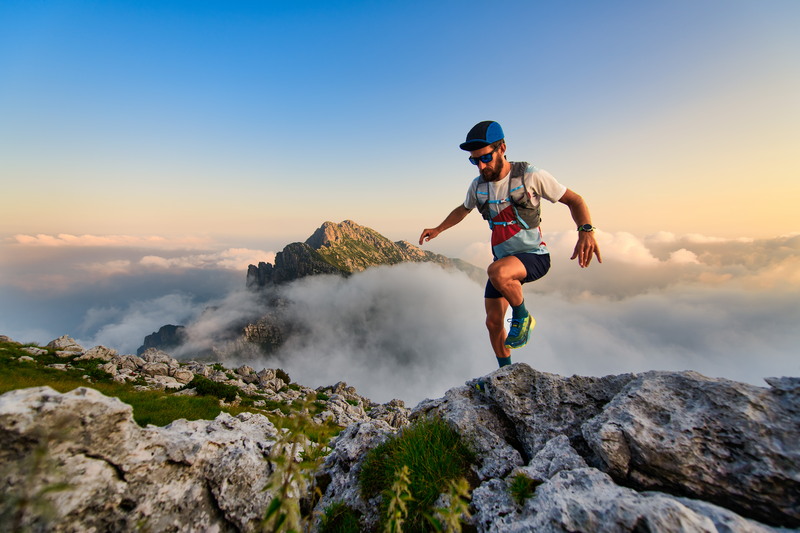
95% of researchers rate our articles as excellent or good
Learn more about the work of our research integrity team to safeguard the quality of each article we publish.
Find out more
BRIEF RESEARCH REPORT article
Front. Phys. , 14 March 2022
Sec. Interdisciplinary Physics
Volume 10 - 2022 | https://doi.org/10.3389/fphy.2022.836286
This article is part of the Research Topic Microscopic Structure Effect on the Macroscopic Property of Geomaterials View all 63 articles
Columnar jointed rock masses (CJRM) are characterized by significant anisotropy. The mechanical properties of CJRM are complicated by the presence of columnar joints. In this paper, based on the Voronoi random graph generation algorithm, the irregular CJRM numerical model is established, in which columns are simulated by solid elements while joints are simulated by contact surface elements. Uniaxial compression tests on irregular CJRM are then conducted by using FLAC3D to investigate the deformation and strength characteristics, and failure modes. Results indicate that irregular CJRM exhibit strong anisotropy under uniaxial compression, and the compressive strength varies with joint angle in a typical U-shape curve. Failure modes can be classified as three categories: splitting failure along loading direction, shear-sliding failure along columnar joint, and combined failure of column fracturing and joint splitting. The numerical results are then compared with the experimental results. It demonstrates the effectiveness and reliability of applying numerical simulation to investigations on mechanical properties and failure mechanism of irregular CJRM. The results of this study provide helpful information for the design and construction of the project involving CJRM.
Columnar joint is a primary tensile-fracture structure with polygonal columnar shape, which is widely developed in basalt [1–3]. Columnar jointed rock mass (CJRM) exhibits distinct characteristics of discontinuity, nonlinearity, heterogeneity and anisotropy, resulting in poor integrity and mechanical properties [4–7]. With the development of hydropower resources, CJRM is encountered in the construction of large and medium-sized hydropower engineering, such as Xiluodu, Baihetan, Jin’anqiao Ertan hydropower station in Southwest China. The existence of CJRM has caused many technical problems to the construction of these hydropower stations.
Over the past years, substantial efforts have been carried out to understand the engineering geological characteristics, physical and mechanical characteristics of CJRM and its influence on engineering characteristics by means of engineering geological investigation, in-situ test, laboratory test and numerical simulation. Based field true triaxial tests and acoustic emission technology, Shi [8] studied the failure mechanism of CJRM. Jiang [9] investigated and experimentally studied the anisotropy of deformation and strength of CJRM based on field tests. The results show that the crack propagation of columnar jointed rock mass is closely related to the primary joints and loading direction. In situ test is the most direct and effective method to obtain the mechanical parameters of rock mass in practical engineering. However, due to the high cost and complex practical environment, it is impossible to carry out a large number of repeatable tests.
Laboratory tests provide an alternative way to obtain the physical and mechanical parameters of CJRM. Due to the large sizes of individual hexagonal column in the field, it is difficult to obtain complete CJRM specimens. Laboratory model tests are widely carried out in recent years. Based on the similarity principle, Ji [10] and xiao [11] carried out uniaxial and triaxial mechanical tests on columnar jointed rock-like specimens with a similar geological structure as CJRM. Xiang [12] studied the mechanical and hydraulic responses of CJRM under coupled hydro-mechanical conditions on artificial rock-like specimens with regular arrays of hexagonal prism. By using 3D printing technology, columnar jointed rock-like specimens with complex joint network fracture are prepared to the anisotropy of strength and deformation, stress structure effect and failure mechanism of CJRM [13–15]. These results provide a new way to intuitively understand the anisotropic mechanical properties and deformation and failure mechanism of CJRM.
Numerical simulation is also an effective method to study the mechanical properties and deformation and failure mode of CJRM. Systematic research have been conducted by Die [16], Yan [17], Yan [18], from the view of establishment of numerical model, determination of characterization unit, anisotropic mechanical characteristics and the engineering application of CJRM. But it should be found that the research object is regular CJRM in these studies. In this paper, a columnar jointed rock mass model with similar column section to the field is established according to the random Voronoi graph generation algorithm. In the model, the solid element is used for the column and the contact surface element is used between the columns. To study the stress-strain relationship, anisotropic characteristics, failure modes and slip law of joint plane of irregular CJRM under uniaxial stress state, uniaxial compression numerical test of CJRM with different joint angles are carried out. The anisotropic mechanical properties and failure mechanism of irregular CJRM are revealed.
A two-dimensional Voronoi diagram with column section similar to the actual statistical law in the field is generated by using improved Voronoi iterative algorithm, shown in Figure 1A The three-dimensional joint network is then generated by stretching the two-dimensional diagram to a certain height, shown in Figure 1B. A more detailed description of the method and generated model is shown in the literature of [19]. According to the International Society for Rock Mechanics (ISRM), the numerical model of columnar jointed rock mass is cut to be circular cylinders with a height of 100 mm and a diameter of 50 mm at different column joint angles, shown in shown in Figure 1C.
FIGURE 1. Numerical model of columnar jointed rock mass. A two-dimensional Voronoi diagram with column section similar to the actual statistical law in the field is generated by using improved Voronoi iterative algorithm, shown in A. The three-dimensional joint network is then generated by stretching the two-dimensional diagram to a certain height, shown in B. A more detailed description of the method and generated model is shown in the literature of [19]. According to the International Society for Rock Mechanics (ISRM), the numerical model of columnar jointed rock mass is cut to be circular cylinders with a height of 100 mm and a diameter of 50 mm at different column joint angles, shown in C.
The contact surface element is used to simulate the mechanical properties between columns of columnar jointed rock mass. The slip, split and closure characteristics of joint surface can be simulated through interface in the FLAC3D software.
Based on the similarity theory, the similarity between the mechanical properties of model samples and in-situ columnar jointed rock mass is studied in the literature, in which high grade cement mortar is used to simulate basalt column, and appropriate proportion of white cement slurry is used as cementing material to simulate joints. Based on the uniaxial compression tests of cement mortar sample and column jointed basalt block sample, the characteristics of stress-strain curve, peak characteristics and failure mode are analyzed. Also, the mechanical parameters of column, joint surface and column size are determined. The column determined in Ref. [10] is a regular hexagonal prism with diameter of the column of 10 mm. In this paper, an irregular column is generated based on Voronoi diagram, with a diameter range of 7–10 mm.
The strain softening model is adopted during the numerical test calculation process. The model can better simulate the stress-strain characteristics of the specimen in the process of uniaxial compression. The column and joint parameters of columnar jointed rock mass in numerical simulation refer to the parameters calibrated in previous model test [10].
During the numerical simulation, the variation of axial displacement with loading stress is recorded and the stress-strain curves of CJRM with different joint angles under uniaxial compression are obtained, as shown in Figure 2. As can be seen from Figure 2, the stress-strain curves of CJRM with different joint angles can be divided into three stages, linear elastic deformation stage, pre-peak nonlinear deformation stage and post-peak nonlinear deformation stage.
FIGURE 2. Stress-strain curves of uniaxial compression tests. The part labels (A-C) are to distinguish the different stress-strain curves of CJRM with different joint angles (0°, 15°, 30°, 45°, 60°, 75° and 90°).
The deformation prosperities of CJRM exhibit different characters in different stages. It can be found that the proportion of elastic deformation stage in the stress-strain curves increases with the increase of the joint angle. This phenomenon is particularly obvious for CJRM at joint angle of 90°. With the increase of external load, some joint elements first exhibit sliding or tension failure and the stress-strain curve enters the nonlinear deformation stage. The nonlinear deformation before the peak of samples with different joint angles is different and there are obvious stress peak points in each stress-strain curve. In the post-peak stage, the deformation characteristics of CJRM with different joint angles are noticeably different. The deformation characteristics of the specimens after peak are different. For the joint angle of 75° and 90°, the specimens exhibit brittle failure characteristics and an obvious sudden stress drop can be found in the stress-strain curves. For the joint angle of 60°, the stress decreases in fluctuation due to the progressive failure of joint surface elements. For the joint angle of 0°, 30° and 45°, the stress reduction is relatively small, and the stress-strain curves show certain strain softening characteristics.
The deformation modulus, peak strength, and peak strain of columnar jointed rock mass with different dip angles are calculated from the stress-strain curves. Under uniaxial compression, the stress-strain characteristics of columnar jointed rock mass are mainly affected by the joint angle of the column. When the joint angle of the column is 0°and 30°, the strain corresponding to the peak stress of the columnar jointed rock mass is relatively large. The largest axial strain appears at joint angle of 0°, which is 7.56 × 10−3. With the increase of column angle, the strain at the peak stress of columnar jointed rock mass decreases gradually. The mechanical parameters of column are obviously higher than those of joint plane. At joint angle of 45 and 60°, the deformation of the specimen is controlled by the mechanical parameters of the joint. The specimens.
The variations of uniaxial compressive strength of CJRM with joint angle are show in Figure 3A. Obviously, the CJRM show strong anisotropy, where the variation curve of peak strength and joint angle exhibits a typical U-shaped trend. The maximum uniaxial compressive strength is 58.13 MPa, occurring at joint angle of 90°. The minimum strength is 4.81 MPa, occurring at joint angle of 60°.
FIGURE 3. Variation of uniaxial compression strength with dip angles for columnar jointed rock mass.
The deformation modulus is calculated from the stress-strain curves. It is found that the relationship between the deformation modulus and joint angle also exhibits a typical U-shaped trend, shown in Figure 3B. The maximum deformation modulus is 16.2 GPa, occurring at joint angle of 90°. The difference is that the minimum deformation modulus occurs at joint angle of 45°, which is 1.22 GPa.
The anisotropy ratio [20] is used to quantitatively describe the anisotropy degree of CJRM. The calculated strength anisotropy ratio is 12.1 and the deformation anisotropy ratio is 13.3. According to the classification standard of rock anisotropy, the greater the anisotropy ratio, the more significant the anisotropy. The result shows that the irregular CJRM has significant anisotropy under uniaxial stress.
The test results obtained by Ji [10] and Xia [13] are also shown in Figure 3. It is clearly that the relationship between peak strength and joint angle of CJRM all exhibits a typical U-shaped trend. Due to the difference of bonding modes, bonding strength and parameters, the values of peak strength are different. Since the parameters used in this paper are determined on Ji model test, the test results are close to results obtained by Ji [10].
The spatial distribution of joint failure elements at the peak strength of columnar jointed rock mass with different joint angles are shown in Figure 4. By comparing failure characteristics of columnar jointed rock mass with different joint angles, the failure modes can be summarized into the following three categories,
1) At joint angle of 0° and 15°, the CJRM specimens exhibit tensile failure of the joint surface along the loading direction. It can be seen from Fig. 8 (a) and Fig. 8 (b) that the damaged joint elements form a through fracture surface parallel to the loading direction. In the uniaxial stress state, the specimen is not constrained by the lateral confining pressure and the external load is shared by the column and joint. Because the bearing capacity of the joint surface is obviously lower than that of the column, the joint surface distributed vertically under the load first opens and fails, and finally forms a through fracture surface consistent with the loading direction under the continuous load, while there are few units that fail perpendicular to the loading direction.
2) At joint angle of 30°,45°and 75°, the CJRM exhibit shear-sliding failure. With increase of vertical load, the shear stress on the joints increases and gradually exceeds its shear strength. As a result, the joint element yields and the column slides along the yield joints. Finally, sliding failure along the joint direction of the column is formed. It can be seen from Figure 4 that there are multiple slip fracture surfaces for CJRM at joint angle of 30° and 45°.
3) At joint angle of 90°, the CJRM exhibits a combined tension–shear failure, which both crushing along the column and splitting along the joint. The vertical load exerted on the specimen is mainly borne by the column. When the stress borne by the column exceeds its compressive strength and yields, the column will undergo macro fracture, which will lead to the opening failure of the joint surface elements around the yield failure column.
In this section, the failure characteristics of CJRM are also compared with the model test results [10–15]. Overall, the failure modes are similar. The results show that it is feasible to study the anisotropic mechanical properties and failure modes of complex irregular columnar jointed rock mass by numerical simulation. The columnar jointed rock-like specimens will lead to the discreteness of test results due to the uneven adhesion of columns. For irregular columnar jointed rock mass, there are some disadvantages such as difficulties in sample preparation and high cost of repeated test. The above shortcomings can be well solved in numerical simulation, which provide an effective and feasible way to study the mechanical properties and engineering application of similar complex jointed rock mass.
In this paper, a numerical model of irregular columnar jointed rock mass is established, in which solid elements are used to simulate the columns and adopts and contact surface elements are adopted to simulate joint surfaces. Uniaxial compression tests are carried out to investigate the anisotropy characteristics and failure modes of irregular columnar jointed rock mass. The main conclusions are as follows,
1) The curve of peak strength and deformation modulus of irregular columnar jointed rock mass versus joint angle has a U-shape, with the maximum occurring at joint angle of 90° and the minimum occurring at joint angle of 45° and 60°. Under uniaxial compression state, the columnar jointed rock mass exhibits significant anisotropy, where the anisotropy ratios of strength and deformation are 12.1 and 13.3 respectively.
2) The failure modes of irregular columnar jointed rock mass under uniaxial compression can be divided into three categories, which are tensile failure of the joint surface along the loading direction at joint angle of 0° and 15°, sliding failure along the inclined joint surface of the column at joint angle of 30°, 45° and 60° and combined fracture-tension failure at joint angle of 90°.
3) The simulation results are basically consistent with the laboratory model test, which proves that the combined column-joint simulation method can provide a new way to study the mechanical properties of jointed rock mass under complex stress state. The results of this study provide helpful information for the design and construction of the project involving CJRM.
The raw data supporting the conclusions of this article will be made available by the authors, without undue reservation.
LY Established the numerical model and carried out the numerical simulation. ZX wrote the manuscript and analyzed tests data. WX designed the numerical tests. RW analyzed the anisotropic properties. HJ analyzed the failure characteristics.
The financial supports provided by the National Natural Science Foundation of China (Grant No. 52109122), and the Basic Research Fund for Central Research Institutes of Public Causes (No. CKSF2021715/YT) are gratefully acknowledged.
HJ is employed by the Company Power China Huadong Engineering Corporation Limited, China.
The remaining authors declare that the research was conducted in the absence of any commercial or financial relationships that could be construed as a potential conflict of interest.
All claims expressed in this article are solely those of the authors and do not necessarily represent those of their affiliated organizations, or those of the publisher, the editors and the reviewers. Any product that may be evaluated in this article, or claim that may be made by its manufacturer, is not guaranteed or endorsed by the publisher.
1. Weinberger R, Burg A. Reappraising Columnar Joints in Different Rock Types and Settings. J Struct Geology (2019) 125(12):185–94. doi:10.1016/j.jsg.2018.04.015
2. Goehring L, Morris SW, Lin Z. Experimental Investigation of the Scaling of Columnar Joints. Phys Rev E Stat Nonlin Soft Matter Phys (2006) 74(3 Pt 2):036115. doi:10.1103/PhysRevE.74.036115
3. Schultz RA. Limits on Strength and Deformation Properties of Jointed Basaltic Rock Masses. Rock Mech Rock Engng (1995) 28(1):1–15. doi:10.1007/bf01024770
4. Jin C, Yang C, Fang D, Xu S. Study on the Failure Mechanism of Basalts with Columnar Joints in the Unloading Process on the Basis of an Experimental Cavity. Rock Mech Rock Eng (2015) 48(3):1275–88. doi:10.1007/s00603-014-0625-6
5. Hao X-J, Feng X-T, Yang C-X, Jiang Q, Li S-J. Analysis of EDZ Development of Columnar Jointed Rock Mass in the Baihetan Diversion Tunnel. Rock Mech Rock Eng (2015) 49(4):1289–312. doi:10.1007/s00603-015-0829-4
6. Fan Q, Feng X, Weng W, Fan Y, Jiang Q. Unloading Performances and Stabilizing Practices for Columnar Jointed basalt: A Case Study of Baihetan Hydropower Station. J Rock Mech Geotechnical Eng (2017) 9(6):1041–53. doi:10.1016/j.jrmge.2017.07.003
7. Wei YJ, Xu M, Wang WP. Feasibility of Columnar Jointed basalt Used for High-Arch Dam Foundation [J]. J Rock Mech Geotechnical Eng (2011) 03(s1):461–8.
8. Shi AC, Wei YF, Zhang YH. Study on the Strength Characteristics of Columnar Jointed Basalt with a True Triaxial Apparatus at the Baihetan Hydropower Station [J]. Rock Mech Rock Eng (2020) 4(7):178–92.
9. Jiang Q, Wang B, Feng X-T, Fan Q-X, Wang Z, Pei S, et al. In Situ failure Investigation and Time-dependent Damage Test for Columnar Jointed basalt at the Baihetan Left Dam Foundation. Bull Eng Geol Environ (2018) 78(6):3875–90. doi:10.1007/s10064-018-1399-y
10. Ji H, Zhang JC, Xu WY, Wang RB, Wang HL, Yan L, et al. Experimental Investigation of the Anisotropic Mechanical Properties of a Columnar Jointed Rock Mass: Observations from Laboratory-Based Physical Modelling. Rock Mech Rock Eng (2017) 50(7):1919–31. doi:10.1007/s00603-017-1192-4
11. Xiao W-m., Deng R-gui, Deng R-g., Fu Z-b.X-m., Wang C-y.. Experimental Study on the Mechanical Properties of Simulated Columnar Jointed Rock Masses. J Geophys Eng (2015) 12:80–9. doi:10.1088/1742-2132/12/1/80
12. Xiang Z, Wang H, Xu W, Xie W-c.. Experimental Study on Hydro-Mechanical Behaviour of Anisotropic Columnar Jointed Rock-like Specimens. Rock Mech Rock Eng (2020) 53(12):5781–94. doi:10.1007/s00603-020-02245-6
13. Xia Y, Zhang C, Zhou H. Study on Model Structure and Mechanical Anisotropy of Columnar Jointed Rock Mass Based on Three-Dimensional Printing Method[J]. Int J Geomechanics (2020) 20(11). doi:10.1061/(asce)gm.1943-5622.0001854
14. Xia Y, Zhang C, Zhou H. Mechanical Behavior of Structurally Reconstructed Irregular Columnar Jointed Rock Mass Using 3D Printing [J]. Eng Geology (2020) 268.
15. Lin Z, Xu W, Wang H, Zhang J, Wei W, Wang R, et al. Anisotropic Characteristic of Irregular Columnar-Jointed Rock Mass Based on Physical Model Test. KSCE J Civ Eng (2016) 21(5):1728–34. doi:10.1007/s12205-016-1796-3
16. Di S-j., Xu W-y., Ning Y, Wang W, Wu G-y.. Macro-mechanical Properties of Columnar Jointed Basaltic Rock Masses. J Cent South Univ Technol (2011) 18:2143–9. doi:10.1007/s11771-011-0955-4
17. Yan D-x., Xu W-y., Zheng W-t., Wang W, Shi A-c., Wu G-y.. Mechanical Characteristics of Columnar Jointed Rock at Dam Base of Baihetan Hydropower Station. J Cent South Univ Technol (2011) 18:2157–62. doi:10.1007/s11771-011-0957-2
18. Yan L, Xu W, Wang R, Meng Q. Numerical Simulation of the Anisotropic Properties of a Columnar Jointed Rock Mass under Triaxial Compression. Ec (2018) 35(4):1788–804. doi:10.1108/ec-07-2017-0240
19. Meng Q, Yan L, Chen Y, Zhang Q. Generation of Numerical Models of Anisotropic Columnar Jointed Rock Mass Using Modified Centroidal Voronoi Diagrams. Symmetry (2018) 10:618. doi:10.3390/sym10110618
Keywords: numerical simulation, mechanical properties, failure modes, irregular columnar jointed rock mass, anisotropy
Citation: Yan L, Xiang Z, Xu W, Wang R and Ji H (2022) Numerical Simulation of Mechanical Properties of Irregular Columnar Jointed Rock Mass. Front. Phys. 10:836286. doi: 10.3389/fphy.2022.836286
Received: 15 December 2021; Accepted: 24 February 2022;
Published: 14 March 2022.
Edited by:
Qingxiang Meng, Hohai University, ChinaReviewed by:
Feng Xiong, China University of Geosciences Wuhan, ChinaCopyright © 2022 Yan, Xiang, Xu, Wang and Ji. This is an open-access article distributed under the terms of the Creative Commons Attribution License (CC BY). The use, distribution or reproduction in other forums is permitted, provided the original author(s) and the copyright owner(s) are credited and that the original publication in this journal is cited, in accordance with accepted academic practice. No use, distribution or reproduction is permitted which does not comply with these terms.
*Correspondence: Zhipeng Xiang, enB4aWFuZ19oaHVAMTYzLmNvbQ==
Disclaimer: All claims expressed in this article are solely those of the authors and do not necessarily represent those of their affiliated organizations, or those of the publisher, the editors and the reviewers. Any product that may be evaluated in this article or claim that may be made by its manufacturer is not guaranteed or endorsed by the publisher.
Research integrity at Frontiers
Learn more about the work of our research integrity team to safeguard the quality of each article we publish.