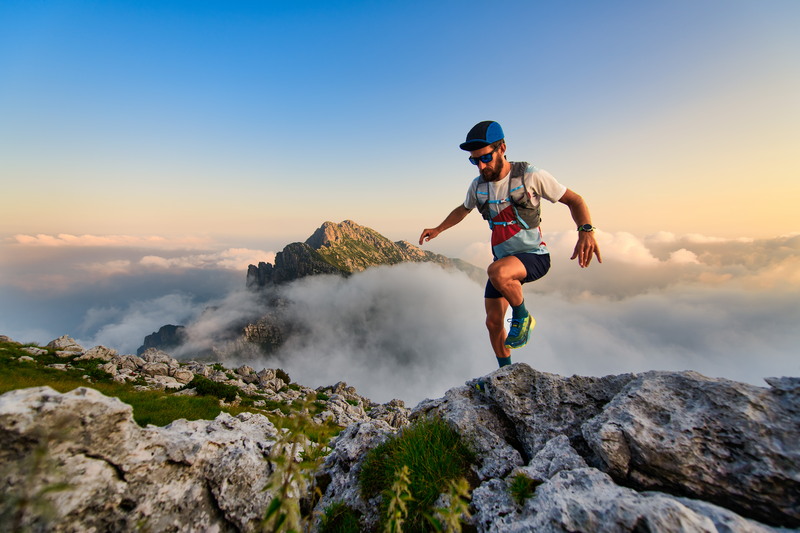
95% of researchers rate our articles as excellent or good
Learn more about the work of our research integrity team to safeguard the quality of each article we publish.
Find out more
ORIGINAL RESEARCH article
Front. Sens. , 23 August 2022
Sec. Optoelectronic and Photonic Sensors
Volume 3 - 2022 | https://doi.org/10.3389/fsens.2022.985963
This article is part of the Research Topic The Future of Sensing Research: Innovators and Early Career Scientists' Perspective View all 6 articles
Single mode-Multimode-Single mode (SMS) sensors have been attracted a relevant attention because of their simple manufacturing, their capability of sensing different quantities, and their enhanced sensitivity compared to the most common fiber optic sensor represented by Fiber Bragg Gratings (FBGs). Moreover, SMS sensors exhibit blue-shift sensitivity to strain, opposite to FBGs, making them suitable in applications where strain-temperature cross-sensitivity may be an issue. SMS sensors are made by splicing a short multimode, preferably a two mode or quasi two-mode, optical fiber jumper between single mode pigtails. The interference of the modes propagating at different phase velocities produces a spectral pattern that shifts with temperature, strain or any perturbation of the phase difference among the modes. In this paper we review the main features of SMSs as temperature sensors and we present a potential biomedical application in an all-fiber flowmeter based on the hot-wire principle: a fiber-coupled laser source at 980 nm is used as a controllable heating source of the SMS sensor that, when immersed in fluid flow, converts the temperature variation, caused by the heat removal, into a wavelength shift of the transmitted spectrum. Thermal characterization and proof-of-concept experiments show the feasibility and functionality of the sensor and provide an outlook on possible developments and potential applications.
The quantitative evaluation of the flow of fluids—be liquid or gaseous—is one the most common measurement requirements for the monitoring of industrial processes and of medical treatments. Targeting the latter, the main applications is in spirometry (Godal et al., 1976; Plakk et al., 1998), infusion therapy, drug delivery, and urodynamics (Poeggel et al., 2015). These measures are typically made with Thermo-Anemometric Flowmeters (TAFs), such as the hot-wire flowmeter, which is well suited to measure turbulent fluids.
The hot-wire flowmeter has been known for over 100 years: despite the different implementations (constant current, constant voltage, and constant temperature), the underlying common principle is to measure the heat loss of a source placed in the fluid stream. In its standard realization, it consists of a thin resistive element, usually a tungsten wire, heated by electrical current (El Abed, 2016).
The necessity of developing an all-optical fiber version of flowmeters stems from the well-known properties of optical fibers, such as small form factor, immunity to electromagnetic interferences, and possibility of remote operation. In addition, biomedical applications benefit from the biocompatibility, intrinsic safety from electrocutions, and absence of interference when used in conjunction with Magnetic Resonance Imaging (MRI).
A recent application of an optical fiber to measure a flow has been presented in (Jderu et al., 2021). The proposed sensor relies on the temperature distributed measurement of a heat pulse by optical frequency domain reflectometry (OFDR). This technique is very interesting because it uses a standard telecom fiber without additional treatments. However, given the high complexity and high cost of OFDR interrogators, it may be limited to specific applications, whereas a compact, low-cost equivalent of the hot-wire flowmeter can be more suitable in mass biomedical applications.
The equivalent of the hot-wire flowmeter can be fabricated in an all-fiber configuration by exploiting light both to generate heat, through the absorption by a dissipative layer, and to interrogate an embedded temperature sensor.
The most widespread fiber temperature sensors are based on Fiber Bragg Gratings (FBGs), in which the temperature induces a shift in the grating spectral response. For example, in the biomedical field FBG sensors have been used to monitor the temperature increase during tumor laser ablation (Liu et al., 2015; Vallan et al., 2017). However, FBG sensors, like all other fiber sensors, suffer from a strain-temperature cross-sensitivity for which deformations induced in the sensitive area produce an effect undistinguishable from a temperature variation, though there have been reported investigations on how to mitigate the cross-sensitivity by proper choosing the materials that make the sensor or its package or by combining a plurality of sensors (Leal-Junior et al., 2019).
Interferometric sensors represent an important alternative to measure the temperature because of their higher sensitivity. This paper studies the possibility to use a particular implementation of such interferometric sensors, known with the acronym SMS and made by the cascade of single mode-multimode-single mode fiber spans. As detailed in the following, besides for the higher sensitivity, SMS sensors are particularly attractive because they can be combined with FBGs to counteract the strain-temperature cross-sensitivity. Indeed, SMS sensors exhibit a red-shift in the spectrum with temperature, as the FBGs, but a blue-shift with strain, opposite to FBGs. This represents a key advantage in medical measurements because it allows compensating for strain-induced artifacts in the temperature measurements due the movements of the patient. As such, an all-fiber flowmeter could find application in “smart” catheters for accurately evaluating the drug release. Another potential application is in the therapy of Obstructive Sleep Apnea (OSA), where an in-vivo real-time monitoring of the ventilation process can enhance the ability of clinicians to distinguish which patients would benefit from one of the variety of treatments, by precisely determining several parameters such as degree of occlusion, severity of reduced air flow, and mechanism of collapse (Wall et al., 2019).
Single mode-Multimode-Single mode (SMS) optical fiber sensors are interferometric sensors in which the quantity under measurement is estimated from the shift in the periodic spectral response obtained from the wavelength-dependent field distribution collected by the receiving single mode fiber and, in turn, due to the interference of the propagating modes in the multimode section. SMS sensors have been investigated in recent years as an alternative to FBGs for temperature monitoring because of their simple fabrication process and higher sensitivity to temperature (Wang et al., 2008; Silva et al., 2012; Zhao et al., 2014). Different approaches can be used to assemble an SMS sensor; in the simplest implementation, as the name implies, a short multimode fiber section is spliced in between two single mode pigtails. The multimode section can be a coreless fiber, a truly multimode fiber, or a fiber operating in a quasi-multimode regime. A more regular spectral dependency, which simplifies and improves the measurements of the shifts, is obtained when only two modes interfere, namely the fundamental LP01 and the first higher order LP11. This can be obtained using, for the multimode section, a short piece of single mode fiber operating close to its cutoff conditions. This situation occurs, for example, using a so-called Bend-Insensitive Fibers (BIF), which is a single mode fiber used in optical communications that, however, becomes an almost two-mode fiber when operated at the short edge of the second optical communications window (Olivero et al., 2016; Olivero et al., 2018). This specific implementation of an SMS sensor is illustrated in Figure 1A. The input fiber that carries the fundamental mode LP01 is offset-spliced to a short BIF jumper to excite both the fundamental and the LP11 modes. Strictly speaking, the LP11 is still not guided, but its attenuation is low enough for the propagation length to produce a non-negligible effect. Therefore, the two modes propagate at different phase velocities and recombine at a second offset splice. The resulting transmission is a periodic interference pattern for the wavelengths at which the LP11 is less attenuated, as clearly visible in Figure 1B. The free spectral range of the interference fringes depends on the optical length of the two-mode section.
FIGURE 1. (A) Schematic of an SMS sensor realized with a bend-insensitive jumper for the “multi-mode” section and (B) experimentally measured transmission spectrum of the resulting SMS structure, in which the spectral oscillations are due to the interference of practically two modes only (the non-flat response is due the spectral emission of the used source and the oscillations become more evident when the wavelength approaches the cut-off of the first higher-order mode).
Therefore, as temperature variation produces both a change of the modal effective indices and a physical modification of the length (elongation or contraction)—collectively indicated with a variation in the so-called optical length –, a shift of the spectral response is obtained.
Sections 2, 3 provide information on the practical realization of this concept and proof-of-concept measurements of the SMS flowmeter, while in Section 4 the conclusions are drawn on these preliminary experiments.
In the all-fiber SMS-based flowmeter the multimode section is optically heated with a laser diode to induce a reference red shift; then, heat removal by the fluid is transduced into a blue shift that can be correlated to the flow speed.
Different SMS prototypes operating at various wavelengths have been fabricated in this work, but always using, for the multimode section, nearly two-mode fibers to obtain a transmission spectrum with smooth periodic oscillations. In particular, some devices intended to be interrogated in the 1,300 nm wavelength range were made with a short piece of BIF compliant optical fiber (as in Figure 1B), model Sterlite BowLite G.657.A2, while other devices operating in the 1500–1700 nm region (a region that includes the third optical communications window) made use of a Thorlabs SM2000 fiber, which is a fiber designed to be single mode around 2000 nm and becomes two-mode in the considered wavelength range.
The excitation of the two interfering modes requires an offset splicing, which must be optimized considering the trade-off between a larger excitation of the higher order mode and the lower transmitted power at the second junction. As for the length of the multimode section, it impacts the free spectral range and the sensing gauge. In the present work this length and the splicing offset were optimized upon an experimental investigation (Olivero et al., 2016; Olivero et al., 2018) and were chosen to be 3 cm and 3 μm, respectively, to produce a spectral pattern with a free spectral range of about 20 nm. The splicing parameters were adjusted to achieve a mechanically stable junction with reproducible core offset and are reported in Table 1 for a portable splicer Fujikura FSM-40 used in “manual” splicing mode.
In order to heat the SMS sensor using an optical source, the multimode section was further coated with an absorptive layer. Given the offset splicing that couples the incident power also outside the core, it is not necessary to remove or etch the cladding, further simplifying the sensor realization. For biomedical applications, to ensure the inertness, the absorbing region is obtained by sputtering on the fiber a thin adhesion layer of titanium, followed by a gold layer and a protective silica layer, for a total thickness of about 80–100 nm. For industrial applications a much simpler, thus cheaper, absorbing region can be fabricated by coating a portion of the fiber with a graphite layer (Kontact Chemie Graphit 33) using a graphite spray normally employed as a conductive paint in electronics, for a thickness of about 20 μm (Figure 2).
FIGURE 2. (A) Schematic of the hot-wire fiber. (B) Microscope image of the optical fiber coated with graphite in a version of the flowmeter. (C) Micrograph of the cross section of the BIF coated with graphite (the red circle is an artifact that indicates the graphite layer). Notice the structure of the core with depressed index profile visible as a dark-grey ring.
The setup for interrogation of the SMS sensor is depicted in Figure 3, in which for the broadband source both a superluminescent light emitting diode (Thorlabs S5FC1550P-A2) and a supercontinuum source (NKT SuperK) were tested. For the version operating in the third optical communications window the setup can be modified by replacing both the source and the spectrometer with commercial swept-laser interrogator (normally used to monitor FBG sensors) to simplify the integration of the proposed sensor in already existing fiber-based sensing systems; in our tests at these wavelengths, we used the Luna Hyperion SI-155, among the most widespread instruments in FBG-based sensing systems.
The heating laser is a 980 nm diode that delivers up to about 200 mW into a single mode fiber; thus, for all the prototypes a 980/1,550 nm coupler has been used (even if for some cases is the sensor is operating out of band) to inject the power laser signal used for heating and the sensing signal.
To demonstrate both the higher sensitivity of the SMS sensor with respect to FBG sensors and the possibility to combine them to reduce the impact of the strain-temperature cross-sensitivity, on the SMS prototype designed to work in the third optical communications window, an FBG has been inscribed in the “multimode” section using the Line-by-Line (LbL) direct writing method with a femto-second laser (Zhou et al., 2010). LbL, as the probably more common Point-by-Point (PbP) writing approach, is a very powerful grating direct writing method because it allows an extreme flexibility in tailoring the grating spectral response. In our case we preferred the LbL over the PbP approach because we experimentally found that it led to gratings with higher contrast in the case of multimode fibers.
The fabricated SMS sensors were initially mounted on a hot plate to characterize the thermal response in terms of spectral shift; then they were tested as flowmeters by coiling the fibers on a reel (just for easy handling) and using controlled air blows.
As already mentioned, sensors using different types of fibers for the multimode section, thus operating in different wavelength ranges, were fabricated; however, they all exhibited a temperature sensitivity of about 50 pm/°C. The exact value depends on the type of fiber used in the multimode section, but it is anyway higher than the typical 10 pm/°C sensitivity of FBGs. The pump power entering the SMS structure was characterized by measuring the output of the pump/signal coupler. The heating of the absorbing layer was measured by thermal images taken with a FLIR A325SC camera; Figure 4 shows an example obtained for the graphite-coated Thorlabs SM2000 multimode section.
FIGURE 4. Thermal images of a hot spot (on the bottom-left corner, highlighted by a dashed circle) on the graphite-coated SMS sensor using the Thorlabs SM 2000: (A) reference: the inset is a snapshot of the SMS section fixed on the optical table and illuminated by a red laser; (B) sensor heated by a laser source emitting about 180 mW at 980 nm. According to the thermal camera the temperature rise is 1.17°C.
The relationship between pump power and temperature increment was found linear with a R-square coefficient >0.99, exhibiting a slope of 0.00455 mW/°C (Figure 5), resulting in an increment of about 1°C for the highest heating power of about 180 mW. It must be considered that the pump power is confined into the core and thermal excitation of the graphite layer occurs because of the misaligned splice and partial excitation of radiating modes. Higher temperature increments could be achieved using for example a higher-power laser diode with multimode delivery fiber. However, energy consumption and safety suggest working at the lowest possible temperature increment, especially for biomedical applications. Moreover, in the case of a diode with multimode delivery, the length of the single mode input pigtail has to be short to avoid loss of the pump before reaching the multimode absorbing section.
FIGURE 5. Temperature against heating pump power for the sensor of which the temperature maps are reported in Figure 4. The error bars refer to the Equivalent Noise Temperature Difference (ENTD) of the thermal camera, which is the minimum detectable difference of temperature between two points.
A proof-of-concept measurement of the SMS flowmeter is reported in Figure 6 for the sensor made with the graphite coated Thorlabs SM 2000: the sensor is optically heated, resulting in a shift of the transmission spectrum of 1.1 nm from the reference (unheated) condition. This is much higher than the shift expected from a bare SMS heated by 1°C. Actually, the temperature coefficient of an SMS sensor is strongly dependent on the materials and fibers involved (sensitivities of more than 3 nm/°C have been recorded (Li and Peng, 2008)). Thus, it was inferred that the temperature dependence is enhanced by the graphite layer, though this behavior has to be further investigated.
FIGURE 6. Air blow experiment: the SMS sensor is optically heated to produce a red-shift of the transmission spectrum that is then compensated by heat removal with an air flow of 4–8 L/min.
An air jet, which has been roughly calibrated with a mechanical flowmeter at 6 L/min, is directed on the graphite-coated multimode section, producing a back-shift to the reference. The spectrum also features a ripple caused by a spurious Fabry-Perot cavity due to connectors. This simple test demonstrates that the flow rate can be transduced as a wavelength shift, just as the conventional hot-wire flowmeter transduces the flow rate into a variation of electrical resistance.
As already mentioned, SMS sensors exhibit a higher sensitivity to temperature than FBG sensors. This can be appreciated from the plot in Figure 7 in which it is shown the spectral response of the SMS designed to work in the third optical communications window and with an FBG inscribed in the middle of the multimode section, for three different temperature values. While the shift is hardly noticeable in the FBG peak, it is well evident in the oscillations of the SMS structure.
FIGURE 7. Spectral response of an SMS sensor for with an FBG at about 1,561 nm under different temperature values.
A proof-of-concept optical fiber flowmeter was fabricated and tested. The sensing element is a single-mode-multimode-single mode fiber structure, where the multimode section is actually a single or nearly single mode fiber offset spliced to the single mode pigtails to produce the excitation of high order modes. The structure, working as a highly temperature-sensitive interferometer, is coated with an absorbing layer, which can be either a metallic layer or, in lower cost versions, a graphite paint that converts optical radiation into heat. Optical heating is then provided by a laser diode that is coupled together with the probing signal into the sensor through a WDM coupler. A ∼170 mW power can rise the temperature of ∼1°C and produce a spectral red-shift of the interferometric transmission spectrum. The optical fiber sensor can be used as a hot-wire flowmeter, where a gas flow removes the optically-generated heat resulting in a spectral blue-shift of the transmission spectrum. Promising, yet preliminary results showed the possibility to monitor an air flow of ∼6 L/min. There is, however, a few open issues that have to be challenged in order to improve these results and make them appealing for biomedical applications. For instance, the effect of the absorbing layer on the propagation properties of the multimode section must be deeply investigated, in order to optimize the relationship between spectral shift and temperature. Moreover, the adhesion of such absorbing (especially for the graphite version) layer to the fiber cladding and long-term stability have to be evaluated. Last but not least, reproducibility of the sensors and their sensing characteristics have to be improved; firmly fixing the input and output pigtails plays a role on the response of the SMS and shall be carefully optimized. Despite the current limitations, the proposed flowmeter can be very attractive because using an SMS structure to measure the temperature change associated to the fluid flow allows using low power heating thanks to the higher sensitivity of SMSs with respect to FBGs. Moreover, it allows combining an FBG inscribed in the multimode section to compensated for the strain-temperature cross-sensitivity, which is particularly detrimental in medical applications.
The raw data supporting the conclusion of this article will be made available by the authors, without undue reservation.
MO and ANB were in charge of the experiments, with support from AUB. AV and GP supervised the activities and supported the data analysis. All the authors contributed to paper, with particular effort of MO and GP.
The activity has been performed with internal funds.
The authors declare that the research was conducted in the absence of any commercial or financial relationships that could be construed as a potential conflict of interest.
The handling editor declared a past co-authorship with several of the authors GP, MO, AUB, AV.
All claims expressed in this article are solely those of the authors and do not necessarily represent those of their affiliated organizations, or those of the publisher, the editors and the reviewers. Any product that may be evaluated in this article, or claim that may be made by its manufacturer, is not guaranteed or endorsed by the publisher.
El Abed, M. (2016). Basic ideas and concepts in hot wire anemometry: An experimental approach for introductory physics students. Phys. Educ. 51 (1), 015008. doi:10.1088/0031-9120/51/1/015008
Godal, A., Belenky, D. A., Standaert, T. A., Woodrum, D. E., Grimsrud, L., and Hodson, W. A. (1976). Application of the hot-wire anemometer to respiratory measurements in small animal. J. Appl. physiology 40 (2), 275–277. doi:10.1152/jappl.1976.40.2.275
Jderu, A., Soto, M. A., Enachescu, M., and Ziegler, D. (2021). Liquid flow meter by fiber-optic sensing of heat propagation. Sensors 21, 355. doi:10.3390/s21020355
Leal-Junior, A. G., Díaz, C. R., Marques, C., A. Frizera, , and Pontes, M. J. (2019). Analysis of viscoelastic properties influence on strain and temperature responses of Fabry-Perot cavities based on UV-curable resins. Opt. Laser Technol. 120, 105743. doi:10.1016/j.optlastec.2019.105743
Li, E., and Peng, G.-D. (2008). Wavelength-encoded fiber-optic temperature sensor with ultra-high sensitivity. Opt. Commun. 281 (23), 5768–5770. doi:10.1016/j.optcom.2008.08.022
Liu, Y., Yu, H., Gassino, R., Braglia, A., Olivero, M., Vallan, A., et al. (2015). “Characterization of tumour laser ablation probes with temperature measuring capabilities,” in 2015 Int. Conf. BioPhotonics, BioPhotonics, Florence, Italy.
Olivero, M., Greborio, L., Orta, R., Pellegrino, P., Perrone, G., and Regio, P. (2016). Multipath interference characterization of bend-insensitive optical fibers and short jumpers. Appl. Opt. 55 (11), 2998. doi:10.1364/ao.55.002998
Olivero, M., Vallan, A., Orta, R., and Perrone, G. (2018). Single mode-multimode-single mode optical fiber sensing structure with quasi-two-mode fibers. IEEE Trans. Instrum. Meas. 67 (5), 1223–1229. doi:10.1109/tim.2017.2771998
Plakk, P., Liik, P., and Kingisepp, P.-H. (1998). Hot-wire anemometer for spirography. Med. Biol. Eng. Comput. 36 (1), 17–21. doi:10.1007/bf02522852
Poeggel, S., Duraibabu, D., Tosi, D., Leen, G., Lewis, E., McGrath, D., et al. (2015). Differential in vivo urodynamic measurement in a single thin catheter based on two optical fiber pressure sensors. J. Biomed. Opt. 20 (3), 037005. doi:10.1117/1.jbo.20.3.037005
Silva, S., Pachon, E. G. P., Franco, M. A. R., Hayashi, J. G., Malcata, F. X., Frazão, O., et al. (2012). Ultrahigh-sensitivity temperature fiber sensor based on multimode interference. Appl. Opt. 51 (16), 3236. doi:10.1364/ao.51.003236
Vallan, A., Perrone, G., Konstantaki, M., Gassino, R., Pissadakis, S., and Liu, Y. (2017). A fiber optic probe for tumor laser ablation with integrated temperature measurement capability. J. Light. Technol. 35 (16), 3447–3454. doi:10.1109/jlt.2016.2618618
Wall, A., Arkwright, J. W., Reynolds, K., Ruiz-Vargas, A., Omari, T., Carney, A. S., et al. (2019). “A multimodal optical catheter for diagnosing obstructive sleep apnea,” in Opt. Fibers sensors med. Diagnostics treat. Appl. XIX. San Francisco, CA. Editor I. Gannot, 10872.
Wang, Q., Farrell, G., and Yan, W. (2008). Investigation on single-mode–multimode–single-mode fiber structure. J. Light. Technol. 26, 512–519. doi:10.1109/jlt.2007.915205
Zhao, Y., Li, X. G., Meng, F. C., and Zhao, Z. (2014). A vibration-sensing system based on SMS fiber structure. Sensors Actuators, A Phys. 214, 163–167. doi:10.1016/j.sna.2014.04.044
Keywords: optical fiber sensors, flowmeter, single mode-multimode-single mode (SMS), optical fiber biomedical applications, spirography, hot wire anemometer
Citation: Olivero M, Bellone A, Bano A, Vallan A and Perrone G (2022) Optical fiber flowmeter based on a single mode-multimode-single mode structure. Front. Sens. 3:985963. doi: 10.3389/fsens.2022.985963
Received: 04 July 2022; Accepted: 29 July 2022;
Published: 23 August 2022.
Edited by:
Daniele Tosi, Nazarbayev University, KazakhstanReviewed by:
Cátia Leitão, University of Aveiro, PortugalCopyright © 2022 Olivero, Bellone, Bano, Vallan and Perrone. This is an open-access article distributed under the terms of the Creative Commons Attribution License (CC BY). The use, distribution or reproduction in other forums is permitted, provided the original author(s) and the copyright owner(s) are credited and that the original publication in this journal is cited, in accordance with accepted academic practice. No use, distribution or reproduction is permitted which does not comply with these terms.
*Correspondence: Massimo Olivero, bWFzc2ltby5vbGl2ZXJvQHBvbGl0by5pdA==
Disclaimer: All claims expressed in this article are solely those of the authors and do not necessarily represent those of their affiliated organizations, or those of the publisher, the editors and the reviewers. Any product that may be evaluated in this article or claim that may be made by its manufacturer is not guaranteed or endorsed by the publisher.
Research integrity at Frontiers
Learn more about the work of our research integrity team to safeguard the quality of each article we publish.