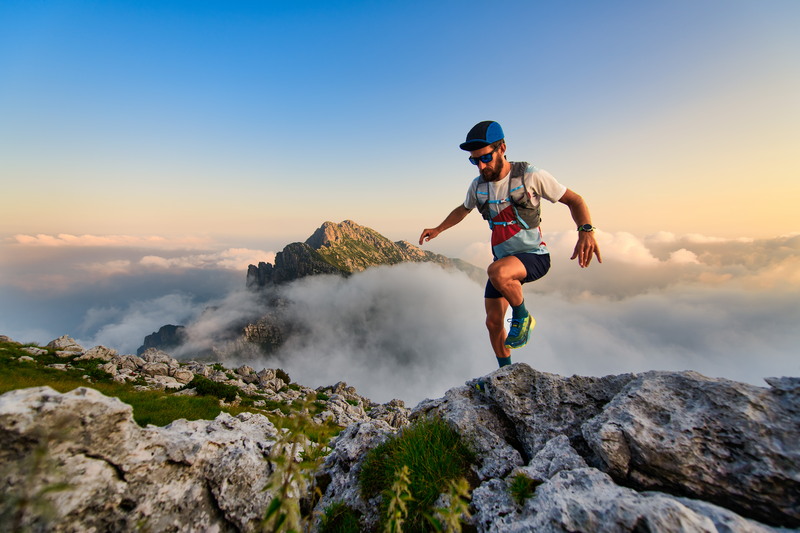
95% of researchers rate our articles as excellent or good
Learn more about the work of our research integrity team to safeguard the quality of each article we publish.
Find out more
ORIGINAL RESEARCH article
Front. Plant Sci. , 27 March 2023
Sec. Sustainable and Intelligent Phytoprotection
Volume 14 - 2023 | https://doi.org/10.3389/fpls.2023.1133969
This article is part of the Research Topic Autonomous Weed Control for Crop Plants View all 8 articles
Tomato is a globally grown vegetable crop with high economic and nutritional values. Tomato production is being threatened by weeds. This effect is more pronounced in the early stages of tomato plant growth. Thus weed management in the early stages of tomato plant growth is very critical. The increasing labor cost of manual weeding and the negative impact on human health and the environment caused by the overuse of herbicides are driving the development of smart weeders. The core task that needs to be addressed in developing a smart weeder is to accurately distinguish vegetable crops from weeds in real time. In this study, a new approach is proposed to locate tomato and pakchoi plants in real time based on an integrated sensing system consisting of camera and color mark sensors. The selection scheme of reference, color, area, and category of plant labels for sensor identification was examined. The impact of the number of sensors and the size of the signal tolerance region on the system recognition accuracy was also evaluated. The experimental results demonstrated that the color mark sensor using the main stem of tomato as the reference exhibited higher performance than that of pakchoi in identifying the plant labels. The scheme of applying white topical markers on the lower main stem of the tomato plant is optimal. The effectiveness of the six sensors used by the system to detect plant labels was demonstrated. The computer vision algorithm proposed in this study was specially developed for the sensing system, yielding the highest overall accuracy of 95.19% for tomato and pakchoi localization. The proposed sensor-based system is highly accurate and reliable for automatic localization of vegetable plants for weed control in real time.
Tomato (Solanum lycopersicon) is one of the major commercial vegetable crops in the world (Johansen et al., 2019). Tomato is considered to be beneficial to human health, and they are widely grown and consumed all over the world (Chaudhary et al., 2018), with great commercial and economic values (Brunetti et al., 2019). However, the production of this crop is being threatened by weeds (Qasem, 2019). The competition between weeds and crops for resources such as sunlight and nutrients is one of the main factors affecting crop yields (Hamuda et al., 2016). Early weed control is one of the most important initiatives to prevent significant crop yield losses (Su et al., 2020a).
The most prominent method of weed management is herbicide spraying throughout the crop area (Pérez-Ortiz et al., 2016), but large-scale spraying of herbicides has a negative impact on the environment (Rodrigo et al., 2014). Moreover, incomplete degradability of herbicides can leave residues in plants (Rojas et al., 2017), creating health risks if the products with herbicide residues were consumed by humans and animals (Manh et al., 2001). Additionally, available herbicides for vegetable crops are very limited (Westwood et al., 2018). As a conventional weeding method, mechanical cultivating is not only able to loosen the soil but also can remove weeds between rows (Wang et al., 2019). Nevertheless, this method does not work for intro-row weeds. Intro-row weeds have traditionally been removed by manual weeding. However, manual weeding is inefficient and particularly prone to errors (Slaughter et al., 2008). This approach is increasingly costly, unsustainable and uneconomical in the long run due to labor shortages (Fennimore et al., 2017).
With the increase of the global population and the improvement of living standards, the demand for healthy food continues increasing. Predicting biomass through various types of sensing technologies has become the focus of precision agriculture and smart farming in recent years (Johansen et al., 2020). Precision weeding is considered as one of the most important measures for sustainable vegetable production (Raja et al., 2020a). There is a need to develop an efficient autonomous weeding robot that can intelligently identify weeds and enable precise herbicide application. The primary task of developing a smart weeder is to identify the vegetable crops and weeds accurately and timely.
Detection methods based on characteristics of crop plants and weeds such as color (Gupta and Ibaraki, 2014), size (Lamm et al., 2002), and spectral reflectance (Borregaard et al., 2000) have been proposed to classify crops and weeds. Blasco et al. (2002) developed a robotic system for weed control in transplanted lettuce, which identified the plants with the accuracies of 84% and 99% for weeds and lettuce based on the plant size, respectively. But the probability of misidentification increases significantly when weeds and crops are of similar size. Vrindts et al. (2002) developed a hyperspectral machine vision system to identify weeds in sugar beet fields. However, their method could not be directly used for the real-time detection of the plants. Lin et al. (2017) established a method combining plant spectrum, shape and texture features to discriminate maize and weed with over 95% accuracy, but the spatial location of the plant was not considered in their study. With the development of computer vision technology, more sophisticated object detection methods based on imaging and machine learning have been developed to distinguish crops from weeds (Hall et al., 2017; Lottes et al., 2017; Milioto et al., 2018; Tang et al., 2018; Rehman et al., 2019; Li et al., 2022). Ahmed et al. (2012) proposed a support vector machine method to classify crops and weeds, which achieved above 97% accuracy. dos Santos Ferreira et al. (2017) developed a ConvNets-based software for detecting weeds in soybean, yielding an average accuracy of 99.5%. Subeesh et al. (2022) applied the InceptionV3 model to identify weeds in sweet peppers with an accuracy of 97.7%. However, the above methods need to obtain a large number of samples in advance to label them accurately for model training.
The up-to-date technology called crop signaling was proposed to simplify weed identification (Raja et al., 2019b). This technology creates a machine-readable signal on plants that allows the marked crops to be readily identified by a computer vision system. Crop signaling technology has been successfully used to identify different target plants in weeds (Nguyen et al., 2017; Vuong et al., 2017; Raja et al., 2019a; Su, 2020). For example, Raja et al. (2020b) developed a device containing two cameras to automatically detect lettuce and weeds based on crop signaling. The classification accuracies of lettuce plants and weeds were 99.75% and 83.74%, respectively. However, the use of two cameras to obtain the location information of plants increased the complexity of image processing. In another study, Su et al. (2020b) applied systemic signaling markers to tomato and lettuce plants, allowing the treated plants to be efficiently detected by a single imaging system. Although their technology enabled the detection of exogenous signals applied to crops, the development of the equipment that can be used for the online detection of plant markers has not yet been reported.
In this study, an intelligent sensing system equipped with six color mark sensors and a color camera is expected to be developed for automatic identifications of weed and tomato plants. The color mark sensor is a photoelectric sensor used to quickly detect a specific color label based on the difference between the gray value of the target label and the reference. The color mark sensor is a reverse device, which realizes detection by receiving and analyzing the scattered light of the detected object. The detection principle of the color mark sensor mainly involves three steps. First, the color mark sensor emits monochromatic light (or white light) with the same intensity to the surface of the measured label. Then, it receives the diffuse reflection from the surface of the measured label. Finally, the label is identified according to whether the intensity of the diffuse reflection is consistent with the preset reference value. Prior to detection, the color mark sensor detects and records the amount of the diffuse reflection from the reference and target, respectively. This amount is used as the preset reference value. When an equivalent amount is detected, the object is the desired target. Although the color mark sensor has been widely used in packaging, printing, spinning and other industries (Yang et al., 2009), it has not been used in plant recognition yet.
The captured images were converted from red-green-blue (RGB) space to hue-saturation-value (HSV) space for color segmentation in this study. The reason is that the images acquired in the natural environment are sensitive to illumination variation, and all three components of the RGB space are closely related to illumination. If the illumination of the image changes, it may not be possible to completely separate the plant pixels from the background using RGB space (Hamuda et al., 2016). In contrast, the HSV space is robust to illumination changes (Siogkas and Dermatas, 2006). Additionally, HSV space is more in line with human color perception (Saxe and Foulds, 1996). This makes HSV space more suitable for segmenting plants and backgrounds (soil and residues) and has been widely used in various computer vision applications (Huang et al., 2015).
The main objective of this study was to develop a novel detection method for smart differentiation of tomato plants from packchoi (Brassica chinensis L.) plants. The specific objectives were 1) developing a smart sensing system containing several color mark sensors and a color digital camera, 2) comparing experimental results of arranging color mark sensors and plant labels in different schemes to determine the best combination. 3) evaluating effects of the signal tolerance zone size on the performance of the system in locating weeds and tomato plants to determine the final solution. As far as we know, this was the first study to realize real-time identification and localization of tomato from background plants using a composite sensing system developed by combining computer vision and color mark sensing.
A series of experiments were carried out in the laboratory of China Agricultural University. 3 week-old tomato plants (height: 15 - 20 cm, the maximum width of the canopy: 10 - 20 cm) were selected as crop samples (300 plants). 1 week-old pakchoi plants (height: 2 - 10 cm, the maximum width of the canopy: 3 - 8 cm) were selected and regarded as control plant (weed) samples (1114 plants). Both plant seedlings purchased from commercial nursery were transplanted into plastic pots filled with moist soil and grown in a controlled environment (temperature = 18–22°C, relative air humidity = 46–50%). Pakchoi seedlings were planted between tomato plants. In this study, tomato plants were labeled by plant labels and the control plants without plant labels were considered as weeds in this study.
Two types of signaling markers including physical labels and topical markers were selected as the plant labels. The physical label (red, white and green) is an environmentally friendly straw (23 cm in length) made of polylactic acid that can be degraded by microorganisms. When the physical plant label was used to label a tomato plant, it was inserted into the soil near the roots of the tomato plant and attached to the main stem of the tomato plant, as shown in Figure 1. The above-ground part of the physical label is divided into three areas, including the lower part (0 - 6cm), the middle part (6 - 12cm) and the upper part (12 - 18cm). The topical marker (white) is an environmentally friendly paint. When the topical marker was used to label a tomato plant, it was applied to the lower main stem of the tomato plant, as shown in Figure 2. Tomato plants were successively marked with different physical labels (red, white, or green) and white topical markers.
Tomato plants with plant labels were placed on a conveyor belt and detected by a color mark sensor 20 cm away from them. Weed stems and tomato stems were successively set as the reference for color mark sensor to determine the best reference for the color mark sensors and the best color for the plant labels. Three areas of physical plant labels and topical plant labels were detected by adjusting the mounting height of the sensor to determine the most suitable detection area. Immediately afterwards, Tomato plants marked with the topical marker (1-6 weed samples were randomly distributed around each tomato plant) was detected by combinations of different number of color mark sensors (2, 4 and 6, as shown in Figure 3) to determine the optimal number of color mark sensors for this system. Finally, the size of the signal circular tolerance zone (r = 2.5mm, r = 5mm, r = 7.5mm, r = 10mm and r = 12.5mm) on the performance of the system was evaluated with tomato plants and weeds.
Figure 3 (A) 2 color mark sensors were applied, (B) 4 color mark sensors were applied, (C) 6 color mark sensors were applied.
The sensing system consists of an adjustable voltage power, a relay, a micro control unit, a personal computer and an enclosed chamber with black vinyl walls. The chamber mainly included a color digital camera, six color mark sensors, four white light emitting diodes (LEDs), as shown in Figure 4. The camera was placed on the vertical centerline between the middle color mark sensors at a height from the plant so that the top view of crop plants was visible. The camera was controlled by the personal computer and was used to capture images of tomato plants and the weeds around them. The color mark sensors emitting red light with a long emission distance of 30 cm were used to detect plant labels. Two middle color mark sensors were positioned parallel to the travel direction. The other color mark sensors were positioned at an angle of 45° relative to the middle sensors. The combination of six color mark sensors allowed the sensing system to cope with situations where the signal was obscured by weeds. The system could detect plant labels as long as two sensors that not on the same detection line were not blocked. The white LEDs were placed below the camera around the upper part of the chamber to provide even illumination for imaging the plants. An adjustable voltage power supply was used to control the brightness of the LEDs. Each color mark sensor was equipped with a relay. When the color mark sensor detected the plant label, it sent a signal to the relay immediately. The microcontroller was connected to all the relays to capture the signals of all the color mark sensors simultaneously. The code received by the microcontroller was interpreted by the software and transmitted to the personal computer to calculate the location of the plant label. The entire system was mounted on a conveyor belt with a speed of 0.91km/h.
An algorithm was especially developed to acquire images of tomato and packchoi plants based on the signals of the smart sensing system and classify them. The ultimate purpose of image processing was to map weeds. The flow chart of the algorithm is shown in Figure 5. The color mark sensors detect passing tomato plants with plant labels while the conveyor is running. When the color mark sensor detects a plant label, the image was captured by the camera. With white LED illumination, the camera’s exposure was set to -6 to obtain sufficient image intensity while eliminating motion blur from the conveyor belt. The image captured by the camera was shown in Figure 6A. Based on the RGB image obtained under controlled illumination, the hue (H), saturation (S) and luminance (V) values were calculated for each pixel and the HSV space model of the image was generated. The HSV space was used for color partitioning of all plants (both tomato plants and weeds) from the background. The threshold of color segmentation was determined based on the appearance of plant colors in the image. The rules for color segmentation were shown in Equation 1.
Figure 6 (A) Image of tomato plant and weeds captured by the system, (B) binary image after morphological operations, (C) binary image with plants contours (yellow), (D) position of the crop signal in the RGB image, (E) position of crop signal in the binary image, (F) crop signal tolerance bands in the binary image, (G) the contours of plants (yellow) and the crop signal tolerance bands (red) in the binary image, (H) the contours of tomato plant (red) and the contours of weeds (green), (I) pixel mapping of weeds (green) and crop plants (red).
Where Ohsv(x, y) represents the mapping of the captured original image in the HSV space model. [Ohsv(x, y)]h,s,v are the hue, saturation and value of Ohsv(x, y), respectively. [Th,s,v]low, are the low thresholds for the H, S and V channel, respectively. Correspondingly, [Th,s,v]high, are the high thresholds for the H, S and V channel, respectively. The thresholds values were selected by pre-experiments. Some images were acquired before the formal experiments and these they were binarized with different thresholds. The most suitable thresholds were selected by comparing the results. The thresholds used in the research were [Th]low= 10, [Th]high= 120, [Ts]low= 10, [Ts]high= 255,[Tv]low = 10, [Tv]high= 255. Rt (x, y) represents the result of color segmentation, a binary image consisting of pixel points in the threshold range.
A 3×3 square structuring element was used for the erosion operation in the binary image. After, tomato plants and weeds in the image were separated from the background. The processed image was then dilated with the same structuring elements to restore the connectivity of the connected domains while maintaining the consistency of the object size. The binary image after morphological operations is shown in Figure 6B. The contour of each connected component was measured in the image and plotted in yellow, as shown in Figure 6C.
As the plant labels pass through the detection area of the sensor combination, they will be detected as positive by multiple sensors. The signals generated by two sensors that are not on the same detection line are combined into a group of available signals. The sensor numbers that make up the available signal are sent to a personal computer as the basis for calculating the positions of the plant labels in the images. According to the data output by the sensor and the moving speed of the device, the detection lines of the sensor were drawn in the captured image, as shown in Figure 6D. The Cartesian coordinate system was established with the point at the upper left of the image as the origin. The detection lines for each sensor were represented by a function equation. The intersection of the sensor detection lines was the position of the plant label in the image, which was plotted on the binary image, as shown in Figure 6E. The rules for calculating the coordinates of the plant labels were shown in Equation 2. Then, a circular tolerance zone was determined. All pixels within the tolerance zone were considered as plant labels, as shown in Figure 6F.
The tolerance zone of the plant labels was integrated with the plant contour, as shown in Figure 6G. The pixel coordinates of each connected area in the image were retrieved. Then, the connected region with the plant labels was considered as tomato plants, which was marked in red. In this study, only one tomato plant was included in each image. The connected region without plant labels was considered as weeds, which was marked in green, as shown in Figure 6H. Based on detection results, the prescription map for the distribution of weeds and crop plants was drawn as shown in Figure 6I.
The effect of two references (the packchoi stem and tomato stem) for color mark sensors on the detection accuracy of physical plant labels of three colors (red, white, and green) was evaluated. As shown in Table 1, the average accuracy of the color mark sensor for plant label recognition was 31.00% when the weed stem was used as the reference. When the tomato stem was used as the reference, 48.89% of the plant labels were successfully identified overall. As can be seen, the color mark sensor with the tomato stem as the reference achieved better recognition performance on plant labels in red or white than that using the weed stem as the reference. Thus, the tomato stem was selected as the reference for color mark sensor for further study.
The optimal plant label color was selected using the tomato stem as the sensor reference. The detectability of plant labels in red, white, and green was evaluated. As shown in Table 1, the detection accuracy of red, white, and green plant labels was 55.33%, 91.33% and 0.00%, respectively. Compared to green plant labels, both red and white plant labels can be detected by the color mark sensor. Although the red labels were able to be used as plant labels, the color mark sensor was more sensitive to the white labels (91.33%). This shows that the white plant label is the best label recognized by the color mark sensor, followed by the red plant label. Thus, the white plant labels were selected for further study.
The detectability of the color mark sensor to the upper, middle and lower regions of the white plant label was analyzed. The feasibility of detecting the three areas of the plant label in the horizontal direction by sensors placed at three heights (lower area: 0-6cm, middle area: 6-12cm and upper area: 12-18cm) was investigated. As shown in Figure 7A, the color mark sensors identify the lower area of the plant label with an accuracy of 90.00%. In contrast, the color mark sensor has lower detection accuracy for the middle and upper areas of the plant labels. This indicated that the lower area of the plant label was the optimal detection area. In order to eliminate the occlusion of plant labels by tomato stems, a new topical label was used in this study, in which white topical markers were applied directly to the tomato stems instead of the use of white physical labels. The sensor detected the white topical marker on the tomato stem with 100% accuracy. Therefore, the white topical marker was chosen as the most appropriate plant label for weed and tomato localization.
Figure 7 (A) Accuracy of detecting different areas, (B)accuracy of different number of sensors being applied.
The effect of the number of selected sensors on the recognition of white topical marker was evaluated. Several weeds were randomly placed around each tomato plant. According to the algorithm developed in this study, the detection of a plant label was considered valid only if it was detected by two or more sensors that were not on the same symmetrical centerline. As shown in Figure 7B, the detection accuracy for plant labels increases as the number of sensors increases from 2 to 6. When 2 color mark sensors were used to detect plant labels, only 20.67% of the plant labels were successfully detected. When 4 color mark sensors work together, 63.33% of the plant labels were effectively detected by this sensing system. When the number of color mark sensors increased to 6, the sensing system detected all plant labels. Therefore, the combination of six color mark sensors was considered as the best solution for the number of sensors in the system.
The effect of the size of the tolerance zone of estimated plant label locations on plant identification was evaluated. Five different sizes of circular tolerance zones (r = 2.5 mm, r = 5 mm, r = 7.5 mm, r = 10 mm and r = 12.5 mm) were set up as a basis for evaluating plant locations. As the radius of the tolerance zone increased from 2.5 mm to 12.5 mm, the accuracy of identifying tomato plants increased from 89.00% to 100.00%, while the accuracy of identifying weeds decreased from 95.42% to 93.72%, as shown in Table 2. To quantitatively evaluate all detected plants, the overall accuracy was calculated as shown in Equation 3.
With the increase of the tolerance zone radius, the identification accuracy of all plants first increased then decreased. When the radius was 7.5 mm, the accuracy reached the maximum value of 95.19%. Figure 8 shows data on the number of weeds and tomato plants present and detected in 300 images collected based on a circular tolerance zone with a radius of 7.5 mm. Among the 300 tomato plants and 1114 weed plants used in this experiment, a total of 294 tomato plants and 1052 weed plants were successfully located, which demonstrated that the system proposed in this study can effectively distinguish weeds from tomato plants.
Figure 8 The weed and crop analysis per image: the number of weed/crop present in each image and the weed/crop in each image actually detected by the algorithm.
In this study, color mark sensors and cameras were combined in a pioneering way for plant detection. The development of an integrated sensing system that detects plant labels and calculates their location is the main innovation of this study. In order for the developed system to reliably classify different plants, the parameters of the color marker sensors and plant tags need to be determined, which is very important and necessary. The tomato plants were labeled using plant labels to give them a machine-readable signal. Thus, the algorithm to distinguish tomato plants from another unlabeled plant was simplified to improve the efficiency of computer execution. The system successfully located tomato and packchoi plants in real-time by using integrated sensing technology.
However, there are also a few plants that are not correctly localized by this system. The tomato plants were classified as weeds probably due to the low frame rate of the camera used in this system. After detecting a plant label, the next frame in the video stream was acquired by the computer as the image for calculating the plant location. Thus, the camera shutter did not open at the same moment as the sensor detected the plant labels in this image. The desynchronization between the camera shutter and the sensor caused incorrect predicted position of the plant label, as shown in Figure 9. In the future, high-speed cameras should be considered to improve the accuracy of plant classification. The errors introduced by the low frame rate of the camera and the delay of the command transmission were compensated by tolerance zones. The suitable size of tolerance zone facilitates the system to classify weeds and tomato plants precisely, as shown in Figure 10. In addition, weeds incorrectly classified as tomato plants possibly due to the occlusion caused by the tomato leaves and stem or weeds located too close to the tomato plants, as shown in Figure 11. In the future, an algorithm for segmenting overlapping weeds and tomato plants in the image should be developed to improve the accuracy of weed detection.
The color mark sensor selected in this study distinguished the target from other objects by using the difference in their reflection of red light. Based on this photometric principle, the color mark sensor showed different detection capabilities for objects of different colors or materials (Yang et al., 2008). Due to significant optical differences, the red light emitted by the color mark sensor can hardly be reflected by the stems of tomatoes and weeds, while it can be reflected by special plant labels. Thus, the plant labels were more easily detected by color mark sensors. Further, the weed stem is slightly lighter in color than the tomato stem, so it can reflect more red light. This might be the reason for the lower recognition accuracy of red and white plant labels when weed stem was used as a reference. When the tomato stem was used as the reference, the white plant labels were more readily detected than red and green plant labels. The reason for this may be that white labels reflect any wavelength of red light, while tomato stems reflect little red light. Although red labels can reflect red light, the wavelength range of the red light reflected did not exactly match the wavelength range of filter in the sensor, so only a portion of the red light reflected by the red labels received by the photosensitive element of the color mark sensor (Bayer-Krucsay, 1937). There was no significant difference in the light reflected by the green label and the green tomato stem, thus the color mark sensor could not distinguish between them.
A comparative analysis of the various weed and crop classification systems that have been developed are presented in Table 3. Comparison of crops, sensors, methods, detection speed and accuracy was performed to evaluate the performance of this system. Although only tomato plants were studied in this paper, the methods proposed in the study are applicable to most of the crops that need to be transplanted. Furthermore, although the studies presented in Table 3 targeted different crops, they all used computer vision to identify tomato and packchoi plants. Thus, it is of great interest to compare the results of the present study with them.
The performance of the system is mainly reflected in speed and detection accuracy. Lee et al. (1999) earlier proposed a Bayesian-based classifier to classify tomato plants and weeds, which achieved a speed of 344 ms f-1. However, its accuracy was low, with only 47.6% of the weeds and 75.8% of the crops being successfully classified. Lamm et al. (2002) developed a machine vision system to classify crops and weeds in commercial cotton fields based on their sizes, which improved the weed identification accuracy. Bakhshipour and Jafari (2018); Ma et al. (2019) proposed a weed detection method based on the SegNet semantic segmentation method and achieved a high accuracy rate (93.9% for weeds and 93.6% for crops), but the speed of their method was slow (604 ms f-1). A method for distinguishing weeds in maize fields based on Mahalanobis distance was proposed by Garcia-Santillan and Pajares (2018). The method achieved an accuracy of 91.8% and a processing speed of 280 ms f-1, but this method must obtain crop row information in advance. Then, Raja et al. (2020b) developed a machine vision system based on crop signaling technology to detect weeds in lettuce rows. The system achieved 83.74% weed detection accuracy and 99.75% crop detection accuracy at a processing speed of 160 ms f-1. The crop classification accuracy and speed of this system met the requirements of real-time weeding, but the weed classification accuracy of this system was low. The method proposed in this study achieved the highest weed detection accuracy (98.00%) and the second highest crop detection accuracy (94.44%), which proves the effectiveness of the method. In addition, the system established in this study takes only 30 ms to process an image, which is much faster compared to the existing systems that take at least 160 ms to process an image.
An automatic real-time localization system was developed, which successfully located tomato and packchoi plants using integrated sensing techniques based on the crop signaling. With the plant labels applied to tomato plants, the information acquired by a color camera and six color marker sensors integrated by the developed image recognition algorithm. The results demonstrated that tomato stem was a reliable reference for higher accuracy. The detection accuracy of the white physical plant label was significantly higher than that of the red label and the green label. The lower part of the label was identified with the highest accuracy compared to the upper and middle part of the white physical plant label. The topical marker directly applied to the lower part of the plant stem can be more readily detected than the physical plant label. The combination of six color mark sensors is the best solution for detecting plant labels. A tolerance zone with a radius of 7.5 mm maximizes the accuracy of plant classification. Based on the established systematic method, the identification accuracy of tomato plants was 98.00%, and the accuracy of weeds was 94.44%. In addition, the system took only 30ms to process an image, which was faster than existing detection systems.Therefore, the system developed in this study had strong performance for weed and tomato identifications, which could provide prescription maps for weed control in transplanted vegetables at a faster rate.
The raw data supporting the conclusions of this article will be made available by the authors, without undue reservation.
W-HS supervised this study, conceived the general idea, provided directions for the system development and revised the manuscript. J-LL developed the system, conducted experiments and analysed the data. W-HS, H-YZ and J-LL drafted the manuscript. W-HS and YP revised the manuscript and provided suggestions for the system development. All authors contributed to the article and approved the submitted version.
This research was funded by National Natural Science Foundation of China, grant number 32101610.
The authors declare that the research was conducted in the absence of any commercial or financial relationships that could be construed as a potential conflict of interest.
All claims expressed in this article are solely those of the authors and do not necessarily represent those of their affiliated organizations, or those of the publisher, the editors and the reviewers. Any product that may be evaluated in this article, or claim that may be made by its manufacturer, is not guaranteed or endorsed by the publisher.
Ahmed, F., Al-Mamun, H. A., Bari, A. S. M. H., Hossain, E., Kwan, P. (2012). Classification of crops and weeds from digital images: A support vector machine approach. Crop Prot. 40, 98–104. doi: 10.1016/j.cropro.2012.04.024
Bakhshipour, A., Jafari, A. (2018). Evaluation of support vector machine and artificial neural networks in weed detection using shape features. Comput. Electron. Agric. 145, 153–160. doi: 10.1016/j.compag.2017.12.032
Blasco, J., Aleixos, N., Roger, J., Rabatel, G., Moltó, E. (2002). AE–automation and emerging technologies: Robotic weed control using machine vision. Biosyst. Eng. 83 (2), 149–157. doi: 10.1006/bioe.2002.0109
Borregaard, T., Nielsen, H., Nørgaard, L., Have, H. (2000). Crop–weed discrimination by line imaging spectroscopy. J. Agric. Eng. Res. 75 (4), 389–400. doi: 10.1006/jaer.1999.0519
Brunetti, G., Traversa, A., De Mastro, F., Cocozza, C. (2019). Short term effects of synergistic inorganic and organic fertilization on soil properties and yield and quality of plum tomato. Scientia Hortic. 252, 342–347. doi: 10.1016/j.scienta.2019.04.002
Chaudhary, P., Sharma, A., Singh, B., Nagpal, A. K. (2018). Bioactivities of phytochemicals present in tomato. J. Food Sci. Technol. 55 (8), 2833–2849. doi: 10.1007/s13197-018-3221-z
dos Santos Ferreira, A., Matte Freitas, D., Gonçalves da Silva, G., Pistori, H., Theophilo Folhes, M. (2017). Weed detection in soybean crops using ConvNets. Comput. Electron. Agric. 143, 314–324. doi: 10.1016/j.compag.2017.10.027
Fennimore, S. A., Slaughter, D. C., Siemens, M. C., Leon, R. G., Saber, M. N. (2017). Technology for automation of weed control in specialty crops. Weed Technol. 30 (4), 823–837. doi: 10.1614/wt-d-16-00070.1
Garcia-Santillan, I. D., Pajares, G. (2018). On-line crop/weed discrimination through the mahalanobis distance from images in maize fields. Biosyst. Eng. 166, 28–43. doi: 10.1016/j.biosystemseng.2017.11.003
Gupta, S. D., Ibaraki, Y. (2014). Plant image analysis: fundamentals and applications (Boca Raton, FL: CRC Press).
Hall, D., Dayoub, F., Kulk, J., McCool, C. (2017). “Towards unsupervised weed scouting for agricultural robotics,” in 2017 IEEE International Conference on Robotics and Automation (ICRA). (Singapore: IEEE), 5223–5230.
Hamuda, E., Glavin, M., Jones, E. (2016). A survey of image processing techniques for plant extraction and segmentation in the field. Comput. Electron. Agric. 125, 184–199. doi: 10.1016/j.compag.2016.04.024
Huang, W., Kim, K., Yang, Y., Kim, Y.-S. (2015). Automatic shadow removal by illuminance in HSV color space. Comput. Sci. Inf. Technol. 3 (3), 70–75. doi: 10.13189/csit.2015.030303
Johansen, K., Morton, M. J., Malbeteau, Y. M., Aragon, B., Al-Mashharawi, S. K., Ziliani, M. G., et al. (2019). Unmanned aerial vehicle-based phenotyping using morphometric and spectral analysis can quantify responses of wild tomato plants to salinity stress. Front. Plant Sci. 10, 370. doi: 10.3389/fpls.2019.00370
Johansen, K., Morton, M. J., Malbeteau, Y., Aragon, B., Al-Mashharawi, S., Ziliani, M. G., et al. (2020). Predicting biomass and yield in a tomato phenotyping experiment using UAV imagery and random forest. Front. Artif. Intell. 3, 28. doi: 10.3389/frai.2020.00028
Lamm, R. D., Slaughter, D. C., Giles, D. K. (2002). Precision weed control system for cotton. Trans. ASAE 45 (1), 231. doi: 10.1007/978-3-319-16220-1_8
Lee, W. S., Slaughter, D. C., Giles, D. K. (1999). Robotic weed control system for tomatoes. Precis. Agric. 1 (1), 95–113. doi: 10.1023/a:1009977903204
Li, Y., Guo, Z., Shuang, F., Zhang, M., Li, X. (2022). Key technologies of machine vision for weeding robots: A review and benchmark. Comput. Electron. Agric. 196, 106880. doi: 10.1016/j.compag.2022.106880
Lin, F., Zhang, D., Huang, Y., Wang, X., Chen, X. (2017). Detection of corn and weed species by the combination of spectral, shape and textural features. Sustainability 9 (8), 1–14. doi: 10.3390/su9081335
Lottes, P., Hörferlin, M., Sander, S., Stachniss, C. (2017). Effective vision-based classification for separating sugar beets and weeds for precision farming. J. Field Robotics 34 (6), 1160–1178. doi: 10.1002/rob.21675
Ma, X., Deng, X., Qi, L., Jiang, Y., Li, H., Wang, Y., et al. (2019). Fully convolutional network for rice seedling and weed image segmentation at the seedling stage in paddy fields. PloS One 14 (4), 1–13. doi: 10.1371/journal.pone.0215676
Manh, A. G., Rabatel, G., Assemat, L., Aldon, M. J. (2001). AE–automation and emerging technologies. J. Agric. Eng. Res. 80 (2), 139–146. doi: 10.1006/jaer.2001.0725
Milioto, A., Lottes, P., Stachniss, C. (2018). “Real-time semantic segmentation of crop and weed for precision agriculture robots leveraging background knowledge in CNNs,” in 2018 IEEE International Conference on Robotics and Automation (ICRA). (Brisbane, QLD, Australia: IEEE), 2229–2235.
Nguyen, T. T., Slaughter, D. C., Fennimore, S. A., Vuong, V. L. (2017). “Designing and evaluating the use of crop signaling markers for fully automated and robust weed control technology,” in 2017 ASABE Annual International Meeting (Spokane, Washington, USA: American Society of Agricultural and Biological Engineers), Vol. 1.
Pérez-Ortiz, M., Peña, J. M., Gutiérrez, P. A., Torres-Sánchez, J., Hervás-Martínez, C., López-Granados, F. (2016). Selecting patterns and features for between-and within-crop-row weed mapping using UAV-imagery. Expert Syst. Appl. 47, 85–94. doi: 10.1016/j.eswa.2015.10.043
Qasem, J. R. (2019). “Weed seed dormancy: The ecophysiology and survival strategies,” in Seed dormancy and germination (London, UK: IntechOpen).
Raja, R., Nguyen, T. T., Slaughter, D. C., Fennimore, S. A. (2020a). Real-time robotic weed knife control system for tomato and lettuce based on geometric appearance of plant labels. Biosyst. Eng. 194, 152–164. doi: 10.1016/j.biosystemseng.2020.03.022
Raja, R., Nguyen, T. T., Slaughter, D. C., Fennimore, S. A. (2020b). Real-time weed-crop classification and localisation technique for robotic weed control in lettuce. Biosyst. Eng. 192, 257–274. doi: 10.1016/j.biosystemseng.2020.02.002
Raja, R., Slaughter, D. C., Fennimore, S. (2019a). “A novel weed and crop recognition technique for robotic weed control in a lettuce field with high weed densities,” in 2019 ASABE Annual International Meeting (Boston, Massachusetts, USA: American Society of Agricultural and Biological Engineers), Vol. 1.
Raja, R., Slaughter, D. C., Fennimore, S. A., Nguyen, T. T., Vuong, V. L., Sinha, N., et al. (2019b). Crop signalling: A novel crop recognition technique for robotic weed control. Biosyst. Eng. 187, 278–291. doi: 10.1016/j.biosystemseng.2019.09.011
Rehman, T. U., Zaman, Q. U., Chang, Y. K., Schumann, A. W., Corscadden, K. W. (2019). Development and field evaluation of a machine vision based in-season weed detection system for wild blueberry. Comput. Electron. Agric. 162, 1–13. doi: 10.1016/j.compag.2019.03.023
Rodrigo, M., Oturan, N., Oturan, M. A. (2014). Electrochemically assisted remediation of pesticides in soils and water: a review. Chem. Rev. 114 (17), 8720–8745. doi: 10.1021/cr500077e
Rojas, M. A., Eerd, L. L. V., O’Halloran, I. P., Sikkema, P. H., Robinson, D. E. (2017). Effect of herbicide residues on fall-seeded cover crops influence soil aggregate stability and mineral n. Can. J. Plant Sci. 97 (3), 411–423. doi: 10.1139/cjps-2016-0078
Saxe, D., Foulds, R. (1996). “Toward robust skin identification in video images,” in Proceedings of the Second International Conference on Automatic Face and Gesture Recognition, (Killington, VT, USA: IEEE), 379–384.
Siogkas, G. K., Dermatas, E. S. (2006). “Detection, tracking and classification of road signs in adverse conditions,” in MELECON 2006 - 2006 IEEE Mediterranean Electrotechnical Conference. (Malaga, Spain: IEEE), 537–540.
Slaughter, D. C., Giles, D. K., Downey, D. (2008). Autonomous robotic weed control systems: A review. Comput. Electron. Agric. 61 (1), 63–78. doi: 10.1016/j.compag.2007.05.008
Su, W.-H. (2020). Systemic crop signaling for automatic recognition of transplanted lettuce and tomato under different levels of sunlight for early season weed control. Challenges 11 (2), 23. doi: 10.3390/challe11020023
Su, W.-H., Fennimore, S. A., Slaughter, D. C. (2020a). Development of a systemic crop signalling system for automated real-time plant care in vegetable crops. Biosyst. Eng. 193, 62–74. doi: 10.1016/j.biosystemseng.2020.02.011
Su, W.-H., Slaughter, D. C., Fennimore, S. A. (2020b). Non-destructive evaluation of photostability of crop signaling compounds and dose effects on celery vigor for precision plant identification using computer vision. Comput. Electron. Agric. 168, 1–8. doi: 10.1016/j.compag.2019.105155
Subeesh, A., Bhole, S., Singh, K., Chandel, N., Rajwade, Y., Rao, K., et al (2022). Deep convolutional neural network models for weed detection in polyhouse grown bell peppers. Artif. Intell. Agriculture 6, 47–54. doi: 10.1016/j.aiia.2022.01.002
Tang, J., Zhang, Z., Wang, D., Xin, J., He, L. (2018). Research on weeds identification based on K-means feature learning. Soft Computing 22 (22), 7649–7658. doi: 10.1007/s00500-018-3125-x
Vrindts, E., De Baerdemaeker, J., Ramon, H. (2002). Weed detection using canopy reflection. Precis. Agric. 3 (1), 63–80. doi: 10.1023/A:1013326304427
Vuong, V. L., Slaughter, D. C., Nguyen, T. T., Fennimore, S. A., Giles, D. K. (2017). “An automated system for crop signaling and robotic weed control in processing tomatoes,” in 2017 ASABE Annual International Meeting. (Spokane, Washington: American Society of Agricultural and Biological Engineers), Vol. 1.
Wang, A. C., Zhang, W., Wei, X. H. (2019). A review on weed detection using ground-based machine vision and image processing techniques. Comput. Electron. Agric. 158, 226–240. doi: 10.1016/j.compag.2019.02.005
Westwood, J. H., Charudattan, R., Duke, S. O., Fennimore, S. A., Marrone, P., Slaughter, D. C., et al. (2018). Weed management in 2050: Perspectives on the future of weed science. Weed Sci. 66 (3), 275–285. doi: 10.1017/wsc.2017.78
Yang, Y. C., Cao, W. B., Pan, R. M., Ieee (2009). “The hardware system design of smart color mark sensor,” in International Symposium on Photonics and Optoelectronics, NEW YORK. (Wuhan, China: IEEE). 909–911.
Keywords: crop signalling, computer vision, plant identification, automated weeding, precision agriculture
Citation: Li J-L, Su W-H, Zhang H-Y and Peng Y (2023) A real-time smart sensing system for automatic localization and recognition of vegetable plants for weed control. Front. Plant Sci. 14:1133969. doi: 10.3389/fpls.2023.1133969
Received: 29 December 2022; Accepted: 13 March 2023;
Published: 27 March 2023.
Edited by:
Chuanlei Zhang, Tianjin University of Science and Technology, ChinaReviewed by:
Bin Liu, Northwest A&F University, ChinaCopyright © 2023 Li, Su, Zhang and Peng. This is an open-access article distributed under the terms of the Creative Commons Attribution License (CC BY). The use, distribution or reproduction in other forums is permitted, provided the original author(s) and the copyright owner(s) are credited and that the original publication in this journal is cited, in accordance with accepted academic practice. No use, distribution or reproduction is permitted which does not comply with these terms.
*Correspondence: Wen-Hao Su, d2VuaGFvLnN1QGNhdS5lZHUuY24=
Disclaimer: All claims expressed in this article are solely those of the authors and do not necessarily represent those of their affiliated organizations, or those of the publisher, the editors and the reviewers. Any product that may be evaluated in this article or claim that may be made by its manufacturer is not guaranteed or endorsed by the publisher.
Research integrity at Frontiers
Learn more about the work of our research integrity team to safeguard the quality of each article we publish.