- 1Student Research Committee, Department of Occupational Health and Safety at Work, School of Public Health and Safety, Shahid Beheshti University of Medical Sciences, Tehran, Iran
- 2Environmental and Occupational Hazards Control Research Center, School of Public Health and Safety, Shahid Beheshti University of Medical Sciences, Tehran, Iran
- 3Department of Textile Engineering, Amirkabir University of Technology, Functional Fibrous Structures and Environmental Enhancement (FFSEE), Amirkabir Nanotechnoloy Research Institute (ANTRI), Tehran, Iran
- 4Department of Health, Safety, and Environment (HSE), School of Public Health and Safety, Shahid Beheshti University of Medical Sciences, Tehran, Iran
- 5Workplace Health Promotion Research Center, Shahid Beheshti University of Medical Sciences, Tehran, Iran
- 6Department of Health and Safety at Work, School of Public Health and Safety, Shahid Beheshti Medical Sciences, Tehran, Iran
The main purpose of this study was to evaluate the ultraviolet protective factor (UPF) of fabrics coated with TiO2 nanoparticles made using an in-situ synthesis method and more accurately assess the intrinsic properties of the textile. The cotton-polyester twill fabric (70–30%) (246.67 g/m2) was coated in-situ with TiO2 nanoparticles. In-situ coating is conducted in 4 steps; washing the fabrics, preparation of nanoparticles, injecting the nanoparticles into fabrics, and drying the fabric after coating. The scanning electron microscope (SEM) and X-ray diffraction (XRD), FTIR spectrometer, dynamic light scattering (DLS) and UV-Vis spectrophotometer were used to analyse the data of the coating and UPF results. Also, four standards such as ASTM D737, ISIRI 8332, ISIRI 4199, and ISIRI 567 were used for analyzing the intrinsic properties of a textile. The results of SEM, XRD and DLS altogether confirmed the in-situ formation of nanoparticles onto textile fibers. Moreover, the UPF value of the uncoated and coated fabrics was 3.67 and 55.82, respectively. It was shown that the in-situ deposition of TiO2 nanoparticles on fabric can provide adequate protection against UVR. Also, the results of analyzing the intrinsic properties of the textile showed that there were no significant differences in the intrinsic properties between the coated and uncoated fabrics. Based on the results, it can be concluded that the UV protective properties of workwear fabrics can be improved by coating TiO2 nanoparticles on them without any effect on the cooling effect of perspiration evaporation.
Introduction
The incidence of skin cancer has been rising at an alarming rate over the past few decades due to overexposure to ultraviolet radiation (1). As a result, UV-induced skin damage has become an urgent health challenge (2–4). Accordingly, different strategies have been introduced to protect the skin against ultraviolet radiation which include using sunscreen, avoiding the sun at its highest intensities, and wearing clothing that effectively covers the skin surface. Outdoor workers such as farm workers, mine workers, bricklayers, construction workers, etc., are exposed to UV radiation, more frequently and for longer periods than people working indoors. The clothing worn by them is considered the most important personal protective equipment, preventing cuts and lacerations as well as contact with chemicals. Their clothing can protect their body from radiant heat and harmful rays (2, 4). Also, welders, furnace operators (steel industry and foundries), and even laboratory technicians (for UV disinfection) are exposed to ultraviolet light (5, 6). Wearing protective clothing is the cheapest and easiest way to limit UV exposure. However, intrinsic properties of textiles such as physical structure and chemical composition, low absorption, and UV–induced vulnerability of textiles can affect their UV-blocking properties. Therefore, the UV-blocking properties of the textile should be optimized. In other words, improvement of the Ultraviolet Protection Factor (UPF) is required to change the physical and chemical properties of textiles (7).
Fabrics generally have a UPF rating of 15–50, allowing only 2.5% of the sun's UV rays to pass through and any fabric that allows <2 percent UV transmission is labeled UPF 50+. Researchers have used different coatings as UV protectors for producing textile fibers. Chemical additives used as UV protectors can become toxic and degraded by sunlight (8, 9). Moreover, the preparation of these protectors often involves several steps as well as the use of hazardous chemicals. Hence, advanced protective coatings should be prepared and modified (10). Given that the properties imparted to textiles using conventional methods often do not have permanent effects and loss of function may occur after repeated washing, while the modifications made to the textile structure using nanotechnology and nanofibers are more stable and can improve the durability of textiles, the use of nanotechnology in the textile industry is increasingly attracting worldwide attention due to the existing interests (11). Nanomaterials such as metal oxide nanoparticles can impart UV blocking properties to textiles (12).
Loading the nanoparticles with UV blocking properties onto nanofibers can have a significant effect on the UV blocking properties of the textile. Nanoparticles are more efficient in blocking UV light than larger particles. Metal oxide nanoparticles such as titanium dioxide (TiO2), zinc oxide, selenium dioxide, and aluminum dioxide have been used for this purpose, among which nano-TiO2 is one of the best choices due to its cost-effectiveness, and simplicity, low toxicity, and high surface energy (13). Studies have shown that titanium provides UV protection via an absorption mechanism (14). For instance, Attia et al. (15) coated cotton/polyester (65/35%) fabric with TiO2 and ZnO nanoparticles (20 nm), and the results showed that UPF in treated fabrics was significantly enhanced and achieved more than six fold. Also, Hasan et al. coated aramid fabrics with silver nanoparticles to assess the antibacterial effects of nanoparticles. Results revealed that the fabrics have demonstrated excellent antibacterial action with more than 99% bacterial reduction efficiency against both Escherichia coli (E. coli) and Staphylococcus aureus (S. aureus) (16). At the end, Mondal showed in a review article that several nanomaterials such as ZnO, TiO2, and Carbon nanotube were used in several studies. Also, cotton fabrics were the most used materials to study UPF (17).
Given the vast numbers of outdoor workers and their prolonged exposure to the sun, designing UV-protective textiles is essential since the intrinsic properties of textiles such as physical structure and chemical composition, low absorption, and UV– induced vulnerability of textiles can affect their UV-blocking properties. Therefore, the present study aimed to evaluate the UPF of fabrics coated with TiO2 nanoparticles made using an in-situ synthesis method and more accurately assess the intrinsic properties of the textile (such as air permeability, abrasion resistance, wrap resistance and surface wetting resistance).
Materials and methods
Chemical substances and fabric properties
Chemical substances including Titanium isopropoxide (TTIP) (284.22 g/mol, C12H28O4Ti) (Merck No. 821895), ethanol 99.99%, and sodium hydroxide were purchased from Shimi Parsian Co Tehran, Iran. Also, the cotton-polyester twill fabric (blend ratio: 70/30%) (246.67 g/m2) was provided by Yazd Baf Co, Yazd, Iran. To remove the interference effects of dying on the UPF value, the fabric was purchased from the factory before being dyed. The cotton-polyester twill fabric was used since it is the most common workwear fabric in Iran.
Synthesis of TiO2 nanoparticles on the fabric
TiO2 nanoparticles were In-situ synthesized on cotton fabrics as described as the fabric samples in cuts of 4 × 4 cm were washed with ethanol inside a shaker and then again rinsed in distilled water and dried in an oven at 80°C. Next, a 4.2 mol/L NaOH solution was used for nanoparticle preparation, and the mixture was then subjected to ultrasonic cleaning in an ultrasonic bath (PARSONIC 2600s, Ac 220v/50 Hz) for 15 min. Also, 1 ml of pure ethanol and 4.5 ml of TTIP, and 1 ml of pure ethanol were withdrawn with a 10 ml syringe, respectively. The solution inside the syringe was then added dropwise to the solution containing the fabric in the ultrasonic bath and subjected to the ultrasonic cleaning for 5 h. The fabric samples were then washed three times in distilled water and dried in an oven at 80°C for 2 h.
Structural properties
The morphological structure of the textiles was investigated using a scanning electron microscope (SEM) and energy-dispersive X-ray spectroscopy system (EXD) (XL30, supplied by Philips Healthcare, the Netherlands) and a Philips PW-1510 diffractometer (PW 1510) before and after direct in-situ modification of cotton fabric using TiO2 nanoparticles. The samples were placed on the SEM stub and coated with gold. Image Analysis Software was used after x-ray diffraction imaging, morphological analysis, and particle size analysis. An FTIR spectrometer (Tensor 27, Bruker, Ettlingen, Germany) was used to analyze the chemical composition of synthesized TiO2 nanoparticles and the amount of metal loaded, and a dynamic light scattering analyzer (Microtrac MRB's NANOTRAC Wave, USA) was used to analyze TiO2 nanoparticle size. The energy-dispersive X-ray spectroscopy system, attached to the same microscope, was also used for elemental analysis. The structure of the In-situ-modified fabric samples was identified via X-ray diffraction (XRD) analysis at room temperature using an X-ray diffractometer (Panalytical X'PERT PRO) with a Cu Kα anode operating at 40 kV and 50 mA and λ = 1.5406). Diffraction data were collected over the 2θ range of 10–50° with a step size of 0.02 ° and a scan speed of 1 s. The use of these instruments as well as how to do it is designed and implemented based on previous studies (18–21).
UV protection
The UV transmittance spectra (280–400 nm) of the textile were measured at a distance of 5 nm using a spectrophotometer (Varian Cary 100, Australia) (22). The UPF, UV-A (315-400) protection factor, and the UV-B (280-315) protection factor were evaluated using AS/NZ 4399:1996 and equation 1. Three replicated measurements were carried out for each sample and an average value was reported (22). According to the AS/NZ 4399: 1996 standard, the spectral intensity of radiation proportional to that of the solar spectrum (Sλ) in the spectrophotometer was proportional to any wavelength from 290 nm (4–10 × 767/0 W.m−2.nm−1) to 400 nm (180/1 W.m−2.nm−1).
Equation 1 (22).
Where:
Eλ: Relative efficiency of the radiation source.
Sλ; Initial spectrum of the radiation source (W.m-2. nm-1).
dλ: Bandwidth (nm).
Tλ: The amount of light transmitted.
Intrinsic properties of the manufactured textiles
The intrinsic properties of fabrics contribute to their performance, resistance, and heat transfer, so the effect of nanoparticles, applied as a coating, on these properties should be investigated. The properties examined in this study include:
1- Air permeability: the rate of airflow passed through the pores. This property, which indicates the fabric's resistance to sweating-induced evaporative cooling, was tested via ASTM D737 method using the TF164E Air Permeability Apparatus (23).
2- Abrasion resistance: the ability to resist wearing and indicates the cut resistance. This property was estimated using ISIRI 8332 standard (24).
3- Wrap resistance: resistance to tensile force and indicates fabric's strength against tearing. This property was evaluated using ISIRI 4199 (25).
4- Surface wetting resistance: the penetration of water through the fabric or the resistance to wetting. It was measured using ISIRI 567 (26).
Results and discussion
Properties of the fabrics coated with TiO2 nanoparticles
Coating thickness was determined by gravimetric analysis. The results showed that the weight of the fabric was 0.4297 g before coating and 0.4745 g after coating, so 10.42% of TiO2 nanoparticles had been coated on the surface of the fabric. Micrographs and EDX analysis as well as SEM images confirmed the in-situ formation of nanoparticles onto the textile fibers (Figure 1). Ti signals observed in EDX analysis patterns of the fabric modified with TiO2 nanoparticles were recorded. The diameter of TiO2 nanoparticles on the textile fibers was measured using the DLS method. The nanoparticle average diameter determined by DLS was found to be 98.15 nm (Figure 2). Dense TiO2 nanoparticles were observed on the fabric, indicating the effect of the chemical composition of the fabric on the nature of the prepared TiO2 nanoparticles (27, 28). The EDX spectra revealed the presence of C, O, and Ti on the surface of cotton fabrics.
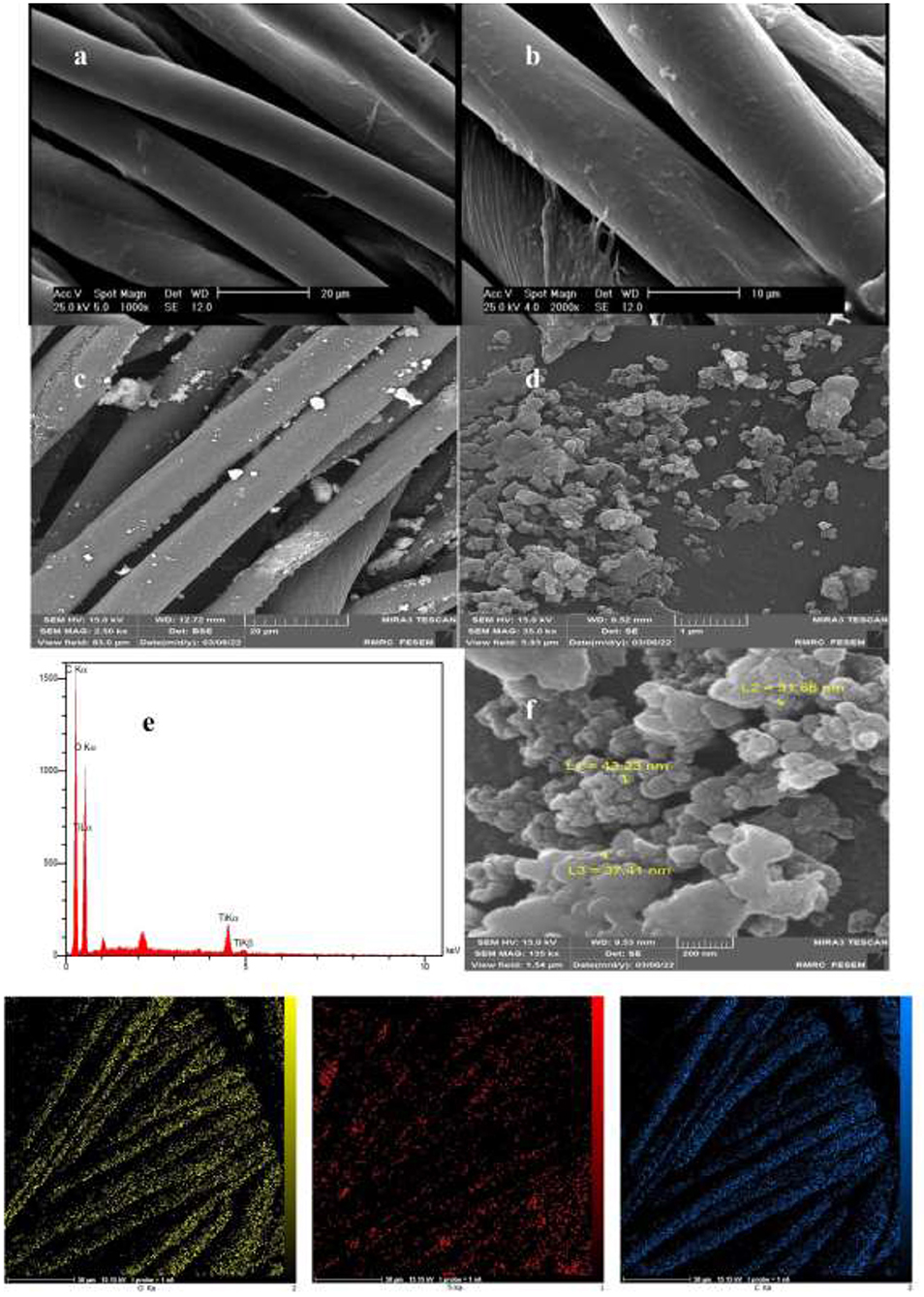
Figure 1. EDX and SEM analysis of TiO2 nanoparticles coating: (a,b) Imaging of the uncoated fabric with image sizes of 20 and 10 μm. (c,d,f) Imaging of TiO2 -coated fabric with image sizes of 20, 1 μm, and 500 nm. (e) EDX spectra of the agents coated onto the fabric surface.
The XRD analysis confirmed the in-situ synthesis of the TiO2 on the fabric surface (Figure 3). As can be seen, the diffraction peaks were located at 5.45, 6.90, 8.08, and 29.37°. Also, consistent with previous studies, after surface modification, some 2θ peaks (base peaks) of the TiO2 nanoparticles were located at 16.74, 22.75, and 34.70° according to the TiO2 nanoparticles (29). The results of the SEM, XRD, FTIR, DLS of the present study are similar to the results of other studies (30–32).
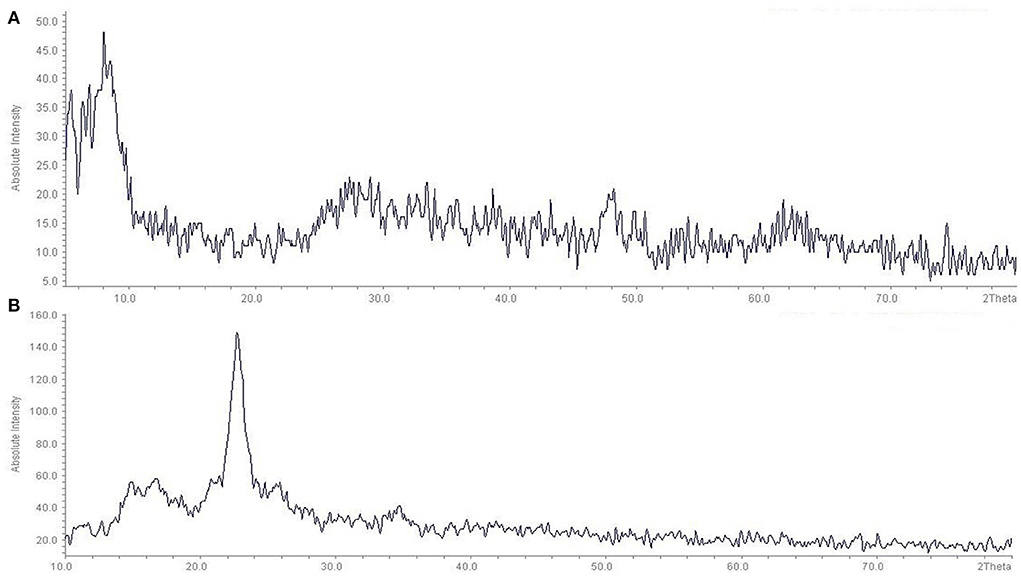
Figure 3. XRD patterns of pure TiO2 Nanopowder and fabric coated with TiO2 nanoparticles: (A) Pure TiO2 Nanopowder, (B) fabric coated with TiO2 nanoparticles.
The chemical composition of the fabric was investigated using FTIR before and after the in-situ formation of the TiO2 nanoparticles (Figure 4). Note the broad peak at 3,305 cm-1 due to the O–H stretch. The broad peak around 2,904 cm-1 also resulted from the C-H stretch. Despite the CH groups of cellulose, the symmetric and asymmetric stretching peaks were not separated as sharp peaks. The peak near 1,706 cm-1 can be attributed to the absorption of water molecules. The broad absorption bands at 434 cm-1 and 722 cm-1 were caused by the bending vibrations of the Ti-O and -O-Ti-O groups, and the peak observed at 1,114 cm-1 was due to the bending vibration of Ti-O-Ti. The vibration bands observed at 1,300–4,000 cm-1 can be attributed to the chemical and/or physical co-adsorption of the H2O and CO2 molecules. Therefore, it can be concluded that the fabrics were well coated with the TiO2 nanoparticles. These results are consistent with other studies on TiO2 nanoparticles (29, 33–37).
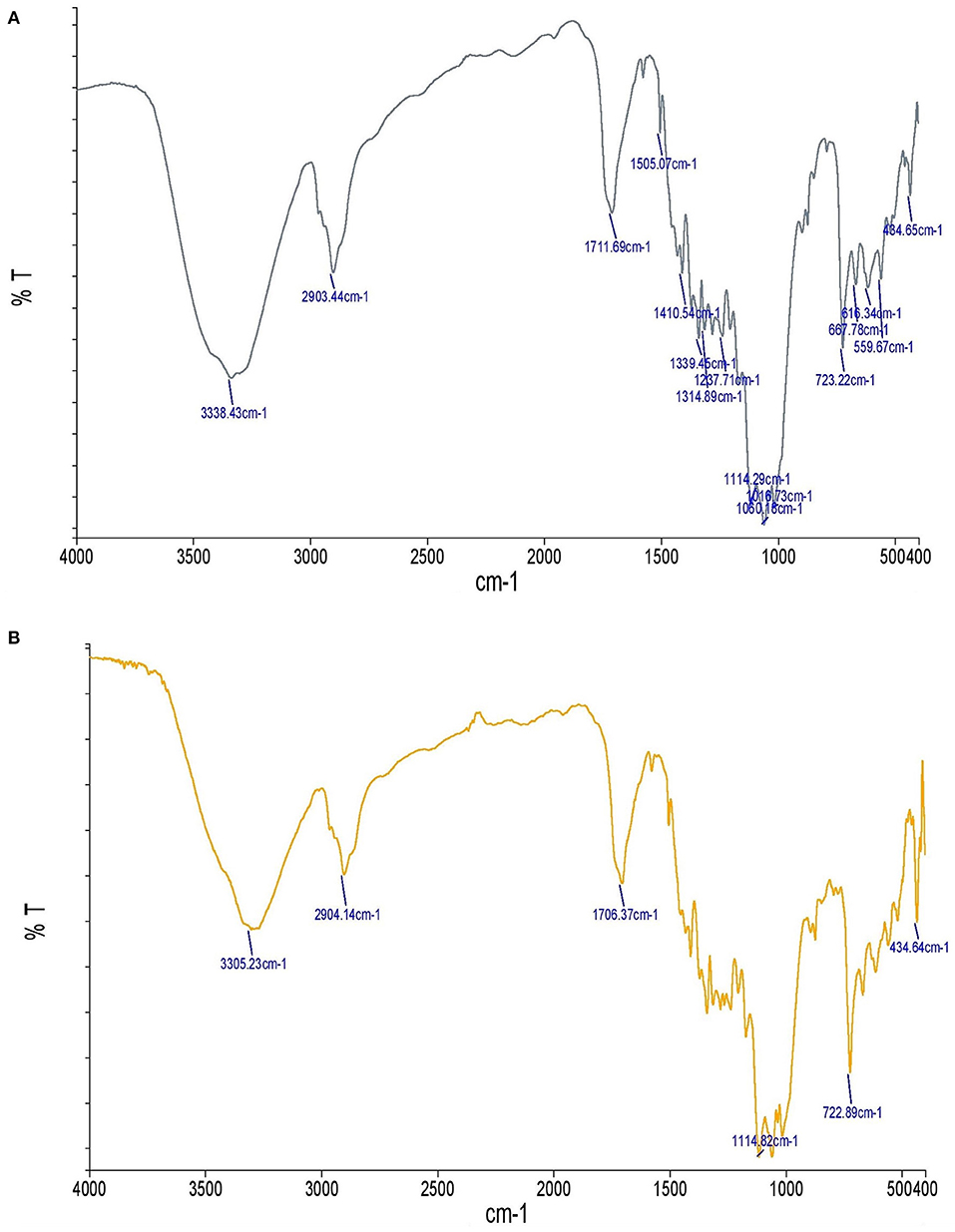
Figure 4. FTIR spectra of uncoated fabric compared with the fabric coated with TiO2 nanoparticles: (A) Uncoated fabric, (B) fabric coated with TiO2 nanoparticles.
UPF values
The UPF of uncoated and coated fabric by measuring the transfer rate (T) for UVR and its spectral results is shown in Figure 5. According to the results, the UPF value of the uncoated fabrics calculated via Equation 1 was 3.67 and the UPF value of fabrics coated with TiO2 nanoparticles was 55.82, indicating the strong UV blocking ability of the coated fabrics. It was confirmed that the in-situ deposition of TiO2 nanoparticles on fabric can provide adequate protection against UVR.
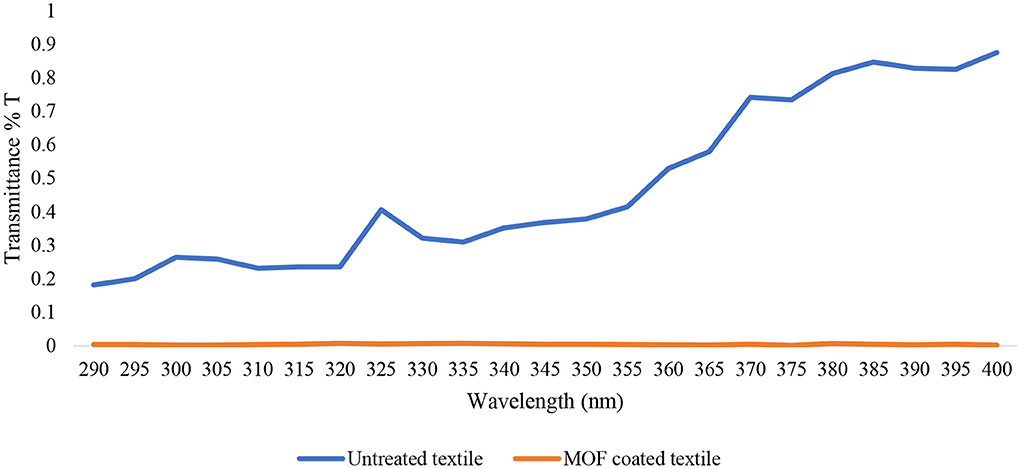
Figure 5. UVR transmittance property of uncoated fabrics and fabrics coated with TiO2 nanoparticles according to AS/NZS 4399 Sun Protective Clothing standard.
According to the Australian/New Zealand Standard and the British standard (22), uncoated fabrics with UPF < 20 have insufficient UV protection. After direct in-situ modification, the fabrics reached UPF > 50 and could be classified in the excellent UV protection category according to the mentioned standard. Other studies have also shown that TiO2 nanoparticles coated on fabric can provide adequate protection against UVR (38, 39). Moreover, previous studies have revealed the enhancement of UV absorption in the TiO2 nanoparticles formed on cotton fabrics. The cotton fabrics loaded with dense layers of the TiO2 nanoparticles exhibited greater UPF values after a longer deposition period (40). Alebeid et al. also showed that the TiO2 nanoparticles can block UV more efficiently compared with dyes, implying that dye is not a reliable indicator of the UV protection provided by dyed fabrics (41–43).
Some studies have shown lower UPF values and this difference can be due to fiber type. For example, Kathirvelu et al. found that 100% cotton fabrics coated with the TiO2 had UPF values lower than the adopted standard and it cannot be classified in the excellent “UV protection category. However, cotton and polyester blended fabrics treated with the TiO2 nanoparticles exhibited higher UPF values and woven fabrics made of polyester-cotton blend yarns showed better UV absorption properties compared to other fabrics (44). Consistent with other studies, the present study indicated that coating fabrics with TiO2 nanoparticles can significantly increase UPF values and improve anti-ultraviolet performance. The difference in the anti-ultraviolet performance can be attributed to different concentrations of the TiO2 nanoparticles and increasing the concentration of TiO2 nanoparticles can increase the UV protection capacity of the fabric (45). In addition, according to studies, the increase in UPF values can be attributed to the natural UV absorption properties of TiO2 and can be explained by the band theory of solids. The TiO2 is a semiconductor with a wide bandgap (3.2 eV) between the low energy valance band and the high energy conduction band. When the TiO2 is activated with light waves of energy greater than its bandgap, the electrons will absorb UV light due to its wide bandgap; that is why the TiO2 can protect against ultraviolet radiation (46).
Many studies have investigated the UV-blocking capacity of TiO2 nanoparticles and have shown that the in-situ synthesis of TiO2 nanoparticles on the fabric surface can lead to UV protection capacity, confirming that in-situ deposition of TiO2 nanoparticles on fabric can provide good to excellent UV protection (28, 29).
Structural properties of the fabric
The present study compared the fabric coated with the TiO2 nanoparticle and the uncoated fabric to investigate the effect of coating on the intrinsic properties of the fabric, including wrap resistance, air permeability, abrasion resistance, and surface wetting resistance. Wrap resistance and abrasion resistance indicate the ability of fabric in various conditions and environments. Also, air permeability and surface wetting resistance refer to the rate of airflow and moisture transfer through the fabric, respectively. This can affect the sweat absorption and comfort properties of the fabric. The results showed no significant difference in the intrinsic properties between the coated and uncoated fabrics, implying that coating the fabric with the TiO2 nanoparticles had no effect on the intrinsic properties of the fabric and caused no reduction in its resistance, air permeability, and the cooling effect of perspiration evaporation (Table 1). This lack of difference shows that coating the fabrics with the TiO2 nanoparticles did not affect their intrinsic properties and the heat and air transfer capacities of the modified fabric were similar to those of the uncoated fabric. Also, the modified fabric had sufficient resistance to withstand work environments. Few studies have investigated the intrinsic properties of the fabric after coating it with the TiO2 nanoparticles and the majority of studies conducted in this field aimed to make fabrics waterproof. No study has been conducted to design workwear fabrics with high UPF values without imposing changes to their intrinsic properties. However, previous studies have also shown that hydrophilicity is also an important property that refers to absorbing moisture vapor and can add to the comfort properties of fabric (47, 48).
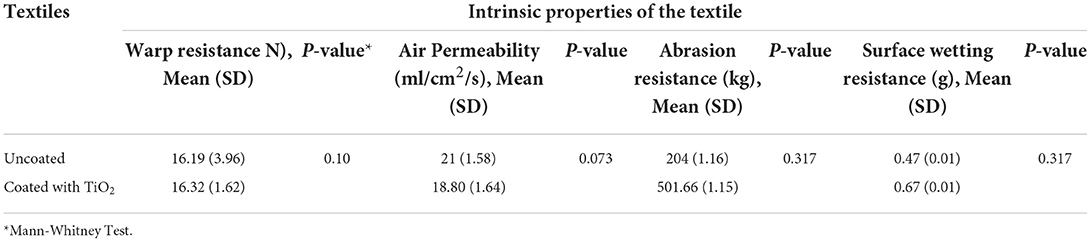
Table 1. Comparison of uncoated and coated textile with TiO2 nanoparticle in terms of intrinsic properties of the textile.
Conclusion
The present study aimed to evaluate the UPF (ultraviolet protective factor) of fabrics coated with the TiO2 nanoparticles made using an in-situ synthesis method and more accurately assess the intrinsic properties of the textile. The results showed that the textile coated with the TiO2 nanoparticle had greater UPF values than the uncoated textile and also the intrinsic properties of the coated fabric did not change significantly. Based on the results, it can be concluded that the UV protective properties of workwear fabrics can be improved by coating the TiO2 nanoparticles on them without any effect on the cooling effect of perspiration evaporation. However, the production of workwear fabrics requires further research. Future studies can evaluate the cytotoxicity and antibacterial properties of the TiO2 nanoparticles to ensure that the TiO2 coating of fabrics has no adverse effects on human skin.
Data availability statement
The original contributions presented in the study are included in the article/supplementary material, further inquiries can be directed to the corresponding author.
Ethics statement
Ethical approval for this study was obtained from School of Public Health and Neuroscience Research Center, Shahid Beheshti University of Medical Sciences (IR.SBMU.PHNS.REC.1400.045).
Author contributions
SF was the leader of study and edited the final manuscript. HR and AK gathered data and performed laboratory experiments and were a major contributor in writing the manuscript. MM analyzed laboratory experiments about fabrics and was a major contributor in writing the manuscript. SK analyzed nanomaterials laboratory experiments and was a major contributor in writing the manuscript. All authors read and approved the final manuscript. All authors contributed to the article and approved the submitted version.
Funding
This study was part of the research projects supported by Shahid Beheshti University of Medical Sciences (Grant No. 28591).
Acknowledgments
This study is related to the project No. 28591 from Student Research Committee, Shahid Beheshti University of Medical Sciences, Tehran, Iran. We also appreciate the Student Research Committee and Research and Technology Chancellor in Shahid Beheshti University of Medical Sciences for their financial support of this study.
Conflict of interest
The authors declare that the research was conducted in the absence of any commercial or financial relationships that could be construed as a potential conflict of interest.
Publisher's note
All claims expressed in this article are solely those of the authors and do not necessarily represent those of their affiliated organizations, or those of the publisher, the editors and the reviewers. Any product that may be evaluated in this article, or claim that may be made by its manufacturer, is not guaranteed or endorsed by the publisher.
References
1. Gambichler T, Rotterdam S, Altmeyer P, Hoffmann K. Protection against ultraviolet radiation by commercial summer clothing: need for standardised testing and labelling. BMC Dermatol. (2001) 1:6. doi: 10.1186/1471-5945-1-6
2. Jiang S, Ma BC, Reinholz J, Li Q, Wang J, Zhang KA, et al. Efficient nanofibrous membranes for antibacterial wound dressing and UV protection. ACS Appl Mater Interfaces. (2016) 8:29915–22. doi: 10.1021/acsami.6b09165
3. Li N, Pranantyo D, Kang ET, Wright DS, Luo HK. In situ self-assembled polyoxotitanate cages on flexible cellulosic substrates: multifunctional coating for hydrophobic, antibacterial, and UV-Blocking applications. Adv Funct Mater. (2018) 28:1800345. doi: 10.1002/adfm.201800345
5. Ogulata RT. The effect of thermal insulation of clothing on human thermal comfort. Fibres Text East Eur. (2007) 15:67–72.
6. Mijović B, Salopek Cubrić I, Skenderi Z. Measurement of thermal parameters of skin-fabric environment. Periodicum Biologorum. (2010) 112:69–73.
7. Emam HE, Bechtold T. Cotton fabrics with UV blocking properties through metal salts deposition. Appl Surf Sci. (2015) 357:1878–89. doi: 10.1016/j.apsusc.2015.09.095
8. Hai FI, Yamamoto K, Fukushi K. Hybrid treatment systems for dye wastewater. Crit Rev Environ Sci Technol. (2007) 37:315–77. doi: 10.1080/10643380601174723
9. Vallejo JJ, Mesa M, Gallardo C. Evaluation of the avobenzone photostability in solvents used in cosmetic formulations. Vitae. (2011) 18:63–71.
10. Xiao X, Liu X, Cao G, Zhang C, Xia L, Xu W, et al. Atomic layer deposition TiO2/Al2O3 nanolayer of dyed polyamide/aramid blend fabric for high intensity UV light protection. Polymer Eng Sci. (2015) 55:1296–302. doi: 10.1002/pen.24068
11. Becheri A, Dürr M, Lo Nostro P, Baglioni P. Synthesis and characterization of zinc oxide nanoparticles: application to textiles as UV-absorbers. J Nanoparticle Res. (2008) 10:679–89. doi: 10.1007/s11051-007-9318-3
12. Kalantary S, Jahani A, Jahani R. MLR and Ann approaches for prediction of synthetic/natural nanofibers diameter in the environmental and medical applications. Sci Rep. (2020) 10:1–10. doi: 10.1038/s41598-020-65121-x
13. Paul R, Bautista L, De La Varga M, Botet JM, Casals E, Puntes V, et al. Nano-cotton fabrics with high ultraviolet protection. Text Res J. (2010) 80:454–62. doi: 10.1177/0040517509342316
14. Yang h, Zhu S, Pan N. Studying the mechanisms of titanium dioxide as ultraviolet-blocking additive for films and fabrics by an improved scheme. J Appl Polym Sci. (2004) 92:3201–10. doi: 10.1002/app.20327
15. Attia NF, Moussa M, Sheta AM, Taha R, Gamal H. Effect of different nanoparticles based coating on the performance of textile properties. Prog Org Coat. (2017) 104:72–80. doi: 10.1016/j.porgcoat.2016.12.007
16. Hasan KF, Wang H, Mahmud S, Genyang C. Coloration of aramid fabric via in-situ biosynthesis of silver nanoparticles with enhanced antibacterial effect. Inorg Chem Commun. (2020) 119:108115. doi: 10.1016/j.inoche.2020.108115
17. Mondal S. Nanomaterials for UV protective textiles. J Ind Text. (2021) 50:1528083721988949. doi: 10.1177/1528083721988949
18. Dastan D. Nanostructured anatase titania thin films prepared by sol-gel dip coating technique. J At Mol Condens Matter Nano Phys. (2015) 2:109–14. doi: 10.26713/jamcnp.v2i2.331
19. Dastan D, Chaure N. Influence of surfactants on TiO2 nanoparticles grown by sol-gel technique. J Mater Mech Manufact. (2014) 2:21–4. doi: 10.7763/IJMMM.2014.V2.91
20. Dastan D, Leila Panahi S, Yengntiwar AP, Banpurka RA. Morphological and electrical studies of titania powder and films grown by aqueous solution method. Adv Sci Lett. (2016) 22:950–3. doi: 10.1166/asl.2016.7130
21. Dastan D, Chaure N, Kartha M. Surfactants assisted solvothermal derived titania nanoparticles: synthesis and simulation. J Mater Sci Mater Electron. (2017) 28:7784–96. doi: 10.1007/s10854-017-6474-9
22. AS/NZ. Sun Protective Clothing–Evaluation and Classification. Australian/New Zealand Standard. Sydney, NSW: Joint Technical Committee TX/21 (1996).
23. Majumdar A, Mukhopadhyay S, Yadav R. Thermal properties of knitted fabrics made from cotton and regenerated bamboo cellulosic fibres. Int J Therm Sci. (2010) 49:2042–8. doi: 10.1016/j.ijthermalsci.2010.05.017
24. (ISIRI) I. O. S. A. I. R. O. I. Textile - Abrasion resistance of fabrics (rotary platform, double- head method). Iran (2003).
25. (ISIRI) I. O. S. A. I. R. O. I. Method for Measuring the Resistance of Warp and Weft Fabrics Against Abrasion by Pendulum Falling Method. 4199. Iran (1994).
26. ISIRI IOSAIROI. Textile – Determination of fabric resistance to surface wetting (spray test) 567. Iran (2014).
27. Kamal Alebeid O, Zhao T. Anti-ultraviolet treatment by functionalizing cationized cotton with TiO2 nano-sol and reactive dye. Text Res J. (2015) 85:449–57. doi: 10.1177/0040517514549989
28. Becenen N, Altun Ö. Applications of TiO2, ZnO and Ag nanomaterials to denim fabric. J Nanosci Nanotechnol. (2016) 16:5359–63. doi: 10.1166/jnn.2016.12650
29. El-Naggar ME, Shaheen TI, Zaghloul S, El-Rafie MH, Hebeish A. Antibacterial activities and UV protection of the in situ synthesized titanium oxide nanoparticles on cotton fabrics. Ind Eng Chem Res. (2016) 55:2661–8. doi: 10.1021/acs.iecr.5b04315
30. Dastan D, Londhe PU, Chaure NB. Characterization of TiO2 nanoparticles prepared using different surfactants by sol–gel method. J Mater Sci Mater Electron. (2014) 25:3473–9. doi: 10.1007/s10854-014-2041-9
31. Dastan D, Panahi SL, Chaure NB. Characterization of titania thin films grown by dip-coating technique. J Mater Sci Mater Electron. (2016) 27:12291–6. doi: 10.1007/s10854-016-4985-4
32. Dastan D. Effect of preparation methods on the properties of titania nanoparticles: solvothermal versus sol–gel. Appl Phys A. (2017) 123:1–13. doi: 10.1007/s00339-017-1309-3
33. Liang L, Shi Z, Tan X, Sun S, Chen M, Dastan D, et al. largely improved breakdown strength and discharge efficiency of layer-structured nanocomposites by filling with a small loading fraction of 2D zirconium phosphate nanosheets. Adv Mater Interfaces. (2022) 9:2101646. doi: 10.1002/admi.202101646
34. Sun L, Shi Z, He B, Wang H, Liu S, Huang M, et al. Asymmetric trilayer all-polymer dielectric composites with simultaneous high efficiency and high energy density: a novel design targeting advanced energy storage capacitors. Adv Funct Mater. (2021) 31:2100280. doi: 10.1002/adfm.202100280
35. Zhang M, Shi Z, Zhang J, Zhang K, Lei L, Dastan D, et al. Greatly enhanced dielectric charge storage capabilities of layered polymer composites incorporated with low loading fractions of ultrathin amorphous iron phosphate nanosheets. J Mater Chem C. (2021) 9:10414–24. doi: 10.1039/D1TC01974K
36. Abbasi S, Dastan D, Tălu S, Tahir M, Elias M, Tao L, et al. Evaluation of the dependence of methyl orange organic pollutant removal rate on the amount of titanium dioxide nanoparticles in MWCNTs-TiO2 photocatalyst using statistical methods and Duncan's multiple range test. Int J Environ Anal Chem. (2022) 103:1−15. doi: 10.1080/03067319.2022.2060085
37. Altaf F, Ahmed S, Dastan D, Batool R, Rehman Z, Shi Z, et al. Novel sepiolite reinforced emerging composite polymer electrolyte membranes for high-performance direct methanol fuel cells. Mater Today Chemist. (2022) 24:100843. doi: 10.1016/j.mtchem.2022.100843
38. Yang Y, Huang W, Guo Z, Zhang S, Wu F, Huang J, et al. Robust fluorine-free colorful superhydrophobic PDMS/NH2-MIL-125 (Ti)@ cotton fabrics for improved ultraviolet resistance and efficient oil–water separation. Cellulose. (2019) 26:9335–48. doi: 10.1007/s10570-019-02707-3
39. Emam HE, Abdelhameed RM. Anti-UV radiation textiles designed by embracing with nano-MIL (Ti, In)–metal organic framework. ACS Appl Mater Interface. (2017) 9:28034–45. doi: 10.1021/acsami.7b07357
40. Khan MZ, Militky J, Baheti V, Wiener J, Vik M. Development of durable superhydrophobic and UV protective cotton fabric via TiO2/trimethoxy (octadecyl) silane nanocomposite coating. J Text Inst. (2021) 112:1639–50. doi: 10.1080/00405000.2020.1834235
41. Akgun M, Becerir B, Alpay HR. Ultraviolet (UV) Protection of Textiles: A Review International scientific conference-UNITECH (2010).
42. Abidi N, Hequet E, Tarimala S, Dai LL. Cotton fabric surface modification for improved UV radiation protection using sol–gel process. J Appl Polym Sci. (2007) 104:111–7. doi: 10.1002/app.24572
43. Alebeid OK, Zhao T, Seedahmed AI. Dyeing and functional finishing of cotton fabric using henna extract and TiO2 Nano-sol. Fibers Polymers. (2015) 16:1303–11. doi: 10.1007/s12221-015-1303-3
44. Kathirvelu S, D'Souza L, Dhurai B. A comparative study of multifunctional finishing of cotton and P/C blended fabrics treated with titanium dioxide/zinc oxide nanoparticles. Indian J Sci Technol. (2008) 1:1–12. doi: 10.17485/ijst/2008/v1i6.6
45. Chaudhari S, Mandot A, Patel B. Effect of nano TiO2 pretreatment on functional properties of cotton fabric. Int J Eng Res Dev. (2012) 1:24–9.
46. Palaskar S, Desai A, Shukla S. Development of multifunctional cotton fabric using atmospheric pressure plasma and nano-finishing. J Text Inst. (2016) 107:405–12. doi: 10.1080/00405000.2015.1034932
47. Li W, Wang S, Wang W, Qin C, Wu M. Facile preparation of reactive hydrophobic cellulose nanofibril film for reducing water vapor permeability (WVP) in packaging applications. Cellulose. (2019) 26:3271–84. doi: 10.1007/s10570-019-02270-x
Keywords: TiO2, nanoparticles, UPF, in-situ, textile
Citation: Rabiei H, Farhang Dehghan S, Montazer M, Khaloo SS and Koozekonan AG (2022) UV protection properties of workwear fabrics coated with TiO2 nanoparticles. Front. Public Health 10:929095. doi: 10.3389/fpubh.2022.929095
Received: 26 April 2022; Accepted: 12 July 2022;
Published: 01 August 2022.
Edited by:
Jochen Schmidt, Friedrich-Alexander-Universität Erlangen-Nürnberg, GermanyReviewed by:
Dalia El-Sawy Abulyazied, Egyptian Petroleum Research Institute, EgyptDavoud Dastan, Georgia Christian University, United States
Copyright © 2022 Rabiei, Farhang Dehghan, Montazer, Khaloo and Koozekonan. This is an open-access article distributed under the terms of the Creative Commons Attribution License (CC BY). The use, distribution or reproduction in other forums is permitted, provided the original author(s) and the copyright owner(s) are credited and that the original publication in this journal is cited, in accordance with accepted academic practice. No use, distribution or reproduction is permitted which does not comply with these terms.
*Correspondence: Somayeh Farhang Dehghan, c29tYXllaC5mYXJoYW5nQHNibXUuYWMuaXI=
†ORCID: Somayeh Farhang Dehghan https://orcid.org/0000-0002-6607-6396