- German Aerospace Center (DLR), Robotics and Mechatronics Center, Weßling, Germany
We propose a fault-tolerant estimation technique for the six-DoF pose of a tendon-driven continuum mechanisms using machine learning. In contrast to previous estimation techniques, no deformation model is required, and the pose prediction is rather performed with polynomial regression. As only a few datapoints are required for the regression, several estimators are trained with structured occlusions of the available sensor information, and clustered into ensembles based on the available sensors. By computing the variance of one ensemble, the uncertainty in the prediction is monitored and, if the variance is above a threshold, sensor loss is detected and handled. Experiments on the humanoid neck of the DLR robot DAVID, demonstrate that the accuracy of the predicted pose is significantly improved, and a reliable prediction can still be performed using only 3 out of 8 sensors.
1 Introduction
Robotic systems with deliberately introduced elasticity have become a promising alternative to classical rigid robots, be it in manipulation or locomotion tasks, in humanoid or animoid robots. Apart from their favorable dynamic properties, passive compliance protects the actuators from peak forces or torques that arise from collisions, be they unexpected or intentional. In this context, the development of distinct joints arose termed continuum mechanism. They extend the current portfolio of joints with passive compliance and use a spring element made out of a continuously deformable soft material with a beam-like geometry. As an example, the neck joint of the humanoid robot David (Reinecke et al., 2016) is shown in Figure 1.
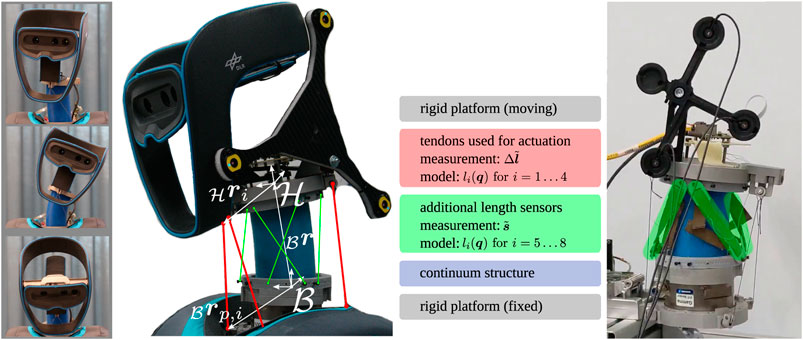
FIGURE 1. Neck and head of the humanoid robot David. Left: Motion capability of the structurally flexible neck joint. Middle: Close up scheme of the experimental system and the necessary length information from the respective sensors. Right: Experimental setup with the LEDs used by the tracking system (in black) and the additional length sensors (highlighted in green).
The application requires to control the pose of the top end of the continuum mechanism, termed end effector pose, along trajectories or toward equilibrium positions in its workspace. Rigorous models which relate encoder values of the actuation to end effector poses are computationally expensive and prone to model parameter uncertainties. As we are aiming for mobile systems, the need of external tracking system must be limited to calibration and evaluation of a pose estimation method. At deployment time, such pose estimation method must use onboard sensors only.
In this paper, we propose a data-driven approach to pose estimation for elastic structures, which also features uncertainty estimation and error-handling. The specific contributions, which also define the structure of the paper, are:
• A data-driven approach for real time six-DoF pose of tendon-driven continuum mechanism using few data points. The model-free estimator can be trained in the experiment and requires only a small number of measurements (Section 4.1).
• Uncertainty estimation to detect sensor failure (e.g., slack tendons). This is done by creating an ensemble of estimators, where each estimator takes only a subset of sensor information as an input, and monitoring the uncertainty (Section 4.3).
• A strategy to handle sensor by adapting the pose estimation. As soon as an anomaly is detected, we select the estimators not using the faulty sensors and continue predicting accurately the pose. To the best of our knowledge, this is the first work dealing with failure detection and handling in the context of continuum mechanisms (Section 4.3).
• Demonstrating the effectiveness of these methods on the elastic neck of the DLR robot DAVID. In particular, we demonstrate that the accuracy of the pose estimation is significantly improved, and that reliable predictions can still be made with only 3 out of 8 sensors (Section 5).
Before following this structure, we first formalize the problem statement in the next section.
2 Problem Statement
This work treats the estimation problem of the position and orientation (pose) of the upper platform of a tendon-driven continuum mechanism. The considered mechanism is depicted, in its current application in Figure 1, and a schematic drawing to illustrate the kinematics in Figure 2. It consists of a inertial fixed lower platform, a moving upper platform and a continuum structure in between. The inertial frame of reference is denoted
where
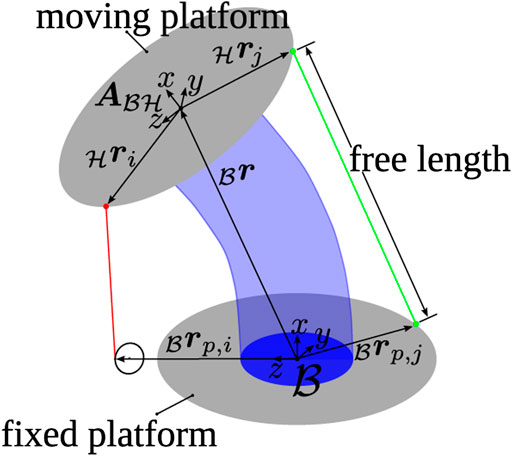
FIGURE 2. Schematic image of the tendon-driven continuum mechanism including the used coordinate frames and vectors to build up the kinematic model of the length measurement.
For actuation, tendons are connected to the upper platform. By putting tension on them, a loading is introduced onto the upper platform which deforms the continuum and initiates a motion. The tendons are routed alongside the continuum to the lower platform without touching, Figure 1 indicated with red. In the lower platform, the tendons actuators are located. The incorporated position measurement
Furthermore, four additional length sensors are placed on the system indicated in green in Figure 1. They are also spanned from the upper to the lower platform and provide sensor values
with the constant calibration matrix
In a prior publication (Deutschmann et al., 2019), the estimation problem was solved using the geometric model for the length sensors of Eq. 5. An online minimization of the error
Sources of error using this pose estimation technique are related to the following assumptions. First, it is assumed that the sensor readings in Eqs 3, 4 correspond linearly to a length of the tendons or sensors. Second, the geometric model in Eq. 5 relies on the accurate knowledge about the pulley kinematics of the tendons, and perfectly known attachment points and straight sensors. If these assumptions do not hold, the accuracy of the resulting pose which minimizes Eq. 6 might be affected.
In tests on the real hardware, the pose could be predicted with a maximum estimation error of
3 Related Work
There are two main approaches to pose estimation for elastic structures. If the geometric and material parameters are known with high accuracy, geometric (Jones and Walker, 2006) or static (Camarillo et al., 2009; Rucker and Webster, 2011) deformation models are employed. As these models require information about actuator positions or forces/torques, a common strategy is to use actuation sensors or additional sensors such as passive cables (Rolf and Steil, 2012) or fiber-bragg sensors (Roesthuis and Misra, 2016). More recently, a pose estimation technique without a deformation model for tendon-driven continuum mechanism was proposed (Deutschmann et al., 2019). It uses encoder values of the tendon actuation, additional deformation based length sensors and a model for the pose-dependent length measurements to extract the pose by nonlinear optimization or an Extended Kalman Filter. Two disadvantages of model-based approaches is that they are prone to parameter uncertainty, and also rely on the assumption of taut tendons (and length sensors) which might be jeopardized in fast motions or external contacts.
The second approach is to use data-driven methods, which learn a direct input-output behavior from measured data. The inputs are commonly actuation torques or actuator positions, and the corresponding output is the end effector pose. Popular models are based on neural networks to approximate the static characteristics from actuation forces (Braganza et al., 2007; Giorelli et al., 2015), or a Gaussian mixture model to relate actuator lengths to end effector poses (Malekzadeh et al., 2016).
Fault detection in robotic systems (Khalastchi and Kalech, 2018) is a particular instance of the wide field of anomaly detection (Chandola et al., 2009). Three main approaches to tackle the issue are distinguished (Khalastchi and Kalech, 2018): 1) knowledge-based, 2) data-driven-based and 3) model-based approaches.
The fundamental assumption in knowledge-based approaches are that all faults and their corresponding symptoms are known. Then, casual analysis is used based on the fault-symptom relationship to find to fault which is occurring. In (Hamilton et al., 2001) this approach is used to for autonomous underwater vehicles.
Similarly, a common technique in machine-learning is train a model to classify normal and abnormal behaviors in a supervised fashion (Hornung et al., 2014). This requires a labeled dataset, and is unlikely to generalize to unseen faults. When no labels are available, unsupervised methods such as distance to a nearest neighbor (He and Wang, 2007) or data clustering (e.g., fitting a Gaussian mixture model to the data (Yu et al., 2010)) can be used instead.
Machine learning techniques belong to the second category, i.e., data-driven approaches and represent a large source for possible fault detection techniques. Other approaches covers the generation of data for nominal behavior by a physical simulator (Haidu et al., 2015). Based on the data, a failure envelope is learned for each datatype and failures are distinguished if the envelope is violated during task execution.
Other data-driven approaches make use of statistical filters. A common approach in mobile systems is the usage of Kalman-filters. A fast approach which utilizes one Kalman filter can be found in (Schmid et al., 2012; Steidle et al., 2016). Faulty sensors used in the process update are handled based on a confidence measure of the sensor data. Depending on that confidence, sensor information is added or removed in the process update. Also, a bank of Kalman-filters is utilized where each Kalman-filter predicts the nominal state of a systems assuming a specific failure has occurred. For a mobile autonomous robot in (Goel et al., 2000), a bank of eight filters are utilized (implying eight possible failure sources) and the most reliable filter, used for state estimation, is chosen based on pre-trained neural-network using the filter residuals. As every filter is related to a specific failure, diagnosis is already incorporated.
The last category are model-based approaches. Commonly, they utilize a model of the system for a nominal behavior and fault are correspondingly identified if the real behavior, measured by some signals, is not coherent with the model of this signal. For hardware failures, physically inspired models are commonly used and a comprehensive treatment can be found in (Chen and Patton, 2012).
Our proposed method is a data-driven approach which utilizes machine learning with unsupervised training as it does not require labels. Unlike the previous approaches, that only detect a potential failure, we leverage minimal knowledge about the task to detect and handle the fault.
4 Method
4.1 Pose Estimation as a Regression Problem
The problem of predicting the six-DoF pose
where
This is a classic regression problem that can be solved using various techniques (Stulp and Sigaud, 2015). In this paper, we use linear models
4.2 Uncertainty Estimation Using Bootstrapped Ensemble
Querying only one predictor
Uncertainty estimation can be achieved by training an ensemble of n models
where
Unfortunately, such an ensemble underestimates the epistemic uncertainty, as all the models are trained on the same dataset
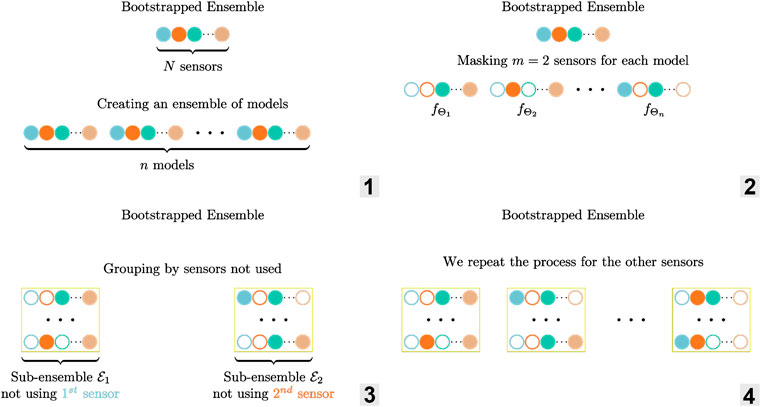
FIGURE 3. Illustration of the ensemble
4.3 Failure Detection and Handling
The ensemble of estimators presented in the previous section gives us an uncertainty measure: the variance
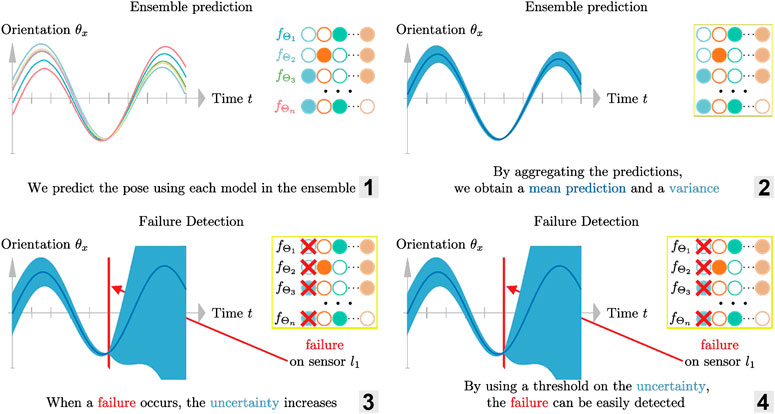
FIGURE 4. Illustration of the failure detection using an ensemble of estimator. 1. Predicting the pose which each model in the ensemble 2. Aggregating the predictions to obtain a mean and a variance 3–4. Detecting failure by using a threshold on the variance (measure of uncertainty).
For our six-DoF pose estimation problem, we have redundant sensor information: there are more sensors than needed and there is coupling in the system. Because of the extra sensors, we can detect which one(s) failed, and react to it by grouping the predictions. This allows to estimate the pose
To illustrate the idea, we now consider the case where we mask
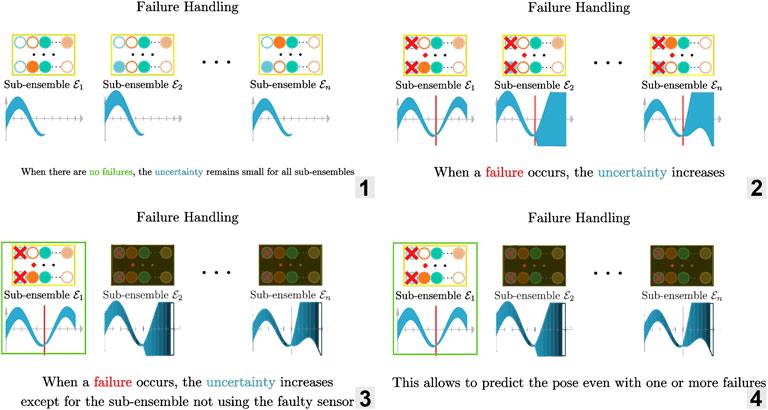
FIGURE 5. Illustration of the failure handling using an ensemble of estimator. 1. Predicting the pose using each sub-ensembles when there is no failures: the uncertainty remains small 2–3. When a failure occurs, the uncertainty increases except for the sub-ensemble not using the faulty sensor 4. Because there is a sub-ensemble not affected by the failure, we can continue to predict accurately the pose.
In order to check if a sub-ensemble
The previous example was for one failed sensor only. To detect and handle more than one, we repeat three steps:
1. Ensemble prediction: predict the pose using each model from the ensemble
2. Group predictions by sensors not used to create the sub-ensembles
3. Check the variance of each sub-ensemble to detect failure
We start with
To detect
We then repeat that process with additional sensors masked, until there are not enough sensors left to have a reliable prediction. For the experimental platform used in this paper, the experiments reveal that relying on 3 (out of
Concretely, to be robust up to 4 failures, we need to cover the cases where:
• there is one failure, therefore mask 2 sensors and train
• there are two failures, therefore mask 3 sensors and train
• there are three failures, therefore mask 4 sensors and train
• there are four failures, therefore mask 5 sensors and train
Which means we have to train
Although simple, this naive way of creating subsets does not scale well if the number of sensors or failures handled increases. We discuss in Section 5.6 how to optimize that process.
5 Experiments
The goal of this section is to evaluate the performance of the proposed method in terms of speed and accuracy, and investigate its robustness against one or more sensor failures.
5.1 Experimental Setup
The experimental setup consists of the tendon-driven continuum mechanisms used as the neck of the humanoid robot DAVID, Figure 1. The upper platform is equipped with a marker target of an external camera tracking system, which serves as the ground truth data of the pose. The tracking system is only used for training, evaluation and is not needed afterward. The pose dependent length information that is retrieved at a frequency of 300 Hz comes from two sources. The tendon lengths are given by the tendon actuators from Robodrive and the four additional length sensors are provided by Kinfinity UG.
The placement of the two type of sensors is not arbitrary. The tendons, i.e., the power transmission element of the actuation, decide the reachable workspace of the mechanism and therefore their routing cannot be changed. In contrast the placement of length sensors can be chosen almost freely. In (Deutschmann et al., 2019), different placements of the sensors were experimentally investigated regarding their accuracy. To provide a fair comparison, the configuration yielding best results was also chosen for the present paper. The system is driven to different poses or along trajectories by commanding different sets of tendon-tension, which are realized by a local tendon-tension controller in each of the actuators (Chalon et al., 2011).
5.2 Data-Driven Pose Estimation
5.2.1 Static and Dynamic Estimation Error
Static Pose Estimation. To assess the performance of our six-DoF estimator and compare it to previous work, we first command the neck to reach 200 static poses. For each pose, we retrieve the ground truth
Dynamic Pose Estimation. We then evaluate the pose estimation method trained with static poses only on dynamic motions. For that, we record the ground-truth and estimated pose on a pre-defined trajectory. We provide the reader with a Supplementary Video showing the method in action.
5.2.2 Results
Static Pose Estimation. The results are summarized using mean error and standard deviation over the test poses in Table 1, runtimes are included when available. We also show the error distribution in position and orientation in Figure 6.
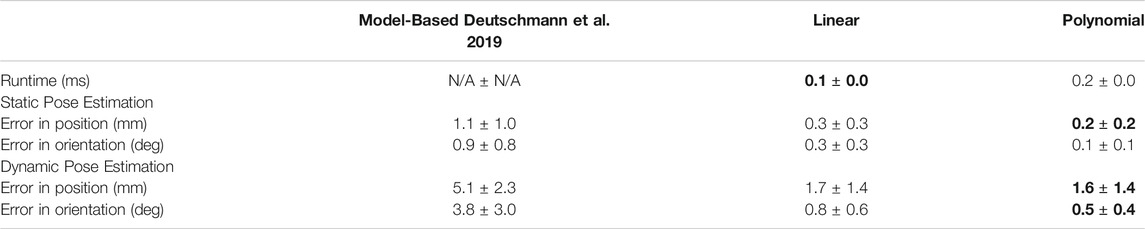
TABLE 1. Comparison of mean runtime and error (both in position and orientation) for each method. The data-driven approaches are fast and also more accurate than the model-based approach. For each metric, we bolded the best mean. “N/A” means that the data is not available.
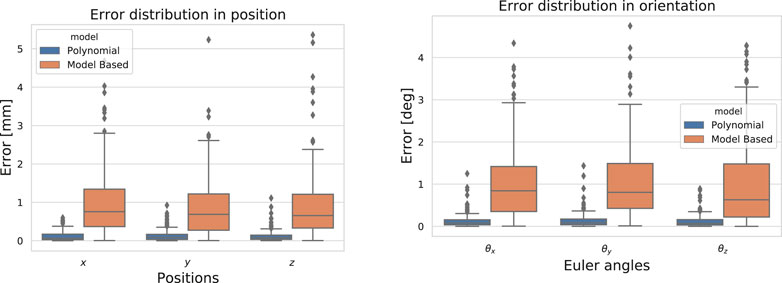
FIGURE 6. Error distribution in position and in orientation on 180 static poses for the model-based approach (Deutschmann et al., 2019) and the polynomial model.
Overall, the data-driven approaches are fast (they run at ∼ 5000 Hz) and more accurate than the model-based one: the mean error is reduced up to 5 times (cf. Table 2). As expected, the linear model runs faster at a cost of some accuracy compared to the polynomial model.It is worth mentioning that although the model-based approach appears inaccurate in the present comparison, it is fairly accurate and fast to compute when compared to other model-based pose estimation techniques as reported in (Deutschmann et al., 2019).
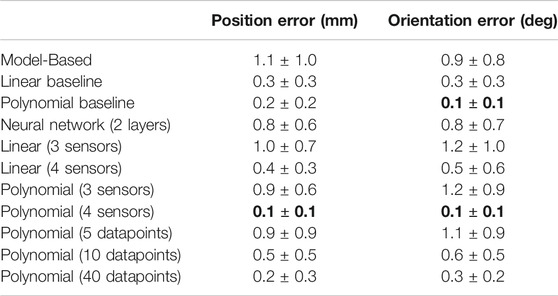
TABLE 2. Ablation study: influence of the amount of training data, number of sensors and type of model on the performance. We bolded results with the best mean error. Baseline models are trained using 20 datapoints and 8 sensors.
Dynamic Pose Estimation. To report also on the dynamic estimation behavior, the experimental platform is driven to several static poses subsequently and the estimated pose for the model-based and the present approach are recorded. The mean-error along the trajectory of 200 subsequent poses is given in Table 1 and the corresponding trajectories of four estimated coordinates
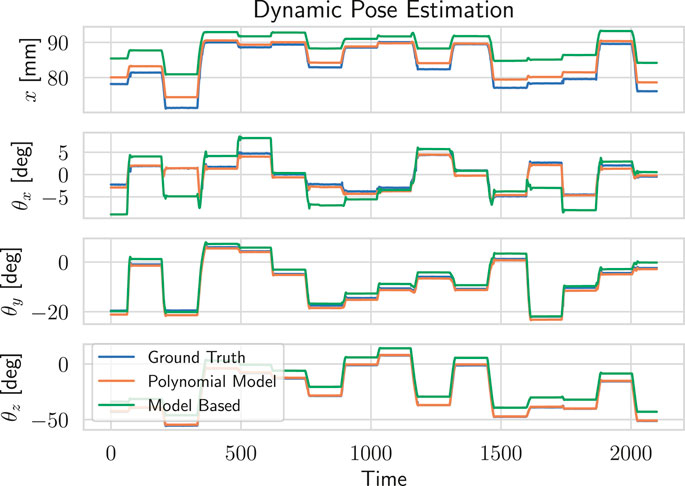
FIGURE 7. Qualitative comparison of the model-based and polynomial estimators for dynamic pose estimation.
As for static poses, the data-driven approaches perform best, with the polynomial model being more accurate than the linear one. Mean error reported in Table 1 is higher than for static poses for two reasons. First, it now accounts for the transition error between two static poses, that are not covered at all during training. Then, as we are considering trajectories, static errors at fixed poses accumulate yielding a higher mean value.It is worth noting that those models were only trained on static poses and therefore the results could be improved if part of the dynamic poses where included in the training set.
5.3 Hyperparameters Study
To study the effect of the different hyperparameters (type of model, training set size, number of sensors) on the performance, we compare the baseline regressors (20 datapoints and 8 sensors) to several variants. One datapoint corresponds to training data at a specific pose. We present the results in Table 2.
Effect of the training set size. We vary the training set size from 5 datapoints to 40 datapoints for the polynomial model. Overall, with more training data, the performance improves. However, after a certain amount (here 30 datapoints), adding more data does not improve the results anymore. This is due both to the irreducible error (sensor noise) and to the limited capacity of the polynomial model. Although the results are slightly worse with 40 datapoints, the difference is not significant.
Effect of the type of model. We compare linear, polynomial and neural network1 models. Although the neural network yields good performance, it is less sample efficient than the two others, i. e., with more training data it would reach the same accuracy. It also requires hyperparameter tuning (learning rate, mini-batch size, …) and has more parameters (
Effect of the number of sensors. We compare the baseline linear and polynomial models (8 sensors) to models using less sensors (3 and 4 sensors). As expected, adding more sensors reduces the error for the linear model. Almost no changes can be observed for the polynomial model with more than 4 sensors: the results are slightly worse but the difference is not significant. As discussed in Section 4.3, having redundant sensor information is key to detect and handle potential failures. The more sensors we have, the more failure we can handle. Therefore having 8 sensors is preferable.
Effect of the placement of sensors. Because the polynomial model performs well with only 4 sensors (for instance when using only the tendon length sensors), the placement of the 4 additional length sensors will not affect much the accuracy. However, the positioning would affect the ability to detect failures: if the information that a sensor provides is not useful for the prediction, then it will not be used by the polynomial model, the weight for this input feature will be close to zero. As a result, if such sensor fails, as it does not affect the variance of the predictions, the failure will not be detected but the pose will still be predicted accurately.
5.4 Failure Detection and Handling
To evaluate the effectiveness of the proposed approach for detecting and handling failures, we simulate the loss of sensors while the neck is moving. A common failure is when a length sensor outputs wrong values because a tendon goes slack. Instead of a correct measurement, it outputs zeros. Another type of failure, harder to detect, is when the sensor freezes and outputs a constant value. In Figures 8A,B, we show the effect of both failures on the uncertainty: a jump can be observed right after the loss of tension in Figure 8A. When the sensor freezes (cf. Figure 8B), as expected, the failure is detected only when the neck position changes. Because in both cases the variance increases by a large amount, no careful tuning of the detection threshold is required. To show that the method can handle more than one failure, we simulate in Figure 9 the loss of four sensors.
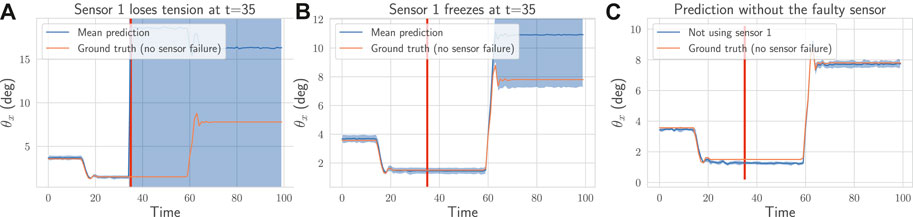
FIGURE 8. On a recorded trajectory, we simulate two types of failures (depicted as the red vertical line): (A) one tendon goes slack at
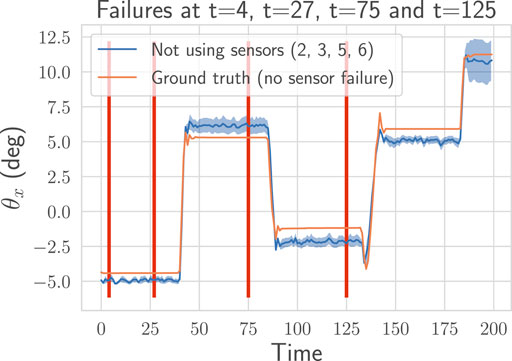
FIGURE 9. On a recorded trajectory, we simulate four failures (depicted as the red vertical lines). The proposed method detects automatically those four failures (sensors
In Figures 8C, 9, we display the prediction over time for the sub-ensemble not using the broken sensors. We use the ground-truth pose as a reference. The approach successfully detect all the failures and handle them by using the sub-ensemble not affected by the loss of the sensors. As a result, the proposed method can robustly and still accurately (cf. Table 2) predict the pose even with multiple losses.
5.5 Comparison With the Linearized Model
The geometry of the deformation of the neck system and the coupling of the tendon motion is highly nonlinear (Deutschmann et al., 2018). The geometrical exact nonlinear mapping can be found in (Deutschmann et al., 2019). This work confirms the non-linearity as a polynomial model of order two reveals the best prediction results. However, as stated in Table 2, the linear models already yield results comparable to the model-based approach. We therefore compare the first-order term of the trained linear coefficients for four sensors used with the partial derivative of the
The top three rows correspond to positions and the bottom three rows to orientations. The trained coefficients (9) and the model-based coefficients (10) have the same signs and symmetries, indicating that the sensor information is used in a similar fashion to predict the direction of the pose. However, the magnitude of the values defers largely: simply linearizing the model would not be as accurate as the trained linear model.
5.6 Limitations
We have shown in the previous sections that the proposed approach yields a good estimation of the pose and handle failures while keeping a low runtime. However, we have to train
6 Discussion and Conclusion
In this work, we show that data-driven approaches are competitive alternatives to estimate the pose of a tendon-driven continuum mechanism. The linear and polynomial models are fast to train, require only a small amount of data and prove to be more accurate that the model-based approach. As mentioned in the end of Section 2, assumptions about the sensor linearity and perfectly known kinematics are made which, in cases where the loose their validity, may result in larger errors in the pose estimation. In other words, small deviations or modeling errors in the kinematics of the tendon pulleys or the attachment points of the sensors will cost accuracy in the estimated pose. In contrast, the polynomial model learns a direct mapping from sensor readings to the measured pose and does not make these assumptions, allowing an improved accuracy.
To detect and handle sensor failures, we make use of ensembling technique and minimal knowledge about the system. By clustering the different models, our method predicts the pose accurately even with 4 out of 8 faulty sensors.
The presented method embodies a computationally fast and accurate pose estimation method. This method was already employed to train a reinforcement learning controller (Raffin and Stulp, 2020) and could also replace the model-based approach, currently used in the model-based control approach implemented on the neck system (Deutschmann et al., 2017). This would result in a more accurate positioning given the more accurate estimated pose.
One limitation is the scalability of the method, as discussed in the previous section, which should be addressed in the future. Apart from that, our method is in fact not specific to tendon-driven continuum mechanism: it only requires sensor redundancy and learn to predict the pose directly from data.
Data Availability Statement
The raw data supporting the conclusions of this article will be made available by the authors, without undue reservation.
Author Contributions
AR conceived of the presented idea and carried out the experiment with the help of BD, AR and BD wrote the manuscript with support from FS.
Funding
This work was partially funded by the Deutsche Forschungsgemeinschaft (DFG, German Research Foundation)—Grant Number 405032572, the European Union's Horizon 2020 Research and Innovation Program under Grant Number 951992 (project VeriDream) and by the Hermann von Helmholtz-Gemeinschaft Deutscher Forschungszentren e. V. under Grant ZT-I-0010 (RedMod) and ZT-I-PF-5-20 (LearnGraspPhases).
Conflict of Interest
The authors declare that the research was conducted in the absence of any commercial or financial relationships that could be construed as a potential conflict of interest.
Supplementary Material
The Supplementary Material for this article can be found online at: https://www.frontiersin.org/articles/10.3389/frobt.2021.619238/full#supplementary-material.
Footnotes
12 fully-connected layers of 256 units each, trained with Adam optimizer until convergence using a learning rate of
References
Braganza, D., Dawson, D. M., Walker, I. D., and Nath, N. (2007). A neural network controller for continuum robots. IEEE Trans. Robot. 23, 1270–1277. doi:10.1109/tro.2007.906248
Camarillo, D. B., Carlson, C. R., and Salisbury, J. K. (2009). Configuration tracking for continuum manipulators with coupled tendon drive. IEEE Trans. Robot. 25, 798–808. doi:10.1109/tro.2009.2022426
Chalon, M., Friedl, W., Reinecke, J., Wimboeck, T., and Albu-Schaeffer, A. (2011). “Impedance control of a non-linearly coupled tendon driven thumb,” in IEEE/RSJ International Conference on Intelligent Robots and Systems, San Francisco, CA, September 25–30, 2011 (Piscataway, NJ: IEEE), 4215–4221.
Chandola, V., Banerjee, A., and Kumar, V. (2009). Anomaly detection: a survey. ACM Comput. Surv. 41, 1–58. doi:10.1145/1541880.1541882
Chen, J., and Patton, R. J. (2012). Robust model-based fault diagnosis for dynamic systems, Heidelberg, Germany: Springer Science and Business Media.
Deutschmann, B., Chalon, M., Reinecke, J., Maier, M., and Ott, C. (2019). Six-dof pose estimation for a tendon-driven continuum mechanism without a deformation model. IEEE Robot. Autom. Lett. 4, 3425–3432. doi:10.1109/lra.2019.2927943
Deutschmann, B., Dietrich, A., and Ott, C. (2017). “Position control of an underactuated continuum mechanism using a reduced nonlinear model,” in IEEE 56th annual conference on decision and control, Melbourne, VIC, December 12–15, 2017 (Piscataway, NJ: IEEE), 5223–5230.
Deutschmann, B., Eugster, S. R., and Ott, C. (2018). Reduced models for the static simulation of an elastic continuum mechanism. IFAC-PapersOnLine 51, 403–408. doi:10.1016/j.ifacol.2018.03.069
Efron, B. (1992). Bootstrap methods: another look at the jackknife. Breakthroughs Stat. 569–593. doi:10.1007/978-1-4612-4380-9_41
Giorelli, M., Renda, F., Calisti, M., Arienti, A., Ferri, G., and Laschi, C. (2015). Neural network and jacobian method for solving the inverse statics of a cable-driven soft arm with nonconstant curvature. IEEE Trans. Robot. 31, 823–834. doi:10.1109/tro.2015.2428511
Goel, P., Dedeoglu, G., Roumeliotis, S. I., and Sukhatme, G. S. (2000). “Fault detection and identification in a mobile robot using multiple model estimation and neural network,” in IEEE International Conference on Robotics and Automation, San Francisco, CA, April 24–28, 2000 (Piscataway, NJ: IEEE), 2302–2309.
Haidu, A., Kohlsdorf, D., and Beetz, M. (2015). “Learning action failure models from interactive physics-based simulations,” in IEEE/RSJ international conference on intelligent robots and systems, Hamburg, Germany, 28 September–2 October, 2015 (Piscataway, NJ: IEEE), 5370–5375.
Hamilton, K., Lane, D., Taylor, N., and Brown, K. (2001). “Fault diagnosis on autonomous robotic vehicles with recovery: an integrated heterogeneous-knowledge approach,” in Proceedings 2001 ICRA. IEEE International Conference on Robotics and Automation, Seoul, South Korea, May 21–26, 2001 (Piscataway, NJ: IEEE), 3232–3237.
He, P., and Wang, J. (2007). Fault detection using the k-nearest neighbor rule for semiconductor manufacturing processes. IEEE Trans. Semicond. Manuf. 20, 345–354. doi:10.1109/tsm.2007.907607
Hornung, R., Urbanek, H., Klodmann, J., Osendorfer, C., and Van Der Smagt, P. (2014). “Model-free robot anomaly detection,” in IEEE/RSJ international conference on intelligent robots and systems, Chicago, IL, September 14–18, 2014 (Piscataway, NJ: IEEE), 3676–3683.
Jones, B. A., and Walker, I. D. (2006). Practical kinematics for real-time implementation of continuum robots. IEEE Trans. Robot. 22, 1087–1099. doi:10.1109/tro.2006.886268
Kendall, A., and Gal, Y. (2017). What uncertainties do we need in bayesian deep learning for computer vision?. Adv. Neural Inf. Process. Syst., 5574–5584. doi:10.5555/3295222.3295309
Khalastchi, E., and Kalech, M. (2018). On fault detection and diagnosis in robotic systems. ACM Comput. Surv. 51, 1–24. doi:10.1145/3146389
Malekzadeh, M. S., Queißer, J. F., and Steil, J. J. (2016). “Learning the end-effector pose from demonstration for the bionic handling assistant robot,”in Proceedings of the 9th international workshop on human human friendly robotics, September 29 and 30, 2016, Genoa, Italy.
Metris, k. C. (2016). Available at: http://www.metris3d.huw (Accessed August 31, 2020).
Raffin, A., and Stulp, F. (2020). Generalized state-dependent exploration for deep reinforcement learning in robotics,
Reinecke, J., Deutschmann, B., and Fehrenbach, D. (2016). “A structurally flexible humanoid spine based on a tendon-driven elastic continuum,” in International conference on robotics and automation, Stockholm, Sweden, May 16–21, 2016 (Piscataway, NJ: IEEE), 4714–4721.
Roesthuis, R., and Misra, S. (2016). Steering of multisegment continuum manipulators using rigid-link modeling and FBG-based shape sensing. IEEE Trans. Robot. 32, 372–382. doi:10.1109/tro.2016.2527047
Rolf, M., and Steil, J. J. (2012). Constant curvature continuum kinematics as fast approximate model for the bionic handling assistant,”in International conference on intelligent robots and systems, Vilamoura-Algarve, Portugal, October 7–12, 2012 (Piscataway, NJ: IEEE), 3440–3446.
Rucker, D. C., and Webster, R. J. (2011). Statics and dynamics of continuum robots with general tendon routing and external loading. IEEE Trans. Robot. 27, 1033–1044. doi:10.1109/tro.2011.2160469
Schmid, K., Ruess, F., Suppa, M., and Burschka, D. (2012). “State estimation for highly dynamic flying systems using key frame odometry with varying time delays,”in International conference on intelligent robots and systems, Vilamoura-Algarve, Portugal, October 7–12, 2012 (Piscataway, NJ: IEEE), 2997–3004.
Steidle, F., Tobergte, A., and Albu-Schäffer, A. (2016). “Optical-inertial tracking of an input device for real-time robot control,”in International conference on robotics and automation, Stockholm, Sweden, May 16–21, 2016 (Piscataway, NJ: IEEE), 742–749.
Stulp, F., and Sigaud, O. (2015). Many regression algorithms, one unified model: a review. Neural Netw. 69, 60–79. doi:10.1016/j.neunet.2015.05.005
Keywords: pose estimation, fault-tolerant, data-driven, machine learning, continuum mechanism
Citation: Raffin A, Deutschmann B and Stulp F (2021) Fault-Tolerant Six-DoF Pose Estimation for Tendon-Driven Continuum Mechanisms. Front. Robot. AI 8:619238. doi: 10.3389/frobt.2021.619238
Received: 19 October 2020; Accepted: 12 January 2021;
Published: 30 April 2021.
Edited by:
Thomas George Thuruthel, University of Cambridge, United KingdomReviewed by:
Yasmin Ansari, Scuola Sant'Anna di Studi Avanzati, ItalyChaoyang Song, Southern University of Science and Technology, China
Copyright © 2021 Raffin, Deutschmann and Stulp. This is an open-access article distributed under the terms of the Creative Commons Attribution License (CC BY). The use, distribution or reproduction in other forums is permitted, provided the original author(s) and the copyright owner(s) are credited and that the original publication in this journal is cited, in accordance with accepted academic practice. No use, distribution or reproduction is permitted which does not comply with these terms.
*Correspondence: Antonin Raffin, YW50b25pbi5yYWZmaW5AZGxyLmRl