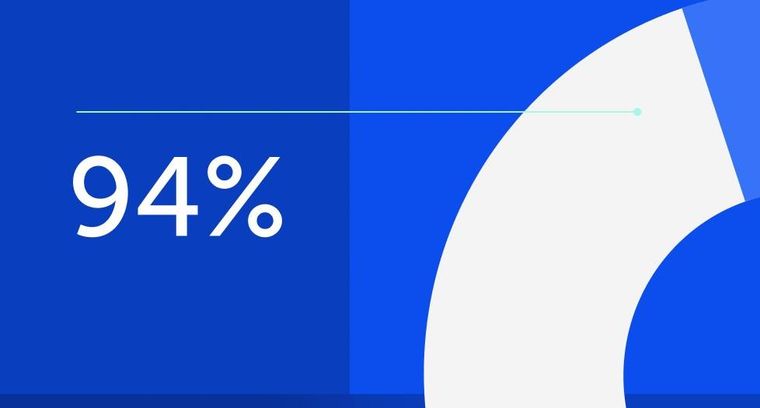
94% of researchers rate our articles as excellent or good
Learn more about the work of our research integrity team to safeguard the quality of each article we publish.
Find out more
ORIGINAL RESEARCH article
Front. Nucl. Eng., 14 March 2023
Sec. Nuclear Materials
Volume 2 - 2023 | https://doi.org/10.3389/fnuen.2023.1119567
This article is part of the Research TopicPlutonium Legacy Storage and DegradationView all 6 articles
Storage of plutonium (Pu)-containing materials requires extremely strict attention to physical safety and material accounting. For the emphasized importance of storage management, many reports are available in the public, e.g., experience in PuO2 storage in the UK and safety standards in the storage of Pu-containing materials in the US. Japan also stores plutonium, mainly in the form of uranium-Pu mixed oxide (MOX) mostly in powder form. Robust conditioning and storage arrangements must be adopted that are appropriate to the characteristics of the MOX, such as raw powder obtained by reprocessing of spent Light Water Reactor fuels, MOX samples from research and development on the remains of fuel fabrication, which can contain organic materials, and dry-recycled powder during fuel fabrication. A reduction in MOX fuel fabrications operations and experience in degradation of MOX containers during extended period of storage have led to JAEA to review the MOX storage arrangements in the Plutonium Fuel Development Center in Japan Atomic Energy Agency. The present work discusses the various nuclear materials, storage methods, experience in degradation of containers that occur during storage, and strategies for future long-term storage.
Actinide facilities in the world consider deliberate measures to safely store plutonium (Pu)-containing materials (Clark, 2019; Gunter, 2018; USDOE, 1994; Haschke and Ricketts, 1995; Stone, 2012; Ammerman et al., 1998; Dunn et al., 2013; Rigaut and Amouroux, 2013; Bradley and Koenig, 2019; GOV.UK, 2022; Sutherland-Harper et al., 2018; Sutherland-Harper et al., 2019; I.A.E. Agency, 2002; I.A.E. Agency, 2003). The Plutonium Fuel Development Center (PFDC) in Japan Atomic Energy Agency has stored tons of Pu-containing materials. Decisions have been made toward long-term storage of Pu-containing materials with reference to DOE-STD-3013-2018 (Gunter, 2018) that describes detailed safety standards and measures for storage of Pu-containing materials in the Department of Energy in the US, e.g., the Pu-containing materials in the PFDC are heat-treated so that the water content needs to be below 0.5 wt% before they are packed into containers.
The PFDC started operations in 1966 to study the properties of mixed oxide (MOX) fuels and develop a fabrication technology in a relatively small-scale facility in the Plutonium Fuel Development Facility (PFDF). Subsequently, the facilities were expanded in 1972 to start manufacturing MOX fuels in a larger scale facility in the Plutonium Fuel Fabrication Facility (PFFF) for reactors, e.g., Fugen and Joyo. In these facilities, a stainless-steel container with external double layer of polyvinyl chloride (PVC) bags, which are permeable to water vapor, was adopted for storing nuclear materials. This storage method is similar to what was adopted in the Sellafield site for PuO2 from spent-fuel reprocessing using the PUREX (Plutonium Uranium Reduction Extraction) process prior to 1975 (a PVC-free method was used from 1975 onwards) with an aluminum screw-top can inside a PVC bag and outer aluminum screw-top can (GOV.UK, 2022). The resulting inventory contains Cl contamination, that is corrosive to metallic container materials. The effect of heat treatment on PuO2 and the consequent Cl behavior was investigated, which revealed that Cl on the surface of PuO2 is volatilized above 923 K (Sutherland-Harper et al., 2018; Sutherland-Harper et al., 2019; Webb et al., 2019; GOV.UK, 2022).
The manufacture of MOX fuels was extended in 1988 to a larger scale with a new facility in the Plutonium Fuel Production Facility in Joyo and Monju. In the new facilities, the raw materials used for MOX fuel fabrication were stored in an aluminum-alloy container (not airtight) with an external stainless-steel canister (airtight) that was free from PVC bags.
In the subsequent years of absence of reactor operations and stagnation in fuel fabrication in which degradation was discovered in the storage containers, the storage methods were reviewed. In particular, the degradation of the storage containers was investigated even if the tracked information was limited. The current study presents various nuclear materials and impurities, storage methods, experience of degradation of containers that occurred during storage, and strategies for future long-term storage.
PFDC stores Pu-containing materials from research and development and fuel fabrication operations as well as unused raw materials. The major chemical forms are MOX and PuO2. PuO2 was originally imported from overseas. Whereas MOX was produced in Japan. The MOX powder was obtained using the PUREX (Koizumi et al., 1983; Mckibben, 1984; Viala et al., 1991) method at the Tokai Reprocessing Plant from spent LWR fuels, blending of UO2 and PuO2 powders, and MOX powder recycled by either dry or wet process (Suzuki et al., 2018). The majority of material is in a powdered form but the properties, e.g., powder-size distribution, were diverse. The Pu/oxide ratio of the MOX covers a wide range from 0% to 50% depending on the original feed and targeted fuels, namely, Fugen, Joyo, and Monju types.
Various impurities contaminated the nuclear materials and could result in storage problems. Organic materials, such as zinc stearate, which were used as lubricant and binder, remained when mixed but not sintered. Residue plutonium materials recovered from glovebox (GB) operations include contamination from, for example, small fragments of grinding wheels, oils, and other debris from fuel research. Furthermore, ion chromatography measurements using NaOH solution to leach materials indicate chloride contamination in Pu-containing materials that have been stored in PVC bags. This results show that the HCl produced from the PVC degradation (both radiolytically and thermally) is deposited in the material. Removal of the Cl deposited in the material requires heating at high temperatures.
A stainless-steel (SUS304) container with PVC bags is used to store nuclear materials in PFDF and PFFF. Figures 1A, B show a photograph and schematic diagram of the container system, respectively. Nuclear materials are directly packed into a stainless-steel container that is typically 11 cm in diameter and 22 cm in height, which is considered physically robust. A screw lid is designed to confine the powder inside and but not airtight. The nuclear materials are manually packed in an air atmosphere GB without humidity control. Thus, the outer surface of the container is handled as a contaminated part due to the adhesion of nuclear-material powder despite the efforts of wiping it before it is packed with a PVC bag. The PVC bag is 0.3-mm thick and contains plasticizer (19–29 wt% of 2-ethylhexyl phthalate and 3 – 7 wt% of 2-ethylhexyl). The stainless-steel container is packed into the first PVC bag by taking it out at a loading port installed at the GB wall. The edges of the PVC bag that contains the stainless-steel container are thermally welded. The red tape is used to cover the welded areas which are considered to have a higher risk of contamination. Finally, the stainless-steel container with the first PVC bag is further packed into a second “clean” PVC bag. Contamination at the outer surfaces of the PVC bags is strictly controlled and are not tolerated.
FIGURE 1. (A) Photograph of the stainless-steel canister and (B) schematic diagram of the storage system with a stainless-steel container and double PVC bags. Nuclear materials are manually packed into the stainless-steel container in a GB, and the stainless container is packed into the first PVC bag by taking it out at a loading port. Then, it is again packed into a second “clean” PVC bag.
Visual inspections of the stainless-containers and PVC bags and all the items stored in the PVC bags are annually performed. The inspection of the stainless-steel containers focuses on the existence of rust, corrosion, and deformation that present the risk of damaging the PVC bags, leakage of nuclear materials from inside, and contamination accidents. Focus is also concentrated on the existence of damages, contaminations, and inflation during the annual inspection of the PVC bags. The PVC bags must also remain transparent so that the stainless-steel container can be visibly inspected. They are changed if any of the abovementioned problems are found. Furthermore, as a preventive measure against radiation or heat damage, the PVC bag is changed before the integration of decay heat of each item reaches 7 kWd which is evaluated based on the tensile-strength test on the irradiated PVC bags. In the investigation, 50% decrease of tensile elongation was considered as a reasonable criterion and was obtained on the PVC bags with the decay heat of 10 kWd. By considering 2-sigma of the tensile elongation data, 7 kWd was adopted as a criteria of bag exchange.
In the inspections carried out annually and also before the integration of decay heat of each item reaches 7 kWd, inflation of PVC bags is sometimes found in a storage facility. Unfortunately, there are insufficient records such as detailed time to develop the inflation, repeated occurrence on the same material, nor the condition of heat treatment. A critical cause for the inflation is hydrogen generation by radiolysis (Hamill, 1969; Burns and Sims, 1981; LaVerne and Tandon, 2003) from the organic materials that are not removed by heat treatment. Because the PVC is permeable to the H2 and H2O gases, the inflation can actually occur when the gas generation rate exceeds the permeation rate. Hydrogen-gas generation during storage has been pointed out many years ago (Stakebake, 1971) and is unavoidable if water/organic materials are absorbed onto the Pu oxide. Internal pressurization presents a risk of PVC bag rupture, which can result in large-scale contamination and must be controlled by appropriate management of water or organic materials whereas heat-treatment is not a mandatory process for the PVC-type storage method prior to packing; the heat-treatment is strictly required for the PVC-free storage method.
Degradation of PVC bags and stainless-steel containers has been observed during inspections, although the recorded information of storage history was limited. Figures 2A–E show examples of degraded containers together with the usage periods of the PVC bags, and Figure 2F shows those of the stainless container. These are the recorded examples of severely degraded containers that were found in the regular inspections and repacking in new containers. Unfortunately, the usage period of the degraded stainless-steel container was not recorded except for that shown in Figure 2F. The color of the PVC bags turned from blue to yellow/brown, and the texture changed to slightly soft and sticky. Severe rusts were formed at the surface of the stainless-steel containers. The PVC bags were damaged by gamma radiation from inside of the container and from outside because of the presence of other stored items. Alpha irradiation from small amount of Pu that remains between the PVC bag and the stainless-container may also damage the PVC bag. The degradation of the PVC could be accelerated by the heat from the surface of the container. Temperatures on the surface of one stainless-container, which was selected as one of the hottest items containing MOX with 25.5W, ranged from 34°C–67°C. On the other hand, the degradation of the stainless-steel containers due to rust on the surfaces was considered to occur because of H2O permeated through the PVC bag and HCl that was generated from the PVC bags, which were damaged by gamma radiation (and possibly by alpha radiation) (Miller, 1959; Palma and Carenza, 1970; Clough and Gillen, 1981). Adsorbed water can migrate out of the screw lid container driven by the thermal gradients in the contained material and the water can permeate through the PVC bag. The resulting humid environment can accelerate the corrosion of stainless steel exposed to HCl.
FIGURE 2. Photographs of degraded PVC bags and stainless-steel containers. The Pu contents are (A) 770, (B) 840, (C) 1,400, (D) 84, (E) 820, and (F) 260 g. The usage periods of the PVC bags are (A) 822, (B) 531, (C) 245, (D) 7791, (E)–left 784, and (E)–right 795 days. Those of the stainless-steel container are (F)–left 2226 and (F)–right 5438 days.
Table 1 and Figure 3 show the selected list of Cl contents analyzed by ion chromatography in the nuclear materials and photograph of the Cl-contaminated MOX powder (1,600 ppm), respectively. The highest Cl content thus found was 2800 ppm, and no unique appearance of the Cl-contaminated MOX powder was observed. In addition, no correlation existed among the total weight, Pu weight, uranium (U) weight, Pu/(U + Pu), and Cl content.
Figure 4 shows the relationship of the U and Pu contents of the nuclear materials in the degraded stainless-steel containers. No obvious correlation existed between U and Pu, indicating that the degradation of the stainless-steel containers occurred for all stored material types, i.e., U-rich and Pu-rich, U-rich and Pu-poor, U-poor and Pu-rich, and U-poor and Pu-poor items. The stainless-containers which contain UO2 or extremely small amount of MOX were corroded. The Pu content in the container and its radiation were not an unique causality, and the degradation of the PVC bags was due to the gamma-radiations from both inside the container and the nuclear materials outside, which were stored in the same facility. However, we need to note that the alpha-radiation due to contamination on the bag surface could occur and also the alpha decay of Pu increased the temperature of the stainless container and PVC bags, which could have accelerated the degradation (Palma and Carenza, 1970; Braun, 1971; Clough and Gillen, 1981). Whereas the degradation of the stainless-steel container was mostly found at the outer surface, extraordinarily high Cl contents were found in the nuclear materials because HCl transferred from the PVC bags into the stainless-steel containers through the screw lid (not airtight), which is the similar scenario of Cl-contaminated PuO2 in UK. To study the Cl-contaminated MOX and develop the method of removing Cl, thermogravimetric analysis (TGA) is planned.
The storage method that uses PVC bags cannot prevent radiation/heat damage and generation of HCl (Miller, 1959; Palma and Carenza, 1970; Clough and Gillen, 1981), which corrode the stainless-steel containers. In addition, regular inspections of the PVC bags and stainless-steel containers as well as their replacements when necessary poses the risks of radiation exposure and contamination. Thus, for long-term storage, a programme of shifting storage type, PVC method to PVC-free methods, has been started. Within the frame, necessary heat treatment/sintering, and repacking the MOX are ongoing. Because the PVC-free methods in PFDC use airtight metallic containers, a strict management for removing water and organic materials from the nuclear materials is important to prevent internal pressurization and corrosion of the containers.
Figures 5A, B show the aluminum-alloy container and stainless-steel canister, respectively. In principle, the storage method is adopted for raw powders used in the fuel fabrication. In GBs, nuclear materials are directly packed in the 12.5-cm-diameter and 25-cm-high aluminum-alloy container. A maximum of four aluminum-alloy containers are vertically stacked into the stainless-steel canister. The stainless canister with screw lids (not welded so that the inside can be regularly inspected) is stored in an uncontaminated storage pit. To receive the aluminum-alloy containers into the stainless-steel canister, the canister is hermetically docked at the bottom of GB. The lids of stainless-steel canister and GB are also hermetically attached to each other with a lip seal so that the uncontaminated surfaces remain as they are. The attached lids are opened to the GB side, the aluminum-alloy containers are loaded into the stainless-steel container, and the attached lids are closed and detached. Finally, the lip seal which is subjected to the GB atmosphere is decontaminated for the risk of small contamination. Whereas the aluminum-alloy container is not airtight, the external stainless-steel canister contains double lids with a silicon seal at the first lid and two O-rings made of fluorine-containing rubber at the second lid.
FIGURE 5. (A) Aluminum-alloy containers that can directly pack nuclear materials and (B) stainless-steel canister in which a maximum of four aluminum-alloy containers are vertically stacked.
The nuclear materials are heat-treated in a batch-type furnace before packing to remove water and organic materials. Subsequently, the H2O, Cl, C, and F contents as well as the metallic impurities are measured. In principle, the H2O content, which is measured by coulometry using phosphoric anhydride to absorb moisture, must be reduced to below 0.5 wt%, although 1.0 wt% can be acceptable with annual inspections on randomly selected items. The criteria was decided based on DOE-STD-3013-2018 (Gunter, 2018), which is considered as a reasonable balance between difficulty of reducing H2O content and tolerance of internal pressurization. Similarly, the Cl content must be reduced to as low as possible, and visual inspections will be required for all items with Cl > 25 ppm and H2O > 0.5 wt% to check the conditions of the canister lid, existence of rusts, corrosions, deformation, and contamination on the outer and inner surfaces of the canister and outer surface of the aluminum-alloy container. For the criteria, the specification of MOX fuel pellets was used since there is no limit for the chloride content for long-term storage. The Cl content in the heat-treated MOX is below lower limit of detection whereas the MOX with high level of Cl contamination has not yet been heat-treated.
The second storage type has a fuel-assembly form of the Fugen or Monju type. The remaining components of these fuel assemblies have been used as containers because both reactors stopped operation. Similar to that in the fuel-assembly, MOX powder is sintered into pellets, and fuel assemblies are produced where zircaloy or stainless steel is used as a cladding material. During sintering, the organic materials contained in the powders are removed because the temperature is sufficiently high to volatilize them. Because these sintered pellets are not intended for use in a nuclear reactor, general specifications as sintered pellets are not required. Only an appropriate diameter is needed so that the pellets can be filled in the claddings. The storage method that uses fuel assemblies provides special advantages of utilizing the sintering facilities, specific space that can only be used for assemblies, and experience for fuel fabrication. A large capacity for pellet sintering and assembly storage is provided in PFDC as a MOX fuel fabrication facility.
Heat treatment to remove water and organic materials before packing into the abovementioned storage types is considered as a critical safety measure for long-term storage. For the majority of MOX, a fuel fabrication facility is utilized with a batch size of approximately 18 kg MOX. On the other hand, an experimental furnace is used with 1–2 kg batch size for MOX with high level of Cl contamination because the fuel fabrication facility should not be exposed to a risk of furnace damage. The powder form is heat-treated in air at more than 1073 K for longer than 1 h, whereas the pellet form is heat-treated in H2/Ar gas mixture at more than 1873 K for longer than 2 h. These temperatures are decided based on the specifications of the existing furnaces and also the suggested temperature in the DOE-STD-3013-2018 (Gunter, 2018); all plastics less than about one inch in diameter and any other organic materials likely to accompany unstabilized plutonium materials are completely oxidized at 1073 K (Nelson, 1995; Wey and Chang, 1995; Bockhorn et al., 1996; Panagiotou and Levendis, 1996; Zevenhoven et al., 1997). Heat treatment of powder is minimized because only an experimental furnace can treat powder with 1–2 kg batch size in the PFDC and also storing powder is inefficient in the volume, unless fabrication of the sintered pellets is physically difficult because of impurities or powder geometry. The risk of vaporization of HCl and possible corrosion of the furnaces and exhaust pipes should be considered when the HCl-contaminated items are heat-treated.
The details of stored Pu-containing materials, storage methods, degradation experience in storage containers, and strategies for long-term storage in PFDC are presented in this study. The major chemical forms were MOX and PuO2 and stainless-steel containers with screw lids (not air-tight) and double layers of PVC bags are used to store them. Degradation in both the PVC bags and stainless-containers are observed at visual inspections. The degradation of the PVC bags is considered to occur by gamma irradiation from inside the container and from the other stored nuclear materials, alpha irradiation from small amount of Pu remaining on the PVC bag, and the heat from the surface of the stainless-steel container. On the other hand, the degradation of the stainless-steel containers is considered to occur due to the HCl generation from the damaged PVC bags. The fact that the stainless-containers with UO2 or small amount of MOX were corroded indicates that the gamma irradiation on the PVC bags from the other stored nuclear materials can be a significant source for the HCl generation. Furthermore, Cl-contaminated nuclear materials are found, which indicates that HCl transfers from the PVC bags into the stainless-steel containers.
For long-term storage that is free from Cl contamination, storage method has shifted to the PVC-free methods, namely, aluminum-alloy containers with a stainless-steel canister and fuel assemblie. Because Pu-containing materials are air-tightly contained in the methods, they are heat-treated or sintered prior to packing to remove water and organic materials. The conditions of the heat treatment and the criteria of residue H2O/Cl are decided based on the specifications of existing furnace in PFDC and the DOE-STD-3013-2018; the powder form is heat-treated in air at more than 1073 K for longer than 1 h and the pellet form is heat-treated in H2/Ar gas mixture at more than 1873 K for longer than 2 h. The H2O content needs to be below 0.5 wt% although 1.0 wt% can be acceptable with annual inspections. The Cl content must be reduced to as low as possible, and visual inspections will be needed for the items with Cl > 25 ppm and H2O > 0.5 wt%. Heat treatment of the pellet form is more favorable because the PFDC has smaller capacity of powder processing and storage.
The storage methods for Pu in PFDC are presented for the first time in this open literature. In conclusion, more analysis is needed to improve safety and efficiency by studying individual problems and sharing information from laboratories that store Pu-containing materials in the world.
The original contributions presented in the study are included in the article/Supplementary Material, further inquiries can be directed to the corresponding author.
SH contributed to collecting and evaluating the data and writing the original manuscript. SN contributed to collecting and evaluating the data. TMu contributed to conceptualization and editing the manuscript. TMa and RT contributed to collecting the data.
SH, SN, TMu, TMa, and RT were employed by Japan Atomic Energy Agency.
All claims expressed in this article are solely those of the authors and do not necessarily represent those of their affiliated organizations, or those of the publisher, the editors and the reviewers. Any product that may be evaluated in this article, or claim that may be made by its manufacturer, is not guaranteed or endorsed by the publisher.
Ammerman, D. J., Geinitz, R., Thorp, D., and Rivera, M. (1998). “Development of A container for the transportation and storage of plutonium bearing materials,” in Proceedings of the 12th International Symposium on the Packaging and Transportation of Radioactive Materials PATRAM 1998, Paris, France, May 10-15, 1998.
Bockhorn, H., Hornung, A., Hornung, U., Teepe, S., and Weichmann, J. (1996). Investigation of the kinetics of thermal degradation of commodity plastics. Combust. Sci. Technol. 116, 129–151. doi:10.1080/00102209608935546
Bradley, L., and Koenig, R. (2019). “Packaging options for materials processed through the SRNL mobile plutonium facility,” in Proceedings of the 19th International Symposium on the Packaging and Transportation of Radioactive Materials PATRAM 2019, New Orleans, August 4-9, 2019.
Braun, D. (1971). Thermal degradation of polyvinyl chloride. Pure Appl. Chem. 26, 173–192. doi:10.1351/pac197126020173
Burns, W. G., and Sims, H. E. (1981). Effect of radiation type in water radiolysis, J. Chem. Soc. Faraday Trans. 77, 2803–2813. doi:10.1039/F19817702803
Clark, D. L. (2019). Plutonium Handbook: Nuclear science and materials science. USA: American Nuclear Society.
Clough, R. L., and Gillen, K. T. (1981). Combined environment aging effects: Radiation-thermal degradation of polyvinylchloride and polyethylene. J. Polym. Sci. Polym. Chem. Ed. 19, 2041–2051. doi:10.1002/pol.1981.170190816
Dunn, K. A., Steve Bellamy, J., Chandler, G., Iyer, N. C., Koenig, R. E., Leduc, D. R., et al. (2013). “Removal of legacy plutonium materials from Sweden,” in Proceedings of the 17th International Symposium on the Packaging and Transportation of Radioactive Materials PATRAM 2013, San Francisco, CA, USA, 18–23 August 2013.
GOV.UK (2022). The 2016/17 technology development and delivery summary. Available at: https://www.gov.uk/government/publications/the-201617-technology-development-and-delivery-summary (accessed September 21 2022).
Gunter, H. A. (2018). Stabilization, packaging and storage of plutonium-bearing materials — DOE technical standards program. Available at: https://www.standards.doe.gov/standards-documents/3000/3013-astd-2018 (accessed August 30 2022).
Hamill, W. H. (1969). Model for the radiolysis of water. J. Phys. Chem. 73, 1341–1347. doi:10.1021/j100725a027
Haschke, J. M., and Ricketts, T. E. (1995). Plutonium dioxide storage: Conditions for preparation and handling. United States: OSTI.GOV.
I.A.E. Agency (2002). Long term storage of spent nuclear fuel - survey and recommendations, long term storage of spent nuclear fuel - survey and recommendations. Available at: https://www.iaea.org/publications/6422/long-term-storage-of-spent-nuclear-fuel-survey-and-recommendations (accessed January 25, 2023).
I.A.E. Agency (2003). Storage of spent fuel from power reactors. Available at: https://www.iaea.org/publications/6902/storage-of-spent-fuel-from-power-reactors (accessed January 25 2023).
Koizumi, M., Ohtsuka, K., Ohshima, H., Isagawa, H., Akiyama, H., Todokoro, A., et al. (1983). Development of a process for co-conversion of Pu-U nitrate mixed solutions to mixed oxide powder using microwave heating method. J. Nucl. Sci. Technol. 20, 529–536. doi:10.1080/18811248.1983.9733431
LaVerne, J. A., and Tandon, L. (2003). H2 production in the radiolysis of water on UO2 and other oxides. J. Phys. Chem. B 107, 13623–13628. doi:10.1021/jp035381s
Mckibben, J. M. (1984). Chemistty of the purex process. Radiochim. Acta 36, 3–16. doi:10.1524/ract.1984.36.12.3
Miller, A. A. (1959). Radiation chemistry of polyvinyl chloride. J. Phys. Chem. 63, 1755–1759. doi:10.1021/j150580a045
Nelson, G. L. (1995). Fire and polymers II, fire and polymers II. United States: American Chemical Society.
Palma, G., and Carenza, M. (1970). Degradation of poly(vinyl chloride). I. Kinetics of thermal and radiation-induced dehydrochlorination reactions at low temperatures, J. Appl. Polym. Sci. 14 1737–1754. doi:10.1002/app.1970.070140708
Panagiotou, T., and Levendis, Y. A. (1996). Observations on the combustion of pulverized PVC and poly(ethylene). Combust. Sci. Technol. 112, 117–140. doi:10.1080/00102209608951952
Rigaut, E., and Amouroux, V. (2013). “Overview of the specification and the organization for the transport of radioactive sources from the CEA,” in Proceedings of the 17th International Symposium on the Packaging and Transportation of Radioactive Materials PATRAM 2013, Francisco, CA, USA, 18–23 August 2013.
Stakebake, J. L. (1971). The storage behavior of plutonium metal, alloys, and oxide: A review. J. Nucl. Mater. 38, 241–259. doi:10.1016/0022-3115(71)90054-7
Stone, T. A. (2012). Los Alamos national laboratory overview of the SAVY-4000 design: Meeting the challenge for worker safety. Los Alamos, NM (United States): Los Alamos National Lab. doi:10.2172/1188163
Sutherland-Harper, S., Livens, F., Pearce, C., Hobbs, J., Orr, R., Taylor, R., et al. (2019). Interactions of HCl and H2O with the surface of PuO2. J. Nucl. Mater. 518, 256–264. doi:10.1016/j.jnucmat.2019.02.036
Sutherland-Harper, S., Pearce, C., Campbell, C., Carrott, M., Colledge, H., Gregson, C., et al. (2018). Characterisation and heat treatment of chloride-contaminated and humidified PuO2 samples. J. Nucl. Mater. 509, 654–666. doi:10.1016/j.jnucmat.2018.07.031
Suzuki, K., Okita, T., and Aono, S. (2018). Experiences in MOX fuel fabrication at the PFPF for the fast reactor. Vienna, Austria: International Atomic Energy Agency.
USDOE (1994). Assessment of plutonium storage safety issues at Department of Energy facilities. Washington, DC (United States): USDOE Assistant Secretary for Defense Programs. doi:10.2172/10122659
Viala, M., Bernard, C., and Miquel, P. (1991). Advance purex process for the new reprocessing plants in France and in Japan. France: International Nuclear Information System.
Webb, K., Taylor, R., Campbell, C., Carrott, M., Gregson, C., Hobbs, J., et al. (2019). Thermal processing of chloride-contaminated plutonium dioxide. ACS Omega 4, 12524–12536. doi:10.1021/acsomega.9b00719
Wey, M. Y., and Chang, C. L. (1995). Kinetic study of polymer incineration. Polym. Degrad. Stab. 48, 25–33. doi:10.1016/0141-3910(94)00125-R
Keywords: MOX, plutonium, storage, degradation, inspection, stabilization, heat treatment
Citation: Hirooka S, Nakamichi S, Matsumoto T, Tsuchimochi R and Murakami T (2023) Toward long-term storage of nuclear materials in MOX fuels fabrication facility. Front. Nucl. Eng. 2:1119567. doi: 10.3389/fnuen.2023.1119567
Received: 09 December 2022; Accepted: 27 February 2023;
Published: 14 March 2023.
Edited by:
Edgar C. Buck, Pacific Northwest National Laboratory (DOE), United StatesReviewed by:
Robin Orr, National Nuclear Laboratory, United KingdomCopyright © 2023 Hirooka, Nakamichi, Matsumoto, Tsuchimochi and Murakami. This is an open-access article distributed under the terms of the Creative Commons Attribution License (CC BY). The use, distribution or reproduction in other forums is permitted, provided the original author(s) and the copyright owner(s) are credited and that the original publication in this journal is cited, in accordance with accepted academic practice. No use, distribution or reproduction is permitted which does not comply with these terms.
*Correspondence: Shun Hirooka, aGlyb29rYS5zaHVuQGphZWEuZ28uanA=
Disclaimer: All claims expressed in this article are solely those of the authors and do not necessarily represent those of their affiliated organizations, or those of the publisher, the editors and the reviewers. Any product that may be evaluated in this article or claim that may be made by its manufacturer is not guaranteed or endorsed by the publisher.
Research integrity at Frontiers
Learn more about the work of our research integrity team to safeguard the quality of each article we publish.