- 1Department of Mathematics, Air University, Islamabad, Pakistan
- 2Department of Basic Sciences, College of Science and Theoretical Studies, Saudi Electronic University, Riyadh, Saudi Arabia
- 3Department of Mathematics, University of Management and Technology, Lahore, Pakistan
- 4Department of Mathematics, College of Science Al-Zulfi, Majmaah University, Al-Majmaah, Saudi Arabia
In this work, we analyze the characteristics of periodic flows in non-isothermal viscous fluid over a heated block in the presence of thermal plates at Reynolds number
Introduction
Thermal flow over a stationary heated cylinder does not have many physical applications such as thermal processing of electronic cooling, fibrous suspensions, and others, moreover, use in a specific region of heat transfer for space economy. For more appropriate settings of visco-thermal flows, most excessive mixtures of fluid flow (emulsions, suspensions of paper pulps, foams, etc.) and most expensive systems of molecular polymers (blends, melts, etc.) have revealed shear-thickening or shear-shinning characteristics in the literature for a decade. In general, the geometrical configuration is categorized for the heated cylinder with thermal plates flowing toward the upstream direction. Yang et al. [1] analyzed the characteristics of thermal flow over the heated rectangular cylinder by the implementation of an arbitrary Lagrangian–Eulerian kinematic (ALEK) descriptive technique. Also, the effects of periodic flow with time state and average Nusselt number are presented. The influence of fluid flow in a heated pipe filled with nanomaterial is considered by Kamyar et al. [2]. Valipour et al. [3] depicted the influence of flow pattern and energy exchange over the square block by capitalizing of the finite volume scheme (FVS). Mostafa et al. [4] examined the flow visualization of thermal flow around the elliptic cylinder based on a large Reynolds number. They also analyzed the effects of fluid forces over the block. Kumar et al. [5] analyzed the influence of forced convection flow of generalized Newtonian fluid over the confined semiheater. Furthermore, hydrodynamic forces and Nusselt number are described by fluent. The forced convection thermal flow over the blocks embedded in a permeable medium was considered by Sayehvand et al. [6], and also, the results of a blind and porous medium channel were compared. Thermal flow around the block in the channel for large Reynolds number
Computational elucidation of the generalized Newtonian fluid flow behaviors, thus, becomes a famous topic from the perception of both academics and the application. Considerations in this field have been continuing for over a decade, which contained Newtonian or non-Newtonian models, linear or nonlinear viscoelastic models, etc. Particularly, the viscous models preserved the general form of Navier–Stokes (NS) for Newtonian fluid because it depends on shear rate. Puente et al. [13] examined the effects of viscous fluid flow in a permeable channel as imposed binary constituency mixture in the domain. Despite the nonlinearity of the work, the methodology gives us stability and accuracy of outcomes. Two dimensionally, the incompressible flow of power law fluid around the obstacle in the range of large Reynolds number
Wu et al. [25] imposed a fancy numerical scheme (LBM) for control of the flow pattern over the cylinder in a channel. Also, the effects of fluid forces over the block with a high Reynolds number
Furthermore, such numerical approaches in this field have been studied in [40–45]. Mahmood et al. [41, 42] examined the features of viscous fluid flow in a channel-driven cavity based on FEM computation. Also, the effects of shape function for quadratic and linear profiles were described. The variations of a hybrid computational mesh based on FEM for the physical configuration of the problem are presented. Also, the characteristics of fluid forces over the square block are discussed.
In most of the relevant studies available in the literature, the drag and lift coefficients have been computed in isothermal problems; however, in the present study, a non-isothermal flow regime is developed and the impact of forced convection on
Physical Problem and Mathematical Modeling
We consider two-dimensional, unsteady, incompressible, viscous fluid flow over the circular heated obstacle with thermal plates installed at the walls of the channel. The physical domain with height
The average velocity
The following assumptions are made for analysis:
• The characteristics of unsteady and non-isothermal fluid flow depending on the shear rate are studied
• The influence of parabolic inlet flow is studied, and the body force effects are neglected
• Boundary condition (no-slip) is assumed on the surface of the block as well as both symmetric walls of the channel
The governing equations of unsteady, non-isothermal, and viscous incompressible fluid flow over an endlessly long heated circular block are the classical continuity, momentum, and energy equations. The dimensionless form of the governing equations is defined as follows [45]:
where
Here,
The boundary conditions for thermal flow field are described as follows:
• At the inlet region:
• At the outlet region:
• At the surface of the cylinder:
• At the surface of heaters (plates):
• The other surfaces of the channel have no-slip conditions for velocity with
The computational solution of governing Eqs. 1–3 is found along with the implementation of a specific boundary condition flow domain by capitalizing variables
• Drag coefficient:
• Lift coefficient:
• Local Nusselt number:
• Average Nusselt number:
The dimensional net drag
Numerical Procedure
A complex discretization of a given domain is shown in Figure 2. The overall dimension of the computational domain is
A mathematical formulation consisting of governing equations is attained and handled with FEM computation. For the enlargement of finite element method discretization, the elements are capitalized triangular and quadratic in shape. The finite element method formulations attain the nonlinear algebraic equations by the implementation of the Newton–Raphson (N-R) iterative scheme. For validation of code, we compute the lift coefficient of the benchmark problem for the present work at
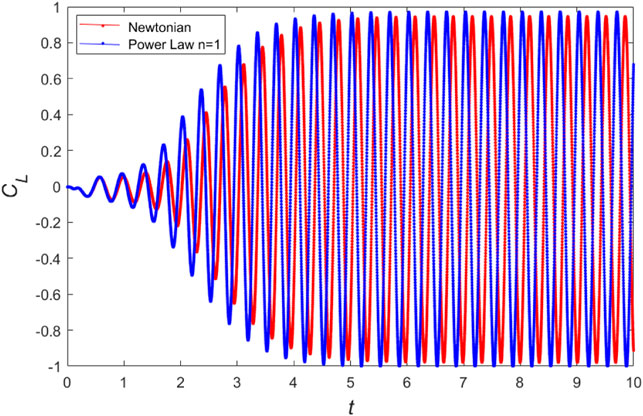
FIGURE 3. Lift comparison test for Newtonian fluid
Weak Formulation
To solve the system of Equations 1–3, the underlying methodology is based on the finite element method. The first step is to transfer the model equation into the so-called weak formulations. Introducing the tested and tried spaces, we proceed as follows:.
Let
For numerical approximation, we compute the continuous solutions with the discrete ones in the finite-dimensional subspaces.
Using Eq. 9 in Eqs. 5–8, the following discrete version is obtained:
Basis functions are defined for the discrete solution as follows:
where
In the matrix form,
which can be written as
All parameters have their usual meanings, and to compute the solution, this complex system is iterated till a particular convergence criterion is met. The nonlinear iterations are stopped when the residual is dropped by 10–6.
Results and Discussion
In this manuscript, we have considered the governing parameters for thermal flow characteristics as follows: Grashof number (Gr) from 1 to 10, power law index (n) from 0.6 to 1.4, Prandtl number (
(1) Fluid Flow
In this section, the effects of superimposed phenomena on viscous fluid flow are considered. The drag and lift coefficients, viscosity, and shear rate are provided for incompressible unsteady viscous (power law) fluid flow over a circular heated block situated in a channel with a fixed Reynolds number
Figure 6 illustrates the effects of flow behavior index (n) on the time evaluation of
Figure 8 illustrates that the influence on the pressure profile at the stagnation position for an oscillating flow regime. The frequency of periodicity of the pressure profile is minimum when the
(2): Thermal Flow Behavior
In this section, the influence of the flow behavior parameter
In Figure 11, the average Nusselt number
Conclusion
Numerical simulations have been carried out to investigate the fluid flow over a uniformly heated cylindrical block in a channel with thermal plates installed at the walls of the channel. The fluid model incorporated is the Ostwald de-Waele power law rheological model that describes a wide range of shear-thinning and shear-thickening fluids. A highly refined hybrid grid is generated at the preprocessing stage to achieve high accuracy in the solution, and a code validation study is also performed. Based on the obtained results, the following conclusions are drawn:
i. The amplitude of drag and lift increases for shear-thinning cases
ii. For
iii. Average Nusselt number increases with the Prandtl number and reaches an oscillatory steady state in all cases after
iv. For Newtonian and shear-thinning cases,
v. Phase plots of
This work can be extended in many directions, for instance, selecting higher values of
Data Availability Statement
The original contributions presented in the study are included in the article/Supplementary Material, further inquiries can be directed to the corresponding author.
Author Contributions
AH has performed modeling and computed data. RM has supervised the work. IS has written the manuscript.
Conflict of Interest
The authors declare that the research was conducted in the absence of any commercial or financial relationships that could be construed as a potential conflict of interest.
Publisher’s Note
All claims expressed in this article are solely those of the authors and do not necessarily represent those of their affiliated organizations, or those of the publisher, the editors, and the reviewers. Any product that may be evaluated in this article, or claim that may be made by its manufacturer, is not guaranteed or endorsed by the publisher.
References
1. Yang SJ, Fu WS. Numerical Investigation of Heat Transfer from a Heated Oscillating Rectangular Cylinder in a Cross Flow. Numer Heat Trans (2010) 45:569–91.
2. Kamyar A, Ong KS, Saidur R. Effects of Nanofluids on Heat Transfer Characteristics of a Two-phase Closed Thermosyphon. Int J Heat Mass Transfer (2013) 65:610–8. doi:10.1016/j.ijheatmasstransfer.2013.06.046
3. Valipour M, Masoodi R, Rashidi S, Bovand M, Mirhosseini M. A Numerical Study on Convection Around a Square cylinder Using AL2O3-H2O Nanofluid. Therm Sci (2014) 18(4):1305–14. doi:10.2298/TSCI121224061V
4. Mostafa M, Kamal R, Gobran M. Flow and Heat Transfer Characteristics Around an Elliptic cylinder Placed in Front of a Curved Plate. Therm Sci (2014) 18(2):465–78. doi:10.2298/TSCI120307054M
5. Kumar A, Dhiman A, Baranyi L. CFD Analysis of Power-Law Fluid Flow and Heat Transfer Around a Confined Semi-circular cylinder. Int J Heat Mass Transfer (2015) 82:159–69. doi:10.1016/j.ijheatmasstransfer.2014.11.046
6. Sayehvand H-O, Dehkordi K, Basiri P. Numerical Analysis of Forced Convection Heat Transfer from Two Tandem Circular Cylinders Embedded in a Porous Medium. Therm Sci (2017) 21(5):2117–28. doi:10.2298/TSCI150307081S
7. Hassanzadeh R, Darvishyadegari M. Influence of Rotation on the Heat and Fluid Flow Around a Circular Cylinder. Int J Mod Stud Mech Eng (2018) 2018:1. doi:10.20431/2454-9711.0404002
8. Sayehvand H-O, Yari S, Basiri P. Numerical Study of Forced Convection Heat Transfer over Three Cylinders in Staggered Arrangement Immersed in Porous media. Therm Sci (2018) 22(1):467–75. doi:10.2298/TSCI150808249S
9. Dyakova OA, Frolov OY, Frolov OY. Investigation of the Structure of Nonisothermal Power-Law Fluid Flow in an L-Shaped Channel. Tomsk State Univ J Math Mech (2019) 2019(58):71–83. doi:10.17223/19988621/58/6
10. Athinarayanan A, Gurunathan M, Parthasarathy R, Taler J, Oclon P, Taler D. Numerical Investigation of Heat Transfer from Flow over Square cylinder Placed in a Confined Channel Using Cu-Water Nanofluid. Therm Sci (2019) 23:1367–80. doi:10.2298/TSCI19S4367A
11. Perumal S, Sundaresan D, Thanikodi S, Sivanraju R, Tesfil N, Ramalingam K. Heat Transfer Analysis in Counter Flow Shell and Tube Heat Exchanger Using of Design of Experiments. Belgrade, Serbia: Therm. Sci. (2020).
12. Javidi Sarafan M, Alizadeh R, Fattahi A, Valizadeh Ardalan M, Karimi N. Heat and Mass Transfer and Thermodynamic Analysis of Power-Law Fluid Flow in a Porous Microchannel. J Therm Anal Calorim (2020) 141(5):2145–64. doi:10.1007/s10973-020-09679-8
13. Puente JAA, Martins-Costa ML, Costa Mattos H. Numerical Simulation of Power-Law Fluid Flows in a Porous Channel. Braz Congr. Therm. Sci. Eng. (2012) 3:1.
14. Ehsan I, Mohammad S, Mohammad Reza N, Ali J, Sharifi Tashnizi E. Power-law Fluid Flow Passing Two Square Cylinders in Tandem Arrangement. J Fluids Eng Trans ASME (2013) 135–6. doi:10.1115/1.4023853
15. Houssem L, Bouzit M. Suppression of Flow Separation of Power-Law Fluids Flow Around a Confined Circular cylinder by Superimposed thermal Buoyancy. mech (2017) 23(2):220–7. doi:10.5755/j01.mech.23.2.14342
16. Xin L X, Lai H. The Simulation of Non-newtonian Power-Law Fluid Flow in a Centrifugal Pump Impeller. J Appl Mech Eng (2017) 05(4):381–90. doi:10.4172/2168-9873.1000230
17. Siddiki MN-A -A, Molla MM, Thohura S, Saha SC. Lattice Boltzmann Simulation of Non-newtonian Power-Law Fluid Flows in a Bifurcated Channel. AIP Conf Proc (2018) 1980:040023. doi:10.1063/1.5044333
18. Borzenko EI, Dyakova OA. Power-law Fluid Flow in a T-Shaped Channel with Slip Boundary Conditions on the Solid walls. J Phys Conf Ser (2018) 1128(1):012013. doi:10.1088/1742-6596/1128/1/012013
19. Ameur H. Pressure Drop and Vortex Size of Power Law Fluids Flow in Branching Channels with Sudden Expansion. Jafm (2018) 11(6):1739–49. doi:10.29252/jafm.11.06.28831
20. Vishal G, Tomar J, Bharti RP. Critical Parameters for Non-newtonian Power-Law Fluid Flow across a Channel Confined Circular cylinder. New York: arXiv (2019).
21. Tang M, He L, Ma R, He S, Yao G. Modeling of Yield-Power-Law Fluid Flow in an Eccentric Annulus with Fixed Horizontal Cuttings Bed. Energy Sourc A: Recovery, Utilization, Environ Effects (2019) 2019:1–16. doi:10.1080/15567036.2019.1683649
22. Akyildiz FT, Siginer DA, Boutaous Mh. Unsteady Flow of Power Law Fluids with Wall Slip in Microducts. J Fluids Eng Trans ASME (2019) 141–8. doi:10.1115/1.4042558
23. Chen Z, Shu C. Simplified Lattice Boltzmann Method for non‐Newtonian Power‐law Fluid Flows. Int J Numer Meth Fluids (2020) 92(1):38–54. doi:10.1002/fld.4771
24. Yang X-J. The Vector Power-Law Calculus with Applications in Power-Law Fluid Flow. Therm Sci (2020) 24:4289–302. doi:10.2298/TSCI2006289Y
25. Wu J, Qiu YL, Shu C, Zhao N. Flow Control of a Circular cylinder by Using an Attached Flexible Filament. Phys Fluids (2014) 26:103601–10. doi:10.1063/1.4896942
26. Seyed-Aghazadeh B, Modarres-Sadeghi Y. An Experimental Investigation of Vortex-Induced Vibration of a Rotating Circular cylinder in the Crossflow Direction. Phys Fluids (2015) 27(6):067. doi:10.1063/1.4921683
27. Ahmed RA. Simulation of Unsteady Flow Around a Cylinder. ejuow (2015) 3(2):28–49. doi:10.31185/ejuow.vol3.iss2.38
28. Abbasi WS, Islam SU. Transition from Steady to Unsteady State Flow Around Two Inline Cylinders under the Effect of Reynolds Numbers. J Braz Soc Mech Sci Eng (2018) 40(3):1–12. doi:10.1007/s40430-018-1083-y
29. Behara S, Ravikanth B, Chandra V. Flow-induced Oscillations of Three Tandem Rotating Cylinders. Phys Fluids (2018) 30:113604. doi:10.1063/1.5051773
30. Abbasi WS, Islam S-u., Rahman H, Manzoor R. Numerical Investigation of Fluid-Solid Interaction for Flow Around Three Square Cylinders. AIP Adv (2018) 8(2):025221. doi:10.1063/1.5004631
31. Sarwar Abbasi W, Ul Islam S, Faiz L, Rahman H. Numerical Investigation of Transitions in Flow States and Variation in Aerodynamic Forces for Flow Around Square Cylinders Arranged Inline. Chin J Aeronautics (2018) 31(11):2111–23. doi:10.1016/j.cja.2018.08.020
32. Behara S, Chandra V, Ravikanth B, Kotteda VMK. Oscillation Responses and Wake Modes of Three Staggered Rotating Cylinders in Two- and Three-Dimensional Flows. Phys Fluids (2018) 30:103602–10. doi:10.1063/1.5049347
33. Wang E, Xu W, Gao X, Liu L, Xiao Q, Ramesh K. The Effect of Cubic Stiffness Nonlinearity on the Vortex-Induced Vibration of a Circular cylinder at Low Reynolds Numbers. Ocean Eng (2019) 173:1. doi:10.1016/j.oceaneng.2018.12.039
34. Abbasi WS, Islam SU, Rahman H. Proximity Effects on Characteristics of Flow Around Three Inline Square Cylinders. Math Probl Eng (2019) 2019:1–14. doi:10.1155/2019/1752803
35. Abbasi WS, Mahmood R, Naheed A. On the Wake Interference Effects for Flow Around Tandem Bodies. J Braz Soc Mech Sci Eng (2020) 42(1):1–20. doi:10.1007/s40430-019-2137-5
36. Chen W, Rheem C-K, Lin Y, Li Y. Experimental Investigation of the Whirl and Generated Forces of Rotating Cylinders in Still Water and in Flow. Int J Naval Architecture Ocean Eng (2020) 12:531–40. doi:10.1016/j.ijnaoe.2020.03.004
37. Wang H, Yu G, Yang W. Numerical Study of Vortex-Induced Vibrations of Three Circular Cylinders in Equilateral-triangle Arrangement. Adv Mech Eng (2013) 5:287923. doi:10.1155/2013/287923
38. Mahmood R, Bilal S, Majeed AH, Khan I, Sherif E-SM. A Comparative Analysis of Flow Features of Newtonian and Power Law Material: A New Configuration. J Mater Res Technol (2019) 9:1.
39. Abali BE. An Accurate Finite Element Method for the Numerical Solution of Isothermal and Incompressible Flow of Viscous Fluid. Fluids (2019) 4:5–1. doi:10.3390/fluids4010005
40. Ahmad H, Mahmood R, Hafeez MB, Majeed AH, Askar S, Shahzad H. Thermal Visualization of Ostwald-De Waele Liquid in Wavy Trapezoidal Cavity: Effect of Undulation and Amplitude. Netherlands: Case Studies in Thermal Engineering (2022).
41. Mahmood R, Bilal S, Majeed AH, Khan I, Nisar KS. Assessment of Pseudo-plastic and Dilatant Materials Flow in Channel Driven Cavity: Application of Metallurgical Processes. J Mater Res Tech (2020) 9(3):3829–37. doi:10.1016/j.jmrt.2020.02.009
42. Mahmood R, Bilal S, Majeed AH, Khan I, Nisar KS. CFD Analysis for Characterization of Non-linear Power Law Material in a Channel Driven Cavity with a Square cylinder by Measuring Variation in Drag and Lift Forces. J Mater Res Tech (2020) 9:3838–46. doi:10.1016/j.jmrt.2020.02.010
43. Bilal S, Mahmood R, Majeed AH, Khan I, Nisar KS. Finite Element Method Visualization about Heat Transfer Analysis of Newtonian Material in Triangular Cavity with Square cylinder. J Mater Res Tech (2020) 9(3):4904–18. doi:10.1016/j.jmrt.2020.03.010
44. Majeed AH, Mahmood R, Abbasi WS, Usman K. Numerical Computation of MHD Thermal Flow of Cross Model over an Elliptic Cylinder: Reduction of Forces via Thickness Ratio. Math Probl Eng (2021) 2021:1–13. doi:10.1155/2021/2550440
45. Majeed AH, Jarad F, Mahmood R, Siddique I. Topological Characteristics of Obstacles and Nonlinear Rheological Fluid Flow in Presence of Insulated Fins: A Fluid Force Reduction Study. Egypt: Mathematical Problems in Engineering (2021).
Keywords: thermal flow, power law fluid, fluid forces, FEM computation, weak form
Citation: Hussain Majeed A, Mahmood R, Hamadneh NN, Siddique I, Khan I and Alshammari N (2022) Periodic Flow of Non-Newtonian Fluid Over a Uniformly Heated Block With Thermal Plates: A Hybrid Mesh-Based Study. Front. Phys. 10:829085. doi: 10.3389/fphy.2022.829085
Received: 04 December 2021; Accepted: 14 January 2022;
Published: 01 April 2022.
Edited by:
Jordan Yankov Hristov, University of Chemical Technology and Metallurgy, BulgariaReviewed by:
Krunal Gangawane, National Institute of Technology Rourkela, IndiaA. Mahdy, South Valley University, Egypt
Copyright © 2022 Hussain Majeed, Mahmood, Hamadneh, Siddique, Khan and Alshammari. This is an open-access article distributed under the terms of the Creative Commons Attribution License (CC BY). The use, distribution or reproduction in other forums is permitted, provided the original author(s) and the copyright owner(s) are credited and that the original publication in this journal is cited, in accordance with accepted academic practice. No use, distribution or reproduction is permitted which does not comply with these terms.
*Correspondence: Nawaf N. Hamadneh, bnd3YWY5NzdAZ21haWwuY29t