- Shanghai Key Lab for Urban Ecological Processes and Eco-Restoration, School of Ecological and Environmental Sciences, East China Normal University, Shanghai, China
Water hyacinth was used as substrate for bioethanol production in the present study. Combination of acid pretreatment and enzymatic hydrolysis was the most effective process for sugar production that resulted in the production of 402.93 mg reducing sugar at optimal condition. A regression model was built to optimize the fermentation factors according to response surface method in saccharification and fermentation (SSF) process. The optimized condition for ethanol production by SSF process was fermented at 38.87°C in 81.87 h when inoculated with 6.11 ml yeast, where 1.291 g/L bioethanol was produced. Meanwhile, 1.289 g/L ethanol was produced during experimentation, which showed reliability of presented regression model in this research. The optimization method discussed in the present study leading to relatively high bioethanol production could provide a promising way for Alien Invasive Species with high cellulose content.
Introduction
The major source of energy comes from non-renewable fossil fuel that caused global warming, environmental degradation, and human health problems (Patil et al., 2014). The growing energy demands encourage scientists to explore low cost, environmental friendly and sustainable alternative energy sources (Cheng et al., 2015a,b; Lin et al., 2015; Merino-Pérez et al., 2015).
Bioethanol, as a clean, safe and renewable resource, is considered as a potential alternative to fossil fuels (Rezania et al., 2015). However, it is mainly produced from either starch- or sugar-rich crops that may raise land competition between food production and biomass energy utilization, and can lead to deforestation (Zhao and Xia, 2010; Das et al., 2015). Hence, lignocellulose is gradually considered as more attractive because of its low cost and easy availability (Valentine et al., 2012; Bayrakci and Koçar, 2014).
Water hyacinth (Eichornia crassipes), which is originated from Amazon basin (Barrett, 1989), is listed as one of the world's most invasive and recalcitrant weeds because of its availability in large quantities, extraordinary adaptive ability, and remarkable growth rate (Hu et al., 2015). It grows at an extreme rapid rate and produce almost 2 tons of biomass per acre and its population doubles every 5–15 days (Craft et al., 2003). Water hyacinth is usually blamed for depleting nutrients and oxygen from water bodies, increasing evapotranspiration, and reducing biodiversity, which could influence fishing, shipping, irrigation, and destroy aquatic eco-system (Malik, 2007; Guerrero-Coronilla et al., 2015). This species was brought to mainland China in the 1930s. With its extremely high growth rate, this floating plant has infested many aquatic systems in 19 provinces of China (Xia et al., 2013). Moreover, water hyacinth is considered as an attractive raw material for the bioenergy production including bioethanol, hydrogen, and biochar in many tropical regions of the world among various types of lignocellulosic substances (Masto et al., 2013; Buller et al., 2015; Jiu et al., 2015; Zhang et al., 2015).
Due to its abundant availability and high carbohydrate contents, water hyacinth highly satisfies the requirements as a potential substrate for bioethanol production (Ganguly et al., 2012; Rezania et al., 2015). The dry biomass of water hyacinth mainly comprises low lignin (7–26%) and high amount of cellulose (18–31%) and hemicellulose (18–43%), which can be easily hydrolyzed to reducing sugars and then fermented to bioethanol by effective yeasts (Bergier et al., 2012). However, there are many problems hindering the effective enzymatic hydrolysis. One of these problems is the lignin seal that prevents penetration by degrading enzymes (Taniguichi et al., 2005). Thus, many researchers tried to seek effective pretreatment methods to break the lignin seal (Forrest et al., 2010; Ma et al., 2010; Gao et al., 2013; Yan et al., 2015). Another bottleneck is the feedback inhibition of cellobiose on fermentation process after hydrolysis during bioethanol production (Guan et al., 2013; Ha et al., 2013; Cheng et al., 2015a,b). The most effective method to solve the feedback inhibition problem is simultaneous saccharification and fermentation (SSF), a process in which enzymatic process hydrolyzes lignocelluloses to sugars and ferments to bioethanol simultaneously, being already used in many lignocelluloses fermentation systems (Huang et al., 2013; Soares and Gouveia, 2013). However, there is no detail report on SSF process using water hyacinth as substrate.
In the present study, water hyacinth was collected from wastewater and pretreated. The major factors affecting the efficiency of SSF process were analyzed by response surface method (RSM) that provided an optimal fermentation parameter for bioethanol production by water hyacinth.
Materials and Methods
Materials and Microorganism
Water hyacinth was obtained from Huangpu River, Minhang District, Shanghai, China. It was washed three times with tap water to remove extraneous matter and roots, and then smashed by grinder below 40 meshes for further use.
Cellulase extracted from Trichoderma viride was bought from Sinopharm Chemical Reagent Co., Ltd, Shanghai. The activity of cellulase is 15000 U/g.
Saccharomyces cerevisiae was preserved in Shanghai Key Lab for Urban Ecological Processes and Eco-Restoration at East China Normal University (SHUES, ECNU), Shanghai. To prepare the yeast inoculum, one loop of S. cerevisiae spores was suspended in fluid enrichment medium (10 g/L yeast extract, 20 g/L peptone and 20 g/L glucose) for 24 h. The exponential inoculum was centrifuged at 4000 r/min for 5 min, followed by washing the precipitate by deionized water. After calculating dry weight of the yeast, 2 g/L yeast inoculum was prepared finally.
Pretreatment of Water Hyacinth
Smashed water hyacinth was pretreated before enzymatic hydrolysis. Acid pretreatment (1% H2SO4 at 100°C for 30 min when solid-liquid ratio was 1:30), alkaline pretreatment (0.5% NaOH at 40°C for 30 min when solid-liquid ratio was 1:16) and microwave-alkaline combined pretreatment (150 W microwave combined with 0.5% NaOH for 0.5 min when solid-liquid ratio was 1:16) were used after optimization by orthogonal experiment. The specific conditions of the orthogonal experiment followed our previous research (Wang, 2015). Reducing sugars in hydrolysates were also determined.
Enzymatic Hydrolysis
The solid residue after pretreatment was collected by filtration and washed extensively with distilled water until neutral pH. Subsequently, this pretreated water hyacinth was dried in the oven at 70°C to maintain a constant weight to be used as the substrate for enzymatic hydrolysis.
Cellulase dosage, hydrolysis temperature and time were selected as three factors for single factor experiment. The reducing sugars in hydrolysates were detected to determine an optimum enzymatic hydrolysis process.
Saccharification and Fermentation Process
One gram smashed water hyacinth sample was firstly pretreated by acid (1% H2SO4) at the optimal condition followed by alkali (6 mol/L NaOH) was used to regulate pH value to 5.3. After that the mixture was autoclaved at 121°C for 20 min, and 0.05 g cellulase with 0.05 g CaCl2 were added to the pretreated sample to hydrolyze. Meanwhile, yeast inoculum was added into pretreated sample according to the experimental design along with 2.0 g/L yeast extract, 0.2 g/L (NH4)2HPO4 and 0.02 g/L MgSO4. Nitrogen was aerated to exclude air in the system, and SSF was carried out at constant temperature shaker with the speed of 120 rpm. After SSF process, the fermented samples were centrifuged at 5000 rpm for 8 min and supernatant was used for bioethanol determination.
Response Surface Method
The main factors that affect ethanol production, including fermentation temperature (X1), fermentation time (X2) and inoculums dosage (X3), were chosen to be optimized by RSM. Seventeen group experiments designed by Box-Behnken were conducted to seek the highest ethanol production, which were listed in Table 2.
Analytical Methods
The moisture content of water hyacinth was detected by oven drying method at 105°C for three times, and the average value was calculated ultimately. Cellulose, hemicelluloses and lignin contents in water hyacinth were determined by the methods of Goering and Van soest (1970). The DNS method was used for the measurement of total reducing sugar contents (Miller, 1959).
The bioethanol production during fermentation was measured using headspace sampling Gas Chromatography (GC, Agilent 7890A) method. HS-9A was selected as heated static headspace. The treated samples were examined by GC on a HP-5MS capillary column (30 m × 0.25 mm × 0.25 μm) with FID detector. Nitrogen was used as carrier gas. All the experiments and sample injection were performed in triplicates, and the average values were represented and used ultimately. The conditions were as follow:
(1) Static headspace: Vial 70°C; TR Line 90°C; Loop 80°C, 1 mL; Loop Fill Time 1 min; Ressuriz Time 0.2 min; Vial EQ Time 10 min.
(2) GC: The inlet temperature for GC was kept at 180°C with a Split ratio of 30:1. The oven temperature was kept at 180°C for 5 min at a flow rate of 2 mL-min−1.
(3) FID: Temperature 80°C; Hydrogen flow 30 mL-min−1; Air flow 400 mL-min−1; Make-up gas flow 25 mL-min−1.
Results
Constitution of Water Hyacinth
The average value of moisture content in water hyacinth sample was 90.85%, which is much higher than the other cellulosic wastes. The contents of cellulose, hemicellulose and lignin in different organs of water hyacinth were determined (Table 1). Compared to leaf and stem, the whole plant of water hyacinth possessed a little higher cellulose (18.07%) and hemicelluloses content (28.21%), and low lignin content (7.03%). Part of the erosion roots that was included in the whole plant of water hyacinth was removed before hydrolysis, so the composition of roots was not provided in Table 1. Considering the convenience and validity of utilization, the whole plant was finally selected as substrate for bioethanol production.
Pretreatment and Hydrolysis of Water Hyacinth
Three kinds of pretreatment methods, including acid pretreatment, alkali pretreatment and microwave-alkaline combined pretreatment, were used before hydrolysis and fermentation. Acid pretreatment was the most effective method to increase the sugar contents in samples. After grinding to 60 mesh, the water hyacinth sample was pretreated by 1% sulfuric acid at 100°C for 30 min when solid-liquid ratio was 1:30. An amount of 197.60 mg/g reducing sugars was obtained in hydrolysates. However, only 22.41 mg/g and 99.12 mg/g reducing sugars were obtained after alkaline pretreatment and microwave-alkaline combined pretreatment, respectively. Calculated by Hu's method (Hu and Wen, 2008), 37.9, 4.30, and 19.01% water hyacinth samples were converted into reducing sugars after acid pretreatment, alkaline pretreatment and microwave-alkaline combined pretreatment, respectively.
The surplus residue part of water hyacinth was hydrolyzed by cellulase after pretreatment. Various factors that influence cellulase hydrolysis, including cellulase dosage, enzyme temperature and reaction time, were optimized by single factor experiment (Figures 1A–C). The result showed that the yield of reducing sugar could reach 205.33 mg at 45°C at the end of 96 h when 0.05 g cellulase was added. Thus, totally 402.93 mg (197.60 mg in hydrolysates and 205.33 mg by residue hydrolysis) reducing sugar could be produced at the optimal condition.
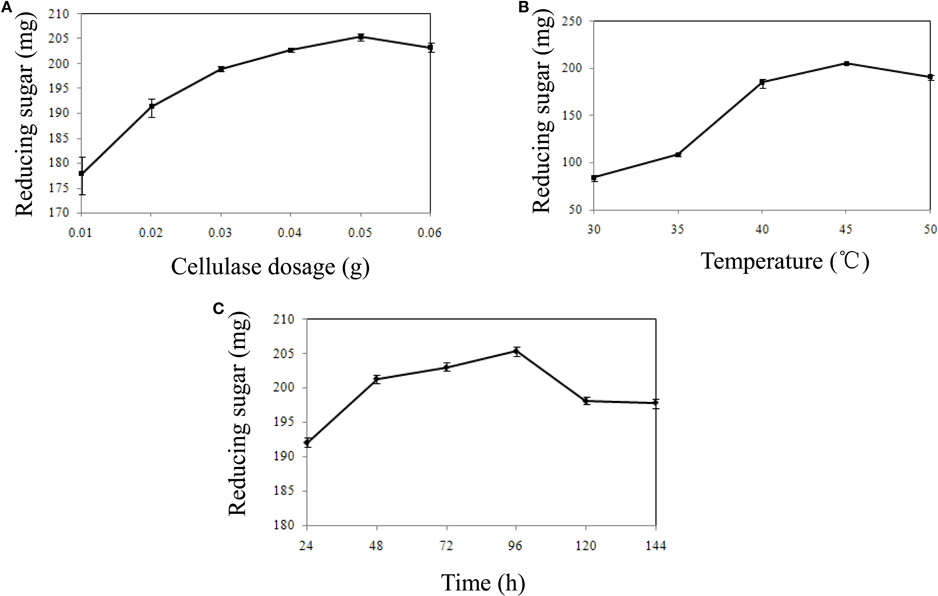
Figure 1. The influence of hydrolysis factors on reducing sugar production. (A) The influence of cellulase dosage on reducing sugar production. (B) The influence of temperature on reducing sugar production. (C) The influence of time on reducing sugar production.
Regression Model and Significance Test by Response Surface Method in Simultaneous Saccharification and Fermentation Process
The Box-Behnken design and experimental results were listed in Table 2. Variance test and regression were analyzed by Design-expert software after manual operation, which was shown in Table 3. It was showed that the regression model was highly significant (P < 0.05) and the regression equation obtained in the present study could predict the response value effectively.
The monomial expression X1 (P = 0.0064) was significant, whereas X2 (P = 0.9766) and X3 (P = 0.8146) were nonsignificant. Thus, fermentation temperature was the most crucial factor that could influence SSF process. The binomial expression X32 (P = 0.0001) was extremely significant, X22 (P = 0.0034) was relatively significant, and there was certain significance for X12 (P = 0.0209). The results indicated the primacy sequence influencing SSF process as fermentation temperature > inoculums dosage > fermentation time.
The secondary multivariate regression equation obtained from Design-expert software was Y = 1.23+0.15X1 − (1.250E-003X2) + 0.010X3 + 0.24 X1X2 − 0.16 X12 − 0.22 X22 − 0.36 X32. According to the secondary multivariate regression equation and regression model, the optimal condition for bioethanol production by SSF process was fermented at 38.87°C for 81.87 h when inoculated with 6.11 ml yeast. The ethanol yield could achieve 1.291 g/L at this condition by our regression model. Furthermore, 1.289 g/L ethanol was produced during real experimentation at this condition, which is very close to our regression model.
The optimal factors and factor levels could be determined and the interaction effects between two factors could be revealed by response surface and contour map. The response surface and contour map of the secondary multivariate regression equation was shown in Figures 2A,B, 3A,B, and 4A,B, respectively. The results showed a remarkable significant interaction between fermentation temperature (X1) and fermentation time (X2). However, there was no significant interaction between fermentation time (X2) and inoculums dosage (X3). Moreover, there was no significant interaction between fermentation temperature (X1) and inoculums dosage (X3), either. Fermentation temperature (X1) was the most important factor influencing SSF process in the present study.
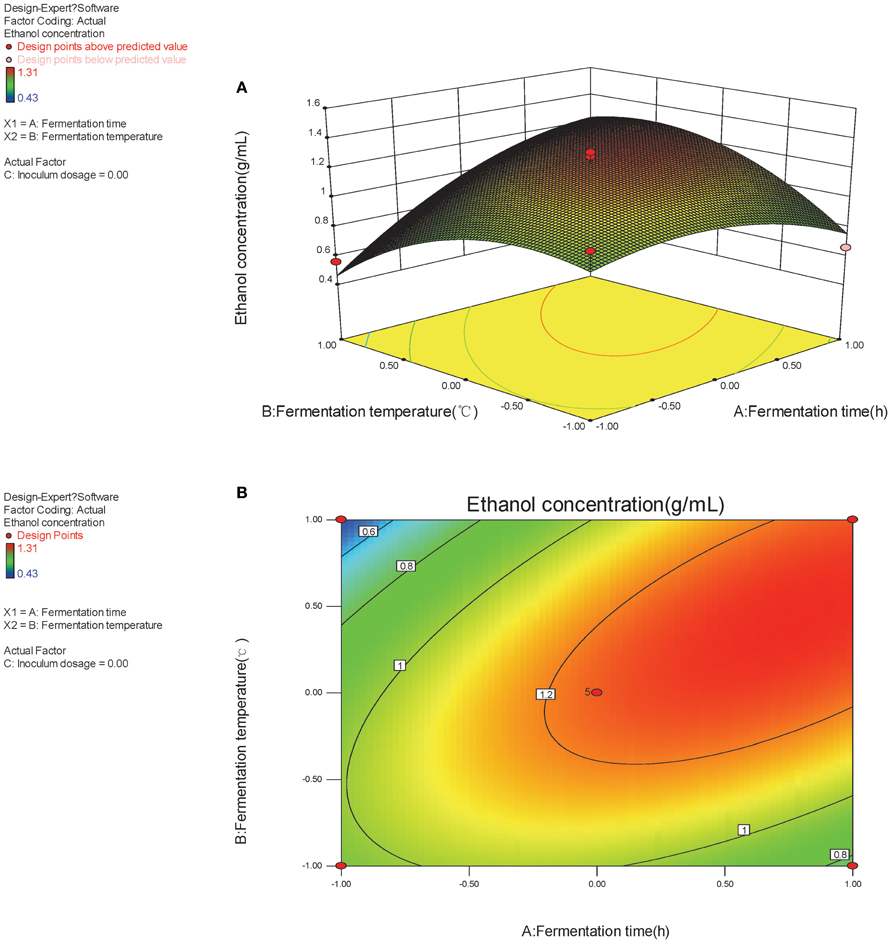
Figure 2. (A,B) Response of bioethanol production to fermentation time and fermentation temperature.
Discussion
Based on our results, the whole plant of water hyacinth possesses the highest cellulose content compared to stem and leaf after removing its rotten part. Therefore, it was selected as substrate for ethanol production, which could make full use of the whole plant.
Biofuel production from cellulosic materials greatly depends on the disruption of its complex lignocellulosic structure, which is recalcitrant to biodegradation. Hence, a suitable and effective pretreatment method should be selected for different cellulosic substrates. Various kinds of pretreatment methods, including acid, alkali, microwave, liquid hot water and compound pretreatments, were investigated nowadays for cellulose hydrolysis (Forrest et al., 2010; Ma et al., 2010; Gao et al., 2013; Timung et al., 2015; Yan et al., 2015). In our previous study, alkaline pretreatment was optimal for bioethanol production by rice straw hydrolysis (Zhang and Cai, 2008). However, acid pretreatment was the most effective method for bioethanol production by water hyacinth compared to other pretreatment methods in this study. The possible mechanism involves dissolution of hemicellulose causing loosening of the structure of raw material, which makes acid pretreatment an important method for the production ofreducing sugars (Ma et al., 2010; Xia et al., 2013). After pretreated by acid, the loosen substrate could increase the contact area between cellulose and cellulase. Meanwhile, it might prevent unproductive binding of enzymes to lignin, thus facilitates reducing sugar production (Zhang et al., 2009).
Cellulase usage is a huge cost in bioethanol production process. Large amounts of cellulases are needed to hasten the hydrolysis process, thereby increasing the cost of the whole processing. In addition, enzyme recycling becomes difficult because of the adsorption of cellulases to residual cellulosic materials (Zhang et al., 2009). Thus, many factors, such as cellulase dosage, enzyme temperature and reaction time, are urgently necessary to be optimized to reduce the cost of bioethanol production. After optimization of such important parameters in the present study, 402.93 mg (197.60 mg in hydrolysates, and 205.33 mg by residue hydrolysis) reducing sugar was produced. The theoretical yield of reducing sugar that produced by water hyacinth was 521.30 mg, counted by Hu's method (Hu and Wen, 2008). Therefore, the real yield of achieved reducing sugar was 77.29% of the theoretical yield by our optimized technique, and is more effective method compared to other reports, which only produce reducing sugars from the hydrolysates (Ma et al., 2010; Yan et al., 2015). However, pentose (such as xylose) sugar could not be digested using S. cerevisiae and remained unchanged during fermentation (Zhang and Cai, 2008). Hence, exploring a hexose-pentose co-fermentation system by genetic engineering method could be a promising way to improve bioethanol production by cellulosic materials.
According to our regression model, the ethanol yield could achieve 1.291 g/L at the optimum condition, while 1.289 g/L ethanol was produced by our real experiment at this condition, which is very close to the predicted model. These results showed the reliability of presented regression model. In terms of factors, which influenced SSF process, fermentation temperature (X1) was the most important compared to other factors, as temperature is crucial for growth and activity of cellulase and S. cerevisiae. Meanwhile, bioethanol production possessed a relatively high value that proved a fact that the SSF process is more effective than SSF separately (Wang et al., 2013; Asada et al., 2015; Saha et al., 2015). Although SSF could solve the feedback inhibition problem of cellobiose on fermentation process, it has some drawbacks, such as gap for the optimum temperature and pH conditions between cellulase and S. cerevisiae. Thus, a pivotal research field is required to develop and regulate a suitable condition for microorganisms in SSF process.
In addition, compared to other cellulosic materials, the moisture content in water hyacinth is much higher that could be solved during bioethanol production by fermentation of water hyacinth in future (Mishima et al., 2008). Further, there are some inhibitors (furfural, furan, phenols, etc.) in the hydrolysates that could destroy the fermentation process (Kalyani et al., 2012; Moreno et al., 2012; Wang et al., 2014), and an effective method to minimize the inhibitors production is urgently required in the future study. Moreover, the solid loading in enzymatic hydrolysis and SSF process might be another important factor, which need to be optimized in our future work.
Conclusion
As a conventional invasive weed, water hyacinth proved its feasibility for bioethanol energy production. In our experiment, 402.93 mg reducing sugar and 1.289 g/L bioethanol were achieved using water hyacinth substrate in Simultaneous SSF process after being optimized by RSM. This relatively high bioethanol production indicates that water hyacinth is a promising plant in research and development of sustainable energy.
Conflict of Interest Statement
The authors declare that the research was conducted in the absence of any commercial or financial relationships that could be construed as a potential conflict of interest.
Acknowledgments
This research is supported by grants from National Natural Science Foundation of China (NSFC, No. 31400513), Ministry of Education of People's Republic of China (No.20120076120019) and Shanghai Science and Technology Committee (No.12ZR1409100).
References
Asada, C., Sasaki, C., Takamatsu, T., and Nakamura, Y. (2015). Conversion of steam-exploded cedar into ethanol using simultaneous saccharification, fermentation and detoxification process. Bioresour. Technol. 176, 203–209. doi: 10.1016/j.biortech.2014.11.039
Barrett, S. C. H. (1989). Water weed invasions. Sci. Am. 264, 90–97. doi: 10.1038/scientificamerican1089-90
Bayrakci, A. G., and Koçar, G. (2014). Second-generation bioethanol production from water hyacinth and duckweed in Izmir: a case study. Renew. Sustain. Energy Rev. 30, 306–316. doi: 10.1016/j.rser.2013.10.011
Bergier, I., Salis, S. M., Miranda, C. H. B., Ortega, E., and Luengo, C. A. (2012). Biofuel production from water hyacinth in the Pantanal wetland. Ecohydrol. Hydrobiol. 12, 77–84. doi: 10.2478/v10104-011-0041-4
Buller, L. S., Ortega, E., Bergier, I., Mesa-Pérez, J. M., Salis, S. M., and Luengo, C. A. (2015). Sustainability assessment of water hyacinth fast pyrolysis in the Upper Paraguay River basin, Brazil. Sci. Total Environ. 532, 281–291. doi: 10.1016/j.scitotenv.2015.05.129
Cheng, J., Lin, R., Song, W., Xia, A., Zhou, J., and Cen, K. (2015a). Enhancement of fermentative hydrogen production from hydrolyzed water hyacinth with activated carbon detoxification and bacteria domestication. Int. J. Hydrogen Energy 40, 2545–2551. doi: 10.1016/j.ijhydene.2014.12.097
Cheng, Y. S., Chen, K. Y., and Chou, T. H. (2015b). Concurrent calcium peroxide pretreatment and wet storage of water hyacinth for fermentable sugar production. Bioresour. Technol. 176, 267–272. doi: 10.1016/j.biortech.2014.11.016
Craft, C. P., Megonigal, S., Broome, J., Stevenson, R., Freese, J., Cornell, L., et al. (2003). The pace of ecosystem development of constructed Spartina alterniflora marshes. Ecol. Appl. 13, 1417–1432. doi: 10.1890/02-5086
Das, S., Bhattacharya, A., Haldar, S., Ganguly, A., Gu, S., Ting, Y. P., et al. (2015). Optimization of enzymatic saccharification of water hyacinth biomass for bio-ethanol: comparison between artificial neural network and response surface methodology. Sustain. Mater. Technol. 3, 17–28. doi: 10.1016/j.susmat.2015.01.001
Forrest, A. K., Hernandez, J., and Holtzapple, M. T. (2010). Effects of temperature and pretreatment conditions on mixed-acid fermentation of water hyacinths using a mixed culture of thermophilic microorganisms. Bioresour. Technol. 101, 7510–7515. doi: 10.1016/j.biortech.2010.04.049
Ganguly, A., Chatterjee, P. K., and Dey, A. (2012). Studies on ethanol production from water hyacinth—a review. Renew. Sustain. Energy Rev. 16, 966–972. doi: 10.1016/j.rser.2011.09.018
Gao, J., Chen, L., Yan, Z., and Wang, L. (2013). Effect of ionic liquid pretreatment on the composition, structure and biogas production of water hyacinth (Eichhornia crassipes). Bioresour. Technol. 132, 361–364. doi: 10.1016/j.biortech.2012.10.136
Goering, H. K., and Van soest, P. J. (1970). Forage Fibre Analysis. Agriculture Handbook. Washington, DC: Agricultural Research Services, United States Department of Agriculture.
Guan, D., Li, Y., Shiroma, R., Ike, M., and Tokuyasu, K. (2013). Sequential incubation of Candida shehatae and ethanol-tolerant yeast cells for efficient ethanol production from a mixture of glucose, xylose and cellobiose. Bioresour. Technol. 132, 419–422. doi: 10.1016/j.biortech.2012.12.040
Guerrero-Coronilla, I., Morales-Barrera, L., and Cristiani-Urbina, E. (2015). Kinetic, isotherm and thermodynamic studies of amaranth dye biosorption from aqueous solution onto water hyacinth leaves. J. Environ. Manage. 152, 99–108. doi: 10.1016/j.jenvman.2015.01.026
Ha, S. J., Kim, S. R., Kim, H., Du, J., Cate, J. H. D., and Jin, Y. S. (2013). Continuous co-fermentation of cellobiose and xylose by engineered Saccharomyces cerevisiae. Bioresour. Technol. 149, 525–531. doi: 10.1016/j.biortech.2013.09.082
Hu, Z., Ma, X., and Li, L. (2015). Optimal conditions for the catalytic and non-catalytic pyrolysis of water hyacinth. Energy Convers. Manage. 94, 337–344. doi: 10.1016/j.enconman.2015.01.087
Hu, Z., and Wen, Z. (2008). Enhancing enzymatic digestibility of switchgrass by microwave-assisted alkali pretreatment. Biochem. Eng. J. 38, 369–378. doi: 10.1016/j.bej.2007.08.001
Huang, Y. H., Jin, Y. L., Fang, Y., Li, Y. H., Zhang, G. H., Xiao, Y., et al. (2013). Simultaneous saccharification and fermentation (SSF) of non-starch polysaccharides and starch from fresh tuber of Canna edulis ker at a high solid content for ethanol production. Biomass Bioenergy 52, 8–14. doi: 10.1016/j.biombioe.2013.02.023
Jiu, B., Li, B. X., and Yu, Q. J. (2015). Effects of Pb on pyrolysis behavior of water hyacinth. J. Anal. Appl. Pyrolysis 112, 270–275. doi: 10.1016/j.jaap.2015.01.015
Kalyani, D., Dhiman, S. S., Kim, H., Jeya, M., Kim, I. W., and Lee, J. K. (2012). Characterization of a novel laccase from the isolated Coltricia perennis and its application to detoxification of biomass. Process Biochem. 47, 671–678. doi: 10.1016/j.procbio.2012.01.013
Lin, R., Cheng, J., Song, W., Ding, L., Xie, B., Zhou, J., et al. (2015). Characterisation of water hyacinth with microwave-heated alkali pretreatment for enhanced enzymatic digestibility and hydrogen/methane fermentation. Bioresour. Technol. 182, 1–7. doi: 10.1016/j.biortech.2015.01.105
Ma, F., Yang, N., Xu, C., Yu, H., Wu, J., and Zhang, X. (2010). Combination of biological pretreatment with mild acid pretreatment for enzymatic hydrolysis and ethanol production from water hyacinth. Bioresour. Technol. 101, 9600–9604. doi: 10.1016/j.biortech.2010.07.084
Malik, A. (2007). Environmental challenge vis a vis opportunity: the case of water hyacinth. Environ. Int. 33, 122–138. doi: 10.1016/j.envint.2006.08.004
Masto, R. E., Kumar, S., Rout, T. K., Sarkar, P., George, J., and Ram, L. C. (2013). Biochar from water hyacinth (Eichornia crassipes) and its impact on soil biological activity. Catena 111, 64–71. doi: 10.1016/j.catena.2013.06.025
Merino-Pérez, O., Martínez-Palou, R., Labidi, J., and Luque, R. (2015). Microwave-assisted pretreatment of lignocellulosic biomass to produce biofuels and value- added products. Prod. Biofuels Chem. Microw. 3, 197–224. doi: 10.1007/978-94- 017-9612-5_10
Miller, G. L. (1959). Use of dinitrosalicylic acid reagent for determination of reducing sugars. Anal. Chem. 31, 426–428. doi: 10.1021/ac60147a030
Mishima, D., Kuniki, M., Sei, K., Soda, S., Ike, M., and Fujita, M. (2008). Ethanol production from candidate energy crops: water hyacinth (Eichhornia crassipes) and water lettuce (Pistia stratiotes L.). Bioresour. Technol. 99, 2495–2500. doi: 10.1016/j.biortech.2007.04.056
Moreno, A. D., Ibarra, D., Fernández, J., and Ballesteros, M. (2012). Different laccase detoxification strategies for ethanol production from lignocellulosic biomass by the thermotolerant yeast Kluyveromyces marxianus CECT 10875. Bioresour. Technol. 106, 101–109. doi: 10.1016/j.biortech.2011.11.108
Patil, J. H., AntonyRaj, M., Shankar, B. B., Shetty, M. K., and Pradeep Kumar, B. P. (2014). Anaerobic co-digestion of water hyacinth and sheep waste. Energy Procedia 52, 572–578. doi: 10.1016/j.egypro.2014.07.112
Rezania, S., Ponraj, M., Md Din, M. F., Songip, A. R., Sairan, F. M., and Chelliapan, S. (2015). The diverse applications of water hyacinth with main focus on sustainable energy and production for new era: an overview. Renew. Sustain. Energy Rev. 41, 943–954. doi: 10.1016/j.rser.2014.09.006
Saha, B. C., Nichols, N. N., Qureshi, N., Kennedy, G. J., Iten, L. B., and Cotta, M. A. (2015). Pilot scale conversion of wheat straw to ethanol via simultaneous saccharification and fermentation. Bioresour. Technol. 175, 17–22. doi: 10.1016/j.biortech.2014.10.060
Soares, M. L., and Gouveia, E. R. (2013). Influence of the alkaline delignification on the simultaneous saccharification and fermentation (SSF) of sugar cane bagasse. Bioresour. Technol. 147, 645–648. doi: 10.1016/j.biortech.2013.08.103
Taniguichi, M., Suzuki, H., Watanabe, D., Sakai, K., Hoshino, K., and Tanaka, T. (2005). Evaluation of pretreatment with Pleurotus ostreatus for enzymatic hydrolysis of rice straw. J. Biosci. Bioeng. 100, 637–643. doi: 10.1263/jbb.100.637
Timung, R., Mohan, M., Chilukoti, B., Sasmal, S., Banerjee, T., and Goud, V. V. (2015). Optimization of dilute acid and hot water pretreatment of different lignocellulosic biomass: a comparative study. Biomass Bioenergy 81, 9–18. doi: 10.1016/j.biombioe.2015.05.006
Valentine, J., Clifton-Brown, J., Hastings, A., Robson, P., Allison, G., and Smith, P. (2012). Food vs. fuel: the use of land for lignocellulosic ‘next generation’ energy crops that minimize competition with primary food production. Global Change Biol. Bioenergy 4, 1–19. doi: 10.1111/j.1757-1707.2011.01111.x
Wang, D. (2015). Optimization of Ethanol Production by Saccharification and Fermentation From Water Hyacinth. M.S. thesis, East China Normal University, Shanghai.
Wang, L., Luo, Z., and Shahbazi, A. (2013). Optimization of simultaneous saccharification and fermentation for the production of ethanol from sweet sorghum (Sorghum bicolor) bagasse using response surface methodology. Ind. Crops Prod. 42, 280–291. doi: 10.1016/j.indcrop.2012.06.005
Wang, W., Liu, Y., Li, T., and Zhou, M. (2014). Heterogeneous Fenton catalytic degradation of phenol based on controlled release of magnetic nanoparticles. Chem. Eng. J. 242, 1–9. doi: 10.1016/j.cej.2013.12.080
Xia, A., Cheng, J., Song, W., Yu, C., Zhou, J., and Cen, K. (2013). Enhancing enzymatic saccharification of water hyacinth through microwave heating with dilute acid pretreatment for biomass energy utilization. Energy 61, 158–166. doi: 10.1016/j.energy.2013.09.019
Yan, J., Wei, Z., Wang, Q., He, M., Li, S., and Irbis, C. (2015). Bioethanol production from sodium hydroxide/hydrogen peroxide pretreated water hyacinth via simultaneous saccharification and fermentation with a newly isolated thermo tolerant Kluyveromyces marxianu strain. Bioresour. Technol. 193, 103–109. doi: 10.1016/j.biortech.2015.06.069
Zhang, F., Wang, X., Yin, D., Peng, B., Tan, C., Liu, Y., et al. (2015). Efficiency and mechanisms of Cd removal from aqueous solution by biochar derived from water hyacinth (Eichornia crassipes). J. Environ. Manage. 153, 68–73. doi: 10.1016/j.jenvman.2015.01.043
Zhang, Q., and Cai, W. (2008). Enzymatic hydrolysis of alkali-pretreated rice straw by Trichoderma reesei ZM4-F3. Biomass Bioenergy 32, 1130–1135. doi: 10.1016/j.biombioe.2008.02.006
Zhang, Q., He, G., Wang, J., Cai, W., and Xu, Y. (2009). Mechanisms of the stimulatory effects of rhamnolipid biosurfactant on rice straw hydrolysis. Appl. Energy 86, S233–S237. doi: 10.1016/j.apenergy.2009.04.030
Keywords: water hyacinth, bioethanol, RSM, SSF, optimization methods
Citation: Zhang Q, Weng C, Huang H, Achal V and Wang D (2016) Optimization of Bioethanol Production Using Whole Plant of Water Hyacinth as Substrate in Simultaneous Saccharification and Fermentation Process. Front. Microbiol. 6:1411. doi: 10.3389/fmicb.2015.01411
Received: 26 August 2015; Accepted: 27 November 2015;
Published: 07 January 2016.
Edited by:
Pankaj K. Arora, Yeungnam University, South KoreaReviewed by:
Uwe Strotmann, Westfälische Hochschule, GermanySachin Kumar, Sardar Swaran Singh National Institute of Renewable Energy, India
Copyright © 2016 Zhang, Weng, Huang, Achal and Wang. This is an open-access article distributed under the terms of the Creative Commons Attribution License (CC BY). The use, distribution or reproduction in other forums is permitted, provided the original author(s) or licensor are credited and that the original publication in this journal is cited, in accordance with accepted academic practice. No use, distribution or reproduction is permitted which does not comply with these terms.
*Correspondence: Qiuzhuo Zhang, cXpoemhhbmdAZGVzLmVjbnUuZWR1LmNu