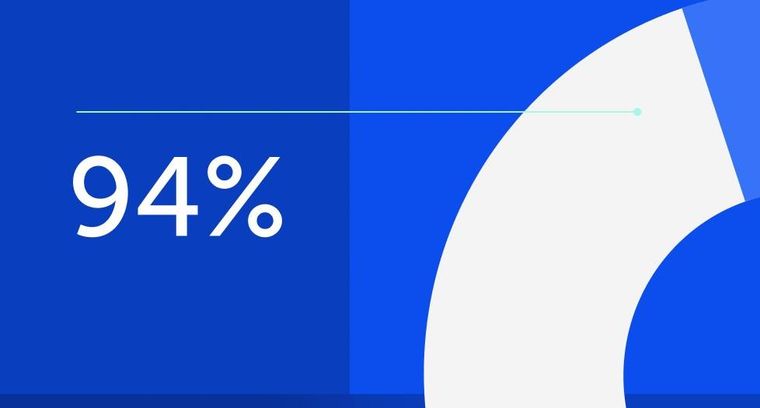
94% of researchers rate our articles as excellent or good
Learn more about the work of our research integrity team to safeguard the quality of each article we publish.
Find out more
ORIGINAL RESEARCH article
Front. Phys., 15 September 2022
Sec. Interdisciplinary Physics
Volume 10 - 2022 | https://doi.org/10.3389/fphy.2022.986501
This study explores the flow irreversibility of the Ellis hybrid nanofluid (containing
At present, the development of the human society depends mainly on energy transfer and energy sources. Improvements with regard to generation and utilization of energy can considerably affect the industrial and engineering fields. Advancements in energy transport mechanisms have been investigated, where the thermal capacitances of the base fluids (water, glycols, and engine oil) are boosted by mixing a nanofluid into them. Nanofluids are widely used for community service applications, such as solar cells, nuclear power plants, refrigerators, heat exchangers, and vehicles. Choi and Eastman [1] first proposed the idea of a nanofluid. Advanced and novel applications of nanofluids in domestic refrigerators, power engines, and chillers were then investigated [2]. The thermal and solutal energy transportation towards a stretching surface in a molybdenum disulfide nanoliquid was studied by Waqas et al. [3]. The heat and mass transport features of Cu- and Ag-water across a porous rotating disc affected by thermal radiation, partial slip, and chemical reactions were examined by Reddy et al. [4]. Krishna and Chamkha [5] surveyed the magnetohydrodynamic (MHD) free convective rotating flow of nanofluids (Ag and TiO2) influenced by the Hall current as well as generation or absorption on a semi-infinite permeable moving plate. The application of the boundary layer flow to nanoparticles along uniform heat flux and heat transport in electronic chips was analyzed by Waqas et al. [6]. Moreover, theoreticians have reported similar studies [6–18]. Hybrid nanofluids are used to enrich the heat transport rates and thermal conductivities of conventional fluids; such hybrid nanofluids are formed by a mixture of nanoparticles immersed in a base fluid to improve the heat transport capacities of the convectional fluids. Turcu et al. [19] and Jana et al. [20] established the idea of hybrid nanofluids that boost the thermal capacitances of regular nanofluids. Devi and Devi [21] presented improved heat transport by distribution of a water-based aluminum oxide (
Chemical reactions are typically categorized into two types as heterogeneous and homogeneous reactions. The processes of burning, fog formation and dispersion, and catalysis occur by such homogeneous and heterogeneous reactions. Homogeneous reactions occur at all phases, while heterogeneous reactions generally occur in confined patches. Chaudhary and Merkin [30] initially proposed the boundary layer flow along the heterogeneous–homogeneous reactions of an isothermal model. Ramzan et al. [31] investigated the electromagnetohydrodynamic hybrid nanofluid flow past two rotating disks along the homogeneous–heterogeneous reaction and its irreversibility analysis. Khan et al. [32] considered the cubic autocatalysis chemical reaction to investigate the flow of magnetized Oldroyd-B fluid across a stretching cylinder. Other investigators have also focused on the influences of the homogeneous–heterogeneous reactions in their recent works [33–38].
The energy losses during an irretrievable process are broadly called as entropy generation. The second law of thermodynamics is considered to measure the energy losses during such irretrievable procedures. Researchers have proposed various approaches to reduce energy losses. The operations of actual systems are unvaryingly related to work losses in accordance with the second law of thermodynamics [39]. Researchers who have investigated entropy generation [40, 41] have deeply analyzed the applications of entropy in several fields. The stagnation point flow of a hybrid nanofluid in the investigation of entropy generation across a stretching sheet was examined by Jakeer and Reddy [42]. Other studies on entropy generation may also be found in literature [43–47].
MHD considerations have many applications in engineering, such as electrical furnaces, nuclear reactors, installation of nuclear accelerators, turbo machinery, and blood flow, and many researchers have investigated their impacts. Ahmad et al. [48] demonstrated the 3D MHD Maxwell nanofluid flow towards a slendering stretching surface affected by joule heating, heat generation, and thermal radiation. Takhar et al. [49] investigated the time-dependent laminar boundary layer flow of an electrically conducting fluid along an aligned magnetic field toward a semi-infinite flat plate. Saeed et al. [50] considered the six-constant Jeffreys nanofluid in an asymmetric channel with inclined magnetic fields to examine the theoretical impact of slip barriers on double diffusion subject to peristaltic flow. The ion and Hall slip impacts on an unstable laminar MHD convective rotating flow of a second-grade fluid across a semi-infinite vertical moving permeable sheet were theoretically investigated by Krishna et al. [51]. Several other researchers [52–59] have also discussed the importance of MHD flows along various geometries.
The main purpose of this work is to explore the 2D boundary layer flow of the Ellis nanofluid (containing
In the mathematical model, we consider a steady 2D laminar incompressible axisymmetric MHD Ellis hybrid nanofluid flow with
The equation of the homo–hetero reaction process is stated as follows [30, 31]:
The first-order isothermal single reaction is stated as
Here,
Using the above assumption and applying the boundary layer theory, the mathematical flow model is defined as [10, 31]
The appropriate conditions at the boundary are as follows [37]:
In Eqs. 3–9, the components of the velocity are
The hybrid nanofluid correlation properties of dynamic viscosity, thermal conductivity, heat capacity, density, and electrical conductivity are defined experimentally.
The applicable similarity variables are as follows [10]:
Using the similarity variables in Eq. 10 and Table 2, Eqs. 4–9 can be rewritten as follows:
The dimensionless forms of the boundary conditions are given as
Assuming that the particles of the substances of both species have the same coefficients of diffusion
The conditions at the boundary are then given as
The governing parameters here are those of the magnetic field
Entropy generation is defined in terms of the magnetic field, joule heating, and viscous dissipation. The equation of entropy generation is as follows:
The entropy generation
where
The numerical solution to the above problem is obtained using bvp4c in MATLAB. Table 3 shows a comparison of the velocity gradient
Figures 2A–D show the impacts of the curvature parameter on the velocity, temperature, homo–hetero reaction, and entropy generation profile. From Figure 2A, it is observed that the fluid velocity profile displays a dual trend with increase in the curvature parameter; for a higher value of the curvature parameter, the fluid velocity near the surface increases, while diminishing away from the boundary. The radius and curvature of the cylinder are inversely proportional; therefore, the radius of the cylinder reduces as the curvature parameter increases. As a result, the contact of the Ellis fluid along the cylinder surface decreases, and the surface supports a small resistance owing to the Ellis fluid particles; further, increasing values of
The
➢ The curvature parameter shows dual behaviors for fluid velocity and entropy generation as the temperature and nanoparticle concentration of the fluid increase.
➢ The momentum boundary layer thickness reduces with stronger estimations of the magnetic and porosity parameters.
➢ The fluid velocity improves with the suction parameter but diminishes for stronger estimation of the material parameter.
➢ The fluid concentration decreases as the surface-catalyzed and homogeneous reaction parameters increase.
➢ The entropy generation profile is improved by the temperature ratio parameter and Brinkman number.
➢ The thermal and velocity slip parameters reduce the temperature distribution.
Finally, we note that our work was built on the Ellis model for fluid rheology using the unique behaviors of the straightforward power-law model. In particular, as the flow rate in the basic state is zero, the power-law model predicts either a zero or an infinite critical estimate for the Darcy–Rayleigh number, as stated in Barletta and Nield [60]. However, the application of the Ellis model results in a nonsingular trend as the basic flow rate approaches zero, reaching the same critical estimate of the Darcy–Rayleigh number in the case of a Newtonian fluid.
The original contributions presented in the study are included in the article/Supplementary Material, and further inquiries can be directed to the corresponding author.
MK: Writing-Original Draft Preparation, Data Curation, Investigation, Visualization, Validation. NA: Help in computation. SA: Conceptualization, Methodology, Software, Formal Analysis, Writing-Original Draft Preparation. ME; Review the modeling of the problem. ET-e; Improve the physical discussion. KG: Performs the critical review. KAG; Help in coding. MY; Help in problem formulation.
The authors extend their appreciation to the Deanship of Scientific Research at King Khalid University, Abha, Saudi Arabia, for funding this work through the Research Group Program under grant no. RGP. 2/19/43. The authors would like to thank the Deanship of Scientific Research at Umm Al-Qura University for supporting this work by Grant Code: (22UQU4331317DSR68). The authors thank to Taif University Researcher for Supporting project number (TURSP-2020/16), Taif University, Taif, Saudi Arabia.
The authors declare that the research was conducted in the absence of any commercial or financial relationships that could be construed as a potential conflict of interest.
All claims expressed in this article are solely those of the authors and do not necessarily represent those of their affiliated organizations, or those of the publisher, the editors, and the reviewers. Any product that may be evaluated in this article or claim that may be made by its manufacturer is not guaranteed or endorsed by the publisher.
1. Choi SU, Eastman JA. Enhancing thermal conductivity of fluids with nanoparticles (No. ANL/MSD/CP-84938. IL (United States): Argonne National Lab. (1995).
2. Saidur R, Leong KY, Mohammed HA. A review on applications and challenges of nanofluids. Renew Sustain Energ Rev (2011) 15(3):1646–68. doi:10.1016/j.rser.2010.11.035
3. Waqas H, Khan SA, Alghamdi M, Muhammad T. Numerical investigation for radiative transport in magnetized flow of nanofluids due to moving surface. Math Probl Eng (2021) 1–10. doi:10.1155/2021/1705736
4. Reddy PS, Sreedevi P, Chamkha AJ. MHD boundary layer flow, heat and mass transfer analysis over a rotating disk through porous medium saturated by Cu-water and Ag-water nanofluid with chemical reaction. Powder Technol (2017) 307:46–55. doi:10.1016/j.powtec.2016.11.017
5. Krishna MV, Chamkha AJ. Hall and ion slip effects on MHD rotating boundary layer flow of nanofluid past an infinite vertical plate embedded in a porous medium. Results Phys (2019) 15:102652. doi:10.1016/j.rinp.2019.102652
6. Waqas H, Khan SA, Farooq U, Muhammad T, Alshehri A, Yasmin S. Thermal transport analysis of six circular microchannel heat sink using nanofluid. Sci Rep (2022) 12(1):8035–19. doi:10.1038/s41598-022-11121-y
7. Khan MN, Nadeem S. A comparative study between linear and exponential stretching sheet with double stratification of a rotating Maxwell nanofluid flow. Surf Inter (2021) 22:100886. doi:10.1016/j.surfin.2020.100886
8. Khan MN, Ahmad S, Nadeem S. Flow and heat transfer investigation of bio–convective hybrid nanofluid with triple stratification effects. Phys Scr (2021) 96(6):065210. doi:10.1088/1402-4896/abf305
9. Alqarni MS, Yasmin S, Waqas H, Khan SA. Recent progress in melting heat phenomenon for bioconvection transport of nanofluid through a lubricated surface with swimming microorganisms. Sci Rep (2022) 12(1):8447–17. doi:10.1038/s41598-022-12230-4
10. Rooman M, Jan MA, Shah Z, Alzahrani MR. Entropy generation and nonlinear thermal radiation analysis on axisymmetric MHD Ellis nanofluid over a horizontally permeable stretching cylinder. Waves in Random and Complex Media (2022) 1–15. doi:10.1080/17455030.2021.2020934
11. VeeraKrishna M, Subba Reddy G, Chamkha AJ. Hall effects on unsteady MHD oscillatory free convective flow of second grade fluid through porous medium between two vertical plates. Phys Fluids (2018) 30(2):023106. doi:10.1063/1.5010863
12. Chamkha AJ, Mohamed RA, Ahmed SE. Unsteady MHD natural convection from a heated vertical porous plate in a micropolar fluid with Joule heating, chemical reaction and radiation effects. Meccanica (2011) 46(2):399–411. doi:10.1007/s11012-010-9321-0
13. Khan Y, Akram S, Athar M, Saeed K, Muhammad T, Hussain A, et al. The role of double-diffusion convection and induced magnetic field on peristaltic pumping of a johnson–segalman nanofluid in a non-uniform channel. Nanomaterials (2022) 12(7):1051. doi:10.3390/nano12071051
14. Akram S, Razia A, Umair MY, Abdulrazzaq T, Homod RZ. Double‐diffusive convection on peristaltic flow of hyperbolic tangent nanofluid in non‐uniform channel with induced magnetic field. Math Methods Appl Sci (2022). doi:10.1002/mma.8188
15. Akram S, Athar M, Saeed K. Numerical simulation of effects of soret and dufour parameters on the peristaltic transport of a magneto six-constant jeffreys nanofluid in a non-uniform channel: A bio-nanoengineering model. Eur Phys J Spec Top (2022) 231(3):535–43. doi:10.1140/epjs/s11734-021-00348-x
16. Akram S, Athar M, Saeed K, Umair MY. Nanomaterials effects on induced magnetic field and double-diffusivity convection on peristaltic transport of Prandtl nanofluids in inclined asymmetric channel. Nanomater Nanotechnology (2022) 12:184798042110486. doi:10.1177/18479804211048630
17. Waqas H, Khan SA, Muhammad T, Naqvi SMRS. Heat transfer enhancement in stagnation point flow of ferro-copper oxide/water hybrid nanofluid: A special case study. Case Stud Therm Eng (2021) 28:101615. doi:10.1016/j.csite.2021.101615
18. Krishna MV, Chamkha AJ. Hall and ion slip effects on MHD rotating flow of elastico-viscous fluid through porous medium. Int Commun Heat Mass Transfer (2020) 113:104494. doi:10.1016/j.icheatmasstransfer.2020.104494
19. Turcu R, Darabont AL, Nan A, Aldea N, Macovei D, Bica D, et al. New polypyrrole-multiwall carbon nanotubes hybrid materials. J optoelectronics Adv Mater (2006) 8(2):643–7.
20. Jana S, Salehi-Khojin A, Zhong WH. Enhancement of fluid thermal conductivity by the addition of single and hybrid nano-additives. Thermochim Acta (2007) 462(1-2):45–55. doi:10.1016/j.tca.2007.06.009
21. Devi SA, Devi SSU. Numerical investigation of hydromagnetic hybrid Cu–Al2O3/water nanofluid flow over a permeable stretching sheet with suction. Int J Nonlinear Sci Numer Simulation (2016) 17(5):249–57. doi:10.1515/ijnsns-2016-0037
22. Maskeen MM, Zeeshan A, Mehmood OU, Hassan M. Heat transfer enhancement in hydromagnetic alumina–copper/water hybrid nanofluid flow over a stretching cylinder. J Therm Anal Calorim (2019) 138(2):1127–36. doi:10.1007/s10973-019-08304-7
23. Sreedevi P, Sudarsana Reddy P, Chamkha A. Heat and mass transfer analysis of unsteady hybrid nanofluid flow over a stretching sheet with thermal radiation. SN Appl Sci (2020) 2(7):1222–15. doi:10.1007/s42452-020-3011-x
24. Acharya N, Maity S, Kundu PK. Framing the hydrothermal features of magnetized TiO2–CoFe2O4 water-based steady hybrid nanofluid flow over a radiative revolving disk. Multidiscipline Model Mater Structures (2019) 16(4):765–90. doi:10.1108/mmms-08-2019-0151
25. Ramesh GK, Shehzad SA, Rauf A, Chamkha AJ. Heat transport analysis of aluminum alloy and magnetite graphene oxide through permeable cylinder with heat source/sink. Phys Scr (2020) 95(9):095203. doi:10.1088/1402-4896/aba5af
26. Farooq U, Waqas H, Muhammad T, Khan SA. Heat transfer enhancement of hybrid nanofluids over porous cone. Int J Chem Reactor Eng (2022) 20(4):465–73. doi:10.1515/ijcre-2021-0109
27. Qin L, Ahmad S, Khan MN, Ahammad NA, Gamaoun F, Galal AM. Thermal and solutal transport analysis of Blasius–Rayleigh–Stokes flow of hybrid nanofluid with convective boundary conditions. Waves in Random and Complex Media (2022) 1–19. doi:10.1080/17455030.2022.2072018
28. Ahmad S, Nadeem S, Khan MN. Enhanced transport properties and its theoretical analysis in two-phase hybrid nanofluid. Appl Nanoscience (2021) 12(3):309–16. doi:10.1007/s13204-020-01634-1
29. Waini I, Khan U, Zaib A, Ishak A, Pop I. Thermophoresis particle deposition of CoFe2O4-TiO2 hybrid nanoparticles on micropolar flow through a moving flat plate with viscous dissipation effects. Int J Numer Methods Heat Fluid Flow (2022). doi:10.1108/hff-12-2021-0767
30. Chaudhary MA, Merkin JH. A simple isothermal model for homogeneous-heterogeneous reactions in boundary-layer flow. I Equal diffusivities. Fluid Dyn Res (1995) 16(6):311–33. doi:10.1016/0169-5983(95)00015-6
31. Ramzan M, Riasat S, Alotaibi H. EMHD hybrid squeezing nanofluid flow with variable features and irreversibility analysis. Phys Scr (2022) 97(2):025705. doi:10.1088/1402-4896/ac49b1
32. Khan M, Yasir M, Alshomrani AS, Sivasankaran S, Aladwani YR, Ahmed A. Variable heat source in stagnation-point unsteady flow of magnetized Oldroyd-B fluid with cubic autocatalysis chemical reaction. Ain Shams Eng J (2022) 13(3):101610. doi:10.1016/j.asej.2021.10.005
33. Puneeth V, Manjunatha S, Makinde OD, Gireesha BJ. Bioconvection of a radiating hybrid nanofluid past a thin needle in the presence of heterogeneous–homogeneous chemical reaction. J Heat Transfer (2021) 143(4). doi:10.1115/1.4049844
34. Elattar S, Helmi MM, Elkotb MA, El-Shorbagy MA, Abdelrahman A, Bilal M, et al. Computational assessment of hybrid nanofluid flow with the influence of hall current and chemical reaction over a slender stretching surface. Alexandria Eng J (2022) 61(12):10319–31. doi:10.1016/j.aej.2022.03.054
35. Gul H, Ramzan M, Chung JD, Chu YM, Kadry S. Multiple slips impact in the MHD hybrid nanofluid flow with Cattaneo–Christov heat flux and autocatalytic chemical reaction. Sci Rep (2021) 11(1):14625–14. doi:10.1038/s41598-021-94187-4
36. Zainal NA, Nazar R, Naganthran K, Pop I. Flow and heat transfer over a permeable moving wedge in a hybrid nanofluid with activation energy and binary chemical reaction. Int J Numer Methods Heat Fluid Flow (2021) 32:1686–705. doi:10.1108/hff-04-2021-0298
37. Ramesh GK, Manjunatha S, Roopa GS, Chamkha AJ. Hybrid (ND-Co3O4/EG) nanoliquid through a permeable cylinder under homogeneous-heterogeneous reactions and slip effects. J Therm Anal Calorim (2021) 146(3):1347–57. doi:10.1007/s10973-020-10106-1
38. Tahir W, Althobaiti N, Kousar N, Alhazmi SE, Bilal S, Riaz A. Effects of homogeneous-heterogeneous reactions on Maxwell ferrofluid in the presence of magnetic dipole along a stretching surface: A numerical approach. Mathematical Problems in Engineering (2022). doi:10.1155/2022/4148401
39. Keenan JH. Availability and irreversibility in thermodynamics. Br J Appl Phys (1951) 2(7):183–92. doi:10.1088/0508-3443/2/7/302
40. Bejan A. Entropy generation minimization: The new thermodynamics of finite‐size devices and finite‐time processes. J Appl Phys (1996) 79(3):1191–218. doi:10.1063/1.362674
41. Bejan A. Entropy generation minimization: The method of thermodynamic optimization of finite-size systems and finite-time processes. CRC Press (2013). doi:10.1201/9781482239171
42. Jakeer S, Reddy PBA. Entropy generation on EMHD stagnation point flow of hybrid nanofluid over a stretching sheet: Homotopy perturbation solution. Phys Scr (2020) 95(12):125203. doi:10.1088/1402-4896/abc03c
43. Khosravi R, Rabiei S, Khaki M, Safaei MR, Goodarzi M. Entropy generation of graphene–platinum hybrid nanofluid flow through a wavy cylindrical microchannel solar receiver by using neural networks. J Therm Anal Calorim (2021) 145(4):1949–67. doi:10.1007/s10973-021-10828-w
44. Mumraiz S, Ali A, Awais M, Shutaywi M, Shah Z. Entropy generation in electrical magnetohydrodynamic flow of Al2O3–Cu/H2O hybrid nanofluid with non-uniform heat flux. J Therm Anal Calorim (2021) 143(3):2135–48. doi:10.1007/s10973-020-09603-0
45. Li YX, Khan MI, Gowda RP, Ali A, Farooq S, Chu YM, et al. Dynamics of aluminum oxide and copper hybrid nanofluid in nonlinear mixed Marangoni convective flow with entropy generation: Applications to renewable energy. Chin J Phys (2021) 73:275–87. doi:10.1016/j.cjph.2021.06.004
46. Riaz A, Almutairi S, Alhazmi SE, Saleem A, Nadeem S, Abdelrahman A. Insight into the cilia motion of electrically conducting Cu-blood nanofluid through a uniform curved channel when entropy generation is significant. Alexandria Eng J (2022) 61(12):10613–30. doi:10.1016/j.aej.2022.04.011
47. Bhatti MM, Riaz A, Zhang L, Sait SM, Ellahi R. Biologically inspired thermal transport on the rheology of williamson hydromagnetic nanofluid flow with convection: An entropy analysis. J Therm Anal Calorim (2021) 144(6):2187–202. doi:10.1007/s10973-020-09876-5
48. Ahmad S, Khan MN, Nadeem S, Rehman A, Ahmad H, Ali R. Impact of Joule heating and multiple slips on a Maxwell nanofluid flow past a slendering surface. Commun Theor Phys (2021) 74(1):015001. doi:10.1088/1572-9494/ac3bc8
49. Takhar HS, Chamkha AJ, Nath G. Unsteady flow and heat transfer on a semi-infinite flat plate with an aligned magnetic field. Int J Eng Sci (1999) 37(13):1723–36. doi:10.1016/s0020-7225(98)00144-x
50. Saeed K, Akram S, Ahmad A, Athar M, Imran M, Muhammad T. Impact of partial slip on double diffusion convection and inclined magnetic field on peristaltic wave of six-constant Jeffreys nanofluid along asymmetric channel. Eur Phys J Plus (2022) 137(3):364. doi:10.1140/epjp/s13360-022-02553-6
51. Krishna MV, Ahamad NA, Chamkha AJ. Hall and ion slip impacts on unsteady MHD convective rotating flow of heat generating/absorbing second grade fluid. Alexandria Eng J (2021) 60(1):845–58. doi:10.1016/j.aej.2020.10.013
52. Chamkha AJ. MHD-free convection from a vertical plate embedded in a thermally stratified porous medium with Hall effects. Appl Math Model (1997) 21(10):603–9. doi:10.1016/s0307-904x(97)00084-x
53. Chamkha AJ, Khaled ARA. Hydromagnetic combined heat and mass transfer by natural convection from a permeable surface embedded in a fluid‐saturated porous medium. Int J Numer Methods Heat Fluid Flow (2000) 10(5):455–77. doi:10.1108/09615530010338097
54. Takhar HS, Chamkha AJ, Nath G. Unsteady mixed convection flow from a rotating vertical cone with a magnetic field. Heat Mass Transfer (2003) 39(4):297–304. doi:10.1007/s00231-002-0400-1
55. Akram S, Athar M, Saeed K, Razia A. Impact of slip on nanomaterial peristaltic pumping of magneto-Williamson nanofluid in an asymmetric channel under double-diffusivity convection. Pramana - J Phys (2022) 96(1):57–13. doi:10.1007/s12043-021-02287-7
56. Ahmad S, Nadeem S. Analysis of activation energy and its impact on hybrid nanofluid in the presence of Hall and ion slip currents. Appl Nanosci (2020) 10(12):5315–30. doi:10.1007/s13204-020-01334-w
57. Bhattacharyya K, Gorla RSR. Boundary layer flow and heat transfer over a permeable shrinking cylinder with surface mass transfer. Int J Appl Mech Eng (2013) 18(4):1003–12. doi:10.2478/ijame-2013-0062
58. Ramesh K, Riaz A, Dar ZA. Simultaneous effects of MHD and Joule heating on the fundamental flows of a Casson liquid with slip boundaries. Propulsion Power Res (2021) 10(2):118–29. doi:10.1016/j.jppr.2021.05.002
59. Vaidya H, Rajashekhar C, Prasad KV, Khan SU, Riaz A, Viharika JU. MHD peristaltic flow of nanofluid in a vertical channel with multiple slip features: An application to chyme movement. Biomech Model Mechanobiol (2021) 20(3):1047–67. doi:10.1007/s10237-021-01430-y
60. Barletta A, Nield DA. Linear instability of the horizontal throughflow in a plane porous layer saturated by a power-law fluid. Phys Fluids (2011) 23(1):013102. doi:10.1063/1.3532805
Keywords: Ellis hybrid nanofluid, joule (ohmic) heating, viscous dissipation, surface-catalyzed reaction, homogeneous–heterogeneous reaction
Citation: Khan MN, Ahammad NA, Ahmad S, Elkotb MA, Tag-eldin E, Guedri K, Gepreel KA and Yassen MF (2022) Thermophysical features of Ellis hybrid nanofluid flow with surface-catalyzed reaction and irreversibility analysis subjected to porous cylindrical surface. Front. Phys. 10:986501. doi: 10.3389/fphy.2022.986501
Received: 05 July 2022; Accepted: 02 August 2022;
Published: 15 September 2022.
Edited by:
Arshad Riaz, University of Education Lahore, PakistanReviewed by:
Hassan Waqas, Government College University, Faisalabad, PakistanCopyright © 2022 Khan, Ahammad, Ahmad, Elkotb, Tag-eldin, Guedri, Gepreel and Yassen. This is an open-access article distributed under the terms of the Creative Commons Attribution License (CC BY). The use, distribution or reproduction in other forums is permitted, provided the original author(s) and the copyright owner(s) are credited and that the original publication in this journal is cited, in accordance with accepted academic practice. No use, distribution or reproduction is permitted which does not comply with these terms.
*Correspondence: Shafiq Ahmad, YXNoYWZpcUBtYXRoLnFhdS5lZHUucGs=
Disclaimer: All claims expressed in this article are solely those of the authors and do not necessarily represent those of their affiliated organizations, or those of the publisher, the editors and the reviewers. Any product that may be evaluated in this article or claim that may be made by its manufacturer is not guaranteed or endorsed by the publisher.
Research integrity at Frontiers
Learn more about the work of our research integrity team to safeguard the quality of each article we publish.