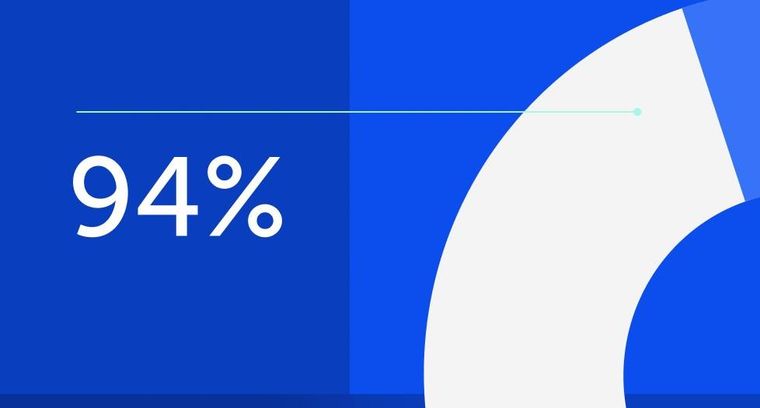
94% of researchers rate our articles as excellent or good
Learn more about the work of our research integrity team to safeguard the quality of each article we publish.
Find out more
BRIEF RESEARCH REPORT article
Front. Space Technol., 22 August 2024
Sec. Advanced Space Engineering
Volume 5 - 2024 | https://doi.org/10.3389/frspt.2024.1448787
This article is part of the Research TopicNext generation of materials for space applicationsView all 5 articles
Sustainable structures are an important area of research, particularly for anticipated extended human presence on the Moon or Mars. Persistent human presence on the Moon will require building materials that are already present at the site to construct bases. The high cost associated with reinforcing metal (rebar) in mission payloads necessitates the exploration of alternative reinforcement methods for sustained lunar bases. Human hair is strong in tensile strength and will become available in any long-term mission. By using otherwise wasted hair instead of heavy metal, mission payloads and costs could be lowered. Concrete workability, compressive strength, and porosity were measured for a series of different cement compositions. These compositions consisted of combinations of Ordinary Portland Cement (OPC), lunar regolith, deionized (DI) water and human hair. Increased workability and porosity were found for increasing hair concentrations. Compressive strength slightly decreased with increased hair concentration.
To construct any permanent structures on the moon or exoplanet, astronauts will need to source the building materials locally using lunar soil and transported resources, which increases mission costs. A local resource that can be found on the moon is lunar regolith, which can significantly reduce the amount of Ordinary Portland Cement (OPC) needed from the earth. When working with cement, metal rebar is utilized to increase the tensile strength. The greatest issue with metal rebar is the further increased cost due to weight and amount of rebar that would be required to construct the permanent structures. One biomaterial that is high in tensile strength is hair. Human hair grows at about 1.25 cm (½ inch) per month (Meghwar et al., 2020). It is made of keratin microfibrils and is considered a bio elastomer due to its elastic qualities. Keratin is a protein and among the toughest biological materials, with both high toughness and high modulus of elasticity. Human hair has a tensile strength of about 225 MPa (Wang et al., 2016). With any long-term mission, personnel may desire to cut or shave their hair for comfort or hygiene reasons. Rather than waste this resource, such hair may be utilized to produce stronger tensile strength building material. Human hair may be ideal for use in concrete if used in the correct proportion and it is completely biodegradable, renewable, and easily available at a negligible cost since it is a waste material (Batham, 2018; Patel and Srivastava, 2021).
Bheel et al. (2018) found 0.25% addition of human hair in plain concrete to increase strength. Meghwar et al. (2020) reported that a 1% addition of human scalp hair of various sizes increased tensile strength in cylindrical concrete samples, but decreased density and workability (Meghwar et al., 2020). Human hair addition of 1.5% has been reported to impede the mixing process, but to improve compressive strength (Zaidi et al., 2018). Gupta (2014) claimed that any kind of hair could be used to increase compressive strength for fly ash based cement (Gupta, 2014). For oil well cement, an addition of 0.4% hair by volume was found to improve cement properties (Al-Darbi et al., 2006). An optimal amount of human hair of 2% has been reported for improvement of flexural and compressive strength in concrete (Manjunatha et al., 2021). Kanwal et al. (2020) found 1.5% human hair addition to improve compressive strength, but noted workability issues (Kanwal et al., 2020). With added silica fume, human hair has been found to increase compressive, flexural, and split tensile strengths (Akbar et al., 2023). The present work investigates the slump, split tensile strength, and porosity of regolith-based cement with human hair added.
Commercial grade from Quikrete Portland cement type I/II (no. 1124) was purchased from Lowe’s. It complies with the American Society for Testing Materials (ASTM) C 150 specifications.
One type of Lunar regolith was used in this study, i.e., Lunar Highlands Stimulant (LHS-1) as shown in Table 1. This was used to create 40% lunar regolith with 60% OPC batches. They were procured from the Exolith Lab (Oviedo, FL, USA).
Table 1. Lunar Regolith (Exolith Lab, 2023) and typical OPC Composition (Holcim (US) Inc. 2020) in mass% concentrations.
Human scalp hair was donated by and collected from a local hair cutting facility, Patterson’s Barber Shop, Ruston, LA. Hair was prepared by drying the hair at ∼378 K (105°C) to remove excess moisture and cut to approximately 10 mm in length before adding it to dry cement. This hair size was chosen to ensure homogeneous dispersion in the cement mortar, reduce entanglement, and decrease shrinkage after casting (Balaguru and Shah, 1992; Chung, 2005; Manjunatha et al., 2021). A mixture of hair shapes was used.
Cement samples were prepared following the ASTM C192 standards. Cylindrical plastic mold casings were used for each batch. Each mold casting was 5.08 cm (2 inches) in diameter and 10.16 cm (4 inches) in height. For this project, a control of OPC was compared to the lunar regolith-based cement with three different concentrations of hair, 0.5%, 1%, and 2%. LHS-1 and OPC were used to create 40% lunar regolith and 60% OPC batches by mass. Using partial regolith at this ratio was recommended by our NASA collaborators. The dried hair (without leftover moisture) was cut to approximately 10 mm segments and stirred with dry cement before being evenly dispersed in the cement bowl. Orientation was impossible to achieve since long hair length segments were not used. Long segments do not give optimal workability and compressive strength (Balaguru and Shah, 1992). Additionally, long hair segments would clog any future automatic mixer-processors. We did not consider the effects of the shape of the hair for this study and a future investigation is planned for that study. Each batch was prepared using a KitchenAid 600™ mixer. Table 2 shows each cement mixture and its respective compositions. The OPC and lunar regolith-based simulant were slowly combined with water until a consistent mixture formed.
The cement mixture was poured into a frustum mini-slump cone (height = 57.0 mm, top internal diameter = 18.8 mm, and bottom internal diameter = 36.8 mm) over a grid plate to measure the slump height and area. This simulates a miniature version of the conventional slump test, a modification of the standard ASTM C134-00 slump cone test. The cone was then lifted upward slowly to allow the cement to spread on the grid plate. The area of the cement spread as well as the height were recorded, and these values used as a measure of the workability of the cement mixture. The average slump height and slump spreading area were found for three samples from three batches of each type of concrete mixture to ensure consistency and minimize standard error. Supplementary Figure S1 shows an image of the method used.
The cement mixture after slump testing was poured into cylindrical molds of 5.08 cm diameter and 10.16 cm height and allowed to cure for 48 h at room temperature, as found to be necessary for regolith-based cement. After 48 h, the cement samples were removed from the molds and placed into a lime bath to allow for curing. The lime bath consisted of 2 g of calcium hydroxide for every 1 L of deionized (DI) water at room temperature ∼298 K (25°C) and atmospheric pressure for 28 days, the standard method for curing.
Split tensile strength testing was performed for each concrete sample after the 28-day curing period. A load rate was manually applied until the sample failed. Once the sample failed, the machine would stop applying the force and display the resulting strength of the sample. The split tensile strength reflected the amount of force the cement sample could carry before breaking. A Test Mark industries compression tester (East Palestine, OH, USA) was used for split tensile testing following ASTM C 496 standard test protocol. In this method, the cylinder is placed sideways in the tester (Supplementary Figure S2).
After tensile testing, each sample and its fractured pieces were labeled and bagged. A fragment of cement from each sample 5–10 g in size was weighed to be used for porosity testing. The weight of each fragment was recorded prior to being submerged into a DI water bath for 24 h to ensure complete saturation. After 24 h, the pieces were removed from the water, lightly patted with a paper towel, and reweighed. Next, the saturated pieces were placed into a drying oven at 105°C to remove moisture from the pores of the cement. After 24, 48, and 72 h, the pieces were removed from the drying oven to cool for 1 h before recording the weight of the pieces and placing them back in the oven. The water retention capacity of each sample when saturated, measured relative to its mass after a 24-h drying period, was used as a quantitative indicator of the material’s porosity. Consequently, the final porosity for each type of concrete mixture, as detailed in Supplementary Table S3: Porosity Data, represents the average porosity calculated from 24 samples. These samples were derived from three batches, with each batch consisting of eight samples, ensuring consistency and minimizing standard error. The percentage of water that each piece held while saturated compared to the 72-h dry mass was considered as a measure of the material’s porous capacity or porosity. This test is preferred compared to mercury intrusion due to the toxicity of mercury.
The results for the mini-slump test height and area performed are shown in Figure 1. The general trend was for the slump height to decrease with increased hair content. Similarly, the slump area decreased with increased hair content, with little difference seen among the samples with hair. As the trend is seen from both measurements, the smaller slump height and area indicates that as hair content increases the cement mixes become less workable with hair addition. These findings are similar to those found in the literature (Kanwal et al., 2020; Meghwar et al., 2020; Zaidi et al., 2018). Another factor to be considered is that adding regolith may change workability compared to samples containing only OPC. A similar study using 30% LHS-1 with 70% OPC indicated that slump increased with regolith addition (Sagar et al., 2024). Thus, hair addition does tend to reduce workability, although a difference cannot be confirmed for the 0.5% hair addition compared to OPC.
Figure 1. Slump for the lunar regolith-based cement at different hair concentrations, (A) slump height, (B) slump area.
After the curing period of 28 days, Figure 2A shows the results for split tensile compressive strength for the different concentrations of hair within the lunar regolith-based cement. The split tensile strength of the samples is similar for the hair free and 0.5% hair concentrations. Similar values are also seen when comparing the 1% and 2% hair concentrations. A larger decrease in split tensile compressive strength when comparing 0.5% and 1% hair concentrations is seen. For the highest compressive strength, no hair or 0.5% hair addition is the most desirable. These results correspond most closely to those of Meghwar et al. (2020) (Meghwar et al., 2020). OPC replacement with LHS-1 has been reported to decrease compressive strength. In a study with 30% replacement of OPC with LHS-1, compressive strength was reduced by nearly 75% compared to OPC with no replacement (Sagar et al., 2024). Although compressive strength and split tensile strength are different, adding hair to the regolith-containing binder may improve its structural integrity.
Figure 2. (A) Tensile split stress of cured regolith-based cement samples. (B) Porosity of cured regolith-based cement samples.
Figure 2B shows the results of the porosity testing. A much higher porosity was found in the samples that did not contain regolith or hair. Replacement of OPC with regolith has been reported to slightly decrease porosity (Sagar et al., 2024). Once hair is added to the regolith-based samples, the porosity increases slightly with increased hair content. When properly dispersed in the cement samples, hair may have a beneficial effect on porosity. Lower porosity is desirable for cement as this tends to decrease the risk of cracking and corrosion. The outside surfaces of a hair contains overlapping scales that can absorb as much moisture as 35% of the hair’s mass, particularly in a high pH environment (Al-Darbi et al., 2006). OPC is known to be of high pH when mixed with water, so that a hair’s surface scales could absorb and trap the cement binder after curing. This could explain the lower porosity of the hair containing samples.
Analysis of the data collected and presented demonstrates that up to 0.5% hair can be added to a regolith-based cement without a significant decrease in workability compared to OPC. Split tensile strength is similar for standard OPC and regolith-based cement samples if 0.5% hair is added. An increase in hair content above 0.5% leads to increased porosity. The increased porosity seen in the cement with higher hair content may have been the leading factor in the decreased tensile strength for samples with 1% and 2% hair added. Future work needed includes finding the effects of varying hair length and shapes. The advantages of hair use in lunar bases include less pollution of the lunar surface with discarded hair, less of a requirement for rebar in the mission payload, and the ease with which hair can be added to the regolith-based cement compared to molding cement around rebar.
The original contributions presented in the study are included in the article/Supplementary Material, further inquiries can be directed to the corresponding author.
MT: Supervision, Data curation, Investigation, Methodology, Writing–original draft. AS: Data curation, Investigation, Methodology, Writing–original draft. EA: Investigation, Methodology, Writing–original draft. VS: Methodology, Writing–review and editing, Supervision. JL: Supervision, Writing–review and editing, Conceptualization, Funding acquisition, Project administration. SG: Investigation, Writing–original draft. SA: Investigation, Supervision, Writing–review and editing.
The author(s) declare that financial support was received for the research, authorship, and/or publication of this article. This work was supported by the Board of Regents of the State of Louisiana [LEQSF (2020-2024)-LaSPACE] and the NASA LaSPACE LURA program (Federal Award No. 80NSSC20M0110).
The authors want to thank Drs. Sven Eklund and Yuri Lvov of Louisiana Tech University for supporting this project with different tests and advice.
The authors declare that the research was conducted in the absence of any commercial or financial relationships that could be construed as a potential conflict of interest.
All claims expressed in this article are solely those of the authors and do not necessarily represent those of their affiliated organizations, or those of the publisher, the editors and the reviewers. Any product that may be evaluated in this article, or claim that may be made by its manufacturer, is not guaranteed or endorsed by the publisher.
The Supplementary Material for this article can be found online at: https://www.frontiersin.org/articles/10.3389/frspt.2024.1448787/full#supplementary-material
Akbar, M., Pan, H., Ou, G., Umar, T., and Hussain, Z. (2023). Effect of human hair fibers on the performance of concrete incorporating high dosage of silica fume. Appl. Sci. Switz. 13 (1), 124. doi:10.3390/app13010124
Al-Darbi, M. M., Saeed, N. O., Ajijolaiya, L. O., and Islam, M. R. (2006). A novel oil well cementing technology using natural fibers. Petroleum Sci. Technol. 24 (11), 1267–1282. doi:10.1081/LFT-200056771
Balaguru, P. N., and Shah, S. P. (1992). Fiber-reinforced cement composites. New York, NY, USA: McGraw-Hill.
Batham, G. (2018). Recent innovations in concrete reinforced with human hair: a review. Int. Res. J. Eng. Technol. 05 (06), 3128–3130.
Bheel, N., Abbasi, S., Meghwar, S., and Shaikh, F. (2018). Effect of human hair as fibers in cement concrete. Sustain. Dev. Civ. Eng., 1–6.
Chung, D. D. L. (2005). Dispersion of short fibers in cement. J. Mater. Civ. Eng. 17 (4), 379–383. doi:10.1061/(ASCE)0899-1561(2005)17:4(379)
Gupta, A. (2014). Human hair “waste” and its utilization: gaps and possibilities. J. Waste Manag. 2014, 1–17. doi:10.1155/2014/498018
Kanwal, H., Aslam, M. S., Mughal, T. L., Asim, M., and Memon, R. M. (2020). Human hair as fiber reinforced concrete for enhancement of tensile strength of concrete. Mehran Univ. Res. J. Eng. Technol. 39 (1), 63–70. doi:10.22581/muet1982.2001.07
Manjunatha, M., Kvgd, B., Vengala, J., Manjunatha, L. R., Shankara, K., and Kumar Patnaikuni, C. (2021). Experimental study on the use of human hair as fiber to enhance the performance of concrete: a novel use to reduce the disposal challenges. Mater. Today Proc. 47, 3966–3972. doi:10.1016/j.matpr.2021.04.039
Meghwar, S. L., Khaskheli, G. B., and Kumar, A. (2020). Human scalp hair as fiber reinforcement in cement concrete. Mehran Univ. Res. J. Eng. Technol. 39 (2), 443–452. doi:10.22581/muet1982.2002.20
Patel, A., and Srivastava, A. (2021). Study of human hair reinforced cement concrete. Int. Res. J. Eng. Technol. 08 (01), 1759–1762.
Sagar, V., Mekalip Lauren, M., and Lynam Joan, G. (2024). Membrane distillation of synthetic urine for use in space structural habitat systems. Green Process. Synthesis 13 (1), 1599–1604. doi:10.1515/gps-2023-0197
Wang, B., Yang, W., McKittrick, J., and Meyers, M. A. (2016). Keratin: structure, mechanical properties, occurrence in biological organisms, and efforts at bioinspiration. Prog. Mater. Sci. 76, 229–318. doi:10.1016/j.pmatsci.2015.06.001
Keywords: moon, sustainable, hair, cement, tensile strength, porosity, workability
Citation: Tarikuzzaman M, Shank AM, Agan EG, Sagar V, Lynam JG, Gordon Ⅱ ST and Alam S (2024) Tensile strength and porosity of regolith-based cement with human hair. Front. Space Technol. 5:1448787. doi: 10.3389/frspt.2024.1448787
Received: 13 June 2024; Accepted: 12 August 2024;
Published: 22 August 2024.
Edited by:
Syafiqah Nur Azrie Safri, Universiti Tun Hussein Onn Malaysia, MalaysiaReviewed by:
Funmilola Oluwafemi, National Space Research and Development Agency (NASRDA), NigeriaCopyright © 2024 Tarikuzzaman, Shank, Agan, Sagar, Lynam, Gordon Ⅱ and Alam. This is an open-access article distributed under the terms of the Creative Commons Attribution License (CC BY). The use, distribution or reproduction in other forums is permitted, provided the original author(s) and the copyright owner(s) are credited and that the original publication in this journal is cited, in accordance with accepted academic practice. No use, distribution or reproduction is permitted which does not comply with these terms.
*Correspondence: Joan G. Lynam, bHluYW1AbGF0ZWNoLmVkdQ==
Disclaimer: All claims expressed in this article are solely those of the authors and do not necessarily represent those of their affiliated organizations, or those of the publisher, the editors and the reviewers. Any product that may be evaluated in this article or claim that may be made by its manufacturer is not guaranteed or endorsed by the publisher.
Research integrity at Frontiers
Learn more about the work of our research integrity team to safeguard the quality of each article we publish.