-criteria decision-making techniques (e.g., optimization) are used to select the top design(s).
4. Analysis of Selected Alternative(s): The generated solution(s) from process synthesis should next be analyzed to predict its detailed characteristics and performance. Process analysis techniques involve computer-aided simulation tools, modeling, empirical/semi-empirical correlations, and assessment of metrics (e.g., resilience, safety, cost, environmental impact). Furthermore, process analysis may include the use of experimental work at the lab and pilot-plant scales, and even tailored experimentation at existing plants.
The value proposition for integrating process design and resilience is substantial with tremendous potential in saving lives, enhancing societal well-being, and reducing economic losses. As an illustration, a group of experts from academia, industry, non-governmental organizations, and emergency response specialists carried out a retrospective analysis for the potential impact of implementing resilient manufacturing strategies in the US Gulf Coast Region (shown by Figure 1). While the estimates varied, the consensus was that about 25% of the economic losses in recent hurricanes were caused by disruptions in production and services, casualties, and spillages associated with manufacturing value chains, and that 40% of these losses could have been averted with the resilient technologies, planning, mitigation, and advanced decision-making methodologies and tools (El-Halwagi, 2019). Much more value can be achieved in terms of protecting lives, livelihoods, public health, and well-being of communities (Hotez et al., 2014; Adeola and Picou, 2017; Benevolenza and DeRigne, 2019).
Extension of effective process integration techniques such as benchmarking, integrated design, multi-scale and multi-objective optimization, integrated design, operation, and control, multi-dimensional metrics, and sustainable design can pave the way to new resilient-design tools and a significant impact on the well-being of the manufacturing sector and adjacent communities.
Data Availability Statement
The raw data supporting the conclusions of this article will be made available by the authors, without undue reservation.
Author Contributions
All authors listed have made a substantial, direct and intellectual contribution to the work, and approved it for publication.
Funding
Funding by the United States National Science Foundation [NSF Award # 1840512, Planning Grant: Engineering Research Center for Resiliency Enhancement and Disaster-Impact Interception (READII) in the Manufacturing Sector] is gratefully acknowledged.
Conflict of Interest
The authors declare that the research was conducted in the absence of any commercial or financial relationships that could be construed as a potential conflict of interest.
The reviewer JP-O declared a past co-authorship with one of the authors ME-H to the handling editor.
References
Abimbola, M., and Khan, F. (2019). Resilience modeling of engineering systems using dynamic object-oriented bayesian network approach. Comput. Indust. Eng. 130, 108–118. doi: 10.1016/j.cie.2019.02.022
Adamo, A., Beingessner, R. L., Behnam, M., Chen, J., Jamison, T. F., Jensen, K. F., et al. (2016). On-demand continuous-flow production of pharmaceuticals in a compact, reconfigurable system. Science 352, 61–67. doi: 10.1126/science.aaf1337
Ade, N., Liu, G., Al-Douri, A. F., El-Halwagi, M. M., and Mannan, M. S. (2018). Investigating the effect of inherent safety principles on system reliability in process design. Process Saf. Environ. Protect. 117, 100–110. doi: 10.1016/j.psep.2018.04.011
Adeola, F. O., and Picou, J. S. (2017). Hurricane katrina-linked environmental injustice: race, class, and place differentials in attitudes. Disasters 41, 228–257. doi: 10.1111/disa.12204
Agrawal, A., Sengupta, D., and El-Halwagi, M. M. (2018). A sustainable process design approach for on-purpose propylene production and intensification. ACS Sustain. Chem. Eng. 6, 2407–2421. doi: 10.1021/acssuschemeng.8b00235
Al-Douri, A., Kazantzi, V., Eljack, F. T., and El-Halwagi, M. M. (2020). Mitigation of operational failures via an economic framework of reliability, availability, and maintainability (RAM) during conceptual design. J. Loss Prev. Process Indust. 67:104261. doi: 10.1016/j.jlp.2020.104261
Al-Fadhli, F. M., Baaqeel, H., and El-Halwagi, M. M. (2019). Modular design of carbon-hydrogen-oxygen symbiosis networks over a time horizon with limited natural resources. Chem. Eng. Process. Process Intensif. 141:107535. doi: 10.1016/j.cep.2019.107535
Allen, R. C., Allaire, D., and El-Halwagi, M. M. (2019). Capacity planning for modular and transportable infrastructure for shale gas production and processing. Ind. Eng. Chem. Res. 58, 5887–5897. doi: 10.1021/acs.iecr.8b04255
Alsuhaibani, A. S., Afzal, S., Challiwala, M., Elbashir, N. O., and El-Halwagi, M. M. (2019). The impact of the development of catalyst and reaction system of the methanol synthesis stage on the overall profitability of the entire plant: a techno-economic study. Catal. Today 343, 191–198. doi: 10.1016/j.cattod.2019.03.070
Avraamidou, S., Baratsas, S. G., Tian, Y., and Pistikopoulos, E. N. (2020). Circular economy-a challenge and an opportunity for process systems engineering. Comput. Chem. Eng. 133:106629. doi: 10.1016/j.compchemeng.2019.106629
Ayyub, B. M. (2014). Systems resilience for multihazard environments: definition, metrics, and valuation for decision making. Risk Anal. 34, 340–355. doi: 10.1111/risa.12093
Bag, S., and Pretorius, J. H. C. (2020). Relationships between industry 4.0, sustainable manufacturing and circular economy: proposal of a research framework. Int. J. Organ. Anal. doi: 10.1108/IJOA-04-2020-2120
Bagajewicz, M. J., and Manousiouthakis, V. (1992). Mass/heat exchange network representation of distillation networks. AIChE J. 38, 1769–1800.
Benevolenza, M. A., and DeRigne, L. (2019). The impact of climate change and natural disasters on vulnerable populations: a systematic review of literature. J. Hum. Behav. Soc. Environ. 29, 266–281. doi: 10.1080/10911359.2018.1527739
Benjamin, M. F. D., Razon, L. F., and Tan, R. R. (2020). “Risk and resilience analysis of integrated biorefineries using input-output modeling,” in Towards Sustainable Chemical Processes (Amsterdam: Elsevier), 99–114.
Bruneau, M., and Reinhorn, A. (2007). Exploring the concept of seismic resilience for acute care facilities. Earthq. Spectra 23, 41–62. doi: 10.1193/1.2431396
Burnak, B., Diangelakis, N. A., Katz, J., and Pistikopoulos, E. N. (2019b). Integrated process design, scheduling, and control using multiparametric programming. Comput. Chem. Eng. 125, 164–184. doi: 10.1016/j.compchemeng.2019.03.004
Burnak, B., Diangelakis, N. A., and Pistikopoulos, E. N. (2019a). Towards the grand unification of process design, scheduling, and control—utopia or reality? Processes 7:461. doi: 10.3390/pr7070461
Caputo, A. C., Kalemi, B., Paolacci, F., and Corritore, D. (2020). Computing resilience of process plants under Na-tech events: methodology and application to sesmic loading scenarios. Reliabil. Eng. Syst. Saf. 195:106685. doi: 10.1016/j.ress.2019.106685
Coy, P. (2020). The Oil Price Crash in One Word: ‘Inelasticity’. Available online at: https://www.bloomberg.com/news/articles/2020-04-20/the-oil-price-crash-in-one-word-inelasticity (accessed August 11, 2020).
Crabtree, E. W., and El-Halwagi, M. M. (1994). Synthesis of environmentally acceptable reactions. AIChE Symp. Ser. 90, 117–127.
CSB (Chemical Safety Hazard Identification Board) (2018). Organic Peroxide Decomposition, Release, and Fire at Arkema Crosby Following Hurricane Harvey Flooding. Washington, DC: CSB Report # 2017-08-I-TX.
de Carvalho Miranda, J. C., Ponce, G. H. S. F., Arellano-Garcia, H., Maciel Filho, R., and Maciel, M. R. W. (2020). Process design and evaluation of syngas-to-ethanol conversion plants. J. Clean. Prod. 269:122078. doi: 10.1016/j.jclepro.2020.122078
Demirel, S. E., Li, J., and Hasan, M. F. (2019). A general framework for process synthesis, integration, and intensification. Ind. Eng. Chem. Res. 58, 5950–5967. doi: 10.1021/acs.iecr.8b05961
Dimitriadis, V. D., and Pistikopoulos, E. N. (1995). Flexibility analysis of dynamic systems. Ind. Eng. Chem. Res. 34, 4451–4462. doi: 10.1021/ie00039a036
Dinh, L. T., Pasman, H., Gao, X., and Mannan, M. S. (2012). Resilience engineering of industrial processes: principles and contributing factors. J. Loss Prev. Process Indust. 25, 233–241. doi: 10.1016/j.jlp.2011.09.003
DiSavino, S. (2020). Explainer: Why Are US Natural Gas Prices in Texas Below Zero? Available online at: https://www.reuters.com/article/us-natgas-pipelines-flaring-explainer-idUSKCN1RL2NL (accessed August 11, 2020).
Dunn, R. F., and El-Halwagi, M. M. (2003). Process integration technology review: background and applications in the chemical process industry. J. Chem. Tech. Biotech. 78, 1011–1021. doi: 10.1002/jctb.738
Ehlinger, V. M., Gabriel, K. J., Noureldin, M. M. B., and El-Halwagi, M. M. (2014). Process design and integration of shale gas to methanol. ACS Sustain. Chem. Eng. 2, 30–37. doi: 10.1021/sc400185b
El-Halwagi, A. M., Kazantzi, V., El-Halwagi, M. M., and Kazantzis, N. (2013). Optimizing safety-constrained solvent selection for process systems with economic uncertainties. J. Loss Prev. Process Indust. 26, 495–498. doi: 10.1016/j.jlp.2012.07.008
El-Halwagi, M. M. (1997). Pollution Prevention through Process Integration: Systematic Design Tools. San Diego, CA: Academic Press.
El-Halwagi, M. M. (2017a). A return on investment metric for incorporating sustainability in process integration and improvement projects. Clean Technol. Environ. Policy (Amsterdam), 19, 611–617. doi: 10.1007/s10098-016-1280-2
El-Halwagi, M. M. (2017b). Sustainable Design through Process Integration: Fundamentals and Applications to Industrial Pollution Prevention, Resource Conservation, Profitability Enhancement, 2nd Edn. Amsterdam: IChemE; Elsevier.
El-Halwagi, M. M. (2019). A retrospective analysis of the impact of resilience enhancement and disaster impact interception (READII): a working session on the US Gulf Coast Region. Presented at the NSF-sponsored workshop on Resilience Enhancement and Disaster Impact Interception (READII) (College Station, TX: The Center for Infrastructure Renewal; Texas A&M University).
El-Halwagi, M. M., Gabriel, F., and Harell, D. (2003). Rigorous graphical targeting for resource conservation via material recycle/reuse networks. Ind. Eng. Chem. Res. 42, 4319-4328. doi: 10.1021/ie030318a
El-Halwagi, M. M., Harell, D., and Spriggs, H. D. (2009). Targeting cogeneration and waste utilization through process integration. Appl. Energy 86, 880–887. doi: 10.1016/j.apenergy.2008.08.011
El-Halwagi, M. M., and Manousiouthakis, V. (1989). Synthesis of mass exchange networks. AIChE J. 35, 1233–1244. doi: 10.1002/aic.690350802
El-Halwagi, M. M., and Spriggs, H. D. (1998). Solve design puzzles with mass integration. Chem. Eng. Prog. 94, 25–44.
Eljack, F., Eden, M., Kazantzi, V., Qin, X., and El-Halwagi, M. M. (2007). Simultaneous process and molecular design- a property based approach. AIChE J. 35, 1232–1239. doi: 10.1002/aic.11141
Gasser, P., Lustenberger, P., Cinelli, M., Kim, W., Spada, M., Burgherr, P., et al. (2019). A review on resilience assessment of energy systems. Sustain. Resilient Infrastruct. 1–27. doi: 10.1080/23789689.2019.1610600
Gong, J., and You, F. (2018). Resilient design and operations of process systems: nonlinear adaptive robust optimization model and algorithm for resilience analysis and enhancement. Comput. Chem. Eng. 116, 231–252. doi: 10.1016/j.compchemeng.2017.11.002
Gowland, R. (1996). Applying inherently safer concepts to a phosgene plant acquisition. Process Saf. Progr. 15, 52–57. doi: 10.1002/prs.680150113
Grossmann, I. E., and Morari, M. (1983). “Operability resiliency and flexibility—process design objectives for a changing world,” in Proceedings Second International Conference Foundations of Computer Aided Process Design (FOCAPD) (Snowmass, CO).
Guillen-Cuevas, K., Ortiz-Espinoza, A. P., Ozinan, E., Jiménez-Gutiérrez, A., Kazantzis, N. K., and El-Halwagi, M. M. (2018). Incorporation of safety and sustainability in conceptual design via a return on investment metric. ACS Sustain. Chem. Eng. 6, 1411–1416. doi: 10.1021/acssuschemeng.7b03802
Hotez, J., Murray, K. O., and Buekens, P. (2014). The gulf coast: a new American underbelly of tropical diseases and poverty. PLoS Negl. Trop. Dis. 8:e2760. doi: 10.1371/journal.pntd.0002760
Ivanov, D. (2018). Structural Dynamics and Resilience in Supply Chain Risk Management. New York, NY: Springer International Publishing.
Jafarinejad, S. (2020). A framework for the design of the future energy-efficient, cost-effective, reliable, resilient, and sustainable full-scale wastewater treatment plants. Curr. Opin. Environ. Sci. Health 13, 91–100. doi: 10.1016/j.coesh.2020.01.001
Jain, P., Pasman, H. J., and Mannan, M. S. (2020). Process system resilience: from risk management to business continuity and sustainability. Int. J. Bus. Continuity Risk Manag. 10, 47–66. doi: 10.1504/IJBCRM.2020.105615
Jain, P., Pasman, H. J., Waldram, S., Pistikopoulos, E., and Mannan, M. S. (2018). Process resilience analysis framework (PRAF): a systems approach for improved risk and safety management. J. Loss Prev. Process Ind. 5, 61–73. doi: 10.1016/j.jlp.2017.08.006
Jain, P., Pasman, H. J., Waldram, S. P., Rogers, W. J., and Mannan, M. S. (2017). Did we learn about risk control since Seveso? Yes, we surely did, but is it enough? An historical brief and problem analysis. J. Loss Prev. Process Ind. 49, 5–17. doi: 10.1016/j.jlp.2016.09.023
Juárez-García, M., Ponce-Ortega, J. M., and El-Halwagi, M. M. (2018). A disjunctive programming approach for optimizing carbon, hydrogen and oxygen symbiosis networks. Process Integr. Optimization Sustain. 3, 199–212. doi: 10.1007/s41660-018-0065-y
Kazantzi, V., El-Halwagi, A. M., Kazantzis, N., and El-Halwagi, M. M. (2013). Managing uncertainties in a safety-constrained process system for solvent selection and usage: an optimization approach with technical, economic, risk factors. Clean Techn. Environ. Policy 15, 213–224. doi: 10.1007/s10098-012-0516-z
Kazantzi, V., and El-Halwagi, M. M. (2005). Targeting material reuse via property integration. Chem. Eng. Prog. 101, 28–37.
Kazi, M. -K., Eljack, F., Amanullah, M., AlNouss, A., and Kazantzi, V. (2018). A process design approach to manage the uncertainty of industrial flaring during abnormal operations. Comput. Chem. Eng. 117, 191–208. doi: 10.1016/j.compchemeng.2018.06.011
Kazi, M. -K., Mohammed, F., AlNouss, A. M. N., and Eljack, F. (2015). Multi-objective optimization methodology to size cogeneration systems for managing flares from uncertain sources during abnormal process operations. Comput. Chem. Eng. 76, 76–86. doi: 10.1016/j.compchemeng.2015.02.012
Kemp, I. (2009). Pinch Analysis and Process Integration - A User Guide on Process Integration for the Efficient Use of Energy, 2nd Edn. Oxford: Butterworth-Heinemann.
Klamka, J. (1991). Controllability of Dynamical Systems, Vol. 48. Dordrecht: Kluwer Academic Publishers, xvi+–248.
Klemeš, J., Dhole, V. R., Raissi, K., Perry, S. J., and Puigjaner, L. (1997). Targeting and design methodology for reduction of fuel, power and CO2 on total sites. Appl. Thermal Eng. 17, 993–1003. doi: 10.1016/S1359-4311(96)00087-7
Lee, J., Cameron, I., and Hassall, M. (2019). Improving process safety: what roles for digitalization and industry 4.0? Process Saf. Environ. Protect. 132, 325–339. doi: 10.1016/j.psep.2019.10.021
Lenhoff, A. M., and Morari, M. (1982). Design of resilient processing plants—I process design under consideration of dynamic aspects. Chem. Eng. Sci. 37, 245–258. doi: 10.1016/0009-2509(82)80159-0
Linnhoff, B., and Hindmarsh, E. (1983). The pinch design method for heat exchanger networks. Chem. Eng. Sci. 38, 745–763. doi: 10.1016/0009-2509(83)80185-7
Ma, S., Zhang, Y., Liu, Y., Yang, H., Lv, J., and Ren, S. (2020). Data-driven sustainable intelligent manufacturing based on demand response for energy-intensive industries. J. Clean. Prod. 274:123155. doi: 10.1016/j.jclepro.2020.123155
Majozi, T. (2010). Batch Chemical Process Integration: Analysis, Synthesis, and Optimization. Heidelberg: Springer.
Mavromatis, S. P., and Kokossis, A. C. (1998). Conceptual optimisation of utility networks for operational variations—targets I, level optimisation. Chem. Eng. Sci. 53, 1585–1608. doi: 10.1016/S0009-2509(97)00431-4
Mencarelli, L., Chen, Q., Pagot, A., and Grossmann, I. E. (2020). A review on superstructure optimization approaches in process system engineering. Comput. Chem. Eng. 136:106808. doi: 10.1016/j.compchemeng.2020.106808
Mohan, T., and El-Halwagi, M. M. (2007). An algebraic targeting approach for effective utilization of biomass in cogeneration systems through process integration. J. Clean Tech. Env. Policy 9, 13–25. doi: 10.1007/s10098-006-0051-x
Moreno-Sader, K., Jain, P., Tenorio, L. C. B., Mannan, M. S., and El-Halwagi, M. M. (2019). Integrated approach of safety, sustainability, reliability, and resilience analysis via a return on investment metric. ACS Sustain. Chem. Eng. 7, 19522–19536. doi: 10.1021/acssuschemeng.9b04608
Mukherjee, R., Asani, R. R., Boppana, N., and El-Halwagi, M. M. (2020). Performance evaluation of shale gas processing and NGL recovery plant under uncertainty of the feed composition. J. Nat. Gas Sci. Eng. 83:103517. doi: 10.1016/j.jngse.2020.103517
Mukherjee, R., and El-Halwagi, M. M. (2018). Reliability of C-H-O symbiosis networks under source streams uncertainty. Smart Sustain. Manufact. Syst. 2, 132–153. doi: 10.1520/SSMS20180022
Noureldin, M. B. (2011). Pinch Technology and Beyond: New Vistas on Energy Efficiency Optimization. New York, NY: Nova Science Publishers.
Ogumerem, G. S., and Pistikopoulos, E. N. (2000). Smart manufacturing. Kirk Othmer Encyclopedia Chem. Technol. 1–10. doi: 10.1002/0471238961.koe00048
Oke, D., Mukherjee, R., Sengupta, D., Majozi, T., and El-Halwagi, M. M. (2020). Hybrid regeneration network for flowback water management. Ind. Eng. Chem. Res. 59, 13143–13159. doi: 10.1021/acs.iecr.0c01361
Olyaei, M. A., Karamouz, M., and Farmani, R. (2018). Framework for assessing flood reliability and resilience of wastewater treatment plants. J. Environ. Eng. 144:04018081. doi: 10.1061/(ASCE)EE.1943-7870.0001422
Onel, M., Burnak, B., and Pistikopoulos, E. N. (2019). Integrated data-driven process monitoring and explicit fault-tolerant multiparametric control. Ind. Eng. Chem. Res. 59 2291–2306. doi: 10.1021/acs.iecr.9b04226
Orosz, Á., Pimentel, J., and Friedler, F. (2020). General formulation for the resilience of processing systems. Chem. Eng. Trans. 81, 859–864. doi: 10.3303/CET2081144
Ortiz-Espinoza, A. P., Kazantzi, V., Eljack, F. T., Jimenez-Gutierrez, A., El-Halwagi, M. M., and Kazantzis, N. K. (2019). A framework for design under uncertainty including inherent safety, environmental assessment and economic performance of chemical processes. Ind. Eng. Chem. Res. 58, 13239–13248. doi: 10.1021/acs.iecr.9b02349
Panjapakkul, W., and El-Halwagi, M. M. (2018). Techno-economic analysis of alternative pathways of isopropanol production. ACS Sustain. Chem. Eng. 6, 10260–10272. doi: 10.1021/acssuschemeng.8b01606
Papoulias, S. A., and Grossmann, I. E. (1983). A structural optimization approach in process synthesis. II. Heat recovery networks. Comput. Chem. Eng. 7, 707–721. doi: 10.1016/0098-1354(83)85023-6
Park, J., Seager, T. P., and Rao, S. C. (2011). Lessons in risk-versus resilience-based design and management. Integr. Environ. Assess. Manag. 7, 396–399. doi: 10.1002/ieam.228
Park, S., Xu, S., Rogers, W., Pasman, H., and El-Halwagi, M. M. (2020). Incorporating inherent safety during the conceptual process design stage: a literature review. J. Loss Prev. Process Indust. 63:104040. doi: 10.1016/j.jlp.2019.104040
Pasman, H., Kottawar, K., and Jain, P. (2020). Resilience of process plant: what, why, and how resilience can improve safety and sustainability. Sustainability 12:6152. doi: 10.3390/su12156152
Pham, V., and El-Halwagi, M. M. (2012). Process synthesis and optimization of biorefinery configurations. AIChE J. 58, 1212–1221. doi: 10.1002/aic.12640
Pistikopoulos, E. N., Faísca, N. P., Kouramas, K. I., and Panos, C. (2009). Explicit robust model predictive control. IFAC Proc. 42, 243–248. doi: 10.3182/20090712-4-TR-2008.00037
Pistikopoulos, E. N., and Grossmann, I. E. (1989). Optimal retrofit design for improving process flexibility in nonlinear systems—II. Optimal level of flexibility. Comput. Chem. Eng. 13, 1087–1096. doi: 10.1016/0098-1354(89)87013-9
Ponce-Ortega, J. M., Pham, V., El-Halwagi, M. M., and El-Baz, A. A. (2012). A disjunctive programming formulation for the optimal design of biorefinery configurations. Ind. Eng. Chem. Res. 51, 3381–3400. doi: 10.1021/ie201599m
Reniers, G., Khakzad, N., Cozzani, V., and Khan, F. (2018). The impact of nature on chemical industrial facilities: dealing with challenges for creating resilient chemical industrial parks. J. Loss Prev. Process Indust. 56, 378–385. doi: 10.1016/j.jlp.2018.09.010
Righi, A. W., Saurin, T. A., and Wachs, P. (2015). A systematic literature review of resilience engineering: research areas and a research agenda proposal. Reliabil. Eng. Syst. Saf. 141, 142–152. doi: 10.1016/j.ress.2015.03.007
Rotstein, E., Resasco, D., and Stephanopoulos, G. (1982). Studies on the synthesis of chemical reaction paths - I. reaction characteristics in the (ΔG, T) space and a primitive synthesis procedure. Chem. Eng. Sci. 37, 1337–1352. doi: 10.1016/0009-2509(82)85006-9
Roy, N., Eljack, F., Jiménez-Gutiérrez, A., Zhang Thiruvenkataswamy, B., El-Halwagi, M., and Mannan, M. S. (2016). A review of safety indices for process design. Curr. Opin. Chem. Eng. 14, 42–48. doi: 10.1016/j.coche.2016.07.001
Rubio-Castro, E., Serna-González, M., Ponce-Ortega, J. M., and El-Halwagi, M. M. (2013). Synthesis of cooling water systems with multiple cooling towers. Appl. Thermal Eng. 50, 957–974. doi: 10.1016/j.applthermaleng.2012.06.015
Salehi, V., and Veitch, B. (2020). Measuring and analyzing adaptive capacity at management levels of resilient systems. J. Loss Prev. Process Indust. 63:104001. doi: 10.1016/j.jlp.2019.104001
Sengupta, D., and Yelvington, P. (2020). Modular intensified processes promote resilient manufacturing. Chem. Eng. Progr. 25.
Smith, D. J. (2000). Cogeneration, distributed generation and peak shaving drive the market for small gas turbines. Power Eng. 104:70. Available online at: https://www.power-eng.com/2000/10/01/cogeneration-distributed-generation-and-peak-shaving-drive-the-market-for-small-gas-turbines/
Son, C., Sasangohar, F., Neville, T., Peres, S. C., and Moon, J. (2020). Investigating resilience in emergency management: an integrative review of literature. Appl. Ergon. 87:103114. doi: 10.1016/j.apergo.2020.103114
Swaney, R. E., and Grossmann, I. E. (1985). An index for operational flexibility in chemical process design. Part I: formulation and theory. AIChE J. 31, 621–630. doi: 10.1002/aic.690310412
Taleb-Berrouane, M., and Khan, F. (2019). Dynamic resilience modelling of process systems. Chem. Eng. Trans. 77, 313–318. doi: 10.3303/CET1977053
Thiel, M. W., Gupta, D., Miller, S., and Gill, J. (2020). “A containment building and scrubber design for reduction of risk in a process with a highly hazardous chemicals,” in 2012 Southwest Process Technology Conference, Proceedings of the 4th AIChE Regional Process Technology Conference. Available online at: https://www.aiche.org/conferences/southwest-process-technology-conference/2012/proceeding/paper/containment-building-and-scrubber-design-reduction-risk-process-highly-hazardous-chemic (accessed September 18, 2020).
Thomaidis, T. V., and Pistikopoulos, E. N. (1994). Integration of flexibility, reliability and maintenance in process synthesis and design. Comput. Chem. Eng. 18, S259–S263. doi: 10.1016/0098-1354(94)80043-X
Tian, Y., Demirel, S. E., Hasan, M. F., and Pistikopoulos, E. N. (2018a). An overview of process systems engineering approaches for process intensification: state of the art. Chem. Eng. Process. Process Intensif. 133, 160–210. doi: 10.1016/j.cep.2018.07.014
Tian, Y., Mannan, M. S., and Pistikopoulos, E. N. (2018b). Towards a systematic framework for the synthesis of operable process intensification systems. Comput. Aided Chem. Eng. 44, 2383–2388. doi: 10.1016/B978-0-444-64241-7.50392-X
Tian, Y., Pappas, I. S., Avraamidou, S., and Pistikopoulos, E. N. (2019). “A modular approach to process integration and intensification,” in 2019 AIChE Annual Meeting (Orlando, FL: AIChE).
Tovar-Facio, J., Eljack, F., Ponce-Ortega, J. M., and El-Halwagi, M. M. (2017). Optimal design of multi-plant cogeneration systems with uncertain flaring and venting. ACS Sustain. Chem. Eng. 5, 675–688. doi: 10.1021/acssuschemeng.6b02033
Vairo, T., Reverberi, A. P., and Fabiano, B. (2020). From risk assessment to resilience assessment. An application to a HazMat storage plant. Chem. Eng. 83.
Wang, Y. P., and Smith, R. (1994). Wastewater minimisation. Chem. Eng. Sci. 49, 981–1006. doi: 10.1016/0009-2509(94)80006-5
Woods, D. D. (2015). Four concepts for resilience and the implications for the future of resilience engineering. Reliabil. Eng. Syst. Saf. 141, 5–9. doi: 10.1016/j.ress.2015.03.018
Yarveisy, R., Gao, C., and Khan, F. (2020). A simple yet robust resilience assessment metrics. Reliabil. Eng. Syst. Saf. 197:106810. doi: 10.1016/j.ress.2020.106810
Yu, D. J., Schoon, M. L., Hawes, J. K., Lee, S., Park, J., Rao, P. S. C., et al. (2020). Toward general principles for resilience engineering. Risk Analysis. 1509–1537. doi: 10.1111/risa.13494
Zhao, S., and You, F. (2019). Resilient supply chain design and operations with decision-dependent uncertainty using a data-driven robust optimization approach. AIChE J. 65, 1006–1021. doi: 10.1002/aic.16513
Keywords: systems, process design, process integration, disaster, resilience
Citation: El-Halwagi MM, Sengupta D, Pistikopoulos EN, Sammons J, Eljack F and Kazi M-K (2020) Disaster-Resilient Design of Manufacturing Facilities Through Process Integration: Principal Strategies, Perspectives, and Research Challenges. Front. Sustain. 1:595961. doi: 10.3389/frsus.2020.595961
Received: 18 August 2020; Accepted: 20 October 2020;
Published: 16 November 2020.
Edited by:
Ruchi Agrawal, Indian Oil Corporation, IndiaReviewed by:
Yogendra Shastri, Indian Institute of Technology Bombay, IndiaJosé María Ponce-Ortega, Michoacana University of San Nicolás de Hidalgo, Mexico
Copyright © 2020 El-Halwagi, Sengupta, Pistikopoulos, Sammons, Eljack and Kazi. This is an open-access article distributed under the terms of the Creative Commons Attribution License (CC BY). The use, distribution or reproduction in other forums is permitted, provided the original author(s) and the copyright owner(s) are credited and that the original publication in this journal is cited, in accordance with accepted academic practice. No use, distribution or reproduction is permitted which does not comply with these terms.
*Correspondence: Mahmoud M. El-Halwagi, ZWwtaGFsd2FnaUB0YW11LmVkdQ==