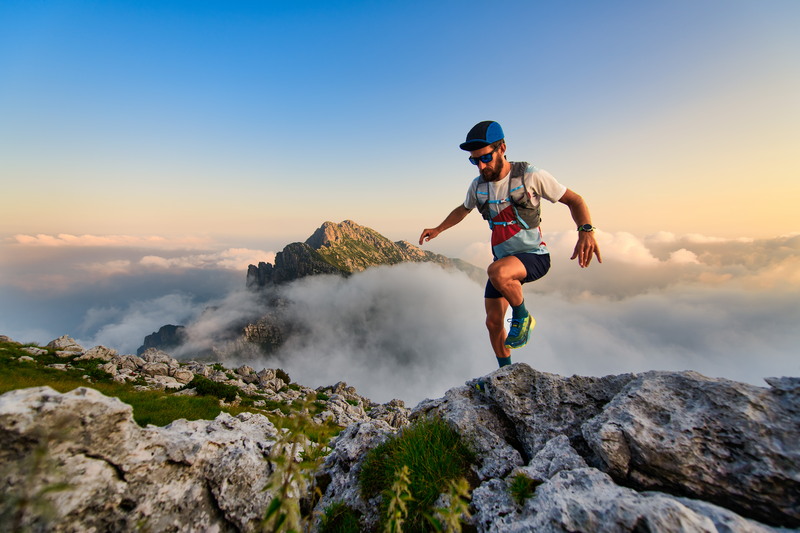
95% of researchers rate our articles as excellent or good
Learn more about the work of our research integrity team to safeguard the quality of each article we publish.
Find out more
ORIGINAL RESEARCH article
Front. Phys. , 12 May 2022
Sec. Physical Acoustics and Ultrasonics
Volume 10 - 2022 | https://doi.org/10.3389/fphy.2022.898464
This article is part of the Research Topic Advances in Phononic and Acoustic Metamaterials View all 7 articles
A thin-film thermal meta-device with a dual-function of thermal shield and generation is proposed and fabricated in this work. The tilted layered structure composed of thermoelectric materials with low thermal conductivity and metal materials with high thermal conductivity is designed to realize the orientation of the incident heat flux and the utilization of heat energy based on the Seebeck effect of the materials. The constructed transverse thin-film thermoelectric device with a Bi2Te3/Cu-layered structure can achieve a maximum output voltage of 20.4 mV and a maximum output power of 7.39 μW at a temperature difference of 80 K. On this basis, the dual-functional film meta-device based on transformation thermodynamics is capable of realizing a heat flux shielding in the central area and generating a transverse output voltage. The experimental results also indicate that there exists a well linear relationship between the output voltage of the meta-device and the temperature difference, which can be extended to accurately monitor the temperature of the central area. This work provides a certain reference for the development of a new class of thermoelectric devices with thermal protection and temperature detection capability.
The significant factors of energy wastage are the uneven dissipation of heat and the reclamation and utilization of low-grade heat [1]. Adeptly and actively directing the heat flux has many practical applications such as solar power generation [2], solar absorber [3], thermophotovoltaics [4], and thermoelectric power generation [5, 6], which can effectively improve energy utilization and thermal management. In the past few years, more and more attention has been paid to “thermal metamaterials” to meet the demand for enhancing the efficiency of low-quality energy utilization [7–10]. The “thermal conductivity substitution method” proposed earlier realized the idea of using layered materials to control the direction and propagation of heat flux [11] and successively verified the heat flux regulation functions such as thermal shielding [12–14], thermal concentrating [15, 16], thermal inversion [17, 18], thermal printing [19], and thermal diode [20]. In addition, thermoelectric devices can generate electricity through the temperature difference based on the Seebeck effect, while the key to the establishment of temperature difference lies in the efficient and directed regulation of heat flow. Introducing the tilted layered structures into thermoelectric devices, which can realize the heterotropic separation and regulation of heat flow and current, has attracted considerable attention because of their potential applications in temperature sensors and power generation.
Artificially tilted multilayer thermoelectric devices, also called transverse thermoelectric devices, have large design freedom to realize the separation of heat flow and current to a certain extent and generate a higher output voltage perpendicular to the direction of heat flow at a limited temperature difference, which further solves the problem of low power generation efficiency of traditional Π-type thermoelectric devices. At present, some reports on the bulk transverse thermoelectric devices have achieved structural optimization and power generation [21–24]. For example, Goldsmid used a single crystal Bi and sintered P-type porous (Bi–Sb)2Te3 to prepare an artificially tilted layered structure, achieving an increase in the transverse ZT from 0.4 to 0.6 by increasing the porosity in (Bi–Sb)2Te3 to reduce the thermal conductivity [25]. Furthermore, Sakai et al. designed a tubular and snake-like transverse thermoelectric device by sparking plasma sintering to obtain a maximum voltage of ∼280 mV [26, 27]. With the development demand of micro-energy collection and self-power technology [28, 29], Xin Mu et al. also fabricated a cross-plane transverse thin-film thermoelectric device composed of Bi/Bi0.5Sb1.5Te3 and achieved a transverse output voltage of 300 μV/K [24, 30]. However, the critical challenge of a cross-plane transverse thin-film thermoelectric device is the difficulty of establishing an effective large temperature difference across the very thin thermoelectric legs, resulting in a lower output power of the device. Therefore, it is quite essential to develop a new type of thin-film thermal meta-device with in-plane heat transfer and large temperature difference establishment.
Micro-scale thermal metamaterials to harvest and protect thermal energy have been systematically studied in our previous work [31]. Combining this novel structural design with the aforementioned transverse thermoelectric effect, we thus proposed a dual-functional thin-film thermal meta-device that enables electricity generation and thermal regulation simultaneously. The in-plane transverse thermoelectric device with Bi2Te3/Cu-layered structure is constructed and fabricated through simple mask-assisted deposition. Based on the effective medium theoretical calculation and simulation analysis, the influences of geometric parameters on the transverse output voltage of thin-film thermoelectric devices are systematically investigated and optimized. In addition, a dual-functional thin-film thermal meta-device assembled by 6 × 6 square layered structures with different tilted angles is designed and fabricated, realizing the dual function of thermal shielding and power generation.
The transverse thin-film thermoelectric device consisting of a single semiconductor material and a metal material can generate a voltage perpendicular to the temperature gradient, as shown in Figure 1A. The output performance of the device is fundamentally determined by the properties and geometry of the material. Based on the effective medium theory, the properties of the transverse thin-film thermoelectric device in parallel (//) and perpendicular (⊥) directions to the layers are expressed as follows [30, 32]:
where
FIGURE 1. (A) Schematic diagram of the in-plane transverse thin-film thermoelectric device. (B) Theoretical effects of θ and α on the transverse Seebeck coefficient Sxz. (C) Design diagram of the thin-film thermal meta-device with a dual-function of thermal shield and generation.
From Eqs 1–5, it is known that the transverse output voltage of tilted thin-film devices is mainly determined by the transverse Seebeck coefficient (
In addition, combined with the directional control of heat flow by the artificially tilted structure and the Seebeck effect of thermoelectric materials, we designed a thin-film thermal meta-device with a dual-function of thermal shield and generation. As shown in Figure1C, the thermal meta-device is made up of 6 × 6 modules in an active region of 28 × 28 mm2, each of which consists of a thermoelectric layer and a metal layer arranged at a certain angle. At the same time, the effect of thermal shielding and power generation of thermal meta-devices with or without a central region is considered and designed. Finite element modeling (by the Workbench software in Ansys 19.2) was used to simulate the temperature distribution and output performance of thermal meta-devices. A three-dimensional thermoelectric coupled model is constructed under a steady-state condition, and each module is assigned with the corresponding material property parameters. The material properties used in this work are listed in Table 1. As for the preparation of thin-film thermal meta-devices, thermoelectric (n-type Bi2Te3) and metal (Cu, Ni) films were deposited by using a magnetron sputtering system (FJL560, SKY Technology Development Co., Ltd. Chinese Academy of Sciences). Before sputtering, the chamber of the instrument was vacuumized to below 6.6 × 10−4 Pa, and the specific preparation parameters of each film in the meta-device are shown in Table 2.
The preconditions of the effective medium theory are an infinite number of layers and an infinite size. For real devices, the structural parameters that affect the output voltage of transverse thin-film thermoelectric devices also include layer width w, length l, height h, and thickness d, which need to be further optimized. Figure 2 shows the effect of geometrical parameters on the output performance of transverse thin-film thermoelectric devices. First, we set the initial structure parameters of the transverse thin-film thermoelectric device as l = 10 mm, h = 5 mm, d = 1 μm, w = 0.2 mm, α = 0.5, and
FIGURE 2. Effect of geometrical parameters on the output performance of transverse thin-film devices. (A) Output voltage curves with respect to h and w; (B) output voltage curves with respect to l and h; (C) output voltage curves with respect to d and h; (D) Voltage and Voltage/Λ with respect to Λ; (E) Temperature distribution and voltage distribution when Λ is 2, 1, and 0.5.
Under the guidance of the theoretical analysis in the previous section, we fabricated a transverse thin-film device with a Bi2Te3/Cu-layered structure and tested its output performance, as shown in Figure 3. The preparation process of the transverse thin-film thermoelectric device is shown in Figure 3A. Firstly, a layer of Bi2Te3 thermoelectric material is deposited on a clean PI substrate using a rectangular pattern mask, and then, the spaced and tilted Ni/Cu strips are deposited on the rectangular thermoelectric material by utilizing a patterned mask. This design method completely solves the problem of excessive internal resistance of the device caused by poor interface between the two materials and considerably improves the time cost and efficiency of device preparation. From Figure 3B, the active region of transverse thin-film thermoelectric devices is 20 × 3 mm2, and the width of each layer is 0.3 mm. The thickness of the Bi2Te3 film is about 7 μm, and the Seebeck coefficient of the Bi2Te3 material is −114 μV/K. The internal resistance of the transverse thin-film thermoelectric device is only 10.4 Ω at room temperature and at ΔT (Thot−Tcold) = 0 K condition. The output voltage and output power with respect to the current of the transverse thin-film device at ΔT from 20 to 80 K have been illustrated in Figure 3C, which shows the interdependencies of voltage, current, and power, revealing the linear dependence of the voltage on current and the parabolic dependence of power on current. As ΔT increases, the short-circuit current (X-intercept) and open-circuit voltage (Y-intercept) rise at the same time. When the maximum ΔT is 80 K, the maximum output voltage is about 20.4 mV, and the maximum output power is about 7.39 μW.
FIGURE 3. (A) Preparation process of the transverse thin-film thermoelectric device by mask-assisted deposition. (B) Photograph of the Bi2Te3/Cu tilted thin-film thermoelectric device. (C) Output performances of the Bi2Te3/Cu tilted thin-film thermoelectric device at different temperature differences ΔTz (ΔTz = Thot–Tcold and Tcold = 293 K).
Based on the theory of transverse thermoelectric effect and transformational heat, a dual-functional thin-film thermal meta-device with thermal shielding and power generation is proposed by controlling the material properties and the tilted angle of layers, which can realize the cooperative control of electricity and heat. We evaluated the effect of a hollow design in the center area and the thickness of the PI substrate on thermal shielding and transverse voltage output through finite element simulation, as shown in Figure 4. Figures 4A, B, 1, and 2 compare the effects of dual-functional thin-film meta-devices with and without a hollow structure on the temperature profiles and voltage output, the temperature and voltage curves of which on the central lines are extracted in Figures 4A, B, 3. The simulated results demonstrate that the hollow design has little effect on the output voltage of the meta-devices. However, the existence of the hollow structure in the center area affects the regulation and propagational direction of heat flow, resulting in an obvious temperature gradient in the center area, as shown in Figure 4B3. At the same time, it can be observed that the voltage on the center line decreases with the decrease in temperature, which also verifies that the output voltage is only determined by the temperature difference applied by the device and the Seebeck coefficient of the materials. Subsequently, the results of Figures 4C1–3 reveal that as the thickness of the thermoelectric film is increased to 50 μm, the temperature gradient is primarily concentrated on the PI substrate without deposited thermoelectric materials at the boundary, resulting in a small temperature difference and a small voltage of 0.24 mV in the active region with the transverse thermoelectric effect.
FIGURE 4. Simulated results of dual-functional thin-film thermal meta-devices. (A1–C1) and (A2–C2) Surface views of temperature distribution and voltage distribution of the dual-functional thin-film thermal meta-devices, respectively, when (A) the center region exists and the thickness of the thin-film is 10 μm, (B) the center region hollows out and the thickness of the thin-film is 10 μm, and (C) the center region hollows out and the thickness of the thin-film is 50 μm. (A3–C3) represents the temperature and voltage curves along the center lines in (A1,2–C1,2), respectively.
To summarize, we can draw the conclusion that this kind of thermal meta-device with a thermoelectric/metal-layered structure tilted at different angles has great potential to realize the dual-function of thermal shielding and transverse power generation at the same time. Considering that the critical factors affecting the transverse output voltage of meta-devices are the inherent Seebeck coefficient of the thermoelectric material and the effective temperature difference on the thermoelectric material, the temperature difference can be directly applied to the boundary of the active area in the subsequent improvement to avoid heat dissipation on the substrate.
In order to verify the aforementioned designed device, we prepared this dual-functional thermal meta-device and characterized its properties simultaneously, the test diagram and experimental results of which are shown in Figure 5. From Figure 5A, the temperatures of the cold side and the hot side of the dual-function thermal device are precisely controlled as 293 and 303 K, respectively. The output property of the meta-device is recorded by using a Keithley 2,400 source meter, and meanwhile, the surface temperature distribution of the meta-devices in the steady state is captured through an infrared camera with a spatial resolution of 3.39 m Rad and a temperature resolution of 0.1 K. As shown in the test setup in Figure 5B, we increased the temperature of the hot side ranged between 303 and 363 K in steps of 20 K while maintaining the temperature of the cold side to 293 K, to measure the output voltage of the meta-device and capture the temperature distribution of the surface simultaneously. Herein, a good linear fitting relationship between the transverse output voltage of the meta-device and the longitudinal temperature difference is observed, indicating that the temperature change of the meta-device can be well reflected by the output voltage. The results also demonstrate that this kind of dual-functional thermal meta-device has great developmental potential in reflecting and monitoring the temperature of the central region in real time according to the measured output voltage.
FIGURE 5. (A) Picture and test drawing of the dual-functional thin-film thermal meta-device. (B) Relationship between the output voltage of the device and the temperature difference set (ΔTz = 10∼80 K). (C) Surface views of temperature distribution of the meta-devices while the hot sides are set to 303, 323, 343, and 363 K. The temperature of the cold side is set to 293 K.
The surface temperature profiles of the meta-devices measured in Figure 5C show that the temperature value measured at the center region increases slightly with the increase in the temperature of the hot side and is closer to the temperature of the cold side. The reason for this result may be that there exists a large contact thermal resistance between the heat source and the PI substrate and the heat loss caused by the air [33] so that the effective temperature difference applied to the meta-device is less than the set temperature difference. In terms of the thermal effect, the temperatures in the center region of the meta-devices are practically constant under different temperature differences, which is comparable to the properties exhibited by a thermal shield. Furthermore, as the temperature difference increases, the temperature of the center becomes larger, and the isothermal region at the center is still retained. Notably, the temperature change caused by Joule heat is almost negligible and does not affect the surface temperature distribution of the meta-device. To sum up, we have achieved a dual-functional meta-device with the novel property of thermal shielding and an output voltage of 4.3 mV at a temperature difference of 80 K simultaneously.
In summary, based on the transverse thermoelectric effect produced by tilted layered structures, we designed and fabricated an in-plane transverse thin-film thermoelectric device with the dual-function of thermal shield and generation. The geometrical parameters of the transverse thin-film thermoelectric device are optimized, and the maximum output voltage can be obtained while θ = 45° and α = 0.5. Consequently, the fabricated transverse thin-film thermoelectric device shows an open circuit voltage of about 20.4 mV and an output power of 7.39 μW at a temperature difference of 80 K. Moreover, combining with the transform heat theory and transverse thermoelectric effect, a dual-functional thin-film thermal meta-device is proposed and designed by 6 × 6 square layered structures with different tilted angles, which can realize thermal shielding and generation simultaneously. Furthermore, the output voltage of the prepared meta-device shows a good linear relationship with the set temperature difference with potential to monitor the temperature of the central area. This work provides a valid strategy for the fabrication and design of multifunctional thin-film meta-devices, promoting a widespread application of thin-film thermoelectric metamaterials.
The original contributions presented in the study are included in the article/Supplementary Material, further inquiries can be directed to the corresponding authors.
WZ and YD contributed to the conception and design of the study. QZ and JY contributed to the numerical simulations and experiments. QZ wrote the first draft of the manuscript. QZ, JY, WZ, and YD contributed to manuscript revision, read, and approved the submitted version.
The work was supported by the National Key R&D Program of China (Grant No. 2018YFA0702100), the National Natural Science Foundation of China (Grant No. U21A2079), the Beijing Natural Science Foundation of China (Grant No. 2182032), the Zhejiang Provincial Key R&D Program of China (Grant Nos. 2021C05002 and 2021C01026), and the Fundamental Research Funds for the Central Universities.
The authors declare that the research was conducted in the absence of any commercial or financial relationships that could be construed as a potential conflict of interest.
All claims expressed in this article are solely those of the authors and do not necessarily represent those of their affiliated organizations, or those of the publisher, the editors, and the reviewers. Any product that may be evaluated in this article, or claim that may be made by its manufacturer, is not guaranteed or endorsed by the publisher.
1. Tan T, Yan Z, Zou H, Ma K, Liu F, Zhao L, et al. Renewable Energy Harvesting and Absorbing via Multi-Scale Metamaterial Systems for Internet of Things. Appl Energ (2019) 254:113717. doi:10.1016/j.apenergy.2019.113717
2. Zhu W, Deng Y, Cao L. Light-concentrated Solar Generator and Sensor Based on Flexible Thin-Film Thermoelectric Device. Nano Energy (2017) 34:463–71. doi:10.1016/j.nanoen.2017.03.020
3. Ma R, Wu D, Liu Y, Ye H, Sutherland D. Copper Plasmonic Metamaterial Glazing for Directional thermal Energy Management. Mater Des (2020) 188:108407. doi:10.1016/j.matdes.2019.108407
4. Hu R, Song J, Liu Y, Xi W, Zhao Y, Yu X, et al. Machine Learning-Optimized Tamm Emitter for High-Performance Thermophotovoltaic System with Detailed Balance Analysis. Nano Energy (2020) 72:104687. doi:10.1016/j.nanoen.2020.104687
5. Wu Z, Zhang S, Liu Z, Mu E, Hu Z. Thermoelectric Converter: Strategies from Materials to Device Application. Nano Energy (2022) 91:106692. doi:10.1016/j.nanoen.2021.106692
6. Sun T, Zhou B, Zheng Q, Wang L, Jiang W, Snyder GJ. Stretchable Fabric Generates Electric Power from Woven Thermoelectric Fibers. Nat Commun (2020) 11:572. doi:10.1038/s41467-020-14399-6
7. Su Y, Li Y, Yang T, Han T, Sun Y, Xiong J, et al. Path‐Dependent Thermal Metadevice beyond Janus Functionalities. Adv Mater (2021) 33:2003084–7. doi:10.1002/adma.202003084
8. Sha W, Xiao M, Zhang J, Ren X, Zhu Z, Zhang Y, et al. Robustly Printable Freeform thermal Metamaterials. Nat Commun (2021) 12:1–8. doi:10.1038/s41467-021-27543-7
9. Zhu Z, Ren X, Sha W, Xiao M, Hu R, Luo X. Inverse Design of Rotating Metadevice for Adaptive thermal Cloaking. Int J Heat Mass Transfer (2021) 176:121417. doi:10.1016/j.ijheatmasstransfer.2021.121417
10. Hu R, Iwamoto S, Feng L, Ju S, Hu S, Ohnishi M, et al. Machine-learning-optimized Aperiodic Superlattice Minimizes Coherent Phonon Heat Conduction. Phys Rev X (2020) 10:21050. doi:10.1103/PhysRevX.10.021050
11. Yang T, Vemuri KP, Bandaru PR. Experimental Evidence for the Bending of Heat Flux in a thermal Metamaterial. Appl Phys Lett (2014) 105:083908. doi:10.1063/1.4894387
12. Zhang J, Huang S, Hu R. Adaptive Radiative thermal Camouflage via Synchronous Heat Conduction. Chin Phys. Lett. (2021) 38:010502–5. doi:10.1088/0256-307X/38/1/010502
13. Hu R, Xi W, Liu Y, Tang K, Song J, Luo X, et al. Thermal Camouflaging Metamaterials. Mater Today (2021) 45:120–41. doi:10.1016/j.mattod.2020.11.013
14. Yang S, Xu L, Huang J. Thermal Magnifier and External Cloak in Ternary Component Structure. J Appl Phys (2019) 125:055103. doi:10.1063/1.5083185
15. Liu D-P, Chen P-J, Huang H-H. Realization of a thermal Cloak-Concentrator Using a Metamaterial Transformer. Sci Rep (2018) 8:1–11. doi:10.1038/s41598-018-20753-y
16. Hai F, Zhu W, Cao L, Yang X, Deng Y. Tunable Control of Extremely Concentrated Heat Flux through a thermal Manipulator. J Appl Phys (2019) 126:135110. doi:10.1063/1.5117858
17. Zhou L, Huang S, Wang M, Hu R, Luo X. While Rotating while Cloaking. Phys Lett A (2019) 383:759–63. doi:10.1016/j.physleta.2018.11.041
18. Keidar M, Shashurin A, Delaire S, Fang X, Beilis . Inverse Heat Flux in Double Layer thermal Metamaterial. J Phys D: Appl Phys (2015) 48:485104. doi:10.1088/0022-3727/48/48/485104
19. Hu R, Huang S, Wang M, Luo X, Shiomi J, Qiu CW. Encrypted thermal Printing with Regionalization Transformation. Adv Mater (2019) 31:1807849–7. doi:10.1002/adma.201807849
20. Zhao W, Zhu Z, Fan Y, Xi W, Hu R, Luo X. Temporally-adjustable Radiative thermal Diode Based on Metal-Insulator Phase Change. Int J Heat Mass Transfer (2022) 185:122443. doi:10.1016/j.ijheatmasstransfer.2021.122443
21. Zhou H, Liu H, Qian G, Yu H, Gong X, Li X, et al. Geometrical Optimization and Transverse Thermoelectric Performances of Fe/Bi2Te2.7Se0.3 Artificially Tilted Multilayer Thermoelectric Devices. Micromachines (2022) 13:233. doi:10.3390/mi13020233
22. Zhu W, Guo X, Sang X, Wei P, Nie X, Zhao W, et al. Fabrication and Performance Prediction of Ni/Bi0.5Sb1.5Te3 Artificially-Tilted Multilayer Devices with Transverse Thermoelectric Effect. J Power Sourc (2021) 512:230471. doi:10.1016/j.jpowsour.2021.230471
23. Uchida K-i., Zhou W, Sakuraba Y. Transverse Thermoelectric Generation Using Magnetic Materials. Appl Phys Lett (2021) 118:140504. doi:10.1063/5.0046877
24. Mu X, Zhou H, Zhao W, He D, Zhu W, Nie X, et al. High-performance YbAl3/Bi0.5Sb1.5Te3 Artificially Tilted Multilayer Thermoelectric Devices via Material Genome Engineering Method. J Power Sourc (2019) 430:193–200. doi:10.1016/j.jpowsour.2019.04.109
25. Goldsmid HJ. Synthetic Transverse Thermoelements Made from Porous Bismuth telluride and Single crystal Bismuth. Phys Stat Sol (A) (2008) 205:2966–9. doi:10.1002/pssa.200824241
26. Sakai A, Kanno T, Takahashi K, Tamaki H, Adachi H, Yamada Y. Enhancement in Performance of the Tubular Thermoelectric Generator (TTEG). J Elec Materi (2013) 42:1612–6. doi:10.1007/s11664-012-2355-4
27. Kanno T, Takahashi K, Sakai A, Tamaki H, Kusada H, Yamada Y. Detection of thermal Radiation, Sensing of Heat Flux, and Recovery of Waste Heat by the Transverse Thermoelectric Effect. J Elec Materi (2014) 43:2072–80. doi:10.1007/s11664-013-2959-3
28. Wang Y, Zhu W, Deng Y, Fu B, Zhu P, Yu Y, et al. Self-powered Wearable Pressure Sensing System for Continuous Healthcare Monitoring Enabled by Flexible Thin-Film Thermoelectric Generator. Nano Energy (2020) 73:104773. doi:10.1016/j.nanoen.2020.104773
29. El Oualid S, Kosior F, Dauscher A, Candolfi C, Span G, Mehmedovic E, et al. Innovative Design of bismuth-telluride-based Thermoelectric Micro-generators with High Output Power. Energy Environ. Sci. (2020) 13:3579–91. doi:10.1039/d0ee02579h
30. Mu X, Zhu W, Zhao W, Zhou H, Sun Z, Li C, et al. Excellent Transverse Power Generation and Cooling Performances of Artificially Tilted Thermoelectric Film Devices. Nano Energy (2019) 66:104145. doi:10.1016/j.nanoen.2019.104145
31. Zhang Q, Zhu W, Feng J, Zhou J, Deng Y. High-efficient Heat Flux Manipulation of Micro-scale thermal Metamaterials with Facile Functional Unit Design. Mater Des (2021) 204:109657. doi:10.1016/j.matdes.2021.109657
32. Bandaru PR, Vemuri KP, Canbazoglu FM, Kapadia RS. Layered thermal Metamaterials for the Directing and Harvesting of Conductive Heat. AIP Adv (2015) 5:053403–26. doi:10.1063/1.4916220
Keywords: thermal meta-device, transverse thermoelectric generation, thermal shielding, artificially tilted structure, finite element simulation
Citation: Zhang Q, Yuan J, Zhu W and Deng Y (2022) A Thin-Film Thermal Meta-Device With Dual Function of Thermal Shield and Generation Based on an Artificially Tilted Structure. Front. Phys. 10:898464. doi: 10.3389/fphy.2022.898464
Received: 17 March 2022; Accepted: 08 April 2022;
Published: 12 May 2022.
Edited by:
Yu-Gui Peng, Huazhong University of Science and Technology, ChinaReviewed by:
Run Hu, Huazhong University of Science and Technology, ChinaCopyright © 2022 Zhang, Yuan, Zhu and Deng. This is an open-access article distributed under the terms of the Creative Commons Attribution License (CC BY). The use, distribution or reproduction in other forums is permitted, provided the original author(s) and the copyright owner(s) are credited and that the original publication in this journal is cited, in accordance with accepted academic practice. No use, distribution or reproduction is permitted which does not comply with these terms.
*Correspondence: Wei Zhu, emh1X3dlaUBidWFhLmVkdS5jbg==; Yuan Deng, ZGVuZ3l1YW5AYnVhYS5lZHUuY24=
Disclaimer: All claims expressed in this article are solely those of the authors and do not necessarily represent those of their affiliated organizations, or those of the publisher, the editors and the reviewers. Any product that may be evaluated in this article or claim that may be made by its manufacturer is not guaranteed or endorsed by the publisher.
Research integrity at Frontiers
Learn more about the work of our research integrity team to safeguard the quality of each article we publish.