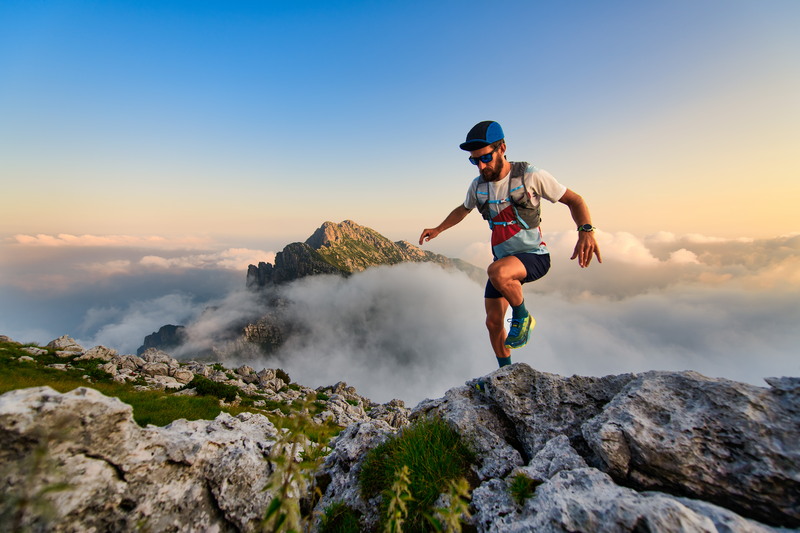
95% of researchers rate our articles as excellent or good
Learn more about the work of our research integrity team to safeguard the quality of each article we publish.
Find out more
ORIGINAL RESEARCH article
Front. Plant Sci.
Sec. Sustainable and Intelligent Phytoprotection
Volume 16 - 2025 | doi: 10.3389/fpls.2025.1575648
The final, formatted version of the article will be published soon.
You have multiple emails registered with Frontiers:
Please enter your email address:
If you already have an account, please login
You don't have a Frontiers account ? You can register here
Research on pineapple harvesting machinery remains in its early stages, and the design and development of such machinery play a crucial role in advancing mechanization and automation within the pineapple industry. This study designs the rotary plate pineapple fruit harvester's cutting table structure based on the physical and mechanical properties of pineapple plants. The design process includes simulating manual harvesting techniques. Initially, a thorough analysis was performed to determine the structural parameters of the cutting table's key components, including the plucking speed ratio, the height of the fruit-picking plate from the ground, and the forward speed of the harvester. A stress analysis of the stem during harvesting was then conducted based on the principle of large deflection. This analysis allowed for the examination of two conditions that occur during fruit picking: (1) the stress state when the fruit and stem are separated at the end of the stem connection, and (2) the stress state when the stem breaks at a point along its length, leading to separation. A simplified rigid-flexible coupling model of the cutting platform and pineapple plant was developed using simulation software, followed by a three-factor, five-level virtual response surface analysis. This analysis was conducted to determine the optimal parameter combinations that would ensure the effective force exerted by the picking plate on the pineapple exceeds the average separation force of 60.45 N, while minimizing the peak force. The optimal parameters included a pulling ratio of 1.8, a picking plate center height of 890 mm above the ground, and a forward speed of the harvester of 0.4 m/s. Subsequent field experiments were carried out to validate the effectiveness of the optimal picking plate parameters. The field experiments with the optimal parameter combination demonstrated that the pineapple fruit picking rate was 71.3%, and the damage rate was 14.8%. The study's results provide valuable insights for future research on pineapple harvesting machinery.
Keywords: harvest1, design2, emulation3, pineapple4, fruit-picker5
Received: 12 Feb 2025; Accepted: 01 Apr 2025.
Copyright: © 2025 Qiu, Duan and Zhong. This is an open-access article distributed under the terms of the Creative Commons Attribution License (CC BY). The use, distribution or reproduction in other forums is permitted, provided the original author(s) or licensor are credited and that the original publication in this journal is cited, in accordance with accepted academic practice. No use, distribution or reproduction is permitted which does not comply with these terms.
* Correspondence:
Xue Zhong, South Subtropical Crops Research Institute, Chinese Academy of Tropical Agricultural Sciences, Zhanjiang, 524091, Guangdong Province, China
Disclaimer: All claims expressed in this article are solely those of the authors and do not necessarily represent those of their affiliated organizations, or those of the publisher, the editors and the reviewers. Any product that may be evaluated in this article or claim that may be made by its manufacturer is not guaranteed or endorsed by the publisher.
Research integrity at Frontiers
Learn more about the work of our research integrity team to safeguard the quality of each article we publish.