- 1National Synchrotron Light Source II, Brookhaven National Laboratory, Upton, NY, United States
- 2Synchrotron SOLEIL, L’Orme des Merisiers, Gif-Sur-Yvette, France
- 3ALBA Synchrotron Light Source, Cerdanyola del Vallès, Spain
Soft X-ray off-axis elliptical mirrors bring new challenges for X-ray mirror metrology. These highly asymmetrically curved elliptical cylindrical mirrors with a total slope range >10 mrad are extremely challenging to measure. Their total slope range exceeds the measuring range of most angular sensors used for X-ray mirror inspection. To overcome this problem, it is possible to stitch partial slope data by measuring the mirror at different pitch angles (multi-pitch angles). By revisiting the theory of the multi-pitch Nano-accuracy Surface Profiler (NSP), we derive the sampling position error on the mirror surface as a function of the mirror height profile and the measurement error of the pitch rotation center. When measuring “extreme”, highly asymmetrically curved, elliptical mirrors, the calculation of the mirror height profile with iterative reconstruction outperforms the classical “flat assumption” (i.e., assuming that the mirror sag is negligible). As demonstrated by our simulations, a proper tolerance evaluation on the measurement of pitch rotation center is needed to assess the measurement accuracy (systematic error) for these strongly aspherical mirrors using the multi-pitch NSP technique. Taking a real design of an “extreme” elliptical mirror as a case study, we conduct a Monte Carlo simulation to mimic the measurement and characterization process to analyze the impact of several error sources. With the measurement uncertainty of the pitch rotation center, the multi-pitch NSP measurement can estimate the grazing angle
Introduction
To match the evolution of the light source facilities (synchrotron radiation and free-electron lasers), X-ray optical elements must be at the diffraction limit to deliver the high-quality X-ray beam to the end station for scientific research. As a type of widely used X-ray optics, X-ray mirrors are required to be fabricated at the sub-100 nrad Root Mean Square (RMS) level for residual slope errors or the sub-nm RMS for residual height errors to preserve the wavefront of the incoming X-ray beam and produce a diffraction limited focal spot. Special dedicated optical metrology systems were developed to characterize such high-precision long rectangular X-ray mirrors. The Long Trace Profiler (LTP) [1] and the Nanometer Optical component measuring Machine (NOM) [2] are two classical optical slope profilers widely used in the light source facilities all over the world [3–8]. With slightly different configuration, the Nano-accuracy Surface Profiler (NSP) [9] was developed with two separate beam arms. The sample beam arm (with the sample beam autocollimator) scans the test mirror surface (x-scan) with a fixed working distance, while the reference beam arm (with reference beam autocollimator) monitors the carriage wobble.
To meet the increasing need of the scientific research, more strongly curved focusing mirrors have been proposed for soft X-ray beamline. A soft X-ray nanoprobe will offer nano-imaging and spectroscopy tools non-destructive capabilities to study advanced materials using Nano ARPES and Nano RIXS experimental techniques [10]. To produce a diffraction-limited spot size for low energy (high λ), X-ray mirrors with high numerical aperture are required. These mirrors can have a total slope range larger than the current measuring range of the LTP/NOM/NSP (10 mrad). To overcome this problem, it is possible to stitch partial slope data recorded by measuring the mirror at different pitch angles. Based on this idea, Polack et al. proposed the Linearity Error Elimination Procedure (LEEP) algorithm [11]. This algorithm can reconstruct not only the mirror slope profile, but also the instrument error of the optical head at the same time. A modified LEEP algorithm was proposed for the NSP setup to reconstruct the instrument error of the sample-beam autocollimator [12]. The ambiguity in the algorithm was addressed by proposing several regularizations in the data acquisition and the algorithm constraints.
On the experimental side, when the LEEP algorithm or any other stitching algorithm is used where the pitch angle must be adjusted between different x-scans, the rotation center of the pitch needs to be known to a certain extent. The error on the position of the rotation center leads to pitch-dependent discrepancies of the sampling positions on the test mirror. For circular cylinders and shallow elliptical mirrors (few mrad total slope), the pitch rotation center does not need to be known with high accuracy, because the sampling position errors introduce little systematic slope errors in the final results (<10 nrad RMS). However, when highly curved and asymmetric elliptical mirrors must be measured, it becomes critical to know the pitch rotation center location with enough accuracy as this error leads to nonnegligible total systematic slope error contribution. In addition, the commonly applied “flat assumption” in the LEEP algorithm or the multi-pitch NSP technique as shown in Figure 1, assuming that the mirror sag is negligible, may no longer be valid when measuring such “extreme” ellipses.
In this work, the theory of the multi-pitch NSP technique is briefly reviewed, followed by the analysis of the influence of the pitch rotation center location with respect to the surface of the mirror under test. We propose a method to overcome the invalid “flat assumption” issue in the reconstruction of “extreme” ellipses. Then we focus on the measurement tolerance of the pitch rotation center location in the horizontal and the vertical directions. Series of simulations with different ellipse geometries are carried out to study the trend between the measurement tolerance of the pitch rotation center location and the curvature variation of the aspherical mirrors. We implement a Monte Carlo simulation with a real mirror design. Taking the uncertainty of the pitch rotation center measurement and the uncertainty of the angle measurement as two inputs, the multi-pitch NSP technique with the Monte Carlo simulation can give the slope residuals and an estimation of the grazing angle
Theory of the Multi-Pitch NSP Technique
Based on the redundant dataset acquired from all the x-scans for different pitch angles, the multi-pitch NSP technique can simultaneously calculate the mirror surface slope, the instrument error of the sample-beam autocollimator, and the introduced pitch angles [12]. For simplicity, we define the origin of the world coordinate system
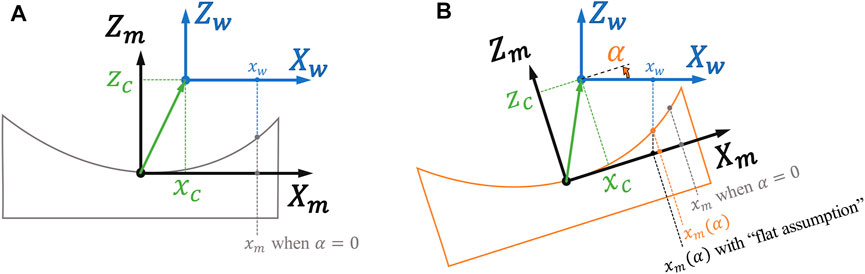
FIGURE 2. The world coordinate system
The center point of the x-scan range on the mirror surface is defined as the origin of the mirror coordinate system
After a rotation in pitch with an angle
The x position in world coordinate system can be calculated as
For a particular measurement (
Under the
Here the instrument error of the reference-beam autocollimator is ignored in our model, as the reference-beam angle
The mirror slope
Once the coefficients
where the first pitch angle
One thing to highlight is that nonuniform pitch steps
To calculate the sampling position
Theoretical Analysis of the Sampling Position Error at Different Pitch Angles Considering the Mirror Height Profile and the Measurement Error of the Pitch Rotation Center Location
The pitch rotation center
If we have a measurement error of
Based on Eq. 3, the estimated sampling position on the mirror
And the true sampling position
The sampling position error
With some simplifications, it becomes
Finally, we have the sampling position error as
Considering the pitch angle
By using a simple measurement tool, such as a metric ruler, and the mechanical tolerances of the pitch rotation system, it is not difficult to determine the pitch rotation center location with a few mm accuracy. For a circular cylinder, this level of uncertainty is enough. The slope profile of a circular cylinder is linear with
For simplicity, the mirror height profile
Simulation Study on Multi-Pitch NSP With “Extreme” Ellipses
To study the influence of
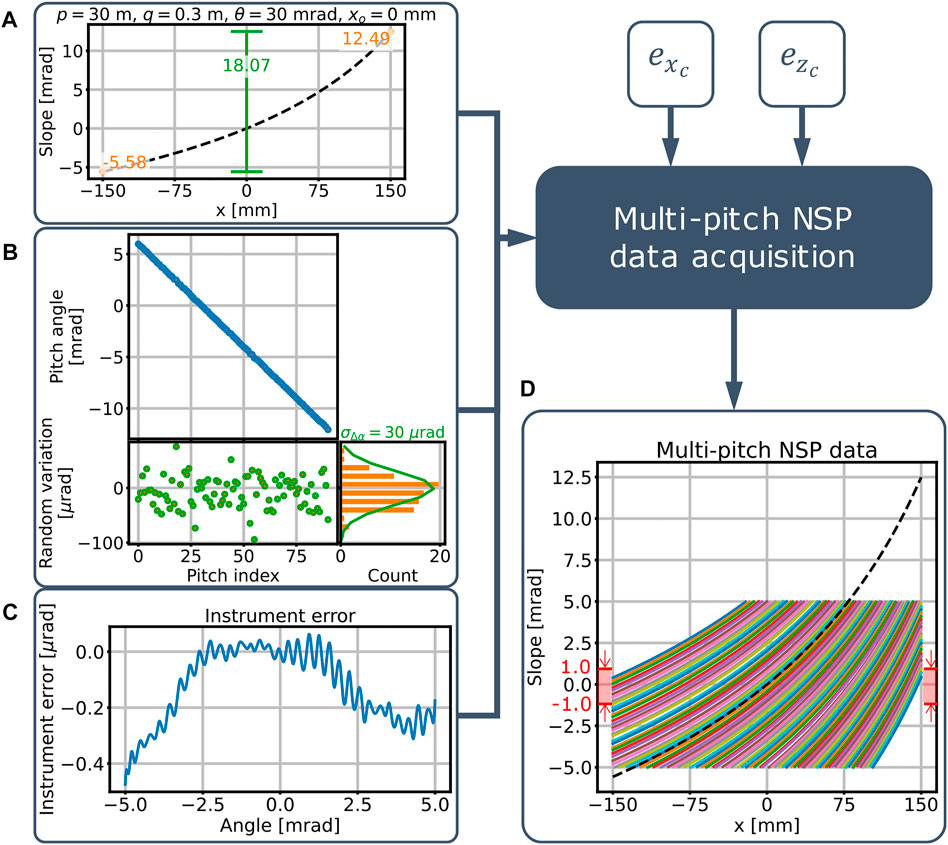
FIGURE 3. The simulation of the multi-pitch NSP dataset. (A) the tangential slope of the elliptical cylinder with the default parameters, (B) the pitch angle and its random variations in step, (C) the instrument error of sample-beam autocollimator from a real multi-pitch NSP measurement, and (D) the simulated multi-pitch NSP data with the dashed curve showing the whole slope profile of the test mirror.
Descriptions of the Multi-Pitch NSP Simulations
In our simulations, as shown in Figure 3A, we used a default ellipse with the following parameters: the source distance
To avoid the known periodic errors in the reconstruction [12], pitch steps with small random variations are implemented. For simplicity as shown in Figure 3B, we choose the average pitch step
The instrument error used in the simulation shown in Figure 3C is a reconstruction of the instrument error from a real multi-pitch NSP experiment [12]. The measurement error of the pitch rotation center
Target Ellipse Fitting
For the characterization of synchrotron mirrors, the target ellipse fitting on slope is usually implemented with
1) The source and image distance values
2) By changing the grazing angle
Therefore, we fit the reconstructed slope to the best ellipse with fixed
Iterative Reconstruction
Our first example is to demonstrate that the “flat assumption” (
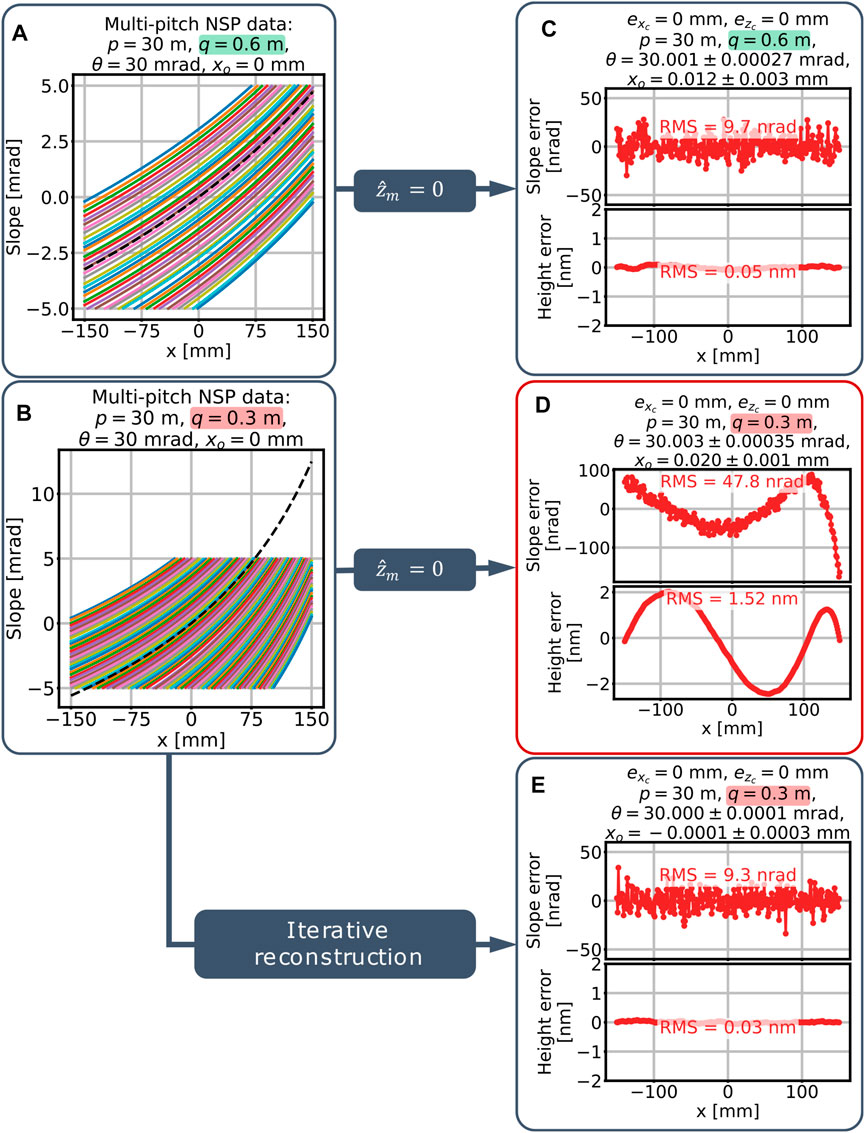
FIGURE 4. The “flat assumption” (
However, as demonstrated in Figure 4, the “flat assumption” does not always give a perfect reconstruction. For the more “relaxed” ellipse with
To measure “extreme” elliptical mirrors, we need to consider the mirror height profile
Using this approach, the
Simulation Study on the Measurement Tolerance of the Pitch Rotation Center
To conduct a tolerance study, we need to set a threshold. Here we set the threshold on the systematic slope error contributed from
The error contribution due to
Default Ellipse Case and Influence of Shape Parameters
Here we take the default ellipse (
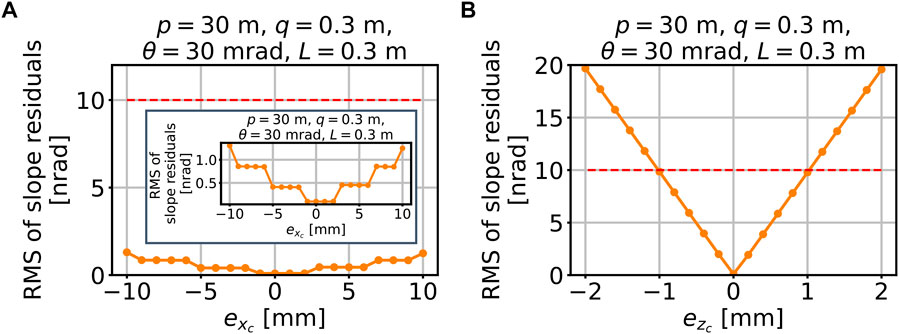
FIGURE 5. Simulation with the default ellipse demonstrates the tolerance of
From Figure 5B, we can see that only when the measurement errors on the vertical distance
Following Eq. 13 and Figure 5, the tolerance of
Starting with the default ellipse parameters, we then modify one of the parameters
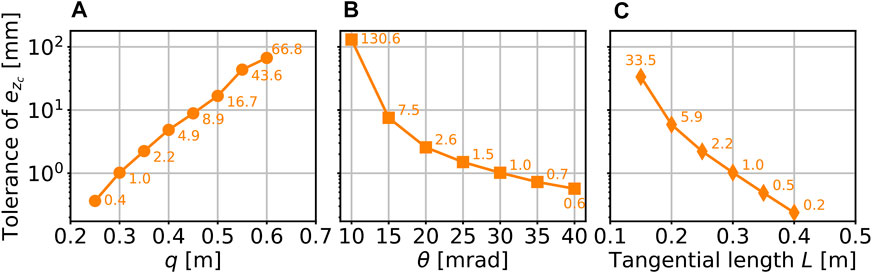
FIGURE 6. Tolerance of
The results in Figure 6 clearly reveal that the more “extreme” are the ellipses, with shorter image distance
Two Ellipses From Beamline Optical Designs
The parameters of two elliptical cylindrical mirrors are listed in Table 1. These two mirrors are taken from two different sets of Kirkpatrick-Baez mirror systems proposed for the NSLS-II ARI beamlines.
To give a better description of these ellipse parameters, the height, slope, Radius of Curvature (RoC), and curvature variations of M1 and M2 are plotted in Figure 7. For M1, the mirror sag is about 0.5 mm, and its total slope range is almost 15 mrad, which is beyond the 10-mrad angular measuring range of the sampling-beam autocollimator in the NSP instrument. It is therefore necessary to change the pitch angle to measure the whole tangential profile of M1. Compared to M1, M2 is even more “extreme”. The mirror sag is 1.65 mm and the total slope range is about 45 mrad.
These mirrors are intended to focus the incoming X-ray beam to a diffraction limited spot size at 1 keV and 250 eV for M1 and M2, respectively (the diffraction limited spot size of about 37 and 72.6 nm for M1 and M2). To satisfy the Maréchal criterion, the height error of the diffraction limited mirror should be less than
In this study, we disregard the RoC limit by the sample-beam autocollimator in our NSP instrument (around 7–8 m). We assume the optical head can measure the mirror surfaces with these RoC values. Our main objective is to evaluate the tolerance of the pitch rotation center location. The RMS values of the multi-pitch NSP reconstructed slope residuals are calculated when the
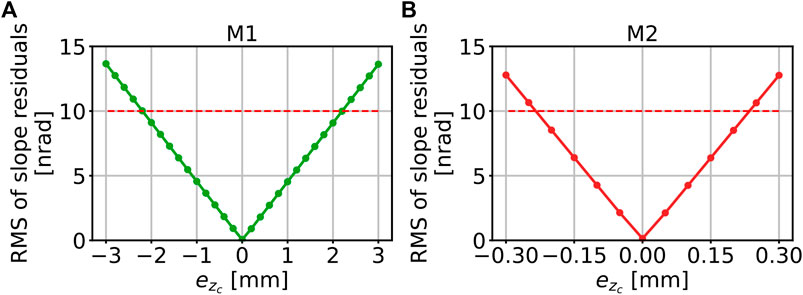
FIGURE 8. The RMS value of the slope residuals varies along the measurement error of the vertical distance
Applying the 10-nrad-RMS threshold as the error budget analyzed above, the tolerance of the
By numerically searching the intersections between the curve of the RMS of slope residuals and the red dash line of 10-nrad-RMS threshold, we can determine the tolerance values of
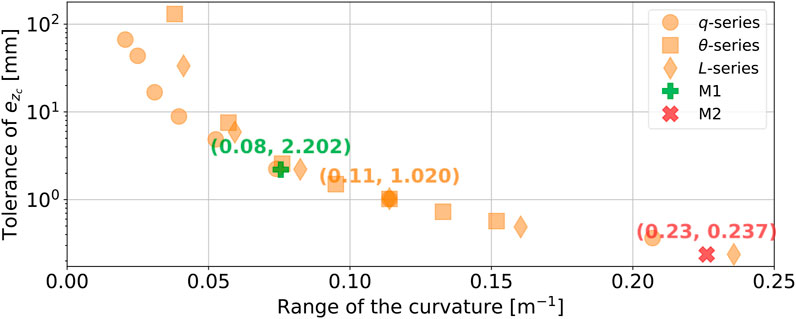
FIGURE 9. The
An elliptical mirror becomes more “extreme” when its curvature varies in a larger range. The requirement on the pitch rotation center measurement becomes tight if the ellipse to test is very “extreme” as shown in Figure 9. The use the multi-pitch NSP technique to measure these kind of X-ray mirrors requires a precise auxiliary measurement of the pitch rotation center.
The vertical error of the pitch rotation center
Let’s take a critical condition, M2 with
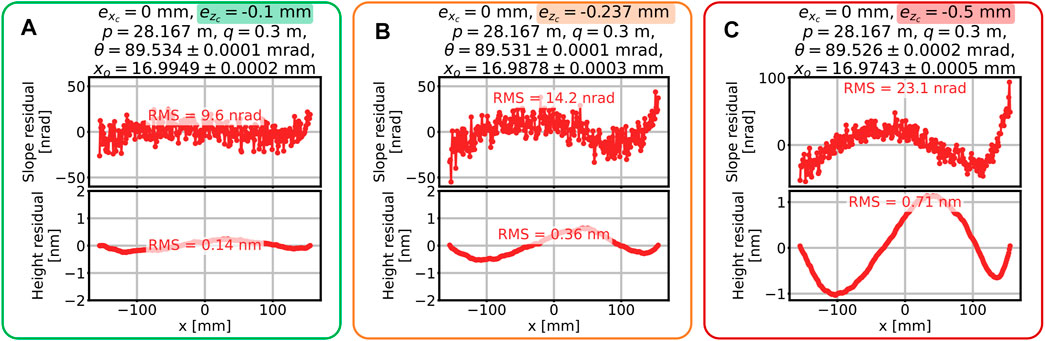
FIGURE 10. The slope and height residuals when measuring M2 with
As shown in Figure 10A, the slope and height residuals are smaller when the center of rotation error is reduced to
When
Framework to Determine the Measurement Tolerance of the Pitch Rotation Center
Before performing a multi-pitch NSP, it is required to ensure that the measurement of the pitch rotation center can meet the tolerance requirement. Therefore, we suggest a framework to determine the needed measurement accuracy of
1) Set the RMS threshold of slope residuals from the best fit. This RMS threshold should be 1/10 of the RMS value of the desired slope errors in total. For example, if 100 nrad RMS total slope error is pursued based on the mirror specification, the RMS threshold of slope residuals should be set as 10 nrad.
2) Calculate the tolerance of the
3) The RMS value
Within this framework, one can estimate if the selected metrology tool is adequate to measure
Moreover, we can also carry out Monte Carlo simulations considering both uncertainties of the angular sensor and of the
Monte Carlo Simulation on M1
From what precedes we can infer that a correlation exists between the error committed on
M1 is selected as the test mirror in this Monte Carlo simulation. The average pitch steps are about 0.2 mrad, and 76 pitch angles are performed in the multi-pitch NSP simulation. As shown in Figures 8, 9, the tolerance of the
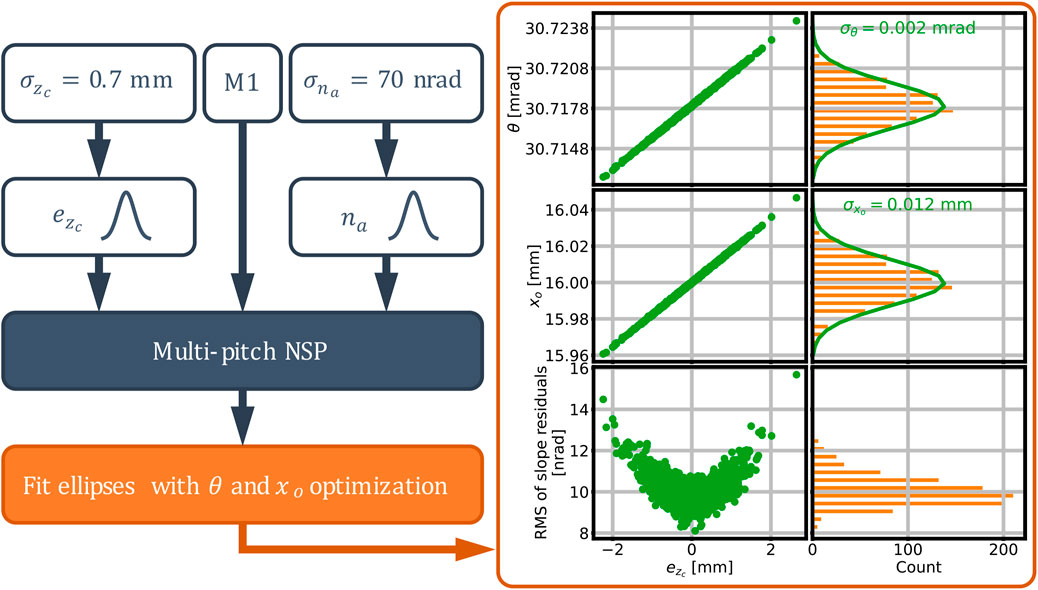
FIGURE 11. The Monte Carlo simulation of measuring M1 using the multi-pitch NSP with a pitch rotation center measurement error
After the best fit of ellipse (optimization of
Conclusion
To take the challenge of measuring extreme off-axis elliptical mirrors, we revisit the multi-pitch NSP technique from its basic theory to the reconstruction algorithm. The true abscissa
The tolerance of the measurement of the pitch rotation center location (
A Monte Carlo simulation on a real design of an “extreme” elliptical mirror shows that, with a known accuracy of the pitch rotation center measurement, we can estimate
This simulation study can guide the real multi-pitch NSP measurement for “extreme” elliptical mirrors. The tolerance of
Data Availability Statement
The original contributions presented in the study are included in the article/Supplementary Material, further inquiries can be directed to the corresponding author.
Author Contributions
LH and MI contributed to conception, methodology and funding acquisition. LH wrote the first draft of the manuscript. TW and KN contributed to the review of the manuscript. FP reviewed and modified the manuscript. JN contributed to the review of the revised version. MI supervised the research. All authors discussed the results, revised the manuscript, and approved the submitted version.
Funding
This work was supported by NSLS-II Facility Improvement Project (21153) and DOE Office of Science (DE-SC0012704).
Conflict of Interest
The authors declare that the research was conducted in the absence of any commercial or financial relationships that could be construed as a potential conflict of interest.
Publisher’s Note
All claims expressed in this article are solely those of the authors and do not necessarily represent those of their affiliated organizations, or those of the publisher, the editors and the reviewers. Any product that may be evaluated in this article, or claim that may be made by its manufacturer, is not guaranteed or endorsed by the publisher.
Acknowledgments
This research used resources of the National Synchrotron Light Source II, a U.S. Department of Energy (DOE) Office of Science User Facility, operated for the DOE Office of Science by Brookhaven National Laboratory under Contract No. DE-SC0012704.
References
1. Takacs PZ, Qian S-n., Colbert J. (1987). Design of A Long Trace Surface Profiler, Metrol Fig Finish, p. 59. Proc. SPIE 0749. doi:10.1117/12.939842
2. Siewert F, Noll T, Schlegel T, Zeschke T, Lammert H. The Nanometer Optical Component Measuring Machine: A New Sub-nm Topography Measuring Device for X-ray Optics at BESSY. AIP Conf Proc (2004) 705:847–50. doi:10.1063/1.1757928
3. Qian S, Jark W, Takacs PZ. The Penta‐prism LTP: A Long‐trace‐profiler with Stationary Optical Head and Moving Penta Prisma). Rev Scientific Instr (1995) 66:2562–9. doi:10.1063/1.1145658
4. Ali Z, Yashchuk VV. Automated Suppression of Errors in LTP-II Slope Measurements of X-ray Optics .(2011) Part 2 : Specification for automated rotating/flipping/aligning system n.d.:1–8. Available at: https://www.osti.gov/servlets/purl/1170543. doi:10.2172/1170543
5. Siewert F, Buchheim J, Zeschke T. Characterization and Calibration of 2nd Generation Slope Measuring Profiler. Nucl Instr Methods Phys Res Section A: Acc Spectrometers, Detectors Associated Equipment (2010) 616:119–27. doi:10.1016/j.nima.2009.12.033
6. Nicolas J, Pedreira P, Šics I, Ramírez C, Campos J. Nanometer Accuracy with Continuous Scans at the ALBA-NOM. Adv Metrol X-ray EUV Opt VI (2016) 9962:996203. doi:10.1117/12.2238128
7. Alcock SG, Sawhney KJS, Scott S, Pedersen U, Walton R, Siewert F, et al. The Diamond-NOM: A Non-contact Profiler Capable of Characterizing Optical Figure Error with Sub-nanometre Repeatability. Nucl Instr Methods Phys Res Section A: Acc Spectrometers, Detectors Associated Equipment (2010) 616:224–8. doi:10.1016/j.nima.2009.10.137
8. Nicolas J, Martínez JC. Characterization of the Error Budget of Alba-NOM. Nucl Instr Methods Phys Res Section A: Acc Spectrometers, Detectors Associated Equipment (2013) 710:24–30. doi:10.1016/j.nima.2012.10.125
9. Qian S, Idir M. Innovative Nano-Accuracy Surface Profiler for Sub-50 Nrad Rms Mirror Test. 8th Int Symp Adv Opt Manuf Test Technol Subnanom Accuracy Meas Synchrotron Opt X-ray Opt (2016) 9687:96870D. doi:10.1117/12.2247575
10. Avila J, Boury A, Caja-Muñoz B, Chen C, Lorcy S, Asensio MC. Optimal Focusing System of the Fresnel Zone Plates at the Synchrotron SOLEIL NanoARPES Beamline. J Phys Conf Ser (2017) 849:012039. doi:10.1088/1742-6596/849/1/012039
11. Polack F, Thomasset M, Brochet S, Rommeveaux A. An LTP Stitching Procedure with Compensation of Instrument Errors: Comparison of SOLEIL and ESRF Results on Strongly Curved Mirrors. Nucl Instr Methods Phys Res Section A: Acc Spectrometers, Detectors Associated Equipment (2010) 616:207–11. doi:10.1016/j.nima.2009.10.166
Keywords: x-ray mirror, mirror metrology, multi-pitch NSP, mirror inspection, tolerance study
Citation: Huang L, Wang T, Polack F, Nicolas J, Nakhoda K and Idir M (2022) Measurement Uncertainty of Highly Asymmetrically Curved Elliptical Mirrors Using Multi-Pitch Slope Stitching Technique. Front. Phys. 10:880772. doi: 10.3389/fphy.2022.880772
Received: 21 February 2022; Accepted: 20 April 2022;
Published: 11 May 2022.
Edited by:
Qiushi Huang, Tongji University, ChinaReviewed by:
Shanyong Chen, National University of Defense Technology, ChinaMaurizio Vannoni, European X-Ray Free Electron Laser, Germany
Copyright © 2022 Huang, Wang, Polack, Nicolas, Nakhoda and Idir. This is an open-access article distributed under the terms of the Creative Commons Attribution License (CC BY). The use, distribution or reproduction in other forums is permitted, provided the original author(s) and the copyright owner(s) are credited and that the original publication in this journal is cited, in accordance with accepted academic practice. No use, distribution or reproduction is permitted which does not comply with these terms.
*Correspondence: Lei Huang, aHVhbmdsZWkwMTE0QGdtYWlsLmNvbQ==