- 1Department of Chemical Engineering, Ege University, Izmir, Türkiye
- 2Department of Environmental Sciences, Graduate School of Natural and Applied Sciences, Ege University, Izmir, Türkiye
- 3Department of Refinery and Petrochemical Technology, Aliağa Vocational School, Ege University, Izmir, Türkiye
- 4Department of International Water Resources, Izmir Institute of Technology, Urla, Türkiye
In this study, high mineral scaling propensity geothermal water was treated using a FilmTech BW30-2540 reverse osmosis (RO) membrane, integrated into a mini-pilot scale membrane test unit installed at a geothermal heating center. The study was conducted in eight cycles by monitoring membrane fouling via membrane flux decline. Firstly, the geothermal water coming from the source at approximately 80°C was taken into holding tanks and allowed to reach approximately room temperature (25°C). Then, the geothermal water that reached this temperature was used in the system. The fouling degree was compared to the initial permeability of the virgin membrane. After each treatment cycle, the membrane’s permeability was evaluated both before and after acid cleaning. Permeability testing was conducted using RO permeate as the feed, under pressures ranging from 8 to 30 bar, with 2-bar increments. The geothermal water treatment was performed at a constant pressure of 15 bar, with a water recovery maintained at approximately 50%. Prior to each permeability test, the membrane underwent a 45-min wash with citric acid, followed by a rinse with RO permeate. During the first five cycles, citric acid was used at a concentration of 1000 mg/L, achieving a flux recovery of 86.6% by the fifth cycle. In the subsequent three cycles, the citric acid concentration was increased to 4000 mg/L, resulting in a flux recovery of 63.4% by the eighth cycle. The study concluded that scale formation on the membrane surface intensified as the number of cycles increased.
1 Introduction
Fresh water is essential not only for sustaining life but also for supporting industrial growth. Over the past decade, rapid population growth and accelerated modernization in many developed and developing countries have significantly increased the global demand for clean water (Baten and Stummeyer, 2012; Goh P. S. et al., 2018). Despite covering 70% of the Earth’s surface, only 0.3% of the available source water is fresh and readily useable, with approximately 90% of global water resources being saline and unsuitable for consumption without proper treatment (Schwarz et al., 1990). To mitigate the depletion of clean and potable water resources, it is imperative to develop and enhance groundwater and saline water treatment processes (Leonard, 1999). Among the alternative water sources that can be treated and utilized for daily needs such as irrigation or portable is spent geothermal water (Baten and Stummeyer, 2012). Nonetheless, geothermal water generally contains high concentrations of dissolved salts and sometimes heavy metals at trace concentrations. Soil and ground water contamination are some of the consequences from direct use of geothermal fluids, which are either for beneficial use or when discarded to receiving bodies or via deep well injection (Jarma et al., 2022). In recent years, various methods and technologies have been developed for the treatment of saline source water, with reverse osmosis (RO) technology emerging and widely adopted across the globe (Baten and Stummeyer, 2012; Goh P. S. et al., 2018; Schwarz et al., 1990). RO technology is recognized for its reliability in producing high-quality water (Jarma et al., 2022), offering membranes that combine excellent contaminants separation and physicochemical properties with high salt rejection, high flux, and robust chemical and thermal stability (Subramani and Jacangelo, 2015).
Despite all of the benefits that the RO membrane offers for generating high-quality water, research investigations over the past several years have concentrated on the creation and upgrading of RO membranes with high salt removal and permeability (Zirehpour et al., 2017; Zhao et al., 2017; Liu et al., 2016). Nonetheless, management of the residual high salinity concentrate (i.e., “brine”) stream, membrane fouling and mineral scaling are lingering major obstacles to even wider scale adoption of RO desalination (Zhao et al., 2017). Depending on membrane characteristics, source water chemistry, and the operational conditions, biofouling, organic fouling, and inorganic scaling may limit the overall performance of RO systems by i) increasing required separation pressure (energy cost), ii) decreasing membrane lifespan, and iii) increasing chemical cleaning frequency (increase downtime) (Saqib and Aljundi, 2016). Membrane fouling seriously impairs the desalination plants’ ability to continue operating sustainably. Fouling can lead to increased operating strain, and a significant reduction in overall efficiency of RO technology (Jiang et al., 2017; She et al., 2016). As a result, the occurrence of scaling is due to (a) precipitation/crystallization of sparingly soluble salts in the bulk of the solution, followed by subsequent deposition onto the membrane surface, and continued crystal growth; and/or (b) direct heterogeneous nucleation on the membrane surface and subsequent crystal growth. In other words, membrane scaling occurs when the concentrations of the scale precursor ions exceed the solubility limits of the mineral salt (Gilron and Hasson, 1987; Lee et al., 1999).
Calcite, silica, and gypsum are the three most prevalent forms of scale in geothermal brine. The calcium compounds, silica and carbonate are commonly found in geothermal brines (Mitrouli et al., 2026). It is therefore common to find scales of metal silicate and metal sulfide in resources that have a higher temperature. Silicate and sulfide scales are commonly associated with several metals, including zinc, iron, lead, magnesium, antimony, and cadmium (Andritsos and Karabelas, 2024).
A few measures, such as enhancing the active layer, were undertaken to address fouling problems in membrane-based desalination processes (Saqib and Aljundi, 2016). However, up to now, periodic freshwater flushing, the use of antiscalants to retard mineral nucleation, or periodic chemical cleaning of the membranes have been some of the methods widely employed to mitigate mineral scaling (Ang et al., 2011). It is noted that insufficient or postponed chemical cleaning can reduce the lifespan of the module and eventually affect the cost of the product water due to higher replacement costs while negatively affecting energy costs due to elevated transmembrane pressure (TMP). The standard methods for evaluating membrane productivity are the rate of flux drop over time and the final product water quality (Klupfel and Frimmel, 2010). Understanding membrane behavior is essential for water productivity. It is therefore of paramount importance to evaluate water permeability of a specific membrane and compared with the subsquent permeability decline for proper desalination plant design.
While antiscalants are a well-established tool in RO system pretreatment, a more systematic and comprehensive understanding of their applications and mechanisms could greatly enhance their effectiveness and sustainability (Goh P. et al., 2018). Membrane fouling is generally divided into removable fouling (loosely attached to the membranes) and permanent fouling such as long-term mineral scaling. Physical cleaning methods, such as air sparging, backwashing, flushing, and vibration, use mechanical forces are some of the methods employed to remove removable foulants from membrane surfaces (Goh P. et al., 2018). Permanent fouling can only be eliminated by chemical cleaning, which should only be performed a few times a year to avoid shortening membrane life (Kimura et al., 2004). Chemical cleaning techniques rely on chemical reactions such as chelation, dispersion, hydrolysis, peptization, saponification, and solubilization are some of the approaches employed for permanent fouling removal (Kimura et al., 2004; Fritsch and Moraru, 2008; Lin et al., 2010). However, it is critical to select the appropriate cleaning agent, cleaning frequency, and cleaning procedure based on the source water chemistry and membrane type (Goh P. et al., 2018; Liikanen et al., 2002). One should also note that frequent chemical cleaning of the membranes will lead to deterioration of the active layer of the membrane and will negatively affect product water quality (Liikanen et al., 2002; Chen et al., 2003).
Although membrane manufacturers suggest an approach of membrane cleaning (Ang et al., 2006), it is of paramount importance to optimize the cleaning agent chemical dose as well as the frequency of chemical cleaning based on the mineral scaling of concern and source water chemistry. The current study therefore aimed to evaluate the efficacy of periodic RO membrane chemical cleaning desalting spent geothermal water of high mineral scaling propensity. The feed to the pilot RO system is a slipstream from the Izmir geothermal heating center spent geothermal fluid stream located in Izmir, Türkiye. A chemical cleaning with a citric acid solution was employed to clean the fouled membranes periodically.
2 Material and methods
The membrane used in the various tests was Filmtech BW30-2540 (Filmtech, Dow Chemicals) 2.5″ x 40″ membrane elements having 2.6 m2 active membrane area and 99.5% NaCl rejection (evaluated for feed solution salinity of 2000 mg/L NaCl at 25°C for applied feed pressure of 15.5 bar), and single element recovery was 15% yielding permeate flow rate of 3.2 m3/day). Other operation conditions of the membrane employed in this study are given in Table 1. Table 2 provides a summary of the characteristics of geothermal water. A Hach-Lange HQ14D model multimeter was used to measure conductivity, pH, total dissolved substances (TDS), and salinity throughout each test. Before starting each test, samples were obtained from the feed. Permeate, feed, and concentrate samples were taken at 30, 60, 120, 180, 240, 270, and 300 min during each membrane test. Boron concentrations in the feed, permeate, and concentrate samples were determined by the curcumin method using Jasco SSE-343 V-530 UV/vis model spectrophotometer. SM 2320 B method was used to calculate the HCO3 concentration during the treatment process.

Table 1. Properties of RO membrane installed at mini-pilot scale membrane test system (Lenntech, 2024).
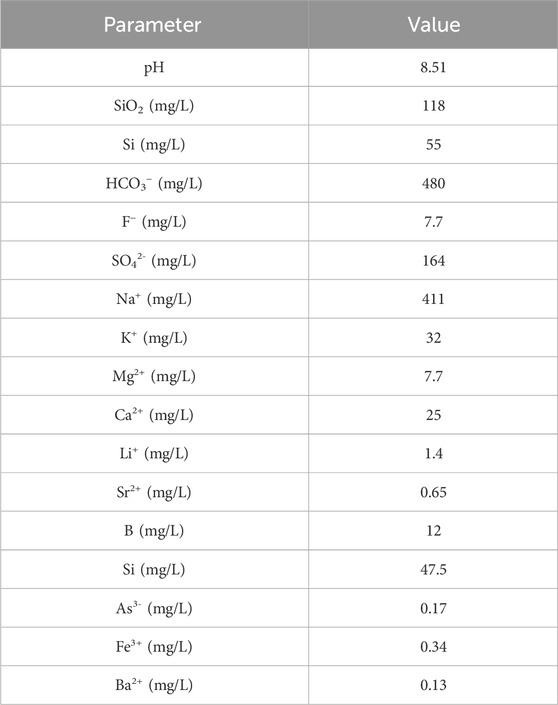
Table 2. The characteristics of spent geothermal water (Jarma et al., 2022).
A mini pilot-scale RO membrane system was installed at the geothermal heating facility in Izmir, Türkiye, as shown in Figure 1. The mini-pilot RO system received its feed from the heating center’s reinjection slipstream at approximately 80°C. The feed to the pilot system was first allowed to cool down to approximately room temperature (25°C) in 5 m3 plastic containers. The RO system was equipped with sensors, along with a control system, for monitoring various streams with respect to pressure, flow rate, and temperature. The RO system water pretreatment train, before RO desalting, included the following two pretreatment options: media filtration using a standard silica sand filter, carbon filter, and 20- and 5-micron cartridge filters. The system is also equipped with an antiscalant dosage pump feeding Ropur (PRI-3000 A) antiscalant at a concentration of 5 mg antiscalant/L-spent geothermal water to be treated, details of the mini-pilot system are given in the literature (Jarma et al., 2021).
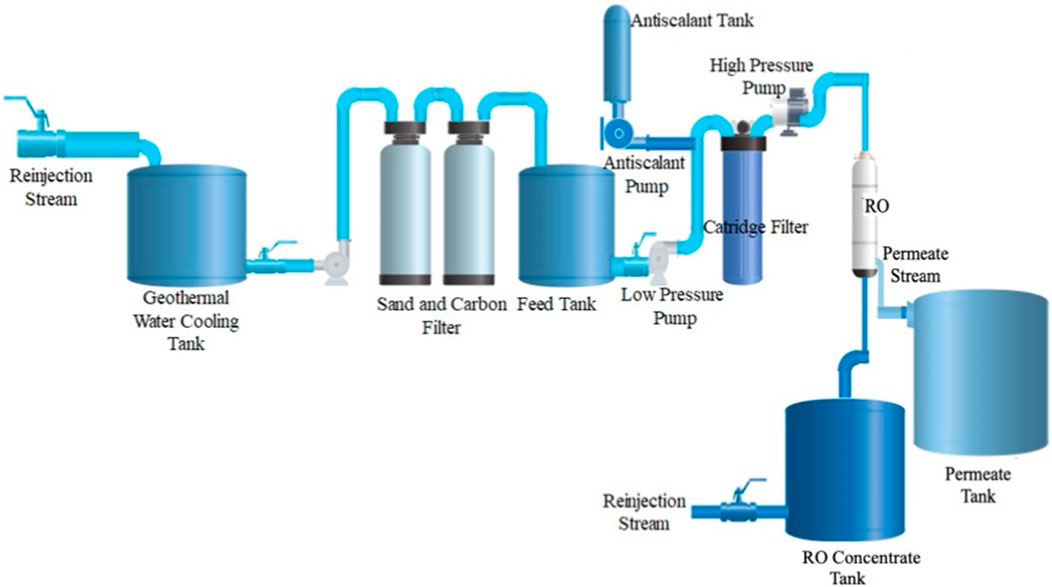
Figure 1. Mini pilot RO system employed for chemical cleaning tests (Adapted from Y.A. Jarma, PhD Thesis, Ege University, 2022 and from A. Zaid, MS Thesis, Ege University, 2023 With permission).
2.1 Calculated parameters for membrane performance evaluation
Equation 1 was used to calculate the permeate flux in this study (Jarma et al., 2021)
where J (L/m2h) and Qp (L/h) are the permeate flux and permeate flow rate, respectively. A (m2) is the membrane active area.
Water recovery of the process was calculated using Equation 2
Qp (L/h) and Qf (L/h) are the flow rates of permeate and feed, respectively.
The membrane rejection in this study was calculated using Equation 3
where Cp (mg/L) and Cf (mg/L) are the concentration of solutes in the permeate and feed streams, respectively.
2.2 Membrane cycle tests
Firstly, the permeability constant of the virgin RO membrane was initiated by passing deionized water through the membrane before the treatment of geothermal water. Permeability experiments were carried out before and after membrane cleaning twice. During the permeability tests, the pressures applied were 8–32 bar with 2 bar increments. Also, oppositely, permeability tests were carried out by decreasing pressure between 32 and 8 bar with a 2 bar decrease. The average values of both measurements were calculated and used in the graph. The treatment of geothermal water was conducted at a constant pressure of 15 bars during 5 h of operation, at a constant water recovery of 50%. Then the RO membrane was cleaned with citric acid for 45 min followed by rinsing with the RO permeate before commencing the permeability test. The chemical cleaning method, which was applied in this study was noted in the literature. The citric acid concentrations during chemical cleaning were kept constant at 1000 mg/L up to the sixth cycle. After the sixth cycle, the water recovery was found to be low, so the acid concentration was doubled to 2000 mg/L for the seventh cycle. To raise the expectations of the study, the eighth cycle was taken as an additional step and the concentration of the citric acid used was doubled to 4000 mg/L.
3 Results and discussion
3.1 Water permeability tests before chemical cleaning
In this study, BW30 type RO membrane was used for the treatment of geothermal water for membrane fouling tests. As mentioned earlier, the permeability of the fresh or virgin membrane is of paramount importance in determining the fouling degree in membrane separation processes. The permeability of a membrane was determined after long-term membrane operation, followed by acid cleaning to remove inorganic foulants. Also, permeability is a measure of the effectiveness of acid cleaning. Since the water to be treated in this study is spent in geothermal water, organic foulants were not expected in the water. Hence, organic cleaning was not considered during the study. Applied pressure of 8–30 bar with increments of 2 bar while RO permeate was used as deionized water was employed during permeability determination. Also, oppositely, permeability tests were performed by decreasing pressure in a range of 32–8 bar with a 2 bar decrease. The average values of both measurements were calculated and used in Figure 2. The slopes obtained from the linearized flux versus pressure plots given in Figure 2 were accepted as permeability as they are very close to the calculated values.
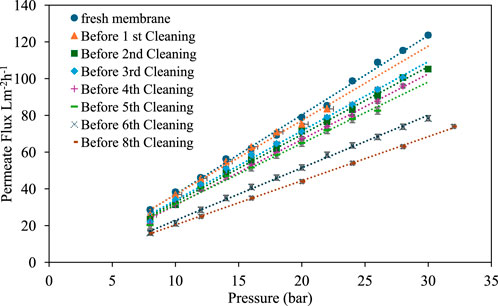
Figure 2. Water permeability test results for BW30 before citric acid cleaning by using RO permeate (Adapted from Y.A. Jarma, PhD Thesis, Ege University (2022) (Jarma, 2022) and from A. Zaid, MS thesis, Ege University, 2023 (Zaid, 2023). With permission).
According to the water permeability tests, the highest permeability value was found using a virgin membrane with a permeability value of 4.04 Lm-2h-1bar-1 from linearized flux vs. pressure plot as shown in Figure 2. The R2 value found from the linearized graph was 0.992 which is very close to 1, meaning that our assumption for the linear relation between flux and pressure was correct. To remove the removable foulants from the surface of the membrane, membrane flushing via the produced permeate was employed before commencing permeability test. Membrane permeability found in our study corresponds to the findings by Ang et al. (2017) where BW30 RO membrane permeability was found as 5 Lm-2h-1bar-1 for applied pressure range of 2–10 bar with 2 bar incrementally. The decline, membrane permeability over several cycles can also be due to structural changes in the polymer, such as pore collapse or the formation of extra cross-links over as observed in the literature by Verbeke et al. (2018).
3.2 Permeability tests obtained before and after chemical cleaning
Permeability data obtained before and after chemical cleaning are presented in Table 3. It was also found that as the number of cycles increased towards 8, membrane permeability decreased. This is because the membrane became increasingly fouled as it was continuously used for the treatment of geothermal water. Wang et al. (2008) reported that foulants that cannot be removed after physical cleaning (flushing in this case) require chemical cleaning (organic or acid cleaning). It is considered that acid cleaning is the prominent subject when water contains inorganic foulants. Strong acids and high acid concentrations, according to some studies, may cause membrane damage since the structure of RO membranes is pH sensitive (D’Souza and Mawson, 2005). Other researchers utilized a variety of acid solutions (hydrochloric, nitric, phosphoric, sulfamic, and citric acids) to clean the RO membrane chemically, with citric acid yielding the best flux recovery (D’Souza and Mawson, 2005; Madaeni and Samieirad, 2010; Mohammadi et al., 2002). Citric acid is employed in the cleaning procedure with an initial concentration of 1000 mg/L in this investigation, based on information from the literature.
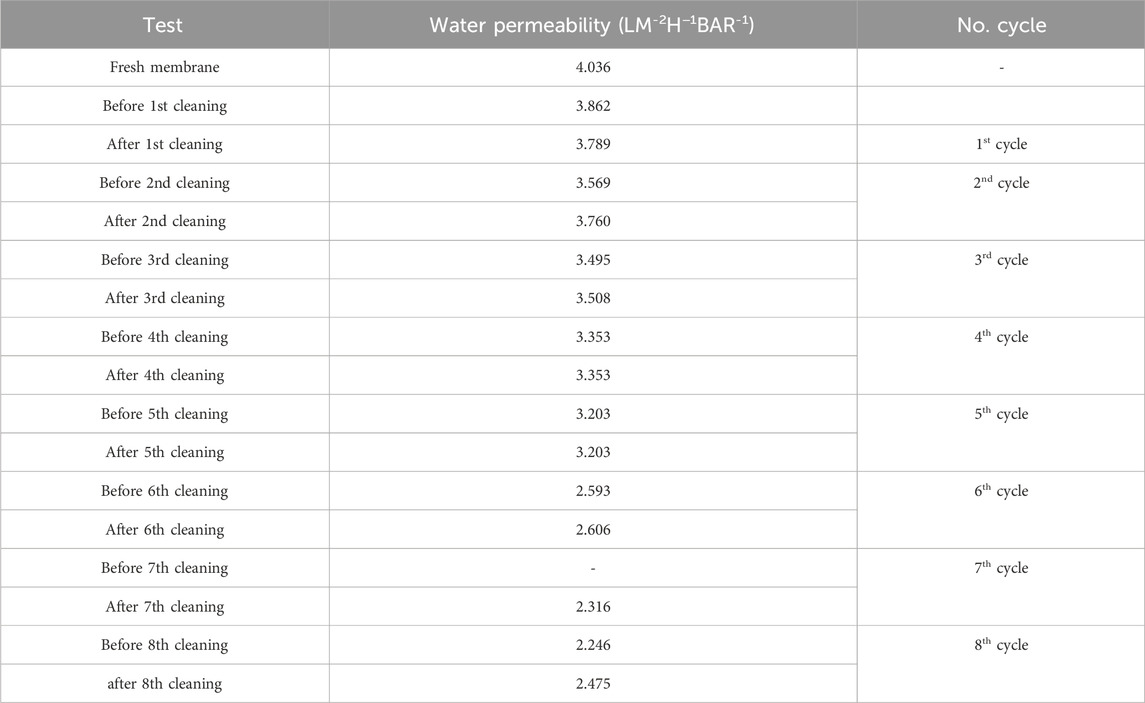
Table 3. Water permeability data before and after citric acid cleaning Adapted from Y.A. Jarma, PhD Thesis, Ege University, 2022 (Jarma, 2022) and from A. Zaid, MS Thesis, Ege University, 2023 (Zaid, 2023).
3.3 Water permeability tests for after chemical cleaning
Since organic foulants are not expected in this study due to the nature of the geothermal water used during desalination, acid cleaning using 1000 mg/L of citric acid was employed to remove inorganic foulants from the membranes. Membranes were cleaned with citric acid for 45 min followed by rinsing with the RO permeate before commencing the permeability experiments. All acid concentrations during chemical cleaning were kept constant at 1000 mg/L except for acid cleaning after the seventh cleaning where acid concentration was doubled to 2000 mg/L. This study used the chemical cleaning (acid cleaning) method provided by literature (Parlar et al., 2019). A study on membrane cleaning (D’Souza and Mawson, 2005) was used to determine the first cleaning durations. It was expected that cleaning efficiency can be increased by cleaning time (contact), or chemical concentration as demonstrated in this study. An initial cleaning approach was devised based on the issues discussed above, and only a few tweaks were made subsequently to improve cleaning performance. Since flux recovery of the membrane was found to be low despite acid cleaning, acid concentration was doubled to 2000 mg/L for the seventh cycle with the expectation of flux recovery to increase. In the eighth cycle, the citric acid concentration was raised four times to test the effect of the acid concentration on the cleaning efficiency.
Figure 3 shows permeate flux vs. pressure plots of the BW30 membrane after applying citric acid cleaning. Permeability from average values as well as from linearized flux vs. pressure values are shown in Table 3. However, no further improvement was observed at the seventh chemical cleaning even after doubling the citric acid concentration. Antiscalant was used to prevent the scaling of inorganic foulants such as Ca2+ and Mg2+. However, silica concentration in the feed water was high as shown in Table 2.
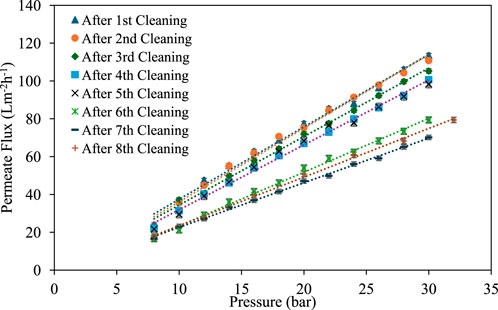
Figure 3. Water permeability test results for BW30 after citric acid cleaning by using RO permeate [Adapted from Y.A. Jarma, PhD Thesis, Ege University, 2022 (Jarma, 2022) and from A. Zaid, MS Thesis, Ege University, 2023 Thesis, Ege University, 2023 (Zaid, 2023)].
3.4 Permeate fluxes vs. time plots during treatment of geothermal water
The possible reason why the used membrane permeability continued to decline despite acid cleaning is considered a result of silica scaling. For that reason, flux decline was observed after every cycle as can be seen in Figure 4 as well as in Table 4. The linear regression assumptions of the flow equation (as linear) for the spent geothermal water permeate are true, as evidenced by high R2 values (>98%). All lines had negative intercepts except one, which was expected because osmotic pressure reduced permeate flux. The flow after the first cleaning was substantially lower than after the second and third cleanings and so on and so forth, which was attributed to the insufficient chemical cleaning of silica. Therefore, the used antiscalant was considered not to be effective towards silica. Silica in natural waters can be found in dissolved, colloidal, or particulate form. Even though the pretreatment unit was integrated with the RO system, removing silica with microfiltration (MF) or sand filter is quite challenging due to its small size. It was mentioned elsewhere by (Wilhelm and Kind, 2015) that the precipitation process of silica in water depends on its pH and concentration. Silica at a concentration higher than 100 mg/L (at a pH of 7.0) starts to polymerize and form a gel-like layer on the active area of the membranes. Therefore, one must be careful with silica concentration as well as the feed water pH when dealing with wastewater containing silica at higher concentrations. There is nothing that can be done with silica concentration hence, the pH of the feed water will surely play a vital role when treating water containing high silica concentration. Bush et al. suggested that maintaining the pH of the feed water at pH <5 or >10 can be employed to avoid or minimize membrane fouling from silica (Bush et al., 2018). Figure 4 shows the average flux obtained during each cycle. We can see that average permeate flux has continued to decline as the number of cycles increased towards the seventh cycle. The findings in the current study followed a similar trend found in the literature where membrane permeability decline is observed in intermittent RO desalting processes. Freire-Gormaly and Bilton (Freire-Gormaly and Bilton, 2019) studied the impact of intermittent operation and fouling using brackish groundwater in a lab-scale desalination. It was reported in their study that there was a membrane permeability decline of up to 87% even after employing both antiscalant and permeate flush at the end of each cycle (after 7 days of operation).
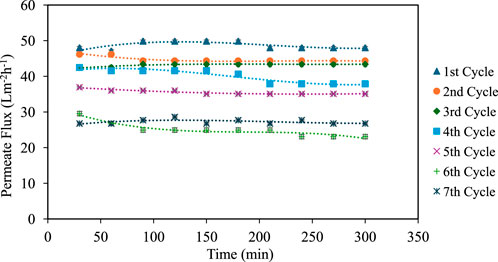
Figure 4. Permeate fluxes vs. time plots during treatment of geothermal water [Adapted from Y.A. Jarma, PhD Thesis, Ege University, 2022 (Jarma, 2022) and from A. Zaid, MS Thesis, Ege University, 2023 (Zaid, 2023), With permission].
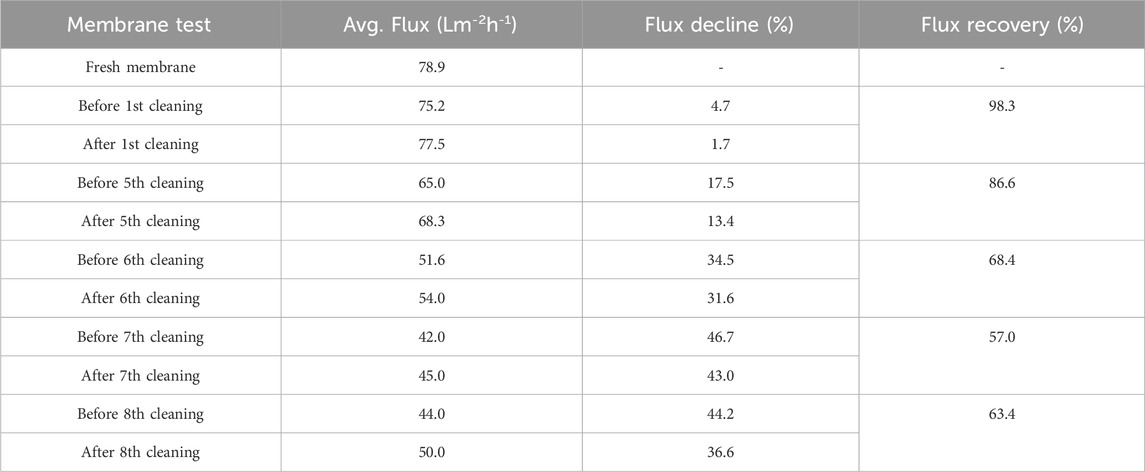
Table 4. Average flux, flux decline, and flux recovery (between permeate flux before and after cleaning) (L m-2 h-1) were obtained by BW30 during the permeability test (15 bar).
Figure 5 summarizes the impact of chemical cleaning on membrane fouling. Like was mentioned earlier, flux recovery was not very high despite cleaning the membrane with citric acid. The percentage of flux drop and flux recovery after applying chemical cleaning are summarized in Table 4.
4 Conclusion
It was evident that the level of membrane scaling increased as the number of treatment cycles increased. After eight cycles with even the doubled concentration of citric acid as 4000 mg/L, the permeate flux drop was 36.6%. It was considered that the use of antiscalant was not very effective for preventing membrane scaling during geothermal water treatment with a mini-pilot scale system. An optimization study is needed for using a more suitable antiscalant and its dosage. In addition, either a more suitable pretreatment method for the removal of scalants from geothermal water prior to RO membrane treatment and/or a new chemical cleaning protocol might be considered for increasing flux recovery.
The recommendations that can help increase the efficiency of spent geothermal water treatment are the use of antiscalants during the treatment process. The use of a more robust pretreatment train such as periodic clean water flush, coagulation to enhance nanoparticles removal, MF, and UF to reduce feed water turbidity beyond membrane manufacturer’s recommendations (<1 NTU for RO feed) before RO train. Early mineral scaling detection while employing chemical cleaning before severe mineral scaling is observed.
Data availability statement
The raw data supporting the conclusions of this article will be made available by the authors, without undue reservation.
Author contributions
AZ: Investigation, Writing–original draft. YJ: Conceptualization, Investigation, Supervision, Writing–original draft. IRAS: Investigation, Writing–review and editing. AK: Investigation, Writing–review and editing. AC: Supervision, Writing–review and editing. AB: Funding acquisition, Project administration, Resources, Writing–review and editing. NK: Conceptualization, Methodology, Supervision, Writing–review and editing.
Funding
The author(s) declare that financial support was received for the research, authorship, and/or publication of this article. This study was supported by an international research project supported by TÜBITAK- NCBR (Project No: 118Y490-POLTUR3/Geo4Food/4/2019).
Acknowledgments
The authors would like to acknowledge TÜBITAK for financial support and the Izmir Geothermal Co. for running membrane tests at the geothermal heating center.
Conflict of interest
The authors declare that the research was conducted in the absence of any commercial or financial relationships that could be construed as a potential conflict of interest.
Author NK declared that she was an editorial board member of Frontiers, at the time of submission. This had no impact on the peer review process and the final decision.
Publisher’s note
All claims expressed in this article are solely those of the authors and do not necessarily represent those of their affiliated organizations, or those of the publisher, the editors and the reviewers. Any product that may be evaluated in this article, or claim that may be made by its manufacturer, is not guaranteed or endorsed by the publisher.
References
Andritsos, N., and Karabelas, A. J. (2024). Sulfide scale formation and control: the case of lead sulfide. Geothermics 20, 343–353. doi:10.1016/0375-6505(91)90025-q
Ang, W. L., Nordin, D., Mohammad, A. W., Benamor, A., and Hilal, N. (2017). Effect of membrane performance including fouling on cost optimization in brackish water desalination process. Chem. Eng. Res. Des. 117, 401–413. doi:10.1016/j.cherd.2016.10.041
Ang, W. S., Lee, S., and Elimelech, M. (2006). Chemical and physical aspects of cleaning of organic-fouled reverse osmosis membranes. J. Membr. Sci. 272, 198–210. doi:10.1016/j.memsci.2005.07.035
Ang, W. S., Yip, N. Y., Tiraferri, A., and Elimelech, M. (2011). Chemical cleaning of RO membranes fouled by wastewater effluent: achieving higher efficiency with dual-step cleaning. J. Membr. Sci. 382, 100–106. doi:10.1016/j.memsci.2011.07.047
Baten, R., and Stummeyer, K. (2012). How sustainable can desalination be? Desal. Water Treat., 1–9. doi:10.1080/19443994.2012.705061
Bush, P. J. A., Vanneste, J., Gustafsona, E. M., Waechter, C. A., Jassby, D., Turchi, C. S., et al. (2018). Prevention and management of silica scaling in membrane distillation using pH adjustment. J.Membr. Sci. 554, 366–377. doi:10.1016/j.memsci.2018.02.059
Chen, J., Kim, S., and Ting, Y. (2003). Optimization of membrane physical and chemical cleaning by a statistically designed approach. J. Membr. Sci. 219, 27–45. doi:10.1016/s0376-7388(03)00174-1
D’Souza, N. M., and Mawson, A. J. (2005). Membrane cleaning in the dairy industry: a review. Crit. Rev. Food Sci. Nutr. 45 (2), 125–134. doi:10.1080/10408690490911783
Freire-Gormaly, M., and Bilton, A. M. (2019). Impact of intermittent operation on reverse osmosis membrane fouling for brackish groundwater desalination systems. J. Membr. Sci. 583, 220–230. doi:10.1016/j.memsci.2019.04.010
Fritsch, J. A. C. I., and Moraru, C. I. (2008). Development and optimization of a carbon dioxide-aided cold microfiltration process for the physical removal of microorganisms and somatic cells from skim milk. J. Dairy Sci. 91, 3744–3760. doi:10.3168/jds.2007-0899
Gilron, J., and Hasson, D. (1987). Calcium sulphate fouling of reverse osmosis membranes: flux decline mechanism. Chem. Eng. Sci. 42, 2351–2360. doi:10.1016/0009-2509(87)80109-4
Goh, P., Lau, W., Othman, M., and Ismail, A. (2018a). Membrane fouling in desalination and its mitigation strategies. Desalination 425, 130–155. doi:10.1016/j.desal.2017.10.018
Goh, P. S., Lau, W. J., Othman, M. H. D., and Ismail, A. F. (2018b). Membrane fouling in desalination and its mitigation strategies. Desalination 425, 130–155. doi:10.1016/j.desal.2017.10.018
Jarma, Y. A. (2022). Application of membrane processes for utilization of geothermal water in agricultural irrigation. Izmir: Ege University. PhD Thesis.
Jarma, Y. A., Karaoglu, A., Tekin, Ö., Baba, A., Okten, H. E., Tomaszewska, B., et al. (2021). Assessment of different nanofiltration and reverse osmosis membranes for simultaneous removal of arsenic and boron from spent geothermal water. J. Hazard. Mater. 405, 124129. doi:10.1016/j.jhazmat.2020.124129
Jarma, Y. A., Karaoğlu, A., Tekin, Ö., Senan, I. R. A., Baba, A., and Kabay, N. (2022). Integrated pressure-driven membrane separation processes for the production of agricultural irrigation water from spent geothermal water. Desalination 523, 115428. doi:10.1016/j.desal.2021.115428
Jiang, S., Li, Y., and Ladewig, B. P. (2017). A review of reverse osmosis membrane fouling and control strategies. Sci. Total Environ. 595, 567–583. doi:10.1016/j.scitotenv.2017.03.235
Kimura, K., Hane, Y., Watanabe, Y., Amy, G., and Ohkuma, N. (2004). Irreversible membrane fouling during ultrafiltration of surface water. Water Res. 38 (14), 3431–3441. doi:10.1016/j.watres.2004.05.007
Klupfel, A. M., and Frimmel, F. H. (2010). Nanofiltration of river water — fouling, cleaning and micropollutant rejection. Desalination 250, 1005–1007. doi:10.1016/j.desal.2009.09.091
Lee, S., Kim, J., and Lee, C.-H. (1999). Analysis of CaSO4 scale formation mechanism in various nanofiltration modules. J. Membr. Sci. 163, 63–74. doi:10.1016/s0376-7388(99)00156-8
Lenntech (2024). DuPont-filmtec BW30-2540 reverse osmosis element. Available at: https://www.lenntech.com/products/DuPont-Filmtec/80766/BW30-2540-Reverse-Osmosis-Element/.
Leonard, B. (1999). 25 Years of the safe drinking water act: history and trends. Collingdale, PA: Diane Publishing Company.
Liikanen, R., Yli-Kuivila, J., and Laukkanen, R. (2002). Efficiency of various chemical cleanings for nanofiltration membrane fouled by conventionally-treated surface water. J. Membr. Sci. 195, 265–276. doi:10.1016/s0376-7388(01)00569-5
Lin, J. C. T., Lee, D. J., and Huang, C. (2010). Membrane fouling mitigation: membrane cleaning. Sep. Sci. Technol. 45, 858–872. doi:10.1080/01496391003666940
Liu, L., Zhu, G., Liu, Z., and Gao, C. (2016). Effect of MCM-48 nanoparticles on the performance of thin film nanocomposite membranes for reverse osmosis application. Desalination 394, 72–82. doi:10.1016/j.desal.2016.04.028
Madaeni, S. S., and Samieirad, S. (2010). Chemical cleaning of reverse osmosis membrane fouled by wastewater. Desalination 257 (1–3), 80–86. doi:10.1016/j.desal.2010.03.002
Mitrouli, S. T., Kostoglou, M., and Karabelas, A. J. (2026). Calcium carbonate scaling of desalination membranes: assessment of scaling parameters from dead-end filtration experiments. J. Membr. Sci. 510, 293–305. doi:10.1016/j.memsci.2016.02.061
Mohammadi, T., Madaeni, S. S., and Moghadam, M. K. (2002). Investigation of membrane fouling. Desalination 153, 155–160. doi:10.1016/s0011-9164(02)01118-9
Parlar, I., Hacıfazlıoğlu, M., Kabay, N., Pek, T. Ö., and Yüksel, M. (2019). Performance comparison of reverse osmosis (RO) with integrated nanofiltration (NF) and reverse osmosis process for desalination of MBR effluent. J. Water Proc. Eng. 29, 100640. doi:10.1016/j.jwpe.2018.06.002
Saqib, J., and Aljundi, I. H. (2016). Membrane fouling and modification using surface treatment and layer-by-layer assembly of polyelectrolytes: state-of-the-art review. J. Water Process. Eng. 11, 68–87. doi:10.1016/j.jwpe.2016.03.009
Schwarz, H. E., Emel, J., Dickens, W., Rogers, P., and Thompson, J. (1990) “Water quality and flows,” in The Earth as transformed by human action. Cambridge, UK: Cambridge University Press.
She, Q., Wang, R., Fane, A. G., and Tang, C. Y. (2016). Membrane fouling in osmotically driven membrane processes: a review. J. Membr. Sci. 499, 201–233. doi:10.1016/j.memsci.2015.10.040
Subramani, A., and Jacangelo, J. G. (2015). Emerging desalination technologies for water treatment: a critical review. Water Res. 75, 164–187. doi:10.1016/j.watres.2015.02.032
Verbeke, R., Gómez, V., Koschine, T., Eyley, S., Szymczyk, A., Dickmann, M., et al. (2018). Real-scale chlorination at pH4 of BW30 TFC membranes and their physicochemical characterization. J. Membr. Sci. 551, 123–135. doi:10.1016/j.memsci.2018.01.019
Wang, Z., Wu, Z., Yin, X., and Tian, L. (2008). Membrane fouling in a submerged membrane bioreactor (MBR) under sub-critical flux operation: membrane foulant and gel layer characterization. J. Membr. Sci. 325, 238–244. doi:10.1016/j.memsci.2008.07.035
Wilhelm, S., and Kind, M. (2015). Influence of pH, temperature and sample size on natural and enforced syneresis of precipitated silica. Polym. (Basel) 7 (12), 2504–2521. doi:10.3390/polym7121528
Zaid, A. (2023) “A study on membrane fouling after treatment of geothermal water by nanofiltration and reverse osmosis membranes,”. MS Thesis, Ege University. Izmir.
Zhao, Y., Zhang, Z., Dai, L., Mao, H., and Zhang, S. (2017). Enhanced both water flux and salt rejection of reverse osmosis membrane through combining isophthaloyl dichloride with biphenyl tetraacyl chloride as organic phase monomer for seawater desalination. J. Membr. Sci. 522, 175–182. doi:10.1016/j.memsci.2016.09.022
Keywords: geothermal water, membrane fouling, reverse osmosis (RO) membrane, scaling, chemical cleaning
Citation: Zaid A, Jarma YA, Ahmed Senan IR, Karaoğlu A, Cihanoğlu A, Baba A and Kabay N (2025) Evaluation of fouling and chemical cleaning of reverse osmosis membrane after treatment of geothermal water. Front. Membr. Sci. Technol. 3:1408595. doi: 10.3389/frmst.2024.1408595
Received: 28 March 2024; Accepted: 02 December 2024;
Published: 08 January 2025.
Edited by:
Jose Luis Cortina, Universitat Politecnica de Catalunya, SpainReviewed by:
Amani Al-Othman, American University of Sharjah, United Arab EmiratesYunhui Zhang, Southwest Jiaotong University, China
Copyright © 2025 Zaid, Jarma, Ahmed Senan, Karaoğlu, Cihanoğlu, Baba and Kabay. This is an open-access article distributed under the terms of the Creative Commons Attribution License (CC BY). The use, distribution or reproduction in other forums is permitted, provided the original author(s) and the copyright owner(s) are credited and that the original publication in this journal is cited, in accordance with accepted academic practice. No use, distribution or reproduction is permitted which does not comply with these terms.
*Correspondence: Nalan Kabay, bmFsYW4ua2FiYXlAZWdlLmVkdS50cg==
†Present address: Yakubu Abdullahi Jarma, Department of Chemical and Biomolecular Engineering, University of California Los Angeles, Los Angeles, CA, United States