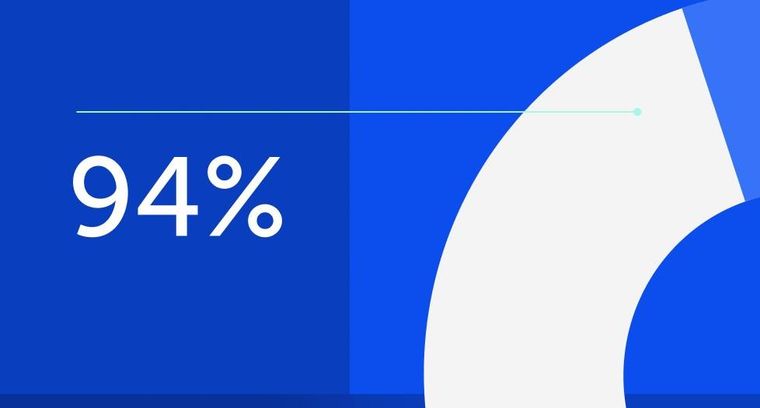
94% of researchers rate our articles as excellent or good
Learn more about the work of our research integrity team to safeguard the quality of each article we publish.
Find out more
PERSPECTIVE article
Front. Membr. Sci. Technol., 06 April 2023
Sec. Membrane Formation and Structure
Volume 2 - 2023 | https://doi.org/10.3389/frmst.2023.1169158
Reverse osmosis desalination is one of the most important and increasingly popular technologies to augment available water resources. Central to the technology is a thin-film-composite polyamide membrane capable of separating pure water from seawater or brine. Since its conception and initiation, the membrane industry has followed a linear life-cycle scheme. However, increasing production costs of fossil-based materials and more stringent environmental regulations drive the initiatives to adapt to a circular economy of membrane materials. In this perspective, we briefly summarize the pressing issues in the state-of-the-art membrane industry, then discuss the opportunities in future technology innovations with a focus on sustainable membrane manufacturing and recycling, and lastly provided an outlook for future membrane design and fabrication towards a circular economy.
Circularity is at the core of a sustainable future. A “circular economy” transforms goods at the end of their use lives into reusable resources, “closing loops” in industrial ecosystems by eliminating waste, circulating products, and preserving the environment (Kümmerer, Clark and Zuin, 2020). Desalination membranes are a critical component to a circular, sustainable future as membrane processes represent so far, the most energy-efficient approach for water purification and resource recovery from many non-traditional water resources (Hube et al., 2020).
As a vital contribution to the nutrients, energy, and water (“NEW”) initiatives (Ren and Umble, 2016), today’s linear economy of desalination membrane materials must be adapted to a circular economy. The current membrane industry suffers from several shortcomings, e.g., usage of fossil-based membrane materials, dependence on organic solvents, and lack of End-of-Life (EoL) management of membrane wastes. The transition towards a circular membrane industry involves system-wide changes and the integration of sustainable manufacturing processes and a membrane-to-membrane circular economy loop based on innovative recycling techniques.
Achieving a circular economy system for desalination membrane materials is hampered by the current “take-make-waste” model of membrane elements (Senán-Salinas et al., 2021). Reverse osmosis (RO), which is the most widely used and energy-efficient desalination technology accounting for ∼80% of the world desalination capacity, follows a linear life-cycle scheme (Ahmed, Hashaikeh and Hilal, 2020; Liang, Dudchenko and Mauter, 2022). This linear scheme includes the extraction of fossil-based materials, manufacturing and packaging of membrane modules in centralized facilities, distribution to desalination plants, use and maintenance, and then disposal to landfills after 5–10 years of service lives (Senán-Salinas et al., 2021).
State-of-the-art membrane manufacturing is energy intensive and consumes fossil fuel-based resources. Today’s commercial thin-film-composite (TFC) RO membranes are fabricated using fossil-based plastic materials, e.g., polyamide (PA), polysulfone (PSF), polyethersulfone (PES) and polyethylene terephthalate (PET). Meanwhile, the industrial fabrication processes of RO membranes [i.e., interfacial polymerization (IP)] have been used and optimized for 4 decades, leaving little room for innovation and the introduction of new, “greener” materials (Nunes et al., 2020). In addition, these processes face substantial challenges due to the increasingly stringent environmental regulations on organic solvent utilization. Commercial membrane production utilizes organic solvents to dissolve polymers during membrane casting and spinning [e.g., dimethylformamide (DMF), n-methylpyrrolidone (NMP), dimethylacetamide (DMAc), tetrahydrofuran (THF), acetone, methanol, and ethanol] or the monomers for IP (e.g., hexane, toluene, chloroform) (Dong et al., 2021). Novel membrane manufacturing includes the use of renewable materials, minimization or replacement of organic solvents, process scalability, and energy input reduction (Nunes et al., 2020).
Lack of effective downstream recycling technologies complicates the end-of-life management of membrane elements. Currently, RO membrane elements constitute the main solid waste in many desalination plants (Senán-Salinas et al., 2021). They are directly disposed in landfills after reaching the end of their use-life. Presently, nearly 840,000 RO modules (>14,000 tonnes/year waste of membrane materials) are discarded every year worldwide and by 2025, this number is projected to rise to two million (Lawler et al., 2015; Senán-Salinas et al., 2021). According to the material intensity studies based on German energy mix (Wuppertal Institute, 2014; Pontié, 2015), disposal of a waste RO membrane element (13.5 kg) in landfills can produce 78 kg of abiotic materials, 2500 kg of water contamination, and 40 kg of air contamination to the environment (Coutinho de Paula and Santos Amaral, 2018). Increasing cost of virgin materials and awareness of the environmental impact of membrane waste are inspiring membrane manufacturers and users to adapt to a circular economy of membrane materials.
Some recycling technologies exist for RO membranes. Direct reuse of RO membranes or recycling into nanofiltration (NF) and ultrafiltration (UF) membranes are the most studied recycling technologies (Lawler et al., 2012; García-Pacheco et al., 2019). Indirect recycling of discarded RO modules as support materials for biofilm reactors or anion exchange membranes is also proposed as waste valorization alternatives (Morón-López et al., 2019; Lejarazu-Larrañaga et al., 2020). Despite the technical efficiency, two challenges remain: 1) direct/indirect recycling will shorten the lifespan of recycled membranes to ∼2 years (Coutinho de Paula and Santos Amaral, 2018), which then become waste materials; and 2) little is known about the environmental and economic potentials of various recycling techniques at full scale (Lawler et al., 2015).
Efforts to rigorously quantify the environmental impact of these manufacturing and recycling alternatives are incomplete. Life cycle assessment (LCA) is a systematic tool for evaluating potential environmental outcomes. While several LCA studies have been carried out on membrane manufacturing and seawater desalination industries, most of them are focused on the process operation, i.e., materials and energy consumption, which were found to be the most impactful factors on the environment (Lawler et al., 2015; Senán-Salinas et al., 2019). However, few studies have explored the environmental effect of membrane manufacturing and end-of life waste.
This perspective will provide a high-level overview of innovations in membrane technology with a focus on sustainable membrane manufacturing and recycling. We begin with a summary of recent developments in sustainable membrane manufacturing and recycling technologies, including both technological discoveries and LCA results. Then we attempt to critically discuss the key opportunities in technology innovations for making membrane and desalination industries more sustainable. Thereafter, we outline a perspective for future membrane design and fabrication towards a circular economy.
The membrane industry uses a well-established portfolio of materials and manufacturing processes to produce membranes. The gold standard TFC RO membranes are industrially fabricated via interfacial polymerization (IP) of diamines and trimethyl chlorides on supporting ultrafiltration (UF) membranes (Liang et al., 2020). A typical IP process involves a large amount of water and organic solvent to dissolve the monomers. Commercial UF membranes are manufactured through phase separation of PSF or PES homopolymers on PET non-woven fabrics. Non-solvent phase separation (NIPS) and temperature-induced phase separation (TIPS) are the two most common methods in the industry for the large-scale production of UF membranes (Dong et al., 2021). Similarly, fabrication of UF membranes utilizes a large amount of water and organic solvents, e.g., DMF and NMP (Nunes et al., 2020). Lastly, porous PET non-woven fabrics are primarily manufactured through melt-blown extrusion (Saleem et al., 2020).
Development of future sustainable membrane manufacturing processes needs to address several challenges. One significant challenge facing existing industrial fabrication processes is the critical need to adopt bio-based materials and solvent-free systems (Nunes et al., 2020). Improving process compatibility and scalability opens new avenues to using renewable materials and minimizing hazardous chemicals and solvents. Another challenge lies in extending the lifespan of membrane material by improving the chlorine resistance, fouling resistance, and chemical and thermal stability (Petersen, 1993). Lastly, sustainable membrane manufacturing should consider the end-of-life recycling of the material and attempt to implement a recyclable-by-design approach to membrane fabrication.
Renewable and biodegradable polymers are promising sustainable alternatives of desalination membrane materials. Polymers derived from renewable, biobased sources can significantly decrease the carbon footprint of the membrane manufacturing processes (Shehata et al., 2023). For example, cellulose, poly (lactic acid) (PLA), and poly (hydroxybutyrate)s are some of the most studied biobased polymers to replace conventional petroleum-based polymers for membranes (Table 1), such as PES, PSU, and PVDF (Dong et al., 2021). Furthermore, these renewable polymers can break down in industrial composting conditions which can reduce the environmental impact of end-of-life disposals of used membrane elements.
Implementing renewable materials in the present membrane manufacturing processes is limited by the inferior performance of these alternatives compared to conventional materials. In order to achieve target performance required for rigorous membrane applications, biobased polymers are often blended with non-biodegradable polymers in manufacturing (Shehata et al., 2023). However, the mix of multiple polymers can easily cause a breakdown of the polymer structure and release non-biodegradable materials into the environment (Shehata et al., 2023). Meanwhile, the impact of biodegradation on the long-term membrane performance is still unknown. Due to uncertainty in the biodegradation rate, the disposed polymers can leak into the ocean, impacting marine animals and the environment (Shehata et al., 2023).
The membrane industry is heavily dependent on traditional toxic organic solvents. Conventional membrane manufacturing processes consume a large number of hazardous solvents, such as DMF, NMP, THF, DMAc, and dimethyl sulfoxide (DMSO) (Dong et al., 2021). These petroleum-derived solvents are non-renewable, highly hazardous, and are known endocrine disruptors. In addition, removal or recycling of these solvents is energy-intensive and dangerous due to their flammability and high boiling point (Dong et al., 2021).
With growing regulations around solvent use in manufacturing processes, substitution of conventional toxic solvents with greener, non-toxic solvents is critical in the realization of future sustainable membrane manufacturing. Non-toxic and eco-friendly solvents can greatly decrease the carbon footprint and environmental impact on membrane manufacturing and recycling. Recently, several sustainable solvent alternatives have been investigated for membrane fabrication. For example, methyl lactate (ML) is a biodegradable solvent that can be used to fabricate cellulose acetate (CA) membranes and polyetherimide (PEI) membranes via phase inversion (Alqaheem et al., 2018). Supercritical carbon dioxide (ssCO2) can be used to produce porous polycarbonate (PC) hollow fiber membranes by melt extrusion (Rasool, Pescarmona and Vankelecom, 2019). Ionic liquids consisting of a polyatomic inorganic anion and an organic cation are promising alternative solvents to prepare cellulose and PSF membranes via phase inversion, and TFC PA membranes through IP (Mariën et al., 2016). Other green solvents, e.g., triethyl phosphate (TEP), organic carbonates, Rhodiasolv® PolarClean, Gamma-valerolactone (GVL), and PolarClean as co-solvents (Table 1), exist to support the versatility of membrane fabrication with improved performance and morphology (Dong et al., 2021; Stone et al., 2022). On the other hand, the prospect of replacing traditional solvents with green solvents faces several challenges: 1) the costs of these safer and greener solvents are typically higher than those of conventional membrane fabrication solvents; 2) biodegradable solvents may cause eutrophication in the water system; and 3) the environmental and economical impact of green solvent recovery remains unknown (Dong et al., 2021).
In addition to switching to renewable chemicals, improving membrane fouling resistance can critically contribute to the future sustainability of membrane materials. Membrane fouling is an inevitable and persistent issue in today’s membrane applications due to the buildup of foulants on membrane surface (Petersen, 1993). Fouling reduces the water treatment efficiency, increases energy consumption of the filtration process, and most importantly, reduces the lifespan of membrane elements because of the frequent chemical cleaning required. The problem of membrane fouling originates from the morphological nature of TFC RO membranes. Thus, solutions to improve the anti-fouling properties of membranes comprise three avenues (Nunes et al., 2020). First, creating a smooth support layer with undulated surface topography for TFC PA membrane fabrication can significantly reduce surface roughness. Second, surface modification with strong electrolytes, surfactants, and hydrophilic polymers enhances the anti-fouling resistance. Last, designing membranes with chlorine-resistant materials can prolong the lifespan of membranes, and reduce waste disposal by extension.
Membranes with improved mechanical, chemical, and thermal stability will further extend the applicability and lifetime of membrane separations (Table 1). Despite the great success of membrane technology in the water sector, tremendous opportunities remain in the chemical, petrochemical, and energy sectors. Highly stable membranes, e.g., crosslinked polyimide, poly (ether ether ketone) (PEEK), polyacrylonitrile, and polydimethylsiloxane are promising materials for chemical and geothermal applications (Dong et al., 2021). Simultaneous improvements in the stability of the support layer and membrane housing also need to be considered to successfully apply these membranes.
Today’s membrane industry follows a linear model of raw materials extraction, centralized manufacturing and distribution, service and maintenance, and disposal to landfills. Lack of considerations in module recycling and reuse in the design phase results in a growing number of discharged RO membrane elements worldwide. It is estimated that the desalination sector will generate 14,000 tons of EoL RO membrane elements annually (Senán-Salinas et al., 2019). The increasing flow of plastic waste into the environment not only leads to significant loss of useful resources but has a profound negative impact on environmental and human health.
Reusing and recycling EoL membrane elements have great potential to reduce the environmental impact and close the loop in the circular economy of desalination membrane materials. In addition to the proper design of membrane elements with renewable and biodegradable materials, innovations in membrane recycling technology are needed. At the same time, LCA represents an important tool that can provide valuable information on the potential environmental outcomes of various recycling techniques.
EoL RO membrane elements can be recycled and reused directly as other types of membrane elements. In addition to the direct RO reuse (Table 1), EoL RO membrane elements can be transformed into forward osmosis (FO), NF, UF, or MF membranes after being cleaned and chemically treated with a NaOCl solution (Lawler et al., 2012; García-Pacheco et al., 2019). A few LCA studies concluded that direct brackish water (BW) RO membrane recycling into UF and seawater (SW) membrane recycling into NF was the second preferable option behind direct RO reuse (Senán-Salinas et al., 2021).
In addition to the materials factor, process parameters also play a vital role in the pilot scale of direct recycling processes. Recent LCA studies compared two pilot-scale direct recycling systems, i.e., an active system (AS) and a passive system (PS) (Senán-Salinas et al., 2019). AS has an internal recirculation of hypochlorite solution inside two pressure tubes, whereas PS has six modules without internal recirculation. Meanwhile, AS and PS systems also have major differences in exposure doses. LCA results revealed that PS lowered the environmental impact of the AS up to 66%–70%. A cost-effective analysis reported the cost of AS was €54.5–73.75/module, and the cost of PS was €25.9–41.5/module. Another LCA study identified that the transportation of waste RO membranes to the recycling location and the distribution of secondary products to end-users play a crucial role in the overall environmental impact (Lawler et al., 2015).
Alternative waste valorization techniques turn recycled RO membranes into the basis of novel membrane technologies (Table 1). A recent study reported the usage of discarded RO membranes as support for a biofilm reactor to remove microcystins (MC) (Morón-López et al., 2019). Unlike direct recycling, used SWRO and BWRO membrane elements did not need cleaning because the fouling membrane surface was advantageous for biofilm attachments. The Recycled-Membrane Biofilm Reactor (R-MBfR) was capable of degrading 2 mg.L−1 of MC in 24 h. Furthermore, a cost assessment analysis reported a 0.140 € m−3 of unitary cost estimation for removing >95% of extracellular MC.
Indirect recycling alternatives represent a versatile and highly tolerant approach to recycling imperfect EoL RO modules. In the case where discarded RO modules are excessively damaged and unable to be directly recycled into UF and NF membranes, indirect recycling can be a more reasonable option. For example, EoL RO elements can be reused as the support for preparing ion exchange membranes (IEM) for electrodialysis (ED) (Lejarazu-Larrañaga et al., 2020). Meanwhile, the polypropylene (PP) feed spacers from the RO modules are reused as turbulence promoters, end plates, and compartments in the ED stack. In this process, 51% of the EoL RO module is successfully recycled into an ED system.
After reuse and direct/indirect recycling, deconstruction of RO membrane materials and upcycling of the deconstructed intermediates to produce new materials may provide a promising solution to end plastic waste in landfills. Commercial RO membrane modules are complex formulations of several types of materials. The spiral-wound element consists of TFC PA membranes, feed spacers, permeate spacers, a permeate tube, and plastic housing. Because of the ultra-thin PA layer and PES support of TFC PA membranes, only the PET non-woven fabrics are economically and technically worth recycling (Nunes et al., 2020). In addition, both permeate and feed spacers are made of polyolefins such as PP and polyethylene (PE) that can be recycled. As a result of this heterogeneity, advanced chemical and/or biological processes are required to break down these complex formulations to upcyclable intermediates.
Mechanical recycling of plastic wastes involves collecting and sorting, then shredding and extruding into pellets or other forms, and reforming into new products. Conventional mechanical recycling can be applied to single streams of materials such as sorted/separated PET, PP, or PE steams, but cannot be applied to mixed materials (Table 1). Furthermore, mechanical recycling usually results in quality loss of the material due to thermal-mechanical degradation that occurs during the recycling process (Li et al., 2022). On the contrary, chemical recycling techniques that break down the material into parent monomers or other chemical building blocks overcome limitations in heterogeneous waste and offer more advantages such as high conversion, contamination resistance, energy saving, and low carbon footprint (Li et al., 2022). For example, various solvolysis methods have successfully been used for PET depolymerization, e.g., glycolysis, methanolysis, and hydrolysis (Li et al., 2022). Pyrolysis is a typical chemical recycling method for polyolefins such as PE and PP, which can break down PE plastics into pyrolysis oil which can be upgraded into fuels or further refined into hydrocarbons for plastic production. Types of pyrolysis include catalytic pyrolysis, hydrogen-assisted pyrolysis, and microwave-assisted pyrolysis (Jha and Kannan, 2021). Last but not the least, combining chemical and biological processes shows great potential for funneling mixed plastics including PET, HDPE, and PS into useful chemical products (Sullivan et al., 2022). Chemical and biological recycling processes are still in development, with few operating at the pilot scale. Regardless, these technologies show promise as effective means of mitigating material waste and keeping carbon building blocks circular.
Despite the great success of RO-based desalination technology in the water sector, today’s linear membrane economy must adapt to a circular economy. Future efforts are needed in technology innovations in scalable, sustainable membrane manufacturing and membrane recycling.
Sustainable membrane manufacturing needs to seek renewable material alternatives, minimize or replace toxic organic solvents, and expand the compatibility of the existing industrial membrane manufacturing process. While it remains challenging to replace the polyamide active layer of the gold-standard TFC-PA RO membrane due to its satisfactory perm-selectivity, innovation concerning the use of renewable or biodegradable materials to replace other elements of RO membrane modules can potentially reduce the environmental impact of waste membranes. More importantly, searching for alternative, green solvents to replace traditional hazardous solvents in the manufacturing process is an urgent need to reduce the solvent emission and meet more stringent regulations.
Extending the lifespan of membrane elements is also of great importance for advancing the sustainability of membrane materials. Membrane fouling remains one of the major concerns in the membrane technology, limiting the membrane lifespan and increasing the operation cost. Therefore, the main improvement area for future RO membranes is fouling resistance and chemical resistance to cleaning agents.
Last but not the least, substantial efforts are needed to address the knowledge gap in the environmental and economic aspects of various recycling technologies for EoL membrane elements. Direct/indirect recycling can extend the lifespan of membrane modules and bring environmental benefits and monetary gains but is not a circular solution for membrane waste. While advanced chemical and/or biological recycling has the potential to break down mixed plastic, the technical efficiency and the associated environmental impacts, especially when applied to membrane recycling, remain understudied.
The original contributions presented in the study are included in the article/supplementary material, further inquiries can be directed to the corresponding author.
YL: Conceptualization, writing—original draft, review and editing. KK: Conceptualization, writing—review and editing.
YL was supported by the National Renewable Energy Laboratory, operated by Alliance for Sustainable Energy, LLC, for the U.S. Department of Energy (DOE).
The authors declare that the research was conducted in the absence of any commercial or financial relationships that could be construed as a potential conflict of interest.
All claims expressed in this article are solely those of the authors and do not necessarily represent those of their affiliated organizations, or those of the publisher, the editors and the reviewers. Any product that may be evaluated in this article, or claim that may be made by its manufacturer, is not guaranteed or endorsed by the publisher.
Ahmed, F. E., Hashaikeh, R., and Hilal, N. (2020). Hybrid technologies: The future of energy efficient desalination – a review. Desalination 495, 114659. doi:10.1016/j.desal.2020.114659
Alonso, D. M., Wettstein, S. G., and Dumesic, J. A. (2013). Gamma-valerolactone, a sustainable platform molecule derived from lignocellulosic biomass. Green Chem. 15 (3), 584–595. doi:10.1039/c3gc37065h
Alqaheem, Y., Alomair, A., Alhendi, A., Alkandari, S., Tanoli, N., Alnajdi, N., et al. (2018). Preparation of polyetherimide membrane from non-toxic solvents for the separation of hydrogen from methane. Chem. Central J. 12 (1), 80–88. doi:10.1186/s13065-018-0449-7
Ambrosi, A., and Tessaro, I. C. (2013). Study on potassium permanganate chemical treatment of discarded reverse osmosis membranes aiming their reuse. Sep. Sci. Technol. Phila. 48 (10), 1537–1543. doi:10.1080/01496395.2012.745876
Clasen, C., Wilhelms, T., and Kulicke, W.-M. (2006). Formation and characterization of chitosan membranes. Biomacromolecules 7 (11), 3210–3222. doi:10.1021/bm060486x
Colburn, A., Vogler, R. J., Patel, A., Bezold, M., Craven, J., Liu, C., et al. (2019). Composite membranes derived from cellulose and lignin sulfonate for selective separations and antifouling aspects. Nanomaterials 9 (6), 867. doi:10.3390/nano9060867
Coutinho de Paula, E., and Santos Amaral, M. C. (2018). Environmental and economic evaluation of end-of-life reverse osmosis membranes recycling by means of chemical conversion. J. Clean. Prod. 194, 85–93. doi:10.1016/j.jclepro.2018.05.099
Da Silva, M. K., Ambrosi, A., dos Ramos, G. M., and Tessaro, I. C. (2012). Rejuvenating polyamide reverse osmosis membranes by tannic acid treatment. Sep. Purif. Technol. 100, 1–8. doi:10.1016/j.seppur.2012.07.027
Davenport, D. M., Deshmukh, A., Werber, J. R., and Elimelech, M. (2018). High-pressure reverse osmosis for energy-efficient hypersaline brine desalination: Current status, design considerations, and research needs. Environ. Sci. Technol. Lett. 5 (8), 467–475. doi:10.1021/acs.estlett.8b00274
Dong, X., Lu, D., Harris, T. A. L., and Escobar, I. C. (2021). Polymers and solvents used in membrane fabrication: A review focusing on sustainable membrane development. Membranes 11 (5), 309. doi:10.3390/membranes11050309
Esfahani, M. R., Taylor, A., Serwinowski, N., Parkerson, Z. J., Confer, M. P., Kammakakam, I., et al. (2020). Sustainable novel bamboo-based membranes for water treatment fabricated by regeneration of bamboo waste fibers. ACS Sustain. Chem. Eng. 8 (10), 4225–4235. doi:10.1021/acssuschemeng.9b07438
Galiano, F., Briceno, K., Marino, T., Molino, A., Christensen, K. V., and Figoli, A. (2018). Advances in biopolymer-based membrane preparation and applications. J. Membr. Sci. 564, 562–586. doi:10.1016/j.memsci.2018.07.059
García-Pacheco, R., Gabarro, J., Suquet, J., Galizia, A., Godo-Pla, L., Molina, F., et al. (2020). “Landfill leachate treatment using second-hand membranes,” in 7th MSA ECR Membrane Symposium. Sydney, Australia: University of Technology Sydney, 1–4.
García-Pacheco, R., Landaburu-Aguirre, J., Molina, S., Rodriguez-Saez, L., Teli, S. B., and Garcia-Calvo, E. (2015). Transformation of end-of-life RO membranes into NF and UF membranes: Evaluation of membrane performance. J. Membr. Sci. 495, 305–315. doi:10.1016/j.memsci.2015.08.025
Hassankiadeh, N. T., Cui, Z., Kim, J. H., Shin, D. W., Lee, S. Y., Sanguineti, A., et al. (2015). Microporous poly(vinylidene fluoride) hollow fiber membranes fabricated with PolarClean as water-soluble green diluent and additives. J. Membr. Sci. 479, 204–212. doi:10.1016/j.memsci.2015.01.031
Huang, Q., Seibig, B., and Paul, D. (1999). Polycarbonate hollow fiber membranes by melt extrusion. J. Membr. Sci. 161 (1–2), 287–291. doi:10.1016/S0376-7388(99)00122-2
Hube, S., Eskafi, M., Hrafnkelsdóttir, K. F., Bjarnadóttir, B., Bjarnadóttir, M. Á., Axelsdóttir, S., et al. (2020). Direct membrane filtration for wastewater treatment and resource recovery: A review. Sci. Total Environ. 710, 136375. doi:10.1016/j.scitotenv.2019.136375
Jarma, Y. A., Karaoğlu, A., Tekin, O., Baba, A., Okten, H. E., Tomaszewska, B., et al. (2021). Assessment of different nanofiltration and reverse osmosis membranes for simultaneous removal of arsenic and boron from spent geothermal water. J. Hazard. Mater. 405, 124129. doi:10.1016/j.jhazmat.2020.124129
Jha, K. K., and Kannan, T. T. M. (2021). Recycling of plastic waste into fuel by pyrolysis-a review. Mater. Today Proc. 37, 3718–3720. doi:10.1016/j.matpr.2020.10.181
Jiang, S., Li, Y., and Ladewig, B. P. (2017). A review of reverse osmosis membrane fouling and control strategies. Sci. Total Environ. 595, 567–583. doi:10.1016/j.scitotenv.2017.03.235
Jung, J. T., Kim, J. F., Wang, H. H., di Nicolo, E., Drioli, E., and Lee, Y. M. (2016). Understanding the non-solvent induced phase separation (NIPS) effect during the fabrication of microporous PVDF membranes via thermally induced phase separation (TIPS). J. Membr. Sci. 514, 250–263. doi:10.1016/j.memsci.2016.04.069
Kim, D., Livazovic, S., Falca, G., and Nunes, S. P. (2019). Oil-water separation using membranes manufactured from cellulose/ionic liquid solutions. ACS Sustain. Chem. Eng. 7 (6), 5649–5659. doi:10.1021/acssuschemeng.8b04038
Kümmerer, K., Clark, J. H., and Zuin, V. G. (2020). Rethinking chemistry for a circular economy. Science 367 (6476), 369–370. doi:10.1126/science.aba4979
Lawler, W., Alvarez-Gaitan, J., Leslie, G., and Le-Clech, P. (2015). Comparative life cycle assessment of end-of-life options for reverse osmosis membranes. Desalination 357, 45–54. doi:10.1016/j.desal.2014.10.013
Lawler, W., Antony, A., Cran, M., Duke, M., Leslie, G., and Le-Clech, P. (2013). Production and characterisation of UF membranes by chemical conversion of used RO membranes. J. Membr. Sci. 447, 203–211. doi:10.1016/j.memsci.2013.07.015
Lawler, W., Bradford-Hartke, Z., Cran, M. J., Duke, M., Leslie, G., Ladewig, B. P., et al. (2012). Towards new opportunities for reuse, recycling and disposal of used reverse osmosis membranes. Desalination 299, 103–112. doi:10.1016/j.desal.2012.05.030
Lawler, W., Wijaya, T., Antony, A., Leslie, G., and Le-Clech, P. (2011). “Reuse of reverse osmosis desalination membranes,” in IDA World Congress (Vol. 2011). Perth, WA: Perth Convention and Exhibition Centre.
Le Phuong, H. A., Izzati Ayob, N. A., Blanford, C. F., Mohammad Rawi, N. F., and Szekely, G. (2019). Nonwoven membrane supports from renewable resources: Bamboo fiber reinforced poly(lactic acid) composites. ACS Sustain. Chem. Eng. 7 (13), 11885–11893. doi:10.1021/acssuschemeng.9b02516
Lejarazu-Larrañaga, A., Molina, S., Ortiz, J. M., Navarro, R., and Garcia-Calvo, E. (2020). Circular economy in membrane technology: Using end-of-life reverse osmosis modules for preparation of recycled anion exchange membranes and validation in electrodialysis. J. Membr. Sci. 593, 117423. doi:10.1016/j.memsci.2019.117423
Li, H., Aguirre-Villegas, H. A., Allen, R. D., Bai, X., Benson, C. H., Beckham, G. T., et al. (2022). Expanding plastics recycling technologies: Chemical aspects, technology status and challenges. Green Chem. 24, 8899–9002. doi:10.1039/d2gc02588d[Preprint] Royal Society of Chemistry
Liang, Y., Dudchenko, A. V., and Mauter, M. S. (2022). Inadequacy of current approaches for characterizing membrane transport properties at high salinities. J. Membr. Sci. 668, 121246. doi:10.1016/j.memsci.2022.121246
Liang, Y., Zhu, Y., Liu, C., Lee, K. R., Hung, W. S., Wang, Z., et al. (2020). Polyamide nanofiltration membrane with highly uniform sub-nanometre pores for sub-1 Å precision separation. Nat. Commun. 11 (1), 2015–2019. doi:10.1038/s41467-020-15771-2
Liu, F., Hashim, N. A., Liu, Y., Abed, M. M., and Li, K. (2011). Progress in the production and modification of PVDF membranes. J. Membr. Sci. 375 (1–2), 1–27. doi:10.1016/j.memsci.2011.03.014
Mariën, H., Bellings, L., Hermans, S., and Vankelecom, I. F. J. (2016). Sustainable process for the preparation of high-performance thin-film composite membranes using ionic liquids as the reaction medium. ChemSusChem 9 (10), 1101–1111. doi:10.1002/cssc.201600123
Medina-Gonzalez, Y., Aimar, P., Lahitte, J. F., and Remigy, J. C. (2011). Towards green membranes: Preparation of cellulose acetate ultrafiltration membranes using methyl lactate as a biosolvent. Int. J. Sustain. Eng. 4 (1), 75–83. doi:10.1080/19397038.2010.497230
Morón-López, J., Nieto-Reyes, L., Senan-Salinas, J., Molina, S., and El-Shehawy, R. (2019). Recycled desalination membranes as a support material for biofilm development: A new approach for microcystin removal during water treatment. Sci. Total Environ. 647, 785–793. doi:10.1016/j.scitotenv.2018.07.435
Nunes, S. P., Culfaz-Emecen, P. Z., Ramon, G. Z., Visser, T., Koops, G. H., Jin, W., et al. (2020). Thinking the future of membranes: Perspectives for advanced and new membrane materials and manufacturing processes. J. Membr. Sci. 598, 117761. doi:10.1016/j.memsci.2019.117761December 2019
Petersen, R. J. (1993).Composite reverse osmosis and nanofiltration membranes J. Membr. Sci., 83. Elsevier, 81–150. doi:10.1016/0376-7388(93)80014-O
Pontié, M. (2015). Old RO membranes: Solutions for reuse. Desalination Water Treat. 53 (6), 1492–1498. doi:10.1080/19443994.2014.943060
Rasool, M. A., Pescarmona, P. P., and Vankelecom, I. F. J. (2019). Applicability of organic carbonates as green solvents for membrane preparation. ACS Sustain. Chem. Eng. 7 (16), 13774–13785. doi:10.1021/acssuschemeng.9b01507
Ray, M., Pal, K., Anis, A., and Banthia, A. K. (2010). Development and characterization of chitosan-based polymeric hydrogel membranes. Des. Monomers Polym. 13 (3), 193–206. doi:10.1163/138577210X12634696333479
Ren, Z. J., and Umble, A. K. (2016). Water treatment: Recover wastewater resources locally. Nature 529 (7584), 25. doi:10.1038/529025b
Rodríguez, J. J., Jimenez, V., Trujillo, O., and Veza, J. (2002). Reuse of reverse osmosis membranes in advanced wastewater treatment. Desalination 150 (3), 219–225. doi:10.1016/S0011-9164(02)00977-3
Saleem, H., Trabzon, L., Kilic, A., and Zaidi, S. J. (2020). Recent advances in nanofibrous membranes: Production and applications in water treatment and desalination. Desalination 478, 114178. doi:10.1016/j.desal.2019.114178
Senán-Salinas, J., Blanco, A., Garcia-Pacheco, R., Landaburu-Aguirre, J., and Garcia-Calvo, E. (2021). Prospective Life Cycle Assessment and economic analysis of direct recycling of end-of-life reverse osmosis membranes based on Geographic Information Systems. J. Clean. Prod. 282, 124400. doi:10.1016/j.jclepro.2020.124400
Senán-Salinas, J., Garcia-Pacheco, R., Landaburu-Aguirre, J., and Garcia-Calvo, E. (2019). Recycling of end-of-life reverse osmosis membranes: Comparative LCA and cost-effectiveness analysis at pilot scale. Resour. Conservation Recycl. 150, 104423. doi:10.1016/j.resconrec.2019.104423
Shehata, N., Egirani, D., Olabi, A. G., Inayat, A., Abdelkareem, M. A., Chae, K. J., et al. (2023). Membrane-based water and wastewater treatment technologies: Issues, current trends, challenges, and role in achieving sustainable development goals, and circular economy. Chemosphere 320, 137993. doi:10.1016/j.chemosphere.2023.137993
Stone, M. L., Webber, M. S., Mounfield, W. P., Bell, D. C., Christensen, E., Morais, A. R., et al. (2022). Continuous hydrodeoxygenation of lignin to jet-range aromatic hydrocarbons. Joule 6 (10), 2324–2337. doi:10.1016/j.joule.2022.08.005
Sullivan, K. P., Werner, A. Z., Ramirez, K. J., Ellis, L. D., Bussard, J. R., Black, B. A., et al. (2022). Mixed plastics waste valorization through tandem chemical oxidation and biological funneling. Science 378 (6616), 207–211. doi:10.1126/science.abo4626
Thakur, V. K., and Voicu, S. I. (2016). Recent advances in cellulose and chitosan based membranes for water purification: A concise review. Carbohydr. Polym. 146, 148–165. doi:10.1016/j.carbpol.2016.03.030
Veza, J. M., and Rodriguez-Gonzalez, J. J. (2003). Second use for old reverse osmosis membranes: Wastewater treatment. Desalination 157 (1–3), 65–72. doi:10.1016/S0011-9164(03)00384-9
Wuppertal Institute, (2014). Material intensity of materials, fuels, transport services, food. Wuppertal, Germany: Wuppertal Institute, 1–12. Available at: https://wupperinst.org/en/a/wi/a/s/ad/365/.
Keywords: circularity, reverse osmosis membrane, sustainable manufacturing, polymer recycling, desalination
Citation: Liang Y and Knauer KM (2023) Trends and future outlooks in circularity of desalination membrane materials. Front. Membr. Sci. Technol. 2:1169158. doi: 10.3389/frmst.2023.1169158
Received: 18 February 2023; Accepted: 20 March 2023;
Published: 06 April 2023.
Edited by:
Santanu Karan, Central Salt and Marine Chemicals Research Institute (CSIR), IndiaReviewed by:
Oded Nir, Ben-Gurion University of the Negev, IsraelCopyright © 2023 Liang and Knauer. This is an open-access article distributed under the terms of the Creative Commons Attribution License (CC BY). The use, distribution or reproduction in other forums is permitted, provided the original author(s) and the copyright owner(s) are credited and that the original publication in this journal is cited, in accordance with accepted academic practice. No use, distribution or reproduction is permitted which does not comply with these terms.
*Correspondence: Yuanzhe Liang, eXVhbnpoZS5saWFuZ0BucmVsLmdvdg==
Disclaimer: All claims expressed in this article are solely those of the authors and do not necessarily represent those of their affiliated organizations, or those of the publisher, the editors and the reviewers. Any product that may be evaluated in this article or claim that may be made by its manufacturer is not guaranteed or endorsed by the publisher.
Research integrity at Frontiers
Learn more about the work of our research integrity team to safeguard the quality of each article we publish.