- 1Department of Nuclear Engineering, Idaho State University, Pocatello, ID, United States
- 2School of Nuclear Science and Engineering, Oregon State University, Corvallis, OR, United States
The Versatile Test Reactor is meant to fill a need in the advanced nuclear reactor development community. Accelerated nuclear testing of fuels and materials is needed to allow designs to proceed. To accomplish this, a fast neutron spectrum is needed. To have a fast neutron spectrum, the reactor coolant needs to not only have excellent heat transfer properties to sufficiently cool the reactor core, but also not significantly slow neutrons down following their birth in the fission process. Sodium is an excellent coolant choice that can fulfill these needs and many others. Sodium is the sixth most abundant element in the Earth’s crust and can be acquired easily through simple chemical separation methods. Sodium, however, reacts when in contact with water and air, but with proper precautions, these scenarios can be avoided. Nuclear reactors that utilize molten sodium as a primary heat transfer medium [a.k.a. sodium-cooled fast-neutron reactors, or SFRs, Figure 1 (1)] provide unique challenges in their daily operation, and therefore require focused training for researchers, scientists, staff, and employees alike to understand these unique challenges. Therefore, a comprehensive understanding of sodium properties is needed by all personnel involved in the design, construction, operation, experiment planning and execution of SFRs. Additionally, several commercial advanced reactor designs are under development which will use sodium for the reactor coolant. These advanced reactor designs include the Natrium reactor from TerraPower and GE-Hitachi (2), the ARC-100 reactor from Advanced Reactor Concepts (3), and the Aurora reactor from Oklo (4).
Introduction
The Versatile Test Reactor (VTR) is meant to fill a need in the advanced nuclear reactor development community. Accelerated nuclear testing of fuels and materials is needed to allow designs to proceed. To accomplish this, a fast neutron spectrum is needed. To have a fast neutron spectrum, the reactor coolant needs to not only have excellent heat transfer properties to sufficiently cool the reactor core, but also not significantly slow neutrons down following their birth in the fission process.
Sodium is an excellent coolant choice that can fulfill these needs and many others. Sodium is the sixth most abundant element in the Earth’s crust and can be acquired easily through simple chemical separation methods. Sodium, however, reacts when in contact with water and air, but with proper precautions, these scenarios can be avoided. Nuclear reactors that utilize molten sodium as a primary heat transfer medium [a.k.a. sodium-cooled fast-neutron reactors, or SFRs, Figure 1 (Gen IV International Forum, 2152)] provide unique challenges in their daily operation, and therefore require focused training for researchers, scientists, staff, and employees alike to understand these unique challenges. Therefore, a comprehensive understanding of sodium properties is needed by all personnel involved in the design, construction, operation, experiment planning and execution of SFRs.
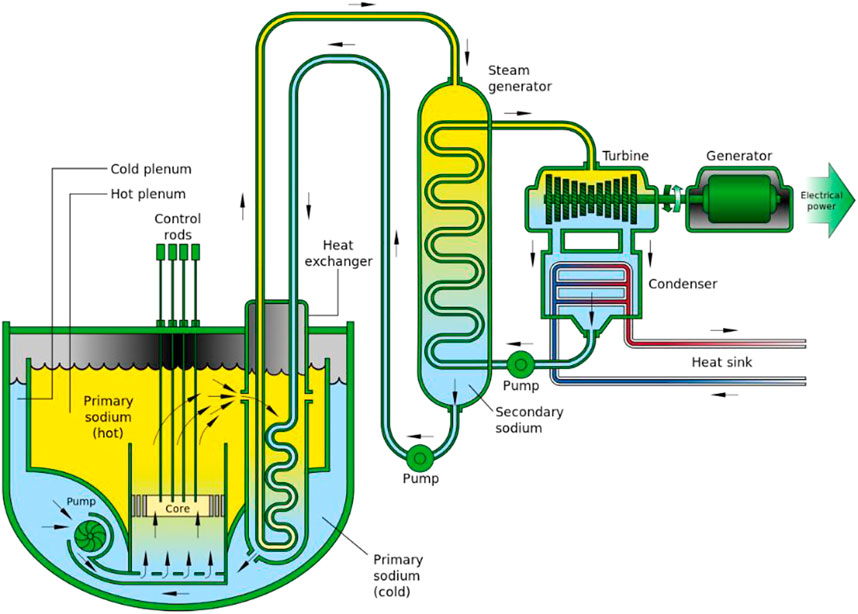
FIGURE 1. Schematic of a sodium fast cooled reactor (SFR) facility (Gen IV International Forum, 2152).
Additionally, several commercial advanced reactor designs are under development which will use sodium for the reactor coolant. These advanced reactor designs include the Natrium reactor from TerraPower and GE-Hitachi (TerraPower, 2023), the ARC-100 reactor from Advanced Reactor Concepts (Advanced Reactor Concepts, 2023), and the Aurora reactor from Oklo (U.S., 2023).
As part of a United States Department of Energy (DOE) supported grant for the VTR project, Oregon State University (OSU) proposed the performance of a scaling analysis on unique fluids from a top-down and bottom-up approach with baselined operational characteristics for each respective working fluid and loop concept, along with the design of an ex-pile loop that provides representative characteristics to that experienced within the VTR with a design basis founded by a set of comprehensive technical and functional requirements. As co-investigator on the project, Idaho State University (ISU) set forth to develop a sodium safety culture program through leveraging collaborations between industry and national laboratory partners, with strategic formation followed by execution of a complete course curriculum (Marcum et al., 2019).
In a parallel, but separate effort, faculty at ISU recognized the opportunity existed for the development of a small test facility to accelerate program development for entities such as the VTR, and expected follow-on and support facilities, with close interaction and feedback from staff and researchers within both the national laboratory system (e.g., Idaho National Laboratory (INL) and Argonne National Laboratory (ANL)) as well as industry leaders (TerraPower, Advanced Reactor Concepts (ARC), and Oklo) during the design, development, and construction phases. In addition, newly established programs for advanced reactor research, such as the Nuclear Reactor Innovation Center (NRIC), may have needs for localized testing that do not necessarily require facility use at INL. Laboratory-scale testing capabilities on nearby university campuses, in principle, could be used to develop and assess the performance of instrumentation that may be used for multiple initiatives, whether in situ reactor testing, fundamental or prototype testing.
Background
Sodium (Na, for the Latin word natrium) metal is soft, malleable, and silvery white in color (Figure 2) (Nuclear Power Online, 2020). Its density is relatively low at 0.97 g/cm3, and its thermal and electrical conductivity values are among the highest of all known materials. Based on its high chemical reactivity, being an alkali metal, elemental sodium is rarely found in nature. Sodium metal most often interacts (via oxidation) with air to form sodium oxide (Na2O), a crystalline material with a high melting point. Like other metals, sodium conducts electricity and heat efficiently; it is approximately 100 times more effective at transferring heat than water, which allows it to be considered for use within nuclear reactors as a coolant (Whaley, 1973).
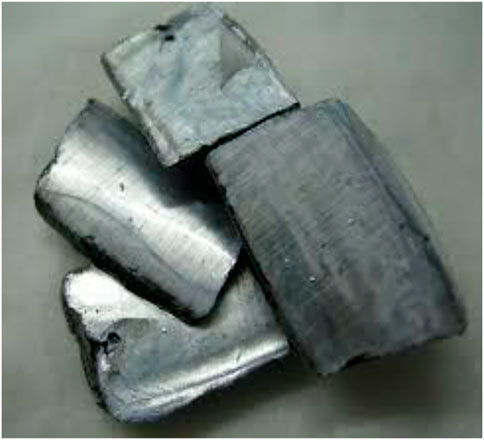
FIGURE 2. Solid sodium metal (Nuclear Power Online, 2020).
Elemental sodium is most often found within the Earth’s crust in the form of sodium chloride. Sodium is also found as the silicate in igneous rocks and natural compounds that include sodium nitrate, sodium sulfate, sodium carbonate, sodium bicarbonate, and sodium tetraborate. In its natural form it can be found in soils, waters, and the bodies of plants and animals. Industrial uses of sodium metal are based primarily on its strong reducing properties. Approximately 80% of worldwide production of sodium in the 20th century was to produce tetraethyllead and tetramethyl lead for use as a gasoline anti-knock compound.
Most of the current production of sodium is now used to manufacture sodium alkyl sulfates, which are utilized in detergent production. Nearly 10% of the annual sodium production is now used to produce titanium metal through the reduction of titanium tetrachloride. The remaining 10% is used to produce compounds, such as sodium hydride, sodium alkoxides and sodium peroxide; as a coolant in fast nuclear reactors; as an electrical conductor in sodium-filled transmission lines; and for a variety of other, smaller uses (Whaley, 1973).
Table 1 and Table 2 (Lennitech, 2020) provide a summary of important physical and chemical properties of solid and molten sodium. Note that at atmospheric pressure, the density of sodium is roughly the same as the density of water at standard atmospheric pressure. Sodium coolant systems often operate near atmospheric pressures due to its large liquidus range and high boiling point. The use of sodium within nuclear reactors requires significantly less pressure than light water reactors, suggesting that sodium-cooled systems provide some inherent safety with regards to reactor operations.
Nuclear properties of the lighter alkali metals have been investigated at considerable length, primarily due to the use of sodium or a sodium-potassium alloy (NaK) as a coolant in fast reactors. Neutron interactions with sodium can include simple capture events that produce Na-24, since sodium has only one stable isotope (Na-23), but it can also undergo (n, 2n) (n, p) and (n, α) reactions, as described in Table 3 (Knolls Atomic Power Laboratory).
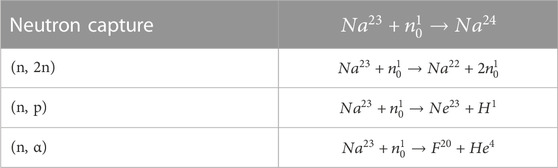
TABLE 3. Sodium nuclear reactions (Knolls Atomic Power Laboratory).
In pool type SFRs, the primary sodium pool will be the main location where neutron capture will occur, while very trivial amounts will occur in the intermediate loop (Figure 1). The neutron capture cross-section value (σn) of sodium at thermal energies (0.025 eV) is 0.53 b, with a total cross section value (σt) at 0.025 eV of 3.9 b. The total cross-section (Figure 3) is relatively constant at about 3 b until 2.85 keV, where a large elastic scattering resonance increases the value to about 370 b (Brookhaven National Laboratory, 2023).
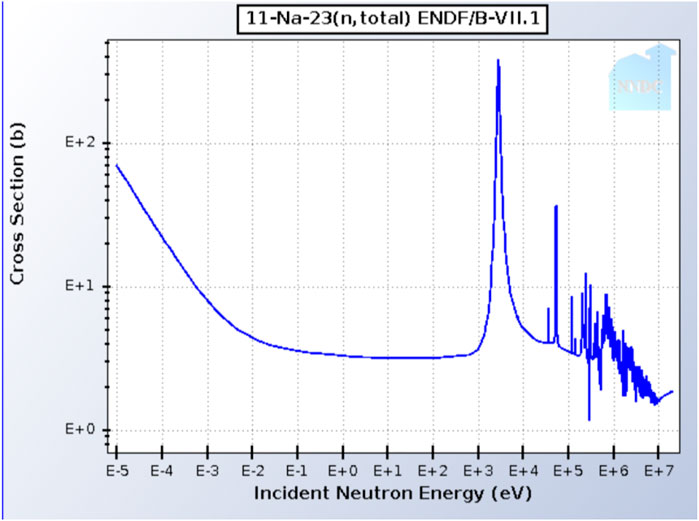
FIGURE 3. Total neutron cross-section for Na-23 (Brookhaven National Laboratory, 2023).
Sodium reactor designs
There are two different types of SFR designs that have generally been used, the pool or loop system. Pool-type reactors use a large pool of sodium that completely engulfs the reactor core and transports heat away from the core. Loop-type reactors utilize a smaller pool and rely more heavily on pumping sodium to cool the reactor. Pool type reactors are generally considered to be safer design options because of the reduction of certain design basis accidents, such as loss of coolant accidents (LOCAs). The possibility of these events are all but eliminated by the pool type SFR design, where the large sodium pool can accommodate the energies released during reactor transient accidents and heat is safely removed through conduction. The current design for the VTR is that of a pool-type reactor, based on the General Electric concept PRISM reactor (Office of Nuclear Reactor Regulation, 1994). Other SFR designs, such as the Natrium reactor from TerraPower, eliminates the generation of steam directly from the hot intermediate sodium through an additional salt loop. A general schematic showing the similarities and differences between pool and loop type reactors is shown in Figure 4.
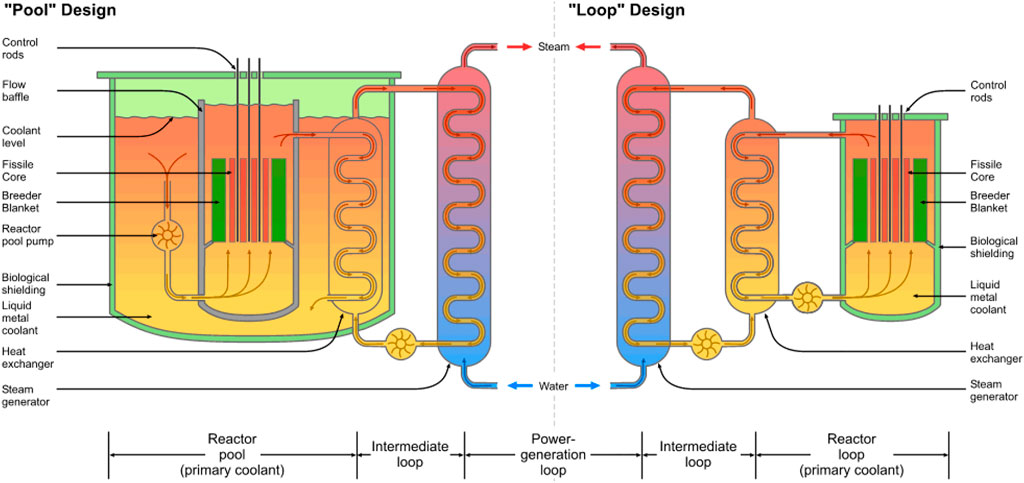
FIGURE 4. Description of pool and loop type reactor designs (Emoscopes, 2006).
Hazards of working with sodium
As mentioned above, sodium metal is highly reactive chemically due to its single valence electron, which is readily available to react with other molecules around it to stabilize sodium with a stable outer shell. Practical treatment of sodium as an industrial hazard can provide significant challenges. Traditional extinguishing agents, such as carbon dioxide, dry chemical foam, and carbon tetrachloride, can cause explosions and fire when interacting with sodium metal.
Sodium as a liquid is opaque, meaning that during the occurrence of a leak, liquid sodium should be visible and is typically accompanied by dense white smoke, thus making emergency responses easy when proper training has occurred. Sodium vapor in heavy layers appears bluish, and at higher temperatures, turns to yellow. In the saturated-vapor state, sodium monomer and dimer are in equilibrium, the dimer being favored by increasing temperature (Foust, 1973).
Sodium-water reactions
One of the primary working hazards for solid or molten sodium is the interaction with liquid water, and particularly the oxygen content within water molecules. Oxygen has two unpaired electrons, which are available to react with the valence electron of sodium. This reaction between sodium and water follows two primary schemes with the formation of three different products and can be seen in Eq. 1. Sodium hydroxide and hydrogen gas are the major products of the exothermic reaction between solid sodium and liquid water (ΔH = 141 kJ/mol at 25°C) (Takashi Takata, 2003):
When liquid water contacts sodium instead of water vapor, hydrogen gas is rapidly emitted and–being an exothermic reaction - can ignite if oxygen is present. Before hydrogen plays a role, however, within just several picoseconds (10−12 s) the sodium loses its valence electron to the surrounding water molecules and causes the sodium atom to ionize. After ionization occurs, the positively charged sodium ions can repel each other with such force that it may cause them to rip apart (Takashi Takata, 2003). This event, along with the possibility of hydrogen gas burning, can lead to an explosion. As these reactions are exothermic in nature, the sodium will heat up and begin to melt if it is in solid form.
The Japan Nuclear Cycle Development Institute studied two types of sodium-water interactions: A liquid sodium-to-water vapor reaction and a gas-to-gas reaction. In the liquid sodium to water vapor reaction, the reaction rate is sufficiently higher than the diffusion rate, resulting in most interactions staying at the liquid sodium surface. The water molecules react with a sodium molecule and remove it from the sodium pool. In a gas-to-gas reaction, a water-sodium complex is first formed, and then subsequently forms sodium hydroxide and hydrogen gas as the major reactants (Takashi Takata, 2003). If sodium and water come in contact within an enclosed area, such as a pipe, the hydrogen gas covers up the liquid-gas interface between the sodium and water vapor, which in turn helps to moderate the sodium-water reaction. With the introduction of hydrogen gas comes a possible rise in pressure, which could cause a breach in the pipe system if not properly designed to handle such incidents.
Sodium-concrete reactions
When concrete undergoes its hydration process, it ends up containing large amounts of water, often up to 20% of total volume. Sodium-concrete interactions play a critical role in the design of sodium cooled reactor facilities due to the widespread use of concrete as infrastructure material. As described earlier in the sodium chemistry section, the interaction of molten sodium with the environment tends to be violent. Hanford Engineering Development Laboratory (HEDL) performed several experiments on this premise in 1979 (Colburn, 1979).
Two of the major safety concerns associated with sodium-concrete reactions are hydrogen gas generation and chemical energy release. The general behavior of sodium-concrete reactions was analyzed by HEDL with the parameters of temperature, penetration, and general observation. The experiments at HEDL considered three types of concrete: Basalt, magnetite and limestone aggregate. All specimens were first cast into hollow cylinders and then had 24 kg of hot sodium (510°C–870°C) poured into their centers. The bulk of the penetration occurred during the initial 8 hours with little additional penetration afterwards. Hydrogen was released in significant quantities and had a 3%–4% increase per hour. A total of 80% of the concrete moisture was released after 8 hours. The initial reaction of sodium with concrete occurs with water being thermally released from the concrete. Most of this water originates at a substantial distance from the reaction interface. Both energy release and hydrogen gas generation are dominated by the reaction of sodium with the thermally-released water to form NaOH.
Sodium fires
Two types of sodium combustion will be discussed in this section: pool fires and jet spray fires. While the boiling temperature of sodium is quite high (881°C), the flame temperature is significantly higher (1350°C). By comparison, the temperature of lava from the Kilauea Volcano in Hawaii is about 1170°Ϲ. The flame temperature of sodium is also equal to the monoxide evaporation temperature which means if there are flames present, then monoxide should also be considered as present. Sodium fires leave two types of residues: aerosols and crust. The aerosols are composed of sodium peroxide, which could be transformed at first into hydroxide and then into carbonate when in contact with air. The crust is a mixture of sodium monoxide, sodium peroxide, and sodium carbonate (MALET, 1310).
Pool fires refer to a leakage of some sort, such as in a pipe or a vessel. Due to their nature, these are a localized phenomenon. In this type of fire, sodium burns either in a vapor phase with the formation of sodium oxide (Na2O) in the flame area, or on the surface with the formation of peroxide. Sodium pool fires usually occur in a gaseous mixture of air, with the sodium temperature between 200°Ϲ and 500°Ϲ. The gas mixture occurring between sodium and air causes fire propagation. Initial temperature of sodium has little to no effect on the combustion rate because the sodium stabilizes during combustion at a value varying between 570°C and 750°C.
Jet spray fires refer to a fast-flowing spray of sodium, that is, ejected from a pipe or vessel. The direction of the jet spray is the most important factor when considering the thermodynamic consequences of this type of fire. Combustion is limited by the diffusion of oxygen towards the jet temperature at 550°Ϲ. Furthermore, when the sodium flowrate increases, the ratio of the mass of sodium burnt and the mass of sodium ejected reaches a limit of 10% (MALET, 1310). This means that segregating the rooms into smaller, separate units is efficient at reducing the thermodynamic consequences of a sodium jet fire.
There are recorded instances where sodium leaks have occurred and led to fires that affected facility operations. One such event took place in 1968, when a sodium leak occurred in the secondary sodium system of the Experimental Breeder Reactor-II (EBR-II) facility at Argonne National Laboratory-West (Sackett, 2008). Approximately 100 gallons of molten sodium spilled onto the floor of the secondary sodium control system. Prior to the accident, a set of repairs to a bellows-seal isolation valve in the secondary-sodium plugging loop were performed, including allowing the sodium to freeze in the pipe, cutting out a section and then re-welding the section of pipe back into the original line. Unfortunately, the frozen sodium plug did not extend as expected beyond the removed section; once welding began, the sodium melted and spilled to the floor. A significant fire occurred but was contained and extinguished by application of Met-L-X (Figure 5).
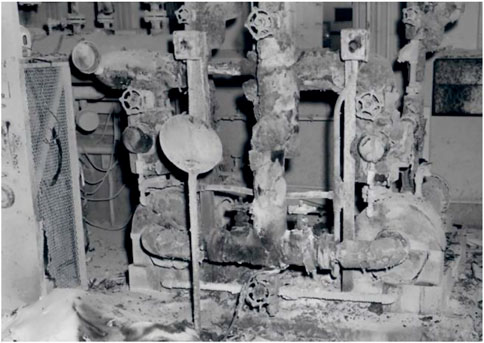
FIGURE 5. EBR-II sodium leak and resulting fire remnants (Sackett, 2008).
Chemical and radiological hazards
Sodium toxicity is comparable to some more commonly known materials using the Protective Action Criteria (PAC) Revision-29 concentration levels (United States Department of Energy, 2020). The escaping particles related to SFRs are elemental sodium and its reaction products with air (sodium oxide) and water (sodium hydroxide). These sodium particles are compared with an equivalently toxic amount of carbon monoxide, cyanide, and formaldehyde. Carbon monoxide, cyanide, and formaldehyde are well known as toxic compounds. Most notably, the most hazardous of these items are the inhalation of sodium oxide and sodium hydroxide. The dispersion of concentrations of aerosol sodium, gaseous sodium or sodium dust, and reaction products is best descried by a Gaussian model for plume diffusion, matching experimental data and is consistent with the randomness of turbulence models for fluid dynamics (Hanna et al., 1982).
In a SFR, the primary sodium will be directly contacting the core and will be activated during operation. The secondary loop however will not be in contact with the core and will be significantly less activated than the primary loop sodium. Neutron-activated sodium will result in varying amounts of resulting sodium isotopes. The most prominent isotope will be Na-24 as all isotopes beyond Na-24 have half-lives less than 1 minute (Knolls Atomic Power Laboratory). Due to the exceptionally large disparity between Na-24 and all other sodium isotopes, all other sodium isotopes are negligible for activation. As an example, the next largest sodium isotope produced is Na-22 with a half-life of 2.6 years. This might seem like a big contributor of radiation; however, Na-22 is produced at a rate of roughly 0.005% as that of Na-24 (Shu, 2020). The Na-24 activity of the primary sodium is plotted against time in Figure 6 where it is seen that after approximately 120 h, the sodium activation reaches an equilibrium. A conservative estimate for the activation of sodium within the loop is based on a neutron flux of 4 × 1015 n/cm2/s, with an estimated core volume of 500 cm3 (with 50% sodium fill capacity).
Radiative capture is a nuclear reaction between a neutron and a nucleus where the nucleus absorbs or captures the neutron, increasing the atom’s A number by one, and emitting extra energy as a gamma ray. When natural sodium undergoes radiative capture, the Na-23 becomes Na-24 or metastable Na-24 m (an isomer of Na-24). Eq. 2 describes the neutron capture of Na-23.
Once the reactor shuts down, the sodium activation process ceases. The neutron-activated sodium then begins the process of radioactive decay to achieve a stable state (Figure 7). There is only one decay mode that applies to Na-24—beta decay–which leads to the production of Mg-24 (Knolls Atomic Power Laboratory). However, those decay events can occur at three different energy levels, through isomeric transition. The most frequent isomer of Mg-24 (E = 4122.9 keV, with 99.985% frequency) subsequently releases two photons (E = 2754 and E = 1368.7 keV) to attain a stable state.
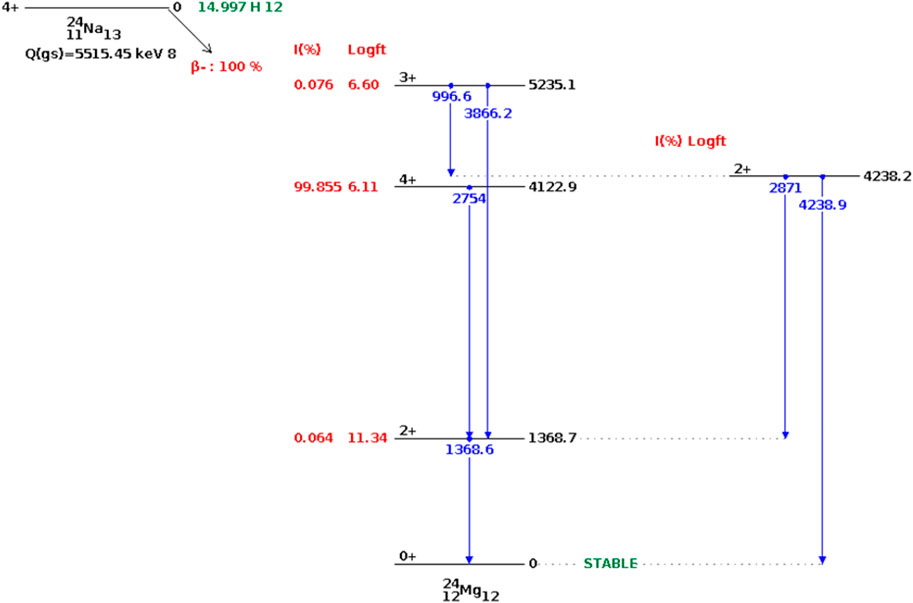
FIGURE 7. Decay of Na-24 nuclei (Shu, 2020).
Engineering and designing sodium systems
When designing sodium systems, several important features must be considered including heat transfer, material compatibility, instrumentation, and mechanical equipment selection. The main purpose that the VTR will fulfill is the testing of fuels and materials to help the advancement of the next-generation of nuclear reactors. The VTR will also be used to validate advanced modeling techniques and prove existing and future designs. This section will go into a general overview of the various systems that are included in the function of most SFRs, using historical examples.
Pumps
There are many different types of pumps that have been utilized over the years to circulate sodium through the reactor and heat exchanger system. Examples include electromagnetic pumps, centrifugal pumps, and others. Provided below are a few examples of pumps used in sodium systems, including their advantages and drawbacks.
Centrifugal pumps
Centrifugal pumps can output varying degrees of head and flow depending on the impeller used. Radial impellers offer a high head but a low flow, while axial impellers offer a low head with high flow. Mixed impellers also are available that offer a mix of head and flow (Foust, 1978). Cavitation is an issue that should be dealt with when working with centrifugal pumps. Due to the high operating temperature that the liquid sodium will be at, mechanical components inside the pump may deteriorate at a faster rate when compared to ambient water cavitation. Centrifugal pumps offer a large range of uses but are often difficult to seal. One solution to this problem has been to implement vertical shaft pumps, which elevates the motor casing above the sodium operating level, as seen in Figure 8. These pumps also offer inherent coastdown which provides a smooth transition to natural circulation flow.
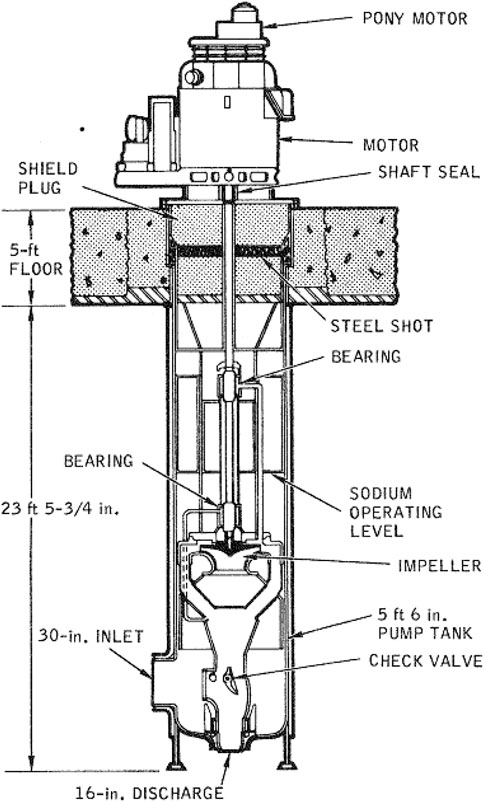
FIGURE 8. Vertical shaft pump used in the Fermi reactor power plant (Foust, 1978).
Electromagnetic pumps
Due to liquid sodium metal being paramagnetic, electromagnetic (EM) pumps are able to circulate liquid sodium through a system using either conduction or induction. The metal moves as it interacts with the current and magnetic field produced. Electromagnetic pumps possess some qualities that are not achievable with mechanical pumps. They are relatively simple and very reliable. Some of the top advantages to EM pumps are explained by Foust as follows;
1) No moving parts are in contact with liquid metal.
2) No seals are required.
3) The piping system carrying the pumped fluid is not rigidly anchored by the pump.
4) The piping system does not have to be opened when pump maintenance is required.
5) EM pumps can operate in any position.
No free surface between cover gas and liquid metal exists in an EM pump. This is of importance in primary coolant systems for nuclear reactors where gas bubbles in the liquid-metal stream create a potential hazard. The change in reactivity as bubbles pass through a reactor core is a potential cause of meltdown. An EM pump installed in a primary coolant system can convert quickly from pumping the coolant to retarding coolant flow immediately following a “scram” event, thereby minimizing stresses in the reactor core (Foust, 1978). Electromagnetic pumps contain many benefits, but they also have their drawbacks. Any voids that are present in the liquid metal may cause a large increase in temperature of the duct and its walls and can lead to pump failure. Overtemperature of the liquid metal or pressure fluctuations inside the duct can also lead to reduced performance. Additionally, these pumps do not offer the inherent coastdown which presents challenges when transitioning to natural circulation.
Sandia National Laboratory (SNL) built the Sandia Sodium Purification Loop (SNAPL) to further the research and development of sodium safety and activated sodium for fast breeder reactors. One component in SNAPL was the implementation of an EM pump, which circulated sodium through both the loop but also through the experimental apparatus when a specific voltage input is supplied (Acton et al., 1985). The pump used is shown in Figure 9, which provides the direction of the current and flux of the magnetic field that moves the sodium through the pump.
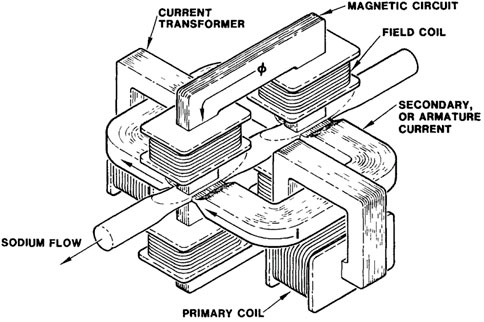
FIGURE 9. Two-stage electromagnetic pump (Acton et al., 1985).
Piping and valves
Degradation of piping systems in a sodium facility is generally less corrosive than for a water system, with stressors of water and steam. Since sodium has such a high boiling point, its systems provide excellent heat transfer properties while operating at near-atmospheric pressure. This lack of needed pressurization can prove advantageous when designing piping and valve systems, whereas light water reactors (LWRs) operate under very high pressures (1,000–2,500 psia).
Even though pure sodium possesses low corrosion characteristics towards stainless steel, monitoring systems should be used to detect any debris or particulate that could affect the performance or coolant flow. Filtration systems should be present to catch any particulates in the coolant that may come from corrosion, reactions with air, or other impurities. Particulates can clog different parts of the heat transfer system and could cause damage to piping, valves, pumps, the reactor core, etc.
Pipes and valves should be made from materials with high hot hardness and good corrosion resistance. This is especially important because the sodium will be working in the temperature range of 600°C. Piping systems should possess some method for preheating prior to hot sodium introduction, as the large temperature gradient between the sodium and piping could cause premature cracking or fissures. This is often done through electric cables or trace heaters.
A very common spot for cracking to occur in piping are welds. Over constraint can occur during heat transients if welds are excessively welded which can cause cracking of welds and result in a coolant leak. Great care should be taken when welding pipes, valves, and other components of the reactor system. Piping oftentimes is built with a double walled system to contain any leaks that may occur. If there is a breach in the main pipeline, sodium will still be retained without leaking into the atmosphere and reacting. This double walled system has proven effective on multiple occasions--for instance, the Experimental Breeder Reactor-II (EBR-II) reactor system did not have a single unwanted sodium exposure due to pipe failure during its lifetime (Grabaskas et al., 2015).
Inert atmospheres are maintained above the sodium pool in pool type SFRs through the use of a cover gas to reduce the likelihood of chemical interactions inside the reactor vessel. This means the piping and valves should have a gas tight barrier. Inert gases used could be nitrogen, helium, argon, or another gas depending on the design, though argon is often the preferred cover gas of choice for SFR systems.
Valves serve several purposes inside the primary and secondary sodium coolant loops. Isolation valves allow operators to isolate certain loops for maintenance or other reasons while still allowing the operation of other loops to continue. Anti-flow-reversal valves permit the flow of sodium in only one direction which permits loops to still operate if other loops lose pumping power. Flow control valves help regulate sodium flow along with pumps to optimize heat removal and dissipation either in a shutdown situation or other scenarios, such as for research purposes. An example sodium loop system with valve placement can be seen in Figure 10 (Acton et al., 1985).
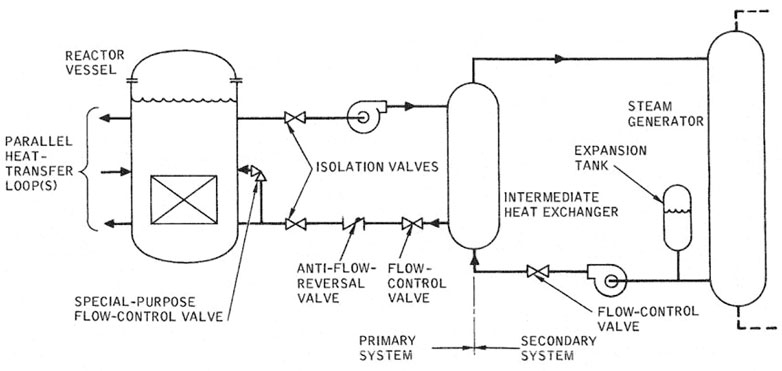
FIGURE 10. Valve placement in a typical heat transport system (Acton et al., 1985).
Sodium leak detection and containment
Sodium-to-atmosphere leaks can occur due to a positive pressure differential between sodium and the surrounding gaseous environment. The escaping sodium can react with the environment, producing numerous by-products including aerosols or vapors. In some reactions, hydrogen gas can be released. In addition, sodium can react exothermically, possibly producing heat, smoke, or fire. Containing the sodium within its respective working area is of the upmost importance because of its reactivity potential with air and water. Leak detection in all areas of sodium systems is important, not just in valves and piping. Here is a description of some of the designs and prototypes of leak detection systems for SFRs.
1) The Sodium Advanced Fast Reactor (SAFR) was designed to be an alternative to the PRISM reactor, with inherent passive safety features and scalable electric capacity (King, 1991). All components within the reactor that contain sodium have multiple insulation layers. The first is a gas annular space of about a 1-inch thickness, which encloses electric heaters that will preheat the sodium and also allows a special atmosphere that will be sampled to detect any sodium leakage. The second layer of insulation is physical insulation (fiberglass or similar) that has an inner stainless-steel sheath that can withstand a jet impingement should a moderate energy fluid system leak occur. Piping will also be present inside the annular gas gap that will allow sodium leaks to drain through gravity and collect in the leak collection header. The collection header will drain the sodium to a drainage vault. This system of sodium detection and draining can be seen in Figure 11.
2) Sodium ionization detectors (SIDs) monitor for sodium aerosol/vapor leaks from the primary and intermediate heat transport systems to the surrounding atmosphere. The SID is activated by passing a gas sample through an ionization chamber operating via a hot filament technique, which ionizes sodium and sodium species, generating a recordable signal. The electrical signal is proportional to the concentration of sodium vapor/aerosol in the gas passing through the SID chamber at any given time, though it is an instantaneous (not cumulative) detection.
3) Liquid sodium leaks can be detected through cable or contact detectors. Both detector types consist of a thin, stainless steel-sheathed, mineral-insulated (MgO) coaxial cable. Cable detectors incorporate perforations in the outer (grounded) sheath (Figure 12). Liquid sodium that penetrates the perforated sheath causes a low resistance path to ground, which then produces an increased voltage drop and activates an alarm. The response to liquid sodium is indicated on a strip recorder and data logger. Contact detectors are joined as an exposed junction within a bonnet at its end (Figure 13). Liquid sodium flowing into the gap provides an electrical short circuit between the exposed junction and the stainless-steel sheath (Doctor, 1977).
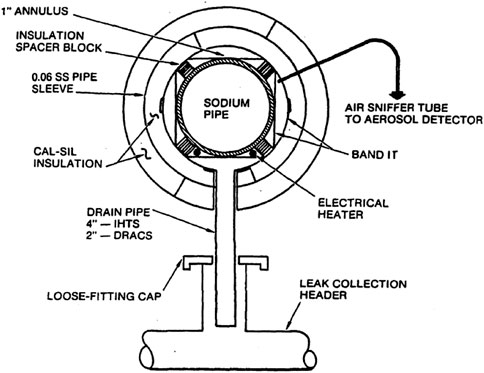
FIGURE 11. Annular channel sniffer (King, 1991).
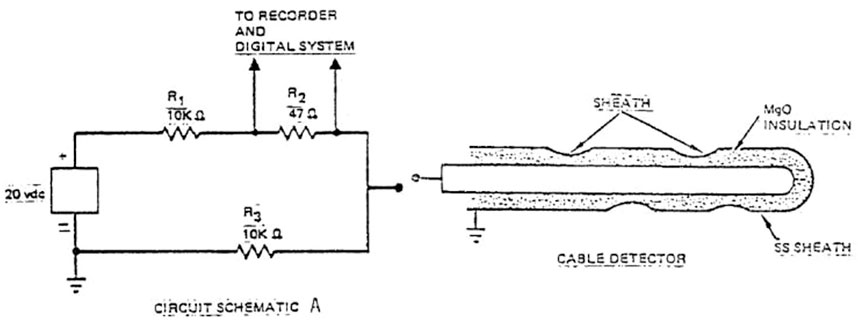
FIGURE 12. Cable detector (Doctor, 1977).
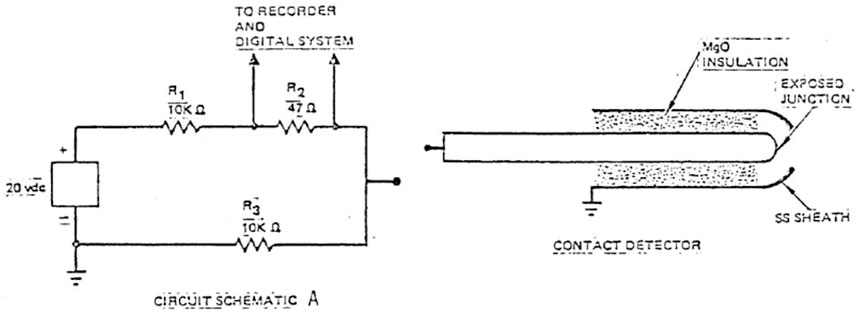
FIGURE 13. Contact detector (Doctor, 1977).
Existing sodium testing facilities
A few select recent advances in working with sodium can be summarized by considering the technologies developed for SFRs in the United States and internationally. Per the International Atomic Energy Agency (IAEA), there are less than ten facilities in the United States that can accommodate testing of materials that support SFR systems; of those, only four identify the use of sodium specifically as the working fluid for cooling systems (International Atomic Energy Agency, 2022). Of these four facilities, three are operated by Argonne National Laboratory (ALEX, METL, SNaKE), with the fourth facility being operated on the campus of the University of Wisconsin-Madison (Figure 14).
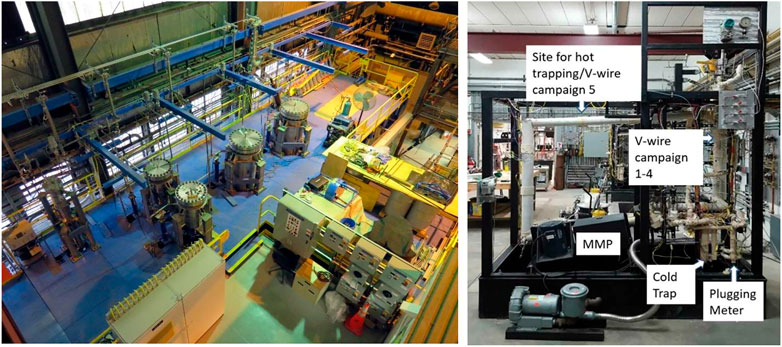
FIGURE 14. Sodium test facilities at Argonne National Laboratory (Argonne National Laboratory) (left) and University of Wisconsin-Madison (Farmer et al., 2022) (right).
The French Alternative Energies and Atomic Energy Commission (CEA) (CEA) is actively involved with defense and security, low carbon energies (nuclear and renewable energies), technological research for industry, and fundamental research in the physical and life sciences. As pioneers of the French Sodium School (Rodriguez et al., 2009; Latgé, 2018), CEA provides contributions on SFR technologies via training courses to provide experience for SFR operators, design engineers, and fire brigades. Their approach to training regarding sodium coolant consists of lectures, discussions, and training on a sodium loop (Figure 15), and includes topics on physical and chemical properties of sodium coolant, purification, corrosion, contamination, cleaning and decontamination, sodium technology, description and operation of components, instrumentation, visualization, inspection, and repair. Regarding sodium safety, the specific hazards induced by the chemical properties of sodium are described as sodium-water reaction and hydrogen risk assessment, sodium fires, safety rules, prevention, intervention, and exercise on a real sodium fire. In support of the processes used for decommissioning SFRs, lecturers present and address the following items: specific risks, dismantling techniques, sodium treatment, sodium waste storage, and decommissioning of Na-K facilities (Latgé, 2018).
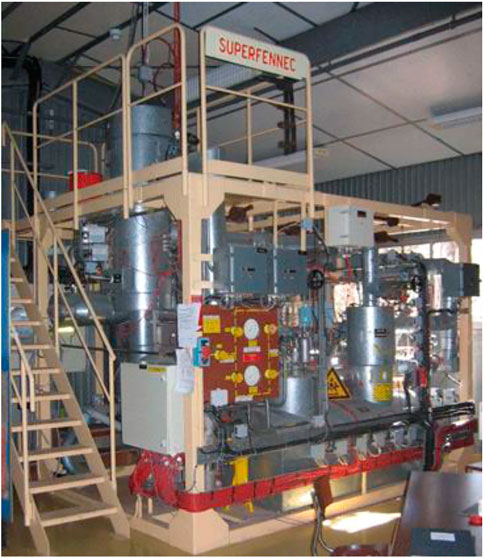
FIGURE 15. CEA sodium training loop (CEA).
Creative Engineers Inc. (CEI) is a company with an emphasis on working with alkali metals and have facilities located in New Freedom, PA and Greenville, SC (Creative Engineers, 2020). Services provided by CEI include designing, building, and operating research projects to meet customers’ needs, while working on equipment such as electromagnetic pumps, electromagnetic flow meters, high temperature pressure transmitters, pump, and flow meter testing. CEI provides certified training courses in the use of alkali metals, which offer a mix of classroom and hands-on training and demonstrations. Typical classroom work includes properties and hazards of alkali metals, fire, spill, emergency response, buildings, equipment, systems, storage, and transportation. Hands-on work includes demonstration of a sodium-water reaction, proper extinguishing technique, and small spill cleanup. This course is tailored for engineers, managers, safety professionals, operators, and fabricators who design or operate systems that contain or use alkali metals.
Recent achievements
At one point in recent history, the United States was an international leader in R&D efforts related to SFRs. However, that expertise has significantly eroded since the 1990s, when the most relevant SFR-related research programs in the United States were scuttled. To regain a foothold in the market of SFR expertise, efforts must be made by United States entities to not only retain the institutional knowledge, that is, held by the remnants of the previous SFR working generation, but to also properly disseminate that knowledge onto the next-generation of SFR workers.
A thorough understanding of sodium properties is needed by all personnel involved in the design, construction, operation, and experiment planning and execution for sodium-cooled systems. Faculty at Idaho State University have developed a base set of handling activities and basic tasks, along with remedial knowledge of safety precautions, related to handling sodium. The goal of this concentrated program was demonstrating the ability to perform tests that would accelerate program development for entities (e.g., VTR) and providing expected follow-on and support facilities for industrial efforts towards SFR deployment (e.g., Natrium, Oklo).
The objectives put forth for the development of a safety culture driven towards working with sodium, as part of a directive towards the VTR project, can be summarized by the following activities:
1) Complete a comprehensive study of sodium properties, uses, hazards, and additional pertinent data
2) Translate the lessons learned from historical campaigns that utilized sodium into hands-on training for current and next-generation sodium systems.
3) Expand upon hands-on training to incorporate safety training and operational training, including activities relevant to sodium reactor systems
Handbook development
The first objective involved the efforts of several students in acquiring the necessary data and information from relevant vetted sources, including interviews with persons with explicit experience with handling sodium for legacy projects, such as Experimental Breeder Reactor-II (EBR-II) and the Fast Flux Test Facility (FFTF). Extensive discussions were also held with leading experts in the development of advanced sodium-cooled reactors, both in the United States (TerraPower, Creative Engineers, Inc.) and internationally (French Alternative Energies and Atomic Energy Commissions, or CEA).
The result of this effort is a 240-page comprehensive summary of information related to uses of sodium in the nuclear industry (Idaho State University, 2021). With an intended audience ranging from scientists to contractors to engineers, this handbook provides information for VTR stakeholders to acquire fundamental sodium knowledge along with discussion of its applications, historical information, and industrial uses. During the development of this handbook, the team began to assemble a set of rudimentary experiments that could be performed to demonstrate the utility, and hazards, of working with sodium metal and, in particular, molten sodium. This collection of tests was noted as the basis for a hands-on curriculum to be developed and vetted at ISU.
Curriculum and workforce development
As part of the effort to champion this resurgent technology, ISU is developing an educational curriculum, that is, suited specifically to addressing the scientific and technological challenges involved with sodium-cooled reactor systems. The process of learning would not rely solely on classroom, but also by exercises performed in the laboratory, where students would gain hands-on expertise in the use of SFR-relative technology, including radioactive materials and molten sodium. The mission of this proposed sodium technology development program includes:
1) Development of educational capabilities in the United Stated for SFR-related research efforts
2) Utilization of classroom and hands-on learning experience to develop and maintain working expertise in the use of molten sodium as a nuclear reactor coolant
3) Creation of a vibrant pathway for the transfer of prior institutional knowledge of sodium experiments (from personnel and documentation) from local, regional, and international experts in the SFR community
The potential implications of a renewed workforce with relevant expertise in handling and performing experiments using molten sodium are numerous, including:
1) Accelerated characterization and qualification of new materials.
2) Testing and demonstration of new sensors and detectors for use in relevant environments.
3) Rapid material compatibility surveys.
4) Develop new insights and understanding of material behavior at the macrostructural and microstructural levels.
5) Verification and validation of modeling and simulation tools and methodologies.
Path forward
A series of preliminary experiments were recently executed by ISU that leveraged existing glovebox capabilities at the Center for Advanced Energy Studies (CAES), such as the use of small laboratory furnaces to heat up an inventory of metallic sodium to prototypical operating temperatures, and an inert gas-filled glovebox to handle such reactive metals (LaBrier et al., 2020). These tests included instrument survivability, evaluation of material performance, and post-experiment examination. In addition, a small molten sodium recirculation loop system is currently designed to perform more prototypical experiments that investigate performance under flowing coolant conditions. Two ISU graduate students led a project (LaBrier et al., 2022) that focused on the interaction of molten sodium with standard insulation types, as described in a recent United States NRC report detailing the hazards associated with advanced non-light-water reactor operational experience (U.S. Nuclear Regulatory Commission, 2019). Additional experimental efforts are underway at the ISU campus.
Author contributions
DL, CP, and WM collaborated on developing the project from its inception. WM led the overall effort, with CP leading the effort at ISU. DL led the effort for workforce development. CP provided invaluable information based on career experiences. DL organized the topics provided in this document, with guidance and input from CP and WM.
Funding
The College of Science and Engineering at ISU has graciously procured a separate inert glovebox system that has been installed at the main campus of ISU for the next phase of the curriculum and workforce development. The funds utilized for this purchase are discretionary funds provided by ISU, and were awarded independent to the VTR grant awarded to OSU and ISU. The summary provided here was funded in part by a second-round VTR award through the United States DOE.
Acknowledgments
Much of the effort to assemble the content presented here was performed by students at Idaho State University, especially Jordan Harley, Tracy Kerbs, and Morgan Robbins, and we thank them for their efforts. We also thank the staff at the CAES facility for their cooperation and guidance in developing these experiential activities.
Conflict of interest
The authors declare that the research was conducted in the absence of any commercial or financial relationships that could be construed as a potential conflict of interest.
Publisher’s note
All claims expressed in this article are solely those of the authors and do not necessarily represent those of their affiliated organizations, or those of the publisher, the editors and the reviewers. Any product that may be evaluated in this article, or claim that may be made by its manufacturer, is not guaranteed or endorsed by the publisher.
References
Acton, R. U., Weatherbee, R. L., Smith, L. A., Mastin, F. L., and Nowotny, K. E. (1985). Sandia sodium purification loop (SNAPL) description and operations manual. Albuquerque, NM, USA: Sandia National Laboratory.
Advanced reactor concepts, "ARC-100 smr," https://www.arc-cleantech.com/technology (2023).
Argonne National Laboratory, . The Mechanisms Engineering Test Loop (METL), 2018, https://www.anl.gov/nse/mechanisms-engineering-test-loop-facility.
Cea, , "De la recherche à l'industrie,"http://www.cea.fr/.2023.
Creative engineers, "Creative Engineers," 2020. https://creativeengineers.com/.
Doctor, C. J. M. A. S. R. (1977). An evaluation of liquid metal leak detection methods for the clinch river breeder reactor plant. Rockville, ML, USA: U.S. Nuclear Regulatory.
Emoscopes, , LMFBR schematics, 2006. https://en.wikipedia.org/wiki/File:LMFBR_schematics.png.
Farmer, M., Weathered, M., Lisowski, D., Bremer, N., Kilsdonk, D., Stack, T., et al. (2022). Development of a sodium fast reactor cartridge loop testing capability for the versatile test reactor. Nucl. Technol. 196, 148–164. doi:10.1080/00295639.2022.2052552
Foust, O. J. (1978). “Sodium--NaK engineering handbook,” in Sodium pumps, valves, piping, and auxiliary equipment (U.S. DOE), Washington, DC, USA,4.
Gen IV international Forum, , Sodium-Cooled Fast Reactor (SFR), 2013, https://www.gen-4.org/gif/jcms/c_42152/sodium-cooled-fast-reactor-sfr.
Grabaskas, D., and Brunett, A., (2015). Regulatory technology development plan. Lemont, IL, USA: Argonne National Laboratory.
Rodriguez, G., "The French sodium School: Teaching sodium technology for the present and future generations of SFR users," Proceedings of the International Conference on Fast reactors and Related Fuel Cycles: Challenges and Opportunities, 7–11. December 2009, Kyoto, Japan.
Hanna, S. R., Briggs, G. A., and Hosker, J. R. P. (1982). Handbook on atmospheric diffusion. Fort Belvoir, VR, USA: Technical Information Center.
Idaho State University, (2021). Sodium coolant properties, experience, and safety culture. Pocatello, USA: Idaho State University.
International Atomic Energy Agency, (2022). Database for liquid metal cooled fast neutron systems. https://nucleus.iaea.org/sites/lmfns/Pages/Home.aspx.
King, R. (1991). Preapplication safety evaluation report for the sodium advanced fast reactor (SAFR) liquid-metal reactor. U.S. Nuclear Regulatory Commission. Rockville, ML, USA,
Knolls Atomic Power Laboratory, Chart of the nuclides. 17. Knolls Atomic Power Laboratory, Ballston Spa, NY, USA,
LaBrier, D., Harley, J., and Robbins, M. Sodium-insulation paper. ASME, Nuclear Engineering and Radiation Science. Little Falls, NJ, USA.
LaBrier, D., Pope, C., and Marcum, W. (2020). Revitalization of sodium-cooled fast reactor competence through the development of a U.S.-Based sodium technology School. Transactions of the American Nuclear Society. American Nuclear Society, La Grange Park, Illinous.
Lennitech, (2020). Water treatment solutions. https://www.lenntech.com/periodic/elements/na.htm#.
Malet, J. Ignition and combustion of sodium-fire consequences-extinguishment and prevention. St-Paul-Lez-Durance Cedex: Institut de Protection et de Surete Nucleaire. Middle East, Iran.
Marcum, W., and Pope, C., (2019). Accelerating the experimental mission of VTR through an ex-pile operational program. U.S. DOE Award, VTR Program, Argonne, ,
Nuclear Power Online, Nuclear power - thermal conductivity of sodium. https://www.nuclear-power.net/nuclear-engineering/heat-transfer/thermal-conduction/thermal-conductivity/thermal-conductivity-of-sodium/(2020).
Office of Nuclear Reactor Regulation, , Preapplication safety evaluation report for the power reactor innovative small module (PRISM) Liquid-metal Reactor, Malden, Massachusetts. 1994.Malden Public Library.
Shu, B. NuDat 2.8. NNDC. https://www.nndc.bnl.gov/nudat2/getdecayscheme.jsp?nucleus=24MG&dsid=24na2020
Takashi Takata, A. Y. (2003). Numerical thermal-hydraulics study on sodium-water reaction. Ibaraki, Japan: Japan Nuclear Cycle Development Institute.
TerraPower, L. L. C. Demonstrating the Natrium™ reactor and integrated energy system. 2023 https://www.terrapower.com/wp-content/uploads/2022/03/TP_2022_Natrium_Technology.pdf.
United States Department of Energy, edms.energy.gov. https://edms.energy.gov/pac/TeelDocs, 2020.
U.S. Nuclear Regulatory Commission, (2019). Rockville, ML, USA.Advanced non-light water reactors materials and operational experience,U.S. Nuclear Regulatory Commission.
U.S.NRC, Nuclear regulatory commission. Aurora - Oklo. 2023 . Idaho National Laboratory, Pocatello, USA,
Keywords: sodium, experiential, safety, workforce, practical, VTR
Citation: LaBrier D, Pope C and Marcum W (2023) On developing a practical safety culture for the advanced reactor workforce: Experiences of working with sodium. Front. Nucl. Eng. 2:1162751. doi: 10.3389/fnuen.2023.1162751
Received: 09 February 2023; Accepted: 08 March 2023;
Published: 17 March 2023.
Edited by:
Khaled Talaat, University of New Mexico, United StatesReviewed by:
Shuprio Ghosh, Los Alamos National Laboratory (DOE), United StatesMd Mehadi Hassan, Los Alamos National Laboratory (DOE), United States
Copyright © 2023 LaBrier, Pope and Marcum. This is an open-access article distributed under the terms of the Creative Commons Attribution License (CC BY). The use, distribution or reproduction in other forums is permitted, provided the original author(s) and the copyright owner(s) are credited and that the original publication in this journal is cited, in accordance with accepted academic practice. No use, distribution or reproduction is permitted which does not comply with these terms.
*Correspondence: Daniel LaBrier, bGFicmRhbmlAaXN1LmVkdQ==