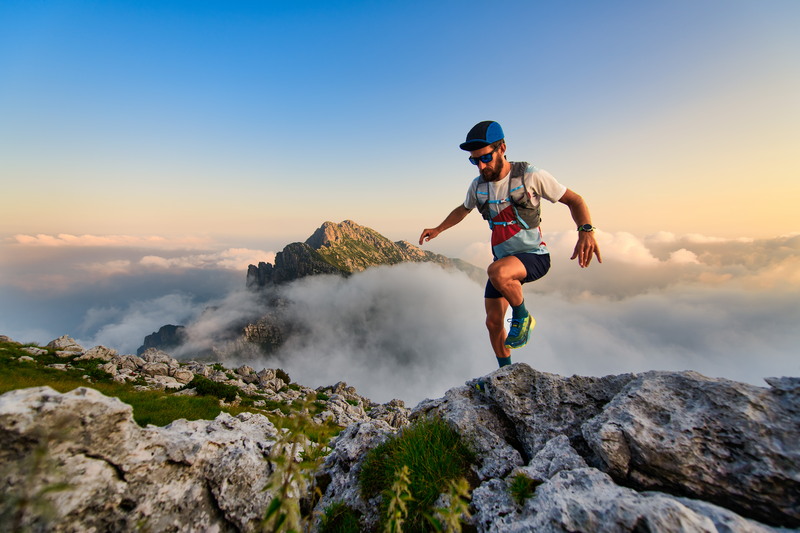
95% of researchers rate our articles as excellent or good
Learn more about the work of our research integrity team to safeguard the quality of each article we publish.
Find out more
ORIGINAL RESEARCH article
Front. Phys. , 26 February 2024
Sec. High-Energy and Astroparticle Physics
Volume 12 - 2024 | https://doi.org/10.3389/fphy.2024.1347162
This paper describes the preparation of radiopure lithium carbonate powder for the needs of low-background research, in particular, AMoRE-II, the second phase of a search for the neutrinoless double-beta decay (0νDBD) of the 100Mo isotope using over 100 kg of 100Mo contained in 200 kg of ultra-pure Li2100MoO4 bolometric crystals. About 150 kg of pure Li2CO3 powder is required to synthesize the crystals. The desired radiopurity for the lithium powder is 40K below 100 mBq/kg, and Th/U and Ra are at a few mBq/kg. Several commercially available powders were tested with ICP-MS and HPGe detectors at the Center for Underground Physics (CUP) of the Institute for Basic Science in Korea. The lowest purity of the tested products was 99.99%. The results of the powders’ radioassay at CUP showed that none of the tested products were suited for the 0νDBD search application. A special purification technology had to be developed to remove the original contamination of the powder with potassium (K), thorium (Th), uranium (U), and radium (Ra). Lithium carbonate crystallization via carbonization technique was inefficient in removing radiochemical impurities. Lithium formate fractional recrystallization effectively removed Ra, K, and Th, but the synthesis of the final lithium carbonate product had a low yield and required the introduction of additional chemicals. The analysis results of raw and purified powders, the decontamination efficiency, and plans are described in the article.
Lithium and its compounds have recently become one of modern science and technology’s most highly demanded rare metals. It is used as electrode materials in electrochemical cells, in the production of ceramics and different types of glass, in pharmacy as a medicine for mental disaster treatment, etc. Recently, lithium compounds have found application in particle physics as a precursor for producing lithium-containing cryogenic crystal detectors [1–4]. Lithium molybdate (Li2MoO4, LMO) crystal scintillators are being used in searches for rare-event processes such as two neutrino double beta decay (2νDBD) [1, 2] and neutrinoless double beta decay (0νDBD) [3, 4]. Lithium fluoride (LiF) crystals are applied to studies of rare α and β decays and dark matter particle searches [5–7]. In particular, the AMoRE collaboration has selected lithium molybdate as the source/detector material for cryogenic measurements. AMoRE is an international collaboration focused on a high-sensitivity search for the 0νDBD of 100Mo nuclei embedded in Li2100MoO4 and 40Ca100MoO4 (CMO) scintillating crystals operating at milli-Kelvin temperatures. Since the Mo-100 isotope has a comparatively high natural abundance (9.74%) [8] and a high Qββ-value of 3,034.40(17) keV [9], it is a promising candidate for a 0νDBD search. However, searching for the 0νDBD is challenging because of the long half-lives, greater than 1.1 × 1024 year for 100Mo [4, 10, 11].
AMoRE experiment is being implemented in a series of phases [12]. The AMoRE-I was carried out in 2021–2023 at the Yangyang Underground Laboratory (Y2L) with five LMO and thirteen CMO crystal detectors (∼3 kg 100Mo mass) [13, 14]. Relative to the CMO crystals [15, 16], the LMO crystals have revealed lower intrinsic radiopurities [17]. Those LMO crystals were produced at the Nikolaev Institute of Inorganic Chemistry (NIIC) [18]. For the crystal’s synthesis, pure lithium carbonate powder was provided by the NIIC and enriched MoO3 powder was purified with the NIIC technique [19, 20]. Based on preliminary estimates, an overall background rate of ∼0.032 count/keVkg·year in the region of interest (ROI) at Qββ (3,034 keV) and the
The AMoRE-II is the next phase of the experiment that will operate at the 1000-m Yemilab facility of the Center for Underground Physics (CUP) at the Institute for Basic Science (IBS) in Korea. About 400 lithium molybdate crystals (∼100 kg of 100Mo) will be assembled in an array of AMoRE-II detector to probe a projected sensitivity goal that corresponds to a decay half-life limit of
For a sensitive and large-scale bolometric experiment like AMoRE-II, the development of a protocol for producing high-quality monocrystal bolometers with an extremely high internal radiopurity, in an ideal case, zero internal radioactive background is needed. The conventional Czochralski technique [3] at CUP and the low-thermal gradient Czochralski (LTG-Cz) technique [19] at the NIIC are used for the production of the AMoRE-II crystals. About 180 kg of molybdenum trioxide (100MoO3), enriched in the 100Mo isotope, and 150 kg of lithium carbonate are used as precursors for the crystal synthesis. The procedure for the purification of enriched 100MoO3 for AMoRE-II was finalized and carried out at the CUP facility [27]. This study was focused on understanding the initial Li2CO3 purity required for AMoRE-II crystal synthesis with both techniques and what purity levels are commercially available in the market.
The process of a single crystal growing is itself a purification technique. Nevertheless, the reduction of impurities (segregation) significantly depends on the purity of initial materials, the method of crystallization, and its yield efficiency. Preliminary purification of the precursors and sequential double crystallization must be additionally implemented in order to ensure the reduction of contaminants and uniform purity of the produced crystals. The potassium content criteria of the Li2CO3 purity makes the issue more complicated. Lithium and potassium belong to the same group of the Periodic Table, have the same ionic charge, and exhibit similar chemical properties. The potassium contamination (on the ppm level) in commercial products would be obvious, but separating K from Li compounds is challenging. Here, crystallization techniques could be more successful than chemical separation. Potassium has a smaller probability of being incorporated into the crystalline structure due to its larger ionic radius of K+ (1.38 Å) in comparison to that of Li+ (0.59 Å) [8].
CUP’s experience of growing LMO crystals using the conventional Cz method showed that a potassium segregation factor of about 50 could be achieved [3]. Crystals with 40K levels of about 10 mBq/kg were produced from the initial mixture (Li2CO3 + MoO3) with 40K at about 500 mBq/kg. The LMO crystals with an acceptable level of <2 mBq/kg of 40K were synthesized using initial materials with potassium content below 100 mBq/kg. For the LMO crystals grown with the LTG-Cz, the segregation factors for potassium were at most a factor of ten, so successive double crystallization was required to reach a few mBq/kg level [26].
The same tendency was observed for 226Ra removal with crystal growing. The upper limit of 3.3 mBq/kg was found for all grown crystals produced from initial materials with different purities (from <100 to 1,000 mBq/kg level) using the conventional Cz method. To reach a segregation factor of ten or higher, double LTG-Cz growing was also required for 226Ra removal. For both techniques, a much stronger segregation effect (a few orders of magnitude) was observed for Th and U, which have a much larger ionic radius and different chemical properties. Despite the purity level of the initial material mixture (from <100 to 1,000 mBq/kg level), the grown crystals had Th and U contents that were below 15 ppt (<0.06 mBq/kg).
High segregation factors benefit the conventional Czochralski technique that allows the use of initial materials with radiopurity at the Bq/kg level. At the same time, the grown crystal ingot is only about 30% of the initial material charge, and the other 70% of the material remains in the residual melt and collects the impurities. High contamination of the residual melt makes the extracting and recycling of expensive enriched 100MoO3 more difficult, while lithium is discarded due to low extraction efficiency. To alleviate the 100MoO3 extraction process and reduce lithium losses, the residual melt could be reused several times in a growing cycle (requires using highly pure initial materials). Compared to the conventional Czochralski technique, the LTG-CZ method has a high crystallization efficiency for the grown ingot, as high as 80% of the initial charge. Such a high crystallization rate affects the segregation efficiency, so the LTG-Cz method is sensitive to the purity of initial materials. To balance the materials recycling routine and ensure the AMoRE-II crystals’ radiopurity and uniformity regardless of the crystallization method, 40K levels below 100 mBq/kg and Th/U levels of several mBq/kg in precursor materials are acceptable.
To fulfill the AMoRE-II needs for the production of the crystals, about 150 kg of this ultra-high-purity (better than 99.99%) lithium carbonate powder is required. The Li2CO3 powder used for AMoRE-I crystal synthesis is from stock, and the production technology has been decommissioned. To find a suitable one, several commercially available high-purity Li2CO3 powders were selected for further radiopurity investigation. The study addressed the sensitive HPGe and ICP-MS radioassay screening and selecting commercial lithium carbonate samples used in the AMoRE-II crystal production. Also, the first attempts at lithium carbonate purification at CUP are described. This paper is structured as follows: methods used for radiochemical analysis of lithium compounds and materials used are described in Section 2. The results of intensive screening of commercially available Li2CO3 carbonate powders are presented in Section 3. Section 4 describes the technique of Li2CO3 purification using the carbonization method. In Section 5, we describe the method of Li2CO3 purification through the lithium formate, LiHCO2, fractional recrystallization. Finally, Section 6 provides the conclusion and discussion of the results.
Sample preparations and ICP-MS measurements were performed in class 1,000 cleanrooms (ISO 6). Quantitative chemical analyses were performed using an Agilent 7900 ICP-MS at CUP [28] and HR-ICP-MS at SEASTAR [29]. The radioactivity levels were measured with two 100% relative efficiency HPGe detectors at Y2L (Canberra Coaxial detectors named CC1 and CC2) [28, 30]. From the 232Th decay chain, the 228Ac activity was assumed to be in equilibrium with 228Ra, and the 212Pb and 208Tl activities were assumed to be in equilibrium and representative of (with branching-ratio correction) 228Th. From the 238U decay chain, the 214Pb and 214Bi activities were measured to represent the 226Ra activity.
Compressed 99.999% CO2 gas was purchased from the local market. Formic acid 88+% used for lithium formate recrystallization and ammonium bicarbonate (99%, for analysis) used for final synthesis, were purchased through Alfa Aesar®. Millipore® 18.2 MΩ cm deionized water was used for dilutions, sample preparation, etc. All labware was made of high-purity quartz or PTFE and, before use, was cleaned in 10% HNO3 solution under 60°C with sonication, rinsed with deionized water three times, and stored filled with water.
For the carbonization method, Li2CO3 powder was dissolved in deionized water under an overpressure of CO2 gas (∼1 atm) in a 6,000 mL pressure vessel that was equipped with an inlet for gas supply and an outlet for the pressure release. During the dissolution, a continuous intense agitation was applied to saturate the mixture with gas and force the process. After the complete dissolution, the lithium bicarbonate LiHCO3 solution (∼1.2 mol L-1) was heated with stirring to 90°C. Once the first crystals of Li2CO3 appeared and the solution became cloudy, the hot mixture was filtered through a membrane 0.1 µm pore size PTFE filter (Advantec®). Then, the filtered solution was forwarded to the final decarbonization procedure. The solution was continuously heated with stirring at the boiling temperature to force the formation of insoluble lithium carbonate powder. The filtered powder was washed with hot water and dried at 150°C.
The lithium carbonate powder was dissolved in about 50% formic acid at 90°C for the lithium formate recrystallization method. The saturated at 95°C lithium formate solution was cooled down to room temperature slowly in an oven for 24 h. The crystals were filtered out and dried at 150°C to check the crystallization efficiency. For the second and third steps of recrystallization, the dried powder obtained in the previous step was dissolved in water at 95°C until saturation, the pH of the solution was adjusted to be slightly acidic, and the crystallization procedure was applied as described above. The mother solution was collected separately in each step and was not reused. Crystals obtained after the third recrystallization step were dissolved in water until saturation at 40°C and mixed with ammonium bicarbonate sludge. The mixture was kept at 40°C for 2 h with continuous stirring. The obtained lithium carbonate powder was filtered, rinsed with hot deionized water, and dried at 150°C.
The radioassay program began with an analysis of the lithium carbonate powder used for the production of AMoRE-I LMO crystals, which was provided from old stocks of the NIIC. The powder was produced several decades ago at the Novosibirsk Rare Metal Plant (NRMP) under USSR purity standard TU 6-09-3728-83. The spodumene pegmatites from the Zavitinskoe deposit were used as raw material [31, 32]. After the depletion of the Zavitinskoe deposit from its subsequent closure, the only source of lithium carbonate in Russia is Chilean lithium of the technical grade. Recent NRMP [33] is a private company that produces lithium carbonate powders with a purity better than 99%, among many other lithium compounds. The company uses the imported lithium sources of technical grade and applies purification methods adopted for the initial material’s composition [31].
At CUP, we extensively tested Li2CO3 powder (TU 6-09-3728-83) preserved from the old NIIC stock and compared it with the powders produced at the NRMP (Table 1). As the highest purity grade available, pharmaceutical grade powder was selected. To better understand the latest production chain, LiOH of technical grade, the initial material for Li2CO3 production at the NRMP, was tested at the same time. The old powder, produced from the spodumene ore and used in AMoRE-I, showed excellent radiopurity that met the AMoRE-II requirements. The 40K activity was below 11.5 mBq/kg, and progenies’ activities from Th/U chains were below 2 mBq/kg. ICP-MS confirmed the levels of 232Th and 238U at about 0.1 and 0.2 ppb, respectively. All other tested chemical impurities were below 1 ppm level. The potassium content in the recently produced pharmaceutical-grade powder was slightly higher but still acceptable, while B, Ba, Ca, Mg, Fe, and Na concentrations were over 1 ppm. The use of initial technical lithium hydroxide, originating from brines, explains the comparatively higher contamination. A226Ra activity at about 3 Bq/kg, which is much too high for AMoRE-II, was found in the powder. Relatively lower 226Ra activity in the raw LiOH indicated that the Ra contamination occurred during manufacturing, specifically in a lime process. The lime (CaO) process is a procedure in which many impurities can find their way into lithium products, notably radium, which commonly occurs in limestone. As an early outcome of the study, we found that potassium and radium activities are the limiting criteria in selecting commercial Li2CO3 for low-background experiments.
Exploring the Certificate of Analysis (CoA) provided by company producers is an unprofitable way to find suitable low-radioactive lithium carbonate powder among commercially available products. Since the usual CoA does not provide information on radioactivity, every product must be tested with HPGe and ICP-MS on-site. As the next target of our investigation, the Puratronic® 99.998% (metal basis excluding Ca; Ca <20 ppm) lithium carbonate from Alfa Aesar® was examined. The ICP-MS analysis of several powders purchased from Alfa Aesar® (now Thermo Fisher Scientific™) (Korea) in different years and preserved at CUP chemical stock had purities that satisfied the AMoRE-II requirements. The K and Na concentrations were about 1 ppm, and the Ca content was at most 5 ppm. Tens of ppt levels for Th and U and ppb levels for all other tested impurities were found in tested powders purchased in 2016, 2018, and 2021.
The radiopurity examination with the HPGe was only performed for powders purchased in 2016 and 2021 (Table 2). The amount of powder purchased in 2018 was insufficient for a sensitive HPGe analysis. A226Ra activity of about 30 mBq/kg was found in the 2021 powder, significantly higher than in the 2016 powder. For reference, a 700 mBq/kg 226Ra activity was reported in [26] for the same brand-name product. Despite the relatively high 226Ra activity, several LMO crystals were grown at CUP using the 2021 Li2CO3 powder. These crystals had a yellowish color and were unsuitable for use in the experiment. The coloration of the crystals could not be caused by impurities from molybdenum since the molybdenum oxide was purified at CUP, and its purity was confirmed [27]. With extensive ICP-MS and HPGe analysis of Li2CO3, we did not find any contaminants at the levels over a few ppm, which may explain the yellowish color of the crystals. Organic carbon-containing impurities could be a reason for that. As the radiopurity of the powder could differ within a few orders of magnitude from lot to lot, and obtaining 150 kg of the powder from a single lot tested in advance was impossible, we decided not to use this powder.
Several 99.999% Li2CO3 powders from three different producers in China were purchased through RNDKOREA [34] and subjected to radioassay. Similar to Alfa Aesar® (Puratronic®) and NRMP (TU 6-09-3728-83) powders, potassium and calcium content in powders A, B, and C was about 1 ppm level. Noticeably high concentrations of Ba were observed in powders B and C, which may indicate a high radium activity. The HPGe analysis confirmed an increasing 226Ra activity in powder with a rising Ba concentration (Figure 1). For powders with a Ba concentration of over 10 ppm, 226Ra activity was over 100 mBq/kg. In powders from Alfa Aesar, NRMP TU 6-09-3728-83, and A, barium concentration varied around 0.1 ppm level, while 226Ra ranged from one to sixty mBq/kg.
Among those tested with ICP-MS and summarized in Table 1, the purest product was found to be powder A from the Chinese market. Relatively to other Chinese products, the lowest Th and Ra levels were measured in powder A, while U contamination was noticeably higher. The radioactivity levels presented in Table 2 showed that the 226Ra activity level fluctuated the most for all tested high-purity powders. Summarizing all powders tested with our extended radioassay program, preliminary concerns about potassium contamination in commercial lithium carbonate powders were not confirmed. However, no suitable powder among the tested commercial products was found. Unacceptable 226Ra and slight Th and U contaminations led us to conclude the need to develop a purification strategy.
Due to its physical and chemical properties, lithium carbonate cannot be purified with sublimation or fractional recrystallization. To be purified, the lithium carbonate must be converted into soluble salts like nitrate, chloride, bicarbonate, oxalate, and formate. Then, the purified salt must be converted back into carbonate. Our first attempts to purify lithium nitrate using MnO2-based sorbent and recrystallization [35] showed high Ra and Th removal. Unfortunately, the final product was cross-contaminated with uranium (about 100 ppt) leached from the sorbent, and the final conversion into carbonate form was complicated and required additional ammonium bicarbonate (NH4HCO3) chemical.
Another method to produce pure lithium carbonate involves the purification of lithium bicarbonate (LiHCO3) solution. Initially, dirty Li2CO3 is dissolved in water under CO2 gas bubbling to make LiHCO3 solution (carbonation). At temperatures over 60°C LiHCO3 decomposes, releasing back Li2CO3 solid and CO2 gas. The utilization of pure CO2 gas eliminates the problem of the introduction of impurities with NH4HCO3. The method is well-known and widely used in lithium manufacturing [36, 37].
A co-precipitation step was introduced into the procedure to remove mechanical and insoluble impurities and, if possible, improve the final product’s purity. As explained above, the Alfa Aesar® 2021, TU and Pharma grade NRMP, and A (from China) lithium carbonate powders were treated with the carbonization technique. Produced Li2CO3 powders were tested with ICP-MS, and Ba reduction was used as an indicator of possible radium removal (Table 3). A high decontamination effect was observed in tested powders for alkalis (K, Na, and Cs), B, Al, Fe, Pb, Ti, V, and U, resulting in satisfactory levels. It is important to note that the uranium reduction was significantly better, to the level below 10 ppt, for the powders with initial U content below 0.2 ppm. For the Pharma NRMP powder, the initial uranium concentration of about 2 ppb was reduced only by a factor of two, resulting in 1 ppb level. Weakened U reduction in Pharma grade powder might be explained by the influence of comparatively high calcium content and the formation of soluble calcium-uranyl carbonate complex compounds [38]. No reduction or only slight contamination with thorium was expected for the final products. In the presence of carbonate anions in the solution, thorium forms stable soluble complexes that are not filterable with a small amount of co-precipitate but partially or fully absorbed on the surface of the final product during final synthesis [39].
As with Th and U, alkaline earth Mg, Ca, Sr, and Ba concentrations increased slightly in the final products. Despite their relatively higher concentrations, the solubility constants were not reached, and the species were presented in the solution in colloidal nonfilterable form. They were partially adsorbed on the final product’s surface. Because of its similar chemical properties, we doubted the possibility of radium separation and did not apply the HPGe measurement.
Due to the chemical form of the impurities in the bicarbonate solution, the carbonization combined with the co-precipitation method was found inefficient for removing Th, U, and Ra. Implementing column chromatography might improve their separation. However, deep, extensive R&D is required to find a proper sorbent material to extract Th, U, and Ra from their stable complex compounds in the lithium bicarbonate solution. The method could not be used alone but might be involved as a final step in combination with other techniques.
Lithium formate, LiHCO2, was selected as the next candidate for further purification experiments. This is a salt of formic acid, has a high difference in solubility at different temperatures, and might be converted into carbonate via thermal decomposition. The powder B (5N grade from the Chinese market) was selected as the initial material for the test. The radioactivity reduction for this product would be easily tracked with HPGe step-by-step. Still, it will not require many repetitive recrystallization steps to reach the lowest level possible for the selected technique.
Since the LiHCO2 solubility in water at room temperature (∼28%) is lower than that at 98°C (∼57%) by a factor of two [40], about 50% recovery efficiency for a single step was reached. Due to the high solubility of LiHCO2 even in cold water (∼24% at 0°C), crystals separated from the mother solution were not rinsed and subjected to the next recrystallization steps. Three successive steps were performed, and the resulting LiHCO2 monohydrate crystals were individually assayed by ICP-MS. The radioactivity reduction was tested by HPGe measurements of the lithium formate crystals obtained after the third recrystallization step and the final Li2CO3 product (Table 4).
ICP-MS analysis confirmed for the first recrystallization step a reduction of K, Ba, and Th by two orders of magnitude and Al and Sr by one order of magnitude. The second recrystallization step improved the Ba and Sr removal by one more order of magnitude, while the third step was nearly inefficient. With the three steps, 232Th and 238U concentrations in LiHCO2 were lowered below 6 ppt, and Ba was reduced by a factor of over a thousand. The 226Ra activity was reduced by two orders of magnitude, resulting in 3.5 ± 1.1 mBq/kg. With successive triple recrystallization of lithium formate, a nearly satisfactory purity was achieved, and the next step was to convert the pure LiHCO2 crystals into final Li2CO3 powder.
Lithium carbonate powder was produced from lithium formate through its thermal decomposition [41]. At 290°C, lithium formate decomposes with the formation of lithium carbonate and the release of CO and H2 gases. About 50 g of powder was heated with a pure air supply to avoid the carbon black formation during decomposition. However, at about 270°C, the powder melted, limiting the air access to the volume [42]. Further slow heating caused the intensive formation of carbon black. It was found impossible to avoid LiHCO2 melting, and lithium carbonate was being synthesized by the interaction of lithium formate and ammonium bicarbonate sludge, according to the reaction:
Due to the relatively high solubility of Li2CO3 in formate-based solutions, a maximum 40% recovery efficiency was reached. The purity of the ammonium bicarbonate involved in the final production step and the purity of the final lithium carbonate powder were tested and shown in Table 4. Relative to the third recrystallized LiHCO2, the concentration of Al, K, Sr, Ba, Pb, and Th, and the activity of 226Ra increased several times. The ammonium bicarbonate used in the synthesis was comparatively pure, and the contamination was caused by partial or complete co-precipitation of impurities with the synthesized lithium carbonate.
A total decontamination factor of about 20 was obtained for potassium, 10 for thorium, and 50 for radium in synthesized Li2CO3 powder, resulting in near-desirable purity. The inefficient synthesis of the final product, which needs an additional chemical, led us to continue the investigation.
Recently, lithium carbonate has been extensively used as the initial material for producing cryogenic bolometers. Low-background conditions of the experiments require extraordinary specifications for the radiochemical purity of the lithium carbonate precursor. A40K level below 100 mBq/kg, Th/U, and Ra at several mBq/kg, and all other chemical impurities below 1 ppm level in precursor materials would be acceptable for crystal production. Eight different commercial products of high purity (better than 99.99% purity grade), purchased from different sources and manufacturing lots, were tested to find a possible candidate for AMoRE-II crystal synthesis. Among tested Li2CO3 powders, no products with the required purity were found. High radium and slight Th/U contamination were observed, and the contamination level varied for different lots of the same brand-name product. Several purification techniques were tested at CUP in order to produce material with the required purity.
Simply performance-wise, carbonization combined with co-precipitation effectively removed mechanical impurities, alkali, transition, and heavy metal contamination to the required level but was inefficient in the removal of alkali earth metals, Th, and U. The chemical formula of these species in the bicarbonate solution made their sorption and extraction complicated and challenging. This method could not be exploited alone, but it could be the finishing step in the multistep purification technology.
Fractional recrystallization of lithium formate showed high Ra and Th reduction, resulting in satisfactory purity after three successive recrystallization steps. Further synthesis of lithium carbonate from purified formate was inefficient and complicated, requiring a large amount of additional ammonium bicarbonate, and the final product has moderate contamination. The same problem was met in our early study [35] of lithium nitrate purification.
We have been searching for new ways to produce the high-purity, low-background lithium carbonate precursor for AMoRE-II crystal synthesis. Column chromatography, nano and ultrafiltration, and sorption methods are being tested to find an efficient technique for removing Th, U, and Ra from the lithium compounds. The measurements and purification methods presented in this article have high importance for radioanalytical chemistry applied for low-background physics aiming for a “zero” background.
The original contributions presented in the study are included in the article/supplementary material, further inquiries can be directed to the corresponding author.
KS: Investigation, Writing–review and editing. CB: Validation, Writing–review and editing. JC: Formal Analysis, Writing–review and editing. OG: Conceptualization, Investigation, Methodology, Writing–original draft, Writing–review and editing. YK: Validation, Writing–review and editing. YdK: Funding acquisition, Project administration, Writing–review and editing. EL: Formal Analysis, Writing–review and editing. ML: Supervision, Writing–review and editing. HY: Investigation, Validation, Writing–review and editing.
The author(s) declare financial support was received for the research, authorship, and/or publication of this article. This work was supported by the Institute for Basic Science (IBS), funded by the Ministry of Science and ICT, Korea (Grant id: IBS-R016-D1).
The authors are pleased to acknowledge the support of the SEASTAR™ analytical laboratory for performing HR-ICP-MS analysis of the samples.
The authors declare that the research was conducted in the absence of any commercial or financial relationships that could be construed as a potential conflict of interest.
All claims expressed in this article are solely those of the authors and do not necessarily represent those of their affiliated organizations, or those of the publisher, the editors and the reviewers. Any product that may be evaluated in this article, or claim that may be made by its manufacturer, is not guaranteed or endorsed by the publisher.
1. Bandac IC, Barabash AS, Bergé L, Borovlev YA, Calvo-Mozota JM, Carniti P, et al. Li2100deplMoO4 scintillating bolometers for rare-event search experiments. Sensors (2023) 23(12):5465. doi:10.3390/s23125465
2. Armengaud E, Augier C, Barabash A, Bellini F, Benato G, Benoît A, et al. Precise measurement of 2νββ decay of 100Mo with the CUPID-Mo detection technology. Eur Phys J C (2020) 80:674. doi:10.1140/epjc/s10052-020-8203-4
3. Son JK, Choe J, Gileva O, Hahn I, Kang W, Kim D, et al. Growth and development of pure Li2MoO4 crystals for rare event experiment at CUP. J Instrumentation (2020) 15:C07035. doi:10.1088/1748-0221/15/07/C07035
4. Augier C, Barabash A. S., Bellini F., Benato G., Beretta M., Bergé L., et al. Final results on the 0vbb decay half-life limit of 100Mo from the CUPID-Mo experiment. The Eur Phys J C (2022)(82) 1033. doi:10.48550/arXiv.2202.08716
5. Abdelhameed A, Angloher G, Bauer P, Bento A, Bertoldo E, Bucci C, et al. First results on sub-GeV spin-dependent dark matter interactions with 7Li. Eur Phys J C (2019) 79:630. doi:10.1140/epjc/s10052-019-7126-4
6. Coron N, Cuesta C, García E, Ginestra C, Gironnet J, de Marcillac P, et al. Neutron spectrometry with scintillating bolometers of LiF and sapphire. IEEE Trans Nucl Sci (2016) 63:1967–75. doi:10.1109/TNS.2016.2561280
7. Aliane A, Avetissov ICH, Barinova OP, de la Broise X, Danevich FA, Dumoulin L, et al. First test of a Li2WO4(Mo) bolometric detector for the measurement of coherent neutrino-nucleus scattering. Nucl Instr Methods Phys Res Section A: Acc Spectrometers, Detectors Associated Equipment (2020) 949:162784. doi:10.1016/j.nima.2019.162784
8. Haynes WM, Lide DR, Thomas J, Bruno . CRC handbook of chemistry and physics: a ready-reference book of chemical and physical data. Boca Raton, Florida: CRC Press (2016).
9. Rahaman S., Elomaa VV, Eronen T, Hakala J, Jokinen A, Julin J, et al. Q values of the 76Ge and 100Mo double-beta decays. Phys Lett B (2008) 662(2):111–6. doi:10.1016/j.physletb.2008.02.047
10. Dell Oro S. Neutrinoless double beta decay: expectations and uncertainties. Nucl Part Phys Proc (2015) 265–6. 31-33. doi:10.1016/j.nuclphysbps.2015.06.008
11. Arnold R. (NEMO-3 collaboration). Results of the search for neutrinoless double-β decay in 100Mo with the NEMO-3 experiment. Phys Rev D (2015) 92:072011. doi:10.1103/PhysRevD.92.072011
12. Alenkov V, Aryal P, Beyer J, Boiko RS, Boonin K, Buzanov O, et al. Technical design report for the AMoRE 0νββ decay search experiment (2015). Available at: https://arxiv.org/abs/1512.05957 (Accessed November 30, 2023).
13. Lee MH. AMoRE: a search for neutrinoless double-beta decay of 100Mo using low temperature molybdenum-containing crystal detectors. J Instrumentation (2020) 15:C08010. doi:10.1088/1748-0221/15/08/C08010
14. Oh Y. AMoRE (2022). [Conference presentation]. May 30 – June 4 NEUTRINO 2022, Virtual Seoul, Korea Available at: https://zenodo.org/record/6683386#.Y_wLRS8RpMQ (Accessed November 30, 2023).
15. Lee JY, Alenkov V, Ali L., Beyer J, Bibi R, Boiko RS, et al. A study of radioactive contamination of 40Ca100MoO4 crystals for the AMoRE experiment. IEEE Trans Nucl Sci (2016) 63(2):543–7. doi:10.1109/TNS.2016.2530828
16. Lee JY, Aryal P, Karki S, Kim HJ, Kim SW, Kim Y, et al. A study of 48deplCa100MoO4 scintillation crystals for the AMoRE-I experiment. IEEE Trans Nucl Sci (2018) 65:2041–5. doi:10.1109/TNS.2018.2818332
17. Kim HB. Result of AMoRE-I. TAUP2023. Austria Aug: University of Vienna (2023). Available at: https://indico.cern.ch/event/1199289/contributions/5445986/attachments/2705064/4696869/TAUP2023_Result_of_AMoRE-I_Experiment_hbkim_v3.pdf (Accessed November 30, 2023).
18. NIIC SB RAS. Nikolaev Institute of inorganic chemistry, siberian branch of Russian academy of sciences (NIIC S SB RAS) (2023). Available at: http://niic.nsc.ru/institute/881-niic (Accessed November 30, 2023).
19. Grigorieva V, Shlegel V, Bekker T, Ivannikova N, Giuliani A, de Marcillac P, et al. Li2MoO4 crystals by low-thermal-gradient Czochralski technique. J Mater Sci Eng B (2017) 7(3-4):63–70. doi:10.1016/j.jcrysgro.2020.125913
20. Berge L, Boiko RS, Chapellier M, Chernyak DM, Coron N, Danevich FA, et al. Purification of molybdenum, growth and characterization of medium volume ZnMoO4 crystals for the LUMINEU program. J Instrumentation (2014) 9:P06004. doi:10.1088/1748-0221/9/06/P06004
21. Kim Hb , Ha DH, Jeon EJ, Jeon JA, Jo HS, Kang CS, et al. Status and performance of the AMoRE-I experiment on neutrinoless double beta decay. J Low Temperature Phys(2022) 209:962–70. doi:10.1007/s10909-022-02880-z
22. Kim WT, Kim SC, Sharma B, Jeon JA, Kim HL, Kim SG, et al. Test measurements of an MMC-based 516-g lithium molybdate crystal detector for the AMoRE-II experiment. J Low Temp Phys (2022) 209:299–307. doi:10.1007/s10909-022-02832-7
23. Kim YD. AMoRE (2019). [Conference presentation]. NEPLES-2019, KIAS, Seoul, Korea Available at: https://indico.cern.ch/event/803690/contributions/3572814/attachments/1917092/3169927/neples-ydkim.pdf (Accessed November 30, 2023).
24. Kim G Low background study for AMoRE through material screening facility at Y2L and Yemilab (2022). [Conference presentation]. LRT 2022, South Dakota Mines, USA https://indico.sanfordlab.org/event/29/contributions/397/attachments/359/880/LRT2022_GWKim.pdf (Accessed November 30, 2023).
25. Barinova OP, Cappella F, Cerulli R, Danevich FA, Kirsanova SV, Kobychev VV, et al. Intrinsic radiopurity of a Li2MoO4 crystal. Nucl Instr Methods Phys Res Section A: Acc Spectrometers, Detectors Associated Equipment (2009) 607(3):573–5. doi:10.1016/j.nima.2009.06.003
26. Armengaud E, Augier C, Barabash AS, Beeman JW, Bekker TB, Bellini F, et al. Development of Mo-containing scintillating bolometers for a high-sensitivity neutrinoless double-beta decay search. Eur Phys J C (2017) 77:785. doi:10.1140/epjc/s10052-017-5343-2
27. Yeon H, Choe J, Gileva O, Hahn KI, Kang WG, Kim GW, et al. Preparation of low-radioactive high purity enriched 100MoO3 powder for AMoRE-II experiment. Front Phys (2023) 11:1142136. doi:10.3389/fphy.2023.1142136
28. Moo Hyun Lee J. Radioassay and purification for experiments at Y2L and Yemilab in Korea. Phys Conf Ser (2020) 1468:012249. doi:10.1088/1742-6596/1468/1/012249
29. SEASTAR CHEMICALS. SEASTAR CHEMICALS (2023). https://www.seastarchemicals.com/our-development/specialized-analysis/(Accessed November 30, 2023).
30. Sala E, Hahn IS, Kang WG, Kim GW, Kim YD, Lee MH, et al. Development of an underground low background instrument for high sensitivity measurements. J Phys Conf Ser (2016) 718:062050. doi:10.1088/1742-6596/718/6/062050
31. Melentiev GB, Yurgenson GA, Delitzyn LM. Prospects and priorities for the reconstruction and development of lithium mining production on the basis of domestic raw materials. IOP Conf Ser Earth Environ Sci (2022) 962:012055. doi:10.1088/1755-1315/962/1/012055
32. Richard ML. Mineral industries of the U.S.S.R paperback – january 1, 1988 (1988), International Review. (Washington: US Department of the Interior, Available at: https://d9-wret.s3.us-west-2.amazonaws.com/assets/palladium/production/mineral-pubs/country/1994/9434094.pdf (Accessed November 30, 2023).
33. Novosibirsk Rare. Novosibirsk rare metal plant (2023). http://cesium.ru (Accessed November 30, 2023).
34. RNDKOREA. RNDKOREA (2023). http://www.rndkorea.co.kr (Accessed November 30, 2023).
35. Gileva O, Aryal P, Choe JS, Kim Y, Kim Y, Lee EK, et al. Purification of lithium carbonate from radioactive contaminants using a MnO2-based inorganic sorbent. Inorganics (2023) 11(10):410. doi:10.3390/inorganics11100410
36. EUROPEAN PATENT SPECIFICATION. Patent ep 1 037 854 B1. Process for the purification of lithium carbonate (2005). Available at: https://patentimages.storage.googleapis.com/dd/bf/19/0c0422d1245c14/EP1037854B1.pdf (Accessed November 30, 2023).
37. Han B, Rana Anwar UH, Louhi-Kultanen M. Lithium carbonate precipitation by homogeneous and heterogeneous reactive crystallization. Hydrometallurgy (2020) 195:105386. doi:10.1016/j.hydromet.2020.105386
38. Bernhard G, Geipel G, Reich T, Brendler V, Amayri S, Nitsche H. Uranyl (VI) carbonate complex formation: Validation of the Ca2UO2(CO3)3(aq.) species. Radiochimica Acta (2001) 89(8):511–8. doi:10.1524/ract.2001.89.8.511
39. LaFlamme BD, Murray JW. Solidsolution interaction: the effect of carbonate alkalinity on adsorbed thorium. Geochimica et Cosmochimica Acta (1987) 51(2):243–50. doi:10.1016/0016-7037(87)90235-3
40. Seidell A. Solubilities of inorganic and metal organic compounds. 3ed. New York: D. Van Nostrand Company (1940). 900–1. 1.
41. Meisel T, Halmos Z, Seybold K, Pungor E. The thermal decomposition of alkali metal formates. J Therm Anal (1975) 7:73–80. doi:10.1007/BF01911627
Keywords: Li2CO3, ultra-low radioactivity, purification, ICP-MS, HPGe
Citation: Shin K, Byeon C, Choe J, Gileva O, Kim Y, Kim Y, Lee E, Lee MH and Yeon H (2024) Selection and purification of Li2CO3 precursor for bolometric double beta decay experiments. Front. Phys. 12:1347162. doi: 10.3389/fphy.2024.1347162
Received: 30 November 2023; Accepted: 06 February 2024;
Published: 26 February 2024.
Edited by:
Frank Franz Deppisch, University College London, United KingdomReviewed by:
Minfang Yeh, Brookhaven National Laboratory (DOE), United StatesCopyright © 2024 Shin, Byeon, Choe, Gileva, Kim, Kim, Lee, Lee and Yeon. This is an open-access article distributed under the terms of the Creative Commons Attribution License (CC BY). The use, distribution or reproduction in other forums is permitted, provided the original author(s) and the copyright owner(s) are credited and that the original publication in this journal is cited, in accordance with accepted academic practice. No use, distribution or reproduction is permitted which does not comply with these terms.
*Correspondence: Olga Gileva, Z2lsZXZhb2xnYUBpYnMucmUua3I=
Disclaimer: All claims expressed in this article are solely those of the authors and do not necessarily represent those of their affiliated organizations, or those of the publisher, the editors and the reviewers. Any product that may be evaluated in this article or claim that may be made by its manufacturer is not guaranteed or endorsed by the publisher.
Research integrity at Frontiers
Learn more about the work of our research integrity team to safeguard the quality of each article we publish.