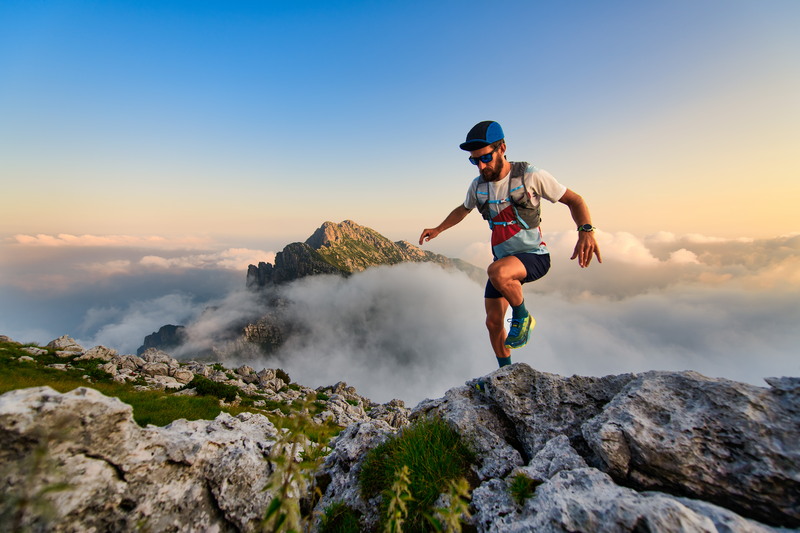
95% of researchers rate our articles as excellent or good
Learn more about the work of our research integrity team to safeguard the quality of each article we publish.
Find out more
PERSPECTIVE article
Front. Met. Alloy , 09 June 2023
Sec. Physical Metallurgy
Volume 2 - 2023 | https://doi.org/10.3389/ftmal.2023.1135481
This article is part of the Research Topic Future Directions in Metals and Alloys View all 3 articles
Metallic materials derive their strength and ductility from their microstructural features. The general principle of alloying is not only to control the phases present in the alloys, but also how the alloying elements can help in microstructural control during the processing of materials. The overall thermodynamic framework of using free energy to explain the stability of an alloy has two significant terms, enthalpy, and entropy. Engineering alloys are processed by several far-from-equilibrium processes. During the processing, the materials are in metastable states. The metastability can also be purposely enhanced through alloy design. This paper provides a perspective on how “high enthalpy states” can be used to tailor the microstructure to overcome the conventional strength-ductility tradeoff. The emergence of new manufacturing processes also provides unique opportunities to design alloys to maximize the potential of such processes. A few illustrative examples are presented to tie the historical use of high enthalpy states and point to future opportunities. Co-development of advanced materials for disruptive new manufacturing processes can be enhanced through integrated computational materials engineering approaches.
Physical metallurgy is a cornerstone of metallic materials (Reza et al., 1973). It encompasses the origin of microstructure and its impact on properties. This perspective paper encourages readers to consider some of the research avenues to control microstructure and publish in this new Frontiers journal that focuses on metals and alloys. In this article, we take a fundamental approach to what aspects control microstructure evolution and, thereby, can be the knobs we turn for microstructural engineering.
A good starting point for this discussion is the basic thermodynamic framework that describes the state of an alloy in equilibrium (DeHoff, 2006; Gaskell David and Laughlin David, 2017). The change in free energy of an alloy during any phase transformation is described in the simplest form as,
where ΔG is the free energy, ΔH is the enthalpy, ΔS is the entropy and T is the temperature. Note that the two terms guiding the discussion are the change in “entropy” and “enthalpy” of the system. In this paper, we are focused mainly on the impact of enthalpy on microstructural evolution and pathways to microstructural engineering. So, why not entropy? The answer is that lattice distortion in an alloy system would be very small and negligible since distortion energy is low compared to the heat of defect formation when subjected to any process. The significant impact would be of the enthalpy as defect formation requires breaking chemical bonds with its neighboring atoms. In contrast, lattice distortion can only change bond length or angle, making “Enthalpy” a significant contributor to tailoring the microstructure.
ΔH or Enthalpy, in thermodynamics of solution, can be explained as the energy required to break 1 mol of bonds of an element. The enthalpy of any system can be altered either chemically or microstructurally (Anand et al., 2021).
• The enthalpy of an alloy is chemically expressed in terms of the bond energy of the constituent elements:
where ω is the interaction parameter. Depending on the nature of the bonds between two elements it is either positive or negative and thus determines the stability of an alloy. Chemically, the enthalpy of some alloys can be tailored by varying the ratios of constituent alloy to produce spinodal microstructure.
• Microstructurally, the enthalpy can be played around by disrupting/altering the local bonds within an alloy, for example, the introduction of vacancies/defects/interstitials.
It varies as:
where ΔNi and ΔNv are the number of interstitials, and vacancies within a system and Ei and Ev are their corresponding energies. While the quantitative increase in enthalpy is given by:
Before getting into specific examples and opportunities for microstructural engineering, we want to briefly capture the well-known microstructural features and how conceptually the enthalpy changes. If we start with a pure metal crystal, at 0 K, it has no lattice defect and it has some intrinsic enthalpy value. As we increase the temperature of this pure metal crystal, an equilibrium concentration of vacancies form (Damask and Dienes, 1971; Miedema, 1979; Novikov et al., 1980; Kobelev and Khonik, 2018). Conceptually we can visualize that the enthalpy of the system is increasing as there is heat of formation associated with each vacancy. This is our baseline of equilibrium value of enthalpy for a given material. Now, let us heat this crystal to 0.9 Tm, where Tm is the absolute melting temperature of this pure metal. If this specimen is then rapidly quenched, then the lattice retains the excess vacancy, i.e., the crystal is at higher state of enthalpy! Such processing step is very common for all precipitation strengthened alloys. Compare the two microstructural states of Al-4%Cu alloy single crystal. If this alloy is very slowly cooled, it will have an equilibrium microstructure consisting of an Al-Cu solid solution matrix and coarse Al2Cu particles (Laird and Aaronson, 1966; Wang et al., 2004). The second phase particle density will be low. However, the quenched specimen will have supersaturated solid solution matrix. The matrix is now in a high enthalpy state because excess number of alloying atoms and thermal vacancies are trapped in the lattice as shown in Figure 1A. Upon low temperature aging, the excess solutes form a large number of small second phase particles. The energy level of the system becomes lower after this step. This refined distribution of precipitates leads to higher strength. Heat treatment of precipitation strengthened aluminum alloys is being practiced for more than a century and is the basis for T6 temper in aluminum alloys (Fine, 1975). The effectiveness of precipitation strengthening is further enhanced in some aluminum alloys by introducing a rolling step after quenching. In such a case, the peak hardened temper is referred as T8 temper. Introduction of dislocations in lattice leads to displacement of atoms from its pristine lattice position. This effect is confined to a finite distance from the dislocation core. Energetically, this is also a higher state of enthalpy as the system’s overall energy is enhanced. The presence of lattice dislocations, provides sites for nucleation of precipitates, thereby enhancing the nucleation density. In certain aluminum alloys, the T3→T8 approach provides more effective precipitation strengthening than T4→T6 path. The only difference being the intermediate step of cold work after solution treatment and quenching.
FIGURE 1. Illustration of higher enthalpy states in (A) a single-phase alloy with lattice defects, and (B) a metastable dual-phase alloy that undergoes deformation induced phase transformation.
Incorporation of interfaces constitutes planar microstructural features and it increases the free energy of the system as well. Over the last 40 years or so, a number of severe plastic deformation processes have emerged that refine the grain size to ultrafine grained regime (grain size < 1 µm) and even nanocrystalline level (grain size <100 nm). The refinement of grains through severe plastic deformation is a top-down approach (McFadden et al., 1999; Mishra et al., 1999; Setman et al., 2010). When the lattice defect densities of 0-dimension (vacancies) (Damask and Dienes, 1971; Mishin et al., 2009; Kobelev and Khonik, 2018; Korte-Kerzel et al., 2021; Varotsos et al., 2022), 1-dimension (dislocations) (Gibbs, 1969)and 2-dimensions (interfaces) are incorporated in a single-phase alloy, the energy state is enhanced. This is schematically illustrated in Figure 1A. Using Eq. 4, we can deduce that enthalpy is directly proportional to the number of defects introduced into the system,
A second category that we want to discuss is the deformation induced transformation of metastable alloys. The metastability engineering is first done through the alloy chemistry. For this, the alloy must have at least two crystal structure or allotropic phases. Figure 1B depicts the deformation induced transformation from phase A to phase B (Agrawal et al., 2020; Gupta et al., 2021). Conceptually the applied stress provides the energy to overcome the thermodynamic barrier for transformation from one phase to another. Note that by incorporating the lattice defects or microstructural features, the intrinsic energy level of the starting alloy is altered, leading to change in the transformation barrier. Such a change can be studied by carefully constructing an experimental matrix that quantifies the rate of deformation induced transformation as well as the full extent of this transformation. A key distinction to note is that while the alloy chemistry provides the possibility of this transformation, thermo-mechanical processing creates microstructural variants. For example, a study on friction stir welded Cu-containing high entropy alloy demonstrated the change in enthalpy for different zones of the weld in comparison to the base material using differential scanning calorimetry (DSC) (Gupta et al., 2021). The DSC results showed that the change in enthalpy was completely dependent upon the microstructure, and we could tailor mechanical strength without compromising the ductility by attaining metastability of phases.
While the phase diagram based predictions are based on equilibrium thermodynamics, most of the conventional processing is non-equilibrium. More than 6 decades ago, researchers realized that major opportunities lie in far-from-equilibrium processing, both liquid-based and solid state-based. In this perspective article, we take two illustrative examples. Both these examples build on efforts to extend the solubility of alloying elements and obtain microstructures that cannot be obtained by conventional processing. During the far-from-equilibrium processing the alloys go through metastable states, which can be fundamentally treated as high enthalpy states that govern the evolution of microstructure.
The evolution of rapid solidification from pioneering work of Pol Duwez and coworkers (Duwez et al., 2004) has been remarkable. The initial work on an immiscible Cu-Ag system showed that metallic glass can be formed at rapid solidification rates. In 1980s, Inoue and co-workers (Chen et al., 1985; Inoue and Zhang, 1996) transitioned this work to bulk metallic glasses through alloy composition design. The bulk metallic glasses could be synthesized at lower cooling rates and resulted in a very large range of compositions. However, balance of mechanical properties remains Achilles heel for metallic glasses and has thus limited its structural applications. During this same period, rapid solidification processing of crystalline metallic alloys was pursued in many forms (Das and Davis, 1988; Froes and Carbonara, 1988; Schwarz and Koch, 1998; Suryanarayana et al., 2013). In 1980s and 90s, two popular forms were atomization of alloys (Lawley, 1981; Lavernia et al., 1992; Bowman et al., 1997) for powders and planar flow casting of ribbons (Carpenter and Steen, 1992; Viala et al., 1996; Lee and Hong, 1997; Lee et al., 1998). Both these forms required further powder processing to produce bulk forms. The advantage of excess solid solubility led to synthesis of bulk ultrafine and nanocrystalline alloys. For example, a number of aluminum alloys were developed with the hope of obtaining creep-resistant alloys or so-called high temperature aluminum alloys. These alloys had as much as 20–30 vol% of second phase particles. Such alloys cannot be conventionally processed! The overall mapping of these efforts in captured in Figure 2.
FIGURE 2. Far-from equilibrium processing of alloys based on extended solid solubility. Liquid metal-based processing of alloys at high cooling rate provides opportunities to tailor microstructure. Previous fundamental knowledge of rapid solidification derived microstructure can now be applied to powder based additive manufacturing processes, like laser-powder bed or direct energy deposition. Solid state processing is based on shear driven dissolution of alloying element.
The laser powder bed additive manufacturing (LPB-AM) is providing an unprecedented component design flexibility and is an excellent approach for unitization of parts. An intrinsic feature of LPB-AM is the in-situ rapid solidification of alloys. But similar to any fusion-based process, LPB-AM does result in solidification related porosity. Mishra and Thapliyal (Mishra and Thapliyal, 2021) reviewed the approaches for LPB-AM of aluminum alloys and suggested that the best properties can be obtained for alloys designed specifically for additive manufacturing. Clare et al. (Clare et al., 2022) have done a broader review of different alloy categories. Philosophically there are two lines of thoughts. One can argue that if we really master the process and print the component in an optimized process window, it will be defect-free. On the other hand, it can be argued that given the physics of volume change associated with liquid to solid transition, there will always be some porosity. The second line of thought can draw from experiences of casting or fusion welding where there is always some level of porosity. If one accepts that the second line of thinking is more practical or appropriate, then the issue turns to “how to maximize the performance for structural applications”. Can one intrinsically change the damage tolerance? Yes, if one designs the alloys for additive manufacturing. Consider these two examples. The first one is for the aluminum alloys. To analyze the stress response of the alloy, one should look at the details of the stress-strain curve. Is there good work hardening? Does the stress-strain curve exhibit good non-uniform elongation as well? Both these features are indications of how stable the deformation of specimen is in the presence of any process-related micro-defects like porosity. For example, a newly designed Al-3Ni-1Ti-0.8Zr alloy shows excellent uniform elongation as well as good resistance to necking in the form of extended non-uniform elongation (Thapliyal et al., 2021; Haridas et al., 2023). The alloy is designed with the help of Scheil-Gulliver model where solidification occurs under rapid solidification, allowing solute redistribution to alter and achieve desired level of properties with minimal defects.
The second example is from Thapliyal et al. (Thapliyal et al., 2020). They describe the “damage tolerant” approach for an AM component. The approach is based on the concept of stress-induced phase transformation. The porosity in a material represents elastic discontinuity. Upon loading, such regions develop stress concentration. The metastable HEAs exhibit transformation induced plasticity (TRIP) (Mishra et al., 2021). These stressed regions locally undergo transformation and hardened the material locally. Such an approach leads to high structural performance by delaying the onset of failure mechanisms. Currently, this has been demonstrated only with FCC to HCP phase transformation. Opportunities exist to use other transformations in the Burgers triangle, namely, any of the other combinations from FCC-HCP-BCC triangle. Note that in the example citing here, FCC to HCP transformation led to reduction in volume. Triggering transformation from FCC or HCP to BCC will result in volume expansion (Agrawal et al., 2020)! So, the possibilities of micromanaging the transformation path through alloy design is tremendous and can be explored with the help of ICME approach.
Solid state processing to force mechanical mixing is another pathway to enhance metastability. This line of research has been developed from 1970s (Liu et al., 1995; Suryanarayana, 2001; Perepezko, 2004). The simplest method was high energy ball milling of constituent elements. Extensive research has been done using this path and it has been demonstrated that mechanical alloying produces metallic glasses in many alloy systems; in fact, this has wider range than rapid solidification approach. The extended solid solubility is also a parallel pathway that has been applied to many metallic systems including immiscible alloys. The comparison of the state of metastability of a hypothetical composition between solid state processed and rapid solidification processed alloy is intriguing. Are both alloys with identical composition in extended solid solution condition same?
Last 3 decades has seen emergence of many severe plastic deformation methods. Friction stir processing among them is a unique high temperature severe plastic deformation method that can create nanostructured immiscible alloys. Remarkably, the Cu-Ag-Nb immiscible system displayed exceptional thermal stability up to 500°C (Raabe and Mattissen, 1998). Initial results show that the approach is amenable to manipulation of matrix and the Cu-Al-Nb system shows low stacking fault energy matrix with thermally stable nanostructures. Additionally, results on metastable HEAs show ability to create highly interfaced materials. The metastability of the HEAs can be altered, which in turn impacts the stress-strain response and associated transformation induced plasticity (TRIP). Solid state processing of such nanostructured alloys and highly interfaced alloys opens a new domain not easily accessible by other processing techniques.
This brief perspective paper highlights numerous possibilities of integrating alloy design with far-from-equilibrium processing to control the microstructural evolution pathways using high enthalpy states. Such approaches can lead to hierarchical activation of deformation mechanisms resulting in better combination of mechanical properties. This new journal of Frontiers in Metals and Alloys encourages researchers to pursue the research opportunities outlined here and submit it for publication.
The original contributions presented in the study are included in the article/supplementary material further inquiries can be directed to cmFqaXYubWlzaHJhQHVudC5lZHU=.
RM contributed to conception of this approach and wrote the first draft of the manuscript. SG helped with literature search and preparation of figures. All authors contributed to the article and approved the submitted version.
RM is grateful for funding from the Army Research Laboratory over the last seven years to study the metastable nature of alloys.
The authors declare that the research was conducted in the absence of any commercial or financial relationships that could be construed as a potential conflict of interest.
The author RM declared that they were an editorial board member of Frontiers, at the time of submission. This had no impact on the peer review process and the final decision.
All claims expressed in this article are solely those of the authors and do not necessarily represent those of their affiliated organizations, or those of the publisher, the editors and the reviewers. Any product that may be evaluated in this article, or claim that may be made by its manufacturer, is not guaranteed or endorsed by the publisher.
Agrawal, P., Shukla, S., Gupta, S., Agrawal, P., and Mishra, R. S. (2020). Friction stir gradient alloying: A high-throughput method to explore the influence of V in enabling HCP to BCC transformation in a γ-FCC dominated high entropy alloy. Appl. Mater Today 21, 100853. doi:10.1016/j.apmt.2020.100853
Anand, S., Male, J. P., Wolverton, C., and Snyder, G. J. (2021). Visualizing defect energetics. Mater Horiz. 8, 1966–1975. doi:10.1039/d1mh00397f
Bowman, R. C., Witham, C., Fultz, B., Ratnakumar, B. v., Ellis, T. W., and Anderson, I. E. (1997). Hydriding behavior of gas-atomized AB5 alloys. J. Alloys Compd. 253–254, 613–616. doi:10.1016/s0925-8388(96)02929-5
Carpenter, J. K., and Steen, P. H. (1992). Planar-flow spin-casting of molten metals: Process behaviour. J. Mater. Sci. 27, 215–225. doi:10.1007/bf02403666
Chen, H. S., Inoue, A., and Masumoto, T. (1985). Two-stage enthalpy relaxation behaviour of (Fe0.5Ni0.5)83P17 and (Fe0.5Ni0.5)83B17 amorphous alloys upon annealing. J. Mater Sci. 20, 2417–2438. doi:10.1007/bf00556071
Clare, A. T., Mishra, R. S., Merklein, M., Tan, H., Todd, I., Chechik, L., et al. (2022). Alloy design and adaptation for additive manufacture. J. Mater Process Technol. 299, 117358. doi:10.1016/j.jmatprotec.2021.117358
Suryanarayana, C., Froes, F. H., and Rowe, R. G. (2013). Rapid solidification processing of titanium alloys. Int. Mater. Rev. 36, 85–123. doi:10.1179/Imr.1991.36.1.85
Das, S. K., and Davis, L. A. (1988). High performance aerospace alloys via rapid solidification processing. Mater. Sci. Eng. 98, 1–12. doi:10.1016/0025-5416(88)90116-4
Duwez, P., Willens, R. H., and Klement, W. (2004). Continuous series of metastable solid solutions in silver-copper alloys. J. Appl. Phys. 31, 1136–1137. doi:10.1063/1.1735777
Fine, M. E. (1975). Precipitation hardening of aluminum alloys. Metall. Trans. A 6, 625–630. doi:10.1007/bf02672283
Froes, F. H., and Carbonara, R. (1988). Applications of rapid solidification. JOM 40, 20–27. doi:10.1007/bf03258827
Gaskell David, R., and Laughlin David, E. (2017). Introduction to the thermodynamics of materials. Sixth Edition. Boca Raton, FL: Taylor and Francis.
Gibbs, G. B. (1969). Thermodynamic analysis of dislocation glide controlled by dispersed local obstacles. Mater. Sci. Eng. 4, 313–328. doi:10.1016/0025-5416(69)90026-3
Gupta, S., Agrawal, P., Nene, S. S., and Mishra, R. S. (2021). Friction stir welding of γ-fcc dominated metastable high entropy alloy: Microstructural evolution and strength. Scr. Mater 204, 114161. doi:10.1016/j.scriptamat.2021.114161
Haridas, R. S., Agrawal, P., Thapliyal, S., Agrawal, P., Dhal, A., Shukla, S., et al. (2023). Synergy of tensile strength and high cycle fatigue properties in a novel additively manufactured Al-Ni-Ti-Zr alloy with a heterogeneous microstructure. Addit. Manuf. 62, 103380. doi:10.1016/j.addma.2022.103380
Inoue, A., and Zhang, T. (1996). Fabrication of Bulk Glassy Zr<SUB>55</SUB>Al<SUB>10</SUB>Ni<SUB>5</SUB>Cu<SUB>30</SUB> Alloy of 30 mm in Diameter by a Suction Casting Method. Mater. Trans. JIM 37, 185–187. doi:10.2320/matertrans1989.37.185
Kobelev, N. P., and Khonik, V. A. (2018). On the enthalpy and entropy of point defect formation in crystals. J. Exp. Theor. Phys. 126, 340–346. doi:10.1134/s1063776118030032
Korte-Kerzel, S., Hickel, T., Huber, L., Raabe, D., Sandlöbes-Haut, S., and Todorova, M. (2021). Defect phases – thermodynamics and impact on material properties. J. Neugebauer 67, 89–117. doi:10.1080/09506608.2021.1930734
Laird, C., and Aaronson, H. I. (1966). Mechanisms of formation of θ and dissolution of θ′ precipitates in an Al-4% Cu alloy. Acta Metall. 14, 171–185. doi:10.1016/0001-6160(66)90298-7
Lavernia, E. J., Srivatsan, T. S., and Rangel, R. H. (1992). Atomization Sprays 2, 253–274. doi:10.1615/atomizspr.v2.i3.40
Lawley, A. (1981). Atomization of specialty alloy powders. J. Metals 33, 13–18. doi:10.1007/bf03354395
Lee, K. Y., and Hong, C. P. (1997). Stochastic modeling of solidification grain structures of Al-Cu crystalline ribbons in planar flow casting. ISIJ Int. 37, 38–46. doi:10.2355/isijinternational.37.38
Lee, S. M., O’Reilly, K. A. Q., Cantor, B., and Hong, C. P. (1998). Microstructural transitions in Al–Cu ribbons manufactured by planar flow casting. Mater. Sci. Eng. A 249, 233–240. doi:10.1016/s0921-5093(98)00482-1
Liu, L., Padella, F., Guo, W., and Magini, M. (1995). Solid state reactions induced by mechanical alloying in metal-silicon (metal = Mo, Nb) systems. Acta Metallurgica Materialia 43, 3755–3761. doi:10.1016/0956-7151(95)90159-0
Makarov, A. S., Afonin, G. v., Konchakov, R. A., Qiao, J. C., Aronin, A. S., Kobelev, N. P., et al. (2021). One-to-one correlation between the kinetics of the enthalpy changes and the number of defects assumed responsible for structural relaxation in metallic glasses. J. Non Cryst. Solids 558, 120672. doi:10.1016/j.jnoncrysol.2021.120672
Miedema, A. R. (1979). The Formation enthalpy of monovacancies ın metals and intermetallic compounds. Zeitschrift Fuer Metallkunde/Materials Res. Adv. Tech. 70, 345–353. doi:10.1515/ijmr-1979-700601
Mishin, Y., Sørensen, M. R., and Voter, A. F. (2009). Density functional theory calculations of the thermodynamic and kinetic properties of point defects in β-U. Philos. Mag. 81, 2591–2612.
Mishra, R. S., Haridas, R. S., and Agrawal, P. (2021). High entropy alloys – tunability of deformation mechanisms through integration of compositional and microstructural domains. Mater. Sci. Eng. A 812, 141085. doi:10.1016/j.msea.2021.141085
Mishra, R. S., McFadden, S. X., Valiev, R. Z., and Mukherjee, A. K. (1999). Deformation mechanisms and tensile superplasticity in nanocrystalline materials. Jom 51, 37–40. doi:10.1007/s11837-999-0010-1
Mishra, R. S., and Thapliyal, S. (2021). Design approaches for printability-performance synergy in Al alloys for laser-powder bed additive manufacturing. Mater Des. 204, 109640. doi:10.1016/j.matdes.2021.109640
Novikov, I. I., Roshchupkin, V. v., Semashko, N. A., and Fordeeva, L. K. (1980). Experimental investigation of vacancy effects in pure metals. J. Eng. Phys. 39, 1316–1319. doi:10.1007/bf00825700
Perepezko, J. H. (2004). Nucleation-controlled reactions and metastable structures. Prog. Mater Sci. 49, 263–284. doi:10.1016/s0079-6425(03)00028-8
Raabe, D., and Mattissen, D. (1998). Microstructure and mechanical properties of a cast and wire-drawn ternary Cu–Ag–Nb in situ composite. Acta Mater 46, 5973–5984. doi:10.1016/s1359-6454(98)00218-3
Reza, A., Lara, A., and Reed-Hill Robert, E. (1973). Physical metallurgy principles. Stamford, CT: PWS-Kent Pub.
Schwarz, R. B., and Koch, C. C. (1998). Formation of amorphous alloys by the mechanical alloying of crystalline powders of pure metals and powders of intermetallics. Appl. Phys. Lett. 49, 146–148. doi:10.1063/1.97206
Setman, D., Kerber, M. B., Schafler, E., and Zehetbauer, M. J. (2010). Activation enthalpies of deformation-induced lattice defects in severe plastic deformation nanometals measured by differential scanning calorimetry. Metall. Mater Trans. A Phys. Metall. Mater Sci. 41, 810–815. doi:10.1007/s11661-009-0058-0
Suryanarayana, C. (2001). Mechanical alloying and milling. Prog. Mater Sci. 46, 1–184. doi:10.1016/s0079-6425(99)00010-9
McFadden, S. X., Mishra, R. S., Vallev, R. Z., Zhilyaev, A. P., and Mukherjee, A. K. (1999). Low-temperature superplasticity in nanostructured nickel and metal alloys. Nature 398, 684–686. doi:10.1038/19486
Thapliyal, S., Nene, S. S., Agrawal, P., Wang, T., Morphew, C., Mishra, R. S., et al. (2020). Damage-tolerant, corrosion-resistant high entropy alloy with high strength and ductility by laser powder bed fusion additive manufacturing. Addit. Manuf. 36, 101455. doi:10.1016/j.addma.2020.101455
Thapliyal, S., Shukla, S., Zhou, L., Hyer, H., Agrawal, P., Agrawal, P., et al. (2021). Design of heterogeneous structured Al alloys with wide processing window for laser-powder bed fusion additive manufacturing. Addit. Manuf. 42, 102002. doi:10.1016/j.addma.2021.102002
Varotsos, P. A., Sarlis, N. V., and Skordas, E. S. (2022). Thermodynamics of point defects in solids and relation with the bulk properties: Recent results. Cryst. (Basel) 12, 686. doi:10.3390/cryst12050686
Viala, B., Degauque, J., Fagot, M., Baricco, M., Ferrara, E., and Fiorillo, F. (1996). Study of the brittle behaviour of annealed Fe-6.5 wt%Si ribbons produced by planar flow casting. Mater. Sci. Eng. A 212, 62–68. doi:10.1016/0921-5093(96)10188-x
Keywords: enthalpy, microstrtural engineering, structural alloys, far-from-equilibrium processing, strength-ductility trade-off, integrated computational materials engineering (ICME)
Citation: Mishra RS and Gupta S (2023) Microstructural engineering through high enthalpy states: implications for far-from-equilibrium processing of structural alloys. Front. Met. Alloy 2:1135481. doi: 10.3389/ftmal.2023.1135481
Received: 31 December 2022; Accepted: 17 May 2023;
Published: 09 June 2023.
Edited by:
Binhan Sun, East China University of Science and Technology, ChinaReviewed by:
Minghui Cai, Northeastern University, ChinaCopyright © 2023 Mishra and Gupta. This is an open-access article distributed under the terms of the Creative Commons Attribution License (CC BY). The use, distribution or reproduction in other forums is permitted, provided the original author(s) and the copyright owner(s) are credited and that the original publication in this journal is cited, in accordance with accepted academic practice. No use, distribution or reproduction is permitted which does not comply with these terms.
*Correspondence: Rajiv S. Mishra, cmFqaXYubWlzaHJhQHVudC5lZHU=
Disclaimer: All claims expressed in this article are solely those of the authors and do not necessarily represent those of their affiliated organizations, or those of the publisher, the editors and the reviewers. Any product that may be evaluated in this article or claim that may be made by its manufacturer is not guaranteed or endorsed by the publisher.
Research integrity at Frontiers
Learn more about the work of our research integrity team to safeguard the quality of each article we publish.