- Department of Mechanical and Industrial Engineering, Louisiana State University, Baton Rouge, LA, United States
The passive, mechanical adaptation of slender, deformable robots to their environment, whether the robot be made of hard materials or soft ones, makes them desirable as tools for medical procedures. Their reduced physical compliance can provide a form of embodied intelligence that allows the natural dynamics of interaction between the robot and its environment to guide the evolution of the combined robot-environment system. To design these systems, the problems of analysis, design optimization, control, and motion planning remain of great importance because, in general, the advantages afforded by increased mechanical compliance must be balanced against penalties such as slower dynamics, increased difficulty in the design of control systems, and greater kinematic uncertainty. The models that form the basis of these problems should be reasonably accurate yet not prohibitively expensive to formulate and solve. In this article, the state-of-the-art modeling techniques for continuum robots are reviewed and cast in a common language. Classical theories of mechanics are used to outline formal guidelines for the selection of appropriate degrees of freedom in models of continuum robots, both in terms of number and of quality, for geometrically nonlinear models built from the general family of one-dimensional rod models of continuum mechanics. Consideration is also given to the variety of actuators found in existing designs, the types of interaction that occur between continuum robots and their biomedical environments, the imposition of constraints on degrees of freedom, and to the numerical solution of the family of models under study. Finally, some open problems of modeling are discussed and future challenges are identified.
Introduction
Continuum robots use material deformation to move instead of joints. They may offer a technological solution to some of the difficult challenges of locomotion, perception, and manipulation found in a variety of unstructured and uncertain environments (Robinson and Davies, 1999). Biomedical applications have been a great motivator in the development of a wide variety of continuum and soft robots, ranging from surgery to therapy and other applications involving physical human-robot interaction. The great recent interest in these design paradigms stems from the observation that success in whatever form it is needed may be achieved without having complete control over the motion of a robot or its forces of interaction with the environment. In some cases, this is advantageous simply for reducing the complexity of engineered systems, and in other cases, performance may be increased beyond what is possible with rigid machines. Several excellent examples of this general principle come from tools of modern medicine. A flexible endoscope can navigate the intestines without a great degree of control over its own shape. The same is true for an intravascular catheter. In these examples, it is the particular combination of geometry and just the right amount of mechanical “softness” that facilitates the completion of the task. Beyond this snake-in-a-pipe approach to navigation, recent research has argued that physical compliance is advantageous in grasping, underwater swimming, robustness to collision, and locomotion on soft terrains where low ground pressure is required. The interested reader is referred to several review articles for a survey of the benefits, applications, challenges, and history of soft and continuum robots (Kim et al., 2013; Burgner-Kahrs et al., 2015; Walker et al., 2016; Cianchetti et al., 2018). Figure 1 shows four examples of continuum robot architectures which range from fully hard materials to fully soft and with composite structures in between these extremes.
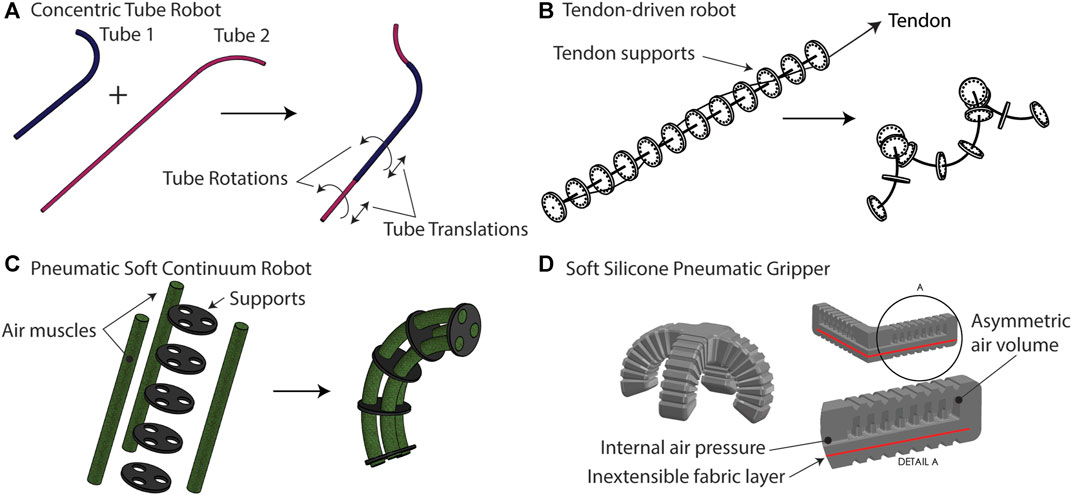
FIGURE 1. (A) Concentric tube robots are comprised of hard (metallic) tubes which are precurved and nested inside one another. Rotating and translating the tubes results in motion. (B) Tendon-driven robots use one or more tendons or cables to provide internal actuation forces that bend a flexible, slender rod. (C) Pneumatic soft continuum robots use soft air muscles, which extend or contract with internal air pressure, to create bending in a composite structure. The supports could be hard or soft materials. (D) A fully soft pneumatic gripper uses asymmetry introduced by an inextensible fabric layer and an asymmetric air volume to create four slender fingers which bend to wrap around objects.
Though there is not universal agreement on definitions, the term continuum robot is generally used to imply that motion is generated without identifiable kinematic pairs, while the term soft robot implies at least a greater degree of mechanical compliance, defined as the ratio of displacement to force, exhibited in response to environmental forces than traditional approaches to robotic interaction. Many soft robots are made of soft materials, which may be characterized in terms of a material parameter such as the modulus of elasticity (Majidi, 2014). Continuum robots made of harder materials can be designed to exhibit high or low mechanical stiffness to external forces depending on the design details.
Continuum robots are classified as under-actuated mechanisms (Spong, 1998). This statement is taken to mean that in a practical sense, and within the context of a pre-defined scope of possible robot-environment interactions, more information than can be collected by a finite set of actuator-collocated sensors is needed to describe the shape and motion of the robot to the degree of accuracy demanded by engineering specifications or by the roboticist’s preference. The practical sense of the definition is emphasized since even rigid robots with revolute or prismatic pairs must deform to a small degree when interacting with their environment via forces. All mechanical systems are underactuated when there exist flexible modes that are not actuated but which should be controlled (Spong and Laurent, 1997). It is well known that the analysis of dynamics of underactuated robots is significantly more complex than for regular, fully actuated robots (Jain and Rodriguez, 1993).
Beyond being under-actuated, the modeler of a continuum manipulator also frequently faces other challenges. Designs are often difficult to separate into “components” since the structure and the actuator may be the same physical body. Actuators based on pneumatics, hydraulics, and composite structures may not be as easily characterized as electric motors. Friction and hysteresis models may be needed to explain observed mechanics, and environments rich with expected contacts may require the solution of contact models based on theories of nonlinear complementarity. Additionally, the standard kinematic descriptions based on the rigid transformations in the special Euclidean group
This paper first reviews the state-of-the-art in the mathematical modeling of continuum manipulators having at least one “long” aspect in terms of its shape, which are termed slender in agreement with the mechanics literature. The goal of these models is to describe the dynamics (or statics) to relate actuator variables, other boundary conditions, and sensor measurements to the motion of the robot. The models are generally not concerned with other important aspects of robot design and analysis, such as repeatability, wear, safety, and other factors. For designs made of slender components, the motion of the robot is dominated by bending or beam-like deformations. This classification can be thought of as “arms,” “snakes,” or the individual “fingers” of a multi-fingered hand. Designs composed of individual components having this property are a natural extension, such as concentric tube robots (Mahoney et al., 2018) or multi-backbone continuum robots (Ding et al., 2013). For robots made of softer materials, such as the STIFF-FLOP designs, localized deformations may be complex, yet the dominant behavior is still beam-like (Cianchetti et al., 2014; Fraś et al., 2014). One of the goals of the work is to express the variety of methods encountered in the literature with a common notation. The review motivates a theoretical discussion rooted in the classical theories of solid mechanics. An analysis of the mechanics is used to support recommendations for future modeling efforts, with the conclusion that some choices for the model structure may result in better absolute model accuracy and efficiency (as quantified by the relationship between accuracy and dimensionality).
Review of the State of the Art
Table 1 presents the unified nomenclature that will be used throughout this paper. In the discussion of other works, the original nomenclature has been changed to match what is shown. There are three primary considerations in any physics-based approach to modeling of solid continua: the adoption of kinematic hypotheses and coordinates describing the configuration of the body, the application of the laws of mechanics, and the selection of mathematical models that describe the behavior of materials (Sadati et al., 2019). Kinematic hypotheses alone allow the modeler to describe the geometry of the robot, but this alone is insufficient for most purposes because it does not reveal which configurations are possible or likely. The mechanics, which are formulated naturally as partial differential equations, provide the relationships between the kinematic degrees of freedom that indicate which path of configurations will be taken if particular conditions (actuation, environments, etc.) are imposed. Finally, the material models are needed to close the relationship between the kinematic degrees of freedom and the kinetic quantities related by the mechanics.
Kinematic Descriptions
The forebears of continuum manipulators are the hyper-redundant robots, defined as those having a large (or infinite in the case of continuum robots) relative degree of redundancy (Chirikjian and Burdick, 1994). In any robot with material deformation which is substantial with regard to the kinematics or dynamics, both the relative degree of redundancy and the degree of under-actuation are theoretically infinite since the configuration space is infinite-dimensional. Here the usual definition of a robot configuration is used: “a complete specification of the location of every point on the robot” (Spong et al., 2006). There have been two primary methods to date of describing the configuration of continuum and soft robots: the curve-based description and the general continuum description.
The Curve-Based Description
The state of the art curve-based description is that of the special Cosserat rod (Antman, 2005). Figure 2 depicts the curve, its relationship to a solid body, and the quantities that are associated with the curve and the boundary conditions of a mechanical model. The elongated form of many continuum manipulators leads naturally to the concept of the “backbone curve,” which is typically defined to be a time-varying, piecewise differentiable curve in the standard three-dimensional affine Euclidean space
The usual type of modeling hypothesis for slender bodies is that other points, which are not located on the backbone, are described by some auxiliary relationship that describes their positions relative to the positions on the backbone. The standard theories from beam mechanics may be adopted for this purpose, in which case the backbone curve may be affixed to the body at the neutral axis of bending1. One example is the Euler-Bernoulli hypothesis, which states that sections normal to the backbone remain normal for all deformations. Another is the hypothesis due to Timoshenko stating that normal sections rotate relative to the backbone but remain planar. Standard “warping” theories can be used to couple motion of the points normal to the sections with twisting about the backbone if the sections are not circular. Regardless of these additional hypotheses, the curve is of fundamental importance to the kinematic description.
Explicitly, the body of the robot is identified by the curve through the consideration of a reference configuration
The vectors
Finally, the vectors
The General Continuum Description
The second approach to describing the configuration of continuum robots is to make as few prior kinematic hypotheses on the configuration as possible. The traditional description of a three-dimensional continuum in solid mechanics is used in this case. In this approach a reference configuration
The amount of stretching can be quantified by the deformation gradient, defined by
The deformation gradient straightforwardly describes the local changes in length (amount of stretching) and therefore plays a major role in the definition of strain measures. Note also that the curve-based description of the configuration, together with the classical Euler-Bernoulli hypothesis, can be placed into this more general framework using
Perspective on Discretization and Configuration Spaces
There are two perspectives that one might take when describing the kinematics or mechanics of continua. In the first perspective, the model consists of a (possibly nonlinear) PDE, a domain on which the PDE applies, and boundary conditions in the form of constraints or measurements. The robot’s state space consists of the dependent variables related by the PDE. The state space is therefore a particular Cartesian product space that might involve, in general, both finite-dimensional spaces and infinite-dimensional function spaces. In the process of computing a numerical solution to a model, any part of the state that belongs to an infinite-dimensional space must be approximated by a finite set of coordinates in
In a second perspective, the equations of an infinite-dimensional model are explicitly discretized through a suitable method such as the finite element method or a finite difference method (Renda et al., 2014; Back et al., 2015; Gilbert and Godage, 2019) or via a spectral method involving a “modal” decomposition (Chirikjian and Burdick, 1994; Godage et al., 2015; Chen et al., 2020). In this perspective, the modeler takes control over the discretization and fixes the dimensionality of the resulting model. One is free to take the perspective that a new model has been created that is not necessarily subordinate in any way to the infinite-dimensional model. In other words, the infinite dimensional dependent variables, ODEs, and/or PDEs, were only a steppingstone to the finite-dimensional model. The dimension may be varied according to a model hyper-parameter
The second perspective is the standard one in generally accepted theories of robot kinematics and dynamics, in which the goal is to find a suitable coordinate set that describes the displacement field
For continuum and soft robots, neither the perspective (finite vs. infinite-dimensional) nor the approach to discretization (choice of coordinates) appears to be standardized. In some cases, restrictive assumptions do allow a set of finite coordinates that uniquely specify the configuration of a continuum robot. For example, Bretl and McCarthy showed that for the Kirchhoff rod with no external loading, a configuration space isomorphic to
with
However, with less restrictive assumptions, low-dimensional configuration spaces are not generally found. Such is the case for parallel continuum robots (Black et al., 2018), for growing robots (Greer et al., 2019), or soft robotic hands (Schlagenhauf et al., 2018). It is in general impossible to find a “minimal” set of coordinates for the C-space of any continuum manipulator when the locations and nature of external loads or contacts are a-priori unknown and when these loads cause substantial changes in the robot shape. The subsections that follow describe a variety of methods that have been used to mathematically represent the configurations of continuum robots.
Spectral Methods
Spectral methods were some of the earliest described methods for the kinematic modeling of backbone curves. In this method, the configuration is represented by a finite number of coordinates
The function
There is a great deal of freedom within this approach. For example, the tangent vector
In the context of continuum robots, to the best of the author’s knowledge, the spectral methods have only been applied in conjunction with the curve-based descriptions discussed in The Curve-Based Description and not for more general continuum descriptions.
Element-Based Methods: PCC
The element-based methods, in contrast to the spectral methods, break up the problem spatially into adjacent sub-domains and attempt to model the kinematics on each sub-domain using a simpler hypothesis. This procedure can be carried out for both the curve-based description and the general continuum description. Many authors have adopted the kinematic hypothesis that the backbone curve is a sequence of circular arcs which are concatenated by imposing tangency conditions. There is a natural extension of this idea to piecewise helical curves. This approximation is termed the “piecewise constant curvature” (PCC) method, and many continuum robots have even been designed to exhibit deformation of this kind, at least in the absence of external loads (Webster and Jones, 2010). For example, multi-backbone robots and tendon-driven robots will adopt, with actuation, shapes very close to circular arcs with appropriate design decisions (Camarillo et al., 2008; Xu and Simaan 2008). On the other hand, even gravitational loading may cause more flexible robots to adopt shapes more complex than a single circular arc (Trivedi et al., 2008).
Within the curve-based framework described above, the “standard” PCC hypothesis including inextensibility and shear-lessness is equivalent to a partitioning of the domain into
A similar approach is called the piecewise constant strain (PCS) method and extends the definition to include an approximating sum representing
The major advantage of the PCC method is that the extrinsic variables
The mapping
The coefficient functions are as follows, with
In IEEE-754 double-precision arithmetic, the author has found that
The PCC and/or PCS methods are the simplest explicit and consistent discretization methods for a framed curve which interpolate the intrinsic (strain) variables rather than the extrinsic (position and orientation) variables. In other words, given a curve with bounded flexural, torsional, shear, and extensional strains, the error between the curve and its PCC or PCS approximation (both in terms of
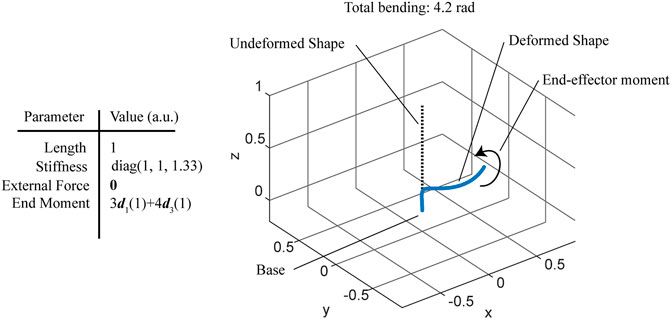
FIGURE 3. Simulation of a cantilevered rod under a combined bending and twisting concentrated moment, forming a helix.
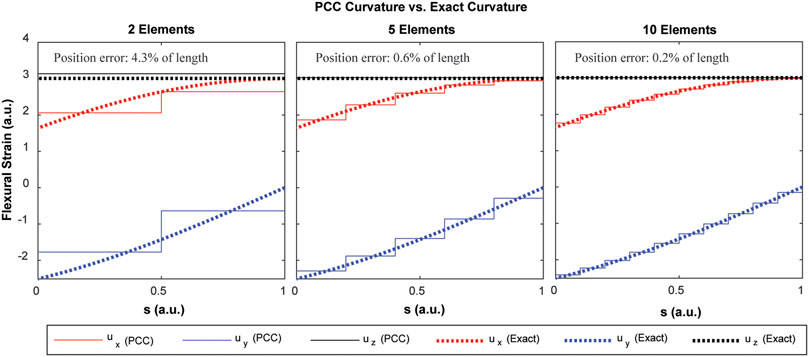
FIGURE 4. Convergence of the PCC discretization to the exact flexural strains of the helical rod shape depicted in Figure 3. Note that the exact flexural strain components are not constant functions of arc length.
Element-Based Methods: Higher-Order One-Dimensional
The discretization of the curve into elements can also be accomplished with higher-order schemes than the piecewise constant strain approach. In general, as with the PCC approach if a boundary condition
The union operator is abused to mean here that the element-local terms contained within each argument of the union are “assigned” to provide the evaluation on that element. The coordinate
Other representations for the C-space based on segmentation into elements are possible but have not been widely pursued within the robotics community. Certainly, the more widely adopted approach within the finite element and computational mechanics communities has been to make the primary kinematic hypothesis at the level of
Element-Based Methods: General Continuum
More general finite-element descriptions have also been used to model soft and continuum robots. In this case, the degrees of freedom
Direct Nodal Discretization
Closely related to the element-based methods are those based on direct discretization of the variables. Differential operators in the mechanics can be replaced by their equivalent finite-difference operators to form algebraic equations directly, operating on the values of field variables specified at discrete spatial locations
Pseudo-Rigid Body Methods
The pseudo-rigid body methods replace the continuum with an approximating rigid linkage. If the curve is broken into a sequence of chords with rotational joints at the nodes joining the chords, then this is equivalent to a spatial “lumping” of the flexural strains into a discrete point via the use of the Dirac delta distribution (Chirikjian and Burdick, 1991; Greigarn et al., 2019).
A universal joint is the result if two orthogonal axes
It has been shown that the kinematics of tip-loaded cantilever beams can be modeled adequately by a serial 3R mechanism (Su, 2009). Other PRB models have been created for modeling of catheters (Ganji and Janabi-Sharifi, 2009), tendon-driven continuum manipulators for minimally invasive surgery (Penning and Zinn, 2014), and MRI-actuated catheters (Greigarn et al., 2017). A 6-DOF PRB segment model has also been proposed (Venkiteswaran et al., 2019). An equivalence has also been shown between the coordinates of a PCC model and a suitably defined pseudo-rigid body model, indicating that PRB model segments with RPPR kinematics can be used to describe the same configuration space as PCC models (Katzschmann et al., 2019a).
Initial Value Problem Concepts
There are additionally a variety of other methods of analysis and computation which do not explicitly select the degrees of freedom in the kinematic description. In these methods, the unknowns are conceptually left as unknown functions, and numerical methods are used which automatically select the degrees of freedom used to represent the unknown functions, usually via an error estimation and control algorithm.
These methods have been used when the problem is re-cast as a one-dimensional boundary value problem with split boundary conditions.
Solutions can then be provided by numerical codes which automatically determine the degrees of freedom used to approximate the function
Differential Kinematics for Strain-Variable Hypotheses
It is often necessary to calculate a manipulator “Jacobian field” based on the curve parametrization, and if the generalized coordinates are defined to interpolate the strain variables, this field is not trivial to calculate.
Letting
One must take care when the interpolation is carried out on the strain variables in coordinates of the local frame
From a known boundary condition where
Mechanics
Regardless of how the shape of a robot is described, the principles of classical mechanics are frequently used to describe the relationships between the model’s degrees of freedom, the internal stresses, and any imposed boundary conditions which may include external forces, imposed positions or orientations of parts of the robot, contact conditions. The robot’s actuators may generally be modeled in one of two ways: either they are described as constraints (a form of boundary condition) or as sources of internal stress.
The Equations of Motion for the Special Theory of Cosserat Rods
In the curve-based description, the equations of motion of the special theory of Cosserat rods serve as the strong form differential equations governing the mechanics (Antman, 2005).
The sum from
In the case of a model which allows freedom in all the strain variables,
The parameter
The Equations of Motion for Pseudo-Rigid Body Models
With the PRB-type models, the equations of motion are exactly those of a classical multibody dynamical system with scleronomous, holonomic constraints. These equations are commonly given as follows (Murray et al., 2017).
The right-hand side contains the non-conservative generalized forces associated with actuation and any other forces; since the robots are underactuated there are generally many more rows in this equation than actuator variables
The Equations of Motion for General Deformable Bodies
The dynamic equilibrium conditions of classical continuum mechanics serve as the defining relationship for general three-dimensional finite element models of soft and continuum robots. Rarely are these equations encountered explicitly in the literature on continuum robots, with most authors preferring to state the result after the strong form equations have been converted to the weak form and integrated. The resulting equations, incorporating constraint forces, are of the following form (Goury et al., 2021).
The form of this equation is directly analogous to the classical form of the dynamical equations for rigid multibody systems.
Projection via D’Alembert’s Principle
In the case of the curve-based models using either the PCS or higher-order models, the equations can be projected onto the degrees of freedom of the model using Galerkin’s principle, probably better known among mechanical engineers as the principle of virtual work (Greenwood, 1988). The method is also equivalent in results to Kane’s method of virtual power (Kane and Levinson, 1983; Rone and Ben-Tzvi, 2014). Because the backbone curve descriptions for the PCC, PCS, and higher order strain variable interpolants are described by independent degrees of freedom
The velocity coefficient function and angular velocity coefficient function are defined as
The velocity coefficients are the “Jacobian field” satisfying the relation Eq. 2.
Since the time derivatives of the momentum density and angular momentum density,
In the local frame, the equations take the following forms.
Note also that if
Finally, note that if more than one rod-like body is present, then a sum over the bodies takes place in Eq. 5. Explicit constraints between the bodies may be handled via the method of Lagrange multipliers.
Learning-Based Approaches
Learning-based approaches, which are also sometimes referred to as “model-free” approaches, may be able to describe the relationships between the actuator inputs and observable outputs such as the end-effector motion without recourse to physical parameters and the laws of mechanics. These models usually serve a complementary purpose to those based on physical first principles. Since they require training data from a real robot or from another simulation model, they may be used for on-line control, inverse and forward kinematics, or for off-line analysis and testing of other algorithms such as for navigation and control. The a-priori prediction of behaviors from only design data is generally not possible to date using only learning-based methods.
A variety of purely kinematic approaches have been proposed. One learning approach uses an on-line estimation of the Jacobian matrix relating the time derivatives of the actuation variables
It has also been shown that dynamic models may be learned. Under a state observation of the form
There are also learning-based approaches to control which do not explicitly construct kinematic or dynamic models. One such approach is based on direct learning from demonstration in the actuator space, which was successfully demonstrated on a tendon-driven continuum manipulator (Xu et al., 2016). Learning can form a part of a.
Actuator Models
Actuators in continuum and soft robots have been classified as either extrinsic, in which case the actuators are not a part of the deformable body, or intrinsic, in which case the actuators are an integral part of the deformable body. Examples of the former include tendons, the boundary conditions placed on concentric tube robots. Examples of the latter include soft pneumatic muscles (Walker et al., 2016).
The actuators may be modeled (very generally) as relationships between the actuation variables, generalized forces, and the dynamic state of the robot consisting of q and
However, the nature of the model may change depending on the exact form of
A first example is the model of a fiber-reinforced elastic actuator, in which
Another explicit example is found in the case of a tendon-driven robot. If enough support for the tendon is provided, a reasonable model for the points occupied by the tendon is a continuous curve described by
If the tendons are not fully constrained, other models for
Therefore, the effect of the tendon alone (not considering any frictional forces) must be
Note that the causal form in which the tendon tensions are known is “easier” to handle since no additional equations must be added. The causal form involving known tendon lengths requires the addition of the nonlinear length constraints Eq. 6 to the equation set and the tension becomes an algebraic unknown along with the accelerations, forming a nonlinear differential-algebraic system in the dynamic case or a nonlinear algebraic system in the quasistatic case. The need to solve a DAE system disappears if the tendon is considered a spring element, since then the force is determined as a function of the difference between
The resulting model form as a set of ordinary differential equations or differential algebraic equations is shown for a variety of common continuum robot actuators in Table 2.
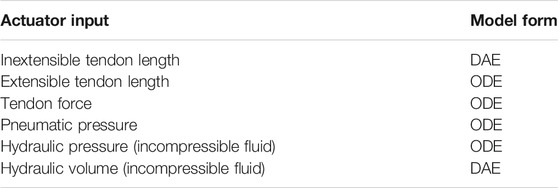
TABLE 2. Model form as an ODE or DAE system based on actuator type, assuming a single rod model architecture for the model.
Materials
The kinematic hypotheses and mechanics models must be augmented by constitutive laws (material models) to complete the model of a continuum robot. For quasistatic models, the choice is usually between linear elasticity and other hyperelastic material models. For dynamic models, an additional choice of damping or friction laws is generally required to produce realistic responses.
Linear Elasticity
In the case of quasistatic models, a common assumption in the literature has been to assume a Hookean (linear) material response. In this case, if one assumes that the backbone curve passes through the neutral axis of bending, the following constitutive laws apply:
The matrices
Note that bending about
Hyperelastic Material Models
Many other hyperelastic models are possible choices, such as Yeoh, neo-Hookian, Gent, Ogden, and Mooney-Rivlin (He et al., 2018; Shiva et al., 2019; Zhang et al., 2019; Antonelli et al., 2020; Bacciocchi and Tarantino, 2021; Zhao et al., 2021). Although in general one may expect that these more complex material models should offer improved model accuracy, it has been shown recently that, at least for some robot designs, a linear stress-strain response may be more than adequate (Shiva et al., 2019). Any hyperelastic law can be represented within the Cosserat rod framework as a strain energy density function
The details of these calculations for each of the respective hyperelastic models is omitted for the sake of brevity and can be found in the cited references.
Damping and Friction
The introduction of dissipative mechanisms is generally necessary to encourage numerical stability in dynamic models and to produce realistic dynamic responses. Additionally, in some cases static friction plays a significant role in determining the quasistatic solutions, such as in tendon-driven catheters (Jung et al., 2014). Viscous damping may be introduced via the Kelvin-Voigt material model, which extends the linear elastic models to include rate-dependence in the stress-strain relationship (Gilbert and Godage, 2019; Mustaza et al., 2019).
In the curve-based framework, the Kelvin-Voigt law takes the following form (Linn et al., 2013):
The matrices
Static friction models have also been considered for concentric tube robots (Lock and Dupont, 2011), tendon-driven continuum robots (Li et al., 2020), and continuum robots having sheathed tendons or multiple actuated backbones (Roy et al., 2017).
Discussion
The wide variety of modeling choices that have been described offer the modeler an almost paralyzing array of choices. In the subsections that follow, several questions are posed. The available evidence from the literature as well as analyses guided by classical theories of mechanics are used to discuss these questions and to provide guidance during the initial stages of selecting modeling approaches.
Considerations for Kinematic Hypotheses
The literature on modeling of continuum and soft robots suggests that errors in kinematic models, quantified by the absolute tip positioning error as a percentage of the overall root length, are typically on the order of a few percent. Therefore, there may be little benefit to increasing the order of a spectral method or to further subdividing the domain in an element-based method once the absolute accuracy with respect to the true solution reaches this point. In the sections that follow, analysis and recommendations for kinematic hypotheses which are derived from consideration of the mechanics of bending are offered. Table 3 provides a summary of the recommendations in terms of increasing either the number of elements or the order of the interpolation (assuming that

TABLE 3. Summary of recommendations to increase either the number of elements or the order of interpolants based on model assumptions and robot-environment conditions.
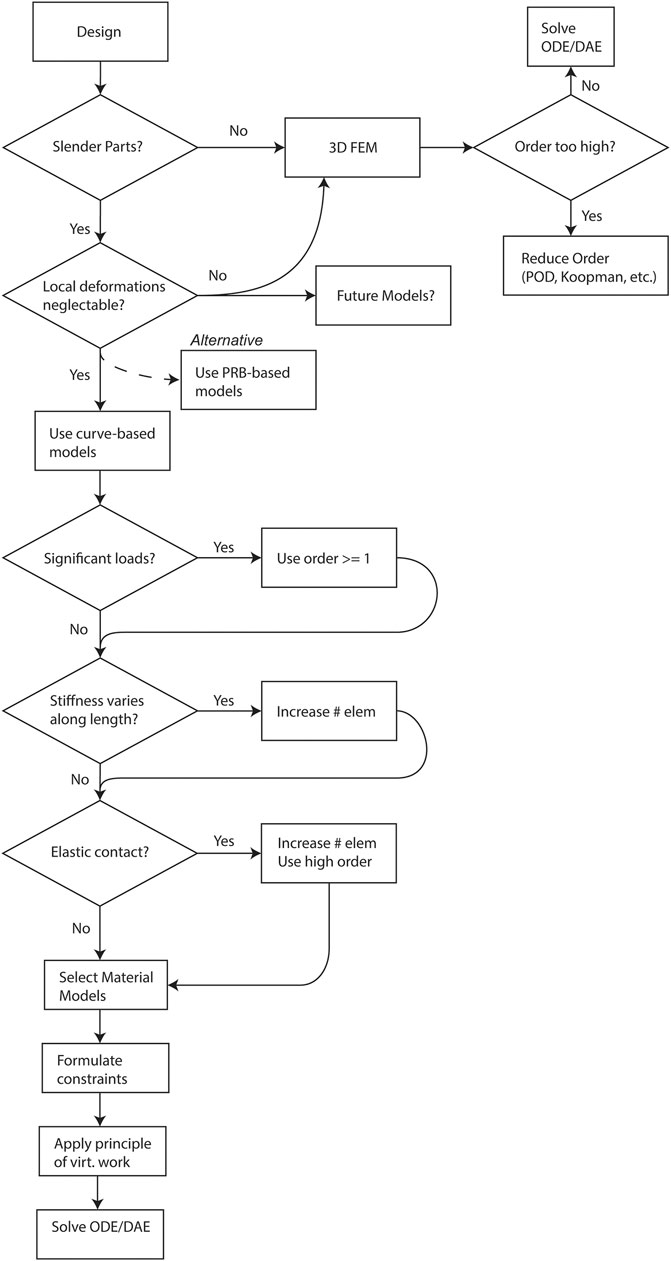
FIGURE 5. Flowchart depicting the modeling decisions to be made when selecting a model type for a biomedical continuum robot.
Considerations for Cantilevered Concentrated Loadings
For continuum robots which are soft enough to exhibit substantial compliance to environmental loads (for example those that may be presented by contact with human anatomy), one of the first considerations for modeling should be consistency with the requirements for accurately modeling cantilevered, concentrated loads.
Let the Cosserat rod equations be recast in terms of the angle of the tangent vector and the load and deformation fixed to the plane defined by
The boundary value problem has a known solution:
The quantity
The PRB models have the attractive property that they map the problem back into the domain of traditional robotic manipulators, with the obvious advantage that all the tools and knowledge that have been developed in that context (in general, restricted to underactuated mechanisms) now apply to the continuum robot. In the traditional PRB models, the inertia properties are lumped into the links formed by the model, and the stiffness and damping properties are lumped into the joints between links. This lumping introduces error, but it has been shown that optimization of the parameters of the rigid body model can lead to accurate mechanical responses for both cantilevered transverse loads and for applied or internal moments (Chen et al., 2011). Given that the optimal 3R planar PRB model has three degrees of freedom, it is a fair comparison to place the model in competition with other three-DOF models. Here we consider the following three sets of potential kinematic hypotheses and matching constitutive laws and compare them with each other and with the exact solution. Without loss of generality, let
Piecewise constant curvature:
PRB:
Spectral:
How well does each of the strategies perform when given 3-DOF to capture the deformation? The answer is depicted in Figure 6, showing tip position error in percent of robot length versus the dimensionless cantilevered load index
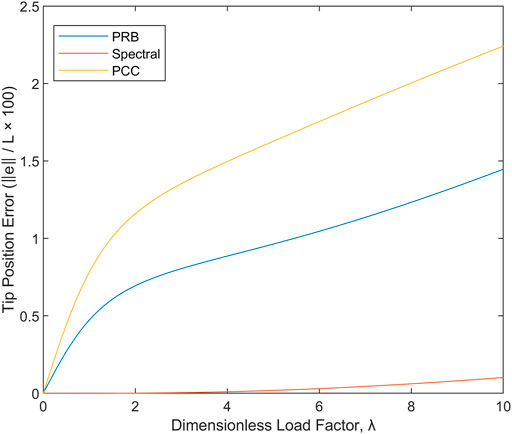
FIGURE 6. Error in reproducing the correct behavior under cantilevered loading conditions for three-DOF kinematic hypotheses of the PCC, PRB, and spectral types.
The results imply that the typical piecewise constant-curvature assumption used in the development of geometrically nonlinear models for robots is a poor choice from the perspective of mechanics whenever a concentrated external load is present and is expected to produce internal shear forces which are transverse to
Considerations for Non-Uniform Flexural Rigidity
In the case of non-uniform flexural rigidity, element refinement is more effective at reducing approximation error than increases in order. This conclusion is easily justified by the observation that if
Considerations for Uniformly Distributed Loads
Distributed loads may act on biomedical continuum robots. The most obvious of these loads is a gravitational force distributed along the length of the robot. Other common forces may include buoyancy forces, electric forces, magnetic forces, and aerodynamic and hydrodynamic forces. The simplest possible model of a distributed load is a uniform one that is applied normal to the body of a robot which is initially in a straight configuration. In this case, the solution to the linearized Euler-Bernoulli equation is in general a fourth-order polynomial in position. The shear force is a linear function of arc length and the internal moment (and hence curvature in the linear elastic case) is quadratic. If the shape is discretized at the level of angle, the discretization should be cubic to accommodate a uniform load.
Considerations for Elastic Environmental Contact
For continuum robots in contact with soft bodies such as the soft tissues of the human anatomy, the contact might be well-described, at least in the region of contact, by a model like the linear elastic foundation model. For small deflections, the linearized Euler-Bernoulli model with a linear elastic foundation is modeled by the following differential equation (see Figure 7A).
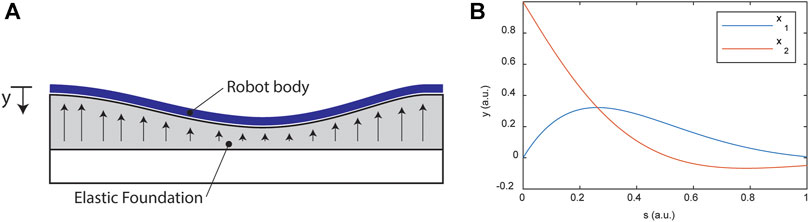
FIGURE 7. (A) Schematic diagram for the beam on an elastic foundation as a model for a continuum robot interacting with soft tissue. (B) Example with
The homogeneous solution to this equation has the following form.
The constant
To what degree of accuracy does a polynomial shape function (assuming the small-deflection case) approximate
To answer this question, one should find the best approximation of
The physical solutions to the equation decay away from the application of a point load. Therefore, we restrict the approximation problem to the consideration of the two functional forms that follow on a domain
See Figure 7B for examples with
For a single 5th order polynomial in shape, the maximum absolute error in approximating either
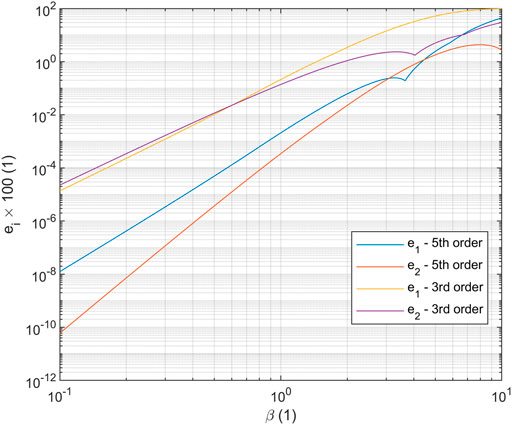
FIGURE 8. Approximation errors for best polynomial fits in the L2 norm to the solution for the linear beam on an elastic foundation problem. Higher-order polynomials permit greater elastic foundation stiffnesses.
To put this in a practical perspective, a typical colonoscope has a linearized flexural rigidity of
Considerations for Numerical Methods
Solution Multiplicity
In general, the problem defined by Eq. 5 together with any constraints is a nonlinear algebraic problem, even if linear material models are used. This is either a consequence of the nonlinear geometry, which shows up in any finite-strain relationship between the strain variables and the position and orientation of the body, or a consequence of nonlinear material behavior, or both. In special cases, the problem may become linear; for example, if the actuators and generalized forces are related linearly, linear constitutive laws are used, and no external loads are present. For nonlinear static problems, the Newton-Raphson method and trust-region methods like the Levenberg-Marquardt method generally work well, but the modeler must be cautious of the possibility of solution multiplicity.
In other words, a function
It is evidently at configurations with singular
Time Stepping
For time stepping, explicit ode integrators can become prohibitively computationally expensive. This is a consequence of the fact that unresolved vibrational modes (as defined for linear test problems) become unstable using explicit methods. Implicit integrators and those designed for solving stiff ODEs and DAEs, such as the trapezoidal method or the backwards difference formulae, are preferable. Energy-preserving integrators have the benefit that the damping behavior is caused entirely by the material model, ensuring repeatable dynamic behavior with different time steps.
Current and Future Challenges in Modeling
Generalizability and Re-Usability
Despite the growing body of evidence that models built on the foundation of the Cosserat rod equations are an adequate description of many continuum robots, one challenge that still faces practitioners is a lack of standardized tools to build new model simulation codes. For rigid robots, a wide variety of domain-specific modeling languages are available and permit concise descriptions within an easy-to-use interface to build new models. One example of this is the Universal Robot Description Format and Gazebo simulator within the Robot Operating System, but there are many others presently available including Simulink/Simscape, Dymola, and other Modelica-language based toolsets such as OpenModelica (Brück et al., 2002; Fritzson et al., 2006; Miller and Wendlandt, 2011; Sucan and Kay, 2019). To enable the widespread re-use of validated modeling components, a library of reusable “model building blocks” for continuum robots should be designed. Some important capabilities of such a library would be the following:
• Coupling of curve-based models to rigid multibody models.
• Coupling of curve-based models and general finite element models.
• Incorporation of common actuator models.
• Incorporation of common constraints (length, concentricity, no-penetration, selective inextensibility/strong anisotropy, revolute and prismatic joints, etc.)
• User-selected switching between dynamic and quasi-static model generation.
For biomedical continuum robots in particular, models which couple to mechanical models of human anatomy are needed. Coupling of state-of-the-art models for continuum robots or their direct incorporation with real-time finite element codes using GPU acceleration is a promising approach (Allard et al., 2007; Duriez and Bieze, 2017).
Novel Kinematic Hypotheses
There is a great deal of freedom in element-based kinematic hypotheses which has yet to be explored. One interesting avenue is the use of a shared or constrained DOF between elements. The motivation for this idea is that for dynamic models, time stepping is sometimes restricted or difficult for “stiff” problems having many eigenvalues. The equations of motion for solid continua are wave equations, which means that if many elements are stacked end-to-end, acoustic waves (axial compression and tension) and twist waves (torsional waves) through the structure may be resolved by the model. For most robotics applications, these modes are likely to be irrelevant, and constraining the problem so that they do not exist in the model may improve computational performance. The elimination of twist waves in elastic rod models was previously considered by an energy minimization argument (Bergou et al., 2008).
Furthermore, adaptive kinematic hypotheses based on pre-defined, switchable degrees of freedom that permit local, automatic refinement of the model may allow greatly improved computational efficiency in problems involving a-priori unknown environmental interactions or constraints. This will permit, for example, a single high-order element to describe the deformation in free-space, while local refinement can take place where a catheter contacts a vessel wall, a robotic endoscopic system contacts the colon, or where multi-fingered hands contact an object to manipulate it.
Learning
Within the context of continuum and soft robotics, data-driven methods have begun to demonstrate strong utility. For example, Long Short Term Memory networks can capture hysteresis in pneumatically actuated catheters (Wu et al., 2021), and offline simulation of first-principles models can be used to learn reduced-order models using the snapshot-based proper orthogonal decomposition, resulting in new models suitable for real-time control and other applications requiring fast computation (Goury and Duriez, 2018; Katzschmann et al., 2019b). The continued development of learning methods enabling low-DoF representations will be an important future area of research.
There are also interesting opportunities for learning that amalgamate first-principles models with data-driven model “correctors,” or which use constrained learning techniques to identify models which are topologically like a curve-based model. One possibility is to use a low-DOF curve-based model capturing some of the behavior and to introduce a nonconservative generalized force
Dynamic Model Validation
Although many dynamic models have been proposed, the validation of these models is currently lacking. There are many opportunities for rigorous evaluation and comparison of models with experimentally obtained data. The best and strongest form of model validation would be to instrument real robots with enough sensors to measure all the quantities appearing in Eq. 5 or the equivalent formulations for PRB and general continuum models, and to calculate the model residuals over conditions ranging over static, low-acceleration, and high-acceleration (e.g. sudden contact) regimes. This is clearly a challenging experimental task that may require state reconstruction and many sensors just to measure the configuration trajectory
There are also many other interesting questions that can be asked and answered which are quantitative in a different sense, but which may be even more aligned with the spirit of soft and continuum robotics theory. For example, a model and simulated controller could be used to predict the success or failure of the navigation of a robotic catheter through tortuous vasculature parameterized by some measure of “tortuosity,” and then the classification error could be assessed via experiment matching the simulations.
Conclusion
Continuum robots offer solutions to problems in biomedical applications which may not be solvable by traditional robotics technologies. With these new robots came the need for new models. A wide variety of physics-based and learning-based approaches to the modeling of continuum manipulators—both those made of hard materials and soft materials—are now available to the roboticist who needs them. This can lead to a dizzying array of choices for the uninitiated. This manuscript has reviewed the state-of-the-art approaches using a common language, discussed considerations which can guide the modeler when selecting which methods to use and some numerical difficulties to be aware of, and offered a view of the current and future challenges in the modeling of continuum robots. As modeling techniques continue to improve in terms of predictive power, as techniques begin to standardize, and as system identification techniques for soft and continuum robots mature, there is every reason to expect that the field will continue to expand, find new applications, and ultimately lead to transformative robotic solutions for human problems.
Data Availability Statement
The raw data supporting the conclusion of this article will be made available by the authors, without undue reservation.
Author Contributions
HG is solely responsible for all aspects of this manuscript.
Funding
This material is based upon work supported by the National Science foundation under Grant No. 2024795. Any opinions, findings, and conclusion or recommendations expressed in this material are those of the author(s) and do not necessarily reflect the views of the National Science Foundation.
Conflict of Interest
The author declares that the research was conducted in the absence of any commercial or financial relationships that could be construed as a potential conflict of interest.
Publisher’s Note
All claims expressed in this article are solely those of the authors and do not necessarily represent those of their affiliated organizations, or those of the publisher, the editors and the reviewers. Any product that may be evaluated in this article, or claim that may be made by its manufacturer, is not guaranteed or endorsed by the publisher.
Footnotes
1There are additional considerations for this placement in the case of dynamical models, discussed below.
References
Ahmadi, M., Topcu, U., and Rowley, C. (2018). “Control-Oriented Learning of Lagrangian and Hamiltonian Systems,” in 2018 Annual American Control Conference (ACC), Milwaukee, WI, June 27–29, 2018, 520–525. doi:10.23919/ACC.2018.8431726
Allard, J., Cotin, S., Faure, F., Bensoussan, P.-J., Poyer, F., Duriez, C., et al. (2007). “SOFA - an Open Source Framework for Medical Simulation,” in MMVR 15 - Medicine Meets Virtual Reality, Palm Beach, 13–18.
Ansari, Y., Falotico, E., Mollard, Y., Busch, B., Cianchetti, M., and Laschi, C. (2016). “A Multiagent Reinforcement Learning Approach for Inverse Kinematics of High Dimensional Manipulators with Precision Positioning,” in 2016 6th IEEE International Conference on Biomedical Robotics and Biomechatronics (BioRob), Singapore, June 26–29, 2016 (IEEE), 457–463. doi:10.1109/BIOROB.2016.7523669
Antman, S. S. (2005). Nonlinear Problems of Elasticity. 2nd ed. Applied Mathematical Sciences, (Springer).
Antonelli, M. G., Beomonte Zobel, P., D’Ambrogio, W., and Durante, F. (2020). Design Methodology for a Novel Bending Pneumatic Soft Actuator for Kinematically Mirroring the Shape of Objects. Actuators 9 (4), 113. doi:10.3390/act9040113
Asadian, A., Kermani, M. R., and Patel, R. V. (2011). “An Analytical Model for Deflection of Flexible Needles during Needle Insertion,” in 2011 IEEE/RSJ International Conference on Intelligent Robots and Systems, San Francisco, CA, September 25–30, 2011, 2551–2556. doi:10.1109/IROS.2011.6094959
Bacciocchi, M., and Tarantino, A. M. (2021). Finite Bending of Hyperelastic Beams with Transverse Isotropy Generated by Longitudinal Porosity. Eur. J. Mech. - A/Solids 85 (1), 104131. doi:10.1016/j.euromechsol.2020.104131
Back, J., Manwell, T., Karim, R., Rhode, K., Althoefer, K., and Liu, H. (2015). “Catheter Contact Force Estimation from Shape Detection Using a Real-Time Cosserat Rod Model,” in 2015 IEEE/RSJ International Conference on Intelligent Robots and Systems (IROS), Hamburg, Germany, September 28–October 2, 2015 (IEEE), 2037–2042. doi:10.1109/IROS.2015.7353647
Bergou, M., Wardetzky, M., Robinson, S., Audoly, B., and Grinspun, E. (2008). Discrete Elastic Rods. ACM Trans. Graph. 27, 1–12. doi:10.1145/1360612.1360662
Bieze, T. M., Largilliere, F., Kruszewski, A., Zhang, Z., Merzouki, R., and Duriez, C. (2018). Finite Element Method-Based Kinematics and Closed-Loop Control of Soft, Continuum Manipulators. Soft Robotics 5 (3), 348–364. doi:10.1089/soro.2017.0079
Bishop, R. L. (1975). There Is More Than One Way to Frame a Curve. The Am. Math. Monthly 82 (3), 246–251. doi:10.1080/00029890.1975.1199380710.2307/2319846
Black, C. B., Till, J., and Rucker, D. C. (2018). Parallel Continuum Robots: Modeling, Analysis, and Actuation-Based Force Sensing. IEEE Trans. Robot. 34 (1), 29–47. doi:10.1109/TRO.2017.2753829
Boyer, F., Ali, S., and Porez, M. (2012). Macrocontinuous Dynamics for Hyperredundant Robots: Application to Kinematic Locomotion Bioinspired by Elongated Body Animals. IEEE Trans. Robot. 28 (2), 303–317. doi:10.1109/TRO.2011.2171616
Boyer, F., Lebastard, V., Candelier, F., and Renda, F. (2021). Dynamics of Continuum and Soft Robots: A Strain Parameterization Based Approach. IEEE Trans. Robot. 37, 847–863. doi:10.1109/TRO.2020.3036618
Bretl, T., and McCarthy, Z. (2014). Quasi-Static Manipulation of a Kirchhoff Elastic Rod Based on a Geometric Analysis of Equilibrium Configurations. Int. J. Robotics Res. 33 (1), 48–68. doi:10.1177/0278364912473169
Brockett, R. W. (1984). “Robotic Manipulators and the Product of Exponentials Formula,” in Mathematical Theory of Networks and Systems. Editor P. A. Fuhrmann (Berlin, Heidelberg: Springer), 120–129. Lecture Notes in Control and Information Sciences. doi:10.1007/BFb0031048
Brück, D., Elmqvist, H., Olsson, H., and Mattsson, S. E. (2002). “Dymola for Multi-Engineering Modeling and Simulation,” in 2nd International Modelica Conference, Oberpfaffenhofen, Germany, March 18–19, 2002, 55-1–55–58.
Bruder, D., Fu, X., Gillespie, R. B., Remy, C. D., and Vasudevan, R. (2021). Data-Driven Control of Soft Robots Using Koopman Operator Theory. IEEE Trans. Robot. 37, 948–961. doi:10.1109/TRO.2020.3038693
Burgner-Kahrs, J., RuckerRucker, D. C., and Choset, H. (2015). Continuum Robots for Medical Applications: A Survey. IEEE Trans. Robot. 31 (6), 1261–1280. doi:10.1109/tro.2015.2489500
Camarillo, D. B., Milne, C. F., Carlson, C. R., Zinn, M. R., and Salisbury, J. K. (2008). Mechanics Modeling of Tendon-Driven Continuum Manipulators. IEEE Trans. Robot. 24 (6), 1262–1273. doi:10.1109/TRO.2008.2002311
Chen, G., Xiong, B., and Huang, X. (2011). Finding the Optimal Characteristic Parameters for 3R Pseudo-rigid-body Model Using an Improved Particle Swarm Optimizer. Precision Eng. 35 (3), 505–511. doi:10.1016/j.precisioneng.2011.02.006
Chen, J., and Lau, H. Y. K. (2016). “Learning the Inverse Kinematics of Tendon-Driven Soft Manipulators with K-Nearest Neighbors Regression and Gaussian Mixture Regression,” in 2016 2nd International Conference on Control, Automation and Robotics (ICCAR) (Hong Kong: IEEE), 103–107. doi:10.1109/ICCAR.2016.7486707
Chen, Y., Wang, L., Galloway, K., Godage, I., Simaan, N., and Barth, E. (2021). Modal-Based Kinematics and Contact Detection of Soft Robots. Soft Robotics 8, 298–309. doi:10.1089/soro.2019.0095
Cheng, H., and Gupta, K. C. (1989). An Historical Note on Finite Rotations. J. Appl. Mech. 56 (1), 139–145. doi:10.1115/1.3176034
Chirikjian, G. S., and Burdick, J. W. (1994). A Modal Approach to Hyper-Redundant Manipulator Kinematics. IEEE Trans. Robot. Automat. 10 (3), 343–354. doi:10.1109/70.294209
Chirikjian, G. S., and Burdick, J. W. (1991). “Hyper-Redundant Robot Mechanisms and Their Applications,” in IEEE/RSJ International Workshop on Intelligent Robots and Systems ’91, Osaka, Japan, November 3–5, 1991, 185–190. doi:10.1109/IROS.1991.174447
Cianchetti, M., Laschi, C., Menciassi, A., and Dario, P. (2018). Biomedical Applications of Soft Robotics. Nat. Rev. Mater. 3 (6), 143–153. doi:10.1038/s41578-018-0022-y
Cianchetti, M., Ranzani, T., Gerboni, G., Nanayakkara, T., Althoefer, K., Dasgupta, P., et al. (2014). Soft Robotics Technologies to Address Shortcomings in Today's Minimally Invasive Surgery: The STIFF-FLOP Approach. Soft Robotics 1 (2), 122–131. doi:10.1089/soro.2014.0001
Crisfield, M. A., and Jelenić, G. (1999). Objectivity of Strain Measures in the Geometrically Exact Three-Dimensional Beam Theory and its Finite-Element Implementation. Proc. R. Soc. Lond. A. 455 (1983), 1125–1147. doi:10.1098/rspa.1999.0352
Della Santina, C., Katzschmann, R. K., Biechi, A., and Rus, D. (2018). “Dynamic Control of Soft Robots Interacting with the Environment,” in 2018 IEEE International Conference on Soft Robotics (RoboSoft), Livorno, Italy, April 24–28, 2018 (IEEE), 46–53. doi:10.1109/ROBOSOFT.2018.8404895
Denavit, J., and Hartenberg, R. S. (1955). A Kinematic Notation for Lower-Pair Mechanisms Based on Matrices. J. Appl. Mech. 22 (2), 215–221. doi:10.1115/1.4011045
Ding, J., Goldman, R. E., Xu, K., Allen, P. K., Fowler, D. L., and Simaan, N. (2013). Design and Coordination Kinematics of an Insertable Robotic Effectors Platform for Single-Port Access Surgery. Ieee/asme Trans. Mechatron. 18 (5), 1612–1624. doi:10.1109/TMECH.2012.2209671
Dupont, P. E., Lock, J., Itkowitz, B., and Butler, E. (2010). Design and Control of Concentric-Tube Robots. IEEE Trans. Robot. 26 (2), 209–225. doi:10.1109/TRO.2009.2035740
Duriez, C., and Bieze, T. (2017). “Soft Robot Modeling, Simulation and Control in Real-Time,” in Soft Robotics: Trends, Applications and Challenges (Springer), 103–109. doi:10.1007/978-3-319-46460-2_13
Fraś, J., Jan, C., Maciaś, M., and Główka, J. (2014). “Static Modeling of Multisection Soft Continuum Manipulator for Stiff-Flop Project,” in In Recent Advances in Automation, Robotics and Measuring Techniques. Editors R. Szewczyk, C. Zieliński, and M. Kaliczyńska (Cham: Springer International Publishing), 365–375.
Fritzson, P., Aronsson, P., Pop, A., Lundvall, H., Nystrom, K., Saldamli, L., Broman, D., and Sandholm, A. (2006). “OpenModelica - A Free Open-Source Environment for System Modeling, Simulation, and Teaching,” in 2006 IEEE Conference on Computer Aided Control System Design, 2006 IEEE International Conference on Control Applications, Munich, Germany, October 4–6, 2006, 1588–1595. doi:10.1109/CACSD-CCA-ISIC.2006.4776878
Ganji, Y., and Janabi-Sharifi, F. (2009). Catheter Kinematics for Intracardiac Navigation. IEEE Trans. Biomed. Eng. 56 (3), 621–632. doi:10.1109/TBME.2009.2013134
George Thuruthel, T., Falotico, E., Manti, M., Pratesi, A., Cianchetti, M., and Laschi, C. (2017). Learning Closed Loop Kinematic Controllers for Continuum Manipulators in Unstructured Environments. Soft Robotics 4 (3), 285–296. doi:10.1089/soro.2016.0051
Gilbert, H. B., and Godage, I. S. (2019). “Validation of an Extensible Rod Model for Soft Continuum Manipulators,” in 2019 2nd IEEE International Conference on Soft Robotics (RoboSoft), Seoul, South Korea, April 14–18, 2019 (IEEE), 711–716. doi:10.1109/ROBOSOFT.2019.8722721
Gilbert, H. B., Hendrick, R. J., and Webster, R. J. (2016). Elastic Stability of Concentric Tube Robots: A Stability Measure and Design Test. IEEE Trans. Robot. 32 (1), 20–35. doi:10.1109/TRO.2015.2500422
Gillespie, M. T., Best, C. M., and Killpack, M. D. (2016). “Simultaneous Position and Stiffness Control for an Inflatable Soft Robot,” in 2016 IEEE International Conference on Robotics and Automation (ICRA), Stockholm, Sweden, May 16–21, 2016 (IEEE), 1095–1101. doi:10.1109/ICRA.2016.7487240
Godage, I. S., Medrano-Cerda, G. A., Branson, D. T., Guglielmino, E., and Caldwell, D. G. (2015). Modal Kinematics for Multisection Continuum Arms. Bioinspir. Biomim. 10 (3), 035002. doi:10.1088/1748-3190/10/3/035002
Goury, O., Carrez, B., and Duriez, C. (2021). Real-Time Simulation for Control of Soft Robots with Self-Collisions Using Model Order Reduction for Contact Forces. IEEE Robot. Autom. Lett. 6 (2), 3752–3759. doi:10.1109/LRA.2021.3064247
Goury, O., and Duriez, C. (2018). Fast, Generic, and Reliable Control and Simulation of Soft Robots Using Model Order Reduction. IEEE Trans. Robot. 34 (6), 1565–1576. doi:10.1109/tro.2018.2861900
Grassmann, R., Modes, V., and Burgner-Kahrs, J. (2018). “Learning the Forward and Inverse Kinematics of a 6-DOF Concentric Tube Continuum Robot in SE(3),” in 2018 IEEE/RSJ International Conference on Intelligent Robots and Systems (IROS), Madrid, Spain, October 1–5, 2018 (IEEE), 5125–5132. doi:10.1109/IROS.2018.8594451
Greenwood, D. T. (1988). “Principles of Dynamics,” in Prentice-hall International Series in Dynamics. 2nd ed. (Upper Saddle River: Prentice-Hall).
Greer, J. D., Morimoto, T. K., Morimoto, A. M., and Okamura, E. W. (2019). A Soft, Steerable Continuum Robot that Grows via Tip Extension. Soft Robotics 6 (1), 95–108. doi:10.1089/soro.2018.0034
Greigarn, T., Jackson, R., Liu, T., and Cavusoglu, M. C. (2017). “Experimental Validation of the Pseudo-rigid-body Model of the MRI-Actuated Catheter,” in 2017 IEEE International Conference on Robotics and Automation (ICRA), 3600–3605. doi:10.1109/ICRA.2017.7989414
Greigarn, T., Poirot, N. L., Xu, X., and Cavusoglu, M. C. (2019). Jacobian-Based Task-Space Motion Planning for MRI-Actuated Continuum Robots. IEEE Robot. Autom. Lett. 4 (1), 145–152. doi:10.1109/LRA.2018.2881987
Hasanzadeh, S., and Janabi-Sharifi, F. (2014). An Efficient Static Analysis of Continuum Robots. J. Mech. Robotics 6 (3), 031011. doi:10.1115/1.4027305
He, L., Lou, J., Dong, Y., Kitipornchai, S., and Yang, J. (2018). Variational Modeling of Plane-Strain Hyperelastic Thin Beams with Thickness-Stretching Effect. Acta Mech. 229 (12), 4845–4861. doi:10.1007/s00707-018-2258-4
Jain, A., and Rodriguez, G. (1993). An Analysis of the Kinematics and Dynamics of Underactuated Manipulators. IEEE Trans. Robot. Automat. 9 (4), 411–422. doi:10.1109/70.246052
Jolaei, M., Hooshiar, A., Dargahi, J., and Packirisamy, M. (2021). Toward Task Autonomy in Robotic Cardiac Ablation: Learning-Based Kinematic Control of Soft Tendon-Driven Catheters. Soft Robotics 8, 340–351. doi:10.1089/soro.2020.0006
Jung, J., Penning, R. S., and Zinn, M. R. (2014). A Modeling Approach for Robotic Catheters: Effects of Nonlinear Internal Device Friction. Adv. Robotics 28 (8), 557–572. doi:10.1080/01691864.2013.879371
Kane, T. R., and Levinson, D. A. (1983). The Use of Kane's Dynamical Equations in Robotics. Int. J. Robotics Res. 2 (3), 3–21. doi:10.1177/027836498300200301
Katzschmann, R. K., Santina, C. D., Toshimitsu, Y., Bicchi, A., and Rus, D. (2019a). “Dynamic Motion Control of Multi-Segment Soft Robots Using Piecewise Constant Curvature Matched with an Augmented Rigid Body Model,” in 2019 2nd IEEE International Conference on Soft Robotics (RoboSoft), Seoul, South Korea, April 14–18, 2019 (IEEE), 454–461. doi:10.1109/ROBOSOFT.2019.8722799
Katzschmann, R. K., Thieffry, M., Goury, O., Kruszewski, A., Guerra, T.-M., Duriez, C., and Rus, D. (2019b). “Dynamically Closed-Loop Controlled Soft Robotic Arm Using a Reduced Order Finite Element Model with State Observer,” in 2019 2nd IEEE International Conference on Soft Robotics (RoboSoft), Seoul, South Korea, April 14–18, 2019 (IEEE), 717–724. doi:10.1109/ROBOSOFT.2019.8722804
Kim, S., Laschi, C., and Trimmer, B. (2013). Soft Robotics: A Bioinspired Evolution in Robotics. Trends Biotechnol. 31 (5), 287–294. doi:10.1016/j.tibtech.2013.03.002
Lai, J., Huang, K., and Chu, H. K. (2019). “A Learning-Based Inverse Kinematics Solver for a Multi-Segment Continuum Robot in Robot-independent Mapping,” in 2019 IEEE International Conference on Robotics and Biomimetics (ROBIO), Dali, China, December 6–8, 2019 (IEEE), 576–582. doi:10.1109/ROBIO49542.2019.8961669
Li, J., Zhou, Y., Wang, C., Wang, Z., and Liu, H. (2020). A Model-Based Method for Predicting the Shapes of Planar Single-Segment Continuum Manipulators with Consideration of Friction and External Force. J. Mech. Robotics 12 (4), 041013. doi:10.1115/1.4046035
Linn, J., Lang, H., and Tuganov, A. (2013). Geometrically Exact Cosserat Rods with Kelvin-Voigt Type Viscous Damping. Mech. Sci. 4 (1), 79–96. doi:10.5194/ms-4-79-2013
Lock, J., and Dupont, P. E. (2011). “Friction Modeling in Concentric Tube Robots,” in 2011 IEEE International Conference on Robotics and Automation, Shanghai, China, May 9–13, 2011 (IEEE), 1139–1146. doi:10.1109/ICRA.2011.5980347
Lutter, M., Ritter, C., and Peters, Jan. (2018). “Deep Lagrangian Networks: Using Physics as Model Prior for Deep Learning,” in International Conference on Learning Representations, New Orleans, LA, May 6–9, 2019.
Mahoney, A. W., Gilbert, H. B., and Webster, R. J. (2018). “A Review of Concentric Tube Robots: Modeling, Control, Design, Planning, and Sensing,” in The Encyclopedia of Medical Robotics (World Scientific), 181–202. doi:10.1142/9789813232266_0007
Majidi, C. (2014). Soft Robotics: A Perspective—Current Trends and Prospects for the Future. Soft Robotics 1 (1), 5–11. doi:10.1089/soro.2013.0001
Mauzé, B., Dahmouche, R., Laurent, G. J., André, A. N., Rougeot, P., Sandoz, P., et al. (2020). Nanometer Precision with a Planar Parallel Continuum Robot. IEEE Robot. Autom. Lett. 5 (3), 3806–3813. doi:10.1109/LRA.2020.2982360
Miller, S., and Wendlandt, J. (2011). Real-time Simulation of Physical Systems Using Simscape. Available at: https://www.mathworks.com/company/newsletters/articles/real-time-simulation-of-physical-systems-using-simscape.html (Accessed September 24, 2021).
Murray, R. M., Li, Z., and Sastry, S. S. (2017). A Mathematical Introduction to Robotic Manipulation. Boca Raton: CRC Press. doi:10.1201/9781315136370
Mustaza, S. M., Elsayed, Y., Lekakou, C., Saaj, C., and Fras, J. (2019). Dynamic Modeling of Fiber-Reinforced Soft Manipulator: A Visco-Hyperelastic Material-Based Continuum Mechanics Approach. Soft Robotics 6 (3), 305–317. doi:10.1089/soro.2018.0032
Nicolai, A., Olson, G., Menguc, Y., and Hollinger, G. A. (2020). “Learning to Control Reconfigurable Staged Soft Arms,” in 2020 IEEE International Conference on Robotics and Automation (ICRA), Paris, France, May 31–August 31, 2020 (IEEE), 5618–5624. doi:10.1109/ICRA40945.2020.9197516
Orekhov, A. L., and Simaan, N. (2020). “Solving Cosserat Rod Models via Collocation and the Magnus Expansion,” in 2020 IEEE/RSJ International Conference on Intelligent Robots and Systems (IROS), Las Vegas, NV, October 24–January 24, 2021 (IEEE), 8653–8660. doi:10.1109/IROS45743.2020.9340827
Parvaresh, A., and Moosavian, S. A. A. (2019). “Linear vs. Nonlinear Modeling of Continuum Robotic Arms Using Data-Driven Method,” in 2019 7th International Conference on Robotics and Mechatronics (ICRoM), Tehran, Iran, November 20–21, 2019 (IEEE), 457–462. doi:10.1109/ICRoM48714.2019.9071914
Penning, R. S., and Zinn, M. R. (2014). A Combined Modal-Joint Space Control Approach for Continuum Manipulators. Adv. Robotics 28 (16), 1091–1108. doi:10.1080/01691864.2014.913503
Platus, D. L. (1999). “Negative-Stiffness-Mechanism Vibration Isolation Systems,” in Proc. SPIE 3786, Optomechanical Engineering and Vibration Control (Denver: SPIE). doi:10.1117/12.363841
Rao, P., Peyron, Q., Lilge, S., and Burgner-Kahrs, J. (2021). How to Model Tendon-Driven Continuum Robots and Benchmark Modelling Performance. Front. Robot. AI 7 (February), 630245. doi:10.3389/frobt.2020.630245
Renda, F., Cacucciolo, V., Dias, J., and Seneviratne, L. (2016). “Discrete Cosserat Approach for Soft Robot Dynamics: A New Piece-Wise Constant Strain Model with Torsion and Shears,” in 2016 IEEE/RSJ International Conference on Intelligent Robots and Systems (IROS), Daejeon, South Korea, October 9–14, 2016 (IEEE), 5495–5502. doi:10.1109/IROS.2016.7759808
Renda, F., Giorelli, M., Calisti, M., Cianchetti, M., and Laschi, C. (2014). Dynamic Model of a Multibending Soft Robot Arm Driven by Cables. IEEE Trans. Robot. 30 (5), 1109–1122. doi:10.1109/TRO.2014.2325992
Roark, R. J., Young, W. C., and Budynas, R. G. (2002). Roark’s Formulas for Stress and Strain. 7th ed. McGraw-Hill.
Robinson, G., and Davies, J. B. C. (1999). “Continuum Robots-A State of the Art.,” in Proceedings 1999 IEEE International Conference on Robotics and Automation (Cat. No. 99CH36288C), 4, Detroit, MI, May 10–15, 1999 (IEEE), 2849–2854.
Rodrigues, O. (1840). “Des Lois Géométriques Qui Régissent Les Déplacements d’un Système Solide Dans l’espace, et de La Variation Des Coordonnées Provenant de Ces Déplacements Considérés Indépendamment Des Causes Qui Peuvent Les Produire. J. de Mathématiques Pures Appliquées 5, 380–440.
Rone, W. S., and Ben-Tzvi, P. (2014). Continuum Robot Dynamics Utilizing the Principle of Virtual Power. IEEE Trans. Robot. 30 (1), 275–287. doi:10.1109/TRO.2013.2281564
Roy, R., Wang, L., and Simaan, N. (2017). Modeling and Estimation of Friction, Extension, and Coupling Effects in Multisegment Continuum Robots. Ieee/asme Trans. Mechatron. 22 (2), 909–920. doi:10.1109/TMECH.2016.2643640
Rucker, D. C., and Webster III, R. J. (2011). Statics and Dynamics of Continuum Robots with General Tendon Routing and External Loading. IEEE Trans. Robot. 27 (6), 1033–1044. doi:10.1109/TRO.2011.2160469
Rucker, D. C., Webster, R. J., Chirikjian, G. S., and Cowan, N. J. (2010). Equilibrium Conformations of Concentric-Tube Continuum Robots. Int. J. Robotics Res. 29 (10), 1263–1280. doi:10.1177/0278364910367543
Rucker, D. C., and Webster, R. J. (2011). “Computing Jacobians and Compliance Matrices for Externally Loaded Continuum Robots,” in 2011 IEEE International Conference on Robotics and Automation, Shanghai, China, May 9–13, 2011 (IEEE), 945–950. doi:10.1109/ICRA.2011.5980351
Runge, G., Wiese, M., Gunther, L., and Raatz, A. (2017). “A Framework for the Kinematic Modeling of Soft Material Robots Combining Finite Element Analysis and Piecewise Constant Curvature Kinematics,” in 2017 3rd International Conference on Control, Automation and Robotics (ICCAR) (Nagoya, Japan: IEEE), 7–14. doi:10.1109/ICCAR.2017.7942652
Sadati, S., Ali, S., Naghibi, S. E., Rucker, D. C., Renson, L., Bergeles, C., et al. (2019). “Reduced Order vs. Discretized Lumped System Models with Absolute and Relative States for Continuum Manipulators,” in Robotics: Science and Systems, 10. doi:10.15607/rss.2019.xv.076
Satheeshbabu, S., Uppalapati, N. K., Chowdhary, G., and Krishnan, G. (2019). “Open Loop Position Control of Soft Continuum Arm Using Deep Reinforcement Learning,” in 2019 International Conference on Robotics and Automation (ICRA) (Montreal, QC, Canada: IEEE), 5133–5139. doi:10.1109/ICRA.2019.8793653
Schaeffer, D. G., and Cain, J. W. (2016). “Ordinary Differential Equations: Basics and beyond,” in Texts in Applied Mathematics (Springer), Availabe at: http://libezp.lib.lsu.edu/login?url=https://search.ebscohost.com/login.aspx?direct=true&db=cat00252a&AN=lalu.4596309&site=eds-live&scope=site&profile=eds-main. doi:10.1007/978-1-4939-6389-8
Schlagenhauf, C., Bauer, D., Chang, K.-H., King, J. P., Moro, D., Coros, S., and Pollard, N. (2018). “Control of Tendon-Driven Soft Foam Robot Hands,” in 2018 IEEE-RAS 18th International Conference on Humanoid Robots (Humanoids), Beijing, China, November 6–9, 2018 (IEEE), 1–7. doi:10.1109/HUMANOIDS.2018.8624937
Sedal, A., Wineman, A., Gillespie, R. B., and Remy, C. D. (2021). Comparison and Experimental Validation of Predictive Models for Soft, Fiber-Reinforced Actuators. Int. J. Robotics Res. 40 (1), 119–135. doi:10.1177/0278364919879493
Shiva, A., Sadati, S. M. H., Noh, Y., Fraś, J., Ataka, A., Würdemann, H., et al. (2019). Elasticity versus Hyperelasticity Considerations in Quasistatic Modeling of a Soft Finger-Like Robotic Appendage for Real-Time Position and Force Estimation. Soft Robotics 6 (2), 228–249. doi:10.1089/soro.2018.0060
Simo, J. C., and Vu-Quoc, L. (1986). A Three-Dimensional Finite-Strain Rod Model. Part II: Computational Aspects. Comput. Methods Appl. Mech. Eng. 58 (1), 79–116. doi:10.1016/0045-7825(86)90079-4
Spong, M. W., Hutchinson, S., and Vidyasagar, M. (2006). Robot Modeling and Control. Hoboken: John Wiley & Sons.
Spong, M. W., and Laurent, P. (1997). “Control of Underactuated Mechanical Systems Using Switching and Saturation,” in Control Using Logic-Based Switching. Editor A. Stephen Morse (Berlin, Heidelberg: Springer Berlin Heidelberg), 162–172.
Spong, M. W. (1998). “Underactuated Mechanical Systems,” in Control Problems in Robotics and Automation (Springer), 135–150.
Su, H.-J. (2009). A Pseudorigid-Body 3R Model for Determining Large Deflection of Cantilever Beams Subject to Tip Loads. J. Mech. Robotics 1 (2), 021008. doi:10.1115/1.3046148
Sucan, I., and Kay, J. (2019). Urdf - ROS Wiki. Available at: http://wiki.ros.org/urdf (Accessed September 24, 2021).
Thuruthel, T. G., Falotico, E., Renda, F., Laschi, C., and Laschi, C. (2017). Learning Dynamic Models for Open Loop Predictive Control of Soft Robotic Manipulators. Bioinspir. Biomim. 12 (6), 066003. doi:10.1088/1748-3190/aa839f
Thuruthel, T. G., Falotico, E., Renda, F., and Laschi, C. (2019). Model-Based Reinforcement Learning for Closed-Loop Dynamic Control of Soft Robotic Manipulators. IEEE Trans. Robot. 35 (1), 124–134. doi:10.1109/TRO.2018.2878318
Till, J., Aloi, V., and Rucker, C. (2019). Real-Time Dynamics of Soft and Continuum Robots Based on Cosserat Rod Models. Int. J. Robotics Res. 38 (6), 723–746. doi:10.1177/0278364919842269
Till, J., Bryson, C. E., Chung, S., Orekhov, A., and Rucker, D. C. (2015). “Efficient Computation of Multiple Coupled Cosserat Rod Models for Real-Time Simulation and Control of Parallel Continuum Manipulators”, in 2015 IEEE International Conference on Robotics and Automation (ICRA), Seattle, WA, May 26–30, 2015 (IEEE), 5067–5074. doi:10.1109/ICRA.2015.7139904
Trivedi, D., Lotfi, A., and Rahn, C. D. (2008). Geometrically Exact Models for Soft Robotic Manipulators. IEEE Trans. Robot. 24 (4), 773–780. doi:10.1109/TRO.2008.924923
Truby, R. L., Santina, C. D., and Rus., D. (2020). Distributed Proprioception of 3D Configuration in Soft, Sensorized Robots via Deep Learning. IEEE Robot. Autom. Lett. 5 (2), 3299–3306. doi:10.1109/LRA.2020.2976320
Venkiteswaran, V. K., Sikorski, J., and Misra, S. (2019). Shape and Contact Force Estimation of Continuum Manipulators Using Pseudo Rigid Body Models. Mechanism Machine Theor. 139 (9), 34–45. doi:10.1016/j.mechmachtheory.2019.04.008
Walker, I. D., Choset, H., and Chirikjian, G. S. (2016). “Snake-Like and Continuum Robots”, in Springer Handbook of Robotics. Editors B. Siciliano, and O. Khatib (Cham: Springer International Publishing), 481–498. doi:10.1007/978-3-319-32552-1_20
Wang, L., Zheng, D., Harker, P., Patel, A. B., Guo, C. F., and Zhao, X. (2021). Evolutionary Design of Magnetic Soft Continuum Robots. Proc. Natl. Acad. Sci. USA 118 (21), e2021922118. doi:10.1073/pnas.2021922118
Webster, R. J., and Jones., B. A. (2010). Design and Kinematic Modeling of Constant Curvature Continuum Robots: A Review. Int. J. Robotics Res. 29 (13), 1661–1683. doi:10.1177/0278364910368147
Webster, R. J., and Rucker., D. C. (2009). Parsimonious Evaluation of Concentric-Tube Continuum Robot Equilibrium Conformation. IEEE Trans. Biomed. Eng. 56 (9), 2308–2311. doi:10.1109/TBME.2009.2025135
Wehrmeyer, J. A., Barthel, J. A., Roth, J. P., and Saifuddin, T. (1998). Colonoscope Flexural Rigidity Measurement. Med. Biol. Eng. Comput. 36 (4), 475–479. doi:10.1007/bf02523217
Wu, D., Zhang, Y., Ourak, M., Niu, K., Dankelman, J., and Poorten, E. V. (2021). Hysteresis Modeling of Robotic Catheters Based on Long Short-Term Memory Network for Improved Environment Reconstruction. IEEE Robot. Autom. Lett. 6 (2), 2106–2113. doi:10.1109/LRA.2021.3061069
Xu, K., and Simaan, N. (2008). An Investigation of the Intrinsic Force Sensing Capabilities of Continuum Robots. IEEE Trans. Robot. 24 (3), 576–587. doi:10.1109/TRO.2008.924266
Xu, W., Jie Chen, Jie., Lau, H. Y. K., and Ren., H. (2016). “Automate Surgical Tasks for a Flexible Serpentine Manipulator via Learning Actuation Space Trajectory from Demonstration,” in 2016 IEEE International Conference on Robotics and Automation (ICRA), Stockholm, Sweden, May 16–21, 2016 (IEEE), 4406–4413. doi:10.1109/ICRA.2016.7487640
Yip, M. C., and Camarillo, D. B. (2014). Model-Less Feedback Control of Continuum Manipulators in Constrained Environments. IEEE Trans. Robot. 30 (4), 880–889. doi:10.1109/TRO.2014.2309194
Yip, M. C., and Camarillo, D. B. (2016). Model-Less Hybrid Position/Force Control: A Minimalist Approach for Continuum Manipulators in Unknown, Constrained Environments. IEEE Robot. Autom. Lett. 1 (2), 844–851. doi:10.1109/LRA.2016.2526062
Zhang, C., He, B., Ding, A., Xu, S., Wang, Z., and Zhou, Y. (2019). Motion Simulation of Ionic Liquid Gel Soft Actuators Based on CPG Control. Comput. Intelligence Neurosci. 2019 (2), 1–11. doi:10.1155/2019/8256723
Zhang, J., and Simaan, N. (2013). Design of Underactuated Steerable Electrode Arrays for Optimal Insertions. J. Mech. Robotics 5 (1). doi:10.1115/1.4007005
Keywords: continuum robots, soft robots, dynamics, statics, mechanics, medical robotics
Citation: Gilbert HB (2021) On the Mathematical Modeling of Slender Biomedical Continuum Robots. Front. Robot. AI 8:732643. doi: 10.3389/frobt.2021.732643
Received: 29 June 2021; Accepted: 20 September 2021;
Published: 05 October 2021.
Edited by:
Elena De Momi, Politecnico di Milano, ItalyCopyright © 2021 Gilbert. This is an open-access article distributed under the terms of the Creative Commons Attribution License (CC BY). The use, distribution or reproduction in other forums is permitted, provided the original author(s) and the copyright owner(s) are credited and that the original publication in this journal is cited, in accordance with accepted academic practice. No use, distribution or reproduction is permitted which does not comply with these terms.
*Correspondence: Hunter B. Gilbert, aGJnaWxiZXJ0QGxzdS5lZHU=