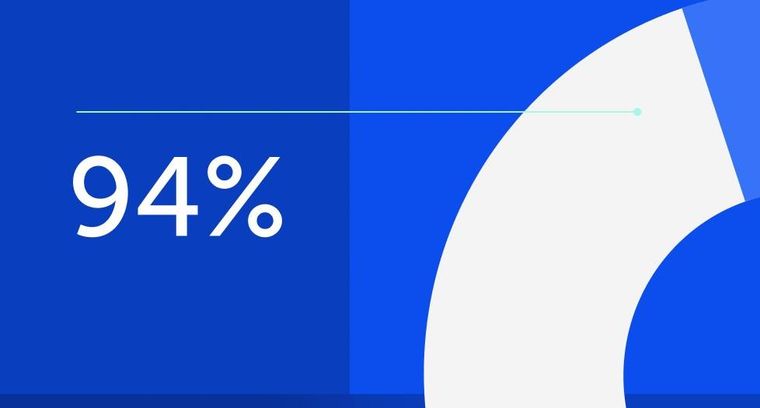
94% of researchers rate our articles as excellent or good
Learn more about the work of our research integrity team to safeguard the quality of each article we publish.
Find out more
REVIEW article
Front. Robot. AI, 16 November 2016
Sec. Soft Robotics
Volume 3 - 2016 | https://doi.org/10.3389/frobt.2016.00069
This article is part of the Research TopicAt the Frontiers of Soft Robotics: Lessons Learnt from the RoboSoft Grand ChallengeView all 8 articles
Soft robotics is a growing area of research which utilizes the compliance and adaptability of soft structures to develop highly adaptive robotics for soft interactions. One area in which soft robotics has the ability to make significant impact is in the development of soft grippers and manipulators. With an increased requirement for automation, robotics systems are required to perform task in unstructured and not well defined environments; conditions which conventional rigid robotics are not best suited. This requires a paradigm shift in the methods and materials used to develop robots such that they can adapt to and work safely in human environments. One solution to this is soft robotics, which enables soft interactions with the surroundings while maintaining the ability to apply significant force. This review paper assesses the current materials and methods, actuation methods and sensors which are used in the development of soft manipulators. The achievements and shortcomings of recent technology in these key areas are evaluated, and this paper concludes with a discussion on the potential impacts of soft manipulators on industry and society.
Interaction with the environment is a requirement for survival of intelligent life in nature. Animals, in particular, have developed a great variety of manipulators to achieve life sustaining, interaction based tasks, such as hunting, nest building, and feeding. The morphology and rigidity of their manipulators varies according to their habitat and demonstrates evolution specific to the environment which they have to interact with (i.e., terrain, preys, mates, etc.). The softness and adaptability of many animals manipulators allow them to interact with the environment in a highly dynamic manner; however, this softness varies in many different ways for different animals. For example, as a member of the invertebrates, the octopus thrives in its habitat by utilizing its soft and long arms. With its ability to elongate, compress, and bend in multiple directions simultaneously, the octopus arm is the representative of soft manipulators in nature (Kier and Stella, 2007). Another example is the human hand; the rigid bone phalanges and the soft ligamentous joints contribute to the overall strength while also providing the necessary flexibility of the human fingers (Kapandji, 1987). With such a manipulator design humans are undoubtedly the most advanced animals, as their manipulator design evolved to allow the crafting of objects and construction of complex structures, from micro-machinery to large buildings.
The early work on robotics focused on the design of arms and manipulators which have been used in industrial applications for several decades (Nof, 1999). Due to the task definitions, these manipulator designs were required to achieve high precision, large force exertion, and low mechanical flexibility which was compensated with adaptive control strategies (Craig et al., 1986). Based on the knowledge and the expertise on rigid body dynamics and inverse kinematics, the initial examples of human inspired robotic hands also utilized rigid body links, fixed degree of freedom (DOF) joints, and low mechanical flexibility. Examples, such as the Utah/MIT Hand (Jacobsen et al., 1986), the Barrett Hand (Townsend, 2000), the Gifu Hand II (Kawasaki et al., 2002) and the DLR/HIT Hand II (Liu et al., 2008), are only few of the several manipulator designs which aim to demonstrate anthropomorphism constructed with rigid elements.
Changing from a machine-like approach, recently a more bio-inspired method has been suggested to build manipulators which behave like or consists of continuum soft materials. While the early examples still used rigid body links such as in Hirose’s soft arm (Hirose and Umetani, 1978), later examples started using soft materials and continuum bodies instead. Manipulators such as Ilievski’s and Cianchetti’s soft grippers (Ilievski et al., 2011; Manti et al., 2015), the Octopus Arm Project (Laschi et al., 2012a), and RBO Hand 2 (Deimel and Brock, 2015) are successful examples of soft manipulators which exercise large deformations and structural conformity due to their high DOF.
Soft robotics refers to robots which utilize materials and actuation methods which are soft, flexible, and compliant (Laschi and Cianchetti, 2014). Many examples of soft robotics take inspiration from biological organisms (bio-mimicry), which have similar properties of those required for soft robots (Kim et al., 2013). The development of soft robotics and the integration of soft materials are a significant change in the direction of robotics research. The integration of soft materials into robotics is driven by both new scientific paradigms and many applications including biomedical, service, and rescue robots (Iida and Laschi, 2011).
The key underlying principle of soft robotics is compliance which allows us to exploit the interaction of the robot with the environment. This “softness” provides adaptability and robustness which is seen in natural organisms, enabling tasks such as grasping and manipulation to be achieved with ease. Using such techniques and methods, soft materials may enable automation of tasks which are currently not possible using existing robotic technologies and solutions (Pfeifer et al., 2012). Such systems have the potential to interact more safely within a human unstructured environment and deal with uncertain and dynamic tasks. This could enable the grasping and manipulation of unknown objects in unstructured environments.
Soft robots developed to date demonstrate a variety of design choices, using highly varying actuation and control methods and displaying great creativity in design. Soft robotics has the potential to enable a radical technology change, which encompasses not only a shift in technologies but also approach. These innovative design principles and methodologies many enable a new generation of robots which can become a more integral part of the human environment (Albu-Schaffer et al., 2008).
In this paper, we will review the current state of the art for soft manipulators considering the material and fabrication processes, actuation and sensing methods, and morphology. The paper concludes with a discussion as to how soft manipulators may be used in the future.
The first RoboSoft Grand challenge was held in Livorno, Italy. The aim of which was to bring together research teams from around the world, to showcase the technologies and approaches for developing softer robots, deviating from the traditional rigid design principles seen in many robots. The challenge had two elements: manipulation and locomotion. The manipulation challenge required dexterous manipulators to be developed which could complete a number of tasks requiring both significant transfer of forces and loads and also highly delicate and fine manipulation; a dichotomy which is often hard to achieve in rigid robotic systems. The challenge required objects of varying sizes, ranging from smaller delicate ones to awkwardly shaped and heavy objects to be located, grasped and returned to a box. Second, the challenge required an arm to navigate through rigid cylinders and, finally, the manipulator must be capable of opening a door using a door handle. As such the challenge required the solution developed to show delicate and highly compliant behavior and also supply enough force. Many robots used a rigid arm combined with a soft manipulator, combining the structural stability of the former with the safe interactions of the latter. Figure 1 shows the manipulator challenge environment and a few of the manipulator solutions which were developed by the teams.
Figure 1. The RoboSoft Grand Challenge manipulator challenge, showing the challenge environment and also a number of the manipulator designs created for the challenge.
In this section, we introduce the main considerations behind the construction of soft manipulators, namely, the materials and fabrication methods used to create such robots, the actuation methods, morphology of manipulators, and finally the soft sensors which can be integrated into manipulators.
There is much variability in the design of a soft manipulator, as there is a continuous spectrum between soft and rigid manipulators. Finding the optimum point along this scale to achieve the desired functionality, and the associated materials and actuation methods is key to the success of the development of manipulators. There has been some initial investigation of this “hybrid” soft-rigid design space (Stokes et al., 2013); however, this has mainly focused on the development of locomotion robots.
Figure 2 is the overview of the manipulator design space according to the choice of materials used in the design. The four axes displaying precision, structural compliance, DOF, and force exertion do not represent a quantitative results but show design trade-offs and hence suggest design choice for specific tasks or environments.
Figure 2. The position of soft and rigid manipulators in the 2D design space. Four key parameters: precision, structural compliance, degrees of freedom (DOF), and force exertion define the manipulator design. The axes only show quantitative change. Human hands lie on the diagonal line (gray colored) of the whole design space which combines soft and hard materials.
Two possible pairings of these qualitative measures are possible. The first is precision and DOF: the greater the number of DOF the harder it can be to control and achieve high precision movements. Second, structural compliance and force exertion can be paired: the greater the force which can be exerted by the system the lower the structural compliance and hence the less compliance and adaptation to the environment the manipulator would show.
Continuum body manipulators made with soft materials exploit large deformation capacities; therefore, they inherit features such as a higher DOF and structural compliance. Although the precise control required for real-world applications might be challenging, the compliance offered by soft manipulators overcomes the need for high-computational power and precision.
The field of Soft Robotics is very broad, as such, in this review, we aim to cover the key areas of soft robotics manipulation, presenting a representative sample of relevant publications. Although the definition of soft robotics is not well defined, this review is limited to soft robotics methods, not those which create “softness” from rigid materials.
Soft robotics exploits the compliance and flexibility of materials to create manipulators which are highly adaptive and allow for safe interactions with objects and the environment. The choice of material and fabrication techniques used in the construction is therefore key to the development of soft manipulators. By removing the design principles and rules used for rigid robots soft robotics makes room for inspiration and creativity in the design and fabrication methods of such robots. Soft robotics also makes use of rapid and adaptable fabrication techniques allowing for a rapid design and test cycle, which is often necessary as it can be hard to model and fully predict their behavior.
Soft robots are composed primarily of materials with Young’s modulus comparable with those of soft biological materials, such as muscles, tendons, and skin, which can be typically considered to be around 1 GPa (Rus and Tolley, 2015). This includes materials such as silicone, rubber, or other elastomeric polymers which can be easily manufactured with varying form factors and material properties (Elango and Faudzi, 2015). Not only is deformability and “softness” achieved by using intrinsically soft materials but also by exploiting morphology and material properties (e.g., considering orientation, and interactions between materials).
Despite the many advantages of soft materials, their usage does present challenges in terms of the non-linear response, difficulty in modeling, requirement for self-repair, fatigue performance, and potential fabrication limits. New materials such as foams are being developed for soft robotic applications and have significant potential with innovative properties such as thermally tuneability and self-healing properties (Cheng et al., 2014).
One of the simplest methods for creating soft robotics is using materials casting or molding processes, in which molds, often 3D printed, are used to cast silicone- or elastomer-based structures (Marchese et al., 2015). This can lead to the creation of robots using a single casting process which eliminates any problems with bonding or joining materials of different properties (Cho et al., 2009). Manipulators created using this method include pneumatic operated manipulators (Ilievski et al., 2011; Homberg et al., 2015) as this method allows for easy integration of pneumatic chambers. Other methods of actuation can be used with fabrication, with tendon-driven locomotion robots also created using similar methods (Lin et al., 2011). This is an extremely rapid method of prototyping and a low cost development method but can lead to manipulators which are planar in structure. This method can also be used or combined with some of the other processes and techniques used in soft robotics.
SDM is a layered-manufacturing technology which allows the creation of 3D objects by building robots through cycles of depositing material, partial removal of material, further deposition, and the use of sacrificial and support material (Merz et al., 1994). This hybrid process of molding and machining away unwanted material allows solid, fully 3D parts composed of multiple materials of different properties to be manufactured (Cho et al., 2009). Sacrificial support material allows for the construction of complex and intricate geometries and allows for the inclusions of sensors, circuitry or actuators (Cham et al., 2002). A key advantage is that complex 3D geometries can be created with limited machinery an allows for internal inclusions of compliant mechanism, sensors and actuators, as demonstrated through robots such as iSprawl (Kim et al., 2006) and Stickybot (Kim et al., 2008). Such methods were used to create a gripper with articulated joints (Dollar and Howe, 2006), and other biomimetic robots, many of which take advantage of the ability to include sensors within the 3D structure (Dollar et al., 2006).
Photolithography is a process which has been used extensively in many scientific and engineering disciplines including MEMS design, sensor design and optoelectronics. A similar process, soft lithography, can be used with the same principle, however, using soft materials such as the elastomer poly(dimethylsiloxane) (PDMS) or other silicone rubbers. This is a process already widely used for applications such as microfluidics (Xia and Whitesides, 1998). In this process, patterned or relief surfaces are created using molds of standard photolithography techniques after which layers can be built up (Marchese et al., 2015). This allows the inclusion of channels for actuation and the addition of materials such as fiber, paper, or plastic field to provide some inextensibility, which may help facilitate actuation or movement of the robot. Due to the wide use of soft lithography in microfluidics, the technique and materials are widely understood.
Many soft fluidic elastomer robots are produced this way due to the ease with which channels can be created. Silicon elastomer robots using elastic actuation (Ilievski et al., 2011; Shepherd et al., 2011) and other methods such as explosion driven actuation (Shepherd et al., 2013) have been created using this technique. Due to layering process used in this method, this process limits the ability to produce truly 3D structures, with robots typically having a planar morphology, unable to achieve an amorphous 3D structure.
The ability to 3D print materials with softer, more elastic materials properties is a recent development and a key enabling technology the rapid development of soft robots. Techniques have now been developed to allow 3D printing of soft materials (Lipson and Kurman, 2013) and also soft actuators, such as dielectric elastomer actuators (Rossiter et al., 2009). Soft robots can be increasingly fully 3D printed (Umedachi et al., 2013) and can use a mix of materials of different properties to provide, for example, variable stiffness, flexibility, friction, or elasticity. It is now possible to entirely 3D print a soft robot, as demonstrated by the inching locomotion robot which uses variable friction legs and SMA actuation (Umedachi et al., 2013), and a combustion actuated variable stiffness jumping robot (Bartlett et al., 2015). Taking this concept one step forward, using 3D printing techniques an entirely soft, standalone robots including a “fuel” source and logic has been developed by embedding microfluidic systems and logic within the soft robot (Wehner et al., 2016). This uses embedded and omnidirectional 3D printing techniques (Wu et al., 2011; Muth et al., 2014). However, although 3D printing allows printing flexible materials in fully amorphous forms, these materials used in 3D printing are relatively brittle in comparison to molded rubbers and are therefore often not well suited to some actuation methods which require pressurization of the rubber.
Another 3D printing method which can be used to develop elastomeric soft robots is spray deposition. By spraying uncured silicone onto an existing surface 3D silicone shapes can be formed. Using this method, dielectric elastomer actuators can be developed (Araromi et al., 2011). Additionally, this method can be incorporated into a 4D system in which silicone can be deposited to form a multilayered tubular system by forming layers onto of an air-permeable shaft, and this allows the development of inflatable balloon-like structures (Coulter and Ianakiev, 2015).
The dynamics of soft grippers can be difficult to model due to the high number of degrees of freedom present and the non-linear material properties exhibited. Typical rigid body methods for modeling which assume rigid links between components can not longer be used (Verl et al., 2015). New techniques to model continuum structures are required.
Many methods which analyze soft body structures use constant curvature approximation (Camarillo et al., 2009). A steady-state model of continuous body system has been developed, although this negates the inclusion of actuators (Jones et al., 2009), as does a method which allows the force and torque acting on a robot to be estimated (Boyer et al., 2006). There are a number of methods for modeling tendon drive continuum robots, and these allow non-constantly curvature of manipulators to be estimated by considering the inherent torsion of the manipulator (Renda et al., 2012). Methods for modeling tendon-driven manipulators include Jacobian methods (Giorelli et al., 2013) and neural network approaches (Giorelli et al., 2013).
One method which can be used to model soft systems is Finite Element Modeling (FEM). By determining the physical constrains of the system and material properties, the behavior of a soft body can be simulated, for many cases, this has been demonstrated to be highly effective (Suzumori et al., 2007). It is also possible to use FEM methods real time for the control of soft elastomer robots (Duriez, 2013).
There are a limited set of simulators available for modeling the response of soft materials. Some simulators have been developed using non-linear relaxation for kinematic simulation, whereby the system is represented by a system of springs, beams, and masses (Lehman and Stanley, 2011; Cheney et al., 2013). This allows the correct physical simulation of large-scale deformations and dynamics of very soft materials and moves away from traditional non-linear finite element methods.
Additionally, soft matter physics engines have also been produced, such as Voxelyze, which can be used with VoxCAD. Using discrete elements, voxels, allows for efficient computation of the force of each constituent element, however, can be less accurate at predicting small scale deformations. A voxel-based, mass-spring lattices physics engines have also been created, which allow simulation of the dynamics of highly deformable heterogeneous materials (Hiller and Lipson, 2014). Approaches to develop models which are geometrically exact have also been developed, taking into account non-linearities and distributed weight and payload (Trivedi et al., 2008).
Soft robotic manipulators and hands need the ability to bend, stretch, and contract. The elastic and soft properties of the materials used require smart actuators which, unlike electric motors acting between two rigid links of a robotic manipulator, share the property of adaptability and deformability. Several actuation methods have been studied to this end in soft robotics, by either transmitting the force coming from rigid actuators via cables or pneumatic channels, or by building actuators that can be deformed such as shape memory alloys (SMA).
Bio-inspired artificial muscles driven by pressurized air have been around since the 1950s, where McKibben developed a stretchable tube surrounded by braided chords, which demonstrated the inherent property of contraction when being pressurized, and slacking when under ambient pressure. The striking analogy to animals’ muscles has inspired many scientists to study and use these actuators for robotic applications (Chou and Hannaford, 1996; Caldwell et al., 2000; Reynolds et al., 2003; Liu et al., 2014). McKibben muscles have also been used in segmented continuum robots to provide antagonistic artificial muscles for bending (Pritts and Rahn, 2004; Kang et al., 2013). The McKibben technique allows the elastic structure to contract instead of bend and expand; yet, sometimes bending and stretching motion is desirable. Soft elastic structures without braided chords promote these properties and have been studied and built for manipulation (Suzumori et al., 1992). Recent advances have shown that unbraided and channeled silicone molds can be used to actuate soft locomotion robots (Shepherd et al., 2011; Morin et al., 2012) and grasping robots (Ilievski et al., 2011; Martinez et al., 2013). The technique of channeled mold actuators are known under different names, such as fluidic elastomer actuators (FEA) (Marchese and Rus, 2015), PneuFlex actuators (Deimel and Brock, 2013, 2015), or Pneumatic Networks (Pneu-Nets) (Polygerinos et al., 2013; Mosadegh et al., 2014). The power source for the pneumatic actuation is usually obtained from a compressor but also on-board chemical pressure generation has been explored (Onal et al., 2011) and optimized in terms of valve efficiency (Marchese et al., 2011). Pneumatic actuation has been applied to a variety of bio-inspired robots, such as a robot fish (Marchese et al., 2014), a snake like robot (Onal and Rus, 2013), a manta ray robot (Suzumori et al., 2007), and even a robot partially actuated by internal combustion inside the mold channel for jumping (Tolley et al., 2014).
Many similarities are shared between pneumatic and hydraulic actuators. Both require an internal pressure to operate, either produced by a compressor, a pump or a lightweight device for portability. The operating principle is essentially the same, and a few pneumatic actuators can be easily converted into hydraulic actuators (McCarthy et al., 2014). The weight difference between pneumatic and hydraulic solutions is an important factor for its applications, and it can be explored for the right applications, such as underwater robotics (Marchese et al., 2015; Katzschmann et al., 2016).
It is important to note that this review does not approach traditional pneumatic and hydraulic actuators, as seen in industrial environments and used in heavier robots. Although we aim to be as comprehensive as possible, such actuator strategies are very well explored and are seldom observed in robots in physical contact with humans.
To fully minimize the inertia of the manipulator, the actuator force needs to be delivered from the source of actuation over the manipulators limbs to the point of target articulation. Critically, the method of force transfer must not limit the movement of manipulator or affect its stiffness. Additionally, the actuation system must generate a considerable amount of force at the actuated manipulator point. Cables can transfer a force from a distant actuator over the manipulator limbs, which enable the moment of inertia to be kept low (Camarillo et al., 2008). The cables can have very high tensile strength in their longitudinal axis but are highly flexible and bendable in other directions. Therefore, they can be guided over complex routes and easily conform to the manipulator structure, carrying forces only in longitudinal axis with no change in size. There must be some consideration for the inclusion of a rigid source of rotary or linear actuation to control the actuation of the tendons.
Many continuum robots make use of cable-driven actuation systems (Cieslak and Morecki, 1999; Gravagne and Walker, 2002; Hannan and Walker, 2003; McMahan et al., 2005; Camarillo et al., 2009). Continuum robots often have a continuous and compliant backbone with a large number of degrees of freedom, for which cables form a simple and straightforward solution for attachment and control (Walker, 2013). Cable-driven actuation has also been applied to replicate an octopus arm with silicone for reaching (Calisti et al., 2010; Wang et al., 2013) and locomotion (Calisti et al., 2011). In analogy to the pneumatically actuated fish robot (Marchese and Rus, 2015), a cable-driven fish robot has been developed (y Alvarado and Youcef-Toumi, 2006).
Tendons are being increasingly adopted for soft robotics, with a large number of manipulator designs choosing to use tendon actuation, including continuum body semi-rigid manipulators (Nguyen and Burgner-Kahrs, 2015) and octopus inspired robots (Calisti et al., 2012). However, the additional requirement for a source of actuation such as a motor or pneumatic actuator can make the systems bulky.
Shape Memory Alloys (SMAs) have the interesting property of being deformable and capable of returning to the initial shape when heated. This effect can be exploited for actuation, which is being done by programming an initial coil-like contracted shape into the alloy. The material can then be stretched and will exert a force upon heating which causes it to move back to the original coiling, and it is this force that can be used for actuation. These one-way SMAs have to be implemented in an antagonistic set-up to enable continuous operation (Kim et al., 2009). SMAs have been used in soft robotics to create inchworm-like locomotion (Koh and Cho, 2013; Umedachi et al., 2013), but there are also examples for peristaltic locomotion (Seok et al., 2010). Furthermore, the contractile property of SMAs was exploited in octopus like robots, where they were used to allow for contraction of the diameter of the octopus arm (Laschi et al., 2012b; Cianchetti et al., 2014b).
With an improvement in the achievable force that can be applied, there is significant potential for SMAs to be used to the actuation of cable-driven systems.
When an electric field is applied electroactive polymers (EAPs) the material deforms, allowing them to be used as actuators; they have the capability to undergo a significant amount of deformation while exerting significant forces (Kim and Tadokoro, 2007). They are used widely in artificial muscles as they are thought to have a close resemblance to biological muscles. They can be integrated into soft structures to produce soft actuators.
Dielectric elastomers are one example of electroactive polymers. By applying a voltage to the elastomer, due to the polarization of the material this induced a deformation (Suo, 2010). These can be used for highly soft actuators (Anderson et al., 2012) which have the advantages of impressive actuation strain and speed, low density, high compliance and silent operation. When laminated, dielectric elastomers can be formed into complex minimum-energy state structures allowing out of plane actuation and displaying self-organization behavior (Kofod et al., 2006). Soft grippers with integrated polymer actuators have been developed (Shintake et al., 2016) which makes use of both electroadhesion and electrostatic actuation to grasp deformable, fragile objects of any shape with a single control signal.
The ability to generate a form and force closure on objects is key for a manipulator achieving complex interactions (Yoshikawa, 1996). Form closure guarantees the immobilization of an object in the manipulator via geometric enclosure during grasping or picking, even if the adopted force is fully passive, and this Section approaches a few of these possibilities.
The universal gripper (Brown et al., 2010) surprised the robotic community by its impressive adaptability and compliance when picking up various objects through mainly form closure, in a semi-passive grasp. Alternatively, the industrial manipulators without deformable limb structures (Nof, 1999) can maintain a large scale of force closures, but cannot enclose objects which require compliance to create a form closure, i.e., non-deformable elements. Soft manipulators can be designed without actuation to passively explore the interaction with objects to manipulate the environment. Figure 3 shows an example of how a simple soft manipulator can be designed (Wang et al., 2014) in order to pick and place objects with the help of interaction forces (Brodbeck and Iida, 2012). The aim is to generate passive force and form closure with a simple design of articulated bendable limbs as shown in Figure 3A. While the main closure comes from the force generated by the elastic limbs, the gripper aims to take the form of the object by deforming around its surface. Hot melt adhesive (HMA) is used to realize the gripper design as shown in Figure 3B. By varying the amount of materials in the design, the limbs remained soft and bendable compared to the tips with rigid structures. The sequence in Figure 3B shows that soft limbs bend like beams while the tips maintain a contact with the object surface and the gripper is pushed against the object using a robot arm. The elastic limbs deform around the object and their elasticity generates a force closure and picks the object successfully. The object is released by pushing the object toward the ground which forces the limbs to deform and lose the contact with the object.
Figure 3. Simple design of the passive soft gripper allows the fingers to bend outwards when pushed against a rigid object which aims to exploit the elasticity of the articulated limb structure (A). A thermoplastic material is used to fabricate the simple design (B). A robotic arm pushes the gripper toward a rigid object to enclose it and the forces generated from the elastic fingers allow a successful closure.
Computational and actuator costs can be drastically reduced as material properties can be exploited to create articulated limbs and manipulate objects without any requirement for actuation. By using a material such as HMA the material properties and compliance of the limbs can be easily altered, allowing manipulators to be designed specifically for a given application.
Under the umbrella of robotics, a wide range of actuating methods exists, and there is no clear definition as to what a soft mechanism is. There are a number of mechanisms which are not soft as such, but behave as if they were soft, by either the addition of an elastic component (Pratt and Williamson, 1995) or by a feedback loop which senses the external forces and comply to this force at a very high frequency (Semini et al., 2008). The concept of emulating soft properties is not new and has been around for more than 30 years (Hogan, 1984), with a great deal of works in this area, and it stands as the last resort from traditional rigid robotics to reach a more friendly interaction with humans and with the environment. In this sense, this paper will not approach these methods, as the number of publications with truly deformable actuators precludes us from giving these methods, such as Impedance Control and Series Elastic Actuators, the space to faithfully depict their scientific significance.
Soft grippers have been designed with many varying morphologies, dependent on the application for which they are required and the design principles used in their development. There is a spectrum of morphologies with varying degrees of freedom. This spectrum can be thought of loosely affecting the qualitative measures of the degree of universality with which objects can be grasped and also the “in hand” abilities to manipulate objects (Figure 4).
Figure 4. Although a higher degree of freedom increases the universe of grasping possibilities, humans rely on the presence of links, and consequently a finite number of joints to manipulate objects.
At one end of the spectrum is the universal gripper morphology, which uses the principle of jamming to alter the stiffness and rigidity of the gripper (Brown et al., 2010) allowing objects to be gripped and released. This morphology allows many objects of varying mass, size, material, and shape to be grasped, which is a key strength of the morphology.
Considering bio-inspired muscular hydrostat type manipulators such as octopus arms or elephant trunks (Hannan and Walker, 2003), this is a morphology which still has a large number of degrees of freedom, but unlike the jamming gripper it usually has better defined joints and are arguably considered to have a finite number of degrees of freedom. This still allows for grasping of many objects, but the ability to manipulate in hand is still reduced. There is considerable work on the development on octopus inspired robotic manipulators (Grissom et al., 2006; Laschi et al., 2009; Calisti et al., 2012) as they have the potential to have highly dexterous movement, and many potential applications such as robotic surgery.
There are also “limb” based multi-finger soft manipulators, such as the MIT hand (Homberg et al., 2015), which introduce a finger-based morphology, drawing inspiration from human hands, and an example of such design can be found at Culha and Iida (2016). The large joint deformations of this design extend the range of motion and ultimately seek to replicate the high dexterity of manipulation which is seen in the human hand.
As discussed, the morphology of the manipulation greatly affects the performance of the device and achievable grasping. The available materials and design processes allow for significant variation in the morphology of a manipulator, and should be chosen to meet the specific application for which the manipulator is required.
The capacity of jamming and stiffening is a great morphological feature, as it constrains body parts into shapes that are advantageous to robot/environment interaction. A method to be taken into account is evacuating internal channels to cause stiffening of the material in order to reach the desired morphology. Indeed, the universal gripper (Brown et al., 2010) is exploiting the fact that small particles trapped inside a flexible material can become very hard and stiff if a vacuum is applied. The effect is called particle jamming and has been applied successfully to end effectors, as the universal gripper demonstrates with its adaptability to almost any shape when inflated, and locking to that shape when evacuated. Recently, the particle jamming technique was also applied to a manipulator for surgery in the stiff-flop module, together with a flexible fluidic actuator (Cianchetti et al., 2013, 2014a). A similar effect can be achieved with a pneumatic actuator where different layers within the actuator, called adjustable stiffness layers, and can be activated to produce a different final stiffness (Firouzeh et al., 2015).
Sensing for soft robotics is acknowledged as a significant current challenge (Kier and Stella, 2007; Iida and Laschi, 2011). Development of soft robotic sensors has the potential to significantly improve the control systems and assist with obtaining information from the environment. Soft sensing is focused on detecting deformations; this could be a small deformation required for obtaining tactile information or significantly larger deformations such as obtaining posture information. However, this is challenging as soft systems do not have a limited and carefully controlled number of DOF, so a single sensor cannot be used to correspond to a single DOF. Soft systems have the potential to have infinite degrees of freedom, and this means that there can no longer be a one-to-one pairing of sensor to DOF, and alternative methods and approaches must be developed. Existing methods of strain and deformation sensing, and their applications and potential limitations are now discussed.
Highly flexible strain sensors have been developed using ionic and liquid metals which have a resistance which varies with the strain applied. Typically, sensors can undergo strains up to 100% (Chossat et al., 2013), with some able to achieve 250% strain (Park et al., 2012) while displaying high accuracy and reliability (Park et al., 2010). The sensors are developed by producing 3D printed molds to form flexible polymers (typically PDMS) with embedded microchannels. A conductive liquid is injected into the microchannels such that the resistance of the liquid varies with strain applied to the sensor. Different sensors exist using this technology. A flexible “skin” sensor has been developed which allows pressure and strains to be identified independently (Park et al., 2012) by using multiple layers of sensor, and choosing a specific morphology. Soft multi-axis force sensors have been also developed (Vogt et al., 2013). These sensors require careful design of the ionic channels, and the morphology must be designed to measure a particular deformation or degree of freedom. Using these sensors, strain and pressure can not be uniquely identified and electrode attachment to the sensor can be technically challenging.
Flexible electronics allow pressure to be detected using highly flexible polymer transistors which use a PDMS substrate (Someya et al., 2004; Mannsfeld et al., 2010; Schwartz et al., 2013). Such flexible pressure-sensitive organic thin film transistors have a high sensitivity, low power consumption and have been demonstrated to have a high stability over time (Noguchi et al., 2006). There are also carbon-nanotube film-based flexible electronic sensors (Lipomi et al., 2011; Park et al., 2013), but there has been limited integration of these sensors into robotics systems. Flexible electronic sensors have applications for use in skin sensing, but the sensors can undergo only extremely limited strain, so their applications are mostly limited to pressure sensing. Current applications include mobile health monitoring and remote diagnostics in medicine.
A range of flexible piezoelectric sensors have been developed, including piezoelectric fine-wires which can demonstrate extremely high sensitivity to strains, but the range of strains which they can undergo is limited (Zhou et al., 2008; Liao et al., 2013). Other methods investigate embedding crystalline piezoelectric material into other materials such as a cellulose mesh (paper) which allows the sensor to undergo greater strains (Gullapalli et al., 2010). Flexible and soft piezoresistive sensors have also been developed some of which use MEMS tecnology (Liu et al., 2011).
Capacitive fiber sensors comprise four concentric, alternating layers of conductor and dielectric (Frutiger et al., 2015). These wearable sensors provide accurate and hysteresis-free strain measurements under both static and dynamic conditions. They are, however, difficult to integrate into existing systems, and allow little flexibility in varying the morphology. Carbon nanotube-based capacitive strain sensors which can detect strains up to 300% with excellent durability over many cycles of strain have also been developed (Cai et al., 2013).
There are a number of sensors which incorporate conductive particles such as carbon black, carbon fiber, or carbon nanotubes into a matrix of thermoplastic or other elastic material. Carbon black has been integrated into thermoplastics (Mattmann et al., 2008) and silicone materials to enable the production of conductive sensing materials. By contrast, the integration of carbon nanotubes has limited repeatability and sensitivity (Pham et al., 2008). Models for the conductivity of materials with the inclusion of conductive particles have been suggested (Luheng et al., 2009).
Due to the increasing usage and interest in wearable devices, there has been a recent research focus on textile strain sensors to detect posture, position and gait. Current sensing systems include thermoplastic thread used to detect upper body posture (Mattmann et al., 2007), thermoplastic integrated into a nylon fabric (Cochrane et al., 2007), a strain sensing polymer printed onto fabric (Calvert et al., 2008), and stretchable carbon nanotube strain sensors integrated into fabrics (Yamada et al., 2011). The strains measured by strain sensing technologies are significantly lower than measured ionic based strain sensors.
A camera to detect the deformations of the inner side of the soft fingertip has a particular texture which allows deformations to be identified with accuracy and sensitivity (Winstone et al., 2013). A tactile fingertip with a soft compliant outer surface has been developed which allows integration into existing robotic manipulators (Winstone et al., 2013). Although powerful for tactile sensing, this technique is not as well suited for larger scale deformations and requires the inclusion of a highly rigid camera close to the source of the deformation. Other alternative methods include using fiber optics and photo detectors to detect deformation due to the changing in transmission through the fiber, however, this requires the inclusion of a non-elastic fiber into the soft system (Park et al., 2007; Puangmali et al., 2008).
It is possible to use an external vision system to track the movement of a soft system, which could be used to determine some tactile system; however, this would require additional infrastructure and does not make use of the inherent compliance of the system which enables the soft interaction with the environment.
Although there are a number of approaches to soft sensing, there has been limited integration into fully soft, continuum style grippers. However, when implemented such adaptations present a considerable amount of success (Homberg et al., 2015). There are challenges for developing soft sensors which can undergo significant deformation and allow localized deformations to be determined with accuracy and precision. Additionally, there are physical implementation issues. Sensors should be developed such that their connection with electrodes or wires does not restrict the behavior of the soft system, and these sensors should be easy to fabricate and integrate in to soft systems.
Although there has been significant development of soft sensors, some of this is purely focusing on the development of sensing material or technique, with limited integration into robotics systems. In some cases, such as the Tactip (Winstone et al., 2013) entire tactile sensing units have been developed which can be added to existing systems. Alternatively, for other sensors such as conductive thermoplastic elastomer sensors, methods of retrofitting sensors onto existing structures and manipulators has been developed (Mattmann et al., 2008), this allows sensors to be added to soft manipulators opposed to designing the soft manipulators to include the sensors. For sensors such as the ionic resistive sensors (Park et al., 2012), research has mainly focused on the development and performance of the sensors, and the inclusion of sensors will require designs which incorporate the sensors.
By addressing the sensing challenges discussed above, this will allow easier physical integration of manipulators in addition to enabling increased control of manipulators, and extraction of tactile information from the gripper to detect information from the surrounding environments.
In this paper, the current state of soft manipulators has been considered. Soft robots will have significant applications in areas which require compliance and soft interactions, as currently seen in human and some industrial environments. However, their inherent lack of repeatability, precision, and lower grasping force can be seen as a limiting factor for their applications.
However, the deviation from the traditional rigid robotics methods demonstrated in soft robotics has a number of key advantages, which fit the needs for twenty-first century Robotics Applications. Soft robots demonstrate the compliance required for daily interaction in unstructured environments. There is increasing pressure to automate industrial and agricultural processes, requiring manipulators with a higher degree of compliance that can cope with uncertainty and allow for safe handling of delicate objects. Soft robotics offer these properties, as such having many applications the number of which will only will only increase as research and developments leads to increase speed and precision of such systems.
This review on soft manipulators highlights the advances in morphology, actuation, materials, and sensors for soft manipulators. There is a notably large range of approaches and methods, with all aiming to achieve the desired precision and strength through different mechanisms. As new technologies arise and push the boundaries of these four frontiers the perceived weaknesses of soft manipulators will be gradually overcome and the uptake of soft robotics will increase significantly. This trend has been present with newer products, such as Festo’s FinGripper and Soft Robotics Inc’s Adaptive Grippers.
In conclusion, this is still a widely unexplored research area, with scientific progress trailing behind the aspirations and requirements for such robotic solutions. A better understanding of soft manipulators is dependent on a stronger academic push in this direction. As the field progresses, there will be new challenges to be overcome to develop soft manipulators, but the current knowledge base of “hard” and “soft” manipulators will scaffold future achievements and lead to the development of innovative and effective solutions.
Conceived the format of the review: JH, UC, FGi, AR, and FI. Curated the existing bibliography: JH, UC, FGi, and AR. Contributed with figures/materials: JH, UC, FGi, and FGu. Contributed to the writing of the manuscript: JH, UC, FGi, and AR. Final proofreading and revision: JH, FGi, AR, and FI.
The authors declare that the research was conducted in the absence of any commercial or financial relationships that could be construed as a potential conflict of interest.
This work was enabled by funding provided by the RoboSoft Coordination Action project (FP7-ICT-2013-C project 619319) and also the EPSRC CDT in Sensor Technologies (Grant EP/L015889/1). Many thanks also to the organizers of the RoboSoft Grand Challenge in Livorno, Italy.
Albu-Schaffer, A., Eiberger, O., Grebenstein, M., Haddadin, S., Ott, C., Wimbock, T., et al. (2008). Soft robotics. IEEE Robot. Autom. Mag. 15, 20–30. doi: 10.1109/MRA.2008.927979
Anderson, I. A., Gisby, T. A., McKay, T. G., OBrien, B. M., and Calius, E. P. (2012). Multi-functional dielectric elastomer artificial muscles for soft and smart machines. J. Appl. Phys. 112, 041101. doi:10.1063/1.4740023
Araromi, O., Conn, A., Ling, C., Rossiter, J., Vaidyanathan, R., and Burgess, S. (2011). Spray deposited multilayered dielectric elastomer actuators. Sens. Actuators A Phys. 167, 459–467. doi:10.1016/j.sna.2011.03.004
Bartlett, N. W., Tolley, M. T., Overvelde, J. T., Weaver, J. C., Mosadegh, B., Bertoldi, K., et al. (2015). A 3D-printed, functionally graded soft robot powered by combustion. Science 349, 161–165. doi:10.1126/science.aab0129
Boyer, F., Porez, M., and Khalil, W. (2006). Macro-continuous computed torque algorithm for a three-dimensional eel-like robot. IEEE Trans. Robot. 22, 563–775. doi:10.1109/TRO.2006.875492
Brodbeck, L., and Iida, F. (2012). “Enhanced robotic body extension with modular units,” in IEEE/RSJ International Conference on Intelligent Robots and Systems (Vilamoura: IEEE), 1428–1433.
Brown, E., Rodenberg, N., Amend, J., Mozeika, A., Steltz, E., Zakin, M. R., et al. (2010). Universal robotic gripper based on the jamming of granular material. Proc. Natl. Acad. Sci. U.S.A. 107, 18809–18814. doi:10.1073/pnas.1003250107
Cai, L., Song, L., Luan, P., Zhang, Q., Zhang, N., Gao, Q., et al. (2013). Super-stretchable, transparent carbon nanotube-based capacitive strain sensors for human motion detection. Sci. Rep. 3, 3048. doi:10.1038/srep03048
Caldwell, D. G., Tsagarakis, N., and Medrano-Cerda, G. (2000). Bio-mimetic actuators: polymeric pseudo muscular actuators and pneumatic muscle actuators for biological emulation. Mechatronics 10, 499–530. doi:10.1016/S0957-4158(99)00071-9
Calisti, M., Arienti, A., Giannaccini, M. E., Follador, M., Giorelli, M., Cianchetti, M., et al. (2010). “Study and fabrication of bioinspired octopus arm mockups tested on a multipurpose platform,” in Biomedical Robotics and Biomechatronics (BioRob), 2010 3rd IEEE RAS and EMBS International Conference on (Tokyo: IEEE), 461–466.
Calisti, M., Arienti, A., Renda, F., Levy, G., Hochner, B., Mazzolai, B., et al. (2012). “Design and development of a soft robot with crawling and grasping capabilities,” in Robotics and Automation (ICRA), 2012 IEEE International Conference on (St. Paul, MN: IEEE), 4950–4955.
Calisti, M., Giorelli, M., Levy, G., Mazzolai, B., Hochner, B., Laschi, C., et al. (2011). An octopus-bioinspired solution to movement and manipulation for soft robots. Bioinspir. Biomim. 6, 036002. doi:10.1088/1748-3182/6/3/036002
Calvert, P., Duggal, D., Patra, P., Agrawal, A., and Sawhney, A. (2008). Conducting polymer and conducting composite strain sensors on textiles. Mol. Cryst. Liq. Cryst. 484, 291–657. doi:10.1080/15421400801904690
Camarillo, D. B., Carlson, C. R., and Salisbury, J. K. (2009). Configuration tracking for continuum manipulators with coupled tendon drive. IEEE Trans. Robot. 25, 798–808. doi:10.1109/TRO.2009.2022426
Camarillo, D. B., Milne, C. F., Carlson, C. R., Zinn, M. R., and Salisbury, J. K. (2008). Mechanics modeling of tendon-driven continuum manipulators. IEEE Trans. Robot. 24, 1262–1273. doi:10.1109/TRO.2008.2002311
Cham, J. G., Bailey, S. A., Clark, J. E., Full, R. J., and Cutkosky, M. R. (2002). Fast and robust: hexapedal robots via shape deposition manufacturing. Int. J. Robot. Res. 21, 869–882. doi:10.1177/0278364902021010837
Cheney, N., MacCurdy, R., Clune, J., and Lipson, H. (2013). “Unshackling evolution: evolving soft robots with multiple materials and a powerful generative encoding,” in Proceedings of the 15th Annual Conference on Genetic and Evolutionary Computation, GECCO ’13 (Amsterdam: ACM), 167–174.
Cheng, N. G., Gopinath, A., Wang, L., Iagnemma, K., and Hosoi, A. E. (2014). Thermally tunable, self-healing composites for soft robotic applications. Macromol. Mater. Eng. 299, 1279–1284. doi:10.1002/mame.201400017
Cho, K.-J., Koh, J.-S., Kim, S., Chu, W.-S., Hong, Y., and Ahn, S.-H. (2009). Review of manufacturing processes for soft biomimetic robots. Int. J. Precis. Eng. Manuf. 10, 171–181. doi:10.1007/s12541-009-0064-6
Chossat, J. B., Park, Y.-L., Wood, R. J., and Duchaine, V. (2013). A soft strain sensor based on ionic and metal liquids. IEEE Sens. J. 13, 3405–3414. doi:10.1109/JSEN.2013.2263797
Chou, C.-P., and Hannaford, B. (1996). Measurement and modeling of mckibben pneumatic artificial muscles. IEEE Trans. Robot. Autom. 12, 90–102. doi:10.1109/70.481753
Cianchetti, M., Licofonte, A., Follador, M., Rogai, F., and Laschi, C. (2014a). Bioinspired soft actuation system using shape memory alloys. Actuators 3, 226–244.
Cianchetti, M., Ranzani, T., Gerboni, G., Nanayakkara, T., Althoefer, K., Dasgupta, P., et al. (2014b). Soft robotics technologies to address shortcomings in today’s minimally invasive surgery: the stiff-flop approach. Soft Robot. 1, 122–131. doi:10.1089/soro.2014.0001
Cianchetti, M., Ranzani, T., Gerboni, G., Falco, I. D., Laschi, C., and Menciassi, A. (2013). “Stiff-flop surgical manipulator: mechanical design and experimental characterization of the single module,” in IEEE/RSJ International Conference on Intelligent Robots and Systems (Tokyo: IEEE/RSJ), 3576–3581.
Cieslak, R., and Morecki, A. (1999). Elephant trunk type elastic manipulator-a tool for bulk and liquid materials transportation. Robotica 17, 11–16. doi:10.1017/S0263574799001009
Cochrane, C., Koncar, V., Lewandowski, M., and Dufour, C. (2007). Design and development of a flexible strain sensor for textile structures based on a conductive polymer composite. Sensors 7, 473–492. doi:10.3390/s7040473
Coulter, F. B., and Ianakiev, A. (2015). 4D printing inflatable silicone structures. 3D Print. Addit. Manuf. 2, 140–144. doi:10.1089/3dp.2015.0017
Craig, J., Hsu, P., and Sastry, S. (1986). “Adaptive control of mechanical manipulators,” in Robotics and Automation. Proceedings. 1986 IEEE International Conference on (North Carolina, NC: IEEE), Vol. 3, 190–195.
Culha, U., and Iida, F. (2016). Enhancement of finger motion range with compliant anthropomorphic joint design. Bioinspir. Biomim. 11, 026001. doi:10.1088/1748-3190/11/2/026001
Deimel, R., and Brock, O. (2013). “A compliant hand based on a novel pneumatic actuator,” in Robotics and Automation (ICRA), 2013 IEEE International Conference on (Karlsruhe: IEEE), 2047–2053.
Deimel, R., and Brock, O. (2015). A novel type of compliant and underactuated robotic hand for dexterous grasping. Int. J. Robot. Res. 1–25. doi:10.1177/0278364915592961
Dollar, A. M., and Howe, R. D. (2006). A robust compliant grasper via shape deposition manufacturing. IEEE/ASME Trans. Mechatron. 11, 154–161. doi:10.1109/TMECH.2006.871090
Dollar, A. M., Wagner, C. R., and Howe, R. D. (2006). “Embedded sensors for biomimetic robotics via shape deposition manufacturing,” in The First IEEE/RAS-EMBS International Conference on Biomedical Robotics and Biomechatronics, 2006. BioRob 2006 (Pisa: IEEE), 763–768.
Duriez, C. (2013). “Control of elastic soft robots based on real-time finite element method,” in Robotics and Automation (ICRA), 2013 IEEE International Conference on (Karlsruhe: IEEE), 3982–3987.
Elango, N., and Faudzi, A. (2015). A review article: investigations on soft materials for soft robot manipulations. Int. J. Adv. Manuf. Technol. 80, 1027–1037. doi:10.1007/s00170-015-7085-3
Firouzeh, A., Salerno, M., and Paik, J. (2015). “Soft pneumatic actuator with adjustable stiffness layers for multi-dof actuation,” in Intelligent Robots and Systems (IROS), 2015 IEEE/RSJ International Conference on (Seattle, WA: IEEE), 1117–1124.
Frutiger, A., Muth, J. T., Vogt, D. M., Mengüç, Y., Campo, A., Valentine, A. D., et al. (2015). Capacitive soft strain sensors via multicore-shell fiber printing. Adv. Mater. Weinheim 27, 2440–2446. doi:10.1002/adma.201570105
Giorelli, M., Renda, F., Ferri, G., and Laschi, C. (2013). “A feed-forward neural network learning the inverse kinetics of a soft cable-driven manipulator moving in three-dimensional space,” in IEEE/RSJ International Conference on Intelligent Robots and Systems (Karlsruhe: IEEE), 5033–5039.
Gravagne, I. A., and Walker, I. D. (2002). “Uniform regulation of a multi-section continuum manipulator,” in Robotics and Automation, 2002. Proceedings. ICRA’02. IEEE International Conference on, Vol. 2 (Washington, DC: IEEE), 1519–1524.
Grissom, M. D., Chitrakaran, V., Dienno, D., Csencits, M., Pritts, M., Jones, B., et al. (2006). “Design and experimental testing of the octarm soft robot manipulator,” in Defense and Security Symposium (Florida, FL: International Society for Optics and Photonics), 62301F–62301F.
Gullapalli, H., Vemuru, V. S., Kumar, A., Botello-Mendez, A., Vajtai, R., Terrones, M., et al. (2010). Flexible piezoelectric ZnO-paper nanocomposite strain sensor. Small 6, 1641–1646. doi:10.1002/smll.201000254
Hannan, M. W., and Walker, I. D. (2003). Kinematics and the implementation of an elephant’s trunk manipulator and other continuum style robots. J. Robot. Syst. 20, 45–63. doi:10.1002/rob.10070
Hiller, J., and Lipson, H. (2014). Dynamic simulation of soft multimaterial 3D-printed objects. Soft Robot. 1, 88–101. doi:10.1089/soro.2013.0010
Hirose, S., and Umetani, Y. (1978). The development of soft gripper for the versatile robot hand. Mech. Mach. Theory 13, 351–359. doi:10.1016/0094-114X(78)90059-9
Hogan, N. (1984). “Impedance control: an approach to manipulation,” in American Control Conference 1984 (San Diego, CA: IEEE), 304–313.
Homberg, B. S., Katzschmann, R. K., Dogar, M. R., and Rus, D. (2015). “Haptic identification of objects using a modular soft robotic gripper,” in Intelligent Robots and Systems (IROS), 2015 IEEE/RSJ International Conference on (Hamburg: IEEE), 1698–1705.
Iida, F., and Laschi, C. (2011). Soft robotics: challenges and perspectives. Proc. Comput. Sci. 7, 99–102. doi:10.1016/j.procs.2011.12.030
Ilievski, F., Mazzeo, A. D., Shepherd, R. F., Chen, X., and Whitesides, G. M. (2011). Soft robotics for chemists. Angew. Chem. Int. Ed. 50, 1890–1895. doi:10.1002/anie.201006464
Jacobsen, S., Iversen, E., Knutti, D., Johnson, R., and Biggers, K. (1986). “Design of the Utah/M.I.T. dextrous hand,” in Robotics and Automation. Proceedings. 1986 IEEE International Conference on (San Francisco, CA: IEEE), Vol. 3, 1520–1532.
Jones, B. A., Gray, R. L., and Turlapati, K. (2009). “Three dimensional statics for continuum robotics,” in IEEE/RSJ International Conference on Intelligent Robots and Systems (St. Louis: IEEE), 2659–2664.
Kang, R., Branson, D. T., Zheng, T., Guglielmino, E., and Caldwell, D. G. (2013). Design, modeling and control of a pneumatically actuated manipulator inspired by biological continuum structures. Bioinspir. Biomim. 8, 036008. doi:10.1088/1748-3182/8/3/036008
Kapandji, I. A. (1987). The Physiology of the Joints: Lower Limb, Vol. 2. Edinburgh: Churchill Livingstone.
Katzschmann, R. K., Marchese, A. D., and Rus, D. (2016). “Hydraulic autonomous soft robotic fish for 3D swimming,” in Experimental Robotics (Tokyo: Springer), 405–420.
Kawasaki, H., Komatsu, T., and Uchiyama, K. (2002). Dexterous anthropomorphic robot hand with distributed tactile sensor: Gifu hand II. IEEE/ASME Trans. Mechatron. 7, 296–303. doi:10.1109/TMECH.2002.802720
Kier, W. M., and Stella, M. P. (2007). The arrangement and function of octopus arm musculature and connective tissue. J. Morphol. 268, 831–843. doi:10.1002/jmor.10548
Kim, K. J., and Tadokoro, S. (eds) (2007). “Electroactive polymers for robotic applications,” in Artificial Muscles and Sensors (London: Springer), 291.
Kim, S., Clark, J. E., and Cutkosky, M. R. (2006). iSprawl: design and tuning for high-speed autonomous open-loop running. Int. J. Robot. Res. 25, 903–912. doi:10.1177/0278364906069150
Kim, S., Hawkes, E., Choy, K., Joldaz, M., Foleyz, J., and Wood, R. (2009). “Micro artificial muscle fiber using niti spring for soft robotics,” in IEEE/RSJ International Conference on Intelligent Robots and Systems (Kobe: IEEE), 2228–2234.
Kim, S., Laschi, C., and Trimmer, B. (2013). Soft robotics: a bioinspired evolution in robotics. Trends Biotechnol. 31, 287–294. doi:10.1016/j.tibtech.2013.03.002
Kim, S., Spenko, M., Trujillo, S., Heyneman, B., Santos, D., and Cutkosky, M. R. (2008). Smooth vertical surface climbing with directional adhesion. IEEE Trans. Robot. 24, 65–74. doi:10.1109/TRO.2007.909786
Kofod, G., Paajanen, M., and Bauer, S. (2006). Self-organized minimum-energy structures for dielectric elastomer actuators. Applied Physics A 85, 141–143. doi:10.1007/s00339-006-3680-3
Koh, J.-S., and Cho, K.-J. (2013). Omega-shaped inchworm-inspired crawling robot with large-index-and-pitch (LIP) SMA spring actuators. IEEE/ASME Trans. Mechatron. 18, 419–429. doi:10.1109/TMECH.2012.2211033
Laschi, C., and Cianchetti, M. (2014). Soft robotics: new perspectives for robot bodyware and control. Front. Bioeng. Biotechnol. 2:3. doi:10.3389/fbioe.2014.00003
Laschi, C., Cianchetti, M., Mazzolai, B., Margheri, L., Follador, M., and Dario, P. (2012a). A bioinspired soft robotic gripper for adaptable and effective grasping. Adv. Robot. 26, 709–727. doi:10.1163/156855312X626343
Laschi, C., Cianchetti, M., Mazzolai, B., Margheri, L., Follador, M., and Dario, P. (2012b). Soft robot arm inspired by the octopus. Adv. Robot. 26, 709–727. doi:10.1163/156855312X626343
Laschi, C., Mazzolai, B., Mattoli, V., Cianchetti, M., and Dario, P. (2009). Design of a biomimetic robotic octopus arm. Bioinspir. Biom. 4, 015006. doi:10.1088/1748-3182/4/1/015006
Lehman, J., and Stanley, K. O. (2011). “Evolving a diversity of creatures through novelty search and local competition,” in Proceedings of the Genetic and Evolutionary Computation Conference, GECCO ’11 (Dublin: ACM).
Liao, Q., Mohr, M., Zhang, X., Zhang, Z., Zhang, Y., and Fecht, H.-J. (2013). Carbon fiber–zno nanowire hybrid structures for flexible and adaptable strain sensors. Nanoscale 5, 12350–12355. doi:10.1039/c3nr03536k
Lin, H.-T., Leisk, G. G., and Trimmer, B. (2011). Goqbot: a caterpillar-inspired soft-bodied rolling robot. Bioinspir. Biom. 6, 026007. doi:10.1088/1748-3182/6/2/026007
Lipomi, D. J., Vosgueritchian, M., Tee, B. C., Hellstrom, S. L., Lee, J. A., Fox, C. H., et al. (2011). Skin-like pressure and strain sensors based on transparent elastic films of carbon nanotubes. Nat. Nanotechnol. 6, 788–792. doi:10.1038/nnano.2011.184
Liu, H., Wu, K., Meusel, P., Seitz, N., Hirzinger, G., Jin, M. H., et al. (2008). “Multisensory five-finger dexterous hand: the DLR/HIT hand II,” in IEEE/RSJ International Conference on Intelligent Robots and Systems (Nice: IEEE), 3692–3697.
Liu, X., Mwangi, M., Li, X., O’Brien, M., and Whitesides, G. M. (2011). Paper-based piezoresistive mems sensors. Lab. Chip 11, 2189–2196. doi:10.1039/c1lc20161a
Liu, X., Rosendo, A., Shimizu, M., and Hosoda, K. (2014). “Improving hopping stability of a biped by muscular stretch reflex,” in IEEE-RAS International Conference on Humanoid Robots (Nice: IEEE), 658–663.
Luheng, W., Tianhuai, D., and Peng, W. (2009). Influence of carbon black concentration on piezoresistivity for carbon-black-filled silicone rubber composite. Carbon N. Y. 47, 3151–3157. doi:10.1016/j.carbon.2009.06.050
Mannsfeld, S. C., Tee, B. C., Stoltenberg, R. M., Chen, C. V. H., Barman, S., Muir, B. V., et al. (2010). Highly sensitive flexible pressure sensors with microstructured rubber dielectric layers. Nat. Mater. 9, 859–864. doi:10.1038/nmat2834
Manti, M., Hassan, T., Passetti, G., D’Elia, N., Lasachi, C., and Cianchetti, M. (2015). A bioinspired soft robotic gripper for adaptable and effective grasping. Soft Robot. 2, 107–116. doi:10.1089/soro.2015.0009
Marchese, A. D., Katzschmann, R. K., and Rus, D. (2015). A recipe for soft fluidic elastomer robots. Soft Robot. 2, 7–25. doi:10.1089/soro.2014.0022
Marchese, A. D., Onal, C. D., and Rus, D. (2011). “Soft robot actuators using energy-efficient valves controlled by electropermanent magnets,” in IEEE/RSJ International Conference on Intelligent Robots and Systems (San Francisco, CA: IEEE), 756–761.
Marchese, A. D., Onal, C. D., and Rus, D. (2014). Autonomous soft robotic fish capable of escape maneuvers using fluidic elastomer actuators. Soft Robot. 1, 75–87. doi:10.1089/soro.2013.0009
Marchese, A. D., and Rus, D. (2015). Design, kinematics, and control of a soft spatial fluidic elastomer manipulator. Int. J. Robot. Res. 35, 840–869. doi:10.1177/0278364915587925
Martinez, R. V., Branch, J. L., Fish, C. R., Jin, L., Shepherd, R. F., Nunes, R., et al. (2013). Robotic tentacles with three-dimensional mobility based on flexible elastomers. Adv. Mater. Weinheim 25, 205–212. doi:10.1002/adma.201203002
Mattmann, C., Amft, O., Harms, H., Troster, G., and Clemens, F. (2007). “Recognizing upper body postures using textile strain sensors,” in 11th IEEE International Symposium on Wearable Computers (Boston, MA: IEEE), 29–36.
Mattmann, C., Clemensand, F., and Tröster, G. (2008). Sensor for measuring strain in textile. Sensors 8, 3719–3732. doi:10.3390/s8063719
McCarthy, G., Effraimidis, D., Jennings, B., Corso, N., Onal, C. D., and Popovic, M. (2014). “Hydraulically actuated muscle (HAM) exo-musculature,” in Robot Makers: The Future of Digital Rapid Design and Fabrication of Robots” (RoMa) Workshop, California, CA.
McMahan, W., Jones, B. A., and Walker, I. D. (2005). “Design and implementation of a multi-section continuum robot: air-octor,” in IEEE/RSJ International Conference on Intelligent Robots and Systems (Barcelona: IEEE), 2578–2585.
Merz, R., Prinz, F., Ramaswami, K., Terk, M., and Weiss, L. (1994). Shape Deposition Manufacturing. Engineering Design Research Center, Carnegie Mellon Univ.
Morin, S. A., Shepherd, R. F., Kwok, S. W., Stokes, A. A., Nemiroski, A., and Whitesides, G. M. (2012). Camouflage and display for soft machines. Science 337, 828–832. doi:10.1126/science.1222149
Mosadegh, B., Polygerinos, P., Keplinger, C., Wennstedt, S., Shepherd, R. F., Gupta, U., et al. (2014). Pneumatic networks for soft robotics that actuate rapidly. Adv. Funct. Mater. 24, 2163–2170. doi:10.1002/adfm.201303288
Muth, J. T., Vogt, D. M., Truby, R. L., Mengüç, Y., Kolesky, D. B., Wood, R. J., et al. (2014). Embedded 3D printing of strain sensors within highly stretchable elastomers. Adv. Mater. Weinheim 26, 6307–6312. doi:10.1002/adma.201400334
Nguyen, T. D., and Burgner-Kahrs, J. (2015). “A tendon-driven continuum robot with extensible sections,” in Intelligent Robots and Systems (IROS), 2015 IEEE/RSJ International Conference on (Hamburg: IEEE), 2130–2135.
Noguchi, Y., Sekitani, T., and Someya, T. (2006). Organic-transistor-based flexible pressure sensors using ink-jet-printed electrodes and gate dielectric layers. Appl. Phys. Lett. 89, 3507. doi:10.1063/1.2416001
Onal, C. D., Chen, X., Whitesides, G. M., and Rus, D. (2011). “Soft mobile robots with on-board chemical pressure generation,” in International Symposium on Robotics Research (Flagstaff, AZ: Springer), 1–16.
Onal, C. D., and Rus, D. (2013). Autonomous undulatory serpentine locomotion utilizing body dynamics of a fluidic soft robot. Bioinspir. Biomim. 8, 026003. doi:10.1088/1748-3182/8/2/026003
Park, S., Vosguerichian, M., and Bao, Z. (2013). A review of fabrication and applications of carbon nanotube film-based flexible electronics. Nanoscale 5, 1727–1752. doi:10.1039/c3nr33560g
Park, Y., Chen, B.-R., and Wood, R. J. (2012). Design and fabrication of soft artificial skin using embedded microchannels and liquid conductors. IEEE Sens. J. 12, 2711–2718. doi:10.1109/JSEN.2012.2200790
Park, Y.-L., Chau, K., Black, R. J., and Cutkosky, M. R. (2007). “Force sensing robot fingers using embedded fiber Bragg grating sensors and shape deposition manufacturing,” in Proceedings 2007 IEEE International Conference on Robotics and Automation (Rome: IEEE), 1510–1516.
Park, Y.-L., Majidi, C., Kramer, R., Bérard, P., and Wood, R. J. (2010). Hyperelastic pressure sensing with a liquid-embedded elastomer. J. Micromech. Microeng. 20, 125029. doi:10.1088/0960-1317/20/12/125029
Pfeifer, R., Lungarella, M., and Iida, F. (2012). The challenges ahead for bio-inspired ‘soft’ robotics. Commun. ACM 55, 76–87. doi:10.1145/2366316.2366335
Pham, G. T., Park, Y.-B., Liang, Z., Zhang, C., and Wang, B. (2008). Processing and modeling of conductive thermoplastic/carbon nanotube films for strain sensing. Compos. B Eng. 39, 209–216. doi:10.1016/j.compositesb.2007.02.024
Polygerinos, P., Lyne, S., Wang, Z., Nicolini, L. F., Mosadegh, B., Whitesides, G. M., et al. (2013). “Towards a soft pneumatic glove for hand rehabilitation,” in IEEE/RSJ International Conference on Intelligent Robots and Systems (Karlsruhe: IEEE), 1512–1517.
Pratt, G. A., and Williamson, M. M. (1995). “Series elastic actuators,” in Intelligent Robots and Systems 95. ‘Human Robot Interaction and Cooperative Robots’, Proceedings. 1995 IEEE/RSJ International Conference on, Vol. 1 (IEEE), 399–406.
Pritts, M. B., and Rahn, C. D. (2004). “Design of an artificial muscle continuum robot,” in Robotics and Automation, 2004. Proceedings. ICRA’04. 2004 IEEE International Conference on, Vol. 5 (Barcelona: IEEE), 4742–4746.
Puangmali, P., Althoefer, K., Seneviratne, L. D., Murphy, D., and Dasgupta, P. (2008). State-of-the-art in force and tactile sensing for minimally invasive surgery. IEEE Sens. J. 8, 371–381. doi:10.1109/JSEN.2008.917481
Renda, F., Cianchetti, M., Giorelli, M., Arienti, A., and Laschi, C. (2012). A 3D steady-state model of a tendon-driven continuum soft manipulator inspired by the octopus arm. Bioinspir. Biomim. 7, 025006. doi:10.1088/1748-3182/7/2/025006
Reynolds, D., Repperger, D., Phillips, C., and Bandry, G. (2003). Modeling the dynamic characteristics of pneumatic muscle. Ann. Biomed. Eng. 31, 310–317. doi:10.1114/1.1554921
Rossiter, J., Walters, P., and Stoimenov, B. (2009). “Printing 3D dielectric elastomer actuators for soft robotics,” in SPIE Smart Structures and Materials+ Nondestructive Evaluation and Health Monitoring (San Diego, CA: International Society for Optics and Photonics), 72870H–72870H.
Rus, W., and Tolley, M. T. (2015). Design, fabrication and control of soft robots. Nature 521, 467–475. doi:10.1038/nature14543
Schwartz, G., Tee, B. C.-K., Mei, J., Appleton, A. L., Kim, D. H., Wang, H., et al. (2013). Flexible polymer transistors with high pressure sensitivity for application in electronic skin and health monitoring. Nat. Commun. 4, 1859. doi:10.1038/ncomms2832
Semini, C., Tsagarakis, N. G., Vanderborght, B., Yang, Y., and Caldwell, D. G. (2008). “Hyq-hydraulically actuated quadruped robot: hopping leg prototype,” in 2nd IEEE RAS & EMBS International Conference on Biomedical Robotics and Biomechatronics (Scottsdale: IEEE), 593–599.
Seok, S., Onal, C. D., Wood, R., Rus, D., and Kim, S. (2010). “Peristaltic locomotion with antagonistic actuators in soft robotics,” in Robotics and Automation (ICRA), 2010 IEEE International Conference on (Anchorage, AK: IEEE), 1228–1233.
Shepherd, R. F., Ilievski, F., Choi, W., Morin, S. A., Stokes, A. A., Mazzeo, A. D., et al. (2011). Multigait soft robot. Proc. Natl. Acad. Sci. U.S.A. 108, 20400–20403. doi:10.1073/pnas.1116564108
Shepherd, R. F., Stokes, A. A., Freake, J., Barber, J., Snyder, P. W., Mazzeo, A. D., et al. (2013). Using explosions to power a soft robot. Angew. Chem. Int. Ed. 52, 2892–2896. doi:10.1002/anie.201209540
Shintake, J., Rosset, S., Schubert, B., Floreano, D., and Shea, H. (2016). Versatile soft grippers with intrinsic electroadhesion based on multifunctional polymer actuators. Adv. Mater. Weinheim 28, 231–238. doi:10.1002/adma.201504264
Someya, T., Sekitani, T., Iba, S., Kato, Y., Kawaguchi, H., and Sakurai, T. (2004). A large-area, flexible pressure sensor matrix with organic field-effect transistors for artificial skin applications. Proc. Natl. Acad. Sci. U.S.A. 101, 9966–9970. doi:10.1073/pnas.0401918101
Stokes, A., Shepherd, R., Morin, S., Ilievski, F., and Whitesides, G. (2013). A hybrid combining hard and soft robots. Soft Robotics 1, 70–74. doi:10.1089/soro.2013.0002
Suo, Z. (2010). Theory of dielectric elastomers. Acta Mech. Solida Sinica 23, 549–578. doi:10.1016/S0894-9166(11)60004-9
Suzumori, K., Endo, S., Kanda, T., Kato, N., and Suzuki, H. (2007). “A bending pneumatic rubber actuator realizing soft-bodied manta swimming robot,” in Proceedings 2007 IEEE International Conference on Robotics and Automation (Rome: IEEE), 4975–4980.
Suzumori, K., Iikura, S., and Tanaka, H. (1992). Applying a flexible microactuator to robotic mechanisms. IEEE Control Syst. 12, 21–27. doi:10.1109/37.120448
Tolley, M. T., Shepherd, R. F., Karpelson, M., Bartlett, N. W., Galloway, K. C., Wehner, M., et al. (2014). “An untethered jumping soft robot,” in IEEE/RSJ International Conference on Intelligent Robots and Systems (Chicago, IL: IEEE), 561–566.
Townsend, W. (2000). The BarrettHand grasper-programmably flexible part handling and assembly. Ind. Robot. 27, 181–188. doi:10.1108/01439910010371597
Trivedi, D., Lotfi, A., and Rahn, C. D. (2008). Geometrically exact models for soft robotic manipulators. IEEE Trans. Robot. 24, 773–780. doi:10.1109/TRO.2008.924923
Umedachi, T., Vikas, V., and Trimmer, B. A. (2013). “Highly deformable 3-d printed soft robot generating inching and crawling locomotions with variable friction legs,” in IEEE/RSJ International Conference on Intelligent Robots and Systems (Tokyo: IEEE), 4590–4595.
Verl, A., Albu-Schäffer, A., Brock, O., and Raatz, A. (2015). Soft Robotics: Transferring Theory to Application. Springer.
Vogt, D. M., Park, Y.-L., and Wood, R. J. (2013). Design and characterization of a soft multi-axis force sensor using embedded microfluidic channels. IEEE Sens. J. 13, 4056–4064. doi:10.1109/JSEN.2013.2272320
Wang, H., Chen, W., Yu, X., Deng, T., Wang, X., and Pfeifer, R. (2013). “Visual servo control of cable-driven soft robotic manipulator,” in IEEE/RSJ International Conference on Intelligent Robots and Systems (Tokyo: IEEE), 57–62.
Wang, L., Brodbeck, L., and Iida, F. (2014). Mechanics and energetics in tool manufacture and use: a synthetic approach. J. R. Soc. Interfaces 11, 20140827. doi:10.1098/rsif.2014.0827
Wehner, M., Truby, R. L., Fitzgerald, D. J., Mosadegh, B., Whitesides, G. M., Lewis, J. A., et al. (2016). An integrated design and fabrication strategy for entirely soft, autonomous robots. Nature 536, 451–455. doi:10.1038/nature19100
Winstone, B., Griffiths, G., Pipe, T., Melhuish, C., and Rossiter, J. (2013). “Tactip-tactile fingertip device, texture analysis through optical tracking of skin features,” in Conference on Biomimetic and Biohybrid Systems (London: Springer), 323–334.
Wu, W., DeConinck, A., and Lewis, J. A. (2011). Omnidirectional printing of 3D microvascular networks. Adv. Mater. 23, H178–H183. doi:10.1002/adma.201190092
Xia, Y., and Whitesides, G. M. (1998). Soft lithography. Annu. Rev. Mater. Sci. 28, 153–184. doi:10.1146/annurev.matsci.28.1.153
y Alvarado, P. V., and Youcef-Toumi, K. (2006). Design of machines with compliant bodies for biomimetic locomotion in liquid environments. J Dyn. Syst. Meas. Control 128, 3–13. doi:10.1115/1.2168476
Yamada, T., Hayamizu, Y., Yamamoto, Y., Yomogida, Y., Izadi-Najafabadi, A., Futaba, D. N., et al. (2011). A stretchable carbon nanotube strain sensor for human-motion detection. Nat. Nanotechnol. 6, 296–301. doi:10.1038/nnano.2011.36
Yoshikawa, T. (1996). “Passive and active closures by constraining mechanisms,” in Robotics and Automation, 1996. Proceedings., 1996 IEEE International Conference on (Minneapolis, MN: IEEE), Vol. 2, 1477–1484.
Keywords: soft robotics, manipulation, RoboSoft Grand Challenge, gripper, bio inspiration
Citation: Hughes J, Culha U, Giardina F, Guenther F, Rosendo A and Iida F (2016) Soft Manipulators and Grippers: A Review. Front. Robot. AI 3:69. doi: 10.3389/frobt.2016.00069
Received: 01 August 2016; Accepted: 25 October 2016;
Published: 16 November 2016
Edited by:
Matteo Cianchetti, Sant’Anna School of Advanced Studies, ItalyReviewed by:
Cagdas Denizel Onal, Worcester Polytechnic Institute, USACopyright: © 2016 Hughes, Culha, Giardina, Guenther, Rosendo and Iida. This is an open-access article distributed under the terms of the Creative Commons Attribution License (CC BY). The use, distribution or reproduction in other forums is permitted, provided the original author(s) or licensor are credited and that the original publication in this journal is cited, in accordance with accepted academic practice. No use, distribution or reproduction is permitted which does not comply with these terms.
*Correspondence: Josie Hughes, amFlaDJAY2FtLmFjLnVr
Disclaimer: All claims expressed in this article are solely those of the authors and do not necessarily represent those of their affiliated organizations, or those of the publisher, the editors and the reviewers. Any product that may be evaluated in this article or claim that may be made by its manufacturer is not guaranteed or endorsed by the publisher.
Research integrity at Frontiers
Learn more about the work of our research integrity team to safeguard the quality of each article we publish.