Introduction
Since the successful operation of the first nuclear reactor, Chicago Pile-1, in 1942, nuclear energy has played a more and more important role in the world’s carbon-free energy supply despite several severe nuclear accidents including those at Three Mile Island (1979), Chernobyl (1986), and Fukushima (2011). At present, there are 441 nuclear power reactors in operation that provide approximately 15% of the world’s electricity supply. The average age of reactors in operation is more than 31 years. The total reactor years of operation of all the nuclear power reactors is 19,329. There are 53 nuclear power reactors under construction and 15 of them are in China. Considering climate change pressures and carbon-neutral targets, nuclear energy is still one of the most important alternative sources of energy. In the past two decades, significant research progress has been achieved but more technical demands and challenges are still needing to be solved. In the following part, the author will summarize the progress of technical research and challenges in advanced nuclear reactor design. The discussion is focused on the grand challenges of advanced Generation IV reactor design, small modular reactors, accident fault-tolerant fuel, nuclear reactor severe accident, and digital reactor technology.
Opportunities and challenges
Advanced generation IV reactor
To advance nuclear energy towards meeting future energy needs, ten countries agreed on a framework for international cooperation in research for future Generation IV nuclear energy systems at the beginning of this century. Figure 1 shows an overview of the generations of nuclear energy systems. Six nuclear systems were recommended as the most promising Generation IV nuclear systems (USDOE, 2002).
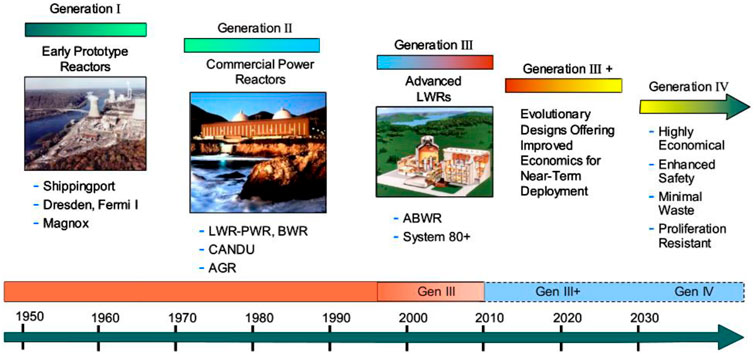
FIGURE 1. Overview of generations of nuclear energy systems (USDOE, 2002).
Supercritical water-cooled reactor-SCWR
The overall plan for the SCWR within GIF is to complete its feasibility phase study around 2020, run a prototypical fueled loop test around 2025, and thus prepare for building a prototype sometime after 2035. The SCWR System Steering Committee (SCC) has four Project Management Boards (PMBs), namely System Integration and Assessment (SI&A, provisional), Thermal Hydraulics and Safety (TH&S), Materials and Water Chemistry (M&C) and Fuel Qualification Testing (FQT, provisional) (Cheng and Liu, 2008). In the past decades, a variety of design schemes for supercritical water-cooled reactors have been proposed internationally, including a variety of different power scales, reactor structures, neutron energy spectra, moderators, fuel assembly forms, working medium circulation methods, and safety system configurations (Schulenberg et al., 2014). Recently, Supercritical Water-cooled Small Modular Reactors (SCW-SMR) have been steadily developed, including overall design principles, main design requirements, and specific design considerations (Zang and Huang, 2021). A new simplification of assembly and core structure was carried out for CSR1000 that significantly simplified the assembly and core structure of SCWR (Yao et al., 2020). The influence of a four-wire structure on the flow and heat transfer process in supercritical water-cooled reactor fuel assembly was verified (Zhao et al., 2022). The thermal and hydraulic characteristics of Al2O3 nanofluid as a coolant in SCWR were studied using a porous media approach (Salehi et al., 2020). Due to improvements in the operating parameters of supercritical water-cooled reactors, the rapid changes in the physical properties of the coolant, and the special design of related structures, the engineering application of this new technology brings challenges in design, thermal hydraulics, and materials. For example, heat flux density or mass flow velocity exceeding design limits can also cause excessive cladding surface temperatures. The non-uniform power distribution and coolant flow distribution in the core coupled with the significant temperature rise of the inlet and outlet coolants easily lead to localized temperature hot spots. Higher fluid temperatures bring higher fuel cladding temperatures, where zirconium alloys are no longer suitable, and new metal materials that can withstand high temperatures must be sought. Dramatic changes in coolant density in the core along the way may induce flow instabilities, as well as changes in neutronic properties and higher fuel cladding surface temperatures. The supercritical water chemistry environment presents challenges for the radiolysis of water and the migration of corrosion products. The mass of the water in the pressure vessel is reduced, so the thermal inertia of the core is reduced, which makes the time scale of the transient process smaller, and puts forward higher requirements for the safety system.
Molten salt reactor
Molten salt reactors (MSRs) are a family of liquid-fueled or solid-fueled fission reactor concepts using fluid molten salt (Behar, 2014). Research on liquid-fueled MSRs has been progressing for more than seven decades, and there has been significant technical progress achieved over this period. Fuel salt cleanup, including pyrochemical separation technologies, extraction of gaseous fission products, and tritium speciation and control have been studied. A novel breed-and-burn molten salt reactor (BBMSR) concept using separate molten salt fuel and coolant in a linear assembly core configuration was proposed (Cuoc et al., 2021). A passive molten salt fast reactor (PMFR) designed as a natural circulation system without any pumps was suggested (Lim et al., 2021). The integral molten salt reactor (IMSR) and molten chloride fast reactor (MCFR) were developed at Terrestrial Energy (Choe et al., 2018; Kovacic and Scott, 2020; Mausolff et al., 2021). The construction of the experimental thorium-based molten salt reactor (TMSR) in Wuwei, China, has been completed, and the trial run is being carried out (Mallapaty, 2021; Zhang et al., 2021).
Research on solid-fueled MSRs or fluoride-salt-cooled high-temperature reactors (FHR) began in 2003 (Forsberg, 2013). Several experiments have been conducted to analyze the heat transfer characteristics of fluoride salts and the corrosion characteristics of structural materials. The conceptual design scheme of FHR and the design of the energy conversion systems have been determined. The primary coolant salt and structural materials have also been selected and several other significant experimental results have been obtained (Jiang et al., 2022). Recently, more and more research institutions have paid attention to FHR. The Kairos Power FHR (KP-FHR) with the available technology of the time was proposed (Bartela et al., 2021; Jiang et al., 2022). The fluoride-salt-cooled high-temperature advanced reactor (FuSTAR) was designed by Xi ’an Jiaotong University (XJTU) (Zhang et al., 2021).
The study of structural materials has become the focus of research and development (R&D) for MSRs. SiC/SiC composites nuclear graphite was developed to enhance corrosion resistance (Kamachi Mudali et al., 2022; Qin et al., 2022). Metallic materials such as Ni-based alloys have been selected and many related corrosion experiments have been performed (Kamachi Mudali et al., 2022).
However, MSRs face several challenges including corrosion of structural materials, instrumentation, and control of liquid salts, requiring a comprehensive understanding of the key physical and chemical properties of the salts, inactive salt testing loops, online fuel processing, mock-up demonstrator without induced fission, and availability of a demonstrator with induced fission (GIF, 2019). Compared with other Generation IV reactors, the unique advantages of MSRs including sustainability, safety, reliability, economic competitiveness, and proliferation resistance will attract more attention (Schulenberg, 2022).
Very-high-temperature gas-cooled reactor
The VHTR is the next step in the evolutionary development of high-temperature gas-cooled reactors. It is a graphite-moderated, helium-cooled reactor with a thermal neutron spectrum (Agency, 2014). The reactor core type of the VHTR can be a prismatic block core such as the Japanese HTTR (Fukaya et al., 2021), or a pebble-bed core such as the Chinese HTR-10 (Mao et al., 2022). While the original approach for VHTR at the start of the Generation IV program focused on very high outlet temperatures and hydrogen production, current market assessments have indicated that electricity production and industrial processes based on high-temperature steam that requires modest outlet temperatures (700–850°C) have the greatest potential for application in the next decade and also reduce the technical risk associated with higher outlet temperatures. As a result, over the past decade, the focus has moved from higher outlet temperature designs such as GT-MHR and PBMR to lower outlet temperature designs such as HTR-PM (Chen and Han, 2021) in China and the NGNP (Sabharwall and Gunnerson, 2009) in the US. The high-temperature, high-neutron dose, and, if using a molten salt coolant, the corrosive environment of the VHTR require materials that exceed the limitations of current nuclear reactors (Clarno et al., 2007). In a study of Generation IV reactors in general (of which there are numerous designs, including the VHTR), Murty and Charit suggest that materials that have high dimensional stability, either with or without stress, maintain their tensile strength, ductility, creep resistant after aging, and are corrosion resistant, are primary candidates for use in VHTRs (Murty and Charit, 2008). Some materials suggested include nickel-base superalloys, silicon carbide, specific grades of graphite, high-chromium steels, and refractory alloys. Further research is being conducted at United States national laboratories as to which specific issues must be addressed in the Generation IV VHTR prior to construction.
Lead-cooled fast reactor
Since lead-cooled fast reactors (LFR) have been conceptualized in the framework of the Generation IV International Forum (GIF), great interest has focused on the development and testing of new technologies related to Heavy Liquid Metal (HLM) nuclear reactors. The basic concept design of LFRs has been developed worldwide, including SVBR (Zrodnikov et al., 2001), BREST (Zhukov et al., 2002), MYRRHA (Maes, 2006), ALFRED (Grasso et al., 2014), CLEAR (Wu, 2016), etc. The validation of the components is ongoing and many experimental validation facilities have been built, including CIRCE (Mansani, 2001), LECOR (Fazio et al., 2003), NACIE-UP (Piazza, 2015), and LIFUS5 (Pesetti et al., 2015). There are still some challenges restricting the development of LFRs. Liquid lead and LBE are both corrosive to the structural materials, and this is the biggest problem restricting the development of LFRs (Zhang and Li, 2008). When steel is in contact with lead or LBE for a long period, elements such as Cr, Ni, and Fe will dissolve therein, causing serious corrosion of structural materials and endangering the integrity of the steel cladding and structures. Operation temperature constraints are another challenge for LFR. The main constraint of the operating temperature is the temperature limit of the applied cladding and structural materials, which is usually 550°C for T91 steel (Bortot et al., 2011). Therefore, some researchers prefer LBE as a coolant to lower the operating temperature slightly and ensure that the peak temperature during the transient state would not exceed the failure temperature of structural materials. Besides, after neutron irradiation, the highly toxic polonium-210, which is volatile and radioactive with a half-life of 138 days, will be produced in lead-based coolants. In pure lead, the production rate of Po-210 is 2–3 orders of magnitude smaller than that in LBE and can be ignored with respect to decay heat (Buongiorno et al., 2004). This is one of the main advantages of pure lead compared with LBE. High Po-210 production in LBE leads to considerable difficulties in operation and maintenance, which also constrains the development of LFRs.
Gas-cooled fast reactor
The GFR is one of the six Generation IV concepts in further development. It combines the advantages of fast spectrum systems for long-term resource sustainability with high temperature for high thermal cycle efficiency and industrial use, such as the generated heat for hydrogen or industrial process. Waste minimization, proliferation resistance, and natural resource optimization are made possible. GFR concepts were first proposed in the 1960s, and have received new attention since 2002. Air, helium, supercritical CO2, or even dissociating gases can be used as coolants. Many countries, such as Germany (Gas Breeder Memorandum, 1969), the United States (General Atomics, 1962), Europe (Gas Breeder Reactor Association, 1970), the Soviet Union (Dissociating coolant, 1970s), the United Kingdom (ETGBR/EGCR, 1970s), and Japan (Prismatic fuel, 1960s), have conducted programs to study it (Rooijen, 2009). The first experimental fast-spectrum gas-cooled reactor, ALLEGRO (Stainsby et al., 2011), is currently being developed by the Czech Republic, France, Hungary, Slovakia, and Poland. However, among the Gen IV concepts, GFR still possesses a relatively low technical maturity (Gougar, 2018). The research areas of contemporary GFR R&D efforts include reactor design, fuel (Hejzlar et al., 2005; Meyer et al., 2007), fuel cycles, structural materials, system optimization, and, most importantly, safety. The main challenge that has to be overcome is developing structural materials that can withstand fast-neutron damage and high temperatures (1,200°C under normal conditions and 1,600°C even 2000°C after a severe accident). Refractory carbide and nitride ceramics have become the most promising materials for fuel fabrication (Fielding et al., 2007). Other problems include low thermal inertia and poor heat removal capability, especially the decay heat removal in post-LOCA situations. Some strategies for decay heat removal have been proposed (Dumaz et al., 2007), while the “guard containment” for fully natural convection or “the batteries for pump” is necessary, because of the high-power density and low thermal capability of the coolant. There has not yet been an acceptable fully passive decay heat removal system for GFR (Pope et al., 2009).
Sodium-cooled fast reactor
Sodium-cooled Fast Reactor (SFR), as one of the most promising Generation-IV nuclear systems (USDOE, 2002; Kelly, 2014), has achieved more than 400 reactor years of operating experience. Its great enhancement of the utilization ratio of uranium, reduction of nuclear waste, use of advanced materials, and innovative design has made a great contribution to the power plant capital cost (Ichimiya et al., 2009), and has attracted worldwide attention to join its development.
The United States built the world’s first sodium-cooled fast reactor, EBR-I, and then built five reactors including EBR-II, Fermi-i, SEFOR, and FFTF (Monti and Toti, 2012). Russia has the most abundant experience in the operation of sodium-cooled fast reactors. It has built and successfully operated 6 famous BOR series (BOR-5, BOR-10, BOR-60) and BN series (BN-350, BN-600, BN-800) sodium-cooled fast reactors (Khrennikov, 2019). France has also made remarkable achievements in the operation of sodium-cooled fast reactors, represented by Rhapsody, Phoenix reactor, and super Phoenix reactor (Niwa et al., 2007). Sodium-cooled fast reactors are an important energy source in Japan (Ito and Yanagisawa, 2012). In 1977 and 1997, Japan built the experimental fast reactor Joyo and the prototype reactor Monju. At present, India has built two sodium-cooled fast reactors. The small fast reactor FBRT, which began operation in 1985, has provided a very rich experience for the construction of India’s sodium-cooled fast reactor. Its prototype fast reactor PFBR, with 500 MW of electric power, has been completed (Mathews et al., 2008). China put forward a three-step strategy for SFR development. As the first step, the experimental fast reactor CEFR achieved full power generation in 2011 (Xu and Yang, 2016). The Chinese demonstration of SFR has been under construction since 2017 and is expected to be critical in 2023.
SFR uses liquid sodium as a coolant, has a wire-wrapped fuel assembly, and is a general pool-type reactor, which is quite different from the traditional pressurized water reactor (PWR), and introduces plenty of challenges (Igor, 2016). The most pressing challenges result from the use of sodium coolant itself. Sodium has a small neutron cross-section and large heat transfer capacity, which is a benefit for a fast neutron spectrum reactor. However, sodium is also a very reactive metal, which might cause severe sodium fires and sodium-water reaction accidents due to sodium leakage (Aoyagi et al., 2021; Cao et al., 2021). Thus, safety protection design for SFR is an issue of high significance. Because sodium has high thermal conductivity and a low Prandtl number, its heat transfer characteristics are quite different from those of conventional fluids. To perform heat transfer experiments using liquid sodium at up to 500°C, and even 600°C temperatures, is dangerous and difficult. Sodium coolant flowing in the reactor pool-type configuration induces abundant new phenomena, such as thermal stratification (Wu et al., 2020), thermal striping, thermal fatigue, and gas entrainment which influence the temperature measurements, in-pile components stress, vessel structural integrity, and natural circulation capacity (Ono et al., 2016). The development of mathematic models, calculation algorithms, analysis code, and V&V experiments (Kim et al., 2016) for the above phenomena in SFR is an urgent issue.
Small modular reactors
Figure 2 shows the SMR designs based on their power range. More than 50 SMR designs are under development for different utilizations at present. The Shidaowan Nuclear Power Plant, which adopted an HTR-PM small modular reactor design, was connected to the grid at the end of 2021 (Guan et al., 2022). Three other industrial demonstration SMRs are in an advanced stage of construction in Argentina (CAREM, an integral PWR) (Nasiri et al., 2022), the People’s Republic of China (ACP100, s), and the Russian Federation (KLT40s, a floating power unit) (Akbari-Jeyhouni et al., 2018). These SMRs were projected to start operation between 2019 and 2022. Furthermore, there are six RITM-200 reactors (an integral PWR) fabricated in the Russian Federation, with four units already installed in the Sibir and Arktika icebreakers, in service in 2020 (Beliavskii et al., 2022). Although remarkable achievements have been fulfilled in various SMR technologies in recent years, some technical challenges still attract considerable attention in the industry and academia. For example, these include control room staffing and human factor engineering for multi-module SMR plants, defining the emergency planning zone source term for multimodule SMR plants, developing new codes and standards, and load-following operability aspects. Some hidden advantages of SMRs like the reduction of public evacuation during an accident or a single operator for multiple modules are under discussion with regulators. Furthermore, although SMRs have lower upfront capital cost per unit, the generating cost of electricity in SMRs will probably be substantially higher than that of large reactors (IAEA, 2018).
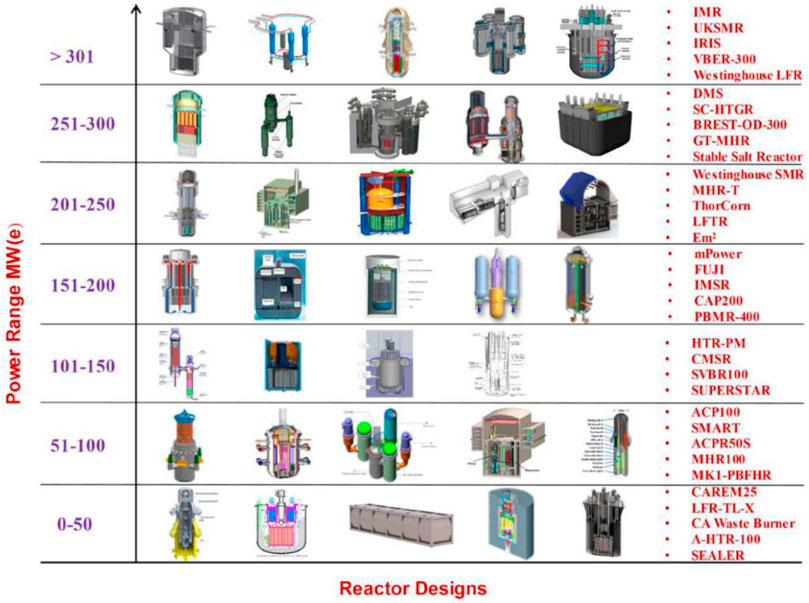
FIGURE 2. SMR designs based on power range (IAEA, 2018).
Accident-tolerant fuel
The accident-tolerant fuels (ATF) design has been proposed since the Fukushima-Daiichi accident and is expected to enhance fuel performance during normal operation, and accident scenarios. Currently, several types of designs are under active development, including advanced fuel pellets (e.g., doped fuel, composite fuel, high-density fuels, and fully ceramic microencapsulated (FCM) fuel), coated cladding (e.g. Cr coated Zircaloy), FeCrAl cladding, and SiC composite cladding (Terrani, 2018). Against conventional UO2 pellets, the Cr2O3 doped fuel shows mitigated fission gas release and pellet-cladding mechanical interaction (PCMI) under reactor transients and has been regarded as a near-term fuel design (Choe et al., 2018). However, the lower uranium density, degraded thermal conductivity, and fuel cracking for doped fuel make it less attractive. In contrast, high-density fuels, consisting of U3Si2 and UN, are much more promising, benefiting from prominently elevated thermal conductivity and uranium content (He et al., 2019a). But it should be noticed that the fuel swelling of U3Si2 and UN is not well understood at present and its poor oxidation resistance with water could hamper its future deployment. Moreover, the much lower specific heat and the melting point of U3Si2 than that of UO2 could significantly reduce safety margins under transient scenarios, especially for reactivity insertion accidents (He et al., 2019a). In addition, FCM fuel is featured for its excellent fission product retaining capability even at temperatures up to 1,600°C, enhanced thermal conductivity, and lower swelling compared to UO2 while showing a small loading volume fraction of fuel, leading to a higher enrichment to achieve a comparable fuel cycle length. Meanwhile, the noticeable stress of the SiC matrix for FCM fuel, even at normal operation, has been observed by simulations (Zhang et al., 2021). As such, investigating fuel kernel material with greater uranium content and fuel optimizing for FCM are required. For Cr-coated cladding, experiments show its reduced ballooning size, enlarged failure time, and significantly reduced oxidation reaction under a simulated loss of coolant accident (Yang et al., 2022). Further, improved behavior concerning debris fretting during an in-pile test was observed. However, investigations into Cr-coated cladding beyond design basis accidents (DBA) are not sufficient and are a necessity for its comprehensive evaluation (Terrani, 2018). Previous results revealed that using the fuel with FeCrAl cladding may have reliable performance both during normal operation and anticipated operational occurrences (Gamble et al., 2017). Furthermore, improved performance can be expected during a LOCA due to its higher strength and high temperature creep resistance. Nevertheless, 4–6 times of thermal neutron capture cross-section of FeCrAl and the potential for enlarged tritium release against that for Zircaloy can be challenges for its further development (Terrani, 2018). As for SiC cladding, specifically, a SiC/SiC Ceramic Matrix Composite (CMC) with chemically vapor deposited (CVD) SiC at the outer surface, owing to its higher mechanical strength and much-improved oxidation resistance at very high temperatures (>1,200 °C), is another promising ATF concept (He et al., 2019b). However, the failure risk of the CVD SiC under PCMI may not be accepted from a full-core perspective (Choe et al., 2018). In the meantime, the thermal shock induced at RIA may lead to a 0.5 m length of cladding being at risk of failure, which can be a threat to its ultimate employment (Choe et al., 2018).
Digital reactors and severe accidents
Severe accidents pose a fatal threat to the safety of nuclear power plants and surrounding residents, such as the TMI-2 accident, the Chernobyl accident, and the Fukushima accident. A severe accident (SA) is defined as an incident involving the melting of the reactor core and the release of fission products from the fuel and the associated risks involved with these processes (Zhang et al., 2015). Numerous experimental and analytical studies had been conducted on SAs during the past five decades, and SA research has provided sufficient information to resolve most of the issues that have been identified for an SA to occur LWRs (Bentaïb et al., 2007; Sehgal, 2010; Zhang et al., 2015). However, many issues are still unresolved during in- and ex-vessel accident progressions, such as uncertainties relating to the modeling codes, phenomena identification, and ranking table for In-Vessel accident progression, and Ex-Vessel molten corium behavior and coolability (Carénini et al., 2020).
In recent years, in order to identify and separate the risks with respect to the importance of a physical process, and to define the physical processes or parameters which could be considered as independent of the other ones, IAEA conducted the Coordinated Research Project on “Developing a phenomena identification and ranking table (PIRT) and a validation matrix, and performing a benchmark for In-Vessel Melt Retention” from 1 July 2020 to 1 October 2024 (IAEA, 2020). The purpose of this CRP is to set up a common phenomena pool and identify the uncertainties and phenomena/variables with the highest (or lowest) importance. These are phenomena for which modeling and codes are necessary in order to be able to provide a reasonable assessment. Ex-vessel molten corium behavior and cooling (EVCC) has been confirmed to be one of the highest research and development priority areas. Cooling the corium released from a failed Reactor Pressure Vessel (RPV) is a possible mitigative measure of the consequences of severe accidents and aims at collecting, spreading, and cooling the corium outside the RPV. Quality numerical simulations and the availability of experimental data are needed for the validation of individual models and codes. Several large-scale experiments and tests with prototypic materials within the international community have been untaken to provide data to facilitate modeling improvements, decreasing the uncertainties of the predictions, and significantly improving the validation of associated codes and models (Miassoedov, 2022).
Numerical reactor technology
With the rapid development of supercomputers and numerical computation methods, it is possible to carry out multi-physical, multi-scale, and multi-process coupling computer analysis of the reactor. This is the concept of numerical reactor technology. In the past decades, numerical reactor technology has become a research hotspot in the world and most countries have released their own numerical reactor research plans. In the I-NERI program initiated by the United States in 2002, the United States and South Korea launched a numerical reactor plan (Gail, 2000; Peter, 2012), which first proposed the concept of a high-fidelity numerical reactor. I-NERI has performed a lot of work around Reactor Concepts RD&D (Reactor Concepts Research, Development, and Demonstration) and FCR&D (Fuel Cycle Research and Development). Based on the program, South Korea has developed a three-dimensional full reactor neutron transport calculation program, DeCART (Joo et al., 2004). DeCART (Cho et al., 2019) considers the feedback of the internal temperature and power distribution of the fuel rod carefully, but the thermal coupling calculation of the whole core of a large commercial reactor is not realized because of the huge calculation cost of the CFD method. Currently, South Korea uses MATRA (a subchannel program) instead of the CFD method to realize the coupling calculation of multi-physical fields in the whole core (Park et al., 2020). In 2010, the United States Department of Energy established the CASL program (ANS, 2020) and the NEAMS program (Lefebver et al., 2020). It aims to predict the performance and safety of nuclear reactors more accurately through advanced simulation technology, and apply this prediction to the United States nuclear industry. At present, the high-fidelity pressurized water reactor system, VERA, has been successfully established, and the calculation and analysis of six key physical phenomena set at the beginning of the CASL plan have been realized based on VERA. The NEAMS program is another project established by the U.S. Department of Energy, which has a broader scope than the CASL program. With the support of the U.S. Department of Energy, NEAMS is now the most important support program for the development of nuclear reactor numerical simulation technology in the United States. In addition to the United States, Europe has also conducted investigations since 2002. In 2005, the NURE series plans, the CORTEX plan, and the HPMC/McSAFE plan have been carried out, and these plans represent a build-up of high-fidelity numerical simulation tools for Europe. The NURE series plans are important projects in the research of advanced numerical methods in Europe, including NURESIM, NURISP, and NURESAFE. All the programs and models from this series of projects are concentrated on the multi-physical coupling platform SALOME (CEA, EDF R&D, 2019). The HPMC/McSAFE plan (Demazi-re et al., 2019) aims to develop high-fidelity simulation analysis tools, and some application analysis has been implemented on LWRs and SMRs. China has carried out the development of a numerical reactor system supported by a major project of the Ministry of Science and Technology. The goal is to develop reactor simulation software for E-class supercomputing and realize demonstration applications. At present, the development of the main modules of the large-scale parallel numerical reactor prototype system, CVR1.0, has been initially completed, and preliminary demonstration application has been performed (Yang et al., 2021). Numerical reactor technology is an integrated technology. The success of numerical reactor technology is based on relatively complete physical models, including reactor physics, thermal-hydraulics, fuel performance analysis, and so on. The development of accurate models requires not only in-depth theoretical work but also a large number of basic experimental data, which brings great challenges to the development and application of numerical reactors. Therefore, more additional works are necessary for the aspects of computing function, multi-physical coupling and model validation, simulation of key physical phenomena in the core, collaborative research, and application promotion during the development of numerical reactors in the future (Figures 3, 4) (Marcus, 2000; Ahmed et al., 2007; Pioro, 2016).
Author contributions
The author confirms being the sole contributor of this work and has approved it for publication.
Acknowledgments
The author is grateful to his colleague DL Zhang, YW Wu, YP Zhang, RH Chen, MJ Wang, CL Wang, J Zhang, K Zhang, KL Guo for their valuable contribution and discussions. The author also thanks Mr. HK Yang for his helpful work in proof correction.
Conflict of interest
The author declares that the research was conducted in the absence of any commercial or financial relationships that could be construed as a potential conflict of interest.
Publisher’s note
All claims expressed in this article are solely those of the authors and do not necessarily represent those of their affiliated organizations, or those of the publisher, the editors and the reviewers. Any product that may be evaluated in this article, or claim that may be made by its manufacturer, is not guaranteed or endorsed by the publisher.
References
Ahmed, B., Gérard, D., William, R., Hervé, B., Cataldo, C., Michel, D., et al. Research and development with regard to severe accidents in pressurised water reactors: Summary and outlook. Rapport IRSN-2007/83, Rapport CEA-2007/351, 2007.
Akbari-Jeyhouni, R., Rezaei Ochbelagh, D., Maiorino, J. R., D'Auria, F., and Stefani, G. L. d. (2018). The utilization of thorium in small modular reactors – Part I: Neutronic assessment. Ann. Nucl. Energy 120, 422–430. doi:10.1016/j.anucene.2018.06.013
ANS (2020). Casl: Consortium for advanced simulation of light water reactors, CASL phase Ⅱ summary report [R]. USA: ANS.
Aoyagi, M., Takata, T., and Uno, M. (2021). Numerical modeling of radiation heat transfer from combusting droplets for a sodium fire analysis. Nucl. Eng. Des. 380, 111258. doi:10.1016/j.nucengdes.2021.111258
Bartela, Ł., Gładysz, P., Andreades, C., Qvist, S., and Zdeb, J. (2021). Techno-economic assessment of coal-fired power unit decarbonization retrofit with KP-FHR small modular reactors. Energies 14, 2557. doi:10.3390/en14092557
Behar, C. (2014). Technology roadmap update for generation IV nuclear energy systems [R]. Brussels, Belgium: OECD.
Beliavskii, S., Anikin, N., Alhassan, S., Kudeev, S., and Nesterov, V. (2022). Effect of fuel nuclide composition on the fuel lifetime of the RITM-200 reactor unit. Ann. Nucl. Energy 173, 109105. doi:10.1016/j.anucene.2022.109105
Bentaïb, A., Ducros, G., Ranval, W., et al. (2007). Research and development with regard to severe accidents in pressurized water reactors: Summary and outlook. Rapport IRSN-2007/83, Rapport CEA-2007/351.
Bortot, S., Moisseytsev, A., Sienicki, J. J., and Artioli, C. (2011). Core design investigation for a SUPERSTAR small modular lead-cooled fast reactor demonstrator. Nucl. Eng. Des. 241, 3021–3031. doi:10.1016/j.nucengdes.2011.04.012
Buongiorno, J., Loewen E, P., Czerwinski, K., and Larson, C. (2004). Studies of polonium removal from molten lead-bismuth for lead-alloy-cooled reactor applications. Nucl. Technol. 147, 406–417. doi:10.13182/nt04-a3539
Cao, H., Sun, P., Luo, G., Wang, K., and Bai, X. (2021). Large-leak sodium–water reaction accident analysis of sodium- cooled fast reactor. Prog. Nucl. Energy 142, 104010. doi:10.1016/j.pnucene.2021.104010
Carénini, L., Fichot, F., Bakouta, N., Filippov, A., Le Tellier, R., Viot, L., et al. (2020). Main outcomes from the IVR code benchmark performed in the European IVMR project. Ann. Nucl. Energy 146, 107612. doi:10.1016/j.anucene.2020.107612
Chen, F., and Han, Z. (2021). Steady-state thermal fluids analysis for the HTR-PM equilibrium core. Int. J. Adv. Nucl. React. Des. Technol. 3, 11–17. doi:10.1016/j.jandt.2021.04.001
Cheng, X., and Liu, X. (2008). Current situation and trend of R&D of supercritical water-cooled reactor at home and abroad. Atomic Energy Sci. Technol. Chin. 42 (2), 167–172.
Cho, J. Y., Han, T. Y., Park, H. J., Hong, S. G., and Lee, H. C. (2019). Improvement and verification of the DeCART code for HTGR core physics analysis. Nucl. Eng. Technol. 51 (1), 13–30. doi:10.1016/j.net.2018.09.004
Choe, J., Ivanova, M., LeBlanc, D., Mohaptra, S., and Robinson, R. (2018). Fuel cycle flexibility of terrestrial ENERGY’S integral molten salt reactor (IMSR®) [C]. Saskatoon, SK, Canada: Sheraton Cavalier Hotel.
Clarno, K., Forsberg, C., Gehin, J., Slater, C., Carbajo, J., Williams, D., et al. (2007). Trade studies for the liquid-salt-cooled very high-temperature reactor: Fiscal year 2006 progress report.
Cuoc, E., Shwageraus, E., Kasam, A., and Scott, I. (2021). Core design of breed & burn molten salt fast reactor [R], EPJ Web of Conferences. EDP Sciences France. doi:10.1051/epjconf/202124701004
Demazi-re, C., Sanchez-espinoza, V. H., and Chanaron, B. (2019). “Advanced numerical simulation and modelling for reactor safety: Contributions from the CORTEX, HPMC, McSAFE and NURESAFE projects [C],” in Proceeding of the 9th European Commission Conference on EURATOM Research and Training in Safety of Reactor Systems, Pitesti, Romania. [s. n.].
Dumaz, P., Allegre, P., Bassi, C., Cadiou, T., Conti, A., Garnier, J., et al. (2007). Gas-cooled fast reactors-status of CEA preliminary design studies. Nucl. Eng. Des. 237, 1618–1627. doi:10.1016/j.nucengdes.2007.03.018
Fazio, C., Ricapito, I., Scaddozzo, G., and Benamati, G. (2003). Corrosion behaviour of steels and refractory metals and tensile features of steels exposed to flowing PbBi in the LECOR loop. J. Nucl. Mater. 318, 325–332. doi:10.1016/s0022-3115(03)00009-6
Fielding, R., Meyer, M. K., Jue, J. F., and Gan, J. (2007). Gas-cooled fast reactor fuel fabrication. J. Nucl. Mater. 371, 243–249. doi:10.1016/j.jnucmat.2007.05.011
Forsberg, C. (2013). Hydrogen, nuclear energy, and the advanced high-temperature reactor. Int. J. Hydrogen Energy 28, 1073–1081.
Fukaya, Y., Goto, M., Inoi, H., Ishitsuka, E., Iyoku, T., Kunitomi, K., et al. (2021). “4 - operation of HTTR [B],” in High temperature gas-cooled reactors. Editors T. Takeda, and Y. Inagaki (Academic Press), 257–311.
Gamble, K. A., Barani, T., Pizzocri, D., Hales, J. D., Terrani, K. A., and Pastore, G. (2017). An investigation of FeCrAl cladding behavior under normal operating and loss of coolant conditions. J. Nucl. Mater. 491, 55–66.
Gougar, H. D. (2018). Gas-cooled fast reactor research and development roadmap. Idaho Falls, ID (United States): Idaho National Lab.
Grasso, G., Petrovich, C., Mattioli, D., Artioli, C., Sciora, P., Gugiu, D., et al. (2014). The core design of ALFRED, a demonstrator for the European lead-cooled reactors. Nucl. Eng. Des. 278, 287–301. doi:10.1016/j.nucengdes.2014.07.032
Guan, C., Chai, X., Zhang, T., and Liu, X. (2022). Transient coupling analysis of loss-of-coolant accidents in HTR-PM based on CFD approaches. Ann. Nucl. Energy 173, 109097. doi:10.1016/j.anucene.2022.109097
He, Y., Shirvan, K., Wu, Y., and Su, G. (2019a). Fuel performance optimization of U3Si2-SiC design during normal, power ramp and RIA conditions. Nucl. Eng. Des. 353, 110276.
He, Y., Shirvan, K., Wu, Y., and Su, G. (2019b). Integrating a multi-layer deformation model in FRAPTRAN for accident Tolerant fuel analysis. Ann. Nucl. Energy 133, 441–454.
Hejzlar, P., Pope, M. J., Williams, W. C., and Driscoll, M. J. (2005). Gas cooled fast reactor for generation IV service. Prog. Nucl. Energy 47, 271–282. doi:10.1016/j.pnucene.2005.05.077
IAEA (2020). The Coordinated Research Project on “Developing a phenomena identification and ranking table (PIRT) and a validation matrix, and performing a benchmark for In-Vessel Melt Retention”. IAEA. CRP J46002, 2020-2024.
Ichimiya, M., Singh, B. P., Rouault, J., Hahn, D., and Abram, T. (2009). “Overview of R&D activities for the development of a generation IV sodium-cooled fast reactor system[C],” in Proceeding of the GIF Symposium, Paris, France, September 2009, 213.
Ito, K., and Yanagisawa, T. (2012). “Last twenty years experiences with fast reactors in Japan[C],” in Proceedings of an International Conference on Fast Reactors and Related Fuel Cycles: Challenges and Opportunities (FR09), Tokaimura, Japan, Mar 2012, 347–362.
Jiang, D., Zhang, D., Li, X., Wang, S., Wang, C., Qin, H., et al. (2022). Fluoride-salt-cooled high-temperature reactors: Review of historical milestones, research status, challenges, and outlook. Renew. Sustain. Energy Rev. 161, 112345. doi:10.1016/j.rser.2022.112345
Joo, H. G., Cho, J. Y., Kim, K. S., Lee, C. C., and Zee, S. Q. (2004). Methods and performance of a three-dimensional whole-core transport code DeCART[C]. Chicago: PHYSOR. [s. n.].
Kamachi Mudali, U., Subba Rao, T., Ningshen, S., Pillai, R. G., George, R. P., and Sridhar, T. M. (2022). A treatise on corrosion science, engineering and technology [M]. Singapore: Springer Nature Singapore.
Kelly, J. E. (2014). Generation IV international Forum: A decade of progress through international cooperation. Prog. Nucl. Energy 77 (2), 240–246. doi:10.1016/j.pnucene.2014.02.010
Khrennikov, N. (2019). “Russian Regulatory Body Approaches for licensing of advanced reactors and related activities[C],” in Eighth Joint IAEA-GIF Technical Meeting/Workshop on the Safety of Liquid Metal Cooled Fast Reactors, Vienna, Austria, Mar 2019.
Kim, J. B., Jeong, J. Y., Lee, T. H., Kim, S., Euh, D. J., and Joo, H. K. (2016). On the safety and performance demonstration tests of prototype Gen-IV sodium-cooled fast reactor and validation and verification of computational codes. Nucl. Eng. Technol. 48 (5), 1083–1095. doi:10.1016/j.net.2016.08.003
Kovacic, D., and Scott, L. (2020). Final report for the cooperative research and development agreement (crada) NFE-18-07194 with terrapower llc [R]. Oak Ridge: Oak Ridge National Laboratory.
Lefebver, R. A., Langley, B. R., Miller, P., Delchini, M., and Baird, M. L. (2020). NEAMS workbench status and capabilities[R]. USA: ORNL.
Lim, J., Shin, D., Kim, T., Park, J. H., Lee, J., Cho, Y. S., et al. (2021). Preliminary analysis of the effect of the gas injection on natural circulation for molten salt reactor type small modular reactor system operated without a pump [R]. Daejeon, Korea: Korean.
Maes, D. (2006). Mechanical design of the small-scale experimental ADS: Myrrha. Energy Convers. Manag. 47, 2710–2723. doi:10.1016/j.enconman.2006.02.009
Mallapaty, S. (2021). China prepares to test thorium-fuel led nuclear reactor. Nature 597, 311–312. doi:10.1038/d41586-021-02459-w
Mansani, L. (2001). The CIRCE test facility [C]. ANS winter meeting AccApp ADTTA’01. Reno, Nevada, USA.
Mao, C., Yin, Z., Zhang, L., and Ding, H. (2022). Analysis of gamma spectra from burnup measurement in HTR-10. Appl. Radiat. Isotopes 186, 110298. doi:10.1016/j.apradiso.2022.110298
Marcus, G. H. (2000). Considering the next generation of nuclear power plants. Prog. Nucl. Energy 37 (1–4), 5–10. doi:10.1016/S0149-1970(00)00016-0
Mathews, T. S., Ramakrishnan, M., Parthasarathy, U., Arul, A. J., and Kumar, C. S. (2008). Functional reliability analysis of safety grade decay heat removal system of Indian 500 MWe PFBR. Nucl. Eng. Des. 238 (9), 2369–2376. doi:10.1016/j.nucengdes.2008.02.012
Mausolff, Z., DeHart, M., and Goluoglu, S. (2021). Design and assessment of a molten chloride fast reactor. Nucl. Eng. Des. 379, 111181. doi:10.1016/j.nucengdes.2021.111181
Meyer, M. K., Fielding, R., and Gan, J. (2007). Fuel development for gas-cooled fast reactors. J. Nucl. Mater. 371, 281–287. doi:10.1016/j.jnucmat.2007.05.013
Miassoedov, A. (2022). IAEA technical meeting on ex-vessel molten corium behaviour and coolability. IAEA.
Monti, S., and Toti, A. (2012). “An overview of the activities carried out by the IAEA technical working group on fast reactors[C],” in Proceedings of the 2012 International Congress on Advances in Nuclear Power Plants-ICAPP'12, Chicago, IL, United States, Jun 2012, 787–792.
Murty, K. L., and Charit, I. (2008). Structural materials for Gen-IV nuclear reactors: Challenges and opportunities. J. Nucl. Mater. 383, 189–195. doi:10.1016/j.jnucmat.2008.08.044
Nasiri, S., Ansarifar, G. R., and Esteki, M. H. (2022). Design of the CAREM nuclear reactor core with dual cooled annular fuel and optimizing the thermal-hydraulic, natural circulation, and neutronics parameters. Ann. Nucl. Energy 169, 108939. doi:10.1016/j.anucene.2021.108939
Niwa, H., Aoto, K., and Morishita, M. (2007). “Current status and perspective of advanced loop type fast reactor in fast reactor cycle technology development project[C],” in Proceedings of GLOBAL 2007 conference on advanced nuclear fuel cycles and systems, Boise, United States, Sep 2007, 62–70.
Ono, A., Kamide, H., Kobayashi, J., Doda, N., and Watanabe, O. (2016). An experimental study on natural circulation decay heat removal system for a loop type fast reactor. J. Nucl. Sci. Technol. 53 (9), 1385–1396. doi:10.1080/00223131.2015.1121844
Park, H. J., Kim, S. J., Kwon, H., and Cho, J. Y. (2020). BEAVRS benchmark analyses by DeCART stand-alone calculations and comparison with DeCART/MATRA multi-physics coupling calculations. Nucl. Eng. Technol. 52 (9), 1896–1906. doi:10.1016/j.net.2020.02.015
Pesetti, A., Del Nevo, A., and Forgione, N. (2015). Experimental investigation and SIMMER-III code modelling of LBE–water interaction in LIFUS5/Mod2 facility. Nucl. Eng. Des. 290, 119–126. doi:10.1016/j.nucengdes.2014.11.016
Peter, B. L. (2012). International nuclear energy research initiative: Fiscal year 2012 annual report[R]. USA: Department of Energy Office of Nuclear Energy.
Piazza, I. D. (2015). NACIE-UP: AN heavy liquid-metal loop for mixed convection experiments with instrumented PIN bundle [R].
Pope, M. A., Lee, J. I., Hejzlar, P., and Driscoll, M. J. (2009). Thermal hydraulic challenges of gas cooled fast reactors with passive safety features. Nucl. Eng. Des. 239, 840–854. doi:10.1016/j.nucengdes.2008.10.023
Qin, Y., Liu, C., Zheng, C., Chen, B., Zhang, J., Feng, S., et al. (2022). The corrosion behavior of CVD SiC coatings on SiCf/SiC composites in a simulated molten salt reactors environment. Corros. Sci. 204, 110411. doi:10.1016/j.corsci.2022.110411
Rooijen, W. F. G. (2009). Gas-cooled fast reactor: A historical overview and future outlook. London, England: Science and Technology of Nuclear Installations.
Sabharwall, P., and Gunnerson, F. (2009). Engineering design elements of a two-phase thermosyphon for the purpose of transferring NGNP thermal energy to a hydrogen plant. Nucl. Eng. Des. 239, 2293–2301. doi:10.1016/j.nucengdes.2009.06.022
Salehi, D., Jahanfarnia, G., and Zarifi, E. (2020). Thermal-hydraulic analysis of Al2O3 nanofluid as a coolant in Canadian supercritical water reactor by porous media approach. Nucl. Eng. Des. 368, 110825. doi:10.1016/j.nucengdes.2020.110825
Schulenberg, T., Leung, L., and Oka, Y. (2014). Review of R&D for supercritical water cooled reactors. Prog. Nucl. Energy 77, 282–299. doi:10.1016/j.pnucene.2014.02.021
Schulenberg, T. (2022). The fourth generation of nuclear reactors: Fundamentals, Types, and Benefits Explained [M]. Berlin, Heidelberg: Springer Berlin Heidelberg.
Sehgal, B. R. (2010). Status of severe accident research for resolution of LWR safety issues, 8th international topical meeting on nuclear thermal- hydraulics, operation and safety. Shanghai, China.
Stainsby, R., Peers, K., Mitchell, C., Poette, C., Mikityuk, K., and Somers, J. (2011). Gas cooled fast reactor research in Europe. Nucl. Eng. Des. 241, 3481–3489. doi:10.1016/j.nucengdes.2011.08.005
Terrani, K. A. (2018). Accident tolerant fuel cladding development: Promise, status, and challenges. J. Nucl. Mater. 501, 13–30.
USDOE (2002). A technology roadmap for generation IV nuclear energy systems. Philos. Rev. 66 (2), 239–241.
Wu, Y. (2016). CLEAR-S: An integrated non-nuclear test facility for China lead-based research reactor. Int. J. Energy Res. 40, 1951–1956. doi:10.1002/er.3569
Wu, Z., Lu, C., Morgan, S., Bilbao y Leon, S., and Bucknor, M. (2020). A status review on the thermal stratification modeling methods for Sodium-cooled Fast Reactors. Prog. Nucl. Energy 125, 103369. doi:10.1016/j.pnucene.2020.103369
Xu, M., and Yang, H. (2016). Safety properties of sodium-cooled fast reactors. Physics 45 (9), 561–568. (In Chinese). doi:10.7693/wl20160902
Yang, W., Hu, C., Liu, T., Wu, M., Wang, Z., and Jiang, Q. (2021). Research progress of virtual reactor system development and demonstration application. Atomic Energy Sci. Technol. 55 (9), 1537–1546. doi:10.7538/yzk.2021.youxian.0707
Yang, J., Steinbrück, M., Tang, C., Große, M., Liu, J., Zhang, J., et al. (2022). Review on chromium coated zirconium alloy accident tolerant fuel cladding. J. Alloys Compd. 895, 162450.
Yao, L., Xia, B., Lu, D., Wang, L., Li, X., Wang, S., et al. (2020). Research on simplified assembly and core structure design of SCWR. Nucl. Power Eng. Chin. 41 (4), 45–49. doi:10.13832/j.jnpe.2020.04.0045
Zang, J., and Huang, Y. (2021). Supercritical water-cooled small modular reactor R&D. Nucl. Power Eng. Chin. 42 (6), 72–76. doi:10.13832/j.jnpe.2021.06.0072
Zhang, J., and Li, N. (2008). Review of the studies on fundamental issues in LBE corrosion. J. Nucl. Mater. 373, 351–377. doi:10.1016/j.jnucmat.2007.06.019
Zhang, Y. P., Niu, S. P., Zhang, L. T., Qiu, S. Z., Su, G. H., and Tian, W. X. (2015). A review on analysis of LWR severe accident. J. Nucl. Eng. Radiat. Sci. 1 (4). doi:10.1115/1.4030364
Zhang, C., Wu, Y., He, Y., Li, Y., Liu, J., Zhang, H., et al. (2021). Investigation on thermo-mechanical performance of fully ceramic microencapsulated fuel. J. Nucl. Mater. 556, 153171. doi:10.3969/j.issn.1009-2412.2021.04.003
Zhao, Z., Shi, J., Sun, B., Chen, Y., Wu, W., and Fu, H. (2022). The influence of four-wire structure on the flow and heat transfer process in supercritical water-cooled reactor fuel assembly. Appl. Therm. Eng. 203, 117941. doi:10.1016/j.applthermaleng.2021.117941
Zhukov, A. V., Kuzina, Y. A., Sorokin, A. P., Leonov, V. N., Smirnov, V. P., and Sila-Novitskii, A. G. (2002). An experimental study of heat transfer in the core of a BREST-OD-300 reactor with lead cooling on models. Therm. Eng. 49:175–184. (English translation of Teploenergetika).
Keywords: generation IV reactor design, small modular reactors, accident-tolerant fuel, nuclear reactor severe accident, digital reactor technology
Citation: Tian W (2022) Grand challenges in advanced nuclear reactor design. Front. Nucl. Eng. 1:1000754. doi: 10.3389/fnuen.2022.1000754
Received: 22 July 2022; Accepted: 14 October 2022;
Published: 09 December 2022.
Edited and reviewed by:
Sergei Dudarev, United Kingdom Atomic Energy Authority, United KingdomCopyright © 2022 Tian. This is an open-access article distributed under the terms of the Creative Commons Attribution License (CC BY). The use, distribution or reproduction in other forums is permitted, provided the original author(s) and the copyright owner(s) are credited and that the original publication in this journal is cited, in accordance with accepted academic practice. No use, distribution or reproduction is permitted which does not comply with these terms.
*Correspondence: Wenxi Tian, d3h0aWFuQG1haWwueGp0dS5lZHUuY24=