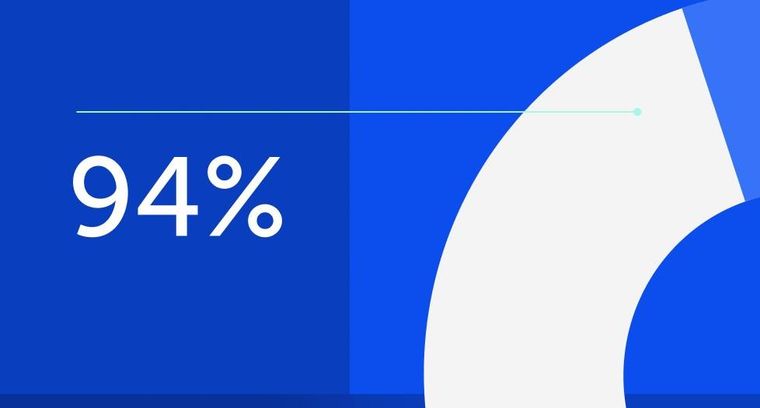
94% of researchers rate our articles as excellent or good
Learn more about the work of our research integrity team to safeguard the quality of each article we publish.
Find out more
SPECIALTY GRAND CHALLENGE article
Front. Membr. Sci. Technol., 18 May 2022
Sec. Membrane Modules and Processes
Volume 1 - 2022 | https://doi.org/10.3389/frmst.2022.913597
Membrane separation of various mixtures of organic and inorganic substances can be considered as one of the most energy-conserving separation methods. Continuing efforts in the development of new membranes with improved thermal, chemical, and enhanced transport properties have led to many new possible applications since the 1960s.
Various types of membranes are employed extensively for desalination, drinking water production, wastewater reclamation, and reuse. Development of novel membranes and new operational approaches offered promising opportunities to industry (Singh, 2015).
The water shortage is one of the serious global threats in the World. Membrane technologies can be applied to produce water of exceptional purity that can be recycled in a variety of places. The reuse of water is widely practiced in many industries and countries to decrease the demand on the available water and reduce stresses on environment and populations (Ali et al., 2017). In addition to the water process, there are many other application areas of membranes such as the manufacture of food and pharmaceutical products, production of base chemicals, energy conversion devices such as fuel cells, and in medical devices such as hemodialysis, blood oxygenators, and controlled drug delivery products, etc. (Singh, 2015). Furthermore, carbon dioxide capture and controlling the greenhouse gas emmisions are other areas of research which membranes have been playing a dominant role (Merkel et al., 2012; White et al., 2015; Sanaeepur et al., 2019). However, in all these applications, the module and process design are crucial. Figure 1 illustrates some important and challenging issues regarding the membrane processes. The discussions towards these issues are presented below.
Membrane system costs and applications depend mostly on the material used. The performance of a membrane for water treatment application is evaluated according to water flux and selectivity. But, an efficient and economically feasible industrial application will be possible if the membranes keep their integrity for their whole lifetime. Therefore, module design and fabrication are still important issues to be tackled. In addition to the compatibility of adhesives, seals, spacers, and feed distributors, some of the membrane system components such as housings and connectors need to be selected carefully. Especially in food applications, all these components have to be food-contact approved. In pressure-driven membrane operations, the use of both concentrates and permeate streams leaving the same membrane unit is another key issue. In most operations, while the product stream so-called permeate is collected, the other one so-called concentrate or brine is discharged as waste in membrane desalination processes. When it is not and the retentate is the desired product, like hemodialysis, food dewatering applications, or nitrogen generation etc. To have an economically feasible application and environmentally benign process, concentrate waste management is another key factor in real desalination operations (Muralidhara, 2010).
In membrane reactors and membrane gas separation, the membrane module should be durable under high operating temperature and pressure. Different parts of the membrane module should be resistant against corrosive chemicals, such as alkaline or acidic solutions. Moreover, the distribution of feed, permeate and retentate flows inside the membrane module is also important. In all these cases, the process requirements should be taken into consideration.
Membrane distillation (MD) process is generally used for treatment of saline wastewater. Although there has been much work on improving the design of MD systems, temperature polarization (TP) and high-energy consumption per unit of product water are the most important obstacles to its commercialization. Modification and configuration of MD systems and utilization of high-performance materials for membrane fabrication are reported in a review paper (Anvari et al., 2020). Coating thermally conductive or photonic nanomaterials on the membrane’s surface or using thermally conductive metallic based membranes are some of the challenges in this area. Also, it was reported that frame-like turbulence promoters and improved feed channels were useful to decrease TP (Anvari et al., 2020).
The first systematic study of how the membrane distillation heat transfer rates change as a function of module size and membrane permeability was studied in the literature (Dudchenko et al., 2020). According to the authors, additional work is needed to understand the effect of mass transfer through the membrane on heat transfer in large modules through multi-physics computational fluid dynamic studies (Dudchenko et al., 2020).
Recently, technology development in three dimensional (3D) printers could shed some light in membrane module design. 3D printing technology can facilitate fabricating membrane modules with complex geometries, which are not manufacturable using conventional techniques. Early research results revealed successful spacer design with promoted turbulence inside the membrane module, which could mitigate the fouling effect and enhance the permeate flux. Research in this field is now focused on printing the entire membrane module, which is really promising. However, there are still some remaining challenges, such as low resolution, material integrity, mechanical strength, etc. (Koo et al., 2021; Soo et al., 2021).
Pressure-driven membrane processes such as reverse osmosis (RO), nanofiltration (NF), ultrafiltration (UF), microfiltration (MF) along with membrane bioreactors (MBRs), membrane distillation (MD) and electromembrane processes such as electrodialysis (ED), electrodeionization (EDI) and reverse electrodialysis (RED) are the most dominant membrane-based technologies for different industrial processes. They offer great solutions to the problems such as water stress, energy production, reductions in mineral resources, etc. in modern society. Designing new unit operations based on membrane technologies and their integrations in the production cycles is needed to establish the best process intensification strategy in process engineering. What is more, when unit separation processes are enhanced by membranes, their effect is improved significantly. Hybrid systems combining membrane processes with other conventional separation technologies provide excellent opportunities to reduce energy consumption and minimize the environmental impact. The separations integrating membrane technology with conventional processes can fill the gap and actively develop the new designs for alternative technologies (Kabay and Bryjak, 2013). Membrane distillation bioreactor (MDBR) is an example in this field. This new approach, which combines the membrane bioreactor and membrane distillation technologies, could perform promisingly in wastewater treatment with minimized waste generation and greenhouse gases emission (Goh et al., 2015).
Similar improvement caused by the use of membrane offers a new perspective for the development of new separation units. As an example, the following systems can be compared: i) liquid-liquid extraction vs. perstraction, ii) sorption vs. sorption membrane filtration, iii) capacitive deionization vs. membrane capacitive deionization, iv) crystallization vs. membrane crystallization, v) distillation vs. membrane distillation, vi) evaporation vs. pervaporation, and so on (Cejna et al., 2021; Nakhjiri et al., 2022).
Recently, the reclamation of wastewater has been developed as an alternative to seawater desalination for industrial makeup, agricultural irrigation, and potable water production for indirect use. Membrane processes can be used in different configurations for wastewater reclamation and reuse in order to meet the quality requirements by water authorities (Cote et al., 2008). However, the membrane selectivity in order to provide high quality product is still challenging. Furthermore, membrane process could effectively be used in CO2 capture and greenhouse gases separation from industrial plant stacks. In the case of CO2 capture, very high gas permeance is a major requirement in order to deal with the very high gas flows.
Membrane processes are well-accepted clean and environmental-friendly separation technologies with lower energy consumption for conventional techniques. However, due to the use of non-degradable polymers and potentially harmful chemicals in membrane, module, and spacer fabrication, current membrane technologies are far from environmentally friendly scenarios. Therefore, the so-called clean nature of such membrane processes is seriously questionable. Moreover, the effect of membrane and module production on microplastic generation, environmental pollution, global warming, and human health, should be considered holistically. Therefore, it is crucial to give some thought to the next generation of membrane processes towards cleaner and more sustainable approaches.
Membrane separation technologies are not only employed for water and wastewater reclamation but are also used for the recovery of various resources such as salts, fertilizers, bio-compounds, energy, or other added-value products from various sources. Membrane technologies can be easily applied in the recovery of raw materials from brines. For this purpose, electrodialysis (ED) and membrane distillation crystallization (MDC) methods are the most often used alternatives. For example, the ion exchange membrane crystallizer combining reactive and membrane crystallization was investigated for recovery of high purity magnesium hydroxide from aqueous solutions (Corte et al., 2020). Membrane crystallization (MCr) is a promising process for ion and metal recovery from a wide range of sources. Recovery of lithium and phosphorous are among the recently recovered value-added chemicals using MCr process (Xie et al., 2016).
Forward osmosis (FO) is also another alternative process for the recovery of high-value compounds, especially in food and beverage rather than water reuse and desalination processes. On the other hand, FO technology is considered to be still in its infancy, and its potential should be demonstrated in full scale (Blandin et al., 2020).
Global energy expenditure is considered to increase due to the rapid growth of populations. Therefore, global warming due to carbon dioxide (CO2) emissions and air pollution issues are also expected to increase by using fossil fuels. By developing alternative and renewable energy resources, global problems regarding the demand for clean energy and environmental concerns might be resolved. A promising alternative to solve these issues is salinity gradient power (SGP) so-called “blue energy” which can generate electrical or mechanical energy by converting the chemical potential when two solutions with different salinities are mixed. As it does not release any toxic gas emissions, it is counted as sustainable and clean energy with minimized carbon footprint. The use of ion-exchange membranes for harvesting renewable energy seem to meet these challenges (Othman et al., 2021).
Recently, nanopore-based membranes were developed for harvesting the salinity gradient (blue) energy. A systematic analysis of the viability of nanopore-based power generation over multiple process scales was carried out (Wang et al., 2021). They studied on the mechanism of harvesting salinity gradient energy and the effects of pore selectivity and conductance on power generation.
Recent achievements in membrane technologies provide new challenges and opportunities to redesign the various processes from industrial production to desalination and water treatment by taking into consideration the basic requirements in the process intensification strategy. Indeed, being an energy-efficient and environmentally benign process giving a high-quality product with low cost will give a high chance to apply a membrane-based process in real industrial operations (Drioli et al., 2019). The development of novel membranes and membrane operations, innovative applications of membrane processes in space, energy production, biotechnology, and medicine are other topics attracting the attention of the new generation membrane engineers.
NK contributed to conception and design of the article and wrote the first draft of the manuscript. All co-authors contributed to manuscript revision, read, and approved the submitted version.
The authors declare that the research was conducted in the absence of any commercial or financial relationships that could be construed as a potential conflict of interest.
All claims expressed in this article are solely those of the authors and do not necessarily represent those of their affiliated organizations, or those of the publisher, the editors and the reviewers. Any product that may be evaluated in this article, or claim that may be made by its manufacturer, is not guaranteed or endorsed by the publisher.
The authors acknowledge Prof. Michael D. Guiver for his kind suggestions to improve this article.
Ali, A., Drioli, E., and Macedonio, F. (2017). Membrane Engineering for Sustainable Development: A Perspective. Appl. Sci. 7, 1026. doi:10.3390/app7101026
Ali, A., Quist-Jensen, C. A., Jørgensen, M. K., Siekierka, A., Christensen, M. L., Bryjak, M., et al. (2021). A Review of Membrane Crystallization, Forward Osmosis and Membrane Capacitive Deionization for Liquid Mining. Resour. Conservation Recycl. 168, 105273. doi:10.1016/j.resconrec.2020.105273
Anvari, A., Azimi Yancheshme, A., Kekre, K. M., and Ronen, A. (2020). State-of-the-art Methods for Overcoming Temperature Polarization in Membrane Distillation Process: A Review. J. Membr. Sci. 616, 118413. doi:10.1016/j.memsci.2020.118413
Blandin, G., Ferrari, F., Lesage, G., Le-Clech, P., Héran, M., and Martinez-Lladó, X. (2020). Forward Osmosis as Concentration Process: Review of Opportunities and Challenges. Membranes 10, 284. doi:10.3390/membranes10100284
Cote, P., Liu, M., and Siverns, S. (2008). “Water Reclamation and Desalination by Membranes,” in Advanced Membrane Technology and Applications”. Editors N. N. Li, A.G. Fane, W.S. Ho Winston, and T. Matsuura (John Wiley & Sons), 171–187. Available at: https://www.wiley.com/en-us/Advanced+Membrane+Technology+and+Applications-p-9780471731672.
Drioli, E., Giorno, L., and Macedonio, F. (2018). “Membrane Engineering”. Berlin/Boston (Walter de Gruyter GmbH). doi:10.1515/9783110281392
Dudchenko, A. V., Hardikar, M., Xin, R., Joshi, S., Wang, R., Sharma, N., et al. (2020). Impact of Module Design on Heat Transfer in Membrane Distillation. J. Membr. Sci. 601, 117898. doi:10.1016/j.memsci.2020.117898
Goh, S., Zhang, J., Liu, Y., and Fane, A. G. (2015). Membrane Distillation Bioreactor (MDBR) - A Lower Green-House-Gas (GHG) Option for Industrial Wastewater Reclamation. Chemosphere 140, 129–142. doi:10.1016/j.chemosphere.2014.09.003
Kabay, N., and Bryjak, M. (2013). “Hybrid Processes Combining Sorption and Membrane Filtration,” in Encyclopedia of Membrane Science and Technology”. Editors E.M.V. Hoek, and V.V. Tarabara (Wiley). doi:10.1002/9781118522318.emst079
Koo, J. W., Ho, J. S., An, J., Zhang, Y., Chua, C. K., and Chong, T. H. (2021). A Review on Spacers and Membranes: Conventional or Hybrid Additive Manufacturing? Water Res. 188, 116497. doi:10.1016/j.watres.2020.116497
La Corte, D., Vassallo, F., Cipollina, A., Turek, M., Tamburini, A., and Micale, G. (2020). A Novel Ionic Exchange Membrane Crystallizer to Recover Magnesium Hydroxide from Seawater and Industrial Brines. Membranes 10, 303. doi:10.3390/membranes10110303
Merkel, T. C., Zhou, M., and Baker, R. W. (2012). Carbon Dioxide Capture with Membranes at an IGCC Power Plant. J. Membr. Sci. 389, 441–450. doi:10.1016/j.memsci.2011.11.012
Muralidhara, H. S. (2010). “Challenges of Membrane Technology in the XXI Century,” in Membrane Technology-A Practical Guide to Membrane Technology and Applications in Food and Bioprocessing”. Editors Z.F. Cui, and H.S. Muralidhara (Chennai: Elsevier), 19–32. doi:10.1016/b978-1-85617-632-3.00002-1
Othman, N. H., Kabay, N., and Guler, E. (2021). Principles of Reverse Electrodialysis and Development of Integrated-Based System for Power Generation and Water Treatment: a Review. Rev. Chem. Eng. doi:10.1515/revce-2020-0070
Sanaeepur, H., Ebadi Amooghin, A., Bandehali, S., Moghadassi, A., Matsuura, T., and Van der Bruggen, B. (2019). Polyimides in Membrane Gas Separation: Monomer's Molecular Design and Structural Engineering. Prog. Polym. Sci. 91, 80–125. doi:10.1016/j.progpolymsci.2019.02.001
Singh, R. (2015). “Introduction to Membrane Technology, Chapter 1,” in Membrane Technology and Engineering for Water Purification”. Second Edition (Singh, Rajindar: AuthorElsevier). Available at: https://www.elsevier.com/books/membrane-technology-and-engineering-for-water-purification/singh/978-0-444-63362-0.
Soo, A., Ali, S. M., and Shon, H. K. (2021). 3D Printing for Membrane Desalination: Challenges and Future Prospects. Desalination 520 (15), 115366. doi:10.1016/j.desal.2021.115366
Taghvaie Nakhjiri, A., Sanaeepur, H., Ebadi Amooghin, A., and Shirazi, M. M. A. (2022). Recovery of Precious Metals from Industrial Wastewater towards Resource Recovery and Environmental Sustainability: A Critical Review. Desalination 527, 115510. doi:10.1016/j.desal.2021.115510
Wang, L., Wang, Z., Patel, S. K., Lin, S., and Elimelech, M. (2021). Nanopore-based Power Generation from Salinity Gradient: Why it Is Not Viable. ACS Nano 15, 4093–4107. doi:10.1021/acsnano.0c08628
White, L. S., Wei, X., Pande, S., Wu, T., and Merkel, T. C. (2015). Extended Flue Gas Trials with a Membrane-Based Pilot Plant at a One-Ton-Per-Day Carbon Capture Rate. J. Membr. Sci. 496 (15), 48–57. doi:10.1016/j.memsci.2015.08.003
Keywords: membrane module, membrane process, membrane technology, membrane separation, membrane
Citation: Kabay N, Shirazi MMA, Güler E and Bryjak M (2022) Grand Challenges in Membrane Modules and Processes. Front. Membr. Sci. Technol. 1:913597. doi: 10.3389/frmst.2022.913597
Received: 05 April 2022; Accepted: 19 April 2022;
Published: 18 May 2022.
Edited and reviewed by:
Michael D. Guiver, Tianjin University, ChinaCopyright © 2022 Kabay, Shirazi, Güler and Bryjak. This is an open-access article distributed under the terms of the Creative Commons Attribution License (CC BY). The use, distribution or reproduction in other forums is permitted, provided the original author(s) and the copyright owner(s) are credited and that the original publication in this journal is cited, in accordance with accepted academic practice. No use, distribution or reproduction is permitted which does not comply with these terms.
*Correspondence: Nalan Kabay, bmFsYW4ua2FiYXlAZWdlLmVkdS50cg==
Disclaimer: All claims expressed in this article are solely those of the authors and do not necessarily represent those of their affiliated organizations, or those of the publisher, the editors and the reviewers. Any product that may be evaluated in this article or claim that may be made by its manufacturer is not guaranteed or endorsed by the publisher.
Research integrity at Frontiers
Learn more about the work of our research integrity team to safeguard the quality of each article we publish.