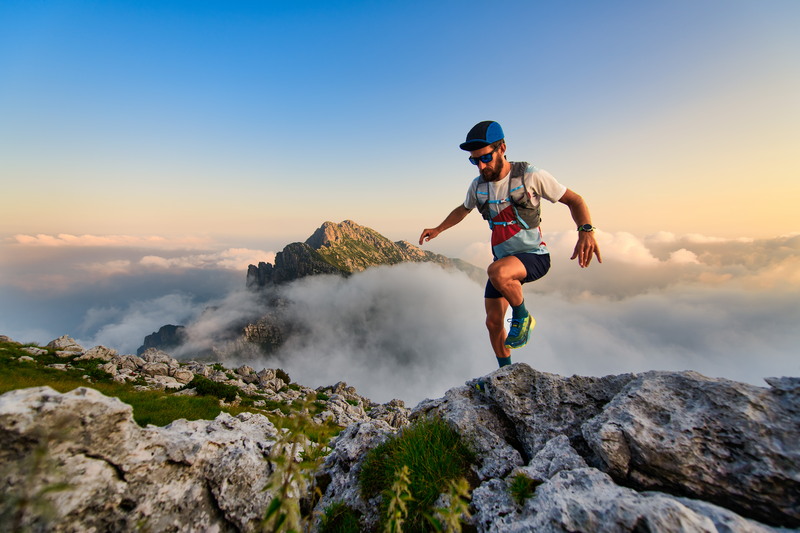
95% of researchers rate our articles as excellent or good
Learn more about the work of our research integrity team to safeguard the quality of each article we publish.
Find out more
ORIGINAL RESEARCH article
Front. Met. Alloy , 14 March 2025
Sec. Physical Metallurgy
Volume 4 - 2025 | https://doi.org/10.3389/ftmal.2025.1528735
Twin-roll casting (TRC) enables the production of near-net-shape semi-finished products in a single forming step, offering significant energy and cost savings compared to conventional rolling. While TRC has been successfully applied to flat magnesium alloy products, its application to long products, such as wires, remains a novel research focus. In this study, the microstructure, texture, and mechanical properties of TRC wires were investigated for the common wrought alloys AZ31 and AZ80, as well as the calcium-containing alloy ZAX210. Microstructural analysis was performed using scanning electron microscopy (SEM) and electron backscatter diffraction (EBSD). Mechanical properties were evaluated through tensile testing at room temperature. The TRC wires exhibited a central segregation zone with a characteristic necklace-like grain structure composed of small and large grains. The addition of Ca in ZAX210 significantly reduced segregation. SEM analysis revealed fine and large network-like intermetallic phases, including Mg17Al12, AlMn, and Ca2Mg6Zn3. Texture analysis indicated a pole split or a shifted basal pole with low intensities. Tensile testing showed that the increased Al content in AZ80 led to lower mechanical properties compared to AZ31. Both alloys displayed low elongation at fracture due to pronounced central segregation and brittle intermetallic phases. In contrast, ZAX210 exhibited a finer and more homogeneous microstructure, resulting in the highest tensile strength and elongation at fracture. These findings suggest that the TRC process introduces characteristic microstructural features that influence mechanical properties. The observed improvements in ZAX210 highlight the potential of calcium additions to refine the microstructure and mitigate segregation effects.
Mg alloys are increasingly attracting attention in a variety of applications. This is due to their low density and high specific strength, making them particularly suitable for saving weight without sacrificing strength. Typical application areas include the automotive industry, aviation, the electrical and sports industries, as well as medicine (Tan and Ramakrishna, 2021; Prasad et al., 2022; Liu et al., 2023). Because of its nearly identical density and elastic modulus compared to human bone tissue, Mg alloys prove to be a promising option for use in implants (Uppal et al., 2022). Mg alloys are also used as a stent, with their good biocompatibility and ability to biologically degrade through corrosion enhancing interest in this material (Ghafari et al., 2023).
In the field of biomedicine, thinner Mg wire are specifically employed (Griebel et al., 2024). The current main methods for producing such wires primarily include caliber rolling (Kong et al., 2020), drawing (Dodyim et al., 2020) and extrusion (TESAŘ et al., 2020). Twin-roll casting represents another method that enables cost-efficient and energy-saving production (Kawalla et al., 2018). By combining casting and rolling in one step, process times and emissions can be reduced. The basis for twin-roll casting of Mg wire builds upon experiences from twin-roll casting of Mg sheets, a practice that has been in place since the 1980s (Javaid and Czerwinski, 2021). In the field of sheet metal, previous studies have shown that twin-roll casting results in a refinement of the microstructure and a weakening of the texture, which can lead to improved mechanical properties (Neh et al., 2015). The process has already been applied to many different Mg alloys, such as AZ31 (Zimina et al., 2018), WE43 (Neh et al., 2014), ZK60 (Bhattacharjee et al., 2014) and ZEK100 (Máthis et al., 2018). In contrast, twin-roll casting of Mg wire, or wire in general, has been studied to a very limited extent. However, Moses (Moses et al., 2023) and Arndt (Arndt et al., 2022) have also observed a similar grain refinement and texture weakening during the twin-roll casting of an AZ31 alloy wire.
This paper focuses on the twin-roll casting process of wire for the AZ31, AZ80, and ZAX210 alloys. The microstructure, texture, and mechanical properties are investigated and presented. The selection of the alloys was based on their distinct chemical compositions and resulting microstructural and mechanical properties. AZ31 is a widely used wrought Mg alloy known for its good formability and moderate strength (Pekguleryuz, 2012). AZ80, with a higher Al content, exhibits increased precipitation of Mg17Al12, which enhances strength but reduces ductility. In contrast, the calcium-containing ZAX210 alloy was included to investigate the role of Ca in modifying the microstructure and texture during twin-roll casting, as it is reported to weaken the texture and improve elongation at fracture (Ding et al., 2015).
The twin-roll cast wires considered for examination were produced at the twin-roll casting plant of the Institute of Metal Forming at the TU Bergakademie Freiberg (Moses et al., 2019). In this process, the Mg alloy is first melted in a furnace under a protective gas and conveyed into a headbox via a dosing tube. Subsequently, the melt flows through a hybrid casting nozzle, consisting of steel and ceramic, into the rolling gap between two counter-rotating, water-cooled rolls (Figure 1A). There, it solidifies from the outside in and undergoes initial deformation. To prevent the melt from adhering to the rolls, a release agent consisting of a water-graphite solution was used. The final wire has an oval cross-section of 9.2 mm in height and 20.0 mm in width due to the groove formed by the rolls in the roll gap (Figures 1B, C). For each alloy, approximately 30 m of wire was produced.
Figure 1. Twin-roll casting of wire: process schematic (A) twin-roll cast wire profile (B) and cross section of the twin-roll cast wire (C).
Temperature control during the twin-roll casting process is crucial to ensure uniform solidification and stable process conditions. The process temperatures depend, among other factors, on the liquidus and solidus temperatures and the resulting solidification interval of the respective alloy. Generally, the melt is heated in the furnace to a temperature approximately 70 K above the liquidus temperature of the respective alloy. However, the ZAX210 alloy, due to its strong sticking tendency caused by the addition of calcium (Kondori and Mahmudi, 2010), requires special considerations, and a lower furnace temperature was chosen. This decision was based on experience, indicating that less superheating is necessary in this case to ensure process stability and minimize sticking tendencies. In all cases, the temperature of the dosing tube was maintained at a constant 750°C to prevent blockages and deposits. This temperature can be sustained by the system components without causing permanent damage and ensures that the melt remains fluid as it is transported to the next stage of the process. In the headbox, the melt’s temperature was maintained to compensate for any heat losses during transfer. For AZ31 and ZAX210, the temperature was set at 720°C to maintain sufficiently high melt temperatures, while for AZ80, a lower temperature of 690°C was chosen, consistent with its lower liquidus temperature. The nozzle temperature was selected to keep the melt fluid enough to allow for even distribution into the rolling gap without premature solidification. The setback (distance between the nozzle and the rolling gap) and the profile height are two constant influencing factors. The twin-roll casting speed (wire speed) is controlled by the roll speed. The highest speeds were required for the AZ80 alloy, as lower speeds led to cracking. A selection of the most important parameters used is shown in Table 1.
The twin-roll cast alloys include the two standard wrought alloys AZ31 and AZ80 (Friedrich and Mordike, 2006) as well as the Ca-containing ZAX210 alloy (Neh et al., 2016). In addition to the main alloying elements Al, Zn and Mn, Si, Fe and Ni are also included. Al and Zn improve strength (Loukil, 2022), while Mn increases corrosion resistance and Si increases the creep properties (Mohammadi Mazraeshahi et al., 2015; Loukil, 2022). Fe, on the other hand, have a detrimental effect on corrosion behavior and must be kept below a critical threshold, often below 0.005 wt% (Yang et al., 2018). The Ca content in the ZAX210 alloy results in grain refinement, which increases creep resistance and improves formability due to the weakening of the rolling texture (Ullmann et al., 2019). The chemical compositions of the twin-roll cast alloys are listed in Table 2.
Table 2. chemical composition of the AZ31, AZ80 and ZAX210 ingots determined by optical emission spectroscopy (wt%).
To investigate the microstructure and texture analysis, the wire was separated, embedded, ground with silicon carbide paper and polished with an oxide polishing suspension. It was then etched with a solution of 70 mL ethanol, 10 mL glacial acetic acid, 4.2 g picric acid and 10 mL distilled water. The Keyence VHX-6000 optical microscope and the ZEISS GeminiSEM 450 scanning electron microscope were used to evaluate the microstructure of the longitudinal section. The chemical composition of individual microstructural constituents was analyzed using energy dispersive X-ray spectroscopy (EDX). Acceleration voltage of 20 kV and a working distance of 8.5 mm were applied. The texture measurements were carried out with the Electron Backscatter Diffraction (EBSD) Detector. The voltage used for acquisition of EBSD data was 15–20 kV, and the step size was 0.65 µm. The analysis of the EBSD data and the calculation of the pole figures were carried out using the MTEX MATLAB toolbox (version 5.9.0, MTEX, Ralf Hielscher, Freiberg, Germany) (Bachmann et al., 2010). For tensile tests, tensile specimens correspond to DIN 50125 shape B with a gauge diameter of 5 mm and a gauge length of 25 mm were machined and used. For each alloy, six tensile tests were performed at room temperature and a traverse speed of 0.625 mm/min.
The twin-roll cast wires were characterized regarding their microstructure, chemical composition, and mechanical properties. Figure 2 shows the overview images of the etched samples of the respective alloys in longitudinal section. Upon contact of the melt with the rolls, a fine edge layer with small grains forms due to the high cooling rate. Due to the heat transfer into the center of the wire, stem-like dendrites form, which are redirected in the direction of the heat flow due to roll rotation (Figure 3). Because of the high cooling rate, there is no time for diffusion processes, leading to the enrichment of the residual melt with alloying elements. The meeting of solidification fronts forms the segregation zone. This zone consists of a coarse, inhomogeneous cast structure with an increased proportion of intermetallic phases, which are unevenly distributed. This typical structure was already observed by Arndt et al., (2022) in the investigation of a twin-roll cast wire of the AZ31 alloy. A similar structure also forms during the twin-roll casting of Mg sheets (Neh et al., 2015). In the case of the AZ80 alloy, it also leads to a formation of an inverse segregation in the center of the wire. Inverse segregation occurs when a highly alloyed liquid phase becomes trapped in the central region of the wire and is subsequently pushed outward toward the wire surface by the roll separating force. This phenomenon is intensified by hydrodynamic effects generated by the rotating rollers, resulting in a non-uniform composition and microstructure (Ullmann et al., 2024). In the case of alloys with a wider solidification range, such as AZ80, the inverse segregations are more pronounced (Park et al., 2007). In the ZAX210 alloy, the segregation region is less pronounced compared to the AZ alloys, only occasional local segregation formation can be observed. Additionally, the structure is notably more homogeneous. The detailed images in Figure 3 also show that the fine dendritic structure is interspersed with small grains and twins.
Figure 2. Microstructures of the investigated Mg alloys in twin roll cast condition. Longitudinal view.
Figure 3. Detailed images of the microstructures of the investigated Mg alloys from the top (A, D, G), the middle (B, E, H) and the bottom (C, F, I) of the longitudinal view.
The region of the segregation zone and the edge area were further examined using scanning electron microscopy. The Mg matrix is depicted in dark, while precipitates appear brighter. Starting with AZ31, the local chemical composition in Figure 4 (point 4), shows that Al and Zn are dissolved in the Mg solid solution, while Mn cannot be detected in the matrix. The mass fraction of Al is 3.53% and that of zinc is 3.03%. Furthermore, large network-like phases are visible. A point analysis for Point 2 reveals an Al content of 25.03% and a Zn content of 18.35%. Based on the chemical composition and comparison with the literature (Sheikhani et al., 2022), this is likely to be the Mg17(Al, Zn)12 phase, commonly found in AZ alloys. It is also evident that Mn appears exclusively in finely dispersed, rounded precipitates (point 1 and 3). Moreover, large amounts of Al are contained in the Mn-rich phases, suggesting the presence of the AlMn phase. The distribution and size of the precipitates are similar in the center and edge regions. In the case of the AZ80 alloy, the images of the center region (Figure 4, d) again show a mixture of fine and coarse, network-like precipitates. The Mg matrix consists of Mg (94.45%) and Al (5.55%), with no presence of Zn and Mn. Measurement of the local chemical composition in the area of the large bright phase (point 7) shows an increase in Al content to 31.52% and Zn content to 2.73%. Additionally, at Point 8, alongside 37.90% Mn, 8.67% Fe and 0.93% Si were measured. Fe particles can occur in the melt due to the manufacturing process, although Fe significantly worsens the corrosion resistance. The addition of Mn in Mg alloys has the advantage of binding Fe particles through the formation of Fe-Mn-containing compounds, thereby mitigating their negative effect on the alloy’s corrosion resistance (Simanjuntak et al., 2015). Furthermore, in contrast to the wire center, the precipitates in the edge region (c) are very fine and evenly distributed. Small round phases, where Mn is dissolved, are also observed here (point 5). In the case of the ZAX210 alloy, the Mg matrix contains only a small amount of Al and Zn, with no dissolved Ca (Figure 4, point 10). The precipitates, especially in the wire center, again appear in network-like structures, but are finer compared to the AZ alloys. The chemical composition of the phase at Point 11 shows a high Zn content of 29.12% and similar contents of Al (9.67%) and Ca (7.77%). According to the literature, this is likely to be the Mg6Ca2Zn3 phase (Katsarou et al., 2016).
Figure 4. EDS measurement of the edge (A, C, E) and the center (B, D, F) with the chemical composition of selected points of the twin-roll cast alloys (wt%).
Figure 5 shows regions within the segregation zone, their {0001} pole figures and the misorientation angle distributions. The inverse pole figure (IPF) map reveals inhomogeneous grain structures consisting of small and large grains, with the small recrystallized grains forming along the grain boundaries. This so-called necklace structure indicates that discontinuous dynamic recrystallization is the dominant recrystallization mechanism (Chen et al., 2022). Twins are also recognizable, especially in the ZAX210 alloy. The misorientation angle distribution allows for an assessment of the dominant twinning systems. All three alloys exhibit the highest peak between 85° and 90°, indicative of {10
Figure 5. Results of EBSD analysis of the twin roll cast wires within the segregation zone: inverse pole figure maps (A, D, G), missorientation angle distribution (B, E, H), {0001} pole figures (C, F, I).
The mechanical properties, including yield strength (YS), ultimate tensile strength (UTS), and elongation at fracture, determined from the tensile tests at room temperature, are presented in Figure 6. Compared to the other alloys, AZ31 exhibits the highest values for YS (176 MPa), but the elongation at fracture is relatively low at 6.9%. AZ80 shows overall lower values compared to AZ31, with an elongation at fracture of only 1.9%. The ZAX210 alloy demonstrates the highest tensile strength at 239 MPa and the highest elongation at fracture at 17.1%, but the lowest yield strength at 118 MPa. One possible reason for the high tensile strength and, especially, the high elongation at fracture observed in ZAX210 could be the addition of calcium. This would be align with Bhattacharjee et al. (2014), who noted that Ca addition in Mg alloys improved both mechanical properties and processability through grain refinement. Similarly, Wang et al. (2020) highlighted the beneficial effects of Ca in enhancing strength and ductility. Furthermore, the relatively low number of precipitates observed, due to the significantly lower aluminum content, indicates that the microstructure retains its ductility. The lower elongation at fracture observed in the AZ alloys may be attributed to the increased presence of the Mg17Al12 phase in the segregation zone. Due to its brittle behavior, this phase adversely affects the ductility of Mg alloys. Additionally, the alloying content in AZ80, and consequently the proportion of segregation, is significantly higher than that of AZ31, which restricts the plastic deformation. Moreover, voids and cracks occur along and within the segregation zone, further contributing to a reduction in elongation at fracture (Krbetschek et al., 2016). Regarding the ZAX210 alloy, the homogeneous microstructure with already recrystallized regions positively influences the elongation at fracture. Simultaneously, the fine microstructure enhances the tensile strength. The unexpectedly low UTS of AZ80 contrasts with theoretical expectations, as its higher aluminum content compared to ZAX210 typically enhances tensile strength by promoting solid solution strengthening and the precipitation of Mg17Al12 phases. However, the severe segregation and resulting structural weaknesses appear to have counteracted this advantage, reducing the effective load-bearing capacity of the alloy under tensile loading.
Within this study, the microstructure, texture, and mechanical properties of twin-roll cast wires of the AZ31, AZ80, and ZAX210 alloys were investigated. The findings of this study can be summarized as follows.
(1) Twin-roll casting results in a microstructure characterized by a central segregation zone, wherein both small and large grains form a necklace-like structure. The addition of Ca significantly reduces the extent of the segregation zone in ZAX210.
(2) SEM analysis reveals the presence of both fine and large network-like intermetallic phases. While the phases in the central and outer regions of AZ31 are similar in size and nature, those in AZ80 and ZAX210 are smaller and more finely distributed in the edge region. Mainly, these phases consist of Mg17Al12, AlMn, and Ca2Mg6Zn3.
(3) No pronounced texture is observed in any of the three alloys. The pole figures of AZ80 and ZAX210 exhibit pole splits with the inclination of intensity maxima in the twin-roll casting direction, whereas the basal pole of AZ31 is shifted in the twin-roll casting direction. Overall, however, the intensity maxima are very low.
(4) Tensile tests at room temperature indicate that the mechanical properties of the AZ80 alloy deteriorate due to the increased addition of Al compared to AZ31. The elongation at fracture is very low in both alloys due to the prominent central segregation, the inverse segregations and the widespread brittle intermetallic phase Mg17Al12. In contrast, the addition of Ca in the ZAX210 alloy and the fewer precipitates, due to the lower aluminum content, results in a finer and more homogeneous microstructure, leading to the highest tensile strength and elongation at fracture.
(5) By optimizing the processing conditions, it may be possible to further enhance and fine-tune the overall properties. Future studies are therefore necessary to systematically investigate the interactions between process parameters, alloying elements, and material properties.
The original contributions presented in the study are included in the article/supplementary material, further inquiries can be directed to the corresponding author.
CK: Conceptualization, Formal Analysis, Investigation, Methodology, Visualization, Writing–original draft. KK: Conceptualization, Methodology, Validation, Writing–review and editing. MU: Conceptualization, Validation, Writing–review and editing. UP: Supervision, Writing–review and editing.
The author(s) declare that financial support was received for the research, authorship, and/or publication of this article. The authors would like to thank the Federal Ministry for Economic Affairs and Climate Action for supporting this research work through the project “CLEAN-Mag: CO2-neutral production of lightweight magnesium components”, project no. 03LB3080A, part of the Technologietransfer-Programm Leichtbau (TTP LB).
The authors declare that the research was conducted in the absence of any commercial or financial relationships that could be construed as a potential conflict of interest.
The author(s) declare that no Generative AI was used in the creation of this manuscript.
All claims expressed in this article are solely those of the authors and do not necessarily represent those of their affiliated organizations, or those of the publisher, the editors and the reviewers. Any product that may be evaluated in this article, or claim that may be made by its manufacturer, is not guaranteed or endorsed by the publisher.
Arndt, F., Berndorf, S., Moses, M., Ullmann, M., and Prahl, U. (2022). Microstructure and hot deformation behaviour of twin-roll cast AZ31 magnesium wire. Crystals 12, 173. doi:10.3390/cryst12020173
Bachmann, F., Hielscher, R., and Schaeben, H. (2010). Texture analysis with MTEX – free and open source software toolbox. SSP 160, 63–68. doi:10.4028/www.scientific.net/SSP.160.63
Bhattacharjee, T., Suh, B.-C., Sasaki, T. T., Ohkubo, T., Kim, N. J., and Hono, K. (2014). High strength and formable Mg–6.2Zn–0.5Zr–0.2Ca alloy sheet processed by twin roll casting. Mater. Sci. Eng. A 609, 154–160. doi:10.1016/j.msea.2014.04.058
Chatterton, M., Robson, J., and Henry, D. (2014). “Texture evolution during wire drawing of Mg-RE alloy,” in Magnesium technology 2014. Editors M. Alderman, M. V. Manuel, N. Hort, and N. R. Neelameggham (Wiley), 251–256.
Chen, X., Li, X., Ning, F., Liao, Q., Le, Q., Zhou, X., et al. (2022). The hot rolling deformation performance of as-cast AZ80 magnesium alloy after ultrasonic processing. J. Mater. Res. Technol. 17, 1707–1715. doi:10.1016/j.jmrt.2022.01.116
Ding, H., Shi, X., Wang, Y., Cheng, G., and Kamado, S. (2015). Texture weakening and ductility variation of Mg–2Zn alloy with CA or RE addition. Mater. Sci. Eng. 645, 196–204. doi:10.1016/j.msea.2015.08.025
Dodyim, N., Yoshida, K., Murata, T., and Kobayashi, Y. (2020). Drawing of magnesium fine wire and medical application of drawn wire. Procedia Manuf. 50, 271–275. doi:10.1016/j.promfg.2020.08.050
Friedrich, H. E., and Mordike, B. L. (2006). Magnesium technology: metallurgy, design data, applications. Berlin/Heidelberg: Springer-Verlag.
Ghafari, C., Brassart, N., Delmotte, P., Brunner, P., Dghoughi, S., and Carlier, S. (2023). Bioresorbable magnesium-based stent: real-world clinical experience and feasibility of follow-up by coronary computed tomography: a new window to look at new scaffolds. Biomedicines 11, 1150. doi:10.3390/biomedicines11041150
Griebel, A. J., David, C. J., Schaffer, J. E., He, W., and Guillory, R. (2024). “Assessment of magnesium wire coatings for absorbable medical devices,” in Magnesium technology 2024. Editors A. Leonard, S. Barela, N. R. Neelameggham, V. M. Miller, and D. Tolnai (Cham: Springer Nature Switzerland), 187–191.
Javaid, A., and Czerwinski, F. (2021). Progress in twin roll casting of magnesium alloys: a review. J. Magnesium Alloys 9, 362–391. doi:10.1016/j.jma.2020.10.003
Katsarou, L., Suresh, K., Rao, K. P., Hort, N., Blawert, C., Mendis, C. L., et al. (2016). “Microstructure and properties of magnesium alloy Mg-1Zn-1Ca (ZX11),” in Magnesium technology 2015. Editors M. V. Manuel, A. Singh, M. Alderman, and N. R. Neelameggham (Cham: Springer International Publishing), 419–423.
Kawalla, C., Berkel, W., Kawalla, R., Höck, M., and Ligarski, M. (2018). Material flow cost accounting analysis of twin-roll casting magnesium strips. Procedia Manuf. 15, 193–200. doi:10.1016/j.promfg.2018.07.194
Kittner, K., Kaden, C., Ullmann, M., and Prahl, U. (2024). Production of AZ80 magnesium alloy wires: influence of heat treatment on microstructure and properties after twin-roll casting. Prod. Eng. Res. Devel. doi:10.1007/s11740-024-01310-1
Kittner, K., Ullmann, M., Henseler, T., Kawalla, R., and Prahl, U. (2019). Microstructure and hot deformation behavior of twin roll cast Mg-2Zn-1Al-0.3Ca alloy. Mater. (Basel) 12, 1020. doi:10.3390/ma12071020
Kondori, B., and Mahmudi, R. (2010). Effect of Ca additions on the microstructure, thermal stability and mechanical properties of a cast AM60 magnesium alloy. Mater. Sci. Eng. A 527, 2014–2021. doi:10.1016/j.msea.2009.11.043
Kong, T., Kwak, B. J., Kim, J., Lee, J. H., Park, S. H., Kim, J. H., et al. (2020). Tailoring strength-ductility balance of caliber-rolled AZ31 Mg alloy through subsequent annealing. J. Magnesium Alloys 8, 163–171. doi:10.1016/j.jma.2019.11.005
Krbetschek, C., Berge, F., Oswald, M., Ullmann, M., and Kawalla, R. (2016). “Microstructure investigations of inverse segregations in twin-roll cast AZ31 strips,” in Magnesium technology 2016. Editors A. Singh, K. Solanki, M. V. Manuel, and N. R. Neelameggham (Cham: Springer International Publishing), 369–374.
Li, B., Liao, M., Ma, Q., and McClelland, Z. (2015). Structure of grain boundaries with 30°[0 0 0 1] misorientation in dynamically recrystallized magnesium alloys. Comput. Mater. Sci. 101, 175–180. doi:10.1016/j.commatsci.2015.01.034
Liu, B., Yang, J., Zhang, X., Yang, Q., Zhang, J., and Li, X. (2023). Development and application of magnesium alloy parts for automotive OEMs: a review. J. Magnesium Alloys 11, 15–47. doi:10.1016/j.jma.2022.12.015
Loukil, N. (2022). “Alloying elements of magnesium alloys: a literature review,” in Magnesium alloys structure and properties.
Máthis, K., Horváth, K., Farkas, G., Choe, H., Shin, K. S., and Vinogradov, A. (2018). Investigation of the microstructure evolution and deformation mechanisms of a Mg-Zn-Zr-re twin-roll-cast magnesium sheet by in-situ experimental techniques. Mater. (Basel) 11, 200. doi:10.3390/ma11020200
Mohammadi Mazraeshahi, E., Nami, B., Miresmaeili, S. M., and Tabatabaei, S. M. (2015). Effect of Si on the creep properties of AZ61 cast magnesium alloy. Mater. and Des. 76, 64–70. doi:10.1016/j.matdes.2015.03.021
Moses, M., Ullmann, M., and Prahl, U. (2023). Twin-roll casting as a grain refinement method and its influence on the microstructure and deformation behavior of an AZ31 magnesium alloy wire. Crystals 13, 1409. doi:10.3390/cryst13101409
Moses, M., Wemme, H., Ullmann, M., Kawalla, R., and Prahl, U. (2019). “Twin-roll casting of magnesium wire: an innovative continuous production route,” in METAL 2019 - 28th international conference on metallurgy and materials (TANGER Ltd), 438–443. doi:10.37904/metal.2019.812
Neh, K., Ullmann, M., and Kawalla, R. (2014). Twin-roll-casting and hot rolling of magnesium alloy WE43. Procedia Eng. 81, 1553–1558. doi:10.1016/j.proeng.2014.10.189
Neh, K., Ullmann, M., and Kawalla, R. (2016). Substitution of rare earth elements in hot rolled magnesium alloys with improved mechanical properties. MSF 854, 57–64. doi:10.4028/www.scientific.net/MSF.854.57
Neh, K., Ullmann, M., Oswald, M., Berge, F., and Kawalla, R. (2015). Twin roll casting and strip rolling of several magnesium alloys. Mater. Today Proc. 2, S45–S52. doi:10.1016/j.matpr.2015.05.013
Nie, J. F., Shin, K. S., and Zeng, Z. R. (2020). Microstructure, deformation, and property of wrought magnesium alloys. Metall. Mater. Trans. 51, 6045–6109. doi:10.1007/s11661-020-05974-z
Onuki, Y., Hara, K., Utsunomiya, H., and Szpunar, J. A. (2015). Textures and microstructures formed in WE43 and AZ31 magnesium alloys during high speed rolling and their formation mechanisms. IOP Conf. Ser. Mater. Sci. Eng. 82, 012028. doi:10.1088/1757-899X/82/1/012028
Park, S. S., Bae, G. T., Kang, D. H., Jung, I.-H., Shin, K. S., and Kim, N. J. (2007). Microstructure and tensile properties of twin-roll cast Mg–Zn–Mn–Al alloys. Scr. Mater. 57, 793–796. doi:10.1016/j.scriptamat.2007.07.013
Pekguleryuz, M. O. (2012). “Current developments in wrought magnesium alloys,” in Advances in wrought magnesium alloys. Elsevier, 3–62.
Prasad, S. V. S., Prasad, S. B., Verma, K., Mishra, R. K., Kumar, V., and Singh, S. (2022). The role and significance of Magnesium in modern day research-A review. J. Magnesium Alloys 10, 1–61. doi:10.1016/j.jma.2021.05.012
Sheikhani, A., Roumina, R., and Mahmudi, R. (2022). Texture softening in a rare earth elements-containing AZ31 magnesium alloy during hot compression deformation. J. Mater. Res. Technol. 18, 4089–4098. doi:10.1016/j.jmrt.2022.04.079
Simanjuntak, S., Cavanaugh, M. K., Gandel, D. S., Easton, M. A., Gibson, M. A., and Birbilis, N. (2015). The influence of iron, manganese, and zirconium on the corrosion of magnesium: an artificial neural network approach. CORROSION 71, 199–208. doi:10.5006/1467
Tan, J., and Ramakrishna, S. (2021). Applications of magnesium and its alloys: a review. Appl. Sci. 11, 6861. doi:10.3390/app11156861
Tesař, K., Balík, K., Sucharda, Z., and Jäger, A. (2020). Direct extrusion of thin Mg wires for biomedical applications. Trans. Nonferrous Metals Soc. China 30, 373–381. doi:10.1016/S1003-6326(20)65219-0
Ullmann, M., Kittner, K., Henseler, T., Stöcker, A., Prahl, U., and Kawalla, R. (2019). Development of new alloy systems and innovative processing technologies for the production of magnesium flat products with excellent property profile. Procedia Manuf. 27, 203–208. doi:10.1016/j.promfg.2018.12.065
Ullmann, M., Stirl, M., and Prahl, U. (2024). Twin-roll casting defects in light metals. J. Mater Sci. 59, 19003–19022. doi:10.1007/s10853-024-10211-8
Uppal, G., Thakur, A., Chauhan, A., and Bala, S. (2022). Magnesium based implants for functional bone tissue regeneration – a review. J. Magnesium Alloys 10, 356–386. doi:10.1016/j.jma.2021.08.017
Wang, X., Du, Y., Liu, D., and Jiang, B. (2020). Significant improvement in mechanical properties of Mg-Zn-La alloy by minor Ca addition. Mater. Charact. 160, 110130. doi:10.1016/j.matchar.2020.110130
Yang, L., Liu, G., Ma, L., Zhang, E., Zhou, X., and Thompson, G. (2018). Effect of iron content on the corrosion of pure magnesium: critical factor for iron tolerance limit. Corros. Sci. 139, 421–429. doi:10.1016/j.corsci.2018.04.024
Zecevic, M., Beyerlein, I. J., and Knezevic, M. (2018). Activity of pyramidal I and II <c+a> slip in Mg alloys as revealed by texture development. J. Mech. Phys. Solids 111, 290–307. doi:10.1016/j.jmps.2017.11.004
Zhang, C., Wu, D., He, Y., Pan, W., Wang, J., and Han, E. (2023). Twinning behavior, microstructure evolution and mechanical property of random-orientated ZK60 Mg alloy compressed at room temperature. Mater. (Basel) 16, 1163. doi:10.3390/ma16031163
Keywords: twin-roll casting, AZ31, AZ80, ZAX210, microstructure
Citation: Kaden C, Kittner K, Ullmann M and Prahl U (2025) Twin-roll casting of wire of magnesium alloys. Front. Met. Alloy. 4:1528735. doi: 10.3389/ftmal.2025.1528735
Received: 15 November 2024; Accepted: 14 February 2025;
Published: 14 March 2025.
Edited by:
Mert Efe, Pacific Northwest National Laboratory (DOE), United StatesReviewed by:
Derya Dispinar, Foseco, NetherlandsCopyright © 2025 Kaden, Kittner, Ullmann and Prahl. This is an open-access article distributed under the terms of the Creative Commons Attribution License (CC BY). The use, distribution or reproduction in other forums is permitted, provided the original author(s) and the copyright owner(s) are credited and that the original publication in this journal is cited, in accordance with accepted academic practice. No use, distribution or reproduction is permitted which does not comply with these terms.
*Correspondence: Christoph Kaden, Y2hyaXN0b3BoLmthZGVuQGltZi50dS1mcmVpYmVyZy5kZQ==
Disclaimer: All claims expressed in this article are solely those of the authors and do not necessarily represent those of their affiliated organizations, or those of the publisher, the editors and the reviewers. Any product that may be evaluated in this article or claim that may be made by its manufacturer is not guaranteed or endorsed by the publisher.
Research integrity at Frontiers
Learn more about the work of our research integrity team to safeguard the quality of each article we publish.