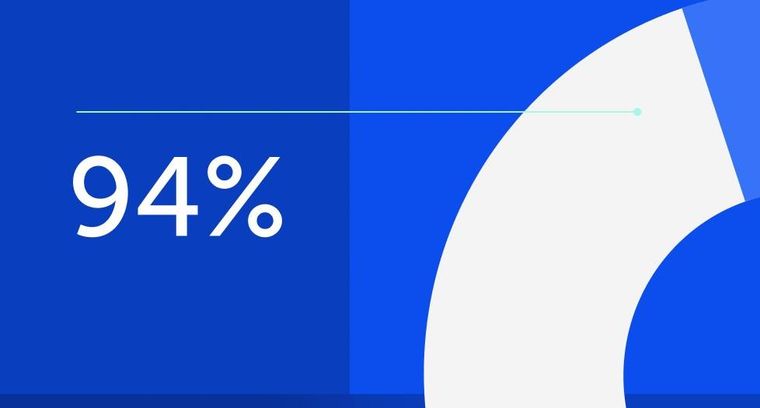
94% of researchers rate our articles as excellent or good
Learn more about the work of our research integrity team to safeguard the quality of each article we publish.
Find out more
SPECIALTY GRAND CHALLENGE article
Front. Membr. Sci. Technol., 16 March 2023
Sec. Membrane Applications - Liquid
Volume 2 - 2023 | https://doi.org/10.3389/frmst.2023.1177528
Membranes have been intensively used in various liquid separation processes including aqueous media and organic solvents because of their small footprint, energy savings, scalability, and simplicity. With the advance of membrane technology, it has emerged as a major field of research, having many practical applications such as wastewater treatment, desalination, hemodialysis, food and beverage processing, biofuel production, pharmaceutical manufacturing, and petrochemical separation. Over the past two decades, the development and commercialization of membrane technologies has revolutionized the way water is treated, enabling higher water quality and lower costs. Taking desalination as a typical example, reverse osmosis (RO) has advanced as the first practical membrane technology from the lab in the 1960’s to current industrial plants, and recently has essentially become a dominant desalination technique to replace thermal desalination (distillation) (Liu et al., 2021b; Guo et al., 2022). Now, more than 95 million m3/day of freshwater is produced from seawater by RO (Eke et al., 2020). Learning from the rapid growth and massive applications of membrane-based processes in aqueous media, similar potential is expected for the membrane-based processes to replace phase-changing thermal technology (distillation or evaporation) for chemical separations and to revolutionize the technology organic solvents are separated and purified. In the last few years, increasing attention has been paid to develop robust membranes and processes for chemical separations in organic solvents (Liang et al., 2019).
Pressure-driven membrane processes are the most used processes where hydrostatic pressure is applied to drive a feed stream to permeate through a membrane for separation. There are four main pressure-driven membrane processes including microfiltration (MF), ultrafiltration (UF), nanofiltration (NF), and reverse osmosis (RO), in which their separation mechanism is mainly governed by size exclusion. Donnan effect (electrostatic interactions) may also play a significant role for a precise separation in NF and RO depending on the physiochemical properties of solutes and membrane surfaces. Non-pressure-driven membrane processes, such as pervaporation (PV), membrane distillation (MD), forward osmosis (FO), dialysis, electro-membrane processes including electro-dialysis (ED), electro-deionization (EDI) and reverse electrodialysis (RED), and a few others, offer significant advantages for efficient separation including mild operating conditions (atmospheric pressure) and on-line separation potential while synthesis of products. Hybrid membrane processes combined with other separation technologies or processes yields feasible and efficient approaches to save energy and protect the environment; one typical example is the membrane bioreactor (MBR), which has expanded rapidly around the world.
With the growing demands of new products and the increasingly stringent environmental regulations, tremendous amounts of liquids including aqueous and organic solutions need be processed economically and in more eco-friendly ways. Huge potential and enormous markets are expected for membrane technology to expand in liquid processing. However, several grand challenges need to be addressed to further motivate the rapid expansion of membrane applications in liquid.
Membrane technology has achieved technical maturity with proven performance, reliability, scalability, and cost-effectiveness for most aqueous separations. As the membrane technology continues to evolve and improve, it is even becoming increasingly important in a wide range of industrial and environmental applications. However, membrane fouling is a significant challenge which limits the wide expansion of membrane applications in aqueous separation, especially for complex aqueous solutions (Zhang et al., 2016). The presence of complex components in aqueous solutions can exacerbate the membrane fouling problem, which leads to reduced permeate flux and decreased separation efficiency of the membrane system. This reduced performance may require more frequent cleaning and maintenance of the membrane system, which can lead to increased operating costs. Taking MBR technology as an example, the specific membrane flux in 19 large-scale MBR plants in China is in the range of 0.5–1.5 LMH/kPa when used for wastewater treatment, which is dramatically lower than the expected specific flux of MF and UF membranes in the range of 3.6–360 LMH/kPa in the absence of fouling (Xiao et al., 2019). Thus, the problem of membrane fouling results in far more membrane area being needed for practical applications of MBR. Moreover, a recent study highlights that the directly attributable cost of fouling in RO plants could be as high as 24% of the operating expenses in the case of surface water treatment in the Netherlands (Jafari et al., 2021). Additionally, if the membrane fouling is not managed properly, it can lead to a deterioration in the quality of the permeate solution, and even system failure. Replacement of RO membranes expends about 13% of the total cost for seawater desalination (Anis et al., 2019).
Therefore, mitigating membrane fouling is critical for the continued growth and expansion of membrane applications in aqueous systems. A variety of strategies have been designed and employed to reduce the fouling potential of the feed solution and improve the overall performance and lifespan of the membrane system. For example, pretreatment of feed solutions, optimization of operating conditions, development of new membrane materials and structures with fouling-resistant properties, selection of appropriate cleaning procedures, and even a combination of these strategies have been often used to achieve the best possible fouling mitigation.
Despite these measures, it is still very difficult to completely avoid membrane fouling, especially in complex or challenging applications. Understanding the mechanisms and characteristics of membrane fouling is essential for developing effective mitigation strategies. Accurate identification and discrimination of foulant compositions at the molecular level is critical for understanding the fundamental mechanisms of membrane fouling. Although molecular spectroscopic techniques are powerful tools for characterizing membrane fouling, the development of non-invasive and online monitoring techniques is the future direction for characterization (Chen et al., 2018). This is because such techniques can provide real-time fouling information, thereby enabling early detection and timely intervention to prevent fouling before it becomes significant. Moreover, accurate prediction of membrane fouling behavior is important to illustrate the fouling mechanisms and thus develop effective strategies to mitigate fouling. Artificial intelligence (AI) algorithms are promising but need further optimization for a more accurate prediction of membrane fouling (Niu et al., 2022).
The development of antifouling membranes is a fundamental approach to mitigate fouling in membrane processes (Zhang et al., 2016). Both surface modification and material design are two major strategies for the fabrication of antifouling membranes via tailoring the membrane surface properties, such as surface hydrophilicity, surface charge, and surface roughness (Zhang et al., 2016). Surface modification can be achieved through coating, grafting, or crosslinking of antifouling agents onto the membrane surface. Surface modification is becoming increasingly popular in practical applications due to its ease of synthesis, cost-effectiveness, and ability to tailor the antifouling properties of membranes to specific separation applications. However, careful-designed chemistry needs to be selected for ensuring the stability and durability of the antifouling agents modified on the membrane surface and overcoming the trade-off between antifouling and separation performance of membranes. Material design involves the synthesis of new materials for fabrication of antifouling membranes or incorporation of antifouling agents into the membrane matrix to create fouling-resistant membranes. Blending antifouling agents with membrane materials is a simple and commonly used method to fabricate antifouling membranes in the industry. However, the effectiveness of this approach may be limited by the concentration and distribution of the antifouling agents in the membrane matrix and may suffer from leaking during long-term use. Block copolymers are emerging membrane materials that offer several advantages for achieving improved separation performance and durable antifouling properties because they can be designed to possess specific antifouling properties and form uniform pores. Moreover, the cost-effectiveness of the antifouling membranes should be considered to ensure their practical applications.
Development of advanced pretreatment techniques has become a more sought-after approach for membrane fouling mitigation, through maximally removing potential foulants in the feed water and improving the quality of feed water for the membrane system. Coupled with applied electric (Yin et al., 2020; Du et al., 2021) and ultrasonic fields (Hou et al., 2017; Qasim et al., 2018) in membrane systems, fouling can be controlled. Cleaning techniques such as air purging, backwashing, and chemical cleaning have demonstrated powerful efficiency to remove foulants and recover membrane performance. Combining these aforementioned strategies may be an advantageous methodology to achieve the best fouling control.
Precise molecule/ion separations are becoming increasingly necessary to separate and purify high-value products, recover nutrients, and valuable elements and metals from different water resources, and remove contaminants with potential health risks from drinking water (DuChanois et al., 2021; Lu and Wang, 2021; Zhao et al., 2021). Conventional membrane processes such as UF and NF can effectively separate molecules exploiting their size differences to an order of magnitude or more, but cannot achieve more precise separations where the size differences between molecules are small to similar. In recent years, precise ion-ion separations have gained increased importance due to the growing demand for scale-forming ion removal (e.g., Ca2+, Mg2+, and SO42−) and valuable metals extraction (e.g., lithium, silver, gold, and nickel) (Zhao et al., 2021). These require the separation of multivalent ions from monovalent ions, and even the separation of ions having the same valence.
For example, the extraction of lithium from salt lakes has attracted substantial interest because of the extensive use of lithium-ion batteries and its relatively low cost compared with lithium extraction from rocks. The global consumption of lithium was around 93,000 tons in 2021 and is estimated to reach about 95,000 tons by 2025 (Zhang et al., 2023). Membrane technology has been recognized as a promising technique for lithium extraction because of the comprehensive economic, environmental, and social benefits. However, the current commercial NF membrane systems have only achieved a very limited selectivity of Li+/Mg2+ towards separation of ion mixtures (Mg2+, Ca2+, Na+, and K+) with very high content of Mg2+ in salt-lake brines and cannot meet the practical needs of economic lithium extraction (Zhao et al., 2021). Separation of Li+/Na+ and Li+/K+ is even more challenging since they have the same valence and similar sizes, and no investigation has been reported for such separations using commercial membranes.
Therefore, the big challenge of membrane applications in precise separations lies in developing “fit-for-purpose” membranes with high selectivity at the molecular and ion levels. This is because current commercial membranes are not specifically designed for such emerging molecular/ion separations. To meet these critically emerging needs, “fit-for-purpose” membranes should be designed to achieve solute-solute selectivity, and selectively remove target solutes effectively while maintaining a high content of each desired solute in the permeate.
Several approaches have been performed to develop such selective membranes with fine-tuning properties. For example, numerous loose NF membranes have been fabricated by phase-inversion for the precise separation of small molecules (e.g., dyes, antibiotics, sugars) and salts (e.g., monovalent salts, divalent salts) via synthesizing new polymer derivatives (Zhou et al., 2019; Liu et al., 2021c), blending nanomaterials with polymers (Li et al., 2019; Zhang et al., 2021), or tailoring membrane surface charge (Tian et al., 2022; Wang et al., 2023). Ion selective NF membranes have also been developed by tailoring the interfacial polymerization process (Pan et al., 2017; Gong et al., 2019; Liang et al., 2020) or modifying the membrane surface to finely tailor the pore size and surface charge of thin-film composite polyamide membranes (Cheng et al., 2018). These strategies are developed mainly based on the well-established membrane manufacturing techniques such as phase inversion and interfacial polymerization and have a promising potential of scalable fabrication and commercialization. However, the ion selectivity enhancement of these membranes is limited owing to their broad pore size distributions associated with the inability of these manufacturing techniques to finely tailor pore size in the angstrom-scale. Very recently, well-defined nano-channel membranes made from various 2D nanosheets (Wang et al., 2020) (e.g., graphene oxide, transition metal dichalcogenides, Mxenes) and porous framework membranes (Dou et al., 2021; Lu and Wang, 2021) made from metal-organic frameworks (MOFs) and covalent-organic frameworks (COFs), achieved well-defined pores with high porosity and tunable pore chemistries, which dramatically enhance the membrane ion selectivity and water permeance. It is still challenging to manufacture these intricate membranes at a large scale for practical implementation, because of the high cost of these materials and the complicated fabrication routes.
The future direction of advancing membrane applications in precise molecule/ion separation is to develop scalable and durable “fit-for-purpose” membranes targeted for a particular separation scenario. Molecular-level understanding of solute and ion transport behaviors through nanoscale pores is necessary to intuitively guide the design of highly selective membranes. Molecular-level design of membrane materials, with the assistance of simulation and modeling, will make breakthroughs possible. The fast-growing technology of Materials Genome Initiative (MGI) (Boyd et al., 2017; Boyd et al., 2019) and machine learning (Zhong et al., 2020) will revolutionize the design and fabrication of membrane materials and make it more efficient and reliable. Optimization of membrane processes and hybrid combination of membrane processes with other separation technologies are necessary to achieve target separation, even when selective membranes are not available for a particular separation. Therefore, the significant advancement of membrane applications in precise separation calls for interdisciplinary collaboration across materials science, chemistry, nanotechnology, and engineering.
Growing freshwater scarcity, global environmental concerns and stringent environmental regulations necessitate the development of zero liquid discharge (ZLD) processes to maximally recover water for reuse from industrial and municipal wastewaters. Particularly in the high-polluting industries such as power, coal-to-chemicals, textile, oil, mining, and others, high volumes of wastewater are produced and must be managed for water reuse. The global market of ZLD is growing rapidly around the world (Tong and Elimelech, 2016).
To reduce energy expenditure of early ZLD systems primarily depending on thermal processes, membrane-based technology such as RO has been adopted to pre-concentrate wastewater and reduce the volume of wastewater required for thermal treatment. It was reported that 58%–75% of energy had been saved when incorporating a secondary RO system to treat RO desalination brines compared to using a stand-alone thermal system (Bond and Veerapaneni, 2008). However, membrane fouling/scaling becomes a severe challenge for the efficient operation of RO in ZLD since the components in the feed water from industrial wastewater are complex and difficult to be removed substantially through pre-treatments (Tong and Elimelech, 2016). The life-time of RO membranes has been shorted significantly when used in ZLD. Another big challenge is that RO has a limited salinity and pressure tolerance (Greenlee et al., 2009; Tong and Elimelech, 2016) since an extremely high hydraulic pressure is required to drive water permeate through the RO membrane to overcome the large osmotic pressure of feed water with hyper-salinity. Ultra-high-pressure RO (UHPRO) emerges to advance RO operation at above ∼100 bar (Davenport et al., 2020; Low and Wang, 2021). Hypersaline feed water can be further concentrated through UHPRO with about a 3-fold energy saving compared to thermal distillation (Davenport et al., 2018). However, long-term stable operation of UHPRO requires compaction-resistant and fouling-resistant membranes and also sophisticated module design to withstand such a high pressure and to mitigate intensified fouling. The water and ion transport mechanisms in UHPRO have yet to be explored but are critical to addressing potential problems associated with the high-pressure operation (Low and Wang, 2021). Membrane development and practical applications of UHPRO are still in their infancy and need intensive research to be well-developed for ZLD.
Other salt-concentrating membrane technologies, such as forward osmosis (FO), membrane distillation (MD) and electro-dialysis (ED), have also been developed as alternative ZLD approaches to replace thermal-based brine concentrators and further concentrate the wastewater following the RO stage. The big advantage of these three membrane-based processes is their capability to treat hypersaline feed waters that cannot be concentrated by RO, but with significantly more energy costs incurred than RO (Tong and Elimelech, 2016). These technologies have not been well-established for practical applications in ZLD. Comprehensive evaluations of their energy consumption and operating costs are highly needed to have a close comparison with thermal-based brine concentrators. Their large-scale performance and long-term viability also need to be examined in practical applications.
The future direction of membrane applications in ZLD is to develop energy-saving and long-term stable membrane processes. RO holds great advantages in ZLD because of its competitive energy efficiency. Upgrading both the pressure-tolerance range and fouling-resistance performance of RO enables it to further concentrate hypersaline wastewater and save the vast energy required for brine concentrators in ZLD. Other salt-concentrating membrane technologies beyond RO are also desirable, but the big challenges for them to be applied in ZLD are to develop high-performance membranes and design efficient systems for the long-term durable operation in wastewater concentration.
Separation processes account for around 40%–70% of both capital and operating costs in numerous industries (Marchetti et al., 2014) and consume 10%–15% of the global total energy (Sholl and Lively, 2016). Thousands of drugs and chemicals in everyday use are produced mainly through organic syntheses, which are frequently performed in organic solvents and need intensive separations of target products from organic solvents. Moreover, organic solvents involved in chemical syntheses need be recovered or treated for economic and environmental considerations. Oil refineries daily process around 160,000 m3 crude oil worldwide (Lively and Sholl, 2017). The volumes of organic liquids required for separation globally are comparable to the scale of seawater treated for worldwide desalination (Lively and Sholl, 2017). These organic liquid separations are mainly performed through energy-intensive thermal processes including distillation, evaporation, extraction, and others.
Membrane technology has demonstrated, as an alternative to thermal separation processes, competitive advantages of saving energy and space with small footprint in separating organic liquids. Membrane applications in organic liquids mainly involve solute–solvent separation and solvent–solvent separation (Liang et al., 2019). Solute–solvent separation is generally used for concentration, solvent exchange, and purification. Organic solvent MF, UF, and NF membranes are often employed for solute‒solvent separation, where the molecular size of solutes is usually one order of magnitude larger than the size of solvents. Solvent–solvent separation is often used for solvent purification. For example, separation of polar/non-polar solvent mixture, aromatic/alkane solvent mixture, isomer solvent mixture, and organic liquid/water mixture are highly desirable, but critically challenging, because of their marginal differences in size. Organic solvent reverse osmosis (OSRO) membranes with MWCO below 200 Da emerge to separate organic solvents (Liu et al., 2021a). Additionally, organic solvent forward osmosis (OSFO) and pervaporation (PV) are capable of both solute–solvent separation and solvent–solvent separation (Liang et al., 2019) and have their particular advantages in the challenging separations where organic solvent nanofiltration (OSN) and OSRO are not applicable.
However, membrane applications in organic liquid separations fall far behind those in aqueous separations because robust and durable membrane systems are currently very limited, to persistently survive in an organic solvent environment (Lively and Sholl, 2017). The grand challenges of membrane applications for solute–solvent separation and solvent–solvent separation are discussed as follows.
During the last two decades, OSN has presented remarkable progress and demonstrated highly efficient solute–solvent separation. OSN membranes generally have a MWCO in the range of 200–1,000 Da and can concentrate high-value chemicals from organic solutions (solute enrichment), recover organic solvents by removing the undesired solutes (solvent recovery) or separate two or more chemicals in an organic solution (purification). The biggest industrial success of OSN so far is to recover dewaxing solvents from lube oil at ExxonMobil Corporation, where around 11,500 m3 of lubrication oil was processed a day in 1998 (Gould et al., 2001). A more recent industrial application of OSN is to concentrate a temperature-sensitive API (active pharmaceutical ingredient) at Evonik-MET Ltd. (Priske et al., 2016). OSN has been operated successfully in the pharmaceutical manufacturing and chemicals processing. Moreover, OSN has major potential applications for recovery of oil, concentration of aromatics, and recycling of homogeneous catalyst (Marchetti et al., 2014).
However, there are several challenges for OSN to achieve its full potential. One of the most important challenges is the lack of highly selective OSN membranes and the resultant incomplete separation at the expense of high product losses (Kim et al., 2014). Although many OSN membranes are commercially available, most of them are polymeric membranes with integrally skinned asymmetric (ISA) structure made by the phase inversion process (Marchetti et al., 2014). Limited by available polymers and membrane fabrication techniques, the selective layer of ISA membranes cannot be finely tailored at the nanometer scale, resulting in the marginal enhancement of separation properties of ISA membranes over the decades. Learning from the development of commercial thin-film composite (TFC) membranes for desalination, TFC OSN membranes have the great potential to become the next-generation commercial OSN membranes because of improved permeability and selectivity via finely tailoring the nanoscale selective layers. The solvent permeance of TFC OSN membranes has been greatly enhanced through fabricating sub-10 nm selective layer membranes (Karan et al., 2015) or by introducing microporosity by using polymers and monomers with intrinsic micro-voids (Jimenez-Solomon et al., 2016). The separation performance of TFC OSN membranes has been significantly improved by creating well-defined pores and channels or tailoring physicochemical properties of membranes. Mixed-matrix membranes (MMMs) are a promising approach towards enhanced permeability and selectivity via creating porosity and entropic selectivity through the addition of structure-design nanomaterials, such as zeolites, silicalite, COFs, MOFs, POCs, and others, into ISA or TFC membranes. In the future, selecting the most promising membrane materials, developing new membrane formation methodologies, and scale up of manufacturing will enable the industrial adoption of OSN for precise and efficient separations in organic solvents.
Another challenge is the lack of intensive study on the process engineering aspect of OSN. In certain cases (Marchetti et al., 2014), it would be extremely challenging or even impossible to achieve a desired separation with one membrane stage, because of physicochemical factors. A multistage OSN process (known as a membrane cascade) or combination of OSN with other processes may provide a feasible approach to achieve a target separation. Different configurations of membrane cascades have been investigated and implemented for aqueous separations, while there is little published work investigating the process optimization of OSN and the implementation of cascades. Thus, it is critically important to adapt the process engineering of membrane systems for aqueous separations to fit for organic liquid separations, thus promoting the OSN applications at the industrial level.
Moreover, identification of the most demanding separation challenges becomes an urgent need in the OSN field (Lively and Sholl, 2017). Some potential targets can be selected for evaluating the separation performance of OSN membranes and processes. For example, specific OSN applications can be considered, including concentration and purification of API in pharmaceutical manufacturing, hydrocarbon fractionation in oil refineries, and solvent recovery in pigment production. Lastly, modeling of fundamental solute and solvent transport on a membrane level and a process level is necessary to efficiently develop high-performance membranes, select the best membrane, and optimize the membrane process for a practical application.
In 1970, Sourirajan pioneered and demonstrated the concept of OSRO for solvent–solvent separation with the ISA cellulose acetate (CA) membranes for alcohol separation from cyclic hydrocarbons and alkyl aromatics (Gantzel and Merten, 1970). OSRO requires pore sizes below 1 nm for solvent separations based on subtle differences (less than 0.1–0.3 nm) in kinetic diameters (Liu et al., 2021a). Solvent transport primarily follows the solution‒diffusion transport model and is mainly driven by a chemical potential. OSRO membranes are critically sensitive to defects and lose selectivity even with minor imperfections, which has resulted in its slow developmental progress compared with the burgeoning growth of OSN membranes reported in literature (Liu et al., 2021a). Although the practical application of OSRO on an industrial scale has not yet been attempted, mainly due to the commercial unavailability, OSRO membrane processes have advantages in energy and cost savings for the separation of organic solvent mixtures compared with thermal distillation and PV (Liu et al., 2021a).
The big challenge of OSRO for practical applications is to develop high-performance membranes at a large scale. A few of OSRO membranes have been synthesized at the laboratory scale and evaluated for various solvent separations. For example, very recently, TFC OSRO membranes made from N-aryl-linked spirocyclic polymers (Thompson et al., 2020) and hydrophobic polyamide (Li et al., 2022) were developed to fractionate light crude oil with high solvent permeance and selectivity. Torlon® hollow fiber OSRO membranes were fabricated using durable polyamide-imide and could separate aromatic molecules with a low molecular weight of 185 g/mol from solvents having a similar size (Jang et al., 2019). Excitingly, these Torlon® OSRO membranes have much potential to be scaled-up because they are not only mechanically, thermally, chemically robust, but are fabricated through the scalable spinning process. Carbon molecular sieves (CMS) made by pyrolysis of polymeric precursors were reported to achieve excellent separation of para- and ortho-xylene isomers based on “entropic selectivity” (Koh et al., 2016). The bis(triethoxysilyl)acetylene (denoted as BTESA)-derived organosilica OSRO membranes enabled separation of organic/organic azeotropes, such as methanol/methyl acetate (MA), methanol/toluene, methanol/dimethyl carbonate (DMC), and methanol/methyl tert-butyl ether (MTBE), through the molecular-sieving mechanism (Dong et al., 2020).
OSRO is just in its early beginning stage and is mainly investigated at the laboratory scale. There is still a long way to go for the adoption of industrial OSRO in organic solvent separation applications. Development of highly robust and durable OSRO membranes with defect-free structures is a necessity for this. With the advance of OSRO membranes, the solvent transport mechanism needs be explored to better guide the membrane design for the target separation systems of organic solvent mixtures, such as polar/non-polar, aromatic/alkane, isomer, and organic liquid/water mixtures. Then, process engineering needs to play a crucial role to scale-up the manufacturing of OSRO membranes and design robust and efficient modules, and optimize the OSRO process through combination with other separation technologies for real applications.
Pervaporation (PV) has been developed as a molecular separation membrane technology for organic liquid mixture separation in petrochemical, food, bioenergy, and other industrial fields (Smitha et al., 2004; Ong et al., 2016; Liu and Jin, 2021). PV can separate organic‒water mixtures and organic‒organic mixtures, primarily including dehydration of organics, recovery of organics from water and separation of organic‒organic mixtures (Smitha et al., 2004). So far, the major industrial application of PV is organic dehydration, where the polymeric (polyvinyl alcohol, PVA) and inorganic (NaA zeolite) PV membranes have been commercialized for practical applications (Liu and Jin, 2021). However, there are much fewer examples of PV applications for the recovery of organics and organic‒organic separations, because of the limited availability of membranes capable of surviving the harsh conditions of diverse organic solvents.
PV is thermally driven by the vapor pressure difference across the membrane, and mass transport across the PV membrane follows solution‒diffusion mechanism. The separation performance of PV is determined by thermodynamic partitioning (sorption coefficients) and kinetic mobility (diffusion coefficients) (Koros and Zhang, 2017). Affinity and size sieving property are two key factors of PV separation to select favorable membrane materials for given mixtures (Liu and Jin, 2021). The permeability and selectivity of PV membrane can be tailored via engineering their affinity (chemical property) and pore size, similar to NF and RO membranes. Generally, hydrophilic PV membranes allow for selective water permeation from solvent‒water mixtures (solvent dehydration), while hydrophobic PV membranes allow for selective solvent permeation from solvent‒water mixtures (solvent recovery). The size sieving effect of PV membranes is beneficial for the diffusion selectivity of different sized organics.
The big challenge of PV is to develop chemically and thermally stable PV membranes for challenging organic‒organic separations, since PV needs be operated at an elevated temperature in organic solvents (Liu and Jin, 2021). Though most polymeric PV membranes suffer from severe swelling in pure organic solutions, some polymers such as polyimides, with rigid chains, are highly scalable and more stable towards aggressive solvents and harsh operating conditions, and have been developed as PV membranes for aromatic/aliphatic (such as toluene/iso-octane mixtures) separation (Xu et al., 2016). The PI selective layer needs be further optimized to improve the permeation flux. Zeolite membranes have demonstrated higher separation performance and stability than polymeric membranes because of their regular and rigid zeolitic pores with tailorable pore size and affinity, but face critical challenges to be industrially manufactured with defect-free structure via hydrothermal synthesis (Liu and Jin, 2021). Hydrophobic zeolite MFI membranes achieved record high ethanol/water selectivity and excellent xylene isomers separation, and their separation performance can be further improved by oriented growth and nanosheet seeding (Pham et al., 2013). Recently, some PV membranes are made of emerging 2D-materials, MOFs, and COFs, as well as mixed-matrix membranes (MMMs), and present promising separation properties for organic liquid mixtures (Liu and Jin, 2021), but they are still in their early developmental stages and must be further optimized for long-term practical applications.
PV requires no hydraulic pressure but uses thermal energy for organic liquid separations and costs much more energy than OSRO. The future research direction in PV is to develop competitive and durable membranes and to find profitable organic liquid mixture separations for practical applications of PV. Combining PV with other separation processes may provide more efficient and economic approaches for organic liquid separations.
Advances in membrane science and engineering during the past few decades have driven the significant progress of membrane applications in liquid separations. Membrane technology has demonstrated great success and societal benefits in aqueous separations such as desalination, wastewater reuse, drinking water purification, resource recovery and others, while it is still in its infancy in organic liquid separation. Learning from the progress of membrane technology in aqueous separation, there exists great potential and tremendous opportunities for the development of organic solvent membrane technology.
The future burgeoning growth of membrane technology in liquid separation highly depends on the scalable fabrication of durable and selective membranes with “fit-for-purpose” properties, and the design and operation of efficient membrane processes with stable separation performance. The development of economical and sustainable membrane systems requires efficient fouling management from the comprehensive approaches, including targeted membrane surface tailoring, effective pretreatments, and on-demand cleaning in a particular liquid separation case.
With the continuous advance of membrane technology, new applications are emerging and provide exciting opportunities to further motivate the sustainable development of human society. The goal of the journal Frontiers in Membrane Science and Technology in the section of Membrane Applications—Liquid is to report high-quality original research and review papers in this specific area by committing to share and motivate the progress of membrane applications involving liquids. Meeting these Grand Challenges and those in other areas of membrane development (Guiver, 2022) will realize multiple benefits towards sustainability.
This article was written by YH.
The author gratefully acknowledges financial support from National Natural Science Foundation of China (No. 21978215) and Cangzhou Institute of Tiangong University (No. TGCYY-F-0101).
The author acknowledges Professor Michael D. Guiver for his edition and valuable suggestions to improve this article. The author thanks Mr. Zhaoqian Zhang for his help to format the references.
The author declares that the research was conducted in the absence of any commercial or financial relationships that could be construed as a potential conflict of interest.
The handling editor MG declares collaboration with author YH.
All claims expressed in this article are solely those of the authors and do not necessarily represent those of their affiliated organizations, or those of the publisher, the editors and the reviewers. Any product that may be evaluated in this article, or claim that may be made by its manufacturer, is not guaranteed or endorsed by the publisher.
Anis, S. F., Hashaikeh, R., and Hilal, N. (2019). Reverse osmosis pretreatment technologies and future trends: A comprehensive review. Desalination 452, 159–195. doi:10.1016/j.desal.2018.11.006
Bond, R., and Veerapaneni, S. (2008). Zeroing in on ZLD technologies for inland desalination. J. AWWA 100 (9), 76–89. doi:10.1002/j.1551-8833.2008.tb09722.x
Boyd, P. G., Chidambaram, A., García-Díez, E., Ireland, C. P., Daff, T. D., Bounds, R., et al. (2019). Data-driven design of metal–organic frameworks for wet flue gas CO2 capture. Nature 576 (7786), 253–256. doi:10.1038/s41586-019-1798-7
Boyd, P. G., Lee, Y., and Smit, B. (2017). Computational development of the nanoporous materials genome. Nat. Rev. Mater. 2 (8), 17037. doi:10.1038/natrevmats.2017.37
Chen, W., Qian, C., Zhou, K.-G., and Yu, H.-Q. (2018). Molecular spectroscopic characterization of membrane fouling: A critical review. Chem 4 (7), 1492–1509. doi:10.1016/j.chempr.2018.03.011
Cheng, W., Liu, C., Tong, T., Epsztein, R., Sun, M., Verduzco, R., et al. (2018). Selective removal of divalent cations by polyelectrolyte multilayer nanofiltration membrane: Role of polyelectrolyte charge, ion size, and ionic strength. J. Membr. Sci. 559, 98–106. doi:10.1016/j.memsci.2018.04.052
Davenport, D. M., Deshmukh, A., Werber, J. R., and Elimelech, M. (2018). High-pressure reverse osmosis for energy-efficient hypersaline brine desalination: Current status, design considerations, and research needs. Environ. Sci. Technol. Lett. 5 (8), 467–475. doi:10.1021/acs.estlett.8b00274
Davenport, D. M., Ritt, C. L., Verbeke, R., Dickmann, M., Egger, W., Vankelecom, I. F. J., et al. (2020). Thin film composite membrane compaction in high-pressure reverse osmosis. J. Membr. Sci. 610, 118268. doi:10.1016/j.memsci.2020.118268
Dong, G., Nagasawa, H., Yu, L., Guo, M., Kanezashi, M., Yoshioka, T., et al. (2020). Energy-efficient separation of organic liquids using organosilica membranes via a reverse osmosis route. J. Membr. Sci. 597, 117758. doi:10.1016/j.memsci.2019.117758
Dou, H., Xu, M., Wang, B., Zhang, Z., Wen, G., Zheng, Y., et al. (2021). Microporous framework membranes for precise molecule/ion separations. Chem. Soc. Rev. 50 (2), 986–1029. doi:10.1039/D0CS00552E
Du, Z., Ji, M., and Li, R. (2021). Alleviation of membrane fouling and enhancement of trace organic compounds removal in an electric field assisted microfiltration system. Chem. Eng. J. 407, 127042. doi:10.1016/j.cej.2020.127042
DuChanois, R. M., Porter, C. J., Violet, C., Verduzco, R., and Elimelech, M. (2021). Membrane materials for selective ion separations at the water–energy nexus. Adv. Mater. 33 (38), 2101312. doi:10.1002/adma.202101312
Eke, J., Yusuf, A., Giwa, A., and Sodiq, A. (2020). The global status of desalination: An assessment of current desalination technologies, plants and capacity. Desalination 495, 114633. doi:10.1016/j.desal.2020.114633
Gantzel, P. K., and Merten, U. (1970). Gas separations with high-flux cellulose acetate membranes. Industrial Eng. Chem. Process Des. Dev. 9 (2), 331–332. doi:10.1021/i260034a028
Gong, G., Wang, P., Zhou, Z., and Hu, Y. (2019). New insights into the role of an interlayer for the fabrication of highly selective and permeable thin-film composite nanofiltration membrane. ACS Appl. Mater. Interfaces 11 (7), 7349–7356. doi:10.1021/acsami.8b18719
Gould, R. M., White, L. S., and Wildemuth, C. R. (2001). Membrane separation in solvent lube dewaxing. Environ. Prog. 20 (1), 12–16. doi:10.1002/ep.670200110
Greenlee, L. F., Lawler, D. F., Freeman, B. D., Marrot, B., and Moulin, P. (2009). Reverse osmosis desalination: Water sources, technology, and today's challenges. Water Res. 43 (9), 2317–2348. doi:10.1016/j.watres.2009.03.010
Guiver, M. D. (2022). Field grand challenge for membrane science and technology. Front. Membr. Sci. Technol. 1. 878879, doi:10.3389/frmst.2022.878879
Guo, Y., Liu, C., Liu, H., Zhang, J., Li, H., and Zhang, C. (2022). Contemporary antibiofouling modifications ofreverse osmosis membranes: State-of-the-art insights on mechanisms and strategies. Chem. Eng. J. 429, 132400. doi:10.1016/j.cej.2021.132400
Hou, D., Lin, D., Zhao, C., Wang, J., and Fu, C. (2017). Control of protein (BSA) fouling by ultrasonic irradiation during membrane distillation process. Sep. Purif. Technol. 175, 287–297. doi:10.1016/j.seppur.2016.11.047
Jafari, M., Vanoppen, M., van Agtmaal, J. M. C., Cornelissen, E. R., Vrouwenvelder, J. S., Verliefde, A., et al. (2021). Cost of fouling in full-scale reverse osmosis and nanofiltration installations in The Netherlands. Desalination 500, 114865. doi:10.1016/j.desal.2020.114865
Jang, H.-Y., Johnson, J. R., Ma, Y., Mathias, R., Bhandari, D. A., and Lively, R. P. (2019). Torlon® hollow fiber membranes for organic solvent reverse osmosis separation of complex aromatic hydrocarbon mixtures. AIChE J. 65(12), 16757. doi:10.1002/aic.16757
Jimenez-Solomon, M. F., Song, Q., Jelfs, K. E., Munoz-Ibanez, M., and Livingston, A. G. (2016). Polymer nanofilms with enhanced microporosity by interfacial polymerization. Nat. Mater. 15 (7), 760–767. doi:10.1038/nmat4638
Karan, S., Jiang, Z., and Livingston, A. G. (2015). MEMBRANE FILTRATION. Sub-10 nm polyamide nanofilms with ultrafast solvent transport for molecular separation. Science 348 (6241), 1347–1351. doi:10.1126/science.aaa5058
Kim, J. F., Székely, G., Valtcheva, I. B., and Livingston, A. G. (2014). Increasing the sustainability of membrane processes through cascade approach and solvent recovery—Pharmaceutical purification case study. Green Chem. 16(1), 133–145. doi:10.1039/C3GC41402G
Koh, D.-Y., McCool, B. A., Deckman, H. W., and Lively, R. P. (2016). Reverse osmosis molecular differentiation of organic liquids using carbon molecular sieve membranes. Science 353(6301), 804–807. doi:10.1126/science.aaf1343
Koros, W. J., and Zhang, C. (2017). Materials for next-generation molecularly selective synthetic membranes. Nat. Mater. 16 (3), 289–297. doi:10.1038/nmat4805
Li, S., Dong, R., Musteata, V.-E., Kim, J., Rangnekar, N. D., Johnson, J. R., et al. (2022). Hydrophobic polyamide nanofilms provide rapid transport for crude oil separation. Science 377 (6614), 1555–1561. doi:10.1126/science.abq0598
Li, Y., Li, C., Li, S., Su, B., Han, L., and Mandal, B. (2019). Graphene oxide (GO)-interlayered thin-film nanocomposite (TFN) membranes with high solvent resistance for organic solvent nanofiltration (OSN). J. Mater. Chem. A 7(21), 13315–13330. doi:10.1039/C9TA01915D
Liang, B., He, X., Hou, J., Li, L., and Tang, Z. (2019). Membrane separation in organic liquid: Technologies, achievements, and opportunities. Adv. Mater. 31(45), 1806090. doi:10.1002/adma.201806090
Liang, Y., Zhu, Y., Liu, C., Lee, K.-R., Hung, W.-S., Wang, Z., et al. (2020). Polyamide nanofiltration membrane with highly uniform sub-nanometre pores for sub-1 Å precision separation. Nat. Commun. 11, 2015(1), doi:10.1038/s41467-020-15771-2
Liu, C., Dong, G., Tsuru, T., and Matsuyama, H. (2021a). Organic solvent reverse osmosis membranes for organic liquid mixture separation: A review. J. Membr. Sci. 620, 118882. doi:10.1016/j.memsci.2020.118882
Liu, C., Wang, W., Yang, B., Xiao, K., and Zhao, H. (2021b). Separation, anti-fouling, and chlorine resistance of the polyamide reverse osmosis membrane: From mechanisms to mitigation strategies. Water Res. 195, 116976. doi:10.1016/j.watres.2021.116976
Liu, G., and Jin, W. (2021). Pervaporation membrane materials: Recent trends and perspectives. J. Membr. Sci. 636, 119557. doi:10.1016/j.memsci.2021.119557
Liu, Y., Wang, J., Wang, Y., Zhu, H., Xu, X., Liu, T., et al. (2021c). High-flux robust PSf-b-PEG nanofiltration membrane for the precise separation of dyes and salts. Chem. Eng. J. 405, 127051. doi:10.1016/j.cej.2020.127051
Lively, R. P., and Sholl, D. S. (2017). From water to organics in membrane separations. Nat. Mater. 16 (3), 276–279. doi:10.1038/nmat4860
Low, Z.-X., and Wang, H. (2021). Challenges in membrane-based liquid phase separations. Green Chem. Eng. 2 (1), 3–13. doi:10.1016/j.gce.2021.02.002
Lu, J., and Wang, H. (2021). Emerging porous framework material-based nanofluidic membranes toward ultimate ion separation. Matter 4 (9), 2810–2830. doi:10.1016/j.matt.2021.06.045
Marchetti, P., Jimenez Solomon, M. F., Szekely, G., and Livingston, A. G. (2014). Molecular separation with organic solvent nanofiltration: A critical review. Chem. Rev. 114 (21), 10735–10806. doi:10.1021/cr500006j
Niu, C., Li, X., Dai, R., and Wang, Z. (2022). Artificial intelligence-incorporated membrane fouling prediction for membrane-based processes in the past 20 years: A critical review. Water Res. 216, 118299. doi:10.1016/j.watres.2022.118299
Ong, Y. K., Shi, G. M., Le, N. L., Tang, Y. P., Zuo, J., Nunes, S. P., et al. (2016). Recent membrane development for pervaporation processes. Prog. Polym. Sci. 57, 1–31. doi:10.1016/j.progpolymsci.2016.02.003
Pan, Y., Xu, R., Lü, Z., Yu, S., Liu, M., and Gao, C. (2017). Enhanced both perm-selectivity and fouling resistance of poly(piperazine-amide) nanofiltration membrane by incorporating sericin as a co-reactant of aqueous phase. J. Membr. Sci. 523, 282–290. doi:10.1016/j.memsci.2016.10.011
Pham, T. C. T., Nguyen, T. H., and Yoon, K. B. (2013). Gel-free secondary growth of uniformly oriented silica MFI zeolite films and application for xylene separation. Angew. Chem. Int. Ed. 52 (33), 8693–8698. doi:10.1002/anie.201301766
Priske, M., Lazar, M., Schnitzer, C., and Baumgarten, G. (2016). Recent applications of organic solvent nanofiltration. Chem. Ing. Tech. 88 (1-2), 39–49. doi:10.1002/cite.201500084
Qasim, M., Darwish, N. N., Mhiyo, S., Darwish, N. A., and Hilal, N. (2018). The use of ultrasound to mitigate membrane fouling in desalination and water treatment. Desalination 443, 143–164. doi:10.1016/j.desal.2018.04.007
Sholl, D. S., and Lively, R. P. (2016). Seven chemical separations to change the world. Nature 532 (7600), 435–437. doi:10.1038/532435a
Smitha, B., Suhanya, D., Sridhar, S., and Ramakrishna, M. (2004). Separation of organic–organic mixtures by pervaporation—A review. J. Membr. Sci. 241 (1), 1–21. doi:10.1016/j.memsci.2004.03.042
Thompson, K. A., Mathias, R., Kim, D., Kim, J., Rangnekar, N., Johnson, J. R., et al. (2020). N-Aryl–linked spirocyclic polymers for membrane separations of complex hydrocarbon mixtures. Science 369 (6501), 310–315. doi:10.1126/science.aba9806
Tian, M., Hui, H., Ma, T., Zhao, G., Zarak, M., You, X., et al. (2022). A novel nanofiltration membrane with a sacrificial chlorine-resistant nanofilm: Design and characterization of tailored membrane pores and surface charge. Desalination 538, 115896. doi:10.1016/j.desal.2022.115896
Tong, T., and Elimelech, M. (2016). The global rise of zero liquid discharge for wastewater management: Drivers, technologies, and future directions. Environ. Sci. Technol. 50 (13), 6846–6855. doi:10.1021/acs.est.6b01000
Wang, R., Wu, J., Zheng, J., Chen, B., and Zhu, X. (2023). Janus membrane with tailored upper and lower surface charges for ion penetration manipulation in high-performance nanofiltration. J. Membr. Sci. 667, 121191. doi:10.1016/j.memsci.2022.121191
Wang, S., Yang, L., He, G., Shi, B., Li, Y., Wu, H., et al. (2020). Two-dimensional nanochannel membranes for molecular and ionic separations. Chem. Soc. Rev. 49 (4), 1071–1089. doi:10.1039/C9CS00751B
Xiao, K., Liang, S., Wang, X., Chen, C., and Huang, X. (2019). Current state and challenges of full-scale membrane bioreactor applications: A critical review. Bioresour. Technol. 271, 473–481. doi:10.1016/j.biortech.2018.09.061
Xu, Y. M., Le, N. L., Zuo, J., and Chung, T.-S. (2016). Aromatic polyimide and crosslinked thermally rearranged poly(benzoxazole-co-imide) membranes for isopropanol dehydration via pervaporation. J. Membr. Sci. 499, 317–325. doi:10.1016/j.memsci.2015.10.059
Yin, X., Li, X., Hua, Z., and Ren, Y. (2020). The growth process of the cake layer and membrane fouling alleviation mechanism in a MBR assisted with the self-generated electric field. Water Res. 171, 115452. doi:10.1016/j.watres.2019.115452
Zhang, R., Liu, Y., He, M., Su, Y., Zhao, X., Elimelech, M., et al. (2016). Antifouling membranes for sustainable water purification: Strategies and mechanisms. Chem. Soc. Rev. 45 (21), 5888–5924. doi:10.1039/C5CS00579E
Zhang, T., Zheng, W., Wang, Q., Wu, Z., and Wang, Z. (2023). Designed strategies of nanofiltration technology for Mg2+/Li+ separation from salt-lake brine: A comprehensive review. Desalination 546, 116205. doi:10.1016/j.desal.2022.116205
Zhang, W., Li, Z., Xu, Y., Lin, H., Shen, L., Li, R., et al. (2021). In situ conversion of ZnO into zeolitic imidazolate framework-8 in polyamide layers for well-structured high-permeance thin-film nanocomposite nanofiltration membranes. J. Mater. Chem. A 9 (12), 7684–7691. doi:10.1039/D0TA11923G
Zhao, Y., Tong, T., Wang, X., Lin, S., Reid, E. M., and Chen, Y. (2021). Differentiating solutes with precise nanofiltration for next generation environmental separations: A review. Environ. Sci. Technol. 55 (3), 1359–1376. doi:10.1021/acs.est.0c04593
Zhong, M., Tran, K., Min, Y., Wang, C., Wang, Z., Dinh, C.-T., et al. (2020). Accelerated discovery of CO2 electrocatalysts using active machine learning. Nature 581(7807), 178–183. doi:10.1038/s41586-020-2242-8
Keywords: grand challenge, membranes, membrane applications, liquid separation, separation technology, membrane science and technology
Citation: Hu Y (2023) Grand challenge in membrane applications: Liquid. Front. Membr. Sci. Technol. 2:1177528. doi: 10.3389/frmst.2023.1177528
Received: 01 March 2023; Accepted: 06 March 2023;
Published: 16 March 2023.
Edited and reviewed by:
Michael D. Guiver, Tianjin University, ChinaCopyright © 2023 Hu. This is an open-access article distributed under the terms of the Creative Commons Attribution License (CC BY). The use, distribution or reproduction in other forums is permitted, provided the original author(s) and the copyright owner(s) are credited and that the original publication in this journal is cited, in accordance with accepted academic practice. No use, distribution or reproduction is permitted which does not comply with these terms.
*Correspondence: Yunxia Hu, eXVueGlhaHVAdGlhbmdvbmcuZWR1LmNu
Disclaimer: All claims expressed in this article are solely those of the authors and do not necessarily represent those of their affiliated organizations, or those of the publisher, the editors and the reviewers. Any product that may be evaluated in this article or claim that may be made by its manufacturer is not guaranteed or endorsed by the publisher.
Research integrity at Frontiers
Learn more about the work of our research integrity team to safeguard the quality of each article we publish.