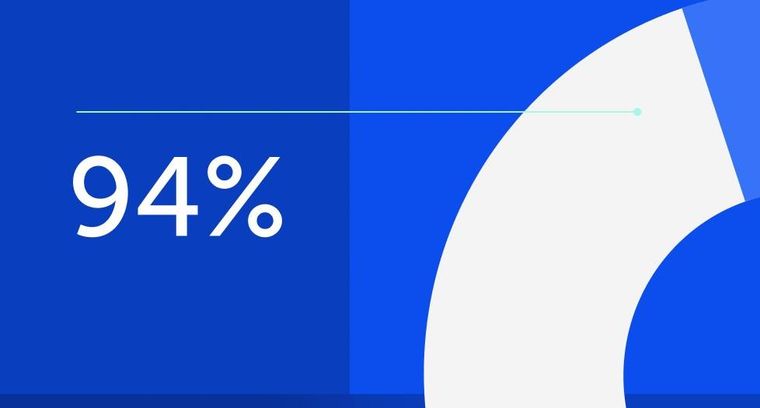
94% of researchers rate our articles as excellent or good
Learn more about the work of our research integrity team to safeguard the quality of each article we publish.
Find out more
ORIGINAL RESEARCH article
Front. Phys., 16 February 2021
Sec. Optics and Photonics
Volume 9 - 2021 | https://doi.org/10.3389/fphy.2021.642682
This article is part of the Research TopicPhysical Model and Applications of High-Efficiency Electro-Optical Conversion DevicesView all 24 articles
A fast response speed of a pixel is important for electrowetting displays (EWDs). However, traditional driving waveforms of EWDs have the disadvantage of long response time. So, a driving waveform, which based on overdriving voltages and charge trapping theory, was proposed in this paper to shorten the response time of EWDs. The driving waveform was composed of an overdriving stage and a driving stage. Firstly, a simplified physical model was introduced to analyze the influence of driving voltages on the response time. Then, an overdriving voltage was applied in the overdriving stage to increase the respond speed of oil, and a target voltage was applied in the driving stage to obtain a target luminance. In addition, the effect of different overdriving voltages and overdriving time values on the response time was analyzed by charge trapping theory to achieve an optimal performance. Finally, the driving waveform was imported into an EWD for performance testing. Experimental results showed that the response time of the EWD can be shortened by 29.27% compared with a PWM driving waveform.
Electrowetting displays (EWDs) are a new type of electronic paper with fast response speed and extremely low energy consumption [1, 2], and it can compensate for the limitations of electrophoretic displays (EPDs) effectively in the two major performances of color and video [3–8]. However, certain improvements are required for commercialization of EWDs, such as enhancement of response speed [9, 10]. In addition, driving waveforms are the voltage sequence applied to the EWD, which can control the movement of oil [11]. Therefore, it is of great significance to shorten the response time of EWDs by optimizing the driving waveform.
At present, the method for shortening the response time of EWDs, including reducing oil oscillation, suppressing charge trapping and suppressing oil backflow, has been proposed [12, 13]. In the study of reducing oil oscillation, an amplitude-frequency mixed modulation driving system was proposed, the oil was driven by a high voltage to achieve a target luminance, and then the driving voltage was decreased to stabilize the oil, this method can improve the response speed of gray scale displaying and reduce the oil oscillation [14]. In addition, the oil oscillation can be reduced by optimizing the rising stage of the driving waveform, a driving waveform with an exponential function rising stage was proposed to reduce the oil oscillation, and it can shorten the response time effectively [15]. But the period of the driving waveform was prolonged by using this method. In the study of suppressing charge trapping, an error diffusion algorithm based on pixel neighborhood gray information and direct current (DC) balanced driving waveform were proposed to suppress the charge trapping, and videos can be played in real-time by using this driving waveform [16]. A driving waveform with sawtooth wave was designed, a section of resetting wave was used to eliminate the influence of charge trapping [17]. The degree of charge trapping in electrowetting liquid lens driven by sinusoidal, bipolar and single pulse has been analyzed, and it was proved that the positive and negative polarities of driving voltages can cause a significant difference in the response speed [18]. However, the EWD was damaged easily by applying the negative polarities of driving voltages [19]. In the study of suppressing oil backflow, a series of sub-frames was used to drive multi-gray pixel data, the time of these sub-frames can be chosen to minimize the effect of the oil backflow in EWDs [20]. But these sub-frames would decrease the stability of oil. Besides, the research of the dynamic model of electrowetting and contact angle saturation has provided a theoretical basis for analyzing the influencing factors of response time in EWDs [21–24].
In this paper, a driving waveform which based on the principle of EWDs and charge trapping, was designed to shorten the response time in EWDs. An overdriving voltage was used to speed up the response speed of oil. Then, the optimal overdriving voltage and overdriving time were determined by the theory of charge trapping and a physical model of EWDs. So, the effect of charge trapping was reduced, and the shortest response time can be obtained.
The structure of EWDs is mainly composed of top plate, white substrate, indium tin oxide (ITO), hydrophobic insulating layer, pixel wall, colored oil and conductive liquid (NaCl solution). An EWD pixel is in an equilibrium state when no voltage is applied, and the colored oil forms a continuous spreading film between the hydrophobic insulating layer and the conductive liquid. So, the pixel can display the color of the colored oil [25, 26], and it is in an “off” state, as shown in Figure 1. Instead, the wettability of the colored oil on the hydrophobic insulating layer can be changed when a certain voltage is applied between a common electrode and a pixel electrode. Then, the colored oil can be shrunk, and the surface of the hydrophobic insulating layer can be displayed. At this time, most of light can be reflected directly through the conductive liquid, only a small part cannot be reflected because of the colored ink. So, the pixel point can display the background color of the white substrate, and it is in an “on” state. The ratio of white area to the pixel area is called aperture ratio, and its can be calculated by Eq. 1.
Where
FIGURE 1. The structure of an EWD pixel. It is in an equilibrium state, and the colored oil forms a continuous spreading film between the hydrophobic insulating layer and the conductive liquid.
A simplified physical model of EWDs is proposed to analyze the influence of driving voltages on oil movement [27]. In the physical model, the pixel of EWDs can be treated as a parallel capacitor when an applied voltage is applied between the common electrode and the pixel electrode. Specifically, the pixel wall and the oil can be treated as connected in series, and then they are connected in parallel with the hydrophobic insulating layer to form a loop. However, the photoresist material of the pixel wall has a lower conductivity compared with the oil. The capacitance of the pixel wall can be neglected. Therefore, the oil and the hydrophobic insulating layer are connected in parallel in the physical model. Ohm’s law can be used to calculate parameters of the physical model. So, the capacitance of the pixel
Where
Where
According to Eq. 2 and Eq. 3, the relationship between the thickness of the hydrophobic insulating layer and the driving voltage can be obtained by Eq. 4.
It can be seen that the driving voltage is proportional to the thickness of the hydrophobic insulating layer, so the thinner the hydrophobic insulating layer, the lower the driving voltage which can be applied. Excessive driving voltage cannot be applied to the EWD, otherwise the hydrophobic insulating layer would be broken down and the EWD would be damaged.
Ions in conductive liquid would be pulled toward the hydrophobic insulating layer by electrostatic force when the driving voltage is applied to a pixel. There is a possibility that charge becomes trapped in or on the hydrophobic insulating layer when the interaction between ions and the hydrophobic insulating layer is stronger than the interaction between ions and the conductive liquid. The phenomenon of charge trapping is shown in Figure 2. The relationship between the contact angle of oil and driving voltage can be determined by Eq. 5 and Ref. 29.
Where
FIGURE 2. The phenomenon of charge trapping. Charges become trapped in the hydrophobic insulating layer. At this time, the interaction between ions and the hydrophobic insulating layer is stronger than the interaction between ions and the conductive liquid.
The response time and the luminance of EWDs need to be tested, then the performance of the driving waveform can be analyzed. So, an experimental platform was developed to test and record luminance data of EWDs. The experimental platform was composed of a driving system and a testing system, it is shown in Figure 3. The driving system was composed of a computer (H430, Lenovo, China), a function generator (AFG3022C, Tektronix, USA) and a voltage amplifier (ATA-2022H, Agitek, China), which was used to generate driving waveforms. The testing system was composed of the computer and a colorimeter (Arges-45, Admesy, The Netherlands), which was used to test and record the luminance data of EWDs.
FIGURE 3. An Experimental platform. It was composed of a driving system and a testing system. (A) a function generator and a voltage amplifier (B) an EWD (C) a computer (D) a colorimeter. The power data was the driving waveform from the voltage amplifier. The luminance data was tested by the colorimeter, then it was recorded by the computer.
In this experiment, an EWD was used as a tested object, and its parameters was shown in Table 1. In the testing process, a driving waveform was edited by Arbexpress (V3.4, Tektronix, USA) waveform editing software in the computer. Then, an edited driving waveform was imported into the function generator by a universal serial bus (USB) interface, and it was amplified by the voltage amplifier. Thirdly, the EWD was driven by the driving waveform from the voltage amplifier, and the luminance data of the EWD was tested by the colorimeter. Finally, collected luminance data was transmitted to the computer, and Admesy software was used to record the luminance data in real time.
The response time of EWDs depend on the design of driving waveforms. Traditional driving waveforms generally used a pulse width modulation (PWM) waveform with a voltage amplitude of 30 V. However, the traditional driving waveform has the disadvantages of a long response time [11]. The proposed driving waveform was composed of an overdriving stage and a driving stage. In the overdriving stage, an overdriving voltage was applied to increase the response speed of the oil, and the duration of the overdriving time was called overdriving time. In the driving stage, a target voltage was applied to achieve a target luminance, and the target voltage was set to 30 V for comparing with the PWM driving waveform. The proposed driving waveform was shown in Figure 4. However, the response time and the luminance of EWDs were affected by the charge trapping. Therefore, the overdriving voltage and overdriving time need to be determined by the experiment to achieve an optimal performance.
FIGURE 4. The proposed driving waveform of EWDs in this paper. It was composed of an overdriving stage and a driving stage. An overdriving voltage was applied in the overdriving stage, and a target voltage was applied in the driving stage.
The effect of overdriving voltages was analyzed by testing the response time and the luminance of the EWD. In the driving waveform, overdriving voltages were set to 32 V, 34 V, 36 V, 38 V, and 40 V. The overdriving time was set to 4 ms. The luminance rising curves of difference overdriving voltages were shown in Figure 5. It can be seen that the luminance of the EWD was 181 when no voltage was applied. Then, the time which was required by the luminance to rise from 181 to 345 was defined as the response time. At the beginning of luminance rising curves, the rising speed of luminance was becoming faster when the overdriving voltage was increased. However, there were two situations during the transition from the overdriving stage to the driving stage. Specifically, the rising speed of luminance remained unchanged when the overdriving voltages were 32 V and 34 V. On the contrary, the rising speed of luminance was decreased when the overdriving voltages were 36 V, 38 V, and 40 V. The reason for this phenomenon was that the charge of the electrode plate in the EWD can be increased rapidly when the overdriving voltage was set higher than 34 V. At this time, the voltage of the equivalent capacitance
FIGURE 5. The luminance rising curves of difference overdriving voltages. At the beginning, the rising speed of luminance was becoming faster when the overdriving voltage was increased. Then, the rising speed of luminance was decreased when the overdriving voltage was set higher than 32 V. The shortest response time was 26.39 ms when the overdriving voltage was 32 V.
FIGURE 6. The luminance of difference overdriving voltages. It was decreased when the overdriving voltage was increased. The highest luminance was 373.81 when the overdriving voltage was 32 V. The lowest luminance was 356.91 when the overdriving voltage was 40 V.
The effect of overdriving times was analyzed by testing the response time and luminance of the EWD. In the driving waveform, the overdriving voltage was set to 32 V, and the overdriving times were set to 2 ms, 4 ms, 6 ms, 8 ms, and 10 ms. The luminance rising curves of difference overdriving times were shown in Figure 7. At the beginning of luminance rising curves, the rising speed of luminance was becoming faster when the overdriving time was increased. However, the rising speed of luminance was decreased during the transition from the overdriving stage to the driving stage when the overdriving time was increased. The reason for this phenomenon was that more charges would be trapped in the hydrophobic insulating layer when the overdriving time was longer than 4 ms. Therefore, the luminance was rose slowly in the driving stage. The shortest response time was 26.39 ms when the overdriving time was 4 ms. The luminance of difference overdriving times was shown in Figure 8. The highest luminance was 373.81 when the overdriving voltage was 4 ms. At this time, the response speed and luminance were increased by overdriving voltages. Therefore, the overdriving time should be set to 4 ms for getting a better performance.
FIGURE 7. The luminance rising curves of difference overdriving times. At the beginning of the luminance rising curves, the rising speed of the luminance was becoming faster when the overdriving time was increased. However, the rising speed of luminance was decreased during the transition from the overdriving stage to the driving stage when the overdriving time was longer than 4 ms. The shortest response time was 26.39 ms when the overdriving time was 4 ms.
FIGURE 8. The luminance of difference overdriving times. The highest luminance was 373.81 when the overdriving time was 4 ms. The lowest luminance was 364.21 when the overdriving time was 10 ms.
A PWM driving waveform was shown in Figure 9, and it was used to compare with the proposed driving waveform [11, 15]. The voltage amplitude, frequency and duty cycle of the PWM driving waveform were 30 V, 1 Hz and 70% respectively. The overdriving voltage and the overdriving time of the proposed driving waveform were 32 V and 4 ms respectively. The comparison of response time between the proposed driving waveform and the PWM driving waveform was shown in Figure 10. It can be seen that the response time of the proposed driving waveform was shorter than that of the PWM driving waveform. Specifically, the response time of the proposed driving waveform was 26.39 ms, and the response time of the PWM driving waveform was 37.31 ms. So, the response time was shortened by 29.27%. The comparison of luminance between the proposed driving waveform and the PWM driving waveform was shown in Figure 11. The luminance of the proposed driving was 373.81, and the luminance of the PWM driving waveform was 364.35. So, the luminance was increased by 2.60%. In the EWD, the response time and the luminance mainly depended on electrostatic force. The electrostatic force of the EWD was increased by the overdriving voltage in the proposed driving waveform. So, the response time can be shortened and the luminance can be increased compared with the PWM driving waveform.
FIGURE 9. A PWM driving waveform. Its voltage amplitude, frequency and duty cycle were 30 V, 1 Hz and 70% respectively.
FIGURE 10. The comparison of response times between the proposed driving waveform and the PWM driving waveform. The red line represented the proposed driving waveform, its response time was 26.39 ms. The black line represented the PWM driving waveform, its response time was 37.31 ms.
FIGURE 11. The comparison of luminance between the proposed driving waveform and a PWM driving waveform. The red line represented the proposed driving waveform, its luminance was 373.81. The black line represented the PWM driving waveform, its luminance was 364.35.
In this paper, a driving waveform, which based on overdriving voltages and charge trapping theory, was proposed to shorten the response time in EWDs. The relationship between driving voltage and response time was established by a physical model of EWDs. Then, the response speed of oil was increased by an overdriving stage. In addition, a better performance of EWDs was achieved by charge trapping theory, and an experimental platform was developed to verify the effectiveness of the driving waveform. The response time of EWDs was shortened by using the driving waveform, which provided a certain reference for the application and development of EWDs.
The original contributions presented in the study are included in the article/Supplementary Material, further inquiries can be directed to the corresponding author.
WZ and ZY designed this project. WZ and MY carried out most of the experiments and data analysis. WZ, SM, and XZ performed part of the experiments and helped with discussions during manuscript preparation. HF, LL, and LS contributed to the data analysis and correction. GZ, JY, and GZ gave suggestions on project management and provided helpful discussions on the experimental results. All authors have read and agreed to the published version of the manuscript.
This research was funded by the Guangdong Basic and Applied Basic Research Foundation (No. 2020A1515010420), the Key Research Platforms and Research Projects in Universities and Colleges of Guangdong Provincial Department of Education (No. 2018KQNCX334), the Zhongshan Innovative Research Team Program (No. 180809162197886), Guangdong Provincial Key Laboratory of Optical Information Materials and Technology (No. 2017B030301007), the Zhongshan Institute high-level talent scientific research startup fund project (No. 416YKQ04), the Project for Innovation Team of Guangdong University (No. 2018KCXTD033), and the National Key R&D Program of China (No. 2018YFB0407100-02).
The authors declare that the research was conducted in the absence of any commercial or financial relationships that could be construed as a potential conflict of interest.
1. Kim DY, Steckl AJ. Electrowetting on paper for electronic paper display. ACS Appl Mater Interfaces (2010) 2:3318–23. doi:10.1021/am100757g |
2. Bai PF, Hayes RA, Jin ML, Shui LL, Yi Z, Wang L, et al. Review of paper-like display technologies. Prog Electromagn Res (2014) 147:95–116. doi:10.2528/PIER13120405
3. Kao WC, Tsai JC. Driving method of three-particle electrophoretic displays. IEEE Trans Electron Dev (2018) 65:1023–8. doi:10.1109/TED.2018.2791541
4. Wang L, Yi Z, Jin ML, Shui LL, Zhou GF. Improvement of video playback performance of electrophoretic displays by optimized waveforms with shortened refresh time. Displays (2017) 49:95–100. doi:10.1016/j.displa.2017.07.007
5. He W, Yi Z, Shen S, Huang Z, Liu L, Zhang T, et al. Driving waveform design of electrophoretic display based on optimized particle activation for a rapid response speed. Micromachines (2020) 11:498. doi:10.3390/mi11050498
6. Yi Z, Bai P, Wang L, Zhang X, Zhou G, An electrophoretic display driving waveform based on improvement of activation pattern. J Cent S Univ (2014) 21:3133–7. doi:10.1007/s11771-014-2285-9
7. Shen S, Gong Y, Jin M, Yan Z, Xu C, Yi Z, et al. Improving electrophoretic particle motion control in electrophoretic displays by eliminating the fringing effect via driving waveform design. Micromachines (2018) 9:143. doi:10.3390/mi9040143
8. Van DR, Feenstra BJ, Hayes RA, Camps IGJ, Boom RGH, Wagemans MMH, et al. Gray scales for video applications on electrowetting displays. Sid Symp Dig Tech Pap (2006) 37:1926. doi:10.1889/1.2433427
9. Chae JB, Hong J, Lee SJ, Chung SK. Enhancement of response speed of viscous fluids using overdrive voltage. Sensor Actuator B Chem (2015) 209:56–40. doi:10.1016/j.snb.2014.11.076
10. Jin ML, Shen ST, Yi ZC, Zhou GF, Shui LL. Optofluid-based reflective displays. Micromachines (2018) 9:159. doi:10.3390/mi9040159
11. Yi Z, Shui L, Wang L, Jin M, Hayes R, Zhou G. A novel driver for active matrix electrowetting displays. Displays (2015) 37:86–93. doi:10.1016/j.displa.2014.09.004
12. Oh JM, Ko SH, Kang KH. Shape oscillation of a drop in ac electrowetting. Langmuir (2008) 24:8379–86. doi:10.1021/la8007359 |
13. Zhang XM, Bai PF, Hayes RA, Shui LL, Jin ML, Tang B, et al. Novel driving methods for manipulating oil motion in electrofluidic display pixels. J Disp Technol (2016).12:200–5. doi:10.1109/JDT.2015.2477947
14. Yi Z, Liu L, Wang L, Li W, ShuiZhou LG. A driving system for fast and precise gray-scale response based on amplitude–frequency mixed modulation in TFT electrowetting displays. Micromachines (2019) 10:732. doi:10.3390/mi10110732
15. Yi Z, Huang Z, Lai S, He W, Wang L, Chi F, et al. Driving waveform design of electrowetting displays based on an exponential function for a stable grayscale and a short driving time. Micromachines (2020) 11:313. doi:10.3390/mi11030313
16. Lin S, Zeng S, Qian M, Lin Z, Guo T, Tang B. Improvement of display performance of electrowetting displays by optimized waveforms and error diffusion. J Soc Inf Disp (2019) 27:619–29. doi:10.1002/jsid.790
17. Li W, Wang L, Zhang T, Lai S, Liu L, He W, et al. Driving waveform design with rising gradient and sawtooth wave of electrowetting displays for ultra-low power consumption. Micromachines (2020) 11:145. doi:10.3390/mi11020145
18. Xie N, Zhang N, Xu RQ. Effect of driving voltage polarity on dynamic response characteristics of electrowetting liquid lens. Jpn J Appl Phys (2018) 57:052201. doi:10.7567/JJAP.57.052201
19. Luo ZJ, Luo JK, Zhao WW, Cao Y, Lin WJ, Zhou GF. A high-resolution and intelligent dead pixel detection scheme for an electrowetting display screen. Opt Rev (2018) 25:18–26. doi:10.1007/s10043-017-0382-3
20. Luo ZJ, Zhang WN, Liu LW, Xie ST, Zhou GF. Portable multi-gray scale video playing scheme for high-performance electrowetting displays. J Soc Inf Disp (2016) 24:345–54. doi:10.1002/jsid.444
21. Zhou M, Zhao Q, Tang B, Groenewold J, Hayes RA, Zhou GF. Simplified dynamical model for optical response of electrofluidic displays. Displays (2017) 49:26–34. doi:10.1016/j.displa.2017.05.003
22. Shubhi B, Prosenjit S. Effect of electrowetting induced capillary oscillations on coalescence of compound droplets. J Colloid Interface Sci (2018) 530:223–32. doi:10.1016/j.jcis.2018.05.090 |
23. Gao J, Mendel N, Dey R, Baratian D, Mugele F. Contact angle hysteresis and oil film lubrication in electrowetting with two immiscible liquids. Appl Phys Lett (2018) 112:203703. doi:10.1063/1.5034510
24. Roghair I, Musterd M, van den Ende D, Kleijn CR, Kreutzer M, Muggle F. A numerical technique to simulate display pixels based on electrowetting. Phys Fluids (2015) 19:465–82. doi:10.1007/s10404-015-1581-5
25. Hayes RA, Feenstra BJ. Video-speed electronic paper based on electrowetting. Nature (2003) 425:383–5. doi:10.1038/nature01988 |
26. Roques CT, Hayes R, Schlangen L. A physical model describing the electro-optic behavior of switchable optical elements based on electrowetting. J Appl Phys (2004) 96:6267–71. doi:10.1063/1.1810192
27. Zhao Q, Tang B, Dong BQ, Li H, Zhou R, Guo YY, et al. Electrowetting on dielectric: experimental and model study of oil conductivity on rupture voltage. J Phys D Appl Phys (2018) 51:195102. doi:10.1088/1361-6463/aabb69
28. Roques CT, Hayes R, Feenstra B, Schlangen L. Liquid behavior inside a reflective display pixel based on electrowetting. J Appl Phys (2004) 95:4389–96. doi:10.1063/1.1667595
29. Verheijen HJJ, Prins MWJ. Reversible electrowetting and trapping of charge: model and experiments. Langmuir (1999) 15:6616–20. doi:10.1021/la990548n
1. Kim DY, Steckl AJ. Electrowetting on paper for electronic paper display. ACS Appl Mater Interfaces (2010) 2:3318–23. doi:10.1021/am100757g |
2. Bai PF, Hayes RA, Jin ML, Shui LL, Yi Z, Wang L, et al. Review of paper-like display technologies. Prog Electromagn Res (2014) 147:95–116. doi:10.2528/PIER13120405
3. Kao WC, Tsai JC. Driving method of three-particle electrophoretic displays. IEEE Trans Electron Dev (2018) 65:1023–8. doi:10.1109/TED.2018.2791541
4. Wang L, Yi Z, Jin ML, Shui LL, Zhou GF. Improvement of video playback performance of electrophoretic displays by optimized waveforms with shortened refresh time. Displays (2017) 49:95–100. doi:10.1016/j.displa.2017.07.007
5. He W, Yi Z, Shen S, Huang Z, Liu L, Zhang T, et al. Driving waveform design of electrophoretic display based on optimized particle activation for a rapid response speed. Micromachines (2020) 11:498. doi:10.3390/mi11050498
6. Yi Z, Bai P, Wang L, Zhang X, Zhou G, An electrophoretic display driving waveform based on improvement of activation pattern. J Cent S Univ (2014) 21:3133–7. doi:10.1007/s11771-014-2285-9
7. Shen S, Gong Y, Jin M, Yan Z, Xu C, Yi Z, et al. Improving electrophoretic particle motion control in electrophoretic displays by eliminating the fringing effect via driving waveform design. Micromachines (2018) 9:143. doi:10.3390/mi9040143
8. Van DR, Feenstra BJ, Hayes RA, Camps IGJ, Boom RGH, Wagemans MMH, et al. Gray scales for video applications on electrowetting displays. Sid Symp Dig Tech Pap (2006) 37:1926. doi:10.1889/1.2433427
9. Chae JB, Hong J, Lee SJ, Chung SK. Enhancement of response speed of viscous fluids using overdrive voltage. Sensor Actuator B Chem (2015) 209:56–40. doi:10.1016/j.snb.2014.11.076
10. Jin ML, Shen ST, Yi ZC, Zhou GF, Shui LL. Optofluid-based reflective displays. Micromachines (2018) 9:159. doi:10.3390/mi9040159
11. Yi Z, Shui L, Wang L, Jin M, Hayes R, Zhou G. A novel driver for active matrix electrowetting displays. Displays (2015) 37:86–93. doi:10.1016/j.displa.2014.09.004
12. Oh JM, Ko SH, Kang KH. Shape oscillation of a drop in ac electrowetting. Langmuir (2008) 24:8379–86. doi:10.1021/la8007359 |
13. Zhang XM, Bai PF, Hayes RA, Shui LL, Jin ML, Tang B, et al. Novel driving methods for manipulating oil motion in electrofluidic display pixels. J Disp Technol (2016).12:200–5. doi:10.1109/JDT.2015.2477947
14. Yi Z, Liu L, Wang L, Li W, ShuiZhou LG. A driving system for fast and precise gray-scale response based on amplitude–frequency mixed modulation in TFT electrowetting displays. Micromachines (2019) 10:732. doi:10.3390/mi10110732
15. Yi Z, Huang Z, Lai S, He W, Wang L, Chi F, et al. Driving waveform design of electrowetting displays based on an exponential function for a stable grayscale and a short driving time. Micromachines (2020) 11:313. doi:10.3390/mi11030313
16. Lin S, Zeng S, Qian M, Lin Z, Guo T, Tang B. Improvement of display performance of electrowetting displays by optimized waveforms and error diffusion. J Soc Inf Disp (2019) 27:619–29. doi:10.1002/jsid.790
17. Li W, Wang L, Zhang T, Lai S, Liu L, He W, et al. Driving waveform design with rising gradient and sawtooth wave of electrowetting displays for ultra-low power consumption. Micromachines (2020) 11:145. doi:10.3390/mi11020145
18. Xie N, Zhang N, Xu RQ. Effect of driving voltage polarity on dynamic response characteristics of electrowetting liquid lens. Jpn J Appl Phys (2018) 57:052201. doi:10.7567/JJAP.57.052201
19. Luo ZJ, Luo JK, Zhao WW, Cao Y, Lin WJ, Zhou GF. A high-resolution and intelligent dead pixel detection scheme for an electrowetting display screen. Opt Rev (2018) 25:18–26. doi:10.1007/s10043-017-0382-3
20. Luo ZJ, Zhang WN, Liu LW, Xie ST, Zhou GF. Portable multi-gray scale video playing scheme for high-performance electrowetting displays. J Soc Inf Disp (2016) 24:345–54. doi:10.1002/jsid.444
21. Zhou M, Zhao Q, Tang B, Groenewold J, Hayes RA, Zhou GF. Simplified dynamical model for optical response of electrofluidic displays. Displays (2017) 49:26–34. doi:10.1016/j.displa.2017.05.003
22. Shubhi B, Prosenjit S. Effect of electrowetting induced capillary oscillations on coalescence of compound droplets. J Colloid Interface Sci (2018) 530:223–32. doi:10.1016/j.jcis.2018.05.090 |
23. Gao J, Mendel N, Dey R, Baratian D, Mugele F. Contact angle hysteresis and oil film lubrication in electrowetting with two immiscible liquids. Appl Phys Lett (2018) 112:203703. doi:10.1063/1.5034510
24. Roghair I, Musterd M, van den Ende D, Kleijn CR, Kreutzer M, Muggle F. A numerical technique to simulate display pixels based on electrowetting. Phys Fluids (2015) 19:465–82. doi:10.1007/s10404-015-1581-5
25. Hayes RA, Feenstra BJ. Video-speed electronic paper based on electrowetting. Nature (2003) 425:383–5. doi:10.1038/nature01988 |
26. Roques CT, Hayes R, Schlangen L. A physical model describing the electro-optic behavior of switchable optical elements based on electrowetting. J Appl Phys (2004) 96:6267–71. doi:10.1063/1.1810192
27. Zhao Q, Tang B, Dong BQ, Li H, Zhou R, Guo YY, et al. Electrowetting on dielectric: experimental and model study of oil conductivity on rupture voltage. J Phys D Appl Phys (2018) 51:195102. doi:10.1088/1361-6463/aabb69
28. Roques CT, Hayes R, Feenstra B, Schlangen L. Liquid behavior inside a reflective display pixel based on electrowetting. J Appl Phys (2004) 95:4389–96. doi:10.1063/1.1667595
29. Verheijen HJJ, Prins MWJ. Reversible electrowetting and trapping of charge: model and experiments. Langmuir (1999) 15:6616–20. doi:10.1021/la990548n
30. Li XM, Tian HM, Shao JY, Ding YC, Chen XL, Wang L, et al. Decreasing the saturated contact angle in electrowetting-on-dielectrics by controlling the charge trapping at liquid-solid interfaces. Adv Funct Mater (2016) 26:2994–3002. doi:10.1002/adfm.201504705
Keywords: electrowetting displays (EWDs), overdriving voltage, response time, driving waveform, charge trapping
Citation: Zeng W, Yi Z, Zhao Y, Zeng W, Ma S, Zhou X, Feng H, Liu L, Shui L, Zhang C, Yang J and Zhou G (2021) Design of Driving Waveform Based on Overdriving Voltage for Shortening Response Time in Electrowetting Displays. Front. Phys. 9:642682. doi: 10.3389/fphy.2021.642682
Received: 16 December 2020; Accepted: 11 January 2021;
Published: 16 February 2021.
Edited by:
Qiang Xu, Nanyang Technological University, SingaporeReviewed by:
Ji-Pei Chen, Guangzhou University, ChinaCopyright © 2021 Zeng, Yi, Zhao, Zeng, Ma, Zhou, Feng, Liu, Shui, Zhang, Yang and Zhou. This is an open-access article distributed under the terms of the Creative Commons Attribution License (CC BY). The use, distribution or reproduction in other forums is permitted, provided the original author(s) and the copyright owner(s) are credited and that the original publication in this journal is cited, in accordance with accepted academic practice. No use, distribution or reproduction is permitted which does not comply with these terms.
*Correspondence: Zichuan Yi, eWl6aWNodWFuQDE2My5jb20=
Disclaimer: All claims expressed in this article are solely those of the authors and do not necessarily represent those of their affiliated organizations, or those of the publisher, the editors and the reviewers. Any product that may be evaluated in this article or claim that may be made by its manufacturer is not guaranteed or endorsed by the publisher.
Research integrity at Frontiers
Learn more about the work of our research integrity team to safeguard the quality of each article we publish.