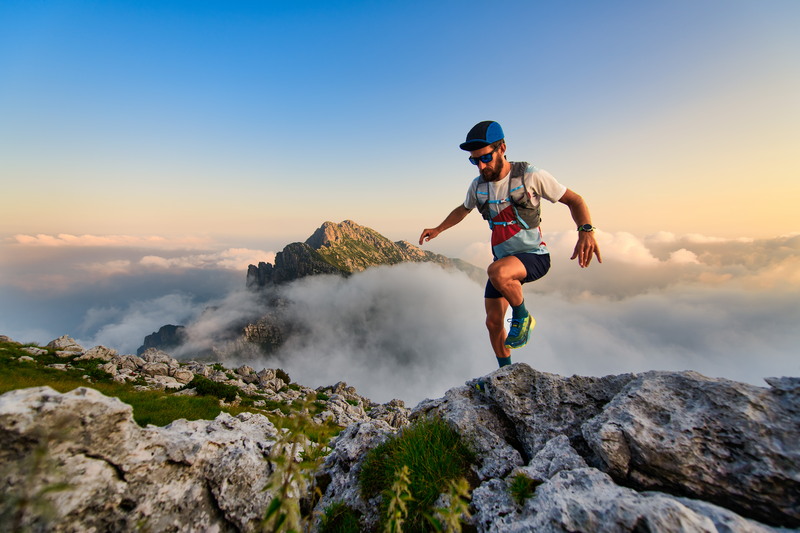
95% of researchers rate our articles as excellent or good
Learn more about the work of our research integrity team to safeguard the quality of each article we publish.
Find out more
BRIEF RESEARCH REPORT article
Front. Phys. , 08 March 2024
Sec. High-Energy and Astroparticle Physics
Volume 12 - 2024 | https://doi.org/10.3389/fphy.2024.1320097
This article is part of the Research Topic Science And Technology In Deep Underground Laboratories View all 19 articles
The Gran Sasso National Laboratory (LNGS) is, at present, the largest deep underground laboratory in operation for astroparticle physics and rare event research. The LNGS was created to carry out this research exploiting an overburden of 1,400 m of rock to reduce the flux of muons from cosmic rays. Operating an underground laboratory and its facilities implies a high level of risk. To mitigate risks at the LNGS, a crucial aspect is represented by the evacuation of people from an underground environment during emergencies. The connection between the underground facilities and the outside infrastructure is limited, and the intervention by rescue teams is complicated. This paper reports the study of an adaptive evacuation system to improve the evacuation performance in underground laboratories. The system proposed is composed of a combination of passive, dynamic, and adaptive signage that is able to adapt itself to lead the laboratory occupants to the safe location for evacuation (assembly point). The system collects information from all safety plants, and the data are processed using a customized path-finding algorithm. In the computational algorithm, the underground laboratory is represented as a grid, and the customized path-finding algorithm discovers all available paths to reach the identified evacuation assembly point.
The Gran Sasso National Laboratory (LNGS) is located between the towns of L’Aquila and Teramo in Italy [1]. The LNGS has two sites: an underground facility along the highway tunnel connecting Teramo to L’Aquila and a surface headquarters on the L’Aquila side. The underground complex consists of three huge experimental halls (each 100 m long, 20 m wide, and 18 m high) and bypass tunnels, for a total volume of about 180,000 m3. The access to the experimental halls is horizontally provided by the highway tunnel. The halls are outfitted with all the technical and safety equipment plus monitoring systems necessary for experimental activities, as well as ensuring proper environmental conditions for the people involved. The main hazards are due to fire (inside the laboratory or outside in the highway tunnel), oxygen deficiency, and earthquakes. Based on these hazards, an internal emergency plan has been developed with three defined evacuation assembly points. Assembly point #1 is the default assembly point, but other assembly points may be more appropriate depending on the emergency scenario. During an emergency situation, part of the laboratory may be not accessible; moreover, the hazard may evolve over time, such as during a fire event. In such circumstances, a static evacuation sign may not help people evacuate in the most effective and efficient manner, especially considering people who may not be very familiar with the local environment.
In this paper, we present an evacuation algorithm that is adaptive to specific dynamic situations in case of an emergency, where real-time environmental data are automatically gained from the safety alarm systems. The underground laboratory and the evacuation assembly points are shown in Figure 1.
Evacuation strategies have already been studied for different risk scenarios. The work in [2] presents a tsunami evacuation strategy; [3] evaluates an adaptive evacuation system that monitors situations in real time and controls the evacuation route dynamically, applicable to large underground areas; and [4] proposes an algorithm that minimizes the total evacuation time of all evacuees for multi-exit buildings.
The main hazard at the LNGS is fire inside the laboratory or in the highway tunnel. In the event of a fire, there is only a short window of time available for evacuation to the designated safe assembly point. In the area or compartment which is directly affected by fire, only few minutes are available after the alert to evacuate the zone. Indeed, smoke from fire can quickly cause reduced visibility making it difficult for people to safely evacuate the area. Moreover, toxic substances generated by combustion, such as carbon monoxide or hydrocyanic acid, are harmful for people and may affect their perception. Another possible danger is an oxygen deficiency hazard (ODH), since in the Gran Sasso laboratory, a number of experimental facilities make use of large quantities of cryogenic liquids and the associated boil-off gas. Other types of danger exist, such as spills of water or dangerous substances and natural events such as earthquakes.
According to the LNGS emergency plan, three evacuation assembly points are defined (assembly point #1, assembly point #2, and assembly point #3). Only one assembly point is designed during an evacuation. Assembly point #1 is the default one, but the emergency team can decide to change the evacuation assembly point after assessing the situation. In addition, we underline that having a clear evacuation route during an emergency is critical in an underground environment since the connection between underground facilities and outside infrastructure is limited.
Static evacuation systems are unable to react to temporary events and may guide the occupants directly to the hazard in the worst case or to the wrong assembly point.
Due to the complexity of the LNGS structure, an adaptive evacuation system offers the advantage of optimizing the escape routing according to the development of the hazardous situation, routing people to a safe escape path and reducing the evacuation time.
The system proposed in this work combines passive and adaptive signs that adapt based on information from an array of safety sensors to lead laboratory occupants to the designed assembly point. The system is an intelligent system able to get information from safety plants. At the LNGS, there are many safety monitors with sensors for detecting fire, gas, and leaking liquid, as well as safety PLC systems, etc. The system collects all the information from the alarm panels and analyzes it to determine the location and intensity of the event. In the computational algorithm, the underground laboratory is represented as a grid, with nodes that are updated in real time to reflect areas that may be not accessible due to a critical event. According to the resulting grid, a customized path-finding algorithm will discover all safe paths to reach the identified evacuation assembly point. The results of this computation is communicated to the field elements (dynamic emergency and evacuation signs), providing occupants the exit route based on the best available information at the time. The system workflow is represented in Figure 2.
In order to develop the algorithm to determine an adaptive evacuation route, we represent the underground laboratory as a weighted grid. Each node (or vertex) is positioned at every change of direction or any decision point in the escape route. Each edge (or link between two nodes) has an associated weight, which represents the path length (in meters) between two nodes. Paths may be assigned a correction factor to define a preferred evacuation path according to various criteria. For example, the weight is increased to minimize the usage of the experimental hall as an evacuation route or to reduce the number of firefighting lobbies crossed during the evacuation. The calculation begins with all possible starting nodes and changes weights as the situation evolves. The resulting grid is a grid where all possible starting vertices, intermediate vertices, and final vertices are determined to perform the calculation. In our case, any node (except the final assembly point nodes) may be a starting node or an intermediate node since people may be located in any part of the laboratory. The baseline grid (without any emergency scenario) is represented in Figure 3.
FIGURE 3. Representation of the Gran Sasso underground laboratory as a weighted grid as the input for the computational algorithm for evacuation path finding.
The LNGS has access to nine fire compartments. A fire compartment is a confined section of the laboratory that is isolated in case of a critical event inside it to prevent its propagation to other areas. Each fire compartment is controlled by a dedicated fire control panel connected to several field detection and extinguishing systems as part of active fire protection. Each control unit generates a “fire alarm in the compartment” and implements both the local and remote signaling procedures and automatic fire extinguishment in the zones where it is foreseen. Moreover, each fire control panel controls the firefighting lobby doors of its fire compartment. In case of fire, the air ventilation stops, all fire dumpers and doors close, and all firefighting lobbies are pressurized by the nearest compartment’s air. This implementation allows all nine compartments to be isolated in case of fire by exploiting the 27 firefighting lobbies. Personnel will not be allowed into the area that triggered the emergency, nor will that area be available for the evacuation route.
The evacuation route algorithm is based on Dijkstra’s algorithm for undirected weighted graphs [5]. Dijkstra’s algorithm is an algorithm to find the shortest path between nodes in a weighted graph. In our implementation, Dijkstra’s algorithm is reiterated until every node of the graph is part of the solution. The process begins with the baseline grid that has no access restrictions, as described previously. The initial graph is the resulting graph without any compartment denied by the access that has been presented in paragraph 5. The final node is the assembly point designated for that evacuation. The graph is updated in real time according to the latest events detected.
The following are the steps of the implemented algorithm:
1) One node is randomly picked as the starting node (not the final node).
2) Dijkstra’s algorithm is run, and the resulting path is identified.
3) Another node which is not in any of the previously identified solutions is run, and step 2 is re-run until all nodes belong to one of the result paths.
4) Step 1 is re-run if the weighted graph has changed. The final result is the best evacuation route identified based on using all the nodes of the graph.
Prototype software is developed using LabVIEW [6] to test the customized algorithm presented in Section 7. Based on the restricted (emergency) area and the designated assembly point, the software generates all possible evacuation solutions, and analysis of the solutions indicates a clear advantage when using adaptive versus static systems. Figure 4A shows the current static system compared to one evacuation route coming from the adaptive system (Figure 4B); this scenario is one of all the possible emergency scenarios. In this case, one of the nine fire compartments is denied due to an accident. In this scenario, an emergency situation is presented where part of the laboratory is not accessible, and the evacuation assembly point remains the default one. The adaptive system calculates all the available paths to reach the assembly point based on the real-time emergency information, while the static system shows evacuation issues near the accident area.
FIGURE 4. Comparison between the actual static evacuation system (A) and the evacuation route generated by the adaptive system for a specific scenario, with the forbidden compartment highlighted by a red cross (B). In (D), the evacuation route from the adaptive system is illustrated for another emergency scenario in which the default evacuation assembly point is inaccessible due to an accident, while in (C), the static evacuation system is depicted.
In other emergency scenarios, where the designated assembly point is not the default one but is another one (assembly points #2 or #3), the advantage of an adaptive system becomes even more relevant, as the static system continues to direct occupants to the default assembly point. At the LNGS, where the evacuation assembly point may change based on emergency assessment as defined in the emergency plan, the use of an adaptive system is crucial despite the existing static system. In fact, the use of the presented adaptive evacuation system provides significant advantages not only in terms of evacuation time but also for better overall performance in terms of the safety and accuracy of the evacuation. For example, in emergency scenarios where the designated evacuation assembly point is assembly point #2, the current evacuation system proves to be entirely inadequate for a proper evacuation. This results in laboratory occupants heading to the default assembly point, which is situated on the opposite side of assembly point #2, with a distance of approximately 400 m between them. Figure 4D shows the evacuation route from the adaptive system for the emergency scenario just described previously, where the main assembly point becomes unavailable due to an accident in close proximity. In this scenario, assembly point #2 is designated for evacuation. The advantage of the adaptive system is evident in the presented scenario, offering a correct evacuation route for occupants, despite the inadequacy of the current evacuation system for this specific case (Figure 4C). Currently, in the event of evacuation to an assembly point other than the default one, occupants can only rely on our voice evacuation system, which is utilized by the emergency team during emergencies.
The system realization is part of a comprehensive recovery project called NextGenerationEU [7], which is funded and currently in the final design phase. The algorithm presented and its solutions are adopted as the input for an industrial adaptive evacuation system that is able to change sign directions according to a set of preconfigured scenarios. Different companies have already developed emergency adaptive evacuation systems. The core of these systems is a central unit that will take care of the scenario changes—evacuation signs are able to change direction or show a red arrow to deny access to a specific area. Different scenarios or sign combinations are activated by closing a pre-determined set of dry contacts in the adaptive system central unit. A specific emergency scenario is described by the type of situation and location (provided by the alarm panels and closed contacts) as well as the chosen assembly point (provided by the emergency team). Communication between all nine alarm panels at Gran Sasso is demonstrated, and logic programming meets the relevant EN 54 European Standards for fire detection and fire alarm systems [8].
In this paper, we present an algorithm to determine an adaptive evacuation route in a complex environment such as the Gran Sasso National Laboratory or any underground laboratory. A static evacuation may not be the best solution in terms of evacuation time and correctness in these peculiar environments. On the contrary, the presented algorithm and the whole implemented evacuation system are able to direct people to the safest evacuation route more quickly than a traditional static system. Moreover, it is able to adapt to changing scenarios and avoid leading people to gather at an inappropriate assembly point or area. Indeed, the evacuation route is calculated based on the current emergency situation obtained from the alarm systems. The presented system is fully integrated with the LNGS safety and security systems and is able to detect an emergency situation and activate the safest evacuation route, avoiding critical and dangerous situations. The tests and performance of the adaptive system based on the presented algorithm are discussed. At the Gran Sasso laboratory, we regularly conduct evacuation drills, simulating various emergency situations to assess both emergency and evacuation management. The presented system will be fully tested during the commissioning phase and evacuation drills to verify the accuracy of evacuations and determine whether there is a need to add monitoring sensors to enhance evacuation performance.
The raw data supporting the conclusion of this article will be made available by the authors, without undue reservation.
PC: validation, software, methodology, conceptualization, and writing–original draft. GB: conceptualization and writing–review and editing.
The authors declare that financial support was received for the research, authorship, and/or publication of this article. This work was supported by the NextGenerationEU, Mission 4 Component 2 Investment 3.1.
The authors declare that the research was conducted in the absence of any commercial or financial relationships that could be construed as a potential conflict of Interest.
All claims expressed in this article are solely those of the authors and do not necessarily represent those of their affiliated organizations, or those of the publisher, the editors, and the reviewers. Any product that may be evaluated in this article, or claim that may be made by its manufacturer, is not guaranteed or endorsed by the publisher.
2. Pratiwi AF, Riyanto SD, Listyaningrum R, Aji GM. The shortest path finder for tsunami evacuation strategy using Dijkstra algorithm. IOP Conf Ser Mater Sci Eng (2020) 854:012035. doi:10.1088/1757-899X/854/1/012035
3. Kasahara Y, Ito A, Tsujiuchi N, Horii H, Kitano K. Evaluation of adaptive evacuation guide sign by using enlarged evacuation simulation at an actual floor plan of underground area. Int J Saf Security Eng (2020) 10(1):35–40. doi:10.18280/ijsse.100105
4. Han L, Guo H, Zhang H, Kong Q, Zhang A, Gong C. An efficient staged evacuation planning algorithm applied to multi-exit buildings. ISPRS Int J Geo-Information (2020) 9(1):46. doi:10.3390/ijgi9010046
6. National Instruments. Design and prototype (2023). Available at: https://www.ni.com/en/solutions/design-prototype.html (Accessed November 9, 2023).
7. European Union. NextGenerationEU (2023). Available at: https://next-generation-eu.europa.eu/index_en (Accessed November 3, 2023).
8. EN 54-1:2021. Fire detection and fire alarm systems – Part 1: introduction (2023). Available at: https://standards.iteh.ai/catalog/standards/cen/1198d5fc-b3d2-48a2-9721-e0dcd3b3772b/en-54-1-2021 (Accessed October 20, 2023).
Keywords: adaptive evacuation route, underground safety, Dijkstra algorithm, decision making, Gran Sasso National Laboratory
Citation: Cavalcante P and Bucciarelli G (2024) An adaptive evacuation system for the Gran Sasso underground laboratory. Front. Phys. 12:1320097. doi: 10.3389/fphy.2024.1320097
Received: 11 October 2023; Accepted: 23 February 2024;
Published: 08 March 2024.
Edited by:
Jeter Hall, SNOLAB, CanadaReviewed by:
Gioacchino Ranucci, Universities and Research, ItalyCopyright © 2024 Cavalcante and Bucciarelli. This is an open-access article distributed under the terms of the Creative Commons Attribution License (CC BY). The use, distribution or reproduction in other forums is permitted, provided the original author(s) and the copyright owner(s) are credited and that the original publication in this journal is cited, in accordance with accepted academic practice. No use, distribution or reproduction is permitted which does not comply with these terms.
*Correspondence: Paolo Cavalcante, cGFvbG8uY2F2YWxjYW50ZUBsbmdzLmluZm4uaXQ=
Disclaimer: All claims expressed in this article are solely those of the authors and do not necessarily represent those of their affiliated organizations, or those of the publisher, the editors and the reviewers. Any product that may be evaluated in this article or claim that may be made by its manufacturer is not guaranteed or endorsed by the publisher.
Research integrity at Frontiers
Learn more about the work of our research integrity team to safeguard the quality of each article we publish.