- 1School of Science and Technology, Meiji University, Kawasaki, Japan
- 2Graduate School of Information Science and Technology, The University of Tokyo, Tokyo, Japan
- 3College of Information Science and Engineering, Ritsumeikan University, Shiga, Japan
A high degree of freedom (DOF) benefits manipulators by presenting various postures when reaching a target. Using a tendon-driven system with an underactuated structure can provide flexibility and weight reduction to such manipulators. The design and control of such a composite system are challenging owing to its complicated architecture and modeling difficulties. In our previous study, we developed a tendon-driven, high-DOF underactuated manipulator inspired from an ostrich neck referred to as the Robostrich arm. This study particularly focused on the control problems and simulation development of such a tendon-driven high-DOF underactuated manipulator. We proposed a curriculum-based reinforcement-learning approach. Inspired by human learning, progressing from simple to complex tasks, the Robostrich arm can obtain manipulation abilities by step-by-step reinforcement learning ranging from simple position control tasks to practical application tasks. In addition, an approach was developed to simulate tendon-driven manipulation with a complicated structure. The results show that the Robostrich arm can continuously reach various targets and simultaneously maintain its tip at the desired orientation while mounted on a mobile platform in the presence of perturbation. These results show that our system can achieve flexible manipulation ability even if vibrations are presented by locomotion.
1 Introduction
Manipulators with redundant degrees of freedom (DOFs) are beneficial for representing various postures as the end-effectors reach a specific position and orientation (Chirikjian and Burdick, 1994; Tatlicioglu et al., 2009; Baur et al., 2012). This feature is characterized by the contribution of additional joints toward higher dexterity in the interior of their workspace, which is often considered a solution for obstacle scenarios (Gong et al., 2016; Xu et al., 2019). However, an increase in the number of actuators for such redundant joints leads to anincrease in the weight along the arm. This increases energy consumption, safety, and tip-over problems when the manipulator is mounted on a mobile platform. The use of under-actuated joints with a tendon-driven system is considered a solution to these problems (Chung et al., 1998), with benefits such as (1) providing flexibility in manipulation, (2) reducing the weight of the arm, and (3) placing the center of mass of the manipulator close to the mobile platform. In our previous work, we proposed a tendon-driven high-DOF underactuated manipulator inspired by the vertebral column of an ostrich, referred to as the Robostrich arm (Mochiyama et al., 2022). However, the inverse kinematics of such a complicated system are too complex to be fully known. This leads to difficulty in controlling the Robostrich arm using traditional model-based control methods, even for simple reach tasks.
Recently, researchers have applied reinforcement learning to manipulator tasks. Reinforcement learning is a trial-and-error-based approach that allows an agent to automatically acquire skills as it interacts with its environment, and is therefore often effective for manipulation tasks. Among these tasks, reaching has been the main subject of studies on the combination of redundant arms and reinforcement learning. Morimoto et al. added a payload to the arm to reach a stick (Morimoto et al., 2021), Satheeshankar et al. studied redundant manipulators that could reach multiple target points (Satheeshbabu et al., 2020). However, the motion of a tendon-driven manipulator is often a complex and nonlinear time-varying system, which is difficult to achieve simply using reinforcement learning methods. In such complex scenarios, it is challenging to design advanced reinforcement-learning techniques for complicated manipulation tasks. In this study, we aimed to address the aforementioned problems regarding design and control issues.
Inspired by the fact that the learning process for humans and animals generally follows an order from easy to difficult, we focus on the concept of curriculum learning (Bengio et al., 2009). Compared with the general paradigm of indiscriminate machine learning, curriculum learning imitates the process of human learning, advocating that the model should start learning from easy samples and gradually progress to complex samples and knowledge, further showing the two advantages for learning. The first is that it can accelerate the training of machine learning models; under the condition that it achieves the same model performance, curriculum learning can speed up training and reduce the number of training iteration steps. The second advantage is that the model can obtain better generalization performance, that is, the model can be trained to a better local optimum state.
On the other hand, constructing simulations often benefits researchers who design robots, helping to confirm the robot’s motion and train it. Software such as Gazebo, CoppeliaSim (previously V-Rep), Multi-Joint dynamics with Contact (MuJoCo), and Matlab have been used to simulate a robot in many studies (Xiao et al., 2017; Huang et al., 2020; Shahid et al., 2021; Rooban et al., 2022). However, in contrast to conventional manipulators with direct motor-driven joints, the relationship between tendons and joints change must be closely considered.
This study particularly focuses on control and simulation problems of a tendon-driven high-DOF underactuated manipulator. A curriculum-reinforcement learning framework was proposed for controlling a complicated manipulator to accomplish complex manipulation tasks. In addition, an approach was addressed to simulate the tendon-driven system for constricting the training environment. We first confirmed the motion of the tendon-driven manipulator using the developed simulator. Next, the workspace of the Robostrich arm was investigated. Simultaneously controlling position and orientation is a challenging task for such a high-DOF underactuated manipulator, in particular when the manipulator is composed of a tendon-driven system. We compared the proposed learning method with conventional Soft Actor-Critic (SAC) learning in a reaching task using the Robostrich arm. Consequently, two application tasks were conducted to investigate the robustness of our method in the presence of noise, which is caused by the locomotion of the mobile base, providing interaction with the environment: (1) stabilize the tip movement during walking; (2) track a set of sub-target positions to pass through a narrow gap and reach the final target position at the top.
The contributions of this study are as follows.
• A Curriculum-reinforcement learning approach is proposed with the learning lesson definitions depending on the complexities. These lessons enable a manipulator with complicated structure to gradually process from simple to more complex tasks.
• A simulator has been developed using MuJoCo to study tendon-driven underactuated manipulators, which can be used for tendon-driven systems whose structures are too complicated to be accurately modeled.
• We demonstrate through simulation that the complicated manipulator can learn to accomplish complex tasks, even under perturbations when the manipulator was mounted on a mobile platform.
The remainder of this paper is organized as follows. In Section 2, related works are addressed. Section 3 introduces the proposed framework of curriculum-reinforcement learning and corresponding lesson definitions. Section 4 describes the simulation environment, experimental setups, and investigation of properties of the Robostrich arm movement. Section 5 presents the simulation results of the proposed learning method. Section 6 presents the conclusions and future work.
2 Related works
2.1 Curriculum with reinforcement learning
Curriculum learning is widely used in machine learning frameworks, especially in tasks dealing with images or natural language processing, where researchers often start training with simple samples progressing to complex ones. For instance, (Mousavi et al., 2022), designed a deep curriculum learning method for the classification of polarimetric synthetic aperture radar image in the order of easy to hard, which is evaluated by the patch complexity criterion, and achieved better accuracy than methods which consider samples in a random order during training. (Xu et al., 2020), proposed a method which is able to distinguish easy examples from difficult ones, and arrange a curriculum for language models, by reviewing the training set in a crossed way. In the application of robotics, researchers have focused more on applying curriculum learning to the generation of subgoals for traditional rigid manipulators. For instance, (Kilinc and Montana, 2020), trained a 7-DOF fetch robot for position to position tasks with a curriculum of intermediary imagined goals resulting in a high learning success rate. Zhou et al. (2021), also trained an industrial robot to overcome obstacles by generally increasing the size of obstacles. Mendoza investigated the curricula of a 6-DOF manipulator with Q-learning, such as the number of moving joints, joint velocities, or initial robot configurations (Diego Mendoza, 2017). The joints of these studied manipulators were directly driven by the corresponding actuators without any underactuated joints, and related research tends to be limited to simpler tasks such as reaching without considering orientation. In comparison, this study particularly focuses on more complicated manipulator structures and complex tasks, with regard to the positional and orientational control of a tendon-driven high-DOF underactuated manipulator.
2.2 Simulation of tendon-driven manipulator
To simulate a tendon-driven robotic system, the traditional approaches simulation often focus on constructing a mathematical model to map the tendon force/length to joint torque/angle, and applying these models to generate the robot motions. For instance, G. Borghesan et al. reported the development of a tendon-driven robotic finger by simulation, in which a finger model was constructed by mapping the joint torques to the tendon forces (Borghesan et al., 2010); Okoli et al. developed a cable-driven parallel robot simulation, in which the robot was investigated by moving an object using the tendon. The tendon length change and object twist was mapped using a Jacobian matrix (Okoli et al., 2019). Ko reported a tendon-driven gripper, constructing a hand model using relationships between tendon tension and joint torques (Ko, 2020). These mathematical-based approaches are often unsuitable for complex manipulator architectures, as (1) when some DOFs are underactuated or the relationship between joints and tendons is not a one-to-one correspondence, it is often difficult to find such a mathematical relationship; (2) the contacts between tendons and links are often changing depending on various postures, these contacts affect the manipulator actuation. Therefore, a mathematical model-free approach is beneficial to simulate such a tendon-driven underactuated manipulator.
2.3 Previous works of Robostrich arm
The Robostrich arm was designed with a focus on the dorsoventral motion of an ostrich neck to represent neck movement in the sagittal plane (Misu et al., 2022). The Robostrich arm comprises 18 rigid links with passive rotational joints, which is similar to the number of real ostrich vertebrae. The mean length of the links was designed according to an earlier anatomical report of a real ostrich and the sizes of the links were scaled to 75% (Dzemski and Christian, 2007). Additionally, the movable range of the joints was determined according to the flexibility measured from real ostriches in that earlier study. Table 1 lists the parameters of the Robostrich arm, and Figure 1A shows the Robostrich arm prototype. The links of the Robostrich arm were numbered from the C2 to C18, corresponding in order from the cranial to the caudal part of the ostrich vertebra. C2 denotes the link which is closest to the atlas (head). The length of the links in Table 1 is defined as the distance between adjacent rotational joint axes in the corresponding links. The masses in Table 1 are the masses of the bone parts, and the atlas mass includes the masses of the beak parts.

TABLE 1. Parameters of Robostrich arm. The links are numbered from C2 to C18 and counted from the cranial side to caudal side (see Figure 1B). C2 denotes the link which is closest to the atlas (head). The length is defined as the distance between the adjacent rotational joint axes in the corresponding link.
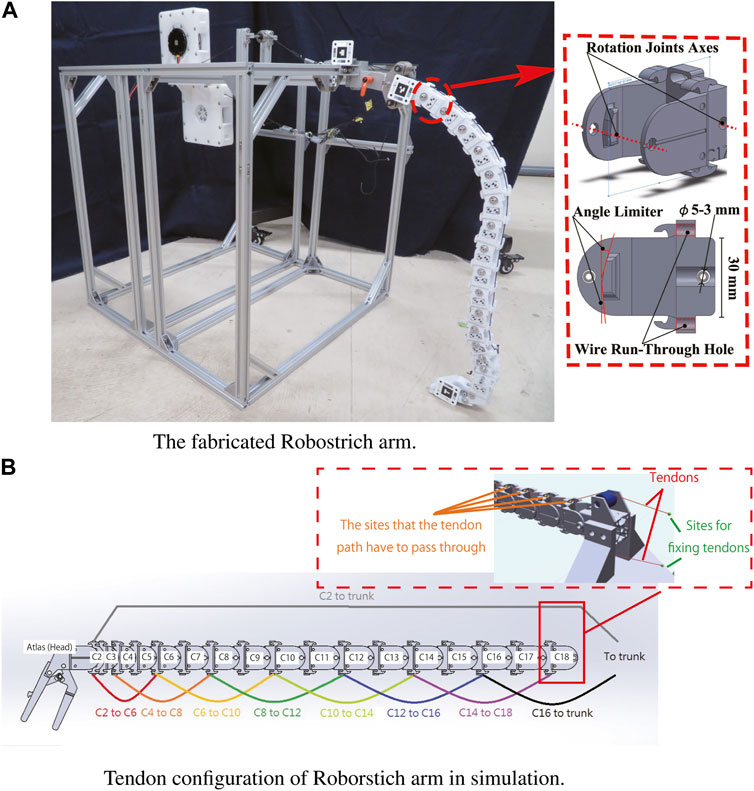
FIGURE 1. The fabricated Robostrich arm and tendon configuration in simulation. (A) The fabricated Robostrich arm. (B) Tendon configuration of Roborstich arm in simulation.
In our previous study, two DC motors were used to connect four tendons to actuate the Robostrich arm, and a simple feed-forward strategy was used to control the manipulator. The preliminary results show that the head-up motion was successful only when the entire arm was maintained in a bar shape during rotation. However, the motion using this strategy limits the dexterity of the high-DOF manipulator. We considered the above problems as caused by a missing model to test its motion and control. However, constructing a mathematical model of such a complicated system is laborious and its parameters are not flexibly changeable, such as inertia moments and tendon attachment positions. Therefore, we aimed to solve the aforementioned issue using a curriculum-reinforcement learning approach.
3 Curriculum-SAC learning
We introduce a novel reinforcement learning-based approach for a complicated manipulator that can learn manipulation tasks. We adopted an architecture based on SAC reinforcement learning (Haarnoja et al., 2018) and curriculum learning (Bengio et al., 2009). In our tasks, SAC achieved the best performance among general reinforcement learning methods, as shown in the Supplementary Material. The neural network policy was trained using reinforcement learning to obtain higher rewards in the simulation environment.
3.1 Soft Actor-Critic
The learning objective of traditional reinforcement learning algorithms is to learn a policy that maximizes the reward of the trajectory.
where ρπ(st|at) denotes the state-action marginals of the trajectory distribution induced by the policy π(at|st). In SAC, a maximum entropy reinforcement learning algorithm aims to learn a policy considering to maximize not only the reward of trajectory but also the entropy of each state, namely:
where
and the Q function is defined by operator Tπ:
Then, we use the soft policy evaluation, let Qk+1 = TπQk, Q0 = S × A → R, |A| < ∞, where k → ∞, Qk converges to a soft Q value. Because of the convergence of Qk, policy π also converges to an optimal policy π∗ when |A| < ∞.
SAC approximates the above formula and uses three parameters φ, and θ, ϕ to parameterize V, Q, and π, and update φ, θ, and ϕ in each step, respectively. Following this trick, we define the following objective:
The soft Q-function is used to minimize the soft Bellman residual as follows:
Where D denotes the replay buffer, and γ denotes the discount factor. In practice, (Fujimoto et al., 2018) used the 2 Q functions Qθ1 and Qθ2. The objective function of the policies to be updated via minimization is as follows:
Where ɛ denote the input noise sampled from the Gaussian distribution N.
The temperature parameter α affects the exploration ability of the policy. We aim to achieve a flexible exploration of the strategy through dynamic automatic adjustment using the following optimal function:
3.2 Curriculum learning
We designed a curriculum course by adjusting the reward functions, initial states, and environmental setting of reinforcement learning, such that the agent can finally learn manipulation tasks and improve the performance from the traditional SAC approach.
In the first lesson, the reward function was defined as follows:
Where, phead and pdesire denote the current and desired head positions, respectively, and d denotes the error tolerance of the head position. In this lesson, the agent is expected to learn a policy to reach the desired position without considering the attitude angle of the head.
In the following lessons, all reward functions are the same but have different initial states or environment settings.
Where θhead and θdesire denote the current and desired attitude angles of the head, respectively. Weight λi determines the importance of the position and orientation of the head in the reward functions. In this lesson, we intended the agent to learn a more difficult policy so that it can reach the desired positions with a certain attitude angle of the head. In particular, in the second lesson, the agent starts learning in each episode with a fixed initial state and is expected to learn the more difficult policy with set position and head orientation. In the third lesson, we make the agent start learning using the final states of the last episode as the initial states, such that the agent can move among states continuously.
In the first three lessons, we intended the agent to acquire basic manipulation abilities to continuously track a set of target positions with specific orientations. In practical usage scenarios, manipulators are often combined with mobile platforms for broader applications (Osman et al., 2020). In contrast to the stationary case, in such scenarios, the influences of the environment should be learned, such as perturbations. Therefore, we introduced a subsequent lesson aimed at allowing the agent to acquire the advanced ability to respond to the environment. In other words, the training environment was modified by mounting a manipulator on a mobile platform.
3.3 Curricula reinforcement learning framework
The final algorithm is shown in Algorithm 1. The method alternates between collecting experience from the environment with the current policy and updating the function approximators in the order of curriculum settings using stochastic gradients from batches sampled from a replay pool. In our curriculum settings, each task is a sub-optimal solution for the next task; therefore, it is possible to help the agent to generate the action that maximizes the performance for a final task.
Algorithm 1. Soft Actor-Critic with Curriculum.
Input:θ1, θ2, ϕ
1:θ1 ←θ1, θ2 ←θ2
2:
3: foreach lessondo
4: foreach iterationdo
5: foreach environment stepdo
6:
7:
8:
9: end
10: foreach gradient stepdo
11:
12:
13:
14:
15: end
16: end
17 end
Output:θ1, θ2, ϕ
Where θ1, θ2, ϕ are parameters to be optimized, D denotes the replay buffer, λ is a parameter in the stochastic gradient method, and π, a, and s are introduced in Section 3.1.
4 Simulation platform
This section describes the simulation environment of the Robostrich arm. Based on this, two setups were prepared for training. In addition, the motion of the Robostrich arm is tested by manually controlling the tendon input in the simulation. Afterward, the workspace of the Robostrich arm is investigated.
4.1 Simulation environment of Robostrich arm
We used MuJoCo (Todorov et al., 2012) with the OpenAI gym toolkit (Brockman et al., 2016) to simulate the Robostrich arm. The assembled model of the Robostrich arm was created using CAD software and rendered in MuJoCo. The parameters of the Robostrich arm, such as the joint limitations and masses of the links, were manually edited according to Table 1. The tendons were defined with the attachment sites and were assigned to pass through the predefined wire run-through holes on the links (see Figure 1). We defined the general actuator properties and assigned them to act on the tendons. Therefore, the control of actuators can produce contraction of the corresponding tendons, thereby leading to the actuation of the manipulator. In this study, we refer to the ventral muscles of ostriches (Cobley et al., 2013) and modified the tendon arrangement from our previous work (illustrated in Figure 1B).
4.2 Experimental setups
To evaluate the performance of the Robostrich arm with curriculum-reinforcement learning, two situations were considered: (1) the Robostrich was mounted on an immobile frame; (2) the Robostrich was mounted on a commercially available quadruped robot (A1; Unitree Robotics, China).
In the first situation, we focused on a stationary situation in which the position of the Robostrich arm base was not changed, and the properties of the Robostrich arm and curriculum-reinforcement learning were investigated while not being affected by the disturbance of the base. In the second situation, vibrations were generated by the walk of the quadruped robot to serve as noise to the manipulator and we investigated the affected performance. In both situations, the timestep was set as 0.008 s. Figure 2 shows these two setups, and Table 2 listed the corresponding action and observation spaces. As summarized in Table 2, the total dimensions of the action space in both environments were identical, however, their total observation space dimensions differed. Additional dimensions were set owing to the locomotion of the quadruped robot. In particular, the walking pattern of the quadrupedal robot was determined by a set of motor data obtained from the walking task of the real A1 robot.
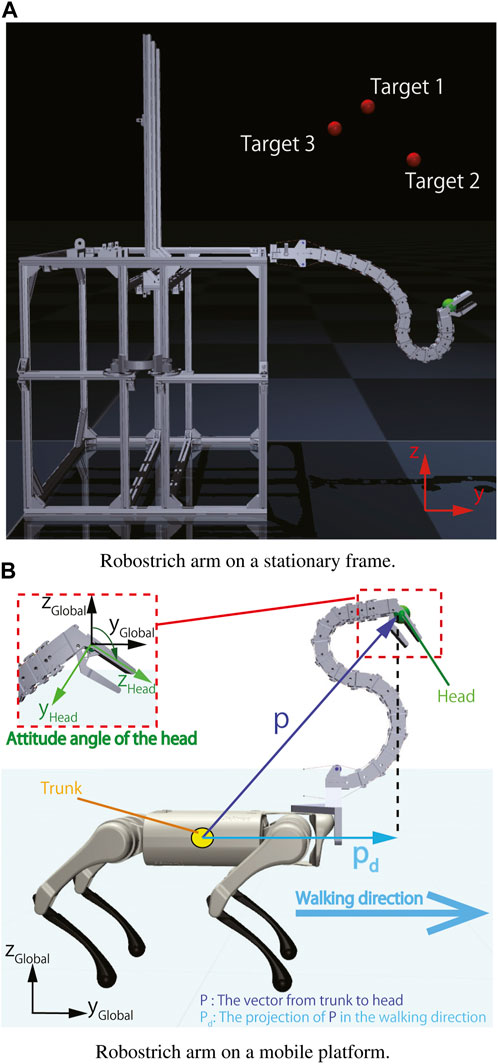
FIGURE 2. Environment setup. (A) Robostrich arm on a stationary frame. (B) Robostrich arm on a mobile platform.
In the training stage, the target positions were randomly sampled from the workspace of the Robotstrich arm. The agent was thereafter trained by following the described curriculum learning process. In these policies, the positional and orientational error tolerances were set as ±0.05 m and ±5°, respectively. After training, all experiments were evaluated using the learned policies. The testing targets were selected based on the requirements of the manipulation tasks, and the desired attitude angle of the Robostrich head was set as 90° with respect to the global coordinate system. This implies that the orientation of the Robostrich head was maintained parallel to the ground during the experiments (see Figure 2B).
4.3 Movement test of Robostrich arm simulation
The rolling and lever patterns are two representative motor patterns in the avian neck system that can be found during feeding or pecking. The rolling pattern can be roughly characterized as the transition of the rostral loop of vertebrae, leading to a change in the length of the cranial region of the neck, which can be partly maintained as a “bar” shape (van der Leeuw et al., 2001). This leads to the fact that the orientation of the head can be maintained during its positional movement. Instead of successive rotations, the lever pattern is characterized by simultaneous rotations in the rostral loop, and the angle between the bars of the caudal loop changes during neck movement, causing the caudal loop to widen during head protraction (the concept was illustrated in Figure 3). Referring to (Nakano et al., 2022) in which rolling and lever patterns were used to test the motions of a tendon-driven manipulator; therefore, we selected these two movements to test our simulation environment. We used the control method proposed by (Nakano et al., 2023) to manually control the contraction of the ventral tendons when maintaining the dorsal tendon length. The experiment was conducted using the immobile Robostrich arm environment. Figures 4, 5 show the tendon inputs, head orientations, and corresponding trajectory samples. It can be observed that the movement of both patterns are reasonably represented in the simulation.
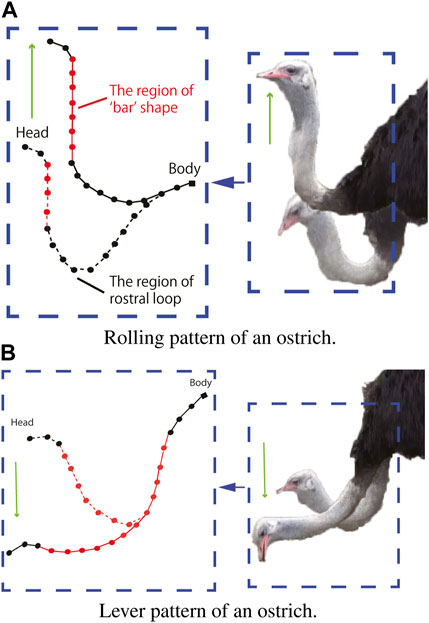
FIGURE 3. Motor pattern of an ostrich. (A) Rolling pattern of an ostrich. (B) Lever pattern of an ostrich.
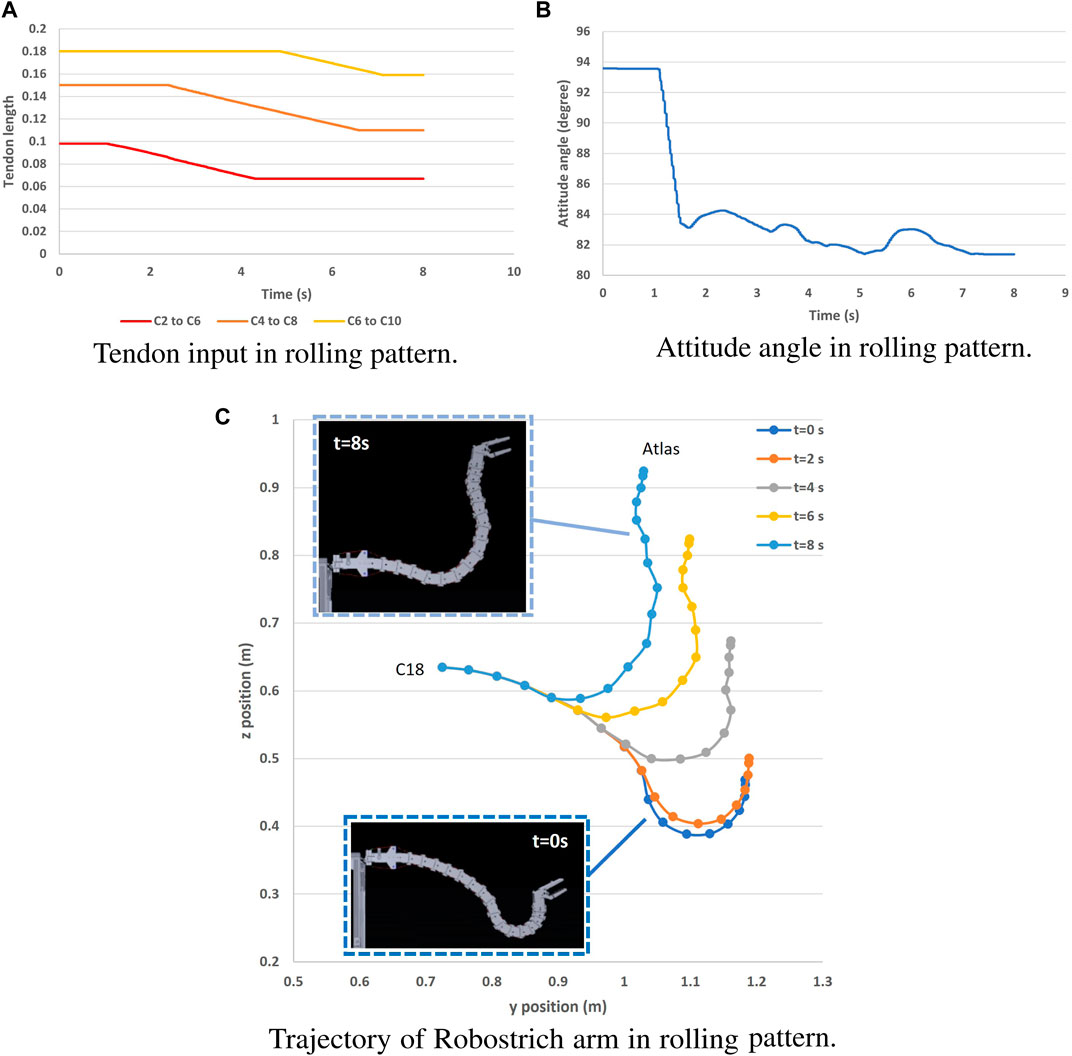
FIGURE 4. Rolling pattern movement of Robostrich arm on an immobile frame. (A) Tendon input in rolling pattern. (B) Attitude angle in rolling pattern.
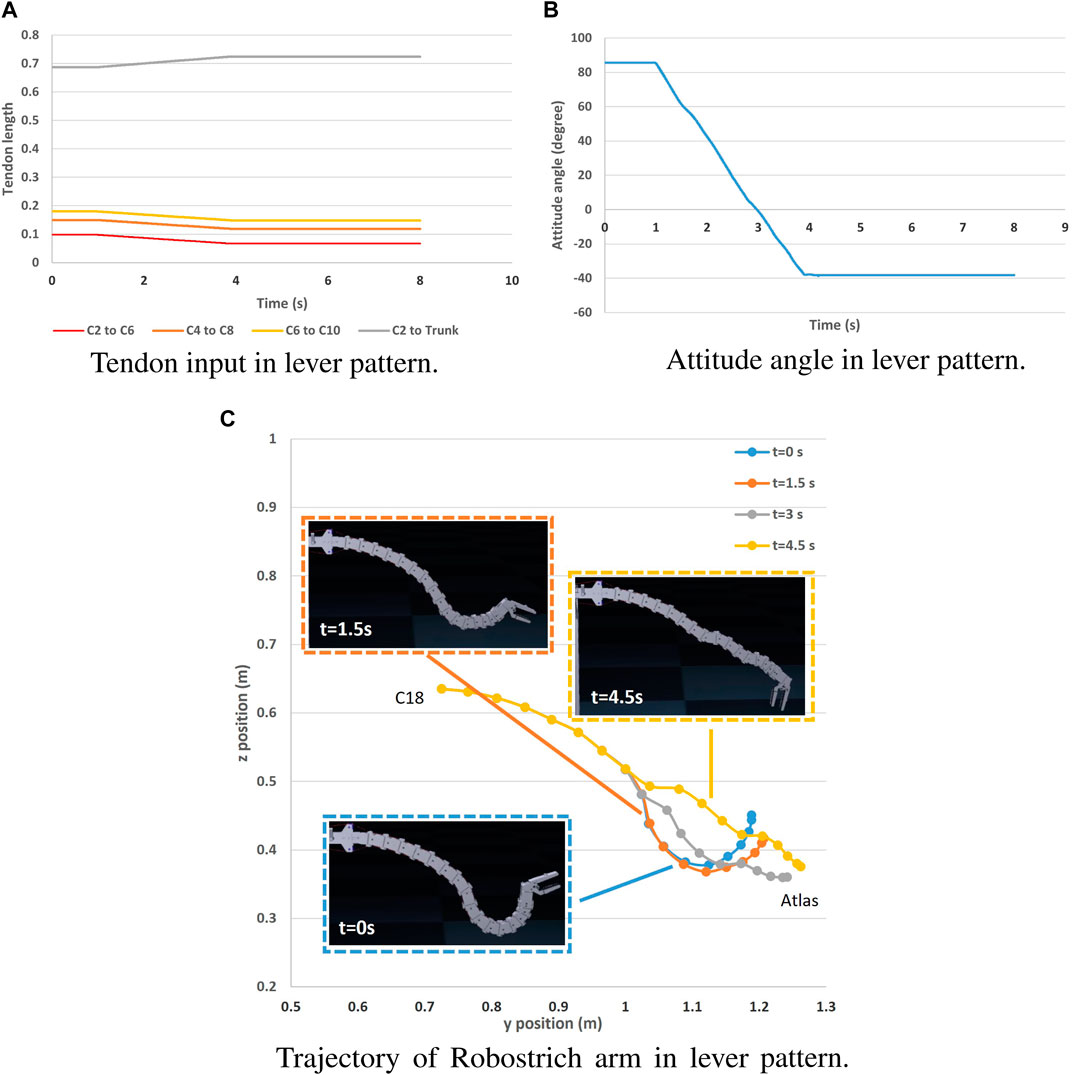
FIGURE 5. Lever pattern movement of Robostrich arm on an immobile frame. (A) Tendon input in lever pattern. (B) Attitude angle in lever pattern. (C) Trajectory of Robostrich arm in lever pattern.
4.4 Workspace of Robostrich arm
After confirming the motion, we determined the feasible area of the Robostrich arm to ensure that the target positions were selected in the workspace of the Robostrich arm. We randomly sampled the joint angles from the joint limitations of the Robostrich arm and plotted the corresponding head positions. Figure 6 shows the theoretical workspace of the Robostrich arm. The black point indicates the joint location between the C18 link and the frame, and the red range shows the area that the Robostrich head can achieve without considering the head orientation. The blue range shows the positions at which the head can achieve a head attitude angle of 90° ± 5°. This implies that if the target position is selected from the blue range, the head of the Robostrich arm can be maintained approximately parallel to the ground during head movement.
5 Experiments with curriculum-SAC learning
In the last section, simple motions were tested by manually controlling the tendons. To achieve more complicated manipulation tasks, the Robostrich arm was trained using the Curriculum-SAC learning approach. In the first experiment of this section, we evaluated the performance of learning methods in a stationary situation. In addition, we further studied the learning approach in the presence of noise with application scenarios (see Supplementary Material).
5.1 Experiment in immobile frame
In this experiment, we targeted a task in which the Robostrich head tracks a set of desired positions in order while keeping level with the ground. The Robostrich arm was trained using curriculum reinforcement learning as mentioned in the previous section, and the target positions were arbitrarily selected from the blue range in Figure 6; thus, the manipulator is theoretically capable of achieving the desired position and orientation (the attitude angle of the head was defined in Figure 2B). We compared the proposed learning method with a prior SAC reinforcement learning approach (Haarnoja et al., 2018), and the performance of the algorithms was evaluated at 140e6 steps because they approached asymptotic performance in our environment. The task of the experiment was to sequentially reach three target positions with the desired head orientation. Figure 7A shows the head trajectory of Robostrich arm using the learned Curriculum-SAC model. Figures 7B–D show the comparisons of the two algorithms regarding the learning curve, position error of the head, and head orientation, respectively.
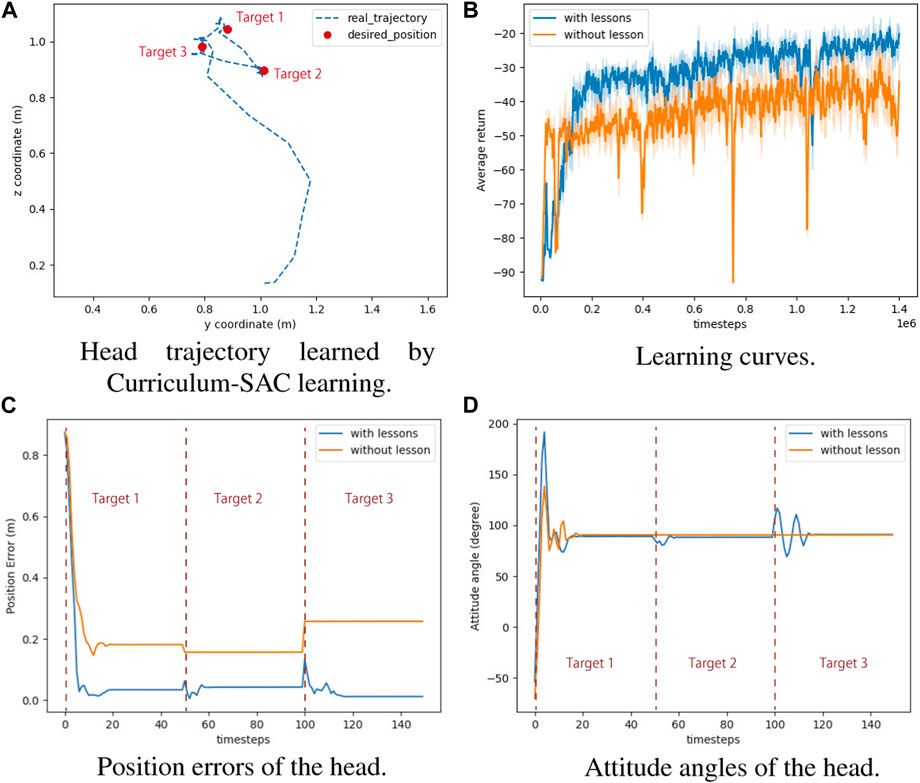
FIGURE 7. The results of reaching task with curriculum-SAC learning. (A) Head trajectory learned by Curriculum-SAC learning. (B) Learning curves. (C) Position errors of the head. (D) Attitude angles of the head.
According to the reward function of reinforcement learning, the agent optimizes both the angular and positional accuracies during motion. The results show that in the no-curriculum SAC, the agent exhibits better angular accuracy, but worse position accuracy. The Curriculum SAC allows the agent to learn the policy of optimizing the position accuracy through the pre-course, and based on this, the next course is learned, such that the position and angle accuracies are both within a reasonable range.
5.2 Experiments in mobile frame
5.2.1 Head stabilization task
Vibration is often generated by the locomotion of a mobile platform, leading to a certain degree of noise in the control of the mobile manipulator. In this experiment, a quadruped robot was used to generate such vibration by controlling it while walking forward; hence the Robostrich arm vibrated depending on the gait of the quadruped robot. Curriculum-SAC learning performance was evaluated using a head-stabilizing task during walking. In addition, various trunk heights were set during walking to investigate the robustness of the controller in this task. In this scenario, walking gait and various trunk heights collaboratively contributed to vibrations in the Robostrich arm. In such a situation, the Robostrich arm must simultaneously control the position and orientation of its head. Therefore, controlling such a high-DOF tendon-driven underactuated manipulator is challenging. In the head stabilizing task, the agent was assigned to simultaneously: (1) maintain its head at a constant height to the ground; (2) maintain the attitude angle of its head near the desired orientation; and (3) maintain constant distance between the A1 trunk and the head of the Robostrich in the walking direction (Pd in Figure 2B). In the training stage, the agent was pre-trained using the first three lessons with the same training step as in the previous experiment when the quadruped platform was standing. Subsequently, an additional 400e6 training steps were performed with the walking of the quadruped platform.
Figure 8 shows the movement of the agent during the experiment, and the corresponding results are shown in Figure 9. Comparing the position of the Robostrich head to the A1 trunk, it is apparent that the A1 trunk vibrated during walking, but a stable position can be found in the Robostrich head even though the height of the A1 trunk change (the timestep between the 500th and 750th, and the timestep between the 1000th and 1250th, in Figure 9A). In addition, the velocity of the Robostrich head is reduced. This implies that the proposed approach is robust against noise from mobile base vibrations. Although Figure 9C shows a certain degree of oscillation in the distance between the Robostrich head and A1 trunk in the walking direction, the mean values of the crests and troughs were approximated to the desired distance. In addition, the result in Figure 9D verified that the Robostrich arm learned to control its head orientation to approach the desired attitude angle, despite the change in A1 trunk height during locomotion.
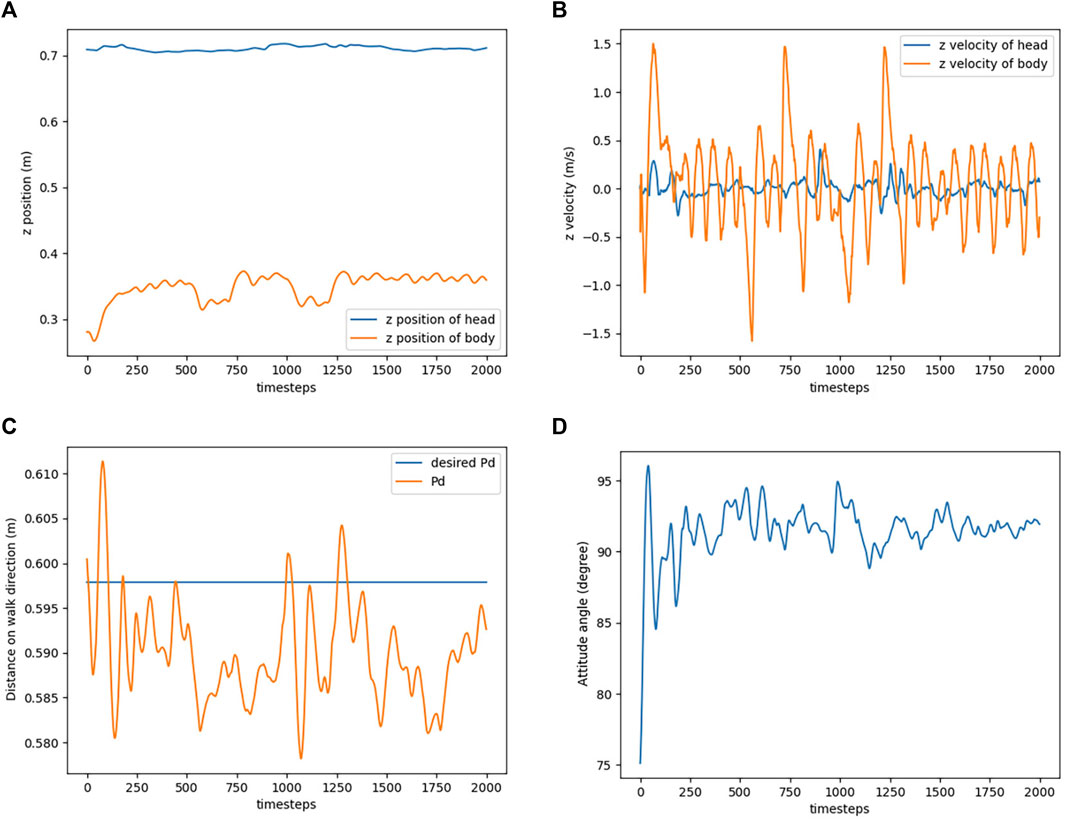
FIGURE 9. Simulation result of head stabilization task. (A) Head and trunk positions in z direction. (B) Head and trunk velocities in z direction. (C) Distance between the trunk and the head on walk direction. (D) Attitude angle of the head.
5.2.2 Reaching task in narrow space
Avoiding obstacles while reaching a target position is a useful feature of redundant manipulators. An experiment was conducted in a scenario where the mobile Robostrich arm passed through a narrow gap and reached a target position at the top of the gap. This is a difficult task for a traditional manipulator, but the additional DOF helps the Robostrich arm accomplish such a challenging task.
The setup for this scenario is illustrated in Figure 10. In this reaching task, the quadruped platform was assigned to walk toward the narrow gap, and the head was assigned to reach target 6 (defined in Figure 10). Because the gap obstructs the Robostrich arm from directly reaching the target point, the arm must to move its head to the bottom of the gap in advance. Subsequently, the arm must lift its head vertically to pass through the gap. This action can be realized by continuously controlling the manipulator to track a set of predefined subtargets. As in the previous experiment, the agent was trained using the first three lessons and the fourth lesson with 140e6 + 400e6 training steps, which corresponded to the standing and walking situations.
Figure 11 shows the movement of the robot during the experiment, and the corresponding head trajectory is shown in Figure 12A. The results indicate that the Robostrich head can approximately track the targets in the desired order (from targets 1–6), and the Robostrich arm can vertically raise its head to pass through the narrow gap, and finally reach target 6 at the top of the gap. The position error and attitude angle in the experiment are shown in Figures 12B,C, respectively. We found that the position error increased when the target position changed because the positional difference between the targets increased. We also found that such an error could be recovered immediately. Although we obtained high orientation errors in a few moments, the system rapidly recovered, and the head orientation was maintained within 90° ± 5°, which fulfills our error tolerance setup in reinforcement learning policies. These results verify that the agent can operate in a narrow space, which is useful for practical robotic applications.
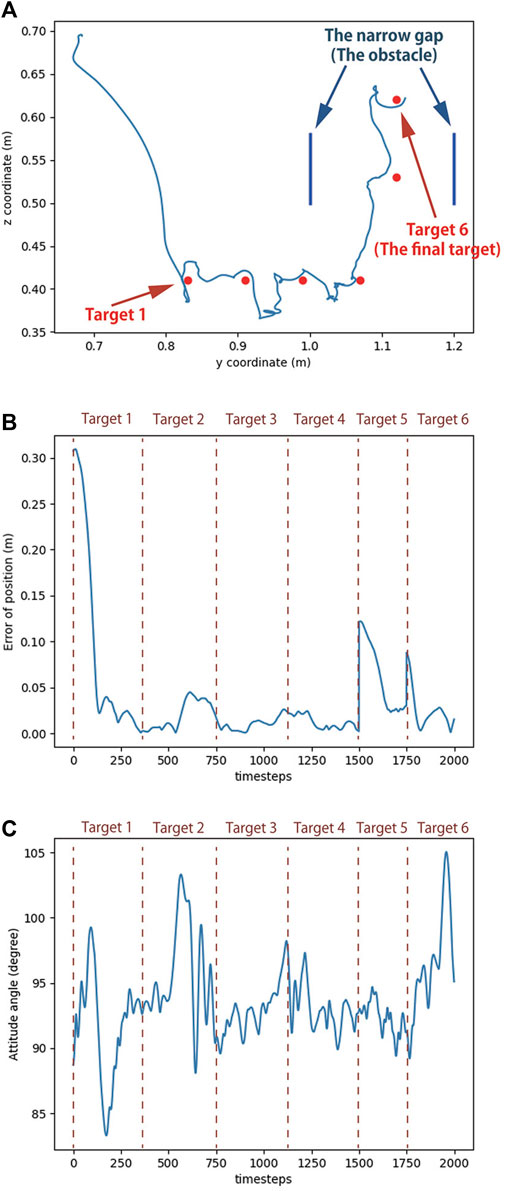
FIGURE 12. Simulation result of reaching task in narrow space. (A) Trajectory of Robostrich head. (B) Position error of the head. (C) Attitude angle of the head.
6 Conclusion and future works
We aimed to develop ostrich-inspired manipulators to achieve dexterous manipulation and flexibility. A tendon-driven high-DOF underactuated manipulator was previously introduced inspired by the vertebral column of a real ostrich neck, known as the Robostrich arm. In this study, we proposed a curriculum reinforcement learning framework, to enable the Robostrich arm to gradually process from simple to more complex tasks. Four reinforcement learning lessons were defined depending on their complexities. These lessons can also be explained as courses from learning fundamental manipulation abilities, to obtaining advanced knowledge for specific tasks. A manual control experiment was conducted to confirm that the motion of the Robostrich arm can be reasonably represented in the simulation environment. In the experiments for training, we compared Curriculum-SAC learning with traditional SAC learning and found that the proposed learning method is effective in improving the accuracy of position control with a slight decrease in the performance of orientation control. However, the total reward of the proposed approach is higher than that of traditional SAC learning. Finally, we investigated the performance of Curriculum-SAC learning in the presence of noise by mounting the Robostrich arm on a quadruped platform. The simulation results demonstrate that the Robostrich arm can stabilize its head movement during walking and flexibly pass through a narrow gap to reach a target position at the top, despite perturbations are presented by locomotion. These results demonstrated the feasibility of curriculum-reinforcement learning for extended applications. Although the Robostrich arm was the focus of this study, our proposed learning method is also suitable for other complicated manipulator systems. In particular, more complex manipulation tasks can be trained by adding additional lessons.
In this study, the early demonstration of this approach was limited to simulation environments which are not a faithful representation of the real world. Some parameters should be further tuned depending on the real robot properties, such as friction coefficient, actuator gain, or sensor selection. To bridge the real world gap and transfer learned policies from simulation, some Sim2Real techniques are likely helpful to implement our approach in a real Robostrich arm, such as: Domain Randomization to randomize the friction and damping parameters in the simulation or add noise to the joint measurement (Tobin et al., 2017); Domain Adaptation to transfer the features from the source to the target domain to encouraging agents to adopt similar behaviors in a real environment (Christiano et al., 2016); Imitation learning to encourage agents to learn the policy for the real robot using the result of the expert policy from simulation, instead of directly applying it (Yan et al., 2017). In addition, only one tendon configuration was tested in the experiments; the comparison of various tendon configurations, and that between simulation and a real robot should be systematically investigated in the future. Regarding the learning method, although two application tasks were presented in this study, the number of tasks remained limited; therefore, verification with a wide range of tasks is necessary. Furthermore, it is necessary to clarify the network properties, such as (1) the factors affecting the control accuracy distribution, such as positions in the workspace, and (2) the relationship between control accuracy and various factors, such as various manipulator postures, different types of noise, or observations.
Data availability statement
The raw data supporting the conclusion of this article will be made available by the authors, without undue reservation.
Author contributions
KO developed the environmental platform, conducted the experiments, and contributed to manuscript writing. KW developed the learning framework, conducted the experiments and contributed to manuscript writing. KN, MI, and MA provided expert advice and assisted with this study. YK and RN supervised and managed the project. All authors contributed to the article and approved the submitted version.
Funding
This work was supported by the JSPS KAKENHI Grant Number JP18H05466 and JP20K19890.
Conflict of interest
The authors declare that the research was conducted in the absence of any commercial or financial relationships that could be construed as a potential conflict of interest.
Publisher’s note
All claims expressed in this article are solely those of the authors and do not necessarily represent those of their affiliated organizations, or those of the publisher, the editors and the reviewers. Any product that may be evaluated in this article, or claim that may be made by its manufacturer, is not guaranteed or endorsed by the publisher.
Supplementary material
The Supplementary Material for this article can be found online at:https://www.frontiersin.org/articles/10.3389/frobt.2023.1066518/full#supplementary-material
References
Baur, J., Pfaff, J., Ulbrich, H., and Villgrattner, T. (2012). “Design and development of a redundant modular multipurpose agricultural manipulator,” in 2012 IEEE/ASME International Conference on Advanced Intelligent Mechatronics (AIM), Kaohsiung, Taiwan, 11-14 July 2012 (IEEE), 823–830. doi:10.1109/AIM.2012.6265928
Bengio, Y., Louradour, J., Collobert, R., and Weston, J. (2009). “Curriculum learning,” in Proceedings of the 26th annual international conference on machine learning (New York, NY, USA: Association for Computing Machinery), 41–48. doi:10.1145/1553374.1553380
Borghesan, G., Palli, G., and Melchiorri, C. (2010). “Design of tendon-driven robotic fingers: Modeling and control issues,” in 2010 IEEE International Conference on Robotics and Automation, Anchorage, AK, USA, 03-07 May 2010 (IEEE), 793–798. doi:10.1109/ROBOT.2010.5509899
Brockman, G., Cheung, V., Pettersson, L., Schneider, J., Schulman, J., Tang, J., et al. (2016). Open gym. arXiv preprint arXiv:1606.01540.
Chirikjian, G., and Burdick, J. (1994). A hyper-redundant manipulator. IEEE Robotics Automation Mag.1, 22–29. doi:10.1109/100.388263
Christiano, P., Shah, Z., Mordatch, I., Schneider, J., Blackwell, T., Tobin, J., et al. (2016). Transfer from simulation to real world through learning deep inverse dynamics model. arXiv e-prints. doi:10.48550/arXiv.1610.03518
Chung, J. H., Velinsky, S. A., and Hess, R. A. (1998). Interaction control of a redundant mobile manipulator. Int. J. Robotics Res.17, 1302–1309. doi:10.1177/027836499801701203
Cobley, M. J., Rayfield, E. J., and Barrett, P. M. (2013). Inter-vertebral flexibility of the ostrich neck: Implications for estimating sauropod neck flexibility. PLOS ONE8, 721877–e72210. doi:10.1371/journal.pone.0072187
Diego Mendoza, B. (2017). Curriculum learning for robot manipulation using deep reinforcement learning. Master thesis. London: Artificial Intelligence of Imperial College London.
Dzemski, G., and Christian, A. (2007). Flexibility along the neck of the ostrich (struthio camelus) and consequences for the reconstruction of dinosaurs with extreme neck length. J. Morphol.268, 701–714. doi:10.1002/jmor.10542
Fujimoto, S., van Hoof, H., and Meger, D. (2018). Addressing function approximation error in actor-critic methods. arXiv.
Gong, M., Chen, K., Zhao, K., and Chang, P. (2016). “Trajectory planning based on multi-objective optimization for redundant robots,” in 2016 3rd International Conference on Systems and Informatics (ICSAI), Shanghai, China, 19-21 November 2016 (IEEE), 133–138. doi:10.1109/ICSAI.2016.7810943
Haarnoja, T., Zhou, A., Abbeel, P., and Levine, S. (2018). Soft actor-critic: Off-policy maximum entropy deep reinforcement learning with a stochastic actor. arXiv e-prints. doi:10.48550/ARXIV.1801.01290
Huang, Z., Li, F., and Xu, L. (2020). “Modeling and simulation of 6 dof robotic arm based on gazebo,” in 2020 6th International Conference on Control, Automation and Robotics (ICCAR), Singapore, 20-23 April 2020 (IEEE), 319–323. doi:10.1109/ICCAR49639.2020.9107989
Kilinc, O., and Montana, G. (2020). Follow the object: Curriculum learning for manipulation tasks with imagined goals. arXiv preprint arXiv:2008.02066.
Ko, T. (2020). A tendon-driven robot gripper with passively switchable underactuated surface and its physics simulation based parameter optimization. IEEE Robotics Automation Lett.5, 5002–5009. doi:10.1109/LRA.2020.3005131
Misu, K., Ikeda, M., Or, K., Ando, M., Gunji, M., Mochiyama, H., et al. (2022). Robostrich arm: Wire-driven high-dof underactuated manipulator. J. Robotics Mechatronics34, 328–338. doi:10.20965/jrm.2022.p0328
Mochiyama, H., Gunji, M., and Niiyama, R. (2022). Ostrich-inspired soft robotics: A flexible bipedal manipulator for aggressive physical interaction. J. Robotics Mechatronics34, 212–218. doi:10.20965/jrm.2022.p0212
Morimoto, R., Nishikawa, S., Niiyama, R., and Kuniyoshi, Y. (2021). “Model-free reinforcement learning with ensemble for a soft continuum robot arm,” in 2021 IEEE 4th International Conference on Soft Robotics (RoboSoft), New Haven, CT, USA, 12-16 April 2021 (IEEE), 141–148. doi:10.1109/RoboSoft51838.2021.9479340
Mousavi, H., Imani, M., and Ghassemian, H. (2022). “Deep curriculum learning for polar image classification,” in 2022 International Conference on Machine Vision and Image Processing (MVIP), Kuala Lumpur, Malaysia, 17-22 July 2022 (IEEE).
Nakano, K., Gunji, M., Ikeda, M., Or, K., Ando, M., Inoue, K., et al. (2023). Robostrich manipulator: A novel mechanical design and control based on the anatomy and behavior of an ostrich neck. IEEE Robotics Automation Lett.8, 3062–3069. doi:10.1109/LRA.2023.3265301
Nakano, K., Ikeda, M., Or, K., Gunji, M., Mochiyama, H., Niiyama, R., et al. (2022). “A study of sagittal motions with a flexible manipulator based on the anatomy of the ostrich neck,” in The Robotics and mechatronics conference 2022 (Japan: Springer).
Okoli, F., Lang, Y., Kermorgant, O., and Caro, S. (2019). “Cable-driven parallel robot simulation using gazebo and ros,” in Romansy 22 – robot design, dynamics and control. Editors V. Arakelian, and P. Wenger (Cham: Springer International Publishing), 288–295.
Osman, M., Mehrez, M. W., Yang, S., Jeon, S., and Melek, W. (2020). End-effector stabilization of a 10-dof mobile manipulator using nonlinear model predictive control. IFAC-PapersOnLine53, 9772–9777. doi:10.1016/j.ifacol.2020.12.2658
Rooban, S., S, I. J., Manimegalai, R., Eshwar, I. V. S., and Mageswari, R. U. (2022). “Simulation of pick and place robotic arm using coppeliasim,” in 2022 6th International Conference on Computing Methodologies and Communication (ICCMC), Erode, India, 29-31 March 2022 (IEEE), 600–606. doi:10.1109/ICCMC53470.2022.9754013
Satheeshbabu, S., Uppalapati, N. K., Fu, T., and Krishnan, G. (2020). “Continuous control of a soft continuum arm using deep reinforcement learning,” in 2020 3rd IEEE International Conference on Soft Robotics (RoboSoft), New Haven, CT, USA, 15 May 2020 - 15 July 2020 (IEEE), 497–503.
Shahid, A. A., Sesin, J. S. V., Pecioski, D., Braghin, F., Piga, D., and Roveda, L. (2021). Decentralized multi-agent control of a manipulator in continuous task learning. Appl. Sci.11, 10227. doi:10.3390/app112110227
Tatlicioglu, E., Braganza, D., Burg, T. C., and Dawson, D. M. (2009). Adaptive control of redundant robot manipulators with sub-task objectives. Robotica27, 873–881. doi:10.1017/S0263574708005274
Tobin, J., Fong, R., Ray, A., Schneider, J., Zaremba, W., and Abbeel, P. (2017). “Domain randomization for transferring deep neural networks from simulation to the real world,” in 2017 IEEE/RSJ International Conference on Intelligent Robots and Systems (IROS), Vancouver, BC, Canada, 24-28 September 2017 (IEEE). doi:10.1109/IROS.2017.8202133
Todorov, E., Erez, T., and Tassa, Y. (2012). “Moco: A physics engine for model-based control,” in 2012 IEEE/RSJ International Conference on Intelligent Robots and Systems, Vilamoura-Algarve, Portugal, 07-12 October 2012 (IEEE), 5026–5033. doi:10.1109/IROS.2012.6386109
van der Leeuw, A. H., Bout, R. G., and Zweers, G. A. (2001). Control of the cranio-cervical system during feeding in birds. Am. Zoologist41, 1352–1363. doi:10.1093/icb/41.6.1352
Xiao, J., Han, W., and Wang, A. (2017). “Simulation research of a six degrees of freedom manipulator kinematics based on Matlab toolbox,” in 2017 International Conference on Advanced Mechatronic Systems (ICAMechS), Xiamen, China, 06-09 December 2017 (IEEE), 376–380. doi:10.1109/ICAMechS.2017.8316502
Xu, B., Zhang, L., Mao, Z., Wang, Q., Xie, H., and Zhang, Y. (2020). “Curriculum learning for natural language understanding,” in Proceedings of the 58th annual meeting of the association for computational linguistics (Stroudsburg, PA: Association for Computational Linguistics), 6095–6104. doi:10.18653/v1/2020.acl-main.542
Xu, Z., Gan, Y., and Dai, X. (2019). “Obstacle avoidance of 7-dof redundant manipulators,” in 2019 Chinese Control And Decision Conference (CCDC), Nanchang, China, 03-05 June 2019 (IEEE), 4184–4189. doi:10.1109/CCDC.2019.8832418
Yan, M., Frosio, I., Tyree, S., and Jan, K. (2017). “Sim-to-real transfer of accurate grasping with eye-in-hand observations and continuous control,” in 31st conference on neural information processing systems (NIPS 2017), Long Beach, CA (Spinger).
Keywords: reinforcement learning, curriculum learning, simulation, tendon-driven system, underactuated manipulator, soft robotics, bio-inspired robot
Citation: Or K, Wu K, Nakano K, Ikeda M, Ando M, Kuniyoshi Y and Niiyama R (2023) Curriculum-reinforcement learning on simulation platform of tendon-driven high-degree of freedom underactuated manipulator. Front. Robot. AI 10:1066518. doi: 10.3389/frobt.2023.1066518
Received: 10 October 2022; Accepted: 22 June 2023;
Published: 12 July 2023.
Edited by:
Egidio Falotico, Sant’Anna School of Advanced Studies, ItalyReviewed by:
Murat Kirtay, Tilburg University, NetherlandsHari Kalidindi, Université Catholique de Louvain, Belgium
Copyright © 2023 Or, Wu, Nakano, Ikeda, Ando, Kuniyoshi and Niiyama. This is an open-access article distributed under the terms of the Creative Commons Attribution License (CC BY). The use, distribution or reproduction in other forums is permitted, provided the original author(s) and the copyright owner(s) are credited and that the original publication in this journal is cited, in accordance with accepted academic practice. No use, distribution or reproduction is permitted which does not comply with these terms.
*Correspondence: Keung Or, b3JAbWVpamkuYWMuanA=
†These authors contributed equally to this work and share first authorship
‡These authors share last authorship