- 1Department of ICT Integrated Ocean Smart Cities Engineering, Dong-A University, Busan, Republic of Korea
- 2Department of Architectural Engineering, Dankook University, Yongin, Republic of Korea
Introduction: Construction worker safety remains a major concern even as task automation increases. Although safety incentives have been introduced to encourage safety compliance, it is still difficult to accurately measure the effectiveness of these measures. A simple count of accident rates and lower numbers do not necessarily mean that workers are properly complying with safety regulations. To address this problem, this study proposes an image-based approach to monitor moment-by-moment worker safety behavior and evaluate the effects of different safety incentive scenarios.
Methods: By capturing workers’ safety behaviors using a model integrated with OpenPose and spatiotemporal graph convolutional network, this study evaluated the effects of safety-incentive scenarios on workers’ compliance with rules while on the job. The safety incentive scenarios in this study were designed as 1) varying the type (i.e., providing rewards and penalties) of incentives and 2) varying the frequency of feedback about ones’ own compliance status during tasks. The effects of the scenarios were compared to the average compliance rates of three safety regulations (i.e., personal protective equipment self-monitoring hazard avoidance, and arranging the safety hook) for each scenario.
Results: The results show that 1) rewarding a good-compliance is more effective when there is no feedback on compliance status, and 2) penalizing non-compliance is more effective when there are three feedbacks during the tasks.
Discussion: This study provides a more accurate assessment of safety incentives and their effectiveness by focusing on safe behaviors to promote safety compliance among construction workers.
Introduction
Worker safety in the construction industry should not be overstated, even though many tasks have recently been automated, and the number of workers on the site is gradually decreasing. Automated processes partially simplify the work process, and these efforts can lead to a reduction in accidents due to human error (1, 2). However, the number of fatal accidents among construction workers is still high (3–6). Although there are several causes of accidents at construction sites, most occur because workers violate minor safety rules (7–9). Previous studies have suggested several interventions that can motivate workers to comply with safety regulations in their tasks (10–14). Workers are offered incentives (i.e., financial or business benefits) for safe behavior if they comply with their safety regulations. Existing studies have validated the effects of policies by counting the frequency of accidents (15–17). Thus, the accident rate is considered as the result of violating safety regulations, and the decreasing accident rate can prove the positive effect of safety incentives. However, this approach cannot ensure that accidents are entirely prevented due to safety incentives. This implies the possibility of an overly optimistic assessment of incentive policies in cases where workers do not comply with safety standards despite the absence of accidents. For a more accurate assessment of safety incentives, it is necessary to evaluate whether such policies induce a behavior change (i.e., compliance with safety regulations) among workers, regardless of the accident rate.
However, measuring behavior change in the context of safety is challenging. To assess whether incentive measures are effective, one must observe whether the relevant measures lead to changes in worker behavior, such as workers being aware of and complying with safety regulations in their tasks. It is difficult to measure these behavioral changes, especially at subtle levels such as increased awareness (e.g., checking or avoiding the hazards). Many studies have confirmed the effectiveness of safety incentive policies, however, have explored them over a relatively long term, such as a few months. Though evaluating incentive programs on a long-term basis is a valid approach for capturing safety behavior, not only the effect of incentive but also the environmental factors of a worksite, safety climate, and group effect of workers can affect the evaluation results. It is required to investigate only focusing on an individual’s safety behavior and the effect of the safety incentive program on behavioral change.
To address these problems, the objective of this study is to capture the moment-by-moment safety behavior of workers under different safety incentive scenarios and evaluate the effects of the corresponding incentive policies. We used an image-based approach to observe workers’ momentary behaviors and their changes. Recently, several researchers (18–26) have developed an image-based approach to detect workers’ behavior using image data collected from construction sites within a certain timeframe. Considering that the human body can be recognized as a skeleton in an image, with sequential data, this study captures the safe behavior of workers using OpenPose and recognizes whether they perform their safe behavior correctly. We designed safety incentive scenarios that differ in the type of incentives [i.e., type (rewards/penalties) and the timing of compliance status]. During experiments with subjects experiencing different incentive scenarios, we evaluated the effects of each scenario by examining subjects’ compliance with safety regulations for each task. The results were compared to the subjects’ average compliance rates for the five incentive scenarios. This study makes a significant contribution of the literature because construction worker safety remains a major concern even as task automation increases. Though safety incentives have been introduced to encourage safety compliance, it is still difficult to accurately measure the effectiveness of these measures. The approach used in this study to determine worker compliance with safety regulations can easily capture momentary safe behaviors and improve existing incentive programs that typically focus on outcomes by focusing more on the safe behaviors themselves.
Related works
Effects of reward and penalty policies on worker safety behavior
Incentive policies in the workplace can improve workers’ task-related behaviors, especially by increasing labor productivity (27–29) and promoting safe behaviors (30–33). Safety incentive programs (SIP) have been introduced, especially in the construction and manufacturing industries, where worker safety is critical (12, 16). To motivate workers to comply with safety regulations without relaxing them, various types of incentive programs have been developed, including financial benefits and personnel appraisals (31, 34–36). Existing studies have confirmed that there is a positive effect on worker safety behavior and investigated which way of providing incentives has higher effects (37–40). Most of them (32, 37, 41, 42) find that financial benefits have larger effects than other types of compensation, even if the magnitude of the effect steadily decreases over time. In terms of how incentives are provided, related studies (34, 38, 43) have compared the influences of incentive and disincentive (i.e., penalty) schemes. The differences between the two were caused by the responses of the corresponding workers’ to positive rewards and negative punishments. According to prospect theory (44–46), a person tends to behave in a more risk-averse manner when their compliance behavior guarantees a reward. A counterargument (36, 47), is that an expected punishment encourages compliance with the rules due to fear of loss. Even when individual differences are taken into account, deterrents have a greater effect on worker compliance with safety regulations in most cases. For example, imposing a penalty may create the impression that workers do not want to incur a loss, and it raises alarms among workers.
Similarly, incentives and penalties may also be an important mechanism influencing incentives for safety behavior. Previous research (34, 36, 48, 49) has found that the severity, certainty, and speed of punishment are related to the effects of penalties on rule compliance in the context of information technology security and driving behavior. Empirical studies (34, 39, 40, 50) have also found that severity and certainty do not proportionally affect rates of rule compliance. Thus, incentive and penalty policies can be effective when attention and empirical learning are present where appropriate rewards and penalties occur.
There are two types of incentive policies for safety behavior: (1) Outcome-Based Safety Incentive Program (OBSIP), and (2) Behavior-Based Safety Incentive Program (BBSIP) (32, 51, 52). These two differ in whether the incentives are based on the outcome or the behavior itself. In the case of construction work, the behavior itself should be more critical than the outcome in evaluating worker compliance. For example, the absence of accidents does not necessarily guarantee compliance with safe behaviors on a construction site. It is rare that non-compliance with safe behavior turns out to be an accident directly, as in many cases, it results in a near miss with some luck (53–55). Therefore, it is critical to determine workers’ adherence to safe behaviors rather than outcomes, because the primary objective of encouraging workers to adhere to safe behavior is to fundamentally prevent accidents through their compliance.
To confirm the effectiveness of reward and punishment mechanisms in compliance with construction work safety rules in an actual working environment, it is necessary to define strategies that vary the intensity and frequency of rewards and punishments, and to measure the compliance rate according to each strategy. To this end, this study requires a model that can identify compliance with momentary safety behaviors that occur in a relatively short period of time (i.e., 1–3 s) and provide feedback to the corresponding workers on compliance results.
Determining worker compliance with safety regulations using sequential images
The safety behavior required during construction work typically consist of sets of continuous moment-by-moment actions. As an example of self-checking for personal protective equipment (PPE), behaviors include raising and lowering the workers’ arms of to tap their safety helmet in a specific sequence, even if the detailed action will vary for each individual. These safety regulations should be performed repeatedly in the short term between tasks or according to the random locations of hazards during workers’ working hours. To determine worker compliance with safe behavior and provide feedback, a monitoring method that can continuously track worker behavior is needed. The image-based human activity recognition approach has been widely used in construction (18, 19, 22, 56) and the performance of the approach has been radically improved for practical use. Recently, human activity or object recognition based on image data obtained from video recordings at a construction site has been used to verify worker safety (20, 24, 26, 56–58) and work progress (59–62).
Among the numerous deep-learning-based algorithms for recognizing objects from visual data, recent studies have used the spatiotemporal graph convolutional network (ST-GCN), which can recognize a series of actions as an activity (63, 64). By detecting the pose per frame based on the corresponding joints and skeletons through OpenPose (65, 66) and using this information as input, the ST-GCN detects the activity while considering the temporal sequence of multiple actions. This approach is widely used in the medical field (67–69) to compare a patient’s gait (e.g., Parkinson’s disease) with that of a healthy person, or to evaluate a patient’s gait over time to track the progression of a disease. Other cases include assessing posture during exercises, such as yoga, to self-detect incorrect postures using video-recordings (70, 71). Because this approach can consider the position of joints and skeleton in successive frames and the temporal sequence of poses simultaneously, it can measure the compliance or compliance level of the activity compared to the correct criterion of the moment-by-moment activities. In addition, it allows automatic verification of behavioral compliance regardless of the duration or frequency of the behaviors. Taking advantage of this, a previous study (20) implemented the identification of typical safety regulations in construction activities to determine whether workers properly comply with the corresponding regulations. The study found that this approach can maximize the efficiency of safety monitoring, which needs to capture multiple behaviors performed sporadically by multiple workers at different locations on a construction site. Based on reliable performance in the construction work environment (20), this approach can be used as a basis for providing feedback to workers or implementing safety incentives by measuring rate of safety compliance by individual workers.
Methodology
To motivate workers to comply with safety regulations at their workplaces, various safety incentives can be created. To evaluate the effectiveness of the incentives, we measured the change in compliance rate after the introduction of the corresponding incentive scenarios. Because the change in compliance rate can directly reflect a change in behavior, this study designed various safety incentive scenarios and compared the compliance rate of each scenario to evaluate the effects of the safety incentive measures. To measure the compliance rate of each subject, a model that could identify the compliance status of each safe behavior from the recorded video was used by incorporating the OpenPose and ST-GCN algorithms. Because numerous workers are simultaneously working on a construction site, monitoring their safe behaviors requires an automatic method to detect many behavior changes.
The OpenPose and ST-GCN algorithms can capture human activities from sequences of images by training the spatio-temporal relationships of joints across consecutive frames of images. The OpenPose provides the input images for the ST-GCN with interconnected lines (i.e., bones) and nodes (i.e., joints). Since this approach can recognize the temporal sequences among multiple images, it is capable of recognizing moment-by-moment behaviors. We used the ST-GCN algorithm developed in our previous work (20), modified (adjusting two hyperparameters) to determine safety compliance from sequential frames of the subjects’ activities, to quantitatively measure the effects of safety incentive scenarios. Figure 1 illustrates the research framework used in this study.
Research questions about the effects of incentives on safety behavior
The main experiment was conducted to test the influence of rewards and penalties on safety behavior. However, previous research has yielded conflicting results depending on the context (i.e., type and duration of work) in which the behaviors are performed. The purpose of this study is to determine the effect of the type of incentives provided to workers on safety behaviors that should be continuous and short term. According to the existing research on human behavior, an individual’s behavior can also be influenced by feedback about their own behavioral state (72–74). This study investigates the effect of providing feedback for improving the safety compliance of workers with varying frequencies of feedback. Three research questions were derived to investigate the effects of the types of incentive programs (i.e., reward and penalty) and the frequency of feedback to workers on safety compliance rates.
Question 1 (Q1) Which type of incentive program-reward or punishment-is more effective in achieving greater compliance with construction safety regulations for construction work?
Question 2 (Q2) Does reminding workers to comply with safety regulations have a greater effect on achieving compliance compared to the case without reminders?
Question 3 (Q3) When giving workers feedback on their compliance with safety regulations, which type of incentive program—reward or punishment—is more effective in achieving greater compliance?
To answer these research questions, we designed five different types of experimental safety incentives by varying the type of incentive and the frequency of feedback.
Experimental setting
We conducted experiments at a construction site to evaluate the different safety incentive scenarios we designed. We recruited 50 healthy construction workers with more than 1 year of work experience. We recorded their work processes using video cameras (iPhone 12) that were installed at each hazard location, as shown in Figure 2. The recorded videos were used to capture the compliance status of the participants and assessed by experts. Information on the participants can be found in Table 1.
Video recordings were used to determine the level of compliance of safe behaviors, validate the process by experts with expertise in safety regulations, and confirm the results. To determine compliance with safety regulations and measure behavioral change based on the moment-by-moment safety behavior of workers, we defined the experimental work cycle as relatively short-term (i.e., the average length of a work cycle: 1 ~ 2 min) which includes the essential movements and required safety regulations of the bricklaying tasks. In addition, we designed a controlled environment that reflected the essential characteristics of a construction site including noise and time pressure. To observe how workers complied with safety regulations according to the incentive scenarios, the subjects were asked to repeatedly lay three bricks on the scaffold. We asked the subjects to lay a total of 60 bricks like a wall in the work area, as shown in Figure 2. Thus, they laid three 3 bricks at once and repeated the task 20 times. To create the closest possible workspace environment, the participants had to complete the brickwork within 30 min (i.e., they were under a normal time pressure). Subjects were informed of each safety regulation that they were expected to follow during their tasks. As shown in Figure 2, the subjects started at the first location while checking their personal protective equipment (PPE) themselves (i.e., whether they were wearing their safety helmet and hook properly). Then they make a detour to the hazard installed on the floor. After passing the danger zone, they should properly attach their safety hooks to the scaffold before laying the bricks. For these three safety behaviors, detailed definitions were defined for the experiment. Table 2 shows the safety behaviors and the corresponding regulations that should be complied with by subjects.
Through this experimental design, we captured the behavioral changes that occur in moment-by-moment terms and compliance with safety regulations (51, 72, 75–77). The validity of experimental design as a safety behavioral intervention was limitedly confirmed for short-term levels of behavior under the consultation of experts with expertise in construction safety regulations (six safety engineers in construction companies).
Designing safety incentive scenarios
To answer the proposed research questions and conduct empirical studies on the effects of safety incentives, we designed five scenarios based on general knowledge about the effects of incentives on human behavior (36, 44–47, 78). Subjects performed three safe behaviors per task cycle at each location on the scaffold. In addition, participants were notified that they would receive monetary rewards or penalties depending on their rate of compliance with the safe behaviors, and that they should do their best to achieve perfect compliance.
We created two categories of incentive scenarios with different (1) types of incentives and (2) frequency of feedback on safety compliance by the workers themselves. To create different types of incentives, we designed reward and penalty incentive scenarios based on workers’ compliance with safety regulations. Based on existing studies (32, 37, 41, 42, 79) showing that financial benefits have greater effects than other types of incentives, we defined the content of rewards and penalties as immediate giving or taking of money depending on the compliance rate. In the case of rewards, subjects would start with a credit balance of zero and receive one dollar for each safety compliance. At the end of the experiment, participants received 10 dollars for their tasks if they completed them on time. In penalty cases, the subjects initially received 60 dollars (i.e., the allotted amount for perfect compliance) and had one dollar deducted for each failure to comply with safety regulations. Thus, all subjects who participated in the incentive scenarios received the same amount of money (i.e., 70 dollars), whether it was a reward or a penalty, if they complied perfectly and on time with all regulations during their tasks. To compare the effects of each incentive scenario, a baseline scenario was designed with no incentive intervention. The baseline scenario was that participants received 70 dollars if they completed their twenty tasks on time. To create some time pressure, we also told subjects that if they could not complete their task on time (i.e., within 30 min) they would be deducted five dollars. Thus, subjects had to comply with the safety regulations 60 times during their 20 cycles of the given tasks.
To vary the frequency of feedback on workers’ compliance with safety regulations, we defined two cases: (1) no feedback and (2) feedback provided three times during the 20 cycles of given tasks. When providing feedback to workers, we informed them of their past compliance rate and current account balance (i.e., reward and penalty outcomes). In the case of three-time feedback, we informed participants of their current compliance rate and account balance after the 5th, 10th, and 15th cycles. Table 3 summarizes the designed safety incentive scenarios.
Five scenarios were developed in which the methods used to create incentives varied. Scenario 1 (S1) was defined as a baseline scenario with no incentives or interventions. Scenario 2 (S2) included a reward without feedback and Scenario 3 (S3) included a penalty without feedback. Scenario 4 (S4) included a reward with three times feedback and Scenario 5 (S5) included a penalty with three-times feedback. The results of S1, S2, and S3 were compared to answer the first research question (Q1), which concerned the effects of different types of incentives on safe behavior. The results of the comparison between S2 and S4 or S3 and S5 can answer the second research question (Q2), which is related to the effects of the frequency of feedback about ones’ own compliance status on workers’ safety behaviors. The third question (Q3) was answered by comparing the results of S2 and S3 or S4 and S5.
Determining workers’ compliance with safe behaviors
As mentioned earlier, each of the 50 participants performed the experiment 20 times. Therefore, 1,000 video records were collected for each safety behavior. As there were three types of safety behaviors in the experiment, the total number of records collected was 3,000. Before classifying the datasets, we edited the videos to include only actions related to the safety regulations of the corresponding spot (i.e., removing scenes of walking from one spot to the next). The videos used in this study were analyzed in AVI format with a frame rate of 30 fps and a resolution of 532 × 300. The average duration of the videos and single activities for each subject were 14.7 s and 3.5 s, respectively. After collecting the data, six safety engineers rated whether the workers followed the safety regulations. Based on the definition of each safety behavior in Table 2, the engineers determined the compliance of each video. For example, the compliance of ‘self-checking for PPE’ was classified as ‘complied’ when all engineers can agree with the presence of activity by tapping the safety helmet and checking the safety belt located at the waist. Table 4 summarizes the results of the data provided by the six safety engineers.
In this study, we used the OpenPose and ST-GCN algorithms to determine subjects’ compliance with safety regulations. Based on the results of a previous study (20) that showed the feasible accuracy (i.e., 0.883 for average F1 score) of the ST-GCN algorithm in identifying the compliance of workers with safety regulations, this methods was also used in this study to automatically detect subjects’ compliance.
In the process of identifying subjects’ compliance, the joints and skeletons of each subject from the OpenPose model were used as inputs to the ST-GCN algorithm. The OpenPose model used in this study applies the Visual Geometry Group (VGG)-19 algorithm (80, 81) to create a feature map. After obtaining sets of sequential images with joint and skeletal information from OpenPose, the ST-GCN algorithm classifies compliance with safety regulations. To implement the ST-GCN algorithm, the sampling function (D) and hyperparameter (Γ) were determined based on an exploratory method with the highest average F-1 scores, D = 1 and Γ = 6. The framework and process of the ST-GCN algorithm developed in previous studies (20) are shown in Figure 1. To train the model and ensure performance, the collected datasets were split into training and testing datasets of 75% and 25%, respectively. The algorithm determines the compliance (i.e., binary classification) of the subjects with the safety regulations at three hazard points of each task cycle. Based on the feasibility of the algorithm established in previous work (20), this study also evaluates the performance of the algorithm under the conditions of this study (i.e., self-checking for PPE, avoiding the hazard, and attachment of a safety hook) by comparing its accuracy with the expert identification results. The performance of the algorithm was evaluated in terms of accuracy, precision, recall, and F1-score. To measure the effect of each incentive scenario, the algorithm calculates the compliance rate of each subject of each work cycle according to the following steps.
1. A worker is required to comply with three safety regulations, and the algorithm calculates the score as 1 if he/she complies with each regulation; otherwise being calculated as 0.
2. For each work cycle for a worker, the average compliance rate is calculated for the compliance of three regulations (i.e., the average compliance rate for a worker for each cycle ranges from 0 to 1).
3. To present the average compliance rate according to the work cycle, the average compliance rate of all workers for each work cycle is calculated for each scenario.
Results
Performance of the determination model
An integrated algorithm of OpenPose and ST-GCN was implemented to determine the appropriateness of the three types of safe behaviors. Figure 3 shows the confusion matrices for each safe behavior. We derived these matrices by comparing the results of the algorithm with the determination results of safety experts, which were applied as the ground truth. Table 5 lists the evaluation results for the proposed algorithm. The accuracy values for identifying the three types of behaviors were all greater than 0.8. The case of avoiding hazards showed relatively lower accuracy among the three cases due to false-negatives, such as avoiding the hazard by moving very little. The recall values were also greater than 0.8 and the precision values were greater than 0.9 for all three behaviors. The F1-score of all three behaviors was also greater than 0.85, demonstrating the feasibility of the algorithm in capturing workers’ non-compliance with safety regulations. As for the performance of the algorithm according to the type of behavior, attaching the safety hook showed the highest values for accuracy, recall, and F1-score. The performance scores showed high accuracy, recall, and F1-score in the order of ‘attaching the safety hook,’ ‘self-checking the PPE,’ and ‘avoiding the hazard.’ Despite the behavior of ‘avoiding the hazard’ being newly added in this study, these performance results are consistent with the results of our previous study (20) on the performance of the integrated algorithm of OpenPose and ST-GCN in capturing workers’ behaviors in the video data. Additionally, the approach of this study was evaluated in aspects of classification performance compared with another existing algorithm [Convolutional Neural Networks—Long Short-Term Memory (CNN-LSTM)] run on our experimental datasets in Table 6. The approach of this study shows higher accuracy than existing models in the performance of classification of moment-by-moment safety behaviors.
Compliance rate according to incentive scenarios
Based on the feasibility of using the algorithm to determine workers’ behavior for proper compliance, we calculated the workers’ compliance rate with safety regulations in our experiment. To quantitatively measure the effect of safety incentive scenarios on worker compliance with safety regulations, we compared the compliance rate of each scenario based on the results from the OpenPose and ST-GCN algorithms.
Based on Q1, Figure 4 depicts the average compliance rate of subjects who were provided with a reward or penalty, each with a comparison with the case of no incentives (Scenario 1). The average compliance value across the entire work cycle was slightly higher in scenario 2 (0.757) than in scenario 3 (0.711). The linear regression graph (LR) shows that providing a reward to the subjects (Scenario 2) resulted in a higher compliance rate trend than providing a penalty (Scenario 3) throughout the entire work cycle. The average compliance rate in both scenarios increased as the work cycle progressed. The linear slope in scenario 2 (α = 0.005, p = 0.013) was slightly greater than that in scenario 3 (α = 0.004, p = 0.160). Both increasing trends throughout the cycle show a higher effect than in Scenario 1, which is the case without safety incentives for the subjects. This implies that providing any safety incentives would have a positive effect on compliance rate improvement. Based on these results, providing a reward has a greater effect than providing a penalty for improving the compliance rate with safety regulations in our experiment.
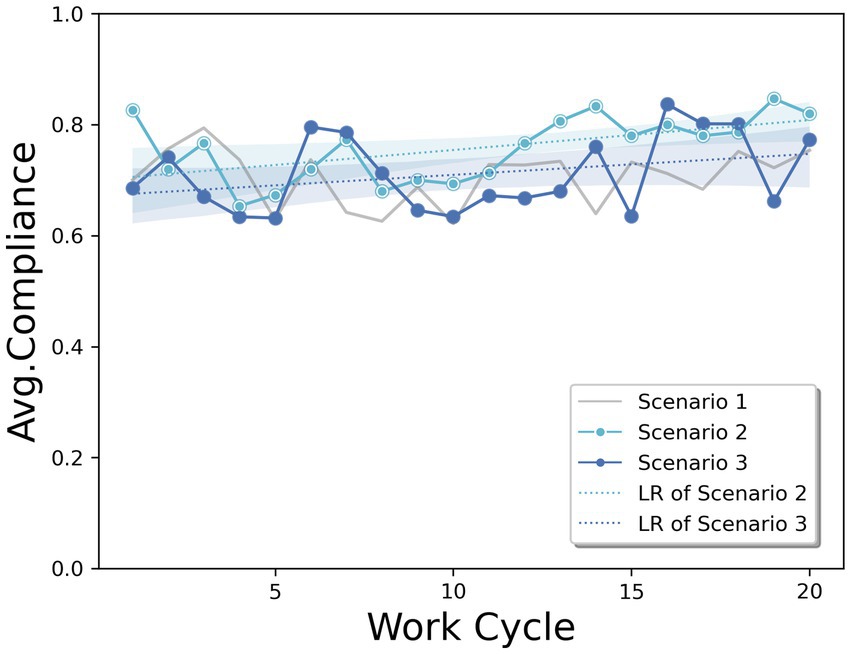
Figure 4. Average compliance rate trends representing the effects of rewards and penalties, including Linear Regression (LR).
Based on Q2, Figure 5 depicts the average compliance rate trends when providing feedback to the participants about their compliance rate. According to the two types of incentives, the average compliance rates are compared for each type; Figure 5A presents the comparison results of the no-feedback case (Scenario 2) and three feedback cases (Scenario 4) in a rewarding scenario. Figure 5B presents the comparison results of the two different feedback cases (Scenarios 3 and 5) in a penalty scenario. As expected, both the reward and penalty scenarios of providing feedback three times (S4:0.776, S5:0.808) showed a higher compliance rate than the no feedback cases (S2:0.757, S3:0.711). In particular, the average value of the compliance rates for both rewards and penalties shows a clear increase immediately after the feedback cycle (i.e., 5th, 10th, and 15th). Thus, direct feedback to workers regarding their compliance status can motivate them to improve their safety behaviors.
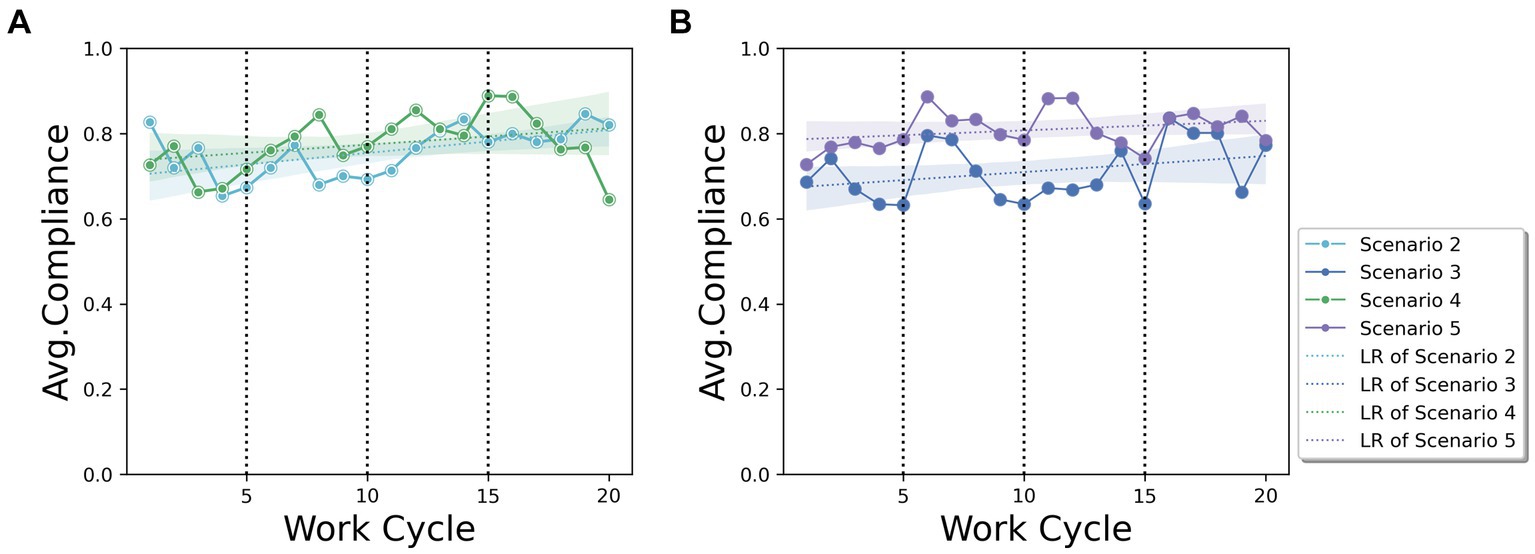
Figure 5. Average compliance rate trends representing the effect of feedback frequency with (A) reward and (B) penalty, including Linear Regression (LR).
Another finding was that the effect of feedback was more drastic in penalty scenarios than in reward scenarios. As shown in Figure 5A, the two scenarios of providing feedback show similar compliance rates, even though the overall trend of the average compliance rate of providing feedback is slightly higher. Figure 5B shows that providing feedback on the worker’s compliance rate increases the compliance rate compared to the no-feedback case in the penalty scenario. These results imply that the effect of providing feedback to workers of their own compliance on improving the compliance rate would be higher by providing them with a penalty for pointing out the non-compliance status rather than providing a reward. In addition to providing feedback with a penalty, the effect across time shows a different side of providing feedback in terms of rewards and penalties. Both scenarios show slightly increasing trends in compliance rates; however, there was little improvement in feedback with a penalty over the work cycle. This implies that repeated mention of penalties can be less effective than repeated mention of incentives in motivating workers to comply with regulations from a long-term perspective.
Based on Q3, Figure 6 shows the evolution of the average compliance rate in a reward and penalty scenario, with feedback given three times during the experiment in both cases. Similar to Figure 5, it can be seen that a penalty produces a higher compliance rate than a reward, in all feedback. This result is in contrast to the finding from Q1, which showed a greater effect of a reward without feedback. Thus, the effect of a reward and penalty scenario can be maximized to improve compliance rates depending on whether workers receive feedback on their own behavior. In our experimental setting, providing a penalty with feedback (Scenario 5) resulted in the highest compliance rate with safety regulations.
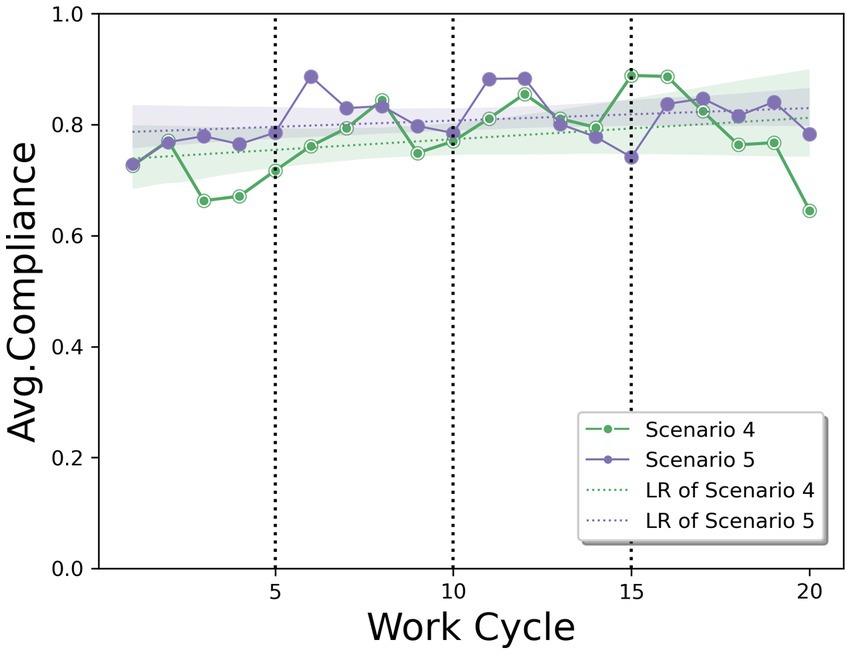
Figure 6. Average compliance rate trends representing the effects of rewards and penalties in the feedback situation, including Linear Regression (LR).
Moreover, the effect of improving the compliance rate across the work cycle was higher when a reward (α = 0.004, p = 0.152) was offered than a penalty (α = 0.002, p = 0.214). This trend is consistent with the findings in Figure 4, which shows scenarios without feedback. These results also support the idea that providing rewards may be more effective in motivating workers to comply with regulations in the long run.
Discussion
Implications for the effects of reward/penalty across work cycles
The results derived from Q1 indicate that rewarding workers is more effective than punishing them when there is no feedback on workers’ compliance. This result includes several aspects, with some previous results indicating that punishment was more effective than reward, although the average value of the compliance rate between a reward (S2:0.757) and a penalty (S3:0.711) is not significantly different. The linearly increasing trend of the compliance rate over the work cycle also showed a higher value for a reward (S2:0.005) than for a penalty (S3:0.004). This implies that a positive incentive is more effective within a relatively short period of time (i.e., 20 work cycles in this study) because it exerts less psychological pressure on workers to comply with safety regulations and complete their tasks on time. Subjects who participated in Scenarios 2 and 4 rarely mentioned non-compliance or the deadline after the experiment (5%); however, 35% of the subjects who participated in Scenarios 3 and 5 related their non-compliance and task failure with their perceived pressure.
In contrast, a penalty case is more effective when three feedback points are provided on the workers’ own compliance rate. Despite the psychological pressure that the participants perceived, a higher effect on the compliance rate was presented by being aware of the risk of non-compliance through feedback. Thus, the effect of safety incentive scenarios may change depending on whether workers perceive the penalties as psychological pressure that may lead to mistakes, or whether they are aware of the potential risks that may lead to strict compliance with regulations. These conflicting results leave room for further research on the effects of providing feedback on workers’ motivation behave safely.
Implications for the effects of feedback with reward/penalty in the extreme case
The results of our experiment (Q2), show that providing a punishment is more effective than providing a reward when we give workers feedback on their own compliance rate and their balance. To investigate the reasons for the differences between reward and punishment with feedback, we conducted an additional experiment of an extreme case in which feedback was given to the subjects. The 10 subjects who had participated in Scenario 1 performed the experiment, in which feedback was given in each work cycle. Figure 7 shows the evolution of the average compliance rate for reward and punishment in each feedback cycle. When participants received a reward, they showed a similar average compliance rate throughout the work cycle with a value of 0.932. In contrast, when a punishment was provided, there was a clear downward trend throughout the work cycle, which was particularly steep in the latter cycles, with a value of 0.784.
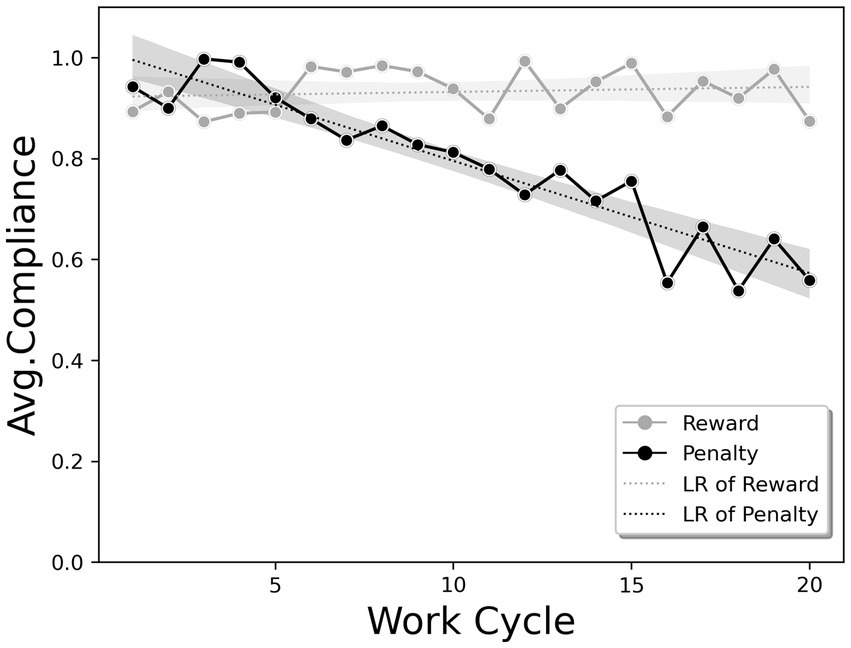
Figure 7. Average compliance rate trends for extreme intervention cases in the form of a reward or penalty, including Linear Regression (LR).
The difference between the two cases stems from the participants different responses to the constant feedback they received. In the reward case, the constant feedback did not elicit any particular response, whereas in the punishment case, some subjects felt a kind of psychological pressure when they were noticed for their non-compliance and the reward balance deducted. The constant feedback on task non-compliance led to a feeling of giving up rather than motivation to complete the task, and some subjects showed very low compliance rates in the latter cycles of the task. In an interview with these participants, they mentioned that the constant reminder of penalties for their non-compliance, especially at the beginning of the cycles, induced panic. These results were more apparent because of the experimental situations (i.e., not realistic, such as wage cuts in the workplace). Nevertheless, this implies that constantly reminding workers of the negative condition of punishment is not effective in motivating safe worker behavior. Moreover, responses to penalties showed greater individual variance across participants than responses to rewards.
Limitations and future applications
Because the decision of how to behave is directly related to the perception of the context associated with the corresponding behavior in question (82, 83), the way in which workers accept safety compliance incentives is critical to improving behavior. Awareness of the type or level of incentives may vary from person to person, and the effect of incentives may not show up consistently, even when a common incentive scenario is applied to a large number of workers. In addition, a particular safety incentive scenario, which was selected as the most effective scenario (Scenario 5), may only be effective in relatively short-term applications, such as the experimental conditions in this study. Therefore, each incentive scenario may have different effects in long-term applications, such as over several months. In the long term, workers could become desensitized to incentive scenarios, leading to a decrease in the effectiveness of the measures. A possible negative work climate is another limitation that was not fully investigated in this study. Depending on the level of reward and penalty, or the way feedback is delivered, the incentive scenario may cause side effects such as excessive tension during work or a culture of competition among workers (84–86), rather than having a positive effect on improving behavior.
Based on the results of this study, construction managers should consider the exact conditions for applying incentive scenarios, such as setting long-term and short-term perspectives according to the conditions of the actual work environment. A method of providing individualized feedback to each worker can also be considered while monitoring the compliance rate of individual workers in terms of their response to the appropriate incentive scenario. Considering the automated approach of this study (i.e., determining the compliance with safety regulations using sequential images), a system can be developed that provides individual feedback to workers in nearly real-time through PPEs (e.g., sensors in safety helmets or safety vests). The algorithm for providing personalized feedback can be defined according to the tendencies of compliance rate trends after feedback (i.e., providing penalty feedback for users who are more responsive to penalties when the compliance rate decreases by more than 10% compared to the previous feedback). This will make the safety incentive program more effective than existing ones, which cannot fully consider the various conditions of individuals, such as the degree of risk of the work, the working environment, and personal perception of incentives/penalties.
Conclusion
The objective of this study was to measure the effect of different types of safety incentives by comparing the average compliance rates of each scenario in experimental settings (i.e., laying bricks on the latter parts of the scaffold while complying with the three types of safety regulations). Using the OpenPose and ST-GCN algorithms, worker compliance rates were calculated in different scenarios with rewards and penalties, with and without feedback. The results showed that each safety incentive had a positive effect on compliance, with a reward having a greater effect than a penalty. The effect of feedback was more significant in the penalty scenarios than in the reward scenarios, and a penalty with feedback resulted in the highest compliance rate with safety regulations. The method used in this study to determine worker compliance with safety regulations can easily capture momentary safe behaviors through video recordings. Therefore, this image-based model can facilitate the design of the safety incentive scenario by focusing more on the safety behaviors themselves, which has improved existing incentive programs that typically focus on outcomes.
This study provides an accurate assessment of safety incentives and their effectiveness using an image-based approach to observe especially workers’ moment-to-moment behaviors and their changes extending the existing works. In aspects of methodologies, the ST-GCN-based algorithms to identify the compliance of workers with safety regulations enable assessing relatively short-momentary behaviors only considering the worker’s sequential poses. This contributes to developing an approach that can determine the finer level of behavioral change that occurs even at the unconscious level. Based on the results of this study, construction managers should consider the exact conditions for applying incentive scenarios, such as setting long-term and short-term perspectives according to the conditions of the actual work environment. A method of providing individualized feedback to each worker can also be considered while monitoring the compliance rate of individual workers in terms of their response to the appropriate incentive scenario.
A possible future study could focus on exploring the long-term effects of safety incentives by using an image-based model to capture workers’ safe behaviors and examine why workers may be more motivated by rewards than penalties in the long run.
Data availability statement
The raw data supporting the conclusions of this article will be made available by the authors, without undue reservation.
Ethics statement
The studies involving humans were approved by the Jieun Kim – Dankook University IRB. The studies were conducted in accordance with the local legislation and institutional requirements. The participants provided their written informed consent to participate in this study.
Author contributions
BL: Conceptualization, Data curation, Formal analysis, Funding acquisition, Investigation, Project administration, Validation, Visualization, Writing – original draft. HK: Conceptualization, Methodology, Resources, Supervision, Validation, Writing – review & editing.
Funding
The author(s) declare financial support was received for the research, authorship, and/or publication of this article. This research was supported by the Basic Science Research Program of the National Research Foundation of Korea (NRF), funded by the Ministry of Education (2021R1I1A1A01052305) and a grant (RS-2024-00143493) from Digital-Based Building Construction and Safety Supervision Technology Research Program funded by Ministry of Land, Infrastructure and Transport of Korean Government. The collection and analysis of the sensor data used in this study were approved by the Dankook University IRB (DKU 2020-09-027).
Conflict of interest
The authors declare that the research was conducted in the absence of any commercial or financial relationships that could be construed as a potential conflict of interest.
Publisher’s note
All claims expressed in this article are solely those of the authors and do not necessarily represent those of their affiliated organizations, or those of the publisher, the editors and the reviewers. Any product that may be evaluated in this article, or claim that may be made by its manufacturer, is not guaranteed or endorsed by the publisher.
References
1. Kamaruddin, SS, Mohammad, MF, and Mahbub, R. Barriers and impact of mechanisation and automation in construction to achieve better quality products. Procedia Soc Behav Sci. (2016) 222:111–20. doi: 10.1016/j.sbspro.2016.05.197
2. Li, RYM. An economic analysis on automated construction safety. Econ Analy Automated Constr Saf. (2018). doi: 10.1007/978-981-10-5771-7
3. Goh, YM, and Ali, MJA. A hybrid simulation approach for integrating safety behavior into construction planning: an earthmoving case study. Accid Anal Prev. (2016) 93:310–8. doi: 10.1016/j.aap.2015.09.015
4. Safety and Health Magazine. Rate of fatal injuries in construction up more than 10% between 2011 and 2020: CPWR report | 2022-05-19 | Safety+Health 2022. Available at: https://www.safetyandhealthmagazine.com/articles/22636-rate-of-fatal-injuries-in-construction-up-more-than-10-between-2011-and-2020-cpwr-report (Accessed March 24, 2023).
5. Trueblood, AB, Brown, S, and Harris, W. Fatal and nonfatal injuries in the construction industry. The Center for Construction Research and Training. (2022) Available at: https://www.cpwr.com/wp-content/uploads/DataBulletin-May2022.pdf
6. Xia, N, Xie, Q, Griffin, MA, Ye, G, and Yuan, J. Antecedents of safety behavior in construction: a literature review and an integrated conceptual framework. Accid Anal Prev. (2020) 148:105834. doi: 10.1016/j.aap.2020.105834
7. Abdelhamid, TS, and Everett, JG. Identifying root causes of construction accidents. J Constr Eng Manag. (2000) 126:52–60. doi: 10.1061/(ASCE)0733-9364(2000)126:1(52)
8. Guo, S, Xiong, C, and Gong, P. A real-time control approach based on intelligent video surveillance for violations by construction workers. J Civ Eng Manag. (2018) 24:67–78. doi: 10.3846/jcem.2018.301
9. Lee, B, and Kim, H. Measuring effects of safety-reminding interventions against risk habituation. Saf Sci. (2022) 154:105857. doi: 10.1016/j.ssci.2022.105857
10. Gangwar, M, and Goodrum, PM. The effect of time on safety incentive programs in the US construction industry. Constr Manag Econ. (2005) 23:851–9. doi: 10.1080/01446190500184527
11. Hasan, A, and Jha, KN. Safety incentive and penalty provisions in Indian construction projects and their impact on safety performance. Int J Inj Control Saf Promot. (2013) 20:3–12. doi: 10.1080/17457300.2011.648676
12. Hedlund, J. Risky business: safety regulations, risk compensation, and individual behavior. Inj Prev. (2000) 6:82–9. doi: 10.1136/ip.6.2.82
13. Hinze, J, Hallowell, M, and Baud, K. Construction-safety best practices and relationships to safety performance. J Constr Eng Manag. (2013) 139:04013006. doi: 10.1061/(ASCE)CO.1943-7862.0000751
14. Opfer, ND. Construction safety improvement through incentive compensation. AACE Int Trans. (1998):PR1.
17. Yeow, PH, and Goomas, DT. Outcome-and-behavior-based safety incentive program to reduce accidents: a case study of a fluid manufacturing plant. Saf Sci. (2014) 70:429–37. doi: 10.1016/j.ssci.2014.07.016
18. Fang, W, Love, PE, Luo, H, and Ding, L. Computer vision for behaviour-based safety in construction: a review and future directions. Adv Eng Inform. (2020) 43:100980. doi: 10.1016/j.aei.2019.100980
19. Fang, W, Ding, L, Luo, H, and Love, PE. Falls from heights: a computer vision-based approach for safety harness detection. Autom Constr. (2018) 91:53–61. doi: 10.1016/j.autcon.2018.02.018
20. Lee, B, Hong, S, and Kim, H. Determination of workers’ compliance to safety regulations using a spatio-temporal graph convolution network. Adv Eng Inform. (2023) 56:101942. doi: 10.1016/j.aei.2023.101942
21. Mneymneh, BE, Abbas, M, and Khoury, H. Vision-based framework for intelligent monitoring of hardhat wearing on construction sites. J Comput Civ Eng. (2019) 33:04018066. doi: 10.1061/(ASCE)CP.1943-5487.0000813
22. Saudi, MM, Hakim, A, Ahmad, A, Shakir, A, Hanafi, M, Narzullaev, A, et al. Image detection model for construction worker safety conditions using faster R-CNN. Int J Adv Comput Sci Appl. (2020) 11:246–50. doi: 10.14569/IJACSA.2020.0110632
23. Tang, S, and Golparvar-Fard, M. Machine learning-based risk analysis for construction worker safety from ubiquitous site photos and videos. J Comput Civ Eng. (2021) 35:04021020. doi: 10.1061/(ASCE)CP.1943-5487.0000979
24. Li, J, Miao, Q, Zou, Z, Gao, H, Zhang, L, Li, Z, et al. A review of computer vision-based monitoring approaches for construction workers’ work-related behaviors. IEEE Access. (2024). doi: 10.1109/ACCESS.2024.3350773
25. Al-Bayati, AJ, Rener, AT, Listello, MP, and Mohamed, M. PPE non-compliance among construction workers: an assessment of contributing factors utilizing fuzzy theory. J Saf Res. (2023) 85:242–53. doi: 10.1016/j.jsr.2023.02.008
26. Lee, D, Khan, N, and Park, C. Rigorous analysis of safety rules for vision intelligence-based monitoring at construction jobsites. Int J Constr Manag. (2023) 23:1768–78. doi: 10.1080/15623599.2021.2007453
27. Faisal Ahammad, M, Mook Lee, S, Malul, M, and Shoham, A. Behavioral ambidexterity: the impact of incentive schemes on productivity, motivation, and performance of employees in commercial banks. Hum Resour Manag. (2015) 54:S45–62. doi: 10.1002/hrm.21668
28. Guzzo, RA, Jette, RD, and Katzell, RA. The effects of psychologically based intervention programs on worker productivity: a meta-analysis. Pers Psychol. (1985) 38:275–91. doi: 10.1111/j.1744-6570.1985.tb00547.x
29. Weiss, A. Incentives and worker behavior: some evidence. National Bureau of Economic Research (1987).
30. Ahmed, I, and Faheem, A. How effectively safety incentives work? A randomized experimental investigation. Saf Health Work. (2021) 12:20–7. doi: 10.1016/j.shaw.2020.08.001
31. Ghasemi, F, Mohammadfam, I, Soltanian, AR, Mahmoudi, S, and Zarei, E. Surprising incentive: an instrument for promoting safety performance of construction employees. Saf Health Work. (2015) 6:227–32. doi: 10.1016/j.shaw.2015.02.006
32. Harianto, F, Anwar, N, Wiguna, I, and Suryani, E. Experiment the effect of providing monetary incentives and safety patrols on work safety behavior in construction project implementation. Proc Sec Int Conf Constr Infrastruct Mater. (2022) 216:449–57. doi: 10.1007/978-981-16-7949-0_40
33. Hasan, A, and Jha, KN. Acceptance of the incentive/disincentive contracting strategy in developing construction markets: empirical study from India. J Constr Eng Manag. (2016) 142:04015064. doi: 10.1061/(ASCE)CO.1943-7862.0001048
34. Herath, T, and Rao, HR. Encouraging information security behaviors in organizations: role of penalties, pressures and perceived effectiveness. Decis Support Syst. (2009) 47:154–65. doi: 10.1016/j.dss.2009.02.005
35. Rangel, T, Vassallo, JM, and Herraiz, I. The influence of economic incentives linked to road safety indicators on accidents: the case of toll concessions in Spain. Accid Anal Prev. (2013) 59:529–36. doi: 10.1016/j.aap.2013.07.014
36. Straub, DW Jr. Effective IS security: an empirical study. Inf Syst Res. (1990) 1:255–76. doi: 10.1287/isre.1.3.255
37. Ai Lin Teo, E, Yean Yng Ling, F, and Ong, DSY. Fostering safe work behaviour in workers at construction sites. Eng Constr Archit Manag. (2005) 12:410–22. doi: 10.1108/09699980510608848
38. Brandhorst, S, and Kluge, A. When the tension is rising: a simulation-based study on the effects of safety incentive programs and behavior-based safety management. Safety. (2021) 7:9. doi: 10.3390/safety7010009
39. Hollinger, RC, and Clark, JP. Deterrence in the workplace: perceived certainty, perceived severity, and employee theft. Soc Forces. (1983) 62:398–418. doi: 10.2307/2578314
40. Oliver, P. Rewards and punishments as selective incentives for collective action: theoretical investigations. Am J Sociol. (1980) 85:1356–75. doi: 10.1086/227168
41. Bronkhorst, B. Behaving safely under pressure: the effects of job demands, resources, and safety climate on employee physical and psychosocial safety behavior. J Saf Res. (2015) 55:63–72. doi: 10.1016/j.jsr.2015.09.002
42. Zhou, Q, Fang, D, and Wang, X. A method to identify strategies for the improvement of human safety behavior by considering safety climate and personal experience. Saf Sci. (2008) 46:1406–19. doi: 10.1016/j.ssci.2007.10.005
43. Zhu, J, Zhang, C, Wang, S, Yuan, J, and Li, Q. Evolutionary game analysis of construction workers’ unsafe behaviors based on incentive and punishment mechanisms. Front Psychol. (2022) 13:1067727. doi: 10.3389/fpsyg.2022.1067727
44. Kahneman, D, and Tversky, A. Prospect theory: an analysis of decision under risk. Handbook of the fundamentals of financial decision making: Part I. Singapore: World Scientific. (2013), p. 99–127.
45. von der Heyde, A, Brandhorst, S, and Kluge, A. The impact of safety audit timing and framing of the production outcomes on safety-related rule violations in a simulated production environment. Saf Sci. (2015) 77:205–13. doi: 10.1016/j.ssci.2015.03.021
46. von der Heyde, A, Brandhorst, S, and Kluge, A. Safety related rule violations investigated experimentally: one can only comply with rules one remembers and the higher the fine, the more likely the “soft violations.” Proceedings of the Human Factors and Ergonomics Society Annual Meeting, vol. 57, SAGE Publications Sage CA: Los Angeles, CA; (2013), p. 225–9.
47. Straub, DW Jr, and Nance, WD. Discovering and disciplining computer abuse in organizations: a field study. MIS Q. (1990) 14:45–60. doi: 10.2307/249307
48. Ahmed, SS, Pantangi, SS, Eker, U, Fountas, G, Still, SE, and Anastasopoulos, PC. Analysis of safety benefits and security concerns from the use of autonomous vehicles: a grouped random parameters bivariate probit approach with heterogeneity in means. Anal Methods Accid Res. (2020) 28:100134. doi: 10.1016/j.amar.2020.100134
49. Islam, M, Alnawmasi, N, and Mannering, F. Unobserved heterogeneity and temporal instability in the analysis of work-zone crash-injury severities. Anal Methods Accid Res. (2020) 28:100130. doi: 10.1016/j.amar.2020.100130
50. Stevenson, M, Harris, A, Wijnands, JS, and Mortimer, D. The effect of telematic based feedback and financial incentives on driving behaviour: a randomised trial. Accid Anal Prev. (2021) 159:106278. doi: 10.1016/j.aap.2021.106278
51. Choudhry, RM. Behavior-based safety on construction sites: a case study. Accid Anal Prev. (2014) 70:14–23. doi: 10.1016/j.aap.2014.03.007
52. Williams, JH, and Geller, ES. Behavior-based intervention for occupational safety: critical impact of social comparison feedback. J Saf Res. (2000) 31:135–42. doi: 10.1016/S0022-4375(00)00030-X
53. Zhang, M, Cao, T, and Zhao, X. Using smartphones to detect and identify construction workers’ near-miss falls based on ANN. J Constr Eng Manag. (2019) 145:04018120. doi: 10.1061/(ASCE)CO.1943-7862.0001582
54. Zhou, C, Chen, R, Jiang, S, Zhou, Y, Ding, L, Skibniewski, MJ, et al. Human dynamics in near-miss accidents resulting from unsafe behavior of construction workers. Phys A Stat Mech Appl. (2019) 530:121495. doi: 10.1016/j.physa.2019.121495
55. Zhou, Z, Li, C, Mi, C, and Qian, L. Exploring the potential use of near-miss information to improve construction safety performance. Sustain For. (2019) 11:1264. doi: 10.3390/su11051264
56. Nath, ND, and Behzadan, AH. Deep learning detection of personal protective equipment to maintain safety compliance on construction sites. Construction research congress 2020: computer applications. American Society of Civil Engineers: Reston, VA. 2020, p. 181–190.
57. Chen, S, and Demachi, K. Towards on-site hazards identification of improper use of personal protective equipment using deep learning-based geometric relationships and hierarchical scene graph. Autom Constr. (2021) 125:103619. doi: 10.1016/j.autcon.2021.103619
58. Wu, J, Cai, N, Chen, W, Wang, H, and Wang, G. Automatic detection of hardhats worn by construction personnel: a deep learning approach and benchmark dataset. Autom Constr. (2019) 106:102894. doi: 10.1016/j.autcon.2019.102894
59. Kim, H, Ahn, CR, Engelhaupt, D, and Lee, S. Application of dynamic time warping to the recognition of mixed equipment activities in cycle time measurement. Autom Constr. (2018) 87:225–34. doi: 10.1016/j.autcon.2017.12.014
60. Memarzadeh, M, Golparvar-Fard, M, and Niebles, JC. Automated 2D detection of construction equipment and workers from site video streams using histograms of oriented gradients and colors. Autom Constr. (2013) 32:24–37. doi: 10.1016/j.autcon.2012.12.002
61. Wong, TKM, Man, SS, and Chan, AHS. Critical factors for the use or non-use of personal protective equipment amongst construction workers. Saf Sci. (2020) 126:104663. doi: 10.1016/j.ssci.2020.104663
62. Chen, X, Wang, Y, Wang, J, Bouferguene, A, and Al-Hussein, M. Vision-based real-time process monitoring and problem feedback for productivity-oriented analysis in off-site construction. Autom Constr. (2024) 162:105389. doi: 10.1016/j.autcon.2024.105389
63. Cao, X, Kudo, W, Ito, C, Shuzo, M, and Maeda, E. Activity recognition using ST-GCN with 3D motion data. Adjunct Proceedings of the 2019 ACM International Joint Conference on Pervasive and Ubiquitous Computing and Proceedings of the 2019 ACM International Symposium on Wearable Computers, New York, NY. (2019), p. 689–692.
64. Yan, S, Xiong, Y, and Lin, D. Spatial temporal graph convolutional networks for skeleton-based action recognition. Thirty-second AAAI conference on artificial intelligence. Palo Alto, California USA: AAAI Press (2018).
65. Cao, Z, Simon, T, Wei, S-E, and Sheikh, Y. Realtime multi-person 2d pose estimation using part affinity fields. Proc IEEE Conf Comput Vis Pattern Recognit. (2017):7291–9. doi: 10.48550/arXiv.1611.08050
66. Qiao, S, Wang, Y, and Li, J. Real-time human gesture grading based on OpenPose. 2017 10th International Congress on Image and Signal Processing, BioMedical Engineering and Informatics (CISP-BMEI), New York, US: IEEE. (2017), p. 1–6.
67. Huang, Y-P, Chou, Y-J, and Lee, S-H. An OpenPose-based system for evaluating rehabilitation actions in Parkinson’s disease. 2022 International Automatic Control Conference (CACS), New York, US: IEEE; (2022), p. 1–6.
68. Sabo, A, Mehdizadeh, S, Iaboni, A, and Taati, B. Estimating parkinsonism severity in natural gait videos of older adults with dementia. IEEE J Biomed Health Inform. (2022) 26:2288–98. doi: 10.1109/JBHI.2022.3144917
69. Som, A, Krishnamurthi, N, Buman, M, and Turaga, P. Unsupervised pre-trained models from healthy ADLs improve Parkinson’s disease classification of gait patterns. 2020 42nd annual international conference of the IEEE engineering in medicine & biology society (EMBC). New York, US: IEEE; 2020, p. 784–788. (2020).
70. Lin, C-H, Shen, S-W, Anggraini, IT, Funabiki, N, and Fan, C-P. An OpenPose-based exercise and performance learning assistant design for self-practice yoga In: 2021 IEEE 10th global conference on consumer electronics (GCCE) New York, US: IEEE (2021). 456–7.
71. Shen, S-W, Huang, W-C, Anggraini, IT, Funabiki, N, and Fan, C-P. Exercise and performance learning assistant system for self-practice dynamic yoga by OpenPose and fuzzy based design In: 2022 10th international conference on information and education technology (ICIET) New York, US: IEEE (2022). 16–21.
72. Zhang, W, Shen, Q, Teso, S, Lepri, B, Passerini, A, Bison, I, et al. Putting human behavior predictability in context. EPJ Data Sci. (2021) 10:42. doi: 10.1140/epjds/s13688-021-00299-2
73. Wisniewski, B, Zierer, K, and Hattie, J. The power of feedback revisited: a meta-analysis of educational feedback research. Front Psychol. (2020) 10:487662. doi: 10.3389/fpsyg.2019.03087
74. Peifer, C, Schönfeld, P, Wolters, G, Aust, F, and Margraf, J. Well done! Effects of positive feedback on perceived self-efficacy, flow and performance in a mental arithmetic task. Front Psychol. (2020) 11:1008. doi: 10.3389/fpsyg.2020.01008
75. Bhandari, S, Hallowell, MR, and Correll, J. Making construction safety training interesting: a field-based quasi-experiment to test the relationship between emotional arousal and situational interest among adult learners. Saf Sci. (2019) 117:58–70. doi: 10.1016/j.ssci.2019.03.028
76. Van Der Molen, HF, Sluiter, JK, and Frings-Dresen, MH. Behavioural change phases of different stakeholders involved in the implementation process of ergonomics measures in bricklaying. Appl Ergon. (2005) 36:449–59. doi: 10.1016/j.apergo.2004.07.004
77. Mullan, B, Smith, L, Sainsbury, K, Allom, V, Paterson, H, and Lopez, A-L. Active behaviour change safety interventions in the construction industry: a systematic review. Saf Sci. (2015) 79:139–48. doi: 10.1016/j.ssci.2015.06.004
78. Matsuo, K, Sugihara, M, Yamazaki, M, Mimura, Y, Yang, J, Kanno, K, et al. Hierarchical Bayesian modeling to evaluate the impacts of intelligent speed adaptation considering individuals’ usual speeding tendencies: a correlated random parameters approach. Analy Methods Accid Res. (2020) 27:100125. doi: 10.1016/j.amar.2020.100125
79. Patel, MS, Asch, DA, Rosin, R, Small, DS, Bellamy, SL, Heuer, J, et al. Framing financial incentives to increase physical activity among overweight and obese adults. Ann Intern Med. (2016) 164:385–94. doi: 10.7326/M15-1635
80. Osokin, D. Real-time 2d multi-person pose estimation on cpu: lightweight openpose. arXiv Preprint arXiv. (2018) 181112004 2018
81. Simonyan, K, and Zisserman, A. Very deep convolutional networks for large-scale image recognition. arXiv Preprint arXiv. (2014) 14091556 2014
82. Pablo, AL, Sitkin, SB, and Jemison, DB. Acquisition decision-making processes: the central role of risk. J Manag. (1996) 22:723–46. doi: 10.1177/014920639602200503
83. Sitkin, SB, and Weingart, LR. Determinants of risky decision-making behavior: a test of the mediating role of risk perceptions and propensity. Acad Manag J. (1995) 38:1573–92. doi: 10.2307/256844
84. Bénabou, R, and Tirole, J. Incentives and prosocial behavior. Am Econ Rev. (2006) 96:1652–78. doi: 10.1257/aer.96.5.1652
85. Pruijssers, JL, Heugens, PP, and Van Oosterhout, J. Winning at a losing game? Side-effects of perceived tournament promotion incentives in audit firms. J Bus Ethics. (2020) 162:149–67. doi: 10.1007/s10551-018-3991-2
Keywords: construction safety incentive program, safety regulations, activity recognition, computer-vision, spatiotemporal graph convolutional network
Citation: Lee B and Kim H (2024) Evaluating the effects of safety incentives on worker safety behavior control through image-based activity classification. Front. Public Health. 12:1430697. doi: 10.3389/fpubh.2024.1430697
Edited by:
Chansik Park, Chung-Ang University, Republic of KoreaReviewed by:
Akeem Pedro, Chung-Ang University, Republic of KoreaRahat Hussain, Chung-Ang University, Republic of Korea
Copyright © 2024 Lee and Kim. This is an open-access article distributed under the terms of the Creative Commons Attribution License (CC BY). The use, distribution or reproduction in other forums is permitted, provided the original author(s) and the copyright owner(s) are credited and that the original publication in this journal is cited, in accordance with accepted academic practice. No use, distribution or reproduction is permitted which does not comply with these terms.
*Correspondence: Hyunsoo Kim, aGtpbTEzQGRhbmtvb2suYWMua3I=