- 1Department of Optoelectronic Engineering, Jinan University, Guangzhou, China
- 2Guangdong Provincial Key Laboratory of Nanophotonic Functional Materials and Devices, School of Information and Optoelectronic Science and Engineering, South China Normal University, Guangzhou, China
- 3Guangdong Provincial Key Laboratory of Optical Fiber Sensing and Communications, Jinan University, Guangzhou, China
- 4Key Laboratory of Optoelectronic Information and Sensing Technologies of Guangdong Higher Education Institutes, Jinan University, Guangzhou, China
- 5Key Laboratory of Visible Light Communications of Guangzhou, Jinan University, Guangzhou, China
We demonstrate an ultrafast humidity micro-fiber sensor based on molybdenum disulfide (MoS2) cladding with three dimensional network structure. The high surface-to-volume rations and porous mesh structure improve the interaction of between MoS2 and water molecules, further enhancing the performance of the humidity sensor. The results demonstrated that the sensor can perform in a wide relative humidity (RH) range between 10%RH to 90%RH with rapid dynamic behavior (response and recovery time are 0.090 and 0.130 s respectively). The sum of response and recovery time (total time) is 0.220 s, which is the fastest in the reported MoS2-based humidity sensors. The sensitivity of this sensor is up to -1.501 dB/%RH in the RH range (77%RH–90%RH). Such a high performance RH sensor will have a wide range of application potential in chemical processing, various medical diagnostics, and so on.
Introduction
The measurement and control of relative humidity (RH) play an important role in agriculture, food industry, and health and medical care [1–4]. Conventional capacitance and resistive electronic humidity sensors have been widely developed and achieved great success [5]. However, they are susceptible to electromagnetic interference and easy corrosion. Optical fiber sensors have several advantages compared to electronical humidity sensors such as immunity to electromagnetic interference, high sensitivity, low cost, remote operation, and the capability to work in hazardous environments [6]. In order to improve the response time and sensitivity of optical fiber sensors, different sensing schemes such as side-polished fibers [7, 8], fiber Bragg gratings [9–11], long period fiber gratings [12, 13], and microfibers [14, 15] have been proposed and demonstrated. To increase the humidity sensitivity, various organic matter and metal oxide such as gelatin [8], polyvinyl alcohol [16], Zinc oxide [17–19], and titanium dioxide [20] have been used as active material. Due to the high specific surface area and high water adsorption capacity, two-dimensional (2D) materials are considered to be excellent humidity sensitizing material. In 2014, few layer reduced graphene oxide (rGO) was coated on the side polished fiber to prepare a humidity sensor whose response and recovery was 5 and 29 s respectively, and its sensitivity was 0.31 dB/%RH [21]. In 2016, rGO was deposited on the outer surface of a hollow core fiber to prepare a humidity sensor, whose response and recovery time were 5.2 and 8.1 s, respectively. Its sensitivity was 0.22 dB/%RH within the 60%RH–90%RH humidity range [22]. Luo et al. demonstrated a new all-fiber moisture sensor consisting of a WS2 film overlay on a side-polished fiber (SPF). In the range of relative humidity 35%RH–85%RH, the response time reached 1 s, the recovery time reached 5 s, and the sensitivity was 0.1213 dB/%RH [23]. In 2017, Ouyang et al. proposed molybdenum diselenide (MoSe2) wrapped on a side-polished fiber (SPF) with response time of 1 s and recovery time of 4 s [24].
As a typical 2D material, Molybdenum disulfide (MoS2) is supposed to be an excellent humidity sensing material due to its unique photoelectric properties and good hydrophilicity [25]. In 2017, with deposited MoS2 nanosheets on etched single-mode fiber (ESMF), Du et al. demonstrated a fiber humidity sensor with response time of 0.066 s and recovery time of 2.395 s while monitoring human breath [26]. In the same year, Li et al. covered MoS2 nanosheets on side polished optical fiber (SPF) and achieved response/recovery time of 850 ms in the human breath testing [27]. Although MoS2-based fiber humidity sensors showed faster response and recovery time than the fiber sensors based on other 2D material, the low sensitivity limited its applications (the dynamic response is 13.5 dB for the humidity ranging from 40%RH to 85%RH [27]). Furthermore, compared to the MoS2-based electrochemical sensing devices, the response and recovery times of MoS2 fiber humidity sensors were longer. For example, in 2018, Li et al. reported on electrochemical humidity sensors whose response and recovery times were 180 and 380 ms respectively [25]. In 2019, by coating three-dimensional (3D) graphene network cladding as a sensitizing layer, we demonstrated a novel microfiber humidity sensor [28]. Because the surface area of graphene was increased by the 3D network structure, its humidity sensitivity is up to -4.118 dB/%RH. Unfortunately, its response and recovery time were large (4 and 23.7 s, respectively).
In this paper, we coated a microfiber with three dimensional molybdenum disulfide network (3-DMN) cladding to achieve high humidity sensitivity. The 3-DMN was fabricated by self-assembly of polystyrene (PS) microspheres, each of which was coated with MoS2 nanosheets. Due to high specific surface area and polyporous structure, the 3-DMN boosts the interaction between water molecules and the MoS2 sensing layer. The microfiber with 3-DMN cladding owned a high sensitivity and fast dynamic behavior. The sensitivity of this sensor is up to -1.501 dB/%RH in the RH range (77%RH–90%RH) while the response and recovery times are 0.090 and 0.130 s, respectively, which is the fastest dynamic performance of MoS2-based humidity sensors to our knowledge. Due to the high performance of the humidity sensors based on 3-DMN covered microfiber, it has a wide range of application potential in chemical processing, various medical diagnostics, and so on.
Sensor Fabrication
Figure 1 shows the preparation process of MoS2/PS composite microspheres, the MoS2 nanosheet-coated PS microsphere structure (MoS2/PS) was manufactured by electrostatic self-assembly. The specific preparation process is as follows: First, 16 uL of 75% Methacryloxye2ltrime2l ammonium chloride (DMC) solution is added to 8 ml emulsion of PS microspheres (6 mg/ml, sphere’s diameter is 2 µm) that was composited by emulsifier-free emulsion polymerization. After ultra-sonication and stirring for 5 min, the temperature of the mixture was kept at 75°C in water bath for 1.5 h. Then, 6.4 ml of 0.1 mg/ml MoS2 nanosheet suspension is added to the mixture. After stirring the mixture for 2 h, the MoS2/PS composite microspheres were prepared.
Figure 2 shows the scanning electron micrograph (SEM) and Transmission Electron Microscope (TEM) images of the nanocomposite particle. As is shown in Figure 2A the PS microsphere was wrapped with MoS2 smoothly. As shown in Figure 2B, the TEM image of the MoS2/PS nanocomposite indicated that the MoS2 nanosheets were uniformly coated around the PS microsphere. The average diameter of the microspheres is 2 µm, and as shown in the inset, the thickness of the MoS2 layer is about 20 nm. To confirm the presence of the MoS2 coating on the PS microspheres, the Raman spectrums were studied. Figure 3 shows the Raman spectrums of MoS2/PS microspheres, MoS2 nanosheets, and pure PS microspheres, measured by Raman microspectroscopy (LabRAM HR Evolution, HORIBA Jobin Yvon, France, lens parameters: ×50 objective, NA = 0.5).
For the pure PS microspheres, a feature peak is observed at 1,001 cm−1, which is due to the γ1 ring-breathing mode of PS [29]. For the pure MoS2 nanosheets (red dash curve), two main feature peaks at 383 cm−1 and 404 cm−1 are present, which are due to the active planar vibrations
The microfiber was prepared by the method of the flame heating and tapering of standard single mode fiber. The microfiber consists of transition region and flat region as shown in Figure 4A. The diameter of the flat region of the microfiber is 5.6 µm and the lengths of flat and transition region of the microfiber are approximately 5 and 7 mm, respectively. Figure 4B is the microscopic image of the flat region of the microfiber.
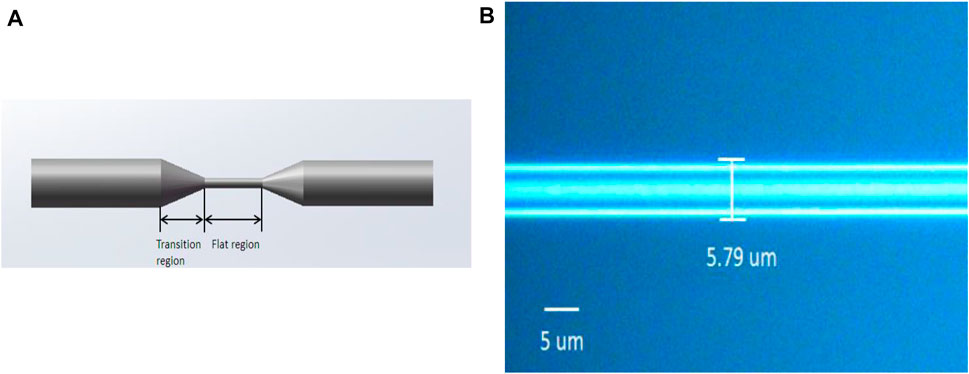
FIGURE 4. (A) the schematic diagram of a microfiber, (B) the microscopic image of the flat region of the microfiber.
As shown in Figure 5A, the microfiber was put in a 35 mm × 5 mm×1 mm rectangular glass basin and fixed by UV glue on both ends. After ultra-sonication at 30°C for 5 min, 200 µL 2 wt% prepared MoS2/PS microspheres suspension was dropped into the rectangular glass basin by using a micropipettor. Then the microfiber was natural dried at room temperature for 6 h. During the deposition process, the MoS2/PS composite microspheres were self-assembled onto the surface of the microfiber and 3D structure cladding was formed (as shown in Figure 5B). In Figure 5B, the MoS2 (blue film) coated around the PS microspheres were connected as a three-dimensional Molybdenum disulfide network (3-DMN) structure. Figure 5C is the SEM image of the microfiber covered by 3-DMN. The microfiber was embedded in the 3-DMN cladding uniformly. The inset is the close-up of the red square region, indicating the microfiber coated with 3-DMN.
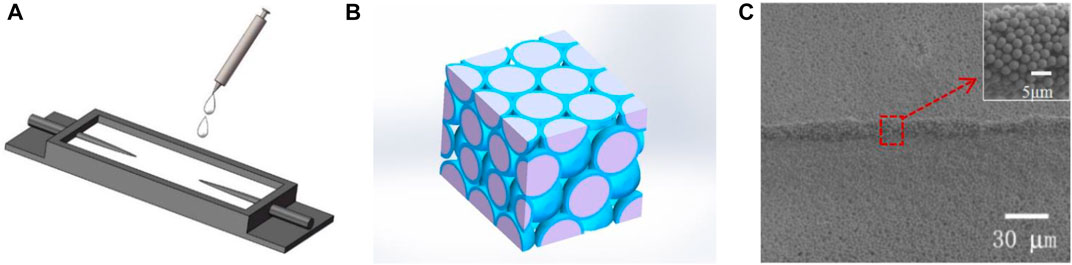
FIGURE 5. (A) The self-assembly process of the 3-DMN coating around microfiber. (B) The diagram of 3-DMN structure. (C) The SEM image of the microfiber covered by 3-DMN.
Humidity Sensing Experiments and Discussion
Figure 6 is the experimental setup for measuring humidity sensitivity of the fabricated sensors. The distributed feedback (DFB) laser at 1,310 nm was used as a light source. The transmission power passing through the sensor was measured by an optical power meter. The sensor was placed in the chamber whose humidity was controlled by the humid air flow. The humid air was produced by mixing the wet and dry airs, whose flow velocities were controlled. The real-time humidity and temperature were monitoring by the commercial hygrometer (175H1, Testo SE & Co. KGaA). In the process of the humidity measuring, the temperature of chamber was kept at 23°C.
The RH in the chamber was gradually ascended from 10.2%RH to 90.9%RH and then descended down to 8.0%RH with a step of about 10%RH. Every RH step was kept for 5 min. Figure 7 is the variations of the RH in chamber and transmission power of the sensor over time. As shown in Figure 7A, the variations of transmission power of the sensor closely follow the changes of the relative humidity. While the RH was ascended from 10.2%RH to 90.9%RH, the transmission power decreased 29.90 dBm (from -41.06 dBm to -70.96 dBm). While the RH was descended from 90.9%RH to 8.0%RH, the transmission power increased 29.97 dBm (from -70.96 dBm to -40.99 dBm). The largest variation of the transmission power of this sensor is twice larger than that of the reported SPF sensor covered with few layer MoS2 nanosheets [27].
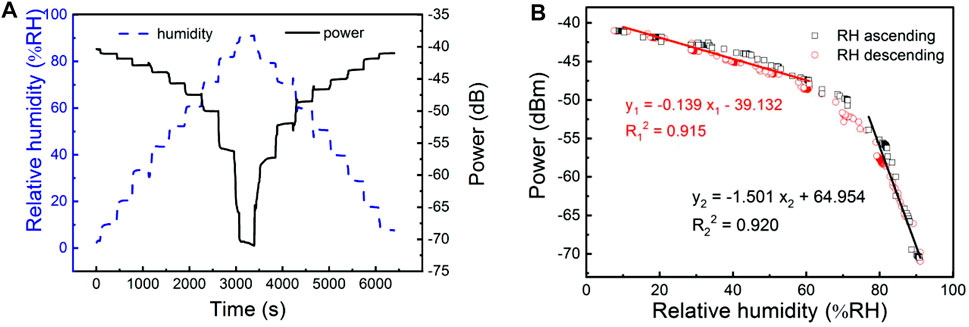
FIGURE 7. (A) Variations of RH and transmission power. (B) The relation between RH and optical transmission power.
The above experiment was repeated to measure the average transmission power at different humidity levels. Figure 7B showed the relationship between the average transmission power and the humidity. As shown in Figure 7B, the black squares (the RH ascending) and red circles (RH descending) almost overlap, indicating that this microfiber sensor with 3-DMN cladding performed good repeatability. In the relative humidity range from 10.0%RH to 90.9%RH, the average transmitted power depends nonlinearly on humidity. However, over smaller humidity ranges (10.0%RH to 60.8%RH and77.0%RH to 90.9%RH), the average transmitted power depends linearly on humidity. The sensitivity of the sensor is -0.139 dB/%RH in the red linear fitting (range from 10%RH to 60.8%RH) and the linear correlation coefficient is 91.5%. The sensitivity of the sensor is -1.501 dB/%RH in the black linear fitting (range from 77.0%RH to 90.8%RH) and the linear correlation coefficient is 92.0%. This sensitivity is 4 times larger than the previously reported work using few layers of 2D materials as sensing materials [26].
It is known that the PS is insensitive to water molecules, so that the 3D MoS2 structure is regarded as the sensing material. While water molecules are adsorbed by the MoS2 nanosheets, an amount of charge will be transferred from H2O to MoS2 [31], which induce the changing of the charge carriers concentration [32–34]. Therefore, following a RH increase, the imaginary part of the effective refractive index (RI) of the MoS2 nanosheets will be enhanced and the light absorption of MoS2 nanosheets is increased [26], resulting in the decreasing of the transmission power of the microfiber with 3-DMN cladding. Furthermore, owing to the porous nature of 3-DMN cladding as shown in Figure 5B, the specific surface area of MoS2 is increased, resulting in the significant improvement of the interaction between MoS2 and water molecules.
To measure the response and recovery time of the sensor, the air mixer in Figure 6 was substituted for solenoid valve. By using the solenoid valve, either dry air (humidity: 10%RH) or wet air (humidity: 90%RH) was selected to flow into the chamber. The humidity of the chamber could switch between high humidity and low humidity quickly. The dynamic performance of the sensor was monitored by photoelectric detector (KG-PR-10M-A, CONQUER) and oscilloscope. The response of each sensor was normalized with respect to the values measured at low humidity (VH, dry air flowed into the chamber) and high humidity (VL, wet air flowed into the chamber): VN = (V -VL)/(VH–VL).
Figure 8 exhibits the repeatability, stability, and dynamic response characteristics of the above microfiber covered by 3-DMN cladding. The modulation frequency of humid air flow is 0.5 Hz. As shown in Figure 8A, during the humidity change between high and low humidity, the transmission power of the sensor almost recovered the same position each cycle, which indicated that the sensor has prominent repeatability and stability. As we can see from Figure 8B, the response time (the normalized power drop from 0.9 to 0.1) and recovery time (the normalized power increase from 0.1 to 0.9) of the sensor were 90 ms and 130 ms, respectively.
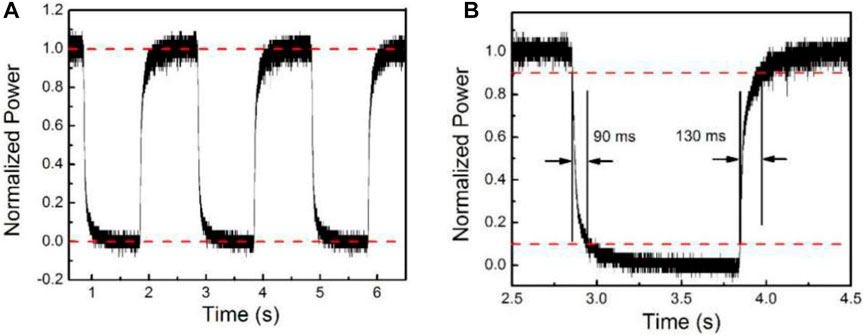
FIGURE 8. (A) Characterization of repeatability and stability of the sensor. (B) Response of the sensor to a modulated humid air flow at 0.5 Hz.
Table 1 compares the performance of RH fiber sensor coating with different materials. It can be seen that the sensor coating with 3-DMN cladding possesses not only higher humidity sensitivity but also faster dynamic response. Its sensitivity is up to -1.50 dB/%RH, which is more than 4 times larger than the other fiber humidity sensors. Furthermore, the sum of response and recovery time (total time) of this sensor is 0.220 s, which is 8 times smaller than that of few layer of MoS2 coated SPF sensor [27]. Owning to the porous nature of 3-DMN cladding as shown in Figure 5B, the water molecules easily accessed the inner 3D cladding structure and the interaction between water molecules and the 3-DMN cladding is enhanced, thereby significantly improving the humidity sensitivity and dynamic performance of the sensor. Since the response and recovery time of MoS2 is faster than that of graphene, which was proved in the previous reports [22, 26, 27], this sensor with 3D MoS2 network cladding owns faster response and recovery time compared to the previous work with 3D graphene network cladding [28].
Table 2 shows the response and recovery time of electrochemical humidity sensor based on MoS2. The response and recovery time of our fiber sensor with 3-DMN cladding is faster than that of the reported electrochemical humidity sensors based on MoS2.
Conclusion
A novel all-fiber humidity relative humidity (RH) sensor with high-sensitivity and fast dynamic response was fabricated. It is based on microfiber covered around three-dimensional molybdenum disulfide (3-DMN), which was prepared by electrostatic self-assembly and drop casting method. Because of the high surface-to-volume ratios and porous mesh structure of the 3-DMN cladding, the interaction between MoS2 and water molecules is improved, and the RH sensor can achieve high sensitivity and fast dynamic performance. In the RH range from 10%RH to 60.8%RH, the sensitivity of the sensor is -0.139 dB/%RH (linear correlation coefficient is 91.5%). In the RH range from 77.0%RH to 90.8%RH, the sensitivity of the sensor is -1.501 dB/%RH (linear correlation coefficient is 92.0%). Furthermore, its response time and recovery time are 0.090 and 0.130 s respectively. The sum of response and recovery time (total time) is 0.220 s which are 8 times smaller than that of a few layer MoS2 coated SPF sensor. To our knowledge, this type of sensor owns the fastest dynamic performance of the reported MoS2-based humidity sensors. The high performance RH sensor will have a wide range of application potential in chemical processing, various medical diagnostics, and so on.
Data Availability Statement
The original contributions presented in the study are included in the article/Supplementary Material, and further inquiries can be directed to the corresponding authors.
Author Contributions
PG planned and supervised the experiments and wrote and revised the manuscript. All authors contributed to the article and approved the submitted version.
Funding
National Natural Science Foundation of China (12174156); Natural Science Foundation of Guangdong Province (2017A030313359, 2021A1575012632, 2019A1515011578); Science & Technology Project of Guangzhou (201803020023); Department of Science and Technology of Guangdong Province (2020B1212060067).
Conflict of Interest
The authors declare that the research was conducted in the absence of any commercial or financial relationships that could be construed as a potential conflict of interest.
Publisher’s Note
All claims expressed in this article are solely those of the authors and do not necessarily represent those of their affiliated organizations, or those of the publisher, the editors, and the reviewers. Any product that may be evaluated in this article, or claim that may be made by its manufacturer, is not guaranteed or endorsed by the publisher.
References
1. Borini S, White R, Wei D, Astley M, Haque S, Spigone E, et al. Ultrafast Graphene Oxide Humidity Sensors. ACS Nano (2013) 7:11166–73. doi:10.1021/nn404889b
2. Chen GY, Wu X, Kang YQ, Yu L, Monro TM, Lancaster DG, et al. Ultra-fast Hygrometer Based on U-Shaped Optical Microfiber with Nanoporous Polyelectrolyte Coating. Sci Rep (2017) 7:7943. doi:10.1038/s41598-017-08562-1
3. Mogera U, Sagade AA, George SJ, Kulkarni GU. Ultrafast Response Humidity Sensor Using Supramolecular Nanofibre and its Application in Monitoring Breath Humidity and Flow. Sci Rep (2015) 4:4103. doi:10.1038/srep04103
4. Zhang D, Tong J, Xia B. Humidity-sensing Properties of Chemically Reduced Graphene Oxide/polymer Nanocomposite Film Sensor Based on Layer-By-Layer Nano Self-Assembly. Sensors Actuators B: Chem (2014) 197:66–72. doi:10.1016/j.snb.2014.02.078
5. Tripathy A, Pramanik S, Cho J, Santhosh J, Abu Osman N. Role of Morphological Structure, Doping, and Coating of Different Materials in the Sensing Characteristics of Humidity Sensors. Sensors (2014) 14:16343–422. doi:10.3390/s140916343
6. Bai Y, Miao Y, Zhang H, Yao J. Simultaneous Measurement of Relative Humidity and Temperature Using a Microfiber Coupler Coated with Molybdenum Disulfide Nanosheets. Opt Mater Express (2019) 9:2846–58. doi:10.1364/OME.9.002846
7. Huang Y, Zhu W, Li Z, Chen G, Chen L, Zhou J, et al. High-performance Fibre-Optic Humidity Sensor Based on a Side-Polished Fibre Wavelength Selectively Coupled with Graphene Oxide Film. Sensors Actuators B: Chem (2018) 255:57–69. doi:10.1016/j.snb.2017.08.042
8. Tang L, Feng Y, Xing Z, Chen Z, Yu J, Guan H, et al. High-sensitivity Humidity Sensing of Side-Polished Optical Fiber with Polymer Nanostructure Cladding. Appl Opt (2018) 57:2539–44. doi:10.1364/AO.57.002539
9. Shivananju BN, Yamdagni S, Fazuldeen R, Kumar AKS, Nithin SP, Varma MM, et al. Highly Sensitive Carbon Nanotubes Coated Etched Fiber Bragg Grating Sensor for Humidity Sensing. IEEE Sensors J (2014) 14:2615–9. doi:10.1109/JSEN.2014.2312353
10. Kronenberg P, Rastogi PK, Giaccari P, Limberger HG. Relative Humidity Sensor with Optical Fiber Bragg Gratings. Opt Lett (2002) 27:1385–7. doi:10.1364/OL.27.001385
11. Yeo TL, Sun T, Grattan KTV, Parry D, Lade R, Powell BD. Characterisation of a Polymer-Coated Fibre Bragg Grating Sensor for Relative Humidity Sensing. Sensors Actuators B: Chem (2005) 110:148–56. doi:10.1016/j.snb.2005.01.033
12. Konstantaki M, Pissadakis S, Pispas S, Madamopoulos N, Vainos NA. Optical Fiber Long-Period Grating Humidity Sensor with Poly(ethylene Oxide)/cobalt Chloride Coating. Appl Opt (2006) 45:4567–71. doi:10.1364/AO.45.004567
13. Venugopalan T, Sun T, Grattan KTV. Long Period Grating-Based Humidity Sensor for Potential Structural Health Monitoring. Sensors Actuators A: Phys (2008) 148:57–62. doi:10.1016/j.sna.2008.07.015
14. Liu H, Miao Y, Liu B, Lin W, Zhang H, Song B, et al. Relative Humidity Sensor Based on S-Taper Fiber Coated with SiO2 Nanoparticles. IEEE Sensors J (2015) 15:3424–8. doi:10.1109/JSEN.2015.2389519
15. Wu Y, Zhang T, Rao Y, Gong Y. Miniature Interferometric Humidity Sensors Based on Silica/polymer Microfiber Knot Resonators. Sensors Actuators B: Chem (2011) 155:258–63. doi:10.1016/j.snb.2010.12.030
16. Gastón A, Pérez F, Sevilla J. Optical Fiber Relative-Humidity Sensor with Polyvinyl Alcohol Film. Appl Opt (2004) 43:4127–32. doi:10.1364/AO.43.004127
17. Harith Z, Irawati N, Batumalay M, Rafaie HA, Yun II G, Harun SW, et al. Relative Humidity Sensor Employing Optical Fibers Coated with ZnO Nanostructures. Indian J Sci Technol (2015) 8:1–5. doi:10.17485/ijst/2015/v8i35/85348
18. Rahman HA, Irawati N, Abdullah TNR, Harun SW. PMMA Microfiber Coated with ZnO Nanostructure for the Measurement of Relative Humidity. IOP Conf Ser Mater Sci Eng (2015) 99:012025. doi:10.1088/1757-899X/99/1/012025
19. Irawati N, Rahman HA, Ahmad H, Harun SW. A PMMA Microfiber Loop Resonator Based Humidity Sensor with ZnO Nanorods Coating. Measurement (2017) 99:128–33. doi:10.1016/j.measurement.2016.12.021
20. Aneesh R, Khijwania SK. Titanium Dioxide Nanoparticle Based Optical Fiber Humidity Sensor with Linear Response and Enhanced Sensitivity. Appl Opt (2012) 51:2164–71. doi:10.1364/AO.51.002164
21. Xiao Y, Zhang J, Cai X, Tan S, Yu J, Lu H, et al. Reduced Graphene Oxide for Fiber-Optic Humidity Sensing. Opt Express (2014) 22:31555–67. doi:10.1364/OE.22.031555
22. Gao R, Lu D-f., Cheng J, Jiang Y, Jiang L, Qi Z-m. Humidity Sensor Based on Power Leakage at Resonance Wavelengths of a Hollow Core Fiber Coated with Reduced Graphene Oxide. Sensors Actuators B: Chem (2016) 222:618–24. doi:10.1016/j.snb.2015.08.108
23. Luo Y, Chen C, Xia K, Peng S, Guan H, Tang J, et al. Tungsten Disulfide (WS_2) Based All-Fiber-Optic Humidity Sensor. Opt Express (2016) 24:8956–66. doi:10.1364/OE.24.008956
24. Ouyang T, Lin L, Xia K, Jiang M, Lang Y, Guan H, et al. Enhanced Optical Sensitivity of Molybdenum Diselenide (MoSe_2) Coated Side Polished Fiber for Humidity Sensing. Opt Express (2017) 25:9823–33. doi:10.1364/OE.25.009823
25. Li N, Chen X-D, Chen X-P, Ding X, Zhao X. Fast-Response MoS2-Based Humidity Sensor Braced by SiO2 Microsphere Layers. IEEE Electron Device Lett (2018) 39:115–8. doi:10.1109/LED.2017.2778187
26. Du B, Yang D, She X, Yuan Y, Mao D, Jiang Y, et al. MoS2-based All-Fiber Humidity Sensor for Monitoring Human Breath with Fast Response and Recovery. Sensors Actuators B: Chem (2017) 251:180–4. doi:10.1016/j.snb.2017.04.193
27. Li D, Lu H, Qiu W, Dong J, Guan H, Zhu W, et al. Molybdenum Disulfide Nanosheets Deposited on Polished Optical Fiber for Humidity Sensing and Human Breath Monitoring. Opt Express (2017) 25:28407–16. doi:10.1364/OE.25.028407
28. Xing Z, Zheng Y, Yan Z, Feng Y, Xiao Y, Yu J, et al. High-sensitivity Humidity Sensing of Microfiber Coated with Three-Dimensional Graphene Network. Sensors Actuators B: Chem (2019) 281:953–9. doi:10.1016/j.snb.2018.11.057
29. Zhong Y, Wang Y, Wang Z, Xing Z, Xiao Y, Yu J, et al. Ultrafast Freestanding Microfiber Humidity Sensor Based on Three-Dimensional Graphene Network Cladding. Opt Express (2020) 28:4362–73. doi:10.1364/OE.379812
30. Najmaei S, Liu Z, Ajayan PM, Lou J. Thermal Effects on the Characteristic Raman Spectrum of Molybdenum Disulfide (MoS2) of Varying Thicknesses. Appl Phys Lett (2012) 100:013106. doi:10.1063/1.3673907
31. Dolui K, Rungger I, Sanvito S. Origin of Then-type Andp-type Conductivity of MoS2monolayers on a SiO2substrate. Phys Rev B (2013) 87:165402. doi:10.1103/PhysRevB.87.165402
32. Cho B, Hahm MG, Choi M, Yoon J, Kim AR, Lee Y-J, et al. Charge-transfer-based Gas Sensing Using Atomic-Layer MoS2. Sci Rep (2015) 5:1–6. doi:10.1038/srep08052
33. Mak KF, He K, Lee C, Lee GH, Hone J, Heinz TF, et al. Tightly Bound Trions in Monolayer MoS2. Nat Mater (2012) 12:207–11. doi:10.1038/nmat3505
34. Mouri S, Miyauchi Y, Matsuda K. Tunable Photoluminescence of Monolayer MoS2 via Chemical Doping. Nano Lett (2013) 13:5944–8. doi:10.1364/OME.7.00168610.1021/nl403036h
35. Guan H, Xia K, Chen C, Luo Y, Tang J, Lu H, et al. Tungsten Disulfide Wrapped on Micro Fiber for Enhanced Humidity Sensing. Opt Mater Express (2017) 7:1686–96. doi:10.1364/OME.7.001686
36. Wang X, Farrell G, Lewis E, Tian K, Yuan L, Wang P. A Humidity Sensor Based on a Singlemode-Side Polished Multimode-Singlemode Optical Fibre Structure Coated with Gelatin. J Lightwave Technol (2017) 35:4087–94. doi:10.1109/JLT.2017.2730484
37. Wang N, Zhang H, Yu X, Yin X, Li Y, Du Y, et al. Optical Fiber Fabry-Perot Humidity Sensor Filled with Polyvinyl Alcohol. Sensors Mater (2021) 33:1051–62. doi:10.18494/SAM.2021.3229
38. Irawati N, Rahman HA, Ahmad H, Harun SW. A PMMA microfiber loop resonator based humidity sensor with ZnO nanorods coating. Measurement (2017) 99:128–33. doi:10.1016/j.measurement.2016.12.021
39. Faruki MJ, Ab Razak MZ, Azzuhri S, Rahman MT, Soltanian MRK, Brambilla G, et al. Effect of Titanium Dioxide (TiO2) Nanoparticle Coating on the Detection Performance of Microfiber Knot Resonator Sensors for Relative Humidity Measurement. mat express (2016) 6:501–8. doi:10.1166/mex.2016.1342
40. Zhang S-L, Choi H-H, Yue H-Y, Yang W-C. Controlled Exfoliation of Molybdenum Disulfide for Developing Thin Film Humidity Sensor. Curr Appl Phys (2014) 14:264–8. doi:10.1016/j.cap.2013.11.031
41. Tan Y, Yu K, Yang T, Zhang Q, Cong W, Yin H, et al. The Combinations of Hollow MoS2 Micro@nano-Spheres: One-step Synthesis, Excellent Photocatalytic and Humidity Sensing Properties. J Mater Chem C (2014) 2:5422–30. doi:10.1039/c4tc00423j
Keywords: micro-fiber, molybdenum disulfide, 3D-structure, humidity sensor, rapid response
Citation: Guo P, Cui D, Dai Q, Cheng H, Yu J, Guan H, Luo Y, Lu H, Xiao Y, Zhong Y, Zhu W and Chen Z (2022) Ultrafast Microfiber Humidity Sensor Based on Three Dimensional Molybdenum Disulfide Network Cladding. Front. Phys. 10:863344. doi: 10.3389/fphy.2022.863344
Received: 27 January 2022; Accepted: 23 February 2022;
Published: 29 March 2022.
Edited by:
Lei Dong, Shanxi University, ChinaReviewed by:
Santosh Kumar, Liaocheng University, ChinaLi Tao, Beijing Institute of Technology, China
Xukun Yin, Rice University, United States
Copyright © 2022 Guo, Cui, Dai, Cheng, Yu, Guan, Luo, Lu, Xiao, Zhong, Zhu and Chen. This is an open-access article distributed under the terms of the Creative Commons Attribution License (CC BY). The use, distribution or reproduction in other forums is permitted, provided the original author(s) and the copyright owner(s) are credited and that the original publication in this journal is cited, in accordance with accepted academic practice. No use, distribution or reproduction is permitted which does not comply with these terms.
*Correspondence: Yongchun Zhong, eWNoemhvbmdAMTYzLmNvbQ==; Wenguo Zhu, emh1d2c4OEAxNjMuY29t