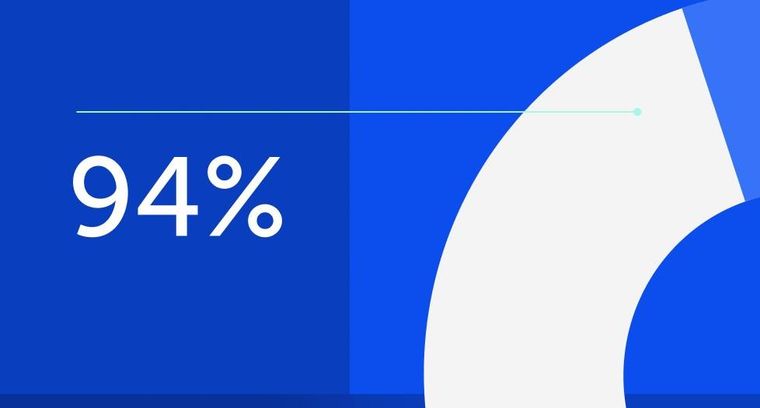
94% of researchers rate our articles as excellent or good
Learn more about the work of our research integrity team to safeguard the quality of each article we publish.
Find out more
REVIEW article
Front. Space Technol., 13 September 2023
Sec. Advanced Space Engineering
Volume 4 - 2023 | https://doi.org/10.3389/frspt.2023.1253419
This article is part of the Research TopicNext generation of materials for space applicationsView all 5 articles
In the last years space technologies have made giant leaps, increasing the feasibility of human exploration and colonization of other celestial bodies. The Moon and Mars have become appealing in these terms, but autonomy, adaptability and high reliability are inevitably needed in long-term missions. Furthermore, new generation spacecraft will have to face challenges related to the degradation of materials and the continuous exposure to the threats of space environment. Novel materials and technologies must hence be developed to satisfy future missions requirements. This paper aims at giving a clear and organic overview of the describes the most significant innovations in the field of materials for space applications, along with the related advantages and challenges. After introducing the main environmental factors in space and their possible risks and effects on materials, the authors proceed with the description of novel materials for space applications, subdivided into polymers, metals, semiconductors, composites, and mixtures. Innovations in manufacturing techniques and in-situ resource utilization are also briefly presented before moving to final considerations on the limitations and future challenges for these innovative materials.
With today’s technological advances the dream of both manned and unmanned exploration and colonization of other celestial bodies is becoming more and more achievable. Two of the most appealing destinations are currently represented by the Moon and Mars.
The exploration of the Moon is of paramount importance since it can prepare to missions towards more distant celestial bodies. The establishment of a lunar base would build the skills required for long-term missions to other planets, such as the creation of essential supplies from in-situ resources. In addition to this, the Moon is still very interesting from a scientific point of view (Freeman, 2023). On the other hand, the proximity and similarity of Mars to the Earth makes it an inevitable target both for scientific exploration and establishment of human settlements. Studies on its evolution and structure may determine whether life exists or existed outside the Earth, and understanding its geophysical processes could also unravel the mysteries of the evolution of other Solar System planets (Why go to Mars? n.d.).
Colonization and exploration missions imply long term exposure of men and devices to the hostile space environment, hence introducing strict requirements on the used technologies. Future spacecraft will need a long lasting, active, extremely reliable, autonomous, and multifunctional structure, able to self-repair and adapt to a wide range of conditions. Other aspects that should be considered are related to mass, volume and power constraints and trade-offs (Menon et al., 2007).
Since traditional design solutions are often unable to adequately match the presented requirements, innovative materials and structures are being developed. Most of them are inspired by nature and actively try to reproduce behaviors that are typical of biological systems. An example is given by robotic probes characterized by adaptive pathfinding and soil penetration strategies inspired by roots, having possible advantages of low power consumption and autonomous decision-taking (Menon et al., 2007). Other promising technologies are given by polyimides (PIs), carbon nanotubes, graphene and ceramics. Traditional PIs as Kapton are used in thermal blankets (radiation insulation), while novel PI shape memory polymers are being considered for space applications as flexible electronics, deployable structures and batteries, solar sails and Sun shields (Gouzman et al., 2019). Carbon nanotubes and graphene could be used in composite propellant tanks, nanoelectronics, electric propulsion systems and self-healing structures, while some interesting ceramics applications are given by protective coatings, high temperature thruster elements and self-healing composites (Levchenko et al., 2018). In general, these materials can be divided into organic and inorganic and different considerations can be made on these two families. The first class includes several polymers, which are fundamental in space due to their high toughness and elasticity, good insulation, and low weight. This last property is particularly useful as it allows to reduce the overall mass of a space system, hence decreasing the related mission costs. Nevertheless, the biggest disadvantage of organic materials is that they experience outgassing under vacuum and thermal cycling, which leads to degradation and contamination of other surfaces, as explained in more detail in section 2. On the other hand, inorganic materials such as coatings, glasses and ceramics typically do not produce contaminants from outgassing.
The materials characterizing a space vehicle highly influence its performance and lifetime, and must resist to the action of space environment and protect crewmembers men and instrumentation from its numerous threats (Levchenko et al., 2018). Important aspects to be considered during their design concern mechanical properties, weight, volatility, thermal stability, chemical reactivity, and durability under specific environmental conditions. Past studies show that the exposure to space for long periods of time causes degradation of these properties, including material aging by UV radiation and atomic oxygen (Miller and Banks, 2010); a specific mission can therefore be seriously compromised or fail if inadequate solutions are adopted.
Depending on its characteristics and purpose, each mission can face different challenges posed by space environment depend on the type and purpose of the mission, but the main issues are typically related to radiation, micrometeoroids and orbital debris (MMOD), ultrahigh vacuum, and thermal solicitations are typically critical factors (Pastore et al., 2020). On the other hand, while atomic oxygen is very important in LEO environment, while it is essentially irrelevant in lunar and Mars missions. In particular, the Moon has a very weak atmosphere that can be virtually considered absent (Earth’s Moon, 2019).
Radiation is very dangerous for both crewmembers and electronics, and the absence of an atmosphere as a protection in deep space requires the introduction of artificial shields. This problem is also present on planets like Mars: on its surface, an astronaut would receive radiation doses that are approximately two and a half times those on the ISS (Mars Radiation Environment, 2023).
Among radiations in space, the cosmic one is very energetic and can cause severe damages and modifications to the DNA of astronauts (The radiation showstopper for Mars exploration, 2019), along with degradation and mass loss of surface materials, and damage to electronic components. Another contribution is given by Solar electromagnetic radiation, mainly composed of UV radiation, is also relevant as it which can break organic chemical bonds. Its effects include and lead to energy loss, creation of volatile fragments with mass loss, and reduction of thermo-optical and mechanical properties (Grossman and Gouzman, 2003).
In addition to the effects on the human body and electronics, radiation may also compromise thermal protection surfaces and devices. In general, external components as thermal blankets, thermal control coatings and optical sensors are mostly affected (Gouzman et al., 2019). It is hence necessary to find materials that can totally or at least partially screen it; lithium, plastics and magnets may be promising in these terms (Chen et al., 2016).
MMOD also pose a serious threat to the integrity of a spacecraft. These objects can be either The term micrometeoroid indicates small pieces of asteroids or comets, called micrometeoroids, or while debris are artificial fragments coming from satellites, named debris. Their characteristic average impact velocities can range from about 11 km/s to 72 km/s for the former, 1 km/s to 15 km/s for the latter (Cwalina et al., 2015). Collision with bodies MMOD below 1 mm can erode thermal surfaces, damage or contaminate optical devices and external parts and puncture fuel lines; on the other hand, fragments with sizes comparable to 1 cm can fatally damage or even destroy the spacecraft (Aïssa et al., 2012). Furthermore, the possible exposure of the damaged zone to UV, charged particles or cyclic temperature variations can increase the damage rates and size (Silverman, 1995), while new debris is also created by the impacts, extending risks to future missions.
On the other hand, the main consequence of high vacuum is the outgassing of material surfaces. Polymer-based components are the most affected by this phenomenon, and the related effects are given by contamination and corrosion of other surfaces and optical devices, loss of dimensional stability and performance and composition alteration (Pastore et al., 2020).
There are Other environmental effects to be taken into consideration are, such as electrostatic discharges and thermal cycles (Grossman and Gouzman, 2003). The first phenomenon is due to non-homogeneous charging of spacecraft surfaces and components, while thermal cycling indicates significant temperature fluctuations of the spacecraft surface. These fluctuations can go from −120°C to 120°C in LEO and −150°C–150°C in geostationary orbit, and may modify the material’s internal and bonding strength, eventually causing it to crack, fall off and age (Chen et al., 2016).
Last but not least, atomic oxygen influences optical properties of materials surfaces and can lead to cause damages related to erosion, cracking and shortened service life (Wang et al., 2018). The oxygen atoms impact with the spacecraft surfaces, breaking the chemical bonds of their materials and significantly modifying their characteristics. Other Additional negative effects to be added to the already cited ones are given by mass loss and degradation of electrical, thermal, and mechanical properties (Bitetti et al., 2007). Polymers and composites are particularly affected by these phenomena. In any case, as already stated, atomic oxygen becomes practically negligible when focusing on missions towards the Moon and Mars. For this reason, this issue will not be deepened in the here presented this review.
It is nevertheless important to point out that one aspect of the environment of the Moon, Mars and other planets may be partially positive for space structures: the reduced gravity with respect to terrestrial conditions, which allows, for example, to A direct consequence is given by the ability to withstand higher weights (Naser and Chehab, 2018).
Future space missions will require multifunctional materials, in which the traditional concept of components with a single specific purpose will be replaced by solutions in which characterized by several different properties (e.g.,: excellent shielding and mechanical characteristics) are embedded in a single material (Laurenzi et al., 2020). This section introduces the main innovative space materials in these terms, which can be divided into different categories, depending on their characteristics and their main function, as indicated in Table 1.
According to their physicochemical properties and their functionality, polymers can be divided into several subclasses. Among them, self-healing polymers have lately become increasingly interesting, since they could mitigate or even completely solve damage issues imparted, for example, by impacts with micrometeoroids and orbital debris (MMOD). Subsequent catastrophic effects on spacecraft and structures as habitats could hence be avoided, leading to higher levels of protection and safety both for devices and human crew. This would result in increased operational life and reliability, which are fundamental for long term missions as the ones planned on Mars and on the Moon.
Self-healing concepts are many and are not exclusive to polymers, but they can all be related either to the intrinsic or the extrinsic category. In the first case, the healing ability is embedded in the material, usually thanks to reversibility of its chemical or physical bonds, and healing can typically occur multiple times. For what concerns extrinsic materials, on the other hand, a healing agent is inserted into them, and repair of a damage cannot be repeated. An example of this second category is given by the space debris impact protection system presented in (Aïssa et al., 2012), formed by different microcapsules containing a monomer, carbon nanotubes and epoxy resin inserted in carbon fibre reinforced polymeric layers. Nevertheless, one of the current main issues of many self-healing materials is that no clear information is available on their actual lifetime and operating temperature range, and on the effects of space environment on them. Furthermore, little is known about part of the mechanisms that trigger the self-healing behavior (Chipara et al., 2006).
Remaining in the category of intrinsic self-healing polymers, more promising than the extrinsic technologies, the properties and suitability to space applications of ionomers and supramolecular polymers have been investigated, among others, by NASA (e.g., efficiency of ionomers for ballistic impact protection) (Gordon et al., 2017), but. Ionomers are thermoplastic polymers with usually up to 20% of ions in their composition. The presence of ionic groups leads to improved mechanical properties of the polymer, such as resistance to traction, impact, tear and abrasion. The reversible nature of ionic bonds is also what makes these materials excellent at self-healing (Ghosh, 2009). On the other hand, supramolecular polymers are polymeric arrays of monomeric units connected through reversible and highly directional secondary interactions, which are the source of their self-repairing ability. Examples of these bonds, referred to as non-covalent, are the Van der Waals interaction, hydrogen bonding, π-π stacking, halogen bonding, and host–guest interaction (van der Zwaag, 2007; Ghosh, 2009). Despite providing the advantage of autonomous repair, high concentrations of noncovalent bonds can lead to a decrease in the material mechanical properties. Consequently, a proper trade-off between healing and mechanical performance must be considered.
A more recent and innovative research example is given by the combination of materials as the EMAA ionomer and supramolecular rubber Reverlink® with optical fibre sensors. The main purpose is to ensure both protection against hypervelocity ballistic impacts with small debris and structural health monitoring of composite overwrapped pressure vessels (COPVs) (Haddad et al., 2018). The result is a multilayer protective wall that also includes impact resistant materials such as Kevlar® and Nextel®. The damage recovery ability of Reverlink® and the possibility of combining it with other materials in multilayers were also presented in (Pernigoni and Grande, 2020; Pernigoni et al., 2023), which also introduced and analyzed poly-urea urethanes (PUUs), another family of intrinsic polymers. This study focused on the case study of a space suit to assess the damage recovery performance of the polymers before and after exposure to space radiation through puncture tests. The related results showed the superior healing ability of the PUUs when compared to Reverlink®, but a slight performance decrease was also found after gamma irradiation, requiring additional future analyses.
Due to the emergence of additive manufacturing and its appeal to the space sector, a photoelastomer self-healing ink has recently been developed for rapid printing of complex 3D shape structures which can autonomously repair and show good response to cyclic solicitations, excellent stability in the 25°C–165°C range and almost complete preservation of their mechanical properties after rupture and repair. This ink contains thiol and disulfide groups (Figure 1), which respectively control the photocuring rate and the self-healing performance (Yu et al., 2019). In addition, it overcomes the main limit of self-healing polymers with hydrogen bonds, which is high sensitivity to moisture (Li et al., 2016). All these aspects make this material and the related manufacturing technique very promising. The most interesting applications are given by soft actuators, structural composites mimicking natural nacre, and self-healing electronics (Benight et al., 2013; Studart, 2016; Adam Bilodeau and Kramer, 2017).
FIGURE 1. Molecular structure of the photoelastomer self-healing ink. Adapted from (Yu et al., 2019) under the Creative Commons Attribution 4.0 International License.
Shape memory polymers (SMPs), on the other hand, can temporarily change their original shape and subsequently restore it by dynamically responding to external stimuli such as heat, electromagnetic or electrical fields, light, and chemical vapors or liquids (Hu et al., 2012). In many cases the external stimulus is given by a temperature gradient: the temperature at which the material can get back to its permanent shape is called switching temperature, and usually corresponds to either glass transition or melting (Ranganatha Swamy et al., 2017). The shape memory effect of SMPs is described with a dual-phase mechanism: the nodes of macromolecule segments related to physical or chemical crosslinks act as a permanent phase, while the molecular chains form the reversible phase. To avoid undesired triggering, the SMP glass transition temperature should be higher than the ambient temperature (Gouzman et al., 2019). SMPs are very appealing for space applications like self-deployable mechanisms (Sokolowski et al., 2008), due to their lightness, low cost, easy manufacturing, good biocompatibility and recovery force, and the possibility to modify their mechanical properties by changing their chemical structure and composition. Some prominent examples are given by epoxy-based SMPs (Liu et al., 2006) and SMP foams, which might be combined with self-healing materials as well (John and Li, 2010).
SMP foams have been analyzed in different studies and are particularly interesting due to the possibility of being significantly compacted and achieving complete recovery after several shape change cycles. Cold hibernated elastic memory (CHEM) foams can be stored in compact state for up to 2 months, without losing their shape memory properties, being thus suitable for space deployable systems (Tey et al., 2001). Shape memory composites (Santo et al., 2014), sandwich structures (e.g.,: SMP foam core, carbon fiber sheets) (Santo and Quadrini, 2015) and the integration of magnetic filler particles in SMP foams (thermal activation of the foam through remote induction on the filler) (Vialle et al., 2009) have also been proposed. Another innovative solution is related to solid state foaming (Squeo and Quadrini, 2010): solid tablets made from uncured resin are heated and produce a thermosetting foam. This technology could lead to SMP materials with unprecedented functional properties, and could also be combined with the recycle of waste epoxy powders (Lucignano et al., 2011). Experiments onboard the ISS (Santo et al., 2012) showed that reduced gravity does not significantly affect the shape recovery ability, which may the other hand be limited by differences in heat transfer and temperature between the Earth and space. Auxetic foams were also studied, showing the ability to switch to positive Poisson’s ratios from solicitation through a given temperature profile (Bianchi et al., 2010). A negative aspect of these materials is given by their reduced mechanical stiffness and strength, due to which it may be necessary to combine them with other materials, such as in composites (Santo, 2016).
Epoxy-based SMPs show both good mechanical and shape memory properties and can be applied in deployable space structures as well. An example is given by the addition of flexible epoxy resin DGEEBA-6 to a common resin, DGEBA, to obtain enhanced toughness, modulus, tensile and impact strength, elongation at break and shape memory properties. Enhances in elongation are very important in space deployables since these structures must be in folded configuration at launch. A study found that some epoxy based SMPs applicable to these structures had a full recovery time of about 80 s for temperatures 20°C above their glass transition temperature. These materials can be inserted in shape memory polymer composites in space structures. Other very positive properties are good processability, chemical resistance and thermomechanical properties (Jo et al., 2019).
The development of polyimide based SMPs for space applications is currently of great interest, too, due to high and low temperature resistance, chemical and radiation resistance, outstanding mechanical properties, flexibility, and excellent dielectric properties of polyimides. Along with deployable solar sails and solar batteries, such applications include large-area flexible electronics and Sun shields for the next-generation of space telescopes (Gouzman et al., 2019).
Polyethylene has a high hydrogen content and is non-toxic, recyclable, chemically stable, relatively cheap and light. If doped with carbon nanotubes or graphene oxide nanoplatelets, it can be used to develop multifunctional nanocomposites with structural and radiation shielding functionality (Laurenzi et al., 2020).
Ultra-high-molecular-weight polyethylene (UHMWPE) could be used in radiation protection as well and could also substitute Kevlar® in novel Whipple shield technologies (protection from impacts, Figure 2). It surpasses Kevlar® in terms of strength-to-weight ratio, modulus-to-weight ratio, and outgassing performance, but is vulnerable to high vacuum and high temperatures related to thermal cycles in space; as a consequence, mitigation of outgassing is anyway required via surface treatment or sealing (Cha et al., 2020).
FIGURE 2. Comparison between conventional and UHMWPE shielding system. Adapted with permission from (Cha et al., 2020), copyright Elsevier, license number 5576551315879.
Biopolymers are also gaining attention: for example, spider silk is characterized by high strength-to-weight ratio, resilience and durability, and superior performances with respect to other classically used materials. With a tensile strength of approximately 1 GPa, it is particularly interesting for structural applications (concrete reinforcement, connection of metallic structures, composites), but its harvesting is challenging. An alternative may be given by the material obtained from silkworms (Bonino, 2003; Hardy and Scheibel, 2009).
Stainless steel and titanium alloys are often used in space as well, and electropulsing proved effective for localized self-healing of these materials. Possible applications could be related to electronic circuits and structural elements (Levchenko et al., 2018). Electropulsing led to crack healing through formation of continuous fine recrystallization regions in SUS304 stainless steel (Yu et al., 2016), and it was able to trigger self-healing of a titanium alloy thanks to material flow and atomic bonding resulting from localized high temperature gradients and compressive stresses (Song et al., 2017). In the second study, the redistribution of currents and the creation of concentrated and diluted regions around the microcracks led to strong temperature gradients and high compressive stresses causing the material to flow and close the cracks.
Organohalide lead perovskites are a novel class of semiconductors considered for applications in space and characterized by low cost and ease of fabrication. Having a power conversion efficiency of about 23.3% and a higher stability when subjected to gamma-ray radiation, they may replace silicon in space solar cells and could also be used in radiation detectors. A very peculiar property of these materials is the ability to recover the losses in power conversion efficiency, related to burn-ins at the beginning of radiation exposure (Figure 3). Nevertheless, a deeper analysis is required to further understand the suitability, stability and performance of these materials in space. (Yang et al., 2019).
FIGURE 3. Recovery mechanism of perovskite after gamma-ray radiation. Adapted with permission from (Yang et al., 2019), copyright John Wiley and Sons, license number 5574860940728.
Composite materials are characterized by high strength-to-weight ratio, excellent dimensional stability, reduced outgassing, low thermal expansion, and almost-zero thermal conductivity. All these properties suggest that this class may respond to harsh environmental solicitations way better than conventional materials, and may be suitable as space construction materials (Naser and Chehab, 2018).
Ceramic matrix composites could be used against extreme thermal, mechanical and corrosion conditions, but they currently have a low TRL, typically between 3 and 4, and research on them is limited (Eswara Prasad et al., 2017). Self-healing ceramic composites (Figure 4) might also be inserted in components requiring both protection from very high temperatures and autonomous restoration after damage (thrusters, hard coatings, circuits). An example is given by the insertion of silicon carbide (SiC) healing activation networks into alumina (Al2O3), which is hard, wear resistant, cheap and readily available (Levchenko et al., 2018).
FIGURE 4. Damage healing in ceramics. (A) TEM image of healed crack in alumina. (B) Self-healing of a TiO2 substrate supercapacitor. (C) Self-healing wires for wearable electronics. (D) Self-healing of alumina. Adapted with permission from (Levchenko et al., 2018), copyright John Wiley and Sons, license number 5574861235182.
Metal matrix composites could be useful for thermal control and seem to resist to most of harsh space conditions, but related raw materials and fabrication processes may be very expensive, and there are doubts about the possibility of long-term performances (the effective operational life could be significantly limited by space environmental solicitations) (Rawal, 2001).
A low thermal conductivity makes aerogel composites very promising for thermal insulation purposes. Aerogels are characterized by light weight and good outgassing properties but are fragile and brittle; as a consequence, they typically need to be combined with reinforcing materials as fibers to increase their mechanical properties, and to potentially further decrease thermal conductivity (Wu et al., 2014). The resulting composites seem particularly suitable at low pressures and cryogenic temperatures, thus being interesting for thermal insulation on Mars (Wordsworth et al., 2019). Two examples are given by quartz fiber reinforced silica aerogel (QTZ/ARG) and polyethylene terephthalate-based fibers reinforced silica aerogel (CDC/ARG) (Figure 5), which are hydrophobic and inorganic and seem to perform better than classical multilayer insulation (MLI) devices for pressures above 1 torr (Johnson et al., 2010). Testing of these composites under simulated Martian conditions showed that their insulation performances are not significantly affected by the Martian environment, and that the storage modulus increases after exposure to gamma-ray radiation. The QTZ/ARG storage modulus is also increased by thermal cycling, while an opposite condition is found for CDC/ARG (Figure 6) (Rocha et al., 2019).
FIGURE 5. Digital microscope images of (A) QTZ/ARG and (B) CDC/ARG. Adapted with permission from (Rocha et al., 2019), copyright Elsevier, license number 5576560163154.
FIGURE 6. Effects of gamma radiation on storage (elastic) modulus. Adapted with permission from (Rocha et al., 2019), copyright Elsevier, license number 5576560163154.
Polyimides can be used as matrices in a composite setup, too. They are characterized by high glass transition temperature, high strength and thermal, radiation and chemical stability (Qu et al., 2017), but there is little information on their structural properties (Naser and Chehab, 2018). An example is given by LaRC RP46, an ultra-high temperature thermosetting polyimide possessing very high thermo-oxidative stability and mechanical performances under high temperature, and good resistance to moisture and corrosion. These properties lead to reduced maintenance and repair costs, as well as size and weight saving (Pater and Curto, 2007).
It was recently demonstrated that addition of bismuth oxide (Bi2O3) to polyimide composites enhances their physical and mechanical characteristics, thermal stability and radiation protection. In particular, the observed ability to shield gamma radiation in the 0.1–1 MeV range makes these composites appealing for local protection of electronics. Expensive radiation-resistant electronics could be indeed replaced with commercial and industrial class ones, leading to significantly reduced mission costs. (Pavlenko et al., 2019).
Carbon nanotubes (CNTs) and graphene can also be used as additives in PI composites (Figure 7), having excellent mechanical properties. Since carbon nanotubes are electrical conductors, they can prevent electrostatic discharge issues that characterize spacecraft electronics under space plasmas. This is particularly useful with polyimides, which are electrical insulators (Gouzman et al., 2019). Furthermore, CNTs are light and characterized by high elasticity and thermal conductivity, and various studies seem to show negligible effects of UV radiation on their performances (Ishikawa et al., 2019). Anyway, currently used incorporation methods in polymeric matrices often lead to degradation of CNT properties (Ma et al., 2010).
FIGURE 7. Polyimide composites. (A) SEM image of the cross section of CNT-graphene oxide-PI nanocomposite. (B) TEM image of graphene-PI nanocomposite. Adapted with permission from (Gouzman et al., 2019), copyright John Wiley and Sons, license number 5574870078470.
Graphene naturally has a 2D configuration, which can be transformed into a 3D one. When inserted into polymers, it improves their electrical and thermal properties. Possible applications are stretchable electronics, energy storage, chemical and mechanical sensing (Chen et al., 2011; Wang et al., 2013; Qin et al., 2015). Combined with piezoelectric substances, graphene also acquires self-healing properties and can be used for damage detection (Huang et al., 2013).
High-temperature polyimide (TriA-X resin) carbon fiber reinforced plastic (CFRP) sandwich panels were also proposed in combination with an ablator, as an alternative to currently used thermal protection systems (TPS) exploited in capsules during atmospheric re-entry (Figure 8). This project may be also interesting for planetary missions. The main advantages of the proposed materials are related to high thermal insulation and good mechanical properties (retention of flexural rigidity and shear strength) at temperatures up to 300 °C at least. It was found that the composite can lead to a reduction of 37%–44% the weight of traditionally used systems, since CFRP panels allow to decrease the thickness of the ablator. A novel ablator architecture was also proposed, containing TriA-X polyimide and carbon fiber cloth reinforcement. No delamination was observed, and the system surpassed currently used solutions in terms of recession resistance. (Kubota et al., 2019).
FIGURE 8. Comparison between existing TPS and the system proposed in (Kubota et al., 2019). Adapted with permission from (Kubota et al., 2019), copyright Elsevier, license number 5576560384832.
Carbon fiber can also be used in self-healing structures (Aïssa et al., 2012), multifunctional structures (Wang et al., 2015), and carbon composites (Krenkel and Berndt, 2005; Pater and Curto, 2007). An innovative carbon reinforced composite was developed by substituting the commonly used resin matrices with active solid-state battery materials having comparable mechanical properties, then combined with carbon fibers; the aim was to obtain a system lighter than traditional energy storage solutions, and with additional structural functionality (Grzesik et al., 2020). However, the current technology readiness level (TRL) of this technology is low, and no effective proof of concept has been done so far, hence requiring further development and characterization.
Carbon fiber reinforced graphite matrix composites were also developed with the ability to significantly preserve their initial strength (Rawal et al., 1990). They can be integrated, among the others, into load bearing and habitat cladding systems. However, research is currently limited, and cracking issues after exposure to thermal cycles are present.
Inserting carbon nanotubes and graphene oxide nanoplatelets into polyethylene-based nanocomposites could enhance the intrinsically weak mechanical, thermal and electrical properties of polyethylene (Adams et al., 2005). Nevertheless, their presence reduces the proportion of hydrogen content, hence decreasing the radiation shielding performance of polyethylene. Simulation of the action of galactic cosmic rays and solar particle events on polyethylene nanocomposites showed a strong dependence of the shielding capability degradation on the radiation source, and that graphene oxide (GO) is the most promising additive. Similarly to polyethylene, GO nanoplatelets contain hydrogen, and they allow to reach the best trade-off between enhanced thermo-electrical-mechanical properties and preserved radiation shielding ability. (Laurenzi et al., 2020). Nevertheless, the effective radiation protection potential of these solutions is currently not fully understood, hence requiring further studies (Cha et al., 2020).
A recently designed TPS was characterized by a self-healing vascular architecture containing NASA Dual Purpose Goop (DPG), a material made of silicone oil (carrier fluid with negligible vaporization and outgassing in space), silicon carbide powder (heat resistant component), and boric anhydride glass (Skolnik and Putnam, 2020). Its characterization proved it to be a promising candidate for self-healing thermal applications in space.
Future exploration and colonization missions on the Moon and Mars will require space structures and habitats characterized by low cost, high reliability, and autonomy from Earth (Menon et al., 2007). Since traditional materials and technologies are typically unable to satisfy these requirements, new design solutions are being proposed (Levchenko et al., 2018). In this regard, the exploitation of in-situ resources is very appealing, since it could significantly lower the cost of space missions, especially for what concerns importing materials. ISRU would lead to reduced or even absent dependence on Earth, and improved financial sustainability. As an example, regolith could be used to obtain materials and products with the most diverse characteristics, through means as, for example, extraterrestrial 3D printing (Yashar et al., 2019).
An interesting ISRU application is concrete production (Khitab et al., 2016). Due to its resilience and durability, this is a very promising material in the field of space constructions, but bringing already built concrete structures would be practically impossible due to excessive weight issues. As a consequence, in-situ processing technologies are needed to make this material effectively usable in space. In this context, different resources, concrete types, and processing techniques are being studied. Substances as alumina, calcium oxide and silicate, from which concrete can be produced, are contained in lunar rocks (Ryder and Norman, 1980; Morris et al., 1983). A similar availability has been confirmed on Mars through information from remote sensing (Pettengill, 1978). A serious issue for classical concrete manufacturing, though, is the need of water which, even if present on both Moon and Mars, may be hardly accessible (Anand et al., 2012). To solve this problem, water substitutes are being studied: an example is given by geopolymers, that also have the advantage of providing radiation protection (Montes et al., 2015). Sulfur concrete is also being considered, due to the possibility of extracting sulfur from lunar and Martian soils. This concrete has compressive strengths ranging from 20 to 63 MPa (Wan et al., 2016), but it is more permeable than common concretes (Osio-Norgaard and Ferraro, 2016), and its strength can be affected by thermal cycling and decrease up to 20% its initial value (Toutanji and Grugel, 2008). In addition to this, it can experience significant mass losses caused by exposure to vacuum (Grugel and Toutanji, 2008).
Metals and alloys could also be produced from in-situ resources (mainly from regolith, once again). Aluminum and Magnesium are the most interesting, since they have low density, good mechanical properties and a low melting point which makes them easier to process. Furthermore, their raw versions are present in higher quantities with respect to other substances as iron and titanium. Again, aluminum could be combined with lunar or Martian soil to produce concrete, while magnesium may be very useful in terms of radiation and impact shielding. The alloys related to these metals could also be used to fabricate space structural components (Bochenek and Basista, 2015). Elemental iron could also be obtained by processing regolith and mixing it with bacteria, water and a growth medium, by means of bioreactors (Lehner et al., 2019).
Lunar regolith may be also useful to produce radiation and MMOD shields, and thermal control systems, since it possesses good thermal insulation characteristics (Higgins and Benaroya, 2020).
Basalt is also widely available and accessible on lunar and Martian soils and is appealing for 3D printing applications. Fibers can be obtained through its extrusion, having double strength with respect to steel, and one-third its weight. Continuous basalt fibers (CBFs) are similar to fiberglass and carbon fibers, and demonstrate good corrosion and heat resistance, and high tensile strength; they could hence be exploited in constructions. Furthermore, plastics as high-density polyethylene (HDPE) and polycarbonate could be produced on Mars from locally available ethylene or methane. (Yashar et al., 2019).
Despite being very appealing, the ISRU approach is still quite underdeveloped, even if some proposals of manufacturing methods and machines have been presented (Naser and Chehab, 2018). As a matter of fact, One of the main issues of ISRU is the current lack or low TRL of the processing methods and tools needed to obtain the final materials and products from the raw sources are currently characterized by a very low TRL.
Materials and processes for space applications raise several challenges, including low mass requirement, small production series, challenging material procurement, very high performances, and very high reliability. Additive manufacturing (AM) is probably the most promising manufacturing technique: it allows to process various materials (polymers, metals, ceramics, composites, tissues and living cells, food for astronauts, etc.) and to obtain complex geometries in a wide range of dimensions (from tens of microns to meters), characterized by increased lightness and reduced waste of resources. AM is well-suited for space applications also because it can be adapted to very small series, provides performance improvement, short lead time, and could be used for in situ manufacturing (Gouzman et al., 2019).
The main problem of extraterrestrial AM is that its TRL is so low that for the moment it is practically impossible to exploit it in situ. In the next decades, though, it will be possible to observe the development of this technology, up to the creation of habitats and constructions. According to recent studies, in addition, it will be also possible to exploit AM to obtain plastics from Martian regolith and other substances as water, carbon dioxide, basalt and ethylene (Yashar et al., 2019).
Other manufacturing techniques and tools have been proposed, but they are essentially currently characterized by criticalities and relatively low technological levels. Nevertheless, they could be very promising in the future years. The most significant ones are listed below.
• Solar and laser sintering (Balla et al., 2012; Meurisse et al., 2018), in which a porous material is heated above its melting point, with the aim of producing objects in a dry environment. sunlight or lasers are used as energy sources.
• Microwave sintering (Agrawal, 2006), which exploits high frequency microwaves to convert electromagnetic energy into thermal energy, used to process ceramic materials and metallic powders.
• Dry-Mix/Steam-Injection (DMSI) (Lin et al., 1996) and Enhanced Dry-Mix/Steam-Injection (E-DMSI) (Wilhelm and Curbach, 2014), for the manufacturing of concrete products with good compressive strength by means of exposure to high temperature vapors.
• Quench Module Insert (QMI) and Diffusion Module Insert (DMI) (Carswell et al., 2003), which are ovens designed to operate on metals and alloys in the 400°C–1600 °C temperature range, under reduced gravity.
To be effectively considered usable in space systems, any new material or structural solution should be able to ensure important mass and cost savings and performance benefits at very low risk (Rawal, 2018). Unfortunately, current systems are still slow and immature for large scale exploration, and improvements in construction materials are required to enable faster space travel and larger payloads. Furthermore, little information is present on the applicability to space of technologies as additive printing, and thermomechanical properties of structures and materials in vacuum have not been fully explored yet (Naser and Chehab, 2018).
An additional strong limitation to the newly proposed materials presented in this review is that no clear information regarding the combined effects of space environment on them, as well as on their actual operational life, is currently available. A deeper knowledge of these aspects is fundamental to assess their applicability of novel materials to the space mission’s environment. In particular, the synergetic action of mechanical damage with radiation and vacuum could lead to the extension of damages and the increase of their propagation rate, hence compromising the performance of materials (Grossman and Gouzman, 2003).
Furthermore, radiation protection still represents a critical issue, especially in manned missions, and the consequent degradation of materials, in particular polymeric ones, must be further understood and quantified. Focusing on galactic cosmic ray (GCR) and solar particle event (SPE) radiation effects on, among the others, inflatable habitats, difficulties are encountered in the evaluation of the actual effects of these radiations and of suitability of polymers for space applications, due to the uncertainties coming from attempts of replicating GCR and SPE space radiation effects with particle beams from terrestrial sources (Norbury et al., 2016). Ions in space radiation are typically related to higher energy values than conventional radiation forms, so even if fluxes in space may be relatively low, damage may be more significant. As a consequence, the dose threshold for polymeric materials above which catastrophic damage is observed is not clearly established for space particle radiations (Waller et al., 2020).
Taking self-healing materials as an example, the effect of particle radiation representative of galactic cosmic rays (GCR) and solar particle events (SPE) on their polymeric subclass is unknown. In addition, self-healing concepts have been demonstrated to work on ground, but there is no evidence of their effectiveness in real space conditions and on how the self-healing functionality will be maintained in time after exposure to space environment. In particular, the effect of space radiation on self-healing polymeric materials in extra-terrestrial applications is not entirely clear, and healing efficiency over time as well as functional behavior under wide temperature ranges need to be explored. Furthermore, to this date, there is no self-healing mechanism that satisfactorily combines proper physical and mechanical properties and a substantial healing efficiency for space applications.
As a solution to the presented issues, mathematical models and simulations are necessary to estimate space suitability of a material, alongside clear common protocols and guidelines for its qualification. Some proposals have been made, for example, in the field of polymers (Waller et al., 2020), and the already present standards such as the NASA standard 6016B (NASA, 2020) can be used as a starting point to be improved and integrated.
Future space missions will require innovative smart materials and related manufacturing techniques; in this review we described some of the most promising solutions. Among them, self-healing polymers can increase the autonomy, reliability, and safety of space structures, but are currently characterized by a limited knowledge of the effects of space on their lifetime and performance, and the mechanisms triggering self-healing are not fully understood yet. On the other hand, SMPs are light, cheap and easy to manufacture, thus being appealing for self-deployable mechanisms; nevertheless, some of them have limited mechanical properties (e.g., SMP foams). Polyethylene and composites are also interesting for multifunctional structures, space construction materials and thermal insulation and protection. Nevertheless, the former is characterized by vulnerability to high temperature and high vacuum, while among the latter ceramic composites have a low TRL, and metal composites have expensive fabrication processes.
In general, all the presented solutions could improve spacecraft mechanical integrity, autonomy, and lifetime, but need further characterization and technological improvement before being actually usable. Thus, in the next years it will be necessary to promote new studies and continue research to fully understand and exploit the here presented materials and manufacturing techniques.
LP: Investigation, Writing–original draft, Writing–review and editing. AG: Funding acquisition, Supervision, Writing–original draft, Writing–review and editing.
This research was supported by ASI (Italian Space Agency), grant agreement 2018-5-HH.0.
The authors acknowledge ASI (Italian Space Agency) for the support.
The authors declare that the research was conducted in the absence of any commercial or financial relationships that could be construed as a potential conflict of interest.
All claims expressed in this article are solely those of the authors and do not necessarily represent those of their affiliated organizations, or those of the publisher, the editors and the reviewers. Any product that may be evaluated in this article, or claim that may be made by its manufacturer, is not guaranteed or endorsed by the publisher.
Adam Bilodeau, R., and Kramer, R. K. (2017). Self-healing and damage resilience for soft robotics: A review. Front. Robot. AI 4. doi:10.3389/frobt.2017.00048
Adams, J. H., Hathaway, D. H., Grugel, R. N., Watts, J. W., Parnell, T. a., Gregory, J. C., et al. (2005). Revolutionary concepts of radiation shielding for human exploration of space. Available at: http://hdl.handle.net/2060/20050180620.
Agrawal, D. (2006). Microwave sintering of ceramics, composites and metallic materials, and melting of glasses. Trans. Indian Ceram. Soc. 65, 129–144. doi:10.1080/0371750X.2006.11012292
Aïssa, B., Tagziria, K., Haddad, E., Jamroz, W., Loiseau, J., Higgins, A., et al. (2012). The self-healing capability of carbon fibre composite structures subjected to hypervelocity impacts simulating orbital space debris. ISRN Nanomater 2012, 1–16. doi:10.5402/2012/351205
Anand, M., Crawford, I. A., Balat-Pichelin, M., Abanades, S., Van Westrenen, W., Péraudeau, G., et al. (2012). A brief review of chemical and mineralogical resources on the Moon and likely initial in situ resource utilization (ISRU) applications. Planet. Space Sci. 74, 42–48. doi:10.1016/j.pss.2012.08.012
Balla, V. K., Roberson, L. B., O’Connor, G. W., Trigwell, S., Bose, S., and Bandyopadhyay, A. (2012). First demonstration on direct laser fabrication of lunar regolith parts. Rapid Prototyp. J. 18, 451–457. doi:10.1108/13552541211271992
Benight, S. J., Wang, C., Tok, J. B. H., and Bao, Z. (2013). Stretchable and self-healing polymers and devices for electronic skin. Prog. Polym. Sci. 38, 1961–1977. doi:10.1016/j.progpolymsci.2013.08.001
Bianchi, M., Scarpa, F., and Smith, C. W. (2010). Shape memory behaviour in auxetic foams: mechanical properties. Acta Mater 58, 858–865. doi:10.1016/j.actamat.2009.09.063
Bitetti, G., Marchetti, M., Mileti, S., Valente, F., and Scaglione, S. (2007). Degradation of the surfaces exposed to the space environment. Acta Astronaut. 60, 166–174. doi:10.1016/j.actaastro.2006.07.019
Bochenek, K., and Basista, M. (2015). Advances in processing of NiAl intermetallic alloys and composites for high temperature aerospace applications. Prog. Aerosp. Sci. 79, 136–146. doi:10.1016/j.paerosci.2015.09.003
Bonino, M. J. (2003). Material properties of spider silk. Rochester, NY, USA: University of Rochester.
Cano, R. J., Grimsley, B. W., Ratcliffe, J. G., Gordon, K. L., Smith, J. G., and Siochi, E. J. (2015). Fracture toughness of carbon fiber composites containing various fiber sizings and a puncture self-healing thermoplastic matrix. CAMX 2015 - Compos. Adv. Mat. Expo., 368–381.
Carswell, W., Kroeger, F., and Hammond, M. (2003). Qmi: A furnace for metals and alloys processing on the international space station. IEEE Aerosp. Conf. Proc. 1, 65–74. doi:10.1109/AERO.2003.1235041
Cha, J. H., Kim, Y. H., Sathish Kumar, S. K., Choi, C., and Kim, C. G. (2020). Ultra-high-molecular-weight polyethylene as a hypervelocity impact shielding material for space structures. Acta Astronaut. 168, 182–190. doi:10.1016/j.actaastro.2019.12.008
Chen, J., Ding, N., Li, Z., and Wang, W. (2016). Organic polymer materials in the space environment. Prog. Aerosp. Sci. 83, 37–56. doi:10.1016/j.paerosci.2016.02.002
Chen, Z., Ren, W., Gao, L., Liu, B., Pei, S., and Cheng, H. M. (2011). Three-dimensional flexible and conductive interconnected graphene networks grown by chemical vapour deposition. Nat. Mat. 10, 424–428. doi:10.1038/nmat3001
Chipara, M., Zaleski, J., Dragnea, B., Shansky, E., Onuta, T., and Chipara, M. D. (May 2006). Self-Healing polymers for space applications. in Proceedings of the 47th AIAA/ASME/ASCE/AHS/ASC Structures, Structural Dynamics and Materials Conference (Newport, Rhode Island). doi:10.2514/6.2006-1946
Cwalina, C. D., Dombrowski, R. D., McCutcheon, C. J., Christiansen, E. L., and Wagner, N. J. (2015). MMOD puncture resistance of EVA suits with shear thickening fluid (STF) - armortm absorber layers. Procedia Eng. 103, 97–104. doi:10.1016/j.proeng.2015.04.014
Earth’s Moon, (2019). NASA sci. Available at: https://solarsystem.nasa.gov/moons/earths-moon/overview/(Accessed January 6, 2020).
Esa, (2019). The radiation showstopper for Mars exploration. Available at: https://www.esa.int/Science_Exploration/Human_and_Robotic_Exploration/The_radiation_showstopper_for_Mars_exploration (Accessed January 4, 2020).
Esa, (2020). Why go to Mars? Available at: https://www.esa.int/Science_Exploration/Human_and_Robotic_Exploration/Exploration/Why_go_to_Mars (Accessed January 5, 2020).
Eswara Prasad, N., Kumar, Anil, and Subramanyam, J. (2017). “Ceramic matrix composites (CMCs) for aerospace applications,” in Aerospace materials and material technologies (Berlin, Germany: Springer), 371–389. doi:10.1007/978-981-10-2134-3_16
Freeman, O. (2023). Future of spaceflight. Available at: https://www.nationalgeographic.com/science/space/space-exploration/future-spaceflight/(Accessed January 4, 2020).
Ghosh, S. K. (2009). Self-healing materials-Fundamentals, design strategies, and applications. Hoboken, New Jersey, United States: Wiley VCH.
Gordon, K. L., Siochi, E. J., Yost, W. T., Bogert, P. B., Howell, P. A., Cramer, K. E., et al. (2017). Ballistic puncture self-healing polymeric materials. Washington, D.C., United States: NASA.
Gouzman, I., Grossman, E., Verker, R., Atar, N., Bolker, A., and Eliaz, N. (2019). Advances in polyimide-based materials for space applications. Adv. Mat. 31, 1807738–1807815. doi:10.1002/adma.201807738
Grossman, E., and Gouzman, I. (2003). Space environment effects on polymers in low earth orbit. Nucl. Instrum. Methods Phys. Res. B 208, 48–57. doi:10.1016/S0168-583X(03)00640-2
Grugel, R. N., and Toutanji, H. (2008). Sulfur “concrete” for lunar applications - sublimation concerns. Adv. Sp. Res. 41, 103–112. doi:10.1016/j.asr.2007.08.018
Grzesik, B., Liao, G., Vogt, D., Froböse, L., Kwade, A., Linke, S., et al. (2020). Integration of energy storage functionalities into fiber reinforced spacecraft structures. Acta Astronaut. 166, 172–179. doi:10.1016/j.actaastro.2019.10.009
Haddad, E., Zhao, Y., Celikin, M., Basti, M., Tagziria, K., Wallach, E., et al. (July 2018). Mitigating the effect of space small debris on COPV in space with fiber sensors monitoring and self-repairing materials. in Proceedings of the ICSO proceedings, (Chania, Greece). doi:10.1117/12.2536183
Hardy, J. G., and Scheibel, T. R. (2009). Production and processing of spider silk proteins. J. Polym. Sci. Part A Polym. Chem. 47, 3957–3963. doi:10.1002/pola.23484
Higgins, M., and Benaroya, H. (2020). Utilizing the Analytical Hierarchy Process to determine the optimal lunar habitat configuration. Acta Astronaut. 173, 145–154. doi:10.1016/j.actaastro.2020.04.012
Hu, J., Zhu, Y., Huang, H., and Lu, J. (2012). Recent advances in shape-memory polymers: structure, mechanism, functionality, modeling and applications. Prog. Polym. Sci. 37, 1720–1763. doi:10.1016/j.progpolymsci.2012.06.001
Huang, L., Yi, N., Wu, Y., Zhang, Y., Zhang, Q., Huang, Y., et al. (2013). Multichannel and repeatable self-healing of mechanical enhanced graphene-thermoplastic polyurethane composites. Adv. Mat. 25, 2224–2228. doi:10.1002/adma.201204768
Ishikawa, Y., Fuchita, Y., Hitomi, T., Inoue, Y., Karita, M., Hayashi, K., et al. (2019). Survivability of carbon nanotubes in space. Acta Astronaut. 165, 129–138. doi:10.1016/j.actaastro.2019.07.024
Jo, M. J., Choi, H., Jang, H., Yu, W. R., Park, M., Kim, Y., et al. (2019). Preparation of epoxy-based shape memory polymers for deployable space structures using diglycidyl ether of ethoxylated bisphenol-A. J. Polym. Res. 26, 129. doi:10.1007/s10965-019-1801-x
John, M., and Li, G. (2010). Self-healing of sandwich structures with a grid stiffened shape memory polymer syntactic foam core. Smart Mat. Struct. 19, 075013. doi:10.1088/0964-1726/19/7/075013
Johnson, W. L., Demko, J. A., Fesmire, J. E., and Weisend, J. G. (2010). Analysis and testing of multilayer and aerogel insulation configurations. AIP Conf. Proc. 1218, 780–787. doi:10.1063/1.3422431
Khitab, A., Anwar, W., Mehmood, I., Kazmi, S. M. S., and Munir, M. J. (2016). Lunar concrete: prospects and challenges. Astron. Rep. 60, 306–312. doi:10.1134/S1063772916020050
Krenkel, W., and Berndt, F. (2005). C/C-SiC composites for space applications and advanced friction systems. Mat. Sci. Eng. A 412, 177–181. doi:10.1016/j.msea.2005.08.204
Kubota, Y., Miyamoto, O., Aoki, T., Ishida, Y., Ogasawara, T., and Umezu, S. (2019). New thermal protection system using high-temperature carbon fibre-reinforced plastic sandwich panel. Acta Astronaut. 160, 519–526. doi:10.1016/j.actaastro.2019.02.004
Laurenzi, S., de Zanet, G., and Santonicola, M. G. (2020). Numerical investigation of radiation shielding properties of polyethylene-based nanocomposite materials in different space environments. Acta Astronaut. 170, 530–538. doi:10.1016/j.actaastro.2020.02.027
Lehner, B. A. E., Schlechten, J., Filosa, A., Canals Pou, A., Mazzotta, D. G., Spina, F., et al. (2019). End-to-end mission design for microbial ISRU activities as preparation for a moon village. Acta Astronaut. 162, 216–226. doi:10.1016/j.actaastro.2019.06.001
Levchenko, I., Bazaka, K., Belmonte, T., Keidar, M., and Xu, S. (2018). Advanced materials for next-generation spacecraft. Adv. Mat. 30, 1802201–1802213. doi:10.1002/adma.201802201
Li, C. H., Wang, C., Keplinger, C., Zuo, J. L., Jin, L., Sun, Y., et al. (2016). A highly stretchable autonomous self-healing elastomer. Nat. Chem. 8, 618–624. doi:10.1038/nchem.2492
Lin, T. D., Tseng, L., and Chou, S. (1996). Lunar concrete made with the dry-mix/steam-injection method. Eng. Constr. Operations Space V, 592–599. doi:10.1061/40177(207)82
Liu, Y., Gall, K., Dunn, M. L., Greenberg, A. R., and Diani, J. (2006). Thermomechanics of shape memory polymers: uniaxial experiments and constitutive modeling. Int. J. Plast. 22, 279–313. doi:10.1016/j.ijplas.2005.03.004
Lucignano, C., Squeo, E. A., Guglielmotti, A., and Quadrini, F. (2011). Recycling of waste epoxy-polyester powders for foam production. Int. J. Manuf. Mat. Mech. Eng. 1, 10–20. doi:10.4018/ijmmme.2011070102
Ma, P. C., Siddiqui, N. A., Marom, G., and Kim, J. K. (2010). Dispersion and functionalization of carbon nanotubes for polymer-based nanocomposites: A review. Compos. Part A Appl. Sci. Manuf. 41, 1345–1367. doi:10.1016/j.compositesa.2010.07.003
Mars Radiation Environment, (2023). Nasa jpl. Available at: https://mepag.jpl.nasa.gov/topten.cfm?topten=10 (Accessed January 4, 2020).
Menon, C., Broschart, M., and Lan, N. (April 2007). Biomimetics and robotics for space applications: challenges and emerging technologies. in Proceedings of the 2007 IEEE International Conference on Robotics and Automation, Roma, Italy
Meurisse, A., Makaya, A., Willsch, C., and Sperl, M. (2018). Solar 3D printing of lunar regolith. Acta Astronaut. 152, 800–810. doi:10.1016/j.actaastro.2018.06.063
Miller, S. K., and Banks, B. A. (2010). Degradation of spacecraft materials in the space environment. MRS Bull. 35, 20–24. doi:10.1557/mrs2010.612
Montes, C., Broussard, K., Gongre, M., Simicevic, N., Mejia, J., Tham, J., et al. (2015). Evaluation of lunar regolith geopolymer binder as a radioactive shielding material for space exploration applications. Adv. Sp. Res. 56, 1212–1221. doi:10.1016/j.asr.2015.05.044
Morris, R. V., Score, R., Dardano, C., and Heiken, G. (1983). Handbook of lunar soils. Washington, D.C., United States: NASA.
NASA (2020). NASA-Std-6016b standard materials and processes requirements for spacecraft. Washington, D.C., United States: NASA.
Naser, M. Z., and Chehab, A. I. (2018). Materials and design concepts for space-resilient structures. Prog. Aerosp. Sci. 98, 74–90. doi:10.1016/j.paerosci.2018.03.004
Norbury, J. W., Schimmerling, W., Slaba, T. C., Azzam, E. I., Badavi, F. F., Baiocco, G., et al. (2016). Galactic cosmic ray simulation at the NASA space radiation laboratory. Life Sci. Sp. Res. 8, 38–51. doi:10.1016/j.lssr.2016.02.001
Osio-Norgaard, J., and Ferraro, C. C. (2016). “Permeability of sulfur based lunar concrete,” in Earth and space 2016: Engineering for extreme environments (Reston, VA, USA: American Society of Civil Engineers), 909–914.
Pastore, R., Delfini, A., Albano, M., Vricella, A., Marchetti, M., Santoni, F., et al. (2020). Outgassing effect in polymeric composites exposed to space environment thermal-vacuum conditions. Acta Astronaut. 170, 466–471. doi:10.1016/j.actaastro.2020.02.019
Pater, R. H., and Curto, P. A. (2007). Advanced materials for space applications. Acta Astronaut. 61, 1121–1129. doi:10.1016/j.actaastro.2007.06.002
Pavlenko, V. I., Cherkashina, N. I., and Yastrebinsky, R. N. (2019). Synthesis and radiation shielding properties of polyimide/Bi 2 O 3 composites. Heliyon 5, e01703. doi:10.1016/j.heliyon.2019.e01703
Pernigoni, L., and Grande, A. M. (2020). Development of a supramolecular polymer based self-healing multilayer system for inflatable structures. Acta Astronaut. 177, 697–706. doi:10.1016/j.actaastro.2020.08.025
Pernigoni, L., Lafont, U., and Grande, A. M. (2023). Self-healing polymers for space: A study on autonomous repair performance and response to space radiation. Acta Astronaut. 210, 627–634. doi:10.1016/j.actaastro.2023.05.032
Pettengill, G. H. (1978). Physical properties of the planets and satellites from radar observations. Annu. Rev. Astron. Astrophys. 16, 265–292. doi:10.1146/annurev.aa.16.090178.001405
Qin, Y., Peng, Q., Ding, Y., Lin, Z., Wang, C., Li, Y., et al. (2015). Lightweight, superelastic, and mechanically flexible graphene/polyimide nanocomposite foam for strain sensor application. ACS Nano 9, 8933–8941. doi:10.1021/acsnano.5b02781
Qu, C., Hu, J., Liu, X., Li, Z., and Ding, Y. (2017). Morphology and mechanical properties of polyimide films: the effects of UV irradiation on microscale surface. Mater. (Basel) 10, 1329. doi:10.3390/ma10111329
Ryder, G., and Norman, M. D. (1980). Catalog of apollo 16 rocks. Washington, D.C., United States: NASA.
Ranganatha Swamy, M. K., Mallikarjun, U. S., and Udayakumar, V. (2017). Shape memory polymers synthesised for controllable switching temperatures. Mat. Today Proc. 4, 11148–11153. doi:10.1016/j.matpr.2017.08.079
Rawal, S. (2018). Materials and structures technology insertion into spacecraft systems: successes and challenges. Acta Astronaut. 146, 151–160. doi:10.1016/j.actaastro.2018.02.046
Rawal, S. P. (2001). Metal-matrix composites for space applications. JOM 53, 14–17. doi:10.1007/s11837-001-0139-z
Rawal, S. P., Misra, M. S., and Wendt, R. G. (1990). Composite materials for space applications. Washington, D.C., United States: NASA.
Rocha, H., Lafont, U., and Semprimoschnig, C. (2019). Environmental testing and characterization of fibre reinforced silica aerogel materials for Mars exploration. Acta Astronaut. 165, 9–16. doi:10.1016/j.actaastro.2019.07.030
Santo, L., Quadrini, F., Accettura, A., and Villadei, W. (2014). Shape memory composites for self-deployable structures in aerospace applications. Procedia Eng. 88, 42–47. doi:10.1016/j.proeng.2014.11.124
Santo, L., and Quadrini, F. (July 2015). Shape memory composite sandwich with self-healing properties for marine applications. in Proceedings of 20th international conference on composite materials (Copenhagen, Denmark)
Santo, L., Quadrini, F., Squeo, E. A., Dolce, F., Mascetti, G., Bertolotto, D., et al. (2012). Behavior of shape memory epoxy foams in microgravity: experimental results of STS-134 mission. Microgravity Sci. Technol. 24, 287–296. doi:10.1007/s12217-012-9313-x
Santo, L. (2016). Shape memory polymer foams. Prog. Aerosp. Sci. 81, 60–65. doi:10.1016/j.paerosci.2015.12.003
Silverman, E. M. (1995). Space environmental effects on spacecraft: LEO materials selection guide. Washington, D.C., United States: NASA.
Skolnik, N. L., and Putnam, Z. R. (January 2020). Evaluation of dual purpose Goop as a candidate for self-healing thermal protection system applications. in Proceedings of the AIAA Scitech 2020 Forum (Orlando, FL, USA: AIAA). doi:10.2514/6.2020-0401
Sokolowski, Witold, Tan, Seng, Willis, Paul, and Pryor, M. (2008). Shape memory self-deployable structures for solar sails. Washington, D.C., United States: NASA.
Song, H., Wang, Z. J., He, X. D., and Duan, J. (2017). Self-healing of damage inside metals triggered by electropulsing stimuli. Sci. Rep. 7, 7097–7111. doi:10.1038/s41598-017-06635-9
Squeo, E. A., and Quadrini, F. (2010). Shape memory epoxy foams by solid-state foaming. Smart Mat. Struct. 19, 105002. doi:10.1088/0964-1726/19/10/105002
Studart, A. R. (2016). Additive manufacturing of biologically-inspired materials. Chem. Soc. Rev. 45, 359–376. doi:10.1039/c5cs00836k
Tey, S. J., Huang, W. M., and Sokolowski, W. M. (2001). Influence of long-term storage in cold hibernation on strain recovery and recovery stress of polyurethane shape memory polymer foam. Smart Mat. Struct. 10, 321–325. doi:10.1088/0964-1726/10/2/318
Toutanji, H., and Grugel, R. N. (2008). “Mechanical properties and durability performance of" waterless concrete,” in Earth & space 2008: Engineering, science, construction, and operations in challenging environments (Washington, D.C., United States: ASCE Library).
van der Zwaag, S. (2007). Self healing materials-an alternative approach to 20 centuries of materials science. Berlin, Germany: Springer. doi:10.2307/4018305
Vialle, G., Di Prima, M., Hocking, E., Gall, K., Garmestani, H., Sanderson, T., et al. (2009). Remote activation of nanomagnetite reinforced shape memory polymer foam. Smart Mat. Struct. 18, 115014. doi:10.1088/0964-1726/18/11/115014
Waller, J. M., Rojdev, K., Shariff, K., Litteken, D. A., and Hagen, R. A. (2020). Simulated galactic cosmic ray and solar particle event radiation effects on inflatable habitat, composite habitat, space suit and space hatch cover materials. Washington, D.C., United States: NASA.
Wan, L., Wendner, R., and Cusatis, G. (2016). A novel material for in situ construction on Mars: experiments and numerical simulations. Constr. Build. Mat. 120, 222–231. doi:10.1016/j.conbuildmat.2016.05.046
Wang, W., Guo, S., Penchev, M., Ruiz, I., Bozhilov, K. N., Yan, D., et al. (2013). Three dimensional few layer graphene and carbon nanotube foam architectures for high fidelity supercapacitors. Nano Energy 2, 294–303. doi:10.1016/j.nanoen.2012.10.001
Wang, X., Li, Y., Qian, Y., Qi, H., Li, J., and Sun, J. (2018). Mechanically robust atomic oxygen-resistant coatings capable of autonomously healing damage in low earth orbit space environment. Adv. Mat. 30, 1803854–1803857. doi:10.1002/adma.201803854
Wang, Y., Peng, C., and Zhang, W. (2015). Thermal analysis of multifunctional structural battery for satellite applications. Appl. Therm. Eng. 78, 209–216. doi:10.1016/j.applthermaleng.2014.12.054
Wilhelm, S., and Curbach, M. (2014). Manufacturing of lunar concrete by steam. Earth Space 2014, 274–282. doi:10.1061/9780784479179.031
Wordsworth, R., Kerber, L., and Cockell, C. (2019). Enabling Martian habitability with silica aerogel via the solid-state greenhouse effect. Nat. Astron. 3, 898–903. doi:10.1038/s41550-019-0813-0
Wu, H., Liao, Y., Ding, Y., Wang, H., Peng, C., and Yin, S. (2014). Engineering thermal and mechanical properties of multilayer aligned fiber-reinforced aerogel composites. Heat. Transf. Eng. 35, 1061–1070. doi:10.1080/01457632.2013.863090
Yang, S., Xu, Z., Xue, S., Kandlakunta, P., Cao, L., and Huang, J. (2019). Organohalide lead perovskites: more stable than glass under gamma-ray radiation. Adv. Mat. 31, 1805547–7. doi:10.1002/adma.201805547
Yashar, M., Ciardullo, C., Morris, M., Pailes-Friedman, R., Moses, R., and Case, D. (2019). Mars X-house: design principles for an autonomously 3D-printed ISRU surface habitat. 49th Int. Conf. Environ. Syst.
Yu, K., Xin, A., Du, H., Li, Y., and Wang, Q. (2019). Additive manufacturing of self-healing elastomers. NPG Asia Mater 11, 7. doi:10.1038/s41427-019-0109-y
Yu, T., Deng, D., Wang, G., and Zhang, H. (2016). Crack healing in SUS304 stainless steel by electropulsing treatment. J. Clean. Prod. 113, 989–994. doi:10.1016/j.jclepro.2015.12.060
Keywords: smart materials, Mars exploration, lunar missions, space environment, materials review
Citation: Pernigoni L and Grande AM (2023) Advantages and challenges of novel materials for future space applications. Front. Space Technol. 4:1253419. doi: 10.3389/frspt.2023.1253419
Received: 05 July 2023; Accepted: 30 August 2023;
Published: 13 September 2023.
Edited by:
Ti Chen, Nanjing University of Aeronautics and Astronautics, ChinaReviewed by:
Yi Wang, Nanjing University of Aeronautics and Astronautics, ChinaCopyright © 2023 Pernigoni and Grande. This is an open-access article distributed under the terms of the Creative Commons Attribution License (CC BY). The use, distribution or reproduction in other forums is permitted, provided the original author(s) and the copyright owner(s) are credited and that the original publication in this journal is cited, in accordance with accepted academic practice. No use, distribution or reproduction is permitted which does not comply with these terms.
*Correspondence: L. Pernigoni, bGF1cmEucGVybmlnb25pQHBvbGltaS5pdA==
Disclaimer: All claims expressed in this article are solely those of the authors and do not necessarily represent those of their affiliated organizations, or those of the publisher, the editors and the reviewers. Any product that may be evaluated in this article or claim that may be made by its manufacturer is not guaranteed or endorsed by the publisher.
Research integrity at Frontiers
Learn more about the work of our research integrity team to safeguard the quality of each article we publish.