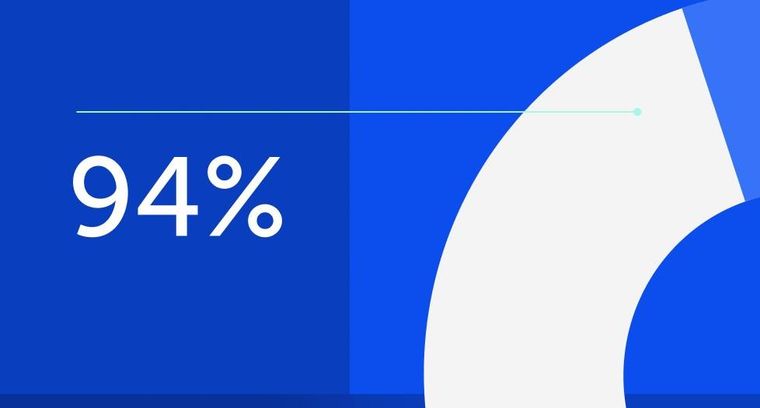
94% of researchers rate our articles as excellent or good
Learn more about the work of our research integrity team to safeguard the quality of each article we publish.
Find out more
ORIGINAL RESEARCH article
Front. Nucl. Eng., 03 February 2023
Sec. Nuclear Materials
Volume 2 - 2023 | https://doi.org/10.3389/fnuen.2023.1123134
This article is part of the Research TopicAdvancements in Nuclear and Irradiation ExperimentsView all 6 articles
The nuclear security community has long been interested in the identification and quantification of nuclear material signatures to understand a material’s provenance, use, and ultimate application. New forensics signatures and methods intended for non-traditional or advanced nuclear fuel applications require fuel irradiation experiments to demonstrate viability and validity. Integral fuel irradiations have historically required significant costs and long timelines to design, irradiate, and characterize. This paper describes how a recently developed nuclear fuel irradiation testbed can be used to provide a low cost, rapid turnaround, modular test environment for irradiation and evaluation of nuclear fuel specimens for nuclear security applications. The irradiation testbed houses six small ‘MiniFuel’ samples within hermetically sealed capsules inside targets that can be removed in between each ∼25-day operating cycle of the High Flux Isotope Reactor (HFIR). As many as nine targets can be irradiated using a single irradiation position (reflector region) in HFIR, allowing for varying irradiation temperatures and burnups. A suite of hot cell capabilities have been established to perform post-irradiation examination for measuring performance (e.g., fuel swelling, fission gas release) and facilitating experiment disassembly for subsequent property measurements, microstructural analysis, or chemical assay. This new testbed allows fuel irradiations to be conducted on an accelerated timeframe to enable rapid proof of concept testing and to provide reference material for nuclear fuel security applications. Recent applications using this testbed include the testing of isotopic taggants in UO2 fuel (intentional forensics), testing of U-10Mo fuel for down-conversion of highly enriched uranium–fueled reactors, and the production of irradiated UO2 fuel material for signature analysis of its isotopic composition (plutonium, fission gases, etc.).
The development of next-generation reactors, advanced fuel forms, and the associated expansion of the nuclear fuel cycle poses new challenges for the nonproliferation and safeguards communities. To stay relevant with advancing technology, the nonproliferation and safeguards communities need a rapid testing capability to test advanced fuel forms and to identify the forensics signatures associated with each new fuel type and cycle. Forensic signatures from advanced fuel forms can help the international community identify the provenance, type, use, and ultimate application of the nuclear fuel for treaty verification and for material found outside of institutional control Hutcheon et al. (2015). Evaluation of new forensic signatures and methods for non-traditional fuel forms requires the ability to fabricate fuel samples, generate fission products through neutron irradiation, and test for forensic signatures during all steps of the fuel cycle. Furthermore, the conversion of highly enriched uranium (HEU)–fueled reactors to low-enriched uranium (LEU)–fueled reactors requires new fuel types to increase the uranium density, which requires extensive testing to ensure that the fuel elements provide similar reactor performance while remaining safe during operation Mayer et al. (2011); Hutcheon et al. (2015).
The increased interest in proliferation-resistant research reactor fuels and forensics techniques to support novel commercial reactor fuels and fuel cycle technologies will require significant experimental evaluations—spanning fuel design, analysis, enrichment, synthesis, fabrication, irradiation testing, post-irradiation examination (PIE), and reprocessing. Perhaps the most challenging part of evaluating new fuels and forensic techniques for the nuclear fuel cycle is performing irradiation testing and PIE: very few facilities worldwide can handle, analyze, and characterize irradiated nuclear fuel. This work describes an experimental testbed that has been developed at Oak Ridge National Laboratory (ORNL) to provide low-cost, accelerated life testing of a wide range of fuel forms with a specific focus on evaluating fuel performance and forensic signatures for nonproliferation and safeguards applications. The ORNL nuclear fuel testbed spans fuel fabrication, irradiation, post-irradiation activities, and reprocessing. The testbed mimics the industrial processes of the nuclear fuel cycle while remaining at a small scale so that rapid and agile changes can be made to address project and stakeholder requirements.
A nuclear fuel fabrication laboratory is set up to batch different uranium fuel concepts (metal, ceramic, tristructural isotropic [TRISO], etc.) with the ability to alter different manufacturing conditions (powder preparation, pressing, sintering, etc.). Characterization of the fuel forms occur at each step of the fuel fabrication process with a wide variety of instruments. Bulk fuel forms produced in the lab, or provided by collaborators, are machined into miniature fuel samples that are compatible with the MiniFuel irradiation vehicle Petrie et al. (2019) in the High Flux Isotope Reactor (HFIR) at ORNL. As discussed in more detail in the following section, the small fuel volume reduces the sensitivity of the irradiation design to changes in fuel composition, enrichment, burnup, and geometry, allowing for a modular, flexible irradiation vehicle to enable high-throughput isothermal fuel testing without significant design efforts for each fuel variant. This enables rapid, cost-effective evaluation of a large fuel test matrix spanning different fuel forms, irradiation temperatures, burnups, and potentially other variables such as the fluid or medium surrounding the fuel during irradiation. Finally, hot cells and radiochemical labs enable PIE to measure fission gas release, dimensional and microstructure changes of the fuel, and to evaluate new forensics or separations techniques for reprocessing, safegaurds, or other applications. Specific analytical capabilities include gamma and alpha spectroscopy, mass spectrometry, acid/base titration, and in situ spectrophotometry. This manuscript provides an overview of the irradiation vehicle and capabilities and of the larger fuel testbed, including how it can be used to drive new innovations in ongoing and future nuclear nonproliferation and nuclear forensics research.
Recently, the MiniFuel concept has been applied to nuclear nonproliferation research in the form of U-10Mo (uranium–molybdenum metal fuel with 10% molybdenum composition) fuel and forensically tagged UO2 fuel. Investigation into the performances of both fuel forms under different reactor environments is being conducted using this testbed. This section briefly describes the methods and materials involved in conducting a MiniFuel experiment, including fuel fabrication, irradiation, PIE, and chemical separation.
The MiniFuel concept was developed at ORNL to provide a low-cost, accelerated life testing platform for advanced fuel types Petrie et al. (2019); Terrani et al. (2020b); Terrani et al. (2020a); Harp et al. (2021). For example, some reactor designs may not tolerate more than negligible swelling or fission gas release. If, for example, the fuel is intended for service in a typical commercial pressurized water reactor, an irradiation time of over 5 years in a prototypical irradiation environment would be needed to approach the required burnup. Conversely, a MiniFuel irradiation of less than one calendar year could reveal problematic behaviors.
The use of accelerated life irradiations as a means to rapidly screen nuclear fuel concepts is not new. The early decades of the nuclear industry relied heavily on the use of accelerated irradiation of fuel forms to rapidly screen uranium and plutonium alloys for problematic behaviors or new material evolutions Whitney et al. (1957); Trauger (1962); Roake (1963); Blake (1961a); Blake (1961b). However, their use fell out of favor in subsequent decades, as the basic behaviors and mechanisms driving fuel performance became widely accepted, and the number of fuel forms utilized in the field fell to a few variants. However, the rapid expansion of reactor types under development and novel nuclear fuels under consideration has motivated revisiting and modernizing this foundational approach to study nuclear fuel materials.
The MiniFuel irradiation vehicle (Figure 1) consists of an aluminum basket placed in a vertical experiment facility (VXF) position within HFIR’s permanent reflector and allows the reactor’s primary coolant to cool up to nine welded stainless-steel targets. Removal and position changing of the targets inside the basket assembly can be done between the HFIR operating cycles. Historically, HFIR operates for 6–8 cycles per year, each cycle lasting approximately 23–25 days. Each target contains six sealed capsules that house the fuel, for a total of 54 fueled capsules in a single reactor position. Within each capsule is a passive silicon carbide thermometry sample for verifying the irradiation temperature Field et al. (2019) as well as several other components composed of molybdenum or other materials with a high atomic number to increase gamma heating, which is used to increase experiment temperatures as the nuclear heating passes through an insulating gas gap that is established between the capsules and the target. Figure 1 shows examples of MiniFuel samples sitting in a molybdenum cup, which in these cases serves to ease pre- and post-irradiation handling of the small fuel samples and prevent chemical interactions between the fuel and the capsule.
FIGURE 1. CAD images of the MiniFuel irradiation vehicle, including the basket, target, and capsule. Reprinted from Journal of Nuclear Materials, Vol. 526, C.M. Petrie et al., “Separate effects irradiation testing of miniature fuel specimens,” Page 151783, Copyright (2019), with permission from Elsevier Petrie et al. (2019).
MiniFuel specimens are designed to be small and numerous so that a single study could encompass a substantial test matrix of sample compositions and irradiation conditions. Importantly, the MiniFuel specimens are still large enough to be produced by conventional or scaled-down processing methods that are representative of their full-scale analogs. The small footprint of the MiniFuel specimens (
A second primary benefit of the MiniFuel design is the isothermal condition that is possible due to the small volume of the fuel. By contrast, fuel temperatures during integral fuel tests are driven entirely by the fuel enrichment and the evolution of the fission heating and thermal properties of the fuel with increasing burnup. Temperature variations in operating LWR fuels (∼8–10 mm diameter pellets) can exceed 1000 K between the centerline and pellet surface. The structure, chemistry, and properties of fuel evolve during irradiation and are a strong function of the irradiation temperature. Therefore, the inherent coupling between fuel temperature and fission rate in integral test irradiations makes it difficult to deconvolute these effects and develop more fundamental fuel performance models. Conversely, the temperature of a fuel sample irradiated using the MiniFuel vehicle is largely insensitive to the fuel enrichment and fission rate. Besides the equilibrium fission heating that is eventually achieved, the small volume of the fuel means that the fuel contributes only a small percentage of the total heat within a capsule. Nuclear heating in the capsule is dominated by gamma heating in the surrounding components, which originates from the HFIR fuel Petrie et al. (2019). Because HFIR operates at a constant power (85 MW) over the entire cycle, the temperatures within fueled capsules remain relatively uniform to within ± ∼50 K, even with significant changes in fuel fission rate. The availability of bulk irradiated fuel samples that have been irradiated under uniform temperatures will enable elucidation of thermophysical and mechanical properties that could not otherwise be measured.
The nuclear fuel fabrication laboratories at ORNL comprise of a connected series of gloveboxes that enable researchers to blend, mill, sinter, and press unique and advanced fuel forms. Ceramic MiniFuel pellets are produced by conventional ceramic processing: milling starting powders, pressing green pellets in dies, sintering the green pellets into fully dense ceramic pellets, and then using metallographic polishing to obtain final dimensions and surface finish. Metal MiniFuel disks have also been made by punching disks from a metal sheet and polishing the disks to final dimensions and surface finish, or by using a low-speed saw to section disks to length from castings of appropriate diameter. Even MiniFuel TRISO compacts have been produced using laboratory-scale processing that is conventional in TRISO research and development: chemical vapor deposition to produce full-sized TRISO particles from sol-gel–derived U-bearing kernels, overcoating TRISO particles with a standard matrix of graphite and pitch, pressing overcoated TRISO particles (∼20 particles each) into miniature green compacts in a heated die, and heat-treating the green compacts to make MiniFuel compacts. Uranium nitride (UN) and uranium carbide (UC) TRISO particle MiniFuel has also been manufactured in our laboratories, using fluidized bed chemical vapor deposition (FBCVD) Terrani et al. (2020b). Images of various MiniFuel compacts can be seen in Figure 2. The ability to fabricate a wide range of fuel forms allows for rapid testing and prototyping of new and advanced fuel forms to identify any performance issues and, concurrently, research signatures for nuclear forensics and safeguards applications.
FIGURE 2. (Top) Photograph of a sintered UO2 MiniFuel compact (A) and a monolithic UO2 disk (B). (Bottom) Image of the cross section of a single TRISO fuel particle (C), radiograph image of TRISO particles in a compact (D), and an image of a compact with TRISO particles imbedded in it (E).
Thermal and neutronic modeling of the MiniFuel specimens under test in HFIR is a routine procedure for a fuel experiment in HFIR and consists of a suite of codes. Neutronic calculations are performed to determine heat generation rates (HGRs) in the fuel and target structures, the fuel burnup, and the transmutation of different elements and isotopes in the fuel. The neutronic calculations are performed using a modified version of the Monte Carlo N-Particle, Version 5 (MCNP5) neutronics code Mosher and Wilson (2018), the SCALE software package Wieselquist et al. (2020), and the ADVANTG Mosher et al. (2013) variance reduction tool. The three codes are integrated using a wrapper code called HFIRCON Daily et al. (2020). The geometry and composition of a MiniFuel experiment is coded into an MCNP file, and the HFIRCON tool proceeds to calculate the neutron and gamma heating, fission rate, fuel burnup, and transmutation as a function of irradiation time in HFIR Xoubi and Primm (2005). A visualization of an MCNP model of a MiniFuel experiment, placed in the VXF 11 irradiation location in HFIR, can be seen in Figure 3. The MCNP results in Figure 3 and for the models in the following sections, were all simulated to a statistical uncertainty of less than 5 percent. The heating rates from the neutronics model are used as inputs into the thermal modeling of the fuel under testing using the multiphysics finite element analysis (FEA) code ANSYS (version 19.2). ANSYS calculates the expected temperature of the fuel during irradiation and is compared to the temperature recorded by the silicon carbide thermometry during PIE.
FIGURE 3. (Top) MCNP model of the HFIR reactor (A) with a close up on the MiniFuel basket in VXF location 11 (B). (Bottom) Cross section of MCNP Model of the MiniFuel basket (C) along with the modeled neutron flux incident on each capsule (D).
MiniFuel targets are shipped to the ORNL Irradiated Fuels Examination Laboratory (IFEL) for disassembly and PIE Raftery et al. (2018); Harp et al. (2021). The priority PIE is determined by the objectives of the experiment; this could be swelling, fission gas release, or evaluation of microstructural evolution under burnup in the case of more conventional fuel irradiations Doyle et al. (2023), or other measurements as dictated by the goals of forensics, nonproliferation, or other nuclear security projects. Examples of the latter category of experiment are given in the following section.
First, the six individually sealed capsules are extracted after cutting the ends of the target with a low-speed diamond saw. The capsules are punctured under vacuum using a specially designed apparatus, and the released gases are swept into cold traps for gamma counting of the frozen Kr-85 content Raftery et al. (2018). After puncturing, capsules are disassembled by cutting the endcaps with a slow-speed diamond saw, allowing retrieval of the silicon carbide thermometry and fuel specimens. The fuel is then transferred to separate facilities for more detailed measurements of isotopics, composition, dimensional changes, x-ray tomography Richardson et al. (2019), or thermomechanical properties. In addition to these basic thermophysical and mechanical properties, optical and electron microscopy are used for microstructural characterization. The absence of large temperature gradients in the samples limits the effects of thermomigration, so fission product phase and fission gas bubble behavior can be studied at a fundamental level. At this small scale, further destructive examinations also are employed as dictated by the aims of the experiment. A typical example is using mass spectrometry to identify fission products and trace elements, thus calculating burnup in the fuel Harp et al. (2014). Other more specialized small-scale characterization methods such as micromechanical property measurement or thermal transport behaviors can be applied to the MiniFuel disks, such as laser flash analysis to measure thermal diffusivity Abdul-Jabbar et al. (2019) or ball-on-ring transverse rupture strength testing to understand fracture strength Lupercio et al. (2021).
IFEL is primarily used for evaluating fuel performance. For nuclear security applications that are more focused on radiochemistry, other ORNL facilities such as the Radiochemical Engineering Development Center (REDC) can be used to perform laboratory- and industrial-scale radiochemical separations to support nuclear fuel reprocessing operations. REDC is one of the only facilities in the United States that can handle industrial-scale quantities of material and routinely performs large-scale separations, including ion exchange chromatography and solvent extraction. An example mixer–settler bank used for liquid–liquid solvent extraction at REDC is shown in Figure 4. These operations can be easily scaled to accommodate small-scale operations for MiniFuel applications. Targets can be handled in various hot cell facilities following neutron irradiation, similar to what has been done at IFEL. After removing samples from the capsule, they can be dissolved and prepared for chemical separations like the Plutonium Uranium Recovery by Extraction (PUREX) process Benedict et al. (1981). Fission product decontamination factors (DF) with respect to uranium and plutonium in irradiated fuels for each element can be quantified throughout various PUREX stages. DF values describe how effectively a contaminant is removed from a product. This information can provide indications of material origins Mendoza et al. (2016). Chemical separations and trace impurity analyses are supported by radioanalytical laboratories at REDC and other facilities at ORNL. Advanced techniques such as laser ablation inductively coupled plasma time-of-flight mass spectrometry (LA-ICP-TOF-MS), automated separations by ion exchange chromatography, and ICP–optical emission spectroscopy/MS methods are well established for effectively quantifying trace impurities in uranium materials Manard et al. (2021). Additionally, recent work on the development of advanced optical spectroscopy monitoring tools could be leveraged to enable rapid in-line feedback during separations to optimize throughput. Sadergaski and Andrews (2022).
This section presents example nuclear nonproliferation and forensics applications of the testbed facilities described in the previous section. Two specific examples of ongoing nuclear security and nonproliferation projects at ORNL are discussed herein: the intentional forensics project investigating the use of ‘intentional taggants’ for material identification purposes and the irradiated UO2 material production for investigating the signatures of various isotopes that are produced in fuel as a function of enrichment and irradiation time. The testing of U-10Mo fuel for down-conversion of highly enriched reactors is also underway using this testbed but was omitted from this manuscript, see Doyle et al. (2023) for more information on that work.
Intentional forensics is the concept of creating unique forensics signatures in nuclear fuel materials. Research in this area has primarily pursued trace additives that are distinct elementally or isotopically from natural trace elements of the fuel. Perturbed isotopics allow use of elements that may be present in the fuel while still creating an “isotopic barcode” Kristo et al. (2007); Lamont et al. (2006). This isotopic barcode could provide information on the provenance of the material if recovered outside of regulatory control. An ideal additive, or “taggant,” would have many of the following features: (1) can be incorporated into nuclear fuel, (2) has a low neutron absorption cross section, (3) the physical properties and the microstructure of the fuel are affected negligibly (melting temperature, porosity, density, etc.), (4) provides multiple isotopes for different barcode permutations, (5) is detectable using standard nuclear forensics methods, including mass spectrometry, and (6) is distinct pre- and post-irradiation and follows the plutonium stream during reprocessing. A successful forensics taggant would not need to possess the final criteria, but it should at least possess the first five. The candidate elements that have been initially identified for oxide fuels are titanium, iron, nickel, chromium, tungsten, molybdenum, cerium, and zinc. Taggant-doped oxide fuel is currently being produced and analyzed at ORNL. First, the ability to incorporate each element into sintered UO2 fuel is being evaluated. Next, the effects of the taggant on the pre-irradiation fuel properties and microstructure are being characterized. Finally, the taggant signatures are being assessed before and after neutron irradiation, including within the plutonium stream during PUREX.
A total of 18 taggant-doped MiniFuel samples (natural enrichment) are being prepared for insertion into HFIR by the end of 2022 with the goal of irradiating fuel samples for six cycles (approximately 150 effective full power days of irradiation) to achieve a burnup similar to that of dicharged PWR fuel (∼40 MWd/kg U). Table 1 summarizes the test matrix, including the taggants, concentrations, and target fuel burnups. Previous irradiations using non-tagged UO2 MiniFuel will be used as control samples for determining the changes in the properties of the tagged MiniFuel samples. Testing of the thermophysical properties of the fuel after irradiation is planned for 2024 and includes the following: analysis of fuel swelling and dimensional changes, thermal conductivity, identification of the isotopic barcode, and analysis of taggant retention in the plutonium stream after reprocessing the MiniFuel samples using the PUREX process.
The α and β designations in Table 1 represent different enriched isotope ratios of the taggants that will be incorporated into the fuel at a 1:5 ratio with the natural element. For nickel, the Ni(α) designation corresponds to a 50:50 ratio of Ni-60 to Ni-61, whereas Ni(β) is a 50/50 ratio of Ni-60 to Ni-62. Similarly, Mo(α) is a 50/50 enriched isotope ratio of Mo-94 to Mo-100, and Mo(β) is a 50/50 enriched isotope ratio of Mo-92 to Mo-97. For the tungsten taggants, W(α) is a 25:75 ratio between W-184 and W-186, whereas W(β) is a 75:25 ratio between W-184 and W-187. Three different fuel burnups were selected for the fuel samples ranging from as low as 20–25 MWd/kgU (three HFIR cycles) to as high as 40–45 MWd/kgU (six HFIR cycles). This test matrix enables the separation of the different effects of burnup, taggant type, and taggant concentration on the microstructure of the tagged fuel samples, as well as study the effects of fission product accumulation and transmutation with taggants and enriched isotopic ratios.
The taggant concentrations were fixed at 100 ppm for most samples, but six of the samples were doped at 1,000 ppm to evaluate the effect of varying taggant concentration on the irradiated fuel’s microstructure. This level of taggant is typical of the commercial nuclear industry Arborelius et al. (2006). Altering the composition of UO2 light-water reactor fuel is common practice to improve sintering, homogenize microstructure, and achieve superior fuel performance Cooper et al. (2018, 2021). MiniFuel samples fabricated for this irradiation incorporated taggants via solid-state mixing of the taggant oxide and UO2 powder feedstock. Necessary pre-irradiation characterization includes evaluation of the microstructure and verification of the taggant isotopics in the as-fabricated state.
Some of the candidate taggant elements that were initially chosen to create isotopic barcodes happen to fall within the fission product range, which complicates the ability to track the isotopic barcode after irradiation. Ideally, the selected taggant would not be affected by fission product accumulation. For example, molybdenum and cerium each has two isotopes that do not accumulate due to fission product decay chains (see Figure 5): Mo-92 and Mo-94 as well as Ce-136 and Ce-138. The other remaining molybdenum and cerium isotopes, if used, are predicted to be washed out by fission product accumulation. The models in Figure 5 were instrumental in choosing which isotopes should be altered to create a barcode for both the molybdenum and cerium taggant fuel.
FIGURE 5. Calculated molybdenum and cerium isotope concentrations in a MiniFuel sample (initial concentration of 1000 PPM of natural molybdenum or cerium) located in the inner VXF irradiation position # 11 in the HFIR reactor (capsule position 10, radial position 2). The cyan bars represent the time HFIR is operating (six cycles).
The ability to read the signature of the taggant isotopes post-irradiation and the ability to have the taggant follow the plutonium stream during reprocessing are stretch goals for nonproliferation purposes, as the PUREX process is designed to filter out most elements. Early research into a candidate taggant that might persist through the PUREX process with the plutonium stream identified rhenium. Unfortunately, rhenium was a poor choice for the other selection criteria (poor integration capability into the fuel and high neutron absorption cross section). However, tungsten is a potential pre-irradiation taggant that conveniently transmutes into rhenium. Figure 6 shows the concentrations of tungsten and rhenium isotopes in the MiniFuel samples as a function of irradiation time in HFIR. The significant in-growth of both Re-185 and Re-187 from the stable W-184 and W-186 isotopes may allow for the isotopic barcode to be transferred from tungsten in the pre-irradiated material to rhenium post-irradiation. Current testing with the ORNL fuel testbed on these intentionally tagged fuels will hopefully provide crucial insights into this safeguards and forensic concept.
FIGURE 6. Calculated tungsten and rhenium isotope concentrations in a MiniFuel sample (initial concentration of 1000 PPM of natural W) located in the inner VXF irradiation position # 11 in the HFIR reactor (capsule position 10, radial position 2). The cyan bars represent the time HFIR is operating (6 cycles).
Plutonium production in reactors is a primary concern for the nuclear nonproliferation community. During an irradiation cycle, plutonium will build in from the transmutation of uranium from neutron capture and decay. The amount of Pu-239 produced over a given irradiation cycle, along with the production of Pu-238 and Pu-240, dictates a fuel’s proliferation resistance and material attractiveness Bathke et al. (2012). Being able to both model and experimentally test an advanced or next-generation fuel and irradiation cycle is important for identifying the proliferation resistance or susceptibility of a particular fuel or reactor type. Figure 7 shows a model of the uranium and plutonium isotope concentrations in a MiniFuel sample as a function of irradiation time in HFIR for a sample fabricated from natural UO2. The ability to preform accelerated life and burnup studies on fuel samples can help validate models of various plutonium isotope in-growth and other signatures in different fuels as a function of irradiation duration and burnup. Additionally, accumulating burnup in new and advanced fuel forms will provide valuable material to test various separations methods. For example, TRISO-based fuels, U–Mo, UN, and other fuel forms will require different reprocessing and separation conditions. The ability to test and measure signatures of these reprocessing schemes on new fuel types can help with the implementations of future safeguards.
FIGURE 7. Model of THE U and Pu isotope concentrations in a MiniFuel sample (natural UO2) located in the inner VXF irradiation position # 11 in the HFIR reactor (capsule position 10, radial position 2). The cyan bars represent the time HFIR is operating (six cycles).
The high neutron flux in HFIR allows for accelerated fission rate fuel irradiation. For fuels fabricated from natural uranium, Pu-239 fission dominates the total fission rate after only one irradiation cycle (25 days or 4 MWd/kg U). After about three cycles in HFIR (16 MWd/kg U), the Pu-239 content in a fuel fabricated using natural uranium will reach a steady state concentration. Subsequent cycles produce more of the proliferation resistant plutonium isotopes only, Pu-238 and Pu-240. Figure 8 shows the evolution of uranium and plutonium isotopes for both 5% enriched UO2 MiniFuel samples and fuel from a typical 17 × 17 Westinghouse PWR bundle (4% enriched UO2 fuel). The PWR fuel bundle model was calculated using the Triton package in SCALE Wieselquist et al. (2020) and assumed three 540 days irradiation cycles with 30 days outages. Using HFIR allows for accelerated life testing as the MiniFuel samples require only ∼5 HFIR cycles, or roughly 200 days, to achieve a similar burnup compared to the 1800 days necessary in a traditional PWR. The ability to rapidly test fuel performance to prototypic burnups and generate fuel samples for reprocessing and other radiochemical studies is the main advantage of using the MiniFuel/HFIR testbed at ORNL.
FIGURE 8. Models of the U and Pu isotope concentrations inside of a Westinghouse 17 × 17 PWR fuel bundle (enriched to 4%) and in a MiniFuel sample (5% enriched UO2) located in the inner VXF irradiation position # 11 in the HFIR reactor (capsule position 10, radial position 2). The cyan bars represent the irradiation time (as opposed to outages).
In addition to plutonium production, another signature that is important in nuclear security and nonproliferation communities is the production of various fission gas isotopes. The effluence emitted during different post-irradiation activities can provide a signature of the fuel irradiation history. In Figure 9, the various fission gas isotopes of krypton and xenon can be seen as a function of irradiation time in both naturally enriched UO2 MiniFuel in HIFR and 4% enriched UO2 fuel in a 17 × 17 Westinghouse PWR bundle. The fission gas isotopic compositions are different between the fuels due to whether the dominant fission source was uranium or plutonium. For the naturally enriched UO2 MiniFuel, plutonium fission dominates the burnup, and thus the fission product yield curve is different compared to the PWR, which is a uranium dominant fission product yield curve.
FIGURE 9. Models of the fission gas concentrations produced by a MiniFuel sample (natural UO2) located in the inner VXF irradiation position # 11 in the HFIR reactor (capsule position 10, radial position 2) and the isotopic concentrations produced by fuel from a Westinghouse 17 × 17 PWR fuel bundle (4% enriched UO2). The cyan bars represent the irradiation time (as opposed to outages).
Use of accelerated life testing obtained through the MiniFuel irradiation vehicle was initially envisioned to provide utility to nuclear fuel qualification Petrie et al. (2019). The community has recently begun re-evaluating non-prototypical neutron irradiation testing as a component of an accelerated testing and qualification paradigm Terrani et al. (2020a). Accelerated life testing provides significant utility for screening behaviors of novel nuclear fuel forms. Numerous avenues of nuclear fuel development stand to benefit from this approach, including those driven by nuclear security. The most familiar of these are long-standing reactor conversion programs. The replacement of reactor fuels using HEU with LEU variants has been successful in reducing HEU in use at research reactors through use of non-traditional fuel forms Van den Berghe and Lemoine (2014). More advanced concepts and fuel designs would be needed for conversion of higher power reactors, such as HFIR Chandler et al. (2019). Use of accelerated life testing will undoubtedly play a role in evaluating nuclear fuels and fuel performance as the nuclear community explores these concepts through advanced fuel forms or fabrication methods Nelson (2023).
Additional work is needed to fully understand the impact of accelerated fission rate testing on the physical phenomena that drive fuel performance. In the example of LEU fuels developed to enable reactor conversion, the necessary fuel burnups exceed 50% of the initial U-235 inventory Keiser et al. (2003). At these high burnups, the differences in fission gas accumulation occurring in MiniFuel versus those of the intended reactor may be significant. For example, at 30 MWd/kg U burnup (approximately 3% of initial heavy metal inventory), Figure 9 shows that MiniFuel would produce approximately 600 appm total xenon. However, the total xenon content occurring in a PWR would be less than 300 appm at the same burnup. This difference will only amplify over time due to the differences in fission product yield in U-235 vs. Pu-239 fission.
Further understanding of the effects, such as variation in fission gas inventories illustrated above, will require further irradiation testing and comparison of PIE outcomes at varied fission rate and across accelerated testing platforms. The most important near-term use of MiniFuel will be screening of novel fuel forms and phenomena relevant to nuclear energy and nuclear security. Data collection and PIE will help refine methods and improved understanding of the attributes and challenges inherent to accelerated fission rate testing.
Since MiniFuel irradiations were first fielded in 2018, the majority of the fuels irradiated have been coated particle fuels. These range from bare kernels and TRISO-coated particles to full compacts. Ongoing PIE efforts are informing and improving irradiation methodologies and enhancing capabilities for these fuel forms. Upcoming PIE performed on larger monolithic fuel disks, as discussed in this manuscript, is similarly expected to result in numerous process improvements. Application of fuel performance models to microstructure and fission gas release data collected from monolithic disks will also demonstrate for the first time use of an accelerated fuel irradiation test to benchmark fuel performance models Cheniour et al. (2022).
Understanding of the full impact of a specific taggant on UO2 performance would require prototypical integral irradiations. However, the time and expense of an integral irradiation is not necessary to screen for gross performance impacts. If taken to an extreme degree, the impact of a taggant could grossly degrade fuel pellet mechanical properties to the extent that pulverization occurs during service. MiniFuel irradiation of a candidate taggant would demonstrate such an extreme response, allowing this taggant to be omitted from future trials. Conversely, a MiniFuel irradiation demonstrating negligible impact of a taggant does not necessarily ensure acceptable performance during an integral test under representative conditions, but it can be used to justify the more expensive and time-consuming irradiation.
The priority PIE of tagged UO2 will be the basic observation of pellet integrity. An absence of extreme temperature gradients in the MiniFuel samples is not expected to induce cracking as would occur in a standard UO2 fuel pellet under LWR service Capps et al. (2021). Observation of extreme cracking or pulverization would therefore be indicative of highly anomalous irradiation behavior induced by the taggant. Fission gas release will also be measured as the subcapsule is opened. The fission gas release in pure UO2 resulting from these irradiation temperatures and burnups will be negligible for pure UO2 Cheniour et al. (2022), so any measurement of fission gas release above background would be a significant finding. Finally, examination of the resulting microstructure following irradiation can provide useful insights into how the taggant behavior or fission product phases evolve with irradiation.
The above examinations are necessary to evaluate how a taggant impacts fuel performance. However, the primary objective of the experiment is driven by forensics. The availability of irradiated fuel samples facilitates preparation and distribution of small samples that can be analyzed to assess the serviceability of the isotopic tag throughout the nuclear fuel cycle. As outlined in Section 3.1, the presence of fission products will alter the isotope ratios used for some taggants of interest. Reconstructing the initial taggant isotopic ratio when conflated by fission product isotopes therefore represents a major technical challenge and dictates a taggant’s viability for its intended purpose at the back end of the nuclear fuel cycle. The MiniFuel irradiation therefore elucidates the impact of a taggant on fuel performance and provides material subjected to a representative nuclear fuel service condition after which recovery and attribution can be benchmarked. These are both key parameters needed to inform future research on this subject.
Nuclear forensics is an application space that could greatly benefit from using the nuclear fuel testbed facilities at ORNL for both generating and characterizing pre- and post-irradiation forensic signatures. The primary objective of nuclear forensic investigations is to identify the origin, intended use, and production history of material found outside of institutional control Hutcheon et al. (2015); Mayer et al. (2011). Additionally, fuel samples and other material can use nuclear forensics to verify that nuclear programs are compliant with declared treaty specifications. Understanding and documenting measurable parameters (isotopes, chemical compositions, physical forms, colors, grain size, particle size distribution, sorting, etc.) of nuclear material can reveal unique material signatures that can help accurately identify the origin and processing method used on the material. Characterization methods for these materials includes microscopy (SEM, TEM, optical, etc.), radiometric (gamma and alpha spectrometry), and mass spectrometry methods (TIMS, ICP-MS, SIMS, etc.). Signatures for nuclear material fall into two categories: comparative and predictive signatures Hutcheon et al. (2015). Comparative signatures typically involve the comparison of the signatures of a nuclear material (isotopic composition, grain size, morphology) to those of a known sample from a database. Predictive signatures are used when representative data are lacking and focus on modeling and overall concepts for material attribution.
Actinide materials irradiated using MiniFuel would clearly develop different signatures compared to material irradiated in other facilities. However, forensic techniques could be benchmarked using material irradiated using MiniFuel combined with detailed characterization of the samples before irradiation and the well known reactor physics of HFIR. This could enable validation and improvement of methods deployed in the field or exploration of new detection or forensic technologies where evaluation against representative materials is challenging.
Irradiations and PIE of MiniFuel samples can also produce both representative and predictive signatures. The ability to simultaneously irradiate multiple fuel samples in HFIR at various burnups and temperatures can produce a large array of representative sample material that can be analyzed and categorized for its isotope ratio changes, plutonium production, and other microstructure changes. Likewise, chemically separating MiniFuel samples with significant burnup can both produce representative material for signature analysis and help identify predictive signatures for various reprocessing methods. Forensics investigations on plutonium are aided by signatures that can help identify the reactor type, irradiation history, and chemical separation method of the material Osborn et al. (2018); using MiniFuel and HFIR can help produce representative material for databases while also investigating new predictive signatures for advanced and unique fuel types.
One major issue with spent fuel isotope measurements for safeguards and security applications is the small quantity and range of samples available for identification, characterization, and quantification of actinide production. Current databases, such as SFCOMPO Michel-Sendis et al. (2017), contain data on spent fuel; however, most of the data are from irradiation conditions of or similar to commercial LWRs. Current nuclear nonproliferation applications require spent fuel samples that are relevant to research, production, and advanced reactor applications with a wide range of fuel materials and irradiation conditions. MiniFuel irradiation could produce irradiated fuels and companion materials well before they are generated in future reactors, enabling nonproliferation research that anticipates rather than reacts to future proliferation scenarios. Furthermore, the advancement of facility capabilities, such as the Mk-18A facility, allows for faster processing of irradiated fuels for sample isotope quantification. This can enable use of high-precision actinide and fission product concentrations via mass spectrometry and microchemical analysis to ascertain reactor operating parameters. Processing of these fuels can also broaden the understanding of source terms for effluent analysis of off-gas systems in nuclear facilities.
Finally, the testbed itself can be used as a source of information for nuclear forensics and nonproliferation signatures. Sample swipes collected from representative process equipment and areas inside of the different labs of the testbed can provide insight into particles, isotopics, and likely contamination areas that would be present in a full-scale operation. Furthermore, contaminants, phase types, and other unintentionally added signatures that are incorporated or created during the fuel cycle can be identified and quantified for attribution of different activities or methods.
The manuscript describes how the MiniFuel irradiation capability is being applied to advance nonproliferation and nuclear forensics applications. Fuel fabrication and pre-irradiation characterization is followed by MiniFuel irradiation to accumulate burnup and develop representative fission product and transuranic inventories in nuclear fuel samples. PIE, evaluation of reprocessing techniques, and other forensic signatures complete the analysis to match the objectives of a wide range of nuclear fuel, nuclear nonproliferation, and nuclear security objectives. For intentional forensics, taggant-doped fuel is irradiated in HFIR to provide an accelerated life test to ensure that the effect of the taggants on fuel behavior is negligible and that the taggants can still provide a unique signature post-irradiation. For plutonium production and fission gas analysis, MiniFuel can be used to test the production of different isotopes and signatures for fuel that has a range of enrichments and irradiation histories. The outcomes of experimental campaigns and studies such as those introduced herein are anticipated to result in increased refinement of methods and understanding, providing value to numerous stakeholders in the coming decades.
The codes and raw datasets used in this manuscript are subject to export control review form the US Department of Energy prior to release. Requests to access the raw datasets should be directed to d2lsc29uYmExQG9ybmwuZ292.
The authors confirm contribution to the paper as follows: BW, AS, AC, CP, and AN contributed to the conception and design of the study as well as the draft manuscript preparation. TU, AK, LS, TG, JH, and AC wrote sections of the manuscript and contributed data and figures. All authors reviewed the results and approved the final version of the manuscript.
This work was funded by the U.S. Department of Energy, National Nuclear Security Administration, Office of Defense Nuclear Nonproliferation R&D.
The authors declare that the research was conducted in the absence of any commercial or financial relationships that could be construed as a potential conflict of interest.
All claims expressed in this article are solely those of the authors and do not necessarily represent those of their affiliated organizations, or those of the publisher, the editors and the reviewers. Any product that may be evaluated in this article, or claim that may be made by its manufacturer, is not guaranteed or endorsed by the publisher.
1This manuscript has been authored by UT-Battelle LLC, under contract DE-AC05-00OR22725 with the US Department of Energy (DOE). The US government retains and the publisher, by accepting the article for publication, acknowledges that the US government retains a non-exclusive, paid-up, irrevocable, worldwide license to publish or reproduce the published form of this manuscript, or allow others to do so, for US government purposes. DOE will provide public access to these results of federally sponsored research in accordance with the DOE Public Access Plan (http://energy.gov/downloads/doe-public-access-plan).
Abdul-Jabbar, N. M., Grote, C. J., and White, J. T. (2019). “Assessment of thermophysical property characterization of MiniFuel scale geometries,” in Tech. Rep. LA-UR-19-24287, los alamos national lab.(LANL) (Los Alamos, NM (United States).
Arborelius, J., Backman, K., Hallstadius, L., Limbäck, M., Nilsson, J., Rebensdorff, B., et al. (2006). Advanced doped UO2 pellets in LWR applications. J. Nucl. Sci. Technol. 43, 967–976. doi:10.1080/18811248.2006.9711184
Bathke, C. G., Ebbinghaus, B. B., Collins, B. A., Sleaford, B. W., Hase, K. R., Robel, M., et al. (2012). The attractiveness of materials in advanced nuclear fuel cycles for various proliferation and theft scenarios. Nucl. Technol. 179, 5–30. doi:10.13182/nt10-203
Benedict, M., Pigford, T. H., and Levi, H. W. (1981). Nuclear chemical engineering. McGraw-Hill Education.
Blake, L. (1961a). Achieving high burn-up in fast reactors. J. Nucl. Energy. Parts A/B. React. Sci. Technol. 14, 31–48. doi:10.1016/0368-3230(61)90071-4
Blake, L. (1961b). Irradiation of uranium-metal and uranium-oxide fuel pins to high burn-up at high temperature. J. Nucl. Energy. Parts A/B. React. Sci. Technol. 15, 140–159. doi:10.1016/0368-3230(61)90050-7
Capps, N., Sweet, R., Harp, J., and Petrie, C. M. (2021). High-burnup fuel stress analysis prior to and during a loca transient. J. Nucl. Mater. 556, 153194. doi:10.1016/j.jnucmat.2021.153194
Chandler, D., Betzler, B., Cook, D., Ilas, G., and Renfro, D. (2019). Neutronic and thermal-hydraulic feasibility studies for high flux isotope reactor conversion to low-enriched uranium silicide dispersion fuel. Ann. Nucl. Energy 130, 277–292. doi:10.1016/j.anucene.2019.02.037
Cheniour, A., Pastore, G., Harp, J. M., Petrie, C. M., and Capps, N. A. (2022). Application of BISON to UO2 MiniFuel fission gas release analysis. J. Nucl. Mater. 565, 153686. doi:10.1016/j.jnucmat.2022.153686
Cooper, M. W., Pastore, G., Che, Y., Matthews, C., Forslund, A., Stanek, C. R., et al. (2021). Fission gas diffusion and release for Cr2O3-doped UO2: From the atomic to the engineering scale. J. Nucl. Mater. 545, 152590. doi:10.1016/j.jnucmat.2020.152590
Cooper, M. W., Stanek, C. R., and Andersson, D. A. (2018). The role of dopant charge state on defect chemistry and grain growth of doped UO2. Acta Mater. 150, 403–413. doi:10.1016/j.actamat.2018.02.020
Daily, C., Mosher, S., Wilson, S. D., and Chandler, D. (2020). “HFIRCON version 1.0. 5 user guide,” in Tech. Rep., Oak Ridge National lab.(ORNL) (Oak Ridge, TN (United States).
Doyle, P., Massey, C., Ulrich, T., Richardson, T., Greenquist, I., Seibert, R., et al. (2023). Accelerated fission rate irradiation design, pre-irradiation characterization, adaptation of conventional pie methods for u-10mo and u-17mo. Front. Nucl. Energy Curr. 1–30. doi:10.3389/fnuen.2022.1054288
Field, K. G., McDuffee, J. L., Gerinsger, J. W., Petrie, C. M., and Katoh, Y. (2019). Evaluation of the continuous dilatometer method of silicon carbide thermometry for passive irradiation temperature determination. Nucl. Instrum. Methods Phys. Res. Sect. B Beam Interact. Mater. Atoms 445, 46–56. doi:10.1016/j.nimb.2019.02.022
Harp, J. M., Demkowicz, P. A., Winston, P. L., and Sterbentz, J. W. (2014). An analysis of nuclear fuel burnup in the agr-1 triso fuel experiment using gamma spectrometry, mass spectrometry, and computational simulation techniques. Nucl. Eng. Des. 278, 395–405. doi:10.1016/j.nucengdes.2014.07.041
Harp, J. M., Morris, R. N., Petrie, C. M., Burns, J. R., and Terrani, K. A. (2021). Postirradiation examination from separate effects irradiation testing of uranium nitride kernels and coated particles. J. Nucl. Mater. 544, 152696. doi:10.1016/j.jnucmat.2020.152696
Hutcheon, I., Kristo, M., and Knight, K. (2015). Nonproliferation nuclear forensics. Tech. rep. Livermore, CA (United States): Lawrence Livermore National Lab. LLNL.
Keiser, D., Hayes, S., Meyer, M., and Clark, C. (2003). High-density, low-enriched uranium fuel for nuclear research reactors. Jom 55, 55–58. doi:10.1007/s11837-003-0031-0
Kristo, M., Robel, M., and Hutcheon, I. (2007). Nuclear forensics and attribution for improved energy security: The use of taggants in nuclear fuel. Tech. Rep. Livermore, CA (United States): Lawrence Livermore National Lab. LLNL.
Lamont, S., Phillips, J., Bedell, J., Goorevich, R., Nusbaum, D., Karpas, Z., et al. (2006). “Use of chemical and isotopic tracers as part of an improved safeguards approach in uranium conversion facilities,” in Tech. Rep., los alamos national lab.(LANL) (Los Alamos, NM (United States).
Lupercio, A. E., Moshkelgosha, E., Winters, R. C., Doyle, C., Mamivand, M., Nelson, A. T., et al. (2021). Ball-on-ring test validation for equibiaxial flexural strength testing of engineered ceramics. Int. J. Ceram. Eng. Sci. 3, 128–139. doi:10.1002/ces2.10085
Manard, B. T., Bostick, D. A., Metzger, S. C., Ticknor, B. W., Zirakparvar, N. A., Rogers, K. T., et al. (2021). Rapid and automated separation of uranium ore concentrates for trace element analysis by inductively coupled plasma–optical emission spectroscopy/triple quadrupole mass spectrometry. Spectrochim. Acta Part B At. Spectrosc. 179, 106097. doi:10.1016/j.sab.2021.106097
Mayer, K., Wallenius, M., Lützenkirchen, K., Galy, J., Varga, Z., Erdmann, N., et al. (2011). “Nuclear forensics: A methodology applicable to nuclear security and to non-proliferation,” in Journal of Physics: Conference Series (Bristol, England: IOP Publishing), 062003.
Mendoza, P. M., Chirayath, S. S., and Folden, C. M. (2016). Fission product decontamination factors for plutonium separated by purex from low-burnup, fast-neutron irradiated depleted uo2. Appl. Radiat. Isotopes 118, 38–42. doi:10.1016/j.apradiso.2016.08.021
Michel-Sendis, F., Gauld, I., Martinez, J., Alejano, C., Bossant, M., Boulanger, D., et al. (2017). Sfcompo-2.0: An oecd nea database of spent nuclear fuel isotopic assays, reactor design specifications, and operating data. Ann. Nucl. Energy 110, 779–788. doi:10.1016/j.anucene.2017.07.022
Mosher, S. W., Johnson, S. R., Bevill, A. M., Ibrahim, A. M., Daily, C. R., Evans, T. M., et al. (2013). Advantg—an automated variance reduction parameter generator. ORNL/TM-2013/416 Rev 1.
Mosher, S. W., and Wilson, S. C. (2018). Algorithmic improvements to mcnp5 for high-resolution fusion neutronics analyses. Fusion Sci. Technol. 74, 263–276. doi:10.1080/15361055.2018.1496691
Nelson, A. T. (2023). Prospects for additive manufacturing of nuclear fuel forms. Prog. Nucl. Energy press 155, 104493. doi:10.1016/j.pnucene.2022.104493
Osborn, J. M., Kitcher, E. D., Burns, J. D., Folden, C. M., and Chirayath, S. S. (2018). Nuclear forensics methodology for reactor-type attribution of chemically separated plutonium. Nucl. Technol. 201, 1–10. doi:10.1080/00295450.2017.1401442
Petrie, C. M., Burns, J. R., Raftery, A. M., Nelson, A. T., and Terrani, K. A. (2019). Separate effects irradiation testing of miniature fuel specimens. J. Nucl. Mater. 526, 151783. doi:10.1016/j.jnucmat.2019.151783
Raftery, A. M., Morris, R. N., Smith, K. R., Helmreich, G. W., Petrie, C. M., Terrani, K. A., et al. (2018). “Development of a characterization methodology for post-irradiation examination of miniature fuel specimens,” in Tech. Rep., Oak Ridge National lab.(ORNL) (Oak Ridge, TN (United States).
Richardson, D., Helmreich, G. W., Raftery, A., and Nelson, A. (2019). “Resolution capabilities for measurement of fuel swelling using tomography,” in Tech. Rep., Oak Ridge National lab.(ORNL) (Oak Ridge, TN (United States).
Roake, W. (1963). “Irradiation alteration of uranium dioxide,” in Radiation damage in reactor materials. Part of the proceedings of the symposium on radiation damage in solids and reactor materials.
Sadergaski, L. R., and Andrews, H. B. (2022). Simultaneous quantification of uranium (vi), samarium, nitric acid, and temperature with combined ensemble learning, laser fluorescence, and Raman scattering for real-time monitoring. Analyst 147, 4014–4025. doi:10.1039/d2an00998f
Terrani, K. A., Capps, N. A., Kerr, M. J., Back, C. A., Nelson, A. T., Wirth, B. D., et al. (2020a). Accelerating nuclear fuel development and qualification: Modeling and simulation integrated with separate-effects testing. J. Nucl. Mater. 539, 152267. doi:10.1016/j.jnucmat.2020.152267
Terrani, K. A., Jolly, B. C., and Harp, J. M. (2020b). Uranium nitride tristructural-isotropic fuel particle. J. Nucl. Mater. 531, 152034. doi:10.1016/j.jnucmat.2020.152034
Trauger, D. (1962). Irradiation testing of fuel materials for egcr. Nucl. Sci. Eng. 14, 69–82. doi:10.13182/nse62-a26200
Van den Berghe, S., and Lemoine, P. (2014). Review of 15 years of high-density low-enriched umo dispersion fuel development for research reactors in Europe. Nucl. Eng. Technol. 46, 125–146. doi:10.5516/net.07.2014.703
Whitney, J., Chandler, E., Gates, J., and Calkins, G. (1957). A radiation effects program. Symposium Radiat. Eff. Mater. 1, 27.
Wieselquist, W. A., Lefebvre, R. A., and Jessee, M. A. (2020). SCALE code SystemTech. Rep. Oak Ridge, TN: Oak Ridge National Laboratory. ORNL/TM-2005/39 Version 6.2.4.
Keywords: nonproliferation and safeguards, nuclear forensic, nuclear fuel, fuel fabrication, fuel reprocessing, nuclear irradiation
Citation: Wilson BA, Conant A, Ulrich TL, Kercher A, Sadergaski LR, Gerczak T, Nelson AT, Petrie CM, Harp J and Shields AE (2023) Nuclear fuel irradiation testbed for nuclear security applications. Front. Nucl. Eng. 2:1123134. doi: 10.3389/fnuen.2023.1123134
Received: 13 December 2022; Accepted: 19 January 2023;
Published: 03 February 2023.
Edited by:
Palash Kumar Bhowmik, Idaho National Laboratory (DOE), United StatesCopyright © 2023 Wilson, Conant, Ulrich, Kercher, Sadergaski, Gerczak, Nelson, Petrie, Harp and Shields. This is an open-access article distributed under the terms of the Creative Commons Attribution License (CC BY). The use, distribution or reproduction in other forums is permitted, provided the original author(s) and the copyright owner(s) are credited and that the original publication in this journal is cited, in accordance with accepted academic practice. No use, distribution or reproduction is permitted which does not comply with these terms.
*Correspondence: Brandon A. Wilson, d2lsc29uYmExQG9ybmwuZ292
Disclaimer: All claims expressed in this article are solely those of the authors and do not necessarily represent those of their affiliated organizations, or those of the publisher, the editors and the reviewers. Any product that may be evaluated in this article or claim that may be made by its manufacturer is not guaranteed or endorsed by the publisher.
Research integrity at Frontiers
Learn more about the work of our research integrity team to safeguard the quality of each article we publish.