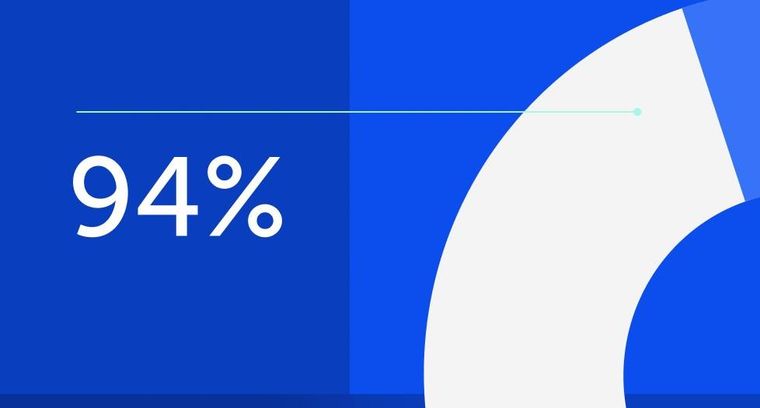
94% of researchers rate our articles as excellent or good
Learn more about the work of our research integrity team to safeguard the quality of each article we publish.
Find out more
MINI REVIEW article
Front. Phys., 06 July 2022
Sec. Optics and Photonics
Volume 10 - 2022 | https://doi.org/10.3389/fphy.2022.932284
This article is part of the Research TopicAdvances in Laser Micro-Processing and ApplicationsView all 5 articles
Laser-induced periodic surface structures (LIPSSs) are a universal phenomenon that can be observed on a variety of materials, including metals, semiconductors, and dielectrics, upon irradiation with ultrafast laser pulses. It has found various potential applications in the fields of optics, biologics, and mechatronics due to its efficient and flexible fabrication process and subwavelength quasi-periodic property. However, LIPSSs face the challenge of uniformity control because the formation of micro-/nanostructures induced by ultrafast laser is a complex process involving multiple interacting factors, including laser energy deposition, phase change, light scattering, and instantaneous local changes of material properties and their feedback mechanisms. Recently, there has been some significant progress regarding the control of LIPSS uniformity. In this work, we review recent experimental and methodological advances on this topic from three aspects: 1) laser-induced modified-LIPSS, 2) feedback mechanism of LIPSS formation, and 3) ultrafast laser pulse shaping. This review can stimulate further investigations into the uniformity control of LIPSSs to support and accelerate the industrial applications of uniform LIPSSs.
Due to ultrashort irradiation periods and ultra-high intensities, ultrafast laser pulses have unique processing advantages such as high processing accuracy, high processing flexibility, and strong material adaptability compared with long laser pulses [1, 2]. Ultrafast laser pulse technology has become one of the promising methods for surface micro/nano structure fabrication [3]. Laser-induced periodic surface structures (LIPSSs) are a universal phenomenon upon irradiation with linearly polarized ultrafast laser pulses, which were first observed by Birnbaum in 1965 [4]. While LIPSS technology is an efficient and flexible method for the fabrication of subwavelength periodic surface structures, the formation of LIPSS is quite a complex process, and the mechanism has not yet been determined. Currently, the widely accepted definition arises from the interaction between an incident ultrafast laser beam and surface electromagnetic waves scattered by rough surfaces and may involve the excitation and propagation of surface plasmon polaritons (SPPs) [5–7]. Huang et al. believed that these periodic structures with periods smaller than the incident wavelength were formed by the interference of the initially excited surface plasmons (SPs) with the incident femtosecond laser and the subsequent grating-assisted SP/laser coupling [8].
After decades of research and discovery, LIPSS investigation has developed into a scientific evergreen [9]. LIPSS technology has been realized on various metals, semiconductors, dielectrics, and polymer films [10–13], and has found plenty of potential applications in the fields of optics, biologics, and mechatronics [9]. Yu et al. [14] proved the potential of LIPSS applied in the field of tribology, and Bonse et al. [15] demonstrated that the coefficient of friction of LIPSS-treated titanium surfaces was reduced by more than two times. Sugioka et al. proposed a novel fabrication of LIPSS inside 3D glass microfluidic channels and realized the application for real-time surface-enhanced Raman spectroscopy (SERS) [16]. Yin et al. utilized the ultrafast laser-induced formation of LIPSS on the surface of a stainless steel mesh to modulate the surface wettability and achieved the preparation of superhydrophilic and underwater superoleophobic structures, which have been applied to oil–water separation [17]. Jalil et al. reported the preparation of nanostructure-covered LIPSS on metal surfaces by ultrafast laser direct writing, which created broadband optical absorbers and selective solar absorbers [18].
Submicron gratings, as one of the most important diffractive optical elements, are favored by researchers because of their outstanding capability of precisely controlling the dispersion and steering characteristics of light [19–21]. LIPSS technology can flexibly fabricate periodically arranged structures with a submicron period, providing a powerful non-contact processing technology for the preparation of surface gratings on various materials [10, 22–25]. Vorobyev et al. reported the creation of various colors on a metal surface by LIPSS technology [10]. Dusser et al. systematically studied the LIPSS morphological changes and their corresponding color gamut properties induced by ultrafast laser pulses with different linear polarizations and realized complex coloring designs on stainless steel surfaces [22].
However, LIPSS technology still faces severe challenges in uniformity control [26, 27], limiting its wide application such as in the field of optics. Laser energy deposition is first absorbed by the electronic system of the irradiated materials, then the deposited energy is transferred to the lattice system, which subsequently induces various thermal effects, possibly hydrodynamic or chemical effects, etc. The effect of ultrafast pulses and the instantaneous local property changes of materials are dynamic processes of mutual feedback, which greatly increase the difficulty of controlling the formation of structures in a reliable way. In conventional LIPSS technologies, periodic structures always arise from the distributed light field caused by the large number of debris and surface defects during laser ablation, making it difficult to ensure long-range uniformity in larger-area preparation. Up to now, there have been a series of studies on the uniformity control of LIPSS. In this work, we review recent experimental advances on this issue from the perspectives of laser-induced modified-LIPSS, the feedback mechanism of LIPSS formation, and ultrafast laser pulse shaping.
In view of the issue about LIPSS uniformity control, a series of studies have been reported. For instance, Ardron et al. utilized linear pre-polished samples to regularize the morphology of LIPSS [28] and Harzic et al. reported an approach to improve the uniformity of LIPSS by using a nanojoule-femtosecond laser at a high repetition rate [29]. However, these methods were all performed under the conventional ablation regime, and the formation of LIPSS is always accompanied by the generation of a large number of debris and surface defects, which greatly affects the uniform excitation/propagation of subsequent SPPs, resulting in non-uniform periodic structures with numerous visible bifurcations [30]. Upon the irradiation of ultrafast laser pulses, the electron temperature and the lattice temperature of the material are in a strong non-equilibrium state, so that the kinetics of the phase transition may lead to a new phenomenon, that is, laser-induced modification. This phenomenon has been realized and applied in various scenarios, such as laser-induced single-crystal silicon [31, 32], Ge2Sb2Te5 [33], MoS2 [34] phase change, and laser-induced reduction of graphene oxide [35]. Based on the above revelations, Puerto et al. reported a regular grating structure preparation in silicon by taking advantage of laser-induced amorphization of crystalline silicon and LIPSS technology [36]. As demonstrated in Figure 1A, the fabricated structures consist of alternating amorphous-crystalline silicon stripes without any visible inhomogeneous cross-linked structure. When the incident laser fluence is higher than the melting threshold of crystalline silicon but lower than its ablation threshold, localized melting occurs under ultrafast laser pulse irradiation. Then liquid phase silicon overheats, and rapidly solidifies into an amorphous phase thin layer [37, 38]. Raman spectroscopic analysis confirmed the existence of laser-induced amorphous silicon, and the maximum thickness of the amorphous phase layer was around 60 nm [39]. Similarly, Zou et al. exploited ultrafast laser pulse for direct writing on graphene oxide (GO) films and successfully produced uniform subwavelength rGO-LIPSS (Figure 1B) [40]. The authors believe that the ultrafast laser-induced nonthermal or thermal photoreduction effects play a crucial role in the uniform formation of LIPSS [40, 41].
FIGURE 1. Laser-induced modified-LIPSS. (A) Femtosecond laser-induced high-precision amorphous-crystalline nanogratings in silicon [36, 39]. (B) Uniform fabrication of subwavelength grating structures on GO thin films by femtosecond laser-induced reduction of GO [40]. (C) Highly homogeneous LIPSS on silicon via chemical etching–assisted femtosecond laser modification [30]. (D) Long-range uniform periodic surface structures realized by a modified regime cylindrically focused on femtosecond laser processing [43].
In addition, on the basis of modified-LIPSS technology, Huang et al. innovatively proposed a chemical etching–assisted ultrafast laser modification method to further promote the uniformity control of LIPSS [30]. As illustrated in Figure 1C, this method combines the advantages of modified-LIPSS with the specialty of great difference in chemical activity between amorphous and crystalline phase of silicon [42]. First, by precisely manipulating the laser-material interaction process, alternating amorphous-crystalline stripes are created by ultrafast laser scanning over silicon substrates; second, assisted by further chemical etching, the amorphous-stripes act as fine etch stops to prepare the uniform structures. The fabricated structures by this chemical etching–assisted ultrafast laser modification method are periodically and regularly distributed, and there is no visible crosslinking (Figures 1Ciii,iv). Compared with the conventional ablation LIPSS (Figures 1Cv,vi), the uniformity of the grating structures is significantly improved [30]. Meanwhile, researchers from the same group extended the laser focusing mode from point to line, further expanding the applicability of the chemical etching–assisted ultrafast laser modification method, and long-range uniformity in larger-area preparation of periodic surface structures is achieved (Figures 1Di–iv) [43]. The incomplete statistics show that the structures fabricated by this technology achieve optimal long-range uniformity compared to the reported LIPSS, which gains a minimum divergence of structure-orientation angles (<5°) [44]. Additionally, the etching time at different positions of the sample can be continuously and accurately controlled by a carefully designed etching process in which the laser-treated samples are gradually and uniformly immersed in the KOH etching solution. Then, periodic surface structures with continuous gradient changes in morphology are prepared in crystalline silicon. Benefiting from the uniformity and topographic features of the grating, the diffraction efficiency of the designed structure exhibits a continuous near-linear variation with the irradiation position, which will be widely used in optical sensing (Figures 1Dv-viii).
As mentioned above, ultrafast laser-induced LIPSS formation is a complex process involving mutual feedback mechanisms. Wang et al. have proved the relationship between the laser-induced plasma layer and the formation of ultrafast laser-induced subwavelength and deep-subwavelength structures on silicon [45]. The study by Han et al. found that the grating structure formed by the pre-pulse would facilitate the SPPs’ coupling and directional scattering effects, thereby enhancing the anisotropic characteristics of the subsequent structure [11]. Recently, Öktem et al. proposed a new mentality based on nonlinear feedback mechanisms and realized the preparation of LIPSS with long-range uniformity on titanium surfaces [46]. The method tightly regulates the formation of nanostructures induced by ultrashort pulses by carefully exploiting feedback mechanisms, which can be summarized in the following steps: 1) An ultrafast laser beam with a peak intensity close to the ablation threshold of titanium is focused on the titanium surface, which is scattered by the existing nanostructures or any surface defects. The interference of the scattered field with the incident field results in the variation of the laser intensity near the scattered points. 2) At points where the laser energy exceeds the ablation threshold, titanium reacts rapidly with O2 in the air and forms titanium dioxide (TiO2). As shown in Figure 2A, the first two steps constitute a positive feedback loop, and as the nanostructure grows, so does its scattering power. 3) The growth mechanism of TiO2 also possesses an imbedded negative feedback loop. As TiO2 grows on top of the titanium, the penetration of O2 through the oxide layer decreases exponentially. Based on this new mentality, various periodic nanostructures with long-range uniformity have been successfully fabricated on titanium. Figure 2Bi presents a photograph of nanostructures covering a 3-mm2 area, consisting of the highly uniform TiO2 nanogratings shown in Figure 2Bii. As demonstrated in Figures 2Biii,iv, a mesh structure is generated on titanium by two scans of orthogonally polarized laser beams, and a regular array of nanocircles is obtained using circularly polarized light. Moreover, Dostovalov et al. successfully fabricated regular periodic structures on metal thin films (such as titanium films and chromium films) by using a similar method [47, 48].
FIGURE 2. The feedback mechanism of LIPSS formation and ultrafast laser pulse shaping. (A,B) Growth of metal-oxide periodic nanostructures with long-range uniformity by exploiting positive non-local feedback to initiate and negative local feedback to regulate [46]. (C,D) Regularizing the generation of subwavelength gratings on SOI by the feedback mechanisms of sample structural properties [50]. (E,F) A highly uniform LIPSS was fabricated on silicon based on temporally shaped femtosecond laser pulses [67].
On the other hand, researchers regulated laser-processed structures by carefully exploiting feedback mechanisms of sample material/structural properties. Feng et al. utilized the feedback mechanism of the thin gold film coat on silicon surfaces for the laser processing, which enhances interfacial electron–phonon coupling to form a high and uniform electron density, and suppresses the impact of defects on the silicon, thereby achieving a uniform and stable LIPSS fabrication [49]. Recently, Huang et al. deeply analyzed the structural characteristics of silicon-on-insulator (SOI) and exploited the feedback mechanism of the intermediate buried oxide layer (SiO2 layer) of the SOI on the laser-induced phase change process to regulate the generation of subwavelength gratings [50]. For a bulk Si wafer, the multi-pulse–induced incubation heat [51, 52] quickly transfers inside the substrate because of the high thermal conductivity of Si, balancing the local surface temperature of the initial structure between melting and vaporization. As demonstrated in Figure 2C, the generated LIPSS structures on the bulk Si were subject to the mechanism of melt flow, in accordance with the results from Tsibidis et al. [53], where the bendings and uneven cross-linkings obviously result from the long-term melt disturbance.
However, for an SOI wafer, the SiO2 layer of SOI plays a critical role in the formation of surface structures. Since the intermediate SiO2 layer possesses high thermal insulation, a feedback mechanism is constituted for the laser-induced incubation heat. The non-local nature of the feedback seriously prevents the incubation heat from spreading into the underneath silicon substrate, resulting in the accumulation of a large amount of heat in the top thin device layer of the SOI, reaching the vaporization temperature threshold. Then, uniform structures are generated on the top Si device layer of SOI as a result of direct local vaporization of the material instead of long-term melt flow. As shown in Figure 2D, highly uniform subwavelength gratings are flexibly prepared on SOI based on exploiting the feedback mechanisms to regulate the formation of structures. Furthermore, periodic surface structures with high uniformity achieve superior structure coloring, and a large-area cross-scale “peace dove” pattern was flexibly prepared on an SOI wafer, which exhibits a vivid and distinguishable structural color under indoor lighting [50].
Under single femtosecond laser beam irradiation conditions, researchers have made efforts to manipulate the characteristics of LIPSS by varying the incident laser parameters (such as wavelength, energy fluence, pulse number, and polarization state) [54–57]. However, the adjusting ability appears to be limited because the formation of LIPSS is essentially determined by the transient properties of the irradiated material [58]. Temporal pulse shaping enables the generation of sub-pulses with ultrashort pulse delays (typically tens of femtoseconds to tens of picoseconds) so that the localized transient material properties can be under control. Ultrafast imaging results show that a transient metallic state can be generated on the material surface within a few tens of ps after femtosecond pulse irradiation and that a transient LIPSS structure has begun to form [59]. Therefore, the formation process of LIPSS can be further regulated by the temporal pulse-shaping method [8]. Several studies have investigated LIPSS formation by using delayed femtosecond double pulses with crossed or parallel polarizations and obtained some interesting results [60, 61]; for example, by controlling the pulse delay to tune the grating period [62], enabling the processing of ring-shaped LIPSS structures [63] and realizing the preparation of large-area 2D metal photonic crystal structures on tungsten surfaces [64].
Recently, ultrafast laser pulse shaping technologies have been used to control the uniformity of LIPSS. Jalil et al. employed a double temporally delayed femtosecond laser beam to adjust the propagation length of excited SPPs to improve LIPSS uniformity [65]. Lei et al. reported the fabrication of uniform subwavelength grating structures on metallic glass by a double-pulse femtosecond laser with nondegenerate directions of the linear polarizations [66]. Additionally, Zhang et al. fabricated a highly regular LIPSS on a silicon wafer by femtosecond laser pulse trains (Figure 2E) with a pulse delay of 16.2 ps and half in a symmetric energy distribution ratio of 0.09:0.13:0.21:0.69 [67]. Figure 2F shows the top-view SEM images (i–ii), cross-sectional SEM images (iii), and the corresponding 2D-FFT image (iv) of the fabricated LIPSS structure, clearly demonstrating that each ripple of the structure is completely straight and uniform, with a small fluctuation of period. The authors suggest that the underlying mechanism for the formation of highly uniform LIPSS is that, first, temporally shaped femtosecond laser pulse can enhance the excitation of the SPPs and periodic energy deposition [8, 59]. Second, the residual thermal effect on the ablation spot is greatly reduced due to the “ablation cooling” effect [68]. Besides, the ejected plume and debris from the previous sub-pulse are further excited by the subsequent sub-pulses, and the debris will be further ionized and vaporized into aerosol, avoiding the deposition of the ejected debris [69]. This ultrafast laser pulse–shaping technology will potentially be extended to other materials as a general process for the fabrication of large-area uniform LIPSS.
In summary, LIPSS shows immense potential for applications in various fields such as optics, biologics, and mechatronics by virtue of its efficient and flexible fabrication process and subwavelength periodic property. However, the formation of LIPSS is determined by the parameters of the incident femtosecond laser, the material properties, and the feedback mechanism of laser-material interaction, which makes the fabrication of LIPSS with high uniformity difficult and greatly limits its application. In this article, recent experimental and methodological advances in LIPSS uniformity control are reviewed and summarized into three aspects: laser-induced modified-LIPSS, feedback mechanism of LIPSS formation, and ultrafast laser pulse shaping, which are discussed separately. The review can provide a reference guide for the research on the preparation of highly uniform LIPSS and will promote the industrial application prospects of LIPSS. In future work, a general process for the preparation of LIPSS with high uniformity on various materials should be further developed.
JH and KW initiated the project. JH wrote the manuscript. YL, SJ, ZW, YQ, JZ, and RQ made intellectual contributions and edited the manuscript.
This work was supported by the National Key R&D Program of China (No. 2021YFF0603600).
The authors declare that the research was conducted in the absence of any commercial or financial relationships that could be construed as a potential conflict of interest.
All claims expressed in this article are solely those of the authors and do not necessarily represent those of their affiliated organizations, or those of the publisher, the editors, and the reviewers. Any product that may be evaluated in this article, or claim that may be made by its manufacturer, is not guaranteed or endorsed by the publisher.
1. Malinauskas M, Žukauskas A, Hasegawa S, Hayasaki Y, Mizeikis V, Buividas R, et al. Ultrafast Laser Processing of Materials: From Science to Industry. Light Sci Appl (2016) 5(8):e16133. doi:10.1038/lsa.2016.133
2. Sugioka K, Cheng Y. Ultrafast Lasers-Reliable Tools for Advanced Materials Processing. Light Sci Appl (2014) 3(4):e149. doi:10.1038/lsa.2014.30
3. Jiang L, Wang A-D, Li B, Cui T-H, Lu Y-F. Electrons Dynamics Control by Shaping Femtosecond Laser Pulses in Micro/nanofabrication: Modeling, Method, Measurement and Application. Light Sci Appl (2018) 7(2):17134. doi:10.1038/lsa.2017.134
4. Birnbaum M. Semiconductor Surface Damage Produced by Ruby Lasers. J Appl Phys (1965) 36(11):3688–9. doi:10.1063/1.1703071
5. Van Driel HM, Sipe JE, Young JF. Laser-induced Periodic Surface Structure on Solids: A Universal Phenomenon. Phys Rev Lett (1982) 49(26):1955–8. doi:10.1103/physrevlett.49.1955
6. Sipe JE, Young JF, Preston JS, Van Driel HM. Laser-induced Periodic Surface Structure. I. Theory. Phys Rev B (1983) 27(2):1141–54. doi:10.1103/physrevb.27.1141
7. Bonse J, Munz M, Sturm H. Structure Formation on the Surface of Indium Phosphide Irradiated by Femtosecond Laser Pulses. J Appl Phys (2005) 97(1):013538. doi:10.1063/1.1827919
8. Huang M, Zhao F, Cheng Y, Xu N, Xu Z. Origin of Laser-Induced Near-Subwavelength Ripples: Interference between Surface Plasmons and Incident Laser. ACS nano (2009) 3(12):4062–70. doi:10.1021/nn900654v
9. Bonse J, Höhm S, Kirner SV, Rosenfeld A, Krüger J. Laser-induced Periodic Surface Structures—A Scientific evergreen. IEEE J selected Top Quan Electron (2017) 23(3):9000615. doi:10.1109/JSTQE.2016.2614183
10. Vorobyev AY, Guo C. Colorizing Metals with Femtosecond Laser Pulses. Appl Phys Lett (2008) 92(4):041914. doi:10.1063/1.2834902
11. Han W, Jiang L, Li X, Liu P, Xu L, Lu Y. Continuous Modulations of Femtosecond Laser-Induced Periodic Surface Structures and Scanned Line-Widths on Silicon by Polarization Changes. Opt Express (2013) 21(13):15505–13. doi:10.1364/oe.21.015505
12. Shimotsuma Y, Sakakura M, Kazansky PG, Beresna M, Qiu J, Miura K, et al. Ultrafast Manipulation of Self-Assembled Form Birefringence in Glass. Adv Mater (2010) 22(36):4039–43. doi:10.1002/adma.201000921
13. Rebollar E, Castillejo M, Ezquerra TA. Laser Induced Periodic Surface Structures on Polymer Films: From Fundamentals to Applications. Eur Polym J (2015) 73:162–74. doi:10.1016/j.eurpolymj.2015.10.012
14. Yu J, Lu Y. Laser-induced Ripple Structures on Ni–P Substrates. Appl Surf Sci (1999) 148(3-4):248–52. doi:10.1016/s0169-4332(98)00900-3
15. Bonse J, Koter R, Hartelt M, Spaltmann D, Pentzien S, Höhm S, et al. Femtosecond Laser-Induced Periodic Surface Structures on Steel and Titanium alloy for Tribological Applications. Appl Phys A (2014) 117(1):103–10. doi:10.1007/s00339-014-8229-2
16. Bai S, Serien D, Hu A, Sugioka K. 3D Microfluidic Surface-Enhanced Raman Spectroscopy (SERS) Chips Fabricated by All-Femtosecond-Laser-Processing for Real-Time Sensing of Toxic Substances. Adv Funct Mater (2018) 28(23):1706262. doi:10.1002/adfm.201706262
17. Yin K, Chu D, Dong X, Wang C, Duan J-A, He J. Femtosecond Laser Induced Robust Periodic Nanoripple Structured Mesh for Highly Efficient Oil-Water Separation. Nanoscale (2017) 9(37):14229–35. doi:10.1039/c7nr04582d
18. Jalil SA, Lai B, ElKabbash M, Zhang J, Garcell EM, Singh S, et al. Spectral Absorption Control of Femtosecond Laser-Treated Metals and Application in Solar-thermal Devices. Light Sci Appl (2020) 9(1):14. doi:10.1038/s41377-020-0242-y
19. Xu T, Wu YK, Luo X, Guo LJ. Plasmonic Nanoresonators for High-Resolution Colour Filtering and Spectral Imaging. Nat Commun (2010) 1(1):59–5. doi:10.1038/ncomms1058
20. Kristensen A, Yang JK, Bozhevolnyi SI, Link S, Nordlander P, Halas NJ, et al. Plasmonic Colour Generation. Nat Rev Mater (2016) 2(1):1–14. doi:10.1038/natrevmats.2016.88
21. Lütolf F, Stalder M, Martin OJF. Metallized Gratings Enable Color Effects and Floating Screen Films by First‐order Diffraction. Adv Opt Mater (2015) 3(12):1793–9. doi:10.1002/adom.201500305
22. Dusser B, Sagan Z, Soder H, Faure N, Colombier JP, Jourlin M, et al. Controlled Nanostructrures Formation by Ultra Fast Laser Pulses for Color Marking. Opt Express (2010) 18(3):2913–24. doi:10.1364/oe.18.002913
23. Jiang H-B, Zhang Y-L, Liu Y, Fu X-Y, Li Y-F, Liu Y-Q, et al. Bioinspired Few-Layer Graphene Prepared by Chemical Vapor Deposition on Femtosecond Laser-Structured Cu Foil. Laser Photon Rev (2016) 10(3):441–50. doi:10.1002/lpor.201500256
24. Drevinskas R, Beresna M, Zhang J, Kazanskii AG, Kazansky PG. Ultrafast Laser-Induced Metasurfaces for Geometric Phase Manipulation. Adv Opt Mater (2017) 5(1):1600575. doi:10.1002/adom.201600575
25. Wang L, Chen Q-D, Cao X-W, Buividas R, Wang X, Juodkazis S, et al. Plasmonic Nano-Printing: Large-Area Nanoscale Energy Deposition for Efficient Surface Texturing. Light Sci Appl (2017) 6(12):e17112. doi:10.1038/lsa.2017.112
26. Sun Q, Liang F, Vallée R, Chin SL. Nanograting Formation on the Surface of Silica Glass by Scanning Focused Femtosecond Laser Pulses. Opt Lett (2008) 33(22):2713–5. doi:10.1364/ol.33.002713
27. Bonse J, Krüger J, Höhm S, Rosenfeld A. Femtosecond Laser-Induced Periodic Surface Structures. J Laser Appl (2012) 24(4):042006. doi:10.2351/1.4712658
28. Ardron M, Weston N, Hand D. A Practical Technique for the Generation of Highly Uniform LIPSS. Appl Surf Sci (2014) 313:123–31. doi:10.1016/j.apsusc.2014.05.154
29. Le Harzic R, Dörr D, Sauer D, Neumeier M, Epple M, Zimmermann H, et al. Large-area, Uniform, High-Spatial-Frequency Ripples Generated on Silicon Using a Nanojoule-Femtosecond Laser at High Repetition Rate. Opt Lett (2011) 36(2):229–31. doi:10.1364/ol.36.000229
30. Huang J, Jiang L, Li X, Wang A, Wang Z, Wang Q, et al. Fabrication of Highly Homogeneous and Controllable Nanogratings on Silicon via Chemical Etching-Assisted Femtosecond Laser Modification. Nanophotonics (2019) 8(5):869–78. doi:10.1515/nanoph-2019-0056
31. Shank CV, Yen R, Hirlimann C. Time-resolved Reflectivity Measurements of Femtosecond-Optical-Pulse-Induced Phase Transitions in Silicon. Phys Rev Lett (1983) 50(6):454–7. doi:10.1103/physrevlett.50.454
32. Sokolowski-Tinten K, Bialkowski J, von der Linde D. Ultrafast Laser-Induced Order-Disorder Transitions in Semiconductors. Phys Rev B (1995) 51(20):14186–98. doi:10.1103/physrevb.51.14186
33. Wang Q, Rogers ETF, Gholipour B, Wang C-M, Yuan G, Teng J, et al. Optically Reconfigurable Metasurfaces and Photonic Devices Based on Phase Change Materials. Nat Photon (2016) 10(1):60–5. doi:10.1038/nphoton.2015.247
34. Zuo P, Jiang L, Li X, Li B, Ran P, Li X, et al. Metal (Ag, Pt)-MoS2 Hybrids Greenly Prepared through Photochemical Reduction of Femtosecond Laser Pulses for SERS and HER. ACS Sustain Chem. Eng. (2018) 6(6):7704–14. doi:10.1021/acssuschemeng.8b00579
35. Zhang Y, Guo L, Wei S, He Y, Xia H, Chen Q, et al. Direct Imprinting of Microcircuits on Graphene Oxides Film by Femtosecond Laser Reduction. Nano today (2010) 5(1):15–20. doi:10.1016/j.nantod.2009.12.009
36. Puerto D, Garcia-Lechuga M, Hernandez-Rueda J, Garcia-Leis A, Sanchez-Cortes S, Solis J, et al. Femtosecond Laser-Controlled Self-Assembly of Amorphous-Crystalline Nanogratings in Silicon. Nanotechnology (2016) 27(26):265602. doi:10.1088/0957-4484/27/26/265602
37. Izawa Y, Izawa Y, Setsuhara Y, Hashida M, Fujita M, Sasaki R, et al. Ultrathin Amorphous Si Layer Formation by Femtosecond Laser Pulse Irradiation. Appl Phys Lett (2007) 90(4):044107. doi:10.1063/1.2431709
38. Garcia-Lechuga M, Puerto D, Fuentes-Edfuf Y, Solis J, Siegel J. Ultrafast Moving-Spot Microscopy: Birth and Growth of Laser-Induced Periodic Surface Structures. ACS Photon (2016) 3(10):1961–7. doi:10.1021/acsphotonics.6b00514
39. Fuentes-Edfuf Y, Garcia-Lechuga M, Puerto D, Florian C, Garcia-Leis A, Sanchez-Cortes S, et al. Coherent Scatter-Controlled Phase-Change Grating Structures in Silicon Using Femtosecond Laser Pulses. Sci Rep (2017) 7(1):4594. doi:10.1038/s41598-017-04891-3
40. Zou T, Zhao B, Xin W, Wang Y, Wang B, Zheng X, et al. High-speed Femtosecond Laser Plasmonic Lithography and Reduction of Graphene Oxide for Anisotropic Photoresponse. Light Sci Appl (2020) 9(1):69. doi:10.1038/s41377-020-0311-2
41. Gengler RY, Badali DS, Zhang D, Dimos K, Spyrou K, Gournis D, et al. Revealing the Ultrafast Process behind the Photoreduction of Graphene Oxide. Nat Commun (2013) 4(1):2560. doi:10.1038/ncomms3560
42. Kawasegi N, Morita N, Yamada S, Takano N, Oyama T, Ashida K. Etch Stop of Silicon Surface Induced by Tribo-Nanolithography. Nanotechnology (2005) 16(8):1411–4. doi:10.1088/0957-4484/16/8/073
43. Huang J, Jiang L, Li X, Wei Q, Wang Z, Li B, et al. Cylindrically Focused Nonablative Femtosecond Laser Processing of Long‐Range Uniform Periodic Surface Structures with Tunable Diffraction Efficiency. Adv Opt Mater (2019) 7(20):1900706. doi:10.1002/adom.201900706
44. Gnilitskyi I, Derrien TJ, Levy Y, Bulgakova NM, Mocek T, Orazi L. High-speed Manufacturing of Highly Regular Femtosecond Laser-Induced Periodic Surface Structures: Physical Origin of Regularity. Sci Rep (2017) 7(1):8485. doi:10.1038/s41598-017-08788-z
45. Wang L, Xu B-B, Cao X-W, Li Q-K, Tian W-J, Chen Q-D, et al. Competition between Subwavelength and Deep-Subwavelength Structures Ablated by Ultrashort Laser Pulses. Optica (2017) 4(6):637–42. doi:10.1364/optica.4.000637
46. Öktem B, Pavlov I, Ilday S, Kalaycıoğlu H, Rybak A, Yavaş S, et al. Nonlinear Laser Lithography for Indefinitely Large-Area Nanostructuring with Femtosecond Pulses. Nat Photon (2013) 7(11):897–901. doi:10.1038/nphoton.2013.272
47. Dostovalov AV, Korolkov VP, Terentyev VS, Okotrub KA, Dultsev FN, Babin SA. Study of the Formation of Thermochemical Laser-Induced Periodic Surface Structures on Cr, Ti, Ni and NiCr Films under Femtosecond Irradiation. Quan Electron. (2017) 47(7):631–7. doi:10.1070/qel16379
48. Dostovalov AV, Derrien TJ-Y, Lizunov SA, Přeučil F, Okotrub KA, Mocek T, et al. LIPSS on Thin Metallic Films: New Insights from Multiplicity of Laser-Excited Electromagnetic Modes and Efficiency of Metal Oxidation. Appl Surf Sci (2019) 491:650–8. doi:10.1016/j.apsusc.2019.05.171
49. Feng P, Jiang L, Li X, Rong W, Zhang K, Cao Q. Gold-film Coating Assisted Femtosecond Laser Fabrication of Large-Area, Uniform Periodic Surface Structures. Appl Opt (2015) 54(6):1314–9. doi:10.1364/ao.54.001314
50. Huang J, Jiang L, Li X, Zhou S, Gao S, Li P, et al. Controllable Photonic Structures on Silicon-On-Insulator Devices Fabricated Using Femtosecond Laser Lithography. ACS Appl Mater Inter (2021) 13(36):43622–31. doi:10.1021/acsami.1c11292
51. Di Niso F, Gaudiuso C, Sibillano T, Mezzapesa FP, Ancona A, Lugarà PM. Role of Heat Accumulation on the Incubation Effect in Multi-Shot Laser Ablation of Stainless Steel at High Repetition Rates. Opt Express (2014) 22(10):12200–10. doi:10.1364/oe.22.012200
52. Liu H, Lin W, Lin Z, Ji L, Hong M. Self‐Organized Periodic Microholes Array Formation on Aluminum Surface via Femtosecond Laser Ablation Induced Incubation Effect. Adv Funct Mater (2019) 29(42):1903576. doi:10.1002/adfm.201903576
53. Tsibidis GD, Barberoglou M, Loukakos PA, Stratakis E, Fotakis C. Dynamics of Ripple Formation on Silicon Surfaces by Ultrashort Laser Pulses in Subablation Conditions. Phys Rev B (2012) 86(11):115316. doi:10.1103/physrevb.86.115316
54. Huang M, Zhao F, Cheng Y, Xu N, Xu Z. Mechanisms of Ultrafast Laser-Induced Deep-Subwavelength Gratings on Graphite and diamond. Phys Rev B (2009) 79(12):125436. doi:10.1103/physrevb.79.125436
55. Bonse J, Krüger J. Pulse Number Dependence of Laser-Induced Periodic Surface Structures for Femtosecond Laser Irradiation of Silicon. J Appl Phys (2010) 108(3):034903. doi:10.1063/1.3456501
56. Yang Y, Yang J, Xue L, Guo Y. Surface Patterning on Periodicity of Femtosecond Laser-Induced Ripples. Appl Phys Lett (2010) 97(14):141101. doi:10.1063/1.3495785
57. Li X, Rong W, Jiang L, Zhang K, Li C, Cao Q, et al. Generation and Elimination of Polarization-dependent Ablation of Cubic Crystals by Femtosecond Laser Radiation. Opt Express (2014) 22(24):30170–6. doi:10.1364/oe.22.030170
58. He W, Yang J, Guo C. Controlling Periodic Ripple Microstructure Formation on 4H-SiC crystal with Three Time-Delayed Femtosecond Laser Beams of Different Linear Polarizations. Opt Express (2017) 25(5):5156–68. doi:10.1364/oe.25.005156
59. Liu J, Jia X, Wu W, Cheng K, Feng D, Zhang S, et al. Ultrafast Imaging on the Formation of Periodic Ripples on a Si Surface with a Prefabricated Nanogroove Induced by a Single Femtosecond Laser Pulse. Opt Express (2018) 26(5):6302–15. doi:10.1364/oe.26.006302
60. Rohloff M, Das SK, Höhm S, Grunwald R, Rosenfeld A, Krüger J, et al. Formation of Laser-Induced Periodic Surface Structures on Fused Silica upon Multiple Cross-Polarized Double-Femtosecond-Laser-Pulse Irradiation Sequences. J Appl Phys (2011) 110(1):014910. doi:10.1063/1.3605513
61. Jiang L, Shi X, Li X, Yuan Y, Wang C, Lu Y. Subwavelength Ripples Adjustment Based on Electron Dynamics Control by Using Shaped Ultrafast Laser Pulse Trains. Opt Express (2012) 20(19):21505–11. doi:10.1364/oe.20.021505
62. Barberoglou M, Gray D, Magoulakis E, Fotakis C, Loukakos PA, Stratakis E. Controlling Ripples' Periodicity Using Temporally Delayed Femtosecond Laser Double Pulses. Opt Express (2013) 21(15):18501–8. doi:10.1364/oe.21.018501
63. Liu W, Hu J, Jiang L, Huang J, Lu J, Yin J, et al. Formation of Laser-Induced Periodic Surface Nanometric Concentric Ring Structures on Silicon Surfaces through Single-Spot Irradiation with Orthogonally Polarized Femtosecond Laser Double-Pulse Sequences. Nanophotonics (2021) 10(4):1273–83. doi:10.1515/nanoph-2020-0568
64. Qiao H, Yang J, Wang F, Yang Y, Sun J. Femtosecond Laser Direct Writing of Large-Area Two-Dimensional Metallic Photonic crystal Structures on Tungsten Surfaces. Opt Express (2015) 23(20):26617–27. doi:10.1364/oe.23.026617
65. Jalil SA, Yang J, ElKabbash M, Singh SC, Guo C. Maskless Formation of Uniform Subwavelength Periodic Surface Structures by Double Temporally-Delayed Femtosecond Laser Beams. Appl Surf Sci (2019) 471:516–20. doi:10.1016/j.apsusc.2018.12.029
66. Lei Y, Yang J, Cong C, Guo C. Fabrication of Homogenous Subwavelength Grating Structures on Metallic Glass Using Double-Pulsed Femtosecond Lasers. Opt Lasers Eng (2020) 134:106273. doi:10.1016/j.optlaseng.2020.106273
67. Zhang Y, Jiang Q, Cao K, Chen T, Cheng K, Zhang S, et al. Extremely Regular Periodic Surface Structures in a Large Area Efficiently Induced on Silicon by Temporally Shaped Femtosecond Laser. Photon Res (2021) 9(5):839–47. doi:10.1364/prj.418937
68. Kerse C, Kalaycıoğlu H, Elahi P, Çetin B, Kesim DK, Akçaalan Ö, et al. Ablation-cooled Material Removal with Ultrafast Bursts of Pulses. Nature (2016) 537(7618):84–8. doi:10.1038/nature18619
Keywords: laser-induced periodic surface structures, ultrafast laser, uniformity control, laser-induced modification, pulse shaping
Citation: Huang J, Liu Y, Jin S, Wang Z, Qi Y, Zhang J, Wang K and Qiu R (2022) Uniformity Control of Laser-Induced Periodic Surface Structures. Front. Phys. 10:932284. doi: 10.3389/fphy.2022.932284
Received: 29 April 2022; Accepted: 26 May 2022;
Published: 06 July 2022.
Edited by:
Shi Bai, RIKEN, JapanReviewed by:
Xiaozhe Chen, China University of Petroleum, ChinaCopyright © 2022 Huang, Liu, Jin, Wang, Qi, Zhang, Wang and Qiu. This is an open-access article distributed under the terms of the Creative Commons Attribution License (CC BY). The use, distribution or reproduction in other forums is permitted, provided the original author(s) and the copyright owner(s) are credited and that the original publication in this journal is cited, in accordance with accepted academic practice. No use, distribution or reproduction is permitted which does not comply with these terms.
*Correspondence: Ji Huang, aHVhbmdqaUBuaW0uYWMuY24=; Kun Wang, d2FuZ2t1bkBuaW0uYWMuY24=
Disclaimer: All claims expressed in this article are solely those of the authors and do not necessarily represent those of their affiliated organizations, or those of the publisher, the editors and the reviewers. Any product that may be evaluated in this article or claim that may be made by its manufacturer is not guaranteed or endorsed by the publisher.
Research integrity at Frontiers
Learn more about the work of our research integrity team to safeguard the quality of each article we publish.