- 1Department of Physics, University of Oslo, Oslo, Norway
- 2Department of Biomechanical Engineering, University of Twente, Enschede, Netherlands
- 3The Intervention Centre, Oslo University Hospital, Oslo, Norway
- 4Department of Informatics, University of Oslo, Oslo, Norway
- 5Department of Technology Systems, University of Oslo, Oslo, Norway
- 6Department of Biomedical Engineering, University of Groningen and University Medical Centre Groningen, Groningen, Netherlands
- 7Department of Clinical and Biomedical Engineering, Oslo University Hospital, Oslo, Norway
This paper introduces and validates a real-time dynamic predictive model based on a neural network approach for soft continuum manipulators. The presented model provides a real-time prediction framework using neural-network-based strategies and continuum mechanics principles. A time-space integration scheme is employed to discretize the continuous dynamics and decouple the dynamic equations for translation and rotation for each node of a soft continuum manipulator. Then the resulting architecture is used to develop distributed prediction algorithms using recurrent neural networks. The proposed RNN-based parallel predictive scheme does not rely on computationally intensive algorithms; therefore, it is useful in real-time applications. Furthermore, simulations are shown to illustrate the approach performance on soft continuum elastica, and the approach is also validated through an experiment on a magnetically-actuated soft continuum manipulator. The results demonstrate that the presented model can outperform classical modeling approaches such as the Cosserat rod model while also shows possibilities for being used in practice.
Introduction
Soft continuum manipulators are flexible and highly deformable robots composed of soft and mostly elastic materials, and can serve as possible substitutes for rigid robots. Advantages of soft manipulator robots such as their compliance, dexterity, and adaptability to complex workspaces are driving the emergent research in this field. By contrast, rigidity of traditional rigid robots limits their use in constrained and confined environments, and reduces the possibilities for safe interaction with humans. Soft continuum manipulators have found applications in many areas, such as dexterous grasping (McMahan et al., 2006; Katzschmann et al., 2015) and assistive devices (Ansari et al., 2017), and particularly in the field of minimally invasive surgeries, such as laryngeal surgery (Simaan et al., 2004), catheter-based endovascular intervention (Grady et al., 2000; Burgner et al., 2013), and cardiovascular surgery (Kesner and Howe, 2011).
Analytical modeling of soft manipulators helps evaluate their motion and determine their workspace, in order to be used for control, motion planning, and animation purposes. Soft manipulators distinguish themselves by having an infinite number of degrees of freedom in any workspace they occupy. This characterization makes modeling complicated for soft manipulators. Several approaches have been investigated thus far in the literature. Most of the approaches consider the kinematic (i.e. static or quasi-static) modeling of the manipulators such as static analysis using virtual-work model (Xu and Simaan, 2010), Cosserat rod theory (Pai, 2002; Jones et al., 2009; Mahvash and Dupont, 2011), and α Lie group formulation (Grazioso et al., 2019). These models do not describe full dynamics of the manipulators, and they may show performance degradation when it comes to high-frequency applications or large and complex deformations. On the other hand, dynamical modeling approaches [e.g. Wen et al. (2012), Jung et al. (2014), Hyatt et al. (2019), Sadati et al. (2019), Till et al. (2019), Tariverdi et al. (2020)], contain dynamics of the manipulators and also take into account time-varying responses of manipulators, including high-frequency modes. However, the dynamic models mostly rely on traditional methods, such as finite elements and finite differences (i.e., quantitative and numerical methods), making the algorithms computationally expensive for real-time applications. In other words, to obtain sufficiently accurate solutions, methods need to deal with fine meshes, which increase memory use and computation time. Another limitation is that their solutions are discrete or not sufficiently differentiable. It is worth noting that in model-based controllers or observers, having a differentiable solution (i.e., a solution that can be evaluated continuously on the workspace) is crucial in the design process. Furthermore, when softer materials are employed for manipulator construction with more complex geometries or large deformations, modeling their behavior analytically becomes challenging. Therefore, there is a need for appropriate data-driven approaches without compromising computational bandwidths and the prediction quality.
Dynamics of soft continuum manipulators have highly nonlinear behavior and are expressed as Partial Differential Equations (PDEs). An effective approach to represent and model PDEs solutions is to use Neural Networks (NN). NN-based solutions of PDEs are infinitely differentiable by eliminating the need for interpolation. Furthermore, compared to finite elements or difference methods, solutions are represented by fewer parameters, which reduces the memory use. There are studies that use machine learning algorithms to find a solution for special types of PDEs such as (Lagaris et al., 1998; Lee and Kang, 1990; Weinan et al., 2017; Raissi et al., 2019). However, to the authors’ best knowledge, there is no study that investigates possible NN-based solutions for partial differential equations that describe the full dynamics of continuum manipulators. In this work, inspired by a time-space integration scheme and by using the Lie group variational integration method (Demoures et al., 2015), the dynamic equations for translation and rotation for each node of a soft continuum manipulator are decoupled, providing an appropriate structure aimed at developing a real-time modeling algorithm. Afterward, Recurrent Neural Networks (RNNs)-based models are employed to approximate the high-dimensional discretized equations. Additionally, external torques and forces (e.g., control inputs, friction, and gravity) are incorporated into the model in a real-time manner for control applications.
The ability of RNNs to learn and approximate large classes of nonlinear functions over sequences of inputs accurately makes them prime candidates for use in dynamic modeling of complex nonlinear systems. RNNs with Long Short-Term Memory (LSTM) layers process sequences by iterating through the sequence elements. Using an internal feedback, the network is capable of preserving long-term dependencies. Essentially, LSTM layers prevent older information from gradually vanishing. These networks also have been used for several applications in soft robotics. To name a few, Thuruthel in Thuruthel et al. (2019) proposes a model-free, real-time sensing method for soft robots perception. The authors in Thuruthel et al. (2017) uses RNNs to model and control soft robotic manipulators. Also, force and motion estimation using RNNs has been investigated in Marban et al. (2019) and Turan et al. (2018), respectively.
This paper aims to develop a real-time dynamic model for analyzing the dynamics of soft manipulators. Investigation of previous work on the modeling of the continuum manipulators suggests that existing literature focuses primarily on static or quasi-static approaches, or does not provide a real-time model. The contribution of this article is to present a scalable, parallel and real-time modeling algorithm for soft manipulators dynamics. The contributions of this paper are as follows.
• Existing approaches primarily deal with kinematic modeling methods. Nevertheless, in this study, real-time prediction of soft manipulators full spatial dynamics is considered in the proposed RNN-based algorithm by proposing multiple light-weight RNN-based models.
• In traditional modeling approaches, there are no systematic methods to obtain knowledge about dissipation forces, in particular friction, in the modeling procedure. The presented algorithm intrinsically takes the dissipation forces into account and incorporates their effects into the model.
• Through an experiment, results of the proposed RNN-based model and Cosserat rod theory method are compared, revealing the practical effectiveness of the proposed methodology.
The remainder of this paper is organized as follows: the problem statement is given in Section 2. Section 3 describes the proposed RNN-based algorithm in details. In Section 4 and Section 5, different simulations and experimental validation are presented to demonstrate the efficacy of the proposed RNN-based method, in terms of the model performances and accurately predicting poses of manipulators. Finally, the main conclusions are stated in Section 7.
2 Problem Statement
Consider a continuum manipulator with large deflections described by dynamic equations of motion [as presented in Tariverdi et al. (2020) and Demoures et al. (2015)] in the PDEs form as
where
Although high fidelity models given in the references can describe continuum manipulators dynamics efficiently, they suffer from limitations that are discussed in Section 1. Inspired by the structure and formulation of the dynamics based on the Lie group variational integration scheme, the aim is to propose distributed deep recurrent neural networks to capture and simulate soft manipulators dynamics in real-time to be able control them more accurately than existing models.
3 Proposed RNN-Based Model
This section is devoted to develop a model based on the time series prediction using RNNs. To solve PDEs numerically using NNs, one approach is to utilize discrete solutions of finite element or difference methods to train an NN. A Lie group variational time integration model is employed to discretize the continuous dynamics of a soft manipulator2. The whole manipulator is discretized into an arbitrary number of nodes where the position and orientation equations of each node are decoupled. In our study, we discretize the manipulator with equidistant nodes, but this can be changed depending on the application.
Figure 1 demonstrates a soft continuum manipulator at time t where
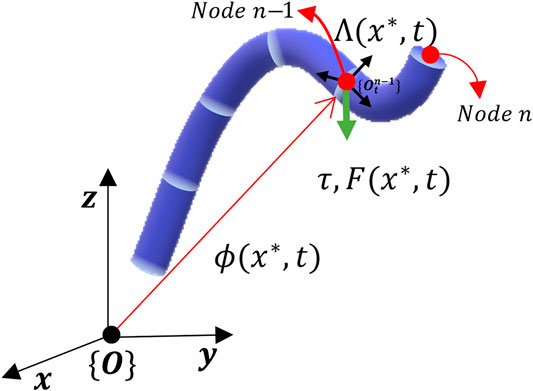
FIGURE 1. A soft manipulator at time t with discretization nodes n and
The discrete equations suggest an appropriate structure for the RNNs-based model. Given time-sequence inputs (as a first input layer), i.e., poses (positions and orientations) of nodes, and also forces and torques (as a second input layer) applied to each node, the RNN-based model of Node n is depicted in Figure 2A,B. For Node n, the first input layer is a time-sequence series of poses
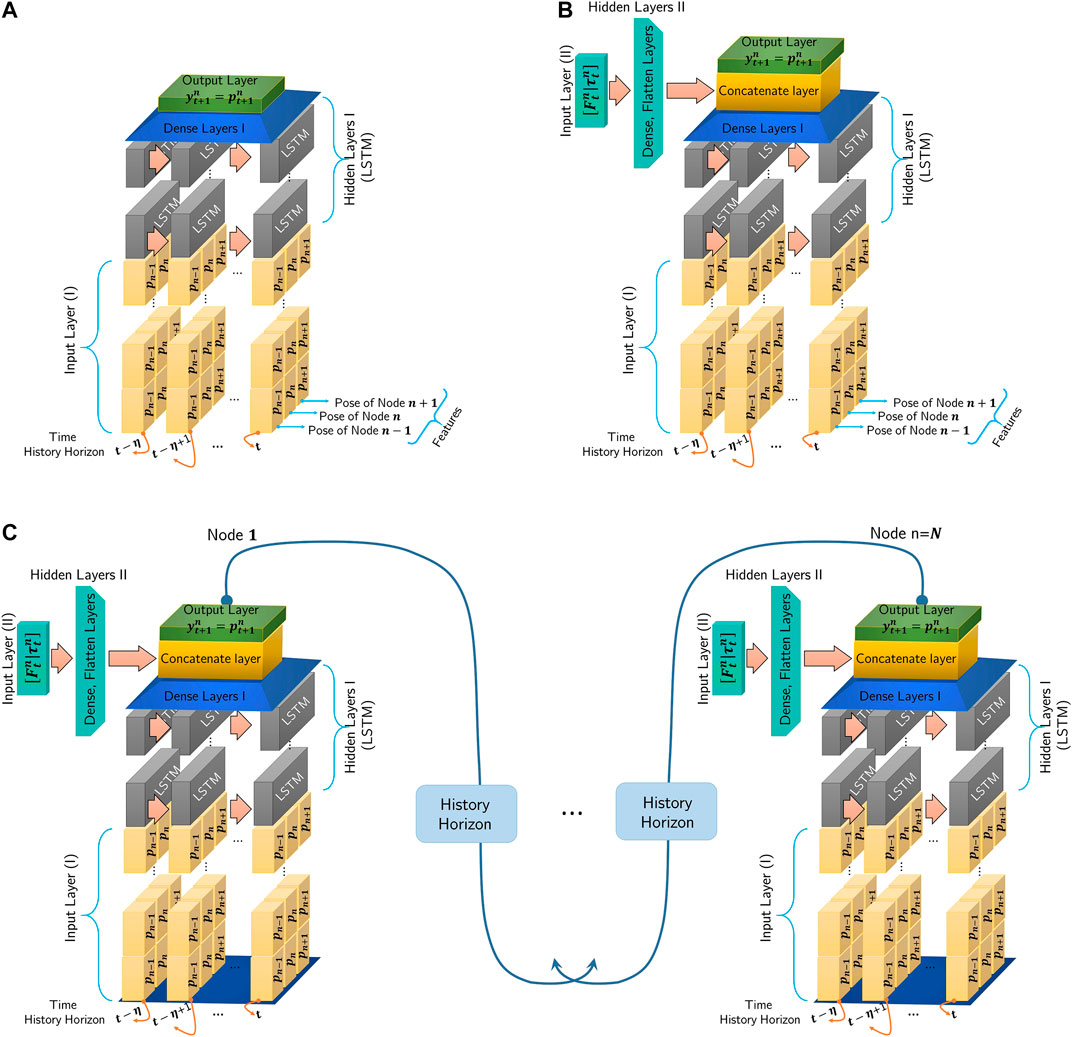
FIGURE 2. Recurrent Neural Network-based model, length of the time history horizon is determined by η and features composed of adjacent nodes pose: (A): Poses of Nodes
The network takes specific size vectors as inputs, which are called input layers. The inputs are transformed through a series of hidden layers (LSTM, dense, or fully connected layers) to produce an output. The output vectors are called an output layer. Dense or fully connected layers perform linear operations (i.e., multiplication and summation) on their inputs. Furthermore, LSTM layers consist of LSTM units, which can process sequences of data of any length, for example, poses of nodes. An LSTM unit controls contributions of each element of the input layer in the output and keeps track of the dependencies between the elements (Hochreiter and Schmidhuber, 1997).
For the training process, data-sets contain time-sequence inputs and forces and torques applied to each node. Also, for each node, the poses of the node and its neighbors are considered features, as shown in Figure 2A,B. The first and second input layers proceed through LSTM layers and dense layers as hidden layers, respectively. Finally, output layers have resulted from fully connected layers.
By augmenting the given models for all nodes (see Figure 2B) as a series, the proposed RNN-based models of the whole continuum manipulator with N nodes with non-conservative forces and torques are depicted in Figure 2C. Output of every node is updated at each time step by using a history (at least two previous time steps) of neighboring node outputs. Therefore, the proposed architecture suggests a suitable framework to construct a parallel modeling algorithm.
4 Simulations Results
In this section, we consider different examples and evaluate the performance of the proposed RNN-based model in Figure 2C. It is worth mentioning that data-sets play a crucial role in efficiency and accuracy in machine learning-based algorithms. The data acquisition process from a robot in real-world environments is both time and cost-consuming (implementation of multiple sensors, data filtering, and fusion, etc.). As an alternative approach, the required data can be acquired through simulations of high fidelity models. The obtained data can thus be transferred to train the algorithms to be implemented in real-world scenarios. In this section and for the presented examples, required data for the training of the proposed RNN-based model are acquired through simulations of the algorithm presented in Tariverdi et al. (2020), Sec. 2). For clarity, this model is henceforth referred to as the analytical dynamic model. In addition, since thin rods are considered in the examples, orientations of cross-sections are not of any concern. Also, it should be noted that orientations, except the twisting angle, can be reconstructed from manipulators’ configuration. Therefore, to obtain a computationally light model, the focus of attention is only on the prediction of positions.
4.1 First Simulation: An Ellipse Without External Wrenches
As a first case, a cylindrical rod is bent into a circle and its ends are attached to one another. The rod is then deformed into an elliptical shape and released. Due to potential energies in the ellipse, it starts to move without any external disturbances. The goal is to model the behavior of the ellipse resultant from its internal elastic energy.
The ellipse is formed in the
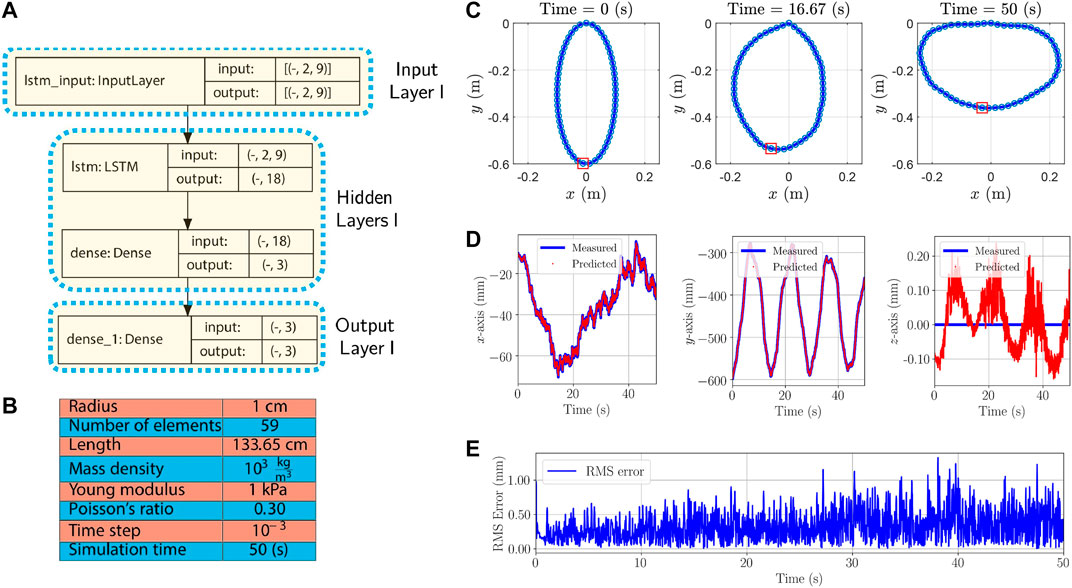
FIGURE 3. First simulation example: (A): The model architecture used for the first simulation example. The first stage is the Input layer, the intermediate stages are the Hidden layers, and the last stage is the Output layer. The first dimension of inputs and outputs in each layer are unspecified and can vary with the size of batches. (B): Rod properties and simulation parameters used in the first example. (C): Initial and time-evolved configurations. Positions of node specified by a red rectangle are measured and predicted. (D): Measured position calculated from analytical dynamic model and predicted by the proposed RNN-based model in the
50,001 position samples are generated from the analytical model for each node. We augment 1-by-3 position vectors of Node 30th and its adjacent nodes (Nodes 29th and 31st) at each time step. Therefore, the augmentation results in a 1-by-9 vector. Furthermore, the size of history horizons is chosen to be 2. In other words,
First, we evaluate the model by using unseen data samples in Data-set I and the results are shown in Figure 3D. The maximum and mean absolute error are
where predicted positions
To demonstrate that the model can be extended to different boundary and initial conditions, the cylindrical rod is employed to form a horizontal ellipse with the width 0.6 m and height 0.2 m. The rod properties and the simulation parameters given in Figure 3B are used. As boundary conditions, the first and last nodes are attached to the origin and their orientations are set to the identity. The manipulator with the new boundary and initial conditions is only used for the evaluation of the trained model by predicting positions of the node located at
Let us assume that the analytical dynamic model is implemented in a parallel scheme, i.e., each node of 59 nodes is handled with a CPU core or different hardware such that there is no latency in communications. Then, the dynamics of each node can be solved in
It is worth mentioning that the considered assumption is very strict, which cannot be satisfied in reality. First of all, conventional algorithms need a relatively high number of nodes to have numerical stability and an acceptable convergence rate. Furthermore, due to limitations in computation resources, more than one node will be assigned to each core of CPU, and there is always latency in communications between threads in parallel programmings. Therefore, reaching the mentioned bandwidth through the analytical dynamic model is infeasible. However, the real-time performance of the proposed RNN-based model can be applicable in closed-loop control applications.
4.2 Second Simulation: A Cylindrical Rod With External Wrenches
In the second example, we simulate a rod with a circular cross section, which is actuated by external forces such that its tip tracks a square in space. In this example, the goal is to model the behavior of the rod which results from applied external forces on its end-effector. For boundary conditions, the first node is fixed to the origin and its orientation is set to the identity for all time steps. The rod properties and simulation parameters, and the structure of the proposed model are given in Figure 4. The trajectory of the end-effector and the applied forces onto it are shown in Figure 5A.
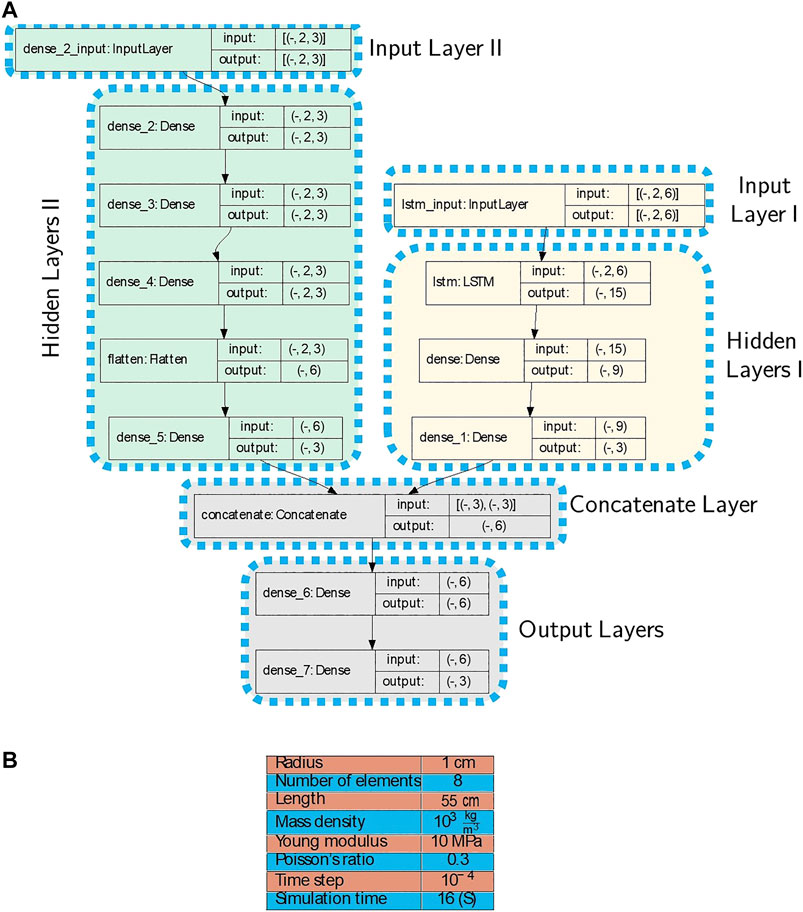
FIGURE 4. (A): The model architecture used for the second simulation example. There are two Input layers, the first one is the poses of the node and the second input is the applied forces on the node. The first dimension of inputs and outputs in each layer are unspecified and can vary with the size of batches. (B): Rod properties and simulation parameters used in the second example.
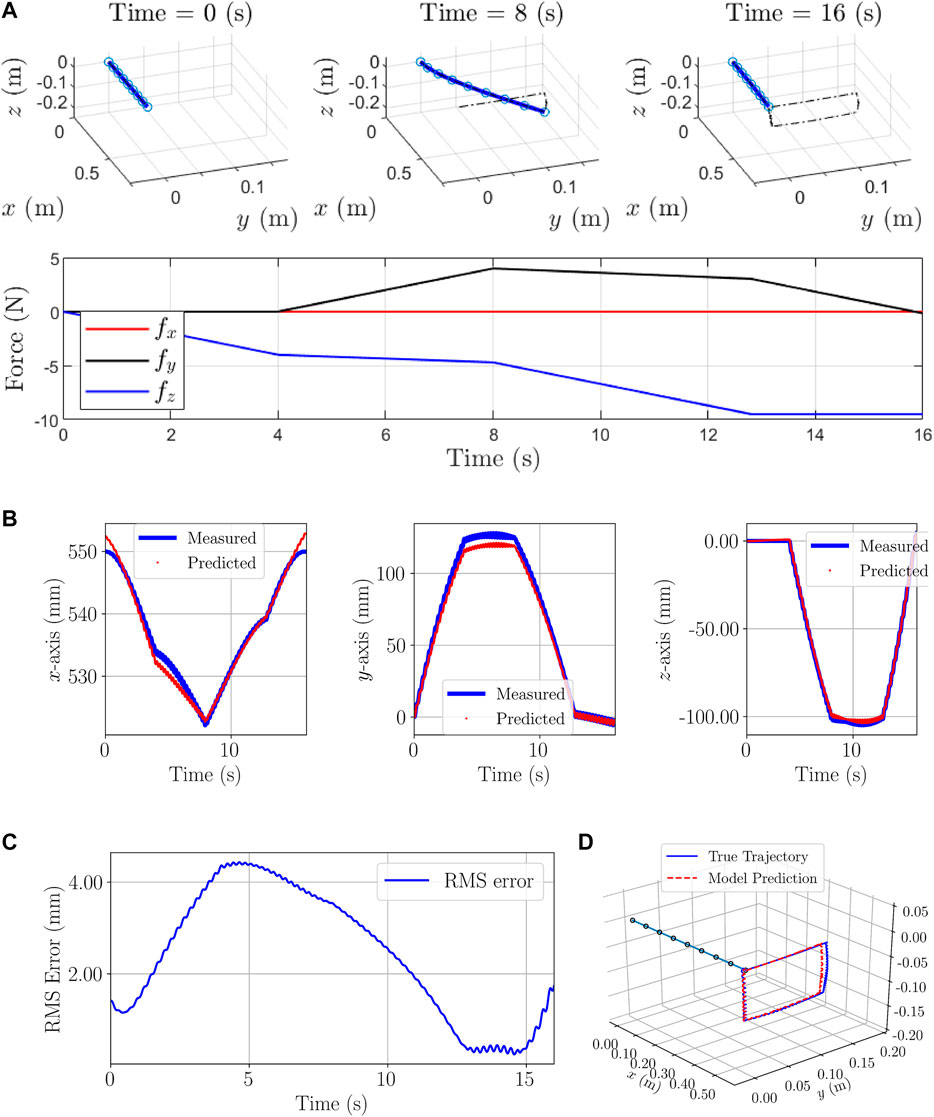
FIGURE 5. Second simulation example: (A): Initial, Time-evolved configurations and forces on the last node. (B): Tip positions: calculated from the analytical dynamic model and predicted by the proposed RNN-based model. (C) RMS error considering all the axes. (D) Predicted and measured trajectories.
160,001 position and force samples are generated from the analytical model for each node. We augment 1-by-3 position vectors of the last node (end-effector) and its adjacent node at each time step. Therefore, the augmentation results in a 1-by-6 vector. Furthermore, the size of history horizons is chosen to be 2 (
First, unseen data samples in Data-set II are employed to evaluate the model, and tip positions are calculated and the results are shown in Figure 5B. The maximum and mean absolute error are
To evaluate the generalizability of the trained model, different profiles of forces are applied to the model aiming at obtaining different position trajectories for the end-effector as depicted in Figure 6A,D. To fulfill the goal of the second example, the new forces are only used for the evaluation of the trained model by predicting the positions of the end-effector. Results of the prediction are plotted in Figure 6B and are as follows: The maximum and mean absolute errors are
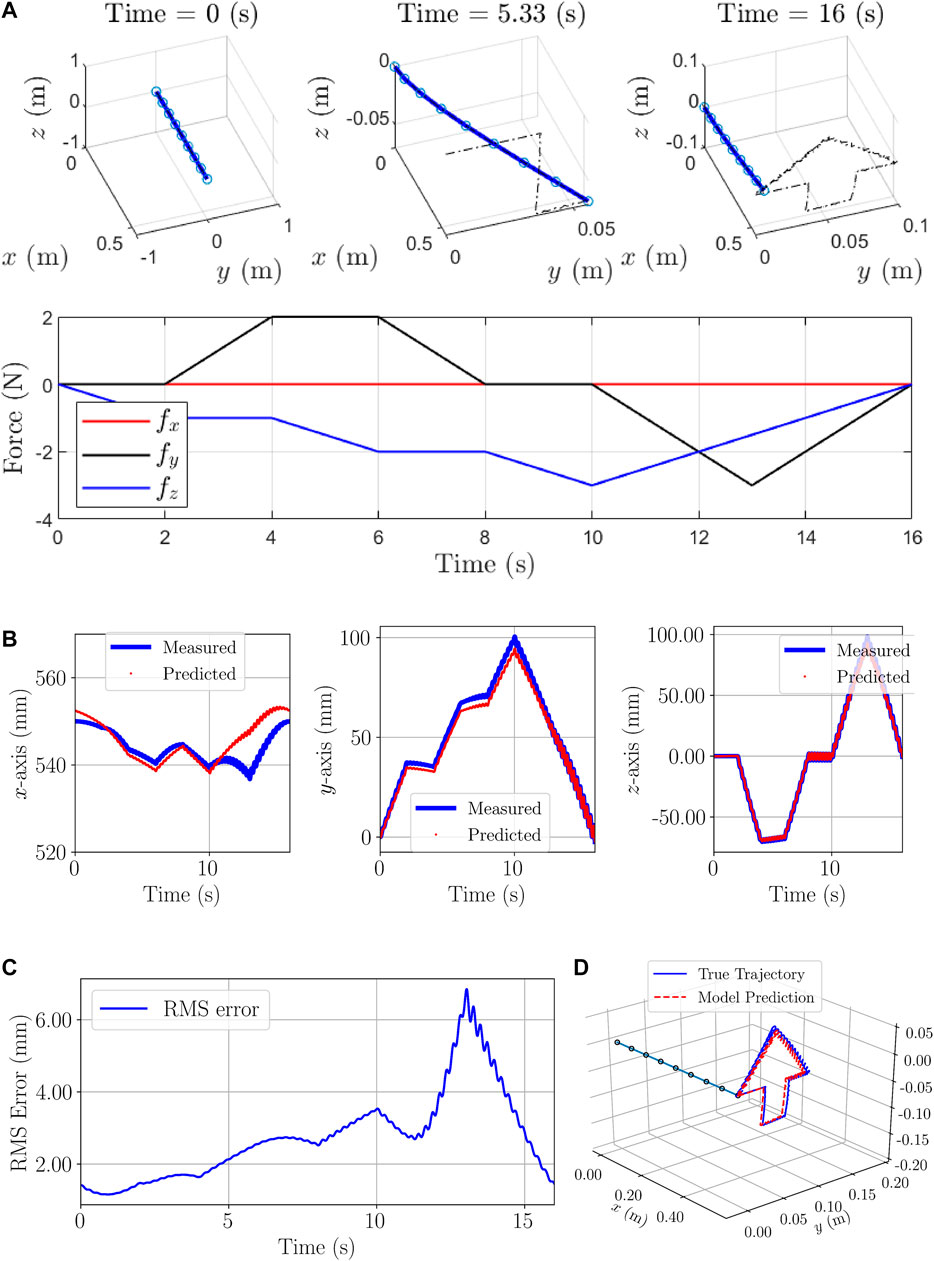
FIGURE 6. Evaluation Example of Second simulation: (A): Initial, Time-evolved configurations and forces on the end-effector (B): Tip positions: calculated from the analytical dynamic model and predicted by the proposed RNN-based model. (C) RMS error considering all the axes (D) Predicted and measured trajectories.
In this example, the maximum constant time step for this simulation is
4.3 Third Simulation: A Cylindrical Rod With and Without External Wrenches
In the last example, we form a semi-circular shape with a cylindrical rod. A force is applied to the middle node—Node 51th—in the -y-axis direction for 0.5 s and then the force is removed. Furthermore, the boundary conditions are as follows: the first and last nodes are fixed to the origin and their orientations are set to the identity and
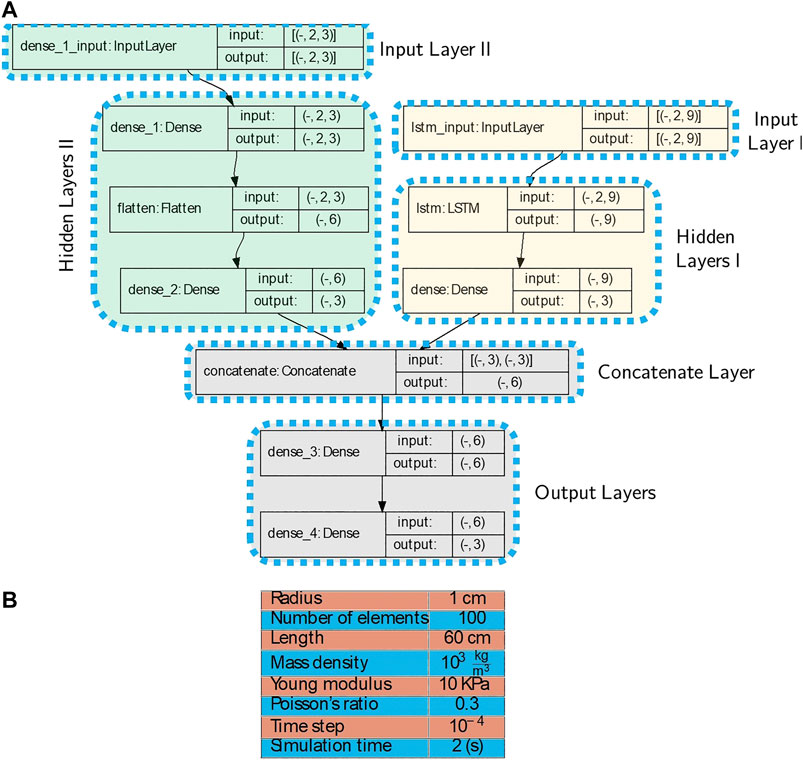
FIGURE 7. (A): The model architecture used for the third simulation example. There are two Input layers, the first one is the poses of the node and the second input is the applied forces on the node. The first dimension of inputs and outputs in each layer are unspecified, and can vary with the size of batches (B): Rod properties and simulation parameters used in the third example.
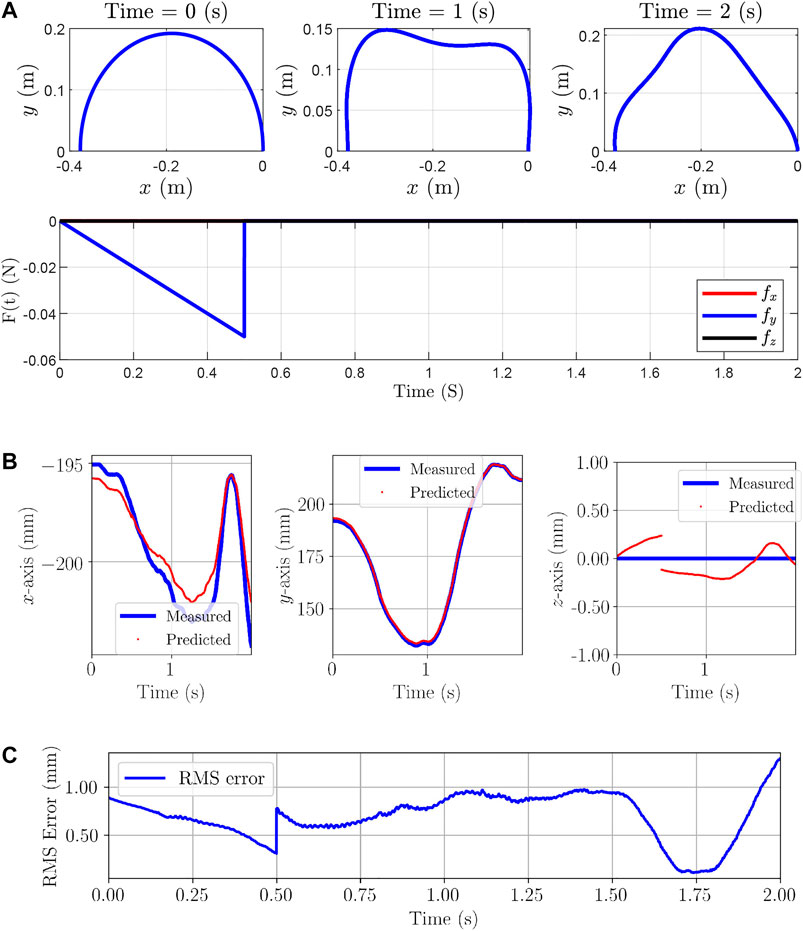
FIGURE 8. Third simulation example: (A): Initial, Time-evolved configurations and forces applied on the rod. Positions of the middle node, where the force is applied, are measured and predicted. (B): Measured position calculated from analytical dynamic model and predicted by the proposed RNN-based model in the
20,001 position and force samples are generated from the analytical model for each node. We augment 1-by-3 position vectors of Node 15th and its adjacent nodes at each time step. Therefore, the augmentation results in a 1-by-9 vector. Furthermore, the size of history horizons is chosen to be 2 (
The positions of Node 51th are predicted using seen and unseen data samples in Data-set III and the results are shown in Figure 8B,C. The maximum and mean absolute error are
For the evaluation of the trained model and to fulfill the goal of this example, force vector
In this example, the maximum constant time step for this simulation is
5 Experimental Results
This section is devoted to the experimental validation of the presented model. To that end, we fabricated a soft manipulator on which magnetic fields are used to produce necessary forces and torques. Compared to the simulations in which positions are predicted, time-sequence input is composed of orientations of nodes in the experiment. Furthermore, to show the performance of the algorithm, results from the presented method and a Cosserat rod-based theoretical model are compared to show the efficiency of the proposed RNN-based model. The Cosserat rod model of the soft manipulator is detailed in Appendix.
5.1 Soft Continuum Manipulator
A soft continuum manipulator is fabricated from a urethane rubber Polymer Matrix Composite 770 (PMC-770, Smooth-On Inc., Macungie, United States) and neodymium (NdFeB) block magnets whose dimensions are given in Figure 9A. When the manipulator is subjected to an external magnetic field, the embedded magnets experience forces and torques. This causes the flexible portions of the manipulator comprised of the PMC to undergo elastic deformation.
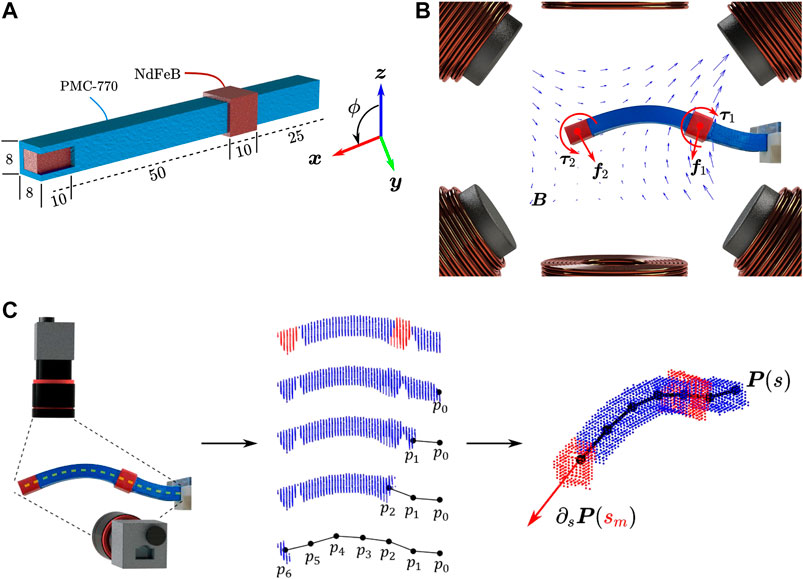
FIGURE 9. (A): Polymer matrix composite 770 (PMC-770) beam continuum manipulator with embedded neodymium (NdFeb) magnets located at tip and intermediate positions. Dimensions are given in millimeter. (B): Experimental setup consists of six stationary electromagnets and contains a segmented photograph of the final shape manipulator. The flexible PMC-770 and rigid NdFeb sections of the manipulator are blue and red, respectively. Six electromagnets generate a magnetic field (
The PMC-770 has a density
5.2 Experimental Setup
The experimental setup consists of 6 stationary electromagnets surrounding a spherical workspace of 100 mm diameter Sikorski et al. (2017). Figure 9B shows the setup of the experiment. In addition, the final shape of manipulator has been segmented and is shown in the workspace. The continuum manipulator is suspended horizontally (along
Figure 9C represents the shape reconstruction of the soft manipulator through images coming from two Dalsa Genie Nano C1940 Red-Green-Blue (RGB) cameras (TeledyneDalsa, Waterloo, ON, Canada). The flexible PMC-770 and rigid NdFeb magnets were colored blue and red, respectively. The RGB cameras (horizontal and vertical) that formed a stereo vision setup recorded the workspace during experiments. First, we discretize the actuation workspace into voxels. The silhouette of the continuum manipulator is segmented as binary masks and the manipulator body represented as a 3D spatial point cloud. The manipulator centerline is approximated by
where
The magnetic torques and forces were computed from the magnets position
The torques and forces exerted on the magnets due to the field is given by
where
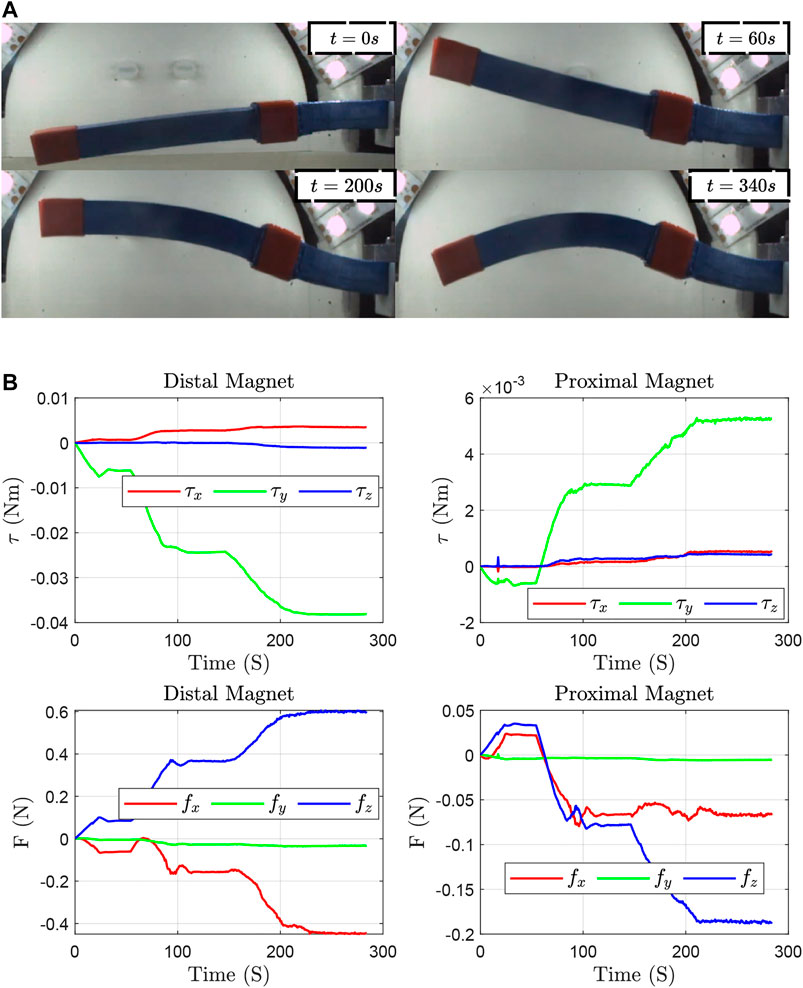
FIGURE 10. (A): Initial and time-evolved configurations. (B): Applied torques and forces on the distal and proximal magnets.
For modeling, we consider three nodes located at the locations of the proximal and distal magnets, and the clamped end of the rod. It should be pointed out that the performance of the proposed RNN-based model, unlike conventional algorithms, is independent of the number of nodes considered for the whole manipulator. Therefore, it is sufficient to model points of interest. The idea is to independently manipulate each magnet (actuation point). However, the setup provides us with 8 degrees of freedom, meaning that positions and orientations (12 degrees of freedom) cannot be manipulated at the same time. Therefore, we carried out the experiment to achieve only orientation control.
669 1-by-3 position samples and 1-by-6 augmented wrench samples (i.e.,
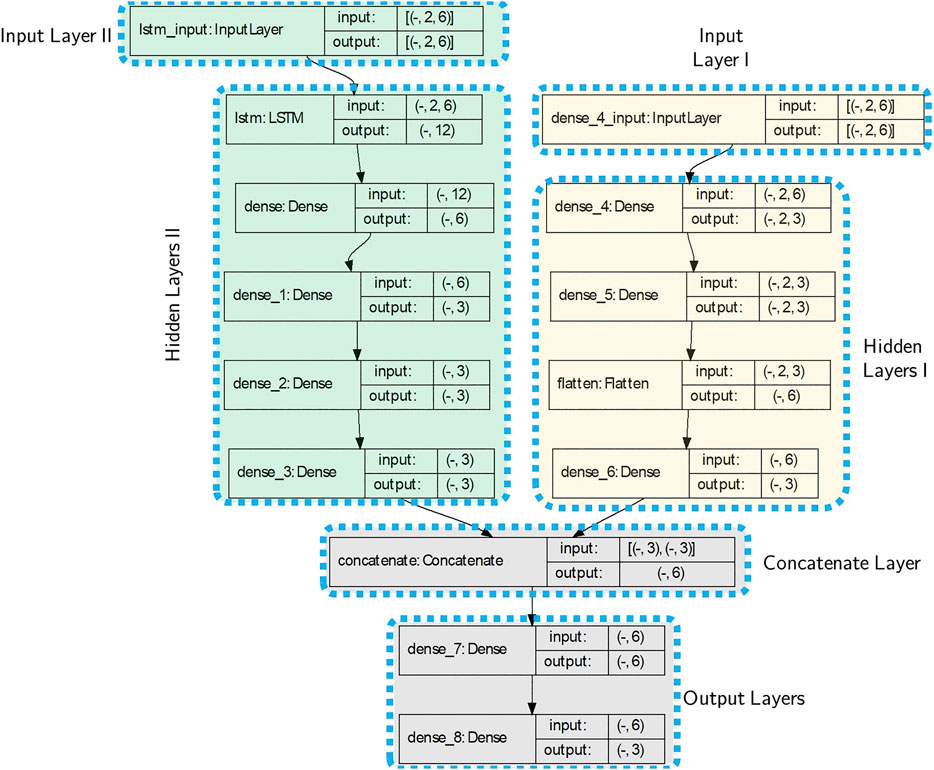
FIGURE 11. The model architecture used for the experiment. There are two Input layers, the first one is the poses of the node and the second input is the applied forces on the proximal node. The first dimension of inputs and outputs in each layer are unspecified, and can vary with the size of batches.
5.3 Results
The distal and proximal node rotations are predicted both by Cosserat rod model and the proposed model, and the results are shown in Figure 12. Also, the maximum and mean absolute errors are stated in an ordered pair in Table 1.
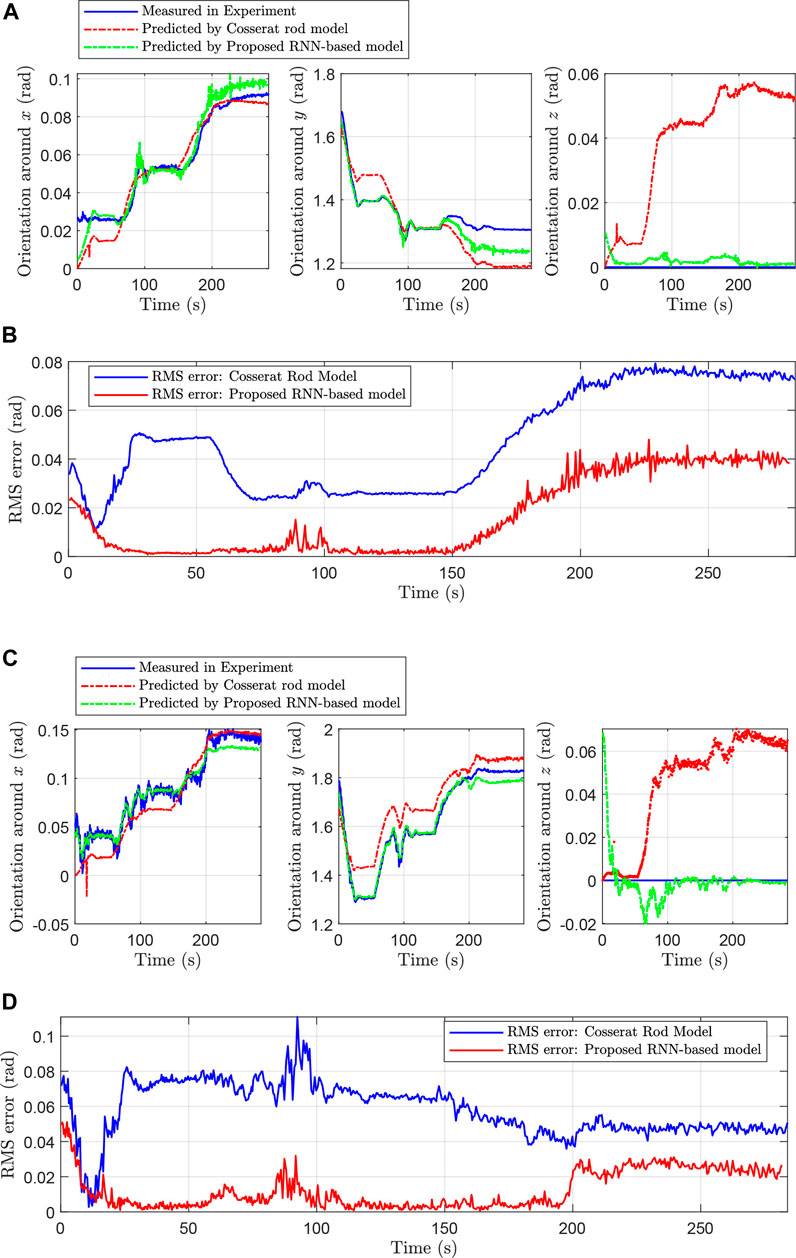
FIGURE 12. (A): Measured and predicted orientations of tip/distal magnet by Cosserat rod model and proposed RNN-based model. (B): RMS error for distal/tip magnet resulted from Cosserat rod model and proposed RNN-based model. (C): Measured and predicted orientations of middle/proximal magnet by Cosserat rod model and proposed RNN-based model. (D): RMS error for middle/proximal magnet resulted from Cosserat rod model and proposed RNN-based model.
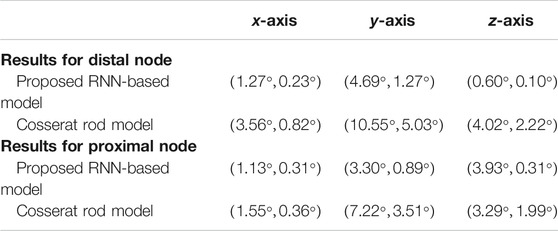
TABLE 1. The maximum and mean absolute errors around the
The computation time required to find a solution of the manipulator statics from a Boundary Value Problem (BVP) with Cosserat rod theory depends on the quality of the initial solution guess, i.e.,
A tolerable error describes the error between the distal internal forces and moments obtained from forward integration which are called
Decreasing the tolerable error increases the solution accuracy, but potentially requires more time to solve convex optimizations for the BVP. Increasing the number of nodes is necessary to describe complex manipulator geometries, but should be chosen to minimize the required steps during forward integration.
To visualize how the required computation time changes with the number of nodes and the tolerable error, multiple simulations were performed by assigning known torques
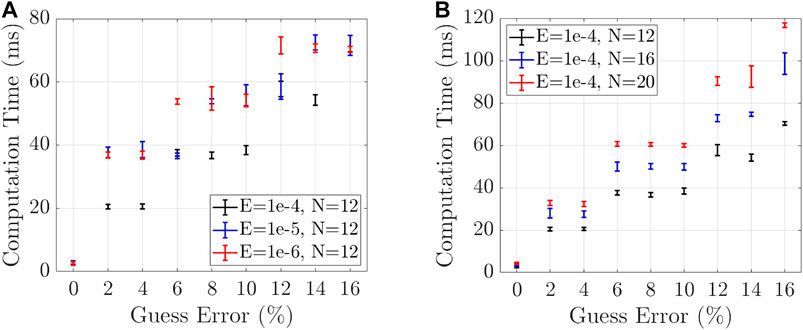
FIGURE 13. (A): Computation time required for solving a solution to the BVP changes with decreasing tolerable error (E) for a constant number of nodes. (B): Computation time required for solving a solution to the BVP changes with an increasing number of nodes (N) and increasing percentage errors from a valid solution, for a constant tolerable error.
Figure 13A shows how the computation time required for solving a solution to the BVP changes with decreasing tolerable error (E) and increasing percentage errors from a valid solution (at
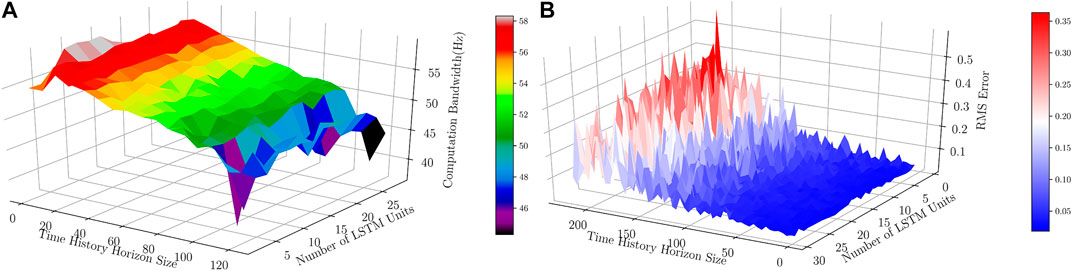
FIGURE 14. (A): Computation bandwidth (Hz) obtained with respect to different number of LSTM units and size of time history horizon (for number of epochs = 25 and batch size = 1). (B): RMS Error (mm) of the prediction on Data-set IV using trained models with different number of LSTM units and size of time history horizons (for number of epochs = 25 and batch size = 1).
To sum up, this experiment demonstrates that not only can the presented RNN-based model outperform classical modeling approaches such as the Cosserat rod model, but also it shows possibilities to use the model in practice for closed-loop control applications.
6 Discussion
This work suggests a distributed architecture for modeling complex dynamical systems by using multiple light-weight RNN-based models. As a result, the architecture would be easier to design and debug, and also benefits from faster convergence compared to one large network. Furthermore, large networks may take longer times to be trained, and they may not show an acceptable performance and readjusting (hyper-)parameters and restarting the training process might be necessary.
Increasing the size of history horizons in training stages may reduce the error to some extent, but on the other hand, it makes the model slower. Based on conventional dynamical models, the length of the history size should be at least 2. To reach a state-of-the-art performance, i.e., having less error and faster model simultaneously, one may prefer varied batch sizes in the training and run-time phases. As a suggestion, we can use different batch sizes for training and run-time stages. A model can be trained with appropriate batch sizes such that the model performance suits the given criteria. Afterward, one can create a new network with the pre-trained weights compiled with a batch size of 1.
The performance, i.e., the convergence and stability, of the presented algorithm in this paper, unlike conventional algorithms, is independent of the number of nodes considered for the whole manipulator. To be specific, in the analytical model, there might be a need for several discretization nodes to achieve a convergent solution with a specific tolerable error; however, in the RNN-based model, only specific points/points of interests (e.g., two actuation points in the experiment) are considered. In other words, in the experiment, 13 nodes (4 for each flexible subsection and two for each magnet, and 1 for the base) were chosen for solving the Cosserat rod model, but two nodes were selected for the RNN-based model. However, the complexity of dynamical systems (i.e., PDEs) affects the complexity of the architecture used in the RNN-based model, i.e., the number of layers and LSTM units and generally how deep the model is. Nevertheless, the suggested model suits parallel implementation and can benefit from a high bandwidth for closed-loop control applications. Furthermore, the architectures of the proposed RNN-based model can be optimized by reducing the number of layers and trainable parameters to maximize the achievable bandwidths.
The evaluations showed that incorporating poses of adjacent nodes and also wrenches as a separated input might help to have, to some extent, a generalizable model rather than just purely learning the structure of data. However, supervised learning methods likely tend to preserve structure of data, and these models might not entirely respect underlying physics (conservation laws). In other words, these methods might not be wholly physics-aware and applicable for untrained/unprecedented dynamics or geometries without any adjustment, re-training, or using techniques such as transfer learning, etc. One possible and interesting solution (Psichogios and Ungar, 1992; Lagaris et al., 1998; Raissi et al., 2019) to overcome this problem and move toward fully physics-aware neural networks is revisiting lost functions for the training process. To be specific, it is mentioned in Problem Statement Section that the idea is finding solutions for PDEs given in Eq. 1, i.e.,
This modified loss function enforces the structure imposed by Eq. 1 for large number (e.g.,
7 Conclusion
This paper describes an approach for the real-time prediction of dynamics for general continuum soft manipulators, based on machine learning techniques and Lie group variational integration methods. Poses of a soft, polymer-based manipulator, in the presence of conservative and non-conservative wrenches, are predicted and validated experimentally. The comparison results of the proposed model and a well-known model for continuum manipulators, i.e., Cosserat rod theory, are also provided, revealing the practical effectiveness of the proposed model. The presented method can be extended to different soft robots with different shapes and materials. In addition, training of physics-aware neural networks for solving PDEs and the procedure of a model-based controller design are topics of research to be studied as future work.
Data Availability Statement
The original contributions presented in the study are included in the article/Supplementary Material, further inquiries can be directed to the corresponding author.
Author Contributions
AT: Formal analysis, Visualization, Writing original draft, VV: Review and Editing, MR: Writing, Analysis, OE: Review and Editing, JT: Review and Editing, KM: Review and Editing, SM: Review, Editing, and Resources for experiment, ØM: Review and Editing.
Funding
This research has received funding from the European Research Council (ERC) under the European Union’s Horizon 2020 Research and Innovation programme (Grant Agreement #866494 - project MAESTRO).
Conflict of Interest
The authors declare that the research was conducted in the absence of any commercial or financial relationships that could be construed as a potential conflict of interest.
Appendix: cosserat rod theory
The Cosserat rod model of the manipulator assigns a position
where
Footnotes
1For the details see Demoures et al. (2015).
2Dynamic equations are given in Tariverdi et al. (2020), Sec. 2.
References
Ansari, Y., Manti, M., Falotico, E., Mollard, Y., Cianchetti, M., and Laschi, C. (2017). Towards the development of a soft manipulator as an assistive robot for personal care of elderly people. Int. J. Adv. Robot. Syst. 14, 172. doi:10.1177/1729881416687132
Antman, S. S. (1995). “Nonlinear problems of elasticity,” in Applied mathematical sciences. Editors J. E. Marsden, and L. Sirovich (New York, United States: Springer), Vol. 107.
Burgner, J., Swaney, P. J., Lathrop, R. A., Weaver, K. D., and Webster, R. J. (2013). Debulking from within: a robotic steerable cannula for intracerebral hemorrhage evacuation. IEEE Trans. Biomed. Eng. 60, 2567–2575. doi:10.1109/TBME.2013.2260860
Demoures, F., Gay-Balmaz, F., Leyendecker, S., Ober-Blöbaum, S., Ratiu, T. S., and Weinand, Y. (2015). Discrete variational Lie group formulation of geometrically exact beam dynamics. Numer. Math. 130, 73–123. doi:10.1007/s00211-014-0659-4
Edelmann, J., Petruska, A. J., and Nelson, B. J. (2017). Magnetic control of continuum devices. Int. J. Robot. Res. 36, 68–85. doi:10.1177/0278364916683443
Grady, M. S., Howard, M. A., Dacey, R. G., Blume, W., Lawson, M., Werp, P., et al. (2000). Experimental study of the magnetic stereotaxis system for catheter manipulation within the brain. J. Neurosurg. 93, 282–288. doi:10.3171/jns.2000.93.2.0282
Grazioso, S., Di Gironimo, G., and Siciliano, B. (2019). A geometrically exact model for soft continuum robots: the finite element deformation space formulation. Soft Robot. 6, 790–811. doi:10.1089/soro.2018.0047
Hochreiter, S., and Schmidhuber, J. (1997). Long short-term memory. Neural Comput. 9, 1735–1780. doi:10.1162/neco.1997.9.8.1735
Hyatt, P., Wingate, D., and Killpack, M. D. (2019). Model-based control of soft actuators using learned non-linear discrete-time models. Front. Robot. AI 6. doi:10.3389/frobt.2019.00022
Jones, B. A., Gray, R. L., and Turlapati, K. (2009). “Three dimensional statics for continuum robotics,” in IEEE/RSJ International Conference on Intelligent Robots and Systems, St Louis, United States, October 11–15 2009.(New York, United States: IEEE), 2659–2664. doi:10.1109/IROS.2009.5354199
Jung, J., Penning, R. S., and Zinn, M. R. (2014). A modeling approach for robotic catheters: effects of nonlinear internal device friction. Adv. Robot. 28, 557–572. doi:10.1080/01691864.2013.879371
Katzschmann, R. K., Marchese, A. D., and Rus, D. (2015). Autonomous object manipulation using a soft planar grasping manipulator. Soft Robot. 2, 155–164. doi:10.1089/soro.2015.0013
Kesner, S. B., and Howe, R. D. (2011). Position control of motion compensation cardiac catheters. IEEE Trans. Robot. 27, 1045–1055. doi:10.1109/TRO.2011.2160467
Lagaris, I. E., Likas, A., and Fotiadis, D. I. (1998). Artificial neural networks for solving ordinary and partial differential equations. IEEE Trans. Neural Netw. 9, 987–1000. doi:10.1109/72.712178
Lee, H., and Kang, I. S. (1990). Neural algorithm for solving differential equations. J. Comput. Phys. 91, 110–131. doi:10.1016/0021-9991(90)90007-N
Mahvash, M., and Dupont, P. E. (2011). Stiffness control of surgical continuum manipulators. IEEE Trans. Robot. 27, 334–345. doi:10.1109/TRO.2011.2105410
Marban, A., Srinivasan, V., Samek, W., Fernández, J., and Casals, A. (2019). A recurrent convolutional neural network approach for sensorless force estimation in robotic surgery. Biomed. Signal Process. Control. 50, 134–150. doi:10.1016/j.bspc.2019.01.011
McMahan, W., Chitrakaran, V., Csencsits, M., Dawson, D., Walker, I. D., Jones, B. A., et al. (2006). “Field trials and testing of the OctArm continuum manipulator,” in Proceedings 2006 IEEE International Conference on Robotics and Automation, Orlando, United States, May 15–19 2006 (New York, United States: IEEE), 2336–2341. doi:10.1109/ROBOT.2006.1642051
Pai, D. K. (2002). Strands: interactive simulation of thin solids using cosserat models. Comput. Graph. Forum 21, 347–352. doi:10.1111/1467-8659.00594
Petruska, A. J., and Nelson, B. J. (2015). Minimum bounds on the number of electromagnets required for remote magnetic manipulation. IEEE Trans. Robot. 31, 714–722. doi:10.1109/TRO.2015.2424051
Psichogios, D. C., and Ungar, L. H. (1992). A hybrid neural network-first principles approach to process modeling. AIChE J. 38, 1499–1511. doi:10.1002/aic.690381003
Raissi, M., Perdikaris, P., and Karniadakis, G. E. (2019). Physics-informed neural networks: a deep learning framework for solving forward and inverse problems involving nonlinear partial differential equations. J. Comput. Phys. 378, 686–707. doi:10.1016/j.jcp.2018.10.045
Rucker, D. C., and Webster III, R. J. (2011). Statics and dynamics of continuum robots with general tendon routing and external loading. IEEE Trans. Robot. 27, 1033–1044. doi:10.1109/TRO.2011.2160469
Sadati, S., Shiva, A., Elnaz Naghibi, S., Rucker, C., Renson, L., Bergeles, C., et al. (2019). “Reduced order vs. Discretized lumped system models with absolute and relative states for continuum manipulators,” in Robotics: Science and Systems XV (Robotics: Science and Systems Foundation), Freiburg im Breisgau, Germany, June 22–26 2019. doi:10.15607/RSS.2019.XV.076
Sikorski, J., Dawson, I., Denasi, A., Hekman, E. E. G., and Misra, S. (2017). “Introducing BigMag—a novel system for 3D magnetic actuation of flexible surgical manipulators,” in IEEE International Conference on Robotics and Automation (ICRA), Marina Bay Sands Singapore, May 29, 2017 (Singapore: IEEE), 3594–3599. doi:10.1109/ICRA.2017.7989413
Sikorski, J., Denasi, A., Bucchi, G., Scheggi, S., and Misra, S. (2019). Vision-based 3-D control of magnetically actuated catheter using BigMag-an array of mobile electromagnetic coils. IEEE/ASME Trans. Mechatron. 24, 505–516. doi:10.1109/tmech.2019.2893166
Simaan, N., Taylor, R., and Flint, P. (2004). “A dexterous system for laryngeal surgery,” in IEEE International Conference on Robotics and Automation, 2004. Proceedings. ICRA ’04, New Orleans, LA, USA, April 26–May 1, 2004. 351–357. doi:10.1109/ROBOT.2004.1307175
Tariverdi, A., Venkiteswaran, V. K., Martinsen, Ø. G., Elle, O. J., Tørresen, J., and Misra, S. (2020). Dynamic modeling of soft continuum manipulators using lie group variational integration. Plos One 15, e0236121. doi:10.1371/journal.pone.0236121
Thuruthel, T. G., Falotico, E., Renda, F., and Laschi, C. (2017). Learning dynamic models for open loop predictive control of soft robotic manipulators. Bioinspir. Biomim. 12, 066003. doi:10.1088/1748-3190/aa839f
Thuruthel, T. G., Shih, B., Laschi, C., and Tolley, M. T. (2019). Soft robot perception using embedded soft sensors and recurrent neural networks. Sci. Robot. 4, eaav1488. doi:10.1126/scirobotics.aav1488
Till, J., Aloi, V., and Rucker, C. (2019). Real-time dynamics of soft and continuum robots based on Cosserat rod models. Int. J. Robot. Res. 38, 723–746. doi:10.1177/0278364919842269
Turan, M., Almalioglu, Y., Araujo, H., Konukoglu, E., and Sitti, M. (2018). Deep EndoVO: a recurrent convolutional neural network (RCNN) based visual odometry approach for endoscopic capsule robots. Neurocomputing 275, 1861–1870. doi:10.1016/j.neucom.2017.10.014
Weinan, E., Han, J., and Jentzen, A. (2017). Deep learning-based numerical methods for high-dimensional parabolic partial differential equations and backward stochastic differential equations. Commun. Math. Stat. 5, 349. doi:10.1007/s40304-017-0117-6
Wen, T., Wan, T. R., Gould, D. A., and John, N. W. (2012). Thien HowA stable and real-time nonlinear elastic approach to simulating guidewire and catheter insertions based on cosserat rod. IEEE Trans. Biomed. Eng. 59, 2211–2218. doi:10.1109/TBME.2012.2199319
Keywords: continuum manipulators, soft robotics, dynamic models, Cosserat rod theory, Lie group variational integration, recurrent neural network
Citation: Tariverdi A, Venkiteswaran VK, Richter M, Elle OJ, Tørresen J, Mathiassen K, Misra S and Martinsen ØG (2021) A Recurrent Neural-Network-Based Real-Time Dynamic Model for Soft Continuum Manipulators. Front. Robot. AI 8:631303. doi: 10.3389/frobt.2021.631303
Received: 19 November 2020; Accepted: 05 February 2021;
Published: 18 March 2021.
Edited by:
Thomas George Thuruthel, University of Cambridge, United KingdomReviewed by:
Marc Daniel Killpack, Brigham Young University, United StatesUtku Culha, Max Planck Institute for Intelligent Systems, Germany
Copyright © 2021 Tariverdi, Venkiteswaran, Richter, Elle, Tørresen, Mathiassen, Misra and Martinsen. This is an open-access article distributed under the terms of the Creative Commons Attribution License (CC BY). The use, distribution or reproduction in other forums is permitted, provided the original author(s) and the copyright owner(s) are credited and that the original publication in this journal is cited, in accordance with accepted academic practice. No use, distribution or reproduction is permitted which does not comply with these terms.
*Correspondence: Abbas Tariverdi, YWJiYXN0QHVpby5ubw==