- 1Institute for Neutron Physics and Reactor Technology, Karlsruhe Institute of Technology, Karlsruhe, Germany
- 2École Supérieure de Physique et de Chimie Industrielles de la Ville de Paris, Université PSL, Paris, France
- 3Facultad de Ingeniería Mecánica, Escuela Politécnica Nacional, Quito, Ecuador
This work presents the further development and application of the multi-physics coupled code Serpent/subchanflow for analyzing cores loaded with fuel assembly designs characterized by complex geometries, such as the VVR-KN fuel assembly. A high-detail steady-state analysis of one VVR-KN fuel assembly is presented and discussed. The VVR-KN is a plate-type fuel assembly, arranged coaxially with hexagonal fuel-plate tubes. Its particular geometry layout configuration challenges both their neutronic and thermal-hydraulic modeling. In this work, the versatility of Serpent’s multi-physics interface is exploited by using the unstructured mesh-based interface to update the properties of the fuel and coolant materials in a coupled neutronic/thermal-hydraulic simulation; these properties are solved and provided by the thermal-hydraulic code Subchanflow. Both neutronic and thermal-hydraulic models are developed for a single fuel assembly of 6.83 cm distance pitch and 60 cm active height, and state conditions for the simulations are defined. Typical material composition and main thermal properties for the fuel-meat (
1 Introduction
In the last decade, considerable research and development was carried out worldwide to develop multi-physics coupling strategies to enhance the prediction accuracy of reactor physics simulations. This multi-physics strategy mainly involves the interaction between neutronics, thermal-hydraulics, and fuel performance codes, profiting from the great versatility of Monte Carlo neutronic codes and today’s availability of powerful high-performance computing environments.
The Karlsruhe Institute of Technology (KIT) was leading different European projects, e.g., HPMC (High-Performance Monte Carlo Methods for Core Analysis) (Demazière et al., 2020), McSAFE (High-Performance Monte Carlo Methods for SAFEty Analysis) (Sanchez-Espinoza VH. et al., 2021), and McSAFER (High-Performance Advanced Methods and Experimental Investigations for the Safety Evaluation of Generic Small Modular Reactors) (Sanchez-Espinoza VH. et al., 2021), where the proof-of-concept, development, optimization, and the verification and validation of multi-physics coupling strategies based on Monte Carlo neutronics for Light Water Reactor applications were performed and demonstrated. These efforts are paving the way for their use in more industry-like and safety relevant applications (Sanchez-Espinoza VH. et al., 2021). In this framework, the coupling between Serpent and Subchanflow based on a internal master-slave approach was developed (Ferraro et al., 2020a). The coupling has been widely tested under different benchmarks such as steady-state analysis on a full VVER-1000 core (Ferraro et al., 2021a), burnup analysis on PWR and VVER fuel assemblies (Ferraro et al., 2021b), and reactivity insertion transient problems on Pressurized Water Reactors (PWRs) (Ferraro et al., 2020b; Ferraro et al., 2020c) and Small Modular Reactors (SMRs) (Mercatali et al., 2023; Huaccho et al., 2025). Additionally, the KIT code Subchanflow developed initially for rod-type fuels has been modified and extended for the thermal-hydraulic analysis of thin plate-type fuels widely used in Material Testing research Reactors (MTRs) (Almachi et al., 2021). With this new extension in Subchanflow, the Serpent/Subchanflow tool has been used additionally to perform steady-state and transient simulations in some MTR-type cores such as the generic IAEA
All the vast applications cited that use the coupling Serpent/Subchanflow rely in particular on one type of multi-physics interface, i.e., the regular mesh-based interface type 2 and the nested version type 22 (Serpent, 2024), which is perfect for modeling most of the standard reactor core designs. This work provides a first step in performing Serpent/Subchanflow coupled simulations using the unstructured mesh-based interface type 7 (Serpent, 2024). Interface type 7 was designed specifically to bring in solutions from solvers based on unstructured meshes such as fluid dynamic (CFD) codes. Its generality for defining different mesh shape geometries makes it suitable for the analysis of more unique core designs.
The structure of this work is as follows: Section 2 presents a general description of the VVR-KN fuel assembly. Section 3 describes the problem and defines the state conditions for the simulations. Section 4 briefly describes the tools and their main characteristics for simulating a coupled problem. Section 5 presents a detailed description of the neutronic and thermal-hydraulic models together with the interfaces based on unstructured meshes. Section 6 presents selected neutronic and thermal-hydraulic results. Finally, section 7 presents the summary and main conclusions of the work.
2 The VVR-KN fuel assembly
The VVR-KN is a hexagonal plate-type Russian fuel assembly design used in some research reactors. It comprises eight coaxial fuel elements (FE), seven having a hexagonal cylindrical shape, as showed in Figure 1. It has a characteristic pitch distance of 6.83 cm and 60 cm active height. The fuel meat is made of a
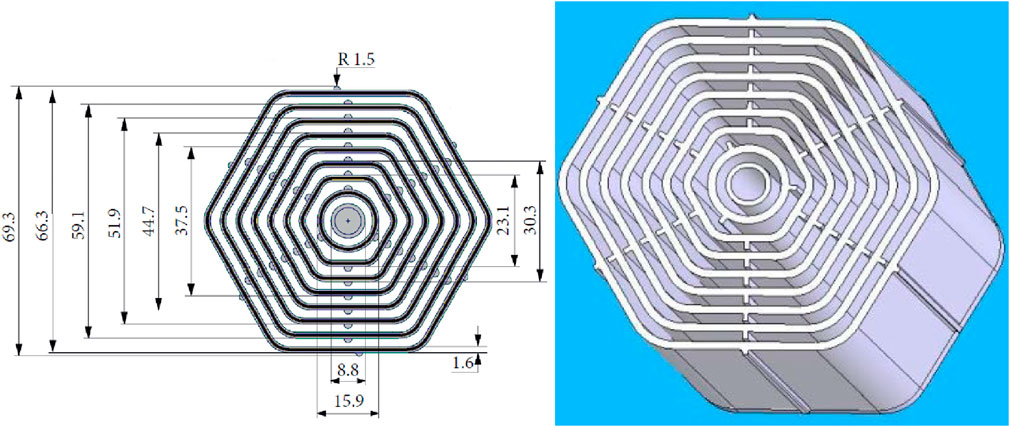
Figure 1. The VVR-KN standard fuel assembly, distances in [mm]. Images extracted from (Nguyen et al., 2020).
3 Problem definition
Imposed thermal-hydraulic (TH) conditions are defined for neutronics stand-alone characterization, and TH boundary conditions (BC) are defined for the steady-state neutronic/TH characterization. Most of the information needed for this work was extracted from (Nguyen et al., 2020). Two imposed TH states are defined, i.e., Cold Zero Power (CZP) condition and Hot Full Power (HFP) without xenon condition, see Table 1.
For the neutronic/TH characterization, boundary conditions for the TH feedback are defined considering nominal operation conditions. The reference values were obtained from (Nguyen et al., 2020), where a 10 MW conceptual core design using VVR-KN fuel assemblies (FAs) was investigated, and a maximum power of 393.49 kW is reported for a single FA. This power is considered as a reference value, and additional BCs are summarized in Table 2.
4 Multiphysics tools
4.1 Serpent
Serpent is a multi-purpose, three-dimensional, continuous-energy Monte Carlo transport code developed since 2004 at VTT Technical Research Centre of Finland Ltd (Leppänen et al., 2015). It represents a state-of-the-art code aimed to perform static, burnup, and dynamic 3-D calculations using standard ACE format Nuclear Data Libraries. Serpent was originally developed as a reactor physics code, but the scope has considerably broadened over the years, bringing the development of many advanced features (Serpent, 2024). One of those main advanced features is the multi-physics (MP) capability (Valtavirta, 2015). The basic idea of the Serpent’s MP capability is to bring certain material properties into the Serpent model, e.g., material’s density and temperature distribution, in order to have more realistic modelling during the simulation. The MP feature is wisely designed by an interface, which is defined on top of the Serpent’s model, i.e., without altering the original model’s geometry. Depending on how the external code solves the problem in terms of physics and geometry discretization, different interfaces are available in Serpent, i.e., point-wise, rectangular and hexagonal regular meshes, unstructured meshes, and many more. Examples of external codes coupled with Serpent via the MP interface are fluid dynamic (CFD) codes, channel thermal-hydraulics, and fuel performance codes (Leppänen et al., 2023; Leppänen, 2013).
One of the interfaces of interest for this work is the one based on unstructured meshes, designed specifically to bring in solutions from solvers based on this type of mesh. The interface is based on point-face-cell hierarchy, where the user gives a number of points that can be combined into a set of planar faces, which make up a set of closed convex cells (Serpent, 2024). The interface definition is based on the OpenFOAM format, and there is support for tetrahedral, hexahedral, and polyhedral-type meshes (Valtavirta, 2015). The Serpent version 2.1.32 is used in this work.
4.2 Subchanflow
Subchanflow (SCF) is a subchannel three-equations and single-phase flow thermal-hydraulic code for steady-state and transient analysis developed at Karlsruhe Institute of Technology (KIT), Germany (Imke and Sanchez, 2012). Subchanflow solves mass, momentum, and energy conservation equations along the axial discretization and between the neighbour lateral channels, i.e., cross-flow between channels. These equations together with a set of empirical correlations to calculate, for example, the pressure drop, heat transfer coefficients, void generation, etc., represent the system of equations of the single-phase (liquid/vapor mixture) flow model (Imke and Sanchez, 2012). Subchanflow was initially developed for rod-type fuel elements, where the geometry is defined as a set of channels and rods with given hydraulic parameters and connectivities. A typical channel is characterized by its area, wetted and heated perimeter, and a list of its neighbour channels; and a typical rod is characterized by its material type for fuel and cladding, rod diameters and gaps, and a list of neighboured channels where the heat is released. The temperature profile inside each rod is calculated by dividing it into several radial rings and solving the heat equation in the radial direction by a finite volume method (Imke and Sanchez, 2012). An extension to plate-type fuel assemblies typically for analyzing MTR research reactors is also available in Subchanflow (Almachi et al., 2021). The Subchanflow version 3.7.1 is used in this work.
4.3 The Serpent/Subchanflow coupling
The Serpent/Subchanflow coupling was developed in the framework of the McSAFE project (Sanchez-Espinoza VH. et al., 2021), and the main implementation aspects were first introduced in (Ferraro et al., 2020a). The coupling relies on the capabilities and advanced features of both codes, e.g., the multi-physics interface in Serpent to interact with other codes and the Subchanflow aptness to be used as an external library. The implementation consists of a high-level set of routines (coupling routines) developed in C language. The coupling routines manage open-door functions defined in the Serpent code, which allows the management of all main aspects of a coupled scheme. Subchanflow is included and used as an external library, resulting in an embedded master-slave implementation (Ferraro et al., 2020a).
Figure 2 shows the flow calculation for a coupled steady-state simulation where successive iterations between Subchanflow and Serpent are performed. The codes exchange the Density-Temperature distribution
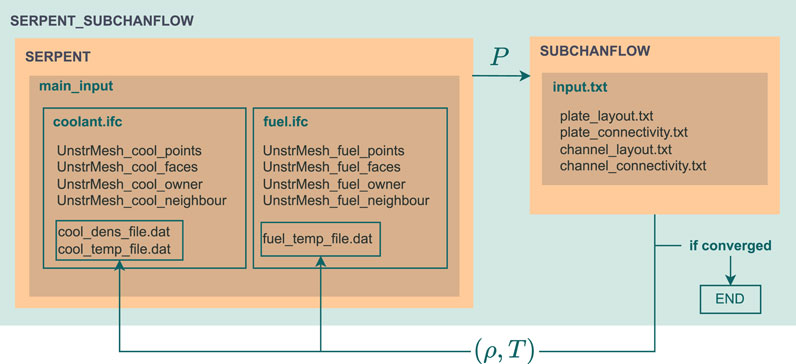
Figure 2. Flow calculation for a steady-state simulation with Serpent/Subchanflow using unstructured mesh-based interfaces for coolant and fuel. UnstrMesh_cool_* and UnstrMesh_fuel_* files define the unstructured superimposed meshes to update coolant and fuel properties.
5 Developed models
5.1 Serpent model
Following the fuel assembly description in Section 2, a 3D model was developed in Serpent as shown in Figure 3. The main assumptions and considerations taken into account are the following:
5.2 Subchanflow model
A thermal-hydraulic model at plate/subchannel level is developed in Subchanflow taking into account the following assumptions and considerations:
6 Results
Stand-alone neutronics and neutronic/TH simulations are presented in this section. All the simulations have been performed in a GNU/Linux single machine with an AMD EPYC 7542 32-Core Processor using 30 OpenMP threads. For the steady-state coupled simulation, eight iterations were performed, obtaining differences between the last two iterations in
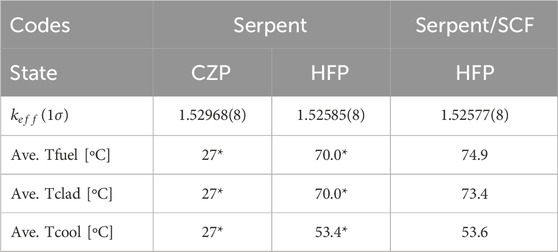
Table 6. Global criticality results. The number in parenthesis is the
In the neutronics stand-alone results, a difference of
Detectors to account for the power in every FE (Fuel Element2) are set up and summarized in Table 7. The higher power density is obtained in the internal FE and decreases slightly, keeping more or less constant in the remaining FEs. The axial power density distribution is shown in Figure 7. Thermal peaks due to the axial reflectors can be observed in both endings. A slight offset (almost negligible) of the axial power distribution in direction to the core inlet can be observed due to the slightly higher density of the coolant at the core inlet.
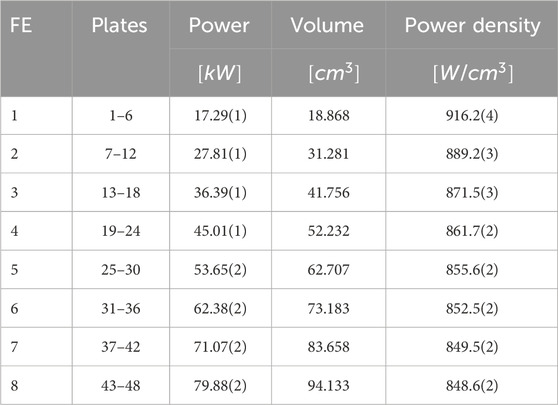
Table 7. Converged power distribution in every FE. The numbers in parenthesis are the
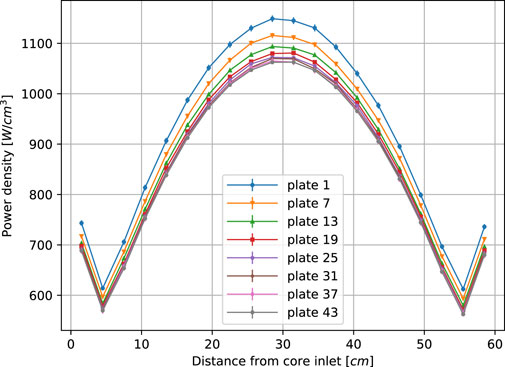
Figure 7. Power density along the active height for the representative plates predicted by Serpent/Subchanflow. Error bars are ±3σ.
Figure 8 shows the axial cladding and coolant temperature distribution in representative plates and subchannels. The highest cladding temperature is obtained in plate 13 (3rd FE), achieving a maximum value of 80.2°C in the 13th axial cell. The coolant temperature in channel 13 achieves a maximum value of 62.9°C in the last axial cell (core outlet). Figure 9 shows radial temperature distribution in all the materials (fuel, cladding, and coolant) at different axial layers.
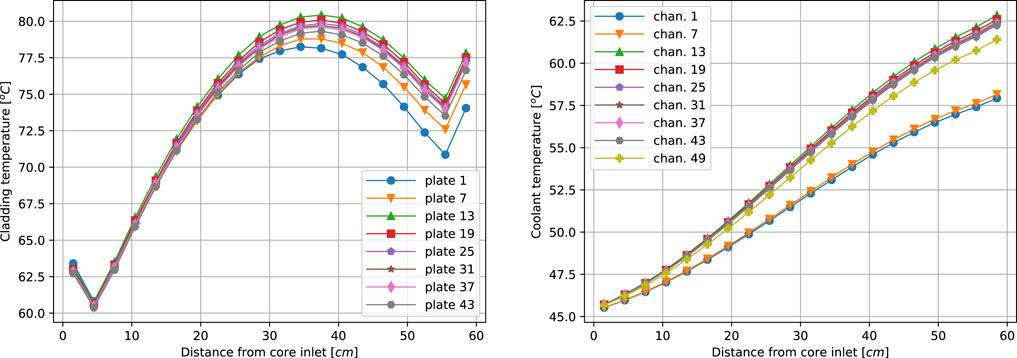
Figure 8. Cladding and coolant temperatures along the active height for representative plates and channels predicted by Serpent/Subchanflow.
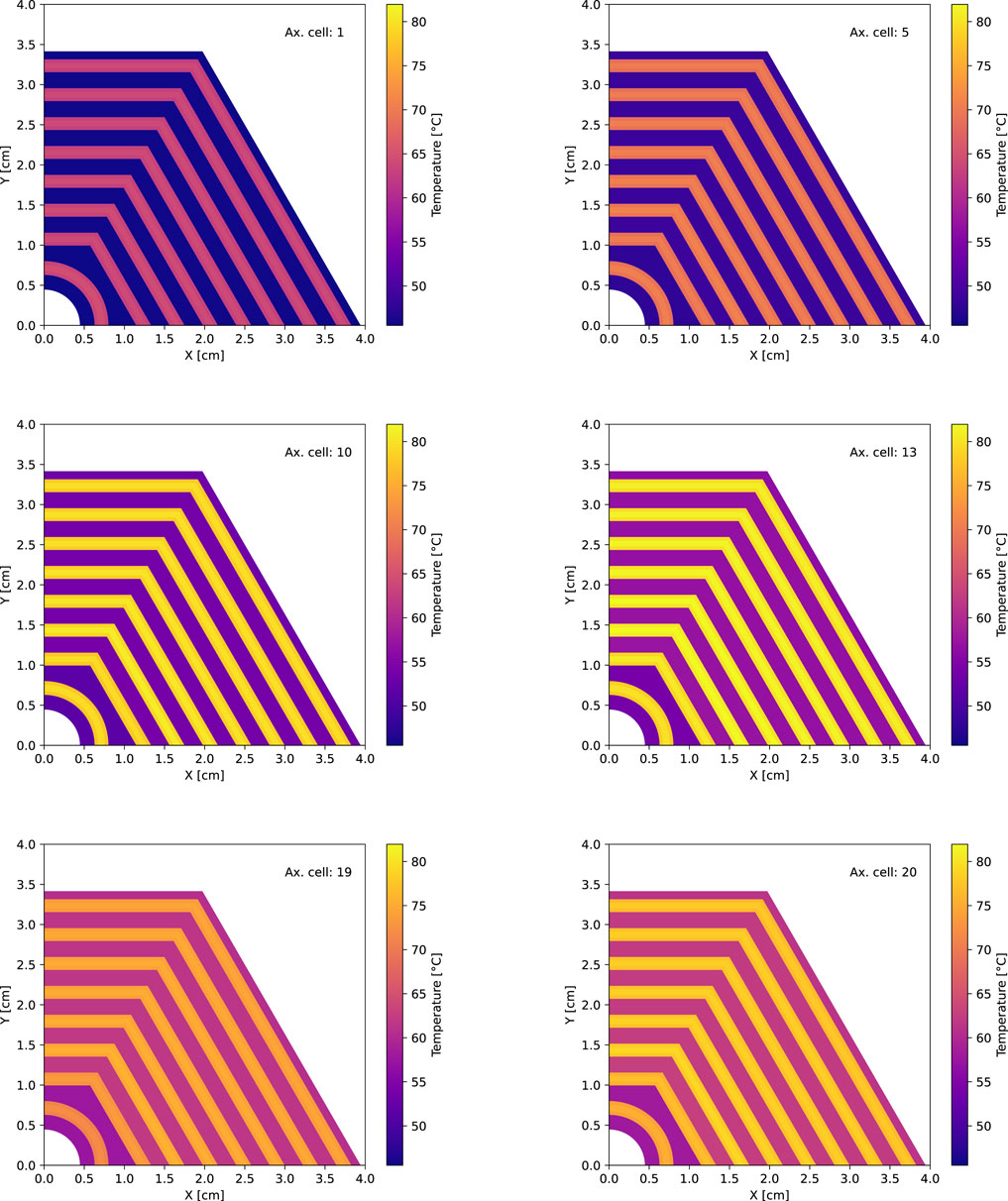
Figure 9. Temperature distribution predicted by Serpent/Subchanflow at different axial layers starting from the inlet to the core outlet. Only 1/4 of the core is shown due to the symmetry of the problem.
The thermal-hydraulic results previously presented were calculated using the Colburn correlation. A sensitivity analysis comparing the Colburn and Dittus-Boelter correlations showed that the Colburn correlation yielded slightly higher temperature. To ensure a conservative approach, the results using Colburn were selected for presentation. The comparative results using these two correlations are summarized in Table 8, showing negligible differences, with temperature variations less than 2°C. The observed difference arises because the Colburn correlation predicts a lower heat transfer coefficient. This results in a higher temperature difference between the coolant and the external cladding surface, leading to slightly elevated cladding and fuel temperatures. Similar findings were reported during the Subchanflow validation for plate-type fuels (Almachi et al., 2021).
As a final step, a comparison against the TH evaluation performed in (Nguyen et al., 2020) is presented. The hottest FA producing
7 Summary and conclusion
A coupled neutronic/thermal-hydraulic simulation of a single VVR-KN fuel assembly using Serpent/Subchanflow was performed. Eight iterations were considered to obtain a converged steady-state solution, capturing consistent results regarding power and temperature profile distributions. Unfortunately, a comparison against experiments or referent simulations was hard to perform because of the simplified problem definition considered in this work and all the required assumptions, e.g., boundary conditions, set of correlations, material composition, and constant thermal properties. Nevertheless, the novelty of the result remains in the high-detail coupled neutronic/thermal-hydraulic solution in a non-regular plate or subchannel shape size, and it paves the way for a more realistic simulation, such as a VVR-KN full-core characterization.
An important remark of the work is the satisfactory use of the Serpent’s unstructured mesh-based interface for the thermal-hydraulic coupling with Subchanflow. It is the first time that this type of interface has been employed within a Serpent/Subchanflow simulation. This interface type offers excellent versatility and more generality for generating non-regular meshes. Minor changes in the coupling routines were required to ensure consistent data exchange between the two codes without affecting their source codes. A better performance could be achieved by exchanging the information directly from RAM memory. However, some changes in the source codes are needed to add this feature to the coupled tool.
Subchanflow has been validated widely for standard PWR and BWR rod-type fuels. However, extra development is still needed to enlarge the thermal-hydraulic analysis in MTR research reactors. Some examples of future developments are implementing critical heat flux correlations for plate-type fuels, temperature-dependent thermal properties for standard MTR materials, and heat expansion treatment.
Data availability statement
The raw data supporting the conclusion of this article will be made available by the authors, without undue reservation.
Author contributions
GH: Conceptualization, Data curation, Formal Analysis, Investigation, Methodology, Software, Visualization, Writing–original draft, Writing–review and editing. TG: Conceptualization, Investigation, Software, Writing–review and editing. VS: Funding acquisition, Project administration, Resources, Writing–review and editing, Supervision. JA: Software, Writing–review and editing. UI: Software, Supervision, Writing–review and editing.
Funding
The author(s) declare that financial support was received for the research and/or publication of this article. The authors thank the HGF-Program NUSAFE at the Karslruhe Institute of Technology (KIT) for the financial support for the research topic multi-physics at the Institute for Neutron Physics and Reactor Technology (INR).
Conflict of interest
The authors declare that the research was conducted in the absence of any commercial or financial relationships that could be construed as a potential conflict of interest.
Generative AI statement
The authors declare that no Generative AI was used in the creation of this manuscript.
Publisher’s note
All claims expressed in this article are solely those of the authors and do not necessarily represent those of their affiliated organizations, or those of the publisher, the editors and the reviewers. Any product that may be evaluated in this article, or claim that may be made by its manufacturer, is not guaranteed or endorsed by the publisher.
Footnotes
1For simplicity,
2The FA is composed of eight coaxially arranged FEs, and every FE in the thermal-hydraulic model is divided in six plates.
References
Abdukadyrova, I. K., Alikulov, S. A., Akhmedzhanov, F. R., Baitelesov, S. A., Boltaboev, A. F., and Salikhbaev, U. S. (2014). High-temperature thermal conductivity of sav-1 aluminum alloy. At. Energy 116, 100–104. doi:10.1007/s10512-014-9825-0
Almachi, J. C., Sánchez-Espinoza, V., and Imke, U. (2021). Extension and validation of the subchanflow code for the thermo-hydraulic analysis of mtr cores with plate-type fuel assemblies. Nucl. Eng. Des. 379, 111221. doi:10.1016/j.nucengdes.2021.111221
Almachi, J. C., Sánchez-Espinoza, V. H., and Imke, U. (2022). High-fidelity steady-state and transient simulations of an mtr research reactor using serpent2/subchanflow. Energies 15, 1554. doi:10.3390/en15041554
Almachi, J. C., Sánchez-Espinoza, V., Imke, U., Stieglitz, R., and Margulis, M. (2024). Validation of the dynamic simulation capabilities of serpent2/subchanflow using experimental data from the research reactor spert iv d-12/25. Nucl. Eng. Des. 418, 112840. doi:10.1016/j.nucengdes.2023.112840
Demazière, C., Espinoza, S., Hugo, V., and Chanaron, B. (2020). Advanced numerical simulation and modelling for reactor safety contributions from the cortex, hpmc, mcsafe and nuresafe projects. EPJ Nucl. Sci. Technol. 6, 42. doi:10.1051/epjn/2019006
Ferraro, D., García, M., Imke, U., Valtavirta, V., Tuominem, R., Bilodid, Y., et al. (2021a). Serpent/subchanflow coupled calculations for a vver core at hot full power. PHYSOR2020 EPJ Web Conf. 247, 04006. doi:10.1051/epjconf/202124704006
Ferraro, D., García, M., Imke, U., Valtavirta, V., Tuominem, R., Leppänen, J., et al. (2021b). Serpent/subchanflow coupled bunrup calculations for vver fuel assemblies. PHYSOR2020 EPJ Web Conf. 247, 04005. doi:10.1051/epjconf/202124704005
Ferraro, D., García, M., Valtavirta, V., Imke, U., Tuominen, R., Leppänen, J., et al. (2020a). Serpent/subchanflow pin-by-pin coupled transient calculations for a pwr minicore. Ann. Nucl. Energy 137, 107090. doi:10.1016/j.anucene.2019.107090
Ferraro, D., García, M., Valtavirta, V., Imke, U., Tuominen, R., Leppänen, J., et al. (2020b). Serpent/subchanflow pin-by-pin coupled transient calculations for the spert-iiie hot full power tests. Ann. Nucl. Energy 142, 107387. doi:10.1016/j.anucene.2020.107387
Ferraro, D., Valtavirta, V., García, M., Imke, U., Tuominen, R., Leppänen, J., et al. (2020c). Oecd/nrc pwr mox/uo2 core transient benchmark pin-by-pin solutions using serpent/subchanflow. Ann. Nucl. Energy 147, 107745. doi:10.1016/j.anucene.2020.107745
Hagrman, D. L., and Reymann, G. A. (1979). Matpro - version 11, a handbook of materials properties for use in the analysis of light water reactor fuel rod behavior. Idaho: EG&C Idaho, Inc. Idaho Falls.
Huaccho, Z. G., Sánchez-Espinoza, V. H., Mercatali, L., and Imke, U. (2025). An overcooling transient analysis in a carem-like smr core using serpent/subchanflow. Ann. Nucl. Energy 214, 111204. doi:10.1016/j.anucene.2025.111204
Imke, U., and Sanchez, V. H. (2012). Validation of the subchannel code subchanflow using the nupec pwr tests (psbt). Sci. Technol. Nucl. Installations 2012, 1–12. doi:10.1155/2012/465059
Konoplev, K. (2010). “Cooling and radiation safety control requirements for safe storage of LEU WWR-M experimental fuel assemblies”. 14. international topical meeting on Research Reactor Fuel Management (RRFM) (RRFM 2010), S. [5 p.].
Leppänen, J. (2013). Modeling of nonuniform density distributions in the serpent 2 Monte Carlo code. Nucl. Sci. Eng. 174, 318–325. doi:10.13182/NSE12-54
Leppänen, J., Pusa, M., Viitanen, T., Valtavirta, V., and Kaltiaisenaho, T. (2015). The serpent Monte Carlo code: status, development and applications in 2013. Ann. Nucl. Energy 82, 142–150. doi:10.1016/j.anucene.2014.08.024
Leppänen, J., Viitanen, T., and Valtavirta, V. (2023). Multi-physics coupling scheme in the serpent 2 Monte Carlo code.
Mercatali, L., Huaccho, G., and Sanchez-Espinoza, V. H. (2023). Multiphysics modeling of a reactivity insertion transient at different fidelity levels in support to the safety assessment of a smart-like small modular reactor. Front. Energy Res. 11. doi:10.3389/fenrg.2023.1130554
Nguyen, N. D., Nguyen, K. C., Huynh, T. N., Vo, D. H. D., and Tran, H. N. (2020). Conceptual design of a 10mw multipurpose research reactor using vvr-kn fuel. Sci. Technol. Nucl. Installations 2020, 1–11. doi:10.1155/2020/7972827
Salikhbaev, U. S., Baytelesov, S. A., Kungurov, F., and Saidov, A. S. (2009). Studying of influence of a neutron irradiation on element contents and structures of aluminum alloys sav-1 and amg-2. Trans. RRFM 2009, Vienna.
Sanchez-Espinoza, V. H., Gabriel, S., Suikkanen, H., Telkkä, J., Valtavirta, V., Bencik, M., et al. (2021b). The h2020 mcsafer project: main goals, technical work program, and status. Energies 14, 6348. doi:10.3390/en14196348
Sanchez-Espinoza, V. H., Mercatali, L., Leppänen, J., Hoogenboom, E., Vocka, R., and Dufek, J. (2021a). The mcsafe project high-performance Monte Carlo based methods for safety demonstration: from proof of concept to industry applications. EPJ Web Conf. 247, 06004. doi:10.1051/epjconf/202124706004
Serpent (2024). A continuous-energy Monte Carlo neutron and photon transport code. Available online at: https://serpent.vtt.fi/(Accessed July, 2024).
Stahl, D. (1982). Fuels for research and test reactors, status review: july 1982. ANL-83-5. Argonne National Laboratory. doi:10.2172/5942981
Valtavirta, V. (2015). Multi-physics capabilities in serpent 2. Serpent and multi-physics workshop LPSC Grenoble, 26–27.
Keywords: Monte Carlo, multi-physics, serpent, subchanflow, VVR-KN, unstructured mesh-based interface, research reactors
Citation: Huaccho Zavala G, Gheeraert T, Sánchez-Espinoza VH, Almachi JC and Imke U (2025) Coupled serpent/subchanflow analysis with unstructured mesh interfaces for a hexagonal, plate-type VVR-KN fuel assembly. Front. Nucl. Eng. 4:1570855. doi: 10.3389/fnuen.2025.1570855
Received: 04 February 2025; Accepted: 17 March 2025;
Published: 01 April 2025.
Edited by:
Deokjung Lee, Ulsan National Institute of Science and Technology, Republic of KoreaReviewed by:
Yunje Cho, Korea Atomic Energy Research Institute (KAERI), Republic of KoreaMuhammad Rizwan Ali, Pakistan Institute of Engineering and Applied Sciences, Pakistan
Copyright © 2025 Huaccho Zavala, Gheeraert, Sánchez-Espinoza, Almachi and Imke. This is an open-access article distributed under the terms of the Creative Commons Attribution License (CC BY). The use, distribution or reproduction in other forums is permitted, provided the original author(s) and the copyright owner(s) are credited and that the original publication in this journal is cited, in accordance with accepted academic practice. No use, distribution or reproduction is permitted which does not comply with these terms.
*Correspondence: Gianfranco Huaccho Zavala, Z2lhbmZyYW5jby56YXZhbGFAa2l0LmVkdQ==