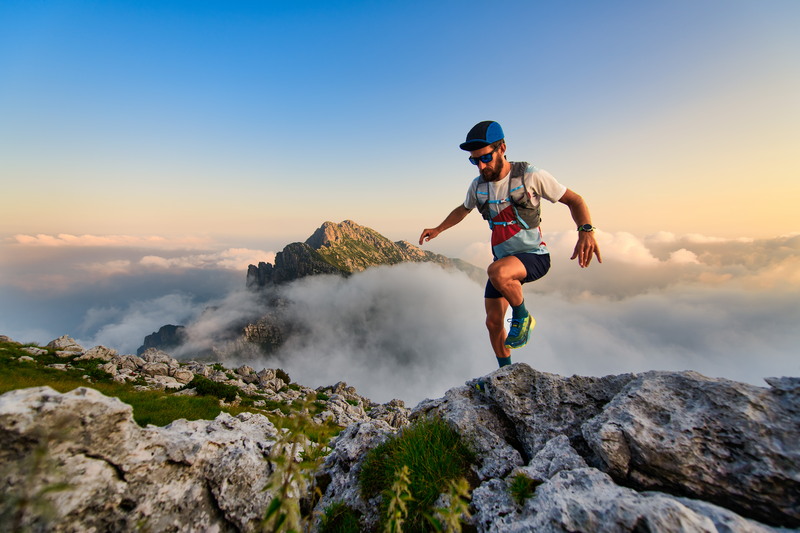
95% of researchers rate our articles as excellent or good
Learn more about the work of our research integrity team to safeguard the quality of each article we publish.
Find out more
REVIEW article
Front. Membr. Sci. Technol. , 09 May 2024
Sec. Membrane Applications - Gas and Vapor
Volume 3 - 2024 | https://doi.org/10.3389/frmst.2024.1390599
This article is part of the Research Topic Celebrating 1 Year of Frontiers in Membrane Science and Technology View all 10 articles
The fabrication of membranes for gas separation presents challenges that hinder their deployment as a truly sustainable technology. This review systematically explores the evolution and advancements in materials and manufacturing methods of polymer-based membranes, with a keen emphasis on sustainability and efficiency. The review delineates a broad spectrum of manufacturing techniques, ranging from traditional methods to cutting-edge approaches such as layer-by-layer assembly, and green synthesis, highlighting their implications for environmental sustainability, performance enhancement, scalability, and economic viability. Key findings indicate a significant shift towards greener solvents, bio-based polymers and processes that reduce waste and costs. Critical analysis uncovers a growing focus on understanding the life cycle of membranes and developing strategies for end-of-life such as recycling and the use of biodegradable materials, underscoring the commitment of the community to minimizing environmental footprints.
Over the past few decades, growing public awareness and concern for climate change and health issues have spurred significant advancements in environmental engineering technologies (Figueroa et al., 2008; Pipitone and Bolland, 2009). A notable area of progress is in membrane technology for gas separation, particularly the separation of natural gas from impurities, such as carbon dioxide (Hosseini and Chung, 2009; Scholes et al., 2012; Sholl and Lively, 2016; Žák et al., 2018; Wojnarova et al., 2023). This development is rooted in the fact that carbon dioxide not only corrodes pipelines but also diminishes the heating value of natural gas. Similarly, the flue gases emitted by industries and power plants, which are a mixture of CO2, SO2, and NOx present an environmental challenge that necessitate the capture and utilization of CO2 for compliance purposes (Du et al., 2011; Dolejš et al., 2014; Pasichnyk et al., 2023). Globally, carbon dioxide emissions from fossil fuels and industry totalled 37.15 billion metric tons (GtCO2) in 2022 and projected to have risen 1.1 percent in 2023 to reach a record high of 37.55 GtCO2. In fact, since 1990, global CO2 emissions have increased by more than 60 percent (Tiseo, 2023). Echoing these concerns, in September 2021, the New England Journal of Medicine and other global health journals jointly published an article, urging immediate action to reduce GHG emissions to protect human health (Atwoli et al., 2021). All of this reports significantly amplifies the demand for and efficient and cost-effective gas separation technologies.
Traditional separation methods, such as distillation and absorption, are effective for separating gas and vapor mixtures. However, they are characterized by high energy demands, accounting for 10%–15% of global energy consumption, significant economic costs, and the production of pollutants (Sholl and Lively, 2016). In the United States, separations account for a significant energy expenditure, consuming about 4500 trillion Btu annually. This represents roughly 22% of all energy used within industrial plants (USDOE, 2005). A substantial portion of this energy is used in distillation processes. With over 40,000 distillation columns operating across the U.S. for more than 200 distinct separations, distillation represents nearly half (49%) of the energy used in industrial separations (USDOE, 2005). These backdrops set the stage for the advent of membrane technology. Membranes stand out due to their high efficiency, cost-effectiveness, environmental sustainability, minimal footprint, and capability for continuous operation, making them a promising alternative to conventional methods. Compared to conventional distillation methods, membrane-based processes have the potential to reduce energy consumption by approximately 90% (Baker, 2002; Sholl and Lively, 2016).
The evolution of membrane technology has been remarkable since the first commercial membrane for gas separation was introduced, for the separation of H2 from N2, argon and CH4 in 1980 (Henis and Tripodi, 1980). In fact, the market response to the gas separation membrane techniques has been overwhelmingly positive, with significant growth observed over the past few decades. A recent market analyst report published by Market Research Future®, reveals that the gas separation membrane industry is projected to grow from USD 2.45 billion in 2023 to USD 4.68 billion by 2030, exhibiting a compound annual growth rate of 10.2% during the forecast period (2023–2030) (Chitranshi Jaiswal, 2024). The growth of the gas separation membrane market is primarily driven by two key factors: firstly, the increasing number of governmental regulations and laws regarding GHG emissions, with specific restrictions on carbon dioxide emissions across various industrial sectors; and secondly, the expansion of industrial processes such as natural gas treatment, hydrogen purification, and hydrocarbon separation, all of which require gas separation membranes (Chitranshi Jaiswal, 2024).
Although market projections for gas separation membranes are impressive, selecting the right materials for gas membrane fabrication is crucial to fully maximizing the economics and efficiency of the technology. Conventionally, membranes are classified based on the material used for its fabrication, the structure, and intended application of the membrane as well as on the mechanism of membrane action (Asad et al., 2020). Depending on the nature of material used, gas separation membranes are classified as organic (polymeric), inorganic/metallic and composite/hybrid membranes. Inorganic/metallic membranes made of metals, ceramic, zeolites, carbon nanotubes, carbon molecular sieves, and mesoporous are very suitable where harsh thermal and chemical conditions are expected, and some of them indicates a high gas flux and selectivity, but they are difficult to process and usually expensive and difficult to fabricate and use at industrial scale because of its brittleness (Chung et al., 2007; Mantzalis et al., 2011; Kosinov et al., 2016; Garcia-Fayos et al., 2020). Hence, polymeric membranes are widely preferred and utilized in gas separation, due to their advantageous mechanical strength, consistent performance, ease of shaping into various modules, and cost-efficiency in processing (Xu et al., 2006; Wang et al., 2007). The versatility and tailorability of polymeric materials further enhance their appeal, allowing for customization to meet diverse industrial needs, including acid gas treatment, nitrogen enrichment, ammonia purge gas recovery, refinery gas purification, syngas ratio adjustment, dehydration, air purification and carbon capture (Sanders et al., 2013; Castel et al., 2021). In addition, the ease of installation and scalability of polymeric membranes significantly benefits their integration into various systems and their adaptation from laboratory research to industrial-scale applications.
Nevertheless, recently, there has been growing concern, particularly regarding the manufacturing techniques and material sustainability of currently used commercial polymeric gas separation membranes, many of which are derived from non-renewable sources. Although widely used synthetic polymers such as polyamides, polysulfones, polyethersulfone, polyacrylonitrile, polyvinylidene fluoride, polypropylene, polysiloxanes or silicone rubber, and polyethylene oxide have demonstrated desirable properties like permeability, selectivity, mechanical strength, and chemical stability (Purkait et al., 2018), the ecological impact of their fabrication and non-recyclability poses significant challenges. This is particularly concerning if membranes dominate the gas separation market, as membrane modules in industrial applications are typically replaced every three to 5 years. This leads to considerable plastic waste, with these non-biodegradable materials often ending up in landfills or natural ecosystems. Likewise, some of the common solvents used in these polymeric membrane fabrication includes N,N-dimethylformamide (DMF), N,N-dimethylacetamide (DMAc), N-methyl-2-pyrrolidone (NMP), dichloromethane (DCM), chloroform, and tetrahydrofuran (THF), many of which are organic and pose environmental and health hazards. The percentage of solvent in the polymer solution can vary widely, depending on the desired thickness and porosity of the membrane, as well as the specific polymer-solvent interaction. Typically, the polymer concentration in the dope solution, which includes the solvent, ranges from 1% to 20% by weight (Figoli et al., 2014).
Consequently, research interest in polymer-based gas membranes is steering towards improving the membrane properties and to go Net-zero by applying advanced and sustainable manufacturing techniques (Jiang and Ladewig, 2020; Bridge et al., 2022). The imperative to shift towards the development of advanced and sustainable polymeric gas separation membranes is underscored by a confluence of factors, including separation efficiency, durability, environmental impact, and economic considerations. This review focuses on reviewing advanced and sustainable manufacturing techniques currently employed for polymeric gas separation membranes. It will highlight study-based evidence of the latest technological advancements, sustainable practices, and potential improvements in gas membrane separation efficiency.
The manufacturing of commercial polymer membranes for gas separation is a crucial process in the field of industrial separation and purification, playing a key role across various sectors, including the petrochemical, environmental, and energy industries. This process typically involves the use of a range of synthetic polymers, semi-synthetic polymers, organic solvents, and established techniques. Over the years, these methods have formed the backbone of membrane manufacturing, driving numerous industrial applications by creating membranes specifically designed for separating different gas mixtures.
Since the discovery of membrane technology, several polymers have been used for the development of gas separation membranes, including polyacetylenes, polyaniline, poly (arylene ether)s, polyarylates, polycarbonates, polyetherimides, poly (ethylene oxide), polyimides, poly (phenylene oxide)s, poly (pyrrolone)s, polysulfones and others (Amooghin et al., 2016). Cellulose acetate (Hu et al., 2022), polysulfone (Mohamed et al., 2023), and polyimide (Ma and Yang, 2018; Ohya et al., 2022) stand out in industrial gas separation for their excellent selectivity and permeability. Specifically, cellulose acetate’s critical role is exemplified by its use in Pakistan’s largest gas separation plant, which utilizes CA membranes for CO2 extraction from natural gas, highlighting its stability and scalability (Hu et al., 2022). Polysulfone gained prominence with the establishment of the first plant using Polysulfone’s hollow fiber membranes for H2/N2 separation in 1980 by Permea, demonstrating Polysulfone’s notable mechanical strength, resistance to compaction, and thermal stability (Mohamad et al., 2016). Similarly, the inaugural deployment of polyimide membranes by Du Pont Co. (United States) and Ube Industries (Japan) marked a significant advancement in H2 separation (Ma and Yang, 2018; Ohya et al., 2022), with polyimides acclaimed for their chemical resistance, thermal endurance, and mechanical durability (Xiao et al., 2009; Bryant, 2014). Their wide use in the membrane industry is also attributed to their ease of processing and ability to be tailored to specific separation needs through modifications and treatments. Most of these polymers are synthetic or semi-synthetic, and their applicability poses several challenges, including the effects of thermal and pressure conditioning, physical and chemical aging, plasticization, and permeation hysteresis. Likewise, the effectiveness of polymeric gas separation membrane is often gauged against the Robeson upper bound, a benchmark that delineates the trade-off between permeability and selectivity (Robeson, 2008). Therefore, to overcome the limitations of both polymeric membranes, mixed matrix membranes (MMMs) have been identified to provide a solution to go beyond the upper-bound trade-off limit of the polymeric membranes, by incorporating innovative material into the polymer matrix (Khorshidi et al., 2019; Xu et al., 2021b; Hu et al., 2022).
Furthermore, factors such as the choice of casting solvent and the impact of impurities or trace contaminants add further complexities in conventional polymeric membrane fabrication and have garnered considerable research interest (Amooghin et al., 2016; Tekin and Çulfaz-Emecen, 2023). The solvents used in fabricating polymeric gas separation membranes play a pivotal role in determining the characteristics and performance of the final product. Often, these solvents are selected based on the type of polymer being used and the desired properties of the membrane. However, the challenge lies in the influence of solvent properties, such as viscosity, dielectric constant, polarity, and boiling point, on the membrane final features and the essential requirement of dissolving the selected polymer (at room or high temperature, depending on the technique) (Anbukarasu et al., 2021). Thus, one of the most challenging yet intriguing tasks for membrane scientists is replacing these conventional solvents. Table 1 shows a list of solvents and polymers traditionally used in membrane preparation and their respective Hansen solubility parameters. Solubility parameters are fundamental in predicting solvent-polymer compatibility, which directly influences membrane structure, performance, and sustainable manufacturability. Most membrane fabrication techniques require dissolving the polymer in a solvent to enable shaping the material in 2-dimensional films. Hansen solubility parameters (HSPs) serve as an indicator of whether a solvent will dissolve a specific polymer. This can be accomplished by calculating the distance (Ra) of the polymer-solvent system (Eq 1); and its ratio with respect to the interaction radius (R0), known as the relative energy distance (RED) (Eq 2). When RED
Table 1. Conventional membrane fabrication solvents and polymers and their Hansen solubility parameters.
The manufacturing technique used to fabricate polymeric or composite membranes plays a fundamental role and depends on the nature of the material and the desired morphology of the membrane. Over the years, various techniques have been used to synthesize polymeric membranes for gas separation. These include solution casting, phase inversion (Loeb and Sourirajan, 1963), interfacial polymerization (Jimenez-Solomon et al., 2016; Zhang et al., 2022), roll to roll coating (Chen et al., 2020), kiss coating (Dibrov et al., 2014), and track etching (Nailwal et al., 2023). Table 2 shows a concise summary of the various techniques. Among them, solution casting, phase inversion, interfacial polymerization, dip coating, roll to roll coating and kiss coating are the most notable, hence is concisely discussed.
The solution casting technique is a fundamental and widely utilized method in the fabrication of polymeric membranes for gas separation. This process begins with dissolving a polymer in a suitable solvent to form a homogeneous solution. Once the polymer solution is prepared, it is spread uniformly on a flat surface or a casting substrate and allowed to evaporate under controlled conditions, leading to the formation of a thin polymeric film (Zou and Zhu, 2020; Alkandari and Castro-Dominguez, 2023). The rate of solvent evaporation is a key factor in this process, as it influences the structure and morphology of the membrane. Slow evaporation under controlled environmental conditions can lead to more uniform membrane structures, whereas rapid evaporation might result in membranes with defects or non-uniformity (Yamasaki et al., 1999). One of the primary advantages of the solution casting technique is its simplicity and the ability to produce membranes with uniform thickness and smooth surfaces. Moreover, it allows for the incorporation of various additives into the polymer solution, providing a way to tailor the properties of the membrane, such as, permeability, and selectivity (Clarizia et al., 2019). However, the choice of solvent is critical in solution casting, as it must not only dissolve the polymer effectively but also be safe and environmentally benign. The disposal of used solvents and the environmental impact of the process are considerations that have led to ongoing research into greener and more sustainable solvent options.
The phase inversion method, initially developed by Loeb and Sourirajan (Loeb and Sourirajan, 1963) for preparing cellulose acetate desalination membranes, later became prevalent in the fabrication of polymeric membranes for gas separation because of its simplicity, economic feasibility, and the ability to create thin membranes (Scholes et al., 2012; Martínez-Izquierdo et al., 2021). The technique involves dissolving a water-insoluble polymer in a high-boiling point solvent to form a viscous polymer dope. This solution is then degassed and spread onto a support using a casting knife (Martínez-Izquierdo et al., 2021), followed by immersion in a coagulation bath of water or solvent, resulting in an asymmetric membrane with a dense top layer and a porous bottom layer. The formation of these distinct layers is influenced by factors like the solution composition, coagulation temperature, and additives (Alam et al., 2012). Three main types of phase inversion techniques exist: thermal induced phase inversion (TIPS), non-solvent induced phase inversion (NIPS), and vapor-induced phase inversion (VIPS). Despite the simplicity and widespread use of phase inversion and solvent evaporation techniques, the multitude of challenges associated with them underscores a vital need for meticulous consideration and innovative approaches that will guide future research and development. A primary challenge in this context is the difficulty in producing defect-free membranes (Higashi et al., 2021; Cui et al., 2023).
Dip coating involves immersing a substrate into a coating solution and then lifting it out at a consistent speed, allowing a thin film to form on the surface. Recognized as one of the most fundamental film deposition techniques (Madaeni et al., 2013), it is particularly beneficial for fabricating membranes used in gas separation, as it facilitates the creation of uniform, precise thin layers crucial for optimal membrane performance (Madaeni et al., 2013). The method is effectively utilized in developing membranes for various gas separations like CO2/N2 (Li et al., 2021), CO2/CH4 (Suleman et al., 2018), H2 (Farjoo and Kuznicki, 2016) and, O2/N2 (Sazali et al., 2020). The optimum concentration of the casting solution and the temperature were identified as key factors in achieving a uniform membrane (Li et al., 2020). Research has demonstrated that parameters such as the concentration of the coating solution (Jamil et al., 2020), withdrawal speed, and the number of coatings applied (Shankar and Kandasamy, 2019) are vital in tuning the membrane’s gas separation characteristics, highlighting the importance of process control in achieving the desired membrane functionality. Furthermore, the dip-coating technique has proven to be highly effective in fabricating composite membranes without defects for gas separation, underscoring the method’s adaptability and efficiency (Tan et al., 2019). However, this technique also has several limitations that can constrain its applicability and complicate its scalability. Initially, this technique may not be ideal for applications requiring coating on only one side of a substrate, as the solution tends to envelop the entire immersed surface. Additionally, it is requiring a significant amount of precursor solution to occupy the coating container, introducing considerable challenges (Ceratti et al., 2015). For instance, managing large quantities of the solution can be hazardous, potentially impacting the environment adversely, and such constraints hold up scalability.
Interfacial Polymerization (IP) is another technique widely used in the fabrication of polymeric membranes, particularly effective for thin-film composite (TFC) and nanofiltration (NF) membranes (Jimenez-Solomon et al., 2016; Zhang et al., 2022). This technique involves a reaction between two monomers, each dissolved in different, immiscible solvents, typically water and solvents. The IP procedure typically consists of two steps: firstly, soaking the porous support in a solution with the first monomers until saturated, then removing excess solution; secondly, immersing the support in another solution with the second monomers for a reaction, followed by removing all solutions and further processing to form a dense polymer skin layer (Sridhar et al., 2007). Key advantages of the IP technique include its ability to produce extremely thin, highly selective, and scalable layers, which are particularly important in gas separation membranes efficiency, as demonstrated by several authors in the context of CO2/CH4, H2/CO and CO2/N2 gas pair separations (Li et al., 2012; Wang et al., 2013; Choi et al., 2015). Moreso, the properties of the resulting membrane, such as permeability and selectivity, can be finely tuned by adjusting factors like the type and concentration of monomers, reaction time, and temperature (Sridhar et al., 2007). However, challenges in this method include controlling the uniformity of the film and managing the interfacial reactions to prevent defects.
Roll-to-roll coating techniques represent a pivotal advancement in the fabrication of membranes, offering a scalable and efficient method for producing thin-film composite membranes. This continuous process involves the deposition of selective layers on a flexible substrate, which is then wound through various coating and drying stages. The technique adaptability allows for the application of multiple layers, each contributing to the membrane’s overall separation performance and mechanical stability. R2R coating encompasses two distinct methods: direct roll coating and reverse roll coating. With direct roll coating, the applicator roll, and the substrate move in the same direction. Conversely, in reverse roll coating, the applicator roll turns against the direction of the substrate’s movement (Makhlouf, 2011; Chen et al., 2020). Vakharia et al., 2018 employed a pilot-scale R2R coating method to manufacture thin polymer membranes on porous supports, aimed at CO2 separation from flue gases. This study highlights the critical role of various parameters, including coating speed, solution viscosity, and the rate at which the coating solution is applied, in determining the final membrane properties. The R2R technique is noted for its efficiency and cost-effectiveness, which are essential for scaling up to industrial levels. However, the method presents challenges, notably in maintaining consistent process conditions to achieve uniform, defect-free membrane coatings. Ensuring the substrate remains perfectly flat during the coating is particularly challenging (Vakharia et al., 2018), as any deviations can introduce defects. Also, R2R direct coating of the membrane presents a challenge because a large amount of coated solution is applied to the substrate at once. Therefore, the interaction time between the dispersion media and the membrane is lengthier than it is for spray coating, which may result in increased absorption and swelling of the membrane (Park et al., 2020). Future research is anticipated to enhance process controls, broaden the range of compatible materials, and incorporate advanced functional materials for R2R coated membranes in gas separation. These improvements aim to boost the efficacy and broaden the use of R2R-coated membranes in gas separation.
The kiss-coating technique is a modified version of the dip-coating procedure. The kiss-coating technique offers an approach for fabricating thin-film composite (TFC) polymeric membranes for gas separation and the approach provides a one-sided contact between the surface of the porous support and the casting solution (Dibrov et al., 2014). Typically, the method involves the delicate application of a polymer solution onto a substrate, where the coating applicator barely “kisses” the surface, hence the name. This approach allows for precise control over the thickness and uniformity of the membrane layer, which are critical factors in determining the membrane’s gas separation performance. Studies have shown that coating methods significantly impact gas separation efficiency. For instance, Bazhenov et al. created composite gas separation membranes with high permeance, aimed at capturing post-combustion CO2, utilizing kiss-coating techniques. These membranes demonstrated favorable CO2 permeance and CO2/N2 selectivity. The high-permeance thin-film composite (TFC) membranes were considered as promising bases for subsequent enhancements through the addition of layers that further improve CO2 selectivity (Bazhenov et al., 2016). Another study Dibrov et al. has development of robust and stable in time poly [1-(trimethylsilyl)-1-propyne] (PTMSP) thin-film composite (TFC) membranes with high CO2 permeance for its application in high pressure/temperature gas–liquid membrane contactors used for amine-based solvents regeneration (Dibrov et al., 2014). Also, Kiss coating enables the precise deposition of a uniform and defect-free selective layer on porous supports, leading to enhanced aging behavior and improved permeance-selectivity balance in thin-film composite membranes for gas separation applications (Foster et al., 2021). Despite these advantages, optimizing the Kiss Coating process for gas separation membrane fabrication requires careful consideration of several parameters, including the viscosity of the polymer solution, the speed of the substrate movement, and the distance between the applicator and the substrate (Bazhenov et al., 2016; Foster et al., 2021). In addition, the technique may be limited by the viscosity and drying rate of the coating solution, which can restrict the type of materials that can be effectively applied. Fine-tuning these parameters ensures the formation of a membrane layer with the desired thickness and material properties, crucial for achieving high separation efficiency.
Over the past decade, the number of publications associated with advanced and sustainable manufacturing techniques has increased considerably as seen in Figure 1. By leveraging novel materials, intricate nanostructures, and sophisticated manufacturing processes, these techniques have opened new possibilities for enhancing membrane performance, durability, and specificity, thereby addressing some of the most pressing challenges in sustainable technology and resource management.
Figure 1. Annual publications on advanced and sustainable membrane fabricate techniques according to Web of Science 2024.
In addition to conventional polymeric materials predominantly used in most commercial membrane manufacturing, several novel materials are gaining prominence in the field of polymeric membrane fabrication. These materials are particularly noted for their enhanced performance in specific applications such as gas separation and carbon capture. They exhibit key characteristics that render them suitable for a range of advanced applications, providing tailored solutions for specific separation challenges across various industries (Jeon et al., 2017; Ulbricht, 2019; Widakdo et al., 2022). These characteristics include: 1) high selectivity and permeability, 2) chemical and thermal stability, 3) mechanical strength, 4) tailored pore structures, and 5) tunable functionalities. These innovative materials are broadly used to either fabricate standalone or composite polymeric membranes, as illustrated in Figure 2. Although many of these advanced materials provide enhanced separation performance; they are not further discussed in this review as their sustainability and scalability traits are yet to be demonstrated.
There has been a significant shift in research towards environmentally friendly and solvent-free manufacturing practices. 3D printing, a technique used to fabricate items by layering of materials in a 3D printer, stands out as a key technology in this shift, particularly in the fabrication of membranes (Lee et al., 2016; Low et al., 2017). 3D printing, developed in 1986 by Hull (1986), has been the subject of intensive research over the past 2 decades. While its use in creating membranes for water treatment has been extensively studied, there is also a growing trend in applying this technology to gas separation membranes (Li et al., 2019; Gutierrez et al., 2021; Gutierrez et al., 2022). The appeal for 3D printing lies in its straightforwardness, eco-friendly nature, efficient design process, and the ability to create intricate shapes (Miramontes et al., 2020; Gutierrez et al., 2021). Additionally, 3D printing is cost-effective, reducing the need for solvents and other manufacturing materials (Gutierrez et al., 2021). It also offers the advantage of customizing surface areas to improve interaction with gases (Miramontes et al., 2020; Gutierrez et al., 2021) and the pore size can be adjusted to optimize gas separation efficiency (Low et al., 2017). Various techniques exist for 3D printing membranes, with material extrusion and photopolymerization being particularly effective methods for creating gas separation membranes (Ligon et al., 2017; Herzberger et al., 2019). Material extrusion is one of the most common forms of 3D printing. It involves extruding a material, typically a thermoplastic filament, through a heated nozzle. The material is deposited layer by layer to build the desired shape (Thiam et al., 2022). The ability to use a variety of materials, including polymers and composites, makes it a versatile choice. For example, Thakkar et al., fabricated zeolite-embedded poly (amide-imide) monoliths using the material extrusion technique, and the resulting 3D-printed membranes displayed CO2 capture capacities proportional to the zeolite loading, while exhibiting high compressive strengths and overall satisfactory mechanical stability (Thakkar et al., 2018).
One of the significant processes in 3D printing is direct ink writing (DIW). It typically involves extruding a paste-like ink, which can be a viscous solution, suspension, or composite material, and allows for the creation of more complex extruded materials (Gutierrez et al., 2023). Gutierrez et al., 2022, studied the fabrication of polydimethylsiloxane (PDMS)-based membranes for CO2/N2 gas separation using DIW 3D printing. To enable printability, silica particles were incorporated into the PDMS ink to introduce thixotropy. This ink was 3D printed into membranes, which displayed smooth surfaces and good silica dispersion as shown in Figure 3. Gas permeation testing showed the printed membranes had a CO2 permeability over 1000 Barrer. A CO2/N2 selectivity around 10 was achieved and the membranes display high thermal and mechanical stability, with a good surface properties. Nguyen et al. developed polymer composite inks, which were 3D printed to create innovative reactor designs aimed at capturing CO2. These inks consisted of sodium carbonate particles embedded in uncured silicone and were applied through DIW. Once printed, the silicone underwent curing, and the structures were then hydrated, resulting in the formation of aqueous sodium carbonate domains that facilitated efficient CO2 absorption (Nguyen et al., 2019).
Figure 3. DIW-printed PDMS membrane and Mechanism of gas separation through the PDMS membrane (Gutierrez et al., 2022).
Unlike the material extrusion technique, photopolymerization involves the transformation of monomers or oligomers from their liquid state into a solid polymer through radical or cationic polymerization. This process is triggered by exposing these materials to light, which can vary in wavelength, in the presence of a photo-initiator (Bagheri and Jin, 2019). This method uses light, typically in the form of ultraviolet (UV) rays, to cure and solidify a photosensitive resin (Low et al., 2017). It is a process known as Stereolithography or Digital Light Processing (DLP) (Figure 4). This technique involves using a laser to trace and instantaneously cure a liquid resin printed cross-section, while the rest of the resin stays liquid (Ligon et al., 2017; Herzberger et al., 2019). The process is carried out layer by layer, repeating the tracing and curing steps until both the 3D printing and curing processes are complete (Low et al., 2017). Gillono et al. developed azobenzene chromophore membranes using DLP. The 3D printed membrane exhibited light-triggered changes in CO2 permeability, with up to a 70% increase under 532 nm laser irradiation due to azobenzene photoisomerization. The permeability increase was tunable based on laser intensity. This outcome highlights the technique’s ability to finely adjust the permeation characteristics of membranes through controlled light exposure (Gillono et al., 2020). This technique, known for its high resolution and accuracy, is the preferred method for creating polymeric membranes, particularly effective in liquid and gas separation membrane fabrication. However, a profound challenge is the typically low mechanical integrity of the printed products (Ligon et al., 2017). Therefore, there is an ongoing exploration of other materials compatible with 3D printing photopolymerization to achieve the necessary characteristics and performance for such applications.
Figure 4. Approaches for 3D printing of membranes: (A) Fuse deposition (FDM); (B) Direct ink writing; and (C) Photopolymerization.
Despite these advancements, a critical evaluation reveals that 3D printing, while innovative, faces significant challenges when compared to methods traditionally employed in membrane production. Firstly, 3D printing is not a cost-effective method for conventional membrane fabrication as the scale and speed of production falls short when compared with conventional methods such as casting. Even so, 3D printing is a good alternative for generating membrane for niche applications (Low et al., 2017). Another issue of this technology is its current inability to consistently produce membranes with the sub-micron thickness required for optimal gas separation without encountering defects. This shortfall makes it challenging for 3D-printed membranes to match the performance and efficiency of their conventional counterparts, which rely on such thin films for enhanced selectivity and permeability. Specifically, FDM technique face limitations in producing membranes at the micro-to nanoscale thickness due to comparatively weak interlayer adhesion. This weakness can lead to structural flaws or voids that compromise the membrane’s integrity, allowing gases to permeate undesirably and detract from the separation process’s efficiency (Gutierrez et al., 2022).
Electrohydrodynamic emission, also known as Electrospinning/Electrospraying (shown in Figure 5), is a relatively novel technique that has garnered considerable interest for creating nanofibrous membranes with high porosity from various polymers and for its diverse applications, including tissue engineering, energy storage, and notably, gas separations (Wu et al., 2014; Tan and Rodrigue, 2019; Asad et al., 2020; Hosseini and Valipouri, 2023). These electrospun nanofibrous membranes (ENMs) exhibit several beneficial characteristics, including a network of interconnected pores, extensive porosity, and pore sizes that range from a few micrometers to several tens of nanometers, alongside a substantial surface-area-to-volume ratio (Hosseini and Valipouri, 2023). Particularly in membrane contactors, the EHD technique proves beneficial due to its promotion of high hydrophobicity, tortuosity, and surface porosity (Li et al., 2011; Li and Wang, 2013). The process of forming these fibrous structures is driven by the uniaxial expansion of a viscoelastic polymer solution (Sun et al., 2022). Although the electrospun membranes are majorly used in liquid separation due to challenges in creating dense membranes, recently, the modification of nanofibers has been applied widely to give them improved properties, as such, it is witnessing a growing use in gas application, particularly in carbon capture, air purification including the removal of NOx, CO, CO2, H2S, VOCs, and SO2 pollutants from air due to its advantageous characteristics (Olivieri et al., 2018; Zhang et al., 2018; Azzam et al., 2019; Huang et al., 2020; Sun et al., 2022). For instance, Huang et al. fabricated an electrospun polystyrene (PS)/polyethylenimine (PEI) fiber membrane to capture CO2 from ambient air before the air is admitted into a Zinc-air batteries (ZABs) to enhance battery performance (Huang et al., 2020). Likewise, Alkandari et al. employed electrohydrodynamic emission and solution casting as a hybrid membrane manufacturing method, to produce ZIF-67/cellulose acetate asymmetric membranes with improved gas permeability and selectivity for CO2/N2, CO2/CH4, and O2/N2 (Alkandari et al., 2023). Also, Elsaidi et al. employed the EHD method to produce thin film MMMs for CO2/N2 separation, resulting in improved CO2 permeance (Elsaidi et al., 2021). Similarly, Katepalli et al., 2011 developed multi-scale ACF-PANS nanofiber structures through electrospinning, which demonstrated high efficiency in the removal of in atmospheric pollutants such as toluene, CO2, SO4, and NO. In addition, Electrospun nanofibers have emerged as a cutting-edge solution for fabricating supports for thin-film composite (TFC) membranes. The support layer of TFC membranes has been underappreciated and the main focused with TFC membranes was directed to the gutter layer and selective layer (Kattula et al., 2015; Yoo et al., 2018). This oversight is partly due to treating TFC supports as mere mechanical support, and not considering their potential impact on the selectivity and permeability of gases. Recent studies have highlighted that modifications to the morphology of the support layer can significantly improve the overall performance of the membranes. For instance, Fan et al., 2023 proposed a facile and versatile support layer modification strategy and they achieved high-performance TFCs with high selectivity and permeance, where the support layer is the porous electrospun nanofiber substrate. Electrospun support layers for TFC membranes, with their porous structure of nanofibers, stand out for their potential in gas separation technologies. They embody a promising direction for the future of TFC membranes by enabling high selectivity and permeance. This is achieved through a facile and adaptable strategy for modifying the support layer, making use of the porous electrospun nanofiber substrate to enhance performance (Fan et al., 2023). The disadvantages of EHD include low throughput, high energy intensive as it operates at high voltages (5 to >20 kV). These factors raise concerns regarding its environmental impact and overall sustainability.
Figure 5. Illustration of the electrospraying process (Alkandari et al., 2023).
Functionalization and surface engineering are critical strategies in membrane fabrication to tailor the properties of membranes for specific applications, such as improving selectivity, permeability, and chemical stability (Ma et al., 2022). These modifications can significantly enhance the performance of membranes in various separation processes, including water treatment, and gas separation. Outlined below are several pivotal methods and strategies deployed in the realm of functionalization and surface engineering tailored for the development of membranes.
The layer-by-layer (LbL) assembly method is an attractive technique for the fabrication of ultra-thin, defect-free films with tailored composition and tuneable properties. At its core, this method utilizes electrostatic interactions between materials of opposing charges. It involves the alternate, sequential layering of positively and negatively charged polyelectrolytes on a charged surface. Each layering step is interspersed with a rinsing phase to eliminate loosely bound polymer chains (Zhao et al., 2019), as demonstrated in Figure 6. To achieve enhanced membrane selectivity, particularly on microporous substrates, a substantial number of anion/cation polyelectrolyte depositions may be required (Ismail et al., 2015). One of the outstanding benefits of the LbL method is the precise control it offers over film thickness at the nanometer scale (Heo et al., 2020). This precision is meticulously adjustable through the number of sequential adsorption steps. The LbL technique is highly versatile, finding applications across various domains of membrane science. It plays a pivotal role in developing membranes for water purification (Dong et al., 2022) and gas separation (Heo et al., 2020). Beyond membrane technology, this technique is involved in biosensors (Correia et al., 2021), drug delivery (Alkekhia et al., 2020), and other nanotechnology applications.
Figure 6. Schematic representation of the LbL film deposition process. Steps 1 and 3 illustrate the adsorption of a polyanion and a polycation, respectively. Steps 2 and 4 are washing step.
The LbL assembly method is renowned for its simplicity and adaptability in producing extremely thin polyelectrolyte multilayers, making it highly effective in membrane separation applications. Unlike conventional membrane fabrication methods, LbL facilitates thorough control over the thickness and structure of membranes, down to the nanometer scale. This is exemplified in studies like those conducted by Heo et al., 2017, where LbL was utilized to construct nanoscale graphene oxide (GO) membranes with controlled structure and thickness by spray assisted LbL assembly to separate CO2. This design enabled the membrane to block N2 and enhance CO2 permeance by controlling the number of GO layers. The study achieved an extraordinary balance of selectivity and permeability. The integration of the LbL technique with other manufacturing methods significantly bolsters its utility in improving membrane separation efficiency. A compelling example of this synergy is found in the work of Li et al., where they combined LbL assembly with a PDMS spraying method to address defects in P84 gas separation membranes initially created through phase inversion. The fabricated membrane significantly improved gas separation performance, with H2/CH4 selectivity increasing by 270% compared to the original P84 membrane (Li et al., 2022). Moreover, Xu et al. drew inspiration from the LbL concept to fabricate 2D membranes with a meticulously ordered superlattice structure. This was achieved through an alternating Layer-by-Layer (LbL) assembly of MgAl-LDH nanosheets and formamidine sulfinic acid (FAS), followed by coating with a thin layer of PDMS as seen in Figure 7. The alternating stacking of LDH and FAS leads to highly ordered sub-nanometre channels just 0.34 nm high between layers, allowing for effective molecular sieving. The combination of LDH’s affinity for CO2 and FAS reversible CO2 binding enhanced CO2 permeation selectively. This approach not only allows for precise control of the membrane separation capabilities but also offers a scalable, cost-effective solution for high-performance CO2 separation (Xu et al., 2021). The thickness of individual layers in LbL assemblies can vary significantly, ranging from a few angstroms to hundreds of nanometers. This thickness is a tunable aspect, adjustable by modifying various characteristics of the deposition mixture. Key factors influencing layer thickness include the pH (Mendelsohn et al., 2000; Heo et al., 2017), deposition time (Tousley et al., 2016), the ionic strength and counter-ions (Scheepers et al., 2021; Scheepers et al., 2023), and the temperature of the mixture. Additionally, the molecular weight of the deposition species (Wong et al., 2009) the relative humidity in the fabrication environment are critical parameters that can significantly impact the individual layer thicknesses (Daio et al., 2015).
Figure 7. Schematic representation for the fabrication of (LDH/FAS)n-PDMS membranes (Xu et al., 2021).
Cross-linking techniques have become a pivotal approach in the fabrication of polymeric membranes for gas separation, offering enhanced stability and performance (Wright and Paul, 1997; Kelman, 2008). These techniques involve the formation of chemical bonds between polymer chains, creating a network structure that significantly improves the membrane mechanical strength and chemical resistance (Liu et al., 2023). Some profound benefits of cross-linked polymeric membranes in gas separation are their enhanced selectivity and permeability, as illustrated in (Figure 8). Cross-linking can reduce the free volume within the polymer matrix, thereby allowing for more selective gas transport. This is particularly beneficial for applications requiring high purity levels, such as in the separation of carbon dioxide from methane in natural gas processing (Hong et al., 2015; Liu et al., 2023). Additionally, cross-linked membranes exhibit improved resistance to swelling, CO2 induced plasticization and chemical degradation, particularly in harsh environments (Wind et al., 2002; Begni et al., 2021). This increased stability extends the membranes operational lifespan and reduces the need for frequent replacements, thus offering economic advantages (Hunger et al., 2012). Various methods can be employed to crosslink polymer membranes for gas separation, such as ionic crosslinking (Schmeling et al., 2010), thermal crosslinking (Alghunaimi, 2013), and photocrosslinking (Decker and Bianchi, 2003; Decker et al., 2004). However, the choice of approach depends on the polymer functional groups and the expected separation attributes of the membrane (Wind et al., 2002; Bolto et al., 2009; Esteban et al., 2022).
Figure 8. Upper bound plot for selected cross-linked membranes of CO2/CH4, Polymers are labelled as follows: (1) PPM-Ƴ-CD-425 (Askari et al., 2012), (2) BMPI-60%-450 (Xu et al., 2021a), (3) 75%-X-PI (An et al., 2018), (4) 6FDA-DAT/DATCA-450 (Tian et al., 2018), (5) 6FDA-DAT1-450-3h (Yerzhankyzy et al., 2022), (6) PI-Im-COOH-450-1 (Shi et al., 2022), (7) FDA-DAPI-DABA-40min (Dose et al., 2019), (8) PIM-BM-70(250C-10h) (Chen et al., 2020), (9) PIM-BM-70(300C-5h)(Chen et al., 2020), (10) 50%-X-PI (An et al., 2018), (11) PIM-300-2d (Li et al., 2012). Adapted from (Liu et al., 2023).
Hunger et al., 2012 demonstrated that copolyimide membranes which are crosslinked exhibit increased resistance to plasticization and maintain their selectivity, showing no notable decline compared to non-crosslinked membranes when subjected to CO2/CH4 or toluene/cyclohexane mixtures. Furthermore, it was found that membranes crosslinked covalently tend to have enhanced separation efficiency compared to those crosslinked ionically. Schmeling et al. investigated the advantages of using 6FDA (4,4′-hexafluoroisopropylidene diphthalic anhydride)-copolyimides with carboxy groups. Their research assessed a range of membrane materials, including non-cross-linked, ionically crosslinked, and covalently crosslinked variants, focusing on their effectiveness in separating CO2/CH4 gas and other liquid mixtures. The study also provided insights into the efficiency and suitability of these membranes for such applications (Schmeling et al., 2010). Zhang et al., 2023 developed a range of cross-linkable Polyimides (PIs) with varying degrees of polymer chain orientation, aimed at improving CO2/CH4 separation efficiency. Unlike traditional PIs, they achieved a 2.3-fold increase in CO2 permeability by precisely controlling the polymer chain orientation, without negatively impacting the membrane resistance to plasticization.
However, the process of cross-linking must be carefully controlled. Over-cross-linking can lead to membranes that are too rigid, reducing their gas permeability (Hong et al., 2015). The choice of cross-linking agents and the conditions under which cross-linking is carried out (such as temperature and time) are critical factors that determine the final properties of the membrane (Wind et al., 2002; Tashvigh et al., 2019).
Recent advancements in cross-linking techniques include the use of UV radiation, thermal treatments, and the incorporation of nanoparticles to initiate or enhance the cross-linking process. These methods offer more precise control over the extent and nature of cross-linking, leading to membranes with tailored properties for specific gas separation tasks (Wright and Paul, 1997; Ismail and Aziz, 2012).
Polymeric membranes, commonly utilized in membrane separation processes, encounter two primary challenges: 1) a trade-off between permeability and selectivity, and limited thermal stability. Notably, these issues are rooted in the materials properties rather than the fabrication methods of the membranes. To address these limitations, a novel class of membranes emerged in the 1970s, incorporating nanomaterials into cellulose acetate (CA) membranes to enhance their resistance to compaction. This innovative approach soon gained considerable attention as a means to adjust and improve membrane performance (Takahashi and Paul, 2006; Khorshidi et al., 2016b; Khorshidi et al., 2016a). For instance, prevalent polymers in membrane technology, such as polyethersulfone (PES), polyvinylidene fluoride (PVDF), polypropylene (PP), and polytetrafluoroethylene (PTFE), typically exhibit hydrophobic characteristics. The integration of hydrophilic nanomaterials into these membranes can transform their nature from hydrophobic to hydrophilic (Yang et al., 2016; Khorshidi et al., 2019). Nanocomposite membranes can be categorized into four distinct types, depending on the placement of the nanomaterials and the membrane structure: 1) conventional nanocomposite, 2) surface-located nanocomposite, 3) thin-film nanocomposite (TFN), and 4) thin-film composite (TFC) with a nanocomposite substrate. Figure 9 provides a schematic representation of these four varieties of nanocomposite membranes. Each category offers specific advantages over the others, highlighting the diversity and adaptability of nanocomposite membranes in enhancing membrane technology (Takahashi and Paul, 2006; Rafiq et al., 2012). Sadeghi et al. investigated the impact of silica nanoparticles on the permeability of CO2, CH4, and N2 gases in polybenzimidazole (PBI) membranes. Their result showed that increasing the silica content in the polymer matrix led to higher solubility but lower diffusivity of gases in the membranes. Consequently, the permeability of CO2 and CH4 was increased, while that of N2 significantly declined as silica content increased (Sadeghi et al., 2009). Song et al. developed a defect-free composite membrane by integrating ZIF-8 nanoparticles into Matrimid 5218 by solution mixing. They found that the addition of ZIF-8 enhanced the membrane’s structure, creating more space within the polymer. This change, coupled with the natural ability of gases to move through ZIF-8 unique structure, significantly improved the membrane’s permeability to gases such as CO2, CH4, O2, N2, and H2 (Song et al., 2012). Rafiq et al. explored the development of mixed matrix membranes (MMMs) by integrating inorganic silica nanoparticles into polysulfone/polyimide (PSF/PI) asymmetric membranes for gas separation, utilizing the phase inversion technique. They observed that the addition of 5.2 wt% silica into a PSF/PI-20% blend significantly enhanced CO2 permeance, and the improvement was proportional to the increase in silica content (Rafiq et al., 2012).
Figure 9. Illustration of typical types of nanocomposite membranes (Asad et al., 2020).
Gas separation membranes still face manufacturing challenges that need to be addressed to exploit their tremendous potential. As presented by Beuscher et al., 2022 “research in membrane separation has focused on developing better membrane materials, yet very few of these materials are being used in commercial applications”. In fact, since 1976 only 10% of all papers containing “polymer,” “material,” “module,” or “process” as keywords have focused on modules and process research. Moreover, currently, prominent players in gas separation membrane manufacturing, including Air Liquide, Air Products, AirRane, Evonik, MTR, and Honeywell UOP, cater to various separation needs such as oxygen/nitrogen generation and carbon dioxide/hydrogen purification. The prevalent commercial membrane materials encompass polyimide, cellulose, and polysulfone, fashioned into hollow fiber or occasionally spiral-wound modules, albeit specific costs remain undisclosed by suppliers, complicating the cost analysis landscape.
The scalability of membrane manufacturing hinges on achieving simplicity, robustness, and replicability to accommodate the diverse spectrum of module sizes dictated by different applications, as shown in Table 3. Furthermore, sustainability imperatives mandate that fabrication processes minimize waste, employ renewable feedstocks, and utilize green solvents. Sustainable manufacturing, therefore, not only prioritizes scalability and waste reduction but also emphasizes energy efficiency and favorable economic attributes.
A comprehensive literature search, querying “polymer membrane technology for gas separation” and “manufacturing costs” via Web of Science, yielded 176 entries, comprising both articles and patents. Cost estimations for polymer membranes, ranging from $10 to $50 per square meter, have been reported for diverse applications including CO2 capture, oxygen-nitrogen separation, and propylene/propane separation (Zarca et al., 2018; Adhikari et al., 2021; Lee et al., 2022). Remarkably, this cost range has remained unchanged since 1992 (Van Der Sluus et al., 1992). The authors advocate for technoeconomic analysis encompassing capital and operating costs (e.g., electricity, raw materials, land, labor) to update contemporary membrane cost profiles and validate economic viability during scale-up processes. Furthermore, in conjunction with technoeconomic assessments, a holistic understanding of the environmental life cycle of membranes is indispensable for developing truly sustainable membrane processes. Such insights will inform decisions throughout the design, fabrication, and deployment stages, ensuring that environmental considerations are integrated into the fabric of gas separation membrane technology.
Traditional polymeric membranes, made from synthetic polymers such as polyamide, polysulfone, polyethersulfone, polyvinylidene fluoride, and others, have been predominant in the industry due to their strong mechanical properties, chemical resistance, and flexibility (Cui et al., 2010; Purkait et al., 2018). However, the environmental impact of their production, including the need for greener processes and effective waste management, presents a significant challenge. In light of these environmental concerns, biodegradable polymeric membranes are gaining attention as a more sustainable alternative, offering a reduced ecological footprint (Galiano et al., 2018; Lasseuguette and Ferrari, 2020). Biodegradable polymer is a type of polymer that can break down into water, carbon dioxide, biomass, and other natural substances under the action of naturally occurring microorganisms such as bacteria, fungi, and algae, within a specific period of time and under environmental conditions (Jami’an et al., 2015; Bandehali et al., 2021). These polymers can be derived from renewable bio-based resources or from synthetic sources that are engineered to degrade (e.g., polycaprolactone (PCL), polybutylene adipate terephthalate (PBAT)).
Likewise, the development of these bio-based membranes involves considerations like choosing appropriate green solvents and optimizing waste management during production. Additionally, factors like reusability, cost-effectiveness, and post-use disposal strategies are crucial for their success in industrial applications (Figoli et al., 2016). Overall, the goal is to achieve membranes with high permeability, selectivity, mechanical and thermal resistance, but at a lower manufacturing cost, addressing the environmental and efficiency challenges in membrane technology.
Eco-friendly polymers, those derived from biological sources, or recycled substances such as cellulose, chitosan (CS), polylactic acid (PLA), polyhydroxyalkanoates (PHA), and others, are attracting significant interest from researchers in the field of polymeric membrane fabrication. This interest is driven by the desire to align industrial practices with environmental conservation and resource management (Zhu et al., 2020; Iulianelli et al., 2022; Torre-Celeizabal et al., 2023). Table 4 presents a summary of the most common bio-based polymers used in membrane production outlining their advantages and disadvantages.
Cellulose biopolymers are plant-based polysaccharide, made up of long macromolecular chains of 1-4-β-glycosidic linked D-glucose units. Among the derivatives of cellulose, the application and performance of cellulose acetate (CA) and cellulose triacetate (CTA) in gas membrane fabrication have been investigated extensively due to its unique properties including easy processability, versatility and eco-friendliness (Wu and Yuan, 2002; Lam et al., 2016; Nikolaeva et al., 2018; Gopi et al., 2019; Raza et al., 2021; Regmi et al., 2021; Alkandari et al., 2023). However, CA is susceptible to plasticization when exposed to CO2. The adsorption of CO2 into the polymer matrix at elevated pressures can lead to an increased free volume and enhanced mobility of the polymer chains, resulting in the plasticization of the material (Donohue et al., 1989; Houde et al., 1996).
Chitosan (CS), a naturally abundant biopolymer produced from the deacetylation of chitin and recognized for its biocompatibility, biodegradability, hydrophilic, and non-toxicity, has been used to fabricate several membranes (de Alvarenga, 2011). CS membranes have proven to be effective in various gas separation applications (Xiao et al., 2007; Torre-Celeizabal et al., 2023). The molecular formation of chitosan is rich in amino and hydroxyl groups, a feature that greatly boosts its capacity to capture CO2, a polar molecule. This absorption capability is particularly enhanced when the membrane is swollen with water or when specialized fillers are incorporated into mixed matrix membranes (MMM). (Ito et al., 2003; Xiao et al., 2007; Li et al., 2022; Torre-Celeizabal et al., 2023). In addition, incorporating small amounts of three-dimensional and two-dimensional particle fillers can enhance both the CO2 capturing ability and the mechanical strength of chitosan (Torre-Celeizabal et al., 2023).
PLA, which are synthesised by a direct polycondensation of hydroxyl acid or ring-opening polymerization of lactide are regarded as exceptional biopolymer for membrane fabrication. Notable for its excellent processability, solubility in a variety of organic solvents, water resistance, and a melting point and glass transition temperature (Tg) ranging from 170°C to 80°C and 50°C–65°C, respectively. The Tg of PLA varies with crystallinity and biopolymer structure, while the crystallinity itself is a function of the proportion of D-lactide acid, which typically ranges from highly crystalline to amorphous (Castro-Aguirre et al., 2018; Galiano et al., 2018). Iulianelli et al. fabricated dense symmetric PLA Easy FilTM-white membranes and tested the gas permeability and ideal selectivity of H2, CH4, CO2, and He at room temperature with transmembrane pressures ranging from 100 to 1200 KPa. They discovered that CO2 permeability reached approximately 70 Barrer, surpassing Robeson’s upper bound for CO2/CH4 separation and achieved a selectivity of 285 (Iulianelli et al., 2019). Additionally, they reported a selectivity of 26.5 for H2/CO2 at room temperature and 1 bar (Iulianelli et al., 2017), making these membranes notably suitable for biogas separation applications. However, several authors have reported that PLA faces a significant limitation due to its susceptibility to hydrolytic degradation when exposed to water, bacteria, or UV radiation. This degradation of its ester bonds occurs under specific conditions such as temperature, humidity, and pH, which can influence its stability and, correspondingly, its practical applications (Moon et al., 2016; Li et al., 2017).
PHA, derived from microbial fermentation of various renewable sources, and their derivatives, poly (3-hydroxybutyrate) (PHB) and polyhydroxyvalerate (PHV), are characterized by desirable properties such as hydrophobicity, optical purity, high processability, and biocompatibility. These features make them suitable for a range of applications, including gas membrane fabrication, as well as packaging and the biomedical industry (Follain et al., 2014; Siracusa et al., 2017; Papchenko et al., 2022). Follain et al., 2014 investigated the application of PHB membranes for pervaporation and gas separation by evaluating the diffusion and gas permeation. They employed two different approaches for homopolymer PHB and copolymer PHBV preparation: 1) a classic film casting using chloroform as a solvent and 2) a compressing preparation technique at elevated temperature. A remarkable selectivity range of 1.5–6.7 for CO2/O2 and 4.8 to 19 for CO2/N2 in PHB and PHBV (3 mol% 3-HV units) were obtained. Siracusa, et al. observed selectivity values ranging from 1.7 to 2.5 for CO2/O2 and 2.2 to 3.4 for CO2/N2 in PHB films (Siracusa et al., 2017). Huh et al., 2017 investigated H2 permeability and selectivity in PHBV (12 mol% 3-HV units) and composite membranes incorporating multiwall carbon nanotubes.
In addition to the characteristics listed in Table 4, it is critical to acknowledge the inherent challenge associated with the permeability and selectivity of bio-based polymers. Due to their semi-crystalline nature (Lam et al., 2016), these polymers generally exhibit low permeability coupled with moderate selectivity, which hinders their applicability as membrane for gas separation. This is clearly shown in Figure 10, where most bio-based polymers are below the 1991 upper bound line. However, it is possible to improve these properties through various synthetic modifications. These include chemically altering the polymer structure, mixing the polymer with plasticizers to make them less brittle or blending them with other polymers (Papchenko et al., 2022), and incorporating additives such as ionic liquids (Lam et al., 2016; Nikolaeva et al., 2018; Alkandari and Castro-Dominguez, 2023). Such enhancements are crucial because one of the main challenges with low-permeability materials is the need to make very thin membranes to maximize gas flux, and thus efficiency (Shen and Lua, 2010). Similarity, methods such as surface modification and the use of nanocomposite membranes have been shown to further improve membrane performance (Mafirad et al., 2018; Dai et al., 2019; Zargar et al., 2019).
Figure 10. Upper bound plot for selected bio-based membranes of CO2/N2, Polymers are labelled as follows: (1) PHB (Follain et al., 2014), (2) PHB3V (Follain et al., 2014), (3) PHBV-DMC (Papchenko et al., 2022), (4) PHBV-CHCL3(Papchenko et al., 2022), (5) PLA(Lehermeier et al., 2001), (6) CTA+[EMIM][BF4] (Lam et al., 2016), (7) PVTCS/73 (Kunalan et al., 2022), (8) CA-ZIF67 (B*) (Alkandari et al., 2023), (9) CA-IL40-e (Alkandari and Castro-Dominguez, 2023), (10) CA (Alkandari and Castro-Dominguez, 2023), (11) PHB (Siracusa et al., 2017).
The evolution of membrane fabrication has increasingly focused on the integration of green solvents and additives, reflecting a growing commitment to environmental sustainability and safer manufacturing practices (Ajari et al., 2019; Sing Soh et al., 2023). Green solvents, characterized by their low toxicity, biodegradability, and minimal environmental impact, are pivotal in this paradigm shift (Capello et al., 2007; Figoli et al., 2014; Marino et al., 2018). These solvents, including substances like γ-valerolactone (GVL), acetyl tributyl citrate (ATBC), and cyrene, offer safer alternatives to traditional, often hazardous solvents used in membrane production, such as N-Methyl-2-pyrrolidone (NMP) (Gu and Jérôme, 2013; Sherwood et al., 2014).
Rasool and Vankelecom, 2019 experimented with GVL and glycerol derivatives to create porous membranes using the NIPS method with common polymers like PI, PES, polysulfone (PSU), cellulose acetate (CA), and cellulose triacetate (CTA), aiming to explore bio-based green solvents in membrane fabrication. Similarly, Sherwood et al., 2014 demonstrated that Cyrene could be efficiently produced from biomass in two simple steps, minimizing environmental impacts. Figoli et al., 2017 applied Cyrene in fabricating PES and PVDF membranes using both VIPS and NIPS techniques, highlighting Cyrene versatility as a solvent for common membrane polymers. And also Bridge et al., 2022 applied the same solvent (Cyrene) in PSF to prepare defect-free asymmetric gas separation membrane via dry/wet NIPS. In addition to solvents, the incorporation of eco-friendly additives has been instrumental in enhancing the performance and sustainability of membranes. These additives can improve membrane properties like mechanical strength, without adding significant environmental burdens (Clarke et al., 2018). Examples include the use of natural polymers, bio-based nanomaterials, and other non-toxic compounds that complement the green solvents (Randová et al., 2016; Fu et al., 2019; Nasar et al., 2019). The synergy of green solvents and additives in membrane fabrication not only aligns with environmental regulations but also sets a new standard for the industry in terms of sustainability and safety. By reducing the reliance on harmful chemicals, this approach significantly diminishes the ecological footprint of membrane production processes. Moreover, it opens up new possibilities for innovative membrane applications in various sectors, including water treatment, gas separation, and biomedical applications, while ensuring compliance with stringent environmental and health standards (Clark and Tavener, 2007; Figoli et al., 2014). The ongoing research and development in this area are poised to yield membranes with improved performance characteristics, such as enhanced permeability, selectivity, and durability, in an environmentally responsible manner. Thus, the use of green solvents and additives represents a crucial step towards more sustainable and eco-friendly membrane technology.
Reusing and recycling of polymer membrane materials are becoming increasingly important in addressing environmental concerns associated with membrane technology. As the demand for membrane-based separation processes grows, so does the need for sustainable practices that minimize waste and reduce the ecological footprint of these technologies (El-Khair and Ali, 2013; Ignatyev et al., 2014; Al-Shaeli et al., 2022). Recycling of polymeric membranes involves the recovery and reprocessing of membrane materials at the end of their useful life. This can be achieved through mechanical recycling, where membranes are ground and remoulded into new products, or chemical recycling, where the polymer is broken down into its monomers or other valuable chemicals as shown in Figure 11. Recycling helps to conserve resources and reduce landfill waste (Achilias and Karayannidis, 2004; Karayannidis and Achilias, 2007; Jiun et al., 2016; Wang et al., 2017). On the other hand, Reusability focuses on designing membranes that can be cleaned and reused multiple times without significant loss of performance. This approach extends the lifespan of membranes, decreasing the frequency of replacement and the associated environmental impact. Strategies for enhancing reusability include developing fouling-resistant membranes or designing membranes that can be easily regenerated through simple cleaning procedures (Patel et al., 2022). Research efforts have primarily focused on recycling end-of-life (EoL) polymeric membranes, especially those used in water treatment processes. For example, Wang et al., who employed N-methyl-2-pyrrolidone (NMP) and DMF to dissolve EoL hollow fiber and flat sheet PVDF membranes used in microfiltration/ultrafiltration (MF/UF). These dissolved membranes were then reformed via phase inversion, resulting in recycled PVDF membranes for potential use as substrates in nanofiltration/reverse osmosis (NF/RO) applications (Wang et al., 2017). However, a notable deficiency remains in the area of recycling strategies for gas separation membranes at the end of their service life, underscoring a critical area for future research and development.
The use of gas separation membranes in commercial settings has been established for decades, with the industry significantly expanding from the 1980s through the early 2000s. Although existing membranes are not appropriate for every gas separation application, they have proven to be highly effective when used appropriately (including suitable feedstock, scale, and purity requirements) and outperforms other separation techniques (IDTechEx, 2023). Currently, the gas separation membrane industry is experiencing a phase growth, driven by key market drivers, particularly the push towards renewable energy and decarbonization initiatives, along with technological innovations aimed at meeting these emerging demands. However, there are prevailing challenges to overcome, which is discussed in the sub-section.
The innovation in membrane materials and sustainable manufacturing techniques presents a significant opportunity for promoting a sustainable and eco-friendly future. The evolving field of polymeric membrane production is marked by a promising convergence of creativity, environmental sustainability, and improved operational efficiency. With the increasing global need for separation technologies, particularly for gas separation, the advancement of eco-friendly polymeric membranes is becoming more crucial. The process of creating polymeric membranes faces the complex task of balancing material characteristics with membrane efficiency, environmental sustainability, and affordability. It is essential to choose the right biodegradable polymer, one that provides an ideal mix of selectivity, permeability, and resistance to chemicals, tailored for specific uses. However, many biodegradable materials lack mechanical stability and degrade under harsh operational conditions. Consequently, polymers derived from fossil fuels are prevalently utilized. To address this, there is a strategy to develop hybrid polymers by blending biodegradable substances with a small quantity of novel materials (such as MOFs, COFs, CNPs, etc.) to bolster mechanical strength while minimally affecting biodegradability. This approach aims to improve the membranes mechanical robustness and stability. Additionally, the application of cross-linking techniques can reinforce the structural stability of biodegradable polymers. Chemical cross-linking can boost the mechanical strength and chemical resistance of membranes, rendering them more adaptable to rigorous uses.
Moreover, The integration of smart materials capable of responding to environmental stimuli (pH, temperature, electric field, etc.) (Ulbricht, 2019; Widakdo et al., 2022), and the incorporation of artificial intelligence and machine learning in polymeric gas membrane material discovery, selection, design and property testing, including degradability, tensile strength and resistance to tearing could revolutionize advanced membrane manufacturing, enabling the optimization of membrane performance and rapid prototyping (Yang et al., 2022). There is potential to compile both experimental and simulated data on membranes made with innovative materials into a vast database for functionality- and performance-based screening. This approach aims to expedite the thoughtful design and selection of membrane materials through machine learning, addressing the challenges posed by the limited nature and difficult-to-control degradability of biodegradable materials, alongside exploring advanced material options.
In the realm of membrane technology research, the initial discovery of new materials with promising selectivity and permeability marks only the beginning of a journey toward practical application. The true challenges, and the source of most difficulties, lie in ensuring membrane stability under operational conditions, scaling up the production of defect-free membranes, and integrating these membranes into functional modules. Despite the variety of materials investigated, industrial-scale applications predominantly utilize a limited array of polymers, such as cellulose acetate, polysulfone, and polyimide highlighting the gap between material discovery and application readiness. Moreover, discovering scalable methods to fabricate thin, impeccable membrane layers that fully utilize a material’s capabilities often presents a greater challenge than merely identifying new materials with enhanced flux and selectivity. This discrepancy highlights a significant research gap: while the quest for superior membrane materials has intensified, the translation of these advancements into commercially viable solutions remains limited. A more concerted effort is necessary to advance beyond material discovery towards the development of reproducible, economically feasible membrane systems. This includes rigorous assessments of cost and scalability to meet industrial demands. Furthermore, it is notable that the cost range for membranes has not shifted significantly since 1992, remaining between $10 to $50 per square meter (Van Der Sluus et al., 1992). Nonetheless, designing membranes must also take economic constraints into account. Achieving this necessitates comprehensive technoeconomic assessments to ascertain the upper limits for polymer/composite costs, alongside the capital and operational expenses tied to the production methods.
Moreover, environmental sustainability of membrane technologies is critical, necessitating a deep understanding of their environmental life cycle. Scalability issues often hinder the adoption of advanced techniques, which, despite their potential, are challenged by the simplicity and cost-effectiveness of conventional methods. Scaling up these advanced techniques involves overcoming numerous obstacles, including high costs of sophisticated equipment and materials, the complexity of maintaining precise control over production parameters, and ensuring consistent quality and performance. Addressing these cost-effectiveness and comprehensive approach: investing in research and development to discover scalable processes, conducting extensive pilot testing, collaborating with material suppliers for availability and cost-effectiveness, and adopting modular scaling strategies. Additionally, focusing on reducing manufacturing costs and waste through strategies like material recycling can make advanced membranes more economically viable. Overcoming these hurdles is crucial for the commercial adoption of advanced gas separation membrane technologies, potentially revolutionizing their use across various industries (Sheng et al., 2021; Swaby et al., 2021).
This review highlights the growing emphasis on innovative and sustainable manufacturing techniques, emphasising the adoption of eco-friendly materials, advanced methodologies, and efforts to minimize waste and cost. The review comprehensively covers a wide array of manufacturing techniques, from conventional methods to advanced approaches, including green synthesis. It underscores the impact of these techniques on environmental sustainability, performance improvement, scalability, and economic feasibility. The exploration into sustainable membrane manufacturing reveals a pressing need for renewable material sources, minimizing or substituting toxic organic solvents, and implementing advanced techniques, such as surface modification and functionalization, in the industry to enhance membrane performance. Despite the potential of advanced manufacturing techniques to yield high-performing membranes, their complexity and cost pose barriers to extensive application compared to conventional techniques such as casting. In addition, a critical analysis within this review examines the potential of bio-based polymers as viable alternatives to fossil fuel-derived polymers, emphasizing the importance of selecting biodegradable polymers that balance selectivity, permeability, and chemical resistance, suitable for specific applications. However, the challenge remains with many biodegradable materials lacking in mechanical stability and performance under harsh conditions, thus maintaining the dominance of fossil fuel-based polymers. To circumvent these limitations, the review discussed several methods to overcome this limitation, for example, the development of hybrid polymers, blending biodegradable materials with innovative substances to enhance mechanical strength and permeability without compromising biodegradability. As the search of advanced membrane materials increases in response to material challenges, the conversion of these innovations into practical, market-ready solutions is still constrained. A more concerted effort is necessary to advance, beyond material discovery, the development of reproducible, economically feasible membrane systems. This process demands thorough evaluation of affordability and scalability by comprehensive technoeconomic assessments to satisfy the requirements of industrial applications.
In light of the challenges identified in this review, it is imperative to undertake innovative measures to advance the development of sustainable gas separation membranes, focusing on the following key aspects:
(1) Advancing material innovation: There is a critical need to develop advanced materials in a sustainable and cost-effective manner. Bio-based and environmentally friendly materials, along with nanomaterials such as metal-organic frameworks and carbon structures, have shown remarkable potential in enhancing membrane performance. However, their widespread industrial adoption is hindered by challenges related to cost and scalability of production. Innovative approaches such as mechanochemical synthesis offer promising avenues for manufacturing these materials at scale, eliminating the use of solvents and reducing production costs. Indeed, leveraging techniques like reactive extrusion and mechanochemistry holds significant promise in overcoming these challenges.
(2) Intelligent membranes for eco-friendly disposal: Developing membranes that react to external triggers could pave the way for sustainable disposal methods at their life cycle’s end. Currently, the predominant approaches to dispose of membranes at the end of their usefulness mirror those of plastic waste, primarily landfilling or burning. However, the introduction of smart membranes designed to break down in response to specific stimuli can help bypass these environmentally damaging disposal practices, thus enhancing the eco-sustainability of membrane technologies.
(3) Incorporating life cycle and economic evaluations in membrane innovation. Traditionally, the emphasis in membrane research has been on improving selectivity and permeability. Yet, it's critical to balance these improvements with considerations of cost and environmental impact. New materials should be developed with an eye toward the entire process, including raw materials, fabrication methods and other factors critical for scaling and deploying the technology effectively.
(4) Embracing digital technologies and modelling. The use of digital tools, including artificial intelligence, can expedite the search for new membrane materials by evaluating multiple optimization goals, such as permeability, selectivity, affordability, and carbon footprint. Additionally, incorporating process analytical technologies within membrane systems allows for real-time monitoring, potentially improving maintenance strategies and extending the lifespan of membranes.
In general, future research endeavors should embrace a holistic strategy, as outlined in Table 5, covering the selection of materials, improvement of fabrication processes, and embedding biodegradable features into the creation of sustainable polymeric gas separation membranes. In conclusion, the evolution of membrane technology is poised at a promising juncture, driven by collaborative efforts across disciplines. By dedicating research to overcome current challenges and unlocking new possibilities for eco-friendly gas separation technologies, the field sets a new benchmark for performance and environmental responsibility in industrial applications. The collective endeavor towards sustainable manufacturing and the development of reproducible, economically viable membrane systems underscores the bright future of membrane technologies (Figure 12), promising not only enhanced performance but also a significant reduction in the ecological impact of gas separation processes.
SA: Data curation, Formal Analysis, Investigation, Software, Visualization, Writing–original draft, Conceptualization, Methodology. BC-D: Supervision, Writing–review and editing, Conceptualization.
The author(s) declare that no financial support was received for the research, authorship, and/or publication of this article.
The authors express their gratitude to the Kuwait Institute for Scientific Research (KISR) for providing financial support for SA’s PhD studies.
The authors declare that the research was conducted in the absence of any commercial or financial relationships that could be construed as a potential conflict of interest.
All claims expressed in this article are solely those of the authors and do not necessarily represent those of their affiliated organizations, or those of the publisher, the editors and the reviewers. Any product that may be evaluated in this article, or claim that may be made by its manufacturer, is not guaranteed or endorsed by the publisher.
The Supplementary Material for this article can be found online at: https://www.frontiersin.org/articles/10.3389/frmst.2024.1390599/full#supplementary-material
Achilias, D. S., and Karayannidis, G. P. (2004). The chemical recycling of PET in the framework of sustainable development. Water, Air, & Soil Pollut. Focus 4, 385–396. doi:10.1023/B:WAFO.0000044812.47185.0f
Adhikari, B., Orme, C. J., Klaehn, J. R., and Stewart, F. F. (2021). Technoeconomic analysis of oxygen-nitrogen separation for oxygen enrichment using membranes. Sep. Purif. Technol. 268, 118703. doi:10.1016/j.seppur.2021.118703
Air Liquide (2024). Membrane technology. Available at: https://advancedseparations.airliquide.com/about/membrane-technology (Accessed March 25, 2024).
Air Products (2024). Prism® membranes. Available at: https://www.airproducts.com/equipment/prism-membranes (Accessed March 25, 2024).
AirRane (2024). Gas separation membrane technology. Available at: https://en.airrane.com/membrane_technology_principle (Accessed March 25, 2024).
Ajari, H., Chaouachi, B., Galiano, F., Marino, T., Russo, F., and Figoli, A. (2019). A novel approach for dissolving crystalline LDPE using non-toxic solvents for membranes preparation. Int. J. Environ. Sci. Technol. 16, 5375–5386. doi:10.1007/s13762-018-2123-y
Alam, J., Dass, L. A., Alhoshan, M. S., Ghasemi, M., and Mohammad, A. W. (2012). Development of polyaniline-modified polysulfone nanocomposite membrane. Appl. Water Sci. 2, 37–46. doi:10.1007/s13201-011-0021-2
Alghunaimi, F. (2013). The performance of a thermally cross-linked polymer of intrinsic microporosity (PIM-1) for gas separation. Saudi Arab KAUST Res. Repos. doi:10.25781/KAUST-F5936
Alkandari, S. H., and Castro-Dominguez, B. (2023). Electro-casting for superior gas separation membrane performance and manufacturing. ACS Appl. Mater Interfaces 15, 56600–56611. doi:10.1021/acsami.3c14742
Alkandari, S. H., Lightfoot, J., and Castro-Dominguez, B. (2023). Asymmetric membranes for gas separation: interfacial insights and manufacturing. RSC Adv. 13, 14198–14209. doi:10.1039/D3RA00995E
Alkekhia, D., Hammond, P. T., and Shukla, A. (2020). Layer-by-Layer biomaterials for drug delivery. Annu. Rev. Biomed. Eng. 22, 1–24. doi:10.1146/annurev-bioeng-060418-052350
Al-Shaeli, M., Al-Juboori, R. A., Al Aani, S., Ladewig, B. P., and Hilal, N. (2022). Natural and recycled materials for sustainable membrane modification: recent trends and prospects. Sci. Total Environ. 838, 156014. doi:10.1016/j.scitotenv.2022.156014
Amooghin, A. E., Sanaeepur, H., Pedram, M. Z., Omidkhah, M., and Kargari, A. (2016). New advances in polymeric membranes for CO2 separation. Polym. Sci. Res. Adv. Pract. Appl. Educ. aspects, 354–368.
An, H., Lee, A. S., Kammakakam, I., Sang Hwang, S., Kim, J.-H., Lee, J.-H., et al. (2018). Bromination/debromination-induced thermal crosslinking of 6FDA-Durene for aggressive gas separations. J. Memb. Sci. 545, 358–366. doi:10.1016/j.memsci.2017.09.083
Anbukarasu, P., Sauvageau, D., and Elias, A. (2021). The effects of solvent casting temperature and physical aging on polyhydroxybutyrate-graphene nanoplatelet composites. Polym. Compos 42, 1451–1461. doi:10.1002/pc.25915
Asad, A., Sameoto, D., and Sadrzadeh, M. (2020). “Overview of membrane technology,” in Nanocomposite membranes for water and gas separation (Amsterdam, Netherlands: Elsevier), 1–28. doi:10.1016/B978-0-12-816710-6.00001-8
Askari, M., Xiao, Y., Li, P., and Chung, T.-S. (2012). Natural gas purification and olefin/paraffin separation using cross-linkable 6FDA-Durene/DABA co-polyimides grafted with α, β, and γ-cyclodextrin. J. Memb. Sci. 390 (391), 141–151. doi:10.1016/j.memsci.2011.11.030
Atwoli, L., Baqui, A. H., Benfield, T., Bosurgi, R., Godlee, F., Hancocks, S., et al. (2021). Call for emergency action to limit global temperature increases, restore biodiversity, and protect health. N. Engl. J. Med. 385, 1134–1137. doi:10.1056/NEJMe2113200
Azzam, S. A., Alshafei, F. H., López-Ausens, T., Ghosh, R., Biswas, A. N., Sautet, P., et al. (2019). Effects of morphology and surface properties of copper oxide on the removal of hydrogen sulfide from gaseous streams. Ind. Eng. Chem. Res. 58, 18836–18847. doi:10.1021/acs.iecr.9b03975
Bagheri, A., and Jin, J. (2019). Photopolymerization in 3D printing. ACS Appl. Polym. Mater 1, 593–611. doi:10.1021/acsapm.8b00165
Baker, R. W. (2002). Future directions of membrane gas separation technology. Ind. Eng. Chem. Res. 41, 1393–1411. doi:10.1021/ie0108088
Bandehali, S., Sanaeepur, H., Ebadi Amooghin, A., Shirazian, S., and Ramakrishna, S. (2021). Biodegradable polymers for membrane separation. Sep. Purif. Technol. 269, 118731. doi:10.1016/j.seppur.2021.118731
Basf, S. E. (2024) Ultrason® – a versatile material for the production of tailor-made membranes – brochure, English.
Bazhenov, S. D., Borisov, I. L., Bakhtin, D. S., Rybakova, A. N., Khotimskiy, V. S., Molchanov, S. P., et al. (2016). High-permeance crosslinked PTMSP thin-film composite membranes as supports for CO2 selective layer formation. Green Energy & Environ. 1, 235–245. doi:10.1016/j.gee.2016.10.002
Begni, F., Lasseuguette, E., Paul, G., Bisio, C., Marchese, L., Gatti, G., et al. (2021). Hyper cross-linked polymers as additives for preventing aging of PIM-1 membranes. Membr. (Basel) 11, 463. doi:10.3390/membranes11070463
Beuscher, U., Kappert, E. J., and Wijmans, J. G. (2022). Membrane research beyond materials science. J. Memb. Sci. 643, 119902. doi:10.1016/j.memsci.2021.119902
Bolto, B., Tran, T., Hoang, M., and Xie, Z. (2009). Crosslinked poly(vinyl alcohol) membranes. Prog. Polym. Sci. 34, 969–981. doi:10.1016/j.progpolymsci.2009.05.003
Bridge, A. T., Pedretti, B. J., Brennecke, J. F., and Freeman, B. D. (2022). Preparation of defect-free asymmetric gas separation membranes with dihydrolevoglucosenone (CyreneTM) as a greener polar aprotic solvent. J. Memb. Sci. 644, 120173. doi:10.1016/j.memsci.2021.120173
Bryant, R. G. (2014). “Polyimides,” in Ullmann’s encyclopedia of industrial chemistry (Weinheim, Germany: Wiley-VCH Verlag GmbH & Co. KGaA), 1–27. doi:10.1002/14356007.a21_253.pub2
Capello, C., Fischer, U., and Hungerbühler, K. (2007). What is a green solvent? A comprehensive framework for the environmental assessment of solvents. Green Chem. 9, 927. doi:10.1039/b617536h
Castel, C., Bounaceur, R., and Favre, E. (2021). Membrane processes for direct carbon dioxide capture from air: possibilities and limitations. Front. Chem. Eng. 3. doi:10.3389/fceng.2021.668867
Castro-Aguirre, E., Auras, R., Selke, S., Rubino, M., and Marsh, T. (2018). Enhancing the biodegradation rate of poly(lactic acid) films and PLA bio-nanocomposites in simulated composting through bioaugmentation. Polym. Degrad. Stab. 154, 46–54. doi:10.1016/j.polymdegradstab.2018.05.017
Ceratti, D. R., Louis, B., Paquez, X., Faustini, M., and Grosso, D. (2015). A new dip coating method to obtain large-surface coatings with a minimum of solution. Adv. Mater. 27, 4958–4962. doi:10.1002/adma.201502518
Chen, J., Jiang, X., Tang, W., Ma, L., Li, Y., Huang, Y., et al. (2020a). Roll-to-roll stack and lamination of gas diffusion layer in multilayer structured membrane electrode assembly. Proc. Inst. Mech. Eng. B J. Eng. Manuf. 234, 66–74. doi:10.1177/0954405419862090
Chen, X., Zhang, Z., Wu, L., Liu, X., Xu, S., Efome, J. E., et al. (2020b). Polymers of intrinsic microporosity having bulky substitutes and cross-linking for gas separation membranes. ACS Appl. Polym. Mater 2, 987–995. doi:10.1021/acsapm.9b01193
Chitranshi Jaiswal (2024) Global gas separation membrane market overview. New York, USA: Spherical Insights.
Choi, W., Ingole, P. G., Park, J.-S., Lee, D.-W., Kim, J.-H., and Lee, H.-K. (2015). H2/CO mixture gas separation using composite hollow fiber membranes prepared by interfacial polymerization method. Chem. Eng. Res. Des. 102, 297–306. doi:10.1016/j.cherd.2015.06.037
Chung, T.-S., Jiang, L. Y., Li, Y., and Kulprathipanja, S. (2007). Mixed matrix membranes (MMMs) comprising organic polymers with dispersed inorganic fillers for gas separation. Prog. Polym. Sci. 32, 483–507. doi:10.1016/j.progpolymsci.2007.01.008
Clarizia, G., Tasselli, F., Simari, C., Nicotera, I., and Bernardo, P. (2019). Solution casting blending: an effective way for tailoring gas transport and mechanical properties of poly(vinyl butyral) and Pebax2533. J. Phys. Chem. C 123, 11264–11272. doi:10.1021/acs.jpcc.9b01459
Clark, J. H., and Tavener, S. J. (2007). Alternative solvents: shades of green. Org. Process Res. Dev. 11, 149–155. doi:10.1021/op060160g
Clarke, C. J., Tu, W.-C., Levers, O., Bröhl, A., and Hallett, J. P. (2018). Green and sustainable solvents in chemical processes. Chem. Rev. 118, 747–800. doi:10.1021/acs.chemrev.7b00571
Correia, A. R., Sampaio, I., Comparetti, E. J., Vieira, N. C. S., and Zucolotto, V. (2021). Detecting cancer cells with a highly sensitive LbL-based biosensor. Talanta 233, 122506. doi:10.1016/j.talanta.2021.122506
Cui, Y., Li, G., Wu, H., Pang, S., Zhuang, Y., Si, Z., et al. (2023). Preparation and characterization of asymmetric Kapton membranes for gas separation. React. Funct. Polym. 191, 105667. doi:10.1016/j.reactfunctpolym.2023.105667
Cui, Z. F., Jiang, Y., and Field, R. W. (2010). “Fundamentals of pressure-driven membrane separation processes,” in Membrane technology (Amsterdam, Netherlands: Elsevier), 1–18. doi:10.1016/B978-1-85617-632-3.00001-X
Dai, Z., Deng, J., Yu, Q., Helberg, R. M. L., Janakiram, S., Ansaloni, L., et al. (2019). Fabrication and evaluation of bio-based nanocomposite TFC hollow fiber membranes for enhanced CO 2 capture. ACS Appl. Mater Interfaces 11, 10874–10882. doi:10.1021/acsami.8b19651
Daio, T., Bayer, T., Ikuta, T., Nishiyama, T., Takahashi, K., Takata, Y., et al. (2015). In-Situ ESEM and EELS observation of water uptake and ice formation in multilayer graphene oxide. Sci. Rep. 5, 11807. doi:10.1038/srep11807
de Alvarenga, E. S. (2011). “Characterization and properties of chitosan,” in Biotechnology of biopolymers (InTech). doi:10.5772/17020
Decker, C., and Bianchi, C. (2003). Photocrosslinking of a maleimide functionalized polymethacrylate. Polym. Int. 52, 722–732. doi:10.1002/pi.1119
Decker, C., Bianchi, C., and Jönsson, S. (2004). Light-induced crosslinking polymerization of a novel N-substituted bis-maleimide monomer. Polym. Guildf. 45, 5803–5811. doi:10.1016/j.polymer.2004.06.047
Dibrov, G. A., Volkov, V. V., Vasilevsky, V. P., Shutova, A. A., Bazhenov, S. D., Khotimsky, V. S., et al. (2014). Robust high-permeance PTMSP composite membranes for CO2 membrane gas desorption at elevated temperatures and pressures. J. Memb. Sci. 470, 439–450. doi:10.1016/j.memsci.2014.07.056
Dolejš, P., Poštulka, V., Sedláková, Z., Jandová, V., Vejražka, J., Esposito, E., et al. (2014). Simultaneous hydrogen sulphide and carbon dioxide removal from biogas by water–swollen reverse osmosis membrane. Sep. Purif. Technol. 131, 108–116. doi:10.1016/j.seppur.2014.04.041
Dong, C., He, R., Xu, S., He, H., Chen, H., Zhang, Y.-B., et al. (2022). Layer-by-layer (LBL) hollow fiber nanofiltration membranes for seawater treatment: ion rejection. Desalination 534, 115793. doi:10.1016/j.desal.2022.115793
Donohue, M. D., Minhas, B. S., and Lee, S. Y. (1989). Permeation behavior of carbon dioxide-methane mixtures in cellulose acetate membranes. J. Memb. Sci. 42, 197–214. doi:10.1016/S0376-7388(00)82376-5
Dose, M. E., Chwatko, M., Hubacek, I., Lynd, N. A., Paul, D. R., and Freeman, B. D. (2019). Thermally cross-linked diaminophenylindane (DAPI) containing polyimides for membrane based gas separations. Polym. Guildf. 161, 16–26. doi:10.1016/j.polymer.2018.11.050
Du, N., Park, H. B., Robertson, G. P., Dal-Cin, M. M., Visser, T., Scoles, L., et al. (2011). Polymer nanosieve membranes for CO2-capture applications. Nat. Mater 10, 372–375. doi:10.1038/nmat2989
El-Khair, A., and Ali, A. A. (2013). The mechanical behaviour of recycled high density polyethylene. Int. J. Mod. Eng. Res. (IJMER) 3.
Elsaidi, S. K., Ostwal, M., Zhu, L., Sekizkardes, A., Mohamed, M. H., Gipple, M., et al. (2021). 3D printed MOF-based mixed matrix thin-film composite membranes. RSC Adv. 11, 25658–25663. doi:10.1039/D1RA03124D
Esteban, N., Juan-y-Seva, M., Aguilar-Lugo, C., Miguel, J. A., Staudt, C., de la Campa, J. G., et al. (2022). Aromatic polyimide membranes with tert-butyl and carboxylic side groups for gas separation applications—covalent crosslinking study. Polym. (Basel) 14, 5517. doi:10.3390/polym14245517
Evonik (2024). Efficient gas separation using hollow-fiber membranes. Available at: https://www.membrane-separation.com/en/efficient-gas-separation-with-sepuran-by-evonik (Accessed March 25, 2024).
Fan, S.-T., Wang, J.-X., Liao, L.-G., Feng, J.-F., Li, B.-J., and Zhang, S. (2023). Enhanced selectivity in thin-film composite membrane for CO2 capture through improvement to support layer. Chem. Eng. J. 468, 143645. doi:10.1016/j.cej.2023.143645
Farjoo, A., and Kuznicki, S. M. (2016). H 2 separation using tubular stainless steel suppoType equation here.rted natural clinoptilolite membranes. Can. J. Chem. Eng. 94, 2219–2224. doi:10.1002/cjce.22589
Figoli, A., Marino, T., and Galiano, F. (2016). “Polymeric membranes in biorefinery,” in Membrane technologies for biorefining (Amsterdam, Netherlands: Elsevier), 29–59.
Figoli, A., Marino, T., Galiano, F., Dorraji, S. S., Di Nicolò, E., and He, T. (2017). “Sustainable route in preparation of polymeric membranes,” in Green chemistry and sustainable technology book series (GCST) (Berlin, Germany: Springer), 97–120. doi:10.1007/978-981-10-5623-9_4
Figoli, A., Marino, T., Simone, S., Di Nicolò, E., Li, X.-M., He, T., et al. (2014). Towards non-toxic solvents for membrane preparation: a review. Green Chem. 16, 4034–4059. doi:10.1039/C4GC00613E
Figueroa, J. D., Fout, T., Plasynski, S., McIlvried, H., and Srivastava, R. D. (2008). Advances in CO2 capture technology—the U.S. Department of energy’s carbon sequestration program. Int. J. Greenh. Gas Control 2, 9–20. doi:10.1016/S1750-5836(07)00094-1
Follain, N., Chappey, C., Dargent, E., Chivrac, F., Cretois, R., and Marais, S. (2014). Structure and barrier properties of biodegradable polyhydroxyalkanoate films. J. Phys. Chem. C 118, 6165–6177. doi:10.1021/jp408150k
Foster, A. B., Beal, J. L., Tamaddondar, M., Luque-Alled, J. M., Robertson, B., Mathias, M., et al. (2021). Importance of small loops within PIM-1 topology on gas separation selectivity in thin-film composite membranes. J. Mater Chem. A Mater 9, 21807–21823. doi:10.1039/D1TA03712A
Fu, Y., Qin, L., Huang, D., Zeng, G., Lai, C., Li, B., et al. (2019). Chitosan functionalized activated coke for Au nanoparticles anchoring: green synthesis and catalytic activities in hydrogenation of nitrophenols and azo dyes. Appl. Catal. B 255, 117740. doi:10.1016/j.apcatb.2019.05.042
Galiano, F., Briceño, K., Marino, T., Molino, A., Christensen, K. V., and Figoli, A. (2018). Advances in biopolymer-based membrane preparation and applications. J. Memb. Sci. 564, 562–586. doi:10.1016/j.memsci.2018.07.059
Garcia-Fayos, J., Serra, J. M., Luiten-Olieman, M. W. J., and Meulenberg, W. A. (2020). “Gas separation ceramic membranes,” in Advanced ceramics for energy conversion and storage (Amsterdam, Netherlands: Elsevier), 321–385. doi:10.1016/B978-0-08-102726-4.00008-9
Gillono, M., Roppolo, I., Frascella, F., Scaltrito, L., Pirri, C. F., and Chiappone, A. (2020). CO2 permeability control in 3D printed light responsive structures. Appl. Mater Today 18, 100470. doi:10.1016/j.apmt.2019.100470
Gopi, S., Pius, A., Kargl, R., Kleinschek, K. S., and Thomas, S. (2019). Fabrication of cellulose acetate/chitosan blend films as efficient adsorbent for anionic water pollutants. Polym. Bull. 76, 1557–1571. doi:10.1007/s00289-018-2467-y
Gu, Y., and Jérôme, F. (2013). Bio-based solvents: an emerging generation of fluids for the design of eco-efficient processes in catalysis and organic chemistry. Chem. Soc. Rev. 42, 9550–9570. doi:10.1039/c3cs60241a
Gutierrez, D. B., Caldona, E. B., Espiritu, R. D., and Advincula, R. C. (2021). The potential of additively manufactured membranes for selective separation and capture of CO2. MRS Commun. 11, 391–401. doi:10.1557/s43579-021-00062-8
Gutierrez, D. B., Caldona, E. B., Yang, Z., Suo, X., Cheng, X., Dai, S., et al. (2022). 3D-printed PDMS-based membranes for CO2 separation applications. MRS Commun. 12, 1174–1182. doi:10.1557/s43579-022-00287-1
Gutierrez, D. B., Caldona, E. B., Yang, Z., Suo, X., Cheng, X., Dai, S., et al. (2023). PDMS-silica composite gas separation membranes by direct ink writing. J. Appl. Polym. Sci. 140. doi:10.1002/app.54277
Hansen, C. M. (2007). “Hansen solubility parameters,” in A user’s handbook. Editor C. M. Hansen (Boca Raton: CRC Press).
Henis, J. M. S., and Tripodi, M. K. (1980). A novel approach to gas separations using composite hollow fiber membranes. Sep. Sci. Technol. 15, 1059–1068. doi:10.1080/01496398008076287
Heo, J., Choi, M., Chang, J., Ji, D., Kang, S. W., and Hong, J. (2017). Highly permeable graphene oxide/polyelectrolytes hybrid thin films for enhanced CO2/N2 separation performance. Sci. Rep. 7, 456. doi:10.1038/s41598-017-00433-z
Heo, J., Choi, M., Choi, D., Jeong, H., Kim, H. Y., Jeon, H., et al. (2020). Spray-assisted layer-by-layer self-assembly of tertiary-amine-stabilized gold nanoparticles and graphene oxide for efficient CO2 capture. J. Memb. Sci. 601, 117905. doi:10.1016/j.memsci.2020.117905
Herzberger, J., Sirrine, J. M., Williams, C. B., and Long, T. E. (2019). Polymer design for 3D printing elastomers: recent advances in structure, properties, and printing. Prog. Polym. Sci. 97, 101144. doi:10.1016/j.progpolymsci.2019.101144
Higashi, S., Yamato, M., and Kawakami, H. (2021). Effect of phase separation due to solvent evaporation on particle aggregation in the skin layer of the gas separation membrane. J. Photopolym. Sci. Technol. 34, 449–456. doi:10.2494/photopolymer.34.449
Honeywell (2024). Honeywell announces new technology for green hydrogen production. Available at: https://pmt.honeywell.com/us/en/about-pmt/newsroom/press-release/2022/03/honeywell-announces-new-technology-for-green-hydrogen-production (Accessed March 25, 2024).
Hong, T., Niu, Z., Hu, X., Gmernicki, K., Cheng, S., Fan, F., et al. (2015). Effect of cross-link density on carbon dioxide separation in polydimethylsiloxane-norbornene membranes. ChemSusChem 8, 3595–3604. doi:10.1002/cssc.201500903
Hosseini, S. S., and Chung, T. S. (2009). Carbon membranes from blends of PBI and polyimides for N2/CH4 and CO2/CH4 separation and hydrogen purification. J. Memb. Sci. 328, 174–185. doi:10.1016/j.memsci.2008.12.005
Hosseini, S. S., and Valipouri, A. (2023). “Chapter 3 - electrospraying for membrane fabrication,” in Electrospun and nanofibrous membranes. Editors A. Kargari, T. Matsuura, and M. M. A. Shirazi (Amsterdam, Netherlands: Elsevier), 53–80. doi:10.1016/B978-0-12-823032-9.00024-6
Houde, A. Y., Krishnakumar, B., Charati, S. G., and Stern, S. A. (1996). Permeability of dense (homogeneous) cellulose acetate membranes to methane, carbon dioxide, and their mixtures at elevated pressures. J. Appl. Polym. Sci. 62, 2181–2192. doi:10.1002/(SICI)1097-4628(19961226)62:13<2181::AID-APP1>3.0.CO;2-F
Hu, Z., Zhang, H., Zhang, X.-F., Jia, M., and Yao, J. (2022). Polyethylenimine grafted ZIF-8@cellulose acetate membrane for enhanced gas separation. J. Memb. Sci. 662, 120996. doi:10.1016/j.memsci.2022.120996
Huang, C.-L., Wang, P.-Y., and Li, Y.-Y. (2020). Fabrication of electrospun CO2 adsorption membrane for zinc-air battery application. Chem. Eng. J. 395, 125031. doi:10.1016/j.cej.2020.125031
Huh, M., Lee, H. M., Park, Y. S., and Yun, S.Il (2017). Biocomposite membranes based on poly(3-hydroxybutyrate-co-3-hydroxyvalerate) and multiwall carbon nanotubes for gas separation. Carbon Lett. 21, 116–121. doi:10.5714/CL.2017.21.116
Hull, C. W. (1986) Apparatus for production of three-dimensional objects by stereolithography, 1–16.
Hunger, K., Schmeling, N., Jeazet, H. B. T., Janiak, C., Staudt, C., and Kleinermanns, K. (2012). Investigation of cross-linked and additive containing polymer materials for membranes with improved performance in pervaporation and gas separation. Membr. (Basel) 2, 727–763. doi:10.3390/membranes2040727
Ignatyev, I. A., Thielemans, W., and Vander Beke, B. (2014). Recycling of polymers: a review. ChemSusChem 7, 1579–1593. doi:10.1002/cssc.201300898
Ismail, A., and Aziz, F. (2012). “Chemical cross-linking modifications of polymeric membranes for gas separation applications,” in Membrane modification (Florida, United States: CRC Press), 363–384. doi:10.1201/b12160-12
Ismail, A. F., Khulbe, K. C., and Matsuura, T. (2015) Gas separation membranes, 10. Switz.: Springer, 973–978. doi:10.1007/978-3-319-01095-3
Ito, A., Sato, M., and Anma, T. (2003). Permeability of CO2 through chitosan membrane swollen by water vapor in feed gas. Die Angew. Makromol. Chem. 248, 85–94. doi:10.1002/apmc.1997.052480105
Iulianelli, A., Algieri, C., Donato, L., Garofalo, A., Galiano, F., Bagnato, G., et al. (2017). New PEEK-WC and PLA membranes for H2 separation. Int. J. Hydrogen Energy 42, 22138–22148. doi:10.1016/j.ijhydene.2017.04.060
Iulianelli, A., Russo, F., Galiano, F., Desiderio, G., Basile, A., and Figoli, A. (2019). PLA easy fil – white-based membranes for CO2 separation. Greenh. Gases Sci. Technol. 9, 360–369. doi:10.1002/ghg.1853
Iulianelli, A., Russo, F., Galiano, F., Manisco, M., and Figoli, A. (2022). Novel bio-polymer based membranes for CO2/CH4 separation. Int. J. Greenh. Gas Control 117, 103657. doi:10.1016/j.ijggc.2022.103657
Jami’an, W. N. R., Hasbullah, H., Mohamed, F., Wan Salleh, W. N., Ibrahim, N., and Ali, R. R. (2015). Biodegradable gas separation membrane preparation by manipulation of casting parameters. Chem. Eng. Trans. 43, 1105–1110. doi:10.3303/CET1543185
Jamil, N., Othman, N. H., Shahrudin, M. Z., Mohd Razlan, M. R., Alias, N. H., Marpani, F., et al. (2020). Effects of pebax coating concentrations on Co2/ch4 separation of rgo/zif-8 pes membranes. J. Teknol. 82. doi:10.11113/jt.v82.13872
Jeon, J. W., Kim, D.-G., Sohn, E., Yoo, Y., Kim, Y. S., Kim, B. G., et al. (2017). Highly carboxylate-functionalized polymers of intrinsic microporosity for CO 2 -selective polymer membranes. Macromolecules 50, 8019–8027. doi:10.1021/acs.macromol.7b01332
Jiang, S., and Ladewig, B. P. (2020). Green synthesis of polymeric membranes: recent advances and future prospects. Curr. Opin. Green Sustain Chem. 21, 1–8. doi:10.1016/j.cogsc.2019.07.002
Jiang, X., Chuah, C. Y., Goh, K., and Wang, R. (2021). A facile direct spray-coating of Pebax® 1657: towards large-scale thin-film composite membranes for efficient CO2/N2 separation. J. Memb. Sci. 638, 119708. doi:10.1016/j.memsci.2021.119708
Jimenez-Solomon, M. F., Song, Q., Jelfs, K. E., Munoz-Ibanez, M., and Livingston, A. G. (2016). Polymer nanofilms with enhanced microporosity by interfacial polymerization. Nat. Mater 15, 760–767. doi:10.1038/nmat4638
Jirsáková, K., Stanovský, P., Dytrych, P., Morávková, L., Přibylová, K., Petrusová, Z., et al. (2021). Organic vapour permeation in amorphous and semi-crystalline rubbery membranes: experimental data versus prediction by solubility parameters. J. Memb. Sci. 627, 119211. doi:10.1016/j.memsci.2021.119211
Jiun, Y. L., Tze, C. T., Moosa, U., and Tawawneh, M. A. A. (2016). Effects of recycling cycle on used thermoplastic polymer and thermoplastic elastomer polymer. Polym. Polym. Compos. 24, 735–740. doi:10.1177/096739111602400909
Karayannidis, G. P., and Achilias, D. S. (2007). Chemical recycling of poly(ethylene terephthalate). Macromol. Mat. Eng. 292, 128–146. doi:10.1002/mame.200600341
Katepalli, H., Bikshapathi, M., Sharma, C. S., Verma, N., and Sharma, A. (2011). Synthesis of hierarchical fabrics by electrospinning of PAN nanofibers on activated carbon microfibers for environmental remediation applications. Chem. Eng. J. 171, 1194–1200. doi:10.1016/j.cej.2011.05.025
Kattula, M., Ponnuru, K., Zhu, L., Jia, W., Lin, H., and Furlani, E. P. (2015). Designing ultrathin film composite membranes: the impact of a gutter layer. Sci. Rep. 5, 15016. doi:10.1038/srep15016
Kelman, S. (2008) Crosslinking and stabilization of high fractional free volume polymers for the separation of organic vapors from permanent gases.
Khorshidi, B., Hajinasiri, J., Ma, G., Bhattacharjee, S., and Sadrzadeh, M. (2016a). Thermally resistant and electrically conductive PES/ITO nanocomposite membrane. J. Memb. Sci. 500, 151–160. doi:10.1016/j.memsci.2015.11.015
Khorshidi, B., Hosseini, S. A., Ma, G., McGregor, M., and Sadrzadeh, M. (2019). Novel nanocomposite polyethersulfone-antimony tin oxide membrane with enhanced thermal, electrical and antifouling properties. Polym. Guildf. 163, 48–56. doi:10.1016/j.polymer.2018.12.058
Khorshidi, B., Thundat, T., Fleck, B. A., and Sadrzadeh, M. (2016b). A novel approach toward fabrication of high performance thin-film composite polyamide membranes. Sci. Rep. 6, 22069. doi:10.1038/srep22069
Kosinov, N., Gascon, J., Kapteijn, F., and Hensen, E. J. M. (2016). Recent developments in zeolite membranes for gas separation. J. Memb. Sci. 499, 65–79. doi:10.1016/j.memsci.2015.10.049
Kunalan, S., Palanivelu, K., Sachin, E. K., Syrtsova, D. A., and Teplyakov, V. V. (2022). Thin-film hydrogel polymer layered polyvinyltrimethylsilane dual-layer flat-bed composite membrane for CO 2 gas separation. J. Appl. Polym. Sci. 139. doi:10.1002/app.52024
Kuruppalil, Z. (2011). “Green plastics: an emerging alternative for petroleum based plastics,” in IAJC-ASEE International Conference, April 29-30, 2011, 59–64.
Lam, B., Wei, M., Zhu, L., Luo, S., Guo, R., Morisato, A., et al. (2016). Cellulose triacetate doped with ionic liquids for membrane gas separation. Polym. Guildf. 89, 1–11. doi:10.1016/j.polymer.2016.02.033
Larsson, M., Markbo, O., and Jannasch, P. (2016). Melt processability and thermomechanical properties of blends based on polyhydroxyalkanoates and poly(butylene adipate-co-terephthalate). RSC Adv. 6, 44354–44363. doi:10.1039/C6RA06282B
Lasseuguette, E., and Ferrari, M.-C. (2020). “Polymer membranes for sustainable gas separation,” in Sustainable nanoscale engineering (Amsterdam, Netherlands: Elsevier), 265–296. doi:10.1016/B978-0-12-814681-1.00010-2
Lee, J.-Y., Tan, W. S., An, J., Chua, C. K., Tang, C. Y., Fane, A. G., et al. (2016). The potential to enhance membrane module design with 3D printing technology. J. Memb. Sci. 499, 480–490. doi:10.1016/j.memsci.2015.11.008
Lee, T. H., Shin, M. G., Jung, J. G., Suh, E. H., Oh, J. G., Kang, J. H., et al. (2022). Facile suppression of intensified plasticization in glassy polymer thin films towards scalable composite membranes for propylene/propane separation. J. Memb. Sci. 645, 120215. doi:10.1016/j.memsci.2021.120215
Lehermeier, H. J., Dorgan, J. R., and Way, J. D. (2001). Gas permeation properties of poly(lactic acid). J. Memb. Sci. 190, 243–251. doi:10.1016/S0376-7388(01)00446-X
Li, F., Li, L., Liao, X., and Wang, Y. (2011). Precise pore size tuning and surface modifications of polymeric membranes using the atomic layer deposition technique. J. Memb. Sci. 385–386, 1–9. doi:10.1016/j.memsci.2011.06.042
Li, F. Y., Xiao, Y., Chung, T.-S., and Kawi, S. (2012a). High-performance thermally self-cross-linked polymer of intrinsic microporosity (PIM-1) membranes for energy development. Macromolecules 45, 1427–1437. doi:10.1021/ma202667y
Li, G., Knozowska, K., Kujawa, J., Tonkonogovas, A., Stankevičius, A., and Kujawski, W. (2021). Fabrication of polydimethysiloxane (PDMS) dense layer on polyetherimide (PEI) hollow fiber support for the efficient CO2/N2 separation membranes. Polym. (Basel) 13, 756. doi:10.3390/polym13050756
Li, G., Si, Z., Yang, S., Xue, T., Baeyens, J., and Qin, P. (2022a). Fast layer-by-layer assembly of PDMS for boosting the gas separation of P84 membranes. Chem. Eng. Sci. 253, 117588. doi:10.1016/j.ces.2022.117588
Li, J., Cheng, P., Lin, M., Wey, M., and Tseng, H. (2020). Uniformity control and ultra-micropore development of tubular carbon membrane for light gas separation. AIChE J. 66. doi:10.1002/aic.16226
Li, N., Wang, Z., and Wang, J. (2022b). Water-swollen carboxymethyl chitosan (CMC)/polyamide (PA) membranes with octopus-branched nanostructures for CO2 capture. J. Memb. Sci. 642, 119946. doi:10.1016/j.memsci.2021.119946
Li, R., Yuan, S., Zhang, W., Zheng, H., Zhu, W., Li, B., et al. (2019). 3D printing of mixed matrix films based on metal–organic frameworks and thermoplastic polyamide 12 by selective laser sintering for water applications. ACS Appl. Mater Interfaces 11, 40564–40574. doi:10.1021/acsami.9b11840
Li, S., Wang, Z., Yu, X., Wang, J., and Wang, S. (2012b). High-performance membranes with multi-permselectivity for CO 2 separation. Adv. Mater. 24, 3196–3200. doi:10.1002/adma.201200638
Li, X., Chu, C., Wei, Y., Qi, C., Bai, J., Guo, C., et al. (2017). In vitro degradation kinetics of pure PLA and Mg/PLA composite: effects of immersion temperature and compression stress. Acta Biomater. 48, 468–478. doi:10.1016/j.actbio.2016.11.001
Li, Z., and Wang, C. (2013) One-Dimensional nanostructures. 1st Edn. Berlin, Heidelberg: Springer Berlin Heidelberg. doi:10.1007/978-3-642-36427-3
Ligon, S. C., Liska, R., Stampfl, J., Gurr, M., and Mülhaupt, R. (2017). Polymers for 3D printing and customized additive manufacturing. Chem. Rev. 117, 10212–10290. doi:10.1021/acs.chemrev.7b00074
Liu, M., Seeger, A., and Guo, R. (2023). Cross-linked polymer membranes for energy-efficient gas separation: innovations and perspectives. Macromolecules 56, 7230–7246. doi:10.1021/acs.macromol.3c01196
Low, Z.-X., Chua, Y. T., Ray, B. M., Mattia, D., Metcalfe, I. S., and Patterson, D. A. (2017). Perspective on 3D printing of separation membranes and comparison to related unconventional fabrication techniques. J. Memb. Sci. 523, 596–613. doi:10.1016/j.memsci.2016.10.006
Ma, T., Janot, J., and Balme, S. (2020). Track-Etched nanopore/membrane: from fundamental to applications. Small Methods 4. doi:10.1002/smtd.202000366
Ma, X.-H., and Yang, S.-Y. (2018). “Polyimide gas separation membranes,” in Advanced polyimide materials (Amsterdam, Netherlands: Elsevier), 257–322. doi:10.1016/B978-0-12-812640-0.00006-8
Ma, Z.-Y., Xue, Y.-R., Yang, H.-C., Wu, J., and Xu, Z.-K. (2022). Surface and interface engineering of polymer membranes: where we are and where to go. Macromolecules 55, 3363–3383. doi:10.1021/acs.macromol.1c02647
Madaeni, S. S., Badieh, M. M. S., and Vatanpour, V. (2013). Effect of coating method on gas separation by PDMS/PES membrane. Polym. Eng. Sci. 53, 1878–1885. doi:10.1002/pen.23456
Mafirad, S., Mehrnia, M. R., Zahedi, P., and Hosseini, S. (2018). Chitosan-based nanocomposite membranes with improved properties: effect of cellulose acetate blending and TiO 2 nanoparticles incorporation. Polym. Compos 39, 4452–4466. doi:10.1002/pc.24539
Makhlouf, A. S. H. (2011). “Current and advanced coating technologies for industrial applications,” in Nanocoatings and ultra-thin films (Amsterdam, Netherlands: Elsevier), 3–23. doi:10.1533/9780857094902.1.3
Marcano, A., Bou Haidar, N., Marais, S., Valleton, J.-M., and Duncan, A. C. (2017). Designing biodegradable PHA-based 3D scaffolds with antibiofilm properties for wound dressings: optimization of the microstructure/nanostructure. ACS Biomater. Sci. Eng. 3, 3654–3661. doi:10.1021/acsbiomaterials.7b00552
Marino, T., Blasi, E., Tornaghi, S., Di Nicolò, E., and Figoli, A. (2018). Polyethersulfone membranes prepared with Rhodiasolv®Polarclean as water soluble green solvent. J. Memb. Sci. 549, 192–204. doi:10.1016/j.memsci.2017.12.007
Martínez-Izquierdo, L., Malankowska, M., Téllez, C., and Coronas, J. (2021). Phase inversion method for the preparation of Pebax® 3533 thin film membranes for CO2/N2separation. J. Environ. Chem. Eng. 9, 105624. doi:10.1016/j.jece.2021.105624
Mendelsohn, J. D., Barrett, C. J., Chan, V. V., Pal, A. J., Mayes, A. M., and Rubner, M. F. (2000). Fabrication of microporous thin films from polyelectrolyte multilayers. Langmuir 16, 5017–5023. doi:10.1021/la000075g
Miramontes, E., Love, L. J., Lai, C., Sun, X., and Tsouris, C. (2020). Additively manufactured packed bed device for process intensification of CO2 absorption and other chemical processes. Chem. Eng. J. 388, 124092. doi:10.1016/j.cej.2020.124092
Mohamad, M. B., Fong, Y. Y., and Shariff, A. (2016). Gas separation of carbon dioxide from methane using polysulfone membrane incorporated with zeolite-T. Procedia Eng. 148, 621–629. doi:10.1016/j.proeng.2016.06.526
Mohamed, A., Yousef, S., Tuckute, S., Tonkonogovas, A., and Stankevičius, A. (2023). Gas permeation and selectivity of polysulfone/carbon non-woven fabric membranes with sponge and finger-like structures. Process Saf. Environ. Prot. 171, 630–639. doi:10.1016/j.psep.2023.01.055
Moon, J., Kim, M. Y., Kim, B. M., Lee, J. C., Choi, M.-C., and Kim, J. R. (2016). Estimation of the microbial degradation of biodegradable polymer, poly(lactic acid) (PLA) with a specific gas production rate. Macromol. Res. 24, 415–421. doi:10.1007/s13233-016-4060-2
MTR (2024). A cleaner approach to carbon capture. Available at: https://mtrccs.com/ (Accessed March 25, 2024).
Nailwal, B. C., Goswami, N., Nair, J. P., Keshavkumar, B., Surendran, P., Gupta, A. K., et al. (2023). Polyethylene terephthalate track etched membrane for recovery of helium from helium-nitrogen system. Express Polym. Lett. 17, 596–609. doi:10.3144/expresspolymlett.2023.44
Nasar, M. Q., Zohra, T., Khalil, A. T., Saqib, S., Ayaz, M., Ahmad, A., et al. (2019). Seripheidium quettense mediated green synthesis of biogenic silver nanoparticles and their theranostic applications. Green Chem. Lett. Rev. 12, 310–322. doi:10.1080/17518253.2019.1643929
Nguyen, D., Murialdo, M., Hornbostel, K., Pang, S., Ye, C., Smith, W., et al. (2019). 3D printed polymer composites for CO 2 capture. Ind. Eng. Chem. Res. 58, 22015–22020. doi:10.1021/acs.iecr.9b04375
Nikolaeva, D., Azcune, I., Tanczyk, M., Warmuzinski, K., Jaschik, M., Sandru, M., et al. (2018). The performance of affordable and stable cellulose-based poly-ionic membranes in CO2/N2 and CO2/CH4 gas separation. J. Memb. Sci. 564, 552–561. doi:10.1016/j.memsci.2018.07.057
Ohya, H., Kudryavtsev, V. V., and Semenova, S. I. (2022) Polyimide membranes. London: Routledge. doi:10.1201/9780203742969
Olivieri, L., Roso, M., De Angelis, M. G., and Lorenzetti, A. (2018). Evaluation of electrospun nanofibrous mats as materials for CO 2 capture: a feasibility study on functionalized poly(acrylonitrile) (PAN). J. Memb. Sci. 546, 128–138. doi:10.1016/j.memsci.2017.10.019
Papchenko, K., Degli Esposti, M., Minelli, M., Fabbri, P., Morselli, D., and De Angelis, M. G. (2022). New sustainable routes for gas separation membranes: the properties of poly(hydroxybutyrate-co-hydroxyvalerate) cast from green solvents. J. Memb. Sci. 660, 120847. doi:10.1016/j.memsci.2022.120847
Park, J., Kang, Z., Bender, G., Ulsh, M., and Mauger, S. A. (2020). Roll-to-roll production of catalyst coated membranes for low-temperature electrolyzers. J. Power Sources 479, 228819. doi:10.1016/j.jpowsour.2020.228819
Pasichnyk, M., Stanovsky, P., Polezhaev, P., Zach, B., Šyc, M., Bobák, M., et al. (2023). Membrane technology for challenging separations: removal of CO2, SO2 and NOx from flue and waste gases. Sep. Purif. Technol. 323, 124436. doi:10.1016/j.seppur.2023.124436
Patel, R. V., Raj, G. B., Chaubey, S., and Yadav, A. (2022). Investigation on the feasibility of recycled polyvinylidene difluoride polymer from used membranes for removal of methylene blue: experimental and DFT studies. Water Sci. Technol. 86, 194–210. doi:10.2166/wst.2022.193
Peelman, N., Ragaert, P., De Meulenaer, B., Adons, D., Peeters, R., Cardon, L., et al. (2013). Application of bioplastics for food packaging. Trends Food Sci. Technol. 32, 128–141. doi:10.1016/j.tifs.2013.06.003
Phaechamud, T., and Chitrattha, S. (2016). Pore formation mechanism of porous poly(dl-lactic acid) matrix membrane. Mater. Sci. Eng. C 61, 744–752. doi:10.1016/j.msec.2016.01.014
Pipitone, G., and Bolland, O. (2009). Power generation with CO2 capture: technology for CO2 purification. Int. J. Greenh. Gas Control 3, 528–534. doi:10.1016/j.ijggc.2009.03.001
Purkait, M. K., Sinha, M. K., Mondal, P., and Singh, R. (2018). “Introduction to membranes,” in Stimuli responsive polymeric membranes: smart polymeric membranes (Cambridge, MA, USA: Academic Press), 1–37. doi:10.1016/B978-0-12-813961-5.00001-2
Rafiq, S., Man, Z., Maulud, A., Muhammad, N., and Maitra, S. (2012). Separation of CO2 from CH4 using polysulfone/polyimide silica nanocomposite membranes. Sep. Purif. Technol. 90, 162–172. doi:10.1016/j.seppur.2012.02.031
Randová, A., Bartovská, L., Morávek, P., Matějka, P., Novotná, M., Matějková, S., et al. (2016). A fundamental study of the physicochemical properties of Rhodiasolv®Polarclean: a promising alternative to common and hazardous solvents. J. Mol. Liq. 224, 1163–1171. doi:10.1016/j.molliq.2016.10.085
Rasool, M. A., and Vankelecom, I. F. J. (2019). Use of γ-valerolactone and glycerol derivatives as bio-based renewable solvents for membrane preparation. Green Chem. 21, 1054–1064. doi:10.1039/C8GC03652G
Raza, A., Farrukh, S., Hussain, A., Khan, I., Othman, M. H. D., and Ahsan, M. (2021). Performance analysis of blended membranes of cellulose acetate with variable degree of acetylation for CO2/CH4 separation. Membr. (Basel) 11, 245. doi:10.3390/membranes11040245
Regmi, C., Ashtiani, S., Sofer, Z., and Friess, K. (2021). Improved CO2/CH4 separation properties of cellulose triacetate mixed–matrix membranes with CeO2@GO hybrid fillers. Membr. (Basel) 11, 777. doi:10.3390/membranes11100777
Robeson, L. M. (2008). The upper bound revisited. J. Memb. Sci. 320, 390–400. doi:10.1016/j.memsci.2008.04.030
Sadeghi, M., Semsarzadeh, M. A., and Moadel, H. (2009). Enhancement of the gas separation properties of polybenzimidazole (PBI) membrane by incorporation of silica nano particles. J. Memb. Sci. 331, 21–30. doi:10.1016/j.memsci.2008.12.073
Sanders, D. F., Smith, Z. P., Guo, R., Robeson, L. M., McGrath, J. E., Paul, D. R., et al. (2013). Energy-efficient polymeric gas separation membranes for a sustainable future: a review. Polym. Guildf. 54, 4729–4761. doi:10.1016/j.polymer.2013.05.075
Sazali, N., Syafiq Sharip, M., Ibrahim, H., Shahir Jamaludin, A., and Norharyati Wan Salleh, W. (2020). Influence of dip-coating times towards oxygen separation performance. IOP Conf. Ser. Mater Sci. Eng. 788, 012035. doi:10.1088/1757-899X/788/1/012035
Scheepers, D., Casimiro, A., Borneman, Z., and Nijmeijer, K. (2023). Addressing specific (Poly)ion effects for layer-by-layer membranes. ACS Appl. Polym. Mater 5, 2032–2042. doi:10.1021/acsapm.2c02078
Scheepers, D., Chatillon, B., Borneman, Z., and Nijmeijer, K. (2021). Influence of charge density and ionic strength on diallyldimethylammonium chloride (DADMAC)-based polyelectrolyte multilayer membrane formation. J. Memb. Sci. 617, 118619. doi:10.1016/j.memsci.2020.118619
Schmeling, N., Konietzny, R., Sieffert, D., Rölling, P., and Staudt, C. (2010). Functionalized copolyimide membranes for the separation of gaseous and liquid mixtures. Beilstein J. Org. Chem. 6, 789–800. doi:10.3762/bjoc.6.86
Scholes, C. A., Stevens, G. W., and Kentish, S. E. (2012). Membrane gas separation applications in natural gas processing. Fuel 96, 15–28. doi:10.1016/j.fuel.2011.12.074
Shankar, K., and Kandasamy, P. (2019). Carbon dioxide separation using α -alumina ceramic tube supported cellulose triacetate-tributyl phosphate composite membrane. Greenh. Gases Sci. Technol. 9, 287–305. doi:10.1002/ghg.1845
Shen, Y., and Lua, A. C. (2010). Effects of membrane thickness and heat treatment on the gas transport properties of membranes based on P84 polyimide. J. Appl. Polym. Sci. 116, 2906–2912. doi:10.1002/app.31810
Sheng, M., Dong, S., Qiao, Z., Li, Q., Yuan, Y., Xing, G., et al. (2021). Large-scale preparation of multilayer composite membranes for post-combustion CO2 capture. J. Memb. Sci. 636, 119595. doi:10.1016/j.memsci.2021.119595
Shenvi, S., Ismail, A. F., and Isloor, A. M. (2014). Preparation and characterization study of PPEES/chitosan composite membrane crosslinked with tripolyphosphate. Desalination 344, 90–96. doi:10.1016/j.desal.2014.02.026
Shenvi, S. S., Rashid, S. A., Ismail, A. F., Kassim, M. A., and Isloor, A. M. (2013). Preparation and characterization of PPEES/chitosan composite nanofiltration membrane. Desalination 315, 135–141. doi:10.1016/j.desal.2012.09.009
Sherwood, J., De bruyn, M., Constantinou, A., Moity, L., McElroy, C. R., Farmer, T. J., et al. (2014). Dihydrolevoglucosenone (Cyrene) as a bio-based alternative for dipolar aprotic solvents. Chem. Commun. 50, 9650–9652. doi:10.1039/C4CC04133J
Shi, Y., Wang, Z., Shi, Y., Zhu, S., Zhang, Y., and Jin, J. (2022). Synergistic design of enhanced π–π interaction and decarboxylation cross-linking of polyimide membranes for natural gas separation. Macromolecules 55, 2970–2982. doi:10.1021/acs.macromol.1c02573
Sholl, D. S., and Lively, R. P. (2016). Seven chemical separations to change the world. Nature 532, 435–437. doi:10.1038/532435a
Sing Soh, L., Uyin Hong, S., Zeng Liang, C., and Fen Yong, W. (2023). Green solvent-synthesized polyimide membranes for gas separation: coupling Hansen solubility parameters and synthesis optimization. Chem. Eng. J. 478, 147451. doi:10.1016/j.cej.2023.147451
Siracusa, V., Ingrao, C., Karpova, S. G., Olkhov, A. A., and Iordanskii, A. L. (2017). Gas transport and characterization of poly(3 hydroxybutyrate) films. Eur. Polym. J. 91, 149–161. doi:10.1016/j.eurpolymj.2017.03.047
SLB (2024). Cynara H2S and CO2 separation membranes. Available at: https://www.slb.com/products-and-services/innovating-in-oil-and-gas/well-production/processing-and-separation/gas-treatment/cynara-h2s-and-co2-separation-membranes (Accessed March 25, 2024).
Sokolov, S., Balynin, A., Bakhtin, D., and Borisov, I. (2021). Influence of spin coating parameters on gas transport properties of thin-film composite membranes. Materials 14, 5093. doi:10.3390/ma14175093
Song, Q., Nataraj, S. K., Roussenova, M. V., Tan, J. C., Hughes, D. J., Li, W., et al. (2012). Zeolitic imidazolate framework (ZIF-8) based polymer nanocomposite membranes for gas separation. Energy Environ. Sci. 5, 8359. doi:10.1039/c2ee21996d
Sridhar, S., Smitha, B., Mayor, S., Prathab, B., and Aminabhavi, T. M. (2007). Gas permeation properties of polyamide membrane prepared by interfacial polymerization. J. Mater Sci. 42, 9392–9401. doi:10.1007/s10853-007-1813-5
Suleman, M. S., Lau, K. K., and Yeong, Y. F. (2018). Enhanced gas separation performance of PSF membrane after modification to PSF/PDMS composite membrane in CO 2/CH 4 separation. J. Appl. Polym. Sci. 135. doi:10.1002/app.45650
Sun, Y., Zhang, X., Zhang, M., Ge, M., Wang, J., Tang, Y., et al. (2022). Rational design of electrospun nanofibers for gas purification: principles, opportunities, and challenges. Chem. Eng. J. 446, 137099. doi:10.1016/j.cej.2022.137099
Swaby, S., Ureña, N., Pérez-Prior, M. T., Várez, A., and Levenfeld, B. (2021). Synthesis and characterization of novel anion exchange membranes based on semi-interpenetrating networks of functionalized polysulfone: effect of ionic crosslinking. Polym. (Basel) 13, 958. doi:10.3390/polym13060958
Takahashi, S., and Paul, D. R. (2006). Gas permeation in poly(ether imide) nanocomposite membranes based on surface-treated silica. Part 1: without chemical coupling to matrix. Polym. Guildf. 47, 7519–7534. doi:10.1016/j.polymer.2006.08.029
Tan, P. C., Ooi, B. S., Ahmad, A. L., and Low, S. C. (2019). Formation of a defect-free polyimide/zeolitic imidazolate framework-8 composite membrane for gas separation: in-depth analysis of organic–inorganic compatibility. J. Chem. Technol. Biotechnol. 94, 2792–2804. doi:10.1002/jctb.5908
Tan, X., and Rodrigue, D. (2019). A review on porous polymeric membrane preparation. Part I: production techniques with polysulfone and poly (vinylidene fluoride). Polym. (Basel) 11, 1160. doi:10.3390/polym11071160
Tashvigh, A. A., Feng, Y., Weber, M., Maletzko, C., and Chung, T.-S. (2019). 110th anniversary: selection of cross-linkers and cross-linking procedures for the fabrication of solvent-resistant nanofiltration membranes: a review. Ind. Eng. Chem. Res. 58, 10678–10691. doi:10.1021/acs.iecr.9b02408
Tekin, F. S., and Çulfaz-Emecen, P. Z. (2023). Controlling cellulose membrane performance via solvent choice during precursor membrane formation. ACS Appl. Polym. Mater 5, 2185–2194. doi:10.1021/acsapm.2c02185
Thakkar, H., Lawson, S., Rownaghi, A. A., and Rezaei, F. (2018). Development of 3D-printed polymer-zeolite composite monoliths for gas separation. Chem. Eng. J. 348, 109–116. doi:10.1016/j.cej.2018.04.178
Thiam, B. G., El Magri, A., Vanaei, H. R., and Vaudreuil, S. (2022). 3D printed and conventional membranes-A review. Polym. (Basel) 14, 1023. doi:10.3390/polym14051023
Tian, Z., Cao, B., and Li, P. (2018). Effects of sub-Tg cross-linking of triptycene-based polyimides on gas permeation, plasticization resistance and physical aging properties. J. Memb. Sci. 560, 87–96. doi:10.1016/j.memsci.2018.05.018
Tiseo, I. (2023) Annual carbon dioxide (CO-) emissions worldwide from 1940 to 2023. Hamburg: Statista.
Torre-Celeizabal, A., Casado-Coterillo, C., Gomis-Berenguer, A., Iniesta, J., and Garea, A. (2023). Chitosan-based mixed matrix composite membranes for CO2/CH4 mixed gas separation. Experimental characterization and performance validation. Sep. Purif. Technol. 325, 124535. doi:10.1016/j.seppur.2023.124535
Tousley, M. E., Shaffer, D. L., Lee, J.-H., Osuji, C. O., and Elimelech, M. (2016). Effect of final monomer deposition steps on molecular layer-by-layer polyamide surface properties. Langmuir 32, 10815–10823. doi:10.1021/acs.langmuir.6b02746
Ulbricht, M. (2019). “Smart polymeric membranes with magnetic nanoparticles for switchable separation,” in Smart membranes (London, United Kingdom: The Royal Society of Chemistry), 297–328. doi:10.1039/9781788016377-00297
USDOE, D. (2005). Materials for separation technologies. Energy and emission reduction opportunities. Energy Emiss. Reduct. Oppor. doi:10.2172/1218755
Vakharia, V., Salim, W., Wu, D., Han, Y., Chen, Y., Zhao, L., et al. (2018). Scale-up of amine-containing thin-film composite membranes for CO2 capture from flue gas. J. Memb. Sci. 555, 379–387. doi:10.1016/j.memsci.2018.03.074
Van Der Sluus, J. P., Hendriks, C. A., and Blok, K. (1992). Feasibility of polymer membranes for carbon dioxide recovery from flue gases. Energy Convers. Manag. 33, 429–436. doi:10.1016/0196-8904(92)90040-4
Wang, L., Cao, Y., Zhou, M., Zhou, S. J., and Yuan, Q. (2007). Novel copolyimide membranes for gas separation. J. Memb. Sci. 305, 338–346. doi:10.1016/j.memsci.2007.08.024
Wang, M., Wang, Z., Li, S., Zhang, C., Wang, J., and Wang, S. (2013). A high performance antioxidative and acid resistant membrane prepared by interfacial polymerization for CO 2 separation from flue gas. Energy Environ. Sci. 6, 539–551. doi:10.1039/c2ee23080a
Wang, X., Xiao, C., Pan, J., Hu, X., and Huan, G. (2017). Recycled performance of waste polyvinylidene fluoride hollow fiber membrane. Gaofenzi Cailiao Kexue Yu Gongcheng/Polymeric Mater. Sci. Eng. 33, 107–113. doi:10.16865/j.cnki.1000-7555.2017.04.019
Widakdo, J., Huang, T. J., Subrahmanya, T. M., Austria, H. F. M., Chou, H. L., Hung, W. S., et al. (2022). Bioinspired ionic liquid-graphene based smart membranes with electrical tunable channels for gas separation. Appl. Mater Today 27, 101441. doi:10.1016/j.apmt.2022.101441
Wind, J. D., Staudt-Bickel, C., Paul, D. R., and Koros, W. J. (2002). The effects of crosslinking chemistry on CO 2 plasticization of polyimide gas separation membranes. Ind. Eng. Chem. Res. 41, 6139–6148. doi:10.1021/ie0204639
Wojnarova, P., Rusin, J., Basinas, P., Kostejn, M., Nemec, J., Stanovský, P., et al. (2023). Unveiling the potential of composite water-swollen spiral wound membrane for design of low-cost raw biogas purification. Sep. Purif. Technol. 326, 124783. doi:10.1016/j.seppur.2023.124783
Wong, J. E., Díez-Pascual, A. M., and Richtering, W. (2009). Layer-by-Layer assembly of polyelectrolyte multilayers on thermoresponsive P(NiPAM-co -maa) microgel: effect of ionic strength and molecular weight. Macromolecules 42, 1229–1238. doi:10.1021/ma802072c
Wright, C. T., and Paul, D. R. (1997). Gas sorption and transport in UV-irradiated polyarylate copolymers based on tetramethyl bisphenol-A and dihydroxybenzophenone. J. Memb. Sci. 124, 161–174. doi:10.1016/S0376-7388(96)00215-3
Wu, B., Li, X., An, D., Zhao, S., and Wang, Y. (2014). Electro-casting aligned MWCNTs/polystyrene composite membranes for enhanced gas separation performance. J. Memb. Sci. 462, 62–68. doi:10.1016/j.memsci.2014.03.015
Wu, J., and Yuan, Q. (2002). Gas permeability of a novel cellulose membrane. J. Memb. Sci. 204, 185–194. doi:10.1016/S0376-7388(02)00037-6
Xiao, S., Feng, X., and Huang, R. Y. M. (2007). Trimesoyl chloride crosslinked chitosan membranes for CO2/N2 separation and pervaporation dehydration of isopropanol. J. Memb. Sci. 306, 36–46. doi:10.1016/j.memsci.2007.08.021
Xiao, Y., Low, B. T., Hosseini, S. S., Chung, T. S., and Paul, D. R. (2009). The strategies of molecular architecture and modification of polyimide-based membranes for CO2 removal from natural gas—a review. Prog. Polym. Sci. 34, 561–580. doi:10.1016/j.progpolymsci.2008.12.004
Xu, D., and Wang, K. (2008). Chitosan membrane in separation applications. Mater. Sci. Technol. 24, 1076–1087. doi:10.1179/174328408X341762
Xu, S., Ren, X., Zhao, N., Wu, L., Zhang, Z., Fan, Y., et al. (2021a). Self-crosslinking of bromomethylated 6FDA-DAM polyimide for gas separations. J. Memb. Sci. 636, 119534. doi:10.1016/j.memsci.2021.119534
Xu, S., Zhou, H., Jia, H., Xu, J., Liu, D., Zhang, M., et al. (2021b). Preparation and high CO2/CH4 selectivity of ZSM-5/Ethyl cellulose mixed matrix membranes. Mater Res. Express 8, 026403. doi:10.1088/2053-1591/abe321
Xu, X., Wang, J., Zhou, A., Dong, S., Shi, K., Li, B., et al. (2021c). High-efficiency CO2 separation using hybrid LDH-polymer membranes. Nat. Commun. 12, 3069. doi:10.1038/s41467-021-23121-z
Xu, Y., Chen, C., Zhang, P., Sun, B., and Li, J. (2006). Pervaporation properties of polyimide membranes for separation of ethanol + water mixtures. J. Chem. Eng. Data 51, 1841–1845. doi:10.1021/je060208l
Yamasaki, A., Tyagi, R. K., Fouda, A. E., Matsuura, T., and Jonasson, K. (1999). Effect of solvent evaporation conditions on gas separation performance for asymmetric polysulfone membranes. J. Appl. Polym. Sci. 71, 1367–1374. doi:10.1002/(SICI)1097-4628(19990228)71:9<1367::AID-APP2>3.0.CO;2-H
Yan, N., Capezzuto, F., Lavorgna, M., Buonocore, G. G., Tescione, F., Xia, H., et al. (2016). Borate cross-linked graphene oxide–chitosan as robust and high gas barrier films. Nanoscale 8, 10783–10791. doi:10.1039/C6NR00377J
Yang, H.-C., Hou, J., Chen, V., and Xu, Z.-K. (2016). Surface and interface engineering for organic–inorganic composite membranes. J. Mater Chem. A Mater 4, 9716–9729. doi:10.1039/C6TA02844F
Yang, J., Tao, L., He, J., McCutcheon, J. R., and Li, Y. (2022). Machine learning enables interpretable discovery of innovative polymers for gas separation membranes. Sci. Adv. 8, eabn9545. doi:10.1126/sciadv.abn9545
Yang, T., Wan, C. F., Zhang, J., Gudipati, C., and Chung, T.-S. (2021). Optimization of interfacial polymerization to fabricate thin-film composite hollow fiber membranes in modules for brackish water reverse osmosis. J. Memb. Sci. 626, 119187. doi:10.1016/j.memsci.2021.119187
Yerzhankyzy, A., Wang, Y., Ghanem, B. S., Puspasari, T., and Pinnau, I. (2022). Gas separation performance of solid-state in-situ thermally crosslinked 6FDA-based polyimides. J. Memb. Sci. 641, 119885. doi:10.1016/j.memsci.2021.119885
Yoo, M. J., Kim, K. H., Lee, J. H., Kim, T. W., Chung, C. W., Cho, Y. H., et al. (2018). Ultrathin gutter layer for high-performance thin-film composite membranes for CO2 separation. J. Memb. Sci. 566, 336–345. doi:10.1016/j.memsci.2018.09.017
Žák, M., Bendová, H., Friess, K., Bara, J. E., and Izák, P. (2018). Single-step purification of raw biogas to biomethane quality by hollow fiber membranes without any pretreatment – an innovation in biogas upgrading. Sep. Purif. Technol. 203, 36–40. doi:10.1016/j.seppur.2018.04.024
Zarca, G., Urtiaga, A., Biegler, L. T., and Ortiz, I. (2018). An optimization model for assessment of membrane-based post-combustion gas upcycling into hydrogen or syngas. J. Memb. Sci. 563, 83–92. doi:10.1016/j.memsci.2018.05.038
Zargar, V., Asghari, M., and Afsari, M. (2019). Gas separation properties of swelled nanocomposite chitosan membranes cross-linked by 3-aminopropyltriethoxysilane. Int. J. Environ. Sci. Technol. 16, 37–46. doi:10.1007/s13762-017-1554-1
Zargar, V., Asghari, M., and Dashti, A. (2015). A review on chitin and chitosan polymers: structure, chemistry, solubility, derivatives, and applications. ChemBioEng Rev. 2, 204–226. doi:10.1002/cben.201400025
Zhang, S., Shen, L., Deng, H., Liu, Q., You, X., Yuan, J., et al. (2022). Ultrathin membranes for separations: a new era driven by advanced nanotechnology. Adv. Mater. 34, 2108457. doi:10.1002/adma.202108457
Zhang, Y., Xin, J., Huo, G., Zhang, Z., Zhou, X., Bi, J., et al. (2023). Cross-linked PI membranes with simultaneously improved CO2 permeability and plasticization resistance via tunning polymer precursor orientation degree. J. Memb. Sci. 687, 121994. doi:10.1016/j.memsci.2023.121994
Zhang, Y., Zhang, Y., Wang, X., Yu, J., and Ding, B. (2018). Ultrahigh metal–organic framework loading and flexible nanofibrous membranes for efficient CO 2 capture with long-term, ultrastable recyclability. ACS Appl. Mater Interfaces 10, 34802–34810. doi:10.1021/acsami.8b14197
Zhao, S., Caruso, F., Dähne, L., Decher, G., De Geest, B. G., Fan, J., et al. (2019). The future of layer-by-layer assembly: a tribute to acs nano associate editor helmuth möhwald. ACS Nano 13, 6151–6169. doi:10.1021/acsnano.9b03326
Zhu, B., Jiang, X., He, S., Yang, X., Long, J., Zhang, Y., et al. (2020). Rational design of poly(ethylene oxide) based membranes for sustainable CO 2 capture. J. Mater Chem. A Mater 8, 24233–24252. doi:10.1039/D0TA08806D
Keywords: membrane manufacturing, sustainability, polymeric membranes, gas separation membranes, recyclability
Citation: Alkandari SH and Castro-Dominguez B (2024) Advanced and sustainable manufacturing methods of polymer-based membranes for gas separation: a review. Front. Membr. Sci. Technol. 3:1390599. doi: 10.3389/frmst.2024.1390599
Received: 23 February 2024; Accepted: 16 April 2024;
Published: 09 May 2024.
Edited by:
Johannes Carolus (John) Jansen, Istituto per la Tecnologia delle Membrane, Consiglio Nazionale delle Ricerche, ItalyReviewed by:
Maria Giovanna Buonomenna, Ordine dei Chimici e Fisici della Campania and MIUR, ItalyCopyright © 2024 Alkandari and Castro-Dominguez. This is an open-access article distributed under the terms of the Creative Commons Attribution License (CC BY). The use, distribution or reproduction in other forums is permitted, provided the original author(s) and the copyright owner(s) are credited and that the original publication in this journal is cited, in accordance with accepted academic practice. No use, distribution or reproduction is permitted which does not comply with these terms.
*Correspondence: Bernardo Castro-Dominguez, YmNkMjhAYmF0aC5hYy51aw==
Disclaimer: All claims expressed in this article are solely those of the authors and do not necessarily represent those of their affiliated organizations, or those of the publisher, the editors and the reviewers. Any product that may be evaluated in this article or claim that may be made by its manufacturer is not guaranteed or endorsed by the publisher.
Research integrity at Frontiers
Learn more about the work of our research integrity team to safeguard the quality of each article we publish.