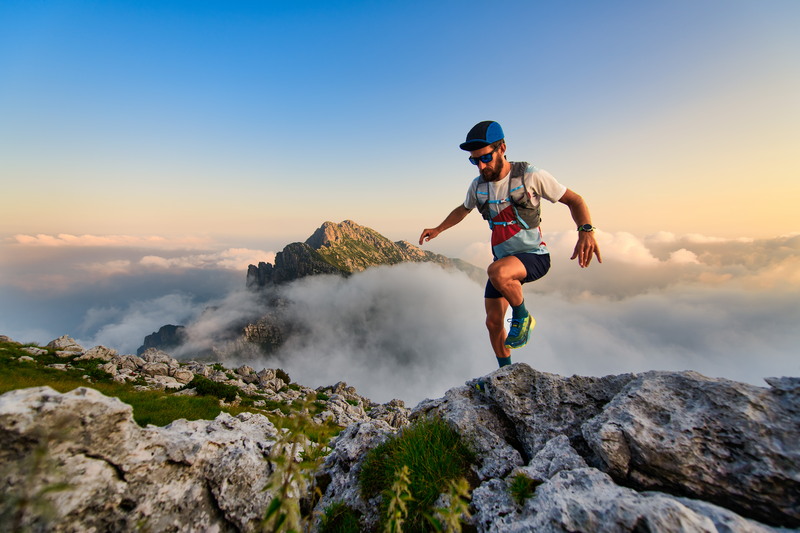
94% of researchers rate our articles as excellent or good
Learn more about the work of our research integrity team to safeguard the quality of each article we publish.
Find out more
HYPOTHESIS AND THEORY article
Front. Mech. Eng.
Sec. Mechatronics
Volume 11 - 2025 | doi: 10.3389/fmech.2025.1562920
The final, formatted version of the article will be published soon.
You have multiple emails registered with Frontiers:
Please enter your email address:
If you already have an account, please login
You don't have a Frontiers account ? You can register here
In response to the problems of low efficiency and safety hazards in traditional subsea pipeline intersection isolation release operations, this study designs a new type of automatic deployment device for subsea oil and gas pipeline intersection isolation, aimed at replacing manual and unmanned underwater vehicles (ROVs) for underwater deployment and monitoring. The device adopts an innovative framework structure design, significantly improving its resistance to water flow, and enhancing the operability and accuracy of underwater operations through a ducted propeller propulsion system. This study used computational fluid dynamics (CFD) combined with multiple reference frame (MRF) method to conduct detailed simulation analysis of the fluid dynamics characteristics of the device under different motion states, and explored its optimal working conditions. The simulation results show that during rotational motion, when the flow velocity exceeds 0.5 m/s, the resistance experienced by the device significantly increases, reaching a maximum of 7066.33 N. In addition, this study conducted an in-depth analysis of the causes of flow separation and resistance distribution under different motion states, revealing the important impact of frame style exterior design on the hydrodynamic performance and stability of the device. The research results indicate that the automatic placement device can efficiently complete the placement task of isolation materials in a water flow environment of 0.75 m/s, with a maximum driving torque of 6750 N*m, and has good engineering application prospects. The design proposed in this article not only provides a new perspective and solution for deep-sea pipeline protection technology, but also lays an important theoretical foundation for research and application in this field through innovative structural design and advanced simulation analysis methods.
Keywords: automatic deployment device, innovative framework structure design, CFD with MRF, a ducted propeller propulsion system, improving resistance to water flow
Received: 18 Jan 2025; Accepted: 17 Feb 2025.
Copyright: © 2025 Han, He, Ma, Li and Wan. This is an open-access article distributed under the terms of the Creative Commons Attribution License (CC BY). The use, distribution or reproduction in other forums is permitted, provided the original author(s) or licensor are credited and that the original publication in this journal is cited, in accordance with accepted academic practice. No use, distribution or reproduction is permitted which does not comply with these terms.
* Correspondence:
Jun Han, China Ship Scientific Research Center (CSSRC), Wuxi City, China
Disclaimer: All claims expressed in this article are solely those of the authors and do not necessarily represent those of their affiliated organizations, or those of the publisher, the editors and the reviewers. Any product that may be evaluated in this article or claim that may be made by its manufacturer is not guaranteed or endorsed by the publisher.
Research integrity at Frontiers
Learn more about the work of our research integrity team to safeguard the quality of each article we publish.