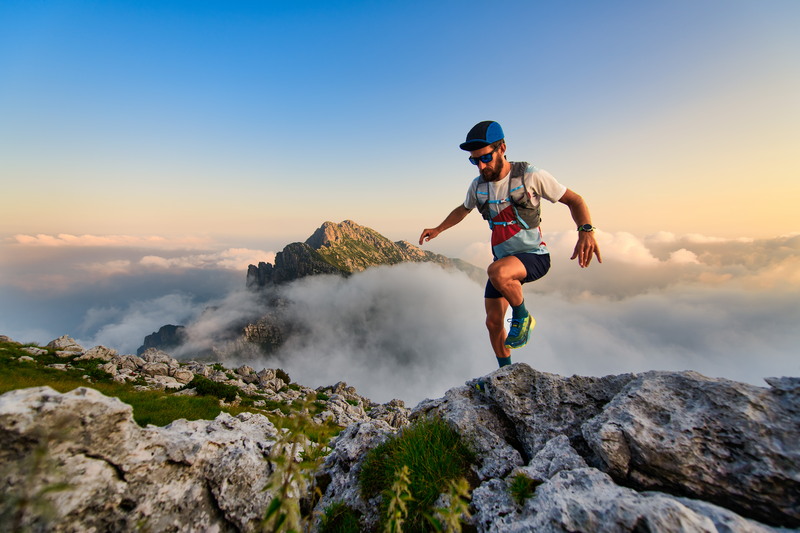
95% of researchers rate our articles as excellent or good
Learn more about the work of our research integrity team to safeguard the quality of each article we publish.
Find out more
SPECIALTY GRAND CHALLENGE article
Front. Membr. Sci. Technol. , 13 April 2022
Sec. Membrane Formation and Structure
Volume 1 - 2022 | https://doi.org/10.3389/frmst.2022.883913
Membrane technology offers a promising solution in various applications such as power generation (Jafary et al., 2020; Awang et al., 2021), gas purification (Mohammed et al., 2019), heavy metal remediation (Nasir et al., 2019a; Nasir et al., 2019b) seawater desalination (Purwanto et al., 2021), pathogen removal (Nasir et al., 2022) and wastewater treatment (Ismail and Goh, 2014). Morphology of the membrane plays a critical role in determining the final performance of the membrane such as the permeability and selectivity. Therefore, controlling the membrane morphology with respect to the desired application during the fabrication process is the main factor in developing efficacious membranes. Over the last few decades, research on membrane fabrication has qualified substantial advances in membrane technology and expanded the practicality of membranes in various applications. The selection of a technique for membrane fabrication depends on a choice of polymer and desired structure of the membrane. The most commonly used techniques for fabrication of membranes include phase inversion, interfacial polymerization, stretching, track-etching and electrospinning.
Aside from the commonly used polymeric membranes, inorganic-based membranes such as metal oxides, metal organic frameworks (MOFs), covalent organic frameworks (COFs), and carbon molecular sieve have sparked great interest in the preparation of inorganic membranes due to their tuneable and nanoscaled structural properties that can provide excellent performance. Metal oxides such as alumina, silica, titania or the mixtures of these components are some of the commonly used commercialized inorganic membranes. Contingent on the nature of the materials, inorganic membranes can be produced in thin film and multi-layer supporting structures that are sufficiently robust and permeable, or they can be constructed in self-supporting structures as freestanding sheets and tubes that are suitably permeable (Goh and Ismail, 2018). A typical inorganic membrane is composed of a macroporous support layer and a mesoporous or microporous active layer. Sol-gel is one of the most feasible methods for the preparation of metal oxide inorganic membranes. Depending on the media or solvent used, this technique can be further divided into the colloidal and polymeric sol-gel routes.
MOFs and COFs are a new class of crystalline porous materials with large surface area, tuneable pore size, and high functionality that make them ideal for membrane applications. Because of its zeolite-like structure and features such as excellent thermal and chemical durability, permanent porosity, and customizable pore diameters, the majority of MOF membranes are fabricated based on the structure of zeolite imidazolate frameworks (ZIFs) (Nordin et al., 2014; Nasir et al., 2018). Typically, MOF and COF membranes can be fabricated by sol-gel, in-situ growth, seeded-assisted or secondary growth, layer-by-layer assembly, interfacial polymerization, vapour deposition and solution casting (Fang et al., 2020). However, MOF membranes have low mechanical stability and the majority of them are fabricated on inorganic or polymeric porous supports in various forms depending on the desired application (Ahmad et al., 2017; Ahmad et al., 2018).
Although inorganic membranes offer high mechanical strength compared to polymer membranes, the processes used for obtaining inorganic membranes are slow and expensive due to high temperature (>1,000°C) requirements for the sintering process (Hubadillah et al., 2016). Industrial usage of inorganic membranes is less common due to their high production costs and difficulties in handling. The manufacturing of a porous membrane often entails numerous phases, with the coating of intermediate and final separation layers being accomplished on the prepared support layer. Normally, high-temperature sintering is necessary to join these layers (Sutharsini et al., 2018). Indeed, the intricacy of membrane manufacture and the high cost of beginning materials have resulted in the high production cost of inorganic membrane. Therefore, streamlining the multistep manufacturing procedures and using inexpensive and natural raw materials have been identified as the easiest ways to reducing inorganic membrane production time and cost.
Phase inversion results by the phase transformation from the liquid form of dope solution into solid membrane through a solidification process. Non-solvent induced phase separation (NIPS) is among the most popular technique for membrane fabrication (Jung et al., 2016). The morphology of the membrane can be tailored to control the mechanical properties, pore size distribution and the flux of the prepared membranes. In this procedure, a homogenous polymer solution is submerged in a coagulation bath and separates into two phases (Nasir et al., 2020).
Phase separation and solidification occur due to the exchange of solvent (from polymer dope solution) and non-solvent (coagulant from coagulation bath). Facilitating the mutual diffusion of coagulant and polymer dope solutions during NIPS is the key to obtain porous membranes with high permeability. These are two of the most significant issues in the phase inversion process; 1) the usage of huge volumes of water in the coagulation bath and 2) the generation of toxic wastewater due to the release of toxic solvent from polymer solution during fabrication of the membrane.
Theoretically, solvent-free membrane manufacturing techniques might be the most ecologically friendly technology. However, membranes have been typically fabricated by solution techniques for several decades. Regretfully, the majority of the solvents employed in membrane manufacture are hazardous, and their industrial application is strictly controlled. For example, the European Union limits the use of N-methyl-2-pyrrolidone (NMP), the most commonly used solvent in membrane production (Sherwood et al., 2018). Therefore, the utilization of green solvents as a strategy for sustainable membrane fabrication was introduced by researchers. Green solvents investigated include tributyl O-acetyl citrate, triethylene glycol diacetate (TEGDA), methyl-5-(dimethylamino)-2-methyl-5-oxopentanoate (RhodiasolvRPolarClean), Cyrene™ and organic carbonates (Figoli et al., 2014). However, the environmental impact of the production of the green solvent itself has not been addressed yet. Thus, any effort towards manufacturing sustainable membranes using a green solvent that is produced in a harmful manner might be worthless. Therefore, rather than focusing on the finished product, it is critical to address the upstream emissions of the solvents employed in membrane production in order to avoid any green solvent recognized as an environmental adverse impact carrier (Kim and Nunes, 2021).
To properly evaluate the sustainability of membrane fabrication, it is important to quantify the effect of the process from several viewpoints, including global warming, human carcinogenic toxicity, human non-carcinogenic toxicity, fossil resource scarcity, and marine ecotoxicity. Yadav et al., evaluated the environmental impact resulting from the choice of solvent (toxic and green solvent), choice of polymer, source of electricity and types of membrane fabrication (Yadav et al., 2021). According to Yadav et al., they found the choice of solvent and polymer and the source of electricity were identified as the major determinants of environmental impact and cost. By using a green solvent like ethylene carbonate, it can minimise environmental expenses and impacts by up to 35%. If a suitable green solvent is not available, a less harmful solvent can be used instead. Replacing fuel-based polymers such as PVDF or PSF with a bio-based alternative like cellulose acetate can have either a positive or negative environmental impact that depends on the production process of cellulose acetate; if the production of the bio-based polymer involves harmful steps, replacement may increase environmental costs. Using electricity obtained from renewable sources such as hydropower can further reduce the environmental impact of membrane production.
The process of interfacial polymerization (IP) is important in the production of thin active layers for both nanofiltration and reverse osmosis membranes (Solomon et al., 2012; Zirehpour et al., 2017). This method produces a highly crosslinked polyamide active layer on the surface of a microporous substrate by copolymerizing two immiscible reactive monomers in two distinct media (aqueous and organic) (Seah et al., 2020). However, the main drawback of this method is that it requires a substantial volume of organic solvents and monomers to accomplish film polymerization. Furthermore, unused solvent and monomers are not reusable unless they are recovered through post-treatment. There also a challenge of making thin film composite (TFC) membranes with alkali/acid stable selective layers. Although TFC membranes have demonstrated vicinity stability in harsh organic solvents, there was a report indicate that polyamide-based membranes lose performance when exposed to a high-pH solution (Lee et al., 2015). They hypothesised that the amide bonds in the polyamide layer are intrinsically prone to hydrolysis under alkaline conditions by direct nucleophilic attack of the hydroxyl group on the carbonyl group. Dissimilar to organic solvent, aqueous solutions at high pH contain extremely reactive ions that interact with covalent bonds in the polymer chain rather than interchain forces (e.g., van der Waals force) (Dalwani et al., 2011). Therefore, by eliminating the carbonyl groups in the selective layer and replacing them with a polyamine layer might significantly improve the alkaline resistance of the membranes. However, the presence of carbonyl groups in trimesoyl chloride (TMC) makes producing an alkaline-resistant TFC membrane when utilising TMC for interfacial polymerization very difficult. As a result, searching for viable monomers to build a thin polyamine layer via IP is a current research area. For the first time, Tashgiv et al., successfully investigated the potential 1,3,5-tris(bromomethyl)benzene (tBrMeB) as a carbonyl-free organic phase monomer in an interfacial polymerization reaction (Tashvigh et al., 2021). They found the membrane can withstand prolonged exposure to extreme pH (of 1 or 13 for 2 months) by manipulating the monomer structures and replacing p-phenylenediamine with m-phenylenediamine.
The addition of inorganic material as an additive in membrane matrix in order to boost the intrinsic properties of the native membrane is also a very popular approach reported by many researchers. The incorporation of the additive can be physically or chemically via many techniques such as simple blending, coatings (spray coating, dip-coating, etc.,), crosslinking by grafting and direct electrospinning. Leaching out of the inorganic materials to the environment could also create adverse effects. Therefore, a strategic selection in determining of the technique of incorporation by considering the stability of the interaction is crucial. For example, the chemical incorporation technique is favourable for a stable membrane structure. Considering pre-treatment or post-treatment on the physical attachment in the membrane is also important to avoid a leaching issue. Toxicity of the selected additive materials should also be main consideration.
Electrospinning is a simple way to make a nanofibrous membrane with a large specific area and porosity, which has a lot of potential in wastewater treatment (Ahmed et al., 2015; Nasir et al., 2021). Briefly, electrospinning is a method of producing nanofibers from a charged or melted polymer solution using a strong electric field. The electrospinning process is a potential method for producing highly productive porous membranes. However, membranes that are fabricated by electrospinning tend to have low mechanical strength due to high porosity. Other major challenges of electrospinning technique include high voltage utilization, high electric field dependency and low throughput. Therefore, it is important to enhance the technique in order to fabricate efficacious membranes.
Stretching is a technique for making highly porous hydrophobic membranes for membrane distillation application. This is a solvent-free method that involves heating the polymer over its melting point and extruding it into thin sheet shapes, then stretching it to make it porous (Wang et al., 2014). Stretching is usually done in two parts, with cold stretching first and then hot stretching. Cold stretching is used to nucleate micropores in the precursor film, followed by hot stretching to increase/control the final pore shape of the membrane. The ultimate porosity structure and qualities of the membranes are controlled by the physical properties of the material (such as crystallinity, melting temperature, tensile strength) and the applied processing parameters in this procedure. However, this technique consumes high energy due to the utilization of high and low operational temperature.
In track-etching technique, a nonporous polymeric membrane is bombarded with energetic heavy ions (such as uranium-235, iodine-127, silver-107, copper-64, and bromine-79), resulting in the development of linear damaged tracks across the irradiated polymeric membrane (Lalia et al., 2013). The irradiation time and temperature dictate membrane porosity, whereas the etching time and temperature determine pore size. However, because of the technological complexity of its fabrication, the main challenge of this approach is its high cost (Apel, 2001). Furthermore, because of their strong resistance to oxidation, certain polymeric materials, such as PVDF, take longer to produce pores.
Other challenges that might impede the fabrication of membranes include, difficulty in simultaneous control of the configuration of the membranes especially in hollow fiber formation. The hollow fiber membranes were tailored by hollow fiber spinning technologies involving a continuous extrusion of single or multiple fibers via a spinneret, followed by a solidification step (Yuliwati et al., 2011). However, there are multiple parameters that influence the properties of the hollow fibers, including air gap, bore fluid composition, bore fluid temperature, bore fluid flowrate, dope extrusion flowrate, dope extrusion pressure, dope viscosity, take-up speed, external coagulation composition, external coagulation temperature, residence time, and residence time. Changes to one parameter could result in undesirable effects to another property.
Membrane distillation (MD) is a thermally induced separation method that allows only vapours to pass through a microporous hydrophobic membrane (El-bourawi et al., 2006). The vapour pressure differential caused by the temperature difference across the membrane surface is the driving force in the MD process. Therefore, in order to fabricate MD membranes, the membrane material must either be hydrophobic by nature or the surface must be modified to be hydrophobic (Parani and Oluwafemi, 2021). The hydrophobicity of the membrane limits mass transfer of the liquid, resulting in the formation of a gas-liquid interface. Commonly, the most used polymers for MD include polypropylene (PP), polytetrafluoroethylene (PTFE), and polyvinylidene fluoride (PVDF) (Eykens et al., 2017). However, some of these membranes have low permeations, low hydrophobicity, fouling, high insolubility and wetting tendency (Purwanto et al., 2021). Another element to consider while selecting good MD membranes is thermal conductivity (Singh and Sirkar, 2012). In general, the thermal conductivity of the membranes should be as low as possible to reduce heat loss. Therefore, membrane properties such as hydrophobicity, pore size, porosity, and pore size distributions must be optimised because they play critical roles in determining MD performance by regulating mass and heat transfer and membrane wetting.
Another grand challenge in membrane fabrication is material selection. Material selection is an important process in membrane fabrication development because the qualities and properties of the materials can have a considerable impact on the physicochemical properties of the membranes that result. Polymers, solvents, additives and nanofillers are materials that are commonly used in fabrication of the membranes.
Polymers are the main component that determine the formation and application of the membrane through their properties. For example, polymeric materials like cellulose acetate (CA) (Riaz et al., 2016), polysulfone (PSf) (Nasir et al., 2019b) polyethersulfone (PES), (Pakdel Mojdehi et al., 2019), PVDF (Kuo et al., 2008), polyamide (PA) (Akther et al., 2019), and polydimethylsiloxane (PDMS) (Sadrzadeh et al., 2009) are often utilised as polymeric materials for membrane fabrication. However, due to the hydrophobic nature of these polymers, the effectiveness of these polymeric membranes for water treatment applications is still limited by low water permeability, selectivity and tendency to fouling.
Solvents have a significant impact on the morphological structure of membranes. The NMP (Li et al., 2014; Delavar et al., 2017), tetrahydrofuran (THF) (Zulhairun and Ismail, 2014), N,N-dimethyl formamide (DMF) (Yu et al., 2010), and N,N-dimethylacetamide (DMAc) are common solvents used to make membranes (Zhu et al., 2014; Karkooti et al., 2018). The desired membrane structure and, as a result, satisfactory membrane separation performance can be obtained with the right solvent selection.
Water-soluble polymers such as polyvinylpyrrolidone (PVP), polyethylene glycol (PEG), and tetraethylene glycol (TEG) have been extensively used as pore-forming additives to improve pore development inside the membrane structure (Bey et al., 2010). To construct membranes with high pure water fluxes, these chemicals are frequently utilised to raise viscosity, introduce hydrophilicity, promote pore formation, and inhibit macrovoid formation. The creation of finger-like or sponge-like structures in the membrane sublayer usually causes an increase in membrane water flow when PVP is added. Researchers previously showed that PVP with a greater molecular weight might reduce macrovoid development, resulting in a thicker skin layer and decreased water flux (Ong et al., 2014). However, excessive pore former addition, on the other hand, might have a negative impact on the pore size and mechanical strength of the resultant porous membranes (Kong et al., 2021).
The addition of nanofillers imparts significant effects on the membrane forming mechanism. Besides the effect of fast solvent-non solvent exchange during the phase inversion process, there is a common understanding that, incorporating hydrophilic nanofillers to the polymer matrix could increase the amorphous nature of membrane and enhance the water permeability. However, improper or excessive addition of nanofiller into the polymer matrix could deteriorate the membrane formation by agglomeration and poor distribution.
Fabrication techniques are continually improving to generate membranes in a more efficient, accurate, and waste-free manner. However, the science underlying modern membrane production is less well understood. The phase separation process, for example, is more of an art than a science when it comes to membrane manufacture (Low and Wang, 2021). Many factors and combinations of these factors, from environmental conditions (e.g., temperature, humidity, air quality) to membrane ingredients and chemicals used in pre-processing, processing, and post-processing (e.g., the composition of the raw materials), always fluctuate. Membranologists work around to modify a formula to achieve the desired membrane properties. Once a viable formula has been established, efforts are made to limit variations to these parameters for the same batch of membranes.
Future approaches for innovative membrane material production procedures should take into account not just the aforementioned challenges, but also more sustainable ways. Novel and green membrane manufacturing methods based on plant-based or agricultural waste should be investigated further. In conclusion, greater research into the material selection, fabrication and mechanism of membrane technology in wastewater treatment is needed. The goal of the journal Frontiers in Membrane Science and Technology in the section of Membrane Formation and Structure is to publish high-quality original research and review papers in this subject area by pledging to help play a key role in addressing and tackling these challenges.
JJ: conceptualization, writing, review and finalizing AN: writing original draft preparation.
The authors declare that the research was conducted in the absence of any commercial or financial relationships that could be construed as a potential conflict of interest.
All claims expressed in this article are solely those of the authors and do not necessarily represent those of their affiliated organizations, or those of the publisher, the editors and the reviewers. Any product that may be evaluated in this article, or claim that may be made by its manufacturer, is not guaranteed or endorsed by the publisher.
Ahmad, R., Kim, J., Kim, J., and Kim, J. (2017). Nanostructured Ceramic Photocatalytic Membrane Modified with a Polymer Template for Textile Wastewater Treatment. Appl. Sci. 7 (12), 1284. doi:10.3390/app7121284
Ahmad, R., Kim, J. K., Kim, J. H., and Kim, J. (2018). Effect of Polymer Template on Structure and Membrane Fouling of TiO 2/Al 2 O 3 Composite Membranes for Wastewater Treatment. J. Ind. Eng. Chem. 57, 55–63. doi:10.1016/j.jiec.2017.08.007
Ahmed, F. E., Lalia, B. S., and Hashaikeh, R. (2015). A Review on Electrospinning for Membrane Fabrication: Challenges and Applications. Desalination 356, 15–30. doi:10.1016/j.desal.2014.09.033
Akther, N., Phuntsho, S., Chen, Y., Ghaffour, N., and Shon, H. K. (2019). Recent Advances in Nanomaterial-Modified Polyamide Thin-Film Composite Membranes for Forward Osmosis Processes. J. Membr. Sci. 584 (May), 20–45. doi:10.1016/j.memsci.2019.04.064
Apel, P. (2001). Track Etching Technique in Membrane Technology. Radiat. Measurements 34 (1–6), 559–566. doi:10.1016/S1350-4487(01)00228-1
Asadi Tashvigh, A., Elshof, M. G., and Benes, N. E. (2021). Development of Thin-Film Composite Membranes for Nanofiltration at Extreme pH. ACS Appl. Polym. Mater. 3 (11), 5912–5919. doi:10.1021/acsapm.1c01172
Awang, N., Nasir, A. M., Yajid, M. A. M., and Jaafar, J. (2021). A Review on Advancement and Future Perspective of 3D Hierarchical Porous Aerogels Based on Electrospun Polymer Nanofibers for Electrochemical Energy Storage Application. J. Environ. Chem. Eng. 9, 105437. doi:10.1016/j.jece.2021.105437
Bey, S., Criscuoli, A., Figoli, A., Leopold, A., Simone, S., Benamor, M., et al. (2010). Removal of As(V) by PVDF Hollow Fibers Membrane Contactors Using Aliquat-336 as Extractant. Desalination 264 (3), 193–200. doi:10.1016/j.desal.2010.09.027
Dalwani, M., Benes, N. E., Bargeman, G., Stamatialis, D., and Wessling, M. (2011). Effect of pH on the Performance of Polyamide/polyacrylonitrile Based Thin Film Composite Membranes. J. Membr. Sci. 372 (1–2), 228–238. doi:10.1016/j.memsci.2011.02.012
Delavar, M., Bakeri, G., and Hosseini, M. (2017). Fabrication of Polycarbonate Mixed Matrix Membranes Containing Hydrous Manganese Oxide and Alumina Nanoparticles for Heavy Metal Decontamination: Characterization and Comparative Study. Chem. Eng. Res. Des. 120, 240–253. doi:10.1016/j.cherd.2017.02.029
El-bourawi, M. S., Ding, Z., Ma, R., and Khayet, M. (2006). A Framework for Better Understanding Membrane Distillation Separation Process. J. Membr. Sci. 285, 4–29. doi:10.1016/j.memsci.2006.08.002
Eykens, L., De Sitter, K., Dotremont, C., Pinoy, L., and Van der Bruggen, B. (2017). Membrane Synthesis for Membrane Distillation: A Review. Separat. Purif. Techn. 182, 36–51. doi:10.1016/j.seppur.2017.03.035
Fang, M., Montoro, C., and Semsarilar, M. (2020). Metal and Covalent Organic Frameworks for Membrane Applications. Membranes 10 (5), 107. doi:10.3390/membranes10050107
Figoli, A., Marino, T., Simone, S., Di Nicolò, E., Li, X.-M., He, T., et al. (2014). Towards Non-toxic Solvents for Membrane Preparation: a Review. Green. Chem. 16 (9), 4034–4059. doi:10.1039/C4GC00613E
Goh, P. S., and Ismail, A. F. (2018). A Review on Inorganic Membranes for Desalination and Wastewater Treatment. Desalination 434, 60–80. doi:10.1016/j.desal.2017.07.023
Hubadillah, S. K., Dzarfan Othman, M. H., Harun, Z., Ismail, A. F., Iwamoto, Y., Honda, S., et al. (2016). Effect of Fabrication Parameters on Physical Properties of Metakaolin-Based Ceramic Hollow Fibre Membrane (CHFM). Ceramics Int. 42 (14), 15547–15558. doi:10.1016/j.ceramint.2016.07.002
Ismail, A. F., and Goh, P. S. (2014). The Role and Prospect of Nanomaterials in Polymeric Membrane for Water and Wastewater Treatment: A State-Of-The-Art Overview. Adv. Mater. Res. 896, 3–6. doi:10.4028/www.scientific.net/amr.896.3
Jafary, T., Al-mamun, A., Alhimali, H., Baawain, M. S., Rahman, M. S., Rahman, S., et al. (2020). Enhanced Power Generation and Desalination Rate in a Novel Quadruple Microbial Desalination Cell with a Single Desalination Chamber. Renew. Sustain. Energ. Rev. 127, 109855. doi:10.1016/j.rser.2020.109855
Jimenez Solomon, M. F., Bhole, Y., and Livingston, A. G. (2012). High Flux Membranes for Organic Solvent Nanofiltration (OSN)-Interfacial Polymerization with Solvent Activation. J. Membr. Sci. 423-424, 371–382. doi:10.1016/j.memsci.2012.08.030
Jung, J. T., Kim, J. F., Wang, H. H., di Nicolo, E., Drioli, E., and Lee, Y. M. (2016). Understanding the Non-solvent Induced Phase Separation (NIPS) Effect during the Fabrication of Microporous PVDF Membranes via Thermally Induced Phase Separation (TIPS). J. Membr. Sci. 514, 250–263. doi:10.1016/j.memsci.2016.04.069
Karkooti, A., Yazdi, A. Z., Chen, P., McGregor, M., Nazemifard, N., and Sadrzadeh, M. (2018). Development of Advanced Nanocomposite Membranes Using Graphene Nanoribbons and Nanosheets for Water Treatment. J. Membr. Sci. 560, 97–107. doi:10.1016/j.memsci.2018.04.034
Kim, D., and Nunes, S. P. (2021). Green Solvents for Membrane Manufacture: Recent Trends and Perspectives. Curr. Opin. Green Sustain. Chem. 28, 100427. doi:10.1016/j.cogsc.2020.100427
Kong, X., Lu, X., and Ren, K. (2021). Towards High-Performance Polysulfone Membranes: A Controllable Membrane Formation Process Using Surfactant in NIPS. J. Taiwan Inst. Chem. Eng. 129, 171–179. doi:10.1016/j.jtice.2021.09.021
Kuo, C.-Y., Lin, H.-N., Tsai, H.-A., Wang, D.-M., and Lai, J.-Y. (2008). Fabrication of a High Hydrophobic PVDF Membrane via Nonsolvent Induced Phase Separation. Desalination 233 (1–3), 40–47. doi:10.1016/j.desal.2007.09.025
Lalia, B. S., Kochkodan, V., Hashaikeh, R., and Hilal, N. (2013). A Review on Membrane Fabrication: Structure, Properties and Performance Relationship. Desalination 326, 77–95. doi:10.1016/j.desal.2013.06.016
Lee, K. P., Zheng, J., Bargeman, G., Kemperman, A. J. B., and Benes, N. E. (2015). PH Stable Thin Film Composite Polyamine Nanofiltration Membranes by Interfacial Polymerisation. J. Membr. Sci. 478, 75–84. doi:10.1016/j.memsci.2014.12.045
Li, S., Liao, G., Liu, Z., Pan, Y., Wu, Q., Weng, Y., et al. (2014). Enhanced Water Flux in Vertically Aligned Carbon Nanotube Arrays and Polyethersulfone Composite Membranes. J. Mater. Chem. A. 2 (31), 12171–12176. doi:10.1039/c4ta02119c
Low, Z.-X., and Wang, H. (2021). Challenges in Membrane-Based Liquid Phase Separations. Green. Chem. Eng. 2 (1), 3–13. doi:10.1016/j.gce.2021.02.002
Mohammed, S. A., Nasir, A. M., Aziz, F., Kumar, G., Sallehhudin, W., Jaafar, J., et al. (2019). CO2/N2 Selectivity Enhancement of PEBAX MH 1657/Aminated Partially Reduced Graphene Oxide Mixed Matrix Composite Membrane. Separat. Purif. Techn. 223, 142–153. doi:10.1016/j.seppur.2019.04.061
Nasir, A. M., Adam, M. R., Mohamad Kamal, S. N. E. A., Jaafar, J., Othman, M. H. D., Ismail, A. F., et al. (2022). A Review of the Potential of Conventional and Advanced Membrane Technology in the Removal of Pathogens from Wastewater. Separat. Purif. Techn. 286, 120454. doi:10.1016/j.seppur.2022.120454
Nasir, A. M., Awang, N., Jaafar, J., Ismail, A. F., Othman, M. H. D., A. Rahman, M. M., et al. (2021). Recent Progress on Fabrication and Application of Electrospun Nanofibrous Photocatalytic Membranes for Wastewater Treatment: A Review. J. Water Process Eng. 40, 101878. doi:10.1016/j.jwpe.2020.101878
Nasir, A. M., Goh, P. S., Abdullah, M. S., Ng, B. C., and Ismail, A. F. (2019a). Adsorptive Nanocomposite Membranes for Heavy Metal Remediation: Recent Progresses and Challenges. Chemosphere 232, 96–112. doi:10.1016/j.chemosphere.2019.05.174
Nasir, A. M., Goh, P. S., and Ismail, A. F. (2019b). Highly Adsorptive Polysulfone/hydrous Iron-Nickel-Manganese (PSf/HINM) Nanocomposite Hollow Fiber Membrane for Synergistic Arsenic Removal. Separat. Purif. Techn. 213, 162–175. doi:10.1016/j.seppur.2018.12.040
Nasir, A. M., Goh, P. S., and Ismail, A. F. (2020). “Synthesis Route for the Fabrication of Nanocomposite Membranes,” in Micro and Nano Technologies (Netherland: Elsevier), 69–89. doi:10.1016/B978-0-12-816710-6.00003-1
Nasir, A. M., Md Nordin, N. A. H., Goh, P. S., and Ismail, A. F. (2018). Application of Two-Dimensional Leaf-Shaped Zeolitic Imidazolate Framework (2D ZIF-L) as Arsenite Adsorbent: Kinetic, Isotherm and Mechanism. J. Mol. Liquids 250, 269–277. doi:10.1016/j.molliq.2017.12.005
Nordin, N. A. H. M., Ismail, A. F., Mustafa, A., Goh, P. S., Rana, D., and Matsuura, T. (2014). Aqueous Room Temperature Synthesis of Zeolitic Imidazole Framework 8 (ZIF-8) with Various Concentrations of Triethylamine. RSC Adv. 4 (63), 33292–33300. doi:10.1039/C4RA03593C
Ong, C. S., Lau, W. J., Goh, P. S., Ng, B. C., Matsuura, T., and Ismail, A. F. (2014). Effect of PVP Molecular Weights on the Properties of PVDF-TiO2Composite Membrane for Oily Wastewater Treatment Process. Separat. Sci. Techn. 49, 2303–2314. doi:10.1080/01496395.2014.928323
Pakdel Mojdehi, A., Pourafshari Chenar, M., Namvar-Mahboub, M., and Eftekhari, M. (2019). Development of PES/polyaniline-modified TiO2 Adsorptive Membrane for Copper Removal. Colloids Surf. A: Physicochemical Eng. Aspects 583, 123931. doi:10.1016/j.colsurfa.2019.123931
Parani, S., and Oluwafemi, O. S. (2021). Membrane Distillation: Recent Configurations, Membrane Surface Engineering, and Applications. Membranes 11 (12), 934. doi:10.3390/membranes11120934
Purwanto, M., Kusuma, N. C., Sudrajat, M. r. A., Jaafar, J., Nasir, A. M., Aziz, M. H. A., et al. (2021). Seawater Desalination by Modified Membrane Distillation: Effect of Hydrophilic Surface Modifying Macromolecules Addition into PVDF Hollow Fiber Membrane. Membranes 11 (12), 924. doi:10.3390/membranes11120924
Riaz, T., Ahmad, A., Saleemi, S., Adrees, M., Jamshed, F., Hai, A. M., et al. (2016). Synthesis and Characterization of Polyurethane-Cellulose Acetate Blend Membrane for Chromium (VI) Removal. Carbohydr. Polym. 153, 582–591. doi:10.1016/j.carbpol.2016.08.011
Sadrzadeh, M., Amirilargani, M., Shahidi, K., and Mohammadi, T. (2009). Gas Permeation through a Synthesized Composite PDMS/PES Membrane. J. Membr. Sci. 342, 236–250. doi:10.1016/j.memsci.2009.06.047
Seah, M. Q., Lau, W. J., Goh, P. S., Tseng, H.-H., Wahab, R. A., and Ismail, A. F. (2020). Progress of Interfacial Polymerization Techniques for Polyamide Thin Film (Nano)composite Membrane Fabrication: A Comprehensive Review. Polymers 12 (12), 2817–2839. doi:10.3390/polym12122817
Sherwood, J., Farmer, T. J., and Clark, J. H. (2018). Catalyst: Possible Consequences of the N-Methyl Pyrrolidone REACH Restriction. Chem 4 (9), 2010–2012. doi:10.1016/j.chempr.2018.08.035
Singh, D., and Sirkar, K. K. (2012). Desalination of Brine and Produced Water by Direct Contact Membrane Distillation at High Temperatures and Pressures. J. Membr. Sci. 389, 380–388. doi:10.1016/j.memsci.2011.11.003
Sutharsini, U., Thanihaichelvan, M., and Singh, R. (2018). “Two-Step Sintering of Ceramics,” in Sintering of Functional Materials. Editor I. Shishkovsky (United Kingdom: InTech), 01–21. doi:10.5772/68083
Wang, H., Ding, S., Zhu, H., Wang, F., Guo, Y., Zhang, H., et al. (2014). Effect of Stretching Ratio and Heating Temperature on Structure and Performance of PTFE Hollow Fiber Membrane in VMD for RO Brine. Separat. Purif. Techn. 126 (Suppl. C), 82–94. doi:10.1016/j.seppur.2014.02.027
Yadav, P., Ismail, N., Essalhi, M., Tysklind, M., Athanassiadis, D., and Tavajohi, N. (2021). Assessment of the Environmental Impact of Polymeric Membrane Production. J. Membr. Sci. 622, 118987. doi:10.1016/j.memsci.2020.118987
Yu, X., Xiang, H., Long, Y., Zhao, N., Zhang, X., and Xu, J. (2010). Preparation of Porous Polyacrylonitrile Fibers by Electrospinning a Ternary System of PAN/DMF/H2O. Mater. Lett. 64 (22), 2407–2409. doi:10.1016/j.matlet.2010.08.006
Yuliwati, E., Ismail, A. F., Matsuura, T., Kassim, M. A., and Abdullah, M. S. (2011). Characterization of Surface-Modified Porous PVDF Hollow Fibers for Refinery Wastewater Treatment Using Microscopic Observation. Desalination 283, 206–213. doi:10.1016/j.desal.2011.02.037
Zhu, W.-P., Sun, S.-P., Gao, J., Fu, F.-J., and Chung, T.-S. (2014). Dual-layer Polybenzimidazole/polyethersulfone (PBI/PES) Nanofiltration (NF) Hollow Fiber Membranes for Heavy Metals Removal from Wastewater. J. Membr. Sci. 456, 117–127. doi:10.1016/j.memsci.2014.01.001
Zirehpour, A., Rahimpour, A., and Ulbricht, M. (2017). Nano-sized Metal Organic Framework to Improve the Structural Properties and Desalination Performance of Thin Film Composite Forward Osmosis Membrane. J. Membr. Sci. 531 (March), 59–67. doi:10.1016/j.memsci.2017.02.049
Keywords: membrane science and technology, membrane fabrication, membrane formation, membrane morphology, membrane structure
Citation: Jaafar J and Nasir AM (2022) Grand Challenge in Membrane Fabrication: Membrane Science and Technology. Front. Membr. Sci. Technol. 1:883913. doi: 10.3389/frmst.2022.883913
Received: 25 February 2022; Accepted: 25 March 2022;
Published: 13 April 2022.
Edited and reviewed by:
Michael D. Guiver, Tianjin University, ChinaCopyright © 2022 Jaafar and Nasir. This is an open-access article distributed under the terms of the Creative Commons Attribution License (CC BY). The use, distribution or reproduction in other forums is permitted, provided the original author(s) and the copyright owner(s) are credited and that the original publication in this journal is cited, in accordance with accepted academic practice. No use, distribution or reproduction is permitted which does not comply with these terms.
*Correspondence: Juhana Jaafar, anVoYW5hQHBldHJvbGV1bS51dG0ubXk=
Disclaimer: All claims expressed in this article are solely those of the authors and do not necessarily represent those of their affiliated organizations, or those of the publisher, the editors and the reviewers. Any product that may be evaluated in this article or claim that may be made by its manufacturer is not guaranteed or endorsed by the publisher.
Research integrity at Frontiers
Learn more about the work of our research integrity team to safeguard the quality of each article we publish.